摘要:对市场上主流的滚动直线导轨副进行了功能可靠性定时截尾试验,同时,针对截尾无故障的试验结果提出了品质量的评价方案。方案中,参考可靠度计算原理,定义了品质量的计算方法,并验证了其取值区间合理性,最后对被测滚动直线导轨副进行了品质量计算,完成了该产品的无故障可靠性评价。为机械产品小子样可靠性试验中无故障结果提供新的评价方法。
关键词:直线导轨;可靠性;无故障;品质;评价
0 引言
机械可靠性是指机械产品在规定的使用条件下、规定的时间内完成规定功能的能力[1]。对于机械产品的可靠性试验和评价,大多来源于电子产品可靠性研究经验基础上的再发展。文献[2]介绍了特征量为结构强度、寿命(服从weibull分布)、功能参数等三种典型非电子产品可靠性试验基本方案,而针对滚动直线导轨副产品进行功能可靠性试验满足特征量为功能参数的非电子产品可靠性基本试验,试验样本小,但零故障的试验结果无法用理论进行有效分析。文献[3]针对数控机床机械产品建立了基于威布尔分布的定时截尾可靠性试验方案,方案中,威布尔分布理论无法应用在无故障的截尾导轨副可靠性试验结果内。刘涛[4]介绍了基于用户需求驱动模型和模糊综合评价模型对汽车整车品质评价指标的研究,将汽车整车分解成多级进行品质评价,为客户提供选择参考。此文将品质评价应用于汽车整车产品中对导轨产品可靠性试验具有借鉴意义。文献[5]将噪声品质作为评价6缸柴油机性能的研究指标,分析了影响这一指标的各参量,通过试验建立了噪声品质预测模型,为直线导轨副品质评价这一方法提供了思路。
针对滚动直线导轨副这一机械产品的可靠性研究可以展开为精度可靠性、功能可靠性、寿命可靠性这三个方面进行。其中,功能可靠性中故障表现形式对照机械系统典型故障模式举例[6]可以具体为:滚动体压溃、滑块卡死、反相器破裂或飞出、密封盖损坏、滚道面出现坑洼破损等。通过定时截尾的功能可靠性试验发现,在截尾里程相同的情况下,选取的4家市场主流导轨产品的试验结果都是无故障。本文在无故障试验结果中,通过分析试验件之间的普遍区别,提出了一种滚动直线导轨副无故障下的可靠性评价方法——品质评价,从而来区分不同滚动直线导轨副在功能可靠性试验后的质量差异,拓宽了功能可靠性试验的意义。
1 功能可靠性试验
普遍的,机械产品可靠性试验周期长,难以获取大量子样容量,费资、费力,备件费用大[7],因此滚动直线导轨副机械产品功能可靠性试验是建立在小子样广义定时截尾试验基础上开展,广义定时截尾试验中的工作时间t在试验中通过设定导轨副跑合里程L来代替。在试验设定的截尾里程L内,考察导轨副的故障次数n。
1.1 试验设备
试验使用了可提供被测导轨承载向最大5t的持续承载载荷的滚动直线导轨副可靠性试验台进行试验,如图1。试验台一次可同时试验两根导轨,采用齿轮齿条驱动龙门往复高速运动,最高速度可达100m/min。龙门两侧安装有手动加载装置,对两侧被测导轨进行对称加载。试验中,设置了噪声采集器,捕捉可靠性试验中滑块工作异常的噪声值,供试验员判断故障;同时,单根被测导轨滑块上安装了两轴振动传感器,采集滑块工作中的振动值,用于故障判断。
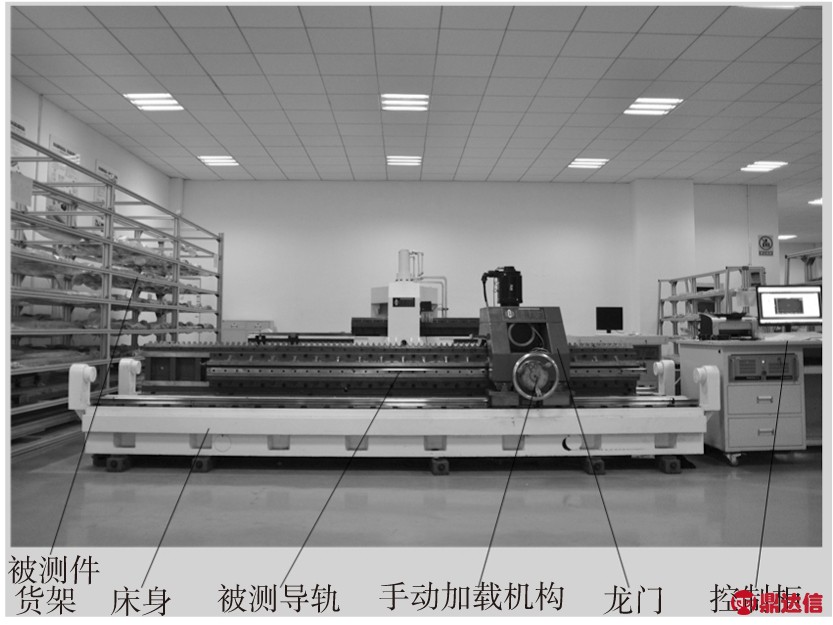
图1 滚动直线导轨副可靠性试验台
1.2 试验条件
试验试件选取四家市场主流导轨产品,具体型号数量如表1(鉴于试验处于研究所设定的条件中进行,结果仅具有科研意义,故将被测件厂家与型号进行处理):
表1 被测试验件型号与数量
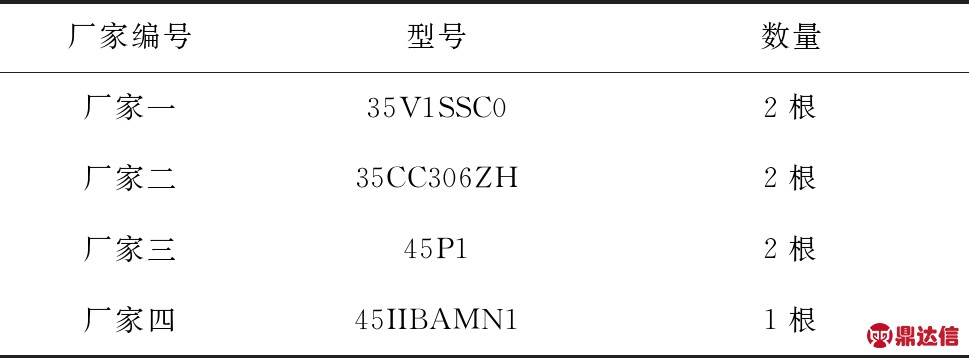
试验被测导轨采用步进加载方式,加载载荷与工作速度、工作里程按表2分配。
表2 被测件试验条件
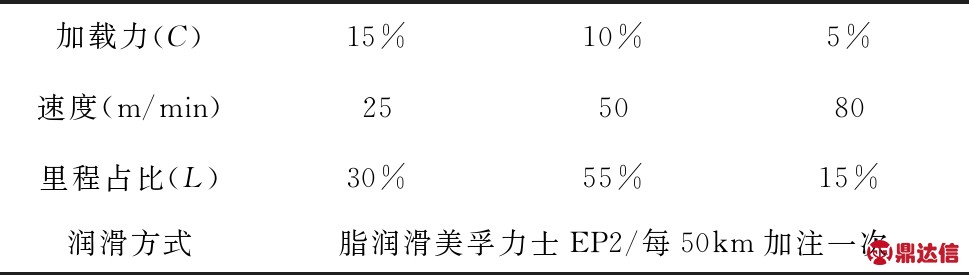
基于步进加载试验当量载荷[8]

(1)
其中:P为重载滚动直线导轨副的全程等效额定载荷,L为重载滚动直线导轨副的全部行程,n为分段跑合次数,qk(1≤k≤n)为对应行程lk的加载载荷,lk为分段的跑合行程。参照公式(1)计算得试验当量载荷P=11.6%C,其中,C为额定动载荷。
1.3 试验过程
试验开始前,以及开始后每运行50km进行一次振动和噪声的测试,并打印报表输出,测试在50m/min的运行速度以及10%C的负载条件下进行。试验中,试验员每日参照滚动直线导轨副功能可靠性试验故障评价指标对被测件进行功能可靠性状况的记录,被测件及试验设备的润滑及维护通过试验员试验值班过程中保证,如图2。
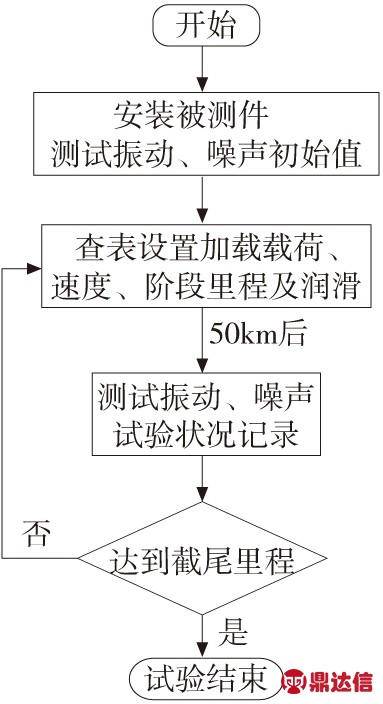
图2 可靠性摸底试验结果
试验中,滚动直线导轨副功能可靠性的故障表现形式通过测试振动与噪声表现,定期测得振动与噪声值与初始值进行比对,比对出的异常振动幅值与噪声分贝值作为故障在试验记录表中记录。
1.4 试验结果
在以上试验计划安排下,对行业内四家厂家进行了功能可靠性的摸底试验,试验结果如表3所示。
表3 可靠性摸底试验结果
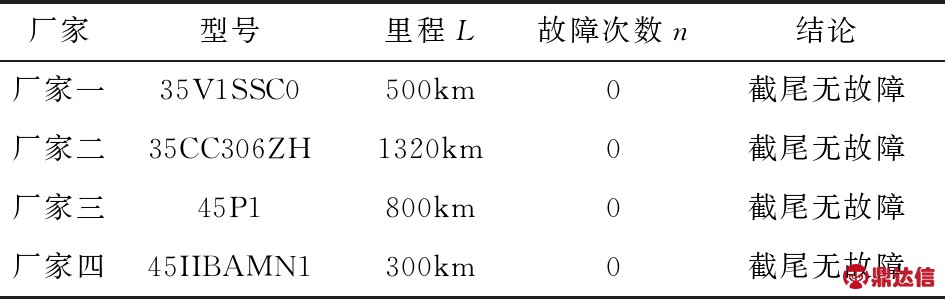
通过试验,可以初步得出判断,市场上主流导轨厂家的主流滚动直线导轨产品都能通过至少300km截尾的功能可靠性试验(当量载荷P=11.6%C)。
可是,通过试验过程中对被测件的细致观察发现,不同厂家的导轨产品在相同的试验条件试验过程中,虽然功能可靠性结果是一致的,但导轨面、滚动体、润滑溢出物等一些方面却有本质的区别:厂家一的产品500km后溢出物清亮、滚道无压痕;厂家二的产品1320km后滚道无压痕、溢出物含有黑色杂质;厂家三的产品400km后溢出红黑色物体、滚动体有红褐色斑痕;厂家四的产品溢出红黑色物体、滚道有轻微压痕;如图3。
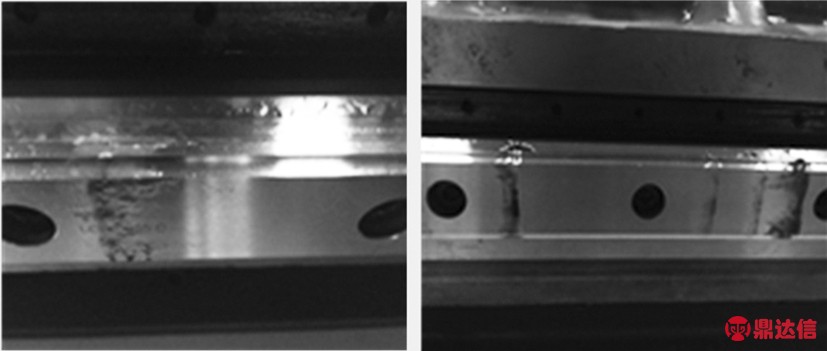
厂家一试验500km后溢出物与滚道状态
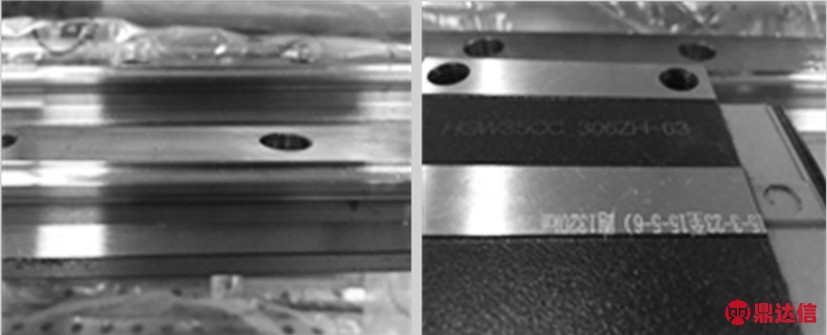
厂家二试验1320km后滚道与滑块状态
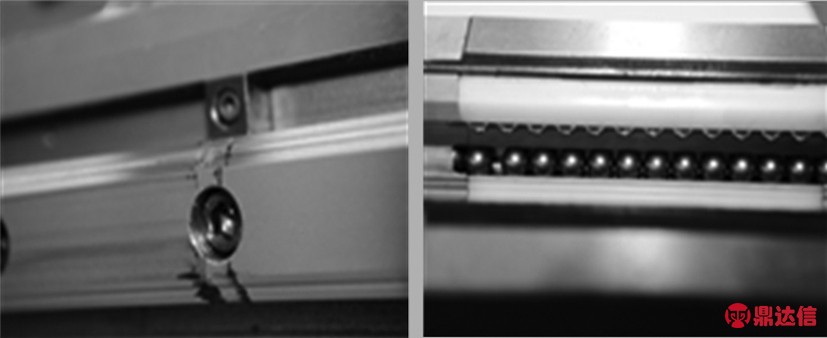
厂家三试验400km后溢出物与滚动体状态
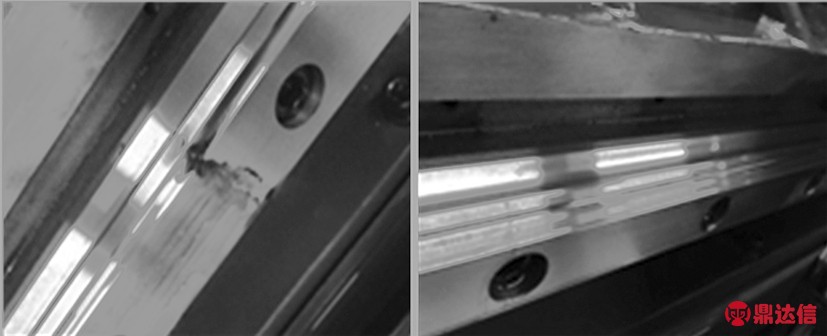
厂家四试验300km后溢出物与滚道状态
图3 试验后导轨状态
2 无故障评价
针对传统的滚动直线导轨副功能可靠性试验,不同厂家、不同型号、不同性能的被测导轨,长期跑和只能得出在截尾里程试验内各种功能故障发生的次数,然而初步试验反映了满足主机使用里程要求内各厂家导轨功能故障次数为零。这些区别目前看,在设定的试验截尾里程内暂不影响导轨功能可靠性,并不排除截尾里程拉长后对功能可靠性故障指标的影响。同时,这些区别反映了不同厂家的导轨用料质量、热处理工艺、加工工序等生产制造环节内的差异,也是不同厂家导轨生产制造经济成本的差异,尤其能反映出滚动直线导轨副产品国内与国外先进水平质量的差异[9],为了在同样无故障试验结果下区别这些差异,引入品质量Q(quality)作为评价指标。
2.1 评价指标定义
品质量Q的定义是:以合格出厂的全新导轨赋予品质量Q=1.0(全新出厂工作里程L=0),工作δ里程后,品质量Q为a,即Q(L=δ)=a(0<a<1,δ>0)。
目前通过试验不同厂家的导轨产品进行观察比对,可以将品质量Q拆分成4个部分,各部分引入品质分量qi作为评价指标,品质分量qi的定义是:以合格出厂的全新导轨在i方面表现赋予品质量qi=1.0(全新出厂工作里程L=0),工作δ里程后,品质分量qi为b,即q(L=δ)=b(0.6<b<1,δ>0)。这4个品质分量为滚道品质分量q1、滚动体品质分量q2、溢出物品质分量q3、其他品质分量qx。每项品质分量的取值需对照品质分量表,查表确定。
2.2 评价指标运算
在进行评价指标模型建立之前,先做两个假设[10]:
(1)单元与系统只可能有两个状态——正常和故障,而没有中间状态。
(2)各单元的失效与否是相互独立的,即任一单元的失效不会引起其他单元的失效。
可靠性理论中关于可靠度的计算,首先对系统中各单元进行串并联判断。如果组成系统的所有单元中任何一个失效就会导致系统失效,则称为串联系统。 串联系统要能正常工作,组成它的所有单元必须都能正常工作,因此串联系统的可靠度为[11]:
Rs(t)=R1(t)R2(t)…Rn(t)
(2)
式中,Ri(t)——单元i的可靠度,i=1,2,…n
滚动直线导轨副作为一个承载导向机械装置,包含了导轨、滚动体、滑块三个元件组成,该系统三个元件必须同时正常工作才能保证整体正常工作,任一元件故障都会导致系统故障,是一个典型的串联系统,其可靠性框图如图3所示。
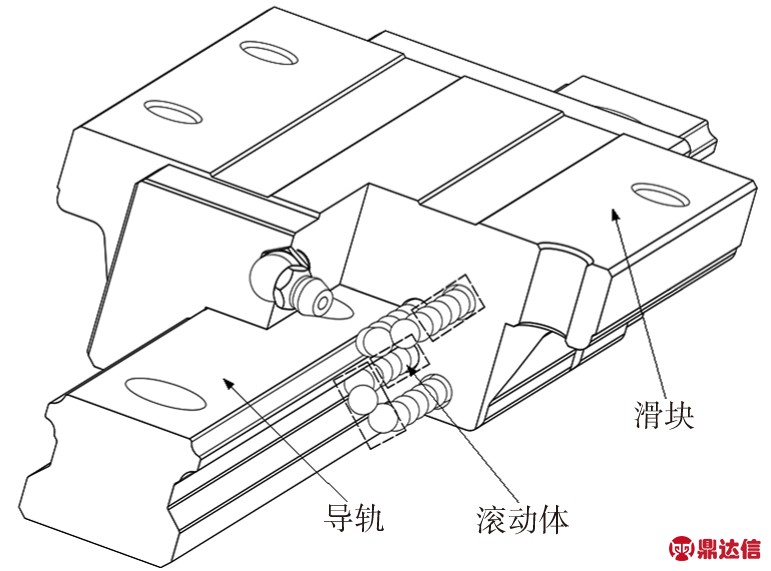
图4 滚动直线导轨副可靠度系统框图
滚动直线导轨副中,滚道、滚动体、溢出物都属于导轨、滚动体、滑块三元件中的各个部分,都能独立导致导轨失效,之间也符合串联关系。参照公式(2)得出品质量表达式为:Q(L=δ)=q1(L=δ)·q2(L=δ)·q3(L=δ)·qx(L=δ)(δ>0)。依据品质分量qi的定义,品质分量q1、q2、q3、qx的取值区间为0.6~1。则品质量极限:
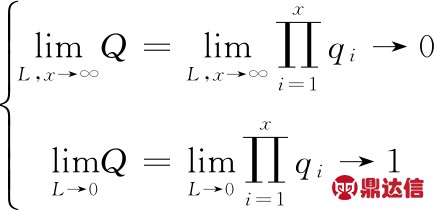
即满足定义要求的且δ>0。
2.3 关于评价指标的说明
①品质量Q是评价滚动直线导轨副功能可靠性试验中无故障结论下的一项指标,滚动直线导轨副在无故障L的定时截尾试验内才有确定值。
②滚动直线导轨副功能可靠性试验条件对品质量Q结果影响巨大,因此,试验过程需严格按照制定的试验条件进行,制定加载载荷、速度、里程比、润滑等统一试验标准是进行功能可靠性试验以及品质量Q计算的前提。
③原则上,不同导轨副产品的品质量Q的相互比较需要在相同的试验里程L与相同的试验条件下才有意义;但明显的,相同试验条件下,不同产品试验不同里程后,大里程产品计算的品质量值若大于小里程产品计算的品质量值则说明大里程产品品质优于小里程产品。
④品质分量qi以0.6为下极限值,低于0.6的试验现象都归结为寿命与故障的表现形式,不加入品质量的计算之中。
⑤品质分量qx作为试验观察中的扩充量,观察到的各项区别可拆分为q4,q5, q6…qr进行细化,没有区别则视为1.0进行计算。
⑥品质分量得分值通过查阅品质分量表(如表4)确定,品质分量表仅适用于滚动直线导轨副截尾试验后的性能评价,随着更大量的截尾试验展开,内容将更加完善。
2.4 滚动直线导轨品质量计算与比较举例:
基于步进加载试验当量载荷P =11.3%C下,试验L=500km中厂家一 35V1SSC0的导轨品质量Q(L=500)的计算如下:
对被测样件500km试验后遵照品质分量q1、q2、q3、qx进行观察。
导轨滚道面光照下几乎无痕迹,
q1 (L = 500) = 0.99;
滑块拆出,光照下滚珠光亮如新,
q2 (L = 500) = 0.99;
导轨两端滑块运动截止处溢出物为清亮油脂与发黑油脂混合状,q3 (L = 500) = 0.95;
其他品质分量未发现,qx (L = 500) = 1.00;
故,此被测导轨品质量评价值
Q(L=500)=q1(L=500)·q2(L=500)·q3(L=500)·qx(L=500)=
0.99·0.99·0.95·1.00=0.93;
基于步进加载试验当量载荷P =11.3%C下,试验L=400km中厂家三45P1的导轨品质量Q(L=400)的计算如下:
对被测样件400km试验后遵照品质分量q1、q2、q3、qx进行观察。
导轨滚道面光照下整条有轻微亮色压痕,q1 (L = 400) = 0.90;
滑块拆出,光照下滚珠有红褐色斑痕,丧失光泽,
q2 (L = 400) = 0.85;
其他品质分量未发现,
qx (L = 400) = 1.00;
表4 品质分量表
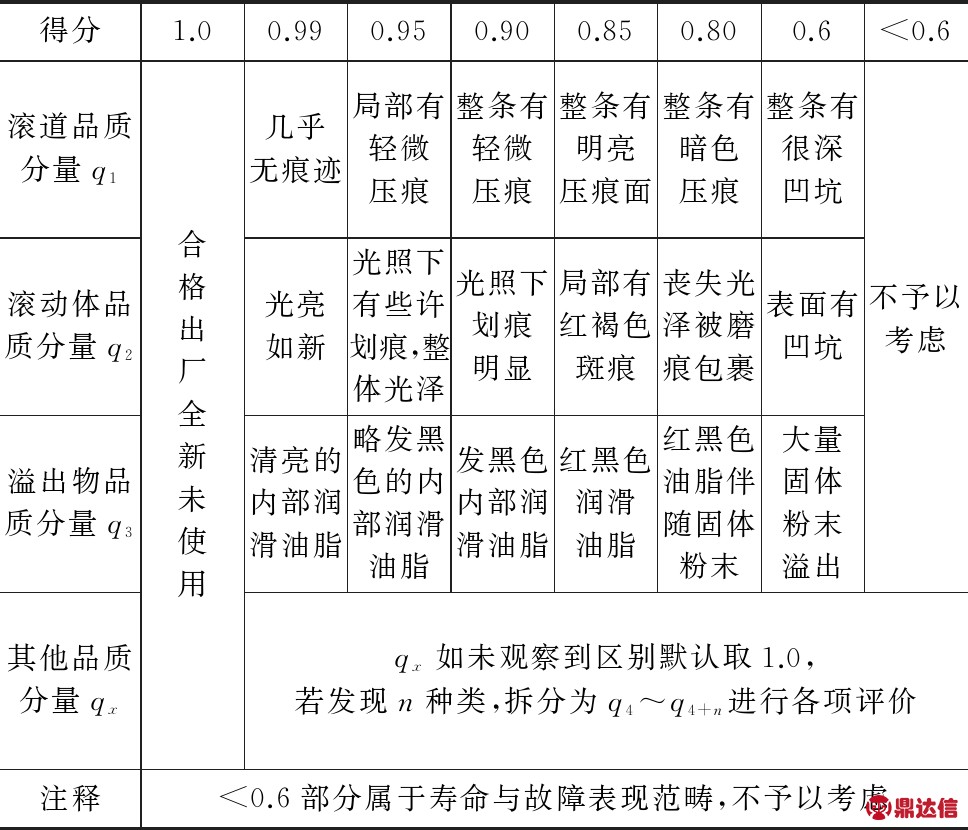
故,此被测导轨品质量评价值
Q(L=400)=q1(L=400)·q2(L=400)·q3(L=400)·qx(L=400)=
0.90·0.85·0.80·1.00=0.61;
对比两家产品试验后计算结果,可以认为,厂家一SHS35V1SSC0在使用过程中产品品质上是优于厂家三LGS-45P1的。
试验中4种被测导轨无故障可靠性评价的品质量Q值如表5所示:
表5 试验无故障可靠性评价计算表
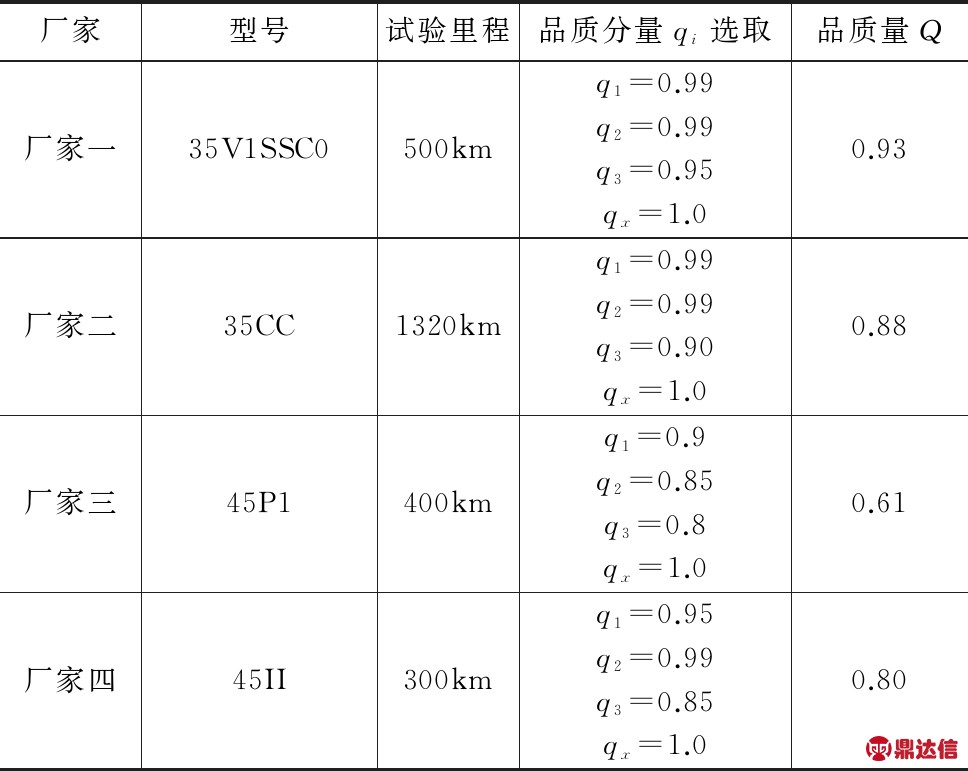
3 总结
基于滚动直线导轨副定时截尾可靠性试验结果中无故障的普遍性以及不同品牌被测导轨的表征显著差异性,提出了品质量Q(quality)的概念;从滚道、滚动体、溢出物、其他品质等四个方面来定性推出Q的值;为滚动直线导轨副无故障结果下的可靠性试验提供评价指标,用于从可靠性试验方向来区分不同导轨厂家的直线导轨产品质量;同时,为研究滚动直线导轨副的科研人员提供一些提高滚动直线导轨副产品质量的研究方向。
滚动直线导轨副品质量Q评价思路可以借鉴应用到其他产品的可靠性试验结果分析中去,以区分不同产品在功能可靠性试验中的质量状况。同时,随着滚动直线导轨副功能可靠性试验的深入开展,试验方案的更加优化,对于其无故障下的评价品质量Q还将更加定量化,从滚道的疲劳损伤深浅、溢出物的金属杂质含量、滚珠表面粗糙度等多重量化角度去研究与分类,更加完善这一品质量定义,让评价结果更加精准。