摘要:具有脱硝除尘一体化功能的催化滤芯在小型燃烧烟气处理中具有广泛的应用前景。采用3种典型商用陶瓷滤芯,涂覆V2O5-WO3-MoO3/TiO2脱硝催化剂,制备了具有脱硝除尘一体化功能的催化滤芯材料,考察了陶瓷滤芯的化学成分和孔径结构对 NH3-SCR脱硝性能的影响。XRD、XRF、SEM、压汞等分析测试结果表明:碱金属与碱土金属元素含量低且孔径分布均匀的纤维状结构陶瓷滤芯,促进了催化剂分散,提升了脱硝活性,且降低了压降。催化滤芯在220~380℃、过滤面速度1 m·min-1、NH3/NO=1条件下脱硝率大于90%;抗水蒸气(15%,体积分数)和SO2中毒(3×10-2%,体积分数)测试表明催化滤芯在260~450℃温区内依然保持脱硝率大于90%,可满足催化滤芯实际工业应用要求。
关键词:陶瓷滤芯;选择催化还原;脱硝除尘一体化;V2O5-WO3-MoO3/TiO2;抗硫
引 言
燃烧烟气污染物综合治理净化是我国能源与环境领域的战略要点,特别是对于治理当前日益严重且广受诟病的大范围雾霾污染具有重大的环境与社会意义[1-3]。相比于当前脱硝、除尘等独立运行的传统烟气净化工艺,一体化烟气净化工艺因其具有工艺流程短、设备投资低、运行费用少以及占地空间小等显著优势,成为当前中小型锅炉烟气净化领域的新发展趋势[4-6]。陶瓷催化脱硝滤芯是一种烟气脱硝除尘一体化新材料,其表层膜具有致密的微米级孔结构,可去除99%以上的烟气粉尘;涂覆催化剂的滤芯内部支撑体,可通过SCR过程同时实现烟气氮氧化物脱除,目前已发展成为一种极具应用前景的脱硝除尘一体化新技术[7-9]。
国外对催化滤芯的研究始于20世纪80年代,目前德国与韩国已经形成了相关的催化脱硝滤芯产品,但其较高的V2O5负载量(> 10%,质量分数)和催化剂涂覆量降低了脱硝选择性并增加了压降,限制了其推广应用。Choi等[10-11]优化了催化滤芯中脱硝催化剂的组成,证明V2O5-WO3/TiO2基的催化滤芯脱硝活性最好。Nacken等[12-14]进一步探索了浸渍法、溶胶-凝胶涂覆法、真空离心辅助涂覆法等不同的脱硝催化剂与陶瓷滤芯复合方法,以增加涂覆催化剂的稳定性和黏附强度,避免堵塞滤芯孔道并降低压降。最近,Zuercher等[15]提出将担载催化剂的泡沫陶瓷芯插入陶瓷内管的新方法,以提高脱硝效率并降低压降。国内相关领域研究刚起步,安振等[16]初步用固定床评价了涂覆催化剂的滤芯颗粒脱硝性能。本课题组[17]先期工作提出了催化剂浆料一步涂覆制备催化滤芯的新方法,实现催化滤芯高效制备,300℃时可达到 85%以上的脱硝效率。催化滤芯的关键技术核心之一在于如何实现在陶瓷滤芯孔道短停留时间内实现高效脱硝,催化滤芯的种类、结构基催化剂的分散将对其脱硝性能和使用压降具有显著的影响。
为进一步提高催化滤芯的脱硝效率,降低压降,并拓宽催化滤芯的脱硝温度窗口,本文选取 3种典型商业陶瓷滤芯,涂覆脱硝催化剂制备催化滤芯,研究了不同滤芯组成、结构与催化剂担载量、脱硝性能和使用压降的内在关联性,为脱硝催化滤芯的国产化,特别是滤芯的选材或定制提供关键依据。
1 一体化催化滤芯制备及评价方法
1.1 材料
工业偏钛酸(河南焦作佰利联有限公司,61%二氧化钛,质量分数),偏钒酸铵(西陇化工股份有限公司,分析纯),偏钨酸铵(国药集团化学试剂有限公司,85%~89%),分散剂聚乙二醇200(国药集团化学试剂有限公司,化学纯),黏结剂二氧化硅溶胶(日产公司,30%二氧化硅质量分数),实验用水为双重去离子水。3种国产陶瓷滤芯(陶瓷滤芯A:广州市嘉秀建材有限公司 Clear Edge XS-1500高温过滤器;陶瓷滤芯B:淄博东强环保设备有限公司DQ-005堇青石陶瓷滤芯;陶瓷滤芯C:固安县丰德过滤器材有限公司丰德滤芯)的外形尺寸均为 35 mm/60 mm/1500 mm(内径/外径/长度),密度分别为 1.99、1.68、2.12 g·cm-3。为方便实验评价工作,将滤芯管切割成5 cm长的样品备用。
1.2 VO x基脱硝功能化滤芯的制备
采用浸渍法涂覆制备钒基一体化催化脱硝滤芯,考察不同陶瓷滤芯对脱硝活性和使用压降的影响。配制5%固含量(以TiO2计,质量分数)的偏钛酸浆液,加入分散剂PEG200(PEG/TiO2=3%,质量分数),SiO2黏结剂(SiO2/TiO2=3.3%,质量分数),室温搅拌至均匀;后依次加入适量偏钒酸铵、偏钨酸铵、钼酸铵及适量去离子水(适当调变固含量浓度以达到不同陶瓷滤芯浸渍浆液后担载相同质量催化剂),室温下搅拌10 h至浆液分散均匀。将不同陶瓷滤芯浸入搅拌好的浆液15 min,后取出并依次在65、105℃下恒温干燥4 h,再从105℃以2℃·min-1升温速率升温至450℃,恒温煅烧4 h,取出待用。制备好的不同催化滤芯担载了相同质量(3 g)与组成的(V2O5-WO3-MoO3/TiO2)的催化剂。
1.3 样品表征
采用PANalyticalX’Pert MPD Pro型X射线衍射仪分析物相结构,CuKα射线(λ=0.15418 nm),管电压40 kV,管电流30 mA,连续扫描范围为10°~90°。
康塔公司Autosorb-1-MP型比表面积和孔隙度分布仪测定样品的比表面积和孔结构,吸附测定之前,样品于 300℃下脱气 10 h。催化剂比表面积通过使用N2为吸附质,在液氮(-196℃)稳定条件下测定样品的比表面积,采用BET二参数方程计算。
美国麦克公司AutoPore 9510全自动固体测汞仪测量不同陶瓷滤芯内部孔结构。日本JEOL公司JSM-7001F+INCA X-MAX型热场发射扫描电子显微镜与能谱分析仪观察催化滤芯内部形貌及催化剂分散度。
1.4 催化滤芯性能评价
采用自主搭建装置(图 1)评价催化滤芯的脱硝性能,该装置由配气系统、反应系统以及分析测试系统(德国ABB-AO2020分析仪)组成,滤芯由垫片压紧密封,模拟烟气外进内出,模拟实际脱硝除尘一体化过程。模拟烟气组成(体积分数):总气量 10.6 L·min-1,670×10-6% NO,670×10-6% NH3,5% O2,N2平衡,300×10-6% SO2,15%(φ)水蒸气(SO2和水蒸气按实验需求调整),滤芯过滤面速度 1 m·min-1。评价温度 50~450℃,反应前后气体中NO、N2O、O2浓度由烟气分析仪实时测试,压差计记录过滤前后压降。
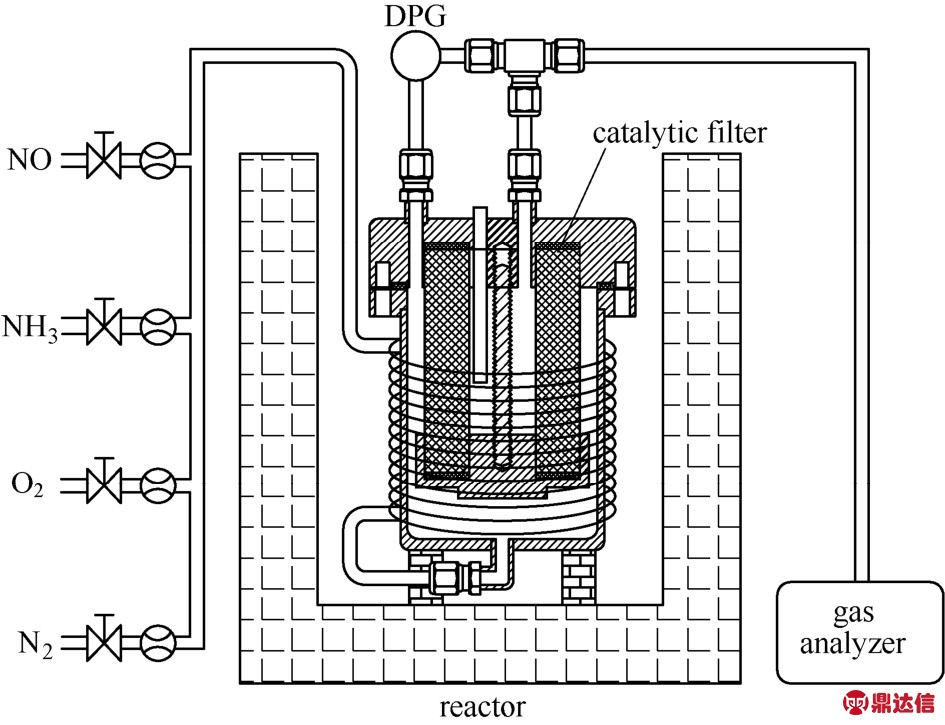
图1 催化滤芯性能评价装置
Fig.1 Experimental unit for assessment of catalytic filter(DPG—differential pressure gauge;TG—thermocouple)
2 实验结果与讨论
2.1 陶瓷滤芯组成与结构表征
表1列举了3种典型商用陶瓷滤芯基材的XRF测试结果(以氧化物质量分数计)。可知3种陶瓷滤芯主要成分均为SiO2和Al2O3。与滤芯A相区别的是滤芯B含有16.27% MgO,而滤芯C含有21.79%Na2O。
为进一步明确不同滤芯的晶相结构,对不同陶瓷滤芯进行X射线晶体衍射分析(图2)。陶瓷滤芯A主要晶体衍射峰位置在25.58°、35.15°、37.78°、43.36°、57.50°,可归属为α-Al2O3结晶,与表1中陶瓷滤芯A含有25.02% Al2O3一致,另外20.86°处隆起的宽峰,属于典型无定形二氧化硅的馒头峰,与表1中陶瓷滤芯A含有72.58% SiO2相符合;陶瓷滤芯B的众多衍射峰均属于硅酸盐结晶衍射峰,其中代表峰有 10.57°、26.64°、36.54°、42.45°、54.37°,结合表1结果可以知道其主要成分为Si、Al、Mg 3种元素,并以硅酸盐化合物形式存在,可归属于堇青石晶相;陶瓷滤芯 C主要晶体衍射峰位置在16.8°、26.4°、42.92°、62.31°,归属于硅铝酸盐结晶,同时发现17.74°、23.12°、30.58°衍射峰归属于硅酸钠结晶,结合表1结果可以知道其主要成分为Si、Al、Na 3种元素,以硅酸盐化合物形式存在。
表1 不同陶瓷滤芯基材的XRF数据
Table 1 XRF analysis results for original ceramic filter materials / %
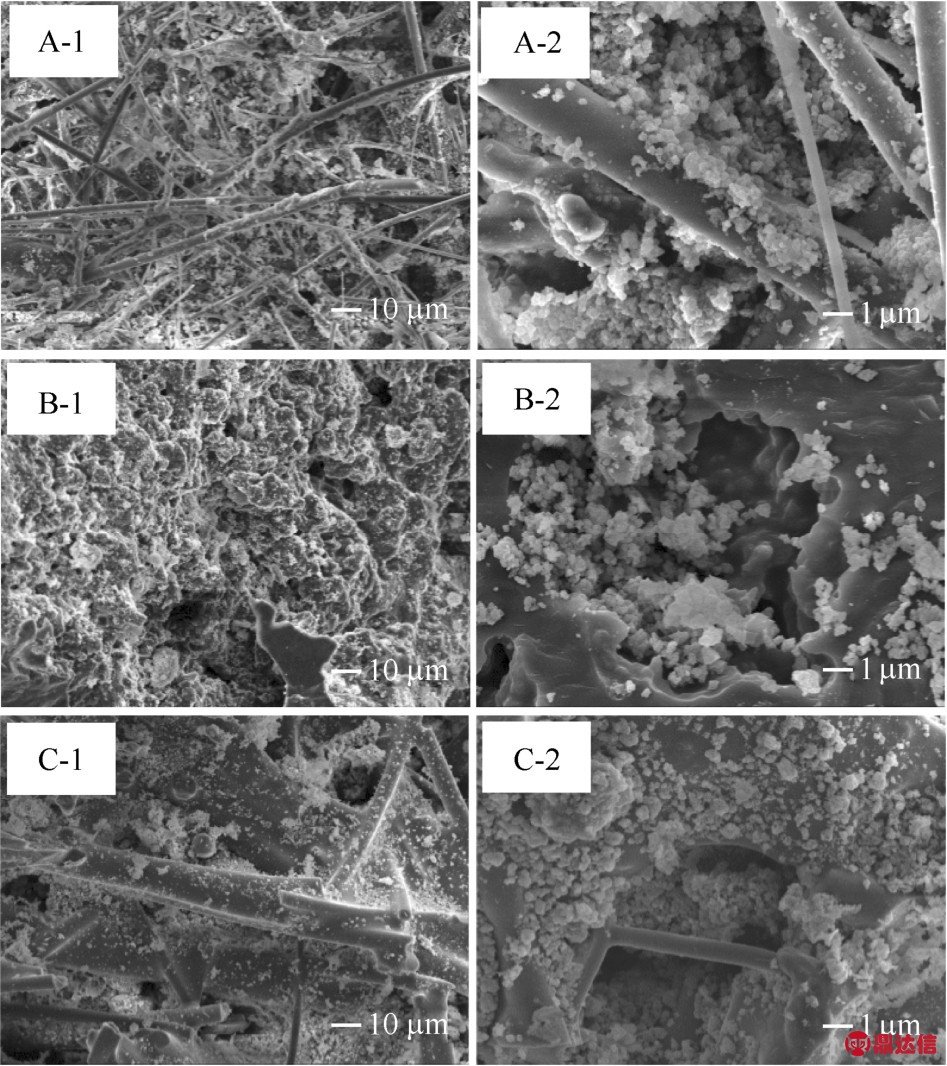
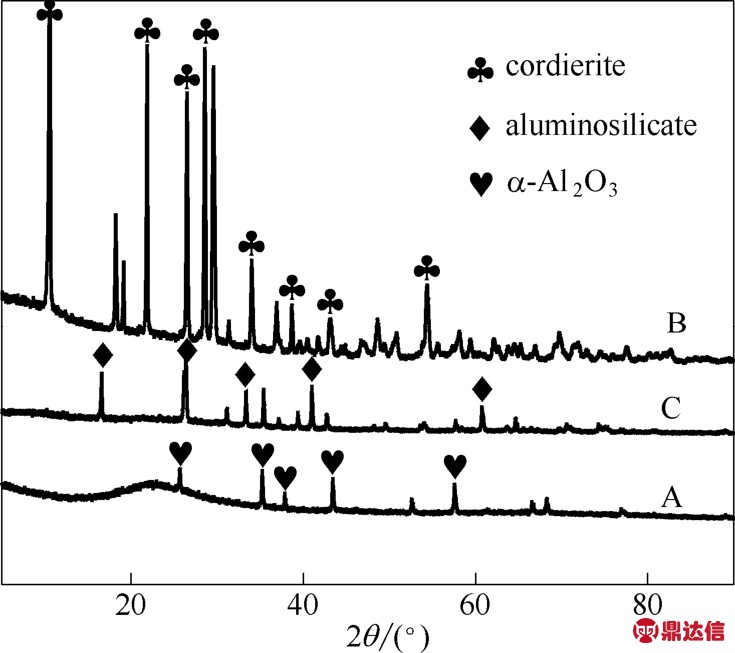
图2 3种商业陶瓷滤芯的XRD谱图
Fig.2 XRD patterns of different ceramic filter materials
3种陶瓷滤芯数码照片及扫描电镜图如图3所示,结果表明陶瓷滤芯A主要由1~3 μm的细纤维和少量黏结状的物质相互堆叠交联构成,孔分布密集且相对均匀,孔径介于 1~15 μm。陶瓷滤芯 B主要为大颗粒状物质高温熔融黏结而成,滤芯主要由熔融实体构成,孔分布稀疏,大孔孔径 50~200 μm,小孔径2~30 μm。陶瓷滤芯 C 为3~10 μm 粗纤维状物质组成,亦具有1~20 μm相对较均匀的孔径与分布。结合上文的组成与晶相分析,可以发现滤芯A主要由氧化铝纤维构成,滤芯B为堇青石颗粒烧结而成,而滤芯C则由硅酸盐纤维构成,且使用了大量的硅酸钠无机黏结剂[18]。
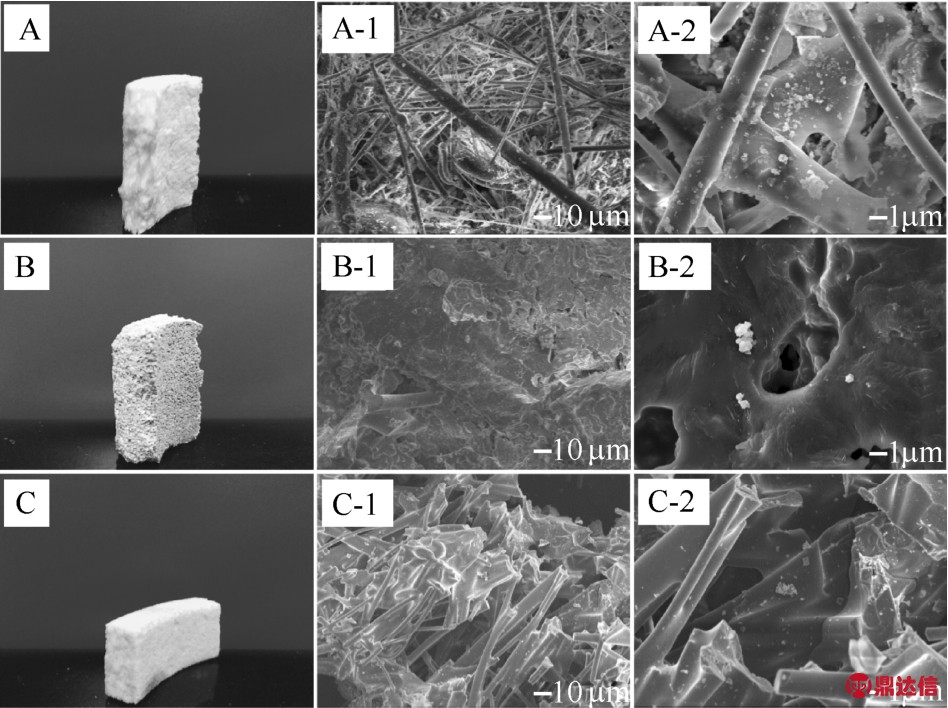
图3 3种陶瓷滤芯实物图及扫描电镜图
Fig.3 Picture and SEM images of different ceramic filter materials
从电镜图可知,3种陶瓷滤芯具有不同的孔结构与分布,为确定不同陶瓷滤芯内部孔道结构定量差异,进一步采用压汞法对3种陶瓷滤芯进行表征,如表2所示。由表可知陶瓷滤芯A与C均具有小孔径、高孔隙率特征,陶瓷滤芯B具有大孔径、低孔隙率特征。典型陶瓷滤芯的平均孔径与图3扫描电镜照片显示具有一定差异性,表明陶瓷滤芯内部有较多的细孔,使得平均孔径值有所缩小。同时压汞的数据也说明采用无机纤维制备的陶瓷滤芯 A和C,实现了纤维之间的搭桥衔接,具有更高的孔隙率,质量密度更低。而采用颗粒堆积的方式所制备的滤芯B,所产生的孔径由颗粒的级配所产生,大孔居多,而且空隙分布均匀性相对较差。因此,3种陶瓷滤芯的比较可以初步判断A、C两种陶瓷滤芯可能更适合脱硝催化剂的担载与涂覆。
表2 不同空白陶瓷滤芯及相应催化滤芯的孔结构参数
Table 2 Pore parameters of blank ceramic filters and corresponding catalytic filters
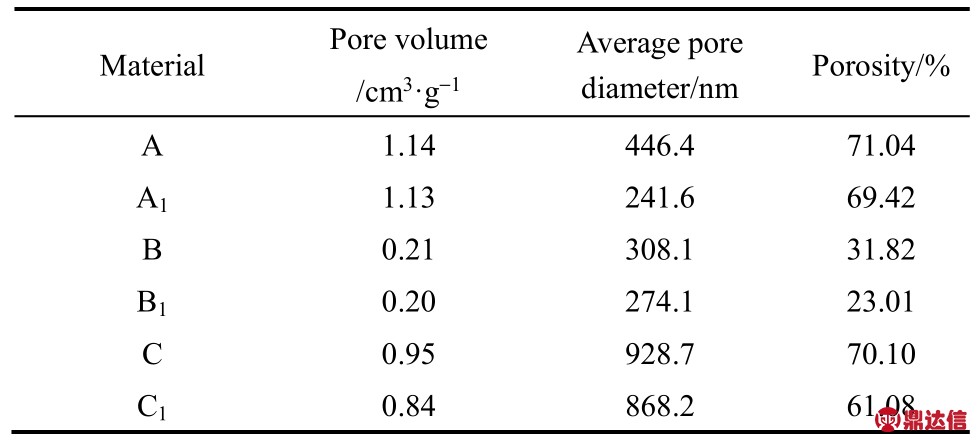
Note:A, B, C stand for original filters.A1, B1, C1 stand for corresponding integrated catalytic filters.
2.2 陶瓷滤芯中催化剂的负载与分散
因每种陶瓷滤芯材质和孔隙率不同,导致其对催化剂浆液吸附量产生差异,用一定量的催化剂浆液浸渍3种陶瓷滤芯15 min,经过65℃—105℃—450℃程序升温焙烧后分别计算担载量,通过调节催化剂浆液浓度(浓度越高,担载量越高)精准调节催化剂担载量,控制不同滤芯担载量在3 g左右,误差不超过0.1 g,而且在前期研究中发现,催化剂的担载量与浆液中的固含量呈正比,如图4所示。在较短的接触反应时间内,提高NO x脱除率,需要优化催化滤芯上催化剂担载量,本工艺通过调变浆液的固含量调控催化剂担载量,实现其应用性能的提升。以陶瓷滤芯A为例,浆液固含量与催化剂担载量呈一次线性关系,浆液固含量越高,催化剂担载量越多。但压降随催化剂担载量的提高而加速增加。如在催化剂担载量6%(质量分数)、温度250℃、工况过滤面速度2 cm·s-1的条件下,催化滤芯压降迅速增加到1150 Pa,是空白陶瓷滤芯A的压降(270 Pa)的4倍。压降与催化滤芯在工业应用中的反吹频率和运行成本紧密相关,滤芯实际担载量的确定尚需依据脱硝除尘操作工艺确定。
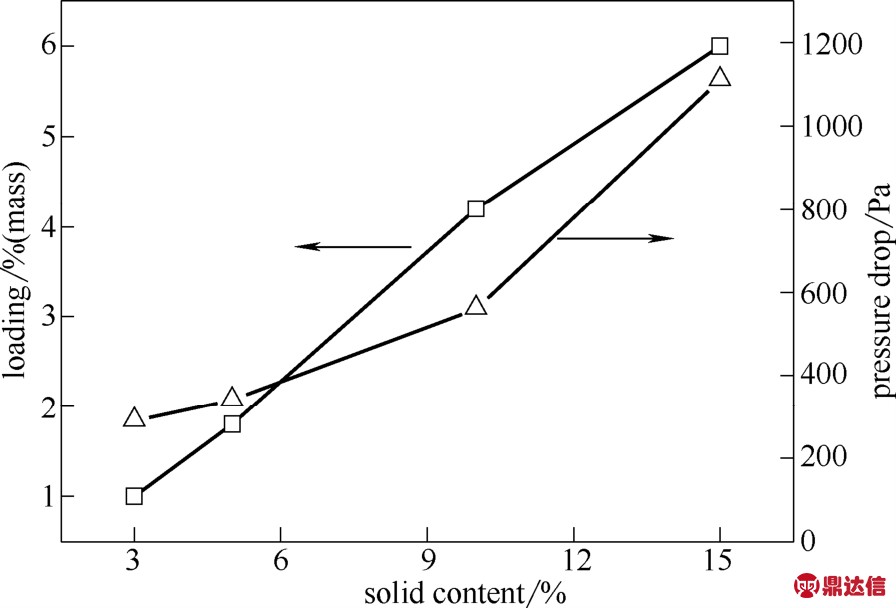
图4 不同固含量浆液制备的催化滤芯催化剂担载量、工况压降与浆液固含量的关系
Fig.4 Relationship between catalyst loading, pressure drop(250℃) and solid content of slurries
不同陶瓷滤芯担载催化剂后的SEM如图5所示,可以看出催化滤芯A上的催化剂颗粒聚集在棒状材料表面,不同细棒互相交叉,由于孔分布较密且均匀,所以催化剂颗粒分散均匀,无明显堵孔现象。催化滤芯B因为孔较稀疏,催化剂颗粒主要聚集在孔洞中间,导致催化剂颗粒团聚现象明显,且容易堵孔。催化滤芯C上的催化剂颗粒分散于表面和部分孔洞中间,其棒状材料黏结在一起,催化剂颗粒较易团聚。
陶瓷滤芯担载催化剂后由于颗粒占据孔道内部空间,导致陶瓷滤芯孔道结构也发生相应改变,并可能影响催化滤芯的脱硝活性与压降,对不同滤芯担载催化剂颗粒后的孔结构进行压汞法表征,结果如表2所示。
对比没担载催化剂的陶瓷滤芯压汞结果,担载催化剂后发现3种陶瓷滤芯的孔容、孔径和孔隙率均有减小,其中陶瓷滤芯B、C的孔隙率减小更严重,这是由催化剂颗粒聚集于孔道内部导致的。
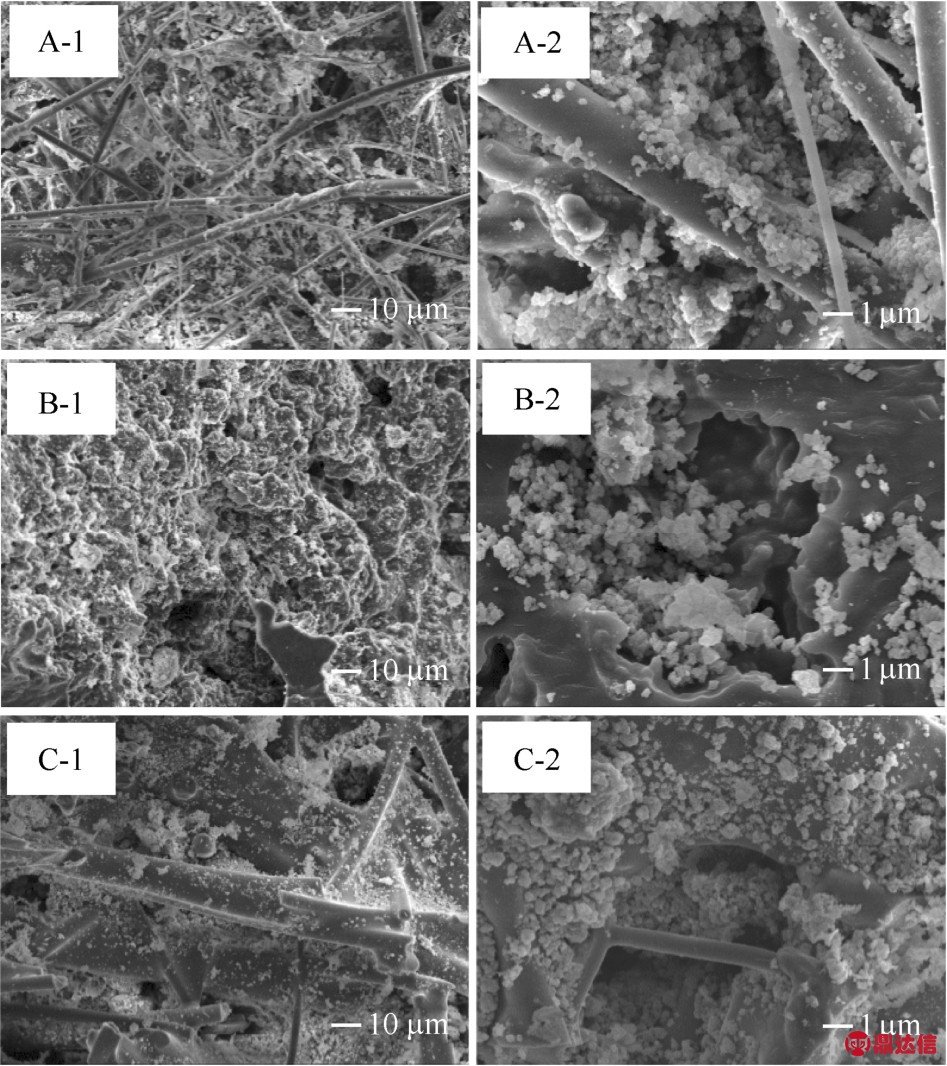
图5 3种涂覆催化剂后催化滤芯的扫描电镜图
Fig.5 SEM images of different catalytic filter materials
2.3 典型催化滤芯的脱硝活性与操作压降
2.3.1 典型催化滤芯的脱硝活性 评价上述3种催化滤芯,结果如图6所示。在整个温度区间内,催化滤芯A脱硝活性最优,在220~380℃温度区间内脱硝率超过90%,催化滤芯B活性次之,催化滤芯C的活性最差,NO x脱除率最大值小于60%。尾气中N2O的生成浓度分析表明,在温度高于300℃时催化滤芯A的N2O生成明显高于B和C样品,表明催化滤芯A具有高脱硝活性的同时,也具有较高的氧化性,有少量的氨气随着温度升高被氧化成N2O,导致反应选择性有所降低。
结合陶瓷滤芯的结构与组成分析,3种不同材质与结构的陶瓷滤芯制备的催化滤芯脱硝性能的显著差异,可能与3种陶瓷滤芯的组成、结构及催化剂在滤芯内部的分布状态有关。从表1中3种陶瓷滤芯的组成可知催化滤芯C中含有21.79% Na2O,碱金属对脱硝活性的抑制已有较多的文献报道[19-20],碱金属易与V O结合生成V—O—Na物种,减少催化剂酸性位,降低NH3的吸附导致催化剂活性降低。且图3所示催化滤芯C多为较粗大的棒状结构相互黏结构成,催化剂在滤芯内的分散相对较差。因此,虽然陶瓷滤芯C具有与陶瓷滤芯A相似的结构特征,但是脱硝活性却远小于陶瓷滤芯A的催化滤芯。结合表2压汞数据和图3的电镜数据可知陶瓷滤芯B具有较大孔容和孔径,导致催化剂颗粒在其表面的分散并不如陶瓷滤芯A均匀,由图5可以看出催化剂颗粒在洞孔常出现堆积现象,这一点也导致催化效果的降低。而陶瓷滤芯B从组成上含有一定量的镁元素,对催化剂活性有一定的抑制[21-23]。但影响其催化活性的主要因素应该与催化剂在滤芯内部的分布和分散状态有关,脱硝反应属于典型的表面反应[24-25],而催化剂在陶瓷滤芯B孔道中聚集严重,这将制约气体在滤芯内与催化剂的有效接触,从而使催化活性有所降低。
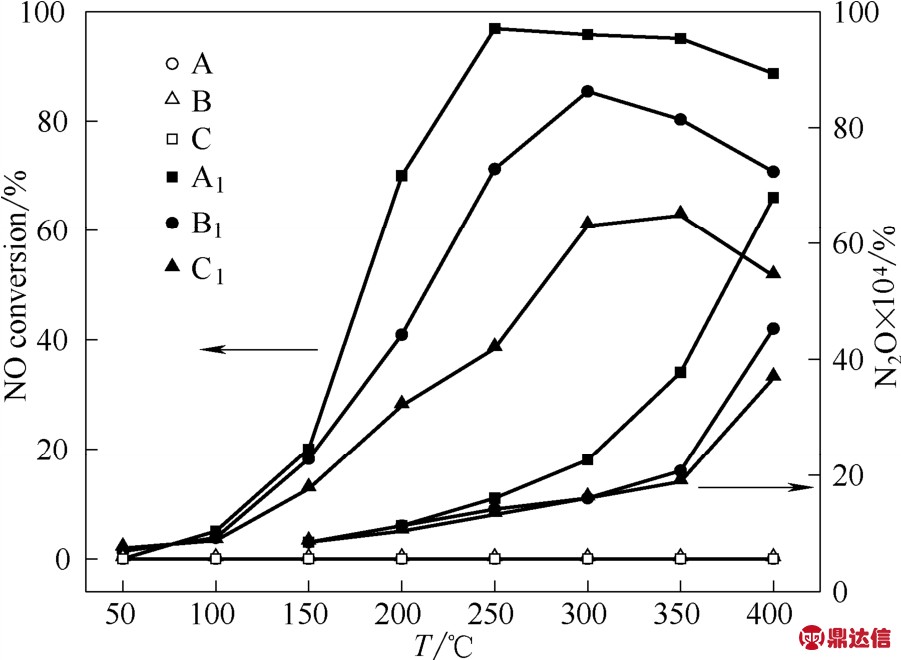
图6 不同催化滤芯脱硝活性及选择性曲线(A、B、C代表空白滤芯,A1、B1、C1代表担载催化剂后的滤芯)
Fig.6 NH3-SCR catalytic performance of different catalytic filters(A, B, C stand for original filters.A1, B1, C1 stand for integrated catalytic filters)
2.3.2 典型催化滤芯的操作压降 压降与流体在孔道内的流速平方呈正比,从图7中不同滤芯的压降变化曲线可以看出,除了滤芯B出现明显的抛物线上升趋势,压降与气速平方的关系明显外,滤芯A和C均体现为直线关系,且相对较小,表明滤芯A、C的孔隙率大,孔径中的气速相对较小,从而在该气速区域内变化并不明显。但从压降的相对增加斜率来看,B > C >A,而且担载催化剂后,压降都有小幅度上升。其中随着气速增大滤芯B的压降增加幅度最大,滤芯A的变化最小,结合担载催化剂后的孔隙分析,表明滤芯B的孔径与孔容减少明显。该结果也进一步表明催化剂在滤芯A内分散状态最好,而且催化剂的涂覆对孔隙和孔结构影响也最小。根据工业应用上压降的要求,催化滤芯压降越小,操作成本越低,催化滤芯A更符合脱硝除尘一体化操作要求。
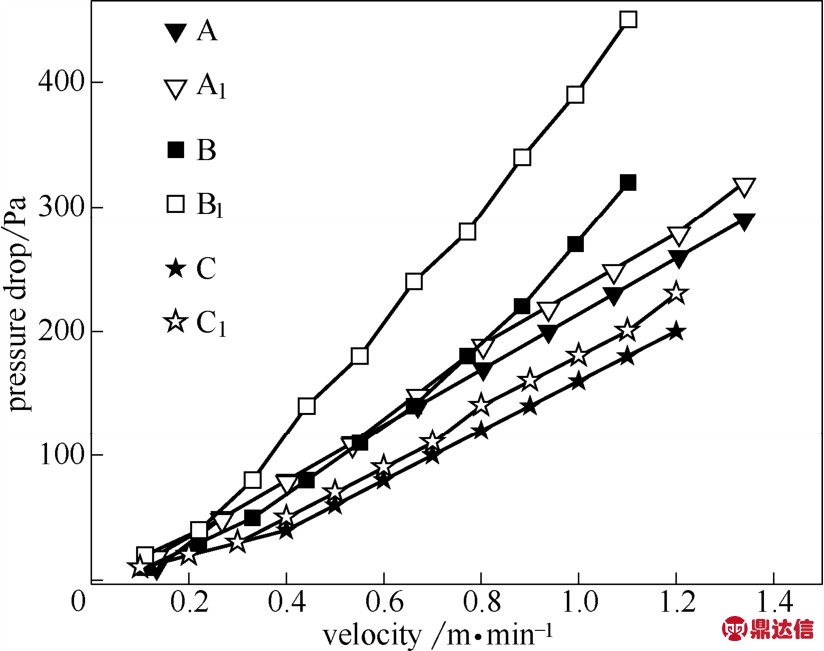
图7 不同陶瓷滤芯压降特性(A、B、C代表空白滤芯,A1、B1、C1代表担载催化剂后的滤芯)
Fig.7 Comparison of pressure drop over different filters
(A, B, C stand for original filters.A1, B1, C1 stand for integrated catalytic filters)
2.4 催化滤芯烟气条件适应性
鉴于A、B催化滤芯具有较好的催化活性,分别以1和2 m·min-1的气速评价催化滤芯A、B(图8),可以看出气速增大后催化滤芯的脱硝活性随之减弱,主要是因为气速变大后气体分子与催化剂颗粒的接触时间变短,导致转化率降低[26-28]。
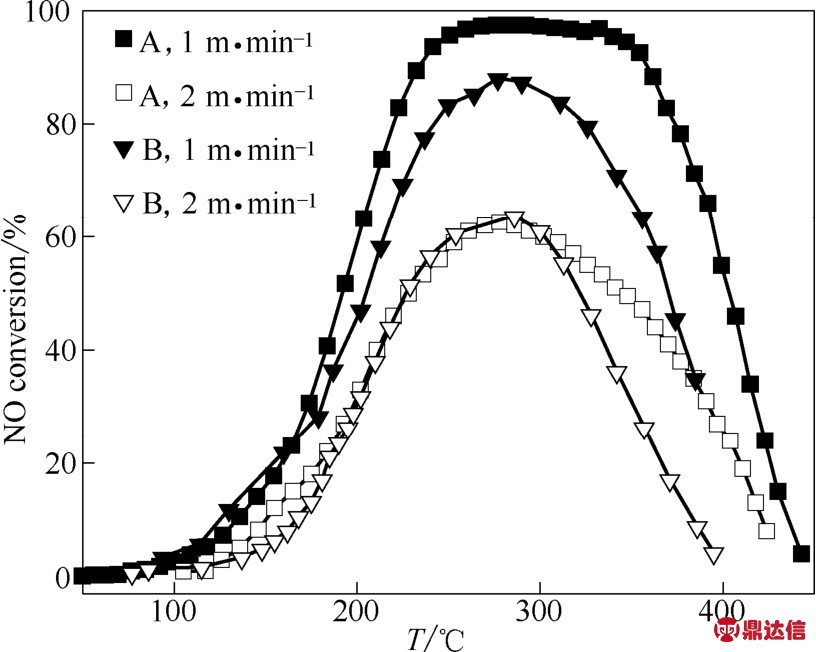
图8 催化滤芯A、B在不同气速下催化活性的对比
Fig.8 Comparison of catalytic activity for NH3-SCR over
A, B catalytic filters under different gas velocity
对比 300℃前后的催化活性与温度的变化关系,可以看出低温条件下,随着气速的增加,两种催化滤芯的活性趋于一致,催化活性直接取决于气体在催化滤芯中的停留时间[29-30];在高温区(T>300℃)催化滤芯A由于气速增加所导致的活性降低现象相对缓和,这是因为催化剂颗粒在滤芯孔道中处于高分散状态,使孔道中有更多活性催化剂与反应气体接触,提高了整体催化滤芯的催化活性。而催化滤芯B中催化剂团聚堆积状态导致氨氧化性增强,使得高温NO转化率随温度升高而减小相对更加明显。
图9展示了水蒸气和SO2对催化滤芯脱硝性能的影响结果。在220℃时通入相当于总气量15%(φ)的水蒸气后,脱硝活性降低了近20%,当温度升至280℃时,脱硝率反而升高至 98%以上,结合 N2O的生成可以发现,水蒸气的加入在催化剂表面参与了与氨的竞争吸附,有效抑制了氨氧化反应的发生,从而提高了高温脱硝活性和选择性[31-34]。
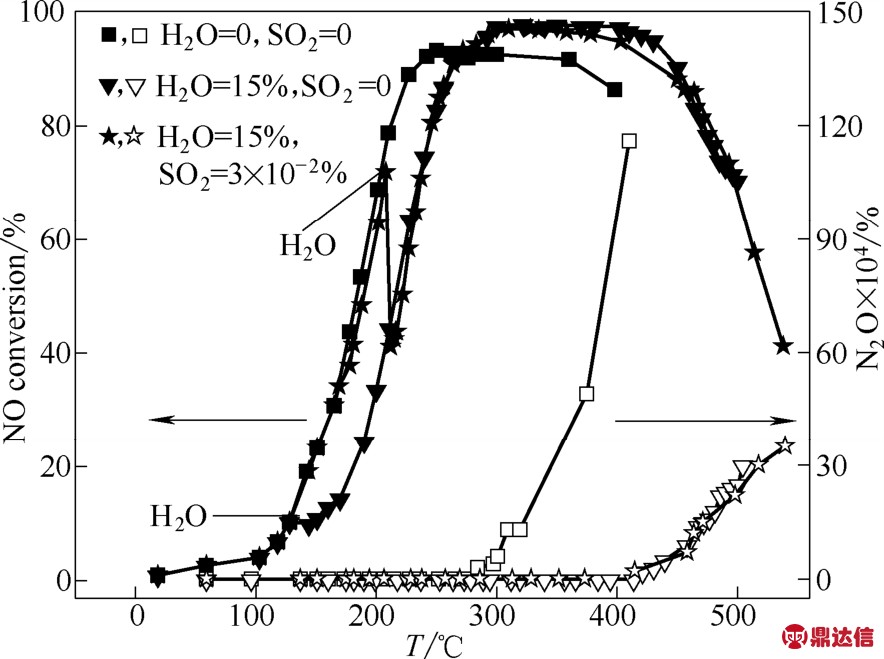
图9 水蒸气和SO2对陶瓷滤芯A脱硝性能的影响
Fig.9 Effect of water vapour and SO2 on catalytic performance for NH3-SCR over catalytic filter A
当模拟烟气同时通入15%(体积分数)水蒸气与3×10-2%(体积分数) SO2后,其NO的脱除率随温度的变化与单独水蒸气存在情况一致,表明在高温条件下SO2对该催化剂无明显影响[35-37],这也符合钒系催化剂的特征。上述结果表明,催化滤芯A可满足不同面速度下抗硫抗水工业脱硝应用性能的要求。
3 结 论
本文用3种典型工业陶瓷滤芯涂覆脱硝催化剂制备催化滤芯的研究可得出以下结论。
(1)3种陶瓷滤芯分别为氧化铝纤维管、堇青石烧结管及硅铝酸盐纤维管。纤维管具有更均匀的孔隙结构与大的孔隙率,在相同催化剂负载量条件下,氧化铝纤维管A中催化剂主要黏结于棒状材料上,分散很均匀,对原始滤芯孔道结构影响较小;堇青石管B中的催化剂颗粒主要黏结于孔道周围,多呈堆积状,孔道堵塞严重;陶瓷滤芯C中催化剂颗粒在孔道中分布介于陶瓷滤芯A和B之间。
(2)陶瓷滤芯的孔隙结构及催化剂在孔隙中的分散状态显著影响滤芯的催化性能与压降。结构表征和脱硝性能测试结果表明催化滤芯A中催化剂分散均匀,且不含抑制催化活性的碱金属与碱土金属成分,显示出最佳的催化活性,在 1 m·min-1过滤速度下,220~380℃温度区间内 NO x转化率超过90%。纤维结构的A与C材料孔隙率大,涂覆催化剂后,催化剂颗粒分散均匀,对滤芯孔道结构改变较小,而B孔隙率低,催化剂颗粒堵孔严重,导致催化滤芯B的压降明显高于A、C。
(3)对催化滤芯A的抗硫抗水性能考察,发现水蒸气的加入显著降低了N2O的生成,拓宽了催化滤芯的高温脱硝温区,在260~450℃温度区间内达到90%以上的脱硝率;而SO2的引入并未对催化剂活性产生抑制作用,满足脱硝除尘一体化工业应用对脱硝率与活性温度窗口的要求。