摘 要:为明确钢中硫质量分数对Ti-Zr脱氧的E36船板钢中夹杂物的影响,在1 873 K下,在MoSi2电阻炉上用φ70 mm×100 mm MgO坩埚开展了3炉E36钢炼钢实验.结果表明,Ti-Zr脱氧钢中夹杂物主要以含TiOx和ZrO2成分的外围包裹MnS的球形夹杂物为主,典型夹杂物为Al2O3-TiOx-MnS,MgO-SiO2-Al2O3,Al2O3-SiO2-TiOx-ZrO2,TiOx-SiO2-Al2O3-MnS等.随着硫质量分数的增加,小于10 μm的夹杂物所占比例逐渐提高到99.5%,夹杂物平均直径由1.7 μm增大到2.3 μm,夹杂物中平均硫质量分数和单个夹杂物中MnS所占的面积百分比均增加,w[S]=0.001 5%时面积比为0.15%,w[S]=0.011%时面积比达到0.72%.
关 键 词:炼钢;船板钢;硫质量分数;夹杂物;脱氧
氧化物冶金技术是近年来国际上新开发的一种利用钢中小于3 μm的夹杂物来改善钢材组织和性能的冶金方法[1-3],其核心技术是在炼钢过程控制合适的原子浓度比条件下加入夹杂物脱氧或脱硫剂,促使钢中生产合适的氧化物、硫化物或控制氮化物的析出等[4-6],通过控制夹杂物的种类、形貌、数量、尺寸、分布等使这些有益夹杂物留在钢中,并在后期轧制或焊接过程中阻止奥氏体晶粒的粗化或促进晶内铁素体的生成,从而细化钢的组织,改善钢的延展性、低温冲击等性能.氧化物冶金技术目前已经成为国内外冶金界开发的焦点课题,但对于钢中硫质量分数对氧化物冶金技术中夹杂物的影响状况尚不明晰[7].
1 实验方法
本实验中除硫质量分数外,实验E36船板钢的目标成分按GB712—2011控制,具体成分见表1.实验时将约1 kg的DT8牌号工业纯铁装入φ70 mm×100 mm MgO坩埚内,然后随坩埚一同放入MoSi2高温电阻炉高温区,对电阻炉通电升温,实验全程通氩气保护,氩气流量3 L/min.工业纯铁熔清并恒温在1 873 K后,采用φ3 mm刚玉管向熔池内吹入氧气,吹氧后用定氧仪测定溶解氧质量分数,将熔池溶解氧质量分数调整为0.06% ~0.08%.添加硅铁、锰铁、铌铁等合金进行合金化,合金原料成分见表2.加入合金搅拌10 s后,添加Ti-Zr脱氧;最后根据实验要求的目标硫质量分数,加入FeS.实验过程中按一定时间间隔取样,60 min后出钢,停气、断电.由于精炼渣会对钢液进行脱硫,影响实验目标硫含量的控制,同时精炼渣也会影响钢中夹杂物的形态,因此,为排出精炼渣对夹杂物的影响,本实验采用不添加精炼渣的方式进行冶炼.实验钢成分利用碳硫分析仪化验钢中碳硫质量分数,其他元素采用化学分析方法进行分析.对实验中所取夹杂物样品进行研磨和抛光后,用SSX-550扫描电镜结合能谱分析夹杂物形貌及成分;用LEICA Q600S图像仪和DMRME显微镜对样品观察30个视场,统计夹杂物的数量、尺寸及分布.
表1 实验钢的化学成分(质量分数)
Table1 Compositions of steels(mass fraction)%
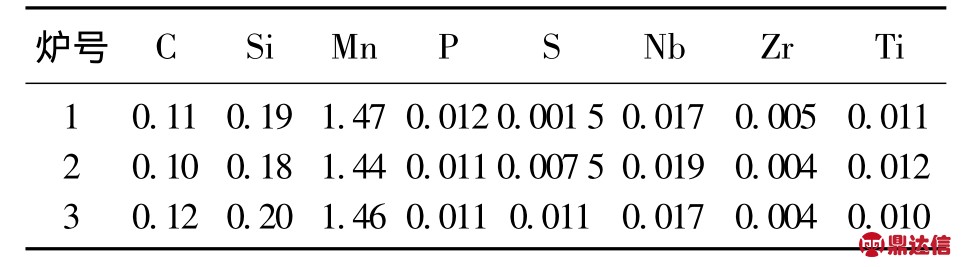
表2 实验原料成分(质量分数)
Table2 Compositions of raw materials(mass fraction) %
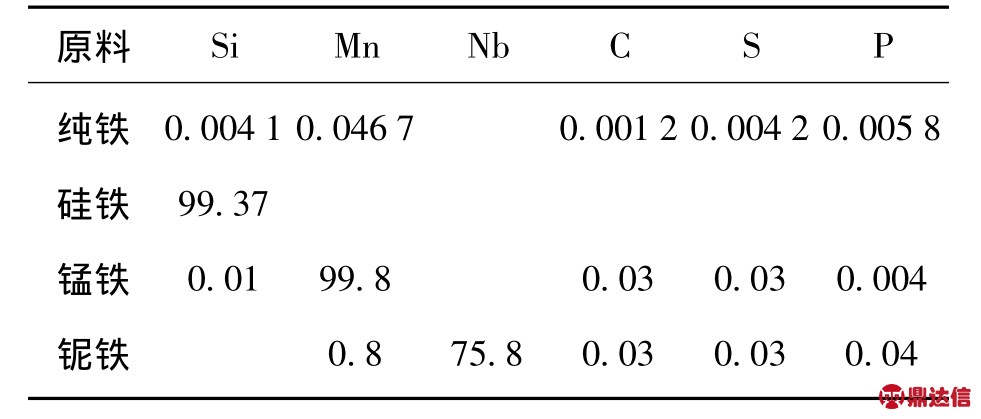
2 实验结果及分析
2.1 脱氧剂及钢中硫质量分数对夹杂物形貌及成分的影响
表3为各组实验夹杂物形貌和成分的整体情况,典型夹杂物形貌见图1.可以看出,由于实验E36钢采用 Ti-Zr脱氧,因此夹杂物中均含有TiOx和ZrO2.同时,由于实验所用硅铁中含有3.2%的铝,因此,大部分夹杂物中含有Al2O3成分.另外,钢中夹杂物的组成、形貌与硫质量分数有关.硫质量分数为0.001 5%的钢中夹杂物多为不规则形状,以 Al2O3-TiOx-MnS、MgOSiO2-Al2O3、Al2O3-SiO2-TiOx-ZrO2、TiOx-SiO2-Al2O3-MnS为主,少量MnS附着在氧化物外围.随着硫质量分数增加,钢中夹杂物趋向于以球形为主,Al2O3-SiO2-ZrO2-TiOx-MnS类夹杂物增多,外围包裹 MnS的夹杂物比例增多.

图1 E36钢中典型夹杂物形貌及能谱
Fig.1 Morphology and spectrum of typical inclusions in steel E36
(a)—Al2O3-SiO2-TiOx-MnS;(b)—Al2O3-SiO2-ZrO2-TiOx-MnS;(c)—Al2O3-SiO2-ZrO2-TiOx-MnS.
2.2 钢中硫质量分数对夹杂物尺寸及数量的影响
表4为w[S]=0.007 5%的钢样中夹杂物的统计结果.可以看出,随着脱氧过程的进行,钢中夹杂物的平均直径呈先增大后减小的趋势,这可能是部分夹杂物冶炼过程碰撞、聚集长大的结果.单位面积夹杂物的个数则持续呈减少趋势.脱氧20 min后,钢中小于3 μm的夹杂物比例超过92%,终点钢样中98.9%的夹杂物小于3 μm.
图2和图3为实验钢中夹杂物数量和尺寸的统计情况.可以看出,随着冶炼时间的延长,过程钢样单位面积上的夹杂物数量逐渐减少,但实验全过程夹杂物去除率均较低,3组实验进行60 min时夹杂物的去除率分别为46.7%,66.2%和35.5%.随着硫质量分数从0.001 5%增加到0.011%,小于10 μm的夹杂物所占比例逐渐提高,3炉结果分别为97.8%,99.4%和99.5%.夹杂物平均直径由小变大,w[S]=0.001 5%时夹杂物的平均直径最小,为 1.7 μm;当 w[S]=0.011%时夹杂物的平均直径则达到2.3 μm.
表3 E36钢中夹杂物情况
Table3 Ⅰnclusions in steel E36
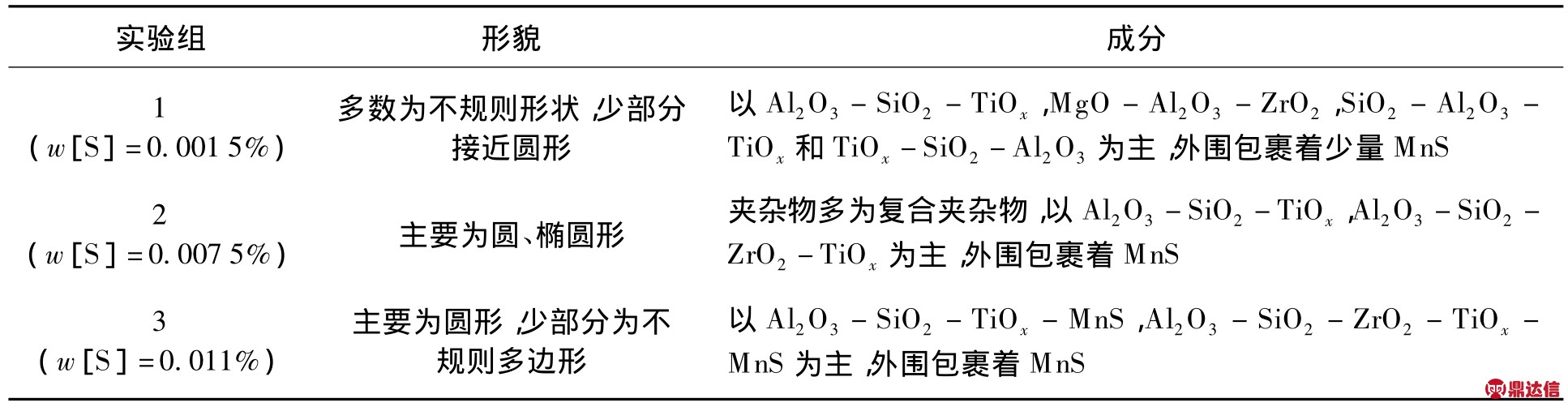
表4 2#钢样过程样金相统计结果(w[S]=0.007 5%)
Table4 metallographic analysis results of 2#process samples
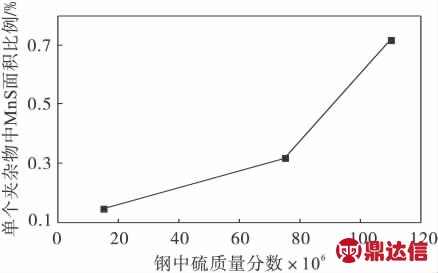
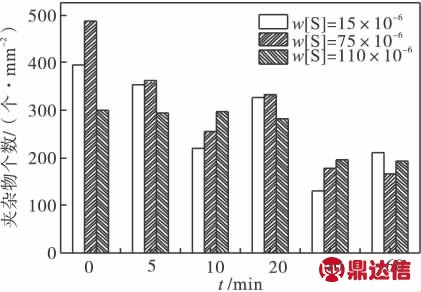
图2 过程钢样中的夹杂物数量
Fig.2 Ⅰnclusion numbers in steel samples
从表4和图3可以看出,本实验中夹杂物平均直径<3 μm.根据文献[8-13]中的伽利略准数Ga'和夹杂物运动的雷诺数ReP的计算公式可得本实验中小于10 μm的夹杂物的 Ga'<9.43×10-3,ReP≤300,在静止钢液中的上浮速度小于4.059×10-3cm/s,夹杂物从坩埚底部上浮到渣金界面的时间>16.4 min.可见,此类夹杂物的运动状态处于斯托克斯区.在本实验仅进行短暂搅拌的条件下,大部分时间熔池处于静止状态,这更不利于小夹杂物的上浮去除,致使处理后钢中小于3 μm的夹杂物较多,去除率较低.
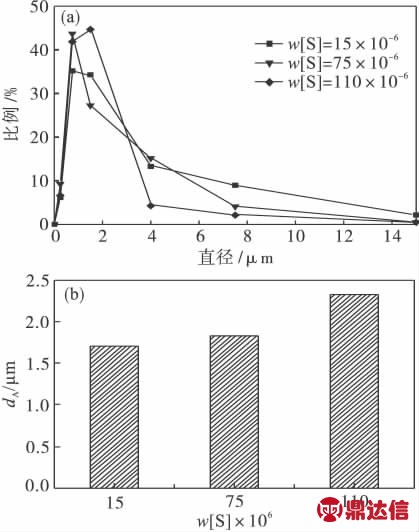
图3 终点钢样中夹杂物尺寸情况
Fig.3 Results of inclusion size in terminal steel samples
(a)—夹杂物尺寸分布;(b)—平均直径.
2.3 钢中硫质量分数对夹杂物中硫的质量分数的影响
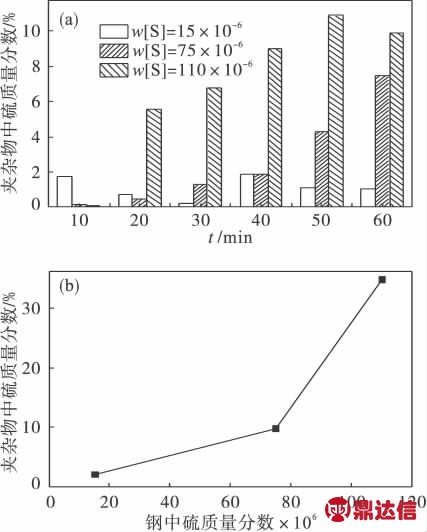
图4 夹杂物中硫质量分数变化
Fig.4 Variation of S content in inclusions
(a)—不同时刻夹杂物中硫质量分数;(b)—钢中硫质量分数与夹杂物中硫质量分数的关系.
图4是实验过程样品夹杂物中硫的质量分数分析结果.由图4a可以看出,当钢中w[S]=0.001 5%时,夹杂物中硫的质量分数随时间变化不大,但是当w[S]=0.007 5%和w[S]=0.011%时,夹杂物中硫质量分数随着冶炼时间的延长显著增加.由图4b可以看出,随着钢中硫质量分数从0.001 5%增加到0.011%,夹杂物中硫质量分数从2.1%增加到34.8%.
图5为MnS夹杂物区域面积百分比变化图.可以看出,随着钢中硫质量分数的增加,单个夹杂物中MnS的区域面积百分比逐步增加,单个夹杂物中MnS所占的面积百分比也显著增加,w[S]=0.001 5%时为0.15%,硫质量分数为0.011%时,则上升为0.72%.这与图6所示的各组实验钢中的典型夹杂物的形貌分析结果基本一致.可见,w[S]控制在0.001 5%以上时即可满足E36钢对含MnS夹杂物的要求.
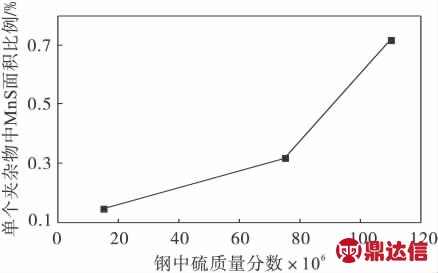
图5 夹杂物中MnS所占面积百分比
Fig.5 Variation of area ratio of MnS in inclusions

图6 硫质量分数对夹杂物形貌的影响
Fig.6 Effects of sulfur content on the morphology of inclusions
(a)—Al2O3-TiOx-MnS(w[S]=0.001 5%);(b)—Al2O3-SiO2-TiOx-MnS(w[S]=0.007 5%);(c)—Al2O3-SiO2-MnS(w[S]=0.011%).
3 结 论
1)Ti-Zr脱氧钢中夹杂物以球形的Al2O3-TiOx-MnS,MgO-SiO2-Al2O3,Al2O3-SiO2-TiOx-ZrO2,TiOx-SiO2-Al2O3-MnS 等为主.随着硫质量分数增加,外围包裹MnS的夹杂物数量增多.
2)钢中单位面积上的夹杂物数量随着冶炼时间的延长逐渐减少,3组实验进行60 min时夹杂物的去除率分别为46.7%,66.2%和35.5%.随着硫质量分数的增加,小于10 μm的夹杂物所占比例逐渐提高到99.5%,夹杂物平均直径由1.7 μm 增加到 2.3 μm.
3)随着钢中硫质量分数的增加,夹杂物中硫质量分数增加,单个夹杂物中MnS所占的面积百分比也显著增加,w[S]=0.001 5%时面积比为0.15%,硫质量分数为 0.011%时,则上升为0.72%.