摘要:机床的横梁在前端运动部件的重力及倾覆力矩的影响下,很难保证横梁导轨所在轴轴线运动的直线度误差和角度偏差满足工艺规定的要求。在实际装配时通过多次刮研导轨面来保证横梁轴轴线运动的几何精度满足工艺规定的要求,装配效率低下,而横梁导轨所在轴最终的几何精度也不高。文中在考虑前端运动部件移动的情况下,利用有限元仿真方法得到了前端移动部件在横梁上各位置处横梁导轨面的变形,并采用反变形原理,对机床的横梁导轨安装面与靠面进行设计,将导轨安装面与靠面加工成微圆弧形式,可以抵消横梁以及前端运动部件引起的重力变形对横梁导轨所在轴的几何精度的影响,从而显著提高机床的装配效率,提高横梁导轨所在轴的几何精度。
关键词:重力变形;导轨面;反变形;微圆弧
0 引言
机床的横梁受到前端移动部件的重力及倾覆力矩的作用,横梁导轨所在轴轴线运动的直线度误差和角度偏差由于重力变形而达不到工艺给定的要求,需要在装配阶段对导轨面进行重新加工以满足工艺给定的精度要求。该种方法需要反复多次刮研导轨面来完成,因此导致装配的效率低下,同时横梁导轨所在轴轴线运动的几何精度也不会太高。
横梁以及前端移动部件的重力变形会导致横梁导轨所在轴轴线运动的几何精度降低,为了解决该问题,已有很多方面的文献进行了研究。张伯鹏[1]等通过建立机床横梁重力变位自演进补偿系统来减小横梁重力变形,从而提高机床横梁部分导轨所在运动轴的几何精度,Han[2]通过优化横梁部分的结构,提高横梁的静刚度,使横梁在重力作用下的变形减小。同样的,关英俊[3]和赵兴玉[4]通过有限元仿真分析了重力及切削力对机床动、静特性的影响,并通过结构改进等方法提高了机床的固有频率和静刚度等。同样的,文献[5-7]通过对机床床身、立柱等大件的筋板、结构形式等进行改进的方法,减小了由于机床自身重力导致的机床变形。但是,上述方法均只考虑了静态下提高横梁导轨部分的精度,且对横梁导轨部分精度提高有限。Ibaraki[8]通过有限元仿真计算和建立并联机床的运动学模型来计算各轴的重力变形,然后通过误差补偿来补偿掉这部分误差。但是,该模型是在静态下计算各点的重力变形,然后再补偿掉这部分的变形。彭志等[9]通过有限元仿真方法计算得到在重力作用下滑板部件在横梁中间点处导轨面的变形,并据此得到了导轨面的反变形量。但是,该方法没有考虑前端移动部件造成的横梁系统重心的变化,因此仅能减小刀具和工件间的相对位姿误差,并不能减小横梁所在轴的直线度误差和角度偏差。
因此,本文在考虑前端移动部件移动的情况下,提出一种从设计制造阶段即可利用反变形原理抵消由于重力变形引起的几何误差的导轨面曲面设计方法,提高了装配效率,同时也提高了机床横梁导轨所在轴轴线的几何精度。
1 导轨面曲面设计原理
1.1 导轨面各点变形量的计算
导轨面曲面设计需考虑托板等前端移动部件在横梁导轨上移动时质心变化对导轨面曲面设计的影响,首先确定前端移动部件在导轨上的行程S,将行程分为若干段,行程上的某一段指的是前端移动部件在横梁上的对应位置。比如将行程分为n段,即对应前端移动部件在横梁或立柱上有n+1个位置,设共有p根导轨,有m个滑块,则设置时需要使m为p的倍数,以利于计算,在移动方向上,两个滑块间的距离为L,在设定n时,使L是S/n的倍数。对于前端移动部件在立柱导轨上的每个位置进行有限元仿真分析,提取m个滑块处各导轨安装面和导轨靠面的变形量,由此共可得到m×(n+1)个变形量数据。为了便于说明,以其中某根导轨的导轨安装面的变形量为例子说明,设该根导轨上共有x个滑块,则
x=m/p
(1)
给该根导轨上的滑块编号,分别为1,2……x,对于位置i,有对应的变形量数据为δi,j,其中,i=1,2……n+1;j=1,2……x,则导轨面上各点滑块经过的次数为1~x次不等,同时,设
q=L/(S/n)
(2)
则对于导轨面上的某一点,其变形量的值为
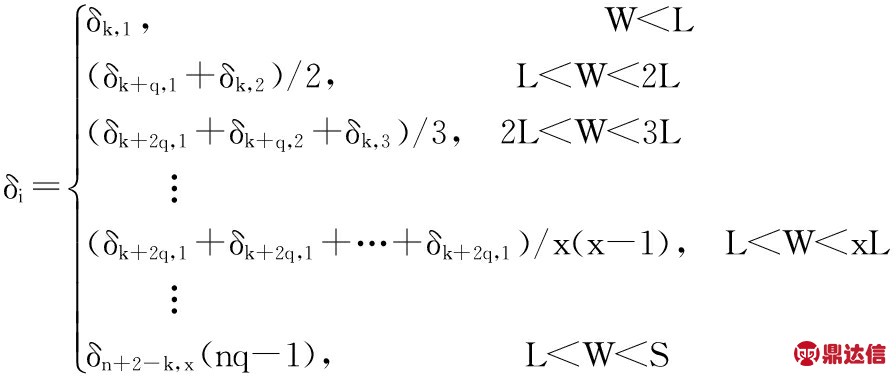
(3)
其中,W为滑块距离初始位置的距离,k=1,2,3……q。如图1所示,是横梁及其前端移动部件的结构简图,前端移动部件往前移动一个移动间隔D计算一次。
然后利用反变形法的原理,设计出导轨安装面与靠面的实际加工曲面,以提高导轨所在轴线运动的几何精度。由于导轨安装面的长比宽大很多,所以在设计时,认为宽度方向的变形量大致相同,导轨安装面曲面设计以一条曲线来表示。反变形法是焊接工艺里的术语,其定义为:事先估计好结构变形的大小和方向,然后在装配时给予一个相反方向变形与焊接变形相抵消,使焊后构件保持设计的要求。[10]应用到本文中,给予反变形法的定义是:为了提高导轨精度,对垂直平面内安装的导轨,根据预先计算出的导轨安装面与靠面的变形量,在加工时给导轨安装面与靠面一个相反方向的变形,从而得出导轨安装面与靠面的加工曲线。
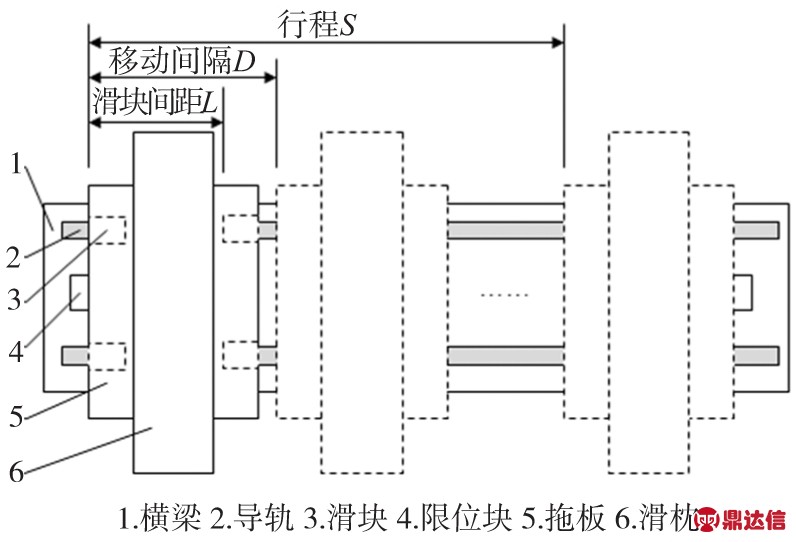
图1 横梁及前端移动部件结构简图
1.2 各点刮研量的修正
实际刮研时,在横梁下垫地脚垫铁,由于横梁受重力作用,在刮研前,横梁导轨面有重力变形。当实际刮研时重力方向与实际使用时重力方向相同时,导轨面的刮研量数据不需要修正,当实际刮研时重力方向与实际使用时重力方向不同时,必须对各点的刮研量数据进行修正。设在实际刮研工艺下,导轨面各点的重力变形为,则修正后各点的刮研量为:
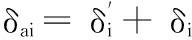
(4)
2 导轨安装面曲面设计实例
由于考虑到垂直平面内安装的直线导轨受到前端部分重力以及倾覆力矩的作用,机床生产厂家为了提高机床导轨部分的精度,在加工导轨面的过程中,都预先设计一个反变形量,以提高导轨的精度。但是,机床厂家给出的量都是根据经验,没有实际的计算原理与准则,在实际装配过程中需要经过多次刮研才能勉强达到工艺规定的要求,机床的装配效率低下,同时装配后机床横梁导轨部分的精度不高。下面就通过有限元方法,计算出导轨安装面与靠面实际的反变形量,从而得出导轨安装面与靠面的加工曲线。
图2为某型号龙门立柱式加工机床横梁导轨安装面的简图,横梁导轨滑块由于承受托板和滑枕重力以及倾覆力矩的影响,如果仍将导轨安装面加工成直线,将对最终的X轴与Y轴造成很大的影响,根据受力分析,很容易想象应该将上下导轨的安装靠面加工成向上凸起的形状,上导轨安装基面加工成向里凹进的形状,下导轨安装基面加工成向外凸出的形状。具体的做法为:对主轴部分在横梁上各个位置进行有限元仿真分析,得出主轴部分在各个位置时候横梁导轨安装面处相应位置的变形,通过反变形的原理,描绘出导轨安装面的加工曲面,由于导轨安装面和靠面长度方向的尺寸相比宽度方向的尺寸大的多,同时,由仿真计算可得,宽度方向的变形相差不大,故将导轨安装面的曲面画成一条曲线的形式。
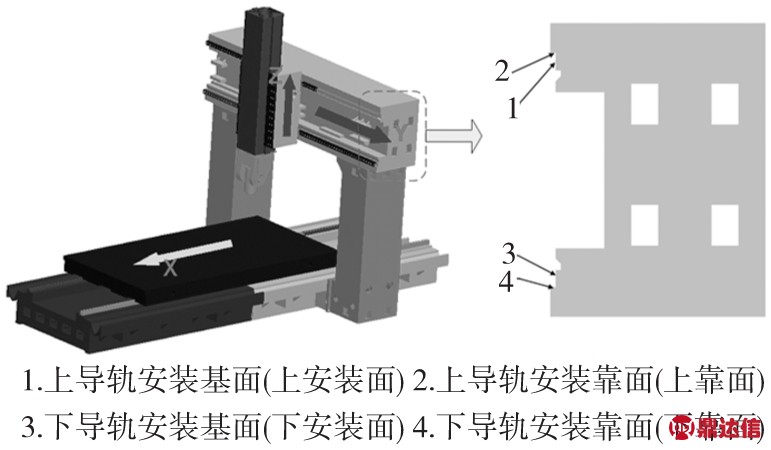
图2 某型号龙门立柱式加工机床
表1为立柱横梁部分各组成部件的材料以及参数。
表1 立柱横梁部分各部件的材料及参数
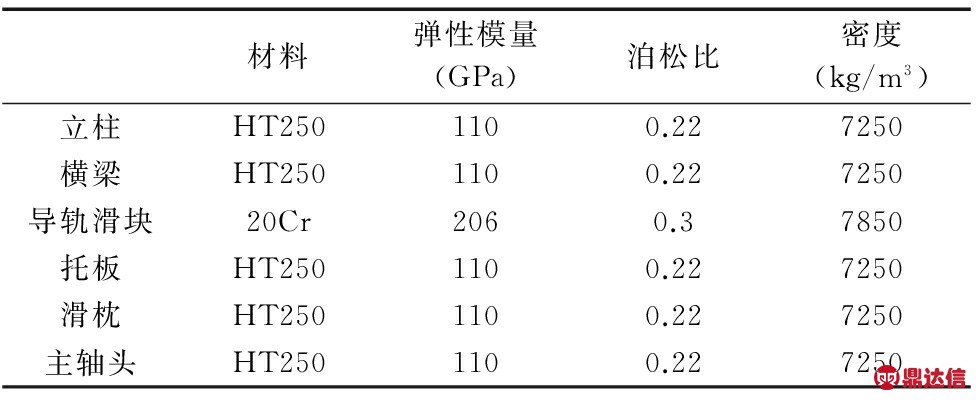
对立柱横梁部分各零部件进行粘结处理,并对各零部件施加重力,用SAMCEF有限元分析软件对主轴部分在横梁上11个位置处进行有限元仿真分析。
一共可得出11个位置在重力作用下变形的仿真分析给出的X向与Z向变形。表2给出了在各个位置的变形量,根据式(3)和式(4),可以得出上下导轨安装面与垂直靠面应该加工成的形状,如图5所示。表2中,200mm,500mm……3200mm分别表示图2中的横梁导轨安装面上,距离横梁左端为200mm,500mm……3200mm的离散点。上导轨安装基准面与靠面的位置如图2所示。
表2 重力作用下导轨安装面的变形数值(μm)
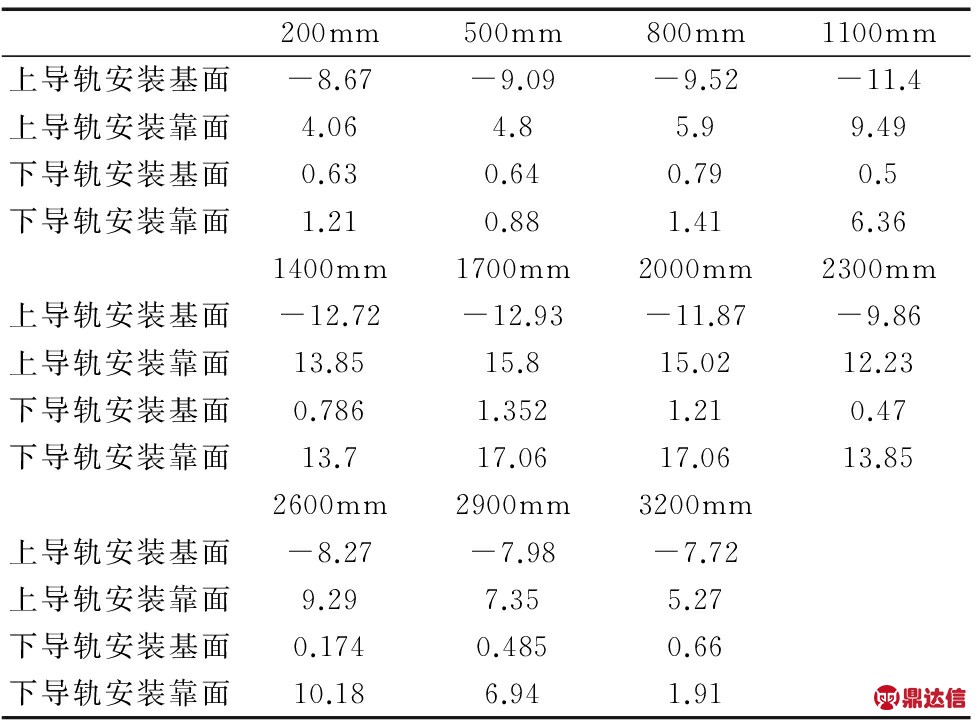
上表为仿真得出在重力下横梁导轨处的变形数值,其单位为μm,表中负值表示受拉,应该把曲线加工成凹形,图3给出了上导轨基面与靠面,下导轨基面与靠面的加工图线。
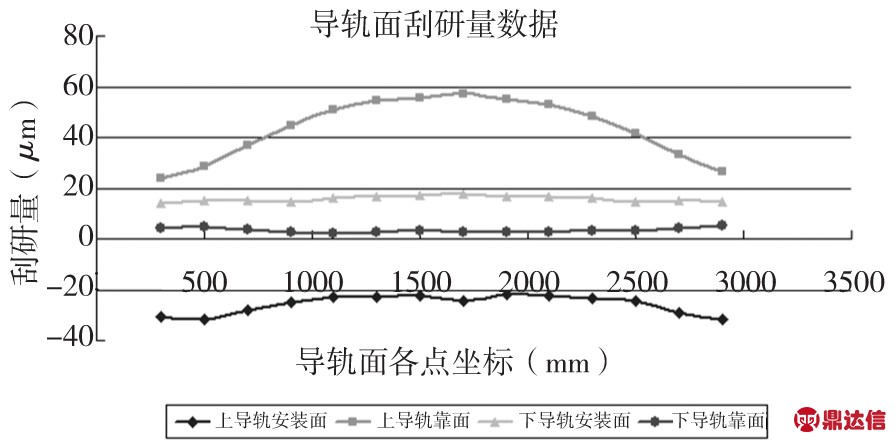
图3 导轨安装面的加工图线
显然,对于此龙门立柱式机床,如果把导轨安装面与靠面简单的加工成直线,则将带来直线导轨所在轴在XOY和YOZ平面内的直线度分别为18μm和15μm,所以应按照如图所示的加工曲线加工,可以消除因为自重以及倾覆力矩带来的导轨精度的降低。
3 测试验证
以图2所示的某龙门立柱式加工机床作为验证对象,得到如表2所示的重力变形数据。在装配完成后,测试得到第一组几何精度测试数据,此时可以忽略残余应力、材料蠕变效应等的影响,而只考虑重力对几何精度的影响。导轨面各点在实际装配完成后的变形量可通过式(5)所示计算:
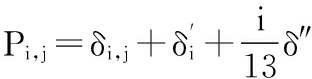
(5)
式中:
Pi,j—理论计算的实际导轨面装配完成后的变形量;j=1,2,3,4时分别表示上导轨安装面、上导轨靠面、下导轨安装面、下导轨靠面的变形量;
δi,j—仿真得到的导轨面的变形量;
—该点导轨面的刮研量;
δ″—床身水平值;
其中,床身水平(正对机床):右端高5μm,,车间实际刮研导轨面时,各导轨面的刮研量如表3所示,通过式(5)可以计算得到最终导轨面各点在重力作用下的计算值,如表4所示,从而通过式(6)、(7)、(8)计算X轴移动的俯仰、倾斜和偏摆误差。表3和表4中,300mm,500mm……2900mm分别表示图2中的横梁导轨安装面上,距离横梁左端为300mm,500mm……2900mm的离散点。
表3 各导轨面刮研量(μm)
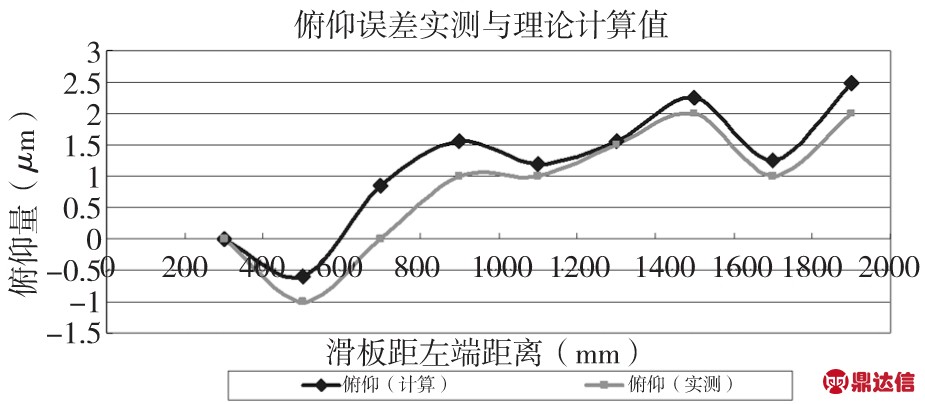
表4 装配完成后导轨面各点变形量(单位:μm)
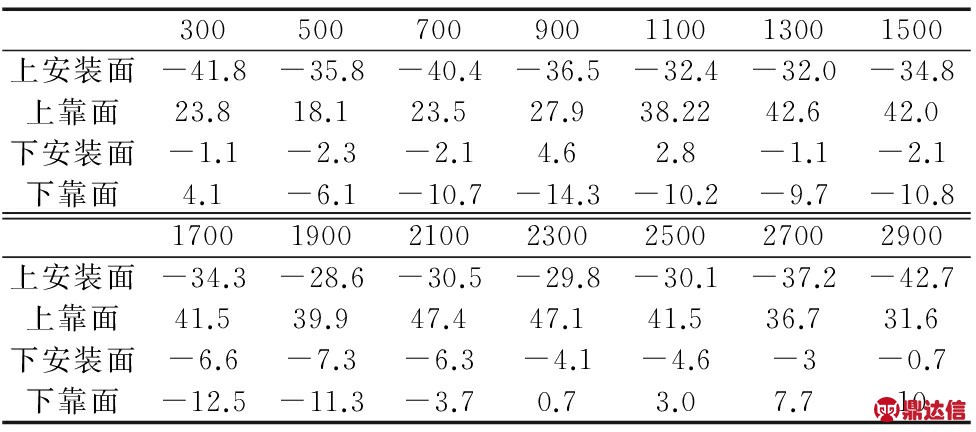
俯仰误差计算公式:
δi1=(Pi+5,2-Pi,2+Pi+5,4-Pi,4)/2
(6)
倾斜误差计算公式:
δi2=(Pi,1-Pi,3+Pi+5,1-Pi+5,3)/2
(7)
偏摆误差计算公式:
δi3=(Pi+5,1-Pi,1+Pi+5,3-Pi,3)/2
(8)
δi1、δi2、δi3分别表示滑板在位置i时X轴的俯仰、倾斜和偏摆误差。下面就X轴俯仰、倾斜、偏摆误差的理论计算值和实际测试值进行对比:
①X轴移动俯仰误差:
由图4可知,由车间实际加工曲线以及重力仿真得到的导轨安装面的变形数据可计算出X轴移动的俯仰误差为3.09μm,而实测值为3μm,俯仰误差的理论计算值与实测值相差不大,且各点的俯仰量的理论计算值与实测值基本相同,相差最大的为滑板距离左端900mm点,其实测值与理论计算值相差0.85μm。
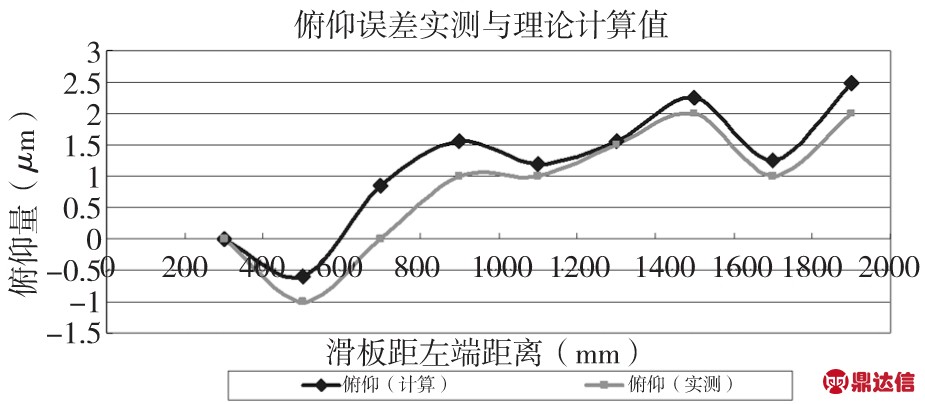
图4 理论计算与实测X轴移动时的俯仰误差
②X轴移动倾斜误差:
由图5可知,由车间实际加工曲线以及重力仿真得到的导轨安装面的变形数据可计算出X轴移动的倾斜误差为7.5μm,而实测值为7μm,理论值与实测值相差不大,且各点倾斜量的理论计算值与实测值基本相同,其中相差最大的为滑板距离左端500mm点,理论计算值与实测值相差0.7μm。
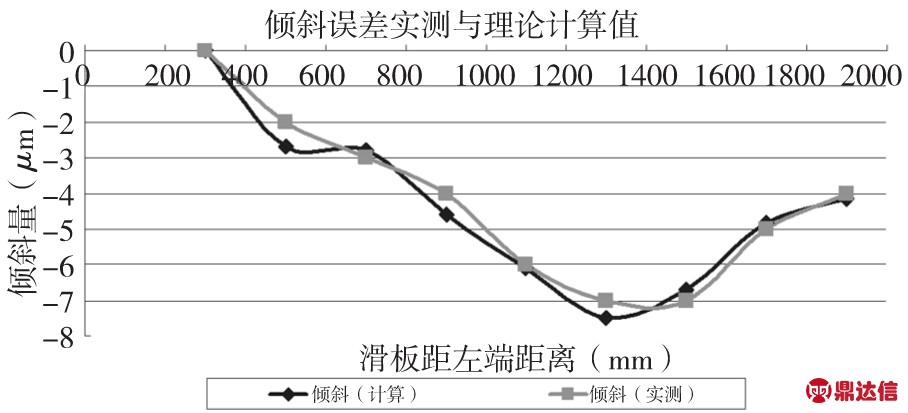
图5 理论计算与实测X轴移动时的倾斜误差
③X轴移动的偏摆误差:
由图6可知,由车间实际加工曲线以及重力仿真得到的导轨安装面的变形数据可计算出X轴移动的偏摆误差为8.65μm,而实测值为10μm,理论值与实测值相差不大,且各点偏摆量的理论计算值与实测值基本相同,其中相差最大的为滑板距离左端300mm点,理论计算值与实测值相差1.35μm。
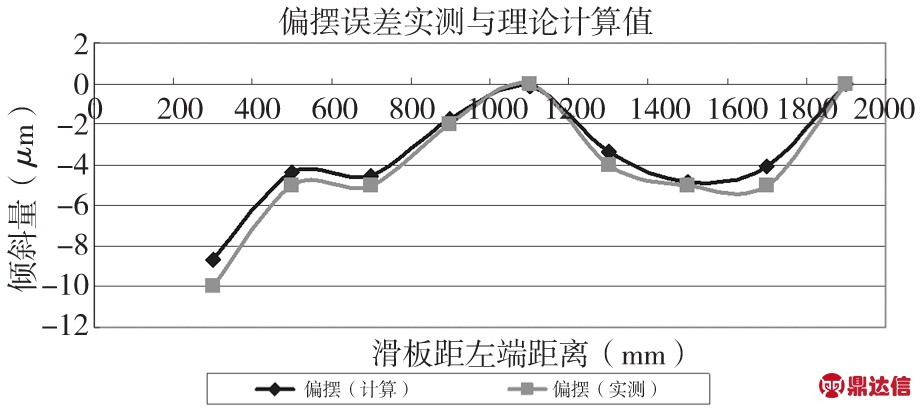
图6 理论计算与实测X轴移动时的偏摆误差
从这些数据可知,俯仰、倾斜和偏摆误差的计算值与实测值很接近,其偏差相当于实际测试误差,其中相差最大的为偏摆误差,计算值和实测值相差13.5%,验证了用反变形原理设计导轨安装面曲面的正确性。
4 结论
通过以上分析,可以得到以下结论:
(1)垂直平面内安装的导轨,由于受到前端主轴部分重力以及倾覆力矩的作用,直接加工成直线不利于提高导轨的精度。通过本文提出的导轨面反变形设计方法,可计算出直线导轨安装面的加工曲线,提高直线导轨所在轴轴线运动的几何精度。
(2)通过对某龙门立柱式加工机床的测试验证,得到X轴移动的角度偏差中,理论计算值与实测值相差最大的为偏摆误差,相差13.5%,验证了用反变形原理设计导轨安装面曲面的正确性。