摘 要:针对超大直径、超高载荷环形导轨低频淬火工艺技术展开研究,根据零件结构特点及技术要求,分析了工艺技术难点,提出了一系列参数和工艺技术假设,在相关试验的基础上,获得了超大直径、超高载荷环形导轨低频的淬火工艺参数。
关键词:超大直径;超高载荷;环形导轨;低频淬火
武汉重型机床集团有限公司承接的某国防重点装备上的关键零件——环形导轨,主要起回转与支承作用,要求其有足够的刚度和精度保持性。导轨面上有车体滚动,车体承重约1 400 t,这就要求导轨面具有非常高的强度和耐磨性。
该项目为国家重点项目,由于技术保密性,国内外没有相关资料可以借鉴。为了确保项目的顺利进行,本文从材料特性分析、零件技术要求、工艺特性分析、热处理工艺参数、淬火感应器的制造、淬火裂纹的控制以及淬火变形校正等几个方面展开研究,并进行了相关试验,得出了合理的热处理工艺参数。
1 40CrNiMoA材料特性分析
在40CrNiMoA超高强度钢中,w(C)=0.36%~0.44%、w(Cr)=0.6%~0.9%、w(Ni)=1.25%~1.75%、w(Mo)=0.15%~0.25%,其经热处理后具有优良的综合力学性能。铬和镍等合金元素的加入使其淬透性较好,并使铁素体的强度和韧度得到提高;钼和铬等碳化物形成元素的加入,可阻止奥氏体晶粒度长大,提高钢的回火稳定性,在使用中有一定的冲击性和断裂韧度,以及高的疲劳强度,可满足环形导轨对材质的要求[1]。
2 环形导轨的零件结构及技术要求
环形导轨材质为40CrNiMoA,毛坯为锻件,外形尺寸如图1所示。环形导轨可等分为10段,单件质量约为4 200 kg,单段长度近5 200 mm。其技术要求为导轨经过调质处理,硬度达到32~36 HRC;导轨面经过表面淬火处理,硬度达到48~52 HRC,淬硬层深度>10 mm,淬火变形<1.5 mm,淬火面不允许存在任何形式裂纹。
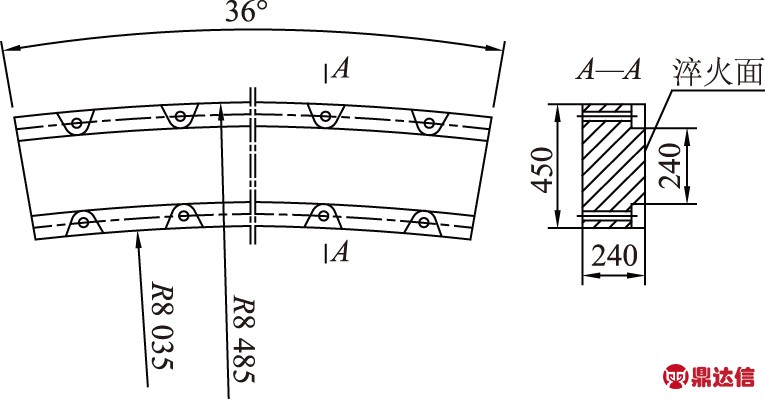
图1 环形导轨零件示意图
3 工艺特性分析
根据零件的结构特点及技术要求分析认为,该环形导轨表面淬火的主要难点如下。
1)很难达到设计要求的硬化层深度(>10 mm)。常规感应淬火一般硬化层深度为3~5 mm,资料数据表明,40CrNiMoA感应淬火最大硬化层深度一般为8 mm。另外,导轨为弧形,弦长5 200 mm,弦高700 mm,要求淬火变压器能两轴联动或者淬火机床回转直径达到16 000 mm,对淬火设备要求较高,在国内多次寻找专业热处理厂家均表示无法满足要求。
2)很难达到设计要求的淬火变形(<1.5 mm)。淬硬层越深,淬火变形越大,变形超差后采用传统的机械校正法几乎难以校平。
3)40CrNiMoA钢淬透性较好,表面淬火时容易产生裂纹,对冷却介质冷却速度要求较高。
针对上述技术难点,采用技术措施如下。
1)现有卧式淬火机床电源为IGBT电源,功率为350 kW,频率为5~30 kHz,设备外形尺寸为14 m×2.5 m×2 m。通过与设备厂家的充分沟通,并进行可行性分析,认为在现有的卧式淬火机床设备的基础上,通过对电源进行局部改造,可使设备频率降到约为1 500 Hz,满足淬火设备频率要求。
2)为减小淬火变形,工艺流程上增加预备正火处理,细化晶粒,消除锻造内应力,为后续热处理作组织准备。淬火变形后,根据变形规律,采用在淬火面背面局部加热的“拉背”技术校正变形,使变形控制在1.5 mm以内。
3)为抑制淬火裂纹的产生,导轨面的边角必须倒钝,同时淬火前增加预热处理,以减少在感应加热过程中因工件截面较大、内部吸热较快而造成的热量损失,便于快速加热。预热可提高热应力,降低淬火冷却过程中开裂的风险。
4 环形导轨热处理工艺
环形导轨工艺流程为:锻造→正火→粗铣→超声波探伤→调质→半精铣→表面淬火→着色探伤→精铣→入库。
4.1 正火处理
大型锻件常常存在成分与组织不均匀、晶粒粗大等缺陷,锻后进行正火处理,可达到细化晶粒,消除内应力,改善钢的切削加工性能,消除由于截面尺寸不同在结晶过程中产生的显微组织的不均匀性,为后序表面淬火作组织准备的目的。为降低正火后的硬度和消除内应力,得到良好的机械加工性,还应进行附加回火。具体工艺曲线如图2所示。
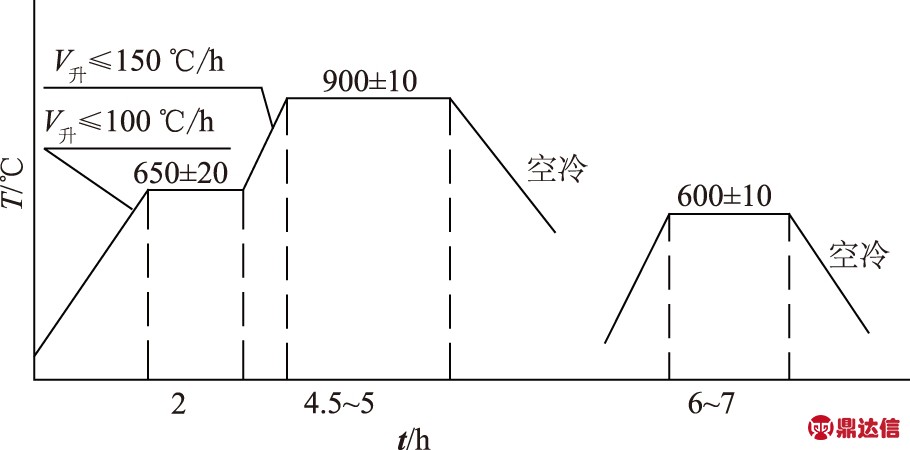
图2 正火处理工艺曲线
4.2 调质处理
在环形导轨粗铣并超声波探伤后进行调质处理,工艺类似正火处理,工艺曲线如图3所示。为了得到更大的淬硬层深度,淬火冷却介质采用体积比为8%浓度的PAG合成淬火液。通过淬火和高温回火处理后,表层硬度达到32~36 HRC,满足设计要求。

图3 调质处理工艺曲线
4.3 表面淬火工艺参数
4.3.1 设备频率的选择
为保证工件表面淬火硬化层的深度,电流的透入深度Δ热应大于所要求的淬硬层深度δ。经验表明,δ≥Δ热/4,而以δ=Δ热/2为最佳。由Δ热可知[2],理想的频率为1 200~1500 Hz。经过电源局部改造,即更换低频电容和变压器,可使卧式淬火机床电源频率达到1 400~1 500 Hz,满足淬火设备频率要求。
4.3.2 感应器设计及导磁体的选择
根据环形导轨淬火面形状,感应器设计成仿形平面淬火感应器,即2根铜管加热,其中一根铜管上带喷水孔,实现边加热边冷却的连续淬火方式。首先,将φ16 mm紫铜管用拉方工装制成截面14 mm×11 mm的方铜管,然后进行弯形、开孔,最后与紫铜板焊接而成。
为提高加热效率,采用导磁体减少磁力线的逸散,它是平面与内孔感应加热不可缺少的附件。此外,导磁体可进一步强化外表面加热和局部加热,改善复杂形状工件加热区的磁场分布,以获得均匀的温度分布[3]。根据导磁体的驱流作用,将其装卡在铜管上。导磁体的材料通常有铁氧体、硅钢片和矽钢片,试验证明,中、高频导磁体对电源振荡波形图有较大干扰,使加热状态极其不稳定;因此,在低频率淬火时应使用低频矽钢片导磁体,且以厚度≤0.2 mm为佳。
淬火感应器上钻有与底面成45°、φ1.5 mm的斜孔,孔间距以3 mm为宜。为防止淬火液倒流,影响加热效果,除喷水孔与淬火面呈一定角度外,还应在感应器前方增加空气吹扫装置,以及时带走回流飞溅的冷却液。
4.3.3 淬火温度的选择
由于感应加热速度快,奥氏体转变在较高温度下进行,在一定的加热速度范围内,临界点随加热速度的增加而提高;另由于感应加热一般不进行保温,为了在加热过程中能使先共析铁素体(亚共析钢)等游离的第2项充分溶解,要求感应加热表面淬火温度采用较高的加热温度。一般感应淬火温度比普通淬火温度高30~200 ℃[4]。40CrNiMoA奥氏体化温度为835 ℃,普通淬火温度为860~880 ℃,感应淬火温度初步选为880~900 ℃。试验证明,采用偏下限的淬火温度时,淬火硬化层深度只有6.5~7 mm;而采用偏上限的淬火温度,虽然淬火硬化层深度可以达到10 mm以上,但淬火面两边易出现淬火裂纹。
4.3.4 淬火速度及工件与感应器之间的间隙选择
中、高频连续淬火速度一般以3~5 mm/s为宜,而对于低频连续淬火,为了得到更深的淬硬层,在保证表面不过热条件下,可采用降低比功率,延长加热时间,增加工件与感应器的间隙,以及预热处理等工艺方法。试验表明,在淬火温度保持不变的前提下,当淬火速度为1.5~2 mm/s时,淬硬层深度达到10.5 mm;当淬火速度为3 mm/s时,淬硬层深度为8.5 mm。试验中发现,在低频淬火时,感应器与工件之间的间隙较常规中、高频淬火的间隙大,这是因为低频淬火时,产生的磁场更强,感应器与工件之间会产生较大的吸引力,可能会导致感应器与工件接触而烧伤工件表面;但感应器与工件之间的间隙也不能太大,否则会减小涡流的透入深度,从而影响淬火硬化层深度。试验证明,工件与感应器的间隙取6~7 mm较为合适。
4.3.5 冷却介质的选择
感应淬火的冷却速度和冷却均匀性是十分重要的参数,如果淬火冷却介质的冷却性能不良或冷却方式不佳,均有可能造成淬火裂纹或其他缺陷,而40CrNiMoA属于低合金高强度高,淬透性较好,资料显示,该钢水淬时最大淬透直径可到100 mm,但水淬时容易产生裂纹。冷却速度太快和淬火冷却不均匀均易引起不同程度的裂纹。试验证明,当淬火水温为30 ℃喷水冷却时,在环形导轨边角处容易出现不同程度的淬火裂纹。通过磨削后着色探伤检测可知,裂纹深度≤0.5 mm。淬火喷射压力越大,淬火裂纹数量越多,这是因为随着喷射压力的提高,喷出的水柱越强劲,冷却的均匀性越差,淬火裂纹自然也越多[5]。实践证明,采用体积比为0.1%~4%浓度的PAG合成淬火液喷冷时,对抑制裂纹效果不明显;当浓度>4%时,虽能有效抑制裂纹的产生,但浓度提高后冷却能力下降,淬火硬化层深度也随之下降。在把淬火硬化层深度作为首要满足要求的前提下,通过对比试验,结果表明,选择喷水冷却,控制喷射水压在0.15~0.2 MPa,同时淬火前进行预备热处理,能大幅抑制淬火裂纹的产生。
4.4 淬火变形校正方法
尽管采取了多种减小淬火变形的方法,但是淬火变形仍不可避免,且淬硬层越深,变形越大。环形导轨表面淬火变形规律为淬火面中部凸起,两端下凹,通过多次试验,测出淬火面中部凸起最大值为7.5~8 mm。由于导轨面硬度高达48 HRC以上,且淬火硬化层深度>10 mm,采用常规的冷压校直法和热校直法均难以校正。根据多年的现场实践经验,采用“拉背”技术校直法,可将变形校正在合适范围。
所谓“拉背”技术校直法,即对淬火面背面进行加热,找出工件凸起部位,以最高点为中心,两头各一段距离,以一端为起点,通过感应加热此区域,采用连续加热法加热淬火面背面,加热温度同淬火温度,以移动至另一端为终点;然后对加热部分进行激冷,使加热部位迅速收缩,以达到校正的一种方法。通过此方法进行校正,可将淬火变形控制在≤1 mm,满足加工余量要求。“拉背”技术校直法的重点在于找出合适的加热部位,控制好加热温度和感应器移动速度,加热完后进行激冷,校正后需要进行回火处理。因为工件畸变矫正的实质是通过外力作用于工件,使其产生与原变形方向相反的变形,从而相互抵消,达到矫正的目的。由于外力的作用产生相反的变形,工件内部必然产生相应的内应力,此应力也称工件的校直应力。若不对其进行消除,工件在后续的加工或使用过程中产生的应力与该应力合成,当合成应力超过工件的屈服极限时,工件就会产生塑性变形,出现新的畸变。
5 结语
40CrNiMoA大直径环形导轨低频感应淬火前应进行预备正火热处理,以达到细化晶粒,消除应力,为后续热处理作组织准备的目的;粗加工后进行调质处理,增加环形导轨整体强度;半精加工后对环形导轨面进行低频感应淬火处理,频率控制在1 400~1 500 Hz较宜,淬火温度为880~900 ℃。为了减少裂纹的产生,低频淬火前应进行350 ℃保温4 h的预备热处理,喷水压力控制在0.15~0.2 MPa。淬火变形后,可通过“拉背”技术校直法将淬火变形校正在合适的工艺留量范围内,以满足后续加工要求。