摘 要: PPPS机构球铰点中心位置对飞机大部件调姿精度有重要影响,为了解决当前常用的球铰点中心位置获取方式在精度或效率上的不足,提出一种PPPS调姿机构球铰点中心位置的闭环标定方法。首先,分析了球铰点中心位置误差与运动学逆解时定位器位移求解偏差的关系及大部件位姿变换参数对其的影响;然后,提出了基于关键特性结合奇异值分解几何意义的飞机大部件位姿参数快速求解方法,使位姿参数求解过程更加直观简捷,同时相较于常用的奇异值分解方法在精度上没有损失;利用一次调姿过程前后大部件位姿参数的变化和定位器的位移反馈,结合运动学逆解对球铰点中心的位置进行闭环标定,最后,以某型号飞机垂尾测试件为例验证了所提出方法的正确性和实用性。
关键词: 大部件调姿; PPPS机构; 球铰点中心位置; 关键特性; 奇异值分解; 闭环标定
PPPS(Prismatic-Prismatic-Prismatic-Spherical)串并联机构具备结构简单、承载能力强、精度高、工作性能稳定可靠等优点[1],广泛应用于飞机大部件调姿[2]。利用PPPS调姿机构和激光跟踪仪,结合相关控制软件,形成飞机大部件调姿系统[3],能够在大部件对接装配[4-5]或精加工[6]时实现对其姿态的测量和自动调整,从而提高装配/精加工的质量和效率。国内外对该类型调姿系统展开了大量的研究,在运动学/动力学解析、位姿计算、调姿轨迹规划、调姿内力优化等方面取得了不少的研究成果。
运动学和动力学解析是其他环节的基础,张洪双等[7-8]在建立调姿机构运动学模型的基础上,研究了定位器支撑点位置的优化选择和定位器的优化布局与行程等问题。
在大部件位姿参数计算方面,一般通过最小二乘法对多个基准点在两个坐标系下的关系进行配准[9-10],常用的方法包括奇异值分解法(Singular Value Decomposition,SVD)、四元数法等[11]。俞慈君等[12]研究了带工程约束的点匹配算法,朱绪胜和郑联语[13]研究了基于关键装配特性的大部件最佳位姿多目标优化算法。
在调姿轨迹规划和调姿内力优化方面,张斌等[14]提出了基于五次多项式的最优时间轨迹规划算法,崔学良等[15]针对大尺寸弱刚性构件提出了基于S型速度曲线的轨迹规划技术,黄鹏等[16]研究了多目标多约束条件下的轨迹规划技术,郭志敏等[17]提出了通过定位器关节驱动力的最小范数解来进行调姿内力的优化和控制。
在PPPS调姿机构中,定位器与大部件的球铰点中心在全局坐标系下的位置是运动学和动力学解析、调姿轨规划等环节的基础,球铰点中心实际位置和理论位置的偏差对大部件调姿的精度有重要的影响[18]。然而,在当前的研究及相关的产品中都将球铰点中心位置作为系统的已知量,如西门子在sinumerik 840D系统下开发了一套冗余分布式笛卡尔坐标系(Redundant Distributed Cartesian Coordinates,RDCC)系统,通过PPPS机构实现大型构件的定位,其中定位器和大构件的球铰点中心在全局坐标系的位置必须作为已知量输入到数控系统中才能进行调姿轨迹规划和程序后置处理。由于球铰点中心在机构内部,最常用的方法是利用激光跟踪仪结合辅助测量装置对其位置进行直接测量[19],这种方式比较繁琐,效率较低。马志强等[20]研究了在给定定位器球铰点初始位置和距离条件下,通过测量驱动器的位移计算调姿过程中球铰点的位置信息,但该方法只是根据球铰点中心的初始位置及其位移量求解出球铰点中心移动后的位置,没有对球铰点中心位置的初值误差进行补偿。
针对以上研究的不足,提出一种PPPS机构球铰点中心位置闭环计算方法,利用大部件姿态参数的变化和定位器的位移反馈对球铰点中心位置进行闭环标定,省去对球铰点中心的测量过程,从而提高调姿的精度和效率。首先在第1节中研究分析PPPS球铰点中心位置对调姿精度的影响,然后在第2节提出基于关键特性的大部件位姿参数快速计算方法,并结合定位器位移量对球铰点中心的位置进行求解,最后通过应用实例验证本文方法的有效性和工程应用效果。
1 PPPS调姿机构描述
PPPS调姿机构是由n个定位器与大部件组成的并联机构,大部件外形尺寸的大小决定了定位器的数量(最少3个),每个定位器是由3个相互正交的移动副组成的串联装置,定位器与大部件通过球铰连接,图 1展示的是最常见的3PPPS调姿机构。
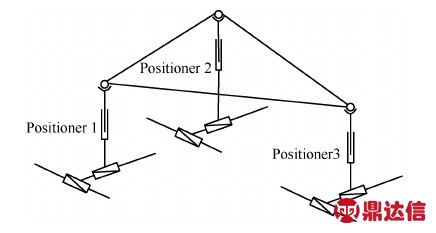
图1 3PPPS机构简图
Fig. 1 Sketch diagram of 3PPPS mechanism
设大部件在全机坐标系{A}下的当前位姿参数为(α,β,γ,x,y,z),其中α、β、γ分别为绕X、Y、Z轴旋转的欧拉角,x、y、z分别为沿X、Y、Z轴的平移量;理论位姿参数为(0, 0, 0, 0, 0, 0);球铰点中心当前坐标为pi(i为定位器编号)。根据运动学逆解可得将大部件调整到理论位姿时球铰点中心坐标表示理论位姿状态)与pi的关系为

(1)
式中:R为旋转矩阵;T为平移矩阵;R按照Z-Y-X的欧拉角旋转顺序可表示为
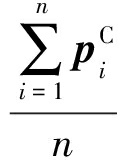
(2)
通过式(1)可以看出球铰点中心位置是调姿运动学逆解的关键。由于球铰点中心通常被球窝包围,如图 2所示,直接测量法需要引出辅助测量杆并测量多个辅助测量点来拟合出球铰中心的位置,比较费时费力。
球铰点中心在定位器坐标系下的位移为

(3)
式中为全机坐标系{A}与定位器坐标系{P}
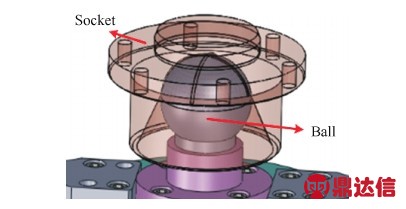
图 2 球铰连接示意图
Fig. 2 Diagram of ball and socket joint
的旋转变换矩阵;E为三阶单位矩阵。
通过式(3)可以看出球铰点中心偏差会对定位器的位移产生影响,对运动学逆解时定位器位移求解偏差的影响可表示为
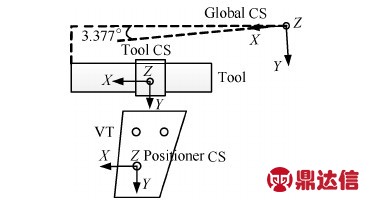
(4)
式中为球铰点中心位置误差,上标E表示误差;ΔPi为定位器位移量受其影响的误差。式(4)表明定位器位移量的误差只与大部件的旋转变换矩阵R和球铰点中心的位置误差
有关,而与平移矩阵T以及其他因素无关(当现场全机坐标系基准建立完毕,定位器安装并校准后,全机坐标系与定位器坐标系的关系
为定值)。
由于和R都各有3个独立变量,将3个变量等量化并用1个变量替代表示,即假设球铰点中心位置在3个方向的误差相等,位姿变换参数的3个欧拉角相等(该假设只是为了便于直观分析定位器位移误差与位姿变换参数和球铰点中心位置误差的关系,不会影响计算结果的量级)。简化后,可得到定位器位移偏差与影响因素之间的关系如图 3所示,通过图 3(a)可以看出随着位姿变换参数中欧拉角变化的增加,球铰点中心位置误差对定位器位移误差的影响也在随之增大,而通过图 3(b)可以看出在极小旋转角时,将球铰点中心位置误差控制在一定范围内,对定位器位移的影响可以忽略。

图3 定位器位移偏差与影响因素之间的关系
Fig. 3 Relation between positioner displacement error and its effect factors
2 球铰点中心位置闭环标定
2.1 基于关键特性的位姿参数快速求解
在飞机大部件精加工或装配对接时,一般都是用部件上的关键测量点来拟合其位姿,而关键测量点的坐标都是在理论全机坐标系下给出的,因此部件的局部坐标系可以看作是理论全机坐标系,而在现场建立的实际基准全机坐标系可以称为全局坐标系。大部件调姿可以看作局部坐标系向全局坐标系转换的过程,大部件位姿参数的求解实质就是计算关键测量点在局部/全局坐标系下的匹配关系。
SVD法是研究两个坐标系转换关系的有效方法,设大部件上的测量点在局部坐标系{C}和全机坐标系{A}下的位置矢量分别为其中i=1,2,…,n,n为测量点数量,SVD法计算位姿参数的基本步骤为
步骤1 计算测量点重心化坐标和
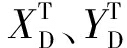
(5)
步骤2 计算协方差矩阵H:
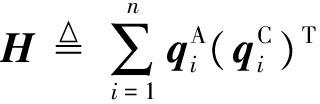
(6)
步骤3 对协方差矩阵进行奇异值分解:
H=UΛVT
(7)
步骤4 计算旋转矩阵:
如果det(V)=1,则
R=VUT
(8)
如果det(V)=-1,分析对角矩阵Λ的3个对角元素,若存在值为0的对角元素,则对矩阵V相应的列取负,例如Λ的第2个对角元素为0,则令V′=[v1 -v2 v3],可得
R=V′UT
(9)
步骤5 计算平移矩阵:
T=-R
(10)
步骤6 计算位姿参数:

(11)
x,y,z=T(1),T(2),T(3)
(12)
式中:R(i,j)为旋转矩阵中第i行第j列元素;T(i)为平移矩阵中第i个元素。
对步骤3的结果进行分析,协方差矩阵进行奇异值分解后得到矩阵Λ为对角矩阵,对角线上的元素为矩阵的奇异值;矩阵U和V是3阶酉矩阵,而从几何意义上分析这两个矩阵分别为测量点在不同坐标系下的标准正交基,因此可以通过两组点坐标构建各自的标准正交基,从而快速求解旋转矩阵。
SVD法在求解位姿参数时以所有基准点的综合转换残差最小为目标,该方法在误差合理分配及点组公差约束方面还存在明显不足,因此本文提出基于关键特性(Key Characteristics,KC)的位姿计算方法,结合SVD的几何意义对大部件的位姿进行快速计算。本文中的关键特性是指飞机大部件上的关键特征,以最常见的平面特征和直线特征为例,描述建立单位正交基向量的方法。
飞机大部件上某直线特征上的一组点,在全局/局部全机坐标系下的坐标值拟合的直线方程分别为
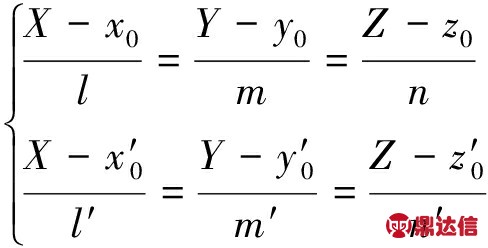
(13)
飞机大部件上某平面特征上的一组点,在全局/局部全机坐标系下的坐标值拟合的平面方程分别为
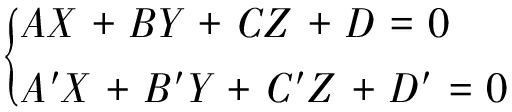
(14)
通过最小二乘法求解出式(13)和式(14)中的直线和平面方程的参数,其中(l, m, n,x0, y0, z0)和(l′, m′, n′, ,
,
)分别为测量点在全局和局部坐标系中拟合出的直线特征参数;(A, B, C, D)和(A′, B′, C′, D′)分别为测量点在全局和局部坐标系中拟合出的平面特征参数。当直线方向矢量与平面法向矢量不平行时,可求解出两组单位正交基向量:
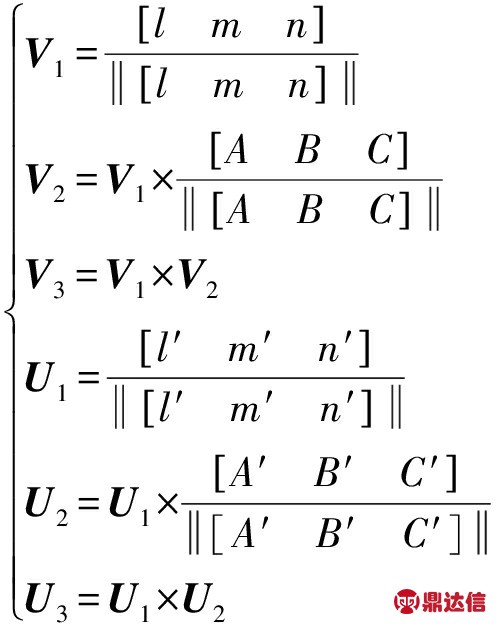
(15)
式中:Vi和Ui分别为U和V的第i个列向量(i=1, 2, 3),结合式(8)即能求解出旋转矩阵。
2.2 球铰点中心位置闭环标定过程
在完成一次调姿后,利用大部件位姿参数的变化和定位器的位移对球铰点中心的坐标进行修正,大部件姿态参数的变化通过2.1节中的方法进行求解,定位器的位移可通过位置反馈装置获取,闭环计算的流程如图 4所示。
步骤1 测量大部件上的关键点。
步骤2 利用2.1节中的方法,计算出大部件的当前位姿参数。
步骤3 判断当位姿是否满足要求,如满足则转步骤10,否则到步骤4。
步骤4 根据大部件理论和当前位姿参数,结合球铰点中心坐标进行运动学逆解,求解出定位器的位移。
步骤5 对大部件的姿态进行调整。
步骤6 测量大部件上的关键点。
步骤7 计算大部件位姿参数。
步骤8 判断当前位姿是否满足要求,如满足则转步骤10,否则转步骤9。
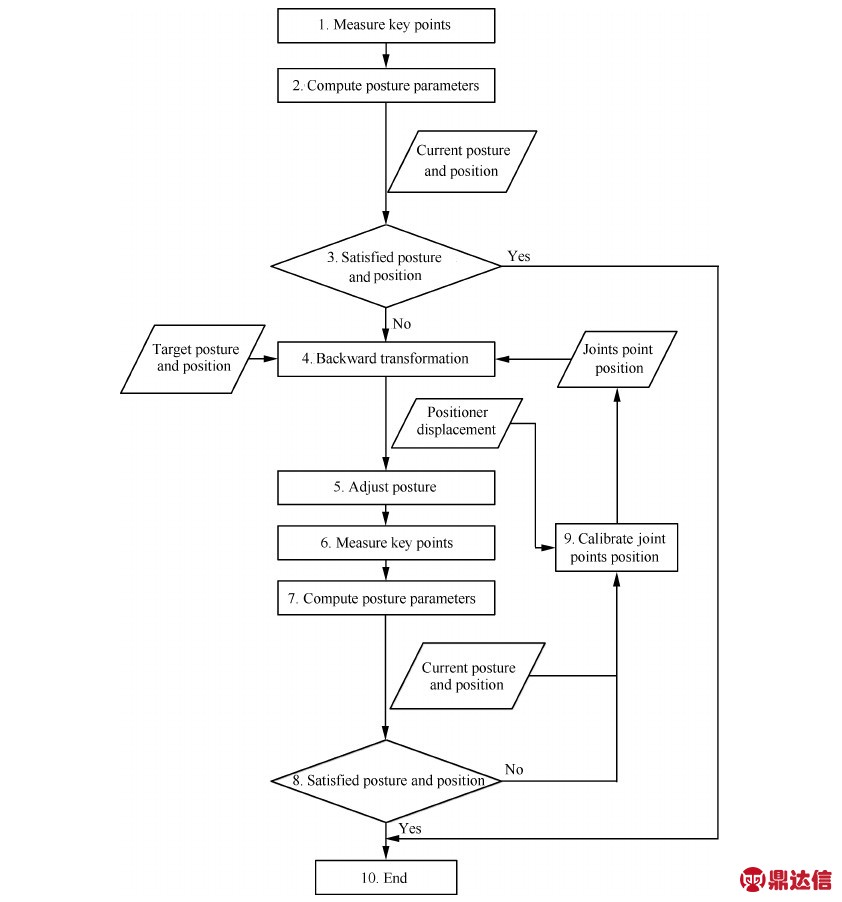
图4 球铰点中心位置闭环标定流程
Fig. 4 Flowchart for closed-loop calibration of ball joint center position
步骤9 利用定位器位移量和调姿前后大部件的位姿参数变化,对球铰点中心位置进行闭环计算,然后重复步骤4~9直至满足位姿要求。
步骤10 结束调姿。
设调姿机构球铰点中心在调姿过程中相对全机坐标系零点的坐标为为定位器编号,k为调姿次数,根据运动学逆解公式可得第k次和第k+1次调姿后球铰点中心的坐标为
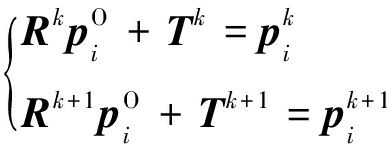
(16)
式中:Ri和Ti为2.1节中求解出的大部件在第i次调姿时相对于理论位姿的旋转矩阵和平移矩阵。通过式(16)可得

(17)
球铰点中心位置矢量的变化通过定位器中的位置反馈系统可描述为

(18)
式中为数控系统中获取的定位器位移反馈,是在定位器坐标系中表示的,因此需要通过旋转矩阵
将其转换为全机坐标系下的值。
联立式(17)和式(18)可得

(19)
因为旋转矩阵R都是满秩的单位正交矩阵,因此可将式(19)简化为
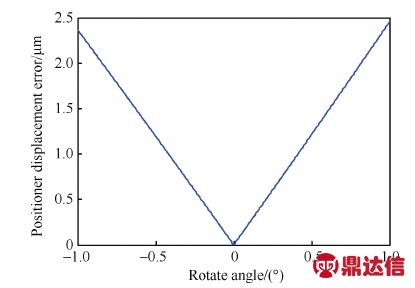
(20)
式中为第k+1次调姿后大部件位姿相对于第k次的旋转矩阵,可表示为

(21)
设

(22)
式中:Ru表示式(20)左边的已知量;Rv表示式(20)右边的已知量。可将式(20)的分析计算简化为以下几种情形:
1) 当第k次与k+1次调姿之间,大部件的位姿变换包括3个欧拉角变换,即两次调姿之间大部件绕3个坐标轴旋转时,可得Ru满秩,式(20)有唯一解,可求解出球铰点中心位置为

(23)
2)当第k次与k+1次调姿之间,大部件的位姿变换只包括2个欧拉角变换,即两次调姿之间大部件只绕2个坐标轴旋转时,以分别绕Y轴和Z轴旋转β和γ角为例,可得
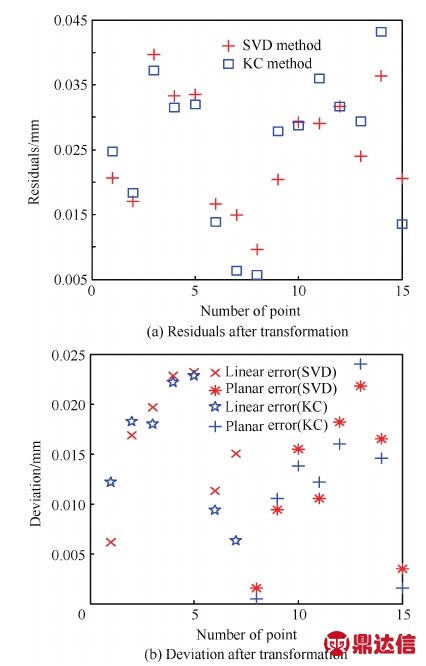
(24)
由于rRu=2,因此Ru不可逆,构建增广矩阵Ru Rv。
当rRu<rRu Rv时,式(20)无解,无法计算球铰点中心位置。
当rRu=rRu Rv时,式(20)有无穷多解,可约束球铰点中心位置的x坐标。
因此,当两次调姿之间绕2个坐标轴旋转时,如果满足rRu=rRu Rv,可以对球铰点中心的另外1个坐标进行修正。
3) 当第k次与k+1次调姿之间,大部件的位姿变换只包括1个欧拉角变换,即两次调姿之间大部件只绕1个坐标轴旋转时,以绕X轴旋转α角为例,可得
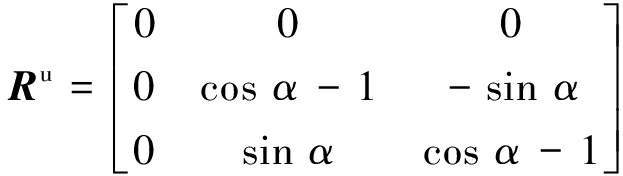
(25)
由于α≠0,因此rRu=2,Ru不可逆,构建增广矩阵Ru Rv。
当rRu<rRu Rv时,式(20)无解,无法计算球铰点中心位置。
当rRu=rRu Rv时,式(20)有无穷多解,可约束球铰点中心位置的y和z坐标。
因此,当两次调姿之间只绕1个坐标轴旋转时,如果满足rRu=rRu Rv,可以对球铰点中心的另外2个坐标进行修正。
4) 当第k次与k+1次调姿之间大部件只有位置平移而无角度旋转时,Ru为零矩阵,式(20)无解,无法计算球铰点中心位置。
3 应用验证
以某型号飞机垂尾(Vertical Tail,VT)测试件在精加工时的调姿过程为研究对象,如图5所示,采用3PPPS机构作为大部件调姿的执行器,利用西门子840Dsl数控系统控制所有定位器(P1、P2、P3)的运动,开发调姿计算和控制软件,实现本文所提出的方法,结合Leica AT901激光跟踪仪,验证基于关键特性的大部件位姿参数快速求解方法和球铰点中心位置闭环计算方法。
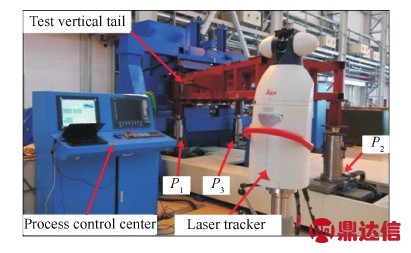
图5 某型号飞机垂尾精加工中的调姿系统
Fig. 5 Posture aligning system in finish machining of a certain aircraft vertical tail
垂尾及其关键测量点如图6所示,包括一组与方向舵连接的铰接点(1JJD-7JJD)和一组以垂直安定面为对称平面分布的全机水平测量点(35#L~38#R),其中“L”和“R”分别表示垂直安定面的左右两侧(沿飞行方向),图6中只展示了“L”测量点。
关键测量点在全机坐标系下的理论坐标值如表1中的和
所示(P表示测量点,N表示理论值),其中每个测量点的位置度约束为0.06 mm,7个铰接头的中心位置与方向舵铰链直线的最大距离误差不超过0.05 mm,8个水平测量点与垂直安定面的最大距离误差不超过 0.05 mm。
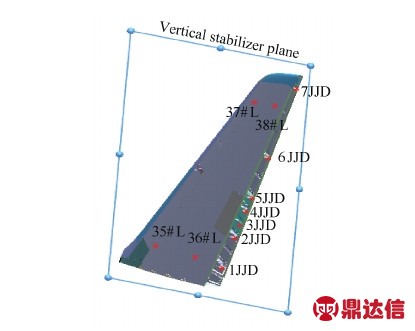
图6 垂尾关键测量点
Fig. 6 Key points of vertical tail
3.1 大部件位姿参数求解方法验证
垂尾上架后,利用激光跟踪仪测量所有关键点,得到其在上架后的实测值如表1中的和
所示(P表示测量点,I表示上架后初始实测值)。利用2.1节中提出的关键特性方法计算出大部件的位姿参数如表2所示,同时也列出了利用SVD法所得到的参数。均方根误差(Root Mean Square,RMS)及平均关键特性误差(直线误差Linear和平面误差Planar)的对比也在表2中展示。
测量点的转换残差如图7(a)所示,可以看出本文提出的关键特性方法比SVD法的转换残差略大,但也在满足要求的误差范围内。测量点转换后与关键特性的距离误差如图7(b)所示,可以看出本文提出的方法与SVD法相比,大部分测量点与关键特性(平面和直线)的距离误差更小。
表1 垂尾关键测量点的理论坐标/上架后的初始测量值/调姿后的测量值
Table 1 Nominal values, initial and measured values before and after alignment of key points on vertical tail
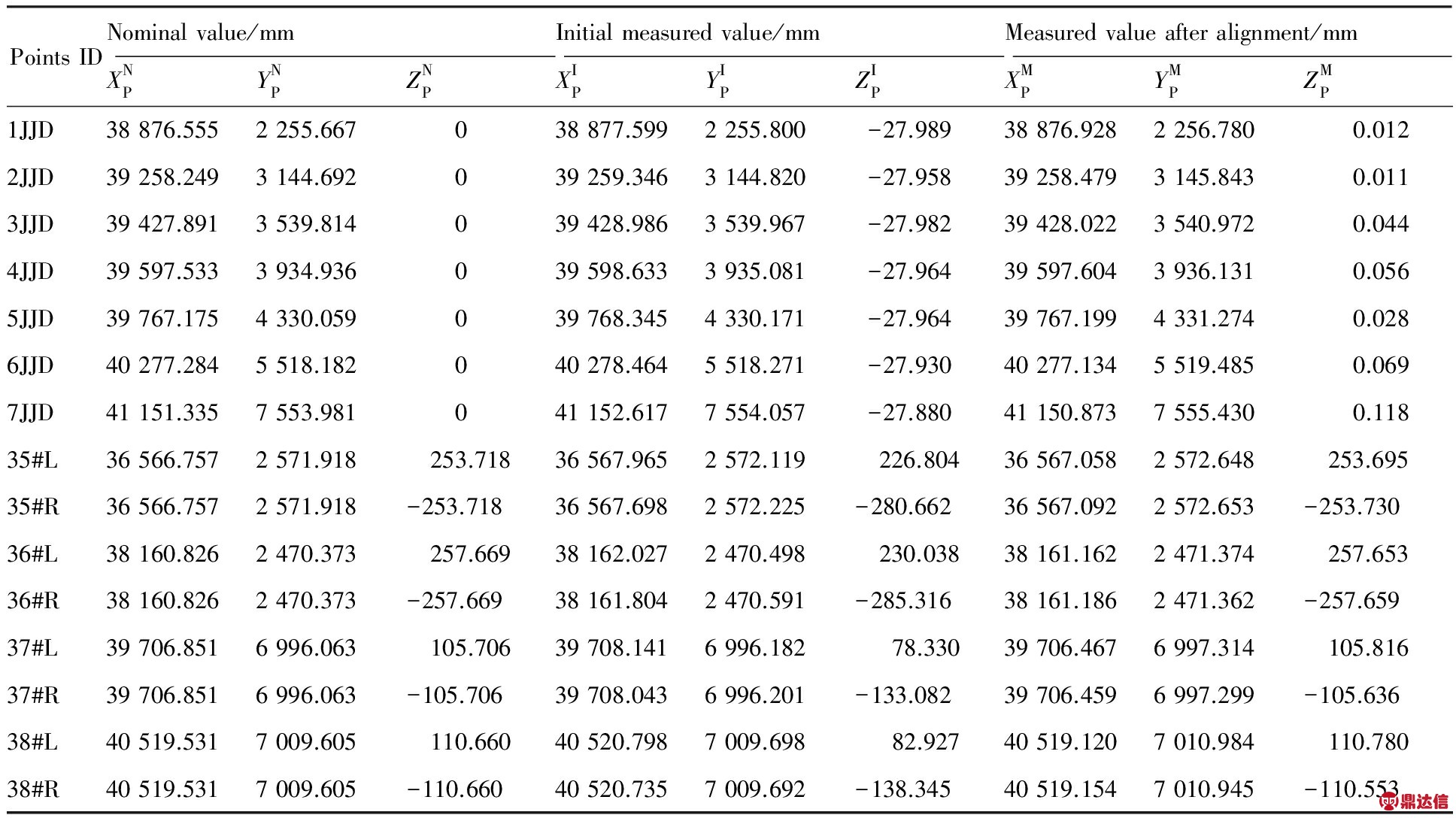
表2 不同方法求解的位姿参数及转换残差
Table 2 Posture parameters and residual errors after transformation by different methods

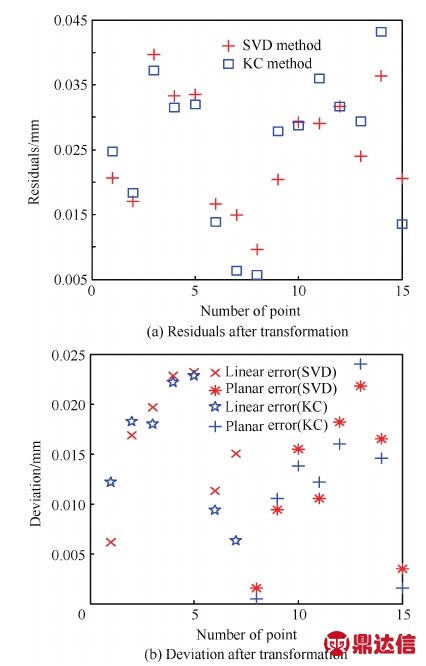
图7 测量点的转换残差与转换误差
Fig. 7 Residuals of points and deviation after transformation
通过两种方法的结果对比可以看出,本文方法的RMS误差比SVD方法的大,但也充分满足精度要求,而测量点在转换后的关键特性误差要比SVD小,而且计算过程直观简单,易于理解。
3.2 球铰点中心位置闭环计算方法验证
大部件与定位器的球铰点中心在全机坐标系下的设计理论值如表3中的和
所示(J表示铰链点,N表示理论值)。利用表2中本文提出方法计算出的位姿变换参数,结合中定位器球铰点中心的理论位置,进行运动学逆解得到定位器的位移如表4中的
和
所示(D表示
定位器的位移,T表示运动学解析),对大部件的位姿进行调整,调姿完成后测得关键点的坐标如表1中的和
所示(P表示测量点,M表示调姿后的实测值)。
利用2.1节中的KC方法求得的位姿参数如表5所示。调姿时定位器的位移量通过数控反馈装置得到,如表4中的和
所示(D表示定位器的位移,F表示数控装置反馈),以定位器坐标系为基准,可以看出定位器的定位误差达到了μm级。
定位器坐标系与全机坐标系的关系如图8所示,定位器坐标系相较于全机坐标系绕Z轴旋转了3.377°。定位器坐标系{P}和全机坐标系{A}之间的旋转变换关系用矩阵表达为
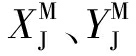
(26)
采用2.2节中的方法对定位器球铰点中心位置进行计算,修正后的坐标如表3中的和
所示(J表示铰链点,C表示修正值)。采用文献[19]中的方法对定位器球铰点中心位置进行测量并通过部件姿态参数反求出球铰点中心在理论位姿下的坐标如表3中的
和
所示(J表示铰链点,M表示修正值)。将定位器球铰点中心坐标的修正值和理论值分别与实测值进行对比,结果分别如表6中的
和
所示(E表示偏差,C表示修正值,N表示理论值)。
定位器球铰中心的理论值与实测值最大偏差高达12 mm,主要原因在于制造的偏差、温差导致的变形以及起吊上架时的受力变形等。而采用本文的闭环标定方法可将球铰点中心位置校准到与实测值相差不超过0.1 mm,以定位器P1为例,利用式(4)可以分析出其球铰中心的标定误差对位移求解的影响,如图9所示,在大部件姿态旋转角小于1°时,标定的球铰中心误差造成的位移求解误差小于2.5 μm,对调姿精度的影响可以忽略。因此采用本文提出的闭环标定方法既避免了直接利用理论值导致精度上的缺陷,又省去了直接测量法消耗的时间。
表3 定位器球铰点中心的理论坐标/修正坐标/实测坐标
Table 3 Nominal, corrected and measured coordinates of positioner joint points

表4 运动学求解的定位器位移和数控装置反馈的位移
Table 4 Displacement of positioners by kinematic transformation and feedback from CNC system

表5 调姿后的位姿参数
Table 5 Posture parameters after alignment
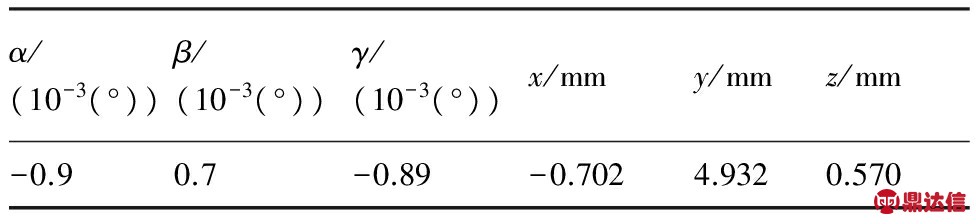
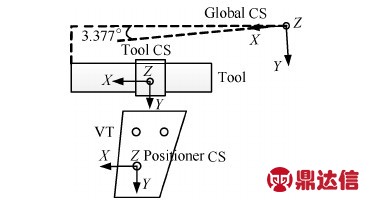
图8 全机坐标系与定位器坐标系的关系
Fig. 8 Relation between positioner CS and global CS
表6 定位器球铰点中心修正坐标和理论坐标与实测值的偏差
Table 6Deviation from corrected coordinates and nominal coordinates to measure values positioner joint points

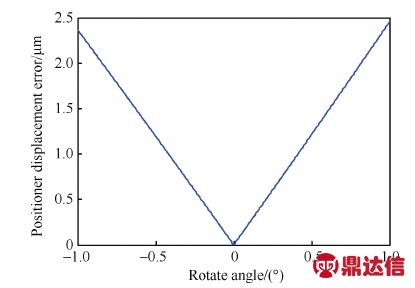
图9 定位器P1球铰中心偏差对其位移求解的影响
Fig. 9 Impact of positioner P1 joint center error on its displacement computation
4 结 论
1) PPPS调姿机构球铰点中心位置误差对定位器位移计算及轨迹规划有重要影响,但在姿态微调时(小于1°)将误差控制在一定范围内(小于0.1 mm),能够满足调姿精度要求。
2) 提出的基于关键特性的大部件位姿快速求解方法既能满足关键特性的约束,又比较直观简捷,能够解决基准点具有关键公差约束时大部件位姿的优化和快速计算。
3) 提出的球铰点中心位置闭环标定方法能够求解出符合精度要求的球铰点中心坐标,相比直接测量法不会造成调姿精度的损失,同时明显提高了调姿效率。