摘要:45000t集装箱滚装船(Con-Ro)创新性地采用连续超高导轨架,配合挡雨盖,对货舱内及货舱以上的集装箱进行约束、导向和承载,从而实现无舱盖、无绑扎,提高码头集装箱驳运效率、减少码头工人的工作强度。对该船的挡雨盖及导轨架进行研究及技术总结,分析其与传统集装箱船的差异和技术难点及设计改进,以期对生产施工有所帮助,提高建造质量,达到预期设计效果。
关键词:集装箱滚装船;导轨架;挡雨盖;连续超高型导轨架;绑扎;精度
0 引 言
45000t集装箱滚装船(以下简称“集滚船”)为全球首批G4型系列高科技船,是目前世界上最大、最先进的集滚船。该船创新性地在集装箱货舱区域采用连续、超高导轨架,由货舱内延伸至货舱外,安装于导轨桥结构上,对货舱内和货舱以上的集装箱进行约束、导向,从而无需任何绑扎。同时,在主甲板处设置有轻质挡雨盖,承载主甲板以上的集装箱,并避免大面积雨水落入到货舱中。该船设计理念新颖,实现了无舱盖、无绑扎,相对于传统的集装箱船,大大提高了码头集装箱驳运效率、降低了码头工人的工作强度,尤其降低了码头工人的工作危险度。
1 连续、超高导轨架
导轨架用于集装箱装载和运营时对货舱内的集装箱进行导向和限制移动。45000t集滚船的导轨架创新性地设计为连续超高型,主甲板以上采用导轨桥式结构而非传统的绑扎桥形式,与货舱的横隔舱同宽,保持导轨架上下连续。
导轨架末端距离货舱底部2100mm,上段导头延伸至四甲板以上导轨桥结构,导轨架最长近39m;导轨架连续延伸出货舱,中间在四甲板处断开,上下导轨架间隔 20mm(见图1)。
驳运集装箱时,需从导轨桥上的导轨架顶端吊放集装箱,然后顺沿导轨架吊落集装箱至货舱或从货舱吊出集装箱,上下行程跨越整根导轨架。不同于传统的集装箱船,该型船的导轨架仅存在于货舱内部,横隔舱上方的绑扎桥尺度略小于横隔舱,因此集装箱可在主甲板上横向驳运移动,不需严格从绑扎桥的顶端落放集装箱(见图2)。但是,传统的集装箱船需对主甲板以上的集装箱采取必要的绑扎措施(例如系固在绑扎桥等结构上,见图3),以防止脱落或碰撞等,因此会有较多的绑扎附件(诸如拉杆、绑扎环等),码头工人需耗费大量的劳动来绑扎集装箱,还会因高空作业造成不安全后果。因采用连续超高的导轨架设计,该型船未设置任何绑扎附件,可通过连续超高的导轨架对集装箱进行必要的约束,实现无绑扎设计。
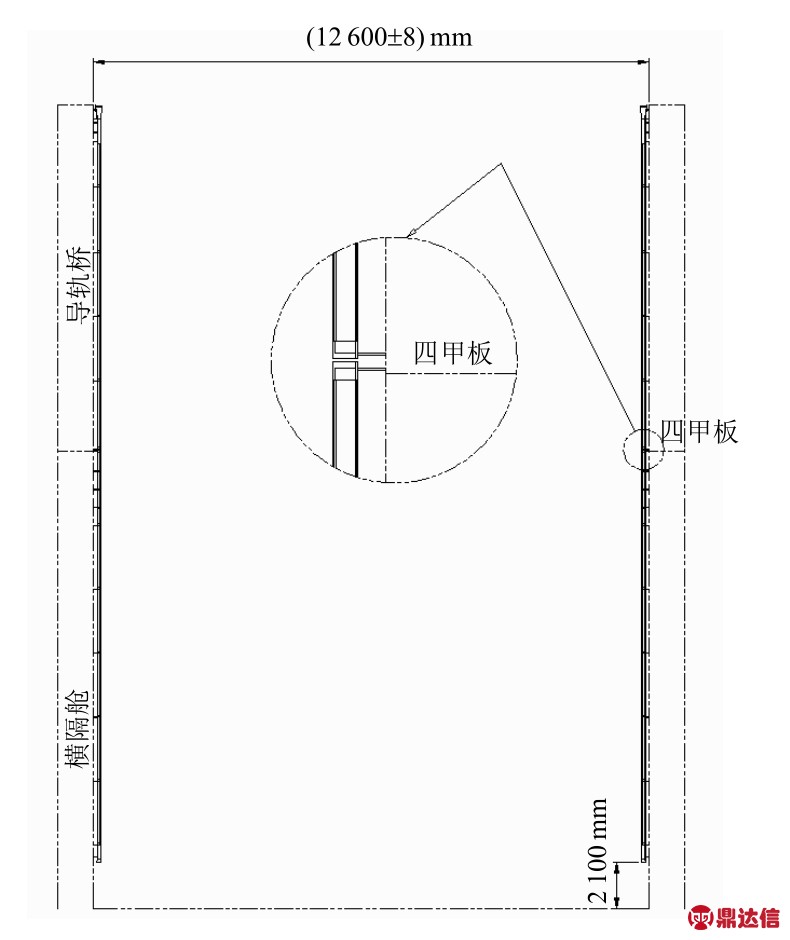
图1 导轨架布置

图2 45000t集滚船导轨桥结构
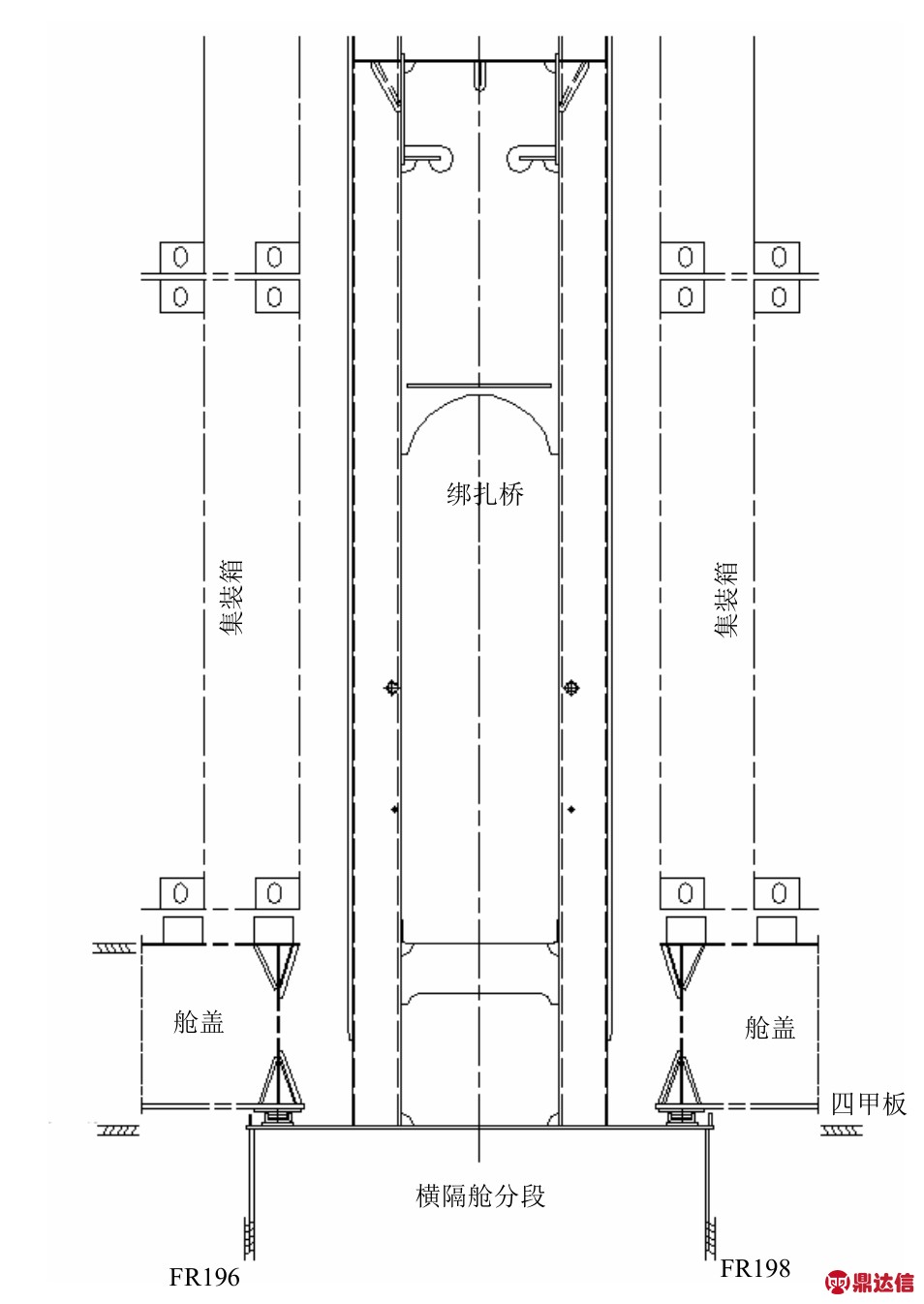
图3 传统集装箱船绑扎桥
该型船的导轨架的设计理念是集装箱不依赖任何辅助绑扎措施。同时,由于导轨架总体长度较长,连续延伸出货舱,而横隔舱区域分段不可能作为一个分段制造,尤其是该船导轨桥结构是横隔舱的延伸结构,这对货舱内的横舱壁及上侧分段搭载总组的精度都提出了较高的要求,不仅单根导轨架制作及安装要保证直线度,而且上下导轨架连接处也必须在允许的公差范围内(单根导轨架直线度±2mm,双拼导轨架直线度±2mm,导头扭曲度±1mm,相邻 2根导轨架水平度±2mm)。因此,必须要求整根导轨架同胎架制作、同批次导轨架同场地制作,且要求整根连续安装,根据导轨桥结构搭载情况适时调整导轨架背面连接肘板的尺寸,以保证导轨架精度在公差允许范围内,从而达到预期技术指标要求[1-2]。图4为导轨架精度控制示意。
连续超高导轨架的背面加强较多。该型船的导轨架肘板是参考麦基嘉(MCG)的要求设计,但根据现场施工反馈并结合传统集装箱船导轨架设计方案,对肘板加强进行了完善。同时,考虑目前空舱质量,对导轨架肘板进行适当的移位调整,并尽量与横隔舱和导轨桥结构现有的加强筋板对接,减少额外加强。此外,还取消及优化部分肘板和肘板背面对应的加强,并对货舱内角隅处肘板也适当移位,避让应力集中区域的结构加强(见图5)。
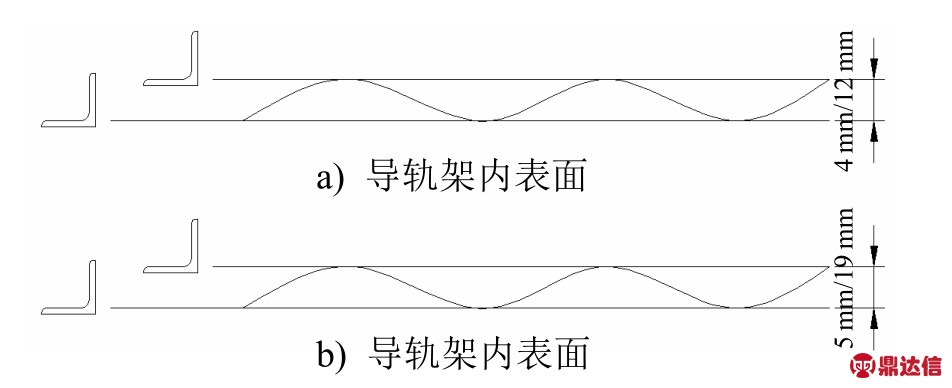
图4 导轨架精度控制示意
2 创新型挡雨盖
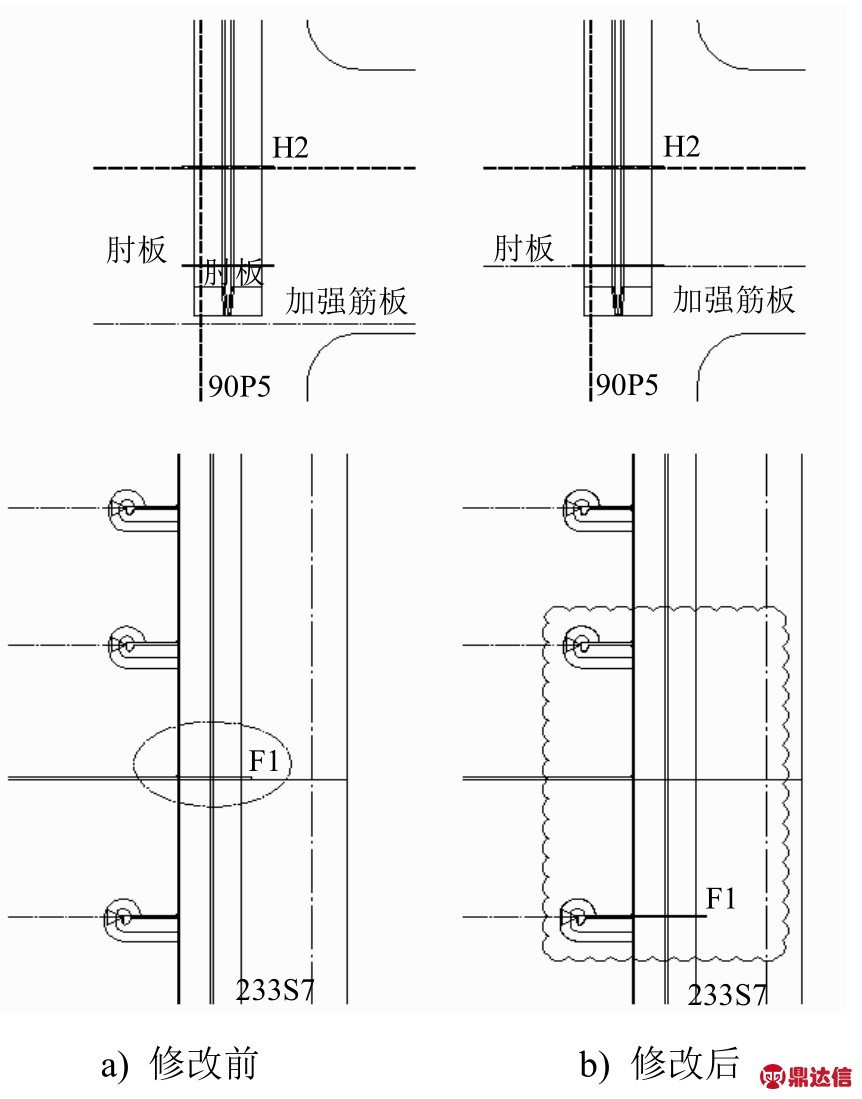
图5 导轨架肘板修改
45000t集滚船货舱区域是大开口、无舱盖形式。为防止大量雨水入舱,首次设计吊离式、非闭合开敞式、轻质、非水密挡雨盖,其尺寸参考 40英尺(1英尺=0.3048m)集装箱,同样依托于导轨架导向进行吊放(见图6)。各个挡雨盖之间相互独立,并可互换以实现无序吊装。全船共计99块挡雨盖,放置于主甲板以下的货舱围壁上,由安装在横舱壁上的角钢支撑。每个挡雨盖由4块微压缩量橡胶垫块与结构支撑连接。不同于传统的集装箱船舱盖承重在主甲板以上的舱口围结构。该挡雨盖覆盖整个货舱开口,且为集装箱跨箱位、混合堆装,因此必须依顺序放置。
该型船的挡雨盖采用开式结构,一方面出于自重考虑,使其轻质、简便;另一方面方便挡雨盖自身强度设计,并保证施工便利和安装精度控制。挡雨盖强度设计是基于堆叠7层40英尺集装箱,承重210t(每个40英尺集装箱计30t)。该挡雨盖设计除了起到防止雨水大面积落入货舱的作用之外,还出于堆重考虑,避免货舱底部过度承重对结构造成破损,以承受堆装在四甲板以上的至多7层40英尺集装箱[3-4]。
挡雨盖本身存在一定的拱度,相邻挡雨盖之间采用弹性橡胶搭接(见图7),横舱壁上的角钢支撑结构同时兼做流水槽(见图8),与纵舱壁上的角钢流水槽构成一体,把落在挡雨盖上的雨水导流至落水管并集中排放舷外,从而起到一定的防雨水作用。
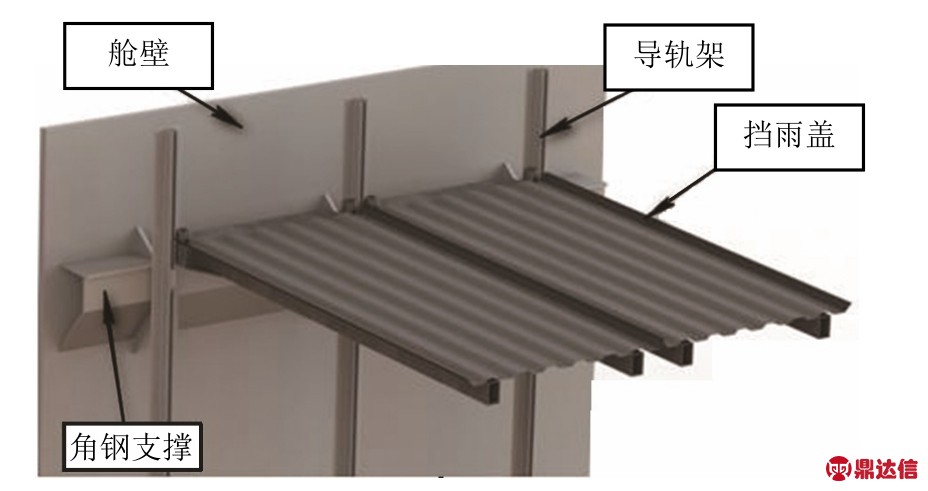
图6 挡雨盖简化模型

图7 相邻挡雨盖安装形式
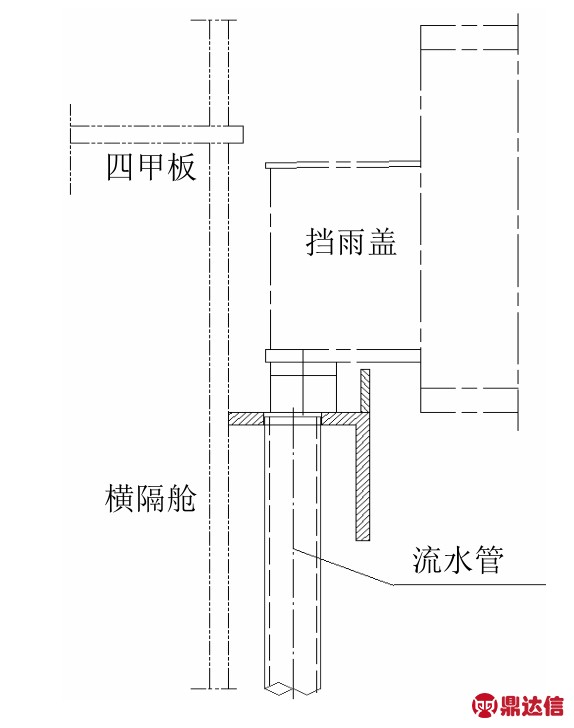
图8 挡雨盖流水槽
挡雨盖以上堆放的集装箱只能为40英尺集装箱,在挡雨盖本体结构上设置有8个埋入式箱脚,均为嵌入式安装,挡雨盖一旦制作完成,箱脚不能进行调整或修改,挡雨盖的堆放及吊运都是借助该箱脚完成。因此,不但要控制挡雨盖结构本身的制作误差,还必须考虑集装箱箱脚的安装精度[5],通过胎架固定,同时制作过程需进行适时监控,并在完成后进行完工测量和矫正(见图9)。而传统集装箱船舱盖上用于堆放和吊放的箱脚为突出形式,可实现混合堆装,还可根据吊箱试验进行调整或修改,因此对安装精度控制要求较低。集装箱箱脚的精度要求见图10。
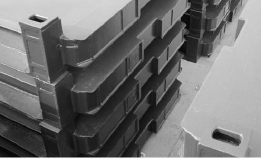
图9 挡雨盖
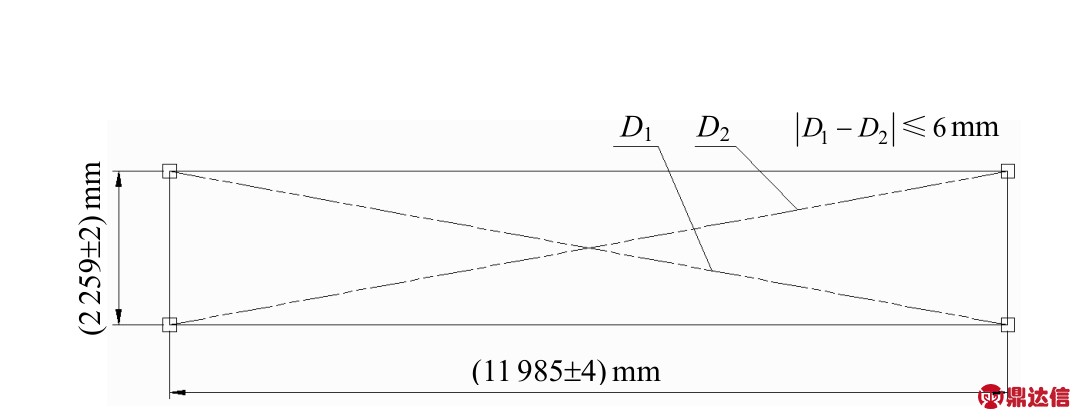
图10 集装箱箱脚的精度要求
挡雨盖支撑本体结构平面与挡雨盖弹性垫块之间有严格的水平度及角度公差要求,以防止挡雨盖上方堆放集装箱时引起高层集装箱向左侧或右侧倾斜。因为该船是无绑扎形式,一旦倾斜角度过大,就会使导轨架及集装箱本身损坏或脱落。在货舱宽度为33m的情况下,要达到设计预期的水平度,生产施工极难保证,因此,考虑在挡雨盖支撑安装后进行调平。由于挡雨盖为互换、无序且独立分体形式设计,相邻挡雨盖之间除了橡胶搭接接触之外无任何紧密度要求,因此可通过在挡雨盖支撑上放置调节垫块来调整单块挡雨盖的水平度,同时控制相邻挡雨盖之间的高度差。图11为挡雨盖水平度要求。
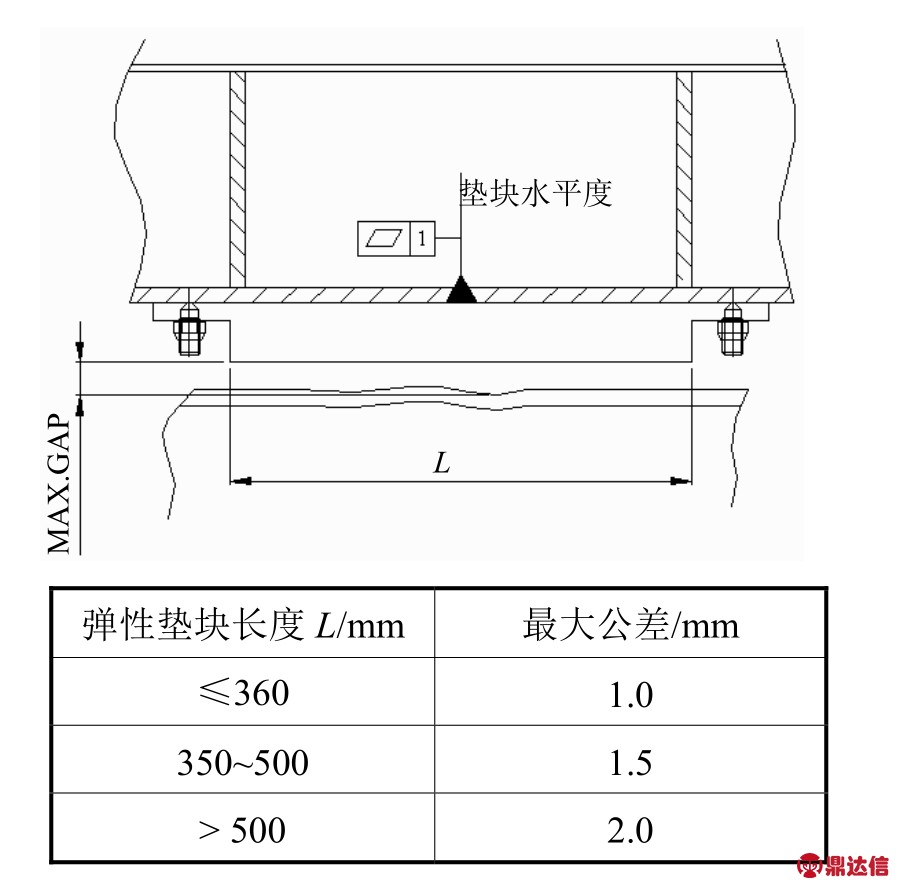
图11 挡雨盖水平度要求
此外,横跨整个货舱的挡雨盖支撑结构位于四甲板以下,安装位置较高,整体安装比较困难。根据分段划分和实际生产制作因素,每个横隔舱上的角钢支撑被人为地分割成几个部件,部件的断开位置尽最大可能避免在同一块挡雨盖的跨度范围内,以利于保证同一块挡雨盖的水平度。同时,为保证总组后各个部件之间的精度,每个部件都有一定的工作余量,并在端头保留50mm不焊,便于2个部件平顺衔接(见图12)。特别需要注意的是,四甲板理论线位置在船中部和两舷侧是不能以同一板厚信息作为参考的,而挡雨盖角钢支撑的定位是以甲板理论线为参照向下313mm安装的,因此在分段预装及总组时就必须考虑到四甲板的板厚变化。
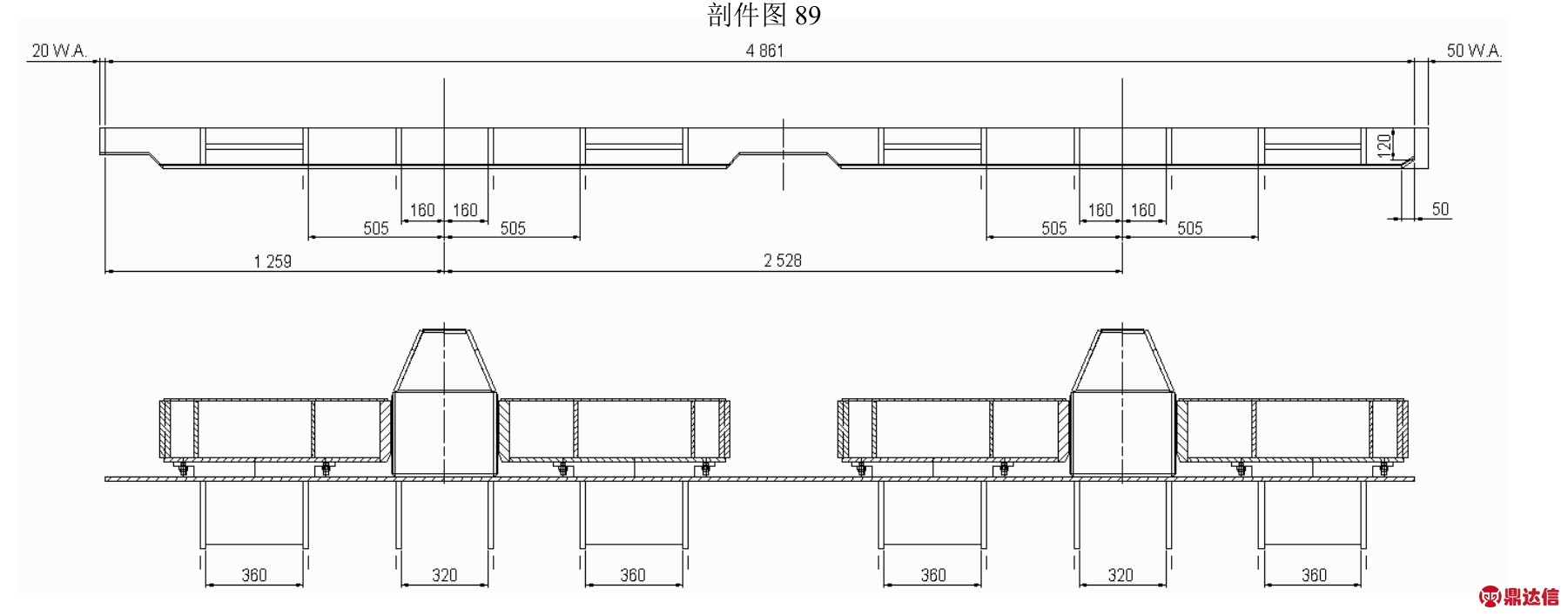
图12 挡雨盖支撑结构部件图(mm)
3 连续、超高导轨架与挡雨盖配合设计
该型船的连续超高导轨架与挡雨盖及挡雨盖的支撑结构是整体设计、相互紧密配合,不同于传统集装箱船的相互独立形式(见图13)。导轨架背面理论距离舱壁170mm,挡雨盖支撑结构最大宽度为150mm,支撑结构安装于导轨架背面以内,防止集装箱吊驳时产生碰撞,理论上两者之间的距离为20mm。然而,该设计用于生产实际施工时20mm间隙极难得到保证,同时受搭载精度和分段制作精度等因素影响,货舱的理论宽度也有偏差,因此20mm间隙要求对现场施工极其不利,同时对货舱的舱容也提出更高的精度要求。
为便于控制施工精度及避免碰撞,允许在货舱净尺度负公差情况下对支撑结构做适当修割,以减少其宽度。同时,对支撑结构与导轨架配合处采取挖槽型结构以增大配合间隙,见图14。
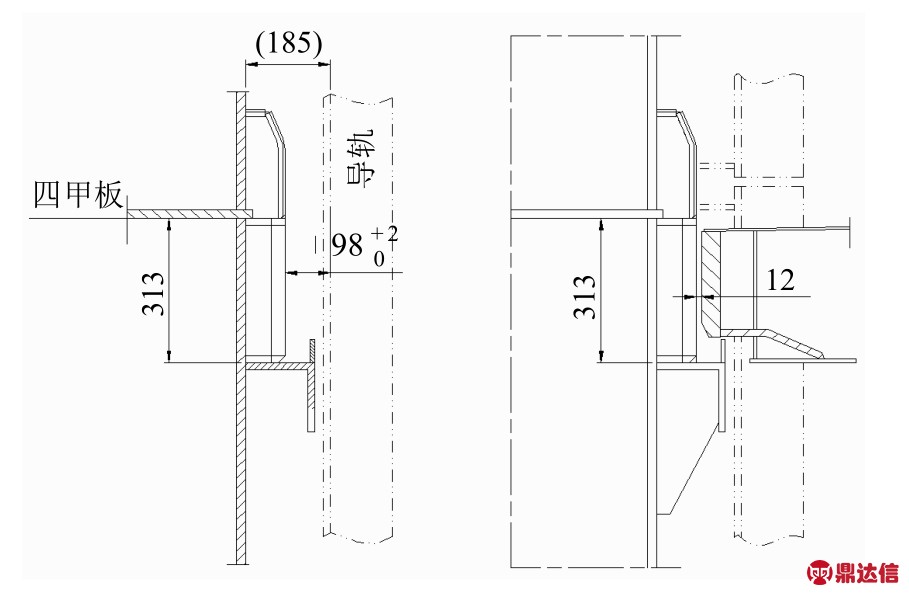
图13 导轨架与挡雨盖支撑结构(mm)
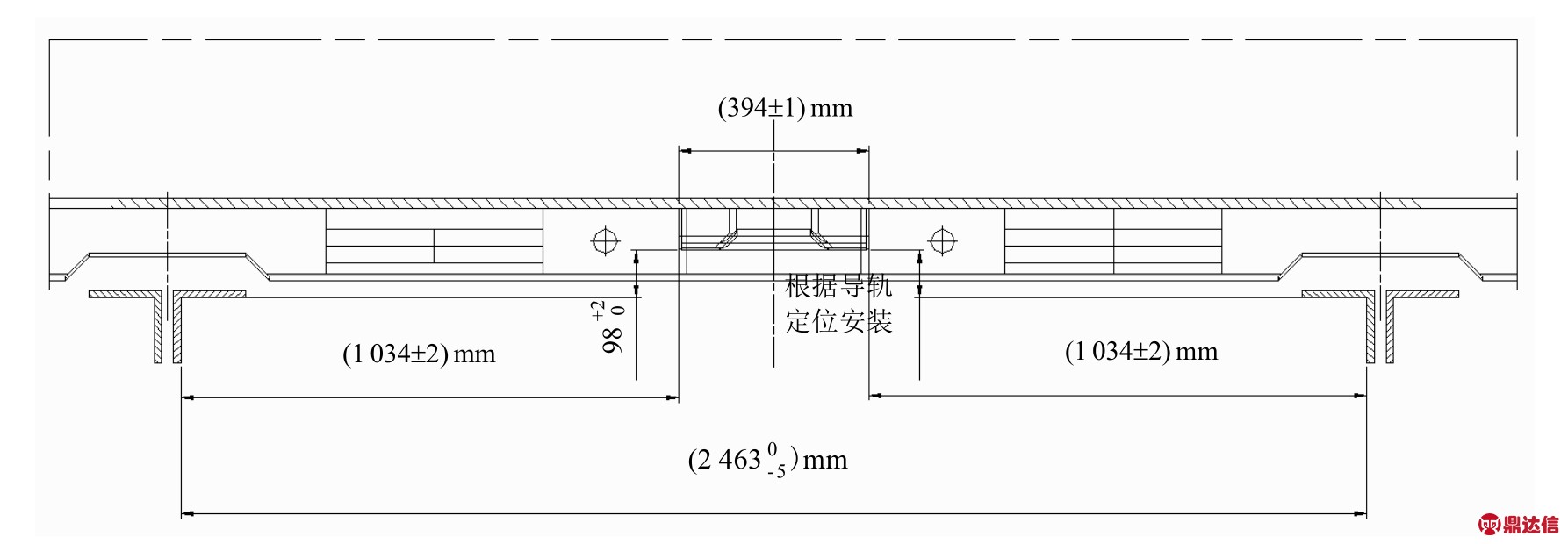
图14 挡雨盖支撑结构挖槽
4 结 语
45000t集滚船无舱盖、无绑扎,以及连续、超长、超高导轨架设计有别于传统集装箱船。该特色正是该型船设计及安装、制造的难点和挑战,是设计思维、安装制作工艺及船舶搭载控制的优化和提升。通过对无舱盖、无绑扎、连续、超长、超高集装箱系统的安装设计,并将其与传统集装箱船进行技术对比和总结,可为同型船舶提供借鉴参考。