铝合金具有质轻、强度高、散热性能好,易加工成型等一系列优点,被广泛应用于工业、建筑和电子产品等领域。特别是带高倍数齿的散热器其导热性能尤为突出,主要以铝合金挤压成型为主[1]。但高倍数齿散热器因齿长且密,对挤压模具设计人员、模具钢的材质及加工工艺提出非常高的要求,任何一项做不到位都会影响模具的质量。这时模具设计尤为重要,加工工艺必须合理优化为辅。本文以实际生产来论述高倍数密齿带管散热器铝型材模具设计及优良的加工工艺的关键点,供相关技术人员参考。
老师要钻研教材,读懂教材,寻找读写结合点,设计写话梯度,给学生一个抓手,让学生写有所仿,创能有法,实现省时高效的写作训练。
读者阅读积分的管理包括积分的获取、积分的兑换、积分统计、积分排行、阅读闯关活动等。系统按照荐阅书目的组别来进行试题分组,并针对读者所选择的组别自动组卷,读者答题并通过得分来获取并累计相应的积分,通过阅读闯关活动、参与书评等方式来获取阅读积分。
1 散热器结构分析
高效散热铝合金型材截面如图1所示,其有以下特点:(1)散热铝型材为挤压空心型材且带高倍数密齿;(2)散热器空心部分带螺丝孔需要装配,精度要求高,尺寸公差±0.1;(3)散热器齿密集,要求不可有变形,且齿部分与根部壁厚落差较大;(4)散热器整个外形长度超过200mm,难度系数较高,要求不容许出现变形,公差为±0.2。
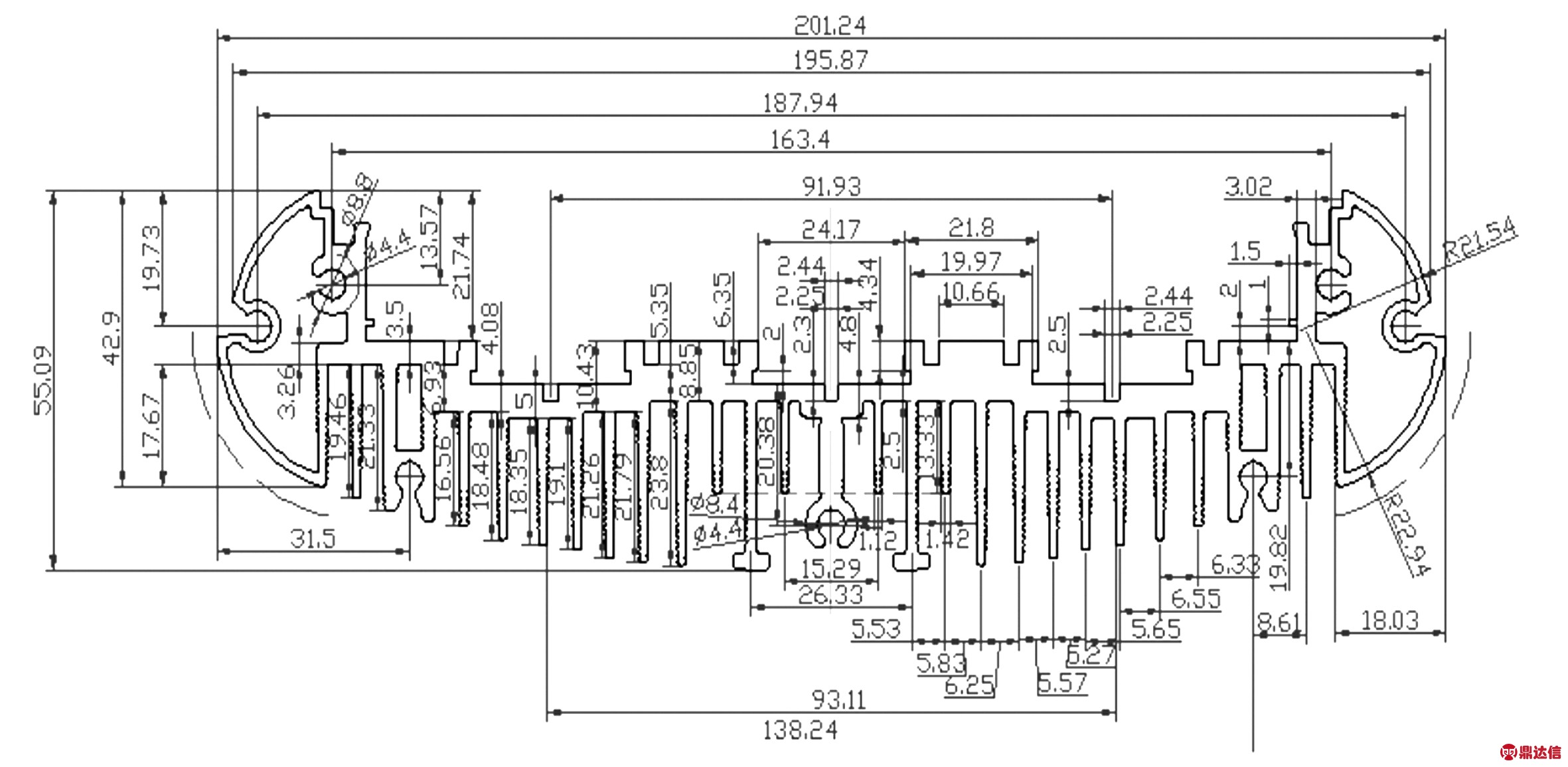
图1 高效散热铝型材截面示意图
Fig.1 Section diagram of high efficiency heat dissipation aluminum profile
2 散热器挤压模具设计
从结构断面分析可以看出散热器型材及截面外形长度为201.24mm,高度为55.09mm,设计有23个19mm~23mm不同的齿高,齿间距为5.5mm,在每个齿的两侧布有高0.3mm、间距1.0mm的齿牙。根据散热器型材悬臂处舌比公式得出23.8/5.83=4.08,显然舌比大于3的齿存在着危险断面[2]。特别是该截面底部壁厚较大(最薄3.5mm,最厚处达8.85mm),而齿最薄处的壁厚仅为1.4mm,截面壁厚相差悬殊,更增大了危险断面的断裂系数。并且还有4个小的空心位,空心位还带有螺丝孔。此散热器型材的难点处较多,空心部位与实心处壁厚落差较大,齿部分还带有空心部分,齿倍数较高且密。截面大小不同,会导致铝料通过模具各个横截面的流量与流速不尽相同。铝料受到相同挤压力的情况下,铝料会出现大部分流向横截面较大的地方,而横截面较小的面积会出现铝料较少,甚至会出现缺料现象,并且横截面积较大部分流速会比横截面积较小的部分流速快,实心部分流速比空心部分流速快,齿部的流速比根部实心部分慢,设计时必须考虑解决流量与流速不等的问题。
母亲病好了没有?母亲自己拾柴烧吗?下雨房子流水吗?渐渐想得恶化起来:她若死了不就是自己死在炕上无人知道吗?
2.1 模具结构的布局
由于该挤压材为空心型材带齿散热器即模具应为分流模结构,分上模与下模组合模具。分析散热器结构、外形长度、米重和机台吨位,最终选择2000T机台Φ205mm挤压筒内径,进料孔直径控制在Φ190mm。考虑到模具强度,必须合理的分配上下模具的厚度,采用下模与上模厚度比例分配系数为0.6∶0.4。为保证散热器挤压后各个部分尺寸达到要求,散热器的缩水会比正常要大些,这里产品设计缩水为1.0127。考虑到空心部分和齿部分的金属流量与流速必须均衡,设计为8个进料孔,;空心部分摩擦力较大,设计孔时加大两侧流量,中心部位实心处底部壁厚较厚,摩擦力会较小,出料易快,采用两个分流孔减少流量;齿部分考虑到其强度及摩擦力大出料会慢,也采用两个分流孔分流,但是要比底部实心处两个孔进料流量大些。考虑到整体金属流量与流速的平衡,保证型材密度、空心部分的壁厚和整体外形的尺寸达到要求,下模焊合室深10mm,上模中间上下两桥沉桥5mm即作为上焊合室用,考虑到两侧空心部位又带螺丝孔流速会偏慢,采取两侧沉桥12mm。模具结构示意图如图2所示,模具结构加工后效果如图3所示。
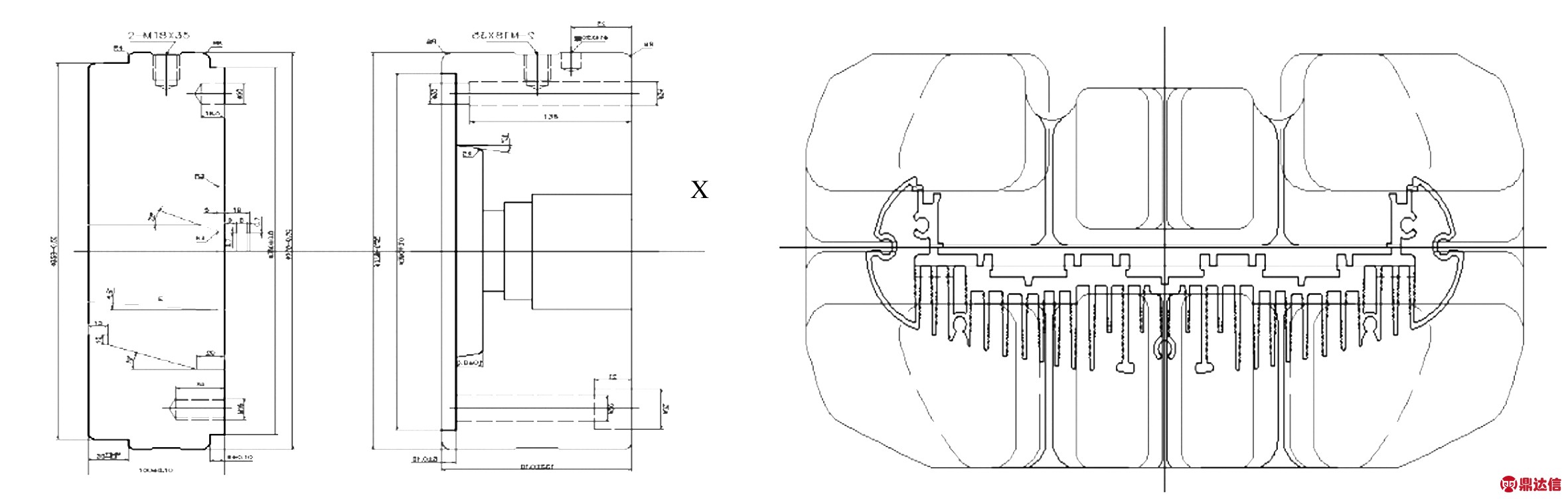
图2 模具结构示意图
Fig.2 Schematic diagram of die structure
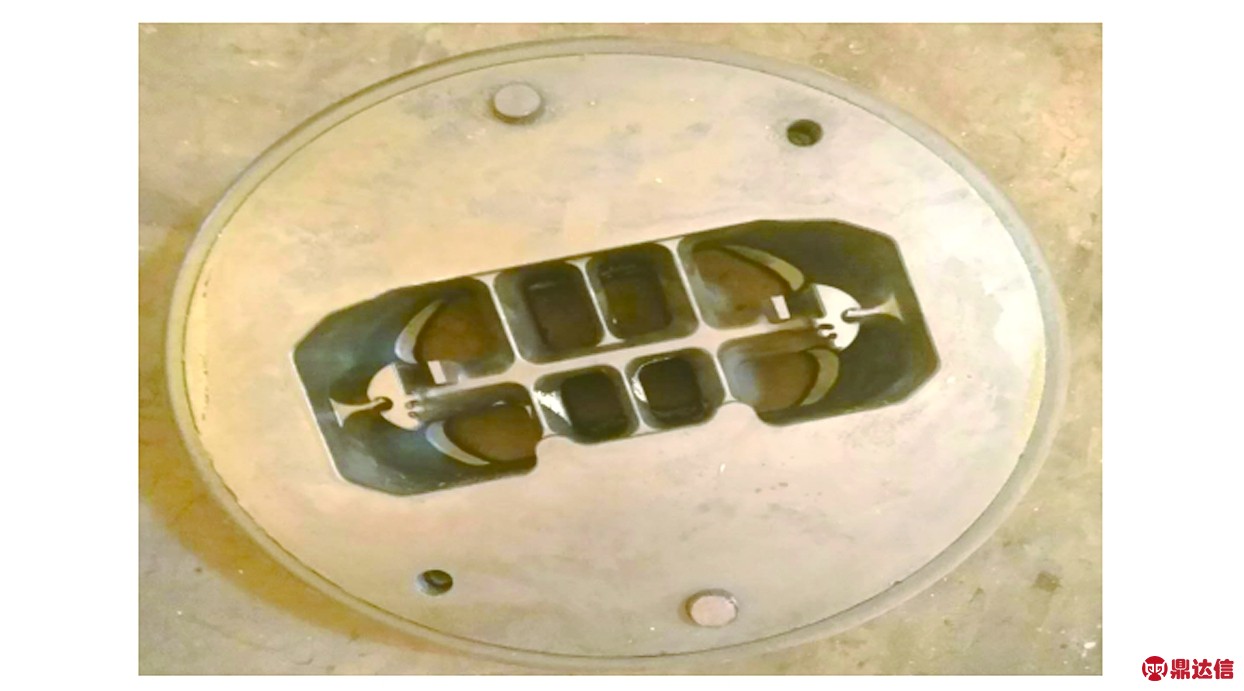
图3 模具结构加工后效果图
Fig.3 Effect diagram of die structure after machining
2.2 挤压模具型孔尺寸
2.2.1 模芯尺寸
因空心部位小、要求精度高,外形尺寸201.24mm尺寸公差为±0.2。要求CNC粗加工留0.05mm,精加工到位,电火花机电流放电为3A。
2.2.2 下模型孔尺寸
考虑到流速的整体平衡,在几处厚处加栏基。下模采用慢走丝加工到位。下模型孔尺寸、下模焊合室、模割电极放电空刀尺寸和下模出料避空位分别如图4、图5、图6和图7所示。
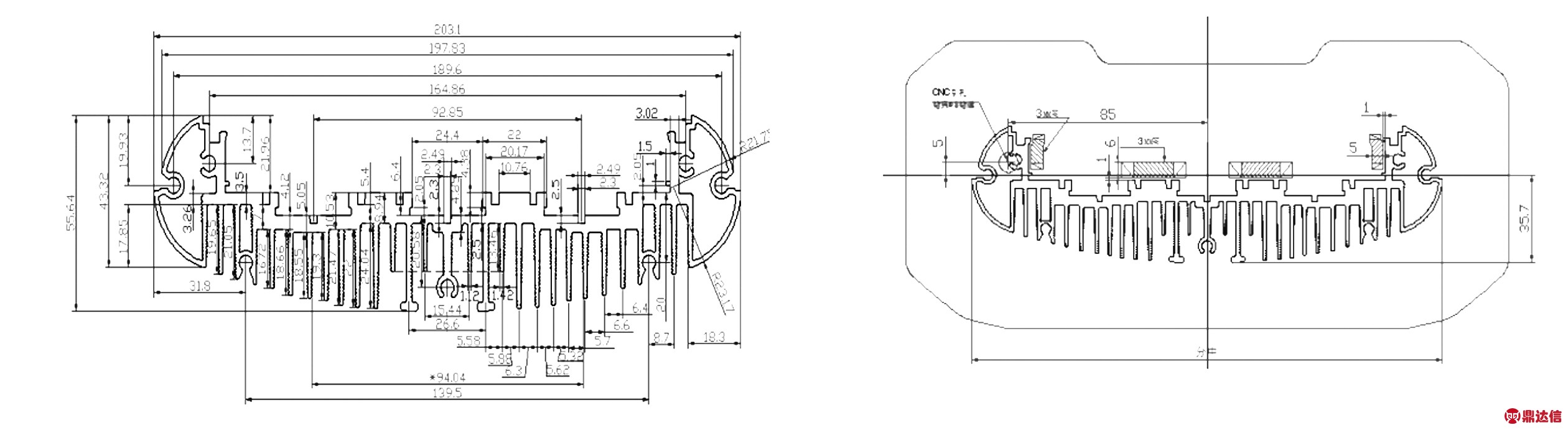
图4 下模型孔尺寸图 图5 下模焊合室图
Fig.4 Dimensions of lower model hole Fig.5 Lower die welding chamber drawing
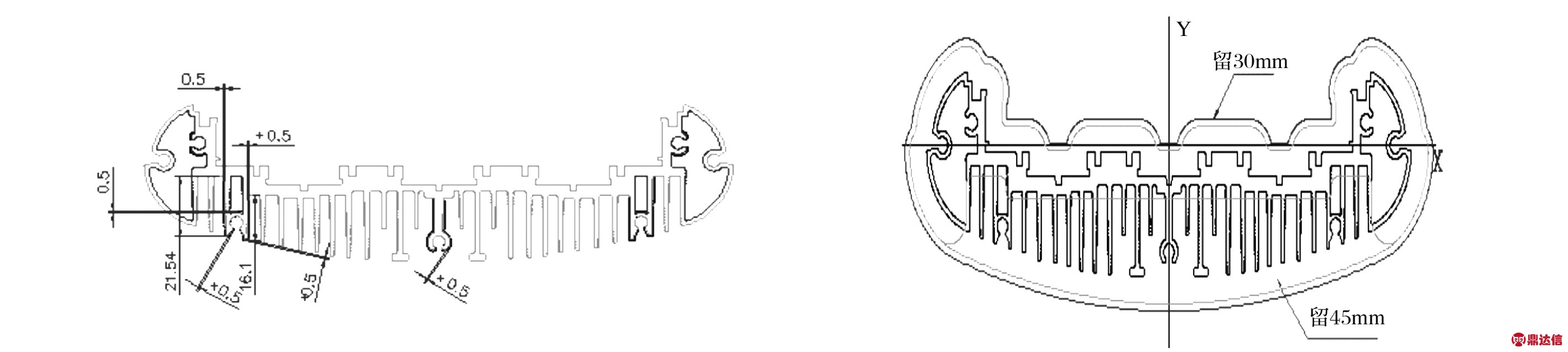
图6 下模割电极放电空刀尺寸图 图7 下模出料避空位图
Fig.6 Dimensions of discharge blank cutter for lower die cutting electrode Fig.7 Space-avoidance diagram for lower mode discharge
2.2.3 模具工作带设计
进料口布局起到影响铝料流量均衡性的作用,工作带就起到调节流速的作用。流速不均会严重影响型材的成型度,引起壁厚偏差及表面不良等情况,考虑到空心部分和齿部摩擦力大,在工作带上设计为短工作带。配合进料孔的流量利用工作带长短平衡流速,在挤压时让其出料两者配合能达到一致性。其下模工作带如图8所示。
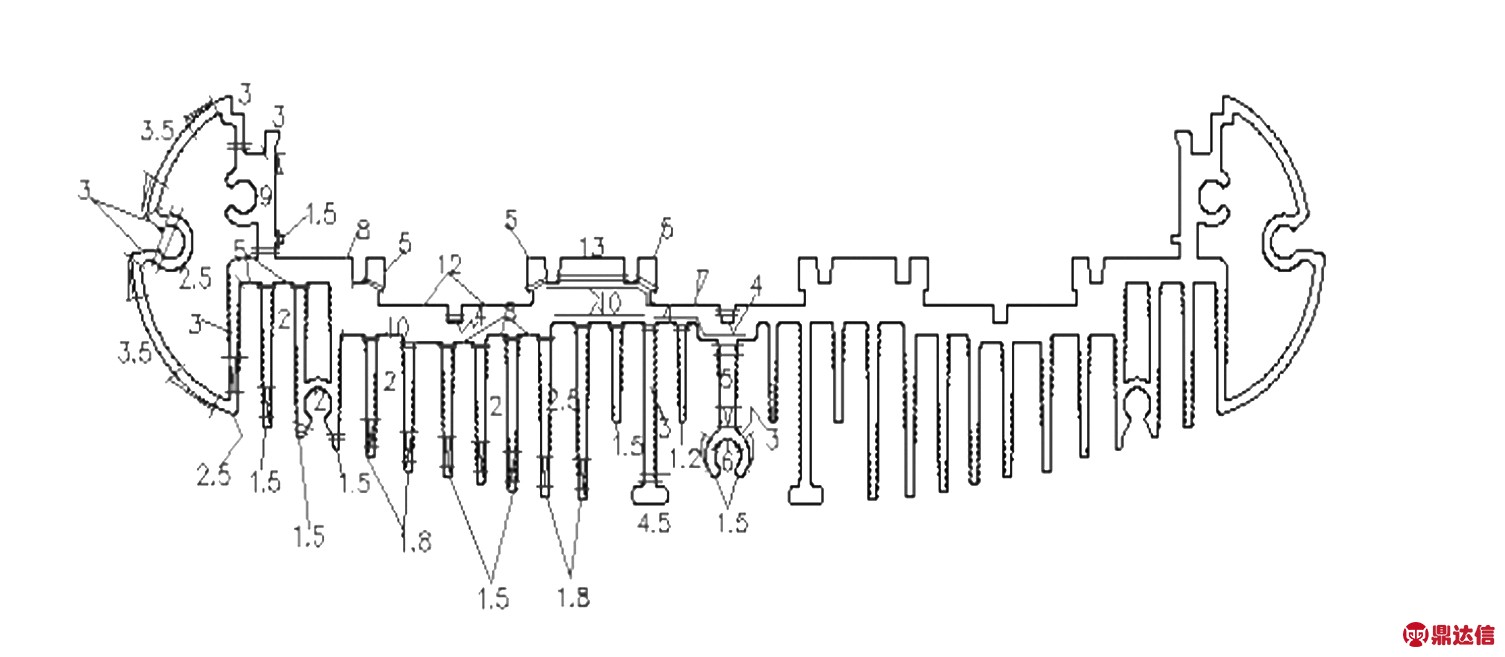
图8 下模工作带图
Fig.8 Lower mode work belt diagram
3 挤压模具加工工艺
3.1 上模与下模的加工工艺
用UG建3D模型,CNC五轴高精度的设备粗精加工,可以有效保证模芯精度、进料孔及下模焊合室的精度;粗精加工工艺孔,慢走丝以基准面为水平面、工艺孔为中心分中加工,保证上下模同芯加工误差小于0.05mm。CNC数控设备很好的解决了因手工铣床加工出现精度不高、易偏差等缺点,下模采用慢走丝加工割一修一,可以有效保证加工精度、垂直度,减少抛光工作量。高精度设备与工艺的优化安排,可以减少分流模因模芯粗精配造成的时间浪费,有效提高效率和模具的精度。
3.2 工艺安排
(1)CNC粗精车必须同心加工。
(2)CNC加工保证基准面的垂直度和光洁度、分流孔的对称性,销钉和螺丝孔上下模必须一致,由CNC粗精加工完成,铣削基准面平面度小于0.05mm,模芯由CNC精加工到位。
(3)电火花加工上下模时,放电量一定要根据图纸要求来加工,电流一定要合适控制在3A。电极工作带采用CNC完成,光滑接顺不可有尖角。
现代医学教育体系下的中医药文化教育尚无系统的方案与计划,医学院校大部分本科生对中医药文化了解不够,缺乏兴趣与热爱,影响了专业信心与学习成绩。
(4)线切割必须以基准面校平行,再用工艺孔分中,误差必须小于0.03mm方可加工。
4 结束语
(1)通过对高效散热型材的模具分流孔、模具工作带等的优化设计,可有效调节金属挤压时的流速,减少模孔危险断面的产生,有效延长模具的使用寿命。
由于国内城市化进程不断取得新成效,商品房销售面积增长,使用锯材消费略增,但整体木质家具使用橡胶木的减少,影响我国锯材进口。
(2)采用先进的高精度数控设备,配合优良的加工工艺,可以提高精度减少误差,提高生产效率,保证型材的顺利挤出。