摘 要:深沟球轴承铆合模通常采用上、下模所有兜孔全定位,下模顶销三、四点拔模设计。由于铆合模兜孔加工需要使用坐标磨设备,属于模具加工中耗时最长工序,制约了模具的加工能力,影响了轴承生产。经过研究,采用新型设计理念,解决了此问题,满足了使用需求。
关键词:深沟球轴承;铆合模;保持架;优化设计
1 前言
深沟球轴承铆合模是深沟球轴承在装配时必不可少的工装。铆合模的质量影响轴承的外观、手感、旋转灵活性等装配质量。铆合模通过兜孔与保持架的全R面定位,将深沟球轴承外圈、内圈、滚动体、保持架组合在一起。铆合模加工精度要求高,加工难度大,加工周期长,返修难度大。
2 保持架的形式
浪形保持架可以通过自动冲压加工成型,效率高,能满足深沟球轴承的需求量。铆合模主要用于铆合带铆钉的浪形保持架,这种保持架为低碳钢板冲压成形,两半浪形保持架相对安装,通过铆钉铆接成一体。
3 原铆合模加工方法
(1)备料。
(2)车工:凸台小外径按大球窝中心径加一个球窝直径尺寸再加大3~5mm加工。止口大球窝按中心径减去一球窝尺寸再减2~3mm加工,两端面留两次磨量,每批活外径相互差0.2mm。
(3)平磨:磨两平面,留0.4~0.8mm。
(4)径磨:统一外径,每批相互差0.01mm。
(5)坐标镗:镗各导柱孔留0.2~0.3mm磨量。
(6)等分车:上等分模具,以导柱孔定位,车等分大小球窝留磨量,等分窝荒合样板。加工好一组后,再用另一组导柱孔定位,加工好其余球窝。
(7)钳工:去刺,打字。
(8)热处理:58~62HRC。
(9)平磨:磨两平面,平行差0.02mm。
(10)坐标磨:等分球窝找正,磨好各导柱孔。
(11)球磨:导柱孔定位,磨各等分球窝。
(12)线切割:等分球窝找正,切割好外形。
(13)平磨:磨好两平面。
4 对比分析
4.1 原铆合模的优点及不足
原铆合模设计理念为多个定位兜孔共同定位,使铆合模在正常工作的情况下,能完好地固定保持架,将保持架铆合后,可以满足设计及使用要求。多个定位兜孔的优势在于定位准确,保持架窜动量小,铆钉位置固定准确,铆合后质量合格,保证要求的旋转灵活性,外观目测较好,达到产品使用要求。原铆合模要求采用多个定位兜孔共同定位,且使用全R面定位,定位精度高,因此,加工定位孔时采用等分球磨,对球面车及球面磨精度要求较高,且由于兜孔为定位表面,要求粗糙度较高,使加工周期过长,而高精度则会导致返修的困难。原铆合模如图 1。
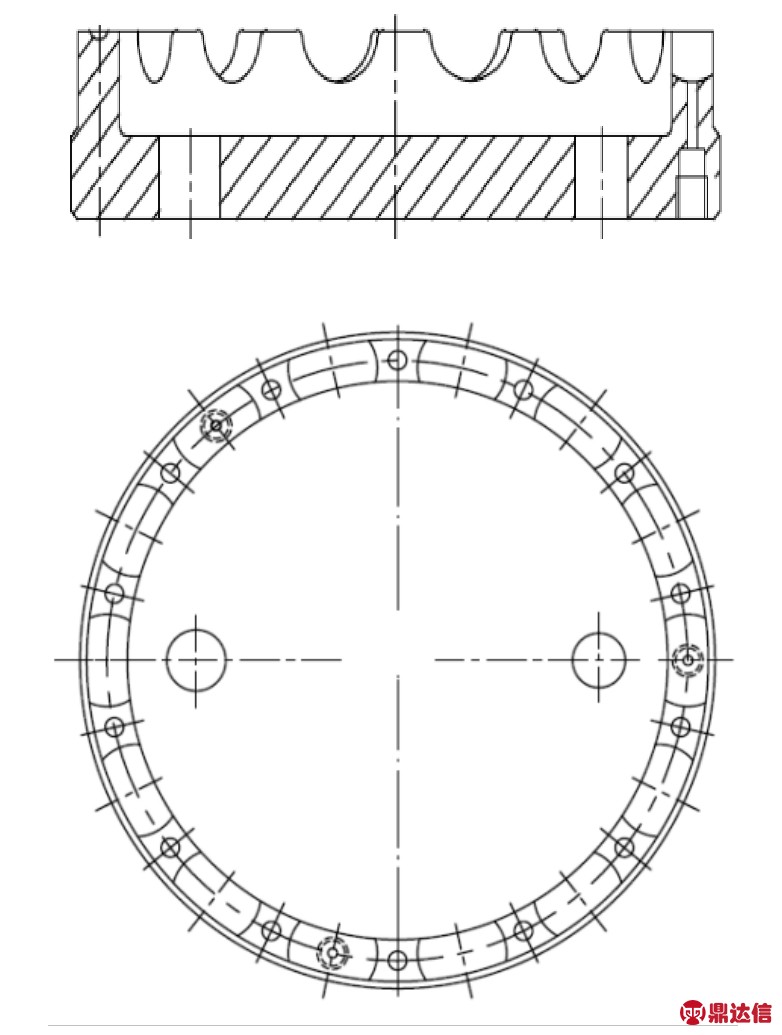
图 1 原铆合模设计图
4.2 改进后铆合模的加工方法
采用改进后的工艺方法加工铆合模时,加工半R面用于定位轴承,即在兜孔底部加工一个通孔,从而使得由原来加工全R面定位孔,变为加工半R面定位孔,且非定位兜孔尺寸与公差适当加大,使加工铆合模的难度下降,并且减少定位兜孔,仅通过加工一小部分定位兜孔,就可以保证铆合模的正常使用,避免了因加工过多的定位孔而导致的加工难度高、加工时间长等问题。将三、四点拔模优化为固定三点拔模,减少了因设计四点拔模需多加工一个通孔的问题,增强了铆合模的稳定性,节约成本,减少加工时间。设计图见图 2。
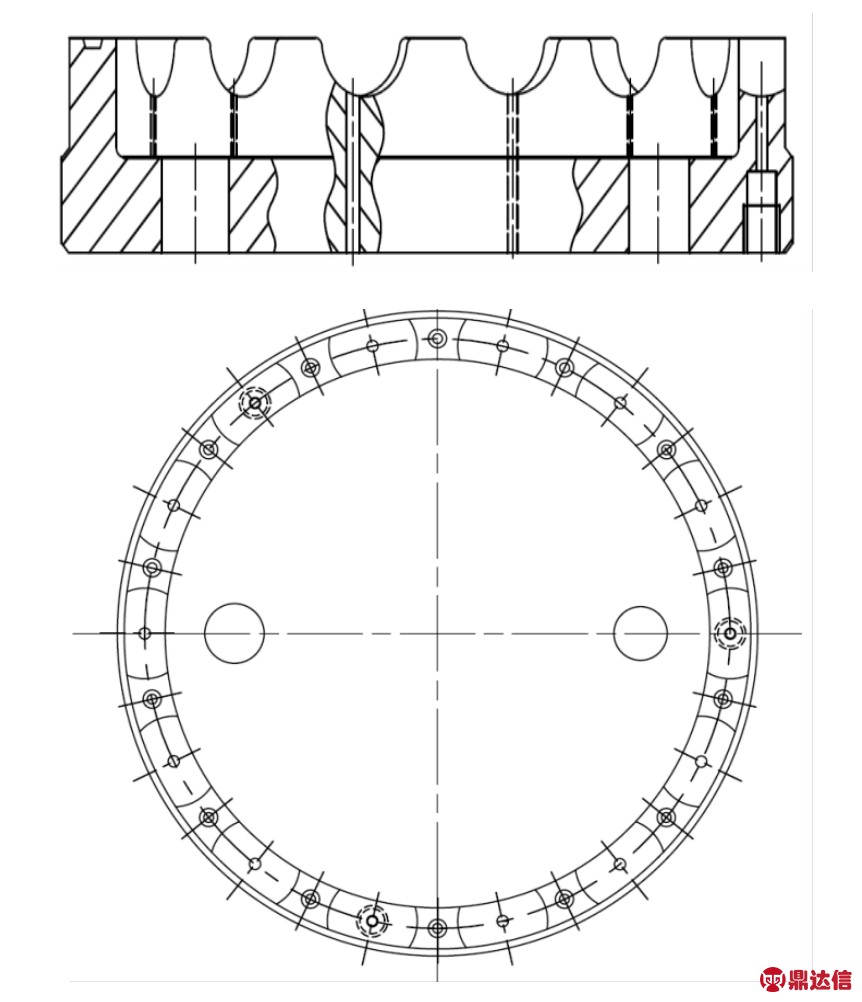
图 2 改进后的铆合模
5 改进后的铆合模的优势
(1)减少了兜孔R面的加工面积,使得从原本加工全R面降为加工半R面,加工球面更加简单化,降低了因加工全R面所带来的难度,提高了工作效率,降低了加工成本。
(2)通过精确的计算,合理确定顶销相关尺寸,将原来设计的三、四点拔模统一更改为三点固定拔模,确保了铆合模在拔模时的正常使用,试验效果良好。
(3)减少定位兜孔的数量,由原来所有兜孔共同定位,降低为1/3~1/2兜孔定位,经过精确的计算,既减少了定位兜孔,又不影响铆合模的定位,而且降低了铆合模的加工难度,缩短了加工时间,提高了加工精度。
(4)减少了模具兜孔磨损后的返修工序,仅返修少量定位兜孔,即可使铆合模正常使用,避免了因铆合模返修而影响加工进度。
6 试验结果
改进后的6220轴承铆合模,在铆合轴承保持架时,未出现不合格产品,外观达到成品要求,旋转灵活性正常,拔模效果良好,未出现卡顿现象,在正常批量使用中,未出现因定位兜孔减少,导致兜孔磨损增加、返修率高的现象。本次试验成功。
7 结束语
通过新思路设计的铆合模,解决了原铆合模加工周期过长,加工难度大的问题,节省了加工成本,使用效果良好,保证了铆合模的正常使用。