摘 要:胶轮导轨电车滚振试验台是研究胶轮导轨电车轮轨关系的重要平台,激振单元是试验台的核心部件。以胶轮导轨电车滚动振动试验台的激振部分为研究对象,利用UG建立三维模型,并将其导入到ANSYS中进行有限元分析,分析试验台激振部分在最大载荷下的合位移、等效应力和等效应变的等值线云图,以及前5阶固有频率及其相应的振型。分析结果表明:伺服液压缸的存在可以提升试验台的结构特性;试验台的1阶固有频率远离激振频率;通过增加调整垫铁的数量可以提高系统的固有频率。分析验证试验台结构设计的合理性,分析数据为试验台结构的优化提供参考依据。
关键词:滚动振动试验台;胶轮导轨电车;有限元分析;静力分析;模态分析
滚动振动试验台是研究轨道车辆的重要平台,通过滚动振动试验台,可以对轨道车辆运行稳定性、轮轨关系、制动性能展开试验研究[1],但试验台的结构特性直接影响试验效果。试验台在最大载荷条件下的变形过大,不仅影响试验数据的准确性,还可能造成导向轮脱离轨道轮,影响试验的正常进行。进行试验时,激振频率若与试验台固有频率重叠,试验台会因产生共振而被破坏[2]。目前,通常采用有限元分析法研究试验台的结构特性,通过三维建模软件建立试验台的三维模型,并导入到有限元分析软件中进行静力学和动力学分析,得到试验台的应变云图和模态分析结果。
试验台激振部分是试验台主要的动作发生装置,其结构设计是否合理直接影响整个试验台的性能。本文在介绍了胶轮导轨电车滚动振动试验台的基本结构和工作原理的基础上,通过UG三维建模软件和ANSYS有限元分析软件对试验台的激振部分进行计算机辅助分析,这些分析不仅可以检验试验台结构设计是否合理、预防试验台发生共振,还可以为试验台的动力学分析提供理论依据。
1 胶轮导轨电车滚振试验台工作原理及激振部分结构简化
1.1 胶轮导轨电车滚振试验台工作原理
胶轮导轨电车动力走行部滚振试验台的功能是在实验室条件下模拟导轨电车的运行状态,通过测量不同工况下的脱轨系数研究其运行稳定性、轮轨关系和制动性能。为了使模拟的导轨电车运行状态更加接近真实的运行状态,试验台不仅要能够控制导向轮的运行速度,还要能够反演美国三级轨道谱、模拟胶轮导轨电车导向轮与钢轨之间的冲角变化和胶轮导轨电车转向的工况。这些动作都是通过试验台的激振部分来完成的,因此对试验台激振部分的结构特性进行分析对于保障整个试验台的正常工作具有重要意义。
胶轮导轨电车滚振试验台结构如图1所示。试验台的激振部分放置在地坑内,其机械结构主要由轨道轮安装底座、转动器、伺服液压缸安装支架和曲线导轨安装底座组成。
轨道轮安装底座用于安装轨道轮和三相交流变频电机。为了模拟导向轮在导向轨上的运动,用与导向轨相同轨头轮廓的轨道轮代替导向轨,通过导向轮在轨道轮上的转动模拟在无限长导向轨上的滚动。三相交流变频电机通过联轴器与轨道轮连接在一起,可以模拟电车0~100km/h的运行速度。
转动器上端通过竖直放置的4个滑块导轨与轨道轮安装底座连接在一起,底端与伺服液压缸安装支架顶端通过螺栓固定在一起,不仅可以实现轨道轮安装底座与伺服液压缸安装支架之间的相对转动,而且可以实现两者之间的垂向相对移动。地坑内的伺服液压缸推动转动器及以上部分作垂向振动,与轨道谱保持同样的振幅和频率,模拟电车运行时的轨道不平顺。轨道轮安装底座和伺服液压缸安装支架之间装有电动推杆,通过控制轨道轮安装底座和伺服液压缸安装支架之间的相对角度,实现导向轮与轨道轮之间的相对角度的控制,模拟电车转向时导向轮和导向轨之间的冲角变化。
伺服液压缸安装支架通过曲线滑块安装在曲线导轨安装底座上,实现试验台主体沿一定曲率的曲线导轨转动。控制转向角的电动推杆与伺服液压缸安装支架通过耳环式连接,可以推动伺服液压缸安装支架和轨道轮安装底座一起沿曲线导轨转动,模拟动力走行部转向的工况。
曲线导轨安装底座与地基之间通过调整垫铁和地脚螺栓完成水平调整和固定。
伺服液压缸通过耳环式连接的方式,一端固定在轨道轮安装支座上,另一端固定在曲线导轨安装支座上。伺服液压缸的最高激振频率为5 Hz,三相交流电机的最高转速为980 rpm,因此试验台最高工作频率为16.3 Hz。
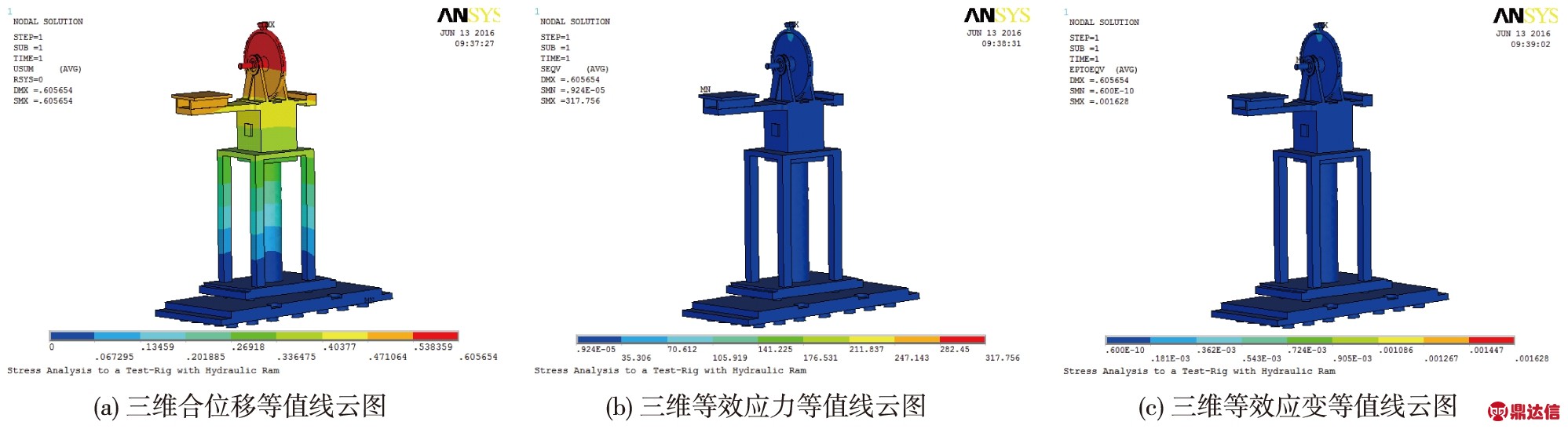
图1 胶轮导轨电车滚振试验台结构
1.2 试验台激振部分结构简化
为了提高计算机的运算速度,降低软件对计算机硬件的要求,顺利通过ANSYS分析软件完成试验台激振部分三维模型的网格划分,试验台激振部分按照质心不变、质量等效的原则进行简化。忽略试验台上的螺纹孔以及倒圆角,用质量等效体代替轴承、地脚螺栓、电动推杆等部件。简化前、后的激振部分的模型如图2所示。
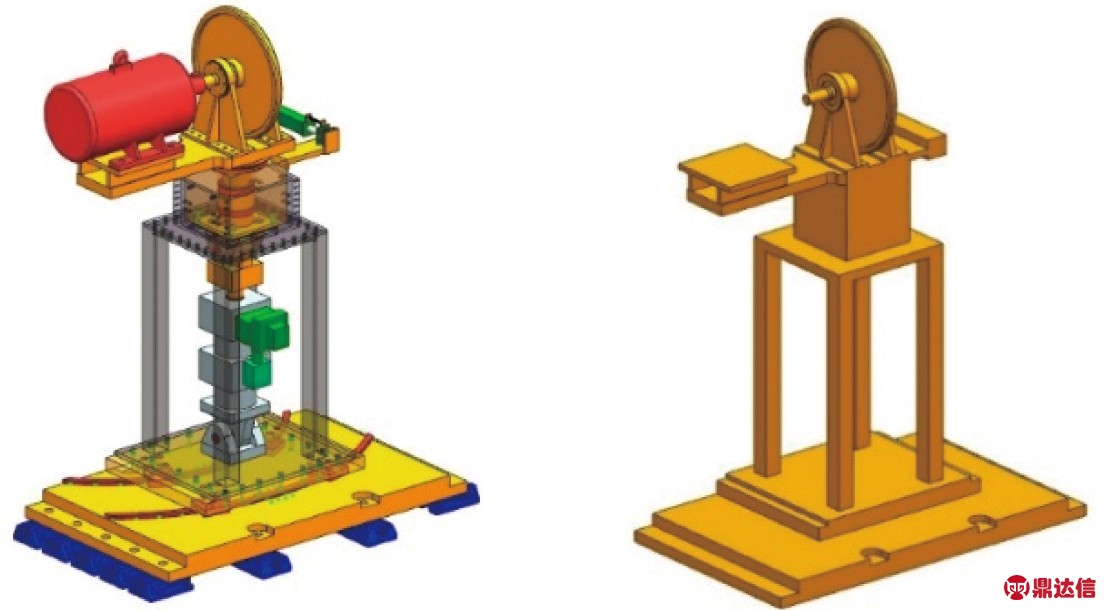
图2 试验台激振部分及其简化图
2 试验台静力学分析
试验台激振部分台架选择Q390碳素钢,抗拉、抗压和抗弯的屈服应力为390 MPa,试验台应变量小于0.005。对试验台进行网格划分,试验台被划分为191 380个单元。添加最大载荷与约束:试验台轨道轮上方添加100 kN的垂向载荷,试验台转动单元外臂添加20 kN的横向载荷,通过对20个调整垫铁的固定完成试验台的约束。最后进行仿真分析。
仿真结果表明:试验台在最大横向载荷的作用下,位移量从上到下递减,最大位移量为1.66 mm;最大应力、应变集中在轨道轮和导向轮接触部位、液压缸支架立柱的两端,最大应力为343.97 MPa,最大应变量为0.001 771。试验台最大载荷下三维合位移等值线云图、三维等效应力等值线云图、三维等效应变等值线云图如图3所示。
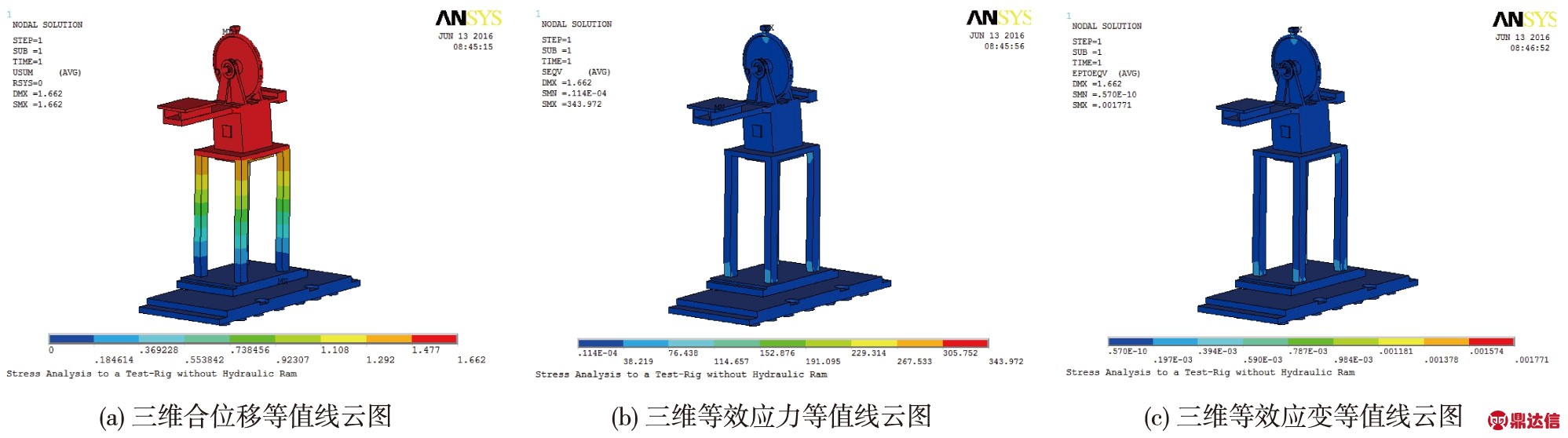
图3 最大载荷下试验台静力学分析结果
伺服液压缸上部连接转动器,底部连接试验台曲线滑块安装底板,并且体积和质量都比较大,因此伺服液压缸对试验台结构的影响不能忽视。对伺服液压缸等质量简化后的分析结果如图4所示。结果表明:液压缸使试验台的受力更加均匀,且最大位移量减小到0.61 mm,减少了63.56%;最大应力减小到317.76 MPa,减小了7.62%;最大应变量减小到0.001 628,减小了8.07%。因此选择Q390碳素钢能够满足试验台强度设计要求。
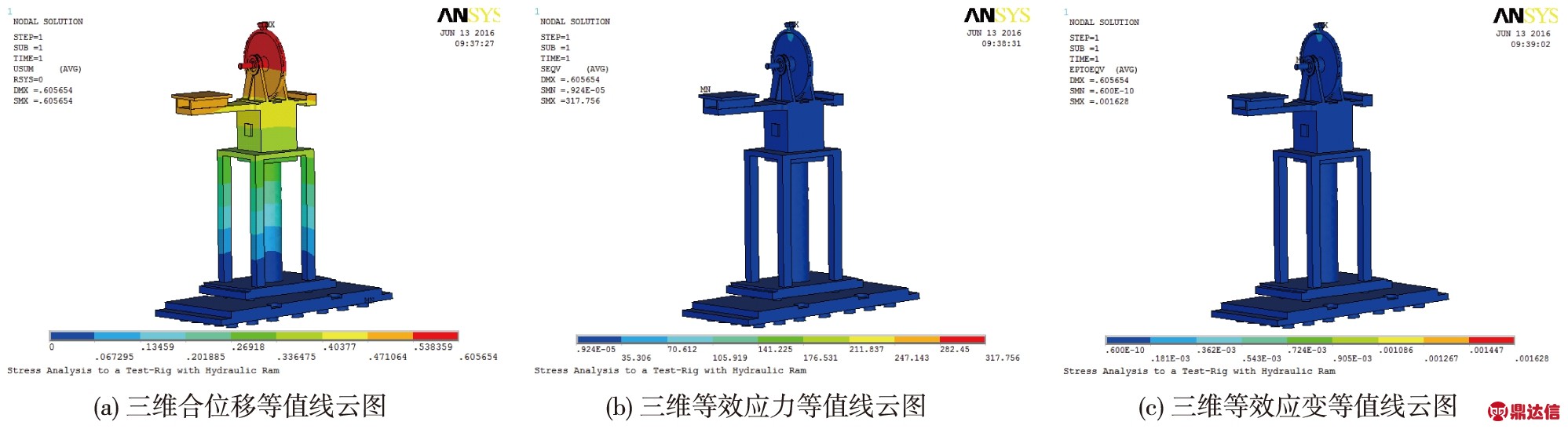
图4 考虑液压缸时最大载荷下试验台静力学分析结果
3 模态分析
3.1 模态分析理论
模态分析是研究结构动力特性的一种近代方法,属于线性分析,主要用于确定结构的振动特性,结构的质量和刚度等物理参数决定系统的固有频率。根据达朗贝尔原理(D’Alembert’s principle)建立动力学方程

式中 [M]——质量矩阵;
[C]——阻尼矩阵;
[K]——刚度矩阵;
加速度;
速度;
{X}——位移;
{P}——载荷。
由于载荷不影响固有模态,结构阻尼对固有模态影响较小,在不考虑载荷和阻尼时,式(1)可以化简为

因为一切振动都可以理解为多个简谐振动的叠加,所以设特解X为频率ω振幅{x}的简谐振动,即{X}={x}cos(ωt+φ)时,可以得到自由振动方程(3),取特征值λ=ω2,由式(3)可以得到式(4)。由式(4)可以求得振动方程(2)的特征值,其特征值即为结构的固有频率。


3.2 试验台模态分析
建立新的ANSYS分析文件,分析类型选择Modal模态分析,去掉试验台的外载荷,对试验台调整垫铁进行固定,定义试验台的材料属性并进行网格划分,模态分析的结果如表1所示。试验台的1阶固有频率为49.265 Hz,远离试验台的最高激振频率,不会引起共振。
表1 试验台装有20个调整垫铁时前5阶固有频率

有文献指出试验台与地面接触模块的数量对试验台固有频率有一定的影响[12],又因为试验台调整垫铁数量已经为20个,所以通过减少调整垫铁的数量来研究试验台固有频率的变化。当试验台调整垫铁减少为4个时,试验台的前5阶固有频率如表2所示。分析结果表明:减少调整垫铁的数量会降低试验台的固有频率,在前5阶固有频率中,对第5阶的固有频率影响最大。
表2 试验台装有4个调整垫铁时的前5阶固有频率

调整垫铁数量为20和4时的试验台前5阶模态图形分别如图5所示。对比分析可知:2种模态下,前4阶模态下试验台的振型是一致的;其中前两阶模态的振型主要表现为试验台架的倾斜;3、4阶模态的振型主要表现为电机支架的变形;5阶模态时,装有20个调整垫铁的试验台振型主要表现为轨道轮的变形,装有4个调整垫铁的试验台振型主要表现为曲线导轨安装底座的变形。

图5 试验台激振部分前5阶特征振形
4 结论
通过UG三维建模软件和ANSYS软件的结合,完成了试验台激振部分的三维建模和有限元分析,分析结果验证了试验台结构设计的合理性。同时通过分析可以得出以下结论。
(1)伺服液压缸可以提高试验台的结构特性,在最大载荷作用下,试验台最大位移量、最大应力、最大应变分别减小了63.56%、7.62%、8.07%。
(2)试验台电机转轴直接通过联轴器与轨道轮连接在一起时,试验台的固有频率远离激振频率,试验时不会产生共振;若电机通过减速器与轨道轮连接在一起时,减速比不能低于1∶3,否则电机会引起试验台的共振。
(3)增加试验台部件间的接触面积可以提高试验台的固有频率。
另外,试验台激振部分的模态分析可以为高速轨道车辆滚振试验台设计优化提供理论数据。