摘要 连铸首炉开浇过程受覆盖剂加入等因素影响,IF钢头坯不同部位大颗粒夹杂物含量高于正常铸坯,轧制后容易在冷轧板表面产生夹杂缺陷,影响产品质量。通过采用氮氧成分分析、大样电解分析、扫描电镜分析等手段,研究了IF钢头坯沿拉坯方向夹杂物分布规律,其中头坯T[O]含量随拉坯长度逐渐降低,距坯头4 m之后T[O]达到30×10-6以下,接近正常铸坯水平。基于研究结果,提出了IF钢头坯科学合理的切割尺寸,降低头坯冷轧后的夹杂缺陷风险。
关键词 IF钢 夹杂物 头坯
0 前言
IF钢又称为无间隙原子钢,因具有良好的延伸率和较低的强度,广泛用来冲压变形复杂的汽车零件以及汽车面板。IF钢头坯是连铸浇次开始必然产生的一类非稳态铸坯,由于浇次开始拉速提升的变化、中间包钢水注入过程的二次氧化,开浇结晶器集中加入保护渣等因素,造成头坯夹杂物含量高、洁净度差,轧材表面缺陷甚至开裂风险增加。因此,分析和评估非稳态条件下头坯洁净度变化规律,可以为头坯合理分切和利用起到指导作用,最大程度降低质量风险,提高铸坯利用率。
1 研究方法
1.1 取样及分析方法
研究钢种为含钛IF钢牌号DC04。铸坯为浇次开始产出的头坯,铸坯尺寸:1 367 mm×241 mm×10 m。以头坯坯头为起点,切割坯头长度1.5 m后,在铸坯宽度1/4处,沿拉坯方向每隔0.5 m用火焰切割方式切取一块铸坯试样,试样尺寸为:100 mm×100 mm×241 mm。
对每块铸坯样进一步加工成50 mm×50 mm×120 mm的试样,用于大样电解分析大颗粒夹杂物含量。同时,对每块铸坯样加工成Φ5 mm×9 mm的气体样,采用惰气脉冲-红外-热导法进行T[O] 及[N] 含量分析。
1.2 试样工艺条件
1.2.1 连铸设备参数
邯钢IF钢主要在邯宝炼钢厂冶炼生产,现有两台2机2流直弧形板坯连铸机,分别于2008年10月和2009年2月投产,设计年产板坯520万t,产品以汽车板、家电板、管线钢为主。具备漏钢预报、在线调宽、中间包快换、浸入式水口快换、动态轻压下等功能。板坯连铸机基本工艺参数见表1。
1.2.2 冶炼工艺
IF钢冶炼工艺路径:铁水预处理-顶底复吹转炉-RH精炼-板坯连铸。
连铸中间包充分烘烤,开浇前中间包停止烘烤至大包开浇期间进行包盖吹氩保护,降低钢水二次氧化机率。试验炉次开浇正常,大包自动开浇,长水口密封正常,覆盖剂熔化均匀,正常浇注过程中间包钢水重量稳定在50 t~56 t。
表1 连铸机基本工艺参数
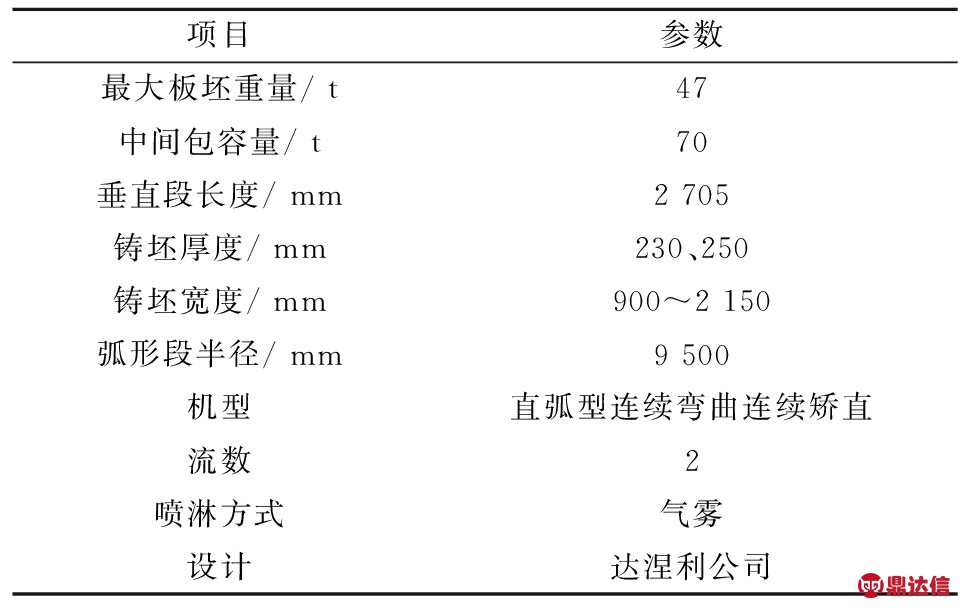
1.2.3 化学成分
化学成分以浇次第一炉浇注中期中间包取样为参考,钢种为DC04(Ti-IF钢),具体成分见表2。
表2 DC04中间包钢水成分 / %

2 检测结果及分析
2.1 头坯氧、氮变化情况
对于IF钢,T[O]包括钢中自由氧和结合氧,当钢水完全脱氧并保持一定酸溶铝含量时,钢中自由氧含量很低。因此一般用T[O]来表征钢中以显微夹杂物形式存在的结合氧水平。钢中氮含量变化来表征钢水二次氧化及吸氮情况。钢中大颗粒夹杂物检测,主要是指颗粒直径大于50 μm的夹杂物每10 kg钢中的质量含量,单位为mg/10 kg钢。所取试样IF钢DCO4头坯不同位置处T[O]、[N]变化情况,如图1所示。沿头坯拉坯方向T[O]、[N]含量整体呈现逐渐降低的趋势。
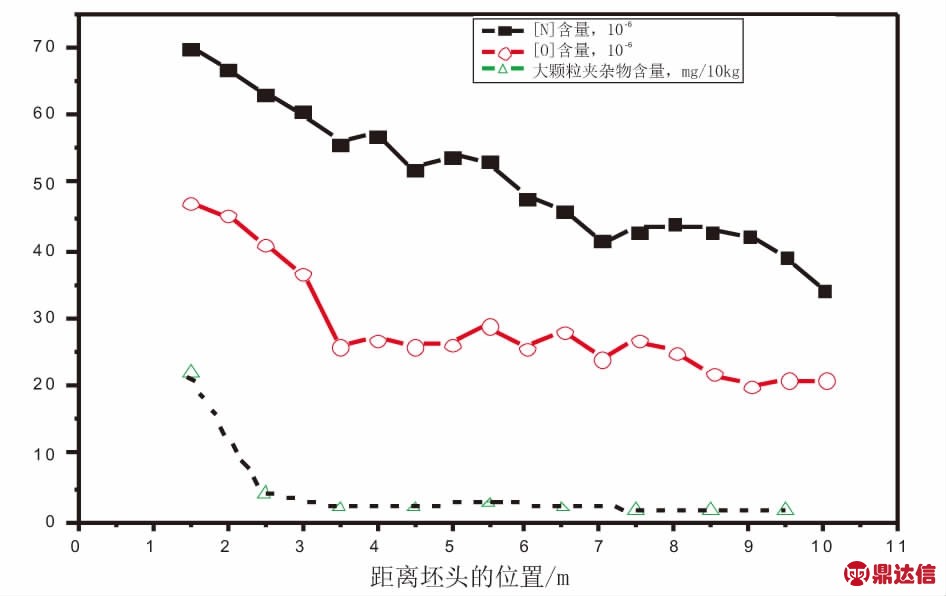
图1 头坯沿拉坯方向不同位置 [O]、[N]及大颗粒夹杂物含量变化
从T[O]变化数据分析,以头坯坯头为起始点,沿拉坯方向自距离坯头1.5 m处至4.0 m处,T[O]含量由47×10-6逐渐降低至30×10-6,接近正常铸坯T[O]水平。IF钢正常铸坯一般T[O]水平控制在15×10-6~25×10-6。
从头坯[N]变化数据分析,自距离坯头1.5 m处至4.5 m处,[N]含量由70×10-6逐渐降低至52×10-6。在距离坯头7.0 m后,[N]含量逐渐降低至43×10-6以下,并且接近正常铸坯水平(36×10-6)。
2.2 头坯中大型夹杂物的分析
对头坯不同位置处铸坯样进行大样电解分析,采用SLIME法电解萃取,过滤分离,对电解后非金属夹杂物进行统计,不同位置头坯中大颗粒夹杂物的含量如图1所示。
沿拉坯方向,头坯中大颗粒夹杂物含量随着距离坯头位置越远,其含量逐步降低。距离坯头1.5 m处,头坯中大颗粒夹杂物含量最高,达到22.1 mg/10 kg钢,这与浇次开浇阶段结晶器保护渣加入及二次氧化有关[1]。此次试验中,距离坯头6.5 m后铸坯大颗粒夹杂物含量趋于稳定,达到2.0 mg/10 kg钢以内。
2.3 大颗粒夹杂物来源
经扫描电镜和能谱定量分析,发现头坯中电解的典型大颗粒夹杂物主要为硅酸盐夹杂和铝酸盐夹杂,尺寸100 μm~300 μm。其中,典型硅酸盐夹杂如图2所示,夹杂物伴有Mg和Ca元素,可能来源于中间包耐材。钢水注入中间包后,中间包镁质耐材在钢水冲刷作用下,随钢流进入结晶器,未及时上浮进入保护渣,被坯壳捕捉。铝酸盐夹杂伴有Mg和Ca元素(如图3所示),可能来源于二次氧化产生的Al2O3夹杂,同时结合中间包覆盖剂中卷入的MgO和CaO,形成复合夹杂物。中间包增加挡渣堰,延长钢水停留时间,可以促进中间包内初始注入的钢水中夹杂物碰撞和上浮[2]。
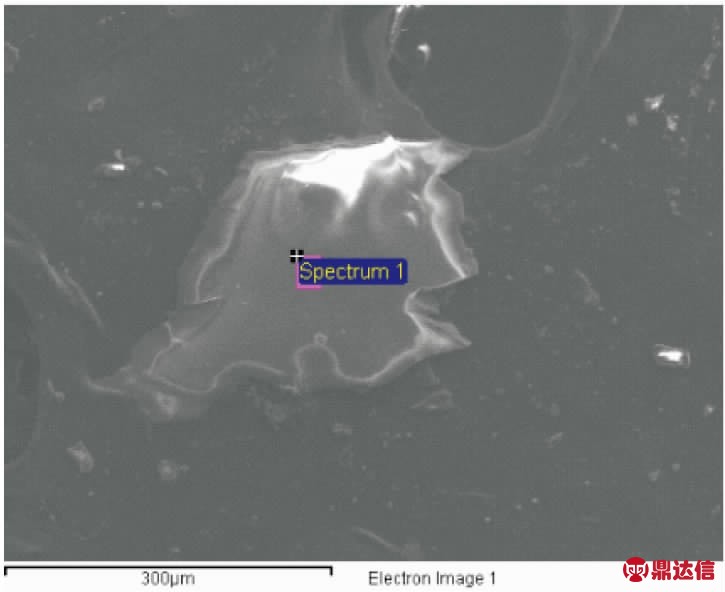
(a) 典型硅酸盐夹杂物形貌
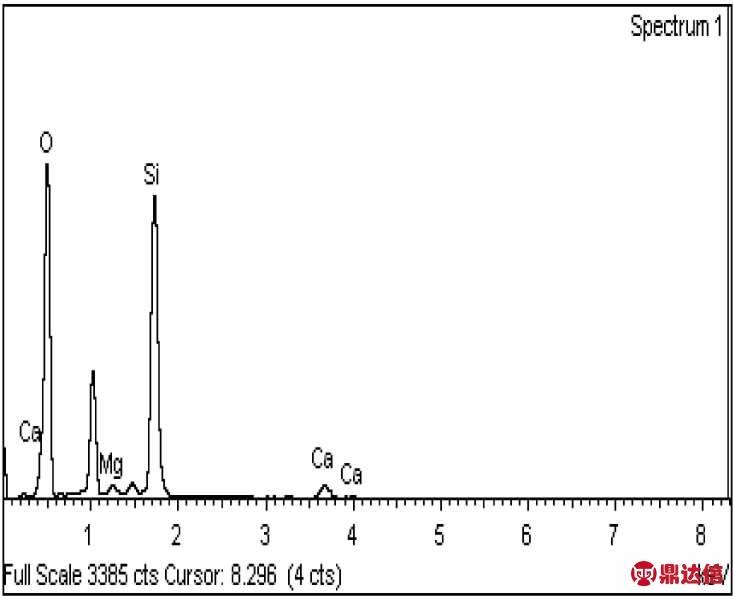
(b) 能谱分析结果
图2 大型夹杂物形貌及能谱检测结果
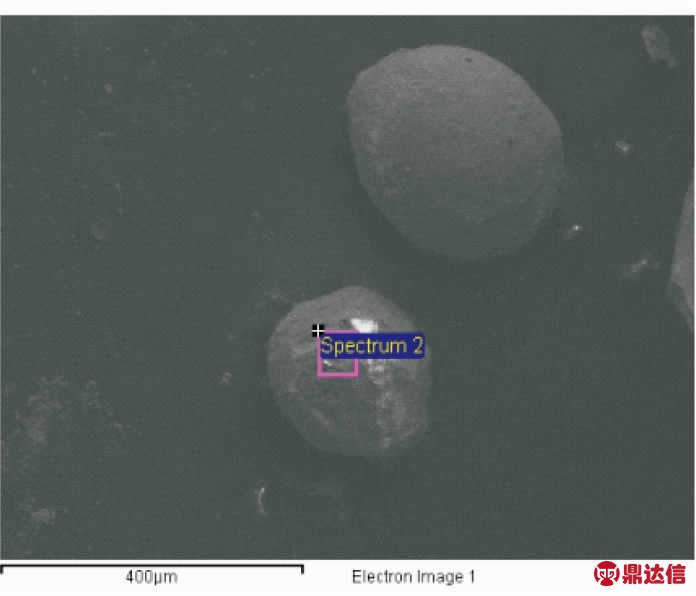
(a) 典型铝酸盐夹杂物形貌
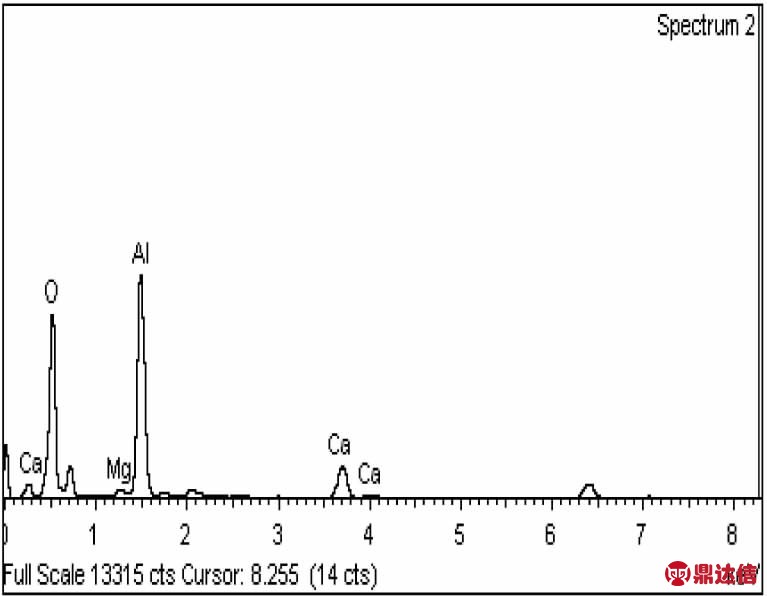
(b) 能谱分析结果
图3 大型夹杂物形貌及能谱检测结果
头坯中大颗粒夹杂物对冷轧板质量影响重大,一般尺寸超过100 μm的大型夹杂物对轧材连续性的破坏作用最大。 如图4所示,金相显微镜下观察到DC04头坯轧制后冷轧钢板中存在的大颗粒夹杂物,尺寸约100μm。夹杂物呈球形,并且基体轧制变形作用下,夹杂物未被轧碎。但是由于夹杂物的存在,轧制后夹杂物周围存在因空洞而产生的微裂纹。能谱检测球形夹杂物的成分为含有Ti的Al-Mg-Si-Ca-O复合夹杂物,其来源于钢液卷渣。
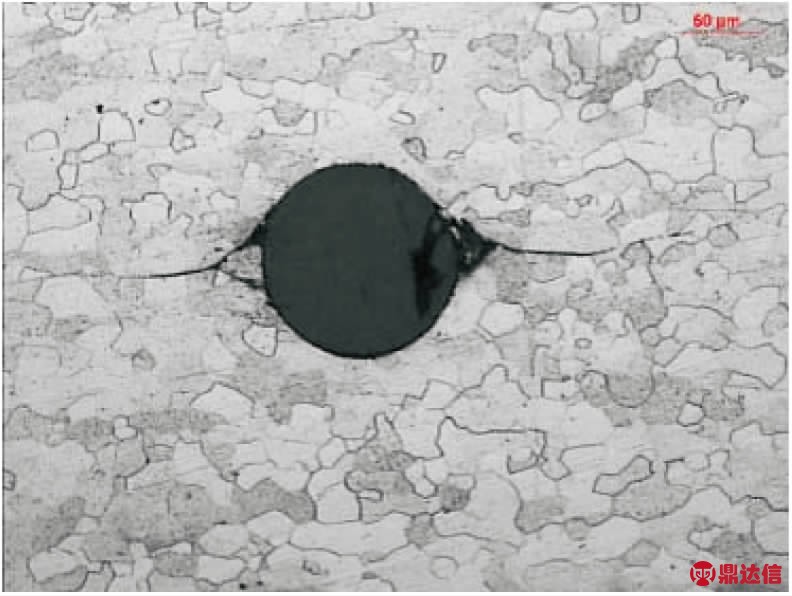
(a) 轧材大型夹杂物形貌
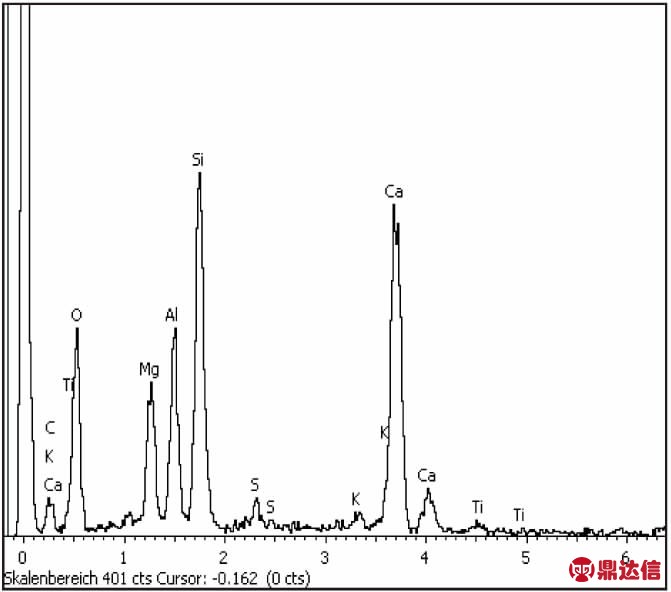
(b) 能谱分析结果
图4 头坯轧材大型夹杂物形貌及能谱检测结果
2.4 头坯切割方式
结合上述分析,IF钢DC04头坯质量主要受到夹杂物含量、氮含量等因素的影响。距坯头4 m之后T[O]达到30×10-6以下,接近正常铸坯水平。距坯头7.0 m后,[N]含量接近正常铸坯水平。距坯头6.5 m后,大颗粒夹杂物含量趋于稳定,达到2.0 mg/10 kg钢以内。因此提出了IF钢头坯切割优化方式,将原先头坯切割1.5 m甩废优化为切割甩废长度6.5 m,保证其后面一块铸坯T[O]、[N]、大颗粒夹杂物含量接近正常铸坯水平,降低产品质量风险。
采用头坯优化切割方式后,跟踪58个浇次IF钢头坯经轧制后未发现冷轧板表面夹杂缺陷。
3 结论
1)沿拉坯方向,IF钢头坯T[O]、[N]、大颗粒夹杂物含量均呈现明显下降趋势。距坯头4.0 m处T[O]接近正常铸坯水平。距坯头7.0 m后,[N]含量接近正常铸坯水平。距坯头6.5 m后,大颗粒夹杂物含量趋于稳定,达到2.0 mg/10 kg钢以内。
2)IF钢头坯中大颗粒夹杂物主要为硅酸盐夹杂和铝酸盐夹杂,一般夹杂物颗粒尺寸100 μm~300 μm,此类夹杂物主要来源于耐材侵蚀、钢液卷渣。该尺寸范围内的大颗粒夹杂物不易被轧碎,在冷轧板轧薄过程对钢板组织会产生微裂纹,是造成冷轧板开裂的裂纹源之一。
3)结合分析,合理界定IF钢头坯甩废长度,降低产品质量风险。