1 闭式液体静压导轨系统
1.1 结构原理
闭式液体静压导轨单对油腔结构原理见图1。其中1为溜板,2为导轨,3为油腔2,4为节流调压阀2,5为油腔1,6为节流调压阀1。与开式静压导轨相比,其油腔相对布置(油腔1、2)。供油系统亦含与各油腔匹配的节流调压阀 R k1、 R k2及安全阀、油泵等。图1上半部分为油腔2的向视图,深色环形区域为油腔封油带。静压导轨通过在各油腔内不断通入的压力油使其与溜板始终保有厚度为 h的油膜而实现纯液体摩擦导向。工作中油腔内外油压分布即图中等腰梯形,由于封油带的压力近似线性递减 [9],故油腔2的有效承油面积可等效为虚线框 A eff2;油腔1的有效承油面积可等效为 A eff1,由图可知
A effi=( A i- a i)( B i- b i), ( i=1,2)
(1)
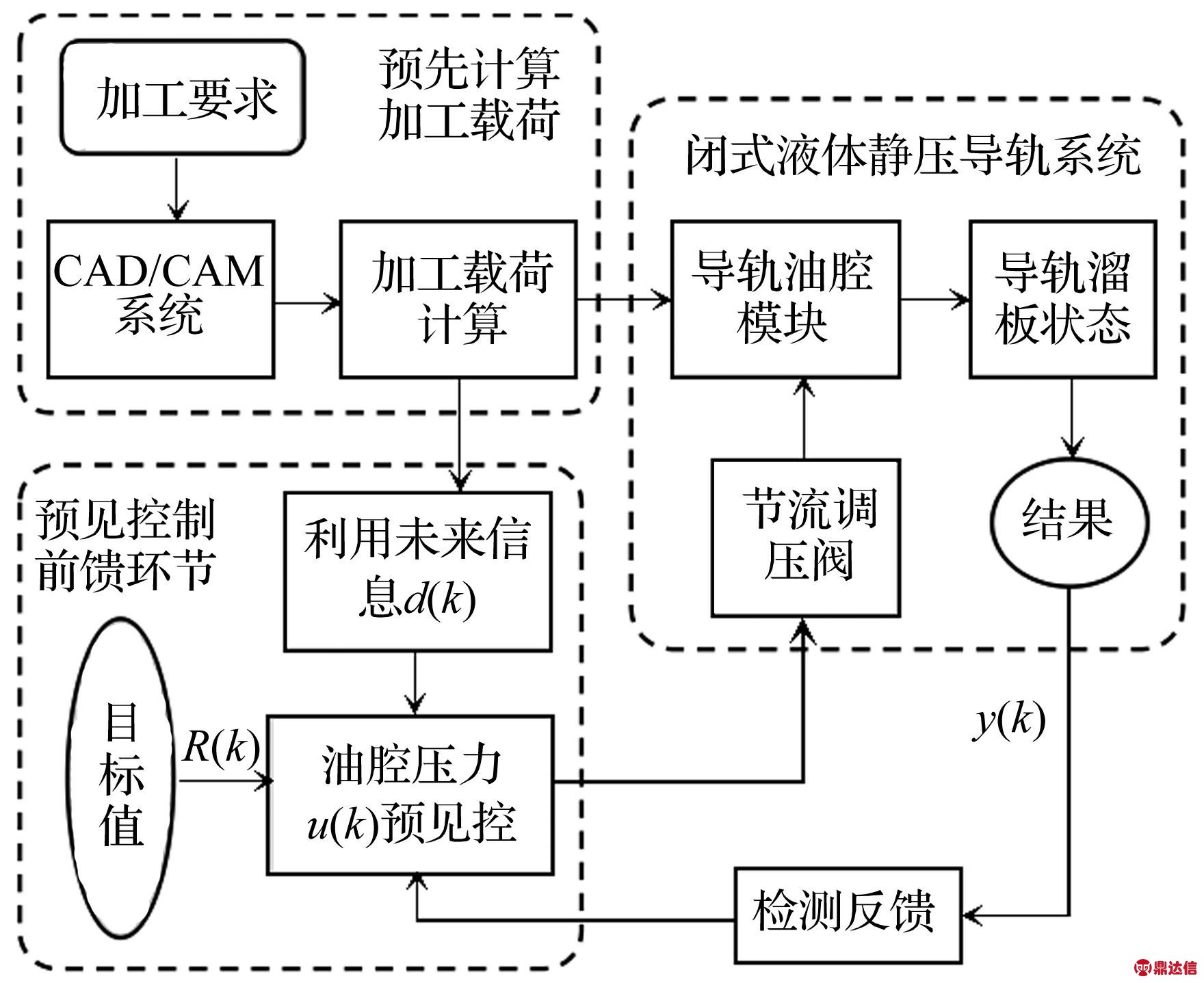
图1 闭式静压导轨系统结构原理图
Fig.1 Schematic diagram of closed hydrostatic guide
1.2 数学模型
实际工作过程中导轨溜板受动态加工载荷f作用,设由此产生的油膜厚度改变量为 x(图1),建立导轨在 X方向动平衡方程为

(2)
式中: m为溜板质量; p 1为油腔1油液压力; p 2为油腔2油液压力。
由于油腔附近油液为缝隙流动,则各油腔内流量 q i与压力 p i的关系为
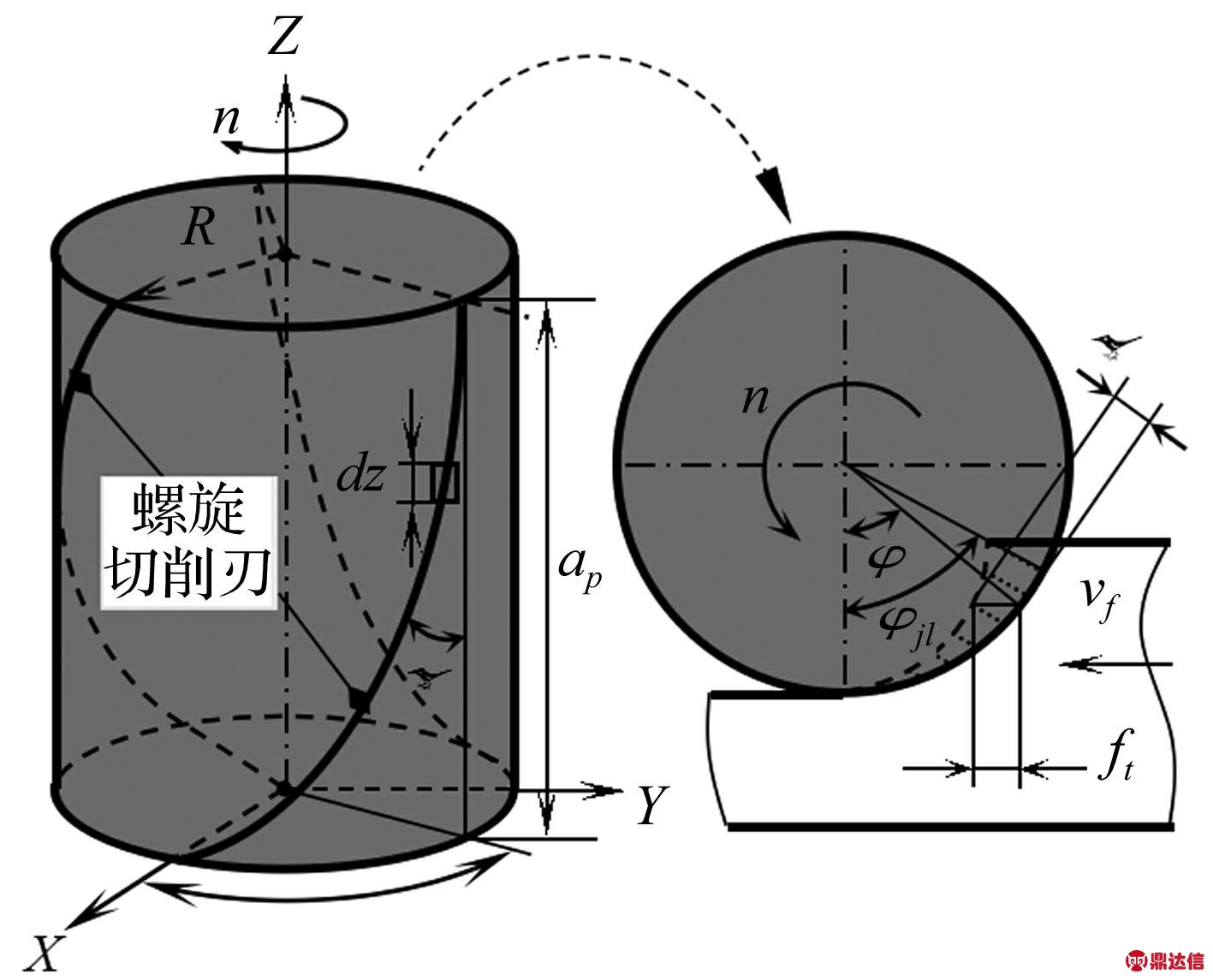
(3)
式中: μ为油液动力粘度; h i为油膜厚度; i为油腔支承流量系数 [10],即

(4)
式中: A i, B i, a i, b i为各油腔结构参数。若未特别注明,均取 i=1,2。
不考虑油液的可压缩性,在变载荷作用下油腔1、2的流量 q 1及 q 2随 x变化关系式为
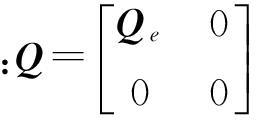
(5)
式中 为油膜厚度, h i0为初始状态油膜厚度。由于初始状态下闭式静压导轨对置油腔油膜厚度相等,故 h 10 = h 20 = h 0; p i为油腔压力; p i0为初始状态下各油腔压力; A bi=( A i-2 a i)( B i-2 b i)为油膜有效挤压面积。
正常工作时安全阀无溢流,泵出口流量为
q= q 1+ q 2
(6)
联立式(2)、(5)、(6),可得

(7)
初始状态( f = 0)下溜板受力平衡,则:
p 20 A eff2= mg+ p 10 A eff1
(8)
联立式(2)、(5)、(8),可得
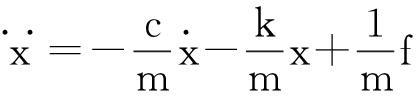
(9)
式中 ;
。
将式(7)与式(9)组合,取状态变量 T,控制变量u= [p 1 p 2 ] T,输出变量y= [x],外扰变量d=[ f],建立闭式液体静压导轨系统状态空间模型为
=AX+Bu+Ed,y=CX
(10)
式中:

C= [0 1 ];
;
由状态空间模型知,油膜厚度 x的波动主要受油腔压力 p 1, p 2及加工载荷 f共同影响,若已知 f的变化规律,则可通过主动调节油腔供油压力补偿油膜厚度波动。
2 数控机床加工载荷可预见性
导轨受加工载荷即刀具对工件施加的切削力。圆柱螺旋铣刀数控铣削过程示意见图2。由于铣刀刀齿形状复杂,且沿空间三维度方向均有变化,故采用微元分割法求解瞬时切削力。
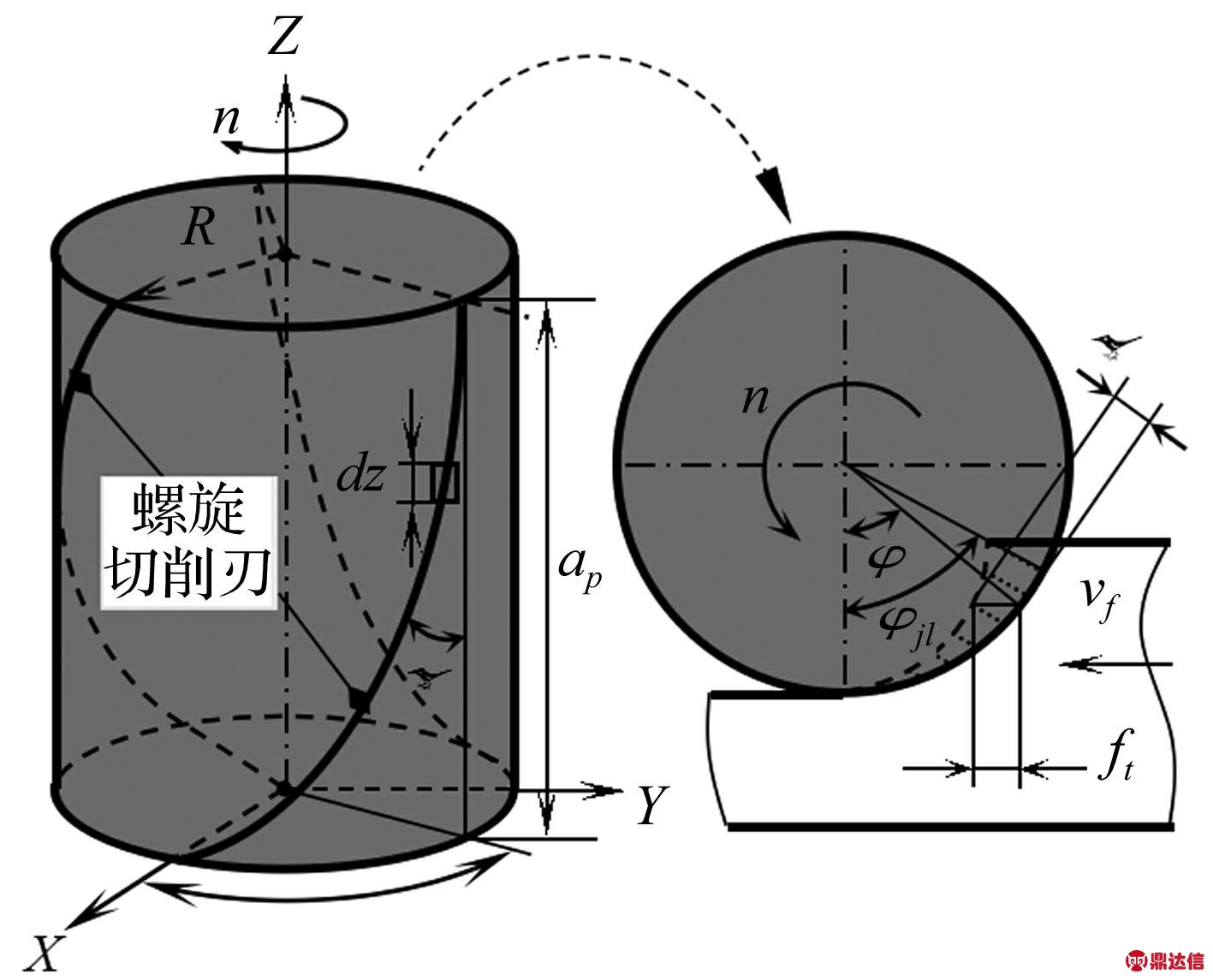
图2 刀齿微元分割及铣削过程示意图
Fig.2 Differential diagram of cutter
teeth and schematic of milling process
据铣削过程瞬时刚性力学原理,得作用于刀齿 j上第 l个切削刃微元的力为
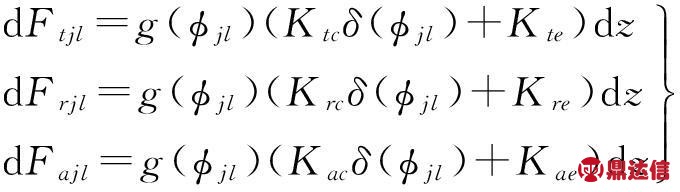
(11)
式中:d F tjl,d F rjl,d F ajl分别为切削刃微元d z的切向、径向、轴向切削力; K tc, K rc, K ac分别为切削刃切向、径向、轴向切削力系数; K te, K re, K ae分别为切削刃切向、径向、轴向刃口力系数; φ jl为第 j个刀齿第 l个切削刃瞬时角位移; δ( φ jl)= f tsin φ jl为相应微元处切削深度, f t为进给量; g( φ jl)为切削刃微元当前是否参与切削的单位阶跃函数。
对d F tjl,d F rjl,d F ajl沿刀具轴向积分可得各刀齿的瞬时切削力,将刀齿切削力沿坐标方向矢量求和可得整个铣刀在 X、 Y、 Z向瞬时加工载荷,即
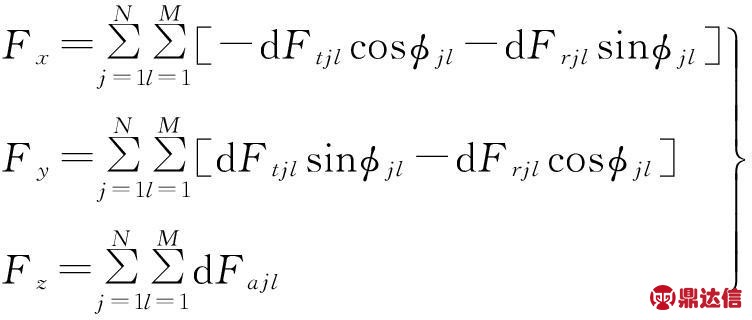
(12)
被加工件形状各异,刀路轨迹往往不会限定在一维空间内,进给量 f t沿 X、 Y方向分量 f tx、 f ty会随时间 t不断变化。圆角矩形凹槽铣削示意见图3。

图3 圆角矩形凹槽铣削过程示意图
Fig.3 Milling process of circular-rectangle groove
以刀具走一个循环 X方向进给量分量 f tx为例,据编译的NC程序,CAM系统对 f tx规划为
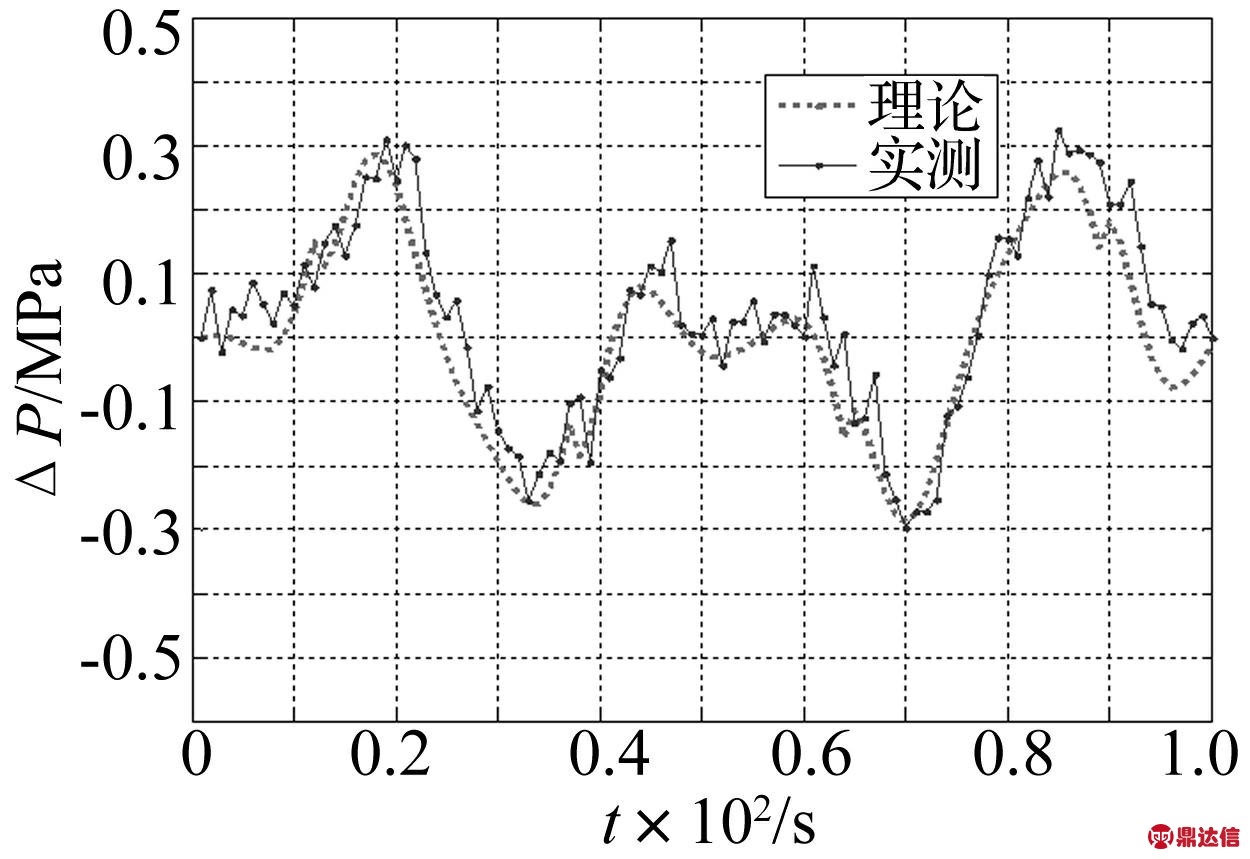
(13)
给定切削参数值,见表1,可得 X方向加工载荷 F x变化曲线,见图4。图中平滑曲线为将刀齿旋转引起的切削力波动每个周期内求平均等效化所得。由图4局部放大曲线可知,等效前 F x呈周期性波动,波幅变化不大。因铣刀高速旋转时刀齿周期性切削工件所致,此周期较小,约0.1 s,对切削效果影响不大,对该波动求均值等效化合理可行 [11]。
表1 铣削过程基本参数
Tab.1 Basic parameters of milling process

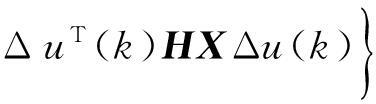
图4 圆角矩形凹槽等效加工载荷F x曲线
Fig.4 Curves of equivalent processing load F xduring
circular-rectangle groove milling process
一旦系统切削参数及NC程序已知,CAM系统可对走刀轨迹预先规划,采用刚性切削力学模型,提前求出溜板各方向载荷大小及变化,作为预见控制系统的未来信息。
3 导轨油膜波动补偿控制系统建模
3.1 预见控制方案设计
因在精密数控加工技术背景下,导轨系统动态加工载荷变化可预知,故引入预见控制模块,通过不断跟随加工载荷变化主动干预液体静压导轨油腔压力,实时补偿油膜厚度波动。静压导轨油腔压力预见控制流程见图5,其中以油膜波动量为目标信号 R( k),以溜板偏移量 y( k)为被控制量。由于静压导轨各油腔间隔分布在工作台溜板下方,加工载荷作用点不断变化时各油腔所受分载荷会随之改变,需对不同油腔压力控制子模块输入不同载荷信息,各油腔分载荷算法见文献 [12 ]。本文仅对其中一个油腔的预见补偿控制方式进行详述。
由图5可知,与普通伺服控制系统相比,预见控制系统加入利用未来信息 d( k)的前馈补偿环节,尽可能减小系统中目标值 R( k)与被控制量 y( k)的相位延迟,使油腔压力能无延迟跟踪载荷变化。
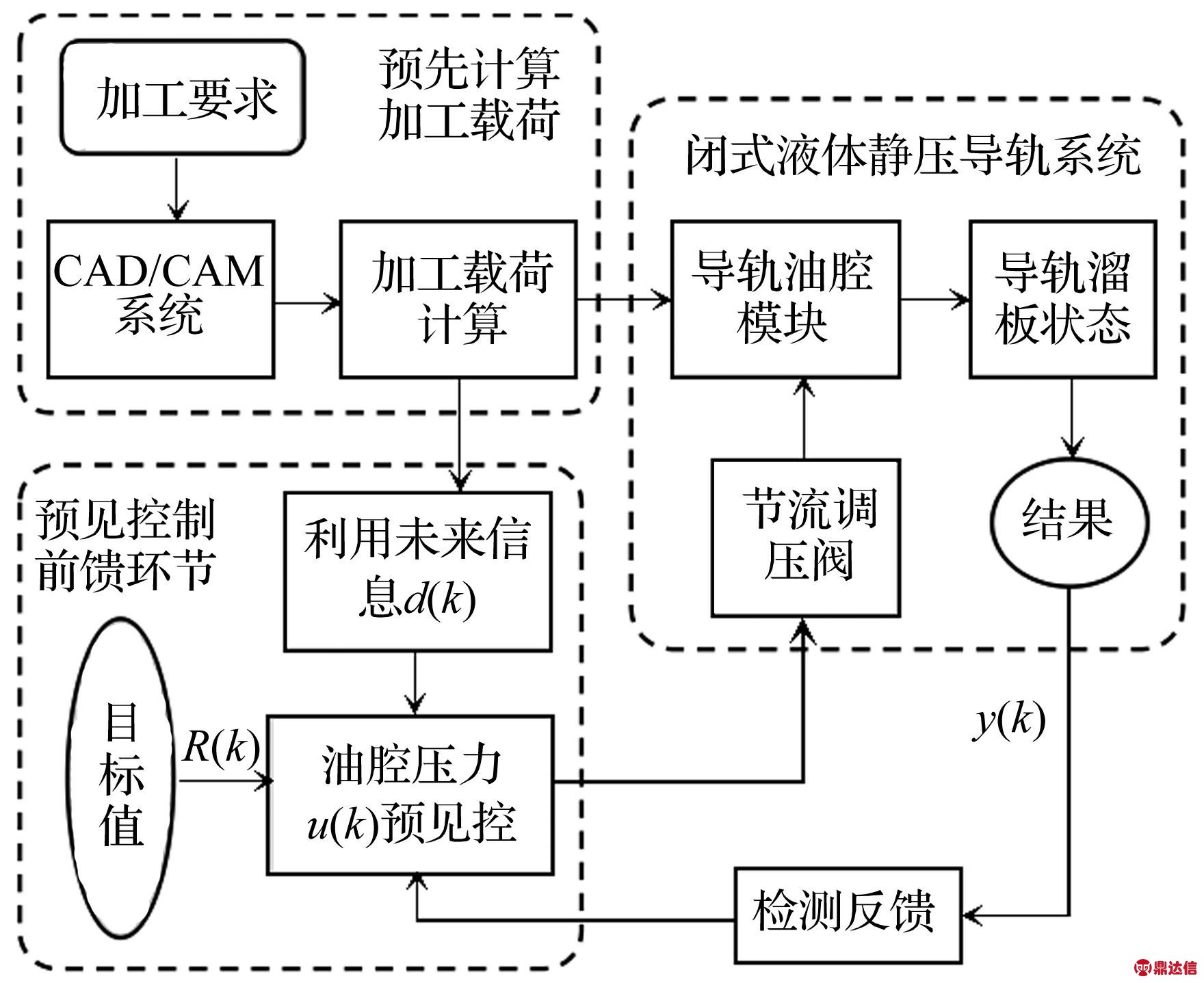
图5 导轨油腔预见控制方案流程图
Fig.5 Flow chart of preview control method to the cavit yoil pressure
3.2 对油腔压力预见控制
欲使油膜厚度不变,应满足 =0。定义误差信号为
e(k)=R(k)-y(k)
(14)
联合式(10)、(14)进行一阶差分,得


式(15)为含新状态变量Δ x( k)及 e( k)的静压导轨误差系统。因实际外扰载荷变化既连续又平滑,故设外扰 d( k)的变化Δ d( k)可提前 M R步被预见,并定义
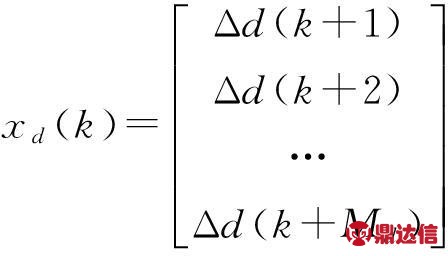
设 d( k+ i)=0( i= M R+1, M R+2,…),因而可将式(15)进一步扩大为

(16)
式中:G pd= [G d 0 … 0 ];Ф,G d为矩阵;
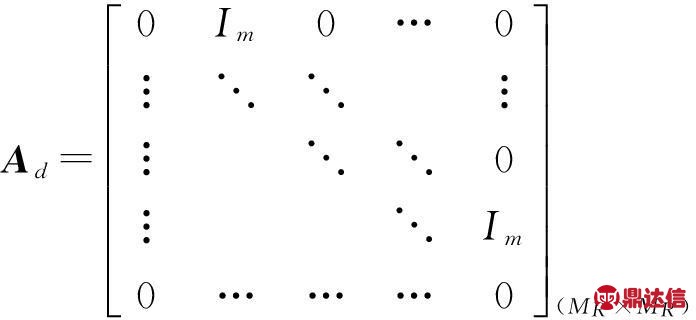
式(16)既含误差项e(k)及控制项u(k),又含可预见外扰载荷信号d(k),因此建立二次型评价函数J求解最优控制信号u(k),即

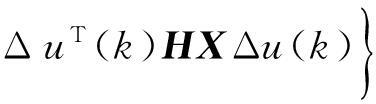
(17)
式中 ,Q e为加权矩阵,用于调节系统对状态的响应。
问题转化为对线性二次型函数的最优化 [13],油腔压力预见控制解可表示为
(18)
式中:F e,F x,F d分别为矩阵。
通过提前 M R步引入加工载荷变化方式,推导出相应步长时油腔压力的最优解,为节流调压阀的输入信号提供依据。
3.3 油腔压力主动干预仿真模型
对油腔压力控制变量 u( k),须以电信号形式作用于节流调压阀 R k上。由于电液比例调压阀已成熟(此处不详述),故直接援引PRED3G比例压力阀控制特性曲线 [14],见图6。由图6可知,该阀具有良好的滞环特性(<3%)及重复精度(<±1%),足够对输入信号做出快速、准确响应。
闭式液体静压导轨系统油腔压力预见控制仿真框图见图7。通过数控机床CAD/CAM控制系统,将计算所得加工载荷 F x输入预见控制模块中作为未来信息,以便提前调节控制信号 u( k),对油腔压力进行主动控制。
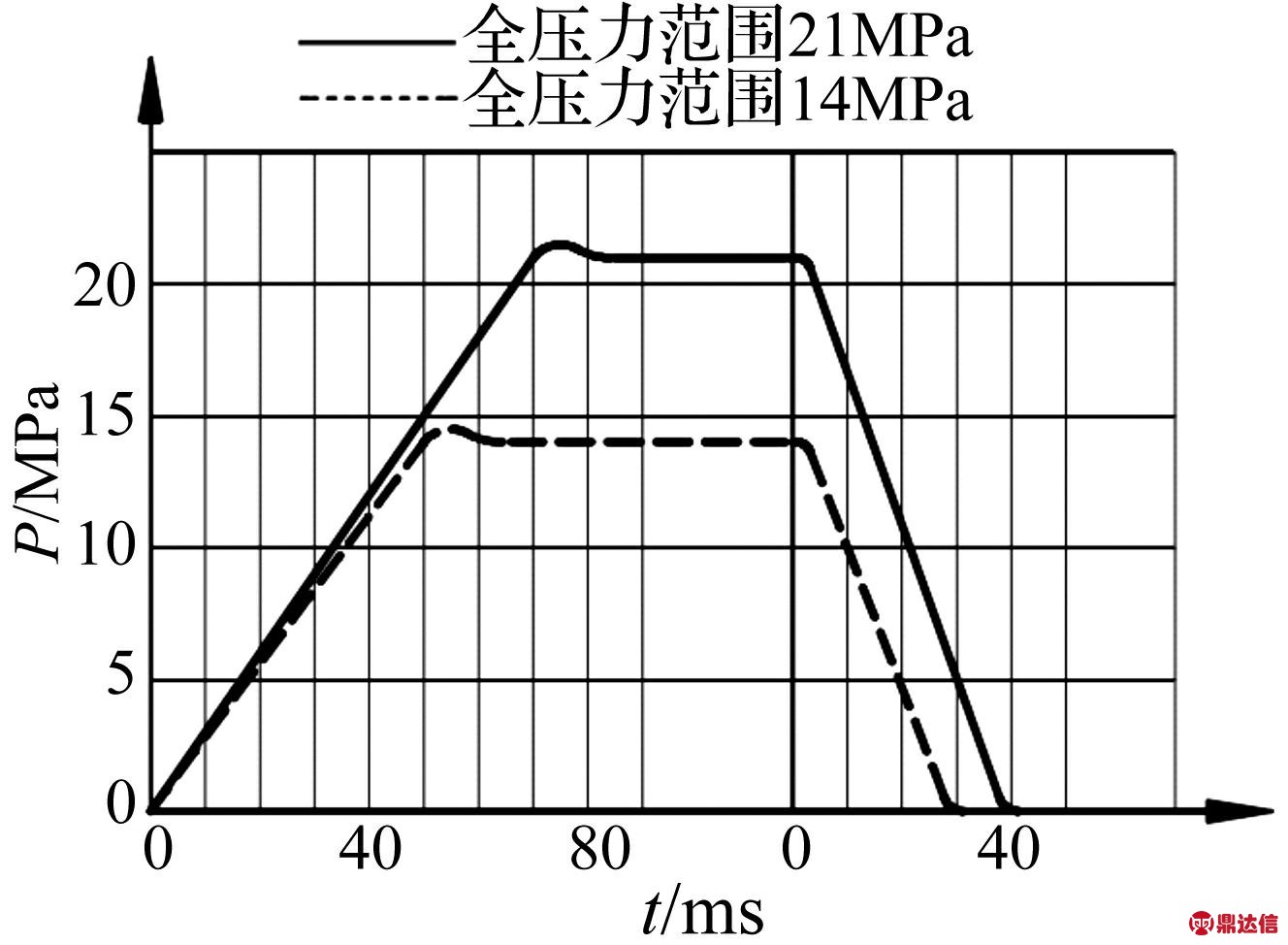
图6 比例压力阀控制特性曲线
Fig.6 Curves of control performance of
proportional pressure control valve
以某精密数控机床液体静压导轨为例建立仿真模型,基本参数见表2。
表2 液体静压导轨基本参数
Tab.2 Parameters of hydrostatic guideway system

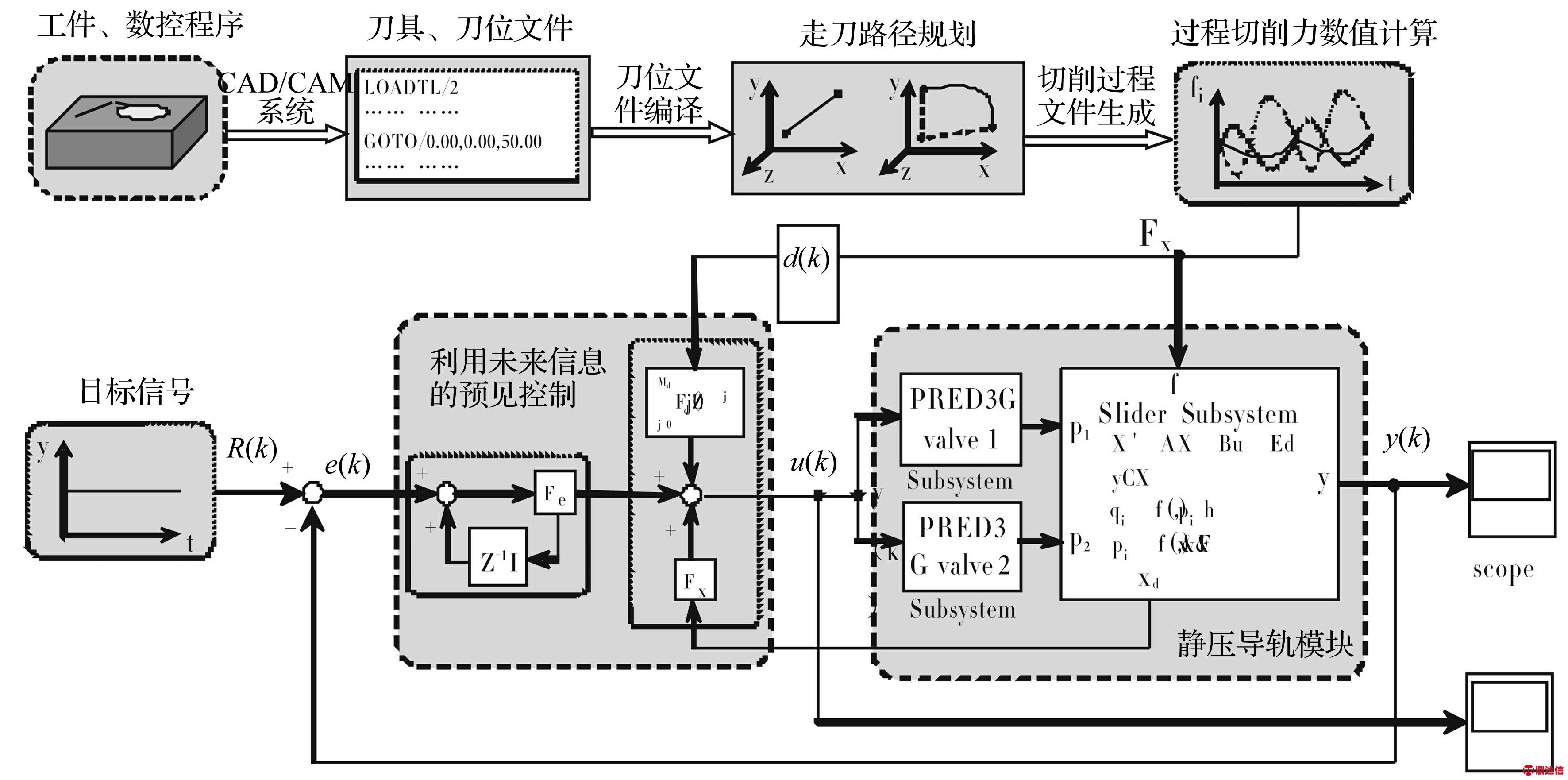
图7 静压导轨系统预见控制仿真模型结构框图
Fig.7 Block diagram of simulation model of preview control strategy for hydrostatic guide system
相同加工载荷下,对导轨油腔压力采取预见控制、最优控制 [15]及不加控制时溜板偏移曲线比较见图8。其中载荷信号为图4中等效的加工载荷。由图8看出,系统不加任何控制时(对应曲线 y n)溜板偏移量在-1.3~1.4 μm间变化,且响应存在明显滞后,约6 s;采用最优控制方式时(对应曲线 y op)溜板偏移量明显减小,波动范围在-0.3~0.3 μm之间,且基本消除响应滞后,仅1.8 s,但波动幅值仍在0.5μm以上;加入预见控制器时溜板偏移量 y pv减小至0.08 μm以下,较最优控制减小73.3%,且响应时间提前约23%。表明加入预见控制模块后,系统可提前对载荷变化进行跟随,预先调节油腔压力控制信号。
采用最优控制及预见控制的油腔2油压变化比较见图9。其中纵轴Δ P为油腔实时压力 p 2与初始压力 p 20差值。由图9看出(对应曲线Δ P op及Δ P pv),预见控制下油腔压力提前约23%发生改变。此因在前馈环节中,引入对未来加工载荷的跟随对调压阀控制信号 u( k)进行控制。而在第12 s、36 s、65 s及90 s时Δ P pv出现小尖峰,因在相应时刻加工载荷增长趋势发生改变。进一步说明预见控制下控制信号对载荷变化趋势跟随性较好。比较Δ P op与Δ P pv的变化幅值可知,或用最优控制或预见控制方式,Δ P的变化范围均维持在±0.3MPa内,较初始压力 p 20=5.38 MPa改变量仅11%,说明引入预见控制不会造成振荡超调,只会在载荷平稳时有轻微波动(对应40~65 s时段),此为等效后加工载荷在平稳阶段仍存在轻微起伏。
刀具初始切入工件时溜板偏移量变化曲线见图10,该过程时间较短。其中曲线 y op为最优控制方式下溜板偏移量,由图10看出,波动幅度接近1μm;而曲线 y pv为采用预见控制时溜板偏移量,波动量被控制在0.05μm以内,较最优控制方式减小约85%。进一步说明对快速变化的加工载荷,采用最优控制方式时,输出信号来不及做出响应,溜板偏移量较大;而采用预见控制方式时,由于能提前获得加工载荷变化趋势预先调整油腔压力,响应灵敏度大幅提高,溜板偏移量显著减小。
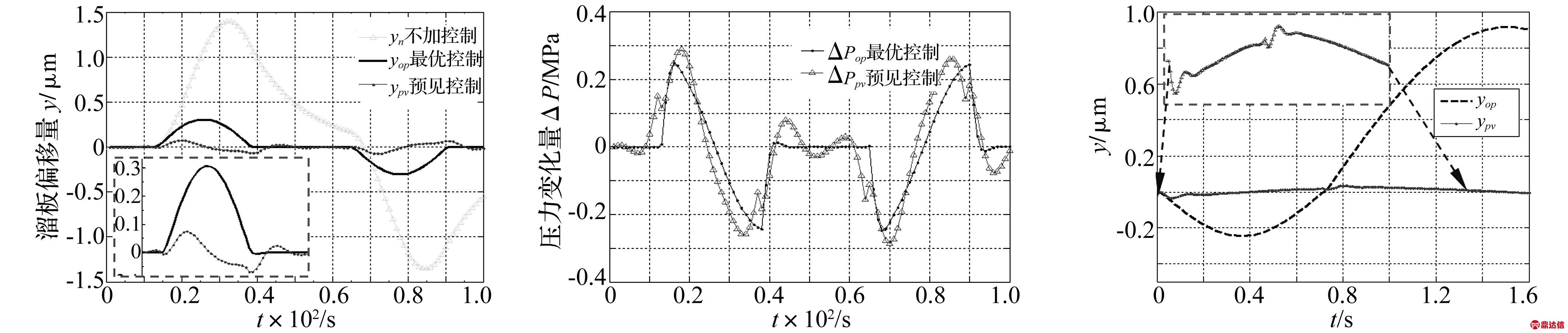

采用不同控制方式时液体静压导轨性能参数比较结果见表3。表中响应快慢以载荷变化时刻为参照,油膜稳定性以溜板偏移量为指标进行评价。表3综合反映出采用预见控制方式时闭式液体静压导轨的优越性,与不加任何控制方式相比其油膜波动量大幅减小,甚至比采用最优控制时减小近73%;且采用预见控制方式时油腔油压响应明显加快,最优控制方式被动控制在响应上存在滞后,而预见控制则完全消除此问题。
表3 不同控制方式下闭式液体静压导轨系统性能参数比较
Tab.3 Comparisons of closed hydrostatic guideway performance with different control methods

4 试验结果及分析
将预见控制策略在Nanosys-300非球面超精密加工系统的超精密液体静压导轨研究平台进行试验验证,采用CapaNCDT6019非接触型位移传感器检测溜板实时偏移量。传感器壳体与基础导轨连为一体,减小由床身振动所致影响,测量精度达20 nm;采用MEA3000压力传感器测量油腔压力变化,在油腔进油口处增加三通接头引出油压信号。位移、压力传感器所测数据信号经放大器后由PCI- 6015数据采集系统传送至PC机,经LabvIEW软件处理成可视实测曲线。实验中切削参数与表1一致,刀具材料为SANDVIK硬质合金,切削工件材料为40Cr合金钢。
溜板偏移量实测与理论曲线对比见图11。图中时段截取与仿真曲线对应的圆角矩形凹槽一个铣削循环过程。由图11可知,溜板实测偏移量在-0.07~0.1 μm之间,较仿真值偏大约6.8%。此与仿真中忽略油液可压缩性有关,加工载荷、油压均增大时,油腔内油膜挤压效应会造成额外偏移量。若略去由于测试系统随机误差、泵出油压力不稳定性及液压阀芯振动等造成的实测曲线毛刺,则溜板实测偏移曲线与仿真曲线吻合良好,已验证引入预见控制仿真模型的合理性。对仿真曲线中40~65 s时段小于0.01 μm的轻微波动,实测曲线并未呈现,与测试系统自身精度局限性有关,需进一步改善。
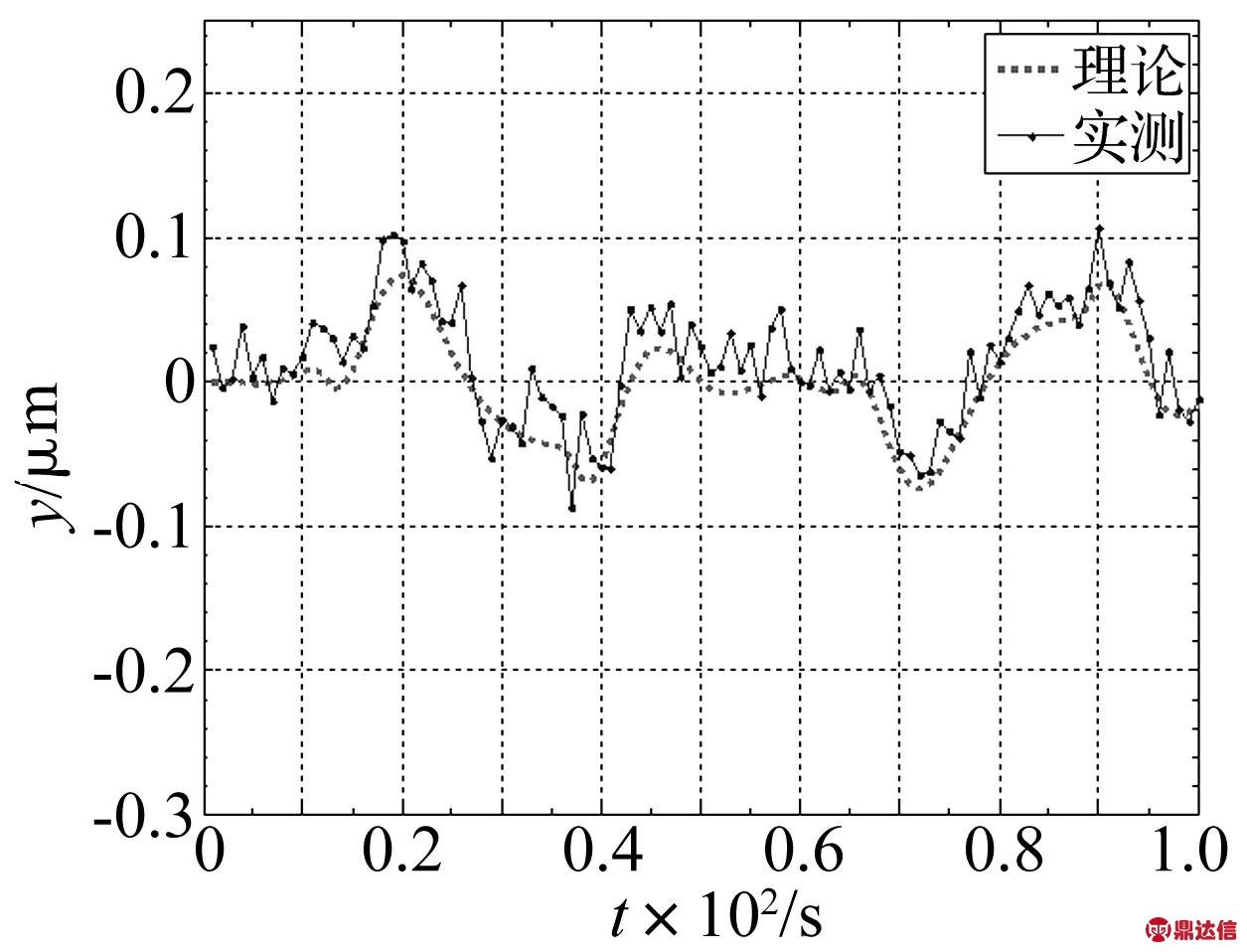
图11 滑块偏移量实测与理论曲线对比
Fig.11 Simulation curves and test
curves comparision of slider deviations
油腔2内压力变化实测与理论曲线对比见图12。同样纵轴△ P及实时压力与初始值的差值。由图12可知,实测压力变化量在±0.3 MPa之间,与理论值较吻合,但延时约0.3 s,此由比例调压阀的滞环特性及液压系统固有阻尼特性所致;且实测压力在82 s后逐渐大于仿真压力值0.05 MPa,因随加工进行调压阀节流作用会使油液温度升高、粘度降低,导致实际误差输入量 e( k)增大,但仿真模型中却未考虑油液温度的改变,需进一步研究。
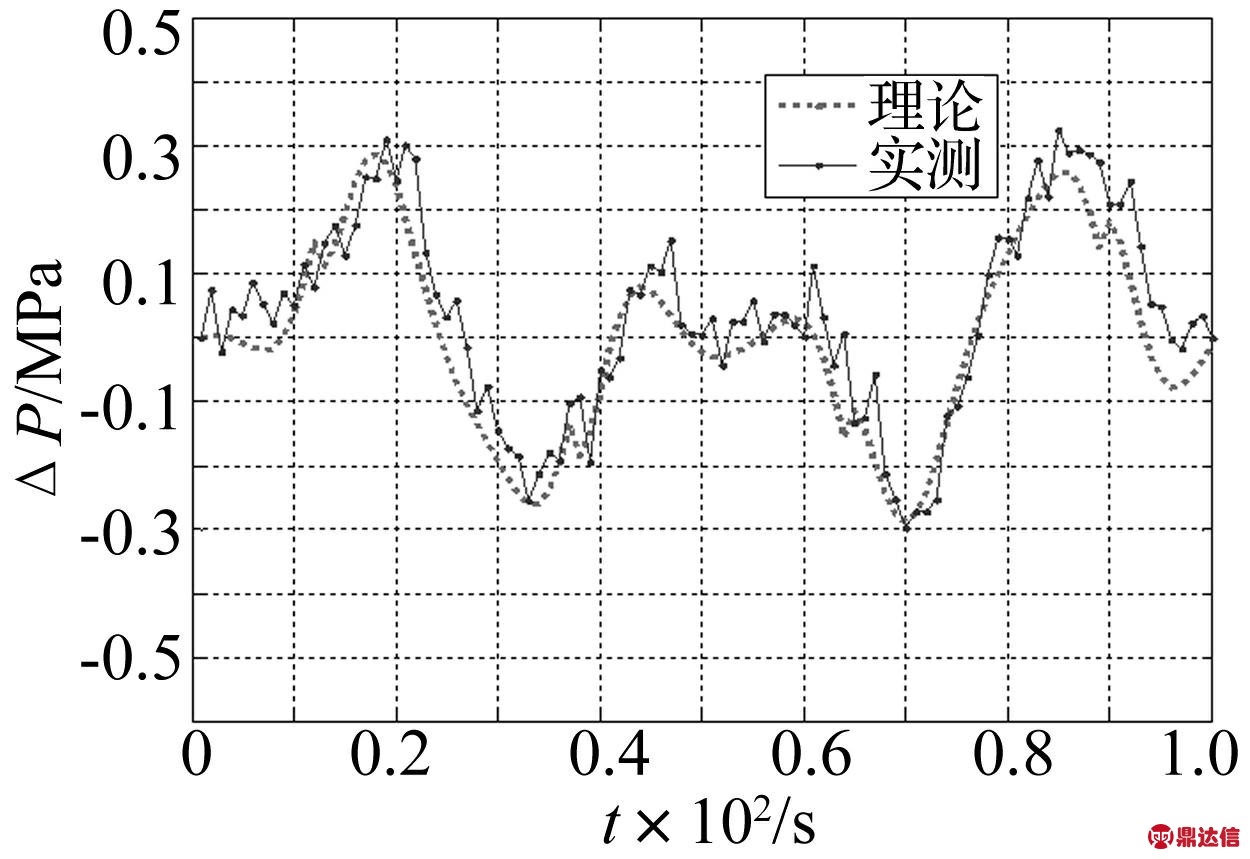
图12 油腔油压改变量实测与理论曲线对比
Fig.12 Simulation curves and test
curves comparision of cavity oil pressure
5 结 论
(1)以油腔压力为被控制量、加工载荷为干扰信号建立的闭式液体静压导轨状态空间方程,便于实现模块化控制,能同时观测溜板偏移量及油腔压力变化。
(2)基于CAM数控技术,结合切削过程瞬时刚性力学原理,获得走刀轨迹与加工载荷的数学关系,并以此为预见控制的前馈补偿环节,实现油腔压力对加工载荷的主动跟随。预见控制器能提前获得加工载荷变化趋势,使油压及溜板偏移响应灵敏度大幅提升。
(3)采用预见控制策略能主动干预静压导轨油腔压力。以加工载荷变化量为未来信息,以油膜波动最小为目标,通过控制节流调压阀输入信号调节油腔压力。能有效减小加工载荷造成的油膜厚度波动,即预见补偿控制策略提高液体静压导轨油膜厚度稳定性切实可行。