摘要:为了提高球栅阵列焊点封装器件的自组装成品率,研究了焊点体积偏差率及焊盘直径对器件自组装成品率的影响。考虑封装器件的温度翘曲变形、焊点体积的不可避免的制造误差及焊点位置的随机性,分析了器件自组装过程。通过求解不同体积焊点的形态,得到了不同体积焊点的液桥刚度曲线。基于不同体积焊点的液桥刚度曲线,仿真分析了焊点体积偏差率及焊盘直径对器件自组装成品率的影响。结果表明,焊点体积偏差率及焊盘直径的减小会增大焊点液桥刚度曲线的公共范围,从而提高器件的自组装成品率。
关键词:球栅阵列封装;成品率;焊盘直径;体积偏差率
0 引言
封装尺寸的逐渐减小及封装密度的不断增大使得自组装的过程很难通过肉眼观察。因此,如何保证自组装过程的可靠性、提高焊接成品率成为业界研究的重点问题[1]。由于当前大多主要封装都采用球栅阵列(BGA)焊点形式,故BGA焊点群的自组装可靠性显得尤为重要。
BGA焊点的桥连、开路及球窝(head-in-pillow,HIP)现象是PoP 封装的主要焊接失效形式[2]。球窝缺陷是由钎料的熔化和凝固温度不同步或界面污染造成的[3]。由于无铅焊接的温度高,而芯片封装体与基板的热膨胀系数(CTE)相差较大,故容易产生翘曲变形,从而导致在焊接组装中,桥连、开路焊接缺陷的发生率明显增加。但是,对于大多数封装形式,器件的翘曲变形是不可避免的。考虑焊点体积的不可避免的制造误差及器件的热翘曲变形,不同体积的焊点需要在器件的任意位置适应不同的器件翘曲变形量才能达到较高的焊接成品率[4]。
本文对电子器件自组装的整个工艺过程进行分析,考虑封装器件随温度变化的翘曲变形、焊点体积不可避免的制造误差以及焊点位置的随机性、自组装过程中不同位置焊点形态及受力的变化,通过数值仿真,分析不同体积焊点的高度范围及其对应的受力关系,为大量焊点的自组装的仿真分析提供参考。最后,分析焊点体积偏差率及焊盘直径对器件自组装成品率的影响,提出焊点液桥刚度曲线的共同范围hh的概念,为焊点自组装成品率提供直接分析指标,得到提高器件成品率的方法。
1 封装器件的自组装过程分析
1.1 考虑器件翘曲变形的器件自组装过程
因器件各层材料热膨胀系数存在差异,故器件会发生温度翘曲变形,以至于有些焊料液桥会承受拉力,而有些焊料液桥则承受压力。由于器件材料与印制电路板(PCB)热膨胀系数不同,PCB在再流焊过程中经受高的再流峰值温度时,器件基体因钎料表面张力的作用翘曲变得更严重。在室温下开始加热后,器件先是凹形翘曲[5];随着焊接温度的逐渐升高,器件封装体变软,伴随着钎料和BGA钎料球的熔融,钎料表面张力增大,拉动器件封装体周边向下坍塌;随着器件的冷却,器件会由凹形翘曲变为凸形翘曲。
再流焊接工艺过程中,器件在回流炉中按照设定好的回流温度曲线进行加热,当温度达到焊料的熔融温度时,BGA焊球及焊膏将会熔化成为熔融状态,在器件之间形成液桥群。在焊料液桥表面张力的作用下完成器件的自对准及自组装过程,当器件的所有焊点液桥承受的力的总和与器件自身的重力达到力平衡状态时,器件就达到了自组装平衡态,表达式为
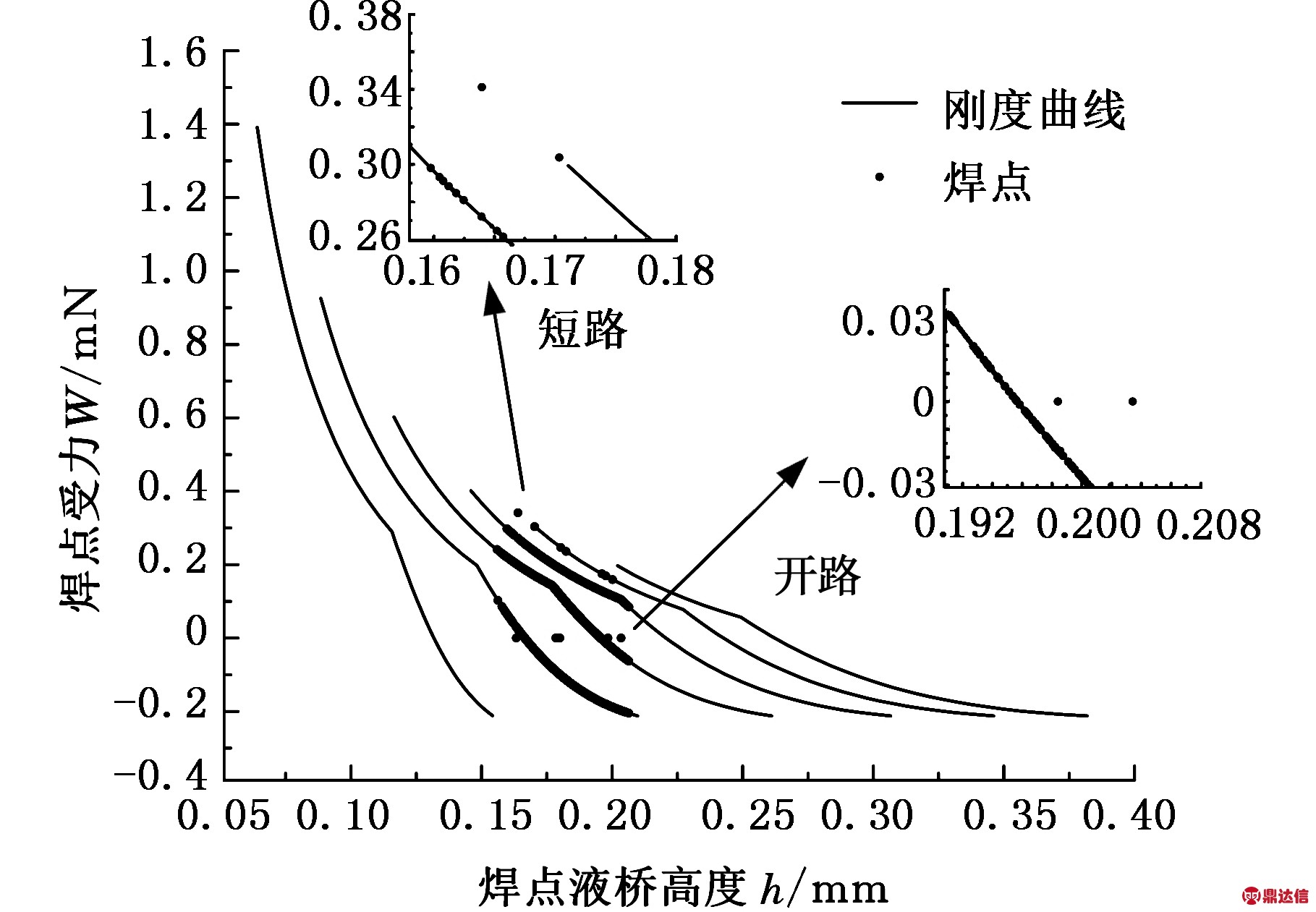
(1)
式中,G为器件的重力;W(i)为各焊点液桥所承受的力;N为焊点数。
达到自组装平衡态的器件经过降温冷却最终完成器件的自组装过程[6]。
当器件进入设定好的回流炉时,会经历升温区、预热区、回流区和冷却区4个阶段。在升温区和预热区时,焊料并没有完全融化,此时的焊点仍处于固态,并没有起到将芯片与PCB刚性相连的作用。当器件进入回流区时,焊料才能够完全进入熔融状态,完成芯片的自组装过程。进入冷却区后,焊点开始固化,将器件与PCB刚性连接。
在这个过程中,考虑到焊球的不可避免的制造误差及器件的翘曲变形,可能导致小焊点开路和相邻大焊点桥连的焊接缺陷。实验证明,钎料球发生开路及桥连缺陷的概率与焊接峰值温度有关。高于熔点的温度越高,产生桥连和开路缺陷的可能性越大。由器件的翘曲变形导致的焊点开路、桥连缺陷如图1所示。
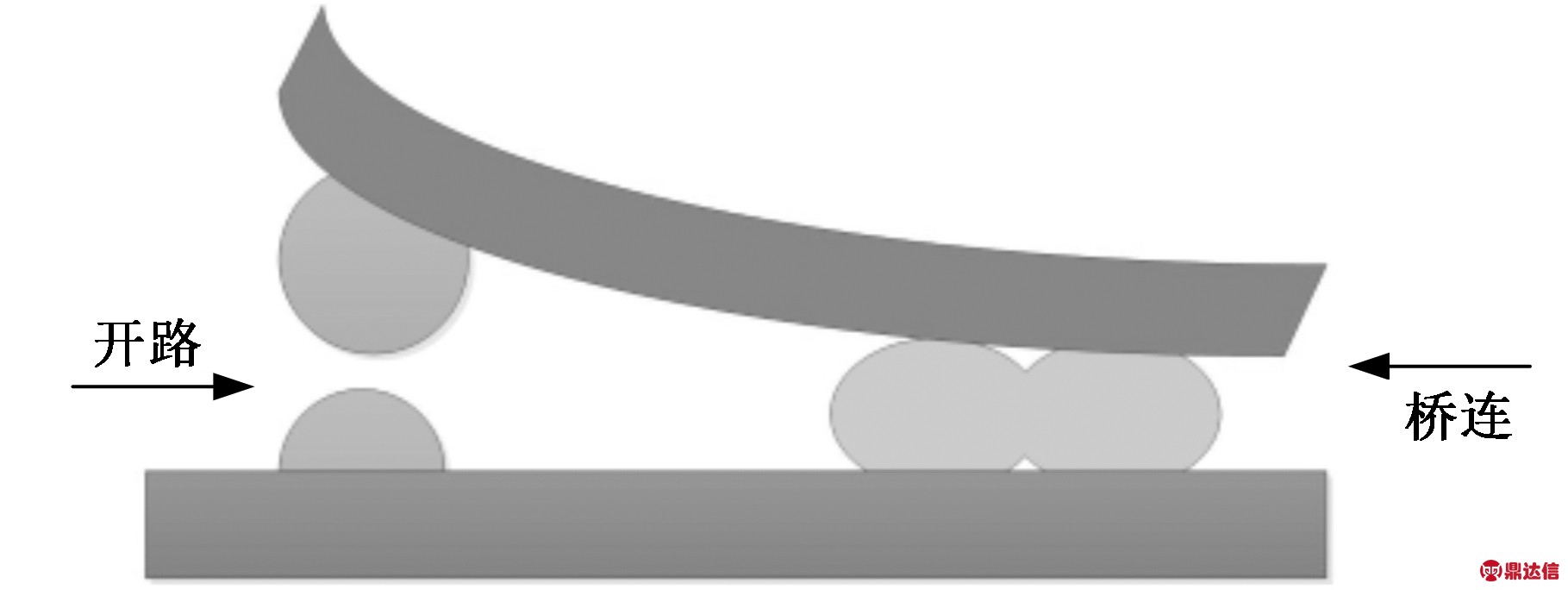
图1 焊点的开路与桥连缺陷
1.2 焊点体积偏差及焊点位置的随机性
PCB及芯片器件基板底部的BGA是由焊料金属液滴形态冷却固化形成的,需要采用锡膏印刷技术。在印刷模版上设计制作漏印网孔,用锡膏印刷机将焊膏刮压(或辊压)入漏印板网孔中,完成剥离印刷模版的脱模工序后,锡膏漏印粘结在基板焊盘上。在回流炉中加热后,焊剂液化、沸腾、挥发后,存留聚合在一起的金属焊料构成一定的金属液体焊球形态,金属不易挥发直至在固体平面上冷却为固化焊球。
引起 “不完全印刷缺陷”的因素很多,可用脱模后的实际印刷体积与理想漏印板孔容积的比值作为计量参数,称为填充率(或称为脱模比)。锡膏印刷机的工艺参数对锡膏刮入漏印板孔的填充率(脱模比)有影响,往往要通过试验反复调整修改才能最终确定工艺参数。锡膏印刷机技术的典型工艺参数有脱模时间、漏印模板厚度、刮刀速度、刮刀压力、脱模分离速度、脱模距离、刮刀倾斜角、印刷精度[7],它们对填充率产生影响,通过控制调整锡膏印刷机印刷工艺参数可以改善印刷效果。因锡膏有黏度,故脱模时可以将涂覆在网版孔壁的锡膏粘连带走。通常网版开孔越小,印刷速度应该越慢,才能保证足够的填充率,但过慢的速度会影响生产线节拍导致效率下降。
由于印刷机刮刀与漏印模版剥离脱模粘黏焊料存在随机性,故焊球的体积会有不可避免的制造误差。最大的体积偏差可能达到50%~60%。考虑到焊点在器件中位置分布的随机性,当体积小的焊点遇到翘曲量较大的位置,则容易发生开路缺陷;当体积较大的焊点分布在翘曲量较低的位置,则容易产生桥连导致短路。要提高器件自组装的成品率,就需要保证不同体积的焊点分布在不同的位置都能成功焊接。
在器件的自组装分析过程中,假定焊点体积在正常误差内以正态分布的规律分布,而每个不同体积的焊点对应在器件上的位置分布则是随机的,这样就可以模拟实际生产过程中的具体情况。按照焊点位置,对每个焊点进行编号,这样每个独立体积的焊点及位置就有了对应关系。
自组装过程,实际上是在回流炉中使焊点随着温度的变化,由固态变化为熔融状态将上下器件连接起来,再冷却为固态的一个过程。考虑器件的对称性,按照1/4器件进行仿真分析,在自组装的坐标系下,焊点液桥的间距如图2所示。
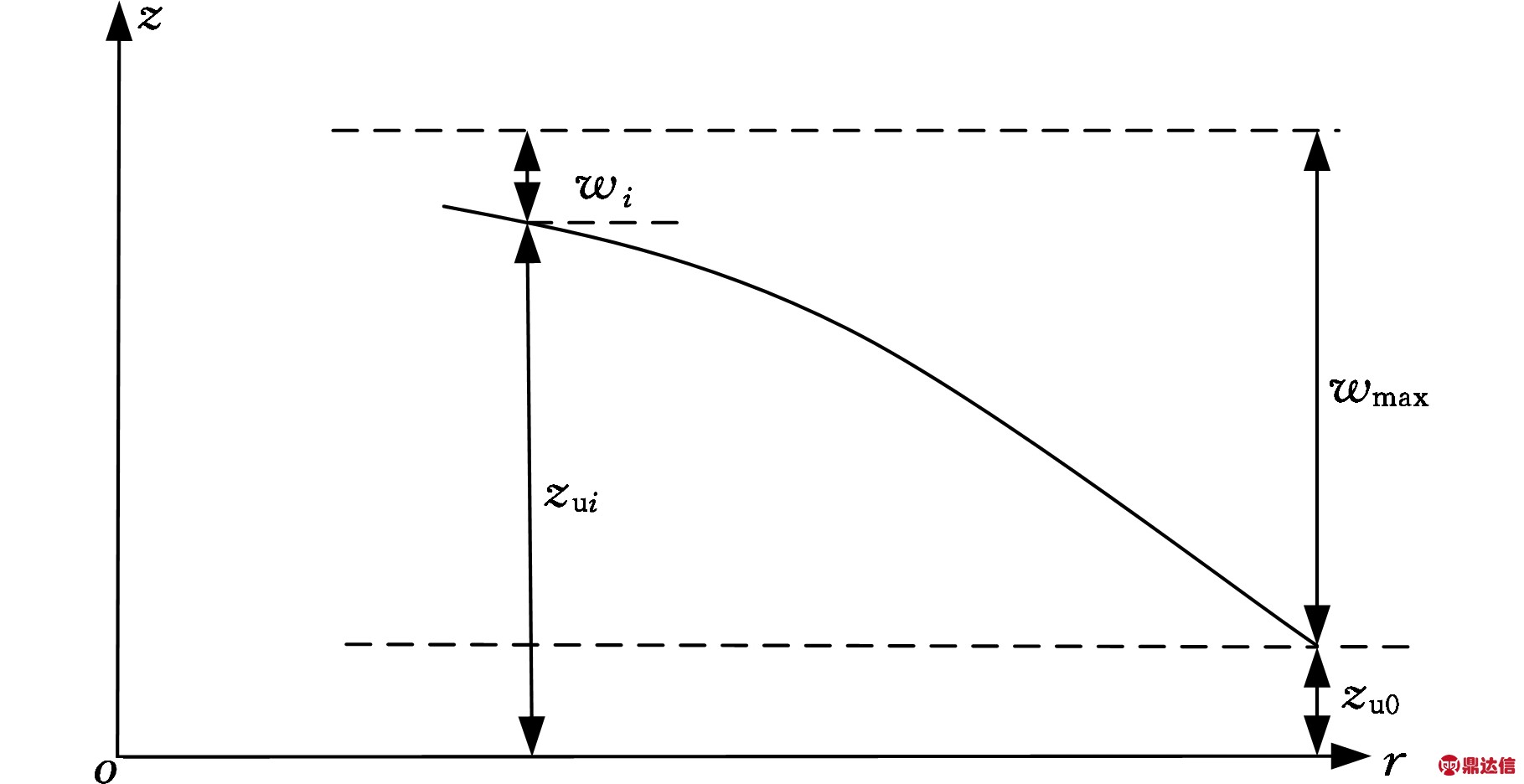
图2 翘曲坐标w与自组装坐标z的变换关系示意图
图2中,r为距器件中心的距离。每个单独焊点液桥的高度为
zui=wmax+zu0-wi i=1,2,…,N
(2)
其中,wmax为器件随温度变化的最大翘曲位移,wi为第i个焊点处的器件随温度变化的翘曲位移,zu0为自组装平衡位置,也表示着上器件翘曲变形位移最大的位置距下器件的距离。根据焊点位置的编号,找到所有对应位置焊点的体积,依据特定焊点体积下焊点受力与焊点高度的关系寻找能使式(1)达到平衡的自组装平衡位置zu0。
2 自组装成品率仿真分析
2.1 焊点受力与焊点高度的关系
Young-Laplace方程可以描述静态液滴在没有容器时的形态。在柱坐标系下 Young-Laplace 方程为
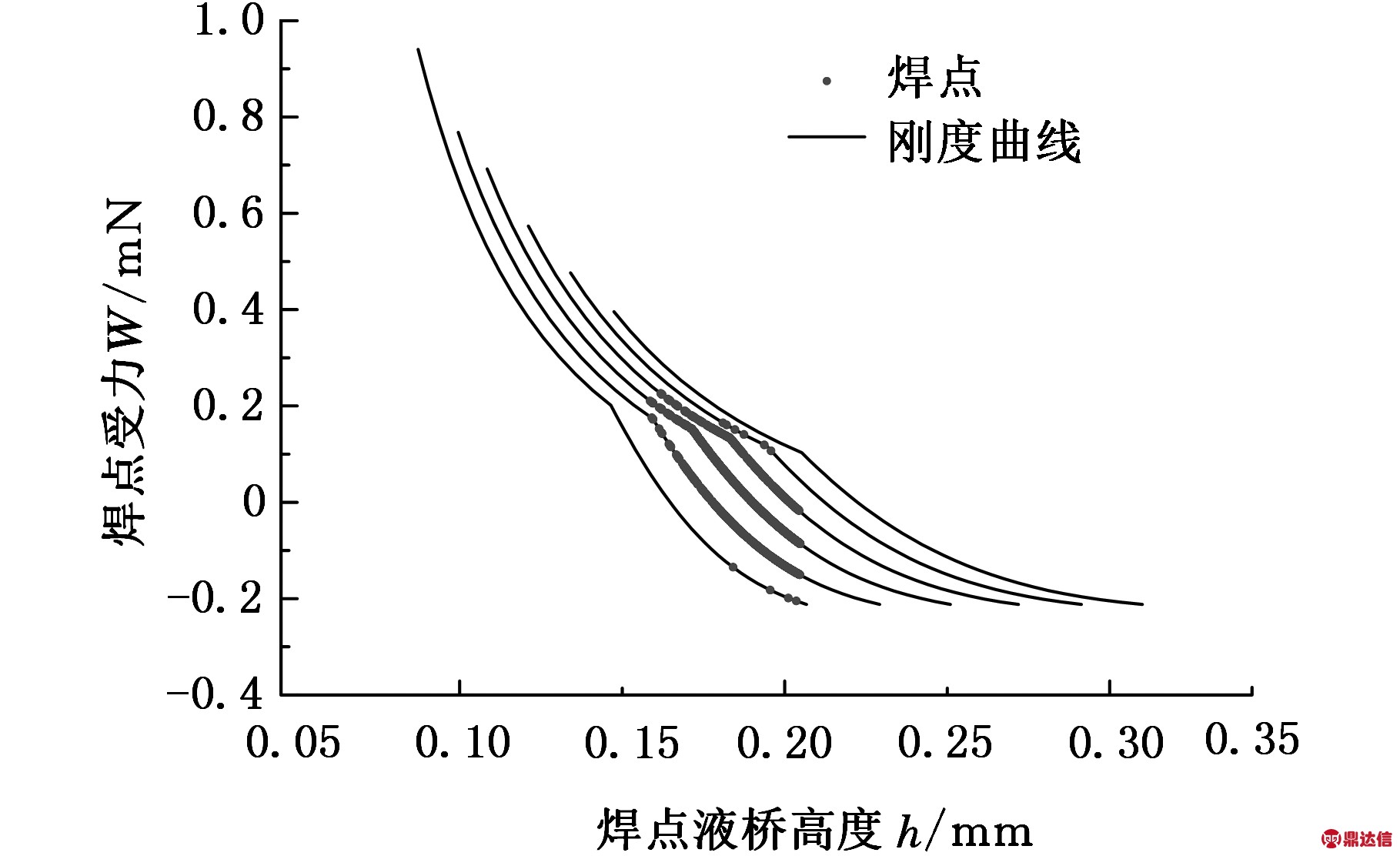
(3)
式中,ρ、ρ′分别为焊点液桥曲面的两个主曲率半径;p为液态焊点内部压力;T为焊点液桥的表面张力。
给定表面张力T、密度ρ0、焊点承载力W和焊点初始体积V0, 使用MATLAB软件通过龙格-库塔方法可以得到焊点的形态[8]。相同体积的焊点在不同的翘曲间距下,焊点的形态并不相同,同时焊点的受力也不相同。图3和图4分别为通过MATLAB软件求解得到的三维凹形焊点及三维凸形焊点。
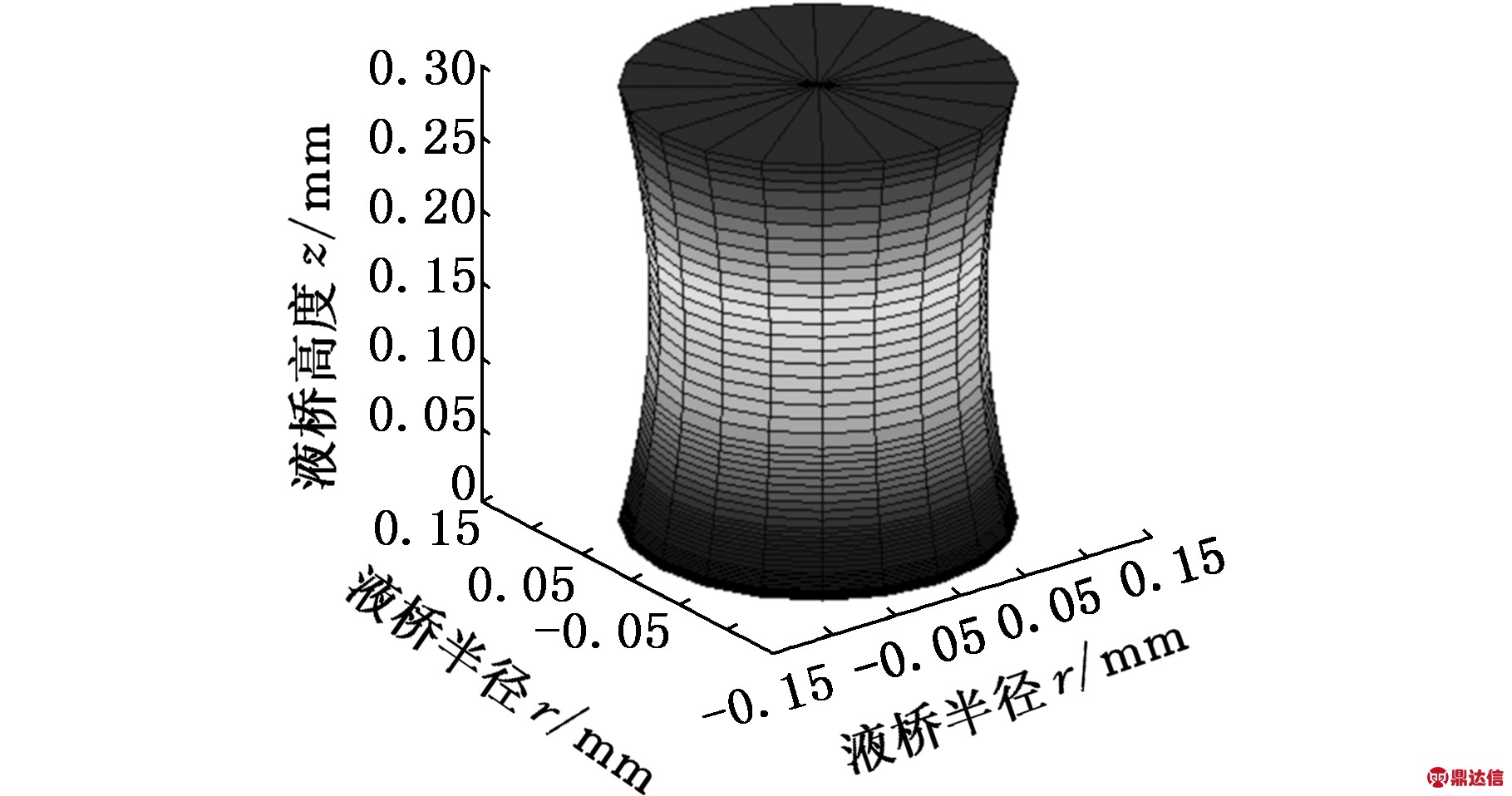
图3 三维凹形焊点形态
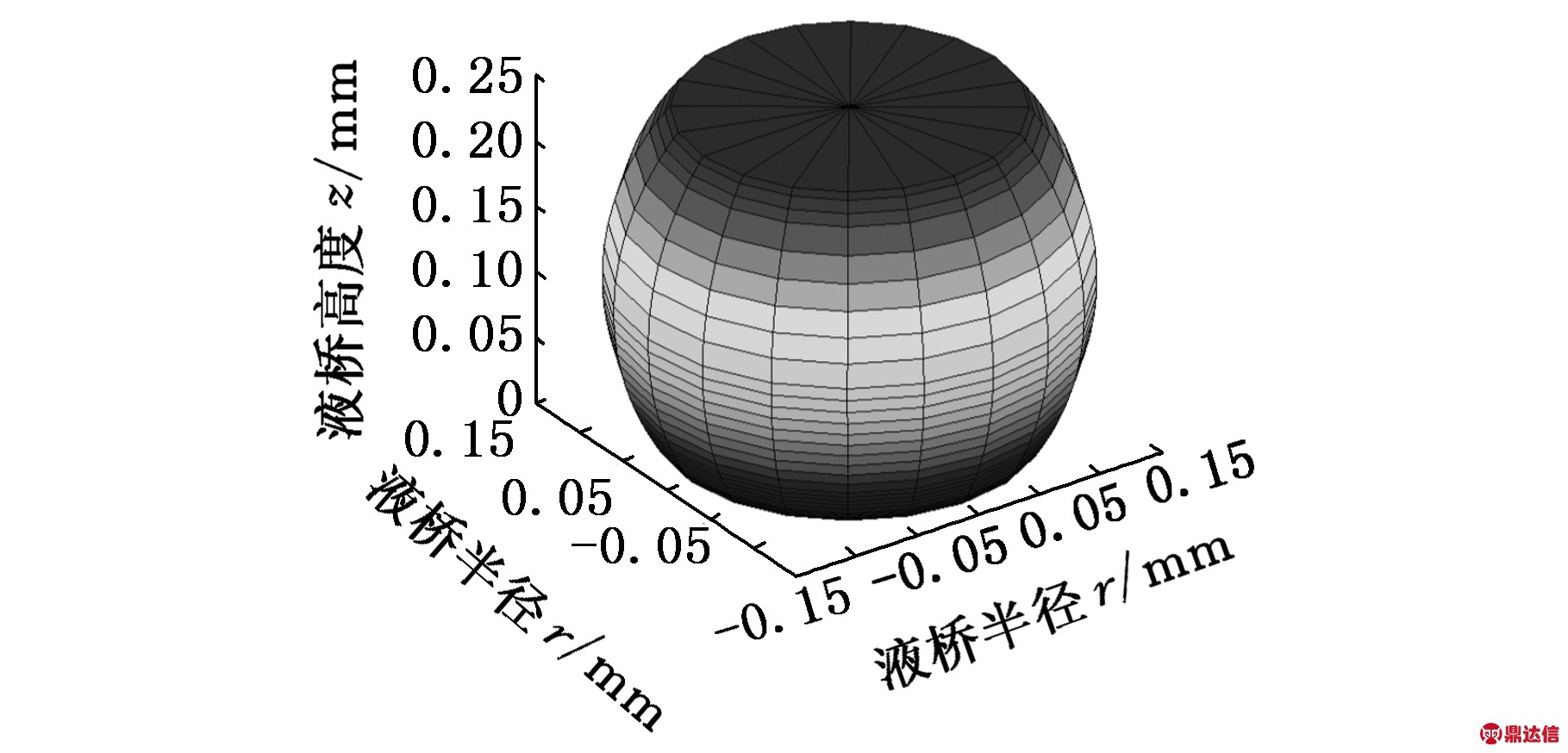
图4 三维凸形焊点形态
一个特定体积的液态焊点在不同的承载力下可以拥有无限种可能的形态。然而,由于焊盘等边界条件及节距的限制,它的最大高度和最小高度是有限的,通过求解不同高度的焊点的形态,可以得到焊点高度与承载力的关系曲线,如图5所示。
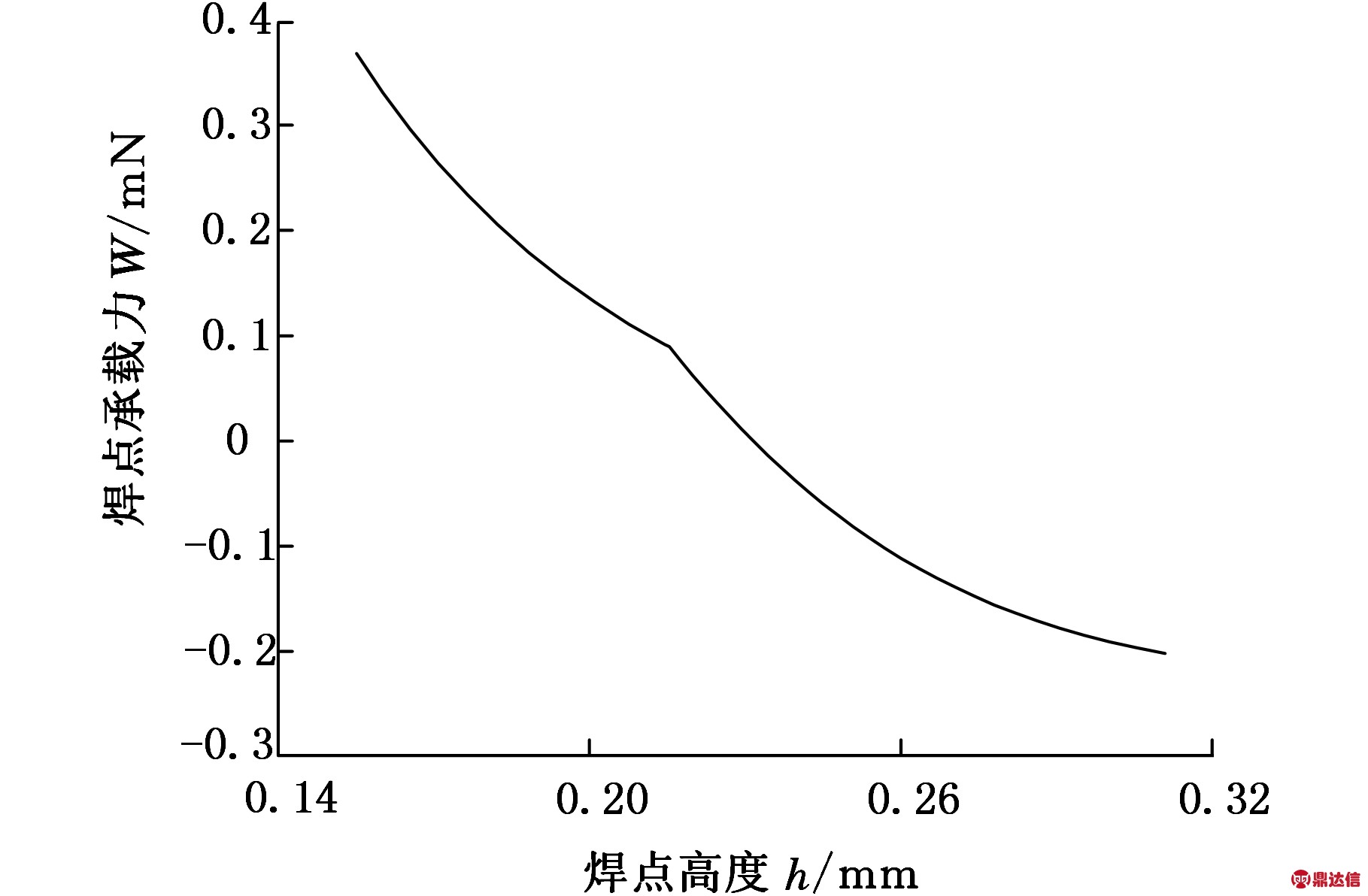
图5 焊点高度与承载力关系
在图5中,横坐标限制了一个特定体积的焊点在特定边界条件下的高度范围,对应的纵坐标则为对应高度时焊点的承载力。我们定义这个表征焊点高度与其承载力关系的曲线为焊点液桥刚度曲线。考虑到焊点体积的不可避免的制造误差,可以得到不同焊点体积的液桥刚度曲线,如图6所示。图6中的焊点液桥刚度曲线从左至右体积依次增大。
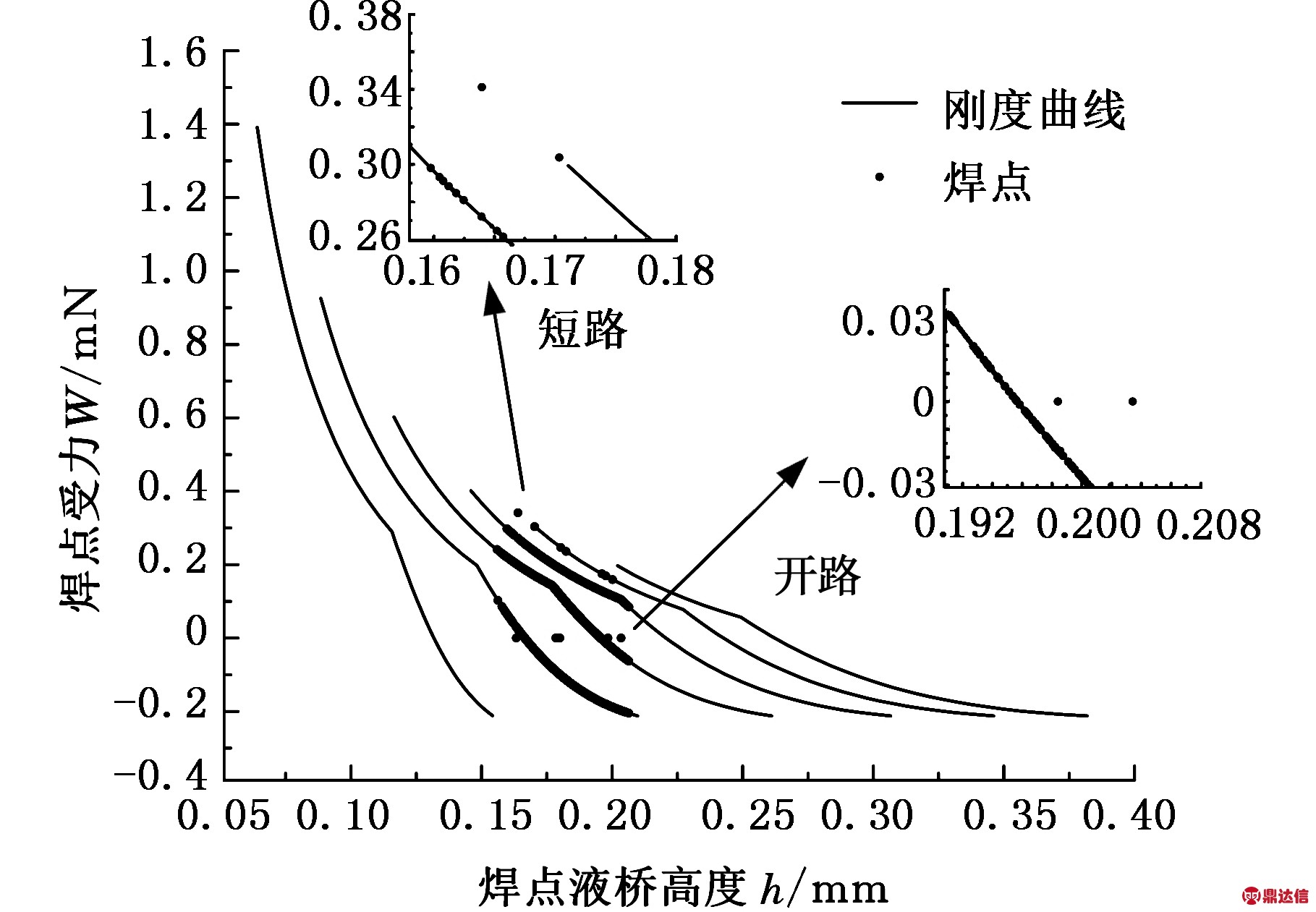
图6 不同焊点体积的液桥刚度曲线
由图6可以看出,焊点体积不同时,焊点高度的范围是不相同的,而图中hh为不同焊点体积的焊点液桥高度的共同范围。考虑到不同体积焊点的位置的随机性,这个焊点液桥刚度曲线的共同范围hh越大,器件的自组装成品率就越高。
2.2 BGA焊点体积偏差对自组装成品率的影响
本文对中兴通讯股份有限公司提供的某型号的封装器件的BGA焊点进行仿真分析,其封装节距为0.4 mm,其器件在固化温度下的最大翘曲变形量为58.1 μm[9]。
器件上分布着904个焊点。考虑器件的对称性,按照1/4器件进行仿真分析。焊点未知的分布如图7所示,器件的结构参数如表1所示。
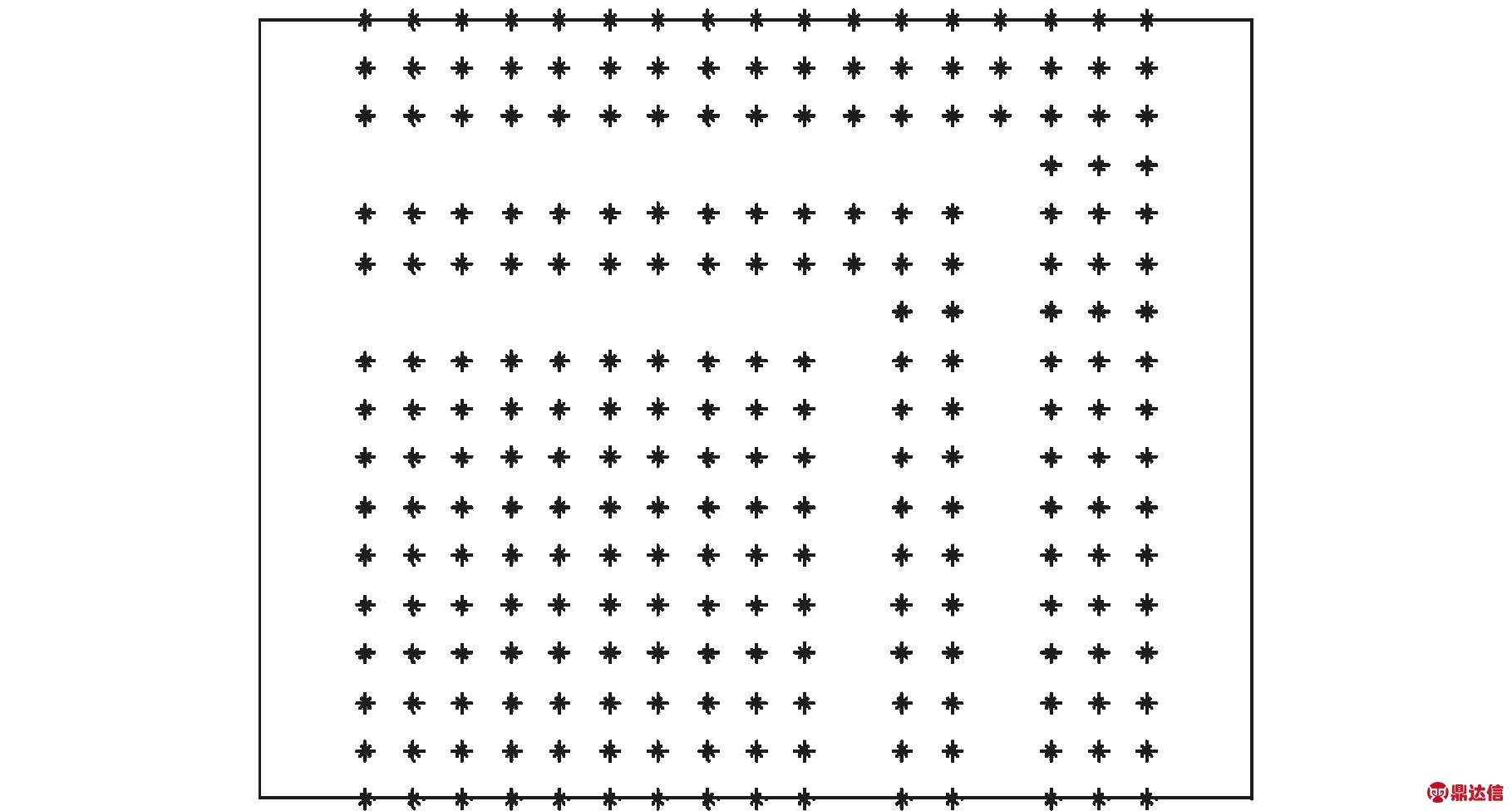
图7 1/4器件的焊点分布图
表1 仿真器件的结构参数

基于1.3节得到的不同体积焊点的液桥刚度曲线,由式(1)和式(2)可快速得到自组装结果。根据最后得到的自组装平衡位置zu0、各个位置焊点的体积及其对应焊点高度,可以在焊点液桥刚度曲线库中找到所有焊点对应的位置,如图8所示。由图8可以看出焊点体积的分布规律及焊点受力情况。如果焊点超出焊点液桥刚度曲线的范围,则认为焊点发生失效。当某个焊点超出该体积焊点液桥刚度左端边界时,认为该焊点被压至过低而发生短路;当某个焊点超出该体积焊点液桥刚度右端边界或受力为0时,认为该焊点被拉断而发生断路。此时会记录短路或断路焊点的位置编号。当器件中有焊点发生短路或断路失效时,认定该器件自组装失败。自组装失败时的各焊点的焊点高度及受力关系如图9所示。
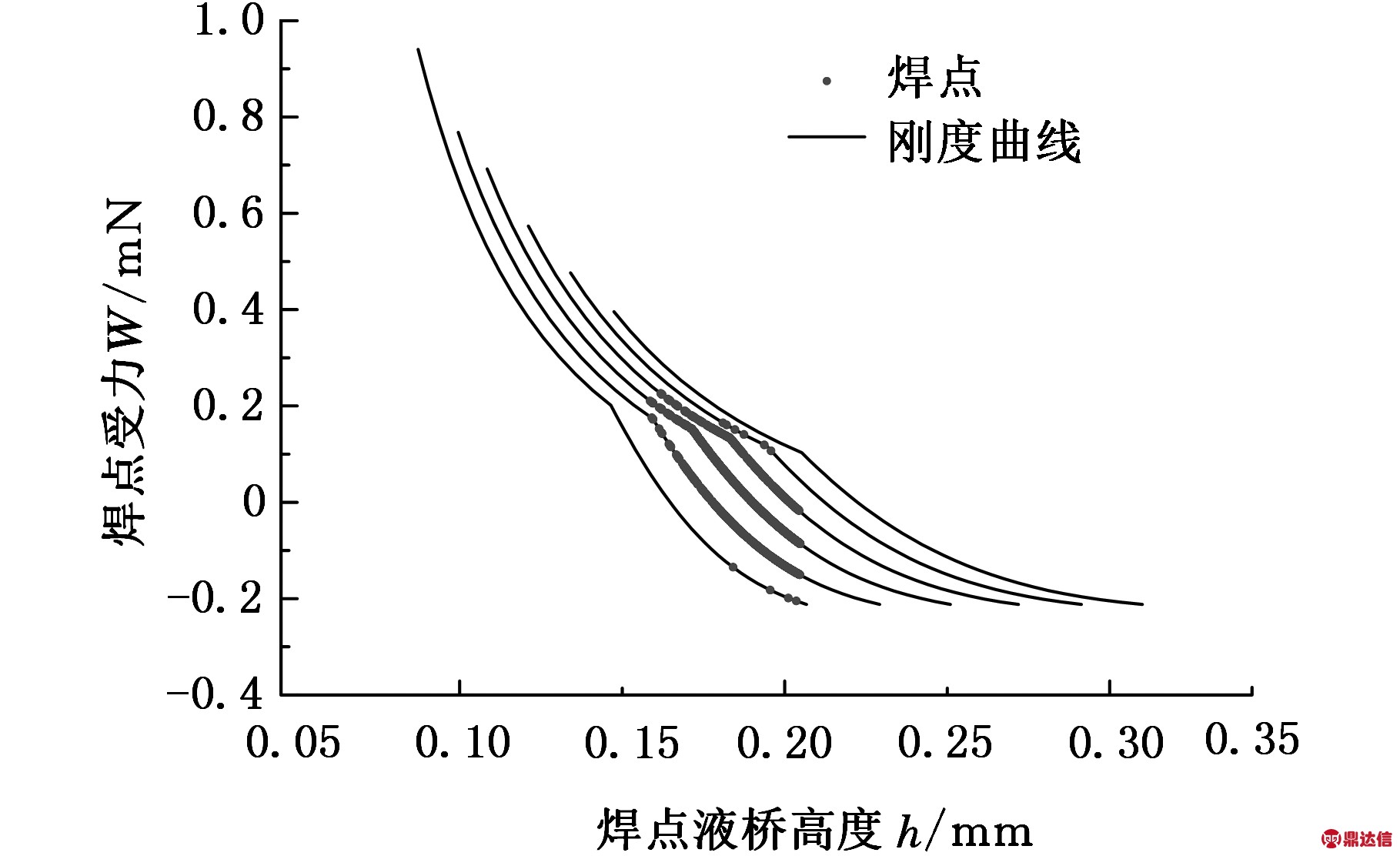
图8 各焊点的焊点高度及受力关系图
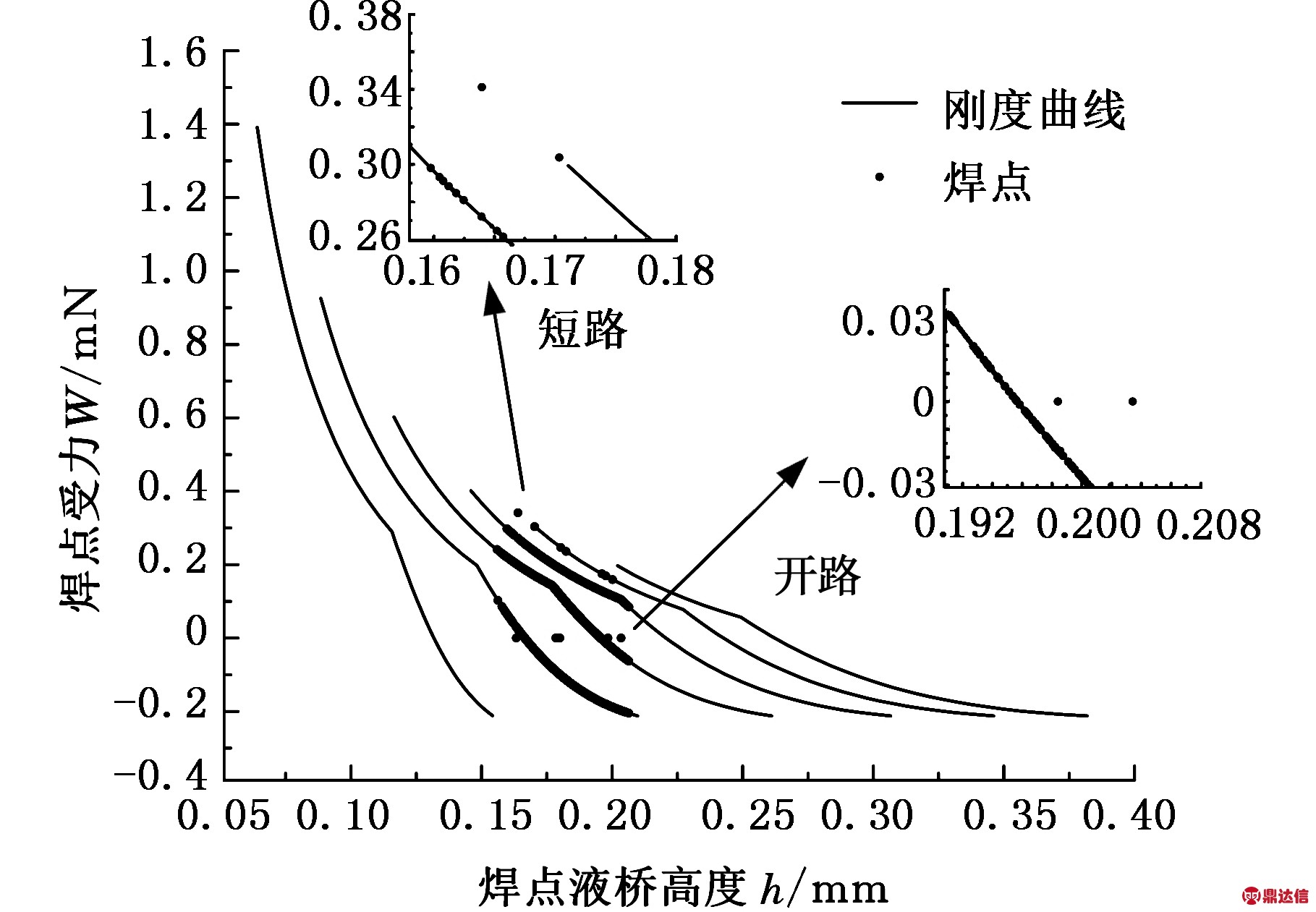
图9 失效器件自组装结果
表2为在焊点体积均值为1.4165×10-2mm3的不同体积偏差率下对1000个器件进行的自组装成品率分析的结果。其中,不同体积大小的焊点的分布概率按照正态分布的概率分布,不同体积大小的焊点的位置按照随机分布形式[10]。
表2 不同焊点体积偏差率的自组装成品率

由表2中的结果可以看出,随着焊点体积偏差率的减小,焊点液桥刚度曲线的共同范围hh逐渐增大,从而器件的自组装成品率也随之提高。可以看出,当焊点液桥刚度曲线的共同范围hh大于器件的最大翘曲变形量时,器件的自组装成品率将达到100%,这为焊点体积的控制提供了一个目标。
2.3 焊盘直径对自组装成品率的影响
焊点体积和焊盘尺寸都是在特定功能的器件设计完成之后可以设计的工艺参数,焊盘的尺寸对焊点的形态也有较大的影响,在焊点体积均值为1.4165×10-2mm3、最大焊点体积偏差为36.88%不变,改变焊盘直径的情况下对1000个器件进行的自组装成品率分析结果如表3所示。
表3 不同焊盘直径下的自组装成品率

由表3 的结果可以看出,当焊点体积偏差不可避免时,适当地减小焊盘的直径也可以增大焊点液桥刚度曲线的共同范围hh,从而提高器件的自组装成品率。
3 结论
(1)不同焊点体积的焊点液桥刚度曲线的共同范围hh对器件自组装成品率起着决定性作用。当hh大于器件的最大翘曲变形量时,器件的自组装成品率可以达到100%。
(2)焊点体积偏差率对器件的自组装成品率有着显著的影响。提高工艺水平,降低焊点体积的最大偏差率,可以增大焊点液桥刚度曲线的共同范围hh,从而提高器件的自组装成品率。
(3)焊盘直径对器件的自组装成品率也有着明显的影响,焊点体积偏差率不变的情况下,减小焊盘直径可以提高器件的自组装成品率。
(4)该方法为工艺参数的匹配提供了改善方向,可通过该方法对更多工艺参数进行仿真分析。
(5)该方法可对不同封装尺寸类型的产品提供一种理论设计方法。对于不同封装尺寸类型的器件,其翘曲变形量及焊点液桥刚度曲线库会有所不同,需重新计算,但是方法具有通用性,可以降低试验成本,提高成品率。