摘 要:针对某车型排气尾管噪声不达标的问题,应用流体动力学仿真分析方法,计算排气消声器内部流场,分析尾管噪声过高是由于消声器内部结构设计不合理产生的气流再生噪声。根据问题真因,进行方案优化,通过对比分析,优化后方案改善明显。同时,为了保证排气系统的声学性能,应用GT-POWER软件搭建单进双出传递损失分析模型,分析优化后方案的消声能力。通过尾管噪声测试,优化方案噪声水平明显降低,并满足目标要求。
关键词:排气消声器;气流再生噪声;模型简化;计算流体力学;声学性能;传递损失;结构优化
排气噪声是汽车车内噪声的主要源头之一,保证排气系统的高消声性能和低流动阻力,是消声器设计的关键[ 1]。以往的消声器设计主要根据设计者的经验和试验,这种方法的针对性差,而且设计周期长、成本耗费大。随着CAE手段的不断进步,三维CFD软件及GT-POWER软件的应用,为消声器结构的优化提供了有力的手段[ 2]。本文针对排气尾管噪声不达标的问题,进行CFD流体动力学仿真分析,查找问题真因,完成方案优化,并用GT软件评估优化后方案的消声能力,最终通过排气尾管噪声测试,设计的消声器满足目标要求。
1 排气尾管噪声问题分析
某车型进行排气系统开发,在试验车阶段,进行问题排查,针对三档全油门加速工况,进行排气尾管噪声测试,排气口总级和阶次噪声如图1所示,噪声总级在2500r/min以上超出目标值,阶次噪声满足低于总级10dB(A)的目标要求;通过图2分析,总级超出目标主要由于650Hz 、850Hz、1000Hz等多个频段处的气流噪声大,由此需要建立排气系统模型,进行仿真分析,确定气流噪声过高产生的根本原因;排气系统总体布置如图3所示。
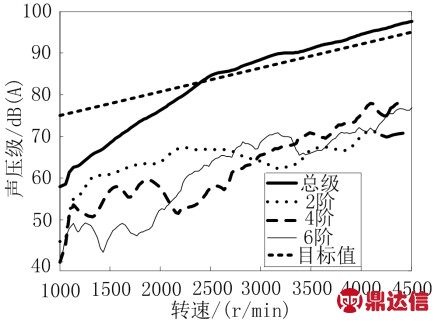
图1 排气噪声总级和阶次图
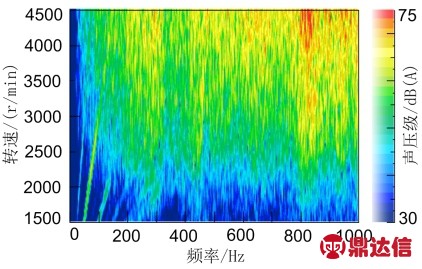
图2 排气噪声频谱图
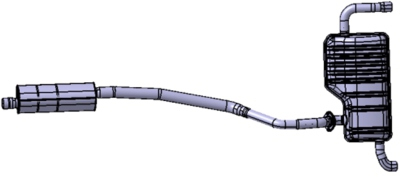
图3 排气系统布置图
2 建立消声器结构模型
本文利用GT-POWER软件中GEM 3D模块对消声器建模,针对各消声器内部结构对气流噪声原因进行初步分析。
GEM3D模型建模步骤为:(1)提取壳体、管路内表面进行网格划分,保存为stl格式的输出文件,以方便在GEM3D模块进行前处理;(2)导入处理好的stl格式文件,在此基础上根据实体参数,建立相应隔板、穿孔等结构,形成GEM模型。
2.1 前消声器结构建模
在图形界面下导入处理好的圆锥形壳体及管路stl格式,添加隔板I、II构成三个腔室,在管路上增加穿孔,同时在腔I、III建立吸声材料,属性采用玻璃丝棉,密度100Kg/m3,其消音棉的质量分别为400g、780g。
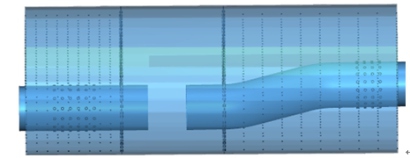
图4 前消声器结构示意图
2.2 后消声器结构建模
在图形界面下导入处理好的异型壳体及各管路stl格式,添加隔板I、II、III、IV,构成五个腔室;在隔板I、II、III和芯管上添加穿孔命令,芯管上穿孔数为100个,穿孔长度50mm;并在第一、三腔室内建立吸音材料,属性采用玻璃丝棉,密度100 Kg/m3,各吸音棉的质量分别为150g、1000g。
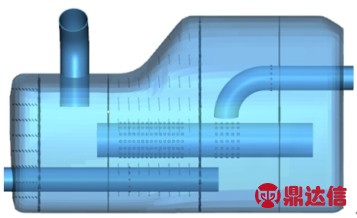
图5 后消声器结构示意图
通过消声器结构分析,前消声器和后消声器都加有吸声材料,并与我司其它车型消声器吸音棉添加质量对比,高频消声能力满足要求,由此判断气流噪声可能不是由于高频消声能力不足引起,需进行流场分析,找出消声器内部结构产生气流再生噪声的原因。
3 消声器流场分析及方案优化
气流再生噪声的声压级大小,通过软件定量计算存在局限性,但可针对消声器内部流场分布进行分析,评估排气消声器内部压力分布、马赫数大小以及内部是否存在明显涡流,从而找出问题真因。
3.1 网格划分
由于只有少部分气流会通过吸声材料,为了简化模型,加有吸声材料的腔体和管路的穿孔去除,并将排气系统冷端模型导入到前处理软件中,进行网格划分;流体分析要求网格质量,将主要网格尺寸设置为6mm,穿孔位置网格进行局部细化,网格模型如图6所示:
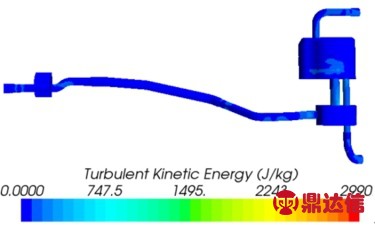
图6 排气系统网格模型
3.2 边界条件设置
假设消声器内部气体为稳态、可压缩的理想气体,应用标准k-ε湍流模型、连续性方程、动量方程、能量方程等控制方程求解[ 3]。
(1)进口:通过发动机台架数据,获取发动机最大转速时的质量流量,这里设为0.225kg/s;
(2)出口:设置出口为压力边界条件,绝对压力为一个标准大气压;
(3)壁面:设置为绝热且无摩擦的无滑移壁面。
3.3 真因分析
(1)排气消声器压力分布
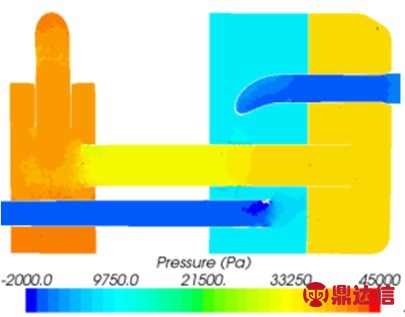
图7 排气系统冷端压力云图
通过流场分析,此套排气系统冷端压力损失为46.3KPa,如图7所示,压力由入口到排气尾口逐渐衰减,前消声器和主消声器之间的弯管有部分压降,由前消声器压力图8所示,副消无明显压降,由图9所示,主消声器第四腔管路打孔位置,
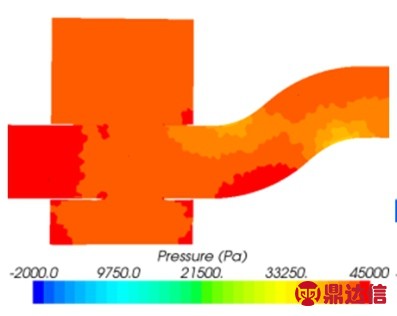
图8 前消声器压力云图
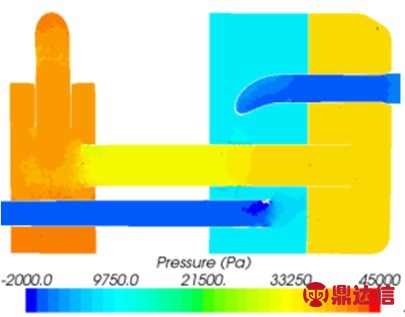
图9 后消声器压力云图
存在较大压降,使得排气背压明显增大,进而影响发动机效率。
(2)排气消声器马赫数分布
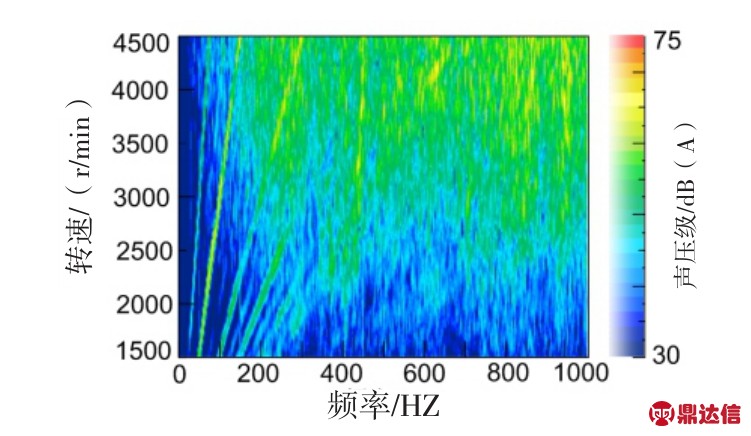
图10 排气系统冷端马赫数云图
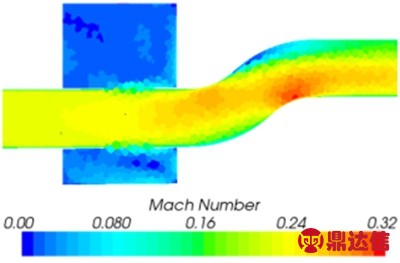
图11 前消声器马赫数云图
排气系统冷端马赫数分布,如图10所示,排气后消声器前管路,弯曲曲率过大,使得局部马赫数偏高;前消声器马赫数如图11所示,内部弯管处马赫数偏高,但第三腔为简化模型,加有吸音棉,不作优化;后消声器马赫数如图12所示,第四腔处的芯管穿孔位置,是排气主流道,但由于穿孔个数较少,使得马赫数偏高;尾管截面如图13所示,排气尾口采用的是扁口形状,使得排气流速分布不均,局部马赫数偏高。
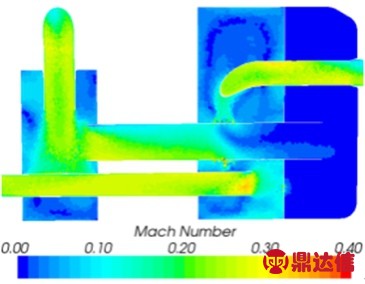
图12 后消声器马赫数云图
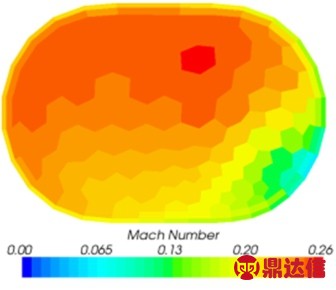
图13 扁口尾管马赫数截面图
(3)消声器内部湍动能分布
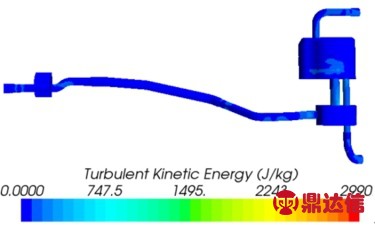
图14 排气系统冷端湍动能云图
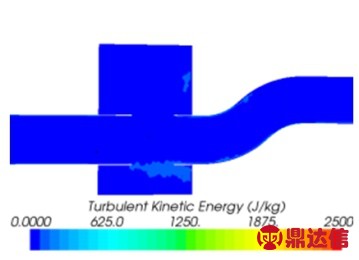
图15 前消声器湍动能云图
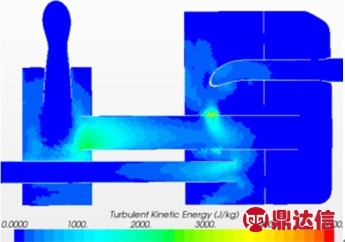
图16 后消声器湍动能云图
由图14和图15所示,排气系统管路和前消声器无明显湍流,湍动能较小;后消声器湍动能如图16所示,芯管穿孔位置湍动能最大,存在较大湍流,易产生气流再生噪声。通过以上分析,同时综合考虑底盘布置空间的限制,确定针对后消声器芯管打孔位置和排气尾管形状进行优化。
3.4 方案优化
(1)排气尾管形状优化
将扁口尾口形状改为圆口形状,进行马赫数对比,圆口尾管截面如图17所示,圆尾管最大马赫数分布区域较小,并且扁口左右尾管平均马赫数分别为0.24和0.2,圆口左右尾管平均马赫数为0.2和0.18。
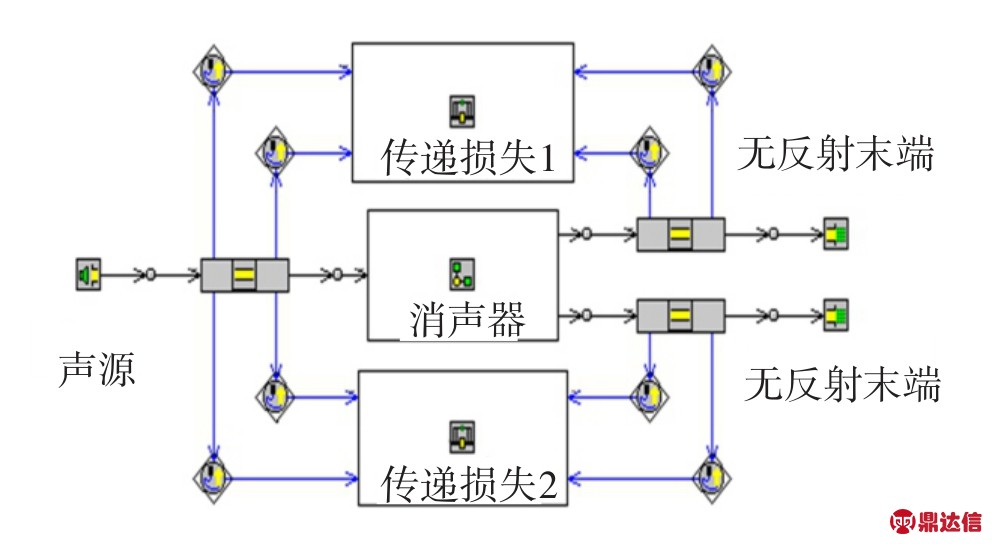
图17 圆口尾管马赫数截面图
(2)后消声器芯管穿孔方案优化
将第四腔芯管穿孔数由100个改为200个,穿孔长度由50mm改为100mm;通过流体分析,排气冷端压力损失为30.7KPa,与原方案对比,压力损失降低15.6Kpa;通过图9和图18对比,优化方案后消声器第四腔芯管和腔体的压力损失降低;通过图12和图19对比,优化方案第四腔芯管穿孔处马赫数降低明显;通过图16和图20对比,优化方案第四腔芯管穿孔处湍流强度降低;综上所述,优化方案改善明显,由于消声器内部结构更改,需进一步评估消声器消声性能,由于消声器内部吸音棉的质量无减少,高频消声性能不会产生明显变化,特主要考虑低频的消声能力。
4 后消声器传递损失分析
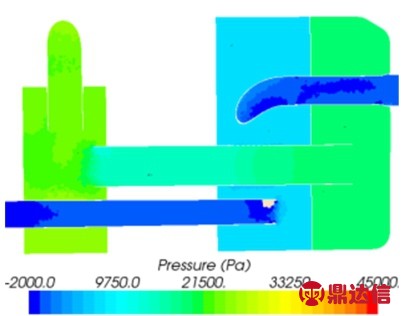
图18 优化后消压力云图
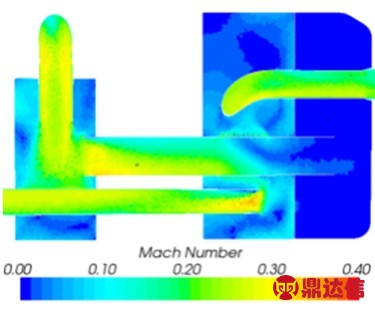
图19 优化后消马赫数云图

图20 优化后消湍动能云图
对上述优化方案进行声学分析--传递损失分析,传递损失分析有两种方法:一、应用三维方法,计算较为准确,可进行消声器高频消声能力的准确预测[ 4][ 5],但建模和计算时间较长;二、应用一维频域和时域方法,未考虑非平面波效应,只适用于低频消声能力预测,本文应用一维GT-POWER软件,在前面建好的模型基础上,考虑排气温度和流速的影响 [6],进行后消声器低频消声能力预测,建立的后消声器传递损失分析模型如图21所示。
后消声器是单进双出口的结构,设置两个无反射末端,并增加传递损失计算模块和压力监测传感器,计算出每个消声器出口的传递损失,并可查看每个出口的传递损失计算结果。
优化前后传损分析对比,如图22所示,优化方案80Hz之前的消声量降低1dB-3dB,120Hz-150Hz的消声能力增加约8dB,通过与原始方案尾管噪声测试数据对比,设计方案消声能力满足要求。
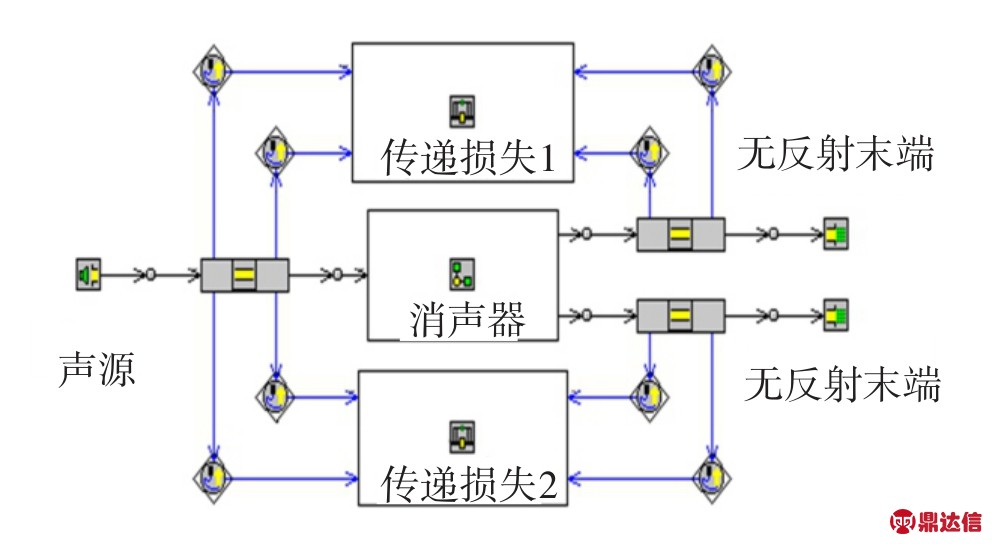
图21 传递损失分析模型
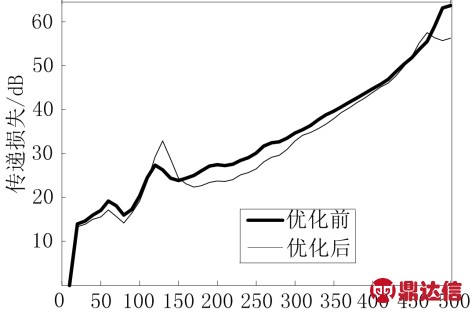
图22 优化前后传递损失分析结果
5 方案验证
优化前后排气尾管噪声总级和阶次对比,如图23所示,在2500r/min以上,优化方案总级降低5dB(A)以上,满足目标要求;在1500r/min以下,二阶升高2dB(A),其原因为尾管口形状变圆孔,扩张比降低,消声量也随之降低,但是降低不明显,同时经主观评价此处声压级的变化对车内影响不大;3500r/min-4000r/min降低2dB(A)-8dB(A),满足二阶目标要求;通过图24显示,在2500r/min以上,高频气流噪声降低明显,最终设计方案具有较高的消声能力和较低的压力损失。
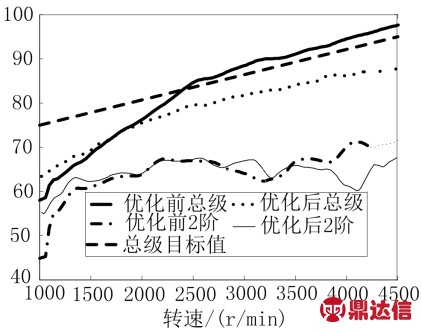
图23 优化前后总级和阶次对比图
6 总结
针对某车型排气噪声不达标的问题,应用流体和声学仿真分析方法,查找真因并完成方案优化,最终得出以下结论:
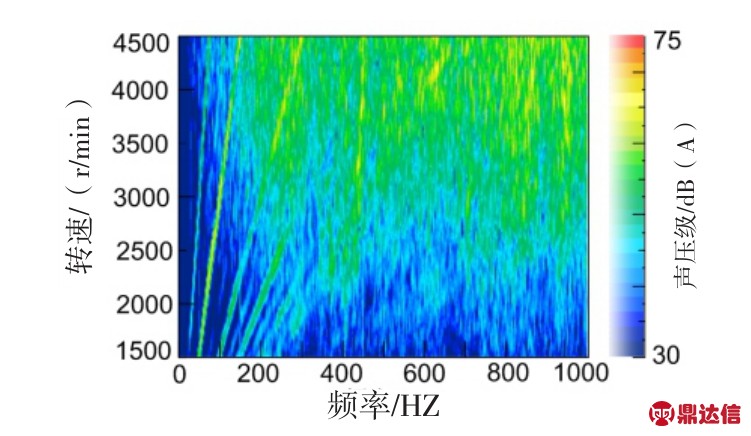
图24 优化后噪声频谱图
(1)排气气流噪声大,主要由于主消声器第四腔芯管穿孔数量少和尾管采用扁口形状;(2)气流噪声大的位置,压力损失增加,引起排气系统背压增大;(3)降低气流噪声,会引起消声器消声能力发生改变;(4)通过增加芯管穿孔个数和长度,并改变尾管形状,气流噪声得到较大改善;(5)搭建的传递损失分析模型,可进行单进双出消声器低频消声能力对比和预测,具有较高精度。