摘 要:钢中刚性夹杂物对钢的品质有很大影响,采用镁处理可以对钢中有害夹杂物进行改性。本文总结了镁脱氧反应热力学与镁处理夹杂物动力学,镁处理钢中夹杂物研究进展以及镁加入方法。镁处理可明显改善钢中刚性夹杂物MO x(M=Al,Ti)的形状,将其由不规则形状改质为近似球形,尺寸明显减小,从而减轻了夹杂物在钢中的危害;钢液中加镁的方法主要为镁蒸气加入和镁合金方式加入,在实验室以及工业生产中取得了一定的进展。
关键词:镁处理;夹杂物;热力学与动力学
钢中的刚性夹杂物是危害钢材组织性能的重要因素[1-3]。长期以来,去除这类夹杂物被认为是提高钢液纯净度及钢材产品质量的唯一有效途径。但自1990年沟口等[4]发现一些氧化物可以改善钢的组织,进而提出了“氧化物冶金”概念,人们逐渐认识到夹杂物有益的功能化优点。实际上,最初对夹杂物进行功能化利用的是采用TiN夹杂物提高钢材组织性能[5],这种方法被称为第一代“氧化物冶金”。但是,在大线能量焊接中,TiN出现了溶解现象,无法稳定地起到有益作用[6]。因此,采用在高温条件下稳定存在的TiO x(Ti2O3、TiO2、Ti3O5)夹杂替代TiN,这种方法被称为第二代“氧化物冶金”[7]。然而,TiO x并不像 Al2O3普遍存在于大多数钢种中。因此,对A l2O3的改质与利用成为近些年提升钢材质量的关键技术,被称为第三代“氧化物冶金”[8]。本文总结了镁脱氧反应热力学与镁处理夹杂物动力学,镁处理钢中夹杂物研究进展以及镁加入方法,以期更好地研究镁处理对钢中夹杂物的影响。
1 Mg处理钢液的热力学
表1总结了钢液中镁处理可能发生的反应及其吉布斯自由能变化。反应1是ITOH等[9]在Mg-O体系下通过计算反应平衡常数得到的吉布斯自由能变化。反应2是FUJII等[10]在Al-Mg-O体系下通过实验测得MgO、Al2O3、MgO-A l2O3的活度得到吉布斯自由能变化。反应3是SEO等[11]在Mg-OAl体系下通过预估尖晶石在Al2O3相中活度为0.64,在MgO相中活度为0.96得到的吉布斯自由能变化。反应4是ITOH[12]在A l-O-Mg-Ca体系下通过测得反应平衡常数得到吉布斯自由能变化。从表1不难看出,相同的反应在不同的反应体系下得到的Gibbs自由能变化不同,如反应2和反应3;反应物存在的位置对Gibbs自由能变化也有影响,夹杂物中Gibbs自由能变化较大,反应越容易进行,对于夹杂物的处理效果会更加明显,如反应3和反应4。
表1 钢液中镁处理可能发生的反应及其吉布斯自由能变化
Tab.1 Possible reactions of magnesium treatment in molten steel and variation of Gibbs free energy
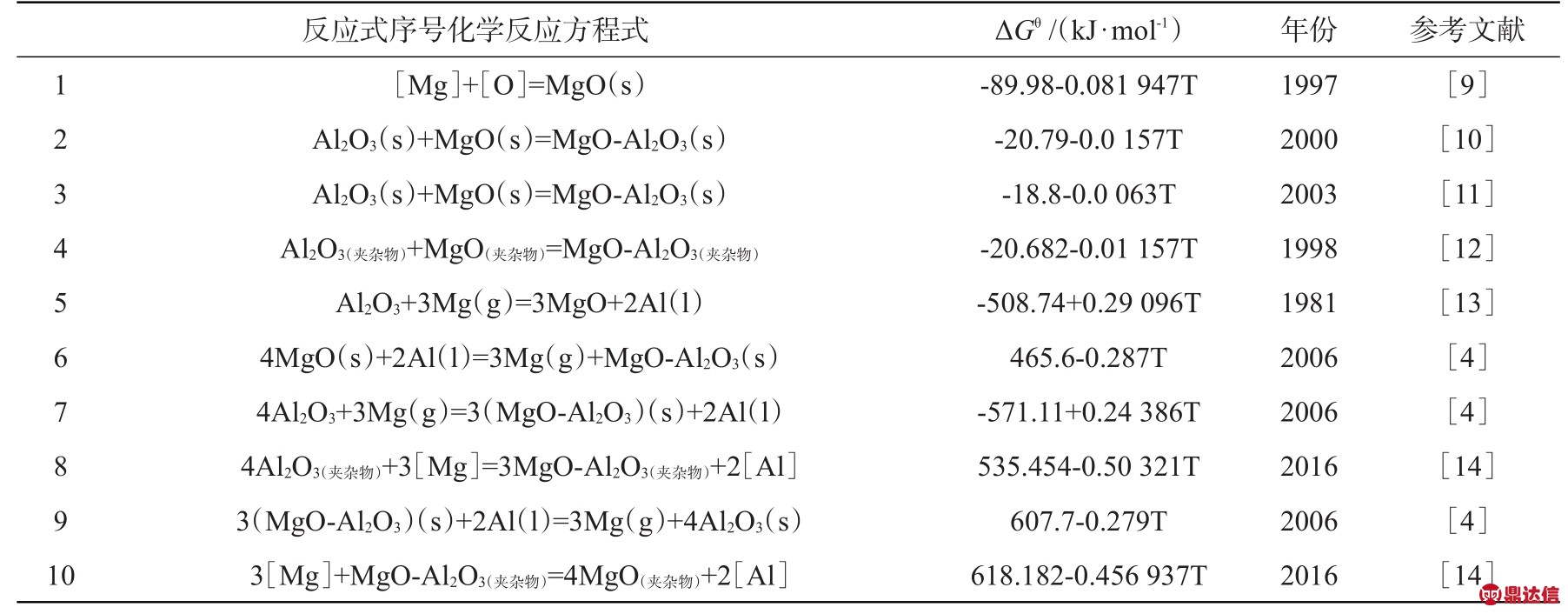
ITOH等[9,15]研究铝镁共脱氧过程中尖晶石形成的热力学时,总结了一阶相互作用系数计算钢中溶解镁[Mg]、溶解氧[O]的关系。INOUE[16]使用垂直电阻炉,在已知MgO活性的CaO-A l2O3-MgO炉渣中获得一阶相互作用系数,如图1a所示。他们发现传统的一阶相互作用系数报道值引起了平衡浓度曲线变成闭合曲线的矛盾,并且对应一个Mg浓度存在多个平衡氧浓度,相互作用系数的应用浓度范围太窄。随后他们通过实验并采用二阶相互作用系数进行计算,得到图1b。
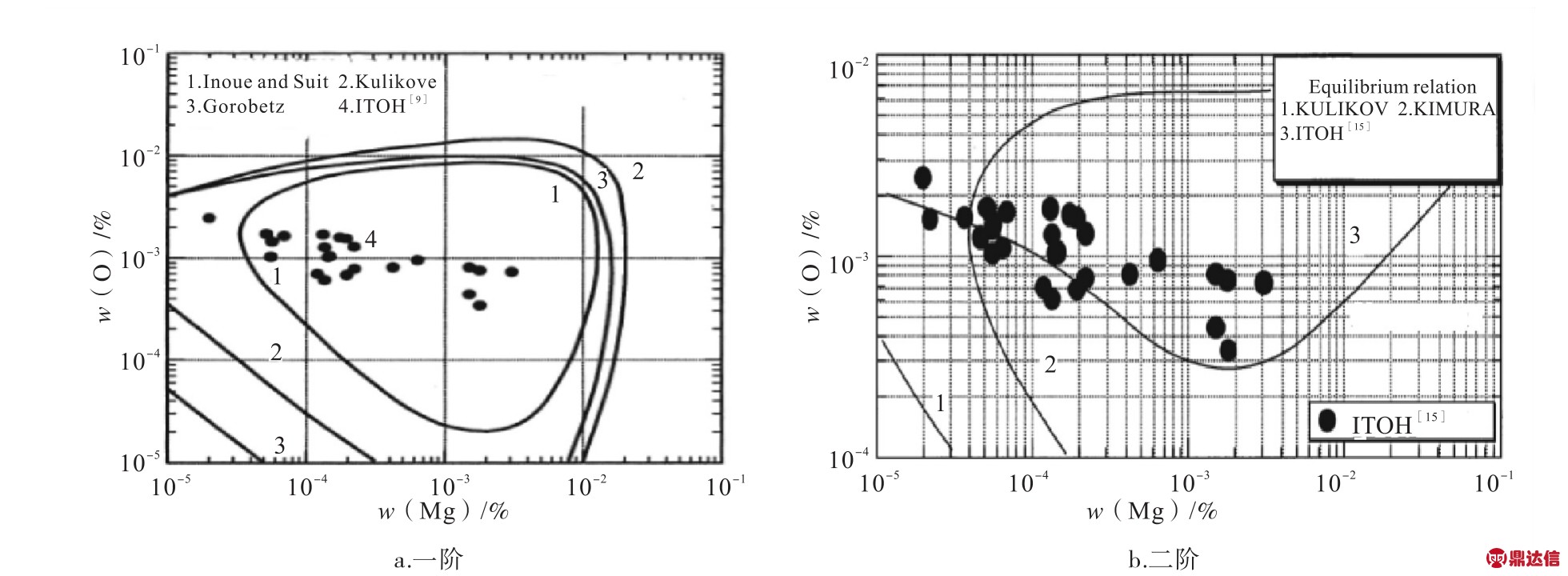
图1 一阶、二阶相互作用系数平衡曲线
Fig.1 Equilibrium curves of first-and second-order interaction coefficients
SEO等[11]通过实验方法研究Mg-O平衡。图2a显示了获得的Mg脱氧平衡数据及前人实验的结果。低Mg浓度范围的数据通过向液态铁中添加Mg或Mg合金而获得,高Mg浓度范围通过Mg蒸气在铁液中的溶解平衡来测定。图中的实曲线是ITOH[9]等在MgO饱和状态下获得的热力学数据采用二阶相互作用系数计算的液态铁中Mg-O平衡。JUNG 等[17]采用 Heuzey和 Pelton模型对SEO[18]在Mg-Al-O体系下测定的实验数据和HAN等[19]在Mg-O体系下测定的实验数据计算钢中[Mg]、[O]的关系,如图2b所示。
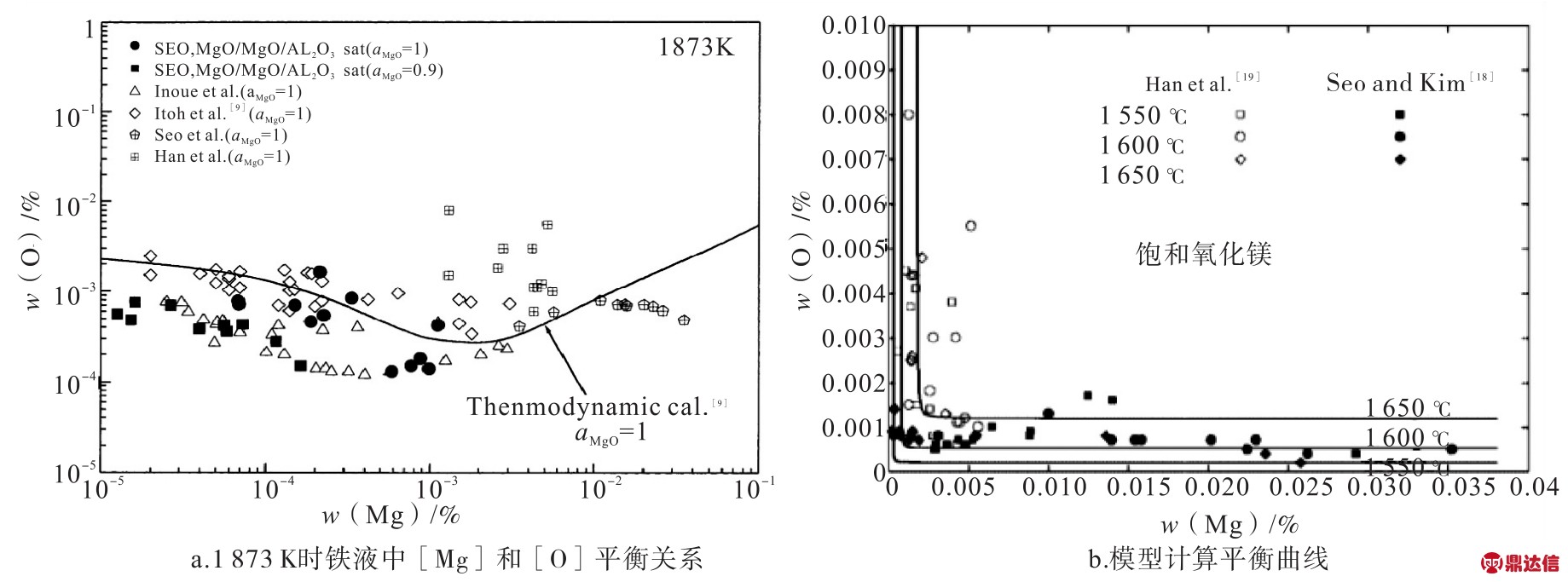
图2 镁氧平衡曲线
Fig.2 Magnesium-oxygen equilibrium curves
2 Mg处理夹杂物动力学
LIU 等[20-21]和 HARADA 等[22]在对含 Mg钢中Al2O3转变成MgO-A l2O3尖晶石夹杂物的动力学研究时,将A l2O3棒浸入钢水中来研究从A l2O3到MgO-Al2O3的转变,发现无论有无炉渣尖晶石层都会出现,其厚度随着浸入的时间增加而增大。作者对A l2O3转变为尖晶石层的限制环节进行推测:(1)钢水边界层Mg的转移;(2)形成的MgOAl2O3尖晶石中MgO的转移;(3)形成的MgOAl2O3与Al2O3界面处的化学反应。通过评估活化能,发现尖晶石层中的MgO扩散被认为是速率控制步骤,如图3所示。
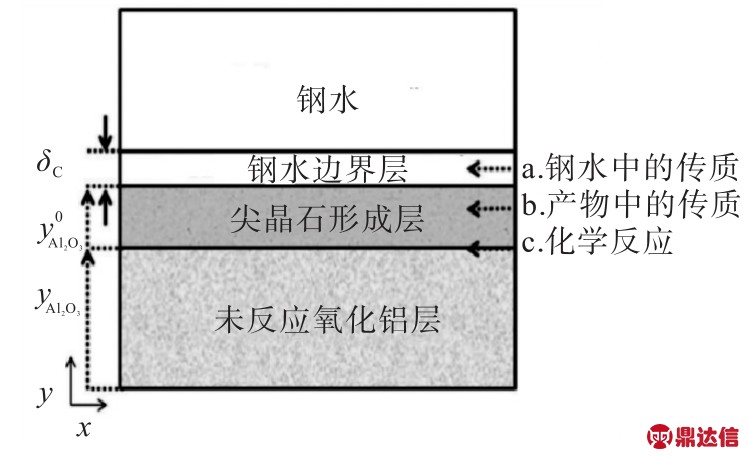
图3 A l2O3表面形成镁铝尖晶石
Fig.3 Magnesia-alumina spinel formed on Al2O3 surface
KIMURA等[23-24]研究低碳钢固液界面前沿非金属夹杂物的动态行为,发现镁铝尖晶石夹杂在固化过程中从前进界面逸出,但在重新熔化期间再次聚集在处理界面处,如图4所示。实验发现一对镁铝尖晶石之间的吸引力为一对Al2O3的十分之一,所以镁铝尖晶石的聚集趋势远远小于A l2O3。DOGAN等[25]通过对镁铝尖晶石的研究也证实了镁铝尖晶石在钢液中不易聚集。
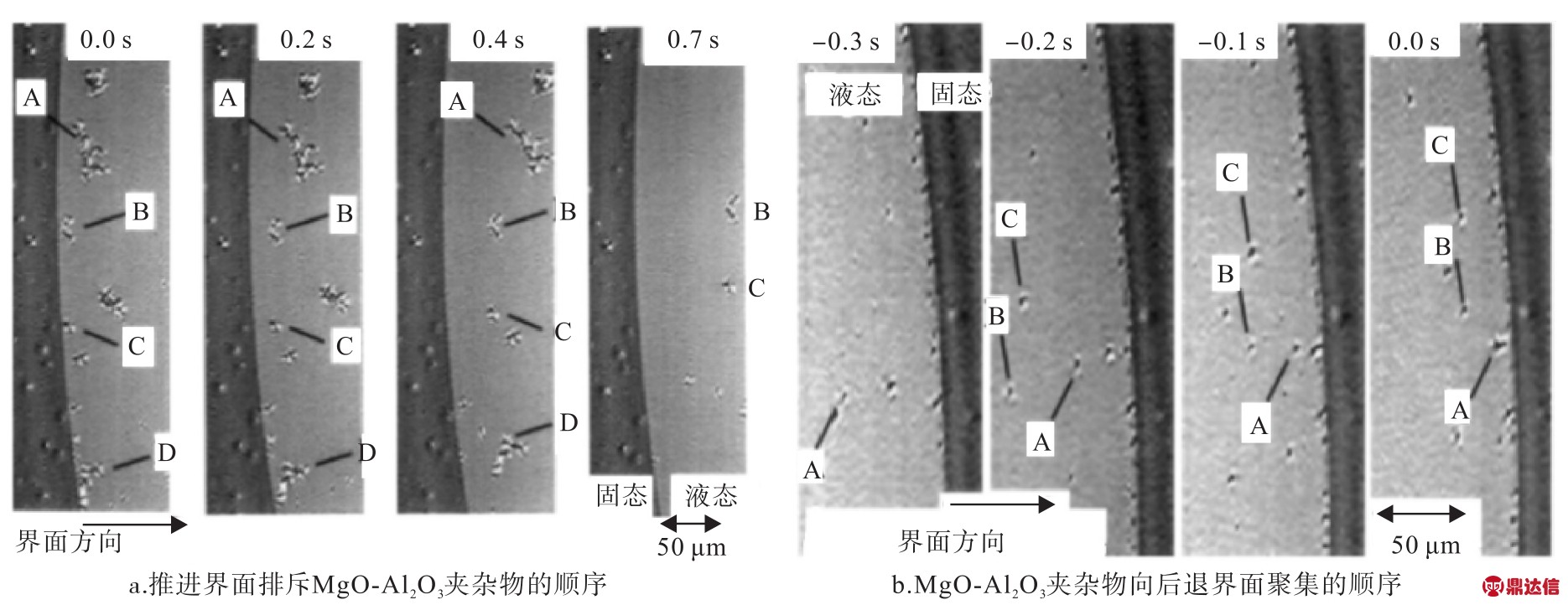
图4 镁铝尖晶石夹杂物动态观察
Fig.4 Dynamic observation of magnesia-alumina spinel inclusions
OKUYAMA 等[26]和 YANG 等[27]对钢中 MgOAl2O3夹杂物形成及动力学进行了研究,发现了镁铝尖晶石的形成过程,如图5a所示。通过未反应核模型比较镁在镁铝尖晶石中的传质以及镁在钢液中的膜传质,发现后者为反应速度的限制环节,如图5b所示。图中[Mg]'表示金属和夹杂物界面处镁的浓度,(Mg)'表示金属和夹杂物界面处夹杂物中镁的浓度。
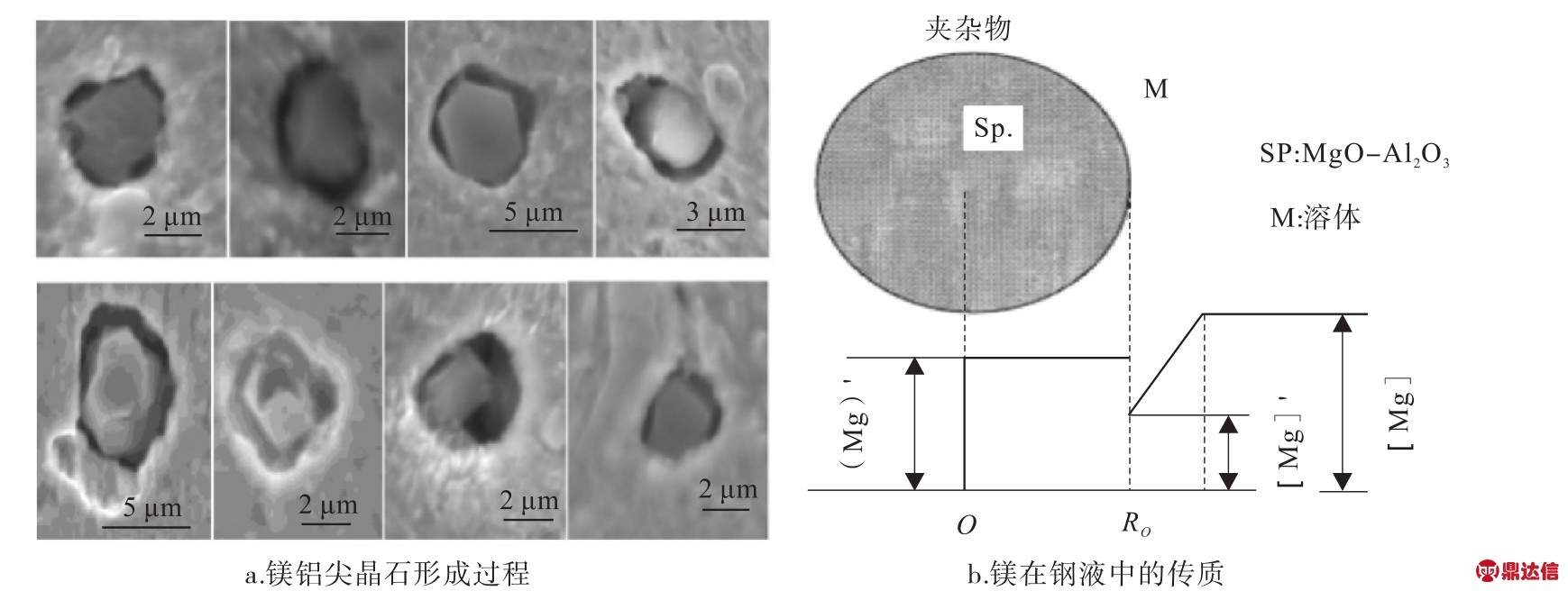
图5 镁铝尖晶石形成的动力学
Fig.5 Kinetics of formation of magnesia-alum ina spinel
YANG等[28]在研究利用镁蒸气进行脱硫研究时,发现在气泡形成和上升过程中,速率控制步骤随着脱硫进程而变化。在形成期开始时,熔体中的硫与气泡中的镁之间的传质速率差异不大,并且两者都应被视为速率限制环节。在上升期结束时,镁分压开始下降接近平衡值。镁在气泡中的传质比硫在熔体中的传质慢得多,并成为速率限制环节。
YANG等[29-30]在研究A l等温还原MgO的动力学的影响时,发现还原后的颗粒大小几乎没有变化,质量略有下降。在图6a中,可以很清楚熔融铝沿各个方向扩散到氧化镁相与氧化镁反应。随后作者推断,氧化镁的铝热还原由以下步骤组成:在铝颗粒表面上形成的氧化铝薄膜破裂并且熔融的铝渗透到氧化镁相中。通过不同还原阶段的颗粒的SEM观察清楚地显示了氧化铝薄膜的分解。在氧化镁颗粒的表面,发生氧化镁的铝热还原。图6b证实了在表面有氧化铝包裹的铝颗粒,熔融铝仅通过裂纹飞出,并且熔融铝和镁颗粒之间的反应区域没有大量增加。在铝颗粒上的其他点处也有镁的存在,是由于在静压机下形成颗粒期间氧化镁颗粒粘附在铝颗粒上造成的。
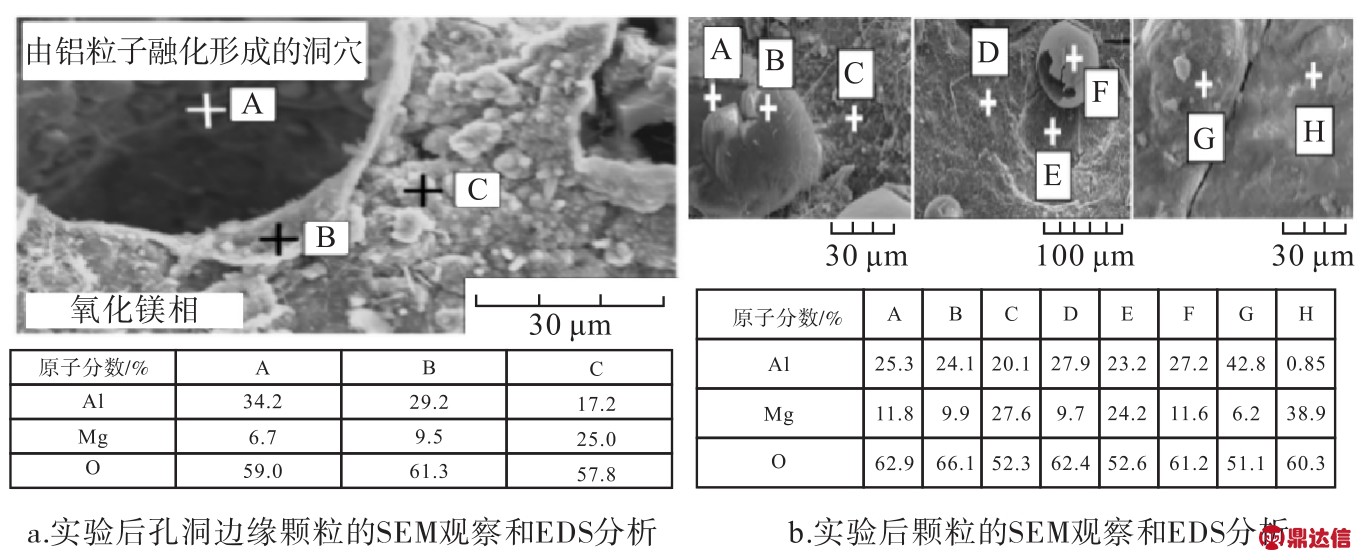
图6 实验后不同位置颗粒的SEM观察和EDS分析
Fig.6 SEM observation and EDS analysis of particles at different positions after experiment
3 镁处理钢中夹杂物研究进展
3.1 Fe-Mg-O-S体系
YANG等[28,31-33]通过向钢液中吹入镁蒸气发现当氧浓度高时,脱氧优先进行,因为镁与氧的平衡浓度远低于镁与硫的平衡浓度,只有当氧浓度很低时才会发生脱硫。在目前的脱硫过程中,镁的浓度首先迅速增加,达到最大值,然后逐渐下降到很低的水平。当镁浓度达到最大时,硫浓度变得非常低。因此,熔体中的镁主要是溶解的镁,随后镁浓度的降低是由于熔体表面的蒸发和溶解的镁向气泡表面的传质。脱硫主要发生在气泡表面,通过气液相质量传递的混合控制模型表明,减小气泡尺寸,增加喷枪浸入深度,并将颗粒装料分成几个部分来提高镁的脱硫效率。
FU等[34]对35CrNi3MoV钢进行铝脱氧,脱氧后添加镁进行处理,发现添加镁后夹杂物尺寸明显减小,细小的近似球状MgO取代了大的三角状Al2O3,形成的MgS-MgO近椭圆的复合夹杂物取代了狭长的MnS夹杂。
王博等[35]通过向钢液中添加镁铝合金,镁形成气泡向钢液表面逸出,气泡上升过程中进行脱氧,同时起到搅拌的作用,有利于夹杂物上浮。脱氧产物随气泡带出钢液。优化了夹杂物的尺寸分布,大尺寸夹杂物比例明显减小,小尺寸夹杂物比例升高。
OHTA等[36]通过研究Fe-10%Ni合金中不同脱氧产物粒度分布特征时,发现脱氧产物的粒径分布宽度以A l2O3>MgO>ZrO2>CaO-A l2O3>MnO-SiO2的顺序降低。随后研究凝固过程中脱氧产物的粒径分布,发现较强脱氧剂的平均粒径比较弱的脱氧剂的平均粒径小,在给定保温时间的固体MgO,ZrO2和A l2O3颗粒的尺寸分布的宽度比液体CaOAl2O3和MnO-SiO2颗粒的宽度宽,如图7所示。因为液态氧化物的界面能小于固态氧化物界面能,所以脱氧液粒子的成核速率变高。这导致初始粒度分布宽度的差异。OHTA等[37-38]通过对均匀形核理论的研究发现,氧化物与钢液之间的界面能越高,形核率反而越低,以MnO-SiO2>CaO-Al2O3>ZrO2>MgO>A l2O3的顺序降低。
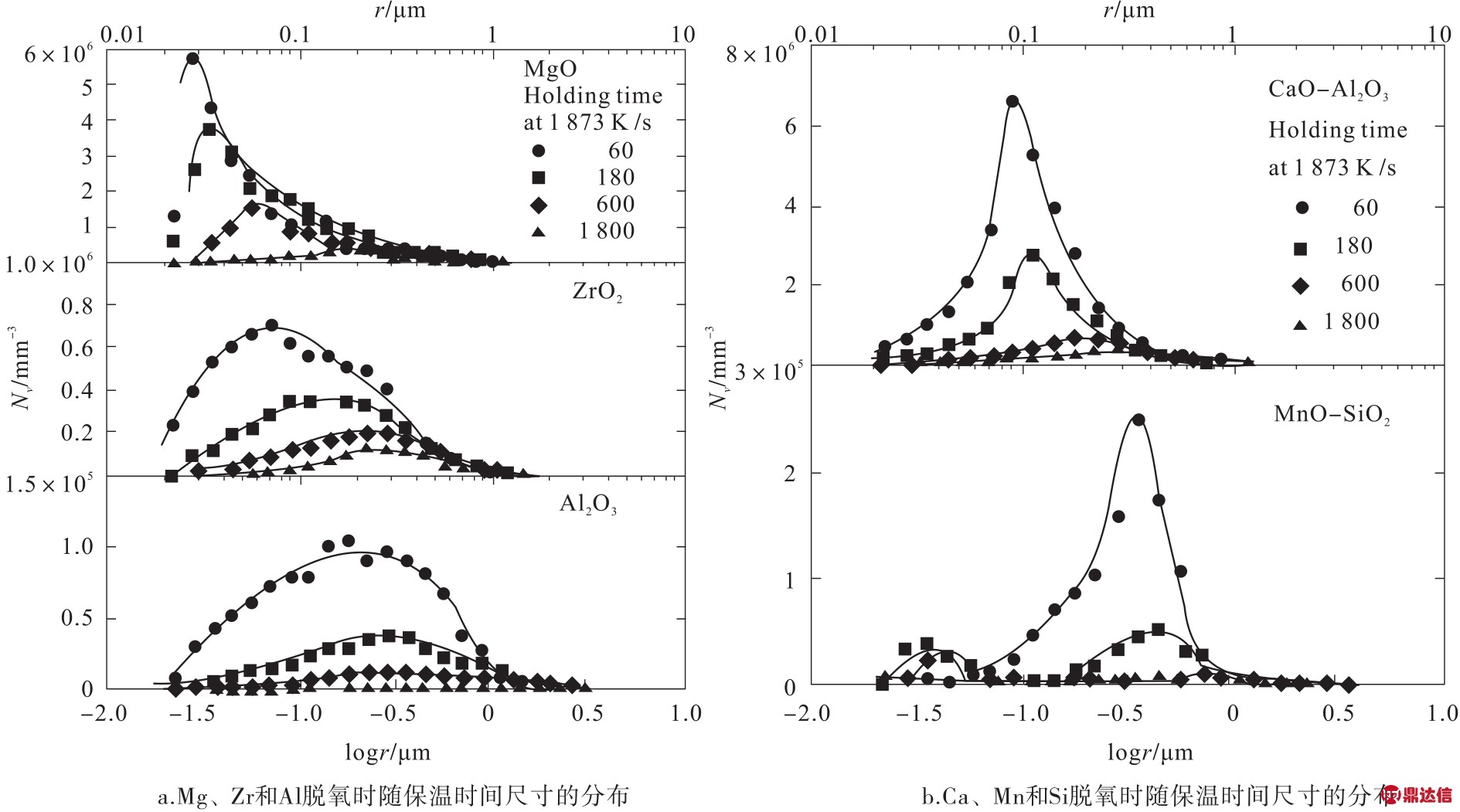
图7 Mg、Zr、Al、Ca和Mn/Si脱氧在1 873 K下保温时尺寸分布
Fig.7 Size distributions of Mg,Zr,Al,Ca and Mn/Sideoxidation products for different holding times at 1 873 K
KARASEV等[39-40]通过使用LA-ICP-MS检测镁脱氧钢以及铝镁复合脱氧钢中脱氧产物在Fe-10%Ni合金中尺寸分布,如图8a所示,由于初生夹杂物的凝结和MgO与来自A l2O3坩埚的溶解A l的反应,MgO颗粒的总数量显著减少并且尺寸随着保持时间的增加而增加。复合MgO-A l2O3颗粒的N V(每单位体积的颗粒数量的变化)和d V(夹杂物的空间直径)值随着保持时间的增加而增加。图8b可以看出,随着保温时间的增加,夹杂物的数量在减少,相同保温时间,单独用镁脱氧与钛镁复合脱氧的N V几乎相同,但镁脱氧下降的速率比钛镁复合脱氧要快。
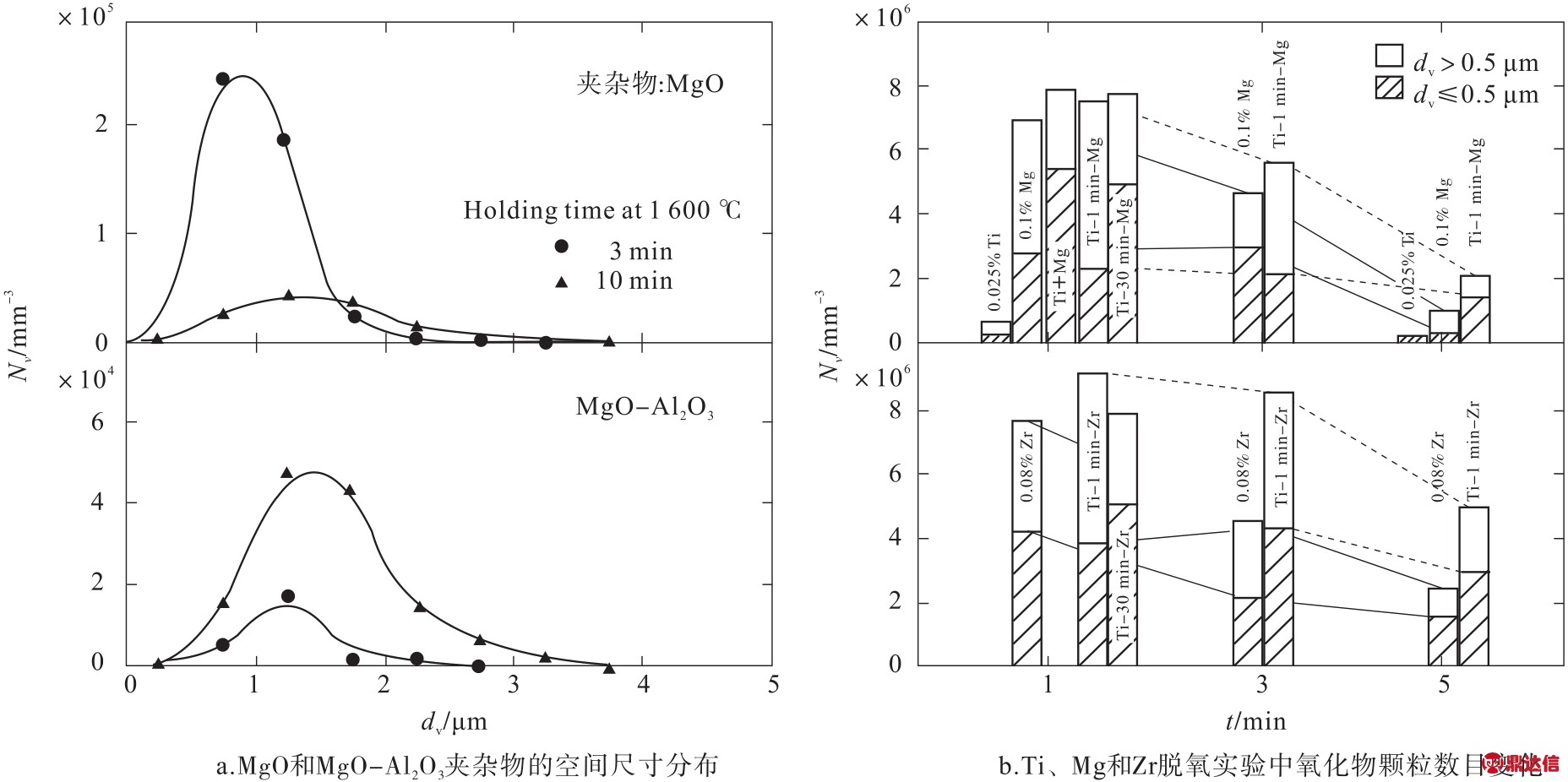
图8 不同种类氧化物颗粒空间尺寸分布及数目变化
Fig.8 Variations in size distribution and number of different types of oxide particles
3.2 Fe-Mg-Al-O体系
TAKATA等[41]通过向钢液中通入镁蒸气进行脱氧实验,发现钢液中全氧含量最终降到1.5×10-5,形成的镁铝尖晶石层围绕在氧化铝夹杂物周围,有效地防止夹杂物的聚集。较大的夹杂物容易通过上浮的气泡浮到钢液表面,较小的夹杂物倾向于留在钢液中,有利于钢在凝固相变过程中晶粒细化。陈斌等[42]对42CrMo钢液进行铝脱氧后进行镁处理,发现铝脱氧进行镁处理钢中总氧含量比铝脱氧后进行钙处理钢要低,并且明显低于单独用铝脱氧的钢。镁处理钢中夹杂物的数量明显少于钙处理以及单独铝脱氧,并且都是细小的,粒度小于2μm的镁铝尖晶石夹杂物。
WANIB等[43]研究发现镁铝尖晶石是由钢液中溶解的铝还原镁质耐火材料形成的,在坩埚界面附近的晶粒逐渐长大,其生长认为是普通的随机机制,没有指向性,形成微观粗糙的表面。而OKUYAMA[26]等通过研究镁质耐火材料的侵蚀问题时采用有渣和无渣两种冶炼方式,同样得到钢液中的镁铝尖晶石同样是由钢中溶解铝与镁质耐火材料反应得到。OHTA[36]通过研究Fe-10%Ni合金中不同脱氧剂加入顺序对脱氧产物的影响时,发现先加铝后加镁的脱氧剂顺序可以有效地得到MgO-Al2O3夹杂物尺寸分布特点与单独进行铝脱氧类似。而先镁后铝的脱氧剂顺序不能将MgO夹杂物进行改性,夹杂物尺寸分布特点与单独用镁脱氧类似,如图9所示。
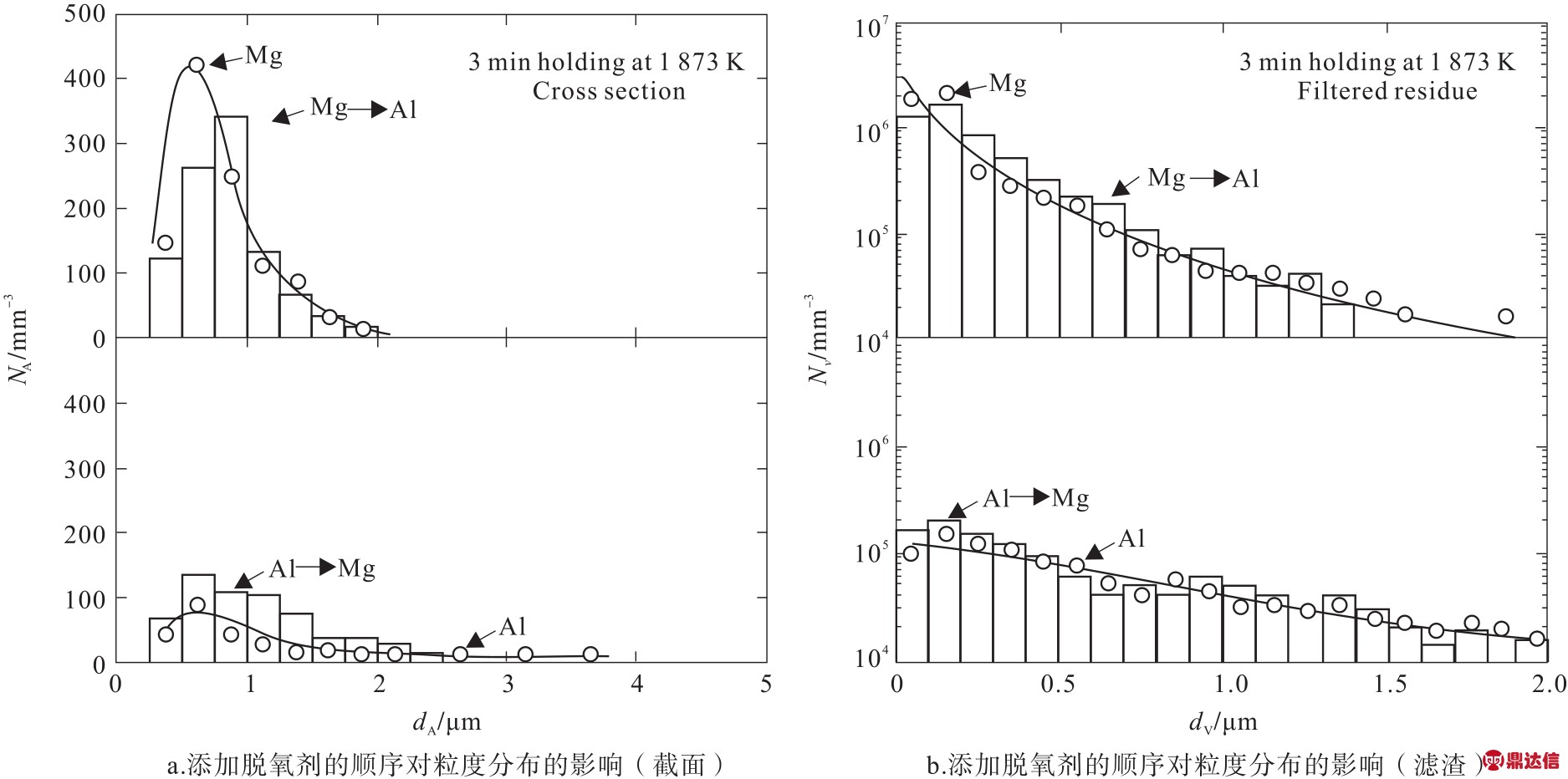
图9 Mg/A l脱氧剂添加顺序的不同对夹杂物粒度的分布影响
Fig.9 Effect of Mg/A l deoxidizer addition order on particle size distribution of inclusions
WANG等[44]研究加入镁对不同铝含量钢中夹杂物均匀分布的影响时,发现当镁含量逐渐增加时,钢液中夹杂物由Al2O3改性为MgO-Al2O3+MgO。随着保温时间的延长,钢液中夹杂物分布越均匀,夹杂物尺寸变小,数量减少。王建等[45]通过研究镁处理对钢中夹杂物的变性研究,发现镁能将钢中的Al2O3夹杂变为镁铝尖晶石,由于镁铝尖晶石在钢水中以固态的形式存在,没有聚合长大的过程。夹杂物的尺寸非常细小,弥散分布在钢中,如图10所示。同时镁可以使钢中的硫化物以MgS或MgS-MnS的形式存在,镁处理后的夹杂物尺寸大大减小。
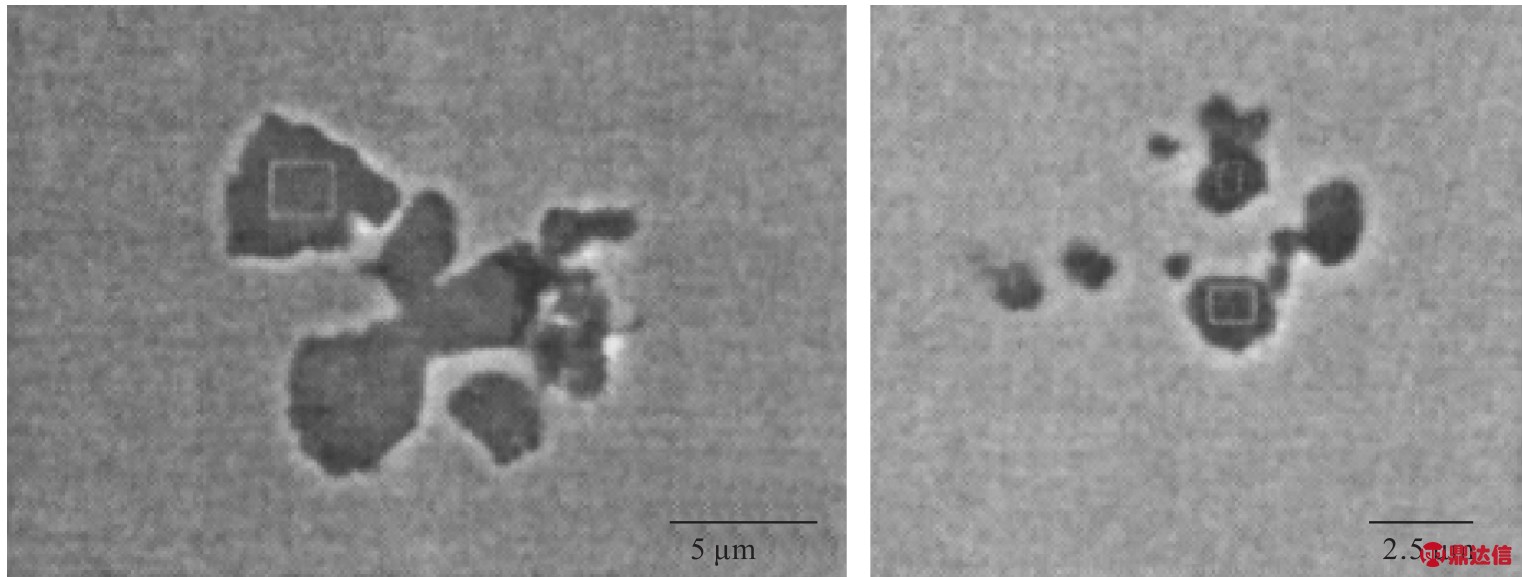
图10 镁对A l2O3夹杂物的改性效果
Fig.10 Modification effect of magnesium on A l2O3 inclusions
3.3 Fe-Mg-Al-Ca-O体系
MA等[46]通过研究钙镁复合处理对轴承钢中夹杂物的演变行为以及粒度影响时发现,添加镁丝不利于二次氧化控制轴承钢中的总氧含量,但镁可以将不规则和团聚的A l2O3夹杂物改性成球形MgO或MgO·A l2O3夹杂物,夹杂物的尺寸更加细小。WANG等[47]在研究MgO基耐火材料的侵蚀时发现,在MgO基材中加入氧化铝生成镁铝尖晶石,可以极大限度地阻止炉渣渗入MgO基材。而镁铝尖晶石的溶解导致液相氧化物相中A l2O3和MgO含量的增加,在晶界处形成固体氧化物相CaO-A l2O3和CaO-MgO-Al2O3会形成妨碍进一步渗透的障碍。
ZHANG等[48]通过研究镁加入对Al-Ca脱氧熔体中夹杂物的影响,在未加镁的情况下夹杂物主要为CaO-A l2O3复合型液态氧化物,尺寸相对较大。加入镁以后,样品中可以观察到CaO-MgOAl2O3复合夹杂物,夹杂物尺寸减小到2μm,可能是由于夹杂物与熔体之间的接触角和表面张力的变化所致。如果镁含量过大,会导致熔体中形成更多的MgO基夹杂物,夹杂物不均匀。钢中夹杂物改性机理如图11所示。
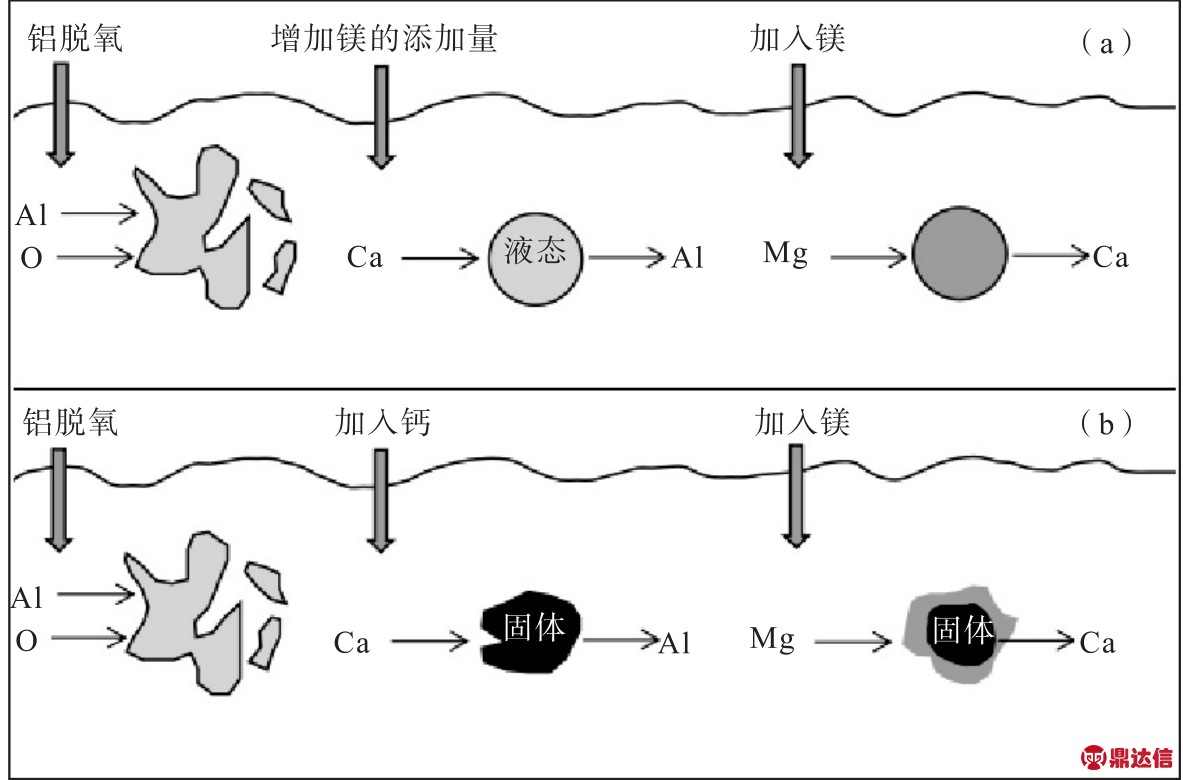
图11 钢液中夹杂物的改性机理
Fig.11 Modification mechanisms of inclusions in liquid steel
NUMATA等[49]通过研究Ca-Mg添加时钢液中夹杂物的组成变化,发现钢液中的钙铝酸盐夹杂物会与溶解镁进行反应生成尖晶石,有效地减小了钢中夹杂物的尺寸。而钙和镁的添加顺序对夹杂物的处理效果几乎不会产生影响。
JIANG等[50-51]在研究高碱性渣精炼高强度合金钢中非金属夹杂物演化机制时,发现42CrMo合金结构钢中夹杂物主要为MgO-A l2O3尖晶石。随着钢水中镁含量的增加,夹杂物中MgO的含量也随之增加。伴随着钢水中镁含量的增加,尖晶石夹杂物逐渐从球状变为角状。夹杂物改质机理如图12所示。YANG等[27]和WANG等[47]通过对镁铝尖晶石进行钙处理,发现夹杂物中微量的钙有助于将镁铝尖晶石改变为球状夹杂物,而且钙处理可以防止耐火材料进一步被侵蚀。
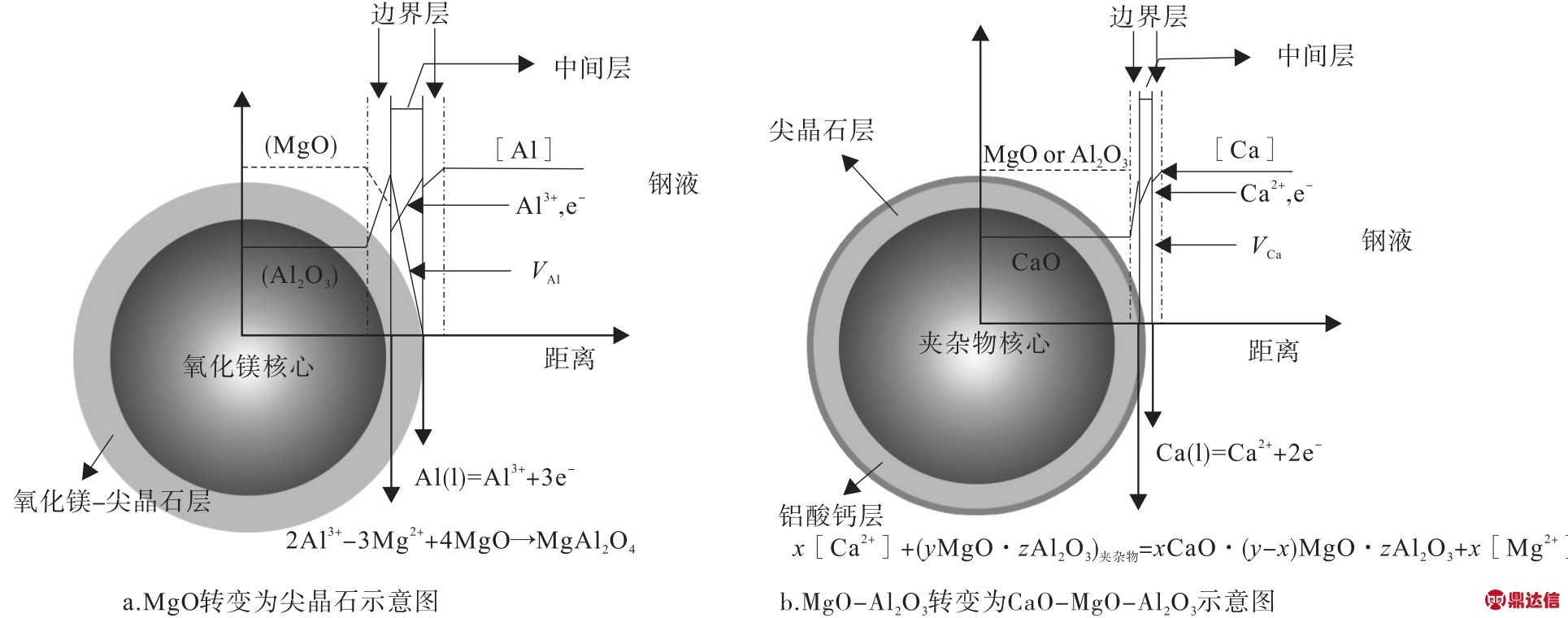
图12 MgO和MgO-Al2O3夹杂物转变模型
Fig.12 Model for MgO and MgO-Al2O3 inclusion transformation
3.4 镁在其他体系下的研究
WU等[52]在研究镁处理Ti-Al复合脱氧钢时,发现钢中生成大量细小的A l2O3-MgO-TiO x复合夹杂物,可为MnS的析出提供核心,诱导贫锰区附近针状铁素体析出,如图13所示。ZHANG等[14]在研究Mg对Al-Ti脱氧熔融钢中夹杂物行为以及粒径的影响,在没加镁的情况下夹杂物主要为Al2O3-Ti3O5复合夹杂物,尺寸相对较大。加入镁以后,样品中可以观察到A l2O3-Ti3O5-MgO复合夹杂物,夹杂物尺寸减小到2μm。镁可以改性熔体中的固体钛酸铝夹杂物,但在初始阶段夹杂物中有未反应的核。可以考虑适当添加钛,以确保液体夹杂物的形成,提高改性效率。为了达到钢液中的全液态夹杂物,镁和钛的添加量应该在实践中同时考虑。
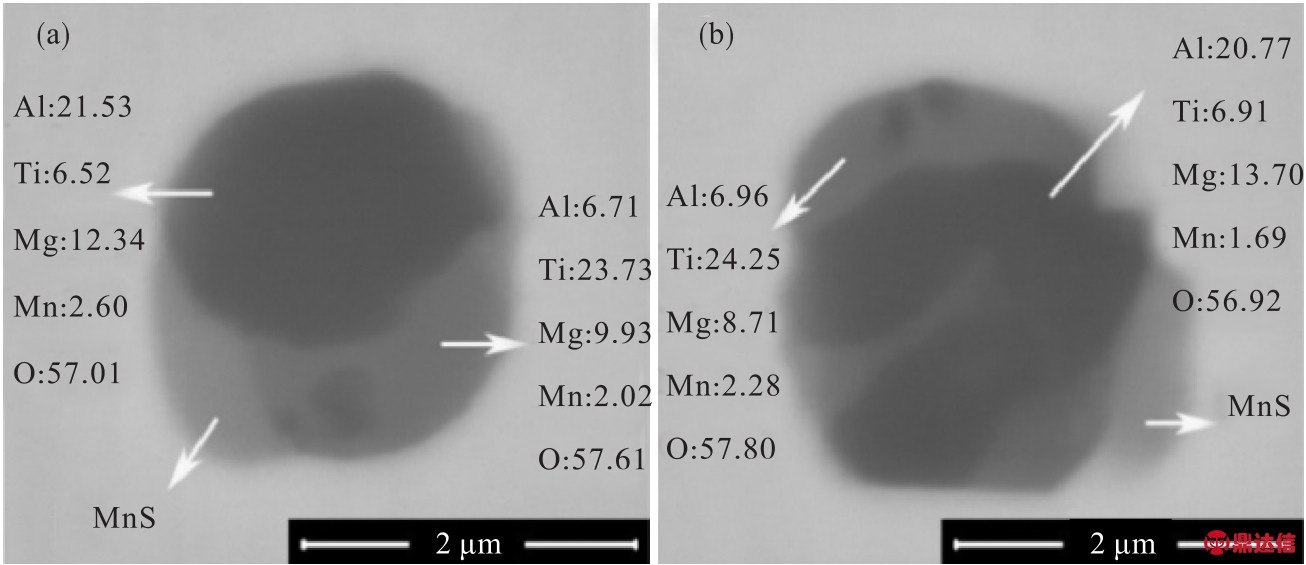
图13 典型夹杂物的形态和组成
Fig.13 Morphology and composition of typical inclusions
HAN等[53]在研究Mg添加对Mn/Si/Ti脱氧钢中夹杂物的影响时发现,钢中夹杂物的典型形态为含有中心氧化物和周边MnS的复杂夹杂物。随着钢中镁含量的增加,夹杂物的中心氧化物相逐渐发生变化,按照 Ti2O3→Ti-Mg-O→MgTiO3→MgO演变,夹杂物的平均尺寸减小,如图14所示。而CHANG等[54]研究Mg对Mn-Si-Ti脱氧钢中非金属夹杂物析出时的影响,发现随着镁含量的逐渐增加,夹杂物的中心氧化物相会按照Ti-Mn-O→Mg-Mn-Ti-O→Mg-Mn-Ti-O+MgO→MgO的顺序演变。

图14 钢中典型非金属夹杂物形貌演变过程
Fig.14 Evolution in morphology of typical non-metallic inclusions in steel
4 镁的加入方法
纯镁的沸点1 090℃,在炼钢温度(1 600℃)下极易气化,使其在钢液中镁的溶解度仅有0.056%[55]。如果采用金属镁的形式加入到钢液中,不能很好地起到脱氧以及对夹杂物的改质处理作用。为了使钢液中能够溶解更多的镁,保证镁的收得率,国内外冶金工作者进行了大量尝试,具体方法及效果见表2。钢液中加镁的方式可以采用纯镁以及镁合金。通过镁蒸气进行脱氧,可以将全氧含量由7×10-5降到1.5×10-5左右,脱氧效果明显。通过镁合金处理钢中夹杂物,可以使钢中夹杂物的形状变得规则,夹杂物由5μm降到2μm以下尺寸明显减小。
表2 加镁方法
Tab.2 Magnesium addition method

5 结语
(1)镁处理钢液的热力学研究发现,相同的反应在不同的体系下得到不同的吉布斯自由能变化。在不同的钢液体系下使用一阶、二阶相互作用系数计算钢液中溶解镁、溶解氧的关系,得到的Mg-O平衡曲线不相同。
(2)通过对镁处理夹杂物动力学的研究,发现在含有镁的夹杂物中,夹杂物不易聚合。
(3)镁处理可明显改善钢中刚性夹杂物MO x(M=A l,Ti)的形状,将其由不规则形状改质为近似球形,尺寸明显减小,从而大大减轻夹杂物在钢中的危害。
(4)总结了向钢液中加镁的方法,加镁方法可分为镁蒸气加入及合金的方式加入。
(5)洁净钢冶炼已经成为现在以及未来的发展必然趋势,镁将会在很大程度上对钢中刚性夹杂进行改性处理,提高钢材的品质。但是加镁的方式尤为重要,在以后的研究中,将会进一步探索。