0 引言
铝合金作为一种可回收利用、耗能少的轻质金属,在汽车、建筑、航空航天等领域应用广泛[1]。热挤压是铝合金生产相同截面挤压型材的主要工艺之一[2]。随着铝合金挤压型材向大型化、复杂化、精密化、多品种、多规格、多用途方向发展,对挤压模提出了越来越高的要求[3]。
近年来,农田种粮效益低,轮作模式单一,农作物产量降低,遭受病虫草害的影响的现象较为普遍。为了能稳粮增效,在共和县塘河地区进行“蚕豆—青稞”轮作种植模式的试验。
铝合金的挤压加工是综合高温、高压、摩擦和塑性变形的复杂非线性成形过程,难以采用试验的方法进行定量研究[4]。利用有限元模拟软件可以对铝合金挤压变形过程中的位移场、应变场、应力场以及温度场等进行模拟,揭示金属的流动规律、各种因素对变形的影响以及成形过程中变形体和模具的力场分布等[4],节省了设计时间和成本,提高了生产效率。现以某边框空心铝型材为研究对象,对其进行挤压模设计、数值模拟和模具结构优化。
1 模具结构设计
空心铝型材横截面形状和尺寸如图1所示,材料为6082铝合金,型材有上、下2个空腔,右上方和左下方各有1个悬臂,壁厚为1~3 mm,横截面积为529.225 mm2。型材截面不规则,且壁厚不均匀,在挤压过程中金属流动速度差异大,产生型材端面不平整、弯曲等缺陷,影响型材的表面质量。
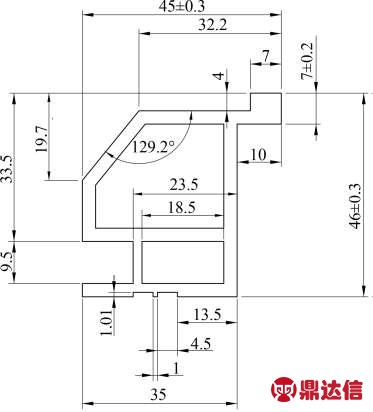
图1 型材截面尺寸
该型材的最大外接圆直径为ϕ70.3 mm,根据铝型材加工实用技术手册[3],选用内径为ϕ130 mm的挤压筒,坯料尺寸为ϕ120 mm×500 mm,采用15 MN的挤压机进行挤压加工,与挤压机配套的模具尺寸为ϕ200 mm×100 mm,上、下模厚度均为50 mm。
大多数空心铝型材,特别是薄壁、多腔、复杂截面的型材,都采用分流模进行挤压生产[5]。现选用平面分流组合模,在保证模具强度的前提下,为了使金属流动更均匀,根据型材挤压形状的实际需要,设置了4个均匀分布的分流模孔,分流桥宽度为18 mm,焊合室高度为16 mm[6],采用蝶形结构,模具初始结构如图2所示。
2 数值模拟
2.1 建立有限元模型
模具材料选用H13钢,确定挤压模拟工艺参数如表1所示。设定材料与挤压筒和模具型腔内壁之间的摩擦均为粘着摩擦,与模具工作带之间的摩擦类型为库伦摩擦,摩擦因数取0.3,模具与坯料的界面换热系数为3 000 W/(m2·K)[7]。
在有限元模拟软件中对导入的铝型材三维模型进行处理,依次进行各部分提取、单元网格划分和3D网格建立,网格大小从0.4 mm逐渐增大,由此得到的有限元模拟模型如图3所示。
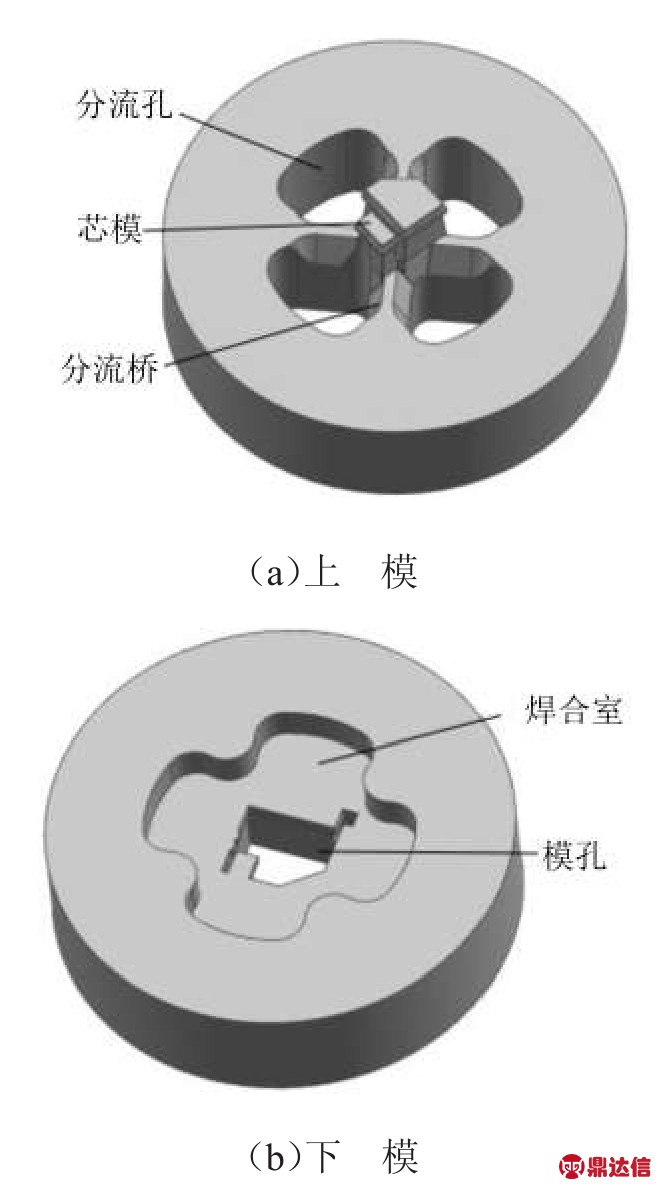
图2 模具初始结构
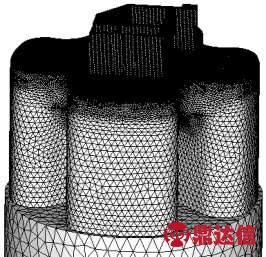
图3 铝型材有限元模型
表1 挤压模拟工艺参数
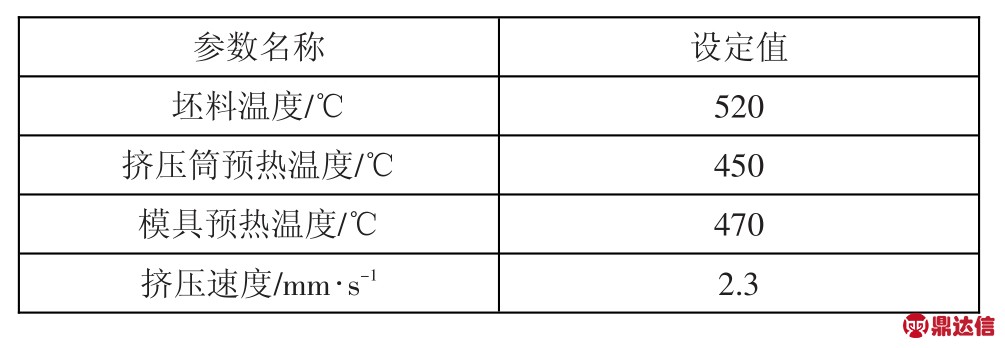
参数名称坯料温度/℃挤压筒预热温度/℃模具预热温度/℃挤压速度/mm·s-1设定值520 450 470 2.3
2.2 初始模拟结果分析
型材挤压时的金属流速分布是否均匀通过速度均方差(SDV)判断,具体公式如下[7]:
研究得出数据通过SPSS19.0软件统计处理,以数(n)或率(%)表示计数资料,以χ2检验,P<0.05说明差异有统计学意义。
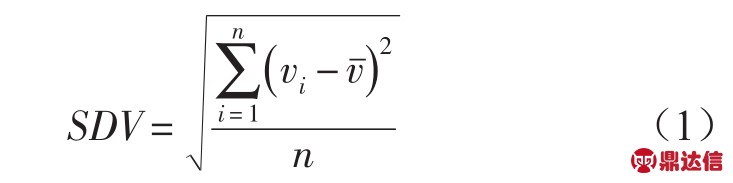
式中:vi——对应的节点速度,mm/s;——所有节点平均速度,mm/s;n——节点数量。
在实际的教学过程中发现,唯有《计算机基础》《C语言程序设计》等职业技能基础课有双语教材,其他的课程要么是全英文教材或是中文教材。然而,全英文教材一般价格较高,且内容与高等职业教育人才培养目标的要求相差甚远。因此,需要对同类英文教材进行修改,或者根据中文教材自行编写英文讲义。
Wang等[3]使用蝙蝠算法(Bat Algorithm, BA)解决了无人战斗机(Uninhabited Combat Air Vehicle, UCAV)的二维路径优化问题,并通过实验与粒子群优化(Particle Swarm Optimization, PSO)算法等其他方法比较,验证了BA的有效性;Zhu等[4]提出使用自组织图和速度合成法对在水下工作区域内的无人潜艇进行三维路径规划,实现潜艇在海洋动态潮流下的任务路径最短;陈家照等[5]提出一种基于改进PSO算法的三维空间路径规划,通过PSO算法将三维路径规划问题转化为二维空间上的路径规划问题,从而解决飞行器的三维路径规划问题。
模具结构设计越合理,金属流动速度越均匀,速度均方差就越小,挤压型材的成形质量就更好。
初始模型经过有限元模拟后,型材出口截面处金属流速分布如图4所示。金属流速分布不均匀,最大速度为79.3 mm/s,最小速度为8.8 mm/s,速度差达到70.5 mm/s,速度均方差为15.6 mm/s,速度均匀性差。型材中部壁厚较小且位于两部分芯模之间,供料有限,周围的材料流入补给的流动阻力较大,所以金属流速相对较慢;而型材右上部的悬臂壁厚较厚,对应模孔较大,材料供应充足且阻力较小,因此金属流速较快。
7大专科,130多种儿科、80余种妇科手术,等待时间缩短50%,住院时间缩短为4~6小时。严卡标准,倡导围术期管理,他们竖起日间手术新高度。
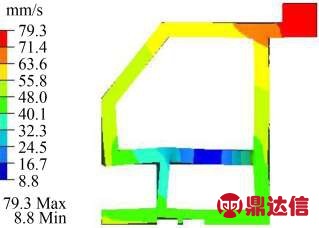
图4 初始模拟金属流速分布
上述情况会使型材中间部分凹陷,悬臂突出,整体端面不平整,甚至产生弯曲、扭转,故初始模具结构设计不合理。可以通过增设引流槽、阻流块和调节工作带长度的方法进行调整,减小截面金属流速差异,提高端面平整度。
3 模具结构改进
3.1 悬臂处增设阻流块
由图4可知,型材右上方的悬臂处金属流速较快,可以在焊合室相应位置增设阻流块来降低金属流速。使用阻流块不需要对模具结构进行大幅度修改,其修模过程也较简单[8],在模孔边缘增加尺寸为1.5 mm×1.5 mm的阻流块,与工作带距离为0.5 mm。在其他参数不变的情况下,挤压模结构与金属流速分布结果如图5所示,流速差减小为62.4 mm/s,计算速度均方差为14.4 mm/s,相比初始模具的流速差降低了7.69%。
增加阻流块可以起到平衡金属流速的效果,但初始设计的阻流块尺寸太小,效果不明显,故逐渐增大阻流块。由图5可知,型材上、下方的金属流速普遍较大,可以在周围设置尺寸为3 mm×3 mm且长度不等的阻流块,与模孔的距离仍为0.5 mm,具体改进方案及其流速分布如图6所示。
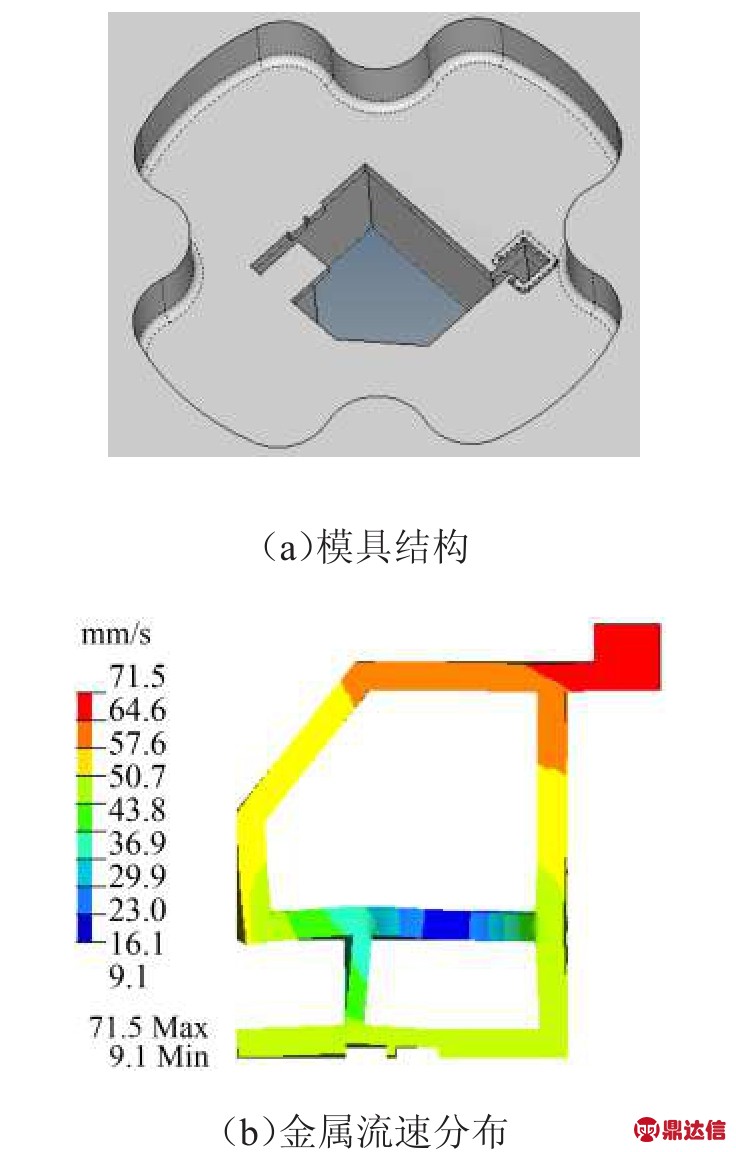
图5 初始设计阻流块后模具结构和金属流速分布
4次改进结果的速度差分别为28.2、17.4、20.0、20.6 mm/s,速度均方差分别为6.28、5.32、4.70、4.96 mm/s,如图7所示。
由图7可知,采用方案三得到的速度均方差和速度差的综合效果较好,故在方案三的基础上继续进行改进。
3.2 中部增设引流槽
通过对改进结果进行分析,发现型材中部由于芯模间隙小,金属流入阻力大,流速较慢,在此处增设引流槽以加快金属向中间流入的速度,增加引流槽后模具结构和模拟结果如图8所示。
目前已知的HPV大约有150个型,其中包括高危型和低危型HPV。低危型包括HPV6、 11、 30、 39、 42、 43、 44等;高危型包括HPV16、 18、 31、 33、 34、 35、 39、 45、 51、 52等。高危型HPV的持续感染是引发宫颈癌的主要病因。在我国,HPV16和18为最常见的两种感染型,这两类HPV也导致了70%以上的宫颈病变,因此目前的研究主要围绕这两类病毒进行[6]。
纵观所有计算机网络系统,都普遍存在一定的漏洞,理论上而言,几乎不会存在没有漏洞的计算机网络系统。事实也的确如此,无论是Windows系统还是Solaris或是Linux等各种系统,都没有办法彻底规避来自系统内部的冲击。当然,计算机更多的漏洞来自于后期用户的自行下载和安装软件的行为,许多不法分子利用这些系统漏洞趁机窃取用户的个人信息,再将这些个人信息进行转卖处理,以此牟利,给计算机网络的使用者带来许多的安全隐患。
增设引流槽后,挤出型材的速度差降为27.8 mm/s,速度均方差为6.96 mm/s。金属流速分布情况得到改善,但仍需进一步改进。考虑模具强度,不对引流槽进行加深、加大处理。
3.3 增加工作带长度
工作带是保证挤压零件形状、尺寸和表面质量的区段,其摩擦阻力可以调整金属流速,合理设计不等长的工作带可以提高型材断面各部分金属流速的均匀性,减少挤压过程中的附加应力和挤压后零件内的残余应力,防止型材变形与开裂。
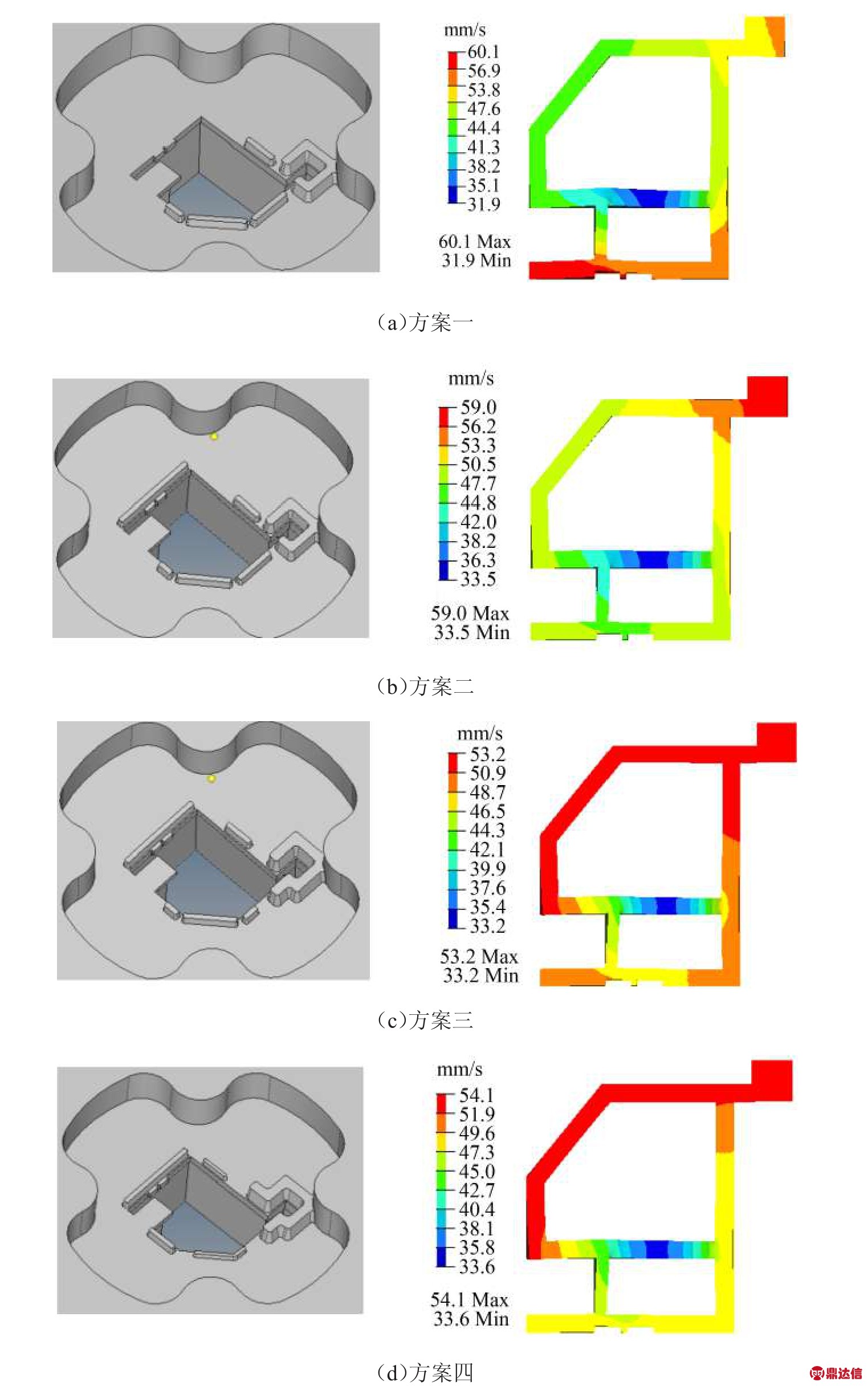
图6 改进阻流块后模具结构和金属流速分布
右上方悬臂处的原始工作带长度为5 mm,为了增大此处的流动阻力,将悬臂处工作带分别增加1、2、3 mm,得到的金属流速分布如图9所示。速度差和速度均方差随工作带长度变化如图10所示,随着悬臂处工作带长度的增加,速度均方差不断降低。工作带长度增加3 mm时,速度均方差降到2.05 mm/s,在合理范围内。综合型材生产质量要求和工作带对模具使用寿命的影响,不再对工作带进行延长。
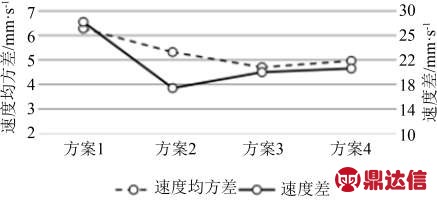
图7 速度差和速度均方差随阻流块变化
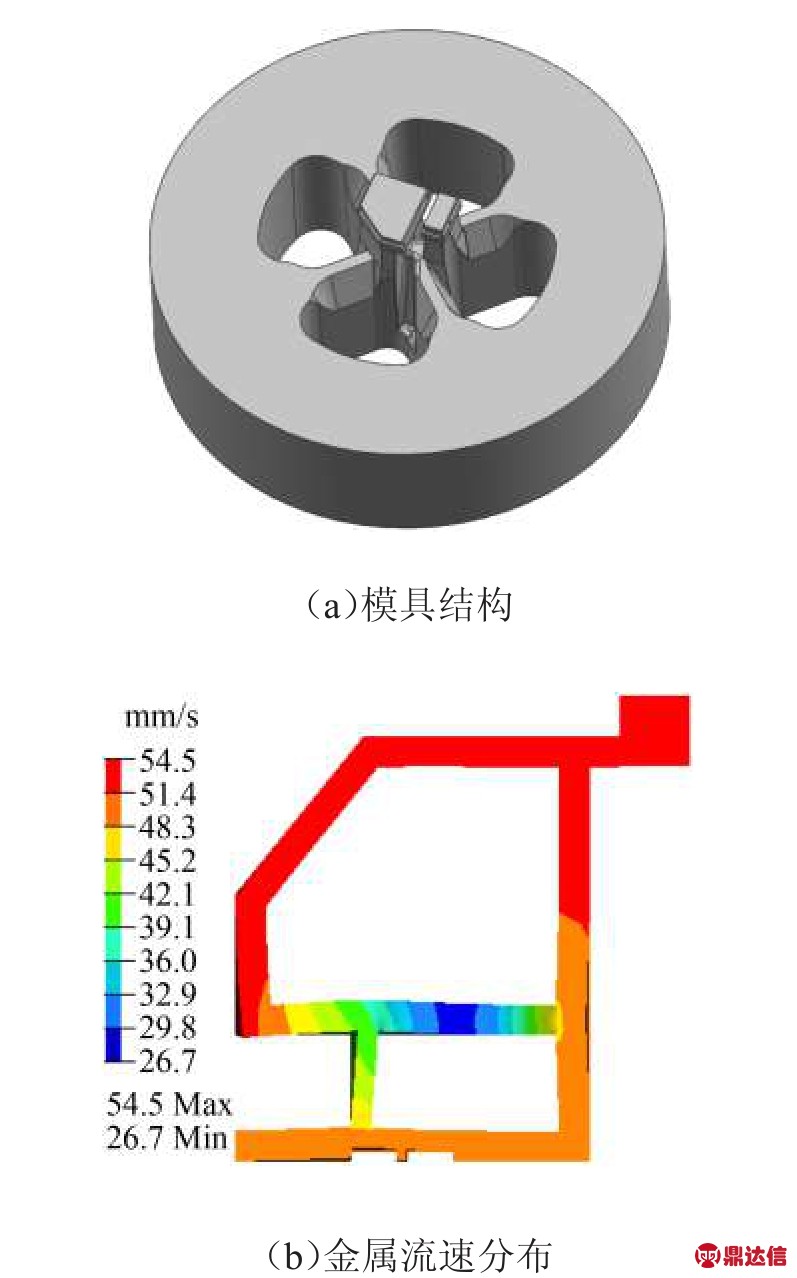
图8 增加引流槽模具结构和金属流速分布
4 结束语
通过对空心铝型材模具进行设计和有限元模拟,得出以下结论。
(1)型材出口流速分布是影响型材质量的重要因素,通过对其进行分析,可有效判断成型质量并实施进一步的改进方法。
(2)对于该零件,增设阻流块、引流槽和改变工作带长度都是有效的改进措施,能降低速度差和均方差,使出口截面速度更均匀。
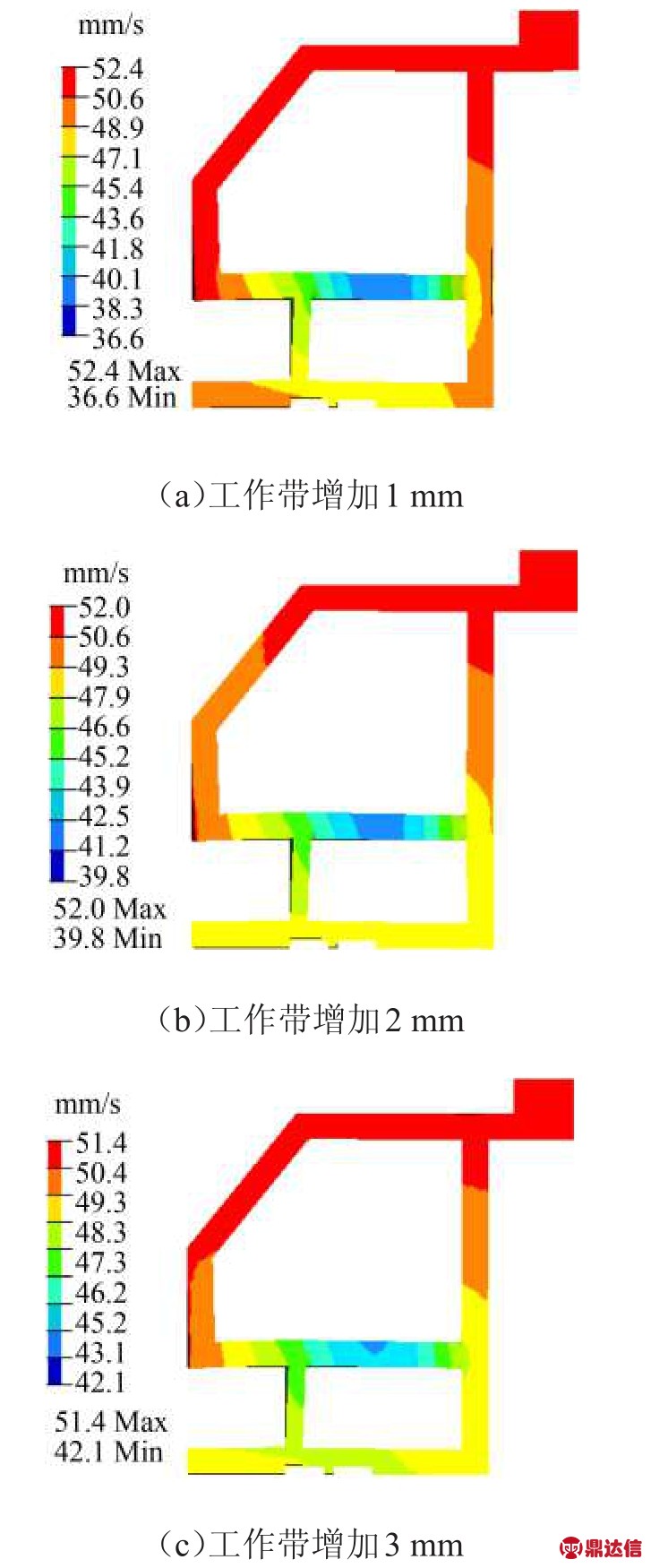
图9 增加工作带长度金属流速分布
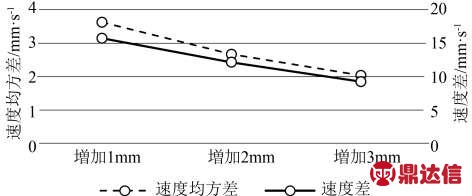
图10 速度差和速度均方差随工作带长度变化
(3)设置阻流块时,既要考虑其形状和大小,也要考虑数量和分布情况,二者兼顾才能得到更合理的设计。