摘 要: 某化工厂焦化装置V401顶安全阀启跳后不回座,安全阀解体后发现其弹簧发生断裂。采用化学成分分析、硬度检测、组织和断口形貌观察、腐蚀产物分析等方法分析了安全阀弹簧的断裂原因。结果表明:安全阀弹簧在湿H2S环境中发生应力腐蚀形成裂纹,裂纹在交变载荷作用下扩展;当弹簧有效横截面积不足以承受介质内压的波动作用时弹簧发生断裂,属于腐蚀疲劳断裂。
关键词: H2S;50CrVA弹簧钢;应力腐蚀;疲劳断裂
0 引 言
2016年11月某炼油厂一联合车间焦化装置V401顶南侧安全阀启跳,启跳后不回座,解体后发现阀内弹簧已经断裂。考虑同期同工艺的北侧安全阀也可能出现该问题,故对其也进行解体,解体后发现北侧安全阀弹簧也已经断裂。两侧安全阀均由北京航天技术设备有限公司生产,型号为HTO-01CB,类型为弹簧式,公称压力为2.0 MPa,公称通径为80 mm,出厂日期为2007年3月1日,投用日期为2009年8月1日。冷态整定压力为1.19 MPa,法兰进口规格为DN80,出口规格为DN100,设计温度为80 ℃,使用温度为40 ℃,设计压力为1.38 MPa,最高操作压力为1.20 MPa,介质为油气,要求整定压力为1.24 MPa,背压为0.05 MPa。为了找到该安全阀弹簧的断裂原因,作者对北侧安全阀弹簧进行了失效分析。
1 理化检验及结果
1.1 宏观形貌
北侧安全阀弹簧为圆形截面右螺旋式压缩弹簧,中径D(弹簧内径和外径的平均值)为72.71 mm,弹簧外圈直径D2为85.42 mm,弹簧内圈直径D1为60.00 mm,弹簧端部用于支承或固定的支承圈数n2为2,用于缠绕弹簧的钢丝直径d为12 mm,螺旋弹簧两相邻有效圈的轴向距离δ为12 mm。弹簧断裂成3段,断裂位置位于弹簧两端1~2圈的位置,3段长度分别为320,950,460 mm,如图1(a)所示。弹簧表面涂有防腐漆,外侧防腐漆覆盖完好,内侧表面有大量腐蚀产物覆盖;近断裂部位的弹簧内侧已完全被腐蚀产物覆盖,如图1(b)所示。
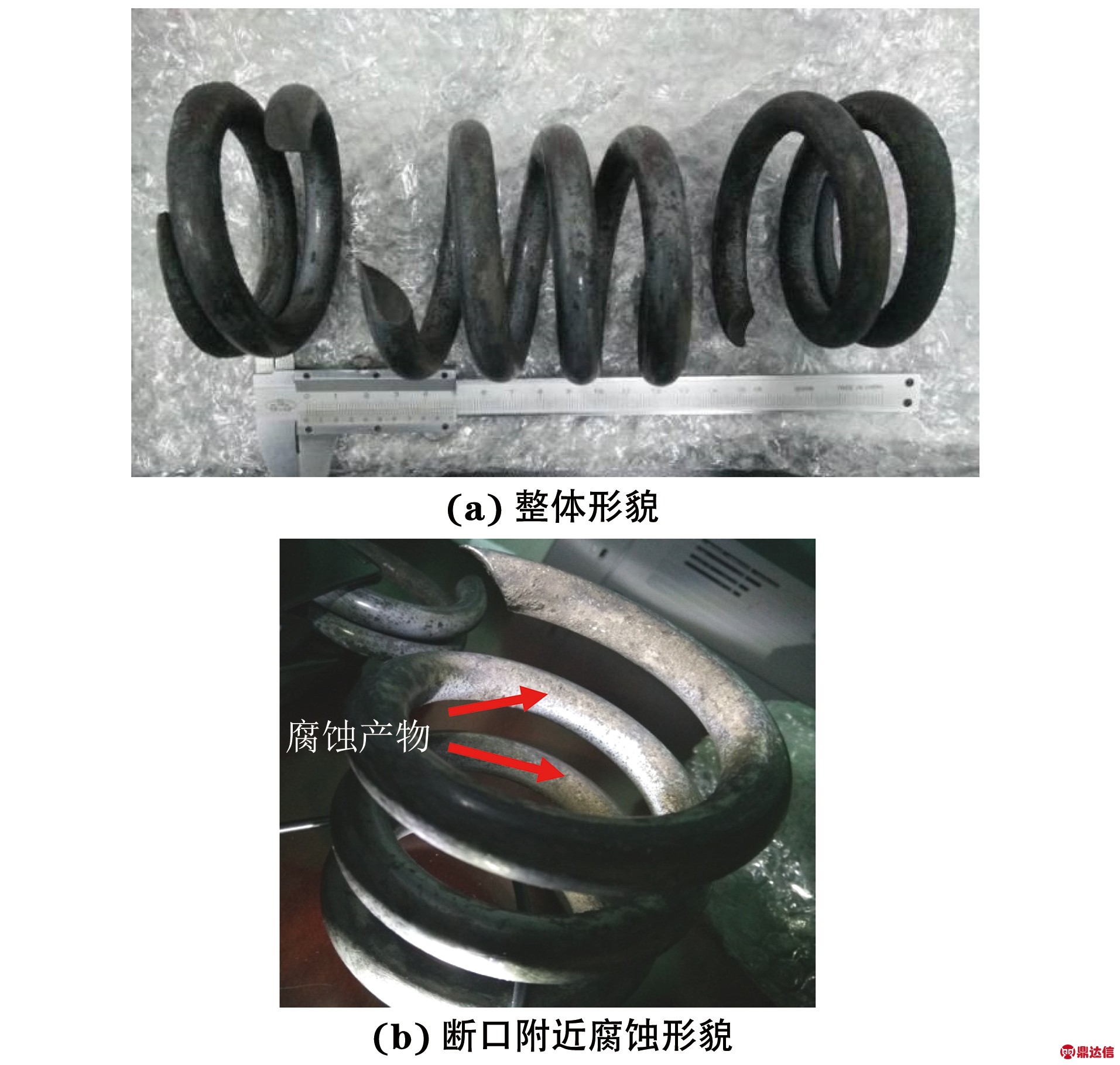
图1 断裂弹簧的宏观形貌
Fig.1 Macromorphology of broken spring: (a) overall view and (b) corrosion morphology near fracture
由图2可以看出:裂纹起裂于弹簧内侧,断口与轴线成45°夹角,表现为脆性断裂;断口可明显观察到裂纹源区、裂纹扩展区和瞬断区[1-2],裂纹源区和裂纹扩展区较平坦,瞬断区存在撕裂棱。此外,在对弹簧检查时可闻到浓重的臭鸡蛋气味。
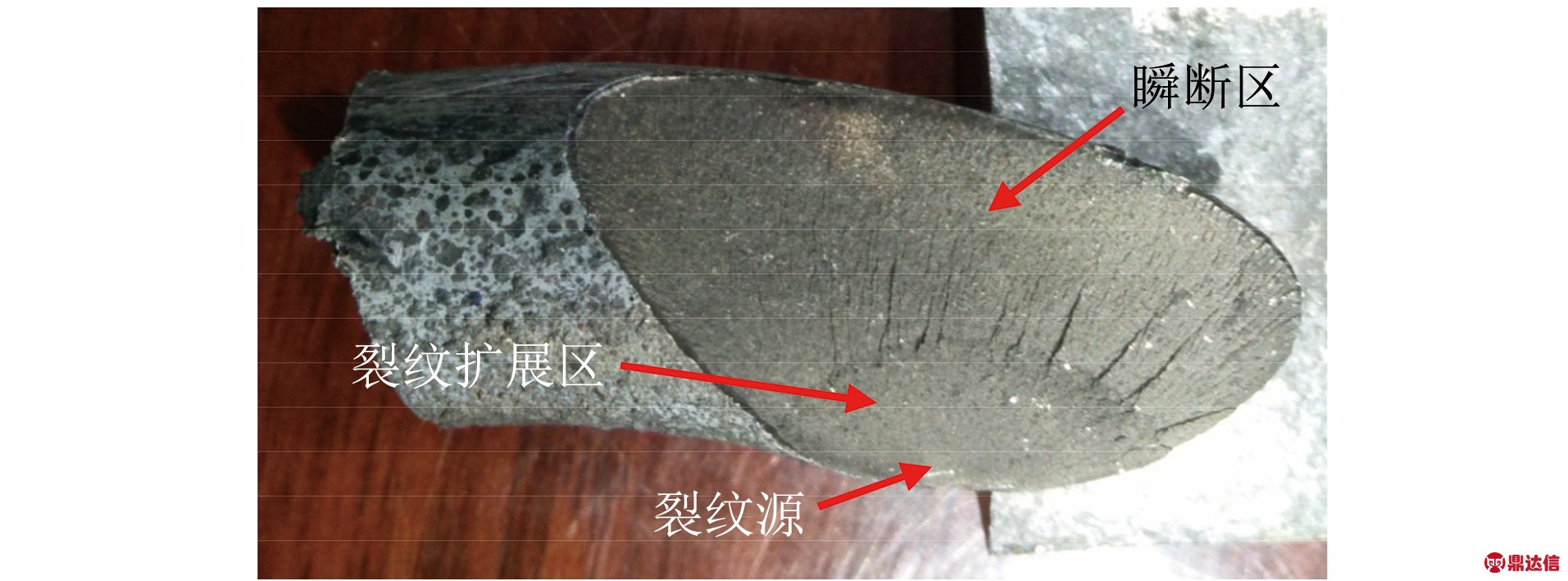
图2 弹簧断口的宏观形貌
Fig.2 Macromorphology of spring fracture surface
1.2 化学成分
在远离弹簧断口的横截面上取样,按照GB/T 4336-2016,使用SPECTRO Lab. M7型固定式直读光谱仪测定化学成分。由表1可知,该弹簧的化学成分符合GB/T 1222-2007中50CrVA弹簧钢的成分要求。
表1 断裂弹簧的化学成分(质量分数)
Table 1 Chemical composition of broken spring (mass) %
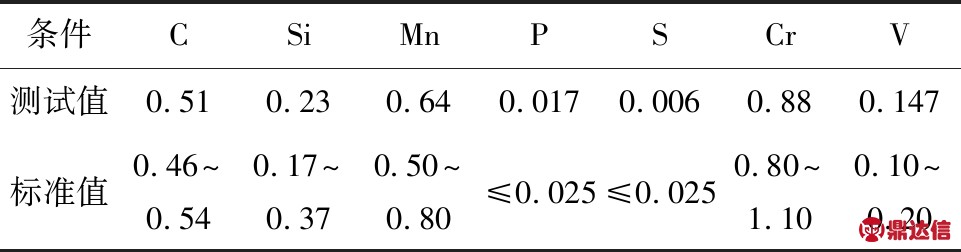
1.3 显微组织和裂纹形貌
采用线切割法在断口附近制取横向金相试样,并将一侧断口沿中心轴线切开后制取纵截面金相试样,按照GB/T 13298-2015进行研磨、抛光,用体积分数4%硝酸酒精腐蚀。使用蔡司Axio Imager A2m型光学显微镜观察抛光态试样中的夹杂物和裂纹形貌,以及腐蚀后的显微组织和裂纹形貌。由图3可知,弹簧横截面上存在条状夹杂物,其宽度为3.37 μm,长度为38.84 μm。按照GB/T 10561-2005,判定夹杂物等级为C1。
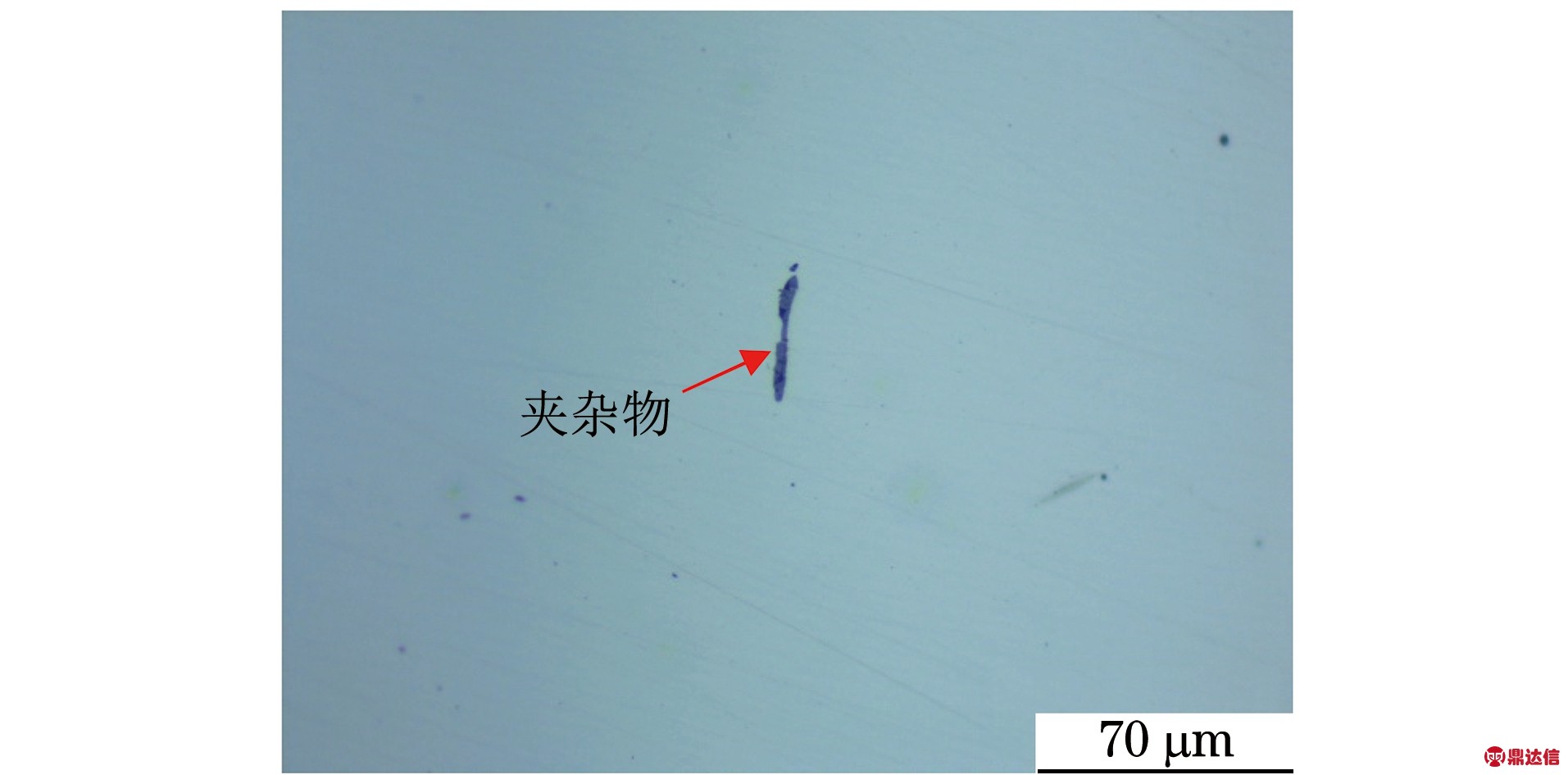
图3 断裂弹簧横截面上的夹杂物形貌(抛光态)
Fig.3 Inclusion morphology on cross section of broken spring (as-polished)
弹簧外侧表面保留的防腐层厚度在69.45~98.00 μm,如图4(a)所示;内侧表面防腐层因腐蚀而消失,弹簧基体表层发生腐蚀的区域可见连续的裂纹,长度约为352.75 μm,近表层处还存在少量球状夹杂物,如图4(b)所示。
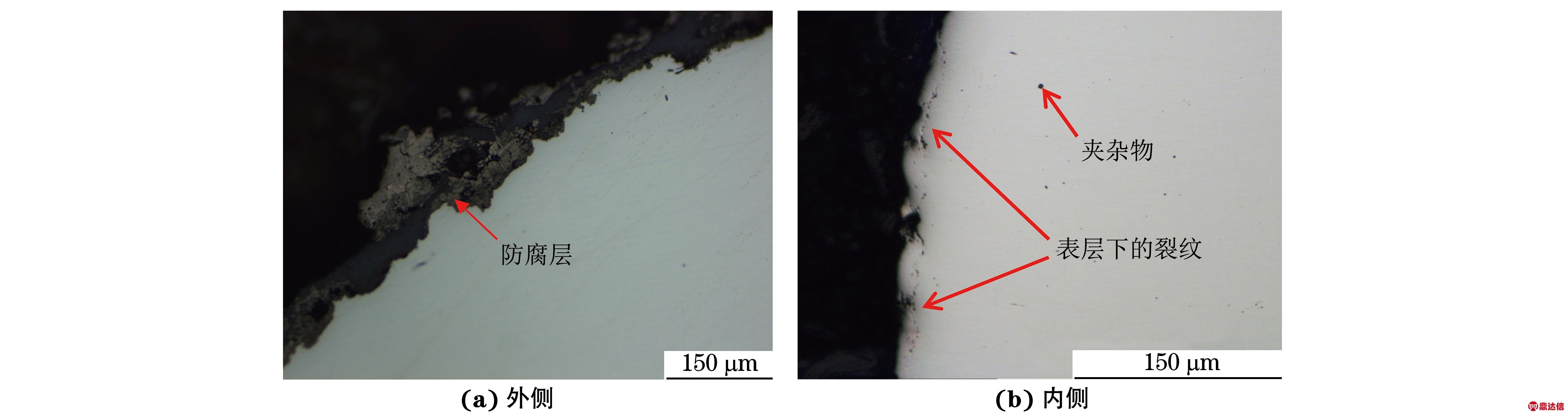
图4 断裂弹簧横截面边缘的微观形貌(抛光态)
Fig.4 Micromorphology at edge of cross section of broken spring (as-polished): (a) outer side and (b) inner side
由图5可见:断裂弹簧内侧表面存在全脱碳层,厚度约为30 μm,组织为铁素体+少量回火屈氏体;向心部延伸的半脱碳层厚度约为65 μm,组织为网状铁素体+少量回火屈氏体[3]。脱碳层中的铁素体组织应为加工时产生的。心部为保持马氏体位向的回火屈氏体+少量马氏体。根据TB/T 2478-1993中的弹簧钢显微组织评级图谱,可知断裂弹簧的马氏体组织为1级,残余铁素体为1级。
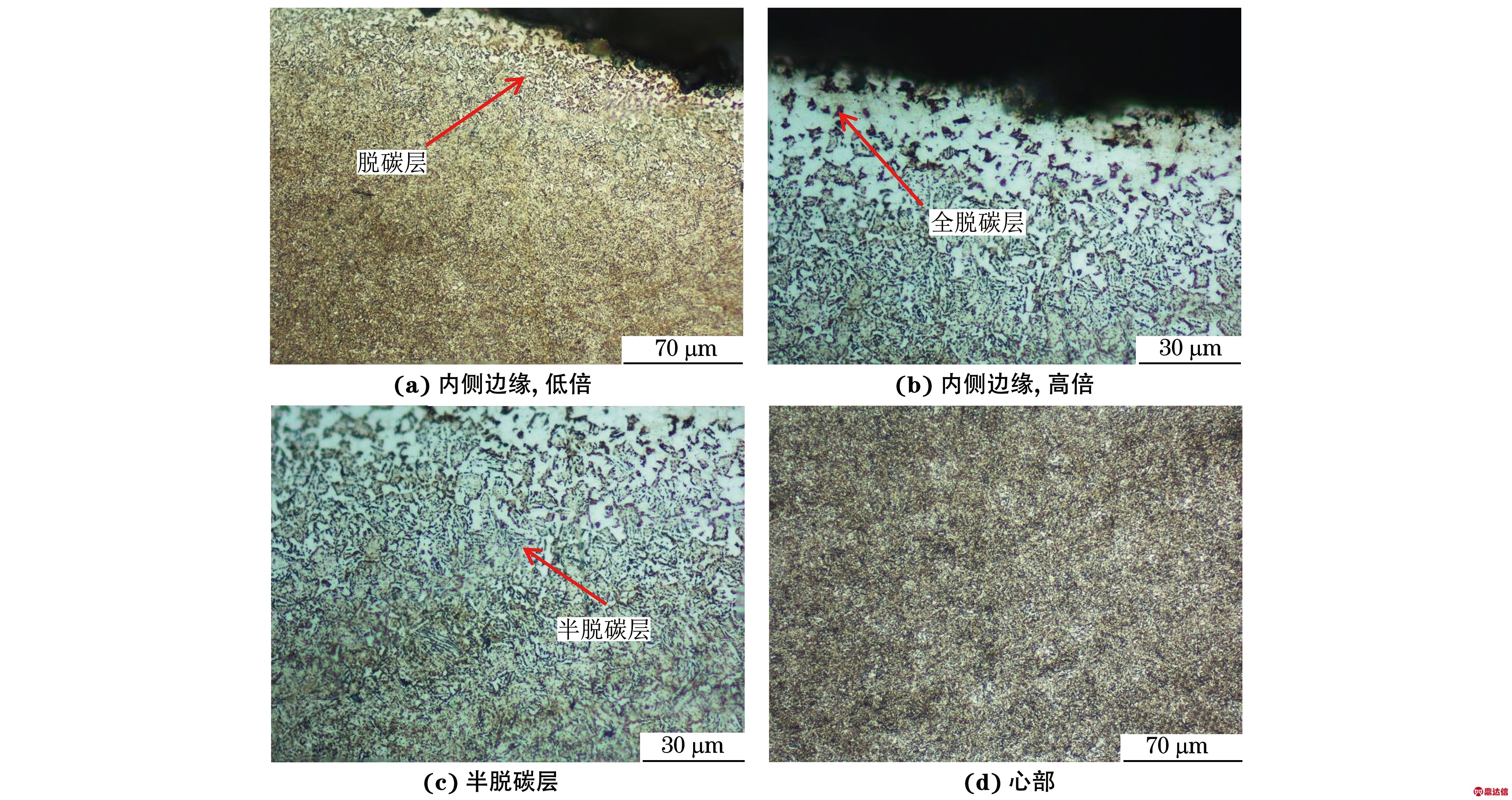
图5 断裂弹簧横截面显微组织
Fig.5 Microstructure on cross section of broken spring: (a) edge of inner side, at low magnification; (b) edge of inner side,at high magnification; (c) half decarburization layer and (d) at core
纵截面金相试样的宏观形貌如图6所示。在试样纵截面上,近断口处存在大量的二次裂纹,裂纹内充满腐蚀产物,如图7(a)所示;二次裂纹与主裂纹成一定角度,沿原奥氏体晶界扩展,如图7(b)所示;腐蚀后的纵截面上可观察到自外侧表面向内部延伸的裂纹,裂纹扩展到脱碳层边缘后停止,如图7(c)所示。
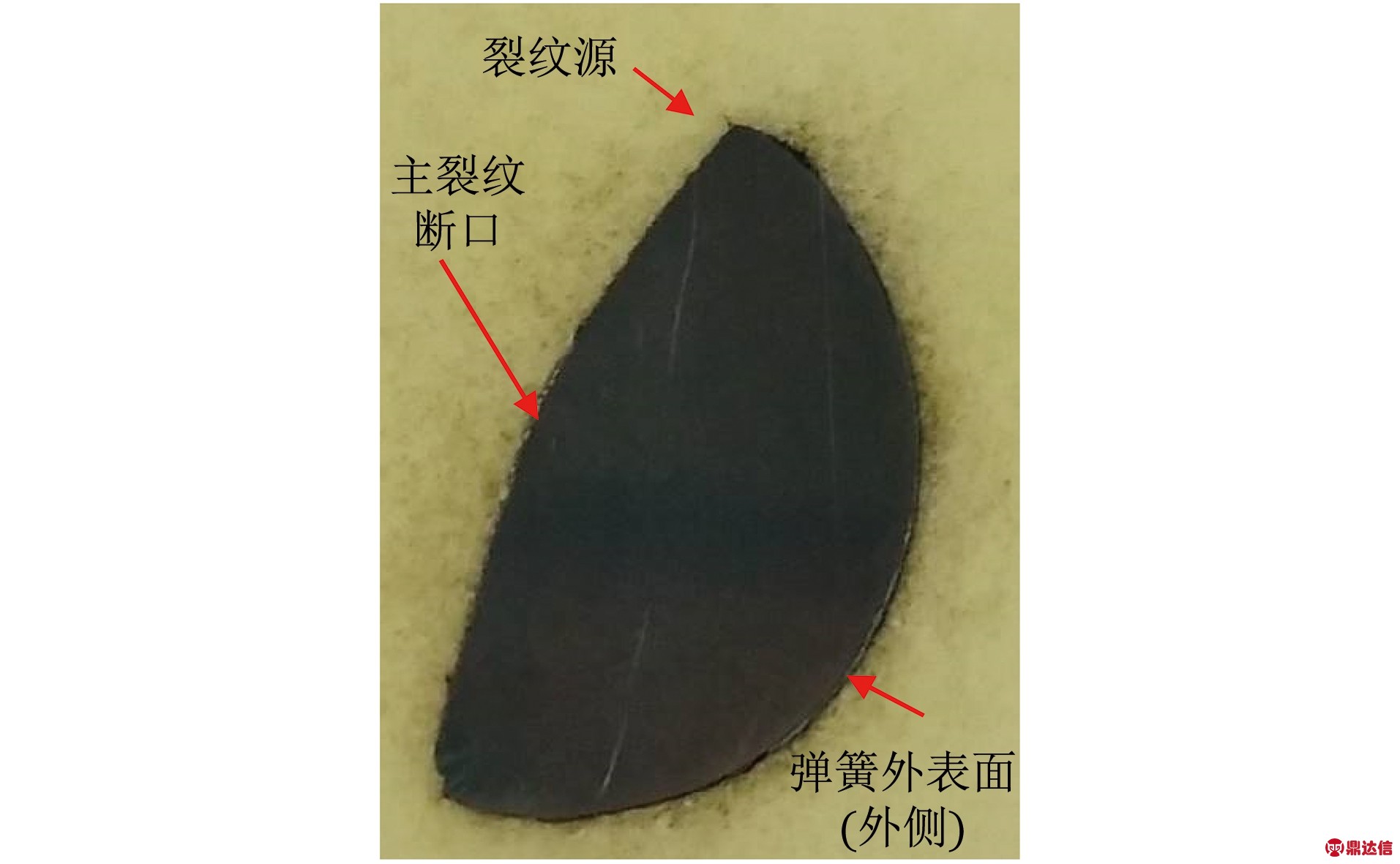
图6 纵截面金相试样的宏观形貌
Fig.6 Macromorphology of longitudinal section metallographic specimen
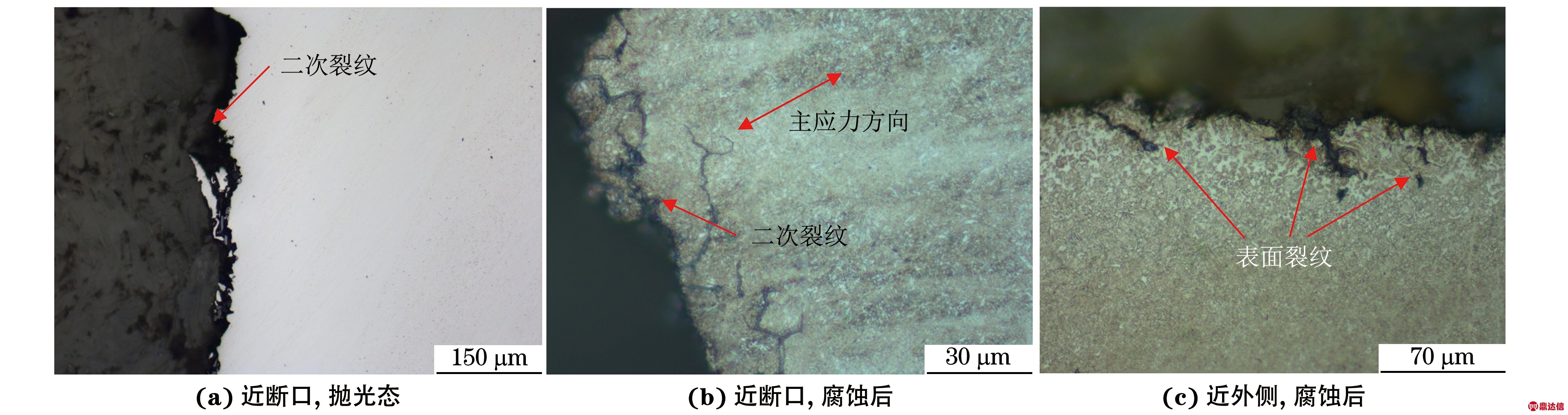
图7 断裂弹簧纵截面不同位置处的裂纹形貌
Fig.7 Crack morphology at different locations on longitudinal section of broken spring: (a) near fracture, as-polished; (b) near fracture, after corrosion and (c) near outer side, after corrosion
1.4 硬 度
按照GB/T 4340.1-2009,使用XHV-1000型全自动自转塔数显显微硬度计,在弹簧横截面上从外向内每隔0.1 mm取点进行显微维氏硬度测试,载荷9.807 N,保载时间30 s。根据GB/T 1172-1999,将检测结果转换成对应的布氏硬度。由图8可以看出,断裂弹簧表面的硬度在480 HBW左右,随着距表面距离的增大,硬度先增大至500 HBW左右再降低,心部硬度低至456.2 HBW。在GB/T 1222-2007中规定,50CrVA弹簧钢的硬度应不大于321 HBW,故可确认该弹簧硬度超标。根据GB/T 1172-1999,由硬度换算得到断裂弹簧表面的抗拉强度为1 617 MPa,心部的抗拉强度为1 517 MPa,硬度最高处的抗拉强度为1 697 MPa。
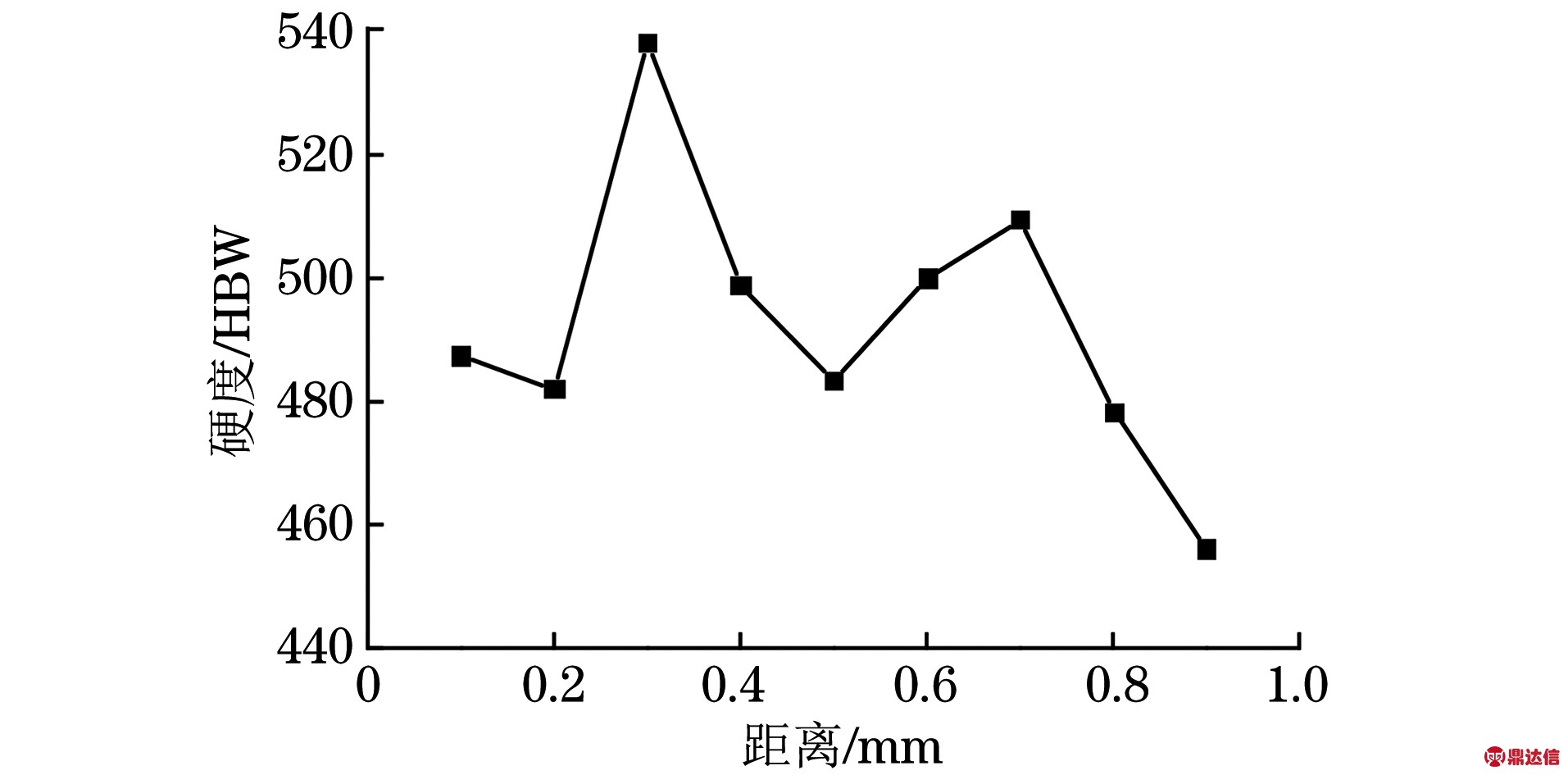
图8 断裂弹簧横截面硬度分布曲线
Fig.8 Hardness profile on cross section of broken spring
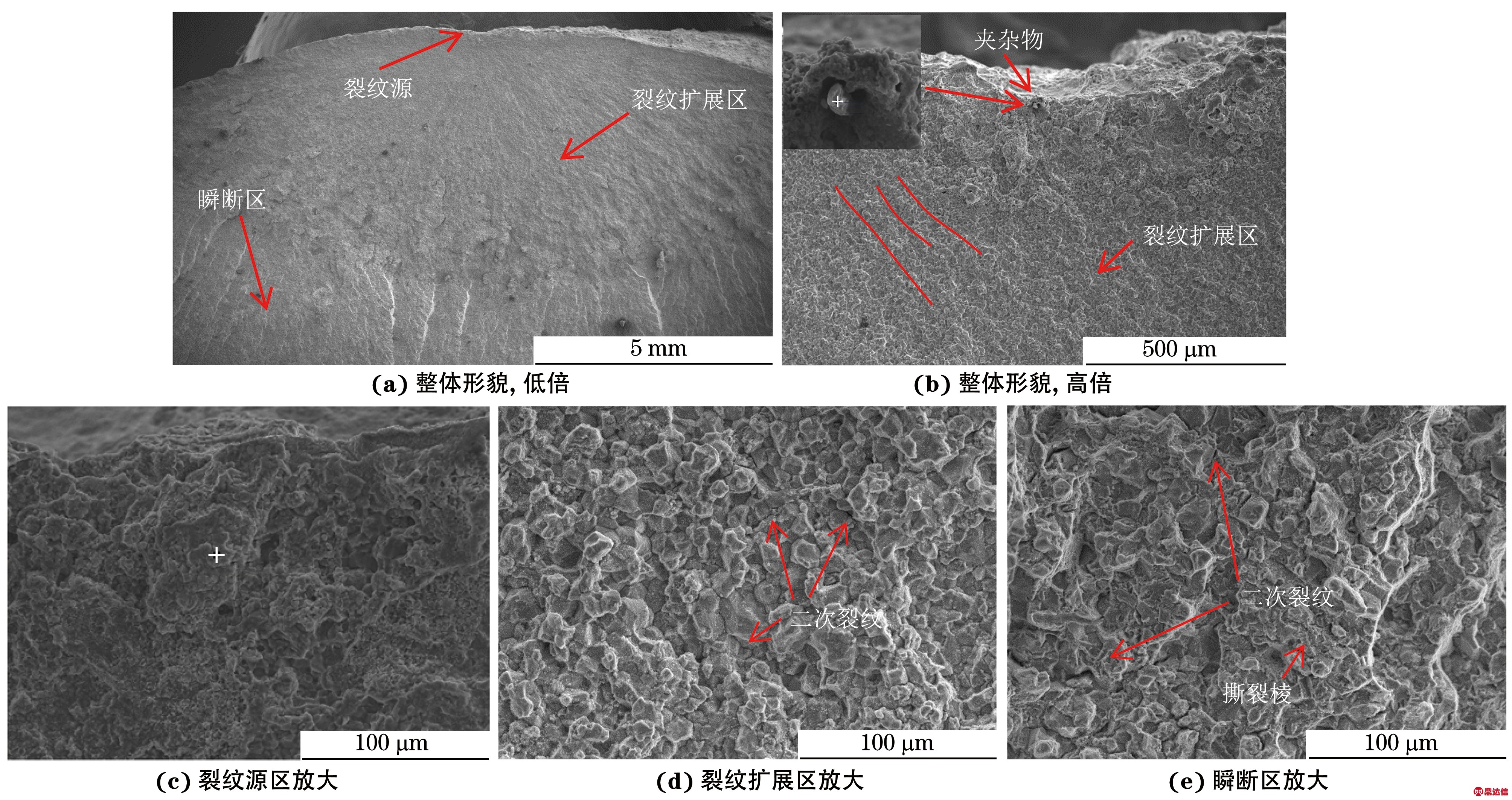
图9 断裂弹簧断口的微观形貌
Fig.9 Micromorphology of fracture of broken spring: (a) overall morphology, at low magnification; (b) overall morphology, at high magnification; (c) enlargement of crack source; (d) enlargement of crack growth zone and (e) enlargement of instantaneous fracture zone
1.5 断口形貌
使用蔡司EVO18型扫描电镜观察清洗后的断口形貌。由图9(a)可以看出:断口可分为裂纹源区、裂纹扩展区和瞬断区,与宏观检测结果一致;在裂纹源区表面有一个小的坑点。由图9(b)可以看出:坑点处存在一个明显的球状夹杂物,周围区域大多呈现腐蚀迹象;裂纹扩展区呈典型的沿晶扩展形貌,邻近裂纹源侧可以观察到与裂纹扩展方向一致的条纹(线条所示),这是疲劳裂纹扩展留下的痕迹。由图9(c)~图9(e)可以看出:裂纹源区呈疏松状,晶粒边界不清晰,腐蚀严重;裂纹扩展区的裂纹沿晶界扩展,并且存在大量的二次裂纹;瞬断区的裂纹有少量沿晶界扩展,其余为穿晶扩展,穿晶区域存在少量撕裂棱,呈现准解理断裂特征,部分区域也存在少量二次裂纹。
采用扫描电镜附带的能谱仪(EDS)对裂纹源区夹杂物进行成分分析,测试位置见图9(b),结果见表2。
表2 裂纹源区夹杂物的EDS分析结果(原子分数)
Table 2 EDS analysis result of inclusion in crack source (atom) %

由表2可知,夹杂物中的硅和氧元素含量较高,推测该夹杂物为SiO2。
在断口裂纹源区进行EDS分析,测试位置见图9(c),测得该处化学成分(原子分数/%)为39.41C,33.63S,26.97Fe。裂纹源区存在大量的硫元素,推测腐蚀是由硫化物造成的。
2 断裂原因分析
2.1 腐蚀环境
该阀门入口端介质为干气,干气压力0.9 MPa,干气中H2S的体积分数为2.4%。安全阀出口连接焦炭塔高温放空线。焦炭塔高温放空时管线内介质为火炬气,其中H2S的体积分数为1.6%,并伴随有大量水汽。阀门不开启时,部分火炬气会从安全阀出口窜入,进入安全阀腔体中,在弹簧表面形成水膜;H2S溶入水膜形成了湿H2S腐蚀环境,pH约为5[4]。放空频率基本为每天一次,这就导致了安全阀内弹簧常年处于湿H2S腐蚀环境中。H2S与弹簧钢发生反应,生成的硫化物不仅能作为析氢反应的毒化剂加速氢向金属中的渗透,而且长时间存在于膜下和点蚀坑底部,造成腐蚀介质浓缩,从而加剧了腐蚀作用。
裂纹源位于弹簧表面剪应力(表现为拉应力)最大处,此处表面被腐蚀产物完全覆盖。制造弹簧的材料为50CrVA弹簧钢,表面硬度高达480 HBW,对应抗拉强度近似为1 617 MPa,属于超高强度钢;强度越高,应力腐蚀敏感性越高[3,5]。综上可知,裂纹源区具备发生应力腐蚀开裂的3个条件:拉应力、腐蚀环境以及对腐蚀环境敏感的材料。弹簧表面被湿H2S覆盖的范围内都发生了不同程度的腐蚀开裂,裂纹由表面向内部扩展,在没有其他因素促进的情况下,裂纹扩展到脱碳层边缘后停止扩展。这些裂纹使弹簧实际受力面积减小,弹簧在压缩量不变的情况下产生的弹力也随之减小。
2.2 疲劳环境
安全阀启跳压力为1.19 MPa,背压为0.05 MPa。在安全阀预载荷作用下,罐内介质压力在没有达到启跳压力前,安全阀不会开启。调出V401储罐内部压力变化记录,可知在2016年10月2日至2016年11月13日期间,该储罐的内压力最小为0.78 MPa,最大为0.82 MPa,未达到安全阀启跳压力。但是随着安全阀内弹簧腐蚀程度的增大,弹簧产生的弹力减小,虽然介质压力未达到安全阀启跳压力,实际安全阀已经发生了微启。
在2016年10月26日之后V401罐内介质压力波动幅值未发生大的改变,但压力波动频率明显增加:之前大致为每1.5 d一次,之后每天都有数次变化,并且在2016年11月5—6日之间出现过一次介质压力达到0.87 MPa的情况。波动压力通过安全阀密封面作用于弹簧,使得弹簧承受了介质压力变动而产生的交变应力。在交变应力的作用下,腐蚀产生的裂纹发生疲劳扩展,且在疲劳裂纹扩展过程中还伴随有湿H2S的腐蚀作用。在疲劳和腐蚀的共同作用下,裂纹不断扩展;当弹簧横截面剩余面积不足以承受内压应力时,弹簧发生断裂,安全阀开启,介质泄漏。
2.3 断裂原因
由理化检验结果可知:断裂弹簧的化学成分符合50CrVA弹簧钢的成分要求;弹簧表面硬度偏低,表层内部硬度增大,与外表面存在脱碳层的情况相符,心部硬度再次降低,这是由于在淬火时弹簧心部的降温速率低于表面的。断裂弹簧经历了淬火和中温回火热处理,组织为保持马氏体位向的回火屈氏体。断裂弹簧表面存在的全脱碳层和半脱碳层应是在制造加工时已经产生,而非使用过程中产生的。脱碳层的存在降低了弹簧的抗疲劳性能及耐湿H2S应力腐蚀开裂能力。弹簧断口分为裂纹源区、裂纹扩展区和瞬断区3个区域,呈现疲劳断裂特征[1-2,5];微观观察时仅在靠近裂纹源区处发现少量的疲劳扩展痕迹,说明疲劳在裂纹扩展过程中起到了一定的作用,但不是主要作用。宏观检查时弹簧散发出浓重的臭鸡蛋气味,应为H2S吸附在弹簧上所致,这与安全阀入口端干气中以及出口端火炬气中含有的H2S有关。裂纹源区发生严重腐蚀,呈疏松状,且检测到大量硫元素的存在,表明腐蚀是由H2S导致的。近断口表层存在大量裂纹,应为氢原子在表层聚合形成H2,H2聚集成气团导致压力升高,压力超过弹簧钢的强度极限而形成的。当氢原子在晶界处聚集时,会降低晶粒间的结合力,从而形成晶间裂纹[6]。
弹簧在未发生开裂时受力情况见图10,图中:F为作用于弹簧的主应力,这里是安全阀结构与介质压力共同对弹簧的作用力;FN为法向力;FQ为切向力;α为弹簧螺旋升角;τmax为最大剪切力。剪切力最大位置如A所示。由图10可以看出,在工作过程中未出现裂纹时,弹簧主要受剪切力作用,在靠近弹簧轴线的内侧边缘受力最大。而当裂纹萌生后,内侧边缘处发生应力集中,改变了力的分布状态,同时也改变了裂纹扩展方向,此时裂纹尖端承受拉应力。
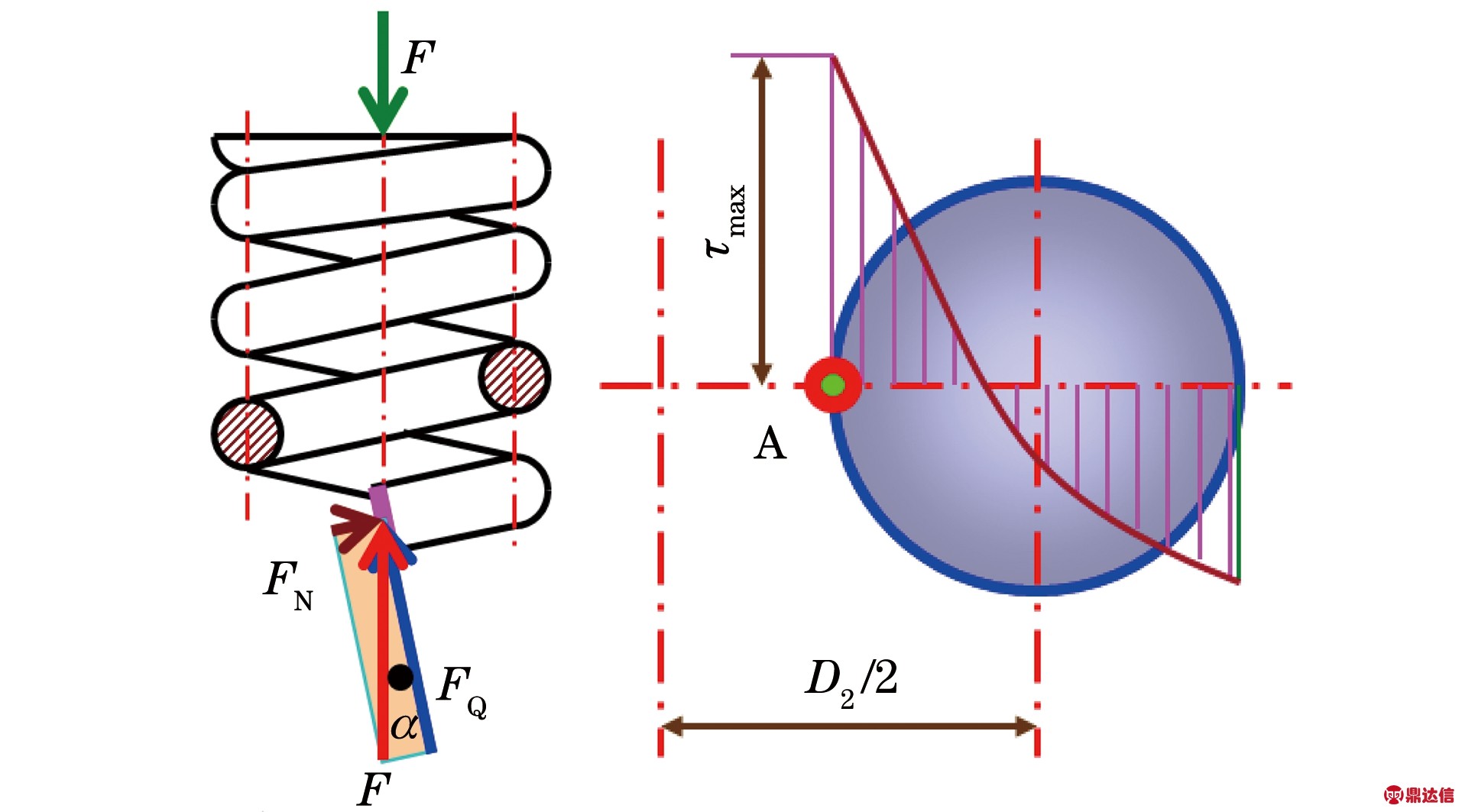
图10 安全阀弹簧在工作中的受力示意
Fig.10 Schematic of force of safety valve spring during operation
裂纹源区检测到SiO2夹杂物,且弹簧横截面上也存在少量夹杂物,说明弹簧材料不够纯净。SiO2夹杂物存在于弹簧的次表面,当H2S导致的裂纹扩展至该位置后即达到疲劳裂纹扩展门槛值,裂纹发生疲劳扩展[7]。湿H2S的腐蚀是导致弹簧断裂的主要原因,介质压力波动产生交变应力,形成的疲劳过程促进了弹簧的断裂,为次要原因。
3 结论和建议
(1) 安全阀弹簧处于湿H2S腐蚀环境,介质压力的波动使弹簧承受着交变应力作用。在运行过程中,弹簧先发生H2S腐蚀而产生应力腐蚀裂纹,在交变载荷的作用下裂纹扩展直至断裂,为腐蚀疲劳断裂。
(2) 建议控制弹簧制造过程,保证表面不出现脱碳层;加强弹簧材料质量控制,提高材料纯净度以防止产生较大的夹杂物[8];根据介质腐蚀特性,更换弹簧表面涂装材料:检修期间检查同批次类似工况安全阀,提前发现问题,解决安全隐患。