摘 要: 为解决双向励磁涡流检测传感器的信号解调问题,设计了适用于低频范围的正交解调电路(包括移相器、模拟乘法器以及低通滤波器),并对电路各模块的特性进行了测试. 通过在移相器中设置滑动变阻器调节两级运放的输入、输出阻抗,可以实现对10~30 kHz内正弦信号的90°相移,测试了乘法器在工作频段内的直流偏置特性. 将解调电路与双向励磁涡流检测传感器应用于钢块不同深度缺陷的检. 结果表明:偏置电压基本不随工作频率而波动,进行差值补偿后,计算与电路输出结果的互相关系数为0.955 1,整体解调电路对信号解调的幅值误差小于13%,相位解调误差小于8%. 可以检测出45号钢中深7 mm的槽型缺陷,且随着缺陷深度的增加,幅值和相位均呈增长趋势.
关键词: 双向涡流; 正交解调; 移相器; 模拟乘法器
受集肤效应限制,常规涡流检测方法对铁磁性构件的表面缺陷较为敏感,一般检测深度小于5 mm[1]. 对于给定的铁磁性构件,提升涡流检测深度最直接方法是降低工作频率,如从较常使用的100 kHz~200MHz改至小于30 kHz的低频范围[2-4]. Joneit等[3]采用频率为50~200 kHz的涡流检测铁磁性地下管道的表面缺损、管壁均匀变薄等腐蚀状况,可检测出深度为0.5~2.0 mm的表面缺陷,且检测信号相位差随缺陷深度增加呈指数递增趋势. Cardoso等[4]采用10~20 kHz的低频涡流检测钢管壁厚,通过改变激励线圈与接收线圈的距离,结果显示接收信号与壁厚近似线性正相关. 另一方面,通过设计励磁线圈的工作模式,可实现表面涡流场的抑制,增强涡流对较深缺陷的检测能力. Janousek等[5]采用2组水平布置的矩形励磁线圈,控制2组线圈的励磁电流方向相反,通过调节励磁电流比例,实现了表面涡流场的抑制,检测出超出集肤深度范围内的缺陷. 陈振茂等[6]在此基础上,进一步调节激励电流相位差,使得导体表面位于检出线圈正下方处的涡流为零,这一改进可将涡流的检测深度加倍.
采用双向涡流检测时,对接收线圈输出电压信号的准确解调是获取缺陷信息的关键. 正交解调是常用的信号解调方法. 李少华等[7]针对电阻率的涡流检测方法,采用MC1496型模拟乘法器设计了正交解调电路模块,测试分析了电路对频率为600 kHz正弦信号的幅值、相位解调性能. 高军哲等[8]基于模拟乘法器AD734和低通滤波器MAX291,设计了正交锁定放大器,用于微弱涡流信号的幅值、相位解调,并在管道涡流探伤系统(工作频率400 Hz)中进行了试验验证.
本文采用双向励磁涡流检测传感器,工作于10~30 kHz低频内,对钢块缺陷中不同深度的槽型缺陷进行扫查检测. 主要针对低频涡流检测信号,设计出一种工作频率可调、解调精度高的解调电路,并进行试验测试,分析出解调得到的电阻抗与槽型缺陷深度的关系.
1 双向涡流检测信号的正交解调
1.1 检测原理
当采用单一圆柱形励磁线圈对被测平面试件提供励磁场时,被测试件中沿深度方向z的涡流密度J(z)与激励频率f,材料磁导率μ及电导率σ有关,表达式为
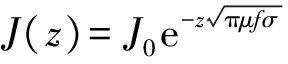
(1)
式中J0为试件表面涡流密度. 一般地,以涡流密度衰减至J0/e对应的深度为涡流的集肤深度. 涡流的探测深度一般以3~5倍集肤深度进行估算. 若铁的相对磁导率为10,工作频率为10 kHz时,单个涡流线圈的探测深度为1.5~2.0 mm.
当工作频率固定为10 kHz时,采用正、反双向励磁线圈形式可有效改善涡流场在试件中的分布,主要体现在表面涡流密度得到抑制,有效集肤深度增加,如图1所示. 正、反向励磁线圈各自在试件中形成的涡流场分布示意图如图2所示. 由于提离距离不同,正、反向励磁线圈在试件表面形成的涡流密度存在差异,相互叠加后归一化合成的涡流场使涡流密度峰值分布向试件内部偏移,此时探测深度可增加至3.6~7.0 mm,即相比单个涡流线圈的探测深度增加1~2倍.
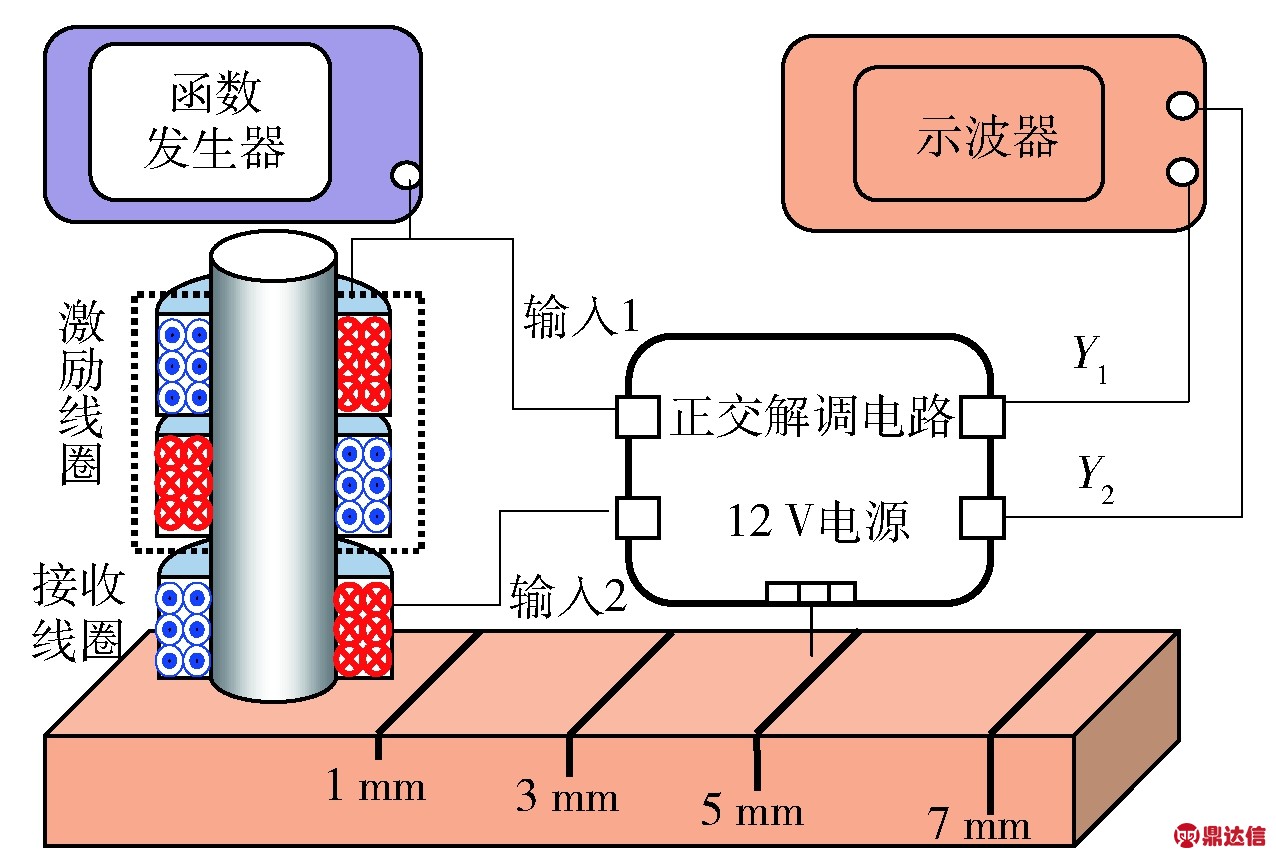
图1 检测装置示意图
Fig.1 Schematic diagram of experimental set-up
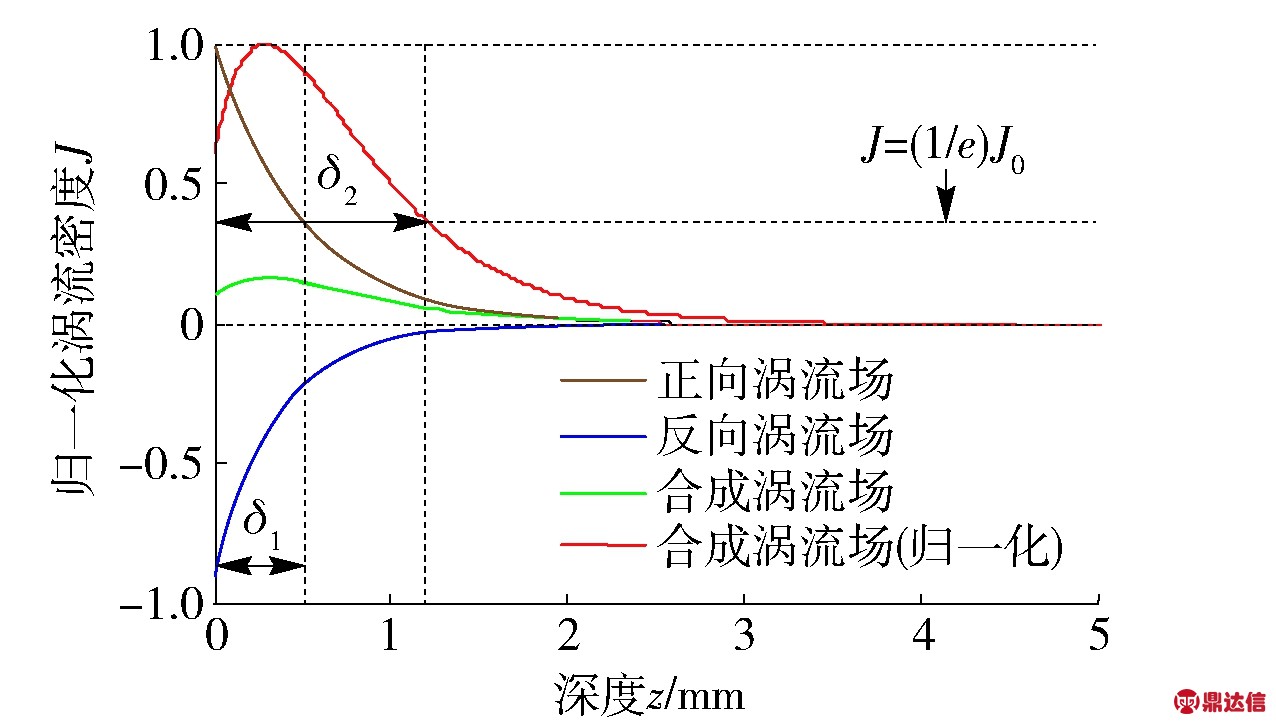
图2 涡流场分布示意图
Fig.2 Eddy current field distribution diagram
采用上述双向励磁方式,设计图1所示涡流检测传感器,通过仿真确定参数. 激励与接收线圈的外径均为20 mm,高度均为15 mm,铜线匝数为300. 3个线圈同轴布置,内部铁氧体磁芯外径为10 mm.
检测时,任意函数发生器输出单频正弦信号至激励线圈,激励信号频率范围为10~30 kHz. 接收信号的检测电压信号输入本文后续设计的正交解调电路,解调后的直流分量被示波器采集. 利用传感器检测图1试件中的槽型缺陷,以获取试验信号,用于测试低频范围(10~30 kHz)内硬件电路对双向励磁涡流检测信号的解调能力. 缺陷为45号钢块中电火花加工的长30 mm、宽1 mm,深度分别为1、3、5、7 mm的4个切槽.
1.2 正交解调电路设计
涡流检测时,激励电压信号Ui(t)以幅值为Ae的单频(角频率为ω)正弦信号模拟.
接收线圈输出的电压信号Uo(t)为
u(t)=Arsin (ωt+α)
(2)
相比激励电压,接收信号幅值Ar,存在一定的相位差α. 当涡流传感器沿试件表面扫查时,幅值Ar和相位α随时间的变化曲线反映缺陷位置及尺寸信息. 因此,从接收信号解调出Ar(t)和α(t)是涡流检测信号分析的前提. 这里基于正交解调方法,采用硬件电路实现信号的解调,制作的解调电路实物如图3所示,包括移相器、2路模拟乘法器和2组低通滤波器.
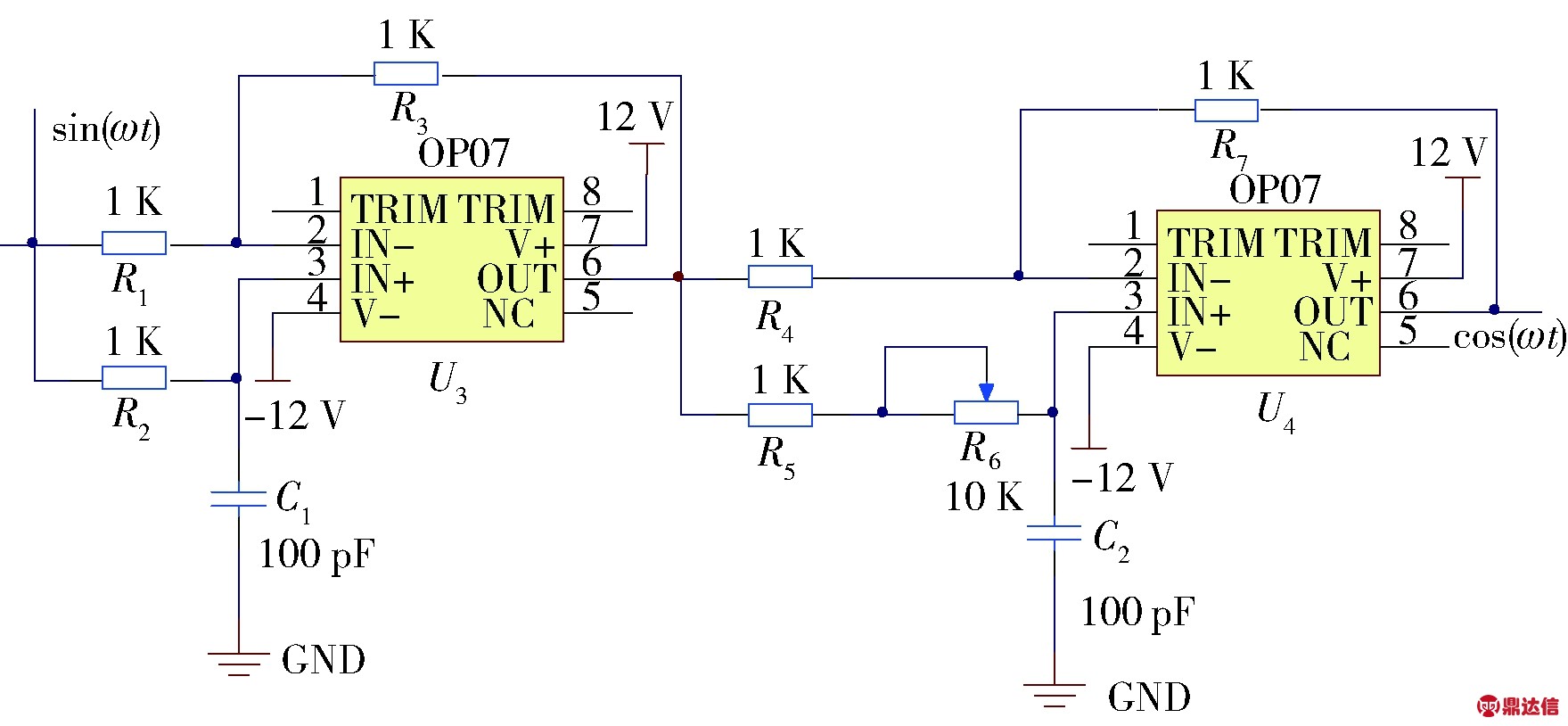
图4 移相器原理
Fig.4 Schematic circuit diagram of phase shifter
首先,采用移相器将激励信号进行相位偏移90°,得到单频余弦信号Us(t);接着,采用2个乘法器,将接收信号Ar(t)分别与上述2路单频信号进行模拟相乘,得到信号
Uo(t)Ui(t)=AeArsin(2ωt+α)+
AeArsin α
(3)
Uo(t)Us(t)=AeArcos(2ωt+α)+
AeArcos α
(4)
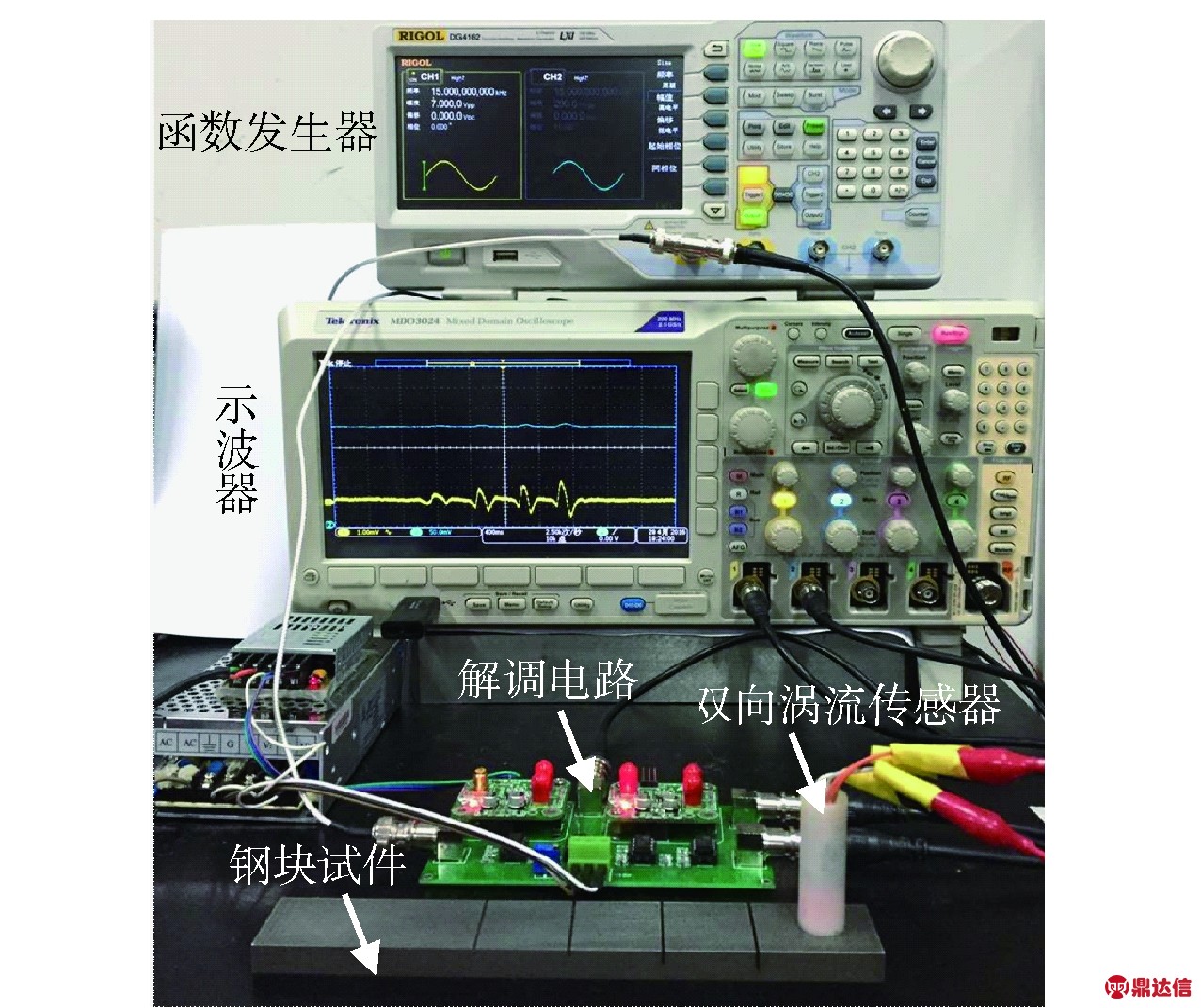
图3 电路实物
Fig.3 Picture of the circuit board
式(3)(4)中右侧第1项为高频成分,第2项为直流分量,分别代表检测线圈阻抗的电阻R和电抗X的信息(包含幅值Ar和相位α信息). 最后,将2路相乘后的信号分别通入低通滤波器,滤除高频成分,即可进行简单计算得出幅值和相位变化曲线Ar(t)和α(t),
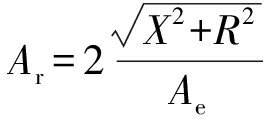
(5)
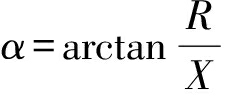
(6)
图4给出了移相器的电路图,基于移相放大器OP07芯片设计. 为实现在不同频率下均可准确相移,在一阶运放输出端与二阶运放输入端间接入滑动变阻器R6,以调整运放的输入阻抗,实现对不同频率信号的相位偏移量控制. 模拟乘法器选用了美国Analog Devices公司的宽带四象限模拟乘法芯片AD835,其在小于250 MHz、±1 V输入电压范围内具有良好的线性度,如图5所示. 选择有源二阶RC电路作为低通滤波器,其截止频率约为5 kHz,可以有效滤除检测信号中包含的10~30 kHz频率成分.
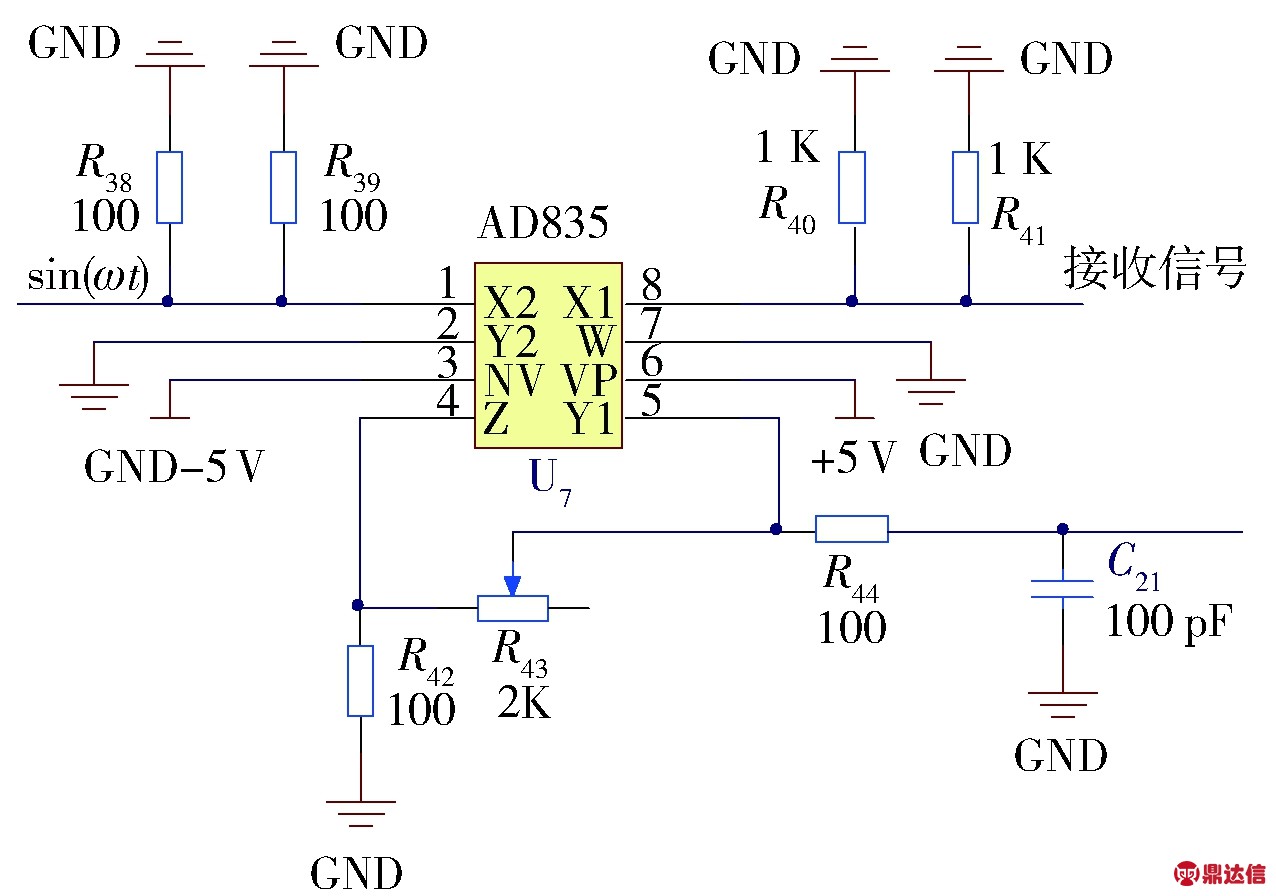
图5 模拟乘法器电路原理
Fig.5 Schematic circuit diagram of anolog multiplier
2 解调电路性能的测试
对图3所示解调电路的各个模块(移相器、模拟乘法器和低通滤波器)分别进行测试,以标定出各模块的电路特性.
2.1 移相器
函数发生器输出单频正弦信号至移相器输入端口,将移相器输出端口的信号与输入信号进行相位差计算,并调整滑动变阻器,改变相移量. 以90°相移为目标,在5~50 kHz内的测试结果如图6所示. 在频率处于10~30 kHz时,电路均能对输入的正弦信号实现精确的90°相移. 对应边界10 kHz和30 kHz的情形,滑动变阻器的阻值分别为最大值(10.3 kΩ)和最小值(0 Ω). 在小于10 kHz和大于30 kHz频率范围,受限于滑动变阻器的调节范围,电路对输入正弦信号的相移量均难以达到90°.
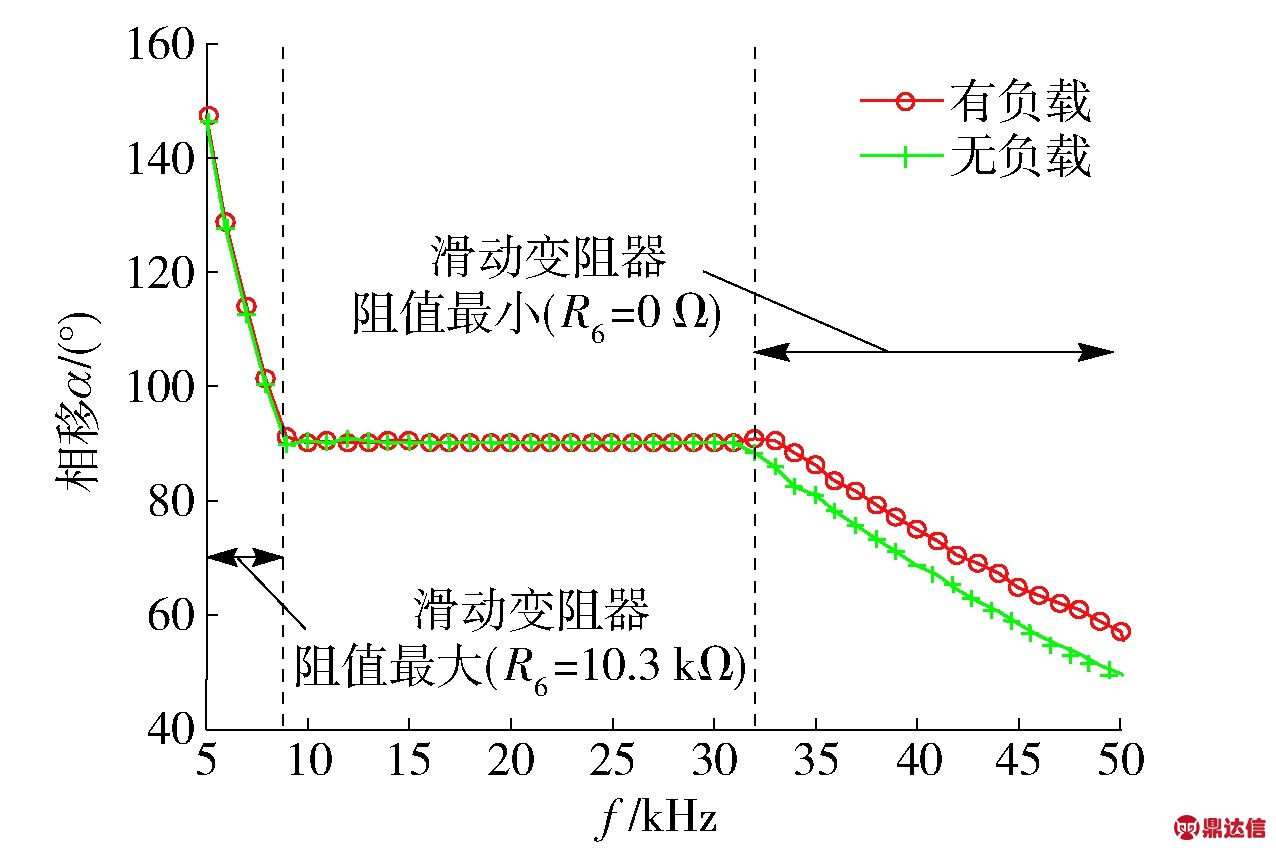
图6 不同频率下的相移情况
Fig.6 Phase shift under different frequency
当移相器与后端电路(乘法器、滤波器)相连接时,后端电路作为负载会影响移相器的输入阻抗部分,进而导致信号产生额外的相位偏移. 进一步地,采用上述方法测试后端电路对移相器特性的影响,如图7所示.
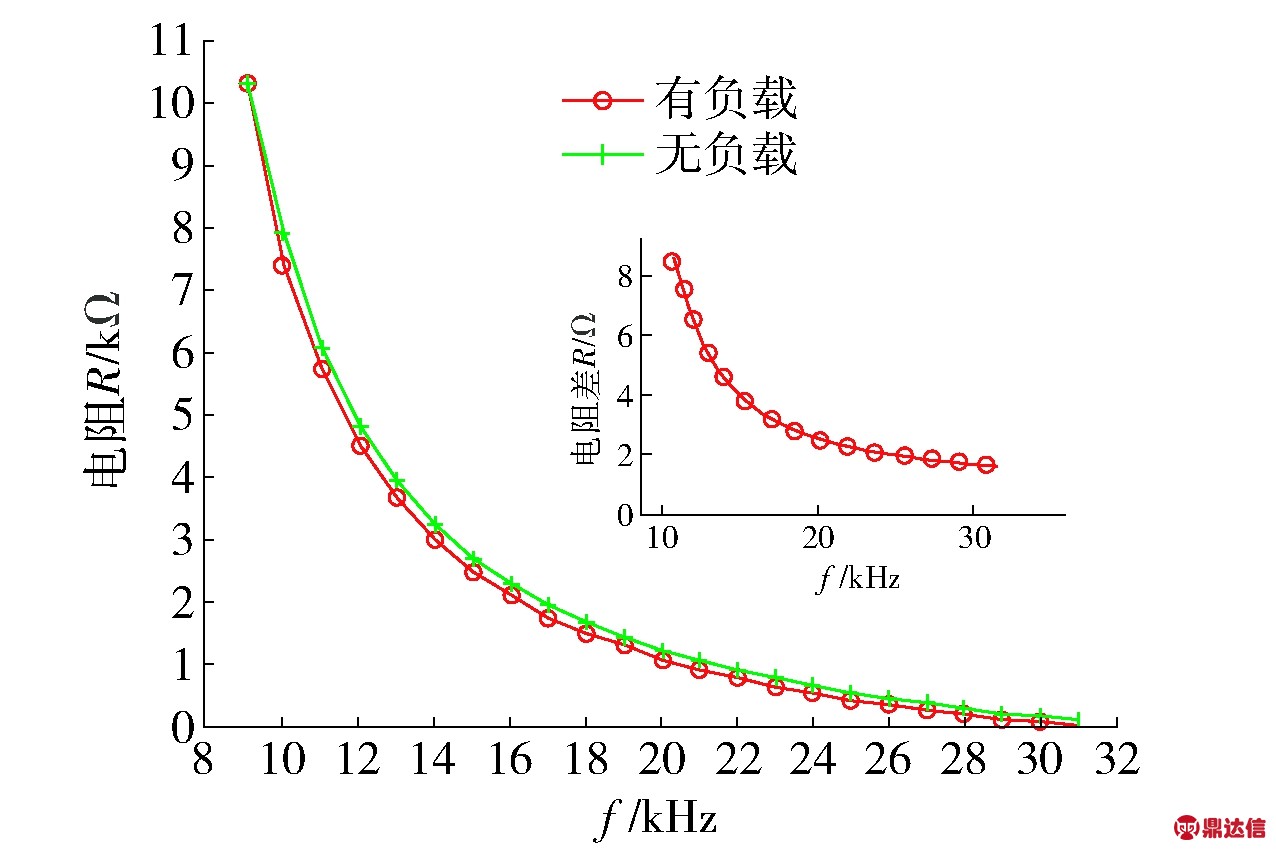
图7 90°相移时频率- 电阻曲线
Fig.7 Resistance-frequency curve under 90° phase shift
对比可看出,引入后端电路后,微小调节滑动变阻器(5~15 Ω),仍可在10~30 kHz内实现90°相移. 例如在频率15 kHz时,初始滑动变阻器阻值为3 kΩ,引入后端电路后,要实现相移90°,只需将阻值增加约5 Ω(原阻值的0.16%). 这表明后续电路负载对移相结果的影响较小. 利用图7标定的阻值- 频率结果,即可针对特定工作频率进行精确调整.
2.2 模拟乘法器
依据前述测试结果,设置移相器参数,使其能够对15 kHz的正弦信号进行准确的相移90°. 将标准正弦信号(相位为0)与相移的信号输入至模拟乘法器,2路信号的幅值均为0.1 V,如图8所示.
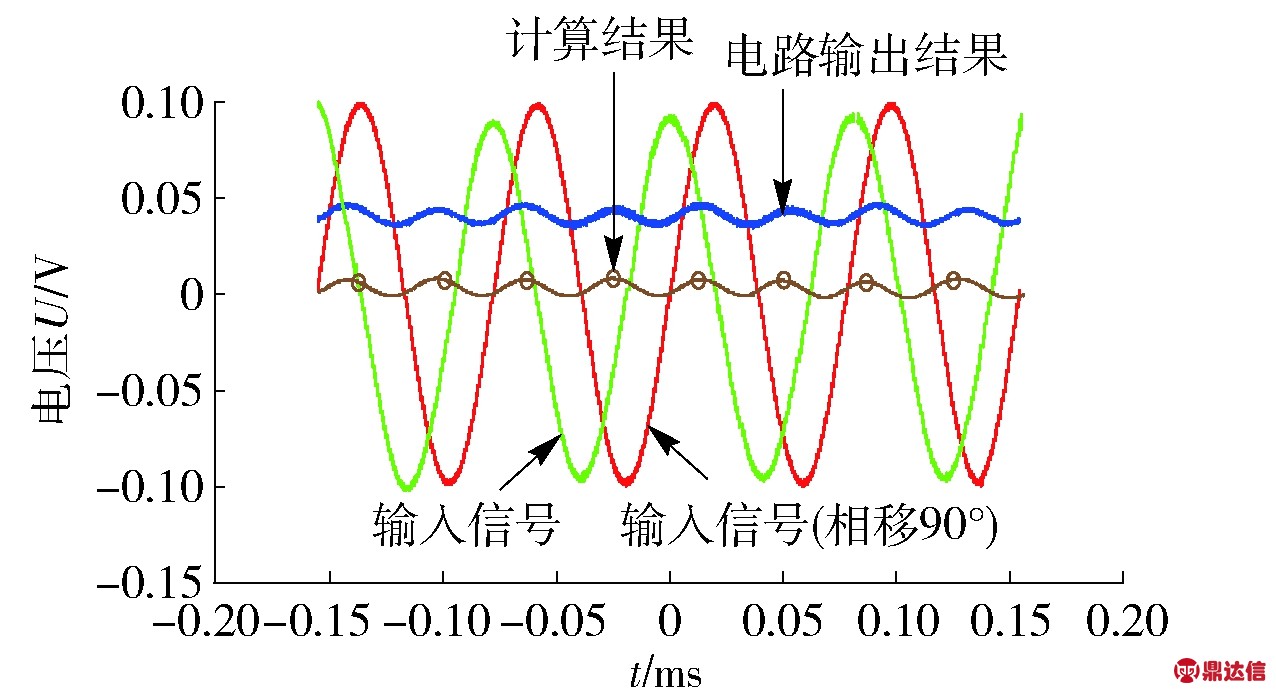
图8 乘法器输入和输出的时域
Fig.8 Multiplier time-domain diagram of input and output
将2路采集的输入信号进行数值乘积运算,并与模拟乘法器电路实际输出的乘积信号结果进行对比(见图8). 可以看出,电路输出信号存在直流偏置,对后续解调信号存在影响. 为探究不同工作频率下的直流偏置电压情况,模拟实际检测条件,输入模拟乘法器的两路信号分别为0.5 V、相位为0的正弦信号(激励信号)和0.1 V、相位90°的正弦信号(接收信号).
在10~30 kHz内,以1 kHz为步长,测得的直流偏置电压结果如图9所示. 直流偏置电压的均值39.4 mV,标准差为0.532. 该直流偏置电压基本不随工作频率而波动,为电路的固有特性,可通过差值方式进行补偿. 补偿后,图8所示的计算与电路输出信号的互相关系数达到0.955 1.
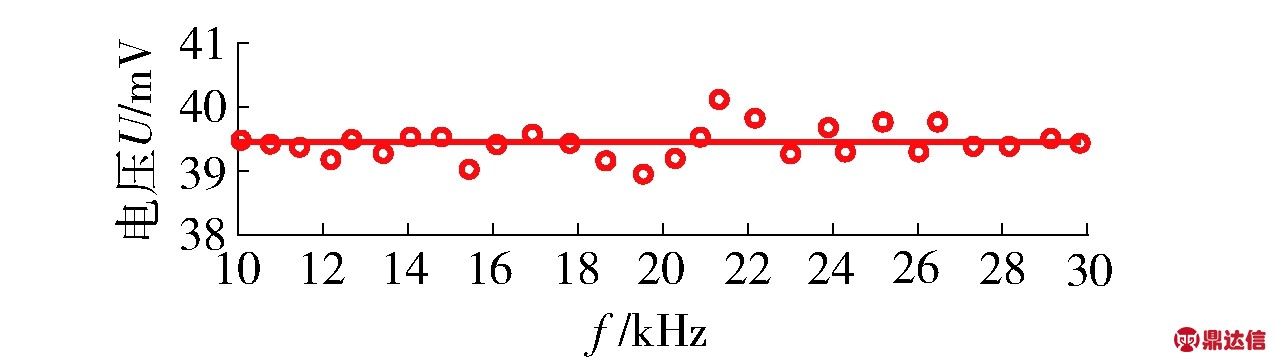
图9 乘法器输出与计算值之差
Fig.9 Difference between output of multiplier and calculated value
2.3 整体调试
将前2部分电路与低通滤波器相连接,测试整体调制电路对信号解调的误差. 测试时,其中一路信号保持不变以模拟激励信号(即参考信号),另一路信号先后改变其幅值和相位,模拟接收线圈经过缺陷时的输出信号(即待解调信号).
首先,测试电路对相位解调的精确度. 在频率为15 kHz下,参考信号幅值为0.2 V,待解调信号幅值为0.1 V,与参考信号的相位差在1°~10°内,以间隔为1°进行测试. 其次,固定待解调信号与参考信号的相位差为5°,调整待解调信号的幅值,从0.1 V以步长0.1 V增加至1 V.
上述2组试验测试中,经低通滤波后的信号均进行直流偏置电压补偿,再计算得出幅值、相位与理论结果的相对误差,如图10所示. 本文所设计的正交解调电路对涡流检测信号幅值解调的相对误差处于10.3%~12.7%,而相位解调相对误差处于4.1%~7.2%.
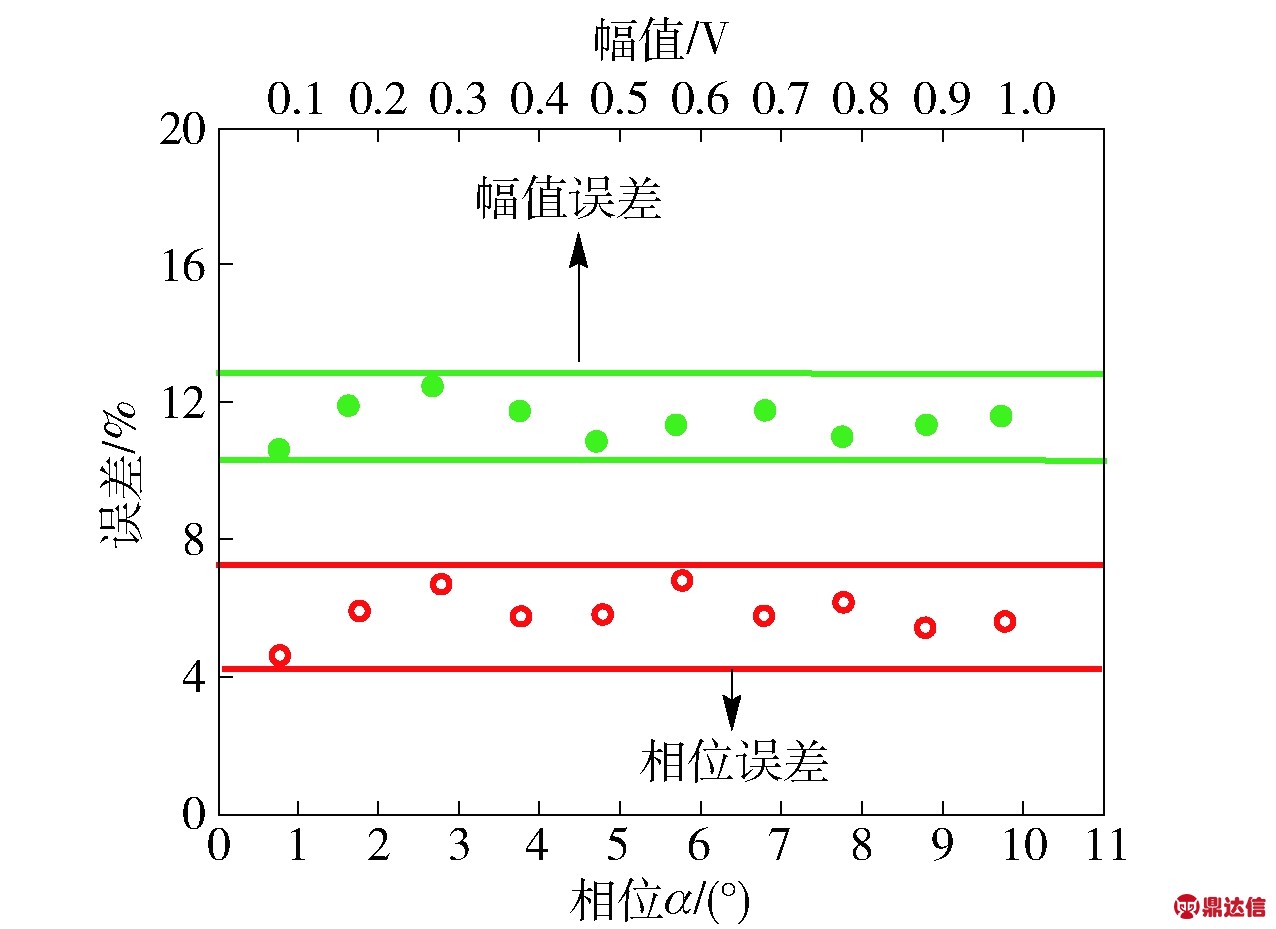
图10 误差百分比
Fig.10 Error percentage
3 钢块缺陷检测试验
将研制的解调电路与双向励磁涡流检测传感器结合用于钢块缺陷试件的检测,图11为试验装置实物图. 使用Agilent 33220A的函数发生器,在频率15 kHz下输出幅值为0.1 V的正弦信号作为激励线圈的输入,使用Tektronix MDO 3024四通道数字示波器显示电路输出信号. 涡流传感器垂直放置于钢块表面(即传感器的敏感方向),沿钢块表面无提离滑动,依次经过4个深度由浅到深的槽型缺陷,将传感器的检测信号在示波器上显示,并依据式(5)和(6)计算为幅值与相位的值,变化曲线分别如图12所示[9-10]. 无论是幅值还是相位变化曲线,均能反映出4个缺陷的存在. 随着缺陷深度的增加,幅值呈增长趋势. 这表明采用双向涡流励磁模式,可以检测出45号钢中深7 mm的槽型缺陷,所设计的解调电路可以对1 mm深缺陷涡流检测信号的幅值、相位进行较好的解调[11].
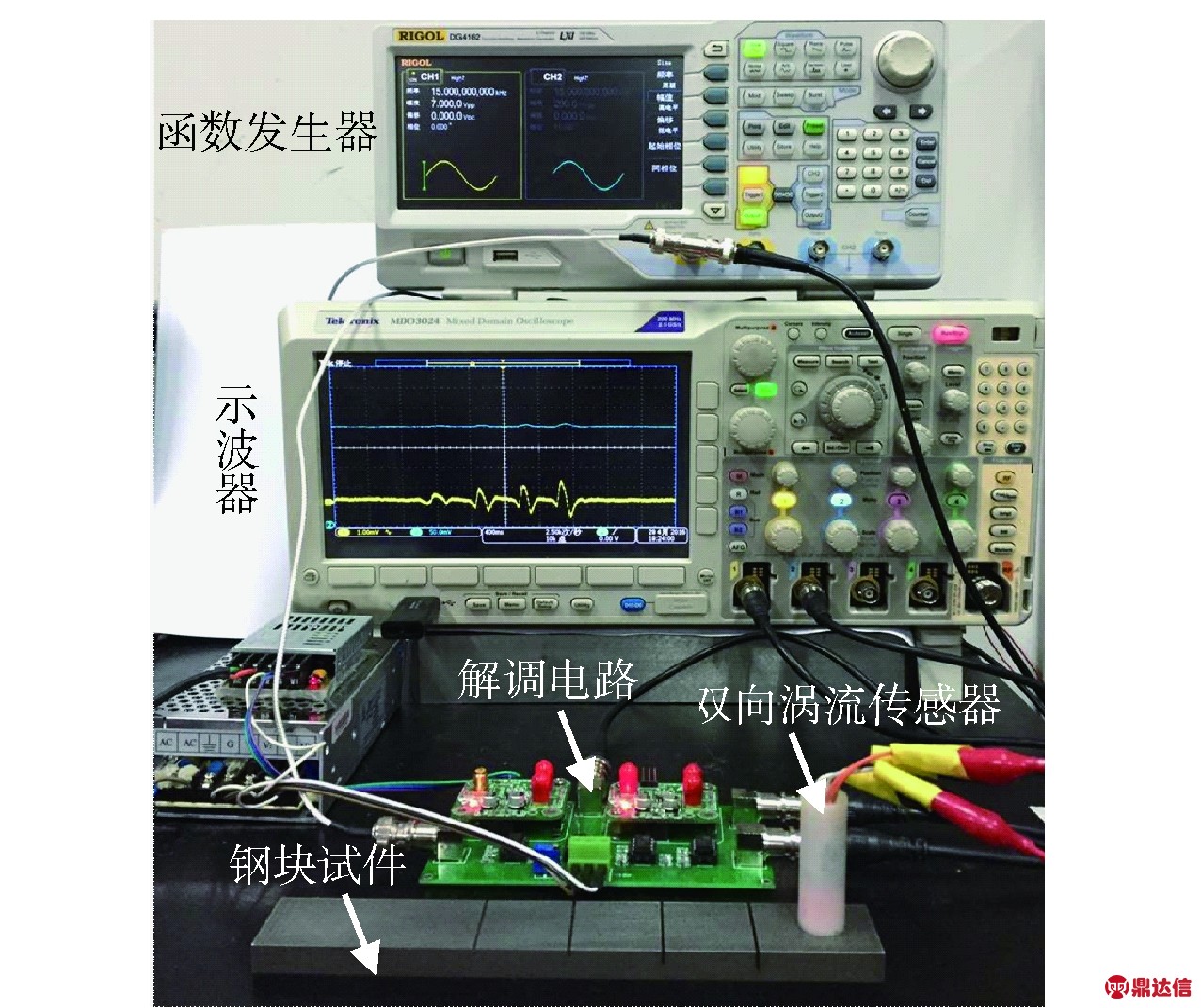
图11 实验装置
Fig.11 Experimental set-up
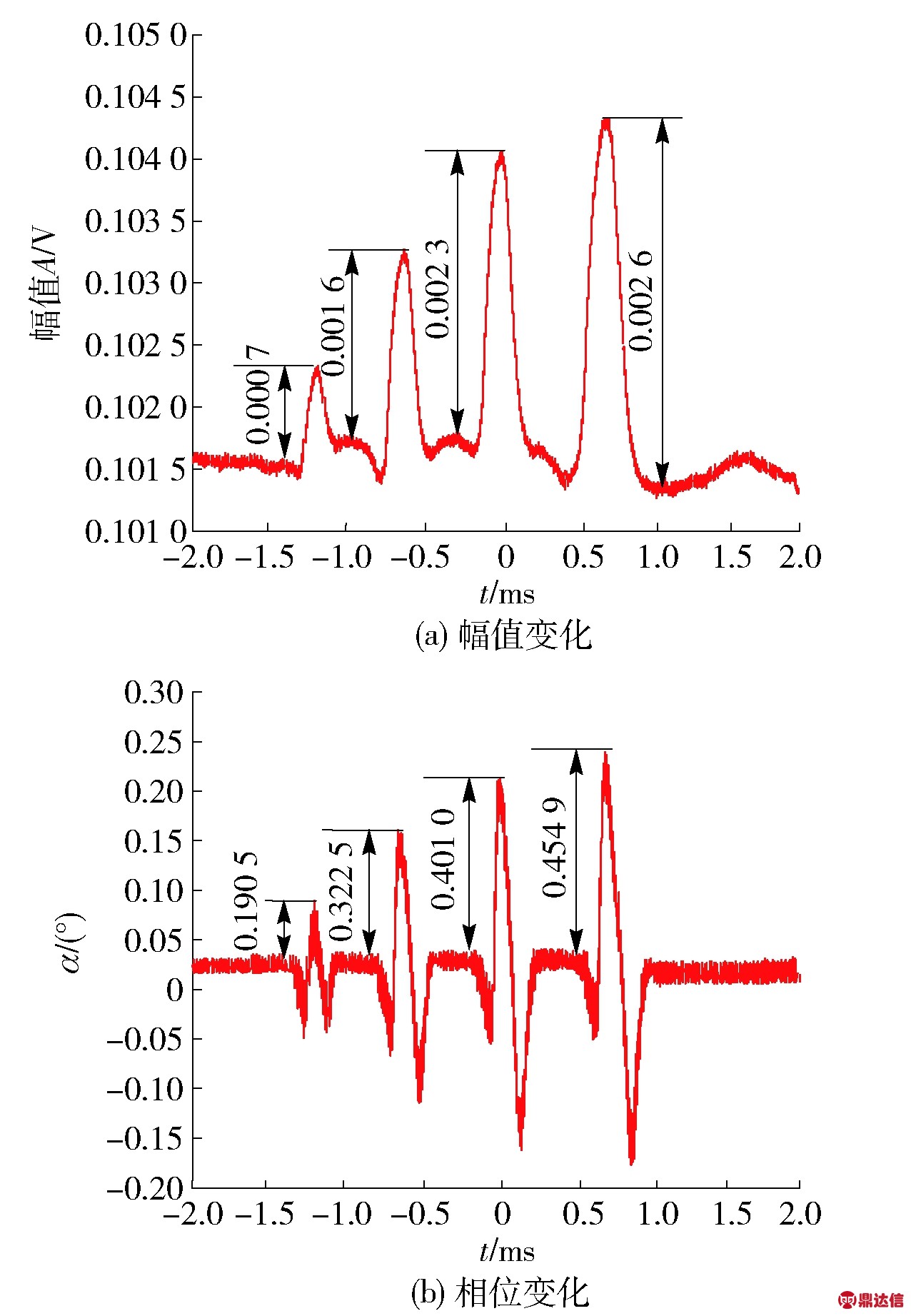
图12 幅值、相位变化情况
Fig.12 Amplitude and phase change
4 结论
1) 移相器:在10~30 kHz频段内,通过调节电路中滑动变阻器的阻值可实现对输入正弦信号的90°准确相移;考虑后端负载电路影响,测试得出了工作频率不同时,能实现准确相移目的的滑动变阻器阻值.
2) 模拟乘法器:试验测试表明,电路对两路标准信号的模拟乘法运算结果与理论计算信号的互相关系数高达0.955 1;相乘得到的信号存在直流偏置电压且基本不随工作频率而波动,可通过直接差除方式进行有效补偿.
3) 在10~30 kHz低频段,无论是涡流检测信号的幅值还是相位变化曲线,均能准确反映出钢块试样中4个槽型缺陷的存在. 随着缺陷深度的增加,幅值和相位均呈增长趋势.