1 模拟过程
1.1 型材断面
该断面为轨道交通车体型材,断面宽550 mm,高40 mm,上下表面为弧形,型材共有8个空腔,薄筋壁厚2 mm,型材截面如图1所示。型材的弧面间隙和壁厚尺寸控制是难点。该断面形状左右对称,对金属流动有一定的好处,均衡宽断面上每处的金属流速是模具设计时要考虑的重点问题。
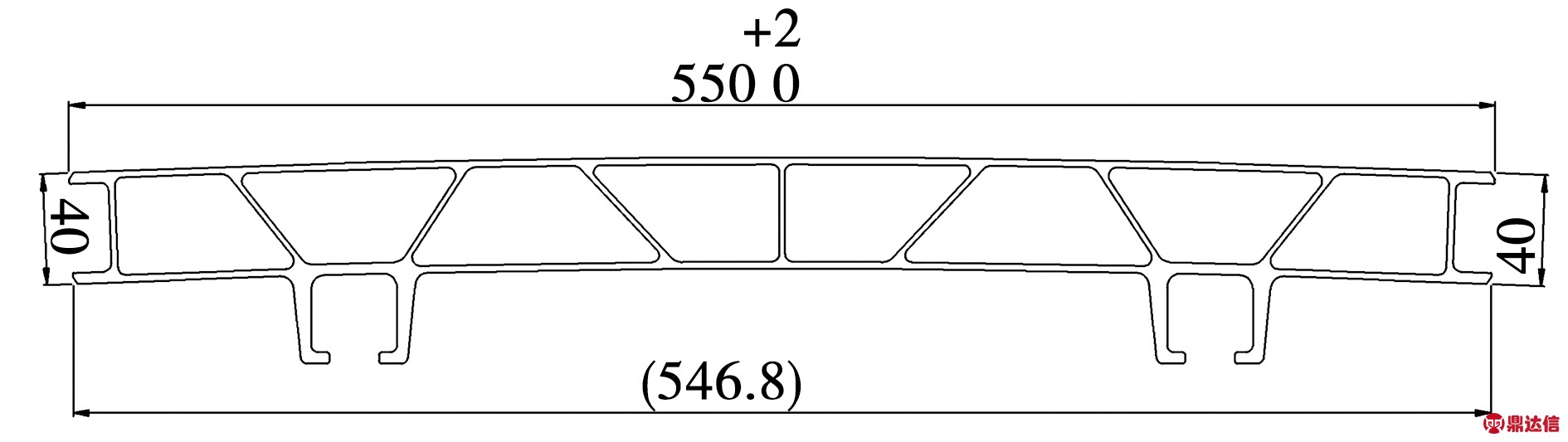
图1 型材截面
Fig.1 Cross-section of the profile
1.2 模具设计
1.2.1 设计方案的确定
根据该断面外形尺寸和模具设计经验,采用φ900 mm×320 mm规格模具,制定了两种模具设计方案,见表1。
表1 φ900 mm×320 mm规格模具的 设计方案
Table 1 Design scheme of the Φ900mm×320mm die

方案一二上模厚度/mm190200下模厚度/mm130120
考虑到上模厚度厚会增大挤压力,下模厚度薄对于抵消模孔变形较为不利。故确定选择方案一。
1.2.2 模具分流孔、分流桥的设计
从上面这个例子可以看出,根本不存在所谓的“理解偏差”,我们面对的实际上是这样一个亟待解释清楚的问题:人们明知道所指不是事物,但一提到所指,为何又自然而然地想到事物?
根据型材左右对称的特点,模具分流孔左右对称布置,上下不对称,在正中间直筋处布置了分流桥。模具两侧设计了分流孔,以保证供料充足。中部直筋位置下侧设计了分流桥,加大、加深了引流槽以保证直筋供料。分流孔和分流桥的设计如图2所示。
用200个勺子图像样本对神经网络进行训练,再用30个勺子图像验证该神经网络的检测效果。其中,30个勺子图像分别为:10个勺子同时具有边缘缺陷和表面缺陷;10个勺子只具有边缘缺陷;10个勺子只具有表面缺陷。检测结果如表1所示。
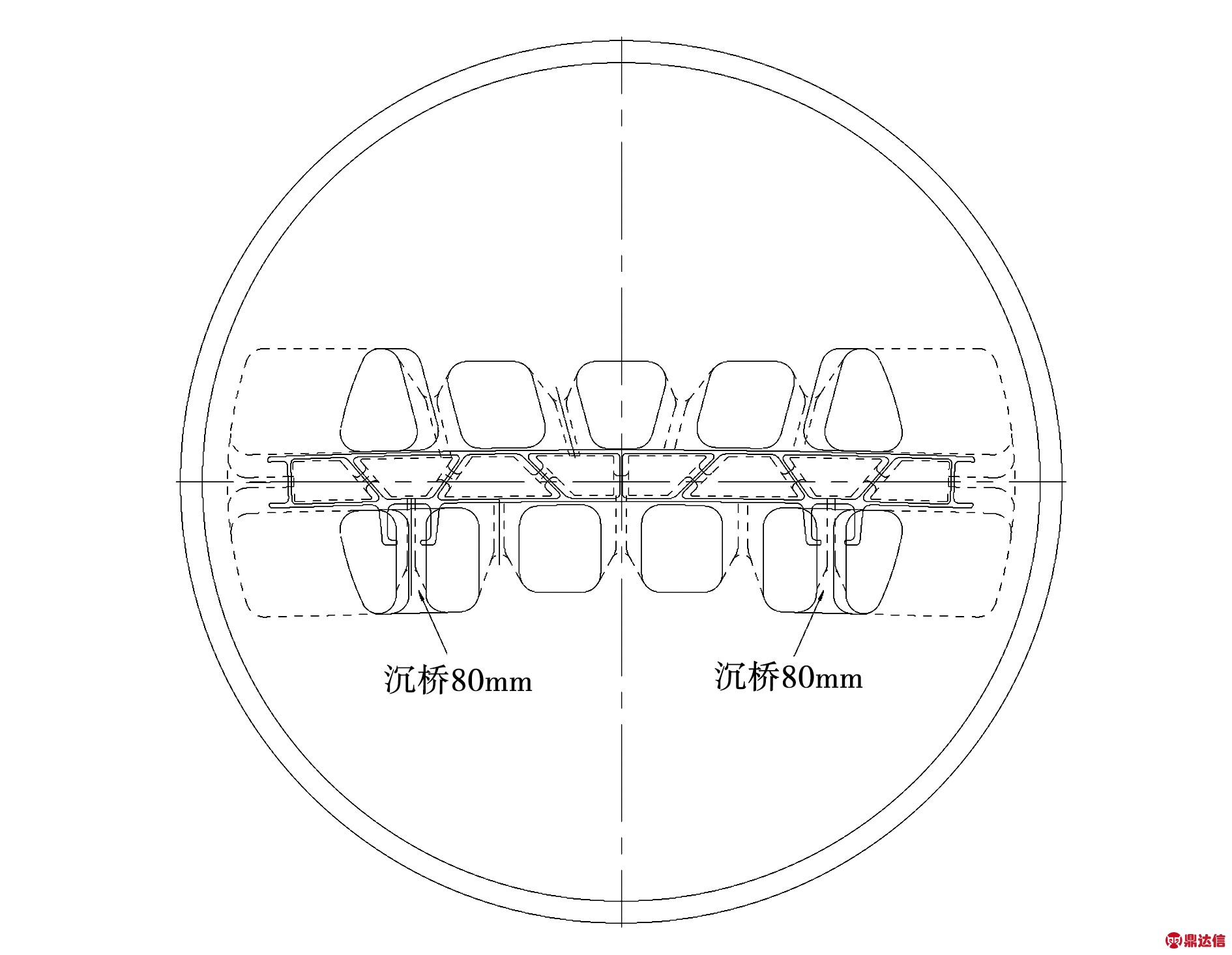
图2 模具上模
Fig.2 Upper Die
1.2.3 模具焊合室、工作带的设计
n—节点数目。
模具设计使用二层焊合室,具体形式见图3所示。模具工作带形式见图4。
根据阅读的深度,可以将阅读分为粗读和精读。除了课上要求的,教育部推荐学生必须要读的,需要精读的课文外,有些时候还需要学生广泛阅读一些书目。对于这些扩展学生视野的读物,学生则可以进行粗读。相反,对于一些经典,则需要学生反复阅读,不断咀嚼,这就是所谓的“精读”。
袁家骝生于世家,是袁克文的儿子,也就是袁世凯的孙子,但是因为父亲袁克文视金钱如粪土,挥霍无度,他们家中虽然衣食不愁,但已绝对谈不上富裕。
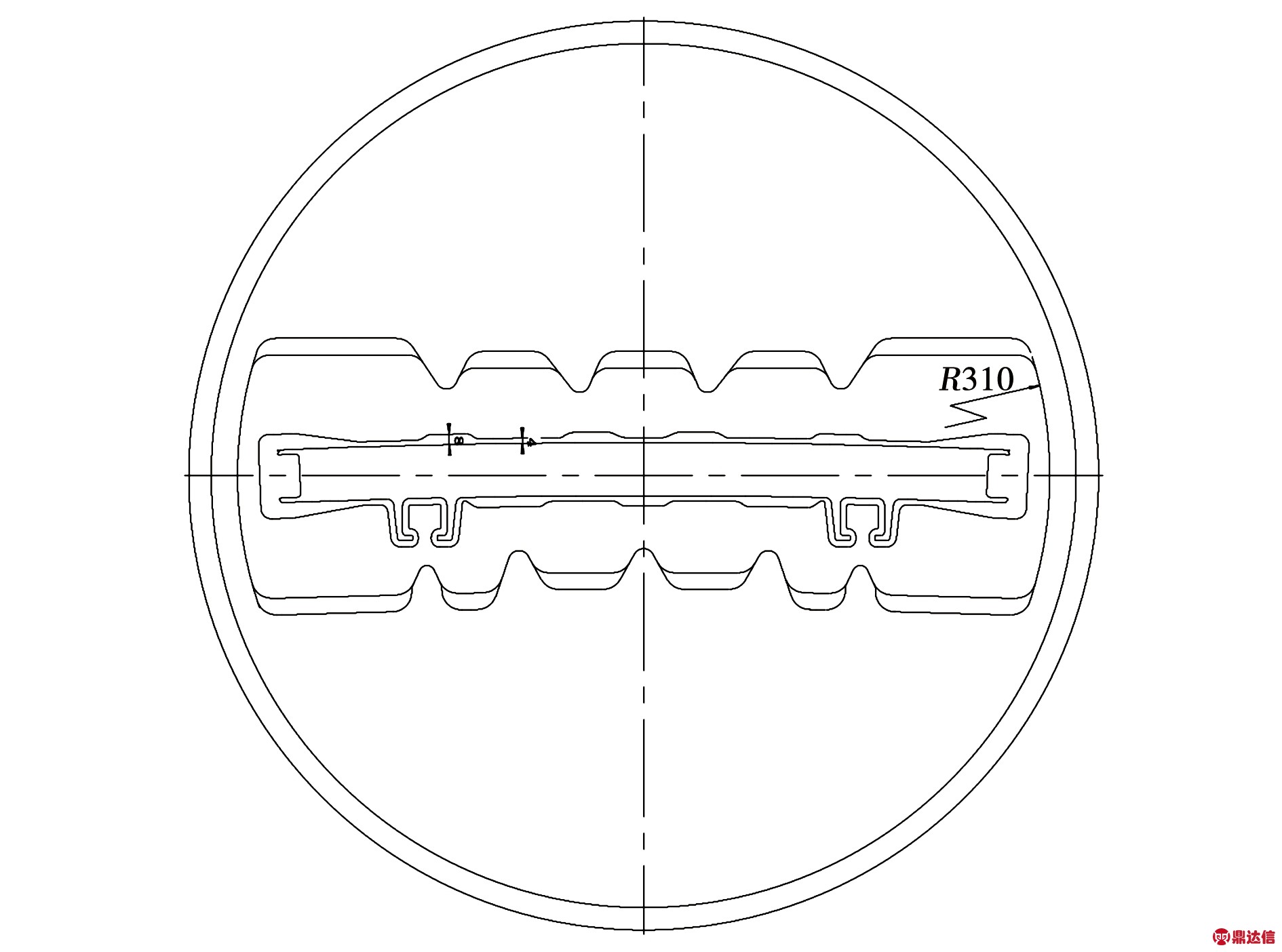
图3 模具下模
Fig.3 Lower Die
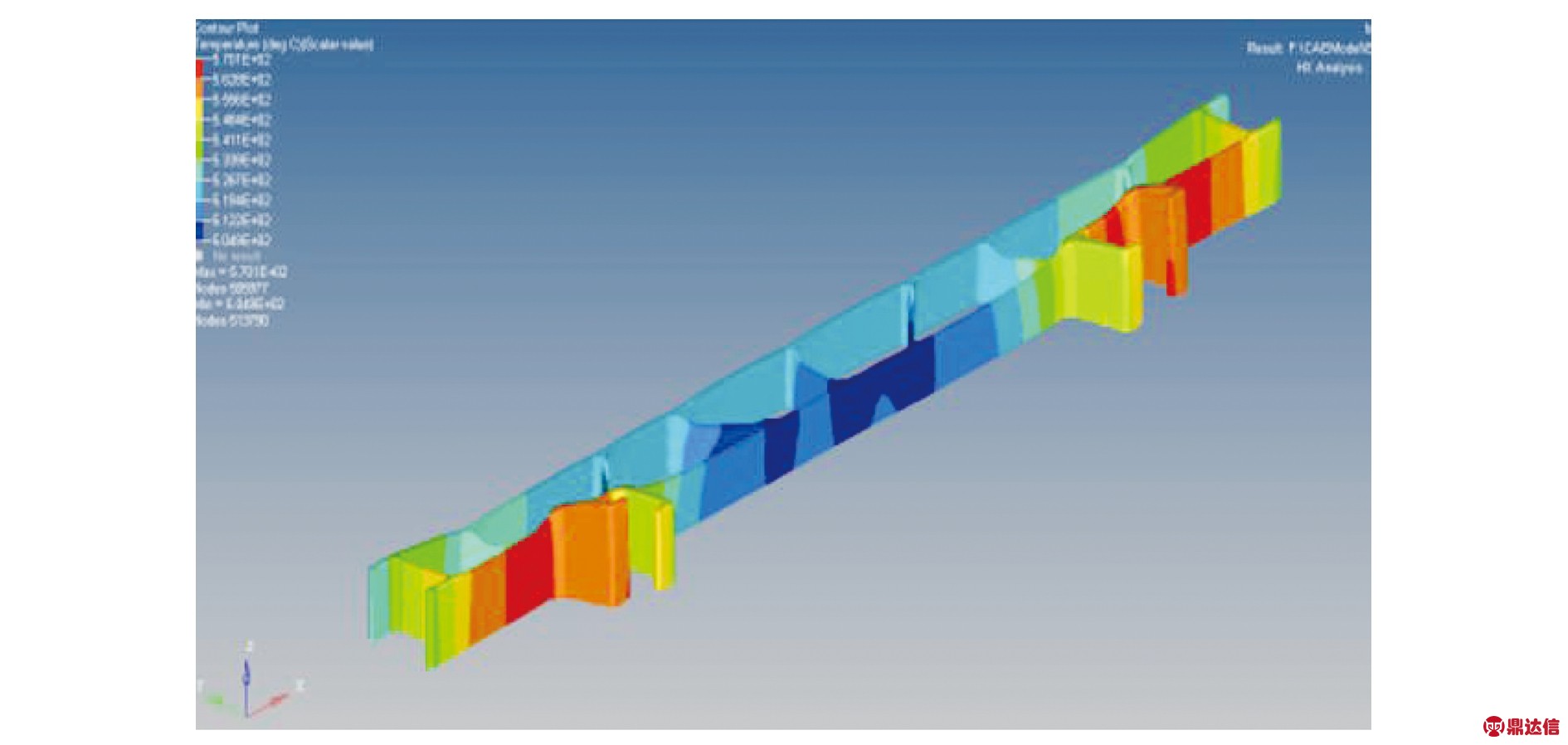
图4 模具工作带(一侧)
Fig.4 Die bearing (one side)
1.3 建立数值模拟分析模型
采用专业数值模拟分析软件HyperXtrude对型材挤压过程进行数值模拟分析,建立挤压材料流动区域的分析模型,具体由铸锭、分流孔、焊合室、工作带组成,如图5所示。
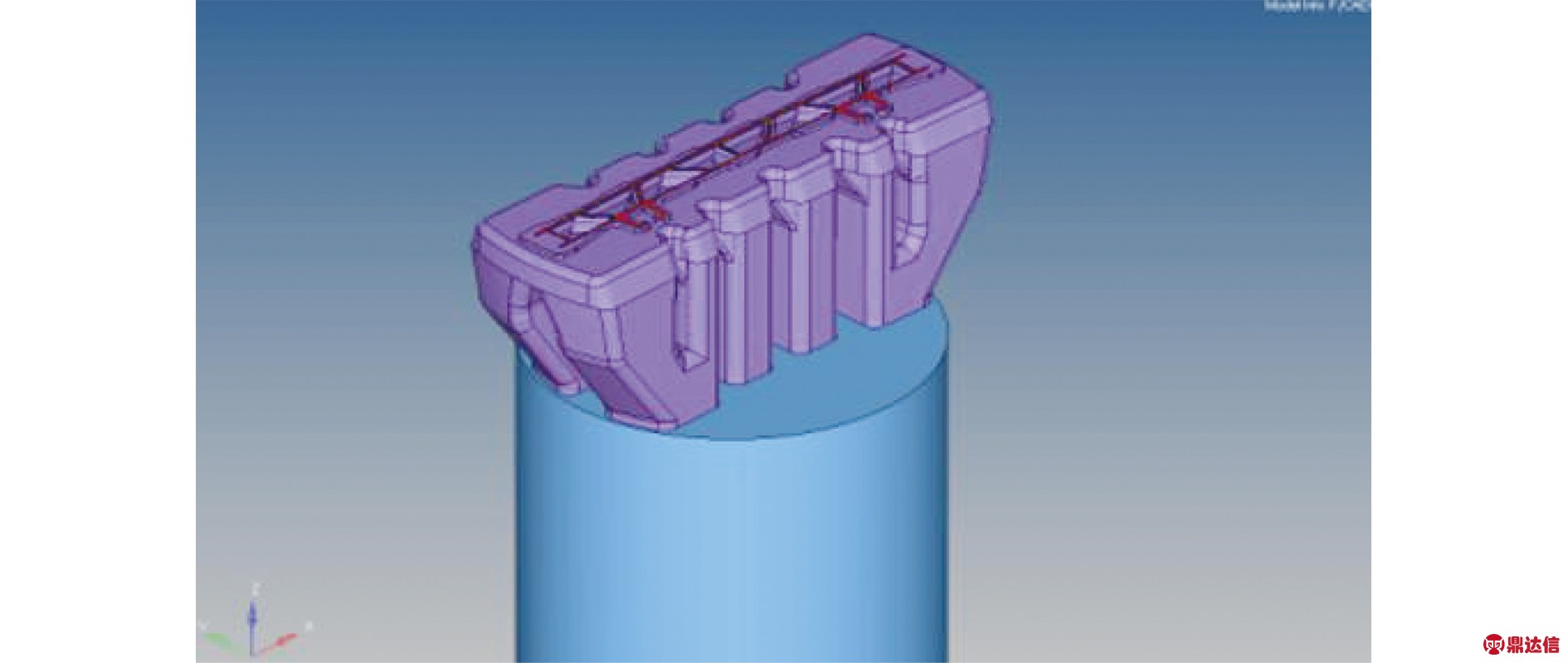
图5 模具分析模型三维图
Fig.5 3D diagram of the die analysis model
将建立的模具模型导入模拟分析软件,进行网格划分。划分网格时要保证工作带处最少4层网格,以便准确分析工作带处金属流动情况,型材高度至少为2倍工作带长,以便准确反映型材出口变形。最终分析模型的三维网格数量为240万个单元,如图6所示。
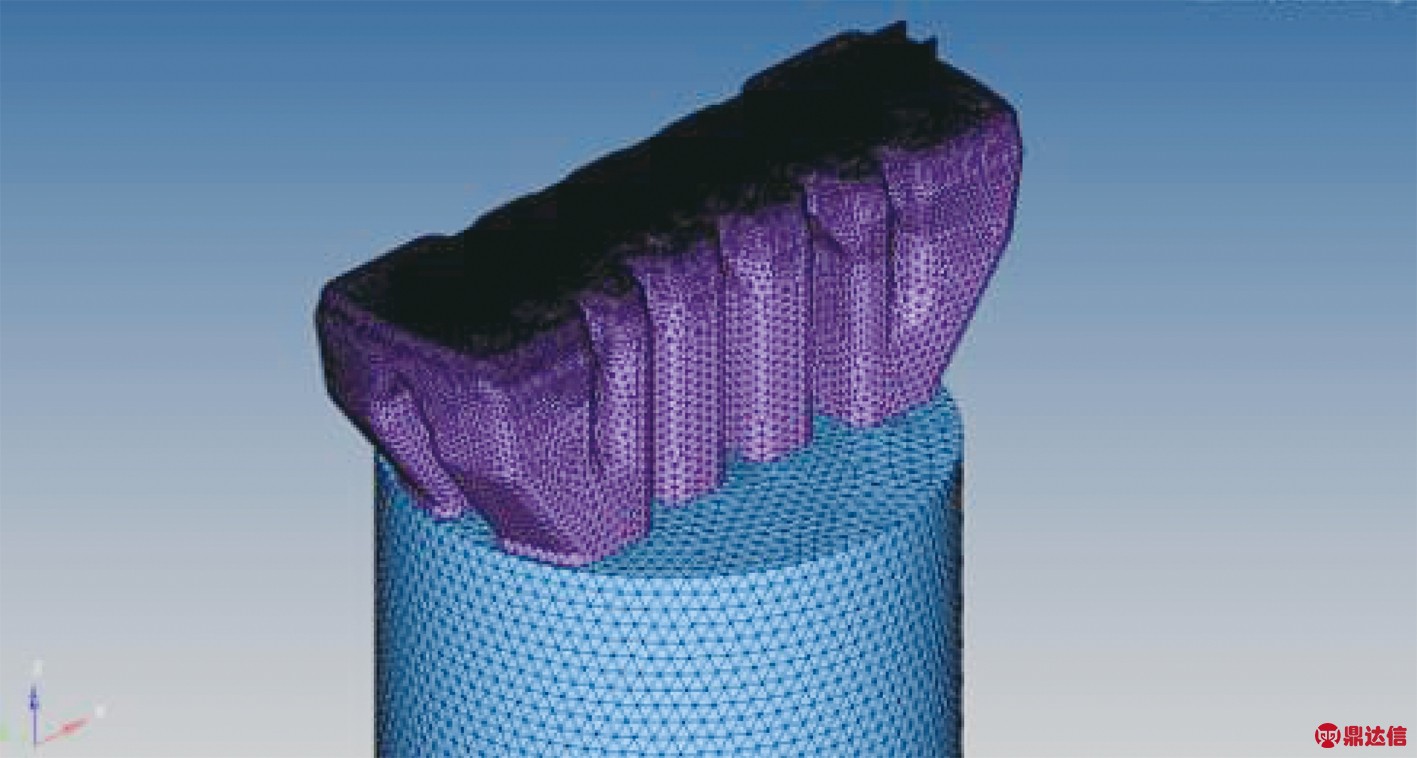
图6 模具分析模型网格图
Fig.6 Grid diagram of the die analysis model
1.4 仿真模拟结果分析
对生成的三维网格模型设定相关挤压工艺参数(如表2)后导入求解器进行求解运算。经过约14 h运算后,结果显示,模型的挤压力约74.7 MN,出口处各点流速见图7。出口处型材各点温度见图8。
表2 挤压模拟工艺参数
Table 2 Simulation parameters of the extrusion process

型材代号合金-状态挤压系数铸锭温度/℃铸锭规格/mm挤压速度/(mm·s-1)模具温度/℃EDSS-002156005A-T633.2500Φ450×10001.5470
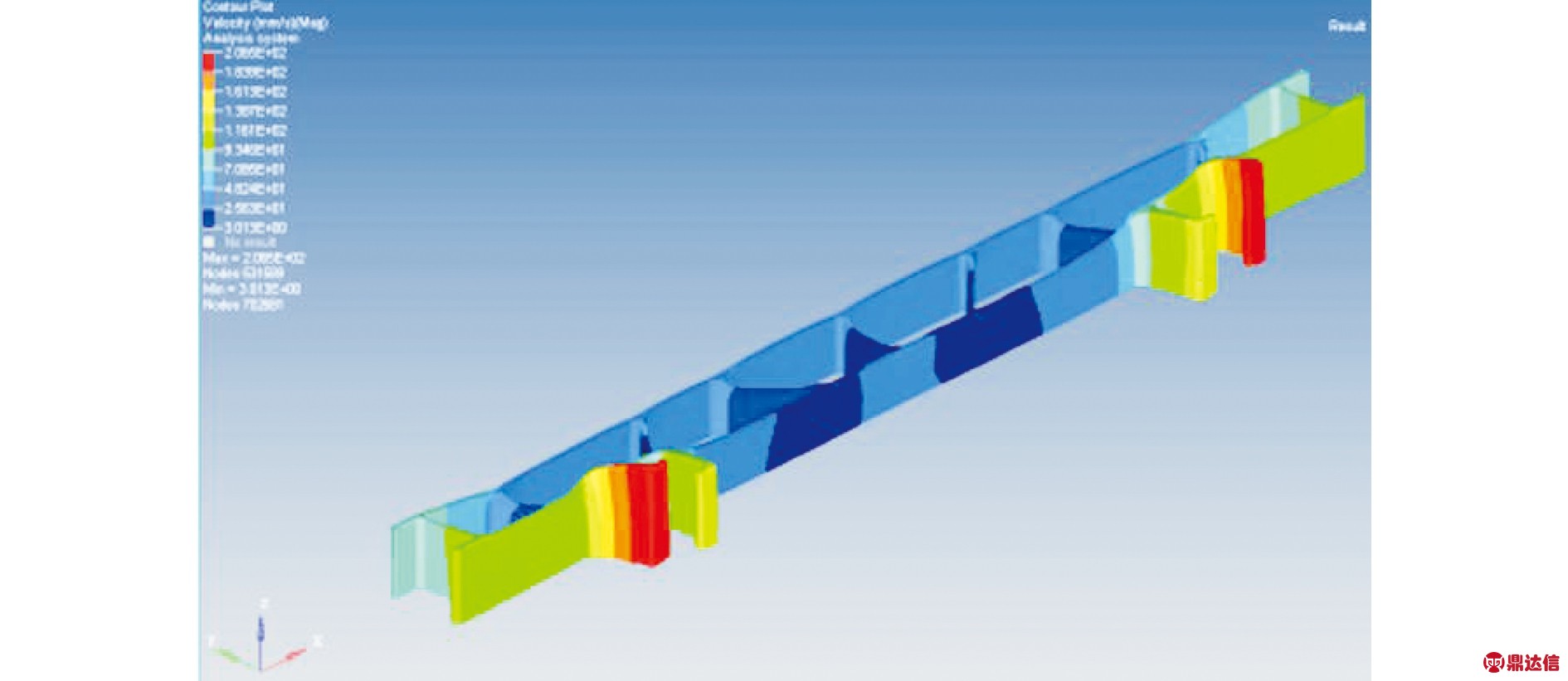
图7 模拟挤压出口处流速图
Fig.7 Diagram of outlet velocity in extrusion simulation
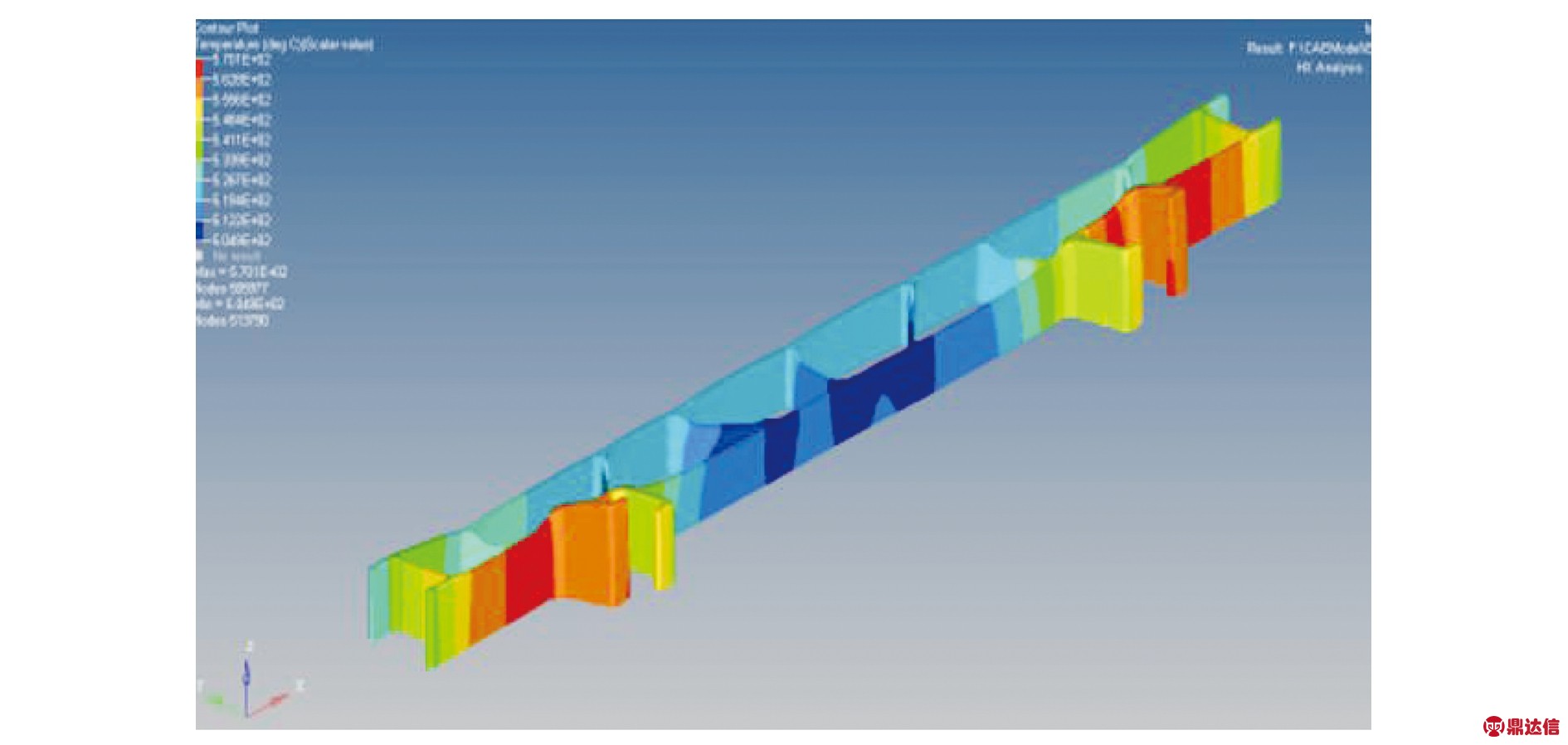
图8 模拟挤压出口温度分布
Fig.8 Diagram of outlet temperature distribution in extrusion simulation
在挤压成形过程中,型材出口断面速度是否均匀,直接影响型材的质量。如果型材截面上的各部分金属挤出模孔时速度不均匀,型材会产生扭拧、波浪等缺陷,甚至会损坏模具。因此,材料流动状态对于挤压生产至关重要。为了准确地描述型材截面上的速度均匀程度,选取金属流速均方差Fsdv 作为判断流速差异大小的依据:
本次论坛围绕“创新引领科技发展、大数据助推资源共享”主题,以长江经济带11省(市)科技资源共享机构为依托,面向全国推动科技资源跨区域共享。在论坛会议期间举行了系列签约活动,作了《逐渐睁开的中国天眼》、《推进科技资源开放共享的工作进展和思考》等4个主题报告,组织了“企业服务面对面”和“科技资源共享助力长江经济带发展经验交流和举措研讨”两个分论坛。(编辑/任伟)
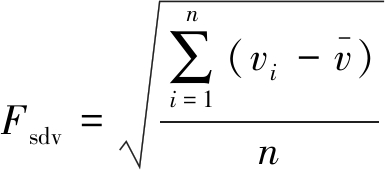
式中:
vi—考察截面上i节点处的流动速度;
v—所有考察节点的平均速度;
大型复杂的宽薄壁空心铝型材已在轨道交通列车车厢中广泛应用,该类型材具有外接圆大、宽厚比大、平面间隙要求严格、断面形状复杂等特点,给模具设计带来较大的困难。挤压模具设计不良容易导致挤出的型材出现拉裂、波浪、扭拧、弯曲和焊合不良等缺陷,严重时不能成型[1]。近年来,金属塑性成型的数值模拟技术在型材挤压加工领域得到广泛应用。采用数值模拟技术,可以预测跟踪金属的流动行为,判断挤压过程中可能出现的缺陷;根据型材的形状和金属的流动规律,进行模具结构优化和工艺参数调整,从而提高模具设计的质量和效率。文献[2]对空心铝型材的挤压成型过程进行了仿真模拟。文献[3]以壁厚为0.8 mm的薄壁铝型材为例,对挤压模具设计及挤压工艺进行仿真模拟,实现了虚拟试模。文献[4]对空心带弧度异形型材初始模具设计进行数值模拟。本文作者对宽展薄壁轨道交通型材模具方案进行了设计,采用基于ALE算法的HyperXtrude模拟分析软件,对宽展薄壁轨道交通型材的挤压过程进行了模拟分析,并将模拟结果与模具实际试模情况进行对比,验证了模拟结果的准确性和可参考性。
Fsdv 越小,金属的挤出速度越均匀,型材变形越小,质量越好;反之,挤出型材变形就越大,难以满足质量要求。
通过图7可以看出,型材两侧的流速较中部快(颜色越深流速越快)。其中型材槽口红色区域流速最快,最大值为20.6 mm/s。型材中部筋处流速最慢,最小值为3.0 mm/s。
通过图8可以看出,型材两侧的流速快,温度也高,最高为570℃。型材中部温度较低,最低为505℃。
2 模具上机试模验证
分别从突破挤压力、稳定挤压力、试模料头料样、型材尺寸等方面对两种模具的上机试模情况进行对比。试模工艺参数与表2的相同。
模具试模突破挤压力约78 MN,稳定挤压力约64 MN。可以看出,不论是突破挤压力还是稳定挤压力,都相对较高。这与自制模具分流孔数目多、桥高度较高有一定关系。另外模具在模拟挤压时的挤压力计算结果为74.7 MN,与实际值78 MN比较接近,说明模拟挤压结果较好地反映了挤压力的情况,试模压力曲线见图9。试模挤压料头、料样见图10和图11。
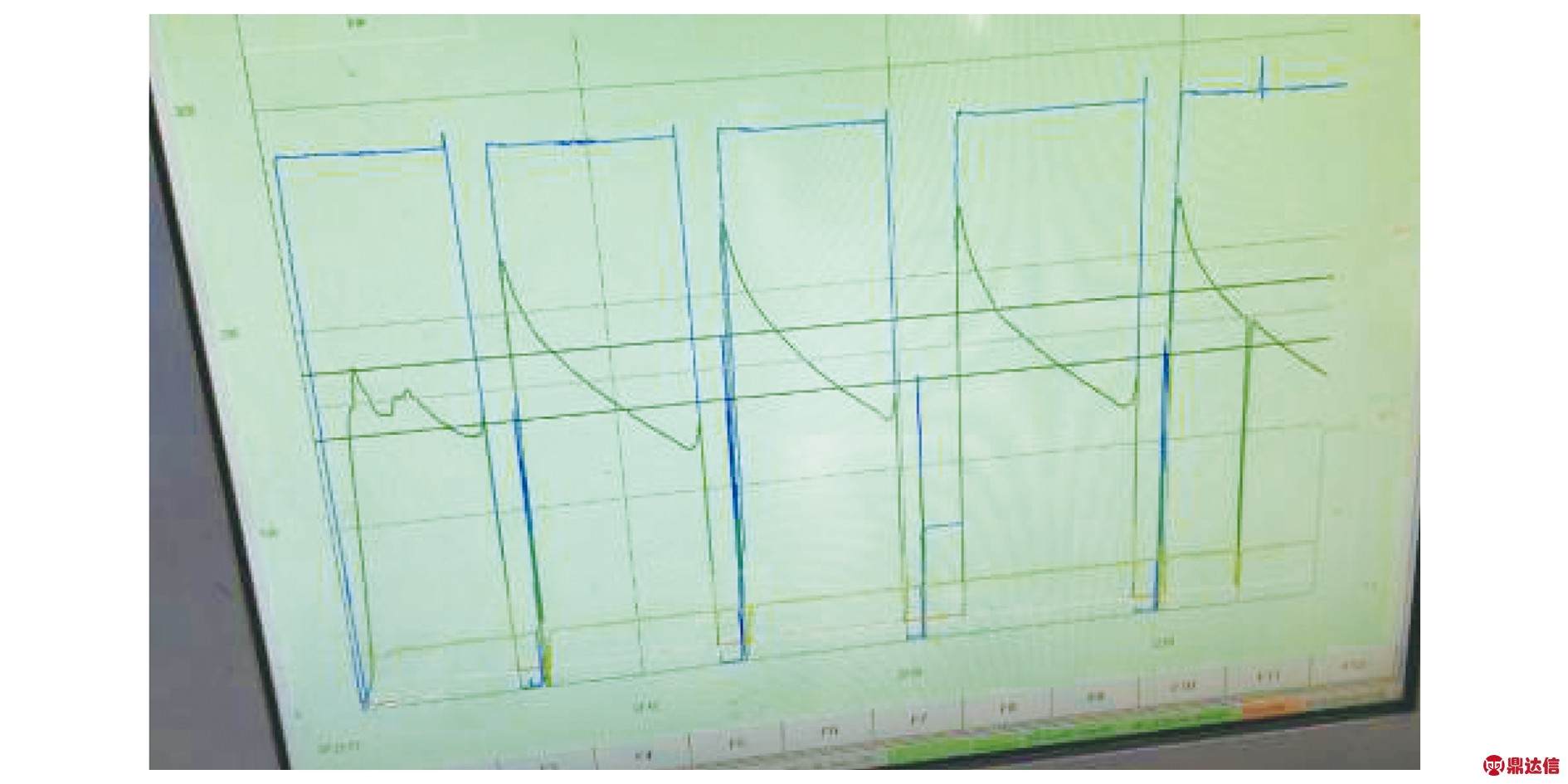
图9 试模挤压压力曲线图
Fig.9 Curves of extrusion pressure in die trial
模具的试模料头反映出模具出口各处的金属流速。由图10和图11可知,模具中间部位流速慢,两侧金属流速快,造成型材两侧挤向中间。T形槽部分流速快,造成型材下表面向上翻,上下表面间隙不良。这与模拟挤压的运算结果是一致的。
第一,资源空间。确定厦门市资源空间容量方面能够容纳旅游者的最大值。第二,基础设施。确定厦门市旅游设施以及基础设施能够承载旅游者的最大值。第三,社会心理。确定厦门市原住民在心理上能够接纳旅游者数量的上限。
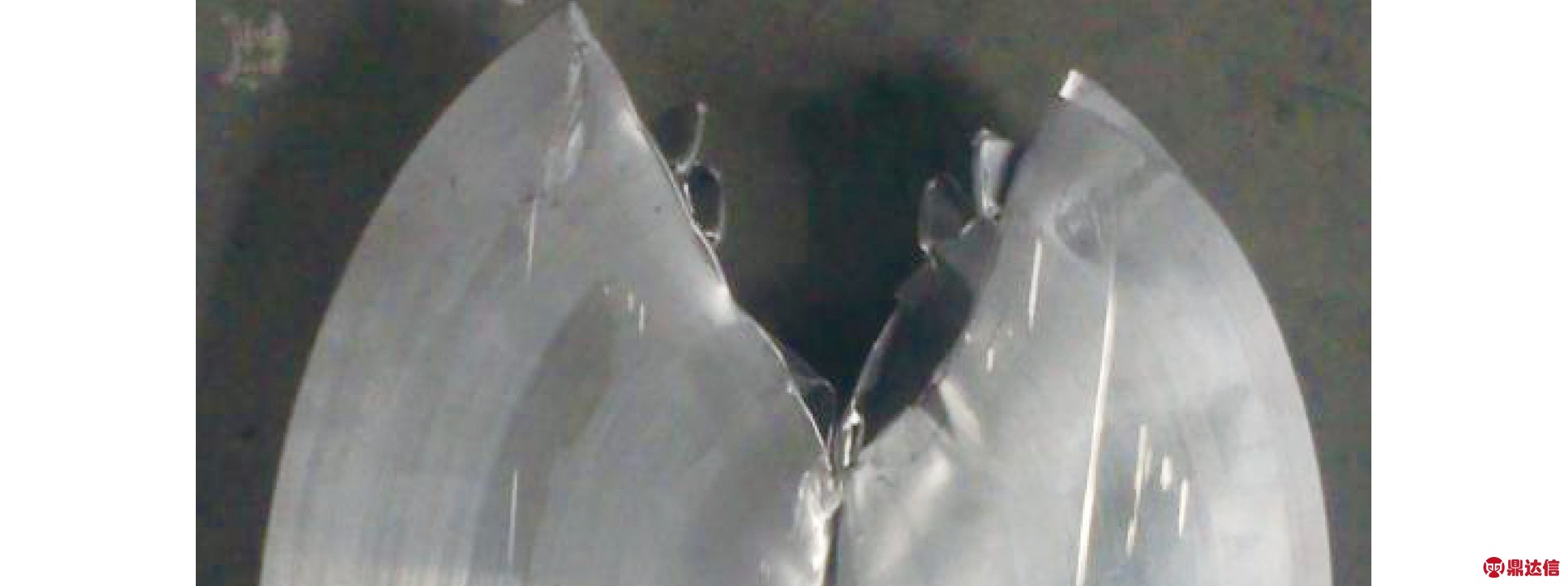
图10 试模挤压料头
Fig.10 Profile head in die trial extrusion
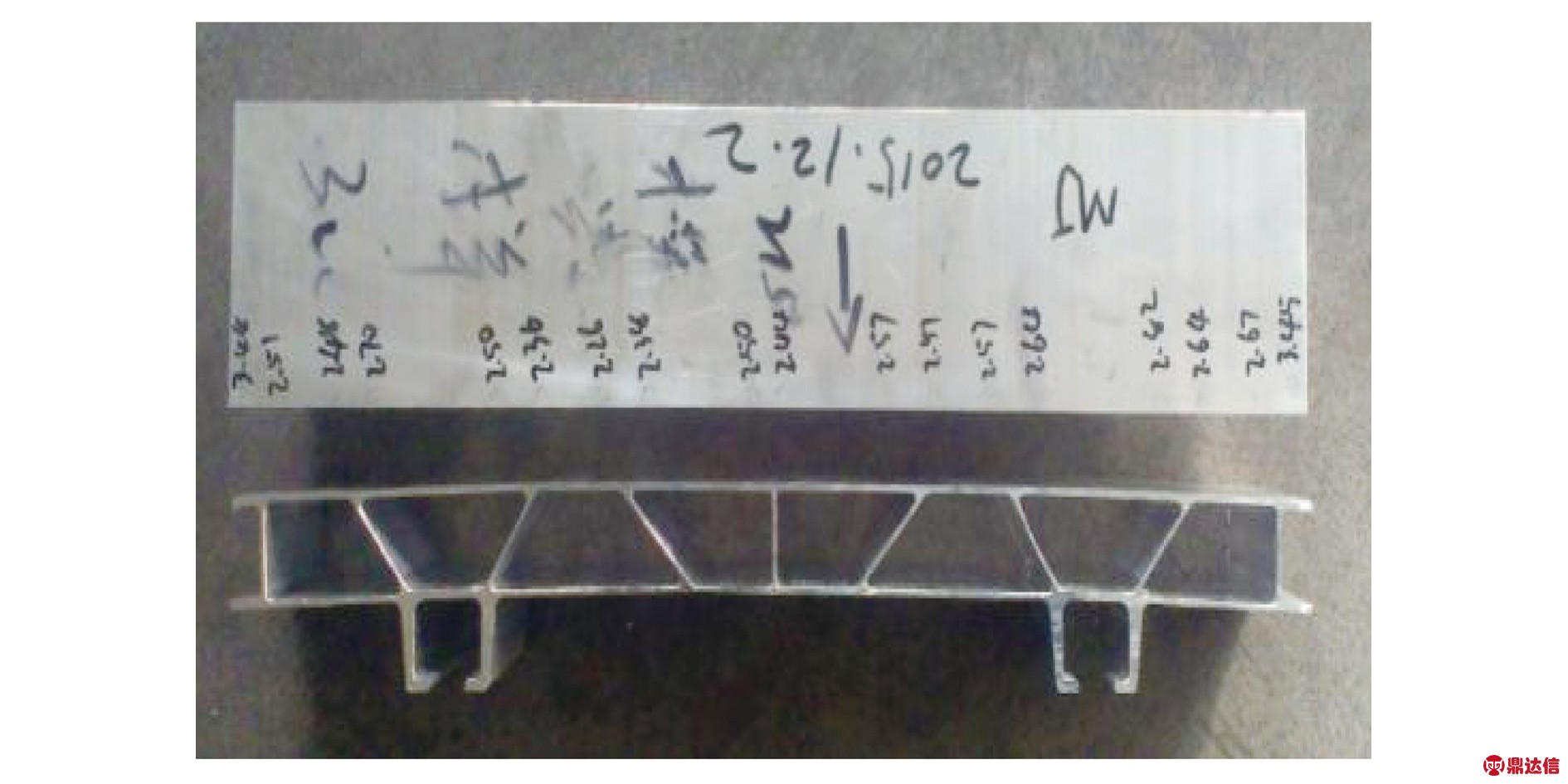
图11 试模挤压料样
Fig.11 Profile sample in die trial extrusion
3 结 论
1)分流孔数目和分流桥的高度与模具上机挤压力有直接关系,一般情况下,分流孔越多、分流桥越厚,挤压力越大。
2)基于ALE算法,可以很好地描述稳态挤压阶段金属的流动情况。
3)数值模拟结果与实际上机生产具有较好的一致性,表明数值模拟可以为扁宽、薄壁、空心、弧形大型铝合金型材挤压模具结构设计提供指导。