摘要:针对套筒零件壁薄刚性差的结构特点,其加工过程中由于切削力、夹紧力和切削热等的作用,易产生变形,影响工件的加工精度和表面粗糙度。选用合理的定位装置和夹紧装置,运用六点定则的方法,使套筒工件在夹具中的位置完全确定,从而进行摩托车分离器套筒工件铣槽的专用夹具设计。该夹具实用性强,操作简单可靠,采用压板和活节螺栓的设计,满足了夹紧可靠的要求;V型块和对刀块的运用进一步保证了加工质量,提高了生产效率,节约了成本。并且利用建模软件Pro/E建立了夹具的三维实体模型,为进一步的的结构分析和优化提供了理论依据。
关键词:套筒零件;六点定则;夹具设计;V型块
随着制造产业的日益进步,套筒类零件更加广泛的应用在机械结构中,其主要是作为支撑元件和导向元件。当下机械行业中使用的大多数套筒零件形状差异不大,由于各个零件的尺寸有所不同而采用了不同类型的铣床夹具,因此增加了夹具的设计制造成本和工件的生产准备周期[1]。套筒零件在机械工程实际的运用中直径不断地增大,这也使得其同轴度要求和壁厚均匀更加难以保证[2]。套筒零件在铣削加工的过程中,由于切削力较大会引起振动[3],从而影响工件的加工精度。正确的选择装夹工具也是套筒零件在加工过程中的一个难点,因为一套合理的装夹工具可以最大限度的降低切削力造成的振动对于工件加工精度的影响。目前机械行业加速发展,在高精度工件生产加工作为机械行业大发展的前提条件下,要实现高精度工件的生产加工就必须具备可靠的夹具,因为只有在可靠夹具的前提条件下才能实现高精度工件的加工。因此夹具的设计至关重要。
套筒类的零件一般可以分为孔、外圆、端面、沟槽四个部分,主要的工作表面是内圆面和外圆面。套筒零件的形状精度和位置精度要求较高,而表面粗糙度值要求较小[4]。套筒零件的孔壁相对于其它零件而言比较薄,由于其在加工的过程中受夹紧力、切削力、切削热等因素的影响[5],因此零件容易发生变形。为了解决现有技术存在的问题,运用夹具设计原理开发了一套全新的专用铣槽夹具。该夹具在使用过程中,操作便捷,结构紧凑,合理可靠,节省了零件装夹的时间;对刀装置的使用,有利于铣刀与夹具之间相对位置的调整,进一步节省了时间。调整件的合理运用,缩短了夹具设计制造周期的同时也降低了制造成本,从而提高了工件的生产效率,加强了企业在市场的竞争力。此夹具在生产实践中具有较强的适应能力。
1 零件工艺分析
本文涉及到的零件其实就是一个套筒类的零件,其组织成分是38CrMnAlA,毛坯件选择为棒料。套筒零件的主要加工表面为内孔面和外圆表面。外圆表面可选择车削和磨削加工。为保证套筒零件孔的加工精度和表面质量,可以经过粗镗、半精镗、精镗等加工工序。套筒主要表面加工在几次安装中进行,先加工外圆,然后以外圆为精基准最后加工内孔,采用这种方法时工件装夹迅速可靠。该零件的主要技术指标是:平面A对于平面B的不平行度不大于0.01 mm,平面AB对于直径34孔轴线的不垂直度不大于0.03 mm,对于直径25孔轴线的不垂直度不大于0.02 mm,零件表面进行发蓝处理,零件进行渗氮处理,孔内径的氮层深度为0.2~0.4 mm,在铣床上进行铣槽加工的时候保证尺寸5.7+0.02 -0.01的加工精度。套筒零件图如图1所示。
该套筒零件的结构特点是孔壁较薄,加工中常因夹紧力、切削力和切削热等因素的影响而产生变形。防止变形应注意以下两点:
(1)粗加工和精加工的分步进行在某种程度上降低了切削力和切削热对套筒工件变形的影响,精加工工序也在一定程度修复了粗加工工序产生的变形误差;
(2)采用轴向夹紧夹具的方法,及在工件上做出增加径向刚性辅助凸边,加工后将凸边切去的方法都可以减少夹紧力对套筒工件加工变形的影响。
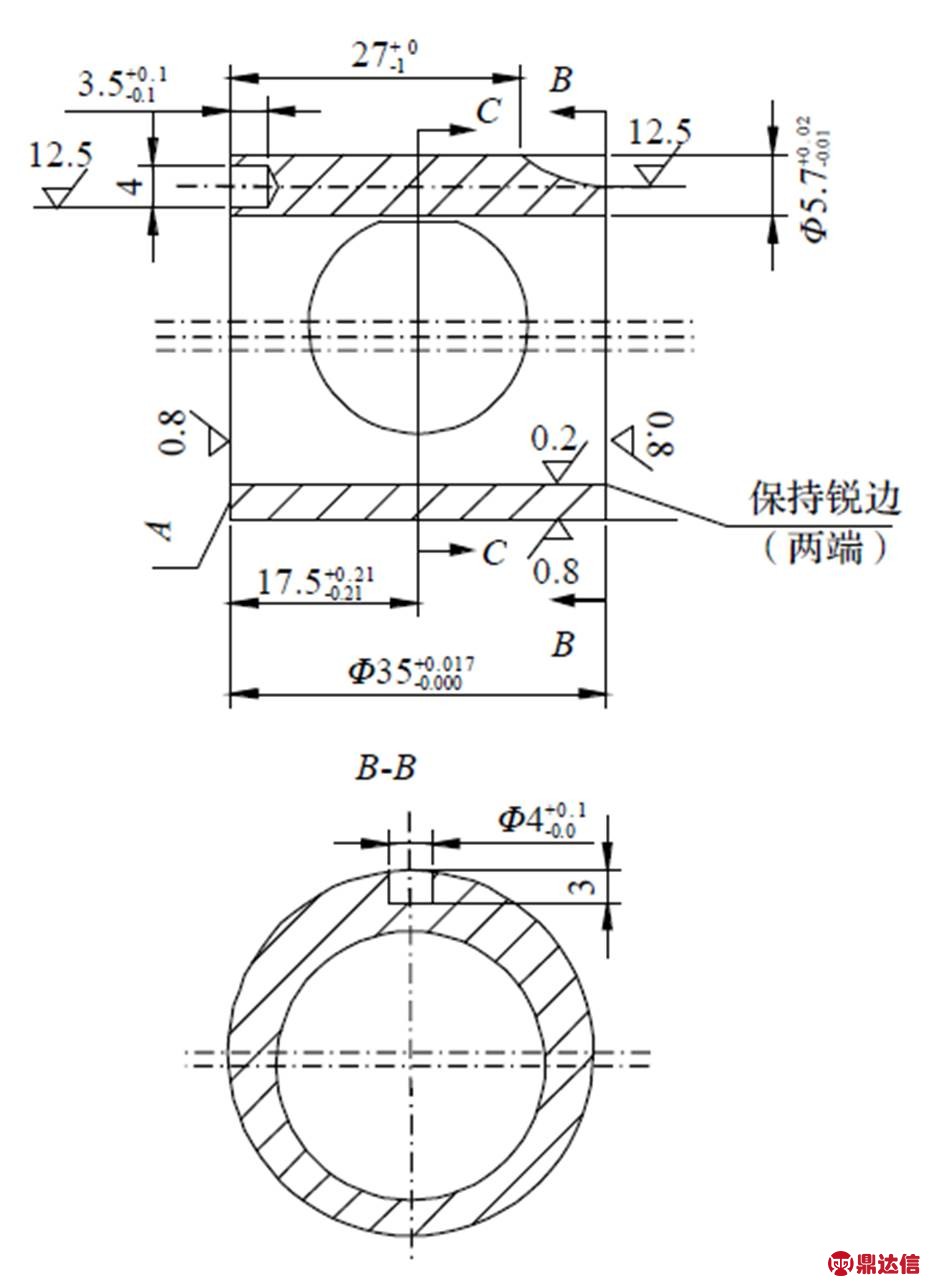
图1 摩托车分离器套筒零件图
2 铣床夹具设计
2.1 定位装置的设计
任何一个工件在没有被确定位置之前的一段时间内,其都是处在三维空间之中自由活动的物体。一个自由活动物体在空间直角坐标系中只存在6种可能的运动形式,即沿着三个坐标轴正负方向的移动,和绕着X、Y、Z三个坐标轴方向的转动,这就是空间自由物体6个自由度的概念。工件在实际的加工过程中,需要确定工件在某个方向上的位置,就必须限制工件在该方向上的自由度。随着6个自由度的完全限制,工件在空间的位置就唯一确定下来了。在分析套筒工件铣槽加工的定位时,采用一个支撑点限制套筒工件的一个自由度。常说的六点定则[6]就是运用一定的规律分配支撑点来限制六个自由度,以此来保证工件在加工的过程中拥有确定的一个位置[7]。在实际的机械生产过程中,往往只需要限制部分自由度的不完全定位就可以满足工件具体的加工要求。
在本次套筒铣槽夹具的设计中,采用了V型块和端面的定位销来实现套筒工件定位准确的要求。这套夹具限制了套筒工件的五个自由度,分别是X轴的转动和移动、Y轴的移动以及Z轴的转动和移动。夹具上的定位键、定位销、六角螺钉、圆柱销都是定位元件,通过它们使套筒工件在夹具中占据正确的位置。定位基准与设计基准重合,满足基准重合原则,无基准不重合原则[8]。
2.2 夹紧装置的设计
夹紧装置的组成一般分为动力装置、夹紧元件、中间传力机构等,作用是将工件压紧夹牢,保证工件在加工过程中受到外力(切削力等)作用时不能离开已经占据的正确位置。套筒工件铣槽夹具设计的过程中,遵循以下原则:符合加工质量的原则,夹具构造简易的原则,效率高且工艺性能良好的原则等。夹紧装置设计的过程中,确定夹紧力的大小、方向、作用点尤为重要,合理的夹紧力通过固定夹具的位置来保证工件的加工精度要求。
在本次套筒铣槽夹具的设计中,采用了压板和T型螺栓来达到套筒工件夹紧可靠的要求,同时也有效的保证了加工过程的稳定性。由于套筒工件壁薄刚性差的特点采用灵活性强的活节螺栓,方便工件的翻转以及拆卸。夹具上的压板、活节螺栓和T型螺栓都是夹紧元件,通过它们来保证套筒工件在夹具中占据的正确位置。
2.3 铣床夹具及夹具装配图
铣削加工的套筒零件是在铣床夹具上安装的,工件会随着机床的工作台一起运动。本次设计的是一种套筒铣槽的专用夹具,由于铣削的加工过程属于断续的加工,切削力较大,比较容易产生振动[9]。因此要求套筒工件的定位必须可靠,夹紧装置可以提供较大的夹紧力;同时铣床夹具要具备足够的强度和刚度,并且能够和机床的工作台紧紧的固定在一起。套筒铣槽的夹具装配如图2所示。
定向键和对刀装置是铣床夹具在结构上的重要特征,它们是用来保证夹具与机床、夹具与刀具之间相对位置关系的。采用定向键有利于夹具的安装,但是定向键的位置精度不是很高。在实际的生产过程中,一些位置精度要求高的夹具,常常在夹具体的一侧设置一个校正面。安装夹具的时候,可以利用校正面进行百分表找正。这个校正面也可以作为定向件、定位件等在夹具体上装配和检验时的基准。铣床夹具在工作台安装好之后,要确保铣刀和夹具的相对位置,这要是为了以后的定距离加工。还可以采用试削调整,用标准件调整和对刀装置调整,其中以用对刀装置(对刀块和塞尺)调整最为方便。
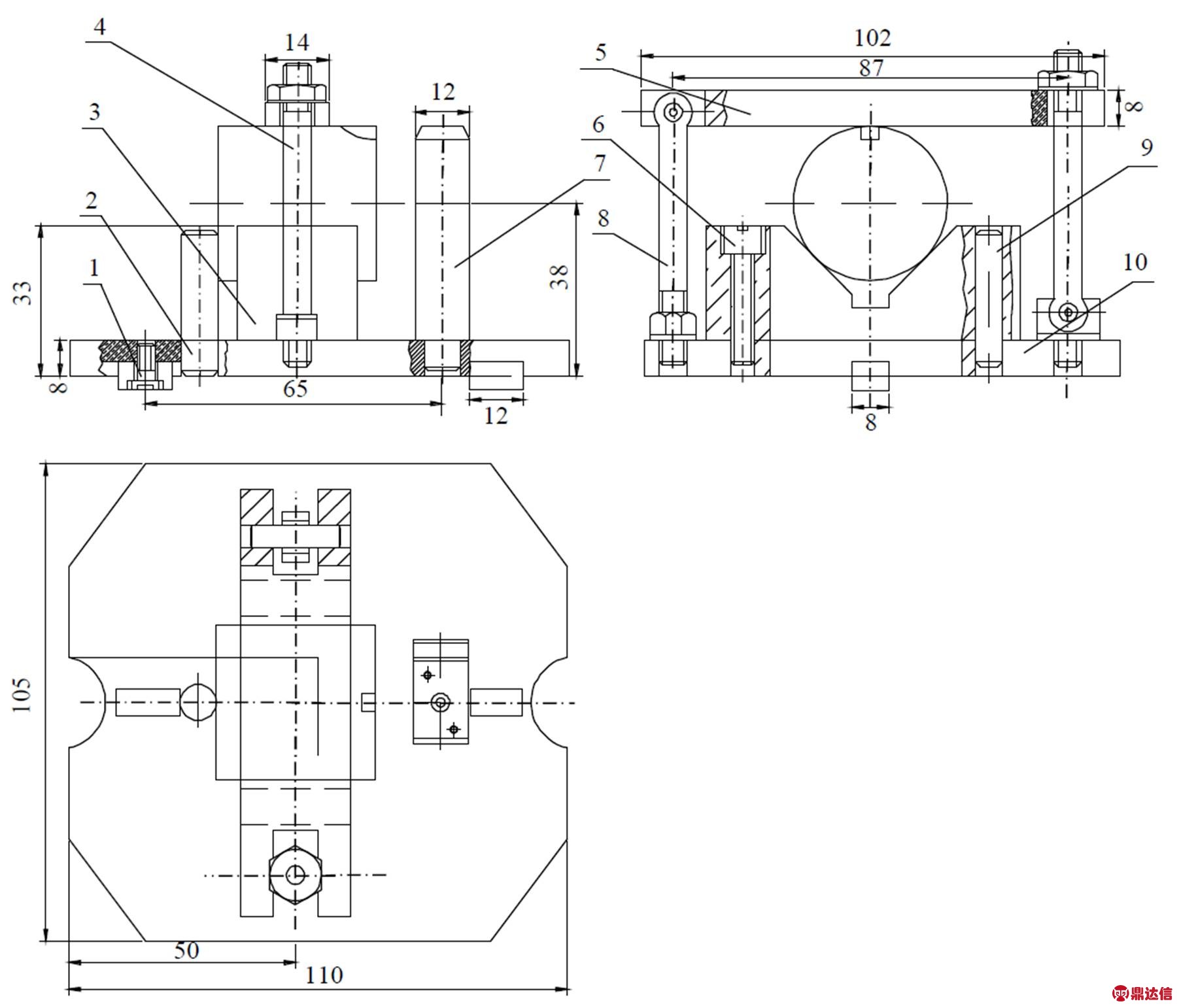
1.定位键 2.定位销 3.V型块 4.T型螺栓 5.压板 6.沉头螺钉 7.对刀块 8.活节螺栓 9.圆柱销 10.机床底座
图2 铣床夹具装配图
2.4 夹具操作简述
首先将套筒零件和铣床夹具轻拿轻放并且擦拭干净,保证没有其它杂物影响装配;然后,将V型块通过沉头螺钉和圆柱销将其固定,拧紧螺钉;再将定位销嵌入夹具底板中,保证高度;将工件套筒放到V型块中间,上铰链螺栓、压板,将铰链螺栓拧紧;然后将对刀块按照需要固定在夹具体上;最后将定位键固定在夹具体上边。运用Pro/E软件建立夹具的三维图,如图3所示。
2.5 夹具精度校核
夹具的各种策划方案初步确定及一些大概的图纸实施后,接下来就是对夹具的精度检测(分步处理以及数据核对)。作用位置的条件有三个模块,确定基准误差、操作安装的误差、进行加工的误差[10]。这三个部分的方方面面都要充分考虑,在铣床上进行铣槽加工的时候,影响尺寸5.7+0.02 -0.01的误差分析:
(1)由于定位基准与工艺基准不重合,则δ定基=0.016 mm,即34+0.000 -0.016的公差0.016 mm。
(2)选择的是平面定位,δ定位可忽略不计。
(3)在夹紧套筒时,夹紧力引起的变形对5.7+0.02 -0.01影响较小,则δ夹紧可以忽略不计。
(4)铣刀在安装时位置发生偏差不会作用5.7+0.02 -0.01尺寸,则δ安装也能忽略。
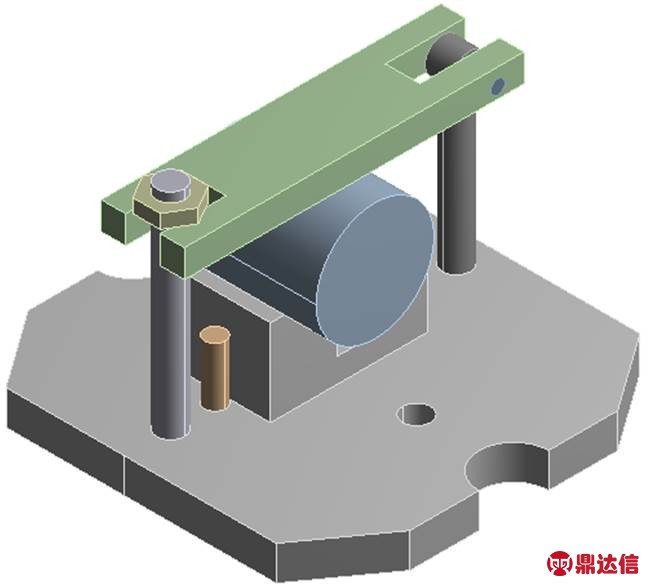
图3 铣床夹具三维图
(5)与加工方法有关的误差δ加工。对刀块的位置尺寸误差、调刀误差、铣刀的跳动、机床工作台面的倾斜和变形等所引起的加工方法误差,可根据生产经验并参照经济加工精度,可以取0.01 mm。
综上所述造成的最大误差为0.026 mm,小于工序误差0.03 mm,精度储备为0.004 mm。因此夹具能够满足工件的精度要求,并且具有一定的精度储备[11]。
3 结论
针对薄壁套筒刚性差的结构特点,其加工过程中由于切削力、夹紧力和切削热等的作用,易产生变形,影响工件的加工精度和表面粗糙度。选用合理的定位夹紧装置,运用六点定则的方法合理地设计了一套套筒工件铣槽的专用铣床夹具。通过夹具的精度校核可以得出此套铣槽夹具的设计能够充分满足工件加工工序的精度要求,且实用性强,操作简单、装夹方便。
套筒铣槽夹具的夹紧装置为压板和活节螺栓,满足了工件夹紧可靠的要求;V型块和对刀块作为定位装置进一步保证了工件的加工质量。并且利用建模软件Pro/E建立了夹具的三维实体模型,为进一步的的结构分析和优化提供了理论依据。