摘要:为提高某固体火箭发动机滚动球窝接头接触承载能力,降低系统摆动力矩,以单珠承载试验模型为计算模型,采用摩擦接触问题的Lagrange乘子法与弹塑性耦合的有限元理论,计算分析了具有不同强化层材料性能的阳球试件与滚动体接触位置处的接触应力、摩擦应力、变形及破坏机理;解决了阳球不同强化层材料性能对接头接触承载性能的影响问题。根据计算分析结果,提出了满足弹塑性摩擦接触性能条件下,小的摩擦系数、小的弹性模量和较大的屈服极限相配合的阳球强化层材料性能要求;通过与单珠承载试验对比分析,检验了有限元建模及计算结果的合理性。
关键词:固体火箭发动机;滚动球窝喷管;强化接头材料性能;弹塑性摩擦接触有限元;单珠承载试验
0 引言
某固体火箭发动机全轴摆动滚动球窝喷管的滚动球窝接头由大尺寸球面的阴球、阳球及数个小尺寸球形滚动体等组成。接头既是活动体与固定体间的连接件,又是载荷支承件,其接触承载能力是决定接头结构设计及系统功能发挥的关键问题之一[1]。
接头的阴球和阳球零件表面须进行强化处理,强化层材料性能必须使阳球表面具有高的接触承载能力,否则在工作载荷作用下,滚动体与阳球接触位置处,阳球表面会产生塑性变形;而系统不允许太大的变形,当变形超过许可范围,则造成摆动力矩增大,增加推力向量控制的难度。因此,强化接头材料必须在满足总体对接头结构质量及接头结构尺寸要求的前提下,保证接头阴、阳球能承受预定的工作载荷而不产生过量的塑性变形。
即使在简单载荷作用下,对于考虑强化层材料性能和摩擦效应,并与弹塑性耦合的接触问题的简单模型,其解析建模及求解也非常复杂困难,一些数学问题亟待进一步解决[2-4]。本文采用更符合工程实际的弹塑性摩擦接触有限元法,计算分析阳球试件经表面强化处理后,强化层具有不同材料性能时(不同弹性模量、屈服极限和滚动摩擦因数),与滚动体间的接触应力、摩擦应力、变形及破坏机理;与单珠承载试验对比分析,为降低系统摆动力矩,增加接触承载能力,同时考虑大尺寸球面(φ≥300 mm)的强化工艺,解决不同强化层材料性能对接头接触性能的影响问题;提出更为合理的满足接头弹塑性摩擦接触承载性能的强化层材料性能要求。
1 弹塑性摩擦接触有限元计算模型
试验中没有观测到滚动体的残余变形,因此计算模型为弹性滚动体与弹塑性阳球试件的摩擦接触模型,摩擦采用库仑摩擦。
1.1 弹塑性摩擦接触有限元计算模型
考虑实际问题的特点,选用计算精度高的接触问题Lagrange乘子法。根据广义变分原理,在计算域中,把接触约束条件与Lagrange乘子相乘,与系统原势能(结构材料的弹塑性势能)一起构成一个修正泛函,把接触问题转换成求修正泛函的驻值问题,即无约束泛函的极值问题。离散接触界面,滚动体与阳球试件间建立面-面接触模型。阳球试件表面为接触面,滚动体表面为目标面。把接触力转换成等效节点接触力向量,写入方程左端,并整合为系数矩阵,引入接触定解条件[5-6],得到弹塑性摩擦接触问题的有限元控制方程。
t+Δt时刻弹塑性摩擦接触有限元控制方程为

式中 t+ΔtKep为t+Δt时刻系统弹塑性总刚矩;Δa为系统的位移增量向量;t+ΔtQl为t+Δt时刻的外载荷向量;t+ΔtQi为 t+ Δt时刻的内力向量;为 t时刻接触点对间距;t+Δtλ为t+Δt时刻拉格朗日乘子(力学意义是接触力)。
设Z、X分别表示接触体在接触界面的法线方向和切线方向。
粘合状态:系数矩阵Kca=。
滑动状态:Kca≠(有摩擦滑动),Kcλ =
(无摩擦滑动),t+Δtλ =t+ΔtλZ,-
=-
。
如果接触状态变化,可能发生不连续,为避免收敛太慢,在每一载荷增量步内用F.N.R迭代求解,其递推迭代公式为
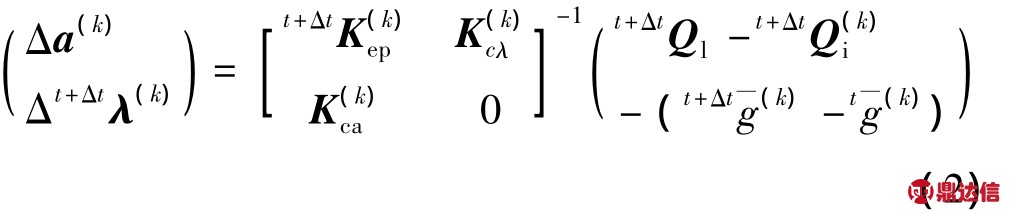
接触计算判定条件为
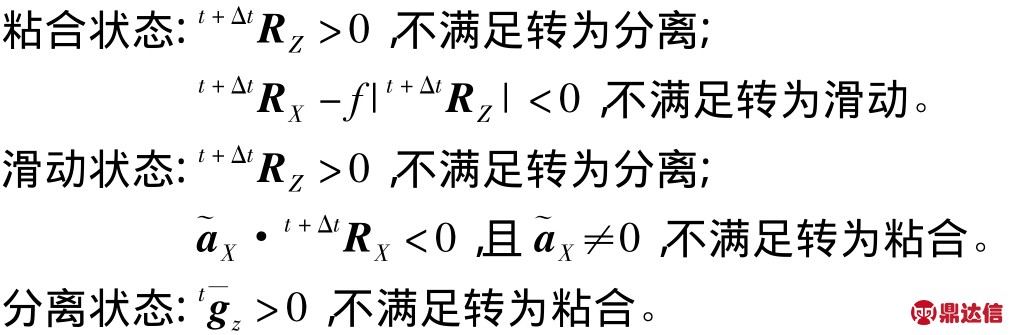
式中 t+ΔtR为t+Δt时刻接触力向量;f为摩擦因数;˜a为相对位移向量。
对于弹塑性摩擦接触问题,由于2个非线性混合在一起,在一个增量步中,每给定一种接触状态,就要解一个弹塑性边值。弹塑性迭代收敛后,检查接触状态,若接触状态与求解前一致,则该增量步的解已获得;不一致,则必须恢复到增量步开始时的状态,否则就把非真实接触条件下的变形历史引入后续计算,造成误差甚至错误的结果。然后,用新接触状态重新求解该增量步,直到弹塑性迭代收敛后,接触状态与求解前假定的一致,得到该增量步弹塑性摩擦接触问题的解,即弹塑性迭代置于内循环,接触迭代置于外循环。
1.2 材料性能及载荷路径
阳球试件表面强化处理后,经计算和试验检测,强化层厚度为 1.22 mm[7],泊松比 μ =0.3。本构关系为弹性区域 σ =Eεe;塑性区域 σ = σs+Hεp,εe、εp分别为弹、塑性应变,强化系数H=1×104MPa,表面强化处理后,其弹性模量E=2×105~3×105MPa,屈服极限σs可达到900 MPa以上。
阳球试件表面经不同强化工艺处理后,其基体材料性能变化不明显。阳球试件基体材料的弹性模量E=2.1 ×105MPa,泊松比 μ =0.3,屈服极限 σs=1 100 MPa。本构关系为弹性区域σ=Eεe;塑性区域由试验测得,见图1。
阳球与滚动体间的滚动摩擦因数f=0.001~0.005[1]。
滚动体弹性模量E=2.54×105MPa,泊松比μ=0.3;滚动体半径r=5 mm。
有限元计算分析中的加载、卸载路径与单珠承载试验中的加载、卸载路径一致。
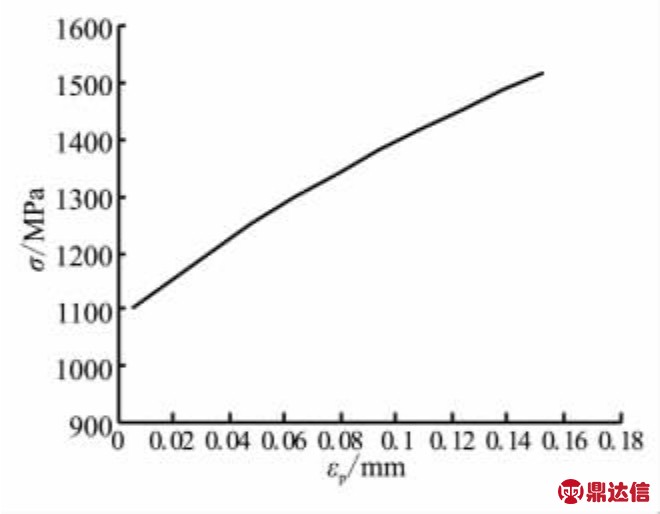
图1 阳球基体材料的应力-应变曲线
Fig.1 Stress-strain curve of the convex sphere materials
2 有限元计算结果与分析
算例为在500 kg载荷作用下,大尺寸球面(φ≥300 mm)的阳球,通过表面层强化后,其强化层材料具有如下属性:滚动摩擦因数f分别为0.003和0.005;弹性模量 E 分别为2.1 ×105、2.54 ×105、3 ×105MPa;屈服极限σs分别为1 000、2 000、3 000 MPa。
根据单珠承载试验中载荷特性和接触体的几何特性,建立滚动体与阳球试件弹塑性摩擦接触轴对称有限元模型(图2)。
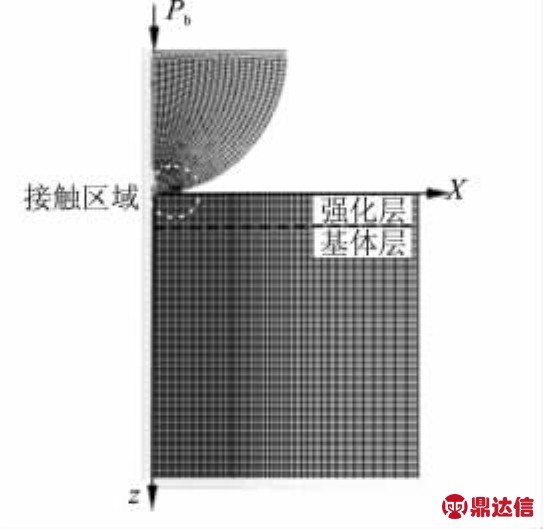
图2 有限元模型
Fig.2 Finite element model
2.1 接触应力及接触变形
图3~图5分别为强化层具有不同摩擦系数、弹性模量和屈服极限时,与滚动体接触位置处,阳球试件表面接触应力σ及弹塑性接触半径a分布、弹塑性接触压深b分布、残余压深b0及残余半径a0分布。
由图3~图5可知:
(1)弹性模量、屈服极限相同
摩擦因数分别为0.003和0.005时,接触应力极值分别为 5 202.9、5 203.7 MPa;弹塑性接触半径分别为 0.60、0.59 mm,残余半径分别为 0.57、0.56 mm;弹塑性接触压深分别为 0.036 828、0.036 821 mm,残余压深分别为 0.016 400、0.016 366 mm。
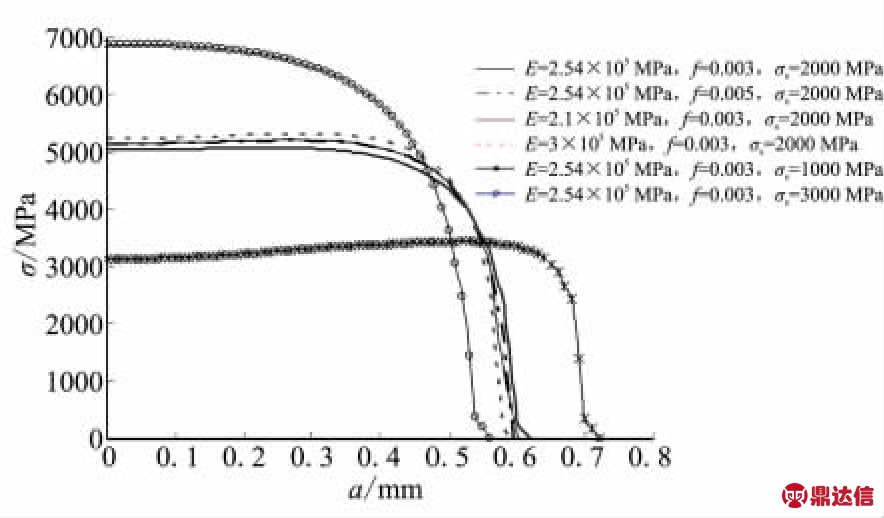
图3 接触应力及接触半径分布
Fig.3 Curves of contact stress and contact radius
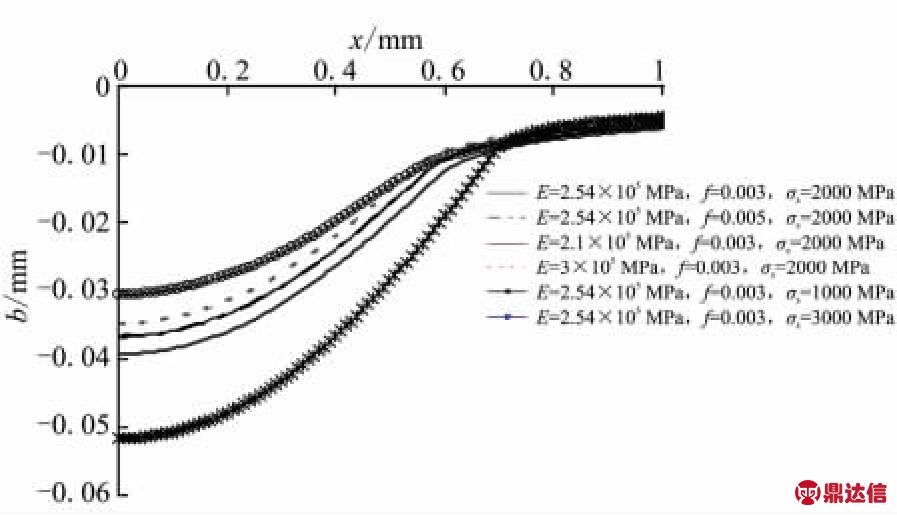
图4 弹塑性接触压深分布
Fig.4 Curves of elasto-plastic indentation deepness
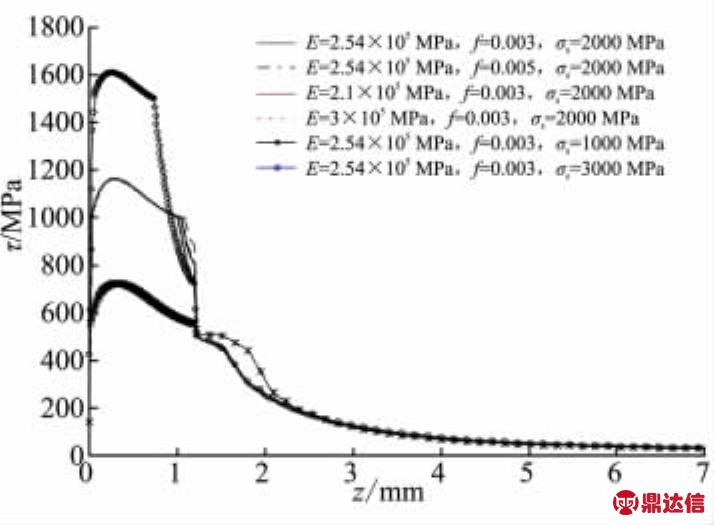
图5 残余压深及残余半径分布
Fig.5 Curves of residual indentation deepness and residual indentation radius
由于摩擦的存在,使得材料产生屈服时,需要更高的法向应力。同时,由于摩擦阻止边界区域的滑动,因此摩擦因数越大,阳球与滚动体间的表面接触应力越大,接触变形越小。总体而言,滚动摩擦因数小,阳球试件与滚动体间的弹塑性摩擦接触应力及接触变形分布差异较小。但为了减小接触应力、增加阳球接触强度、降低系统摆动力矩,应尽量减小摩擦因数。
(2)摩擦因数、屈服极限相同
不同弹性模量的阳球试件,表面接触应力及变形的分布差异较为明显。弹性模量分别为2.1×105、2.54×105、3 ×105MPa时,接触应力极值分别为5 065.4、5 202.9、5324.3 MPa;弹塑性接触半径分别为0.62 、0.60、0.59 mm,残余半径分别为 0.58、0.57、0.56 mm;弹塑性压深分别为 0.039 335、0.036 828、0.034 825 mm,残余压深分别为 0.016 100、0.016 400、0.016 486mm。
弹性模量越小,弹塑性摩擦接触应力越小。材料抵抗弹性接触变形的能力越差;抵抗法向塑性接触变形的能力增强,残余压深减小,有利于系统运动中,接头承受更高载荷而不产生过量的塑性变形,从而减小系统摆动力矩。
(3)弹性模量、摩擦因数相同
由于屈服极限不同,其接触应力和接触变形分布明显不同。屈服极限越小,材料抵抗塑性接触变形的能力越差,塑性变形越大,接触应力越小,接触应力峰值越向接触边缘偏移。
屈服极限分别为1 000、2 000、3 000 MPa时,接触应力极值分别为 3 446.8、5202.9、6 885.5 MPa;弹塑性接触半径为 0.72、0.60、0.56 mm,残余半径为 0.68、0.57、0.51mm;弹塑性压深为 0.051 700、0.036 828、0.030 649 mm,残余压深为 0.035 500、0.016 400、0.007 320 mm。
与σs=2 000 MPa相比,材料的屈服极限减小50%,强化层材料很快屈服,接触应力降低33.752%;弹塑性压深增大40.382%,残余压深增大116.463%。屈服极限增大50%,接触应力增大32.340%;弹塑性压深减小16.778%,残余压深减小55.366%。高的屈服极限虽然使接触应力有所增加,但可有效减小塑性接触变形。
为满足系统摆动力矩要求,规定强化接头残余压深为 0.03 mm[1];企业设计规范要求[8]实际应用中,其安全系数为1.2,则许用残余压深为0.025 mm。强化层屈服极限为1 000 MPa的阳球试件,其表面残余压深已超过许用残余压深。
2.2 摩擦应力
图6为强化层具有不同材料性能时,与滚动体接触位置处,阳球试件表面摩擦应力σf分布。
由图6可知:
(1)屈服极限相同
屈服极限σs皆为2 000 MPa时,由于滚动体与阳球接触表面,接触区整体呈粘合状态,在接触区域内,摩擦应力皆为切向拉应力。
弹性模量为 2.54×105MPa,摩擦因数分别为0.003、0.005 时,最大摩擦应力分别为 9.940、14.553 MPa。摩擦因数为0.003,弹性模量分别为2.1×105、2.54×105、3×105MPa时,最大摩擦应力分别为6.274、9.940、13.057 MPa。
摩擦因数、弹性模量越小,接触表面的摩擦应力越小。
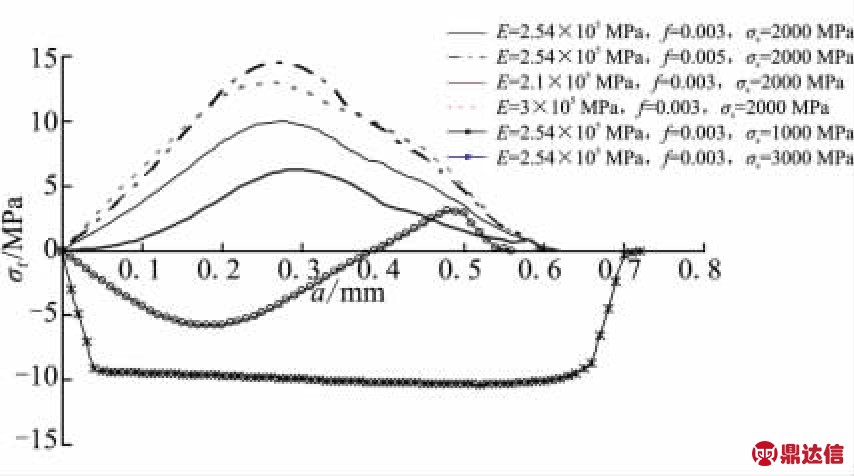
图6 摩擦应力分布
Fig.6 Curves of friction stress
(2)弹性模量、摩擦因数相同
屈服极限对摩擦应力的影响很大。与 σs=2000 MPa相比,屈服极限减小50%,强化层很快屈服,在相同载荷作用下产生更大的径向位移;接触区域滑动,摩擦应力呈较大的压应力状态。当屈服极限达到3 000 MPa时,大的法向接触压力产生大的剪切应力,距接触中心0.38 mm的接触区域内,产生滑动趋势,从而产生相对较小的切向摩擦压应力;摩擦和周围材料的约束使滑动趋势逐渐减弱并阻止了滑动,在0.38 mm之外的接触区域内呈粘合状态,并产生小的切向摩擦拉应力。
2.3 层下应力
图7、图8分别为强化层具有不同材料性能时,阳球试件与滚动体接触表面下方,沿接触中心对称轴z的主剪应力τ和等效Misses应力σv分布。由图7、图8可知,强化层材料性能不同的阳球试件,在接触位置近表层区域内,主剪应力和等效Misses应力迅速增长。沿中心对称轴距接触中心z≥2.5 mm的基体材料内,各应力平缓下降,逐渐趋于一致。
(1)弹性模量、屈服极限相同
由于滚动摩擦因数总体较小,不同摩擦因数对接触表面下方强化层和基体材料内的应力分布影响很小。摩擦因数分别为0.003和0.005时,最大主剪应力和等效Misses应力,分别产生在z=0.275 mm和z=0.272 mm位置处;摩擦使最大主剪应力和等效Misses应力向接触表面移动。
(2)摩擦系数、屈服极限相同
弹性模量为2.1×105MPa时,最大主剪应力和等效Misses应力出现在z=0.29 mm位置处;弹性模量分别为2.54×105、3 ×105MPa,最大主剪应力和等效Misses应力皆出现在z=0.275 mm位置处。弹性模量越大,最大主剪应力和等效Misses应力越向接触表面移动,当弹性模量超过2.54×105MPa时,其位置不再改变。
由于弹性模量不同,在强化层底部靠近基体材料的区域内,应力分布有较为明显的不同;弹性模量越小,在强化层和基体材料交界面处,应力突变越小,越不易引起层间剥离和裂纹[9]的产生。
(3)弹性模量、摩擦系数相同
由于屈服极限不同,强化层内主剪应力和等效Misses应力分布明显不同;强化层与基体材料的屈服极限越接近,材料交界面处的应力突变越小,但在基体材料局部区域内应力增大。
屈服极限分别为3 000、2 000、1000 MPa,最大主剪应力和等效Misses应力分别出现在z=0.26 mm、z=0.275 mm和z=0.32 mm位置处。强化层屈服极限为1 000 MPa,在z≥0.01 mm的区域内,强化层全部屈服。
(4)强化层材料性能不同的阳球试件,其基体材料均未产生塑性变形。理论上,层间不易产生初始裂纹[9]。
考虑大尺寸球面的强化和加工工艺,强化层厚度在1~1.4 mm[7],具有上述不同材料性能的阳球试件,在不同载荷作用下,与滚动体接触位置处,应力和变形分布趋势基本相同。
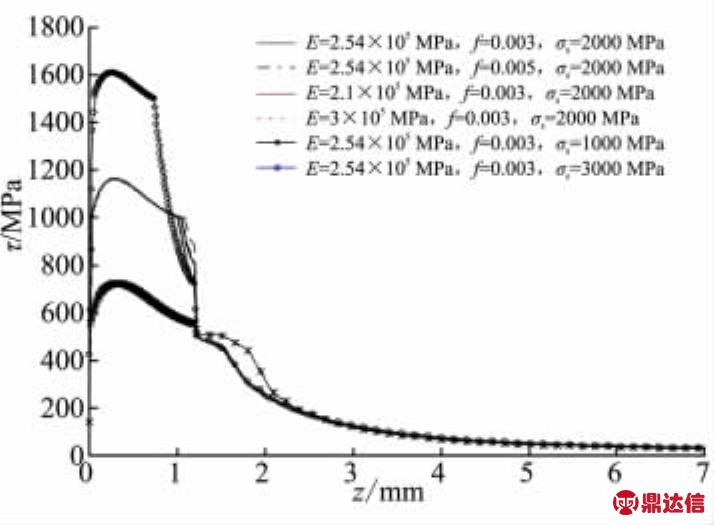
图7 主剪应力分布
Fig.7 Curves of main shear stress
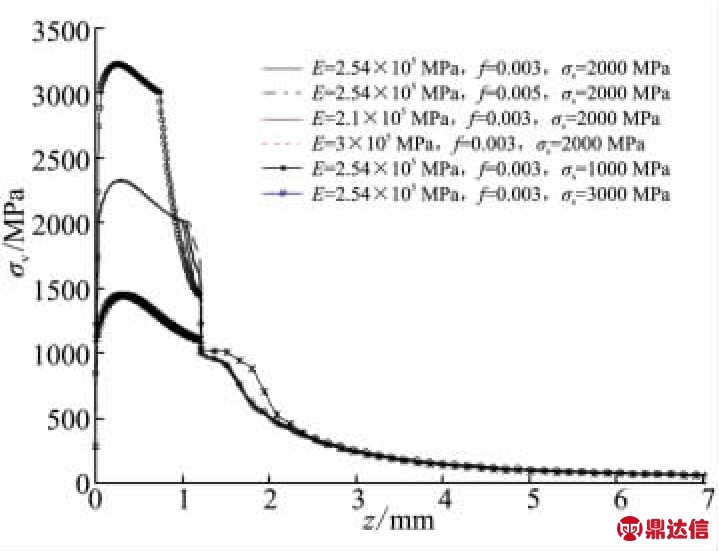
图8 等效Misses应力分布
Fig.8 Curves of equivalent misses stress
因此,从接触性能及破坏机理考虑,对于阳球试件的强化层,小的摩擦系数、小的弹性模量、较高的屈服极限,这样的材料性能相互配合,才能充分发挥强化层和基体材料的综合机械性能,减小系统摆动力矩。
3 试验与计算结果的对比分析
根据有限元计算分析结论,对阳球试件的强化工艺提出要求,以保证其材料性能要求。阳球试件经强化处理,表面精磨0.1 mm后,扫描电镜测得强化层厚度为1.22 mm。弹性模量 E=2.54 ×105MPa,滚动摩擦因数f=0.003,屈服极限σs=2 000 MPa。阳球试件基体材料及滚动体的材料性能检测结果见1.2节。
3.1 单珠承载试验
滚动体与阳球试件接触,载荷作用下阳球试件表面产生弹塑性变形,卸载后有不同程度的压痕。每级加载的压痕不重复。在工具显微镜下测量并记录压痕宽,对每级加载条件下的压痕宽取平均值2¯a0(表1)。
3.2 试验与计算结果的对比分析
不同载荷作用下,压痕的试验测量结果与弹塑性摩擦接触有限元计算结果见表1。
表1 试验结果与弹塑性摩擦接触有限元计算结果
Table 1 Test results and computation results of elasto-plastic friction contact finite element method
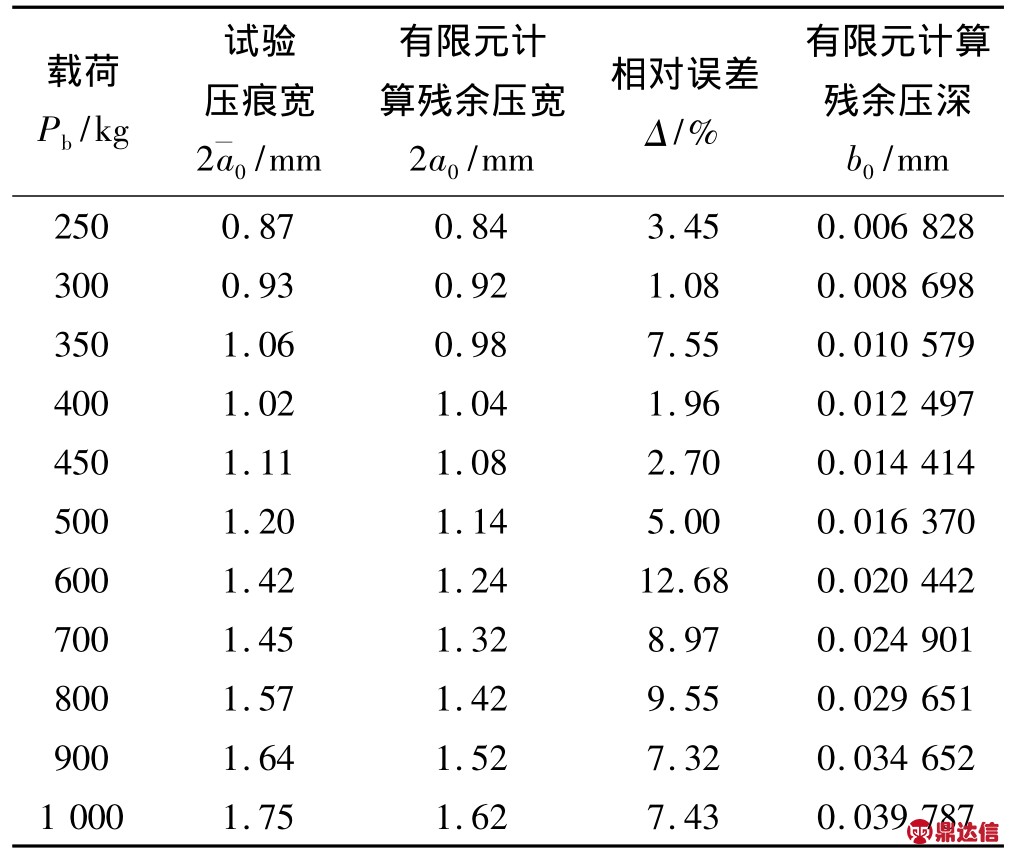
每级载荷作用下,相对于试验测量平均压痕宽,残余压宽的数值计算结果平均误差为6.15%。
电镜下观察压痕(放大100倍),并切片检测,试件在250~1 000 kg载荷作用下,均未发现层间剥离和裂纹。
作为算例的某发动机燃烧室最大工作压强为pcmax=6 MPa,则推力向量控制系统接头内部,阳球承受燃气压强所产生的最大单珠正压力Pbmax为

式中 Rs为阳球半径;φC1及φ为接触角;CF为发动机地面试车状态推力损失系数;Rt为喷喉半径;n为滚动体数目。
由表1可知,该喷管接头在燃烧室最大压强作用下,其接触表面残余压深满足设计要求。
因此,弹塑性摩擦接触有限元算法及其结果合理;通过弹塑性摩擦接触有限元计算分析所提出的阳球试件强化层材料性能要求可靠。
4 结论
(1)弹塑性条件下,滚动摩擦因数主要影响接触表面的摩擦应力和接触状态。弹性模量使接触表面应力和变形分布、强化层底部局部区域的主剪应力和等效Misses应力分布有较为明显的不同。小的摩擦因数、弹性模量使弹塑性接触变形有所增加,但可以有效降低表面接触应力、摩擦应力和残余压深。不同的屈服极限对接触表面应力、变形、接触状态及层下应力分布有很大影响;屈服极限越大,塑性变形越小,可以有效降低系统摆动力矩;但太大的屈服极限,使接触强度显著下降,最大主剪应力和等效应力越接近接触表面。
(2)不同的弹性模量和屈服极限,都会引起强化层和基体材料交界面的应力突变;强化层弹性模量和屈服极限越接近基体材料,应力突变越小,可减小层间产生剥离和裂纹的几率;但当屈服极限σs=1 000 MPa时,其残余压深已超出许可范围,势必增大系统摆动力矩。
(3)综合考虑接触表面及层下应力分布、变形及层间应力突变,对于强化层,小的摩擦系数、小的弹性模量、较高的屈服极限,这样的材料性能相互配合,才能充分提高系统强化接头的接触性能,降低系统摆动力矩。
(4)通过弹塑性摩擦接触有限元计算分析,对阳球材料强化工艺提出要求,通过实测,得到该型号滚动球窝喷管强化接头阳球试件强化层的材料性能:弹性模量 E=2.54 ×105MPa,滚动摩擦因数 f=0.003,屈服极限σs=2 000 MPa;其材料性能可以承受燃烧室最大工作压强。
(5)通过与单珠承载试验对比分析,检验了对阳球试件强化层材料性能要求及有限元建模和算法的合理性。