摘要:本文介绍一种结构简单、使用安全可靠的一种机械压力机气垫导轨双向定位导正气垫顶冠及单顶冠结构,防止气垫往复运动时,因气垫供气气压或受力不均,造成气垫单顶冠呈倾斜状态,消除气垫行程过程中因偏斜造成的单顶冠固定螺栓断裂和活塞与底座连接螺钉断裂现象。
关键词:压力机,气垫,导轨
1 引言
目前,多数机械压力机气垫由三个活塞缸同时供气往复运动,三个活塞缸顶冠、单顶冠采用螺钉与气垫连接,机床负荷运动时,因气垫供气气压或受力不均,造成气垫单顶冠呈倾斜状态,闭锁缸与活塞部分前后晃动且整体偏转约50°。气垫部分在使用中容易发生单顶冠固定螺栓断裂和活塞与底座连接螺钉断裂现象。本文讲诉一种结构简单、使用安全可靠的一种机械压力机气垫导轨双向定位导正气垫顶冠及单顶冠结构,防止气垫往复运动时,因气垫供气气压或受力不均,造成气垫单顶冠呈倾斜状态,消除气垫行程过程中因偏斜造成的单顶冠固定螺栓断裂和活塞与底座连接螺钉断裂现象。
2 故障现象及原因分析
如图1原气垫单顶冠结构示意图所示,压力机气垫负荷运动时,因气垫活塞行程,出厂设计无限位,气垫顶冠下行后卡滞于中间位置,单顶冠极易呈倾斜状态;当单顶冠倾斜时,中间气垫活塞与底座连接螺钉(M20)全部断裂,活塞与闭锁缸整体旋转约50°;气垫活塞及闭锁整体前后晃动量很大,造成气垫运动失效。
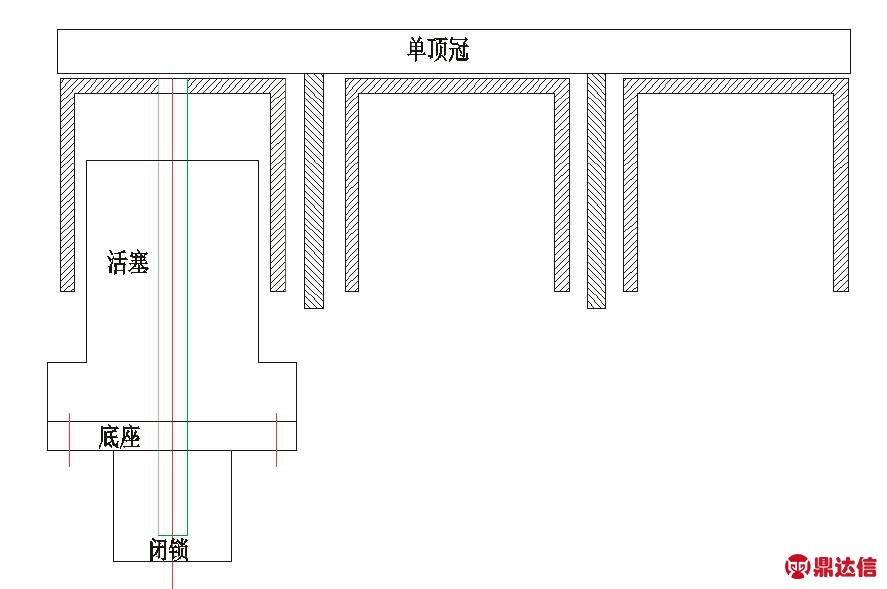
图1 原气垫单顶冠结构示意图
经分析,中间气垫底座平行度偏差过大导致气垫受力后倾斜卡滞,气垫活塞座与底座连接螺钉断裂导致气垫活塞受力后错位,致使气垫顶冠卡滞。此类设备维修及改进难点:1、三套气垫需要全部拆卸,检查导向杆下端磨损情况;2、三套气垫活塞座及底座螺钉孔加工,因气垫体积较大,需拆除地坑盖板及支撑钢构、压缩空气管路及压力容器。工作量较大,维修周期较长。因此设计一种故障率低、工作可靠的机械压力机气垫导轨双向定位导正气垫顶冠及单顶冠结构很有必要,既能保障设备完好性、降低维修成本,又能节约维修时间提升设备产能。
2 气垫优化方法论证
经测算,在气垫顶冠与单顶冠之间加装导轨四周限位,如图2气垫加装导轨示意图所示,当气垫因磨损导致精度下降后,脱开单顶冠与气垫顶冠之间的螺钉硬连接,利用加装的导轨限制单顶冠转动,避免出现气垫间隙过大后,仅依靠气垫顶冠和单顶冠之间的硬连接而出现偏载情况,气垫功能仍可使用。效果图如图3 气垫四周限位效果图。
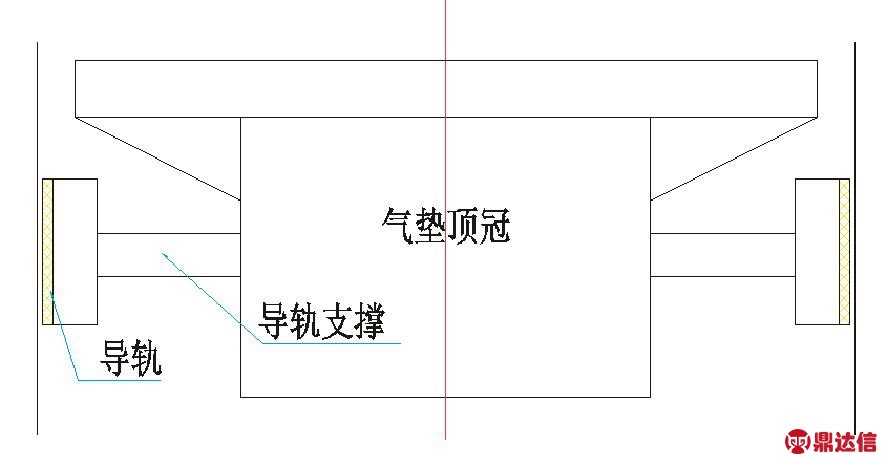
图2 气垫加装导轨示意图
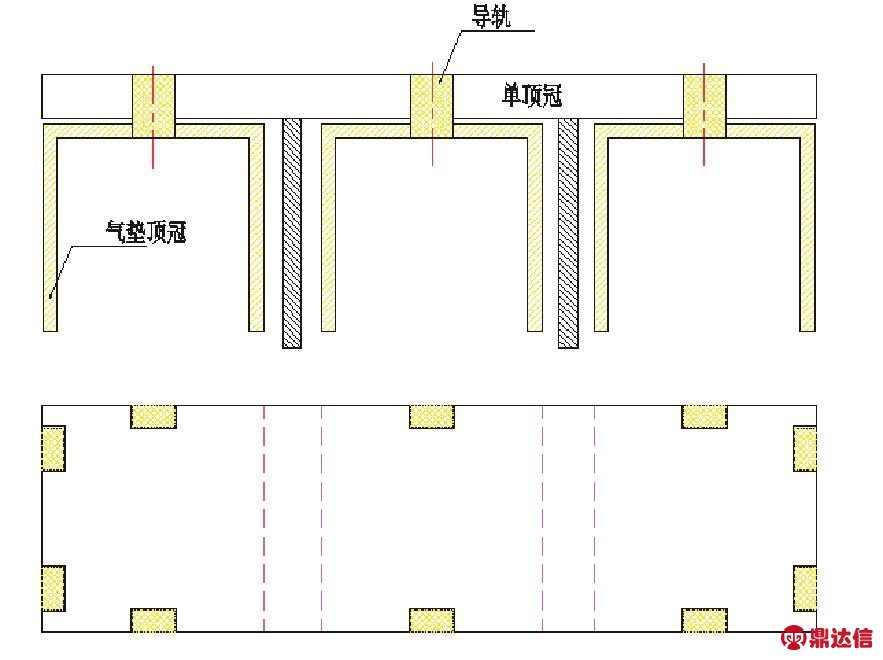
图3 气垫四周限位效果图
3 气垫优化实施方案
如图4气垫导轨双向定位导正气垫顶冠及单顶冠结构装配示意图所示,本技术方案改进部分主要包括钢导轨板1气垫单顶冠,2气垫顶冠,3气垫缸,4胶木导轨板,5通过装配构成气垫导轨总成结构。
图5气垫导轨双向定位导正气垫顶冠及单顶冠结构分解示意图对具体实施方式作进一步说明。先将气垫单顶冠2和气垫顶冠3一起配装上铣床进行铣削加工,均布铣削出100mm宽,40mm深通槽,并在气垫顶冠3导轨槽处均布钻出4个M20的螺钉孔,然后按照四处螺钉孔尺寸,对钢导轨板1进行划线配钻,同时将胶木导轨板5与钢导轨板1进行配钻,并对胶木导轨板进行铣油槽。最终将钢导轨板1、 胶木导轨板5与气垫顶冠进行装配,并把气垫单顶冠2对照导轨板进行配装。装配完成经模拟试车检验:模拟气垫因磨损导致精度下降时,单顶冠与气垫顶冠之间的螺钉硬连接脱离时的状态,人为拆除单顶冠与气垫顶冠之间的螺钉进行试验。此时,气垫在运动中,无螺钉刚性连接,仅利用加装的导轨限制单顶冠的转动,气垫规则均匀往复运动。
此种机械压力机气垫导轨双向定位导正气垫顶冠及单顶冠结构,垫顶冠与单顶冠之间加装导轨(四周限位),能够避免出现气垫间隙过大后,仅依靠气垫顶冠和单顶冠之间的硬连接而出现偏载情况,避免出现气垫行程过程中因偏斜造成的单顶冠固定螺栓断裂和活塞与底座连接螺钉断裂现象,达到了预期效果。
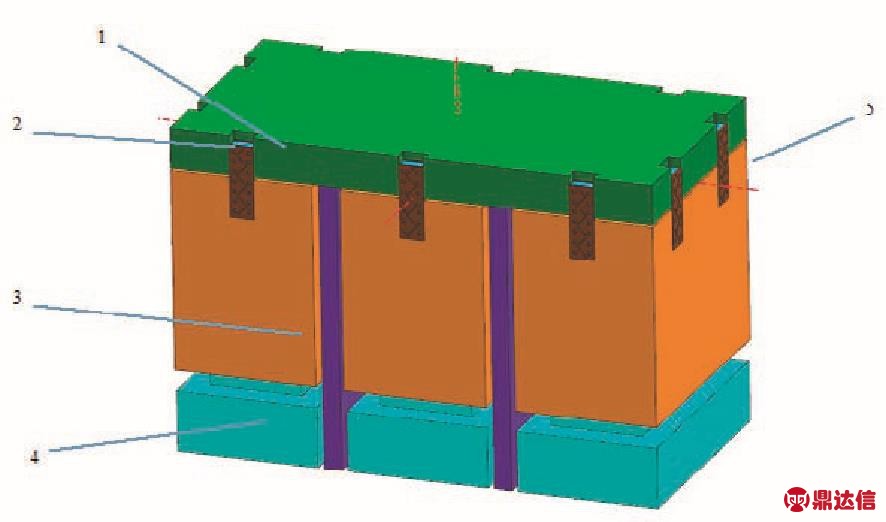
图4 气垫导轨双向定位导正气垫顶冠及单顶冠结构装配示意图
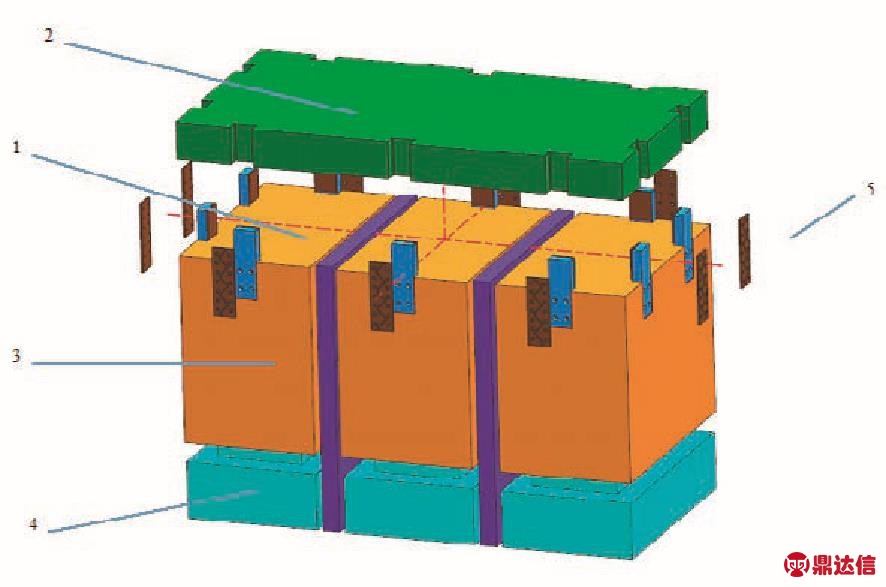
图5 气垫导轨双向定位导正气垫顶冠及单顶冠结构分解示意图
4 结束语
对汽车覆盖件冲压设备而言,尤其是500T以上级的拉延冲压工序,气垫部分的可靠性直接影响产品质量,因此,此种气垫导轨双向定位导正气垫顶冠及单顶冠结构对保证产品质量降低设备故障率起到保障作用。在改进优化此类压力机时,一定要充分的考虑气垫与导轨、顶冠、活塞的间隙,在制作导向板时注意,并对胶木导轨板进行铣油槽,保证使用时正常润滑,延长使用寿命。