对铝型材表面质量要求越来越高,印痕缺陷铝型材表面不允许出现。印痕是空心铝型材“丁字位”区域空心部分和实心部分交接处较水平表面0.03~0.05 mm的凹陷,经喷漆处理后,反光条件下该处出现的折痕。铝挤压厂多采用反复试模和修模方式,以达到产品表面合格。目前不少学者通过有限元仿真技术,对挤压模具 的 分 流 孔[1-2]、 焊 合 室[3-5]、 阻 流 块[6-8]、 工 作带[9-10]、导流板[11]等结构进行了优化。 本文根据实际挤压生产中含“丁字位”结构的空心铝型材表面产生的印痕问题,运用有限元模拟软件模拟挤压过程,分析型材产生印痕的原因,并通过实验验证模拟结果。
1 实 验
1.1 生产中的印痕问题
本文研究对象为某企业实际生产的空心铝型材,图1为其横截面尺寸图。型材的平均壁厚1.4 mm,最小壁厚 1 mm,截面积为 306.48 mm2,周长 413.63 mm。经检测,B处悬臂轻微翘曲,经喷涂处理后,A处反光条件下有微小内凹的折痕,如图2所示。本实验将截取存在印痕的“丁字位”部分进行分析。
1.2 模型的建立
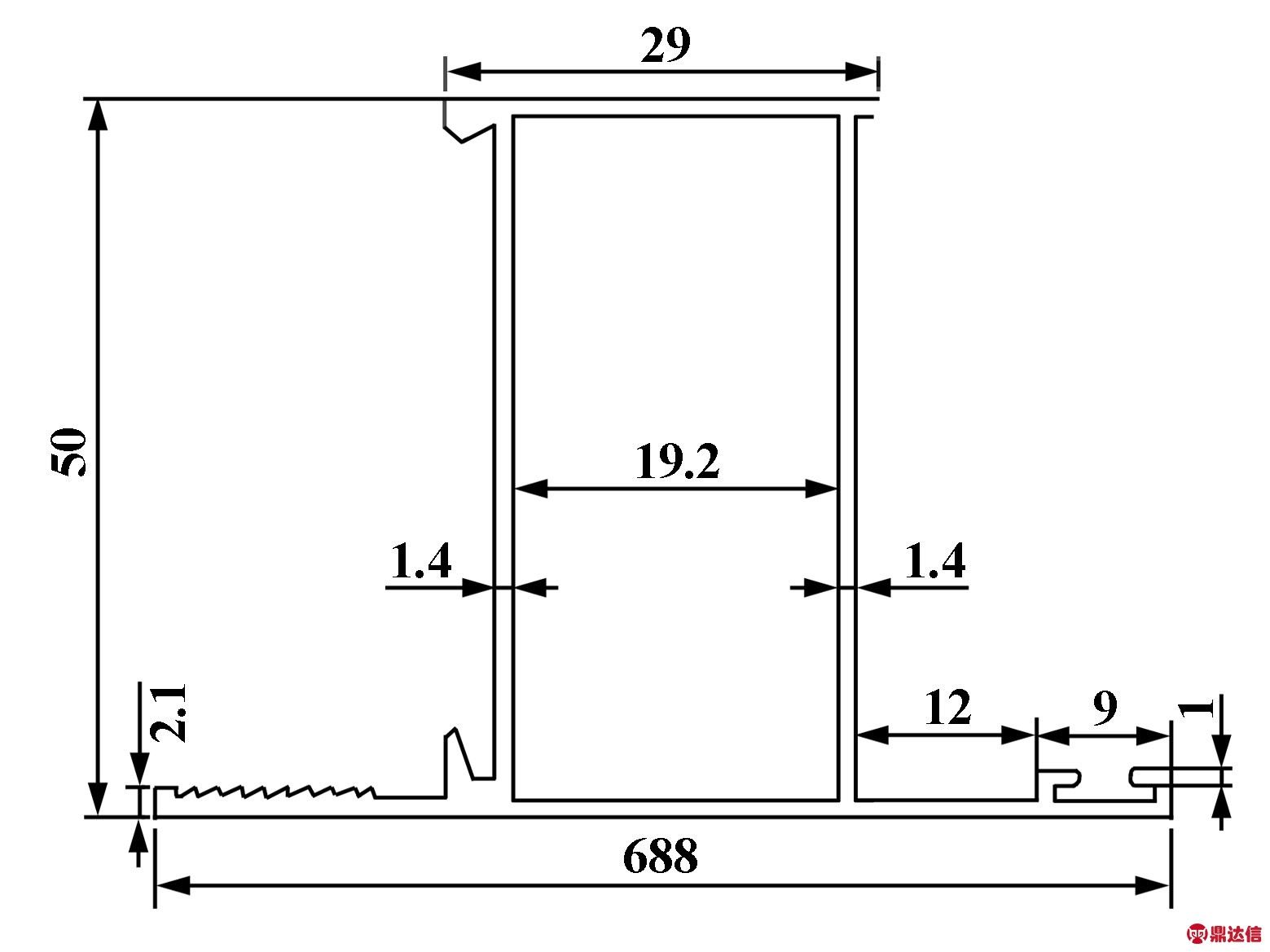
图1 型材横截面(单位:mm)
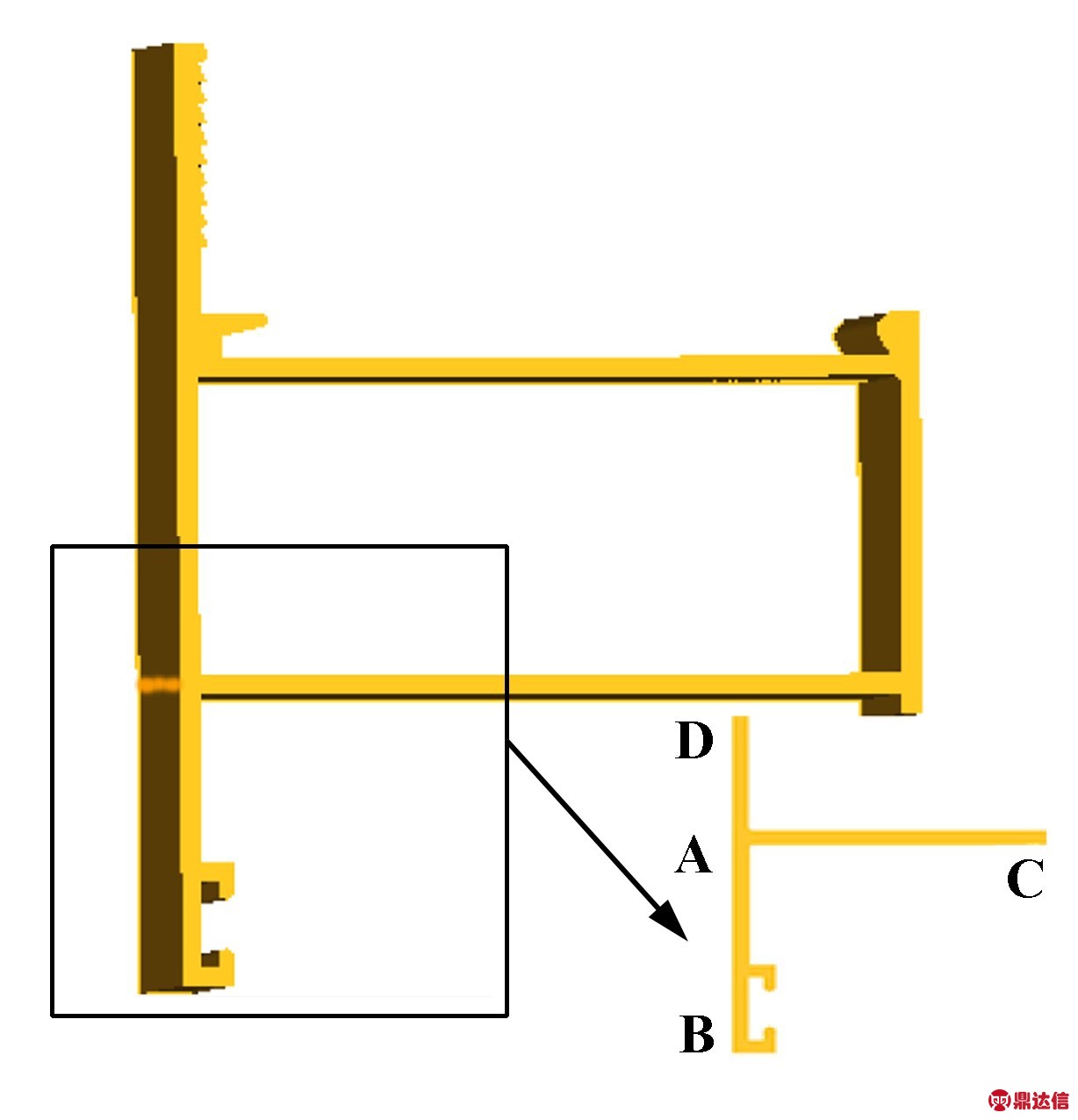
图2 型材三维模型

图3 初始模具三维模型
(a) 上模;(b) 下模
用三维软件绘制的初始模具模型如图3所示。上模尺寸为Φ180 mm×60 mm,下模尺寸为Φ180 mm×60 mm。 将模型导出为stp格式,并导入到基于ALE算法的Click2Extrud软件中,设定挤压方向为Z轴正方向,型材“丁字位”表面内凹方向为X轴正向。挤压材料为6063铝合金,模具材料为H13钢。挤压工艺参数为:坯料加热温度480℃,模具预热温度450℃,挤压筒温度410℃,挤压杆速度8 mm/s,坯料直径120 mm,挤压筒内径130 mm,挤压比为42.8。
那些曾经开过驮子他们玩笑的人,大多数没有开玩笑,但还有几个仍然开,他们说,驮子,你要好好的练功夫,不仅棉花要弹好,床上功夫更加要弹好。驮子听他们这样说时,也笑了,他的脸居然没有红,他说,我现在床上功夫好着呢,不信你安排个女人让我来试试。
2 实验结果及讨论
2.1 仿真结果分析
图4为型材流速分布图。由图4可见,型材Z轴方向流速不均匀。在AC边上,A处到C处的Z轴方向流速逐渐减小,在附加应力的作用下,金属有从A处沿AC方向流向C处的趋势,导致A处金属产生X正方向的流速。B处悬臂流速最大,故金属在X轴负方向产生流速。在X轴方向上,BD面上产生不同方向流速。
在教学实习环节,教师选取一病例,提出相应问题.选取的病例要求典型、有鉴别和分析的价值,并具有病情动态变化特点;所列问题包括回顾复习疾病知识,易被学生忽视的问题,新进展或临床上有争论、目前不确定的问题.学生围绕这些问题复习知识,查阅文献,收集病人资料,反馈教师提出的问题,同时也提出需要进一步探讨的问题.在查房日按病史汇报、床边评估、实施护理操作等步骤进行教学实习.最后进行互动讨论,教师总结评价.在护理教学查房后,要求每位学生画出概念图[2-3],把查房病例涉及的病因、病理生理、临床表现、治疗与护理诊断、护理措施等高度浓缩在概念图里,通过层级结构形式表现,整合新旧知识,构建知识网络.
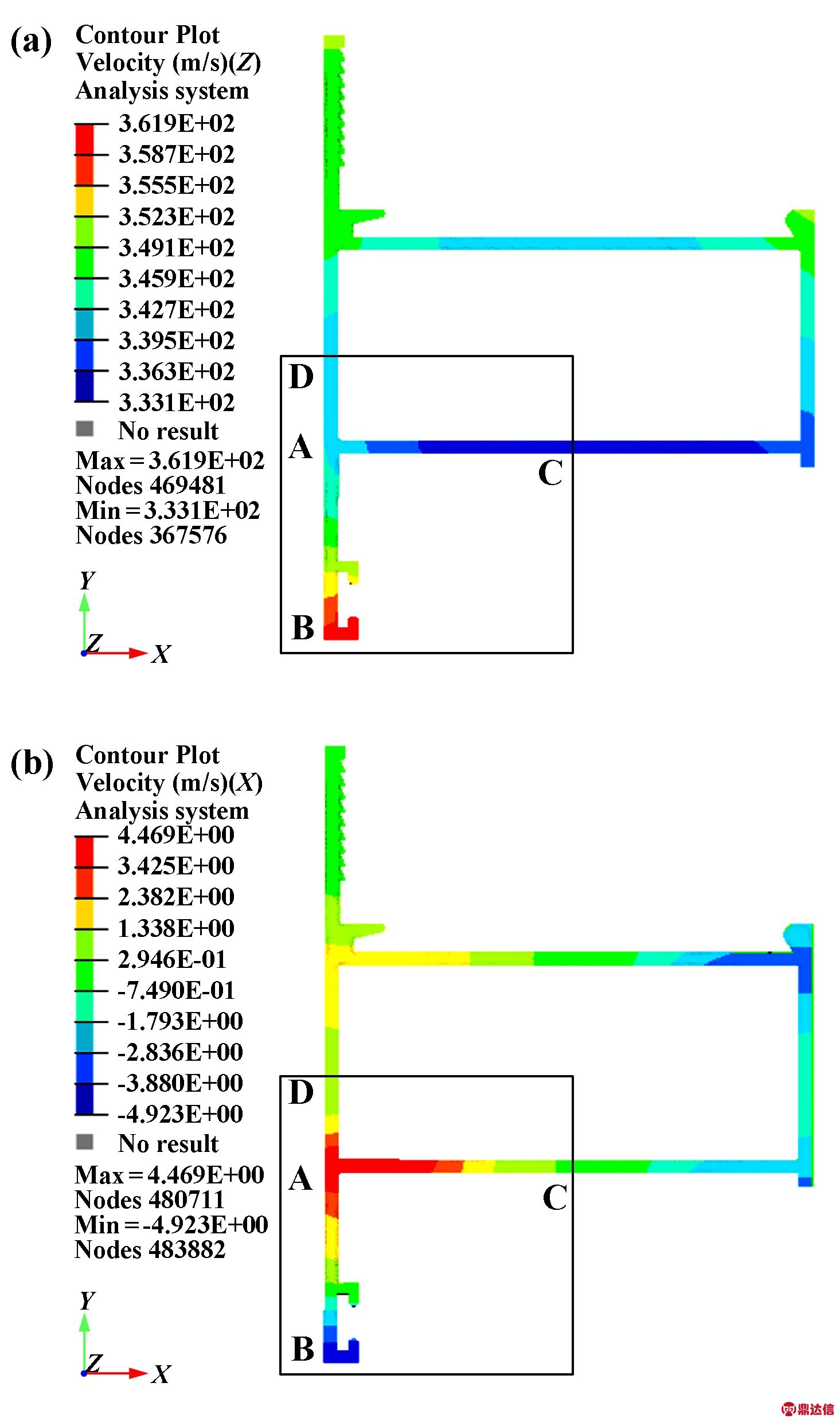
图4 型材流速分布
(a) Z 轴;(b) X轴
型材X轴方向位移见图5。由图5可知,A处轻微内凹,位移为0.052 mm,B处细小悬臂翘曲,位移为-0.062 mm,D 处位移为 0.007 mm。 BD 面上,从 B 到A处倾斜 0.114 mm,D 到 A 处倾斜 0.045 mm,BA 和DA相对A处翘起,使得型材在A处产生折痕。这与实际生产中B处轻微上翘、A处以及其周围产生轻微内凹一致。由此可知,型材的印痕缺陷主要由挤压方向的金属流速不均匀引起。
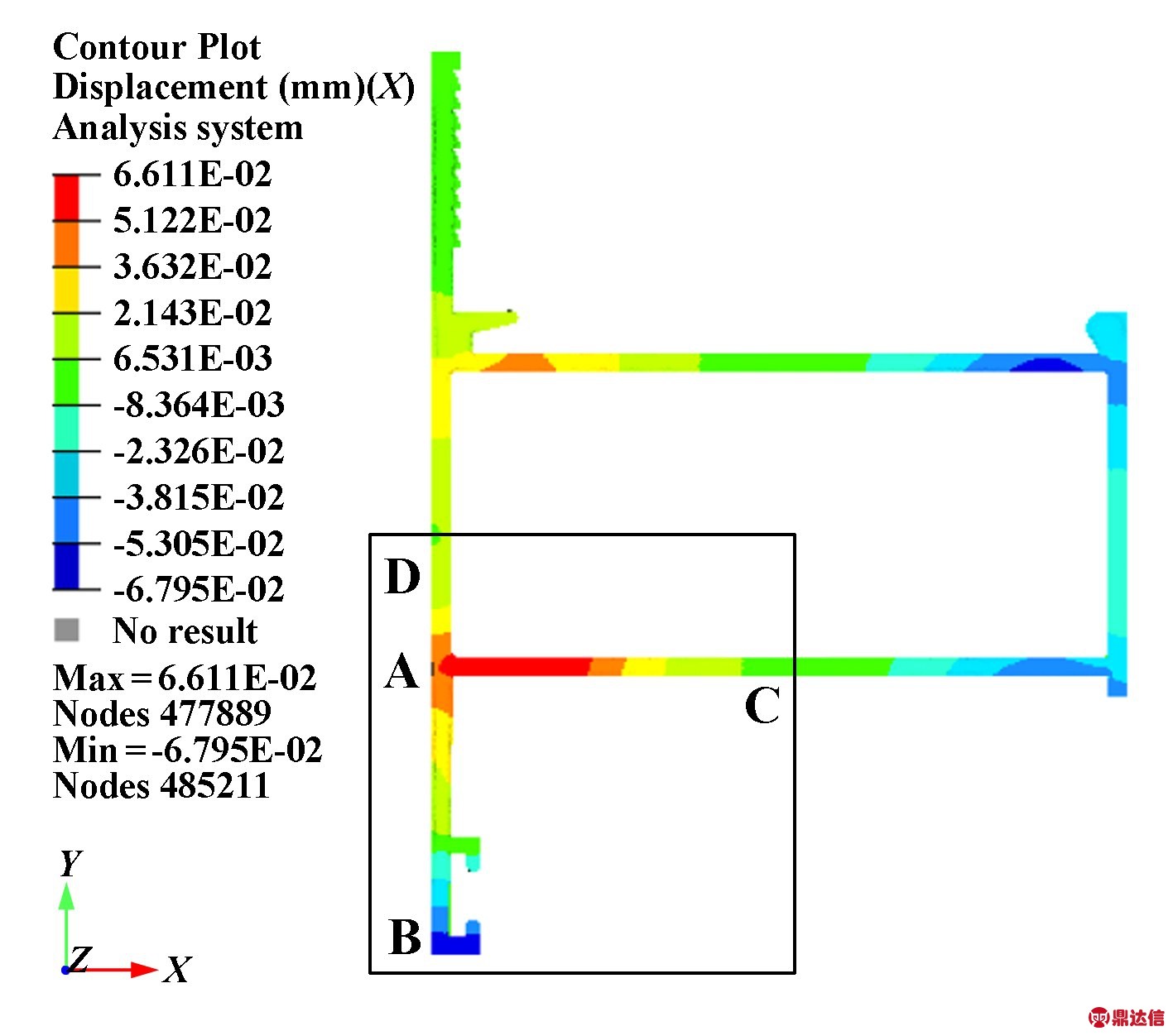
图5 型材X轴方向位移
2.2 模具优化分析
为使金属流速均匀,在流速较快的B处添加阻流块,阻流块长度为9 mm(为悬臂长度),宽度为2 mm(为型材宽度的2倍),高度3 mm(为焊合室的1/3),阻流块到模孔的距离设为0.5 mm。增加阻流块后下模三维模型如图6所示。

图6 增加阻流块后下模三维模型
图7为增加阻流块后型材流速分布图。将研究区域划分为等面积的14段,N为对应段数编号,取各段Z轴方向流速平均值绘制折线图,如图8所示。由于阻流块阻碍悬臂处金属流动,B处悬臂流速降低20 mm/s,C处流速增加7 mm/s,A处流速基本不变,型材Z轴方向金属流速趋于均匀,金属从A处流向C处的趋势变小。故在X轴方向,A处流速降低2.5 mm/s,B处流速降低2.9 mm/s。BD面流速均为X轴负方向流速。
该研究实验组45例患者的治疗依从性为95.56%,而参照组的治疗依从性为82.22%,两组治疗依从性差异明显(P<0.05)。 见表 3。
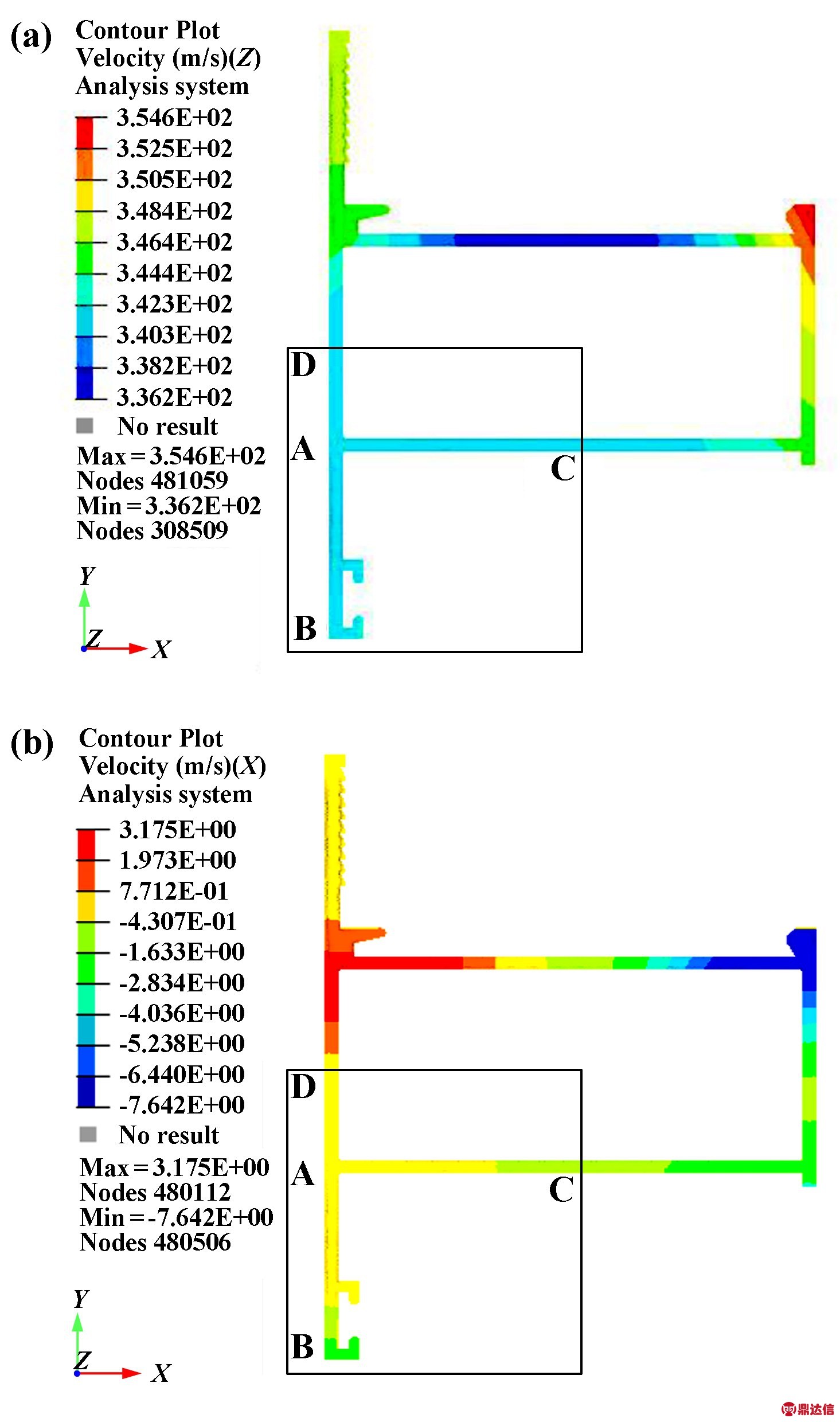
图7 增加阻流块后型材流速分布
(a) Z 轴;(b) X 轴

图8 型材丁字型区域分段及增加阻流块前后Z方向流速对比
增加阻流块后型材X轴方向位移如图9所示。BD面上,A 处位移仅-0.004 mm,B 处位移-0.025 mm,D 处位移0.010 mm。 从 B到 A倾斜0.021 mm,A到 D倾斜0.035 mm,未发生相对A处的折痕,且A处内凹量微小,可忽略不计。
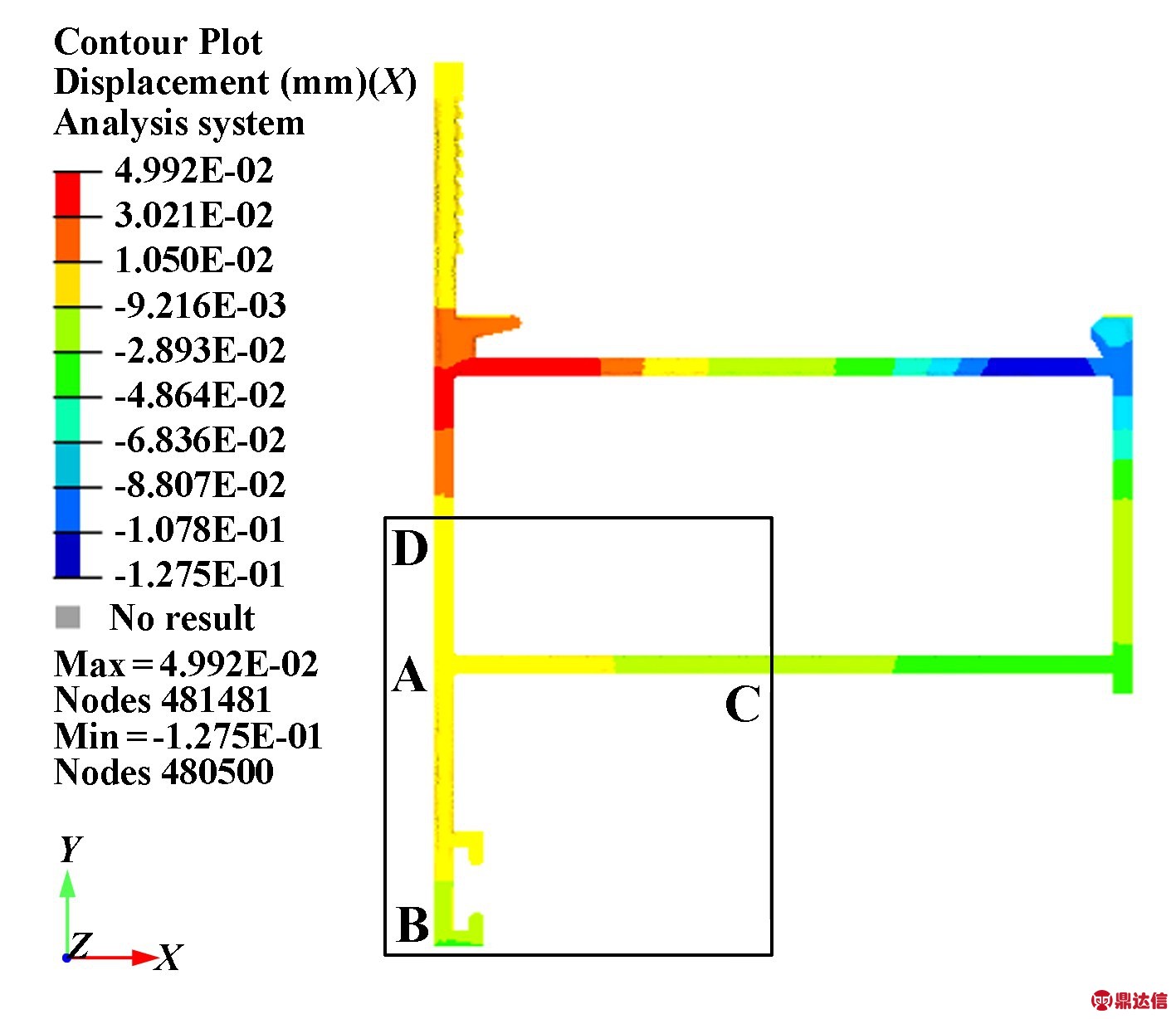
图9 增加阻流块后型材X轴方向位移
2.3 验证实验
在下模的细小悬臂处添加阻流块,按照原挤压参数进行挤压,得到的型材料头如图10所示。比较优化前后的型材料头可知,优化前型材悬臂处金属流速明显高于其它部位,优化后型材整体金属流速较均匀,均与模拟结果一致。经检测,优化后型材尺寸符合要求,型材表面不平整度在标准允许范围内,悬臂处未出现翘曲。经喷漆处理后,“丁字位”凹痕缺陷并不明显,符合生产要求。
通用电气公司把企业文化视为最好的精神黏合剂,把公司所有人紧紧团结在一起,向着共同的愿景目标,协调一致,努力奋斗,从而把通用电气打造成一个年轻而有活力的企业。韦尔奇告诫大家:“人才即是一切,有人才的公司才能成为最大的赢家。”“投资于人才”是通用电气公司核心的管理文化——人才是企业的核心力量,优秀人才是公司最重要的战略资源,是企业价值的主要创造者。在人才全球化战略的指引下,全球范围内寻找最优秀的人才,挖掘有潜力的人才,留住一流的人才,挑选好接班人,始终是通用电气公司最重要的战略规划。通用电气公司的每一个企业都重用当地人才,同时注重培养其全球化工作能力,实现了人才的“全球本土化和本土全球化”。
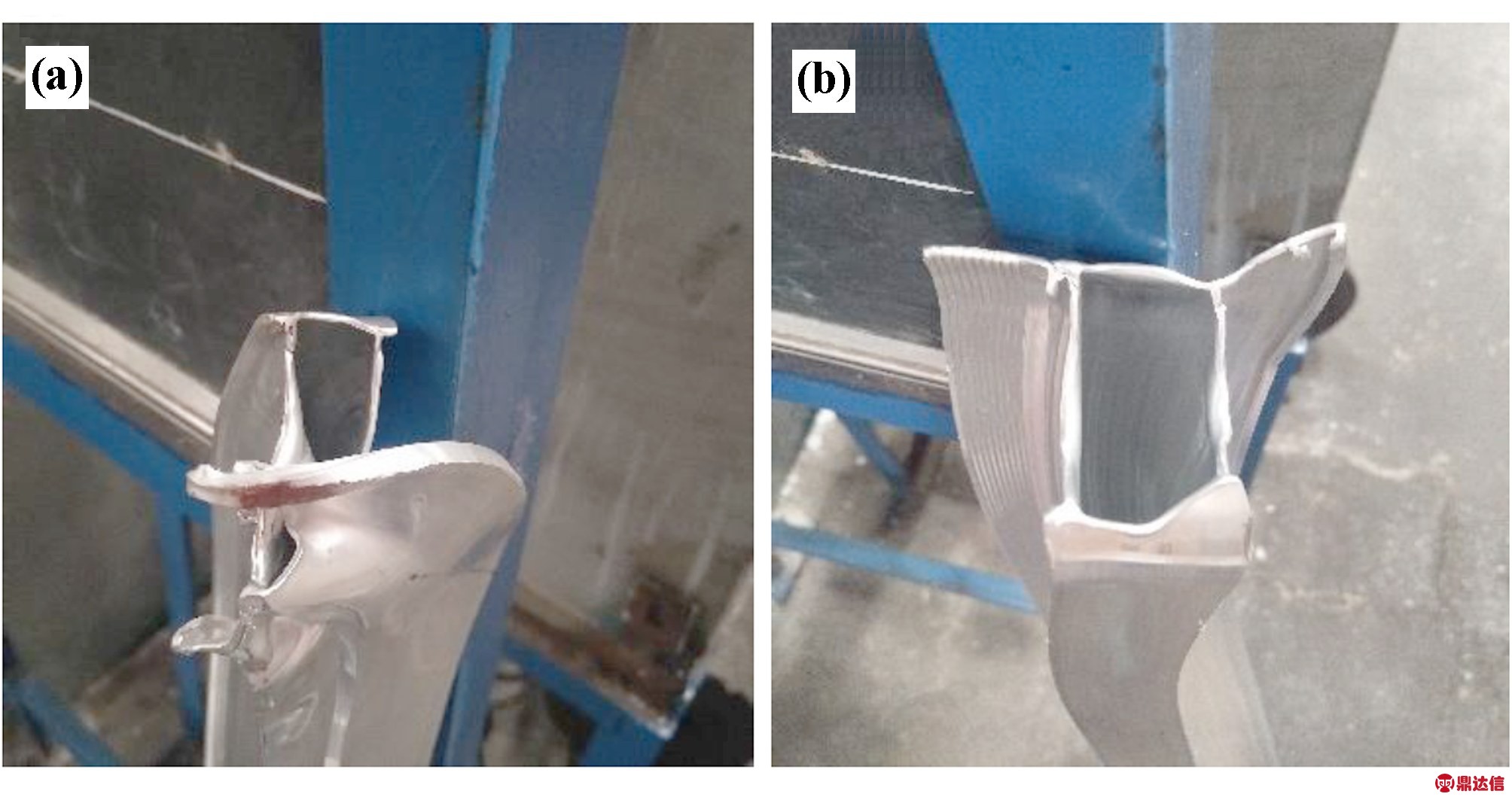
图10 模具优化前后的型材料头
(a) 优化前;(b) 优化后
3 结 论
1)模拟和验证实验均表明,型材“丁字位”表面印痕缺陷是由挤压方向流速不均匀引起的,型材悬臂处流速过大,造成印痕的产生。
2)通过数值模拟,可获得型材内凹方向的位移量,为模具优化提供依据。
3)在流速较快的地方合理添加阻流块能有效降低该处流速,使型材流速均匀。