摘 要:针对天然气输送管路中气体含液浓度变化范围宽且严重影响滤芯正常使用的问题,为了分析气体含液浓度对滤芯压降和含液量的影响,以及研究不同层数滤芯应用于不同浓度工况下的可行性,利用滤芯过滤性能评价装置比较了0.07~1.00 g⋅m-3不同气体含液浓度条件下不同层数滤芯的压降变化。结果表明:气体含液浓度通过改变滤材内运移液体的通道数目而对滤芯通道压降产生较大影响,浓度升高导致通道数目增多、通道形成时间缩短、滤芯各层含液量增多。同时发现,通道压降随气体含液浓度的增大呈非线性增长,其中气体含液浓度影响的滤材含液量是否达到饱和值,是通道压降急剧上升的关键。此外,滤芯层数通过影响通道数目而改变通道压降增长趋势,当气体含液浓度在0.2~0.4 g⋅m-3时,增加滤芯层数,可以降低通道压降。建立的气体含液浓度、滤芯层数与通道压降的关系模型可为工程实际中滤芯结构优化和不同浓度工况下通道压降预测提供指导帮助。
关键词:天然气;气体含液浓度;过滤;压降;滤芯层数
1 前 言
气液聚结过滤器在天然气净化、大型旋转机械曲轴箱通风和压缩空气过滤等领域具有广泛的应用,其性能对于维持系统正常运行、减少环境污染起着关键性作用[1,2]。滤芯作为气液聚结过滤器的核心元件,其压降直接影响着设备运行及自身寿命。有研究表明,低含液量气体对天然气输运效率有很大影响[3],含0.5%凝析液天然气的压降较单相天然气高30%,并且工程现场中发现气体含液量大是造成滤芯压降升高进而造成其破损变形的主要因素之一[4]。因此,针对实际工况下气体含液浓度变化范围宽、不稳定且严重影响滤芯压降的特点,研究气体含液浓度对滤芯气液过滤机理以及优化滤芯结构具有重要意义。
近年来,国内外学者对滤材的气液过滤性能研究主要集中在影响因素(如操作条件、液滴物性和滤材物性等)的考察[5~7]、单根纤维与液滴的相互作用[8,9]、滤材稳态压降与效率的模型建立[10,11]等方面。其中一些学者建立的压降理论模型正在被广泛应用于压降数据的分析。Contal等[12]依据液滴与纤维的不同作用形态,将压降过程划分为四个阶段,分别为洁净、液滴附着、液滴变大成为液桥、液桥相互连接成为液膜。Vasudevan等[13]根据压降随过滤时间的变化,将气液过滤过程划分为起始阶段、润湿阶段、非稳态聚结阶段以及稳态聚结阶段。Kampa等[14]提出“跳跃-通道”理论,该理论将润湿压降分为通道压降与跳跃压降。其中,润湿压降为滤芯压降与初始压降的差值;通道压降为滤材内部液体对气流阻碍所产生的压降,当液滴被纤维拦截后,液滴填充纤维间的空隙,滤材内部逐渐形成向下一层传递液体的通道;跳跃压降为液膜对气流阻碍产生的压降,当液滴运移至亲油型滤材最外层排气侧时,由于亲油型滤材对液滴的黏附作用,液滴在滤材排气侧表面累积形成一层薄的液膜,液膜对气流的阻碍导致压降升高。Chang等[15,16]结合下游液滴计数浓度曲线,确定出通道压降与跳跃压降的分界点。
另外,国内外学者开展过一些关于气体含液浓度的基础研究。Contal等[12]认为气体含液浓度对压降的影响无显著差别,同时,当过滤速度从0.025上升至0.19 m⋅s-1过程中,滤芯压降随着过滤速度升高而增大。但是另外几位专家得到了相反的结论,Kampa等[17]发现气体含液浓度影响亲油型滤材的通道压降,通道压降随气体含液浓度增大呈线性上升,而跳跃压降则相对独立于气体含液浓度。由此可以发现,关于气体含液浓度对亲油型滤材通道压降的影响存在不同的结论,而目前对于这两种相反结论产生的原因并没有研究与解释,弄清气体含液浓度在何种情况下影响通道压降十分必要。
此外,气液聚结滤芯结构的优化集中在对孔径、材料等滤材本身参数[14,18]的研究,而对滤芯层数研究较少,且在不同工况下,滤芯大多为相同层数规格。梁晓光等[19]对毛细管精馏过程中气液两相流动采用CFD模拟计算,发现壁面吸附作用在一定程度上影响气液柱的长度;Mullins、Mead-Hunter等[20,21]将液体在多孔介质通道中的运动类比为液体在毛细管中流动,提出了毛细理论,滤材层数的增多即毛细管长度增加,进而影响液体运移。这些研究为在气体含液浓度不同的工况下气液聚结滤芯层数的优化提供了一种可能。
综上所述,可以发现工程实际方面,管路内气体含液浓度变化范围宽,严重影响滤芯压降,理论研究方面,关于气体含液浓度对通道压降的影响,分析尚不全面,目前存在两种不同的结论,对于这两种结论不同的原因尚未给出解释。同时,针对气体含液浓度不同的工况,关于滤芯层数对通道压降影响的研究较少,通过改变滤芯层数来解决气体含液浓度造成的滤芯压降过高的可行性有待研究。为此,本文利用一套滤芯过滤性能实验装置,在气体含液浓度0.07~1.0 g⋅m-3、工程实际表观气速0.10 m⋅s-1操作条件下对滤芯进行实验。选择相同材料、4种不同层数的亲油型滤芯作为实验材料,对比分析气体含液浓度对不同层数的亲油型滤芯压降以及滤芯内部含液量的影响。
2 实 验
2.1 材料与试剂
实验采用目前国际测试标准中规定的癸二酸二辛酯(DEHS,通辽市威宁化工有限责任公司)作为实验液体,其密度为912 kg⋅m-3,动力黏度为0.023 Pa⋅s,表面张力0.03 N⋅m-1。采用4、6、8、10层的亲油型滤芯A进行实验,分别记为A4、A6、A8、A10,滤芯内径为(50±0.1) mm,有效过滤长度为(105±0.2) mm,其结构组成见表1。为测定滤材A的润湿性,利用瑞典BiolinScientific公司Attension接触角测量仪,测得DEHS液滴自由下落与滤材表面接触瞬间的接触角,重复三次求平均值,得到接触角为(66±3)°,滤材A为亲油型玻璃纤维滤材。 滤材厚度通过千分尺进行测量,滤材克重通过对150 mm×100 mm洁净滤材矩形片称重得到,滤材经扫描电镜拍照后,在照片内随机取20根单根纤维直径,求其平均值得到平均纤维直径。利用美国PMI孔径测试仪测得滤材平均孔径为(3.8±0.1) μm。滤材物性参数见表1。
表1 滤材物性参数
Table 1 Properties of filter materials used in the study

2.2 实验流程与分析仪器
根据中国、欧洲相关测试标准[22,23],建立了滤芯过滤性能实验装置,如图1所示。压缩气体通入气溶胶发生器(ATM240,德国TOPAS公司)后发出气溶胶液滴,在真空泵抽气作用下,上游洁净的气体与气溶胶液滴混合,混合后的气体进入装有待测滤芯的装置,滤芯垂直放置,气流由滤芯内向外穿过,气体中夹带的液滴被滤芯拦截过滤,过滤后的液滴进入集液瓶。在实验过程中,通过控制流量调节阀的开度,使流经滤芯的气体体积流量保持恒定;通过调节浮子流量计(LZJ-10,双环热工仪表有限公司,量程 250~2500 L⋅h-1,精度2.5级)控制进入气溶胶发生器的压缩气体流量来改变发出的气溶胶浓度。在滤芯上、下游处采用光学粒子计数器(OPC,Welas-3000,德国Palas公司)对气体中气溶胶的浓度等进行测量。滤芯的压降变化由压差变送器(BF3051CD,上海倍福自动化科技有限公司,量程0~50 kPa,精度0.5级)实时记录。实验结束后,对滤芯进行分层解剖,利用电子分析天平(AL204-IC,美国梅特勒公司,量程0~220 g,精度0.1 mg)对滤芯内部滤材称重,得到滤芯内部各层滤材的持液量情况。同时利用数码相机(α500,日本SONY公司)对各层滤材拍照。
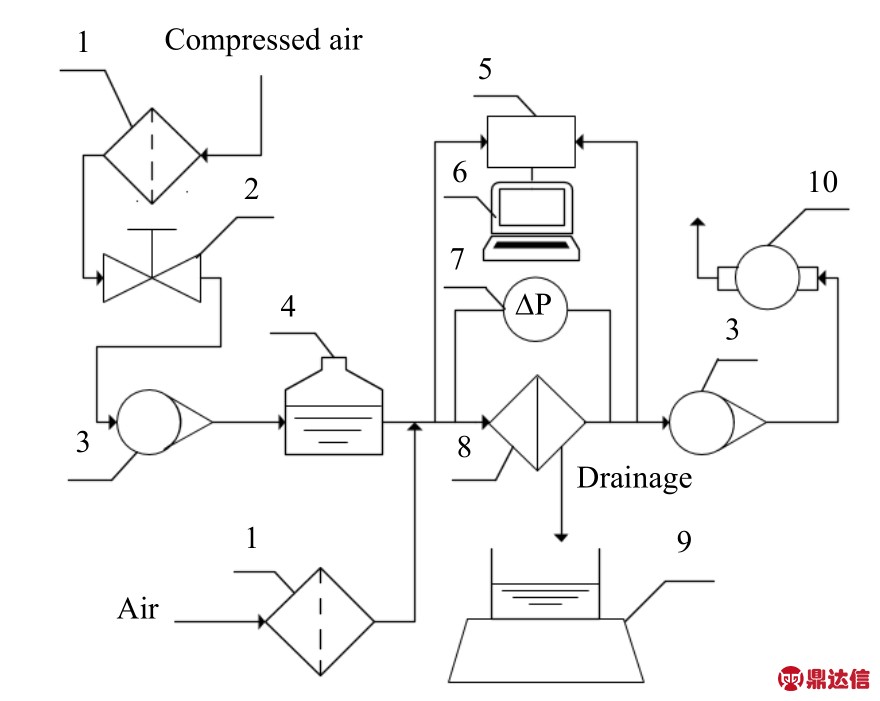
图1 实验装置图
Fig.1 Schematic diagram of experimental set-up
1.HEPA filter 2.pressure valve 3.flow meter 4.atomizer 5.optical particle counter 6.computer 7.pressure transmitter 8.test filter 9.balance 10.vacuum pump
2.3 实验方法
根据天然气长输管道现场检测工况流量6 m3⋅h-1以及现场测试所用有效过滤长度为105 mm、内径为50 mm的滤芯计算得到工程实际表观气速为0.10 m⋅s-1[24],所以在气体含液浓度0.07~1.0 g⋅m-3、实验表观气速为0.10 m⋅s-1操作条件下对不同层数滤芯进行实验,根据ISO12500标准,规定当滤芯压降在1 h内变化小于1% 时认为滤芯达到稳定状态,可以认为该状态下测得的滤芯效率和阻力为滤芯的评价性能数据,故在稳定状态下对滤芯进行分层解剖,分析滤芯内液体分布情况。将滤芯内部各层玻璃纤维制成150 mm×100 mm矩形片,利用电子分析天平称重并与未过滤前滤材重量相比较,即得到滤材持液量及稳态下滤芯饱和度S,S可按照下式进行计算。

其中,Vvoid可用式(2)进行计算。
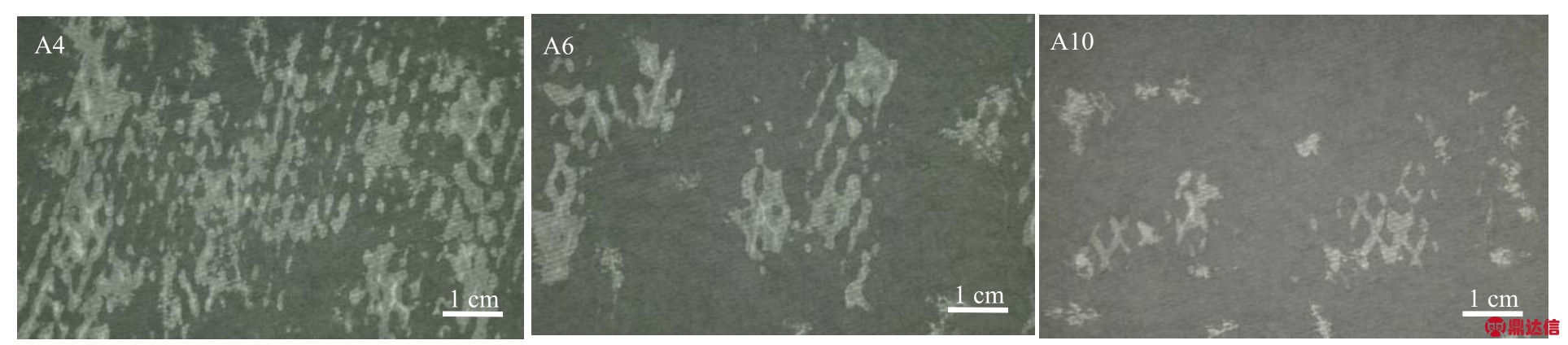
以上两式中,Voil为实验介质在滤材内所占据的体积 m3,ρoil为实验介质密度 kg⋅m-3,Vvoid为滤材空隙体积m3,moil为滤芯中液体持液量g,mfilter为实验后滤芯质量g,mfilter,0为实验前滤芯质量g,为理论上滤芯最大持液量g,V为滤材总体积m3,α为填充密度。
3 结果与讨论
3.1 亲油型滤芯A饱和度与压降曲线分析
为了考察实验所用滤芯的饱和度与压降趋势,方便后续研究,在表观气速0.10 m⋅s-1、气体含液浓度0.493 g⋅m-3的操作条件下进行实验,以滤芯A8为例进行分析。图2为A8滤芯在过滤过程中的各层饱和度与压降曲线。如图2(a)所示,滤材各层饱和度曲线呈凹形,其中,第1层滤材饱和度远高于中间各层滤材饱和度,第7~8层滤材饱和度上升。这说明,滤芯各层含液量分布不均匀。在通道运移过程中,大多数液滴被第 1层滤材拦截吸收,导致后续各层饱和度较低。文献[15]中当液体运移至最后一层,压降还未发生跳跃即滤材外表面还未形成液膜时,停止实验,发现滤芯最后各层饱和度均处于一致水平,这说明在滤芯最外层排气侧处液膜的形成过程中,液膜的存在阻碍了液体的运移,使得靠近液膜的滤材吸收更多的液体,稳定状态时,由于亲油型滤材与液滴的黏附作用,在实验结束停气后,液膜会被重新吸入到最后一层滤材,造成最后一层滤材饱和度增高,故为了排出液膜重新吸入对饱和度的影响,最后一层饱和度与其上一层数值保持一致。如图2(b)所示,压降曲线呈现三段不同斜率增长趋势。依据“跳跃-通道”理论[14]以及文献[16],将A8滤芯的压降过程划分为四个阶段。由图可以看出,A点为压降起始点,C点处下游计数浓度开始上升,D点处下游计数浓度稳定。这意味着A-C为通道压降 ΔpchannelA-C形成阶段(stage1、stage2),压降上升是由于滤芯内部拦截的液体对气流的阻碍造成的,下游计数浓度达到稳定说明液膜形成达到稳定,即C-D为跳跃压降 ΔpjumpC-D形成阶段(stage3),液膜对气流的阻碍造成压降进一步上升,D点至实验结束为稳定阶段(stage4)。
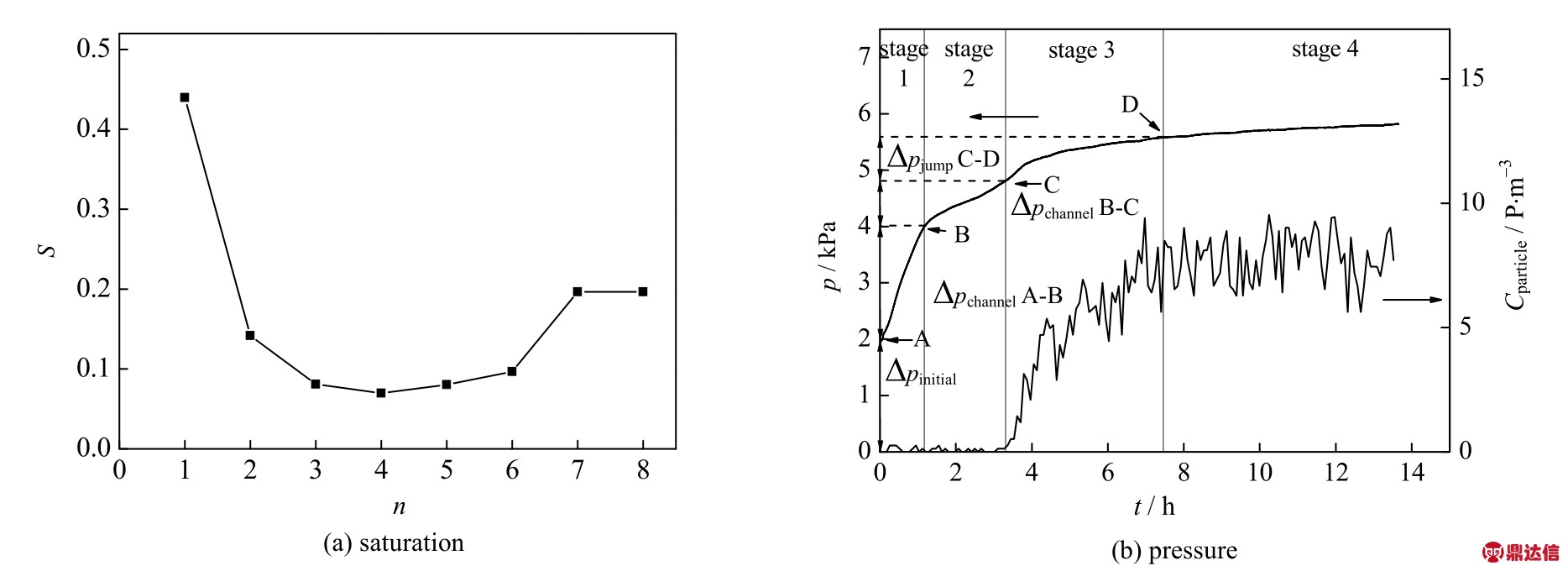
图2 过滤过程中A8滤芯饱和度和压降曲线
Fig.2 Saturation and pressure drop profiles of filter cartridge A8 during experiments
由图2(b)可以发现,在A-C通道形成阶段内,有明显的拐点B。结合图2(a)中滤芯第1层的饱和度远高于其余各层的特点,说明滤芯第1层内部液体对气流阻碍较大,第1层滤材所产生的通道压降应高于其他各层。此外,对比Chang等[15,16]实验所得到压降与饱和度曲线,可以发现,当滤芯第1层饱和度与中间各层饱和度的差异较小时,通道压降呈现平稳增长趋势。因此将通道压降 ΔpchannelA-C分为两个阶段,其中A-B阶段(stage1)是滤芯第1层滤材内部液体对气流阻碍产生的通道压降,记为 ΔpchannelA-B。B-C阶段(stage2)为滤芯其余各层内部液体对气流阻碍产生的通道压降,记为 ΔpchannelB-C。
3.2 不同气体含液浓度对滤芯饱和度及压降的影响
为了研究气体含液浓度对滤芯饱和度及压降的影响,在表观气速0.10 m⋅s-1、气体含液浓度0.070、0.160、0.390、0.469、0.591、0.836、0.988 g⋅m-3的操作条件下进行实验,以滤芯A10为例进行分析。图3为A10滤芯在不同气体含液浓度下的饱和度和压降曲线。由图3(a)可见,在不同气体含液浓度作用下,滤芯饱和度以相同的凹型趋势上下分布。自上而下,气体含液浓度逐渐减小,对应的滤芯各层饱和度递减,即含液量下降。图 3(b)中可以发现,气体含液浓度的增大,导致滤芯整体润湿压降升高,其中,第一阶段由第1层滤材产生的通道压降 ΔpchannelA-B增长显著,同时对比实验最高、最低气体含液浓度下滤芯第一阶段时间 Δt1(虚线)和第二阶段时间 Δt2(实线)可以发现,最高气体含液浓度下Δt1与Δt2均较小。
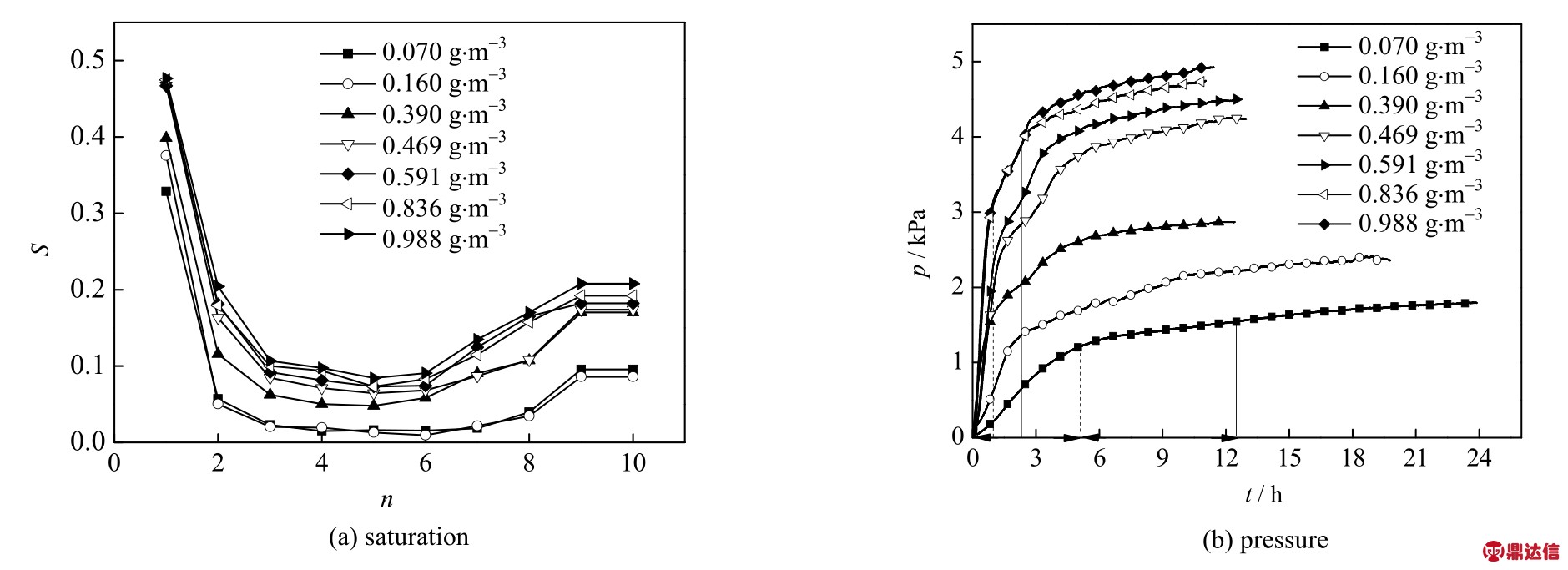
图3 不同气体含液浓度下A10滤芯压降和饱和度曲线对比
Fig.3 Comparison of saturation and pressure drop profiles of A10 under different oil concentrations in gas
结合“跳跃-通道”理论[14]对气体含液浓度变化导致的以上现象进行分析。图4为A10滤芯在不同气体含液浓度下第四层滤材拆解图,由图可见,气体含液浓度较高时,滤材润湿面积较大,根据文献[14],润湿部分实际为运移液体的微小通道,润湿面积的增大说明形成的通道数目增加。因此认为,气体含液浓度增大,相同时间内,更多的液滴到达纤维表面,同时,液滴在纤维上聚结速度加快,这使得,纤维内部运移液体的通道数目增多并且其形成时间缩短,进而导致滤材内部通道内液体含量上升,其对气流产生较大阻碍,引起压降升高。通过图3(a)可以发现第一层滤材拦截的液滴较多,因此造成第1层滤材通道压降 ΔpchannelA-B显著升高。运用毛细理论同样可以证明气体含液浓度影响通道数目,根据文献[20],将滤材通道类比为毛细管,滤材内液体运移的长度x(t)可用式(3)进行计算。
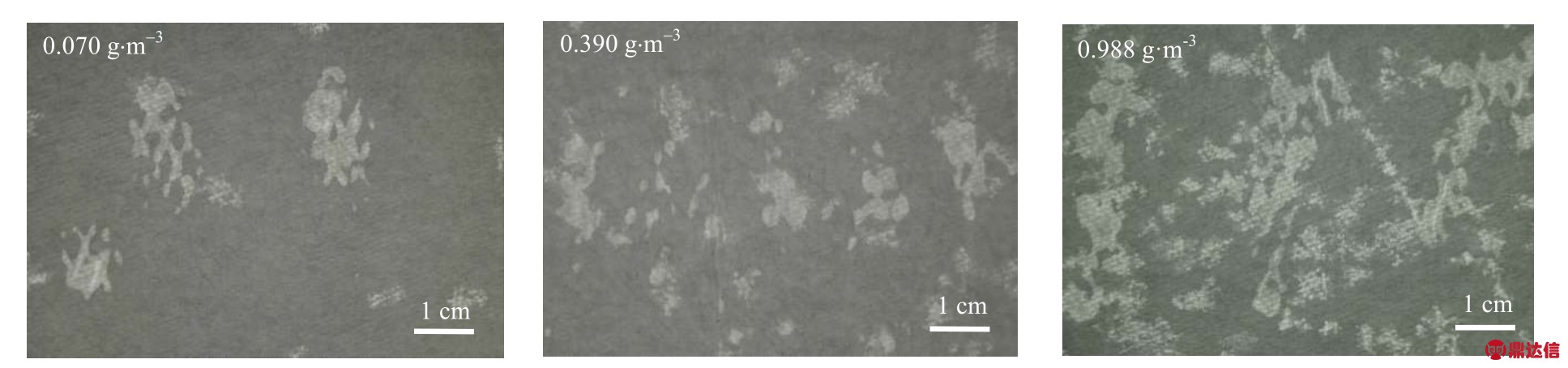
图4 不同气体含液浓度下A10滤芯第四层滤材对比图
Fig.4 Comparison of the forth layers of A10 under different oil concentrations in gas

其中x( t)为t时间时滤材内液体运移长度m,moil(t)为t时间时液体的质量g,ρoil为实验介质密度kg⋅m-3,A为滤材截面积m2,α为填充密度。A(1-α)代表运移液体的孔隙截面面积。由于滤芯层数相同,最终滤材内液体运移长度x(t)相同,当气体含液浓度增大,相同时间内液体质量moil(t)增加,导致A(1-α)的面积增大,即润湿面积增大,通道数目增多。而正是因为运移液体的通道数目增多,各层滤材内含液量更快地接近饱和状态,使得第一、第二阶段时间缩短,加速了液体的传递。
为了进一步说明不同气体含液浓度对滤芯压降的影响,对不同气体含液浓度下A10滤芯的压降进行分阶段研究。图5为不同气体含液浓度下A10滤芯各阶段压降曲线,由图可见,随着气体含液浓度的增大,通道压降第一阶段 ΔpchannelA-B与第二阶段 ΔpchannelB-C以及液膜引起的跳跃压降 ΔpjumpC-D均呈现增长态势,其中,ΔpchannelA-B的增长尤为显著。同时,当气体含液浓度为0.4~0.5 g⋅m-3时,各阶段压降均出现急剧增长。由此首先说明,通道压降更容易受到气体含液浓度的影响,由第1层滤材引起的通道压降 ΔpchannelA-B对于这种影响更为明显,此外更为重要的是,发现随着气体含液浓度增大,通道压降呈非线性增长,当气体含液浓度增大到一定值,通道压降发生跳跃增长。
结合图3(a)不同气体含液浓度下A10滤芯饱和度曲线对通道压降非线性增长进行分析。当气体含液浓度为0~0.4 g⋅m-3时,通道压降呈线性增长,此时,滤材内部并没有被液体填满,由图3(a)第一层饱和度数值可以证明,当气体含液浓度为0~0.4 g⋅m-3时,滤芯第一层饱和度处于上升态势,说明此时滤材内部含液量并未到达饱和状态,滤材拦截液滴与其向下一层运移液滴处于一种动态平衡;当处于 0.4~0.5 g⋅m-3较高的气体含液浓度条件下,滤材内部空隙被迅速填满,图3(a)中该气体含液浓度下的第一层滤材饱和度达到最高值,说明滤材内部含液量已达到饱和状态,这个浓度范围内,滤材拦截液滴的能力超出了其向下一层运移液体的能力,导致自身内部含液量急剧升高至饱和,因此引起 ΔpchannelA-B与 ΔpchannelB-C的急剧增长;当气体含液浓度超过0.5 g⋅m-3,此时,滤材内部液体含量已经处于饱和状态,图3(a)第一层饱和度数值没有变化,因此通道压降增长变缓直至稳定。之所以选第1层滤材分析,是由于其首先与气流携带的液滴的发生拦截作用,因此第1层滤材更容易受到气体含液浓度影响,其变化更为明显。
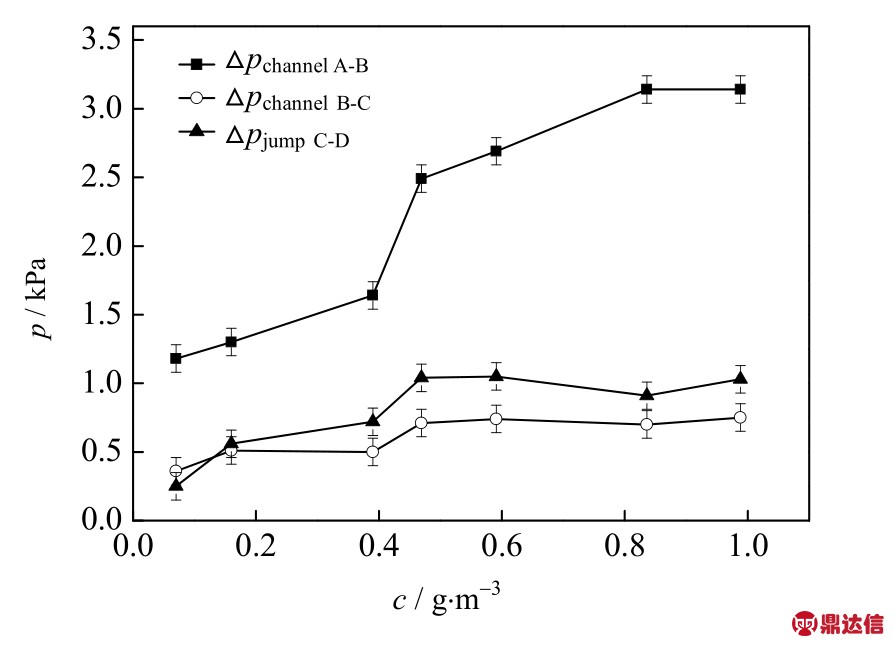
图5 不同气体含液浓度下A10滤芯各阶段压降的变化
Fig.5 Pressure drop of A10 at various stages under different oil concentrations in gas
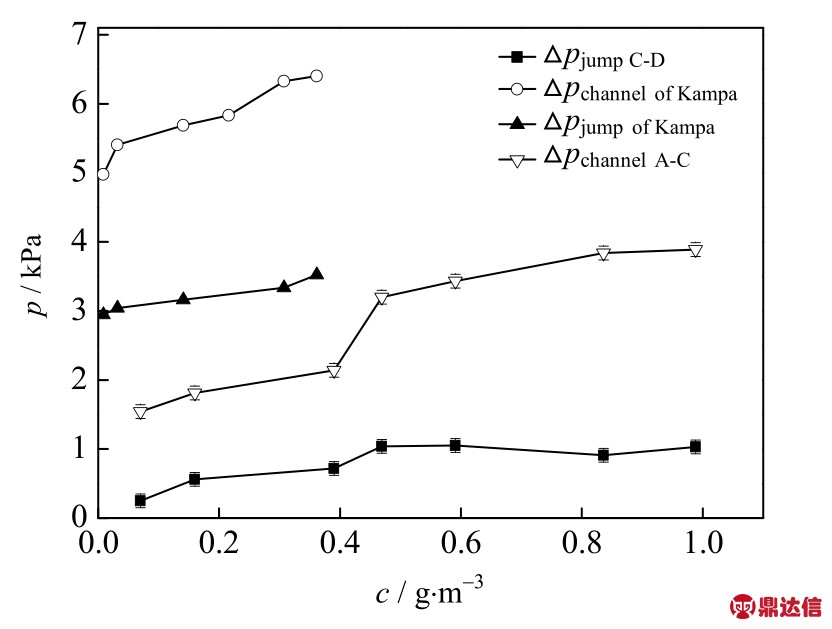
图6 不同气体含液浓度下各阶段压降的对比
Fig.6 Comparison of pressure drop at various stages under different oil concentrations in gas
为了解释目前气体含液浓度对通道压降影响出现两种不同结论的原因,将 Kampa在表观气速 0.3 m⋅s-1、气体含液浓度0.09~0.36 g⋅m-3下得到的实验数据与A10滤芯各阶段压降对比,图6为A10滤芯不同气体含液浓度下各阶段压降与国外专家Kampa[17]实验数据对比曲线,由图可以发现,在重叠的气体含液浓度范围内,实验得到的通道压降和跳跃压降的增长趋势与Kampa得到的趋势相同。这一现象首先证明了实验结果的可靠性,其次说明通道压降在气体含液浓度较低阶段呈线性增长,正如上文分析,气体含液浓度较低时,滤材内部含液量并未达到饱和,含液量随气体含液浓度增大呈线性上升。同时印证跳跃压降确实相对独立于气体含液浓度。当气体含液浓度处于0.6~1.0 g⋅m-3较高范围时,滤材内部含液量已达到饱和状态,导致通道压降急剧增长后,其增长趋势变缓,这与Contal等[12]在气体含液浓度0.6~5.7 g⋅m-3条件下得到的气体含液浓度对压降的增长影响没有显著变化的结论相接近。综上说明,通道压降随气体含液浓度的增大呈非线性增长,其中气体含液浓度影响的滤材含液量是否达到饱和值,是判断通道压降急剧上升的关键。
用A10滤芯在不同气体含浓度下的通道压降数据拟合得到式(4)气体含液浓度与通道压降的关系,如图7所示。

其中X1= 1.54,X2= 3.89,它们的数值与滤材性质有关。
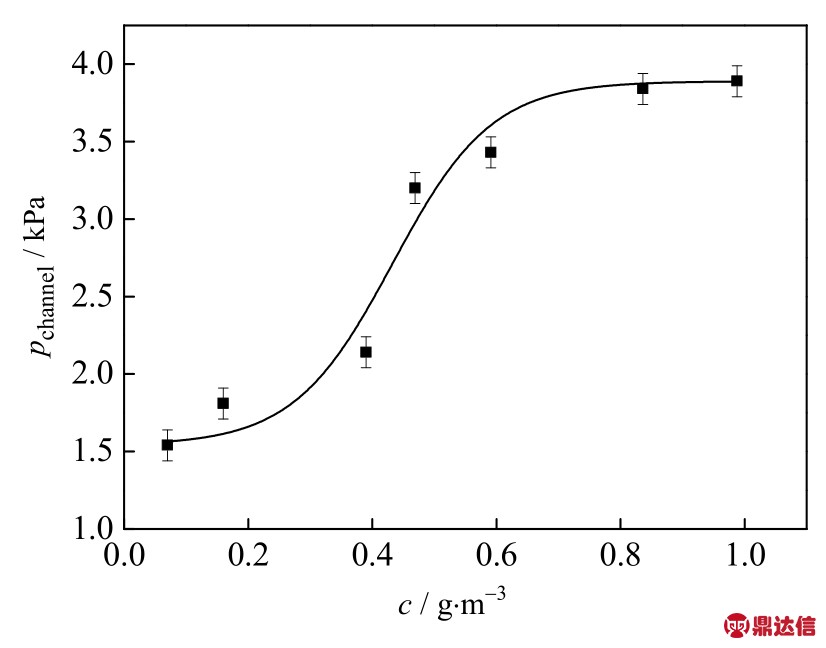
图7 气体含液浓度与通道压降的关系
Fig.7 Relationship between oil concentration in gas and channel pressure drop
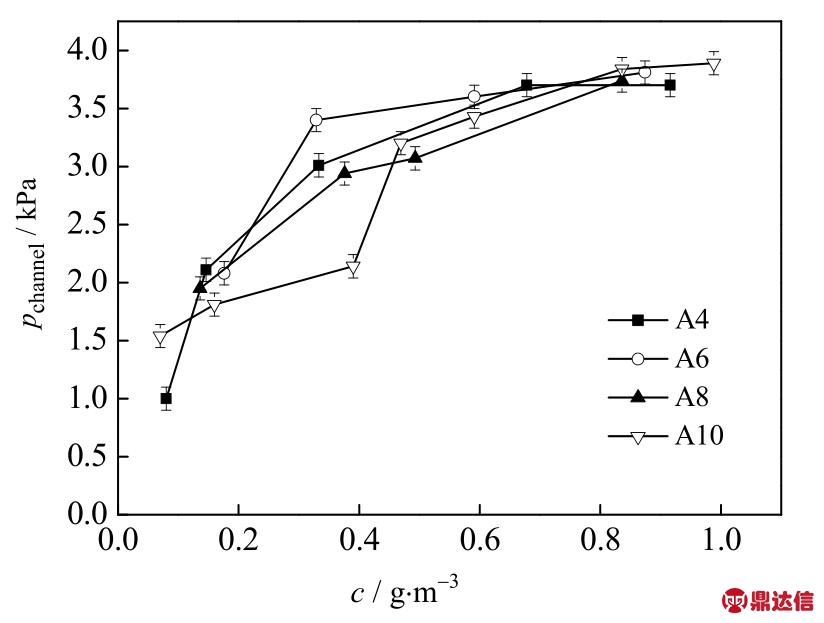
图8 不同气体含液浓度下不同层数滤芯的通道压降对比图
Fig.8 Comparison of △pchannelof filter cartridges with different layers under different oil concentrations in gas
3.3 不同气体含液浓度下滤芯层数对通道压降的影响
基于通道压降 ΔpchannelA-C更容易受到气体含液浓度的影响,进一步研究不同的气体含液浓度操作条件下,滤芯层数对通道压降的影响。在实验表观气速0.1 m⋅s-1、气体含液浓度(0.070±1)、(0.150±1)、(0.390±1)、(0.469±1)、(0.988±0.01) g⋅m-3的操作条件下,对 A4、A6、A8、A10滤芯进行实验。图8为不同层数滤芯在不同气体含液浓度下通道压降的对比曲线。由图可见,在实验气体含液浓度范围内,4种层数的滤芯通道压降均在1~4 kPa,当气体含液浓度低于0.2 g⋅m-3时,4层滤芯通道压降最低;当气体含液浓度处于较低范围0.2~0.4 g⋅m-3时,层数较多的滤芯对应的通道压降较低,而当气体含液浓度超过0.6 g⋅m-3后,不同层数的通道压降均达到同一数值。同时,A4滤芯在0.08~0.30 g⋅m-3的气体含液浓度范围内发生通道压降急剧升高,A6、A8滤芯通道压降急剧升高时对应的气体含液浓度范围为0.15~0.35 g⋅m-3,A10滤芯通道压降急剧升高时对应的气体含液浓度范围为0.4~0.5 g⋅m-3。这说明:不同气体含液浓度下,滤芯层数的变化并没有引起通道压降增幅明显改变,当气体含液浓度足够大时,不同层数滤芯最终的通道压降稳定在同一数值,但滤芯层数变化影响通道压降增长趋势,滤芯层数越多,滤芯通道压降急剧升高时对应的气体含液浓度越大。同时说明,在气体含液浓度在0.2~0.4 g⋅m-3时,增加滤芯层数可以使得通道压降降低。
结合毛细理论中经典的Washburn方程[25]对这种现象进行分析,式(5)为Washburn方程:

其中,l为液体穿过毛细管的长度m,γ为液体表面张力N⋅m-1,cosθ为接触角的余弦值,η为液体动力黏度Pa⋅s,r移为毛细管半径m,t为液体运移时间s。将滤材、液体物性参数以及实验时间14 h带入公式(4)得到l为0.159 m,而滤芯最多层数10层的厚度为0.004 m,因此实验时间内液体均会运移到最后一层。针对多孔材料,假设液体对于多孔材料的穿透体积等于半径为r1,r2,…rn的n个圆柱毛细管总穿透体积的和,因此进入多孔内液体的总体积为:

当同一气体含液浓度下,相同时间内进入多孔内液体的体积V一定,而滤芯层数增多使得液体穿过毛细管的长度l增加,导致所需运移液体的通道面积下降,通道数目减少,因此层数较多的滤芯内部各层含液量较少,其对气流阻碍较小,通道压降较低,正因如此,层数较多的滤芯在更高气体含液浓度下才会到达饱和状态,进而引起通道压降的跳跃。图9为表观气速0.1 m⋅s-1、相同气体含液浓度0.150 g⋅m-3下不同层数滤芯第三层拆解图,由图可以发现,滤芯层数增多,同一层上的润湿面积较小,即通道数目少,这与上述分析吻合。综上所述,滤芯层数影响通道数目,相同气体含液浓度下,增大滤芯层数会减少液体运移通道的数目,造成各层含液量较低。
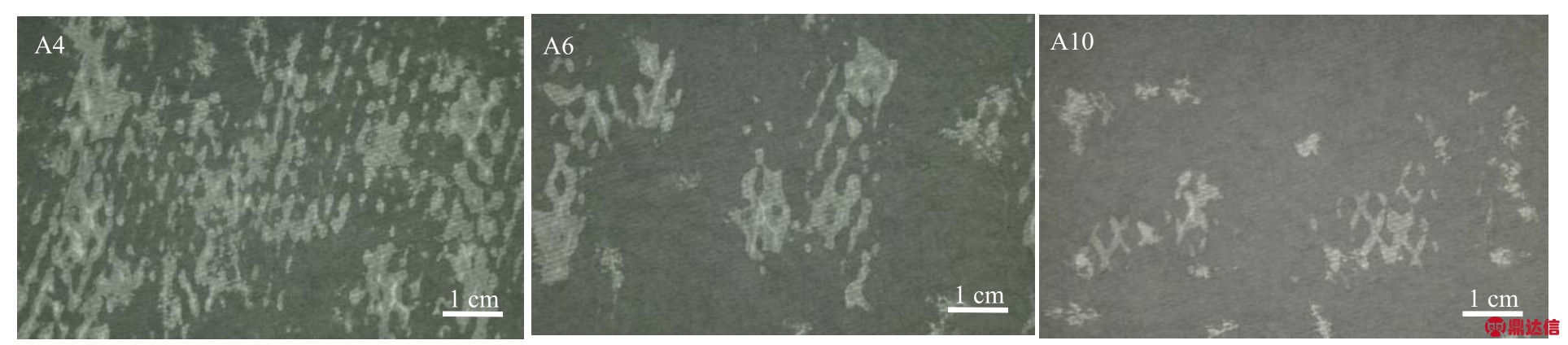
图9 相同气体含液浓度下不同层数滤芯第三层滤材对比图
Fig.9 Comparison of the third layer of filter cartridges with different layers under same oil concentration in gas
文献[24]对比了现场实际工况与实验室滤芯性能测试结果,认为在相同过滤速度下,实验室中所测滤芯过滤性能可等价于现场条件下的过滤性能并且现场实际气体含液浓度普遍较低且长时间处于非稳定状态,实验下的气体含液浓度已完全涵盖工程实际范围,因此气体含液浓度以及滤芯层数对通道压降的影响具有工程适应性。根据实验结果可以为工程实际中不同气体含液浓度工况下滤芯层数优化提供帮助,并且通过滤芯层数以及气体含液浓度建立相应通道压降模型。由于滤芯层数不同导致通道压降急剧升高时对应的气体含液浓度不同,因此通过拟合得到滤芯层数与通道压降跳跃增长时气体含液浓度平均值的函数关系,如图10所示:

其中,climit为通道压降急剧升高时对应的气体含液浓度,称其为极限气体含液浓度,n为滤芯层数。由图8可发现,不同层数的通道压降曲线之间存在近似平移关系,所以将式(7)带入式(4)得到气体含液浓度、滤芯层数与通道压降之间的模型:

将A4、A6、A8滤芯实验时的气体含液浓度带入模型计算得到通道压降预测值,并与实验值比较,如图11所示,预测结果与实测结果吻合性良好,预测误差小于10%。
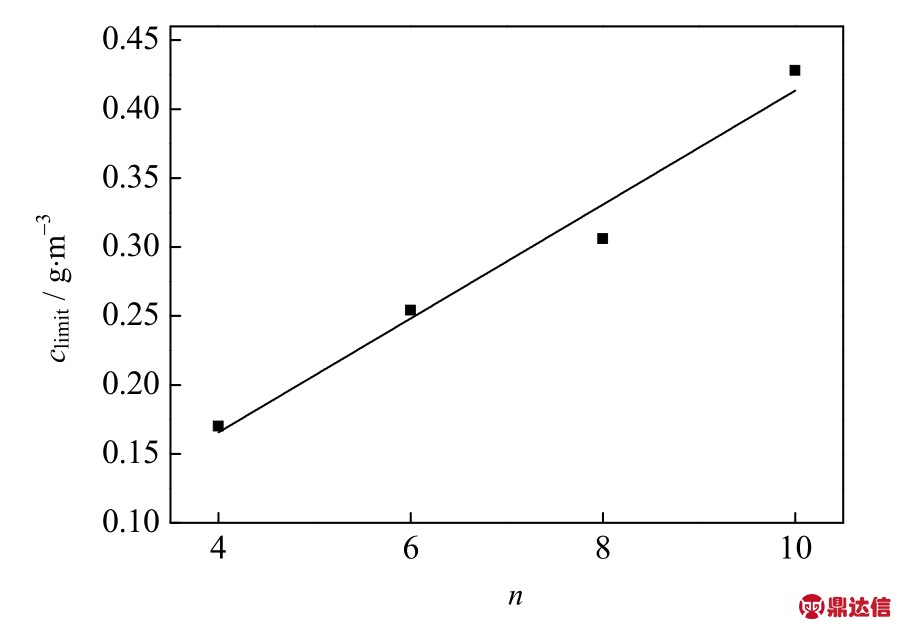
图10 极限气体含液浓度与滤芯层数的关系
Fig.10 Relationship between extreme oil concentrationin gas and filter layers
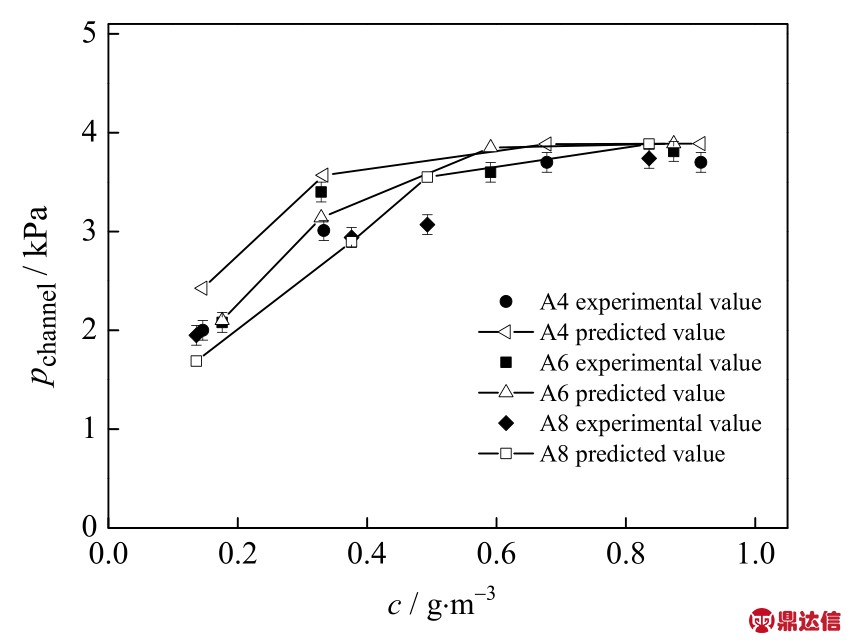
图11 A4、A6、A8滤芯通道压降预测值与实验值对比
Fig.11 Comparison of predicted and measured channel pressure drop values of A4,A6,A8
4 结 论
利用滤芯过滤性能实验装置,研究了气体含液浓度对滤芯压降以及含液量的影响,得到以下结论:
(1) 气体含液浓度对滤芯通道压降影响较大。增大气体含液浓度导致运移液体通道数目增多是通道压降上升的主要原因。同时较高的气体含液浓度可以缩短通道形成的时间,加速通道内液体的运移,增加滤芯各层含液量。
(2) 通道压降随气体含液浓度的增大呈非线性增长,其中气体含液浓度影响的滤材含液量是否达到饱和状态,是判断通道压降急剧上升的关键。当气体含液浓度较低时,滤材含液量未达到饱和状态,通道压降呈线性增长,当气体含液浓度升高使得滤材内部含液量到达饱和时,通道压降急剧升高,当气体含液浓度继续升高时,滤材内部含液量已处于饱和状态,通道压降增长变缓。
7) 主机调速。当主机运行时,根据主车钟令和速度调节曲线计算出给定转速,系统向电喷控制系统发出转速设定指令,由电喷控制系统控制主机调速。