大宽厚比大尺寸空心铝型材因其模具结构复杂,尺寸大,传统的模具设计方法:设计模具—生产模具—试模—修改模具—试模……成本高,周期长,难以适应现代企业精益生产减少浪费的理念。近些年来随着计算机技术的发展,计算机数值模拟仿真技术在模具设计中的应用越来越广泛。黄光法[1]等利用Deform软件对一种大挤压比铝型材的挤压过程进行了数值模拟,通过对比仿真模拟得出带有导流模的平模挤压具有较好的速度分布。林高用等[2]利用Superforge软件对X5214型材的挤压过程进行了模拟,对比分析认为对称倒流模可以获得最佳的速度均匀性,徐卫红等[3]利用有限元分析软件ANSYS对某一高速列车车体材料进行了数值模拟,利用阻流坎和二级焊合室对模具结构进行优化,有效解决了原模具的速度温度分布不均现象,并显著改善了焊合质量。近年来人们更倾向于采用任意拉格朗日-欧拉(Arbitrary Lagrange-Euler,ALE)算法的HyperXtrude对铝合金挤压过程进行仿真研究,陈浩等[4-13]利用HyperXtrude对不同的铝合金型材挤压过程进行了数值模拟,并针对各自型材的结构和模具特点分别提出了各自模具优化方案,并取得较好的优化效果。
利用HyperXtrude软件对一种大宽厚比薄壁空心铝型材的挤压过程进行了稳态模拟仿真,分析了模具内金属的流动规律,根据初始模具型材速度分布不均、变形量大的特点,提出采用调整导流孔大小、设置倒流孔、开设引流槽和调整工作带长度的综合优化方案来平衡金属流动速度,并分析了模具优化前后型材出口温度和应力分布变化。
师:你真了不起,用图形就直观地说明的这三个三角形不可能同时相似,画图有时是一种非常好的方法,当然前提是图形要画得比较准确,这样才能给我们一个初步的判断,直观判断之后我们还要论证.那下面请你来论证一下,行吗?
混凝土面板堆石坝在绕坝渗流研究及数据分析中基本采用过程线分析、圈套图法等。传统分析方法仅对单一孔内水位进行分析,孔位之间、库水位等之间的联系薄弱。本文以线性相关模型为工具,分析孔内水位相关性及与库水位的相关性,通过连通性试验方法。
1 初始模具结构设计
图1为6005-T6铝合金型材的二维截面和三维立体结构图。从图1可知,该型材尺寸为宽厚比较大的复杂多孔型材,最宽处达到了415.7 mm,横截面积为3517.7 mm2,且壁厚不均匀,上壁和中间筋板壁厚最薄只有2.3 mm,下壁厚3.8 mm,最厚处壁厚6.5 mm,大约是最薄处的3倍。该型材的挤压成型模具设计复杂,若采用传统的反复修模—试模的设计方法成本高,设计周期长。因此本设计采用基于HyperXtrude数值模拟仿真的设计方法,减少试模次数,甚至实现零试模。初始模具的设计如图2所示,挤压成型模具主要有上模和下模组成,采用型材中心和模具中心重合的方法设计,上下模的尺寸都为φ650 mm×150 mm。上模的结构主要有分流孔、分流桥、和模芯组成,为了较为合理的分配金属流速,上模开设了6个分流孔,采用中间孔偏小,两端孔偏大的设计来抵消挤压过程坯料中间流速过快的问题。分流桥宽度为32 mm,分流桥焊合角为40°。下模由模孔和焊合室组成,焊合室深度为50 mm。模具初始工作带长度为7 mm。
其次,优化数学史渗透方法。数学教师在数学课堂中渗透数学史时,要注意方法的选择,从而提升渗透效果。比如,教师可以引导学生阅读一些有关数学史的读物,这有利于学生全面的掌握数学史的有关内容并让其感受到数学史的博大精深;此外,教师还可以根据学生的兴趣爱好,运用学生喜欢的教学方式。比如在对数学家华罗庚进行说明时,可以选它的画像、故事、传记以及他的名言“聪明在于学习,天才在于积累”等内容来有机渗透教学,丰富学生学习数学的情感,激发学生热爱数学史的思想情操。

图1 型材的二维截面和三维立体图
Fig.1 Two-dimensional section and three-dimensional
stereo of profiles
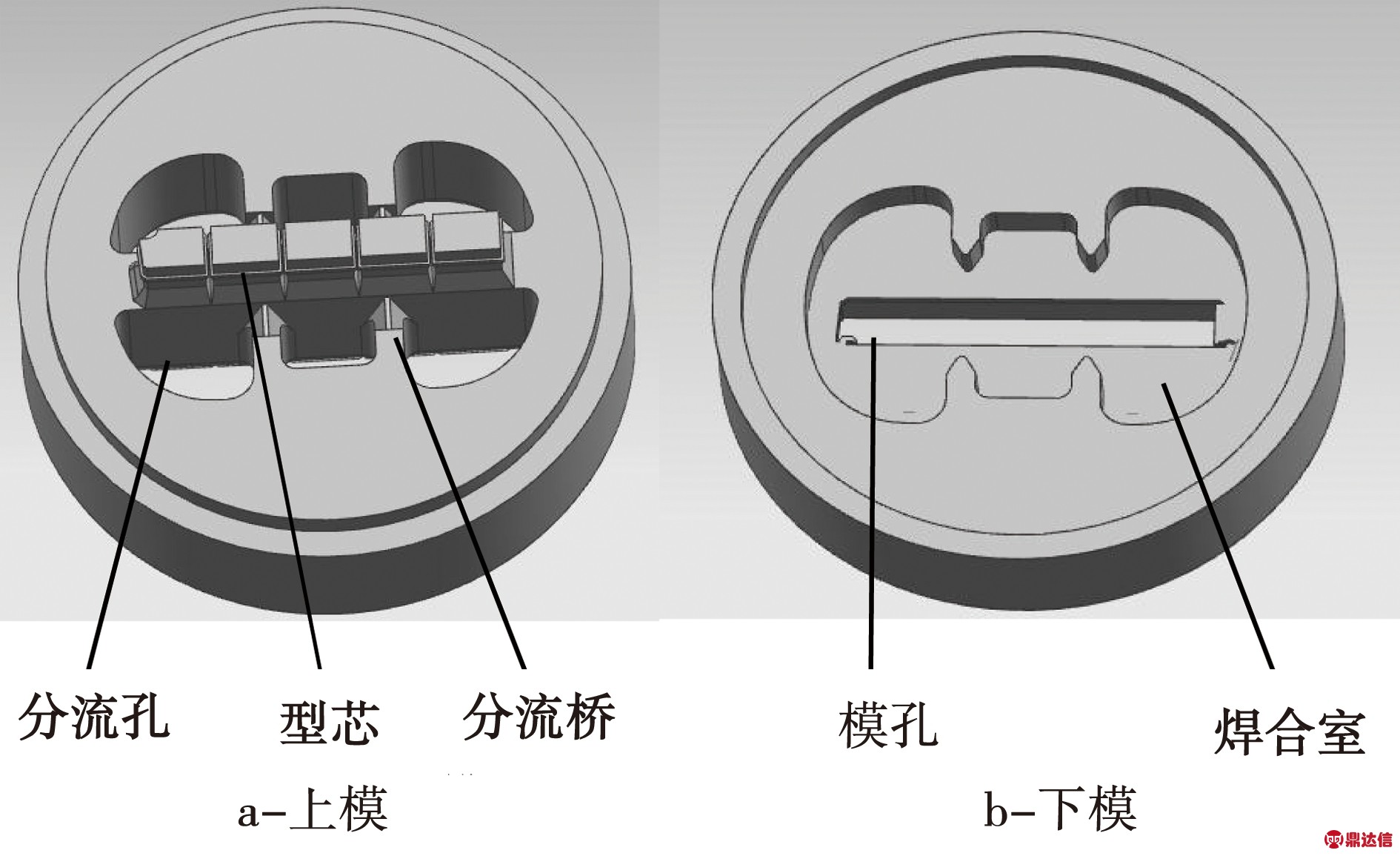
图2 初始模具结构设计
Fig.2 Initial die structure
2 初始模具仿真分析
将模具的三维实体模型导入到Hypermesh中进行网格划分,为保证仿真结果的准确性,型材出口和工作带的网格类型为三棱柱网格,最薄处只有2.3 mm至少应该布置5层网格,因此设定工作带和挤出型材处网格的大小为0.4 mm、总数为55.8万个。其余挤压锭、导流孔和焊合室的网格类型为四面体,网格数为192.3万,总体网格数为248.1万,划分网格后的型材挤压模型如图3所示。在HyperXtrude软件中设定挤压仿真的参数如表1所示,型材模具出口处的金属流动速度越不均匀,则型材的扭拧、波浪、弯曲等变形越严重,将型材各处出口流速的均方差作为衡量出口流速均匀性的指标,流速的均方差Sdv公式为:
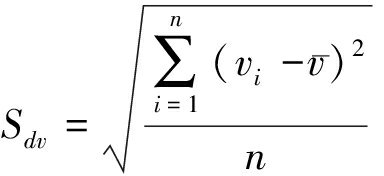
(1)
式中:
1.一些饲料生产企业追求高蛋白质、高产出的配合饲料,致使饲料中蛋白质含量过高,而即将断奶的仔猪对饲料中蛋白质的消化能力差,较多的饲料蛋白质进入肠道后发生腐败,消化酶活性下降,肠黏膜的吸收功能降低,导致消化不良和腹泻。肠道内未被消化吸收的蛋白质或未被吸收的氨基酸不仅会造成肠道内微生物菌群失调,也给致病性大肠埃希氏菌创造了良好的增繁环境,其产生的毒素被肠道吸收,导致水肿病的发生。
vi—节点i处的金属流动速度;
n—所选的节点数目;
位于大漠戈壁的西北油田采油三厂S86卸油站,是一座连续15年被共青团中央授予“全国青年文明号”的基层井站。
所有节点的平均流速。
表1 仿真模拟参数
Table 1 Parameters of simulation experiment

挤压比挤压速度/(mm·s-1)挤压方式铝锭长度/mm铝锭直径/mm铝锭温度/℃模具温度/℃挤压筒温度/℃88.71正向1 200600480450400
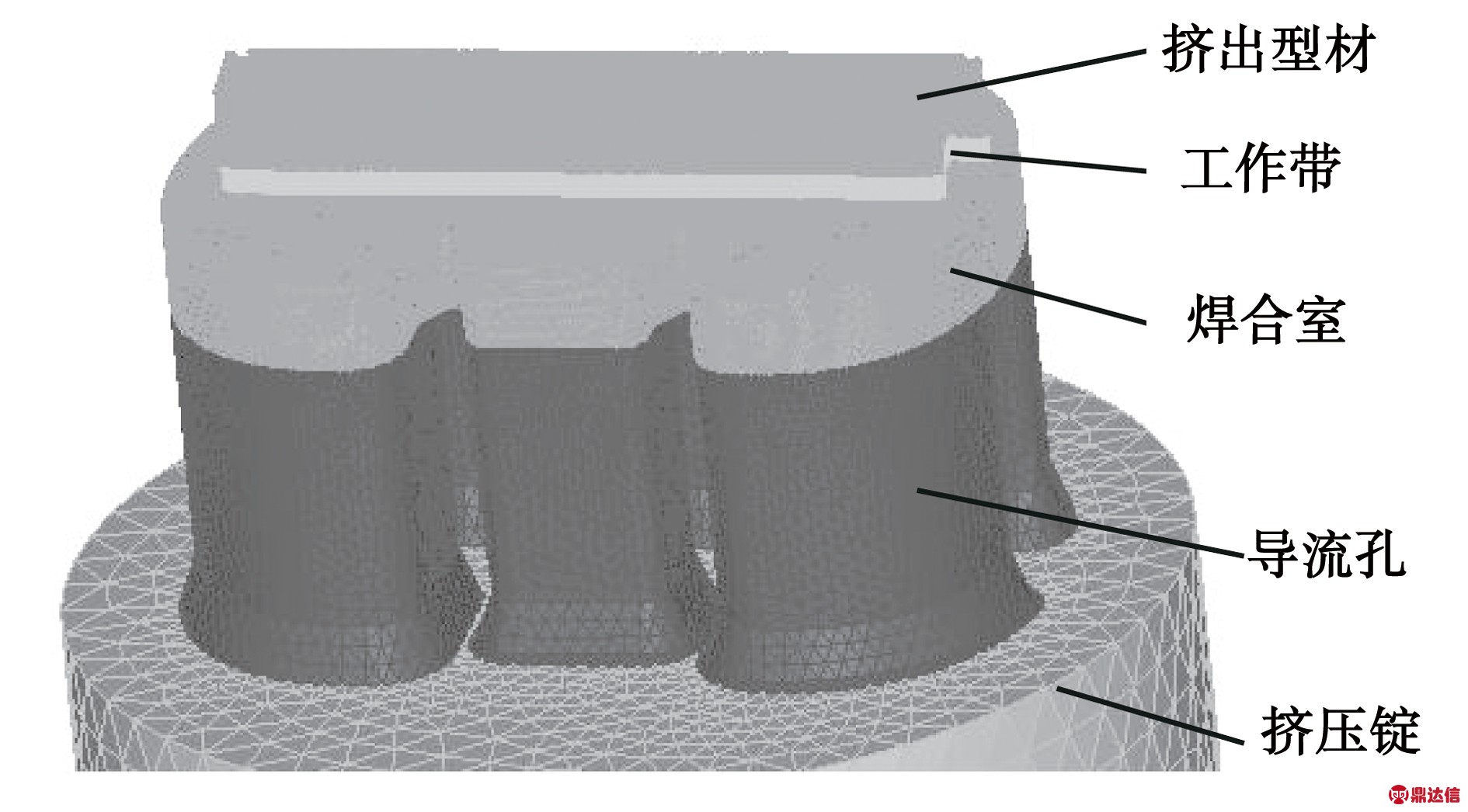
图3 计算机仿真模型图
Fig.3 Diagram of computer simulation
为方便计算,选取了型材在不同壁厚不同位置的共57个节点,其分布如图4所示,结构复杂的部位取点多一些,结构简单的部位取点少一些。图5为初始模具挤压过程型材出口的变形、速度分布云图。由图5可知,由于下底面的厚度为3.8 mm,远大于上底的流出速度。下底面的厚度2.3 mm,在工作带相等的情况下,下底面最大速度达到了146.3 mm/s。型材内部加强筋处,仅靠焊合室的材料流动补充,材料流出明显不足,流出速度最低只有26.8 mm/s,最大速度和最小速度差达到了119.5 mm/s,计算初始模具的挤出的速度均方差Sdv=42.8 mm/s。在如此大的速度差异下型材出现了较大的变形差异,下底面相对于上底面和中间加强筋处的综合变形量达到了47.7 mm。速度和变形不均将会使型材产生严重扭拧变形,甚至塞模不能正常挤压生生产。因此必须对原始模具进行结构优化设计,均衡分布型材出口速度,减少变形,才能生产出合格的产品。

图4 金属流速测量点
Fig.4 Measurement points of metal velocity
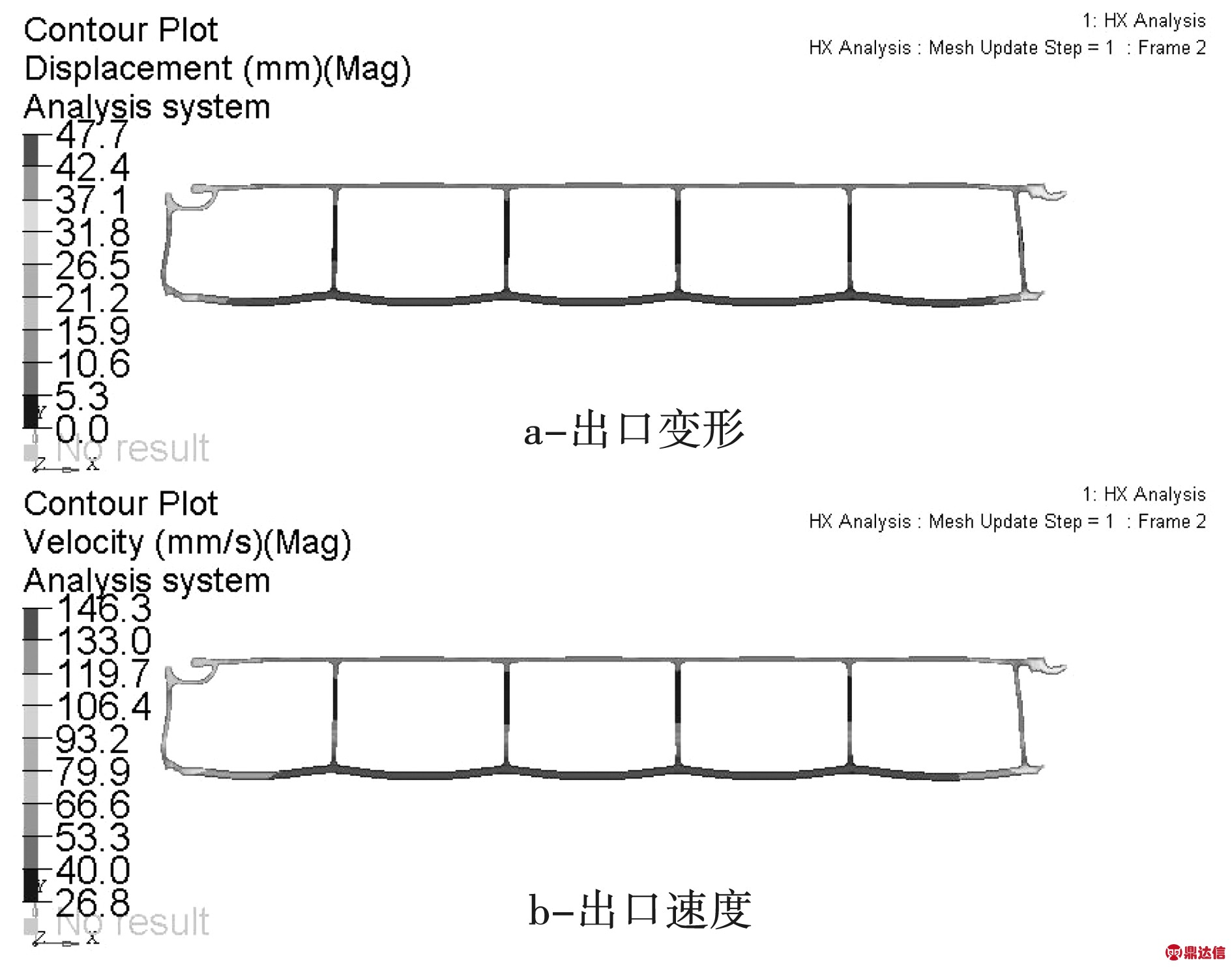
图5 初始模具型材出口的变形、速度分布云图
Fig.5 Cloud diagram of deformation and velocity
distribution at the exit of initial die profile
3 模具结构优化设计
造成型材出口速度分布不均的主要原因是型材的壁厚分布不均,厚壁处材料较薄壁处材料容易流出。因此优化设计的主要工作就是调节模具内金属的流动速度,使其流动更加均匀。通过多次仿真模拟,提出了采用调节导流孔大小和位置、设置阻流坎、开设引流槽等方法先使模具内的金属流速趋于均匀,最后通过调节工作带对型材的出口流速进行微调的方法来优化模具结构,具体优化过程如下。
3.1 调节导流孔
造成型材出口速度分布不均匀的一个重要因素就是导流孔的速度分布不均匀,图6为原始模具的导流孔的速度分布图。图6可以看出,下边导流孔的平均流速为9.2 mm/s,上边导流孔的平均流速为2.7 mm/s,流速比达到了3.41,超出型材上下边的宽厚比1.65一倍以上。因此,模具结构优化先从导流孔开始,调整方案为将下边对应的导流槽的周边向内减少10 mm,横截面积变为原来的0.67倍(2/3),并将导流孔的位置整体向远离中心的方向平移10 mm,调整后的上模结构如图7所示。对导流孔调整完后的模具重新进行挤压仿真得到的分流孔的金属流量分布云图(图8)。从图8中可以看出,下边对应的导流孔的金属流速基本没有变化,但上边对应的导流槽的金属流速增加了,平均流速达到了5.51 mm/s,上下导流孔的流速比减小到1.63,基本与型材的上下边的宽厚比相等。

图6 初始模具分流孔的流量分布云图
Fig.6 Flow distribution cloud of initial die shunting hole
图9为调整分流孔后模具出口的型材变形和速度分布云图。与原始模具相比,调整导流孔大小后,型材出口的速度差异有所减小,由b图可知最大速度从146.3 mm/s减少为132.6 mm/s,最小速度从26.8 mm/s提升到38.0 mm/s,速度均方差减小为Sdv=30.3 mm/s,由图9a可知最大变形量减少为36 mm,但变形量仍然较大,壁厚值较大的下边和上边的左右端点处速度和变形仍然较大,壁厚差异仍然是引起变形的主要原因,因此需要对模具进行进一步优化。
加速推进潜山市内旅游区域公路与各地高速、铁路、国道的对接,全力打造开放性的旅游交通网络,并加快环天柱山旅游公路和龙潭--万涧旅游公路拓改、积翠谷索道等项目的实施,通过“串点成线”打造全域旅游通道,优化城镇与景区、景区与景区间的交通衔接。
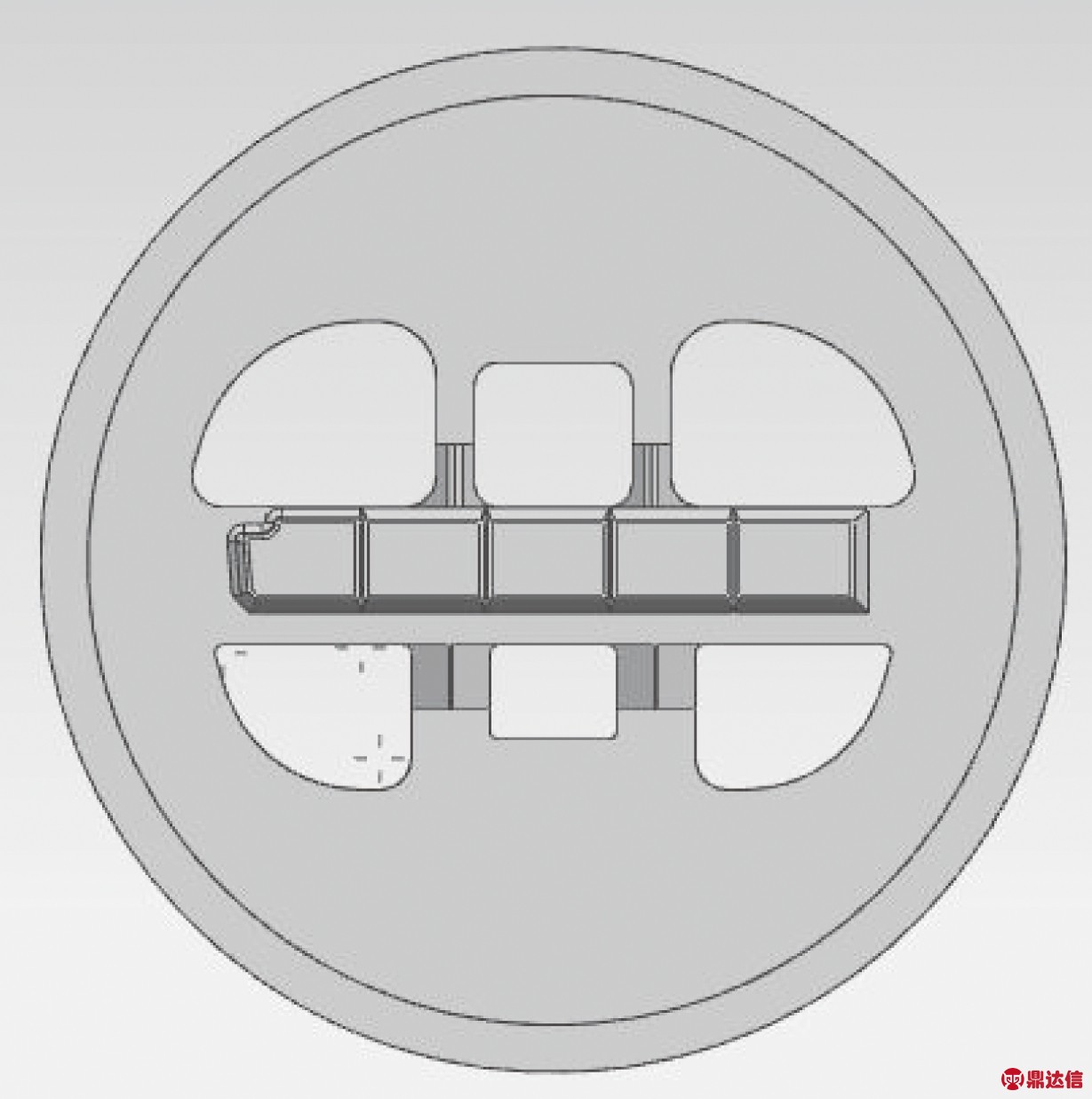
图7 调整导流槽后的上模结构图
Fig.7 Structure diagram of upper die after
adjusting flow guide groove

图8 调整后分流孔的金属流量分布云图
Fig.8 Cloud diagram of metal flow distribution
of adjusted shunt hole
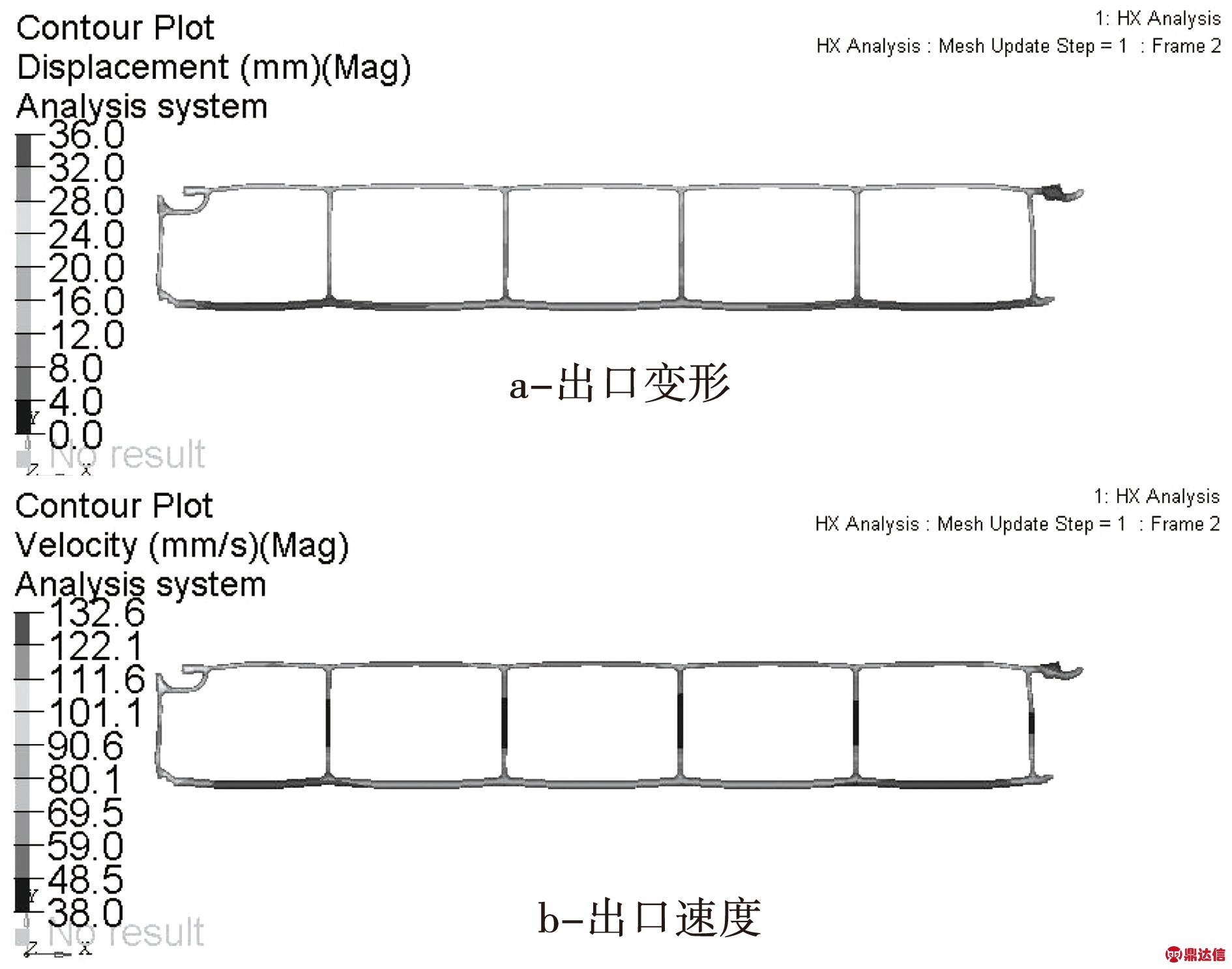
图9 调整分流孔后型材出口的变形和速度分布图
Fig.9 Distribution of deformation and velocity at
profile exit after adjusting shunt holes
3.2 设置阻流坎
通过上面的分析可知,型材壁厚的不均匀是引起型材变形的一个重要因素,调节壁厚引起的速度差异的另一种有效方法是在壁厚处设置阻流坎,通过阻流坎对金属流的阻碍作用来调节金属的流动速率,但过大阻流坎的高度使其强度不足,影响模具使用寿命;另外过大的阻流坎高度对金属流动的扰动较大,使金属产生过大的变形热,温度升高,造成型材温度不均匀,甚至过烧,影响型材的力学性能。本设计的阻流坎设定如图10所示,阻流坎设在壁厚较厚的型材下边和上边的左右端点处,位置为偏离工作带1.5 mm,宽度为6 mm,下边阻流坎的高度为6 mm,上边左右端点处的高度为4 mm。重新进行仿真后型材截面出口的速度和变形分布云图如图11所示。从图11可知,设置阻流坎后,型材出口速度进一步均匀化,型材出口速度的最大值减少为119.9 mm/s,最小速度还是发生在中间筋板处,因为阻流坎的阻流作用筋板处金属流动更加不充分,最小速度减小为32.9 mm/s,速度均方差减少为Sdv=20.7 mm/s,变形量减少为30.2 mm,模具结构还需要进一步优化使出口速度更加均匀,减少变形。

图10 设置阻流坎后的下模结构
Fig.10 Lower die structure after blocking
bucket being set up
3.3 开设引流槽
增设阻流坎后型材出口速度不均匀和变形的主要原因是中间筋板处壁薄,且供料不足,速度低,只有32.9 mm/s。为了减小型材的变形量,应在上模中间筋板处开设引流槽(如图12所示),引流槽宽度为14 mm,从引流孔直达筋板工作带,增加筋板工作带处的金属材料供应,提高筋板处的金属流动速度。图13为开设引流槽后的仿真的速度和变形云图。从图13可知,开设引流槽后型材中间筋板处的最小金属流速由原来的32.9 mm/s提高到51.5 mm/s,型材断面的最高流速由原来的119.9 mm/s降到108.1 mm/s,截面速度均方差减少到11.1mm/s,筋板工作带附近开设导流槽促流后效果明显,但出口流速不均匀和型材变形量仍然不小,需要对工作带的各段长度进行调整,对流速和变形进行微调。

图11 设置阻流坎后型材出口的变形和流速分布云图
Fig.11 Cloud image of deformation and velocity distribution
at profile exit after blocking bucket being set up
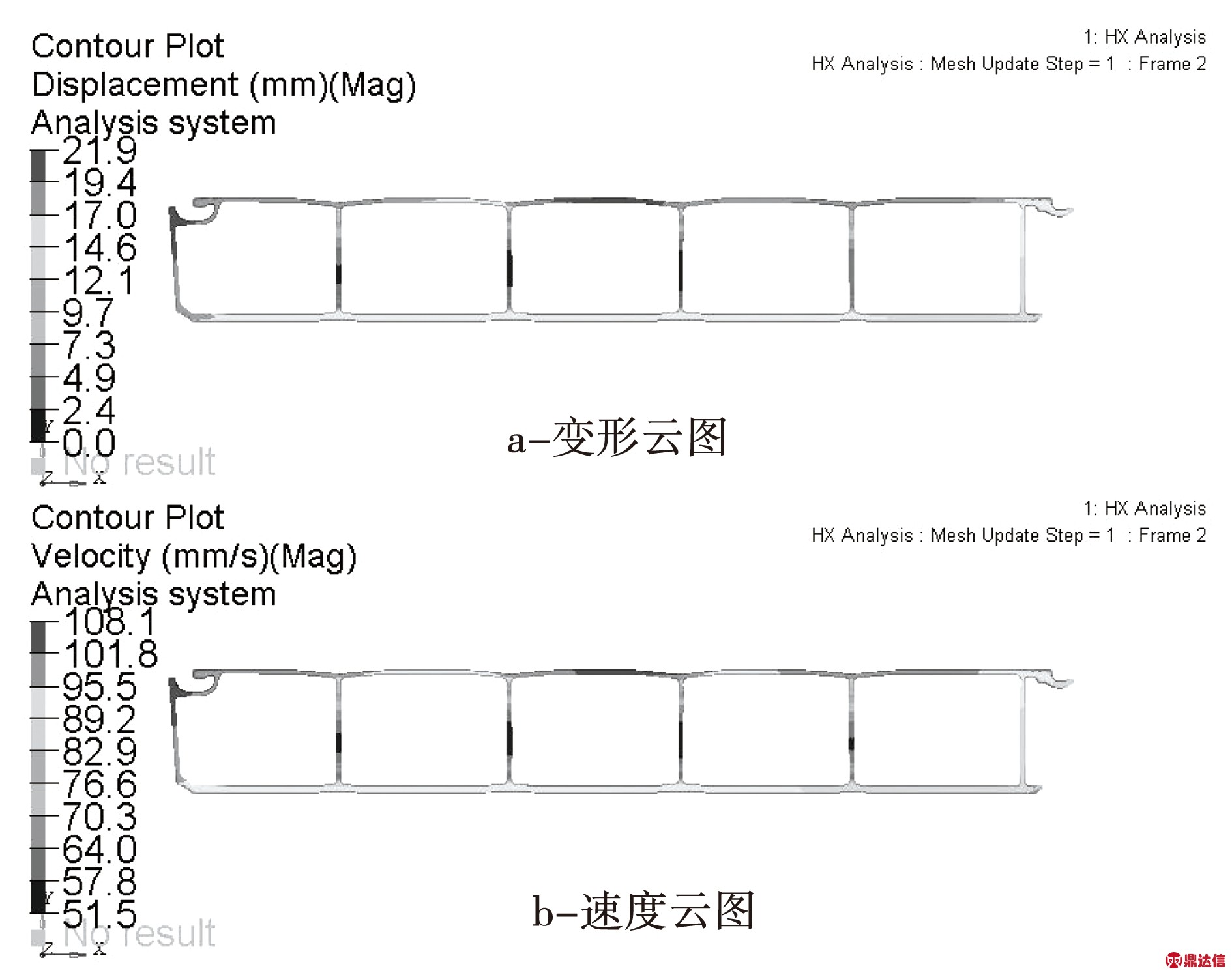
图12 开设引流槽后的上模结构
Fig.12 Upper die structure after drainage
groove being set up
3.4 调整工作带长度
加强筋处壁薄且供料困难,金属的流动性差,工作带长度短;下底面和上底面左右两端的壁厚较大,金属容易流动,工作带较长。经过多次仿真模拟将原来的统一的7 mm长工作带调节为如图14所示的工作带长度分布。调整工作带后型材模具出口的速度和变形分布云图如图15。由图15可知,通过对工作带的调整改进了型材模具出口的速度均匀性,由图15b可知最大速度降为93.9 mm/s,最小速度提高到85.2 mm/s,速度均方差减少到2 mm/s。由图15a可知型材出口最大变形量为11.0 mm,最小变形量为6.2 mm,相对变形量只有4.8 mm,型材变形大幅减小,质量得到较大改进。
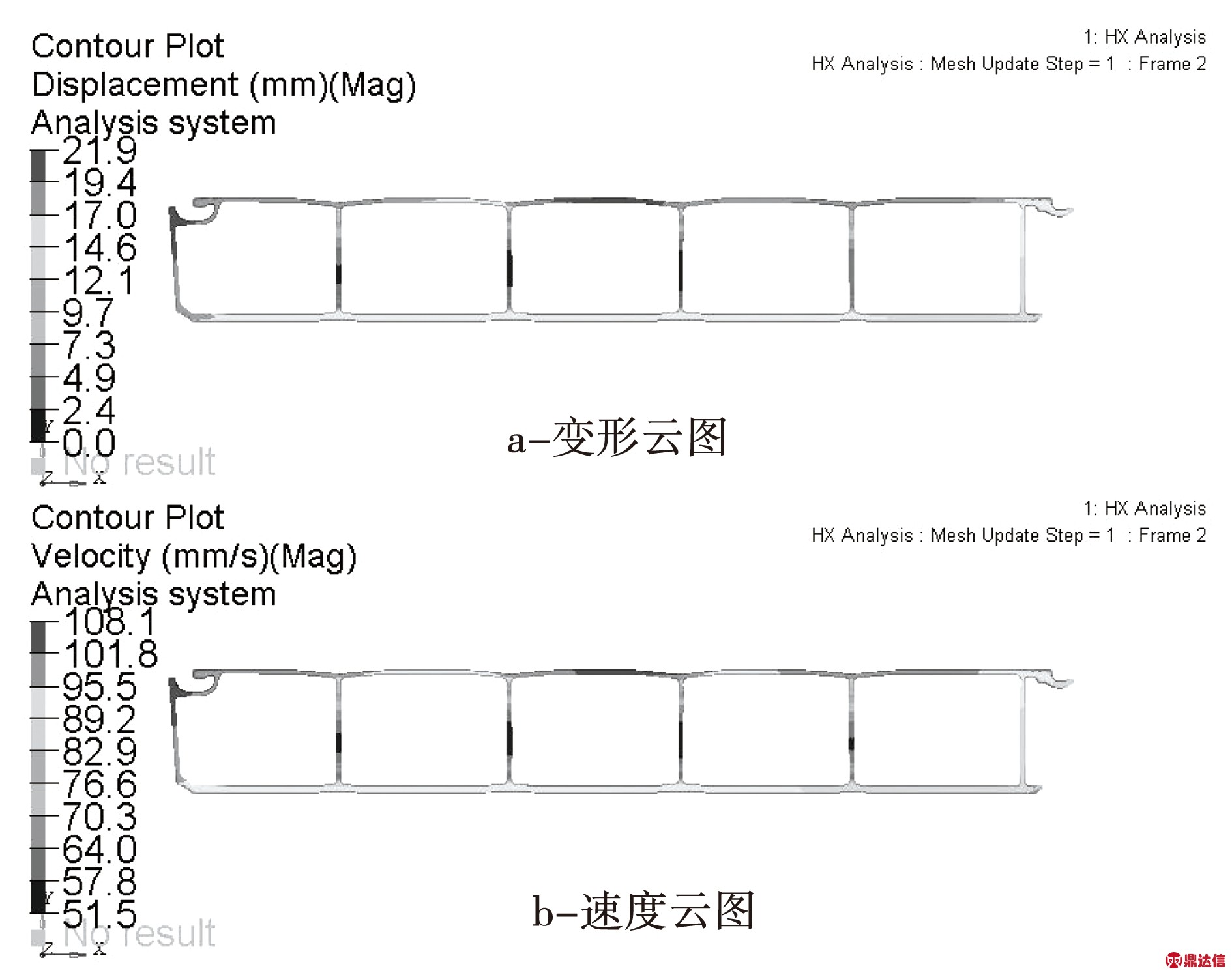
图13 设置引流槽后型材出口的变形和流速分布云图
Fig.13 Cloud image of deformation and velocity distribution
at profile exit after drainage groove being set up
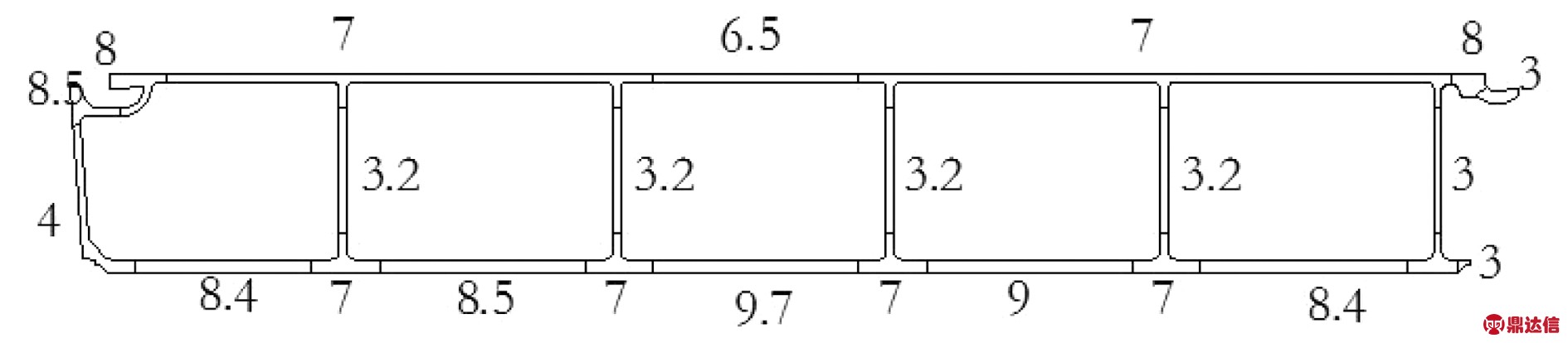
图14 优化后的各部分工作带长度
Fig.14 Optimized length of working belts for each part
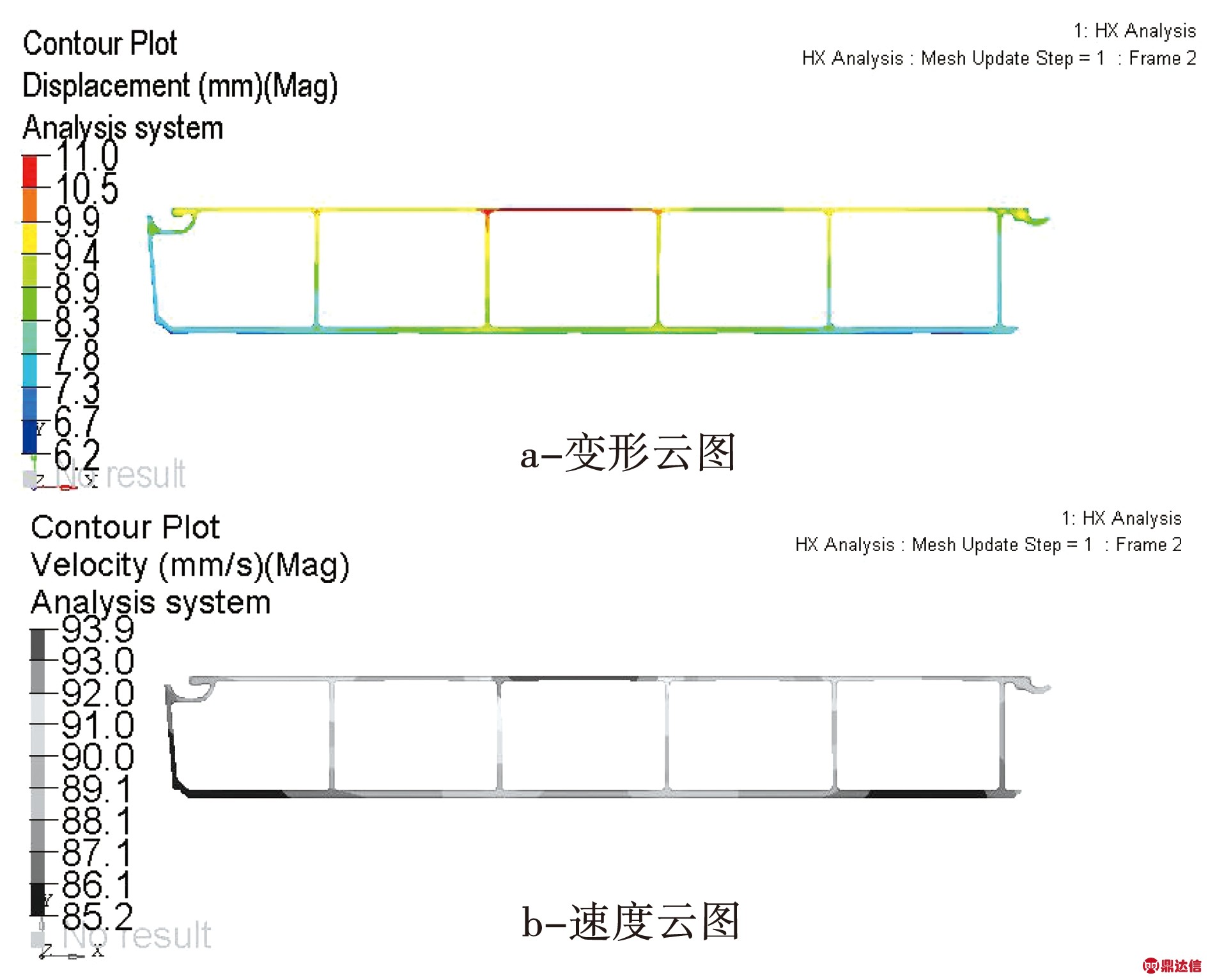
图15 调整工作带后型材出口的变形和速度分布云图
Fig.15 Cloud image of profile exit deformation and
velocity distribution after working belt being adjusted
4 优化前后对比分析
4.1 温度场对比分析
型材的出口温度分布对型材表面质量和随后的热处理会有较大的影响,图16为模具优化前后型材模具出口的温度场分布。由图16可知,模具结构优化后型材的出口温度分布更加均匀,出口温度差从优化前的34.5℃减少到26.6℃,且出口温度的均匀性更好,温度均方差由原来的8.52℃减小到6.43℃。这是因为通过调节导流孔增设阻流坎、开设引流槽和调整工作带长度,使金属在模具内的流动更加均匀,速度不均匀引起的变形热大量减少的结果。
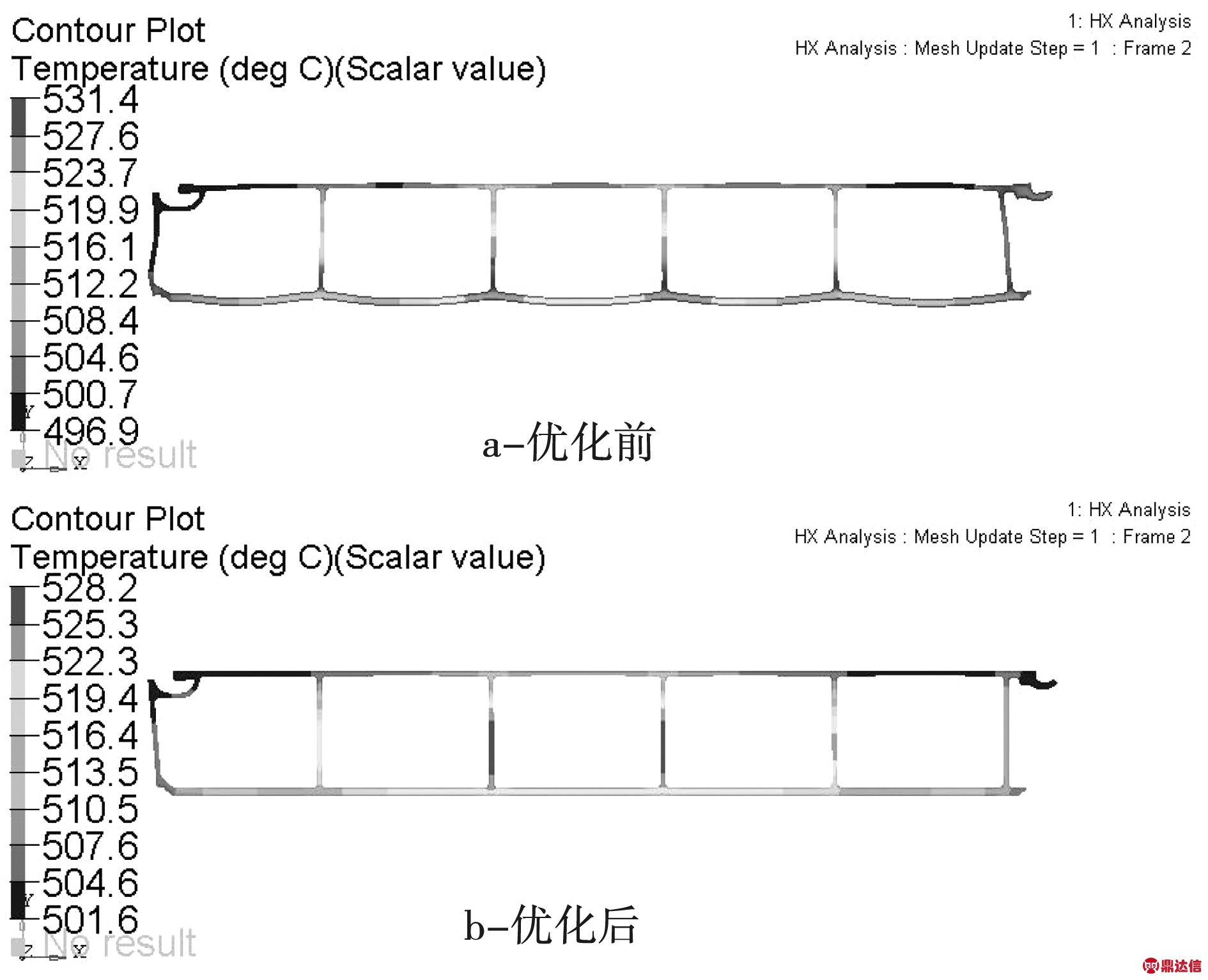
图16 模具优化前后温度场的对比
Fig.16 Temperature field comparison before
and after die optimization
4.2 应力场对比分析
图17模具结构优化前型材出口最大应力为35.8 MPa,模具结构优化后型材出口应力明显减小,最大应力减小到13.6 MPa,而且分布更加均匀。这是因为模具结构优化后,模具内金属的流动更加均匀,金属的变形和应力更加均匀,对提高型材质量和模具寿命有重要意义。
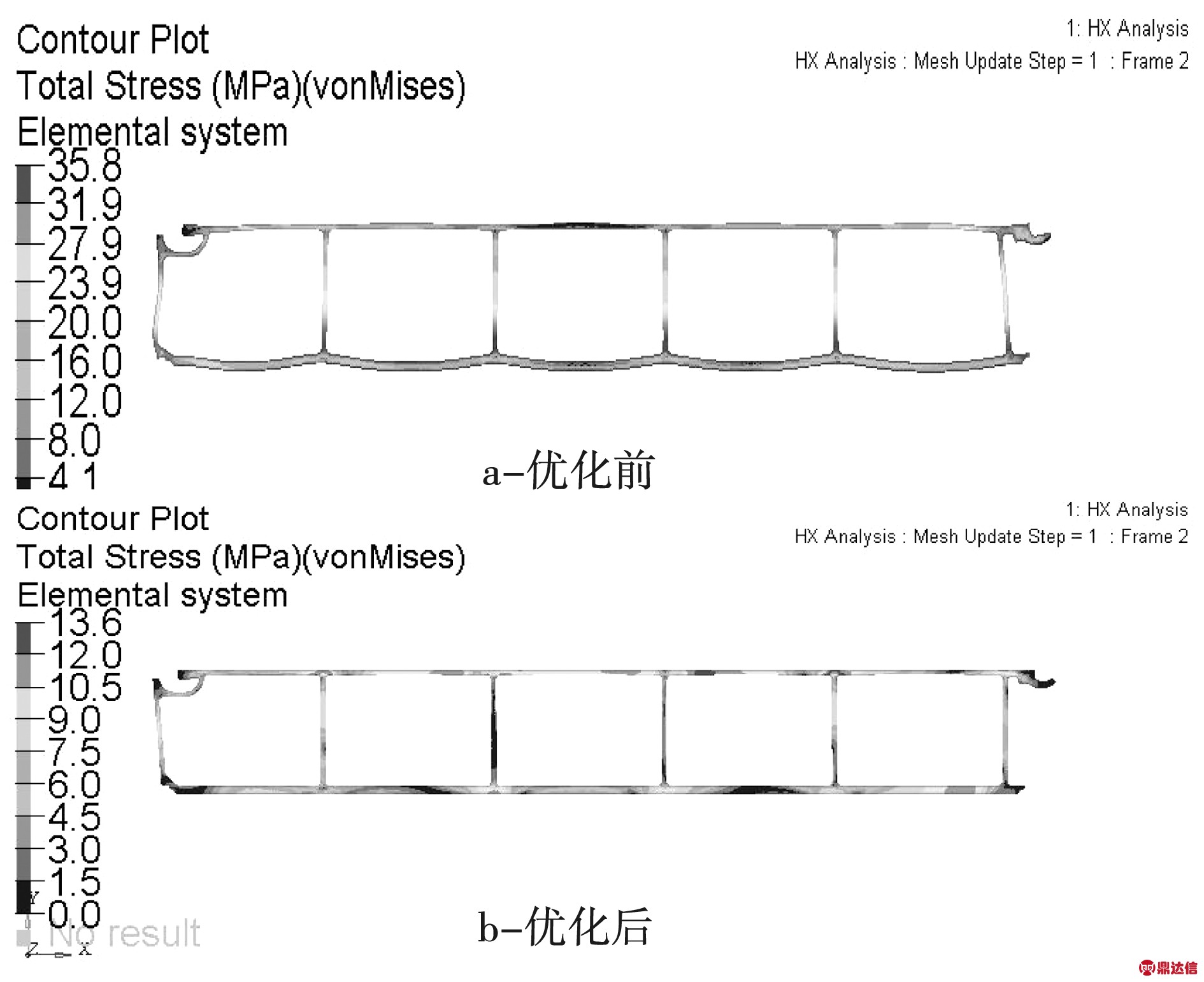
图17 模具优化前后应力场对比
Fig.17 Stress field comparison before and after die optimization
4.3 挤压压力对比分析
图18为模具优化前后挤压力云图的对比,模具结构优化后最大挤压力从480.4 MPa下降为457.5 MPa。这是因为模具结构优化后,材料在模具内的流动更加均匀顺畅,使最大挤压力有所减少。
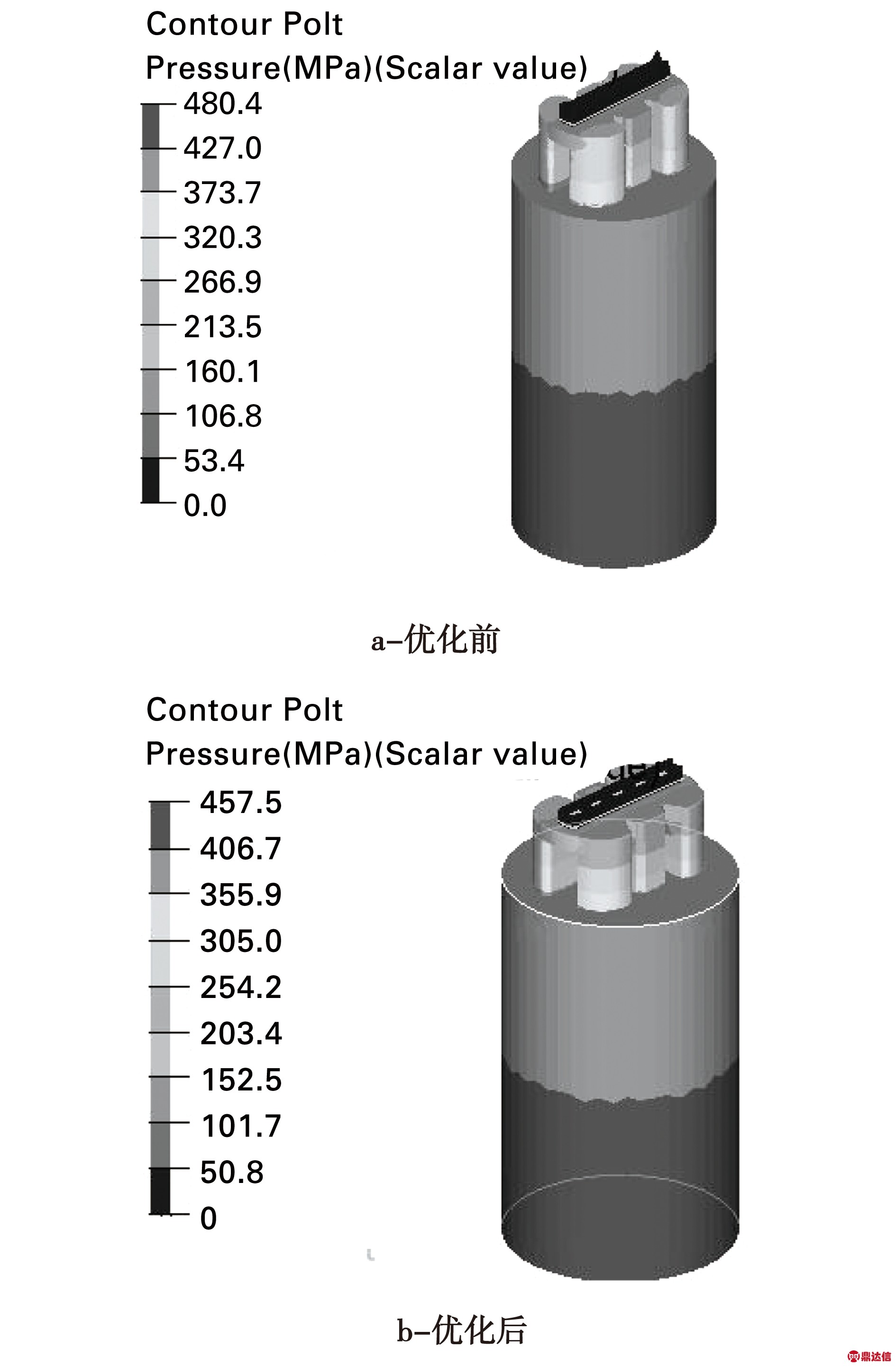
图18 模具优化前后挤压压力对比
Fig.18 Comparison of extrusion pressures
before and after die optimization
5 验证实验
根据优化后的结构参数生产的模具在90 MN正向挤压机上按照模拟实验的工艺参数进行生产,生产出的型材产品如图19所示,模具出口型材流速均匀,没有出现大的扭拧、波浪、弯曲等缺陷,峰值时效后的强度、伸长率、硬度等参数均符合要求。

图19 优化参数后的模具挤压出的型材
Fig.19 The profile extruded by the die after
the parameters being optimized
6 结 论
采用基于ALE算法的HyperXtrude软件对大宽厚比空心铝型材的挤压过程进行了数值模拟,得到了挤压过程的速度场、变形场、温度场、应力场等的分布,通过以出口速度均匀化和减少变形为目标对初始模具进行了优化,并对优化前后的模具方案进行了对比分析,得出以下结论:
1)通过挤压过程的数值模拟使挤压过程中模具内的金属流动情况表现得更加直观,方便设计者针对不同的流动情况采取不同的优化措施。
园路及风景园林内土建部分施工完成后要进行养护,养护的主要方式是适当洒水并覆膜保护,防止水分蒸发过快,导致开裂现象发生;另外在景观小品养护上,要定期巡视,做到每天对指示牌、亭台、楼阁等进行卫生清理,休闲台及板凳等做到清洁卫生;发现垃圾桶损坏或生锈应及时刷油漆。
2)对于变形量较大的型材单纯采用调节导流孔,设置阻流坎、开设引流槽、调整工作带中任一种方法,都不能够使型材获得较均匀金属流速。
3)通过调节导流孔大小和位置、设置阻流坎、开设引流槽对型材的金属流速进行初粗调整,再对工作带长度进行微调,能有效调节模具内的金属流速,减少变形,提高型材质量。
4)对比分析优化前后的温度场和应力场分布可知,模具优化后,金属材料的流动更加均匀流畅,温度和应力最大值都有减小,而且分布更加均匀。
5)通过实际生产验证,仿真结果和实际生产验证数据基本一致,显著减少了模具试制时间和生产成本,提高了模具设计效率。