摘要 为研究滚动直线导轨的润滑性能,对LG-45 型滚动直线导轨进行了运动分析,建立了导轨副的弹流润滑模型,并对其润滑性能进行了研究,分析了不同接触角、滚珠直径、曲率比、润滑油参数下的油膜厚度,同时讨论了滚珠直径、接触角对导轨副润滑状态的影响。结果表明,在接触角增大时,油膜厚度减小;在滚珠直径增大时,油膜厚度增大;在曲率比增大时,油膜厚度增大,但增加的趋势减小;在相同工况下,润滑油黏度和黏压系数较大时,膜厚较大。在文中研究工况条件下,滚珠直径和接触角变化时不会改变导轨副的润滑状态。
关键词 滚动直线导轨 运动分析 油膜厚度 润滑状态
0 引言
滚动直线导轨是一种广泛应用的传动功能部件,导轨沟槽与滑块滚珠之间的摩擦磨损是影响定位精度和使用寿命的主要因素,润滑可以避免沟槽与滚珠之间的直接接触以减少二者之间的摩擦磨损,从而提高定位精度和使用寿命。
现代加工技术对高速、精密和可靠性提出了更高的要求,导轨作为基础部件,其润滑性能对机床的定位精度和使用寿命有重要影响。目前,对导轨副的研究主要有以下3个方面:一是对导轨副滚珠和滚道沟槽接触变形的研究,许向荣[1]对导轨副接触刚度进行研究并建立了接触刚度模型。姜大志等[2-3]以滚珠为分析对象,基于赫兹理论推导出弹性变形求解模型。二是对导轨副摩擦磨损的研究,Li等[4]分析了滚动直线导轨的摩擦变化并设计了摩擦测量系统。赵义鹏等[5]采用试验的方法对导轨副的摩擦磨损特性进行了研究。张怡雯等[6]通过试验探究了速度和供油量对滚动直线导轨副摩擦力的影响。三是对导轨副润滑的研究,申明主等[7]针对滚动直线导轨,选用两种润滑脂进行测试,测量油膜厚度并比较两种润滑脂的润滑性能。张朝辉等[8]27-29用Hamrock-Dowson 经验公式计算了导轨副的最小膜厚以及不同参数对最小膜厚的影响。李林林[9]运用弹流润滑理论、分形理论等对滚动直线导轨的润滑性能进行了分析。
目前,对导轨副的研究主要集中在接触变形、摩擦磨损方面,对滚动直线导轨副润滑的研究多集中于试验研究,理论研究较少。采用经验公式只能估算滚动直线导轨的油膜厚度,无法对润滑状态进行精确的计算和判断。因此,对导轨副的润滑特性的研究具有重要意义。
以LG-45 型导轨为对象,探讨不同接触角、滚珠直径、曲率比对其润滑的影响,以及不同润滑油参数对导轨的润滑特性的影响,并通过计算判定导轨的润滑状态。研究将为滚动直线导轨的润滑提供一定的理论依据。
1 数学模型
1.1 导轨副模型
以四方向等载型导轨为研究对象。图1所示为四方向等载型导轨模型,导轨所受垂直载荷和水平载荷为P(P=F/iz),F 为总载荷,i 为沟槽列数,z 为每列沟槽有效承载的滚珠数目。设θ为接触角,则单个滚珠所承受载荷为w(w=P/cos θ)。其中,滑块的运动方向沿x 方向,x 方向垂直于纸面。滚珠的运动方向如图1所示。
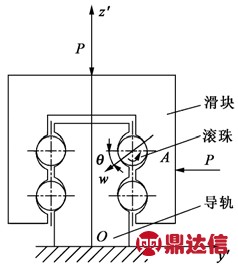
图1 四方向等载型导轨模型
1.2 速度分析
滚动直线导轨传动是通过滚珠在滚道中的循环运动实现的。滚珠在承载区运动时并非纯滚动,滚珠的运动形式比较复杂,包括滚动运动、滑动运动、自转运动以及三者的综合运动形式。选取某一时刻的位置,建立如图2所示的坐标系[10]。
图2(a)中,Oy'x'z'为固定坐标系,滑块沿x轴方向运动,OA 为滚珠的自转轴线,β 为滚珠自转轴线OA 与y'Ox'平面的夹角,β'为滚珠自转轴线OA 在y'Ox'平面内的投影与y'轴的夹角。ω0为滚珠自转角速度,ωx'、ωy'、ωz'分别为ω0在坐标系Oy'x'z'各坐标轴上的投影,则有
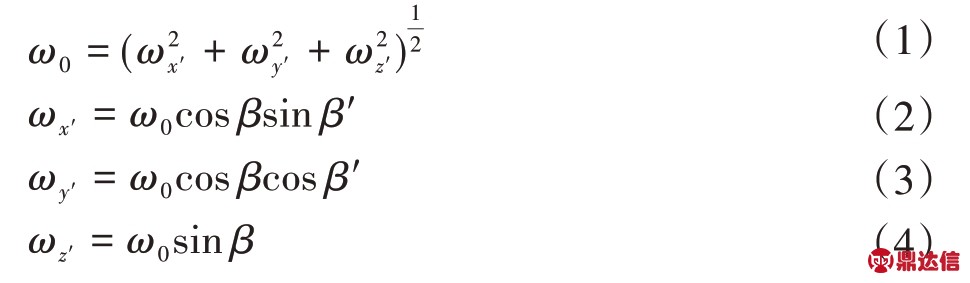
在椭圆接触区中存在N-N,只做纯滚动运动,滑块与滚珠在这两点处的线速度相等。如图2(b)所示,根据赫兹理论,可知该接触椭圆表面的曲率半径Rg为

式中,D 为滚珠直径;f 为沟槽曲率比,f=r/D,其中,r为沟槽半径。

图2 导轨副的速度分析图
滚珠与沟槽之间的接触为椭圆接触,图2(b)中,a、b 分别为接触椭圆的短半轴和长半轴长度。接触平面与y'Ox'平面夹角为θ,滑块运动方向为x'轴方向,卷吸速度方向为接触椭圆坐标系中x轴方向,且x'轴与x轴平行。
假设滑块运动线速度为ua,则有
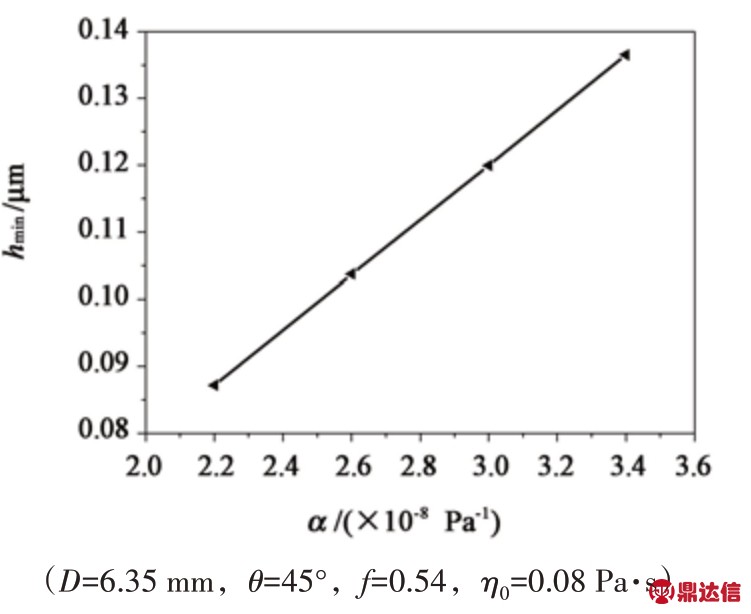
设M(xi,y)i为接触椭圆内任意一点,滚珠沿滚动方向的线速度为ui,则有
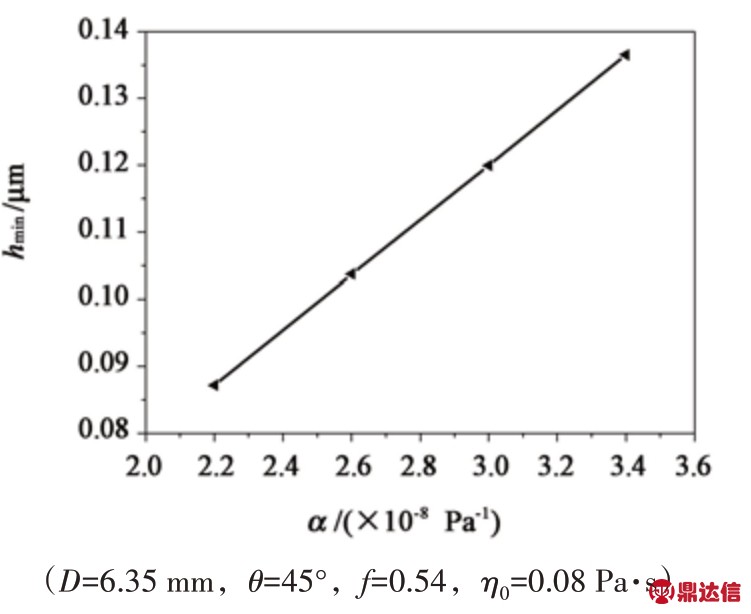
式中,xi和b 相较于Ry和D/2 可以忽略,则式(7)可写为

根据卷吸速度定义,可得导轨副的卷吸速度表达式为
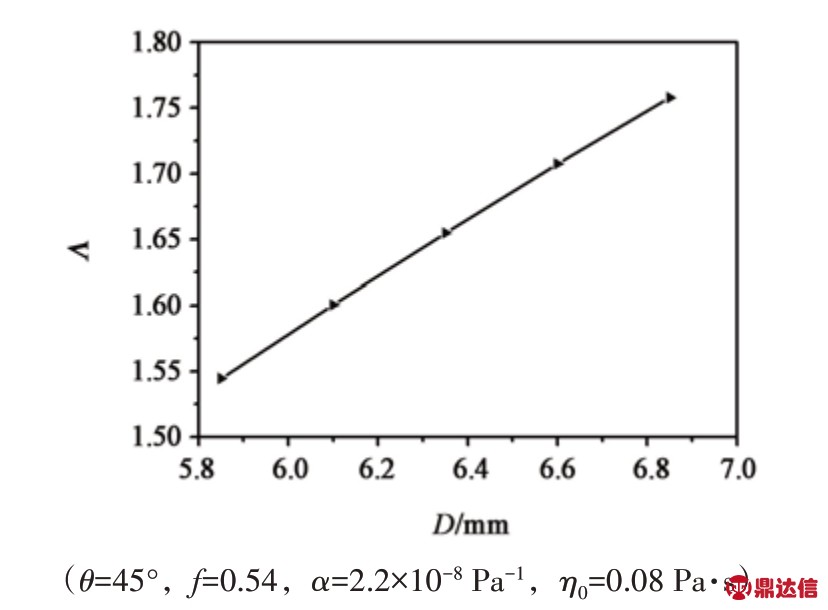
本文中,θ=45°、β=45°、β'=30°,综合式(6)~式(9)可得u=0.966ua。因卷吸速度与滑块速度相差较小,取u=ua。
1.3 Reynolds方程
Reynolds方程为
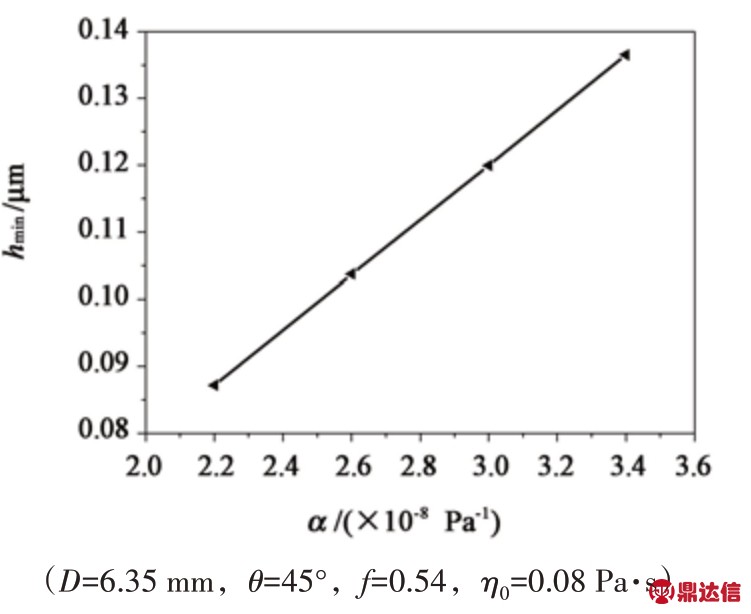
式中,x、y 均为接触椭圆坐标变量;p 为压力;h 为膜厚;u为卷吸速度;ρ为密度;η为黏度。
Reynolds方程的边界条件为

1.4 黏压方程
Reynolds 方程中的黏度η 通过Roelands 黏压关系式[11]求得,即

式中,η0 为环境黏度。z0 与Barus 黏压系数α 的关系为

1.5 密压方程
由Dowson-Higginson 密压关系式[12]求解密度ρ,得

式中,ρ0为环境密度。
1.6 膜厚方程
膜厚方程为

式中,Rx、Ry分别为x、y 方向的综合曲率半径;E为当量弹性模量;h00为刚体中心膜厚。
1.7 载荷方程
载荷方程为

1.8 接触参数
根据Hertz接触理论,有关参数计算用到公式
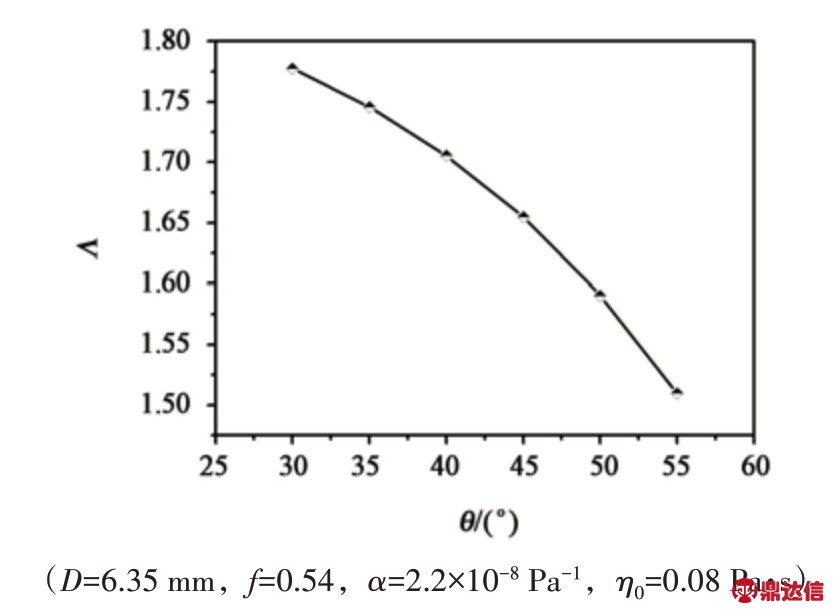
式中,ke为椭圆比;F2为第二类椭圆积分;pH为最大Hertz压力。F2由Marho回归经验公式求得,即

椭圆比计算公式[8]27为

2 数值方法
数值计算需在方程无量纲化后进行,定义无量纲参数为:
采用多重网格法[13]求解油膜压力,采用多重网格积分法[14]计算膜厚方程中的弹性变形。采用5 层网格,沿X、Y 方向节点数分别为257。为保证数值仿真结果的准确性,椭圆接触区边界坐标xin=4.8a、xout=1.6a、yin=4.2a、yout=4.2a。当压力相对误差和载荷相对误差小于1×10-3时,达到收敛精度,跳出循环,计算结束。
3 计算结果及分析
LG-45 型滚动直线导轨的公共输入的导轨参数为:每列滚子有效承载数z=13,沟槽列数i=4,总载荷F=500 N,卷吸速度u=60 m/min。
接触固体基本参数为:综合弹性模量E=226 GPa。
3.1 接触角θ的影响
总载荷F=500 N,接触角θ=30°~55°,间隔5°。图3 所示为D=6.35 mm、f=0.54、α=2.2×10-8 Pa-1、η0=0.08 Pa·s 时最小油膜厚度随接触角θ 的变化趋势。
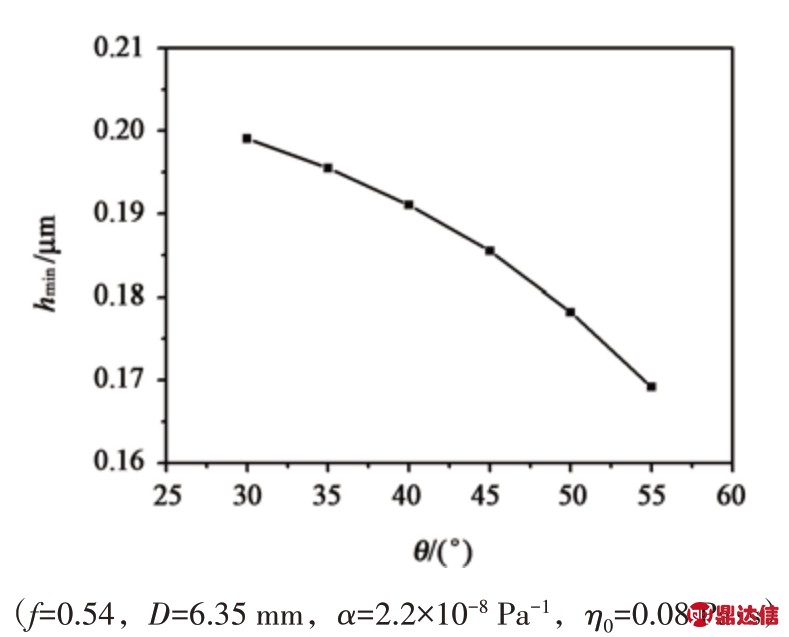
图3 最小油膜厚度随接触角θ的变化
由图3 可知,随着接触角θ 的增大,最小油膜厚度hmin减小,原因是随着接触角θ 的增大,单个滚珠所承受载荷w减小,继而使得膜厚减小。
3.2 滚珠直径D的影响
滚珠直径D范围为5.85~6.85 mm。当θ=45°、f=0.54、α=2.2×10-8 Pa-1、η0=0.08 Pa·s 时,表1 中给出了最大Hertz 压力pH随滚珠直径D 的变化情况,图4 中给出了滚动直线导轨副最小油膜厚度hmin随滚珠直径D的变化趋势。
表1 最大Hertz压力pH随滚珠直径D的变化
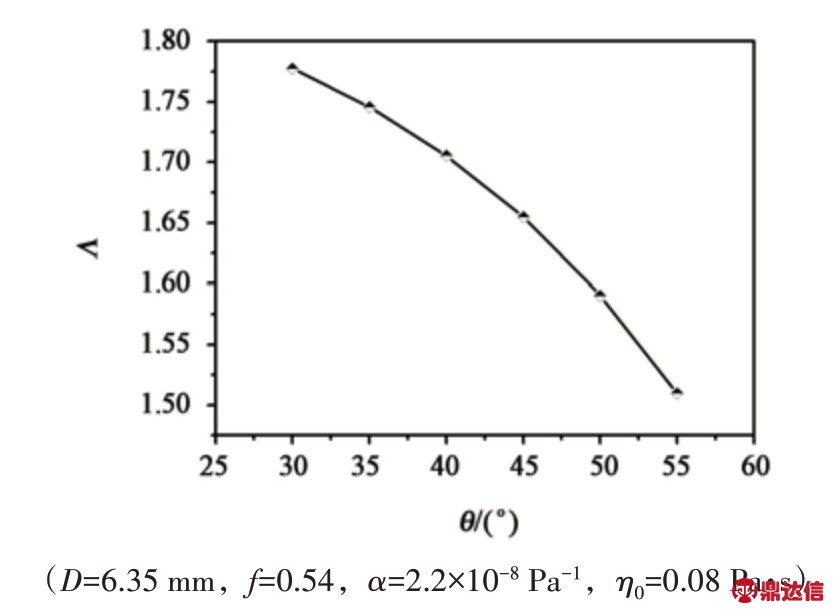
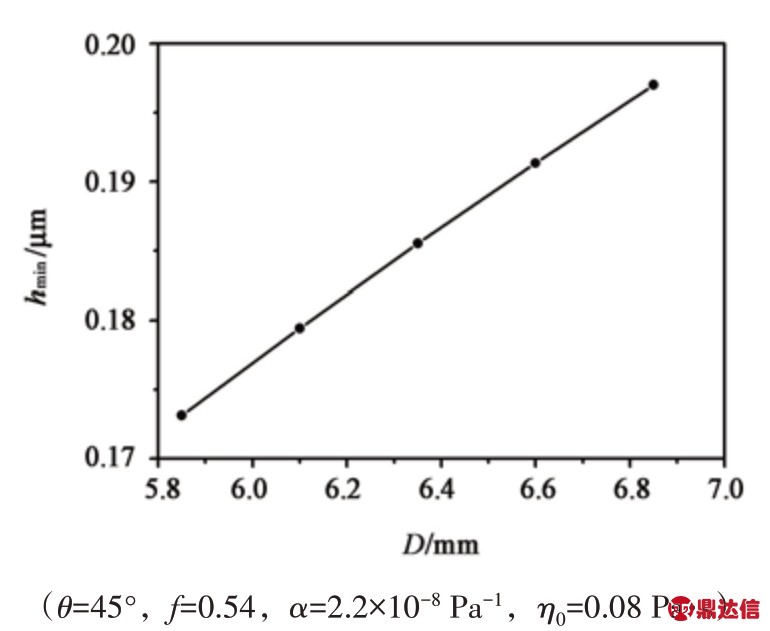
图4 最小膜厚hmin随滚珠直径D的变化
从图4中可以看出,随着滚珠直径D的增大,最小膜厚hmin增大。一方面原因是滚珠直径D 增大,滚珠的线速度ui增大,卷吸速度u增大,使最小膜厚hmin增加;另一方面,由表1可知,最大Hertz压力pH随着滚珠直径D的增大而减小,继而使最小膜厚hmin增大。
3.3 沟槽曲率比f的影响
沟槽曲率比f 的选用范围为0.53~0.57,间隔0.01,速度u=60 m/min。图5中给出了导轨副最小膜厚hmin随曲率比f的变化趋势。
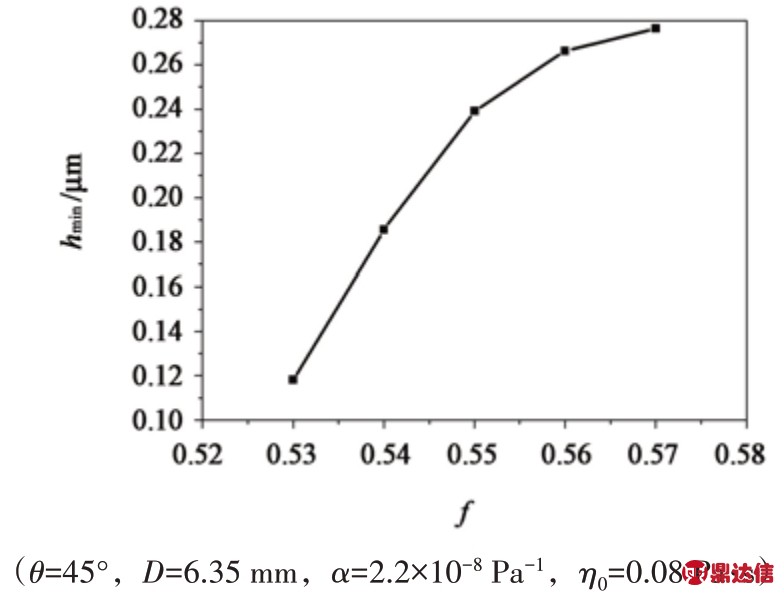
图5 最小膜厚hmin随曲率比f的变化
由图5 可见,随着曲率比f 增大,最小膜厚hmin增大,但是增加的趋势逐渐减小。在工程应用中,导轨副的曲率比取值一般在0.53~0.55 之间,曲率比的细微变化有利于导轨副的润滑。在正常工作条件下,曲率比f的变化不大,它对膜厚的影响一般在5%之内[8]29。
3.4 环境黏度η0的影响
导轨副润滑油的环境黏度选为0.08~0.40 Pa·s。当D=6.35 mm、θ=45°、f=0.54、α=2.2×10-8 Pa-1时,图6给出了最小膜厚hmin随环境黏度η0的变化趋势。
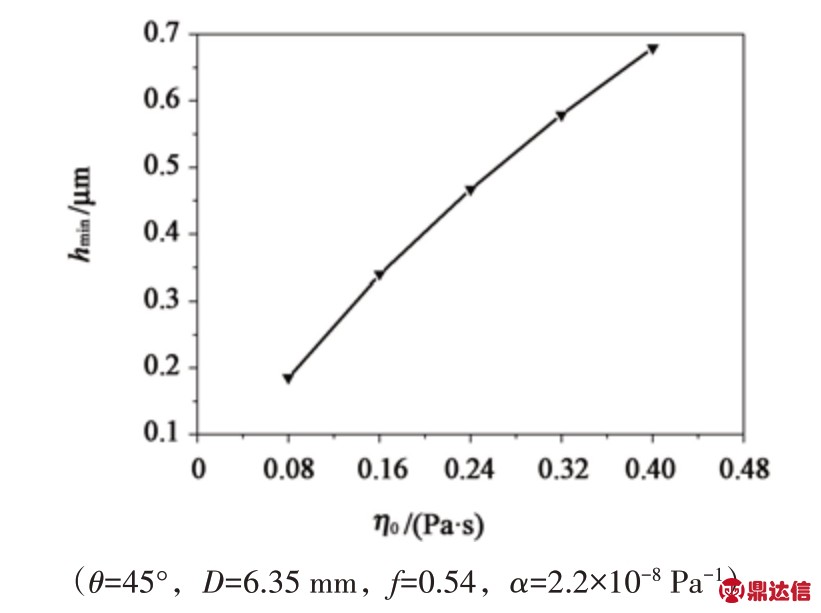
图6 最小膜厚hmin随环境黏度η0的变化
从图6 中可以看出,最小膜厚hmin随着黏度η0的增大而明显增大。
3.5 润滑油黏压系数α的影响
选用黏压系数α 在2.2×10-8~3.6×10-8 Pa-1,当D=6.35 mm、θ=45°、f=0.54、η0=0.08 Pa·s 时,图7给出了最小油膜厚度hmin随黏压系数α 的变化趋势,由图7 可见,随着黏压系数的增大,最小油膜厚度hmin增大。
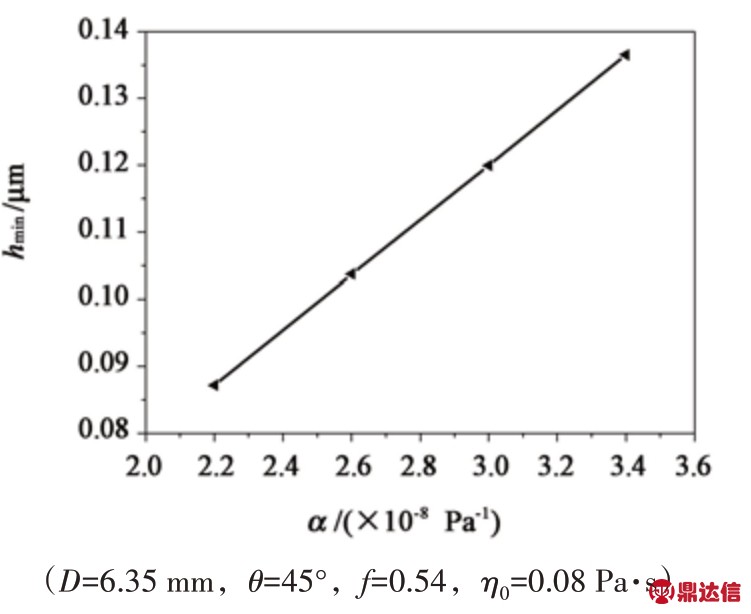
图7 最小油膜厚度hmin随黏压系数α的变化
结合图6 和图7 可知,在相同工况下,黏度越大的润滑油其最小膜厚越大。虽然黏度大的润滑油对导轨副润滑保护效果更好,但也增加了导轨副在做相对运动时的损耗,因此,要选用适宜黏度的润滑油[15]。
4 润滑状态分析
现代机床加工对精度提出了更高的要求,润滑状态取决于润滑油膜厚度和接触体表面粗糙度。对于精密加工,滚珠的表面轮廓均方根偏差值要求为0.05~0.10µm[8]28,滑块沟槽表面轮廓均方根偏差值要求为0.10~0.40µm[8]28。通过计算膜厚比即可判定润滑状态,膜厚比表达式[16]为

式中,σ1、σ2分别为沟槽和滚珠的表面轮廓均方根偏差值。
当Λ≤1 时,为边界润滑状态;当1<Λ≤3 时,为混合润滑状态;当Λ>3时,为全膜润滑状态。
为了研究滚珠直径D和接触角θ对润滑状态的影响,选用沟槽和滚珠的表面轮廓均方根偏差值σ1=0.10µm,σ2=0.05µm。
4.1 接触角θ对润滑状态的影响
当D=6.35 mm、f=0.54、α=2.2×10-8 Pa-1、η0=0.08 Pa·s时,图8中给出了膜厚比Λ随接触角θ的变化趋势。
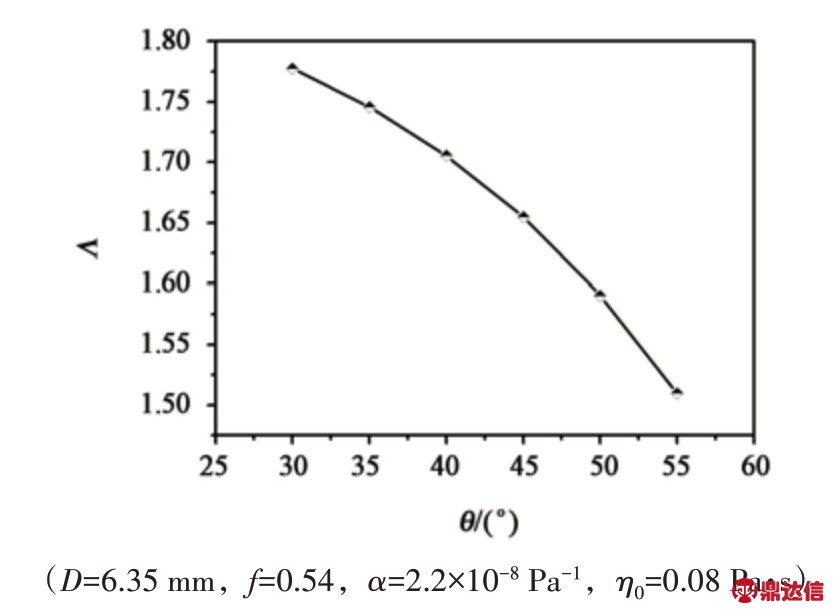
图8 膜厚比Λ 随接触角θ的变化
从图8 中可以看出,随着接触角θ 的增加,膜厚比Λ 减小,且一直处于混合润滑状态。原因是接触角的增加对单个滚珠所受载荷w 减小幅度的影响较小,故膜厚比Λ变化幅度较小。
4.2 滚珠直径D对润滑状态的影响
图9 中给出了膜厚比Λ 随滚珠直径D 的变化趋势,由图9 可见,随着滚珠直径D 的增大,膜厚比Λ增大,膜厚比范围从1.54 到1.76,为混合润滑状态。说明滚珠直径的变化对膜厚比的影响较小。
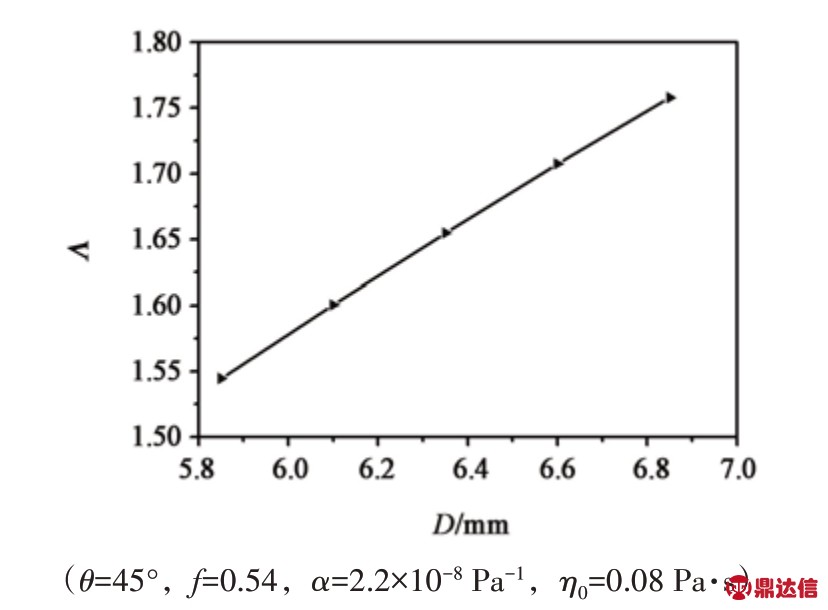
图9 膜厚比Λ随滚珠直径D的变化
5 结论
通过改变导轨参数和润滑油参数,对导轨副的润滑性能进行了研究,得出如下结论:
(1)随着接触角的增大,最小油膜厚度减小。随着滚珠直径的增大,油膜厚度增大。
(2)随着曲率比的增大,油膜厚度增大,但增加的幅度减小。在正常工作条件下,曲率比f的变化不大,其对膜厚的影响不大。
(3)在相同工况下,润滑油环境黏度和黏压系数越大,膜厚越大,但黏度大的润滑油会增加导轨副相对运动的损耗,因此,要选用适宜黏度的润滑油。
(4)在本文研究工况条件下,滚珠直径和接触角不会改变导轨副的润滑状态。