摘要:胶轮单轨电车属于中等运能的新型有轨电车,具有比地铁投资小、工期短,比高架轻轨线路成本低、污染小,且对道路要求较低等优点。对胶轮导轨电车的发展及在国内外的研究现状进行概述,详细说明车辆的工作原理。设计新型导向机构并对导向机构原理、运动规律、锁死机构可靠性进行分析。根据其最小通过曲线半径设计连杆尺,为验证该尺寸是否满足要求,建立拖车转向架动力学模型,对其进行仿真分析,结果表明该方案切实可行。
关键词:胶轮导轨电车;走行部;导向机构
0 引言
19世纪工业革命的出现,推动了现代轨道交通技术的快速发展。进入20世纪,轨道交通以其运量大、快捷、节能环保、安全可靠已成为人类最为重要的交通运输模式之一,对世界经济的发展起到了不可磨灭的贡献。近年来,随着我国国民经济的快速发展人口不断增加,轨道交通已成为我国大城市解决城市交通问题的首选方案。
但是现在几乎所有的有轨电车均采用钢轮钢轨的走行模式,由于车辆在钢轨上行驶时产生振动和噪声,对周围环境的影响已成为限制城市轨道交通发展的突出问题之一[1-2]。自导向胶轮电车应运而生,胶轮导轨电车作为自导向胶轮电车的重要组成形式,具有比地铁投资小、工期短,比高架轻轨线路成本低、污染小的优点,且对道路要求较低,适合在城市中运行[3]。
为满足市场需求,国内正在自主研发一种胶轮导轨电车。对于路面单轨导向胶轮式车辆,导向机构的作用是将导向轮的导向力传递给两侧走行轮。导向机构的设计直接影响车辆的曲线运行性能,本文设计一种导向机构并对其导向可靠性进行研究。
1 发展概述
胶轮单轨电车采用胶轮承载、钢轮导向[4],GLT有轨电车采用H型的导向钢轮,而Translohr有轨电车采用V型导向轮进行导向。
第一条GLT有轨电车线路建于2001年,并在法国Nancy市开通运行,如图1所示。2002年11月,经改造升级后的GLT有轨电车在法国Cean市再次投入运行,如图2所示。
第一条Translohr有轨电车线路于2001年在法国Clermont-Ferrand开通运行,如图3所示。2007年至今,意大利帕多瓦陆续修建3条Translohr线路,贯穿整个城市,如图4所示。由于其运行性能佳,意大利、法国等欧洲国家都选择修建了Translohr线路,如Medellin、Venice等。
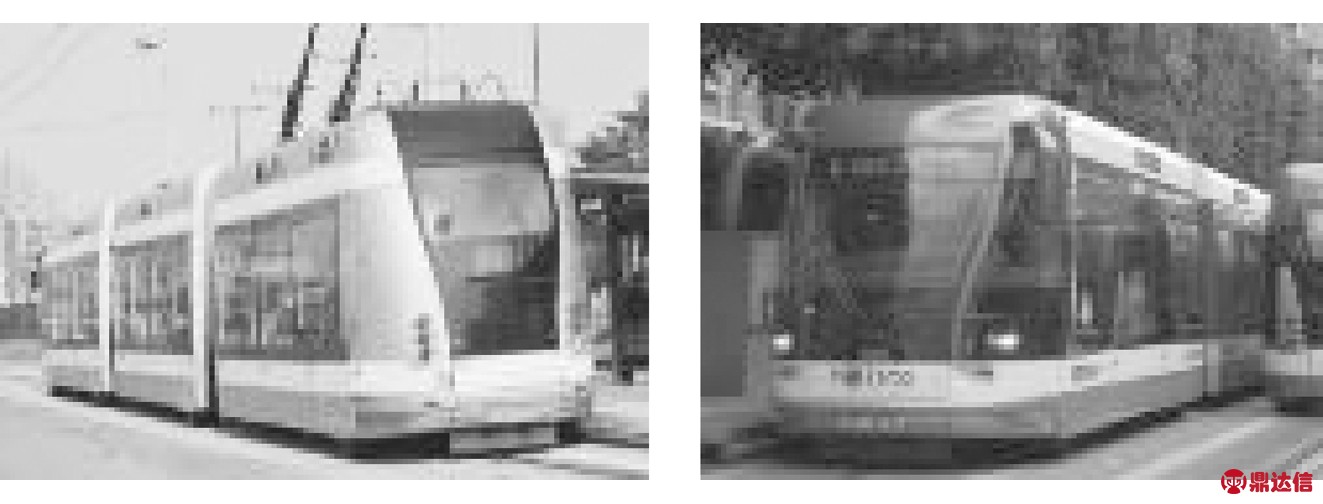
图1 Nacy’s GLT 图2 Cean’s GLT
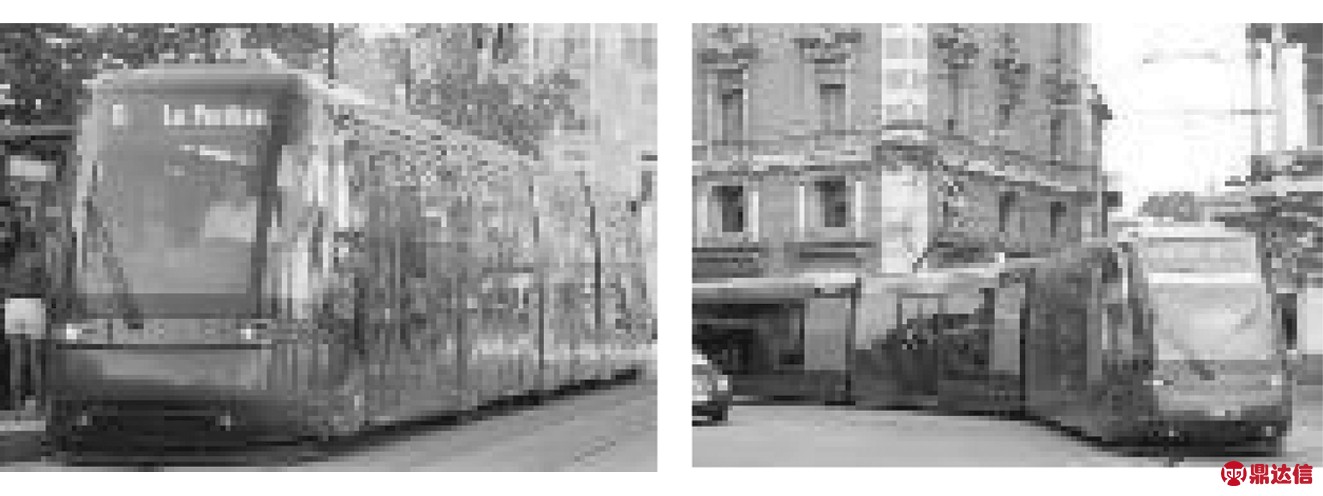
图3 Ferrand’s Translohr 图4 帕多瓦Translohr
近年来,我国十分重视城市有轨电车的发展。2005年,天津市滨海新区建立了首条Translohr有轨电车线路,如图5所示。2007年12月,上海浦东张江高科新区修建了Translohr线路,全长10 km,共设15个站点,如图6所示。
2 技术特点
胶轮导轨电车由多节车体通过铰接组成,图7为三车体编组形式,由终端模块、乘客模块和中间模块组成。终端模块坐落在动力走行部上,设计为驾驶室;两乘客模块通过中间模块相连接,非动力走行部装于中间模块的下方,可以通过增加中间模块和乘客模块来增加客运量[5-7]。
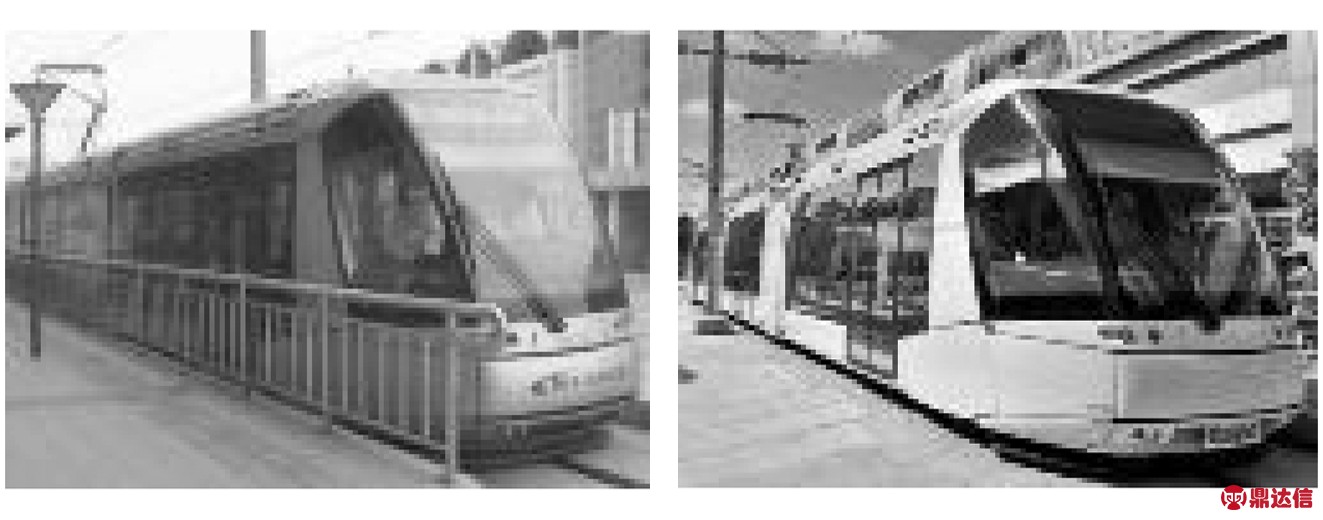
图5 天津Translohr 图6 上海Translohr
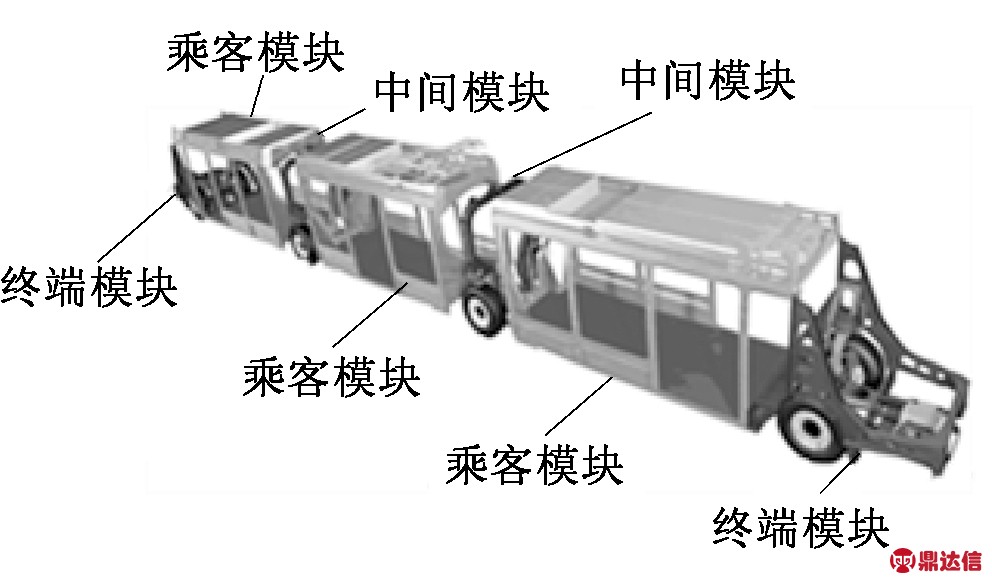
图7 胶轮导轨电车
动力走行部作为车辆的重要组成部分具有承载、牵引、制动、导向的作用,如图8(a)所示,主要由动力轴桥、轮胎、导向机构组成,导向机构通过中心销与动力轴桥相连接,轮胎安装在轴桥端部的转向臂上,转向臂一端与转向杆铰接,转向杆另一端与导向机构铰接。转向臂、转向杆、导向机构、轴桥构成四连杆机构,当导向机构绕轴桥转动一定角度时轮胎也会跟随转动进行转向通过曲线。非动力走行部结构较为简单,如图8(b)所示,轮胎直接铰接于轴桥上,仅能绕横向转动,导向机构连杆直接与轴桥相连接。
3 导向机构研究
导向机构如图9所示,采用双侧轮缘导向轮方式,用多连杆和滑块来保证导向机构处于锁定和自由状态。滑块控制连杆机构横向锁定与释放,在正常运行情况下沿运行方向的四连杆机构处于锁定状态,而相反方向的四连杆机构处于释放状态,处于释放状态的连杆机构不参与导向,仅起保护作用。
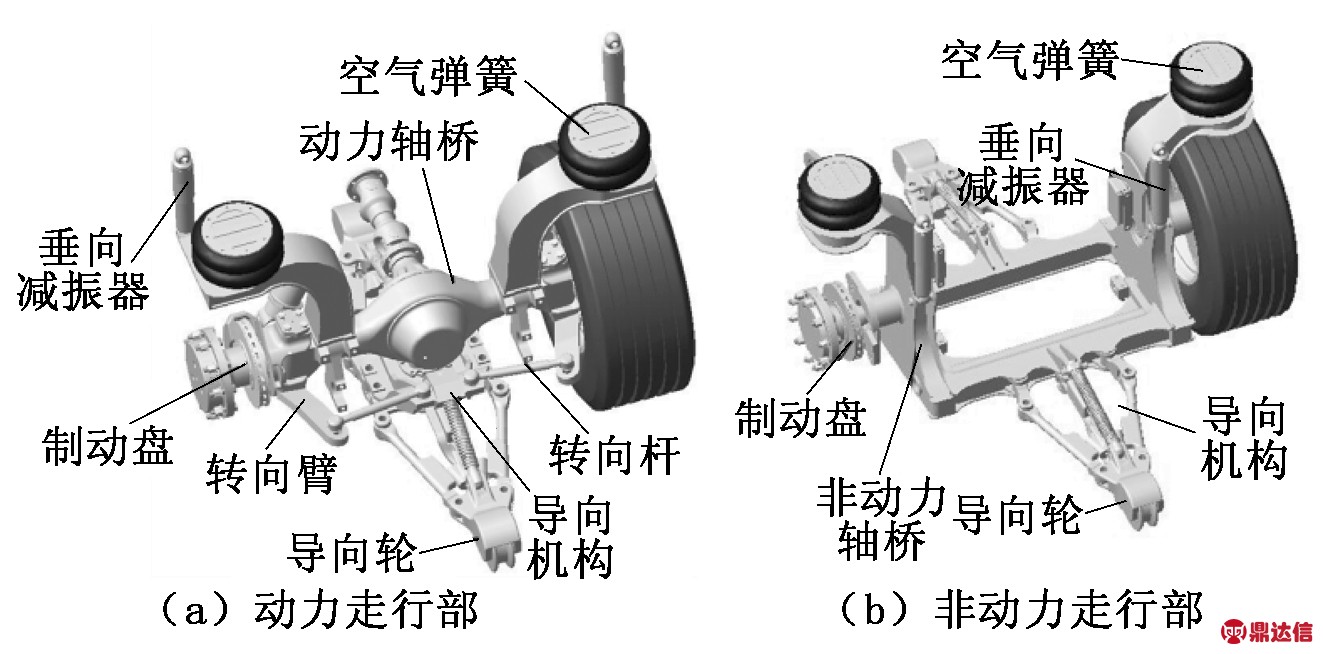
图8 走行部
3.1 导向机构原理
导向机构原理图如图10所示,在自由状态(图10(a))时连杆可以绕其铰接点转动,当需要导向时作动器推滑块1和1′向前运动与2和2′接触(如图10(b)所示)将相应连杆机构锁死,具有导向性能。

3.2 运动规律分析
对单侧连杆机构的运动规律进行分析,各连杆的运动规律如图11所示。机构中间连杆的最大偏转位置如图12中虚线所示,其最大偏转角α可以通过式(1)求得:
.
(1)
式(1)中的L1~L7如图13所示。
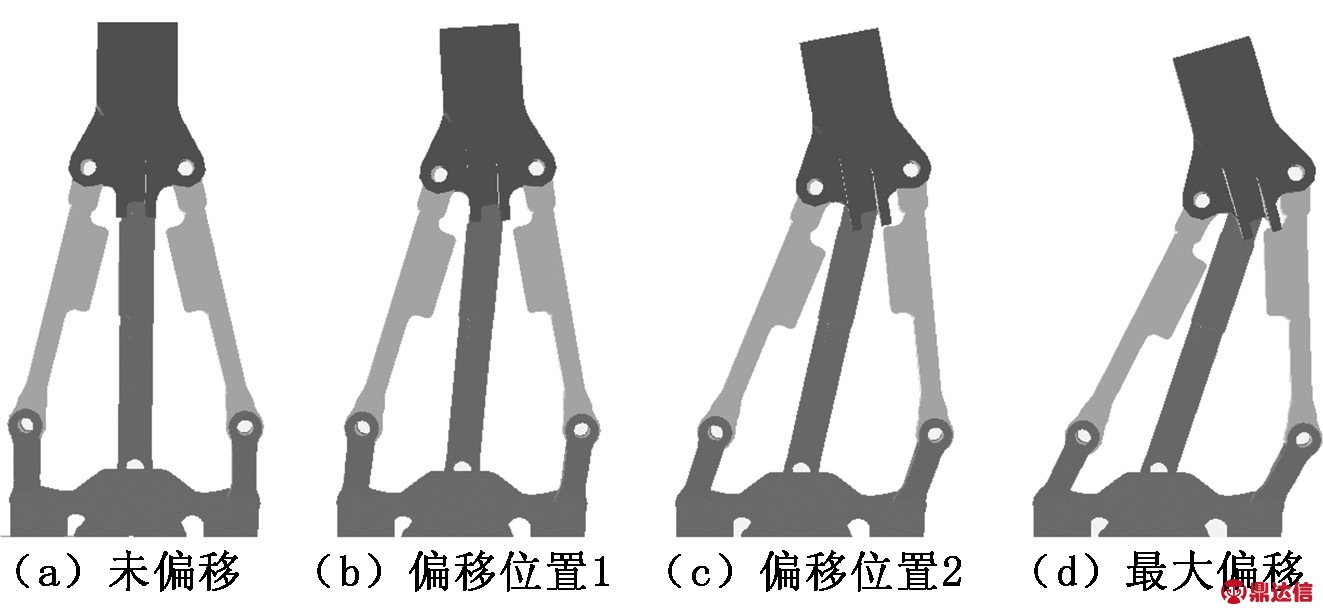
图11 连杆机构运动规律
3.3 锁死机构分析
为了验证锁死机构的可靠性,在SIMPACK中建立导向机构模型,在滑块与两侧连杆使用PCM接触力元模拟滑块与连杆间的接触,在转向杆两侧使用约束使转向臂无法自由运动,在前端导向轮处施加横向力以验证锁死机构的可靠性。结果表明在横向力的作用下导向机构无法自由地运动,说明锁死机构是可靠的。锁死机构模拟图如图14所示。
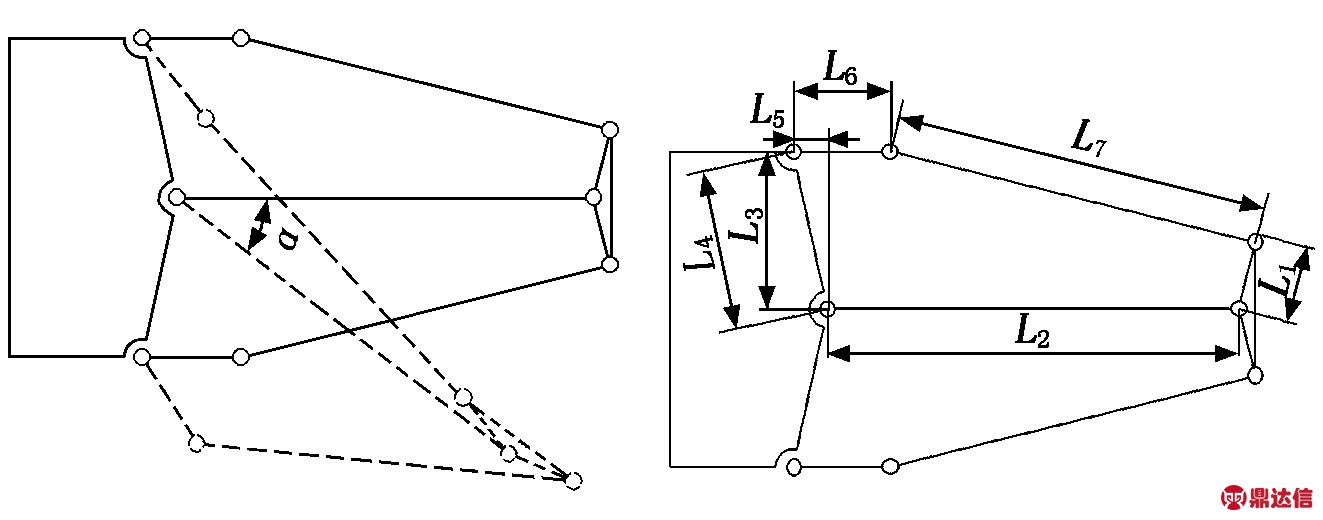
图12 连杆机构极限位置 图13 L1~L7参数图
3.4 连杆尺寸确定
图15为非动力走行部通过曲线时各连杆的状态。由于在通过同样曲线半径时非动力走行部中间连杆ED的转角α大于动力走行部,而通过曲线时转角α的最大值是确定连杆长度的重要因素,故以非动力走行部为研究对象。直线运行时转角α为0,随着前端导向机构逐渐进入曲线,转角α逐渐增大,当前后导向机构完全进入曲线时转角α达到最大,且转角α随着曲线半径的减小而增大。而转角α的大小又受到连杆AB、BC长度之和的限制,在通过最小曲线半径时若想使转角α顺利达到最大值则杆AB、BC长度之和应当大于在最大转角时AC连线的值。由于结构设计空间尺寸的影响除杆DE长度之外其他尺寸均可初步确定,杆DE尺寸确定后杆AB、BC尺寸也可确定。

图14 锁死机构模拟
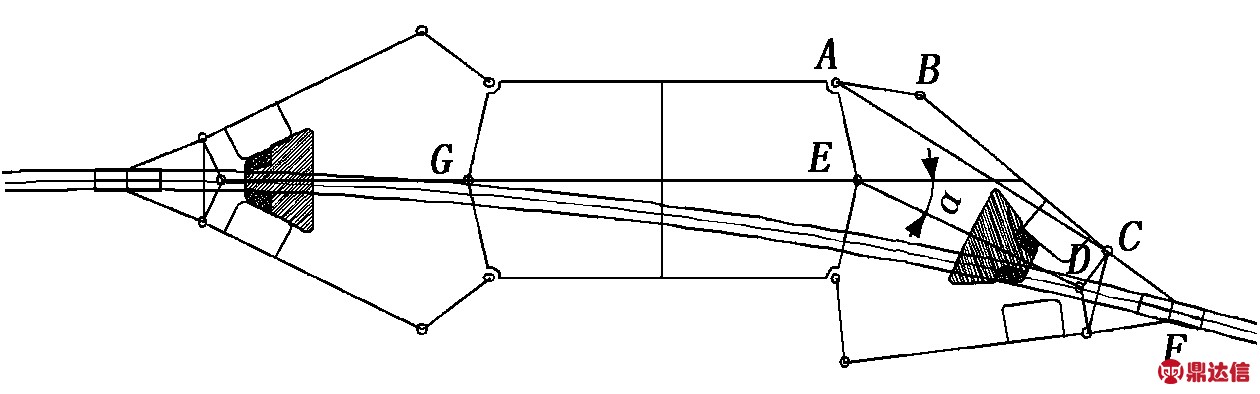
图15 非动力走行部曲线通过图
若导向杆长度太短,在高速时会造成导向运动的阻尼比太小,从而引起导向运动的振荡,参考相关车辆导向机构设计经验,本设计中将中间连杆长度设计为600 mm。根据已知尺寸做出在通过10.5 m曲线半径时导向机构各杆位置,如图16所示。连杆AB、BC长度之和应当大于此时AC连线的值,在此状态时AC连线为770 mm,考虑到作图及设计制造时的误差将AB、BC长度之和设计为800 mm,其中AB为300 mm,BC为500 mm。各连杆尺寸如图17所示。
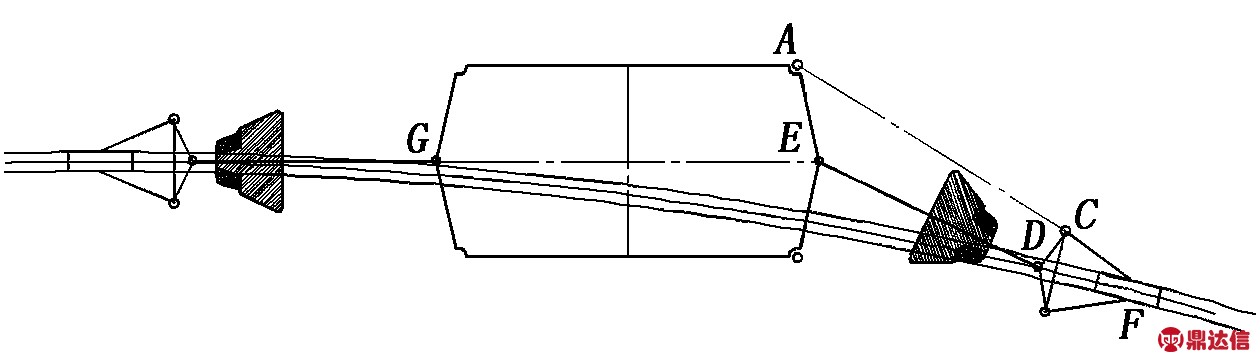
图16 导向机构各杆位置图
为验证该尺寸是否满足要求,建立该尺寸的动力学模型,让其通过10.5 m半径曲线。当导向机构完全进入曲线上时导向机构状态如图18所示。通过验证该连杆尺寸配合可以顺利通过曲线,满足使用要求。
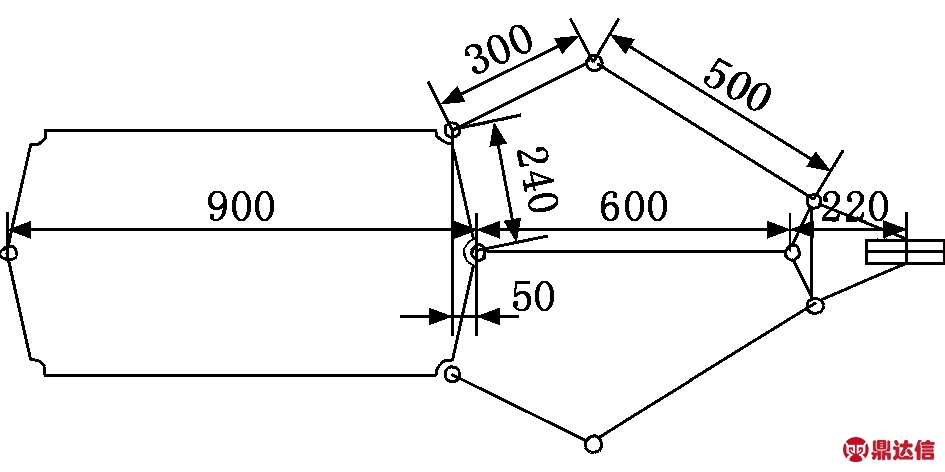
图17 结构尺寸图
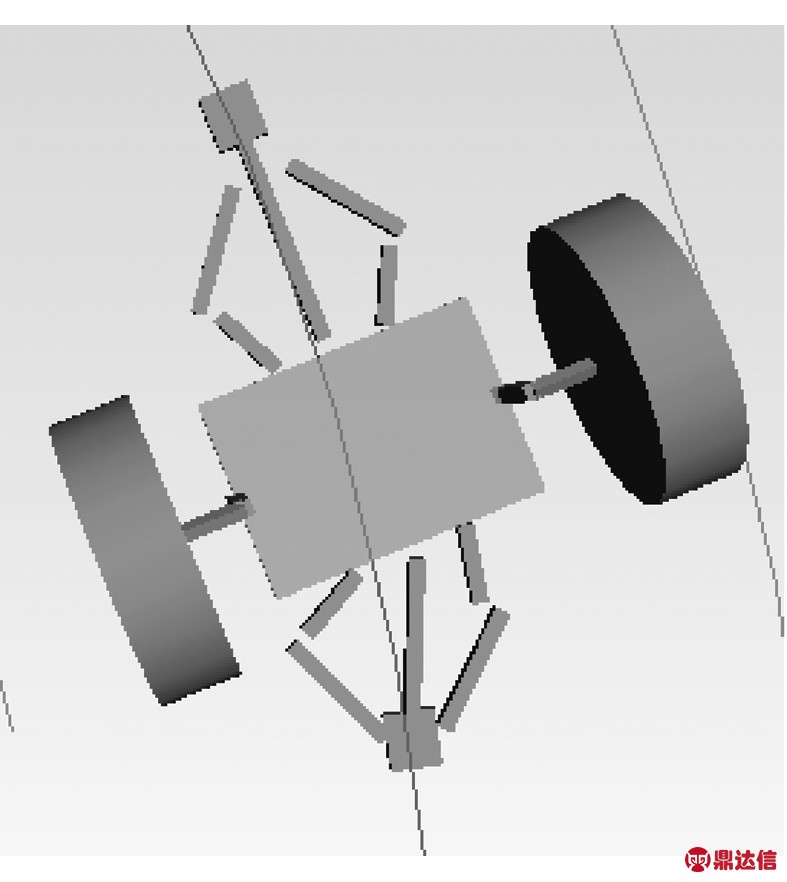
图18 曲线通过图
4 结论
为实现胶轮导轨国产化,本文设计了胶轮导轨电车导向机构,对新导向机构的导向机构原理、运动规律、锁死机构可靠性进行分析,并将设计的导向机构带入非动力走行部动力学模型中进行仿真分析,结果表明该方案切实可行。