摘要:为优化摩托车消声器的设计,利用CFD技术分析多种带多孔管消声器的流场速度、湍动能和压力分布,并计算这些方案的压力损失.结果表明:压力损失随着小孔面积比增大而快速下降,小孔面积比在2.5以上时较合适;多孔管堵头开孔对减小压力损失无明显影响;最大的压力损失位于插入管Ⅰ部位,而非多孔管处,故插入管Ⅰ的直径应大于其他3根管的直径.
关键词:摩托车; 消声器; 多孔管堵头; 流场; 压力损失;k-ε方程
0 引 言
发动机的排气消声器不仅起消声作用,还对发动机动力性能有直接影响.[1]在排气消声器中,为减少流体阻力和增大消声效果,通常会在排气管管壁上设计许多小孔,声波在通过这些小孔时,会有一定的能量衰减.小孔数量的多少对排气阻力和消声效果都有影响:当小孔数量过少时,排气阻力较大;而当小孔数量过多时,又会影响消声效果.
考查摩托车消声器的内部结构可发现,多孔管的穿孔率差异较大,而且多孔管堵头上也有开孔和不开孔2种设计.胡效东等[2]研究单膨胀腔结构的流场,张先腾等[3]和苗勇毅等[4]研究柴油机和汽车消声器的流场.以上研究的对象都与本文研究的摩托车消声器结构差异很大,所以该摩托车消声器小孔数量到底多少才合适、堵头是否应该开孔均无法参照.为优化这种典型消声器的设计,采用流体动力学计算软件FLUENT进行流场分析.
1 数值计算过程
1.1 三维几何模型建立
以一款125 ml排量摩托车常见的消声器结构作为研究对象,见图1.消声器三维模型在UG NX中创建.该消声器由3个膨胀腔组成,排气管插入消声器筒体内部,在排气管的尾部焊接多孔管,多孔管的尾部用堵头封住.所有部件壁厚均为1.2 mm,4根管的内径都为19.6 mm,多孔管中的小孔和堵头上的小孔的直径都为5 mm.为表征多孔管上小孔的数量,定义“小孔面积比”为所有小孔的流通面积之和除以主管的流通面积,例如,当小孔面积比为1.5时,即意味着小孔的总流通面积是主管流通面积的1.5倍.
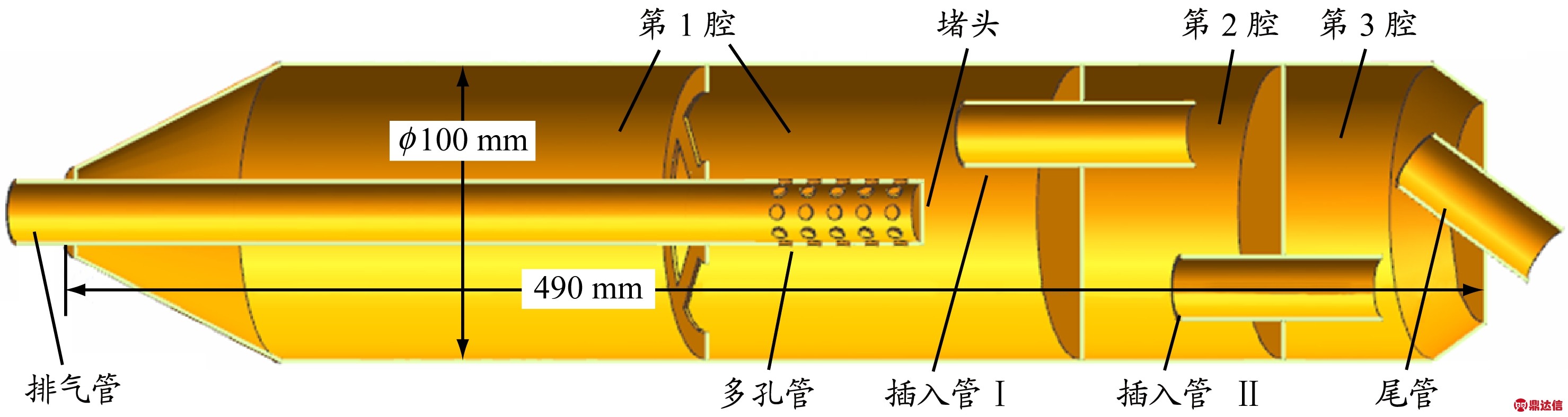
图 1 消声器三维模型
Fig.1 3D model of Muffler
分析不带多孔管以及小孔面积比为1.0,1.5,2.0,2.5,3.0和3.5的6种消声器的压力损失,见图2.这6种消声器又分为堵头开孔和不开孔2种情况.为严格对比,当堵头开孔时,在多孔管侧壁上去掉一个小孔(见图3)以保证堵头开孔和不开孔2种情况下的小孔面积比完全相同.以上方案共计13种组合.
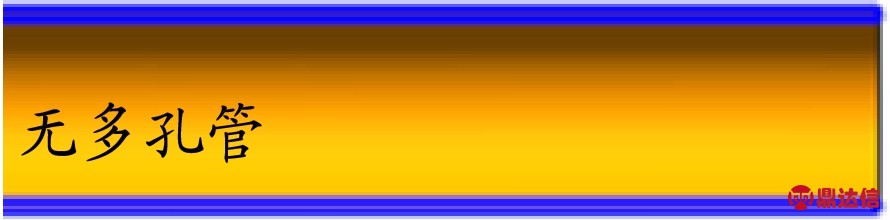
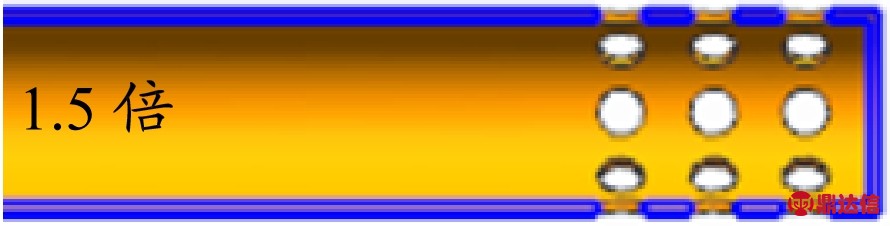
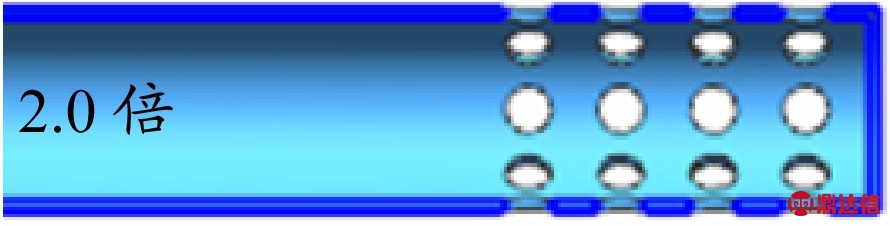
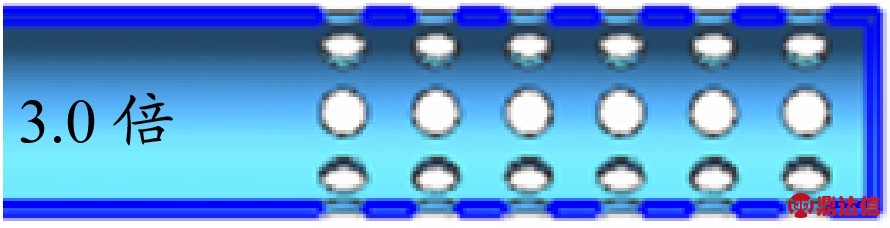
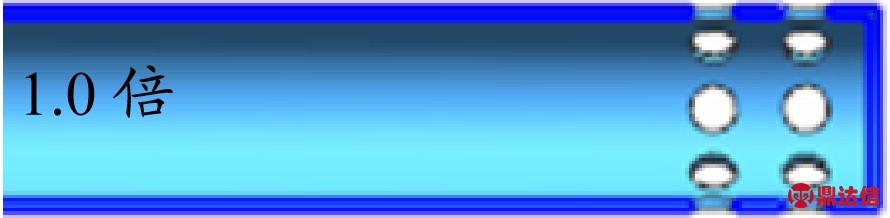
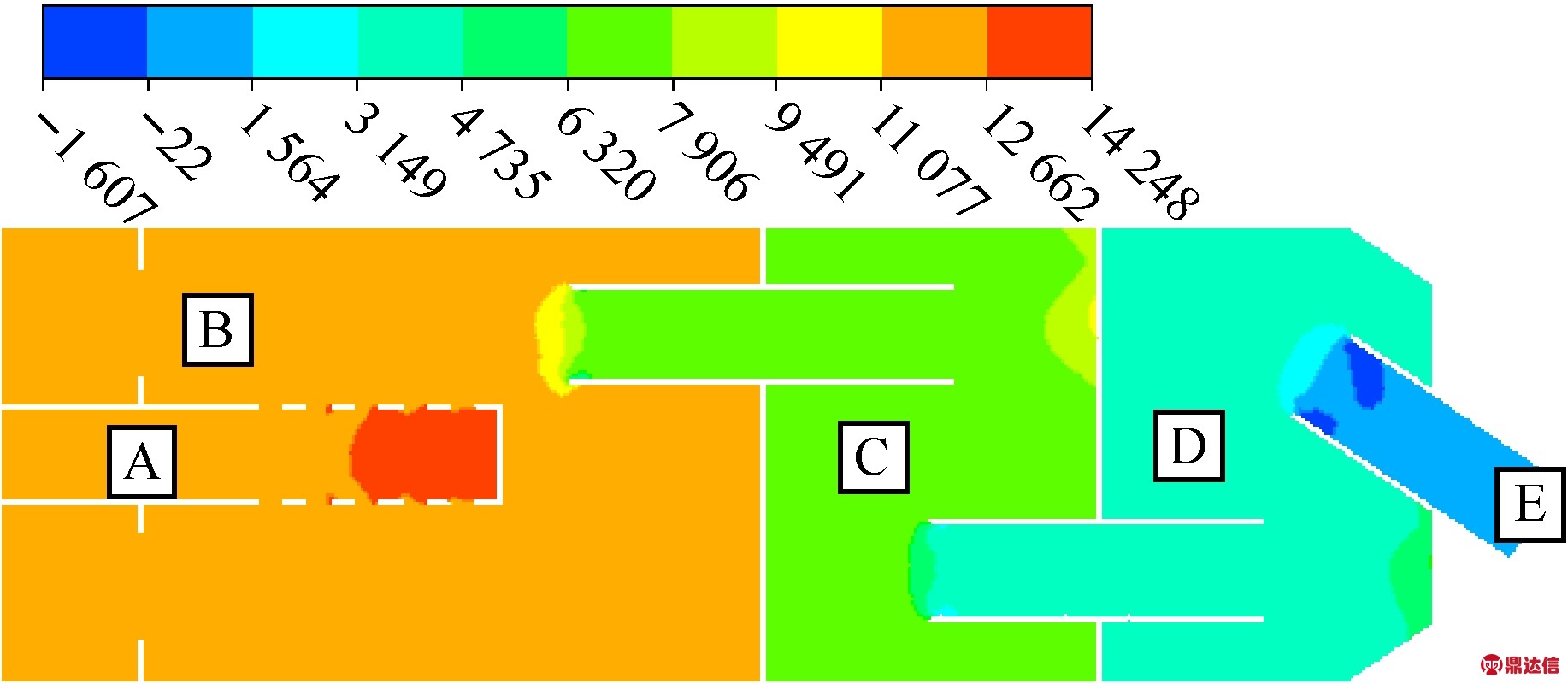

图 2 不同小孔面积比的多孔管
Fig.2 Perforated pipe with different area ratios of small holes
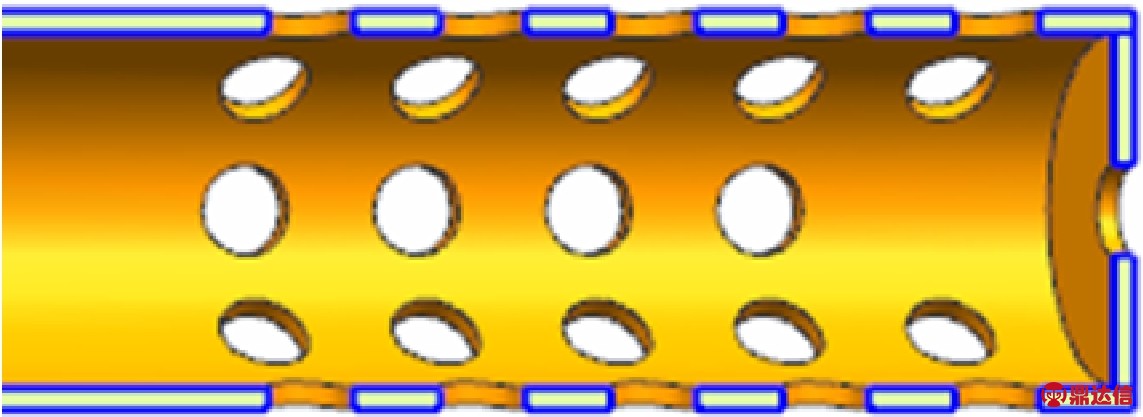
图 3 小孔面积比为2.5时的堵头开孔的多孔管
Fig.3 perforated pipe when plug is with hole and small hole area ratio is 2.5
1.2 网格划分
流场的网格划分越细,计算精度越高,但当网格细化到一定程度时,对计算精度的提高影响不再明显,但计算速度会大大降低.为兼顾计算速度和计算精度,整体采用3 mm的四面体非结构化网格,同时在所有壁面处建立5层棱柱体边界层网格,并在多孔管附近对网格进行加密,流体网格示例见图4,单元网格数约为140万个.

a)整体剖面图
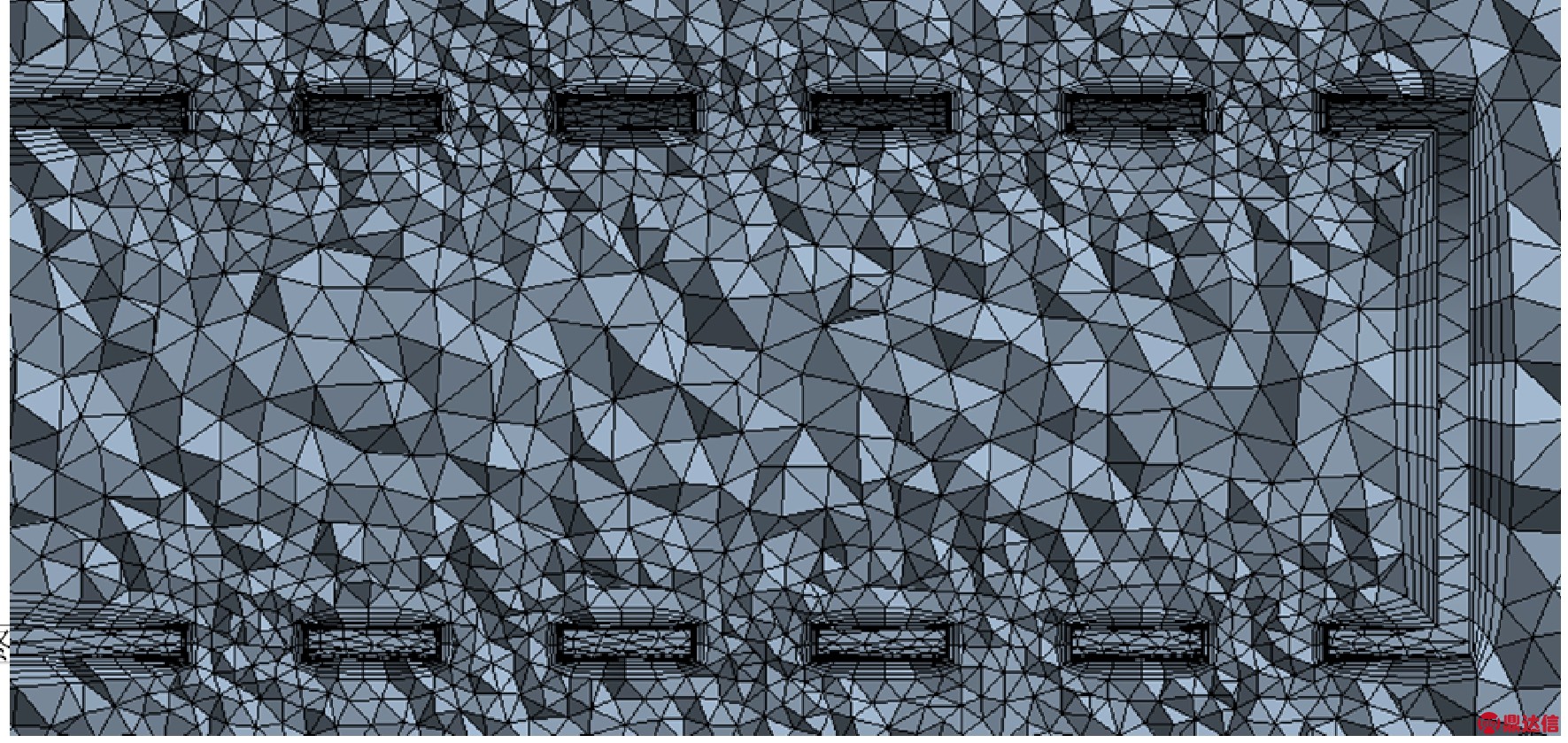
b)多孔管局部放大图
图 4 小孔面积比为2.5时的流体网格
Fig.4 Fluid mesh when small hole area ratio is 2.5
1.3 数学模型
消声器内的气体流动是复杂的三维湍流流动,整个过程可以用连续方程、雷诺时均N-S方程、湍动能k及湍流耗散率ε的输运方程来描述.[5-7]本文采用标准k-ε两方程湍流模型进行模拟,因数使用Launder推荐值[8],即C1ε=1.44,C2ε=1.92,Cμ=0.09,σk=1.0,σε=1.3.近壁区的流动采用标准壁面函数处理[9],不考虑能量方程.由于气流的马赫数较低,可认为流动是不可压缩的.发动机排出的气体中,含有CO,HC和NOx等,所占的比例较小,且大部分气体的分子量和空气相差不大,因此可以将发动机排出的气体近似看作空气[10],密度为1.225 kg/m3.选用SIMPLE算法求解控制方程[5].
1.4 边界条件设定
多孔管的排气阻力随流速的增大而增大,故在发动机高转速状态下,多孔管对排气阻力的影响明显大于低转速状态.本文只研究发动机高速状态下的消声器流场.该消声器装在125 ml排量单缸四冲程发动机上,其正常工作转速范围为2 000~9 000 r/min.本文选定8 000 r/min的高转速工况为边界条件.在8 000 r/min时,排气管处的平均气流速度约为60 m/s,故本次消声器流场计算采用流速为60 m/s的速度入口边界条件;出口为压力边界条件,出口压力设为1标准大气压;其他壁面设为光滑无滑移边界条件.
2 计算结果分析
2.1 压力损失对比分析
每个方案计算完成后,测量进、出口的总压差,即可求得各方案的压力损失.不同小孔面积比的消声器压力损失见图5.图5中虚线位置的压力损失为无多孔管的方案,其压力损失值为8 084 Pa.由此可知:随着小孔面积比增大,压力损失快速减小;当增大到2.5倍后,压力损失曲线逐渐变平缓,即使再继续增加小孔数量,压力损失的减小效果也不明显;当小孔面积比增大到3.5时,压力损失已较为接近无多孔管的状态.
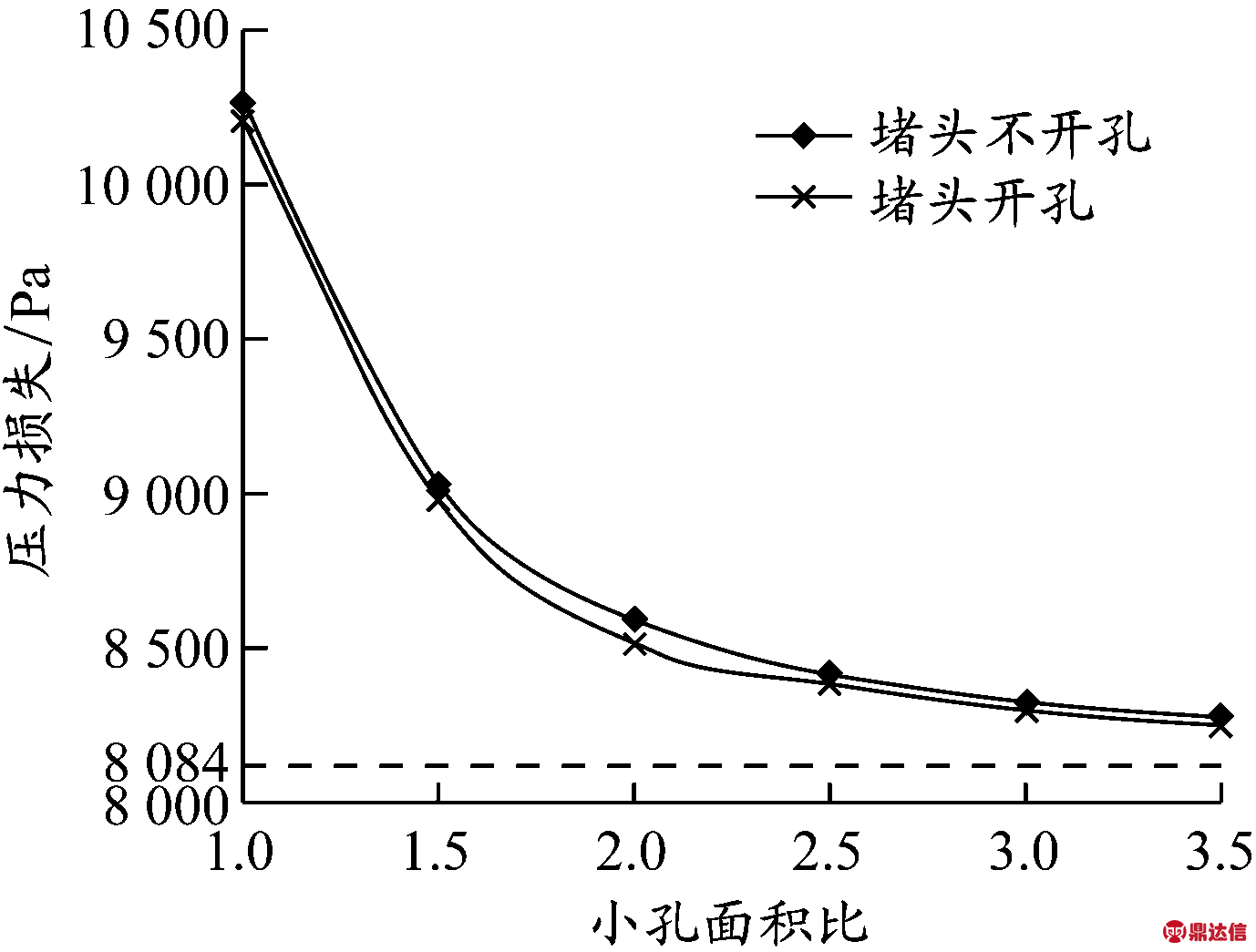
图 5 不同小孔面积比的消声器压力损失
Fig.5 Pressure loss of mufflers with different small hole area ratios
对比图5中堵头开孔和堵头不开孔2条曲线可知:堵头开孔时,压力损失稍小,但压力损失减小的幅度不太大;以小孔面积比2.5倍为例,堵头开孔和堵头不开孔这2种方案的压力损失差异仅为0.4%.
2.2 流速矢量图分析
流速矢量图可以显示速度场的分布,并能清晰地显示涡流、回流等现象,是流体动力学分析中常用的图谱.本文以小孔面积比为2.5时中心(z=0)平面处的流速矢量图(见图6)为例进行分析,其他方案的流速矢量图与此类似.当气流从排气管冲到多孔管部位时,气流从小孔处喷出,越靠近堵头的小孔中流速越高,而第一腔前半部分的气流速度非常低,接近于0.从小孔喷出的一部分气体在碰到消声器筒体壁面后形成尺度较大的涡流.经多个方向汇聚的气体接着进入插入管Ⅰ,该管口部位的流速很高,湍流强度也很大,湍流中流体微团互相碰撞,造成较大的压力损失.从插入管Ⅰ流出的气体冲向隔板,在靠近隔板附近形成较大的回流,回流与主流互相碰撞,导致较大的能量损失,增加压力损失.同样,在插入管Ⅱ冲出的气体在碰撞尾部壁面后也形成较大的回流和涡流,增大压力损失.
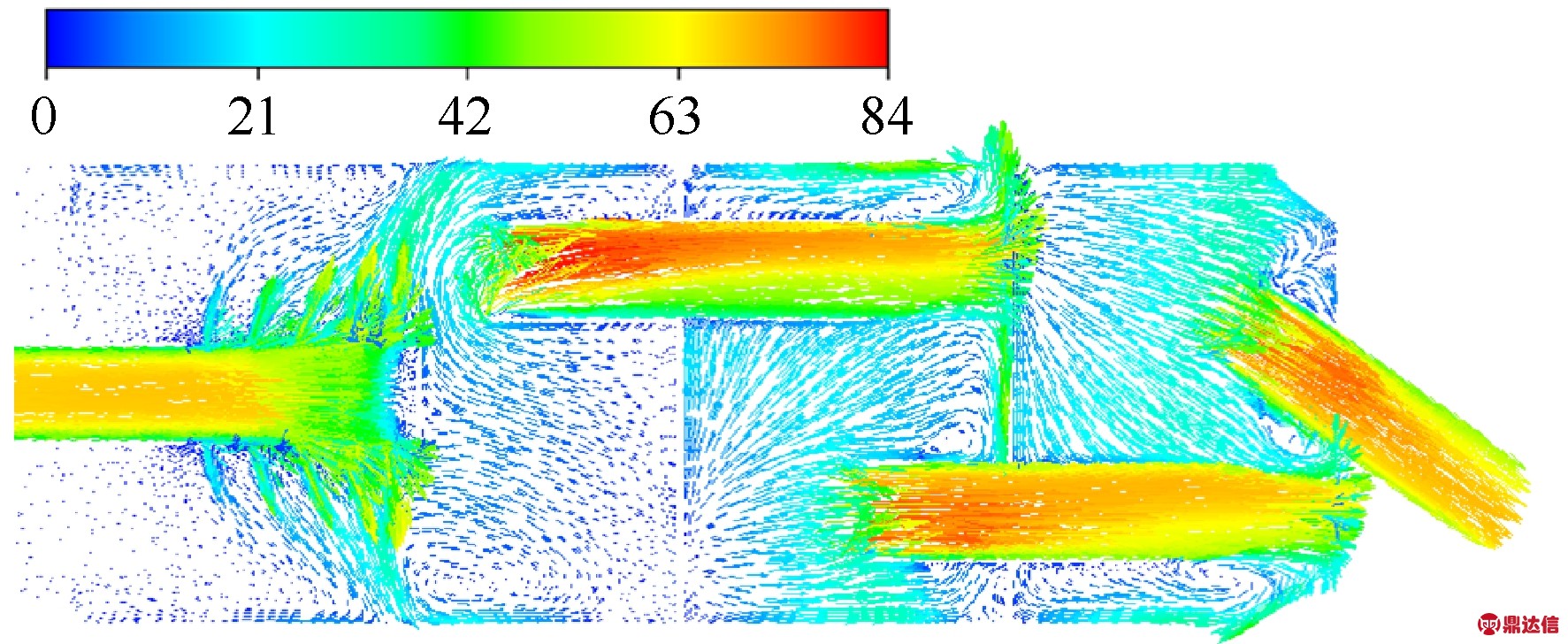
a)堵头无孔
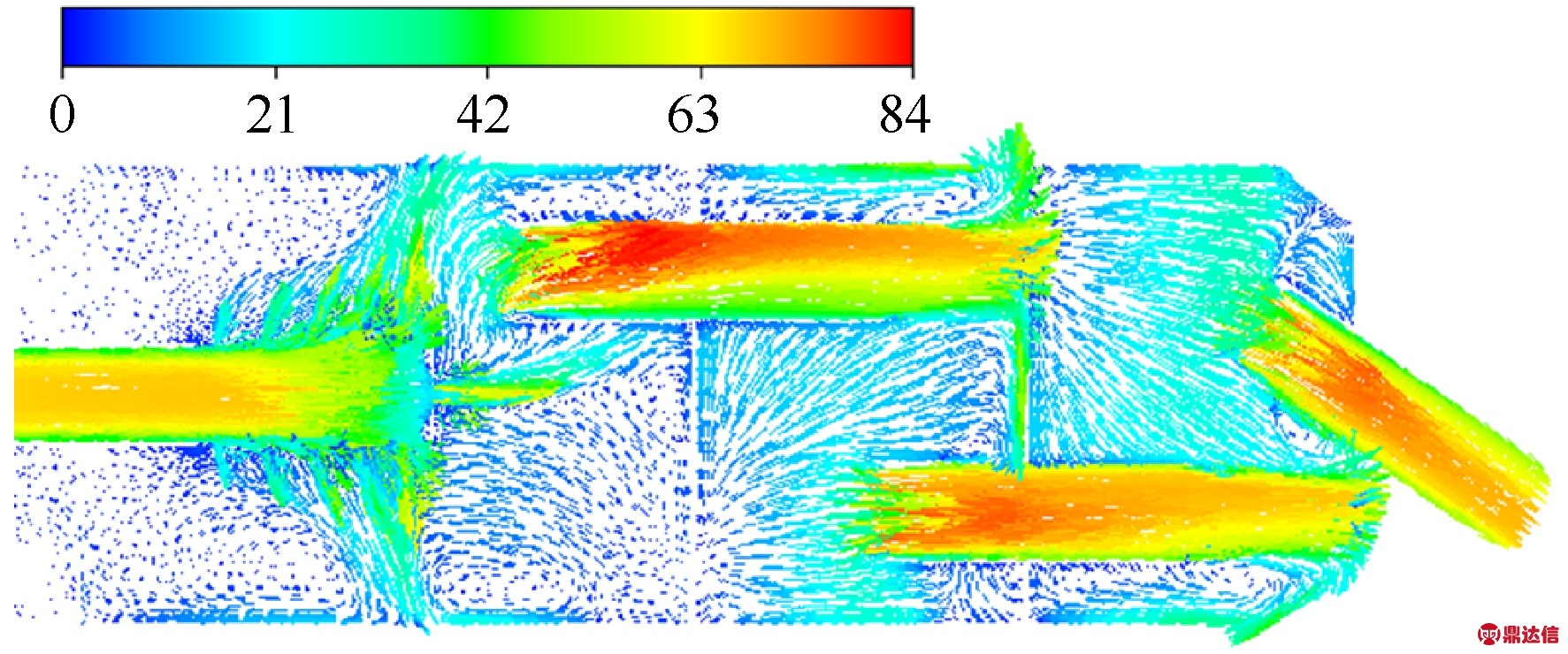
b)堵头开孔
图 6 小孔面积比为2.5时的流速矢量图,m/s
Fig.6 Diagram of velocity vectors when small hole area ratio is 2.5, m/s
堵头开孔时,堵头孔部位有较多气体喷出,如果消声器筒体上布置有玻璃纤维吸声材料,则这部分喷出的气体将难以接触吸声材料,不利于消除中、高频噪声.
2.3 湍动能云图分析
湍动能反映气流速度的波动,湍动能越大,说明速度波动越大,由此造成的能量损失也越大,因此,可根据湍动能的大小及分布分析和评价消声器内压力损失产生的原因.部分方案的湍动能云图见图7.由图7可发现如下一些规律:(1)湍动能较大的部位集中在多孔管处、插入管和尾管的入口处以及插入管出口气流冲击的壁面处,表明这些地方造成的压力损失较大;(2)湍动能最大的部位并不在多孔管附近,而在插入管Ⅰ的入口附近;(3)随小孔面积比逐渐增大,小孔附近的湍动能逐渐减小,与图5的压力损失曲线的变化趋势一致;(4)堵头小孔出流处有一小块区域的湍动能较大.
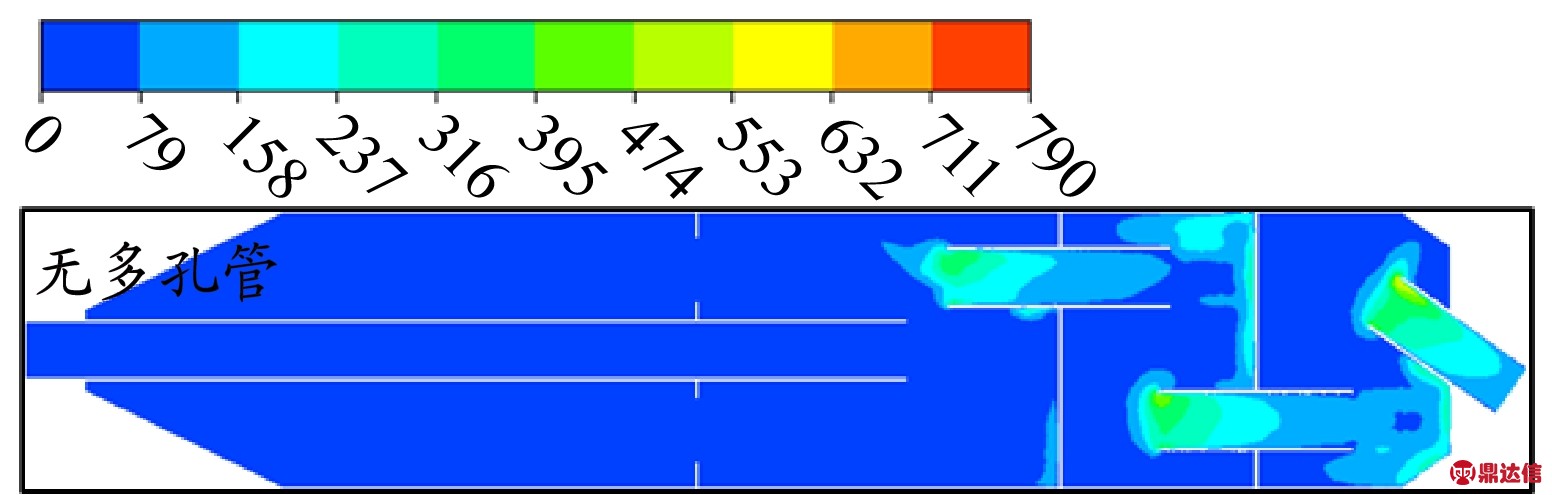




图 7 湍动能分布,J/kg
Fig.7 Turbulence kinetic energy distribution, J/kg
2.4 压力云图分析
以小孔面积比2.5为例,其总压分布见图8,可知每腔压力都有明显差异.根据前文中的湍动能分析可知,压力损失较大的4个部位为多孔管、插入管Ⅰ及其出流冲击壁面区、插入管Ⅱ及其出流冲击壁面区和尾管.为定量分析和比较这4个部位的压力损失,测量A,B,C,D和E这5个部位(位置见图8)的总压并计算其压力差,可以得到各个部位的压力损失的相对大小,统计结果见表1,表中的“A-B”即A处与B处的压力差,其余类同.A-B,B-C,C-D和D-E可分别表征多孔管、插入管Ⅰ及其出流冲击壁面区、插入管Ⅱ及其出流冲击壁面区和尾管这4个部位的压力损失大小.从表1中可发现:(1)小孔面积比小于2.5时,A-B的压差较大,小孔面积比大于2.5时,A-B的压差较小,这与压力曲线的变化趋势以及湍动能的变化规律相一致;(2)无论哪种方案,B-C的压差都是4个部位中最大的,这与流速矢量图和湍动能分布图显示一致.
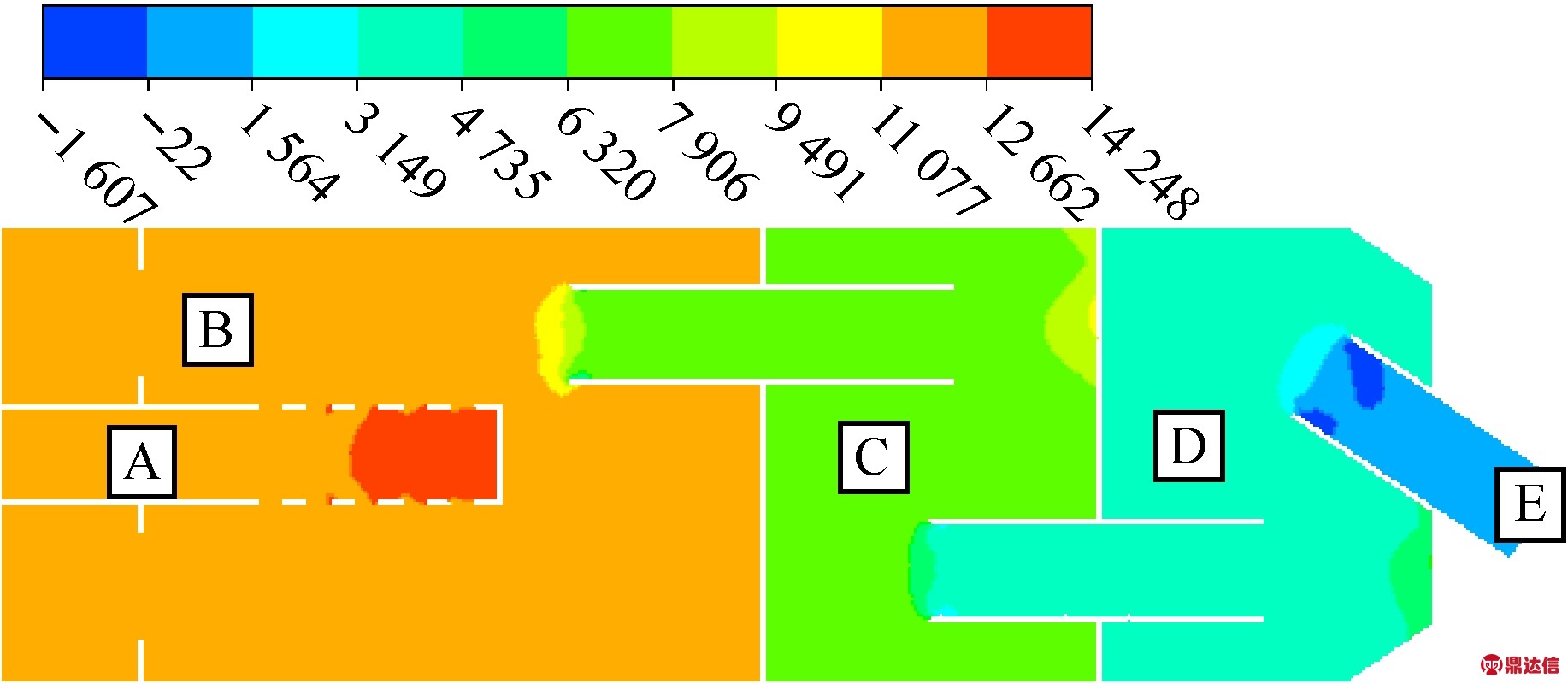
图 8 堵头无孔且小孔面积比为2.5时的总压分布,Pa
Fig.8 Total pressure distribution when plug has no hole and small hole area ratio is 2.5, Pa
表 1 堵头无孔时局部压力损失统计
Tab.1 Statistics of local pressure loss when plug has no hole Pa
3 结 论
通过详细分析多种方案的消声器,给出如下设计建议:(1)建议小孔面积比在2.5以上;(2)当消声器筒体上布置有玻璃纤维吸声材料时,建议堵头不开孔,无玻璃纤维时可考虑堵头开孔;(3)最大的压力损失位于插入管Ⅰ部位,而非多孔管处,故插入管Ⅰ的直径应大于其他3根管的直径.以上结论对同类典型消声器的设计都有通用的指导意义.