摘 要:本文主要介绍了使用BY-4型纳米陶瓷基高温防氧化涂层材料采用喷涂方式在400kA电解槽预焙阳极表面上应用,分析、验证涂层材料对碳素阳极的防氧化效果,并对项目进行了经济效益测算,结果表明,该纳米涂料能够缓解阳极炭块的氧化掉渣,延长阳极使用周期1天以上,并且该纳米涂料带入的 Fe、Si等微量元素对铝液质量影响较小。
关键词:BY-4型纳米陶瓷基;防氧化;碳素阳极;节能环保
炭阳极是铝电解生产的主要原料之一,作为导体将直流电导入电解槽,并作为电解槽阳极材料参与阳极反应。目前每生产一吨铝要消耗420kg~500kg的炭阳极。炭素阳极消耗是电解铝生产的主要成本之一,约占总成本的15%左右,是每一个电解铝生产企业都要考核的重要指标。2018年我国电解铝实际运行产能为3650万吨左右,但是我国电解铝阳极碳耗指标与国际先进水平相比较,却存在较大的差距。据文献报道海德鲁HAL130槽,阳极净耗为406kg/t-al,而我国的电解铝阳极平均净耗却为440kg/t-al左右,不仅造成大量不可再生的优质碳资源的浪费,还严重的制约了我国电解铝工业的进一步发展。
1 技术简介
BY-4型纳米陶瓷基高温防氧化涂层材料为某公司高温防氧化涂层材料第四代产品,利用氧化铝陶瓷基涂层,常温固化,420℃以上烧结致密,毛细孔收缩,在阳极炭块表面形成致密的保护隔绝层,降低阳极四周的氧化掉渣,在系列电流不变的前提下,阳极电流密度会适当降低,故每天消耗的阳极高度也会降低。阳极经过一个周期(33天)的使用可以节约出超过一天的高度,从而延长阳极的使用周期。
2 试验部分
2.1 试验方法
某铝厂5001#—5008#槽使用涂覆BY-4型纳米陶瓷基高温防氧化涂层材料阳极试验槽,5009#-5016#号槽为对比槽。通过测量残极长、宽、高和炭渣量并结合阳极实际使用周期验证涂层材料的抗氧化效果。
2.2 纳米陶瓷基防氧化涂层材料的用量
通过长达6个月对8台槽试验进行试验以来,涂料使用量248.6桶,喷涂阳极2397块,平均用量9.6块/桶。随着喷涂人员对喷涂技术的熟练程度,截止目前平均喷涂用量在10.9块/桶左右。(最佳用量11块/桶)。
2.3 喷涂阳极试验照片
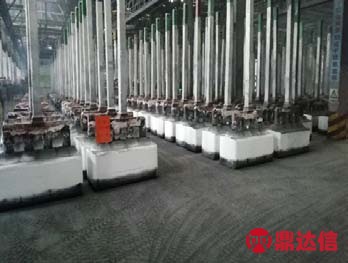
图1 涂层阳极现场摆放
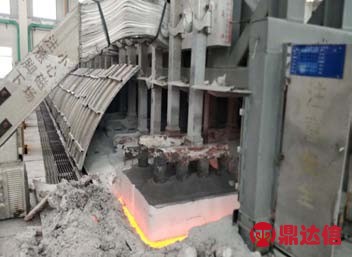
图2 涂层阳极入槽
3 试验结果
3.1 残极尺寸
3.1.1 试验槽与对比槽残极尺寸对比
表1 试验槽与对比槽残极尺寸
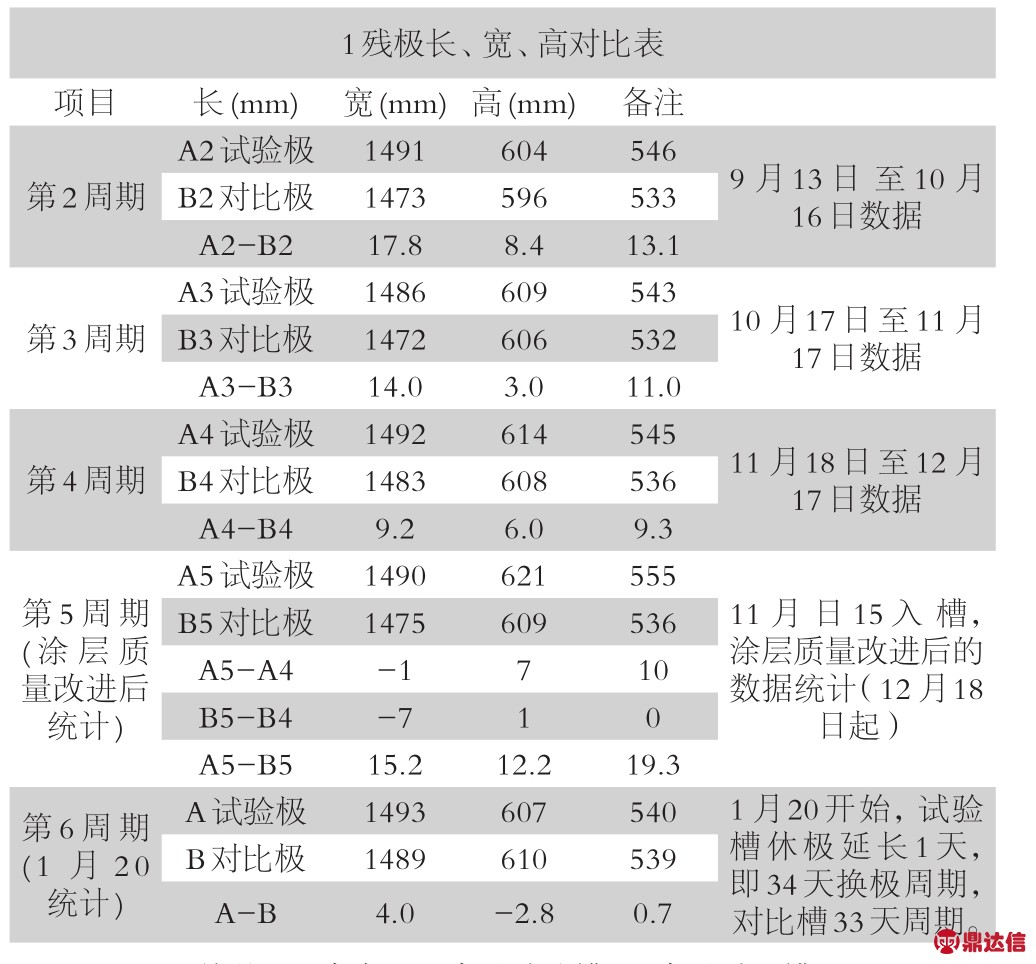
说明:上表中的A表示试验槽,B表示对比槽
表2 涂料用量与残极高度差
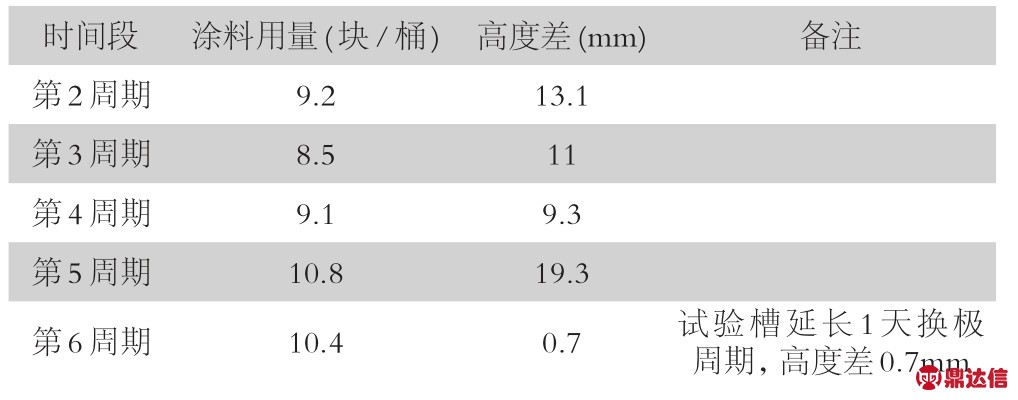
使用分析:
从各周期的残极高度差数据看,第2周期13.1mm适中,第3周期、4周期偏低,第5周期最高,达19.3mm,第6周期试验槽使用周期延长一天后比对比槽高0.7mm。分析:第2周期为过渡期,即该周期内,试验槽所换出的残极在槽内均处在“黑、白”混合的环境,效果受部分黑阳极的影响,不是最佳厚度,所以13.1mm的高度差属正常值。自进入第3周期,理论上因达到正常的抗氧化效果,残极高度差应更大,但由于涂料用量超标,涂层偏厚,再加上环境温度逐渐减低,导致涂层新极入槽时涂料未彻底干燥,新极入槽后鼓包现象普遍,涂层面对炭块表面的保护被破坏,抗氧化效果不增反降,所以第3周期、4周期的高度差不理想。从第5周期开始喷涂作业得到改善,涂料用量平均为10.8块/桶,由于涂层面薄且养护时间长,入槽时涂层得到较好的养护固化,没有出现鼓包现象,所以第5周期高度差为19.3mm,刨除高度600mm以上残极,高度差为17.7mm。第6周期开始,试验槽换极周期延长一天至34天,对比槽为33天,且对比槽高度从最开始的533mm上升至538mm,试验槽与对比槽残极高度相差较小。
3.1.2 单槽平均高度统计
表3 单槽平均高度统计分析
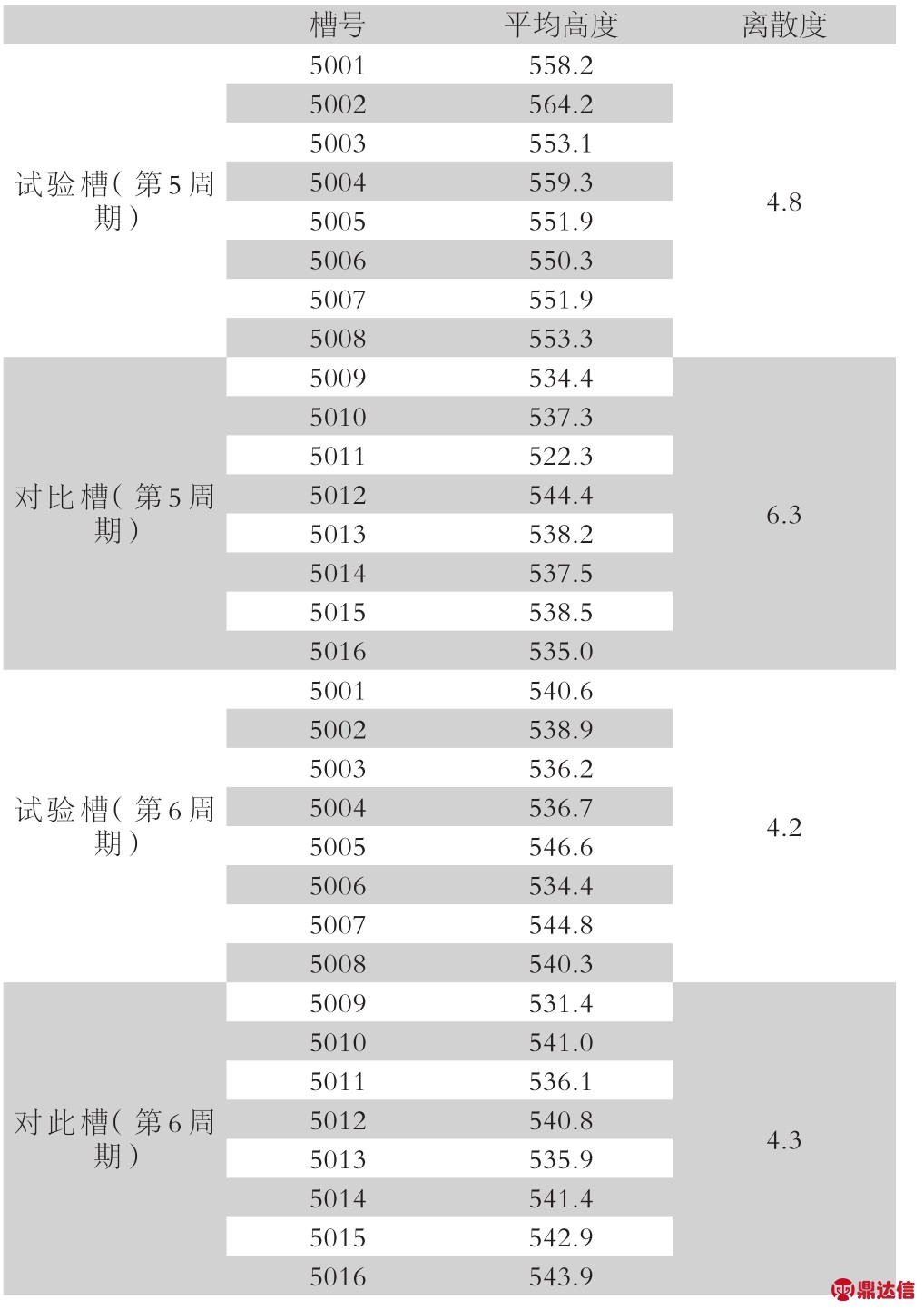
从单槽残极的平均高度可以看出,第5周期试验槽单槽残极高度的离散度小于对比槽单槽离散度;第6周期试验槽单槽残极高度和对比槽基本持平
3.1.3 去掉600及以上残极进行统计
将试验槽与对比槽角部极残极高度≧600残极刨除之后统计残极高度:
第5周期试验槽平均高度555.28mm,对比槽平均高度535.95mm,试验槽-对比槽=19.33mm;
第6周期试验槽平均高度539.8mm,对比槽平均高度539.1mm,试验槽-对比槽=0.7mm;
3.1.4 残极高度<520mm占比
试验槽A5:测量总数据量350个,残极高度小于520mm的有7块,占比2.0%。
对比槽B5:测量总数据量351个,残极高度小于520mm的有52块,占比14.81%。
试验槽A6:测量总数据量326个,残极高度小于520mm的有30块,占比9.2%。
对比槽B6:测量总数据量326个,残极高度小于520mm的有29块,占比8.9%。
(以上A、B分别表示试验槽、对比槽,5、6分别表示第5周期、第6周期)。
试验结果表明在延长一天换极周期后残极高度与对比槽基本持平。
3.1.5 残极高度去角部极(A1、A2、A23、A24)
将试验槽与对比槽所有角部极刨除之后,统计残极高度:
第5周期试验槽平均高度554.33mm,对比槽平均高度535.51mm,试验槽-对比槽=18.82mm。
第6周期试验槽平均高度539.49mm,对比槽平均高度538.57mm,试验槽-对比槽=0.92mm。
3.1.6 平均每天的消耗高度核算
对比槽平均高度536mm,刚好透底残极高度490mm,碳碗深度110mm。
平均每天消耗高度:
[650-(536-490+110)]/33=15mm。
3.1.7 分别统计A、B面平均高度
表4 A、B面平均高度分析
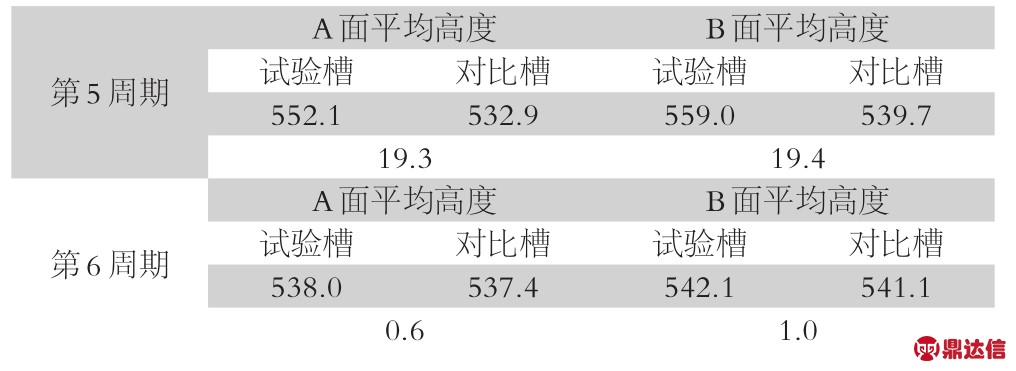
3.2 炭渣数据
数据统计:
统计从12月18日至1月18日炭渣数据,试验槽比对比槽少10.8公斤/天·槽;从12月26日起,试验槽炭渣下降更明显,12月26日至1月18日,试验槽平均每天比对比槽少13.3公斤/槽,炭渣可减少22%~27%。1月20日至2月22日,试验槽平均每天比对比槽少9.2公斤/槽,炭渣减少20%。
3.3 硅、铁含量变化
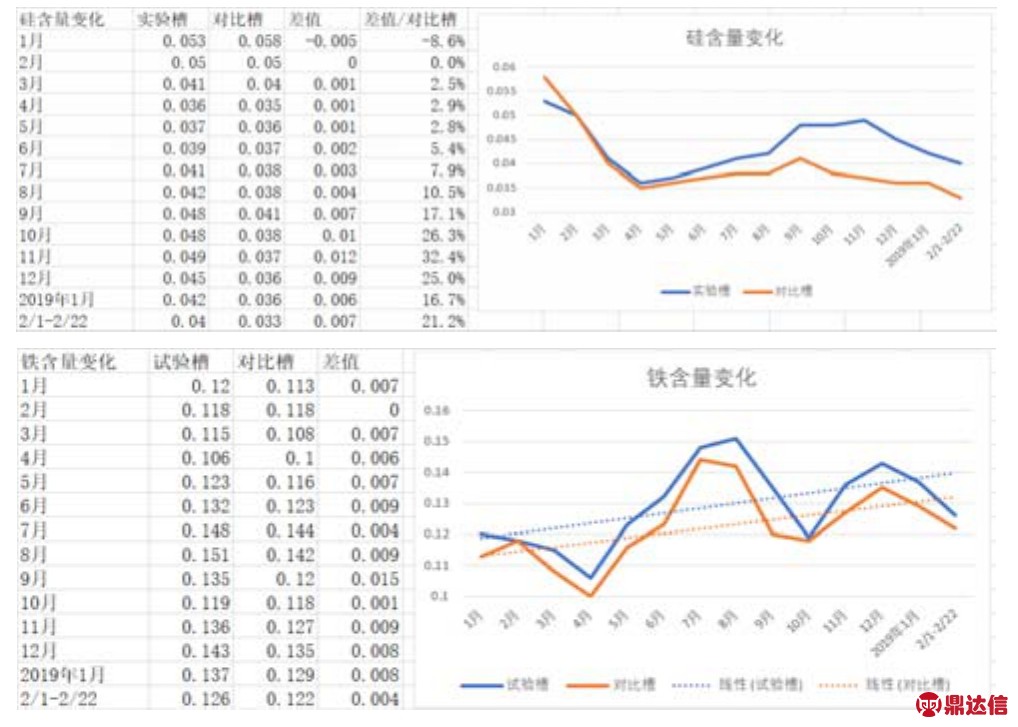
图3 硅铁含量变化
使用喷涂阳极之前试验槽硅含量较对比槽高30ppm(7月份),自8月12日起随着涂层阳极的使用,试验槽硅含量与对比槽的差值呈上升趋势。至11月达最高120ppm。原因分析:主要是涂料用量过大所致(平均喷涂7块/桶~8块/桶)。从11月份起喷涂用量逐步降低,最终控制在每桶喷涂10.5块~11.5块,故11月至2月后整体硅含量呈下降趋势。
目前试验槽硅含量稳定在0.04%,2月差值为70ppm。刨除试验槽与对比槽固有差值(试验前相差30ppm),正常喷涂下试验槽硅含量较对比槽高40ppm。
4 项目推广经济效益测算
表5 某铝厂阳极防氧化项目效益评估表(按照80万吨/年电解铝)
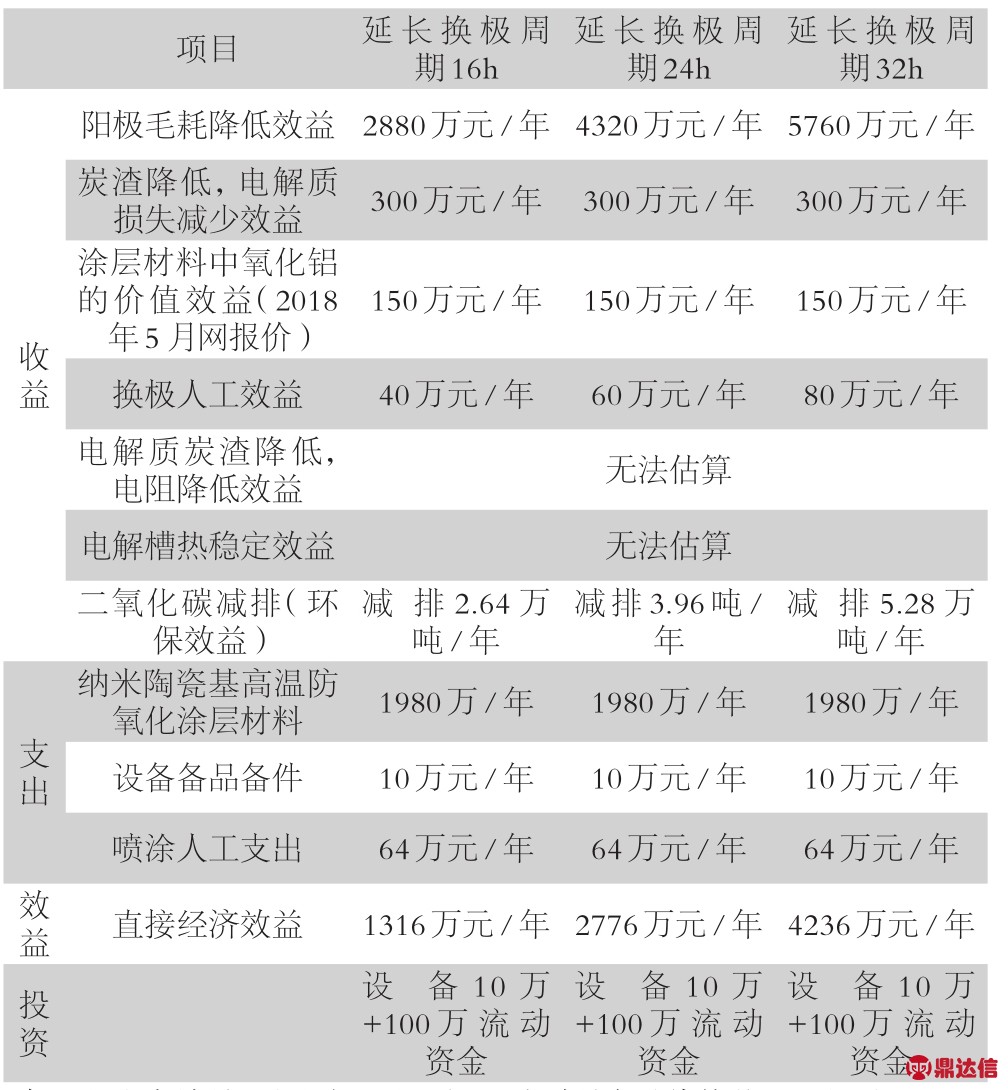
备注 上述净效益,企业投入只需要8台喷涂机(价值约10万元),及20天纳米陶瓷基高温防氧化涂料库存,占用流动资金约100万元。
5 结论与建议
(1)涂层阳极在一个完整的换极周期内能较好的覆盖于碳素阳极外侧,从而缓解炭块的氧化掉渣,使得残极形状方正规整。
(2)延长1天周期后的涂层阳极与未延长周期的正常残极高度比较,涂层阳极延长1天周期后仍可增加残极高度0.7mm。
(3)第六周期:涂层阳极每天可减少炭渣量约9.2公斤/槽,可减少炭渣20%。
(4)建议:喷涂用量为每桶喷涂10.5块~11块,且在目前低温环境下,保证涂层极养护时间在3天以上,确保涂层充分干燥固化,入槽时不鼓包。