0 前言
一模多孔挤压工艺在我国方兴未艾,特别近几年来,广大专家、学者和工程技术人员对此进行了大量的研究和探索。一模四孔挤压模是针对半空心型材而设计的一款一模多孔挤压结构,可在一套模具中同时同步挤出4根相同型材。这种模具是在挤压机装备趋于大型化条件下充分利用和发挥挤压机的潜能而大幅度提高挤压机效率的一种结构改良,更是一种节能、节地、节约成本的新型技术[1]。当今行业的一模四孔挤压模主要是针对空心型材,针对半空心型材的一模四孔挤压模却鲜见。而半空心型材是实践中常见的产品,可有效缓解“小机吃不完,大机吃不饱”的结构性矛盾,采用一模四孔甚至一模更多的孔数是有必要的。本文结合实际例子,介绍一种专门针对半空心型材而采用的一模四孔保护式分流模结构,供同行参考,同时也为企业淘汰产能落后的小型机台提供思路和方法参考。
1 型材断面分析与模具结构
图1所示为一款典型民用建筑门窗型材。其断面面积为291 mm2,断面形状具有对称性,含有窄长悬臂的半空心部位和完全闭合的空心部位。在挤压中,半空心部位的悬臂是最危险的,极容易发生断裂,从而造成模具提前失效。因此,模具设计的重点是针对半空心部位[1]。
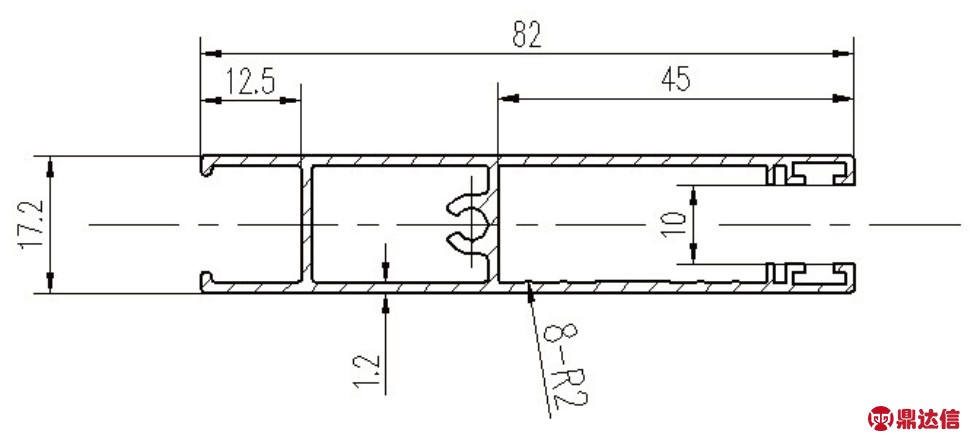
图1 型材断面示意图
采用一模多孔模是需要经过计算和对比来确定的。一方面要综合考虑实现挤压的设备条件、设备的效率和成品率。这里要注意的是,采用的机型越大可采用的模孔数可以越多,设备的效率会越高,成本越低,但成品率会相应降低;另一方面必须考虑模具设计与制造难度以确保挤压的同步性和可操作性。综合考虑,以挤压系数在60~80 范围内、一模四孔较为合适。
在一模四孔中,由于模芯的增加,无法实现像单孔模一样将模芯置于挤压筒的中心区域并使模芯的受力在四周处于平衡状态。因此,这种模具的模芯会受到压力差形成的附加力的作用,在挤压过程中产生弹性偏移,因而容易产生拉丝、起筋、壁厚偏差严重等问题[2]。同时,模芯的增加也增加了制造难度和误差,给实现挤压同步性增加了困难。为了消除这些挤压缺陷,在一模四孔挤压模中,针对危险的悬臂部位采用一种模芯保护结构,就是在上模设置一种“假模芯”,并借助分流桥将悬臂保护起来[3]。“假模芯”并不进入下模的模孔里与下模形成配合。在挤压过程中,由于“假模芯”,悬臂承受金属压力的面积将大幅减小,同时由于分流桥的遮挡保护,悬臂不直接承受金属的冲击压力;即使在分流桥向下发生挠曲时,“假模芯”因为应力间隙也不会触及下模的悬臂,因而改变了悬臂的受力状态并降低了悬臂受力,从而提高了悬臂的强度。模具结构如图2所示。
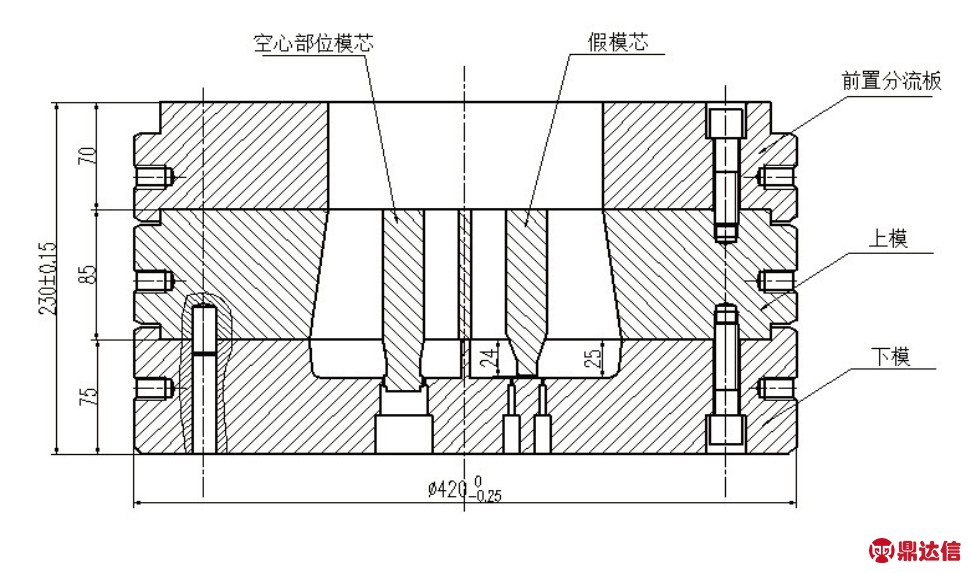
图2 模具结构示意图
2 模具结构参数
根据上述分析以及针对最危险的悬臂部位的保护设计,对模具进行结构参数设计。该设计主要包括模孔的布置、前置分流板的结构、分流孔参数的确定和下模焊合室的设计,具体分析如下。
2.1 模孔的布置
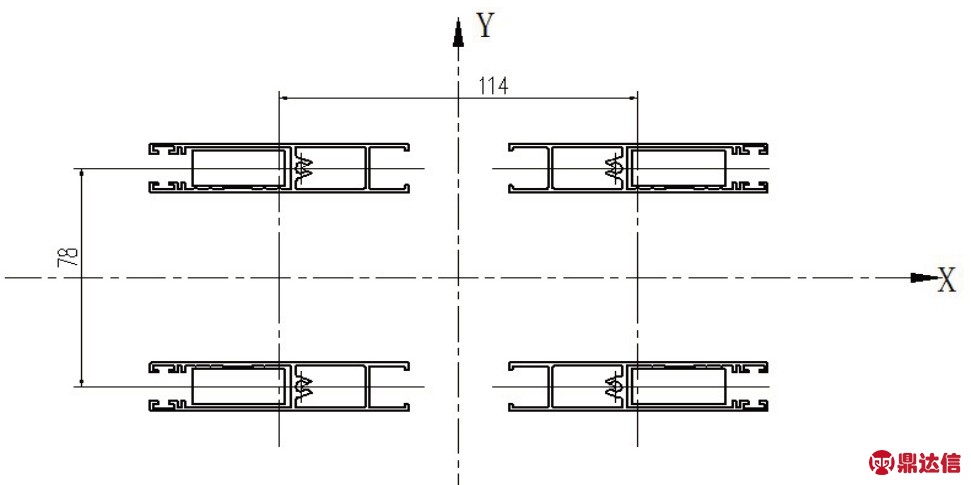
图3 模孔布置示意图
模孔的布置必须考虑能充分利用挤压机的能力、发挥挤压筒的潜能、尽可能避免使模孔过于靠近挤压筒内壁,因为这不利于金属的成形同时将会使模具的尺寸增大[4];同时尽可能使模孔间处于对称排列,这有利于挤压过程中各处金属流速容易趋于一致以及金属流速易于调整和均衡。而对于半空心的窄长悬臂,模孔也应远离中心布置,以减小悬臂的受力。模孔布置如图3所示。
1.1 调查对象 调查数据来源于北京市妇幼保健管理信息系统助产机构上报数据,所有北京市常住人口孕产妇均纳入监测。按照国家卫生计生委关于加强母婴安全保障工作的通知(国卫妇幼发〔2017〕42号)文件,本研究中严重高危妊娠包括橙色及红色高危。
2.2 前置分流板
传统的分流模是由上模与下模组成。但对于在大机台上的一模多孔模具,在强度足够的条件下,上模厚度过大将增加模具的制造难度并降低模具热处理时的淬透性。更重要的是,增设前置分流板可以使金属在进入上模前以较大的分流比对金属进行预分配,这将有利于实现挤压的同步性和降低挤压力。在模孔布置确定的前提下进行前置分流板分流孔的设计,可使左右或上下各两个模孔的金属供应独立开来,其结构如图4所示。
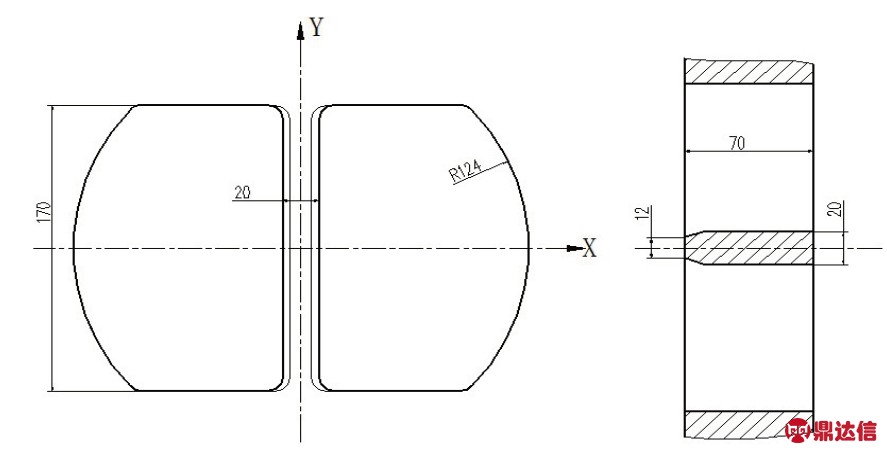
图4 前置分流板结构示意图
2.3 上模分流孔的确定
分流孔的确定包括分流孔的布置、面积的大小计算,更重要的是确定分流孔间的面积关系以及“假模芯”的尺寸[5]。分流孔的布置可以有多种形式。在设计过程中,可借助CAD 软件根据个人经验将相关方案初步设计出来,然后进行分析和对比,选择较为成熟的2至3个方案在UG软件环境下建立三维模型,并将这些模型分别导入计算机模拟软件中进行模拟运算、观察和分析对比。在此过程中结合个人经验进行修改或修正相关参数,然后再模拟和修正,直到确定最佳方案。分流孔的布置如图5所示。
采用模拟软件的好处在于可从模拟中发现分流孔的每一处修改对各处金属流速的影响以及各部位金属的流速是否趋于一致。本案例中的每个模孔由两个分流孔单独供应金属,这样可以使得模拟更易操作,也就是说容易使各处金属的流速趋于一致。由图5可见,只要确定分流孔S1的面积,分流孔S2的面积则较易调整。而且即使可调整的空间大,也不需要对分流桥和模孔的布置进行修正或改变。同时,这样的布置考虑了悬臂保护,可使下模悬臂完全置于分流桥的保护之下,金属不直接冲击悬臂,特别是悬臂的端部,这样悬臂承受的力是最小的,致使其强度最高。更重要的是,可从模拟中发现分流孔面积的变化不会造成悬臂变形。
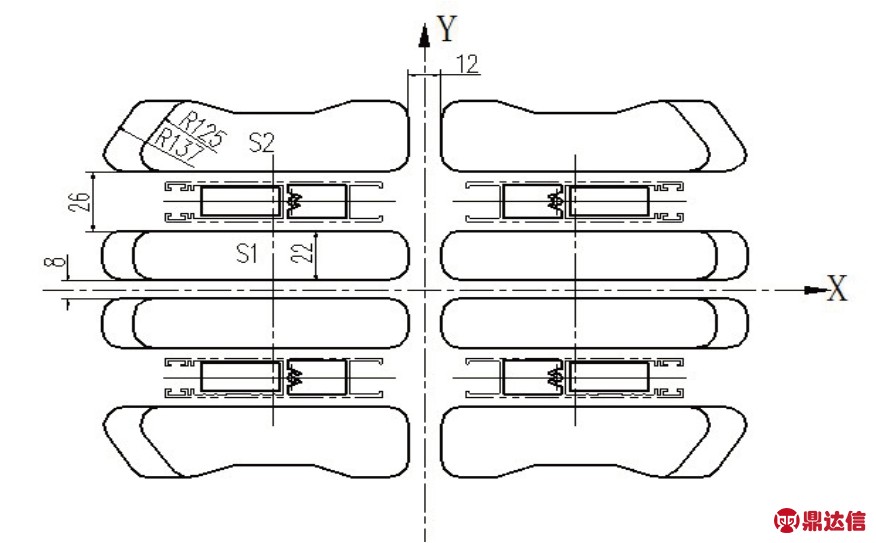
图5 分流孔布置示意图
分流孔主要参数如下:
(1)分流孔比为17.4。
(2)数字货币达不到100%的安全。从目前的数字货币——比特币为例看,存在一定的攻击隐患,这样的安全威胁目前不适合货币金融体系。
余荫山房的空间流线设计极大地影响着空间承载的活动类型与使用者的空间体验。余荫山房中的廊桥(图5)、园路等作为空间骨架组织空间,将园林空间向平面展开,一系列空间在开合、大小、深浅等方面不断变化,构建了“开始—发展—转折—高潮—收尾”的动态而完整的空间体验。
(2)分流桥尺寸为宽度24 mm,厚度85 mm。
(3)分流孔的面积关系为:S1=0.81S2。
从模拟中看出,当分流孔间面积关系为S1=(0.75~0.85)S2时,各处金属更容易趋于一致。
本文主要研究板梁的正常使用极限状态。根据设计图纸,按汽车-超20级和挂车-120活载,并将桥面铺装折算到试验梁上,通过跨中弯矩等效原则,计算得到千斤顶加载值为354kN,因此将354kN定为试验梁的设计荷载。加固前的试验表明,本试验梁加载到480kN后,其挠度与正常使用荷载作用下挠度限值1/600跨径基本一致,且在卸载后挠度、应力及裂缝宽度均能基本回到初始状态,表明试验梁处于弹性工作状态,为保证加固前后试验梁没有过多损伤累积,仍具有相似的承载力,本试验的控制荷载选取为480kN。
(4)分流孔进料口最大外接圆直径为φ270mm。
英格曼神甫说:“还有坏下去的余地吗?”他绝不会放这群穿黄军服的疯狗们从正门进来。让他们从正门进来,就把他们抬举成人类了。
(5)应力间隙取在“假模芯”上,应力间隙依经验取1.0 mm,所以“假模芯”高度为24 mm。
(6)分流桥采用通常的水滴形。
在上模结构参数中,“假模芯”尺寸的确定是十分关键的[5]。经验和模拟运算表明,“假模芯”尺寸以距离模孔边缘2~3 mm作为模芯边界确定,从成形和减小悬臂的受力和变形角度来看是最为合适[6]。保护式“假模芯”尺寸如图6所示。

图6 保护式模芯示意图
2.4 下模焊合室与工作带
下模焊合室与工作带如图7所示。
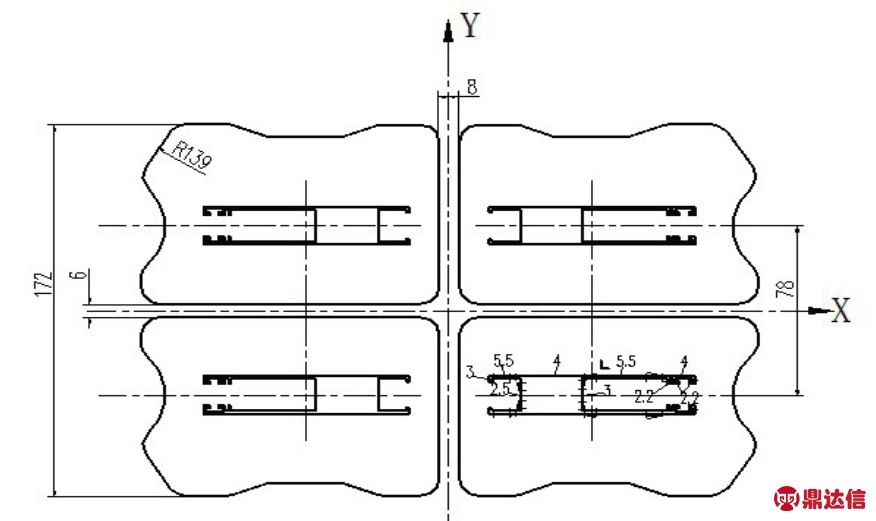
图7 焊合室与工作带示意图
为了使各个模孔的成形互不干涉和影响,并降低制造误差对挤压同步的敏感性,每个模孔都要设置独立的焊合室,采用隔墙的方式将每个焊合室进行分隔,隔墙宽度取8 mm[6]。焊合室的深度根据挤压机的能力相应取25 mm。由于焊合室是独立的,各个模孔的成形互不干涉,因此,工作带的选择也是独立的。所以,只要选定一个模孔的工作带,其它模孔与之相同即可。
2.5 模具强度的校核
对于一模四孔分流模结构,其强度校核同样是针对分流桥进行的。由于每个模孔都是独立的,因此,只需针对一个模孔对应的分流桥进行强度校核即可。
式中:Lp为性能成本函数;tf为终端时间;x0为初始状态向量;x=[q1 q1′ q2 q2′ q3 q3′]T为系统状态向量; 为控制向量;f为系统动力学;gi为不等式约束;ge为等式约束;ρ为可行u(t)控制策略的搜索空间;u(t)为0~tf的时间指标.
3 挤压结果对比
对图1所示型材分别采用传统的单孔普通分流模、单孔切割式分流模结构、一模双孔切割式分流模和保护式一模四孔结构的模具进行试模与挤压生产跟踪,并对不同模具所得型材进行了对比,其结果如表1所示。
选取2015年3月—2016年2月期间,我院收治的动脉瘤患者24例,其中男性患者11例,女性患者13例,患者年龄40至65岁,平均(56.2±7.1)岁,所有患者均经过外科手术证实为动脉瘤。
表1 模具结构与挤压结果对比
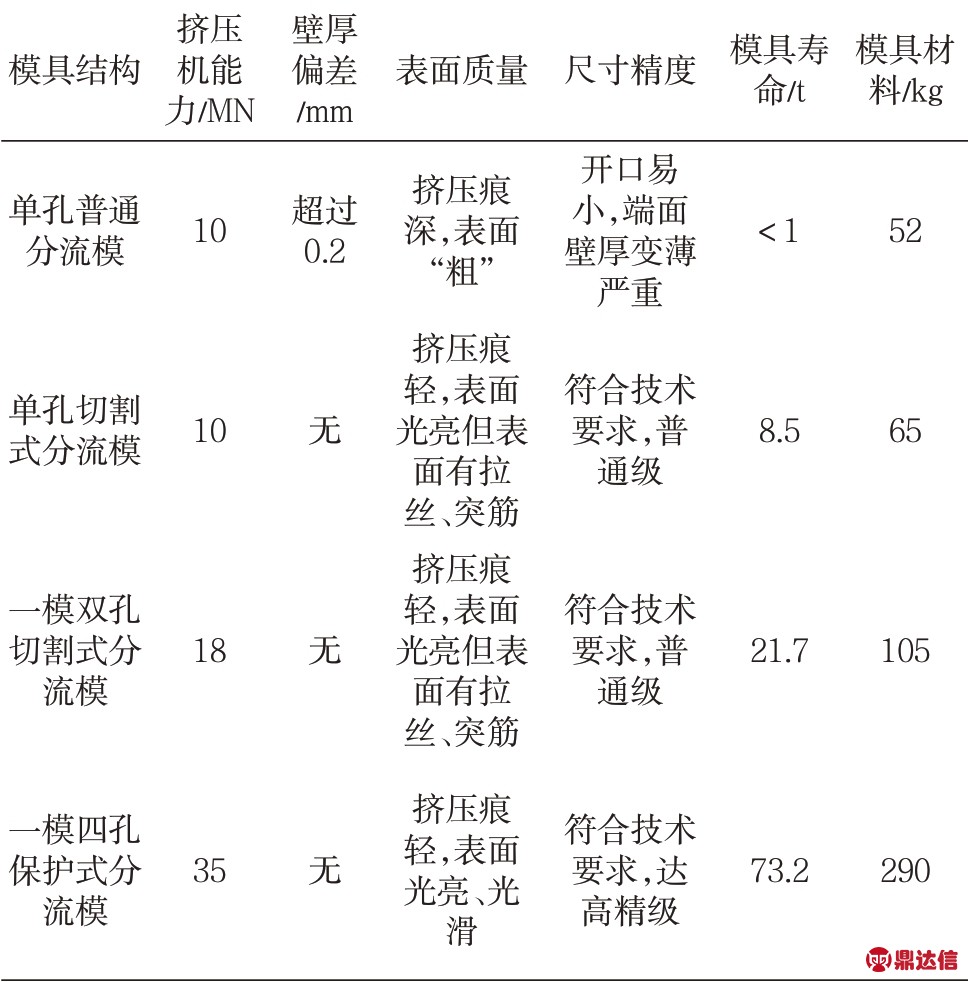
模具结构挤压机能力/MN壁厚偏差/mm表面质量尺寸精度 模具寿命/t模具材料/kg单孔普通分流模10超过0.2开口易小,端面壁厚变薄严重<1 52单孔切割式分流模10无符合技术要求,普通级8.5 65一模双孔切割式分流模18无符合技术要求,普通级21.7 105一模四孔保护式分流模35无挤压痕深,表面“粗”挤压痕轻,表面光亮但表面有拉丝、突筋挤压痕轻,表面光亮但表面有拉丝、突筋挤压痕轻,表面光亮、光滑符合技术要求,达高精级73.2 290
从结果可以看出,针对半空心型材采用保护式一模四孔分流模具进行挤压有明显的优势。
4 结束语
一模四孔保护式分流模结构的使用结果表明,这种结构的模具寿命可达73.2 t,可见这种结构是可以大幅提高挤压机的效率和降低成本的。如果在大机上采用更多的一模多孔模具进行多规格产品生产,则完全可以解决“小机吃不完,大机吃不饱”的问题,并大幅提高生产效率。在半空心型材的一模四孔分流模结构中,挤压机能力的选择、分流孔的确定、下模焊合室结构的确定和工作带的选择等是十分重要的。但更关键的是选择合理和有效的模具结构以降低挤压力和保证悬臂的强度并使加工简单化。这种结构是值得推广的,为半空心型材的一模多孔分流模结构的进一步研究和开发提供了可借鉴的经验和可靠的实践数据。