摘要:针对J201系列车型开发中,分离叉在试验和在其它前期车型使用中均发生多次损坏问题,通过对试验损坏的分离叉进行受力结构分析、断口分析和材料理化检验,确定分离叉断裂主要原因与分离叉断裂部位脆性大有关,即分离叉球窝处渗层部位马氏体组织异常粗大是导致分离叉断裂的主要原因。通过对分离叉热处理工艺的改进使分离叉满足了使用要求,通过了试验验证。
关键词:分离叉 失效分析 马氏体 热处理
1 前言
J201系列轻型车分离叉采用低碳钢板冲压成型工艺加表面渗碳淬火工艺,该工艺制造的分离叉既降低成本又减轻了质量,但是该工艺分离叉在前期试验使用中发生多次损坏,需要分析解决断裂原因,本次检验分析的分离叉就是众多早期损坏试验件之一。
2 分离叉宏观及断口分析
2.1 受力结构分析
分离叉模拟试验装置见图1,分离叉在两端和中间球窝处三点受力,以中间球窝处为支点,通过一端的上下移动带动另一端上下移动。断裂分离叉宏观形貌见图2,断裂就发生在中间球窝处。
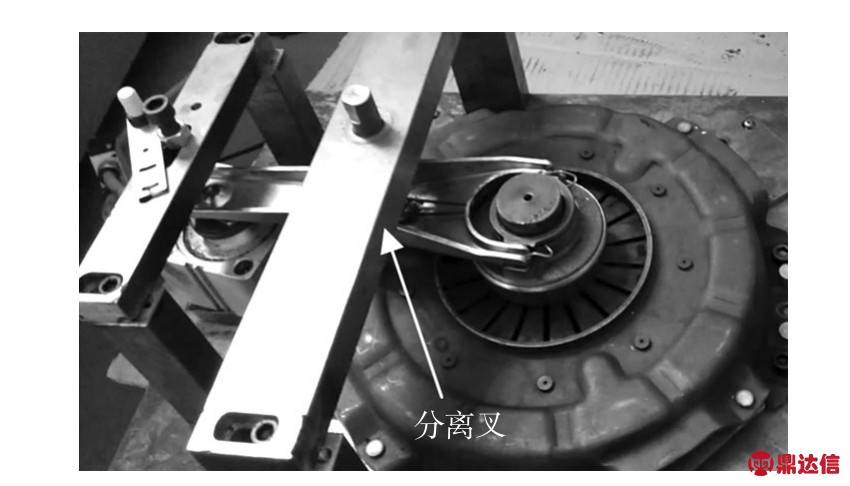
图1 分离叉装配效果示意图
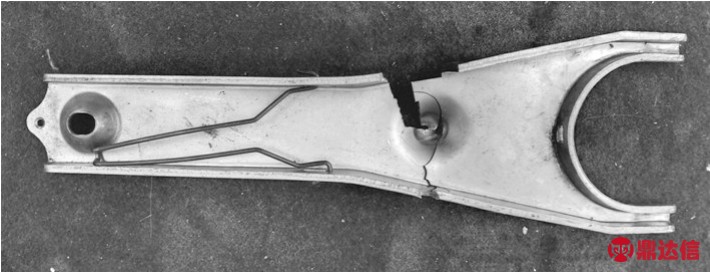
图2 分离叉宏观形貌和开裂位置
2.2 宏观形貌分析
检查断裂分离叉表面发现,在分离叉主断裂面附近上、下表面均存在多条裂纹,见图3a,根据对横断面观察,这些裂纹产生于表面止于心部基体,在分离叉板厚度方向没有贯穿,说明分离叉表层脆性较大。在分离叉中间球窝处的磨损工作面有多条弧形小裂纹,见图3b,将两个断裂的分离叉拼接到一起,这些弧形的裂纹呈现出以接触中心为原点的椭圆形裂纹,见图3c,说明这些裂纹产生于断裂之前,这些裂纹的产生是由于分离叉表面渗层部位脆性大而心部较软,在表面受到较大压力而产生。中变色。分离叉其余部分断口为横向断口,断口有明显的分层,这与分离叉表面渗碳硬化层有关,该部分为终断口,见图5。
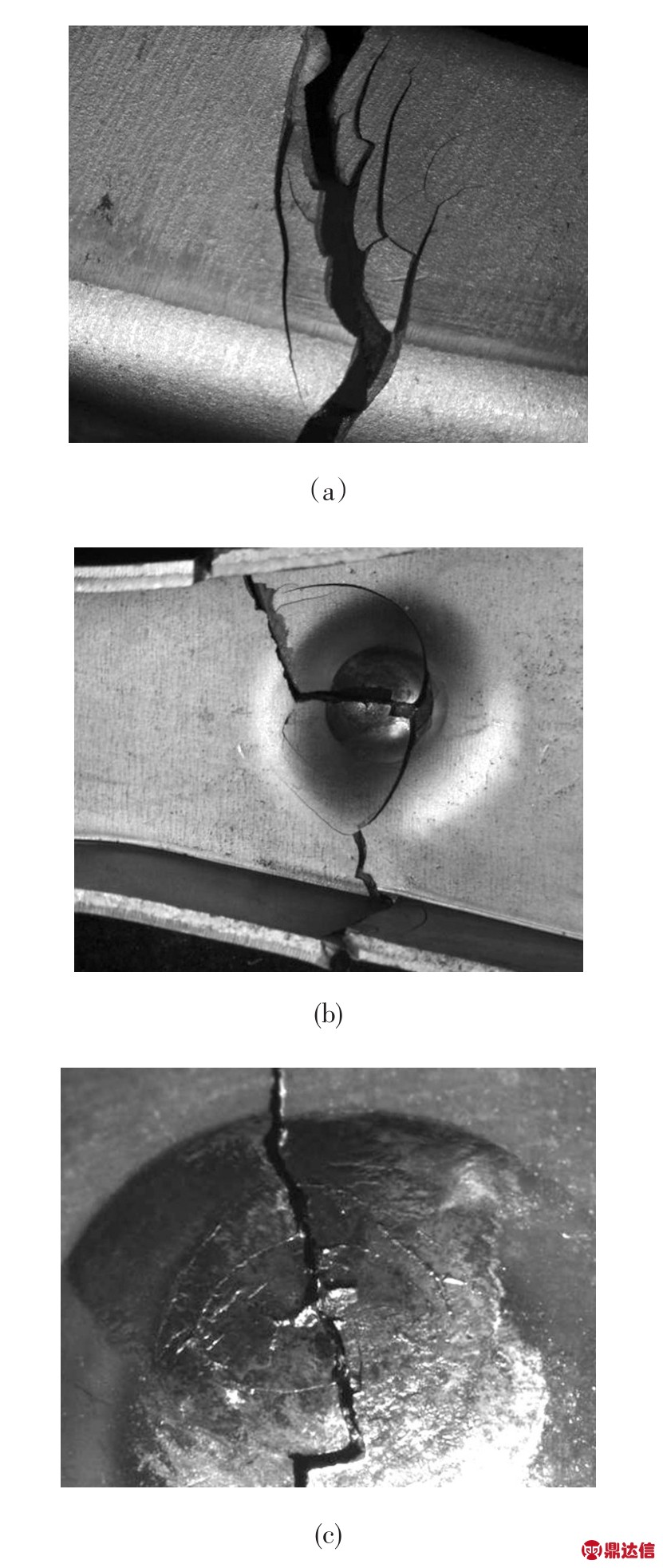
图3 分离叉开裂位置局部形貌观察
将分离叉早期(纵向)开裂部位纵向断口在扫描电镜下观察,断口以沿晶为主,且晶粒非常粗大,见图6。
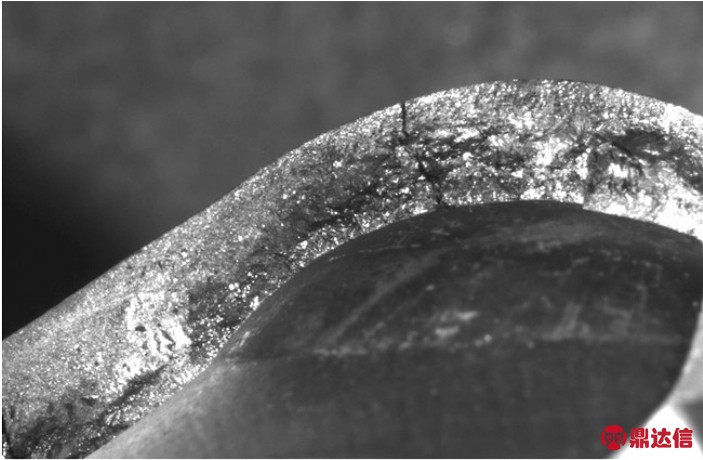
图4 分离叉纵向断口
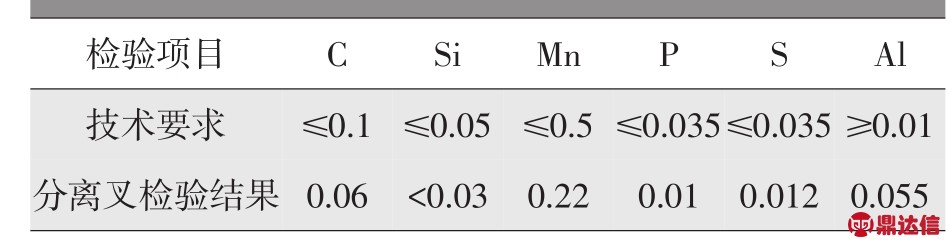
图5 分离叉横向断口
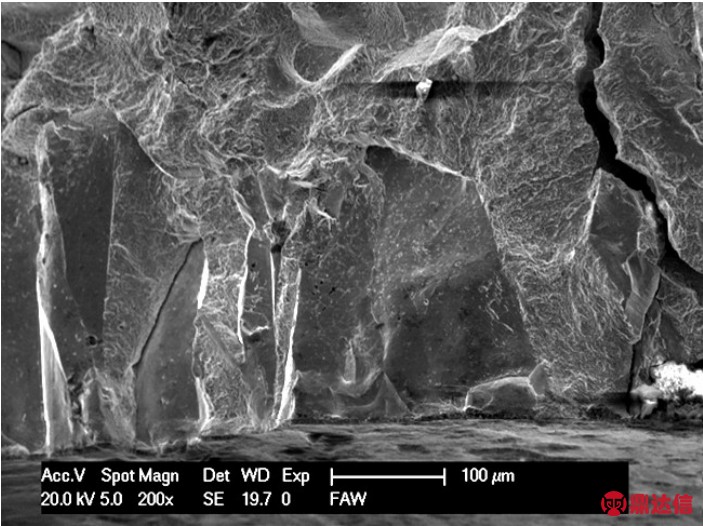
图6 分离叉纵向开裂处微观断口
3 理化检验
3.1 元素含量检验
采用金属材料元素分析仪(光电直读光谱仪),依据GB/T 4336-2002《碳素钢和中低合金钢火花源原子发射光谱分析方法(常规法)》标准进行元素含量检验,检验结果如表1所示。从表1中可以看出,分离叉材料元素含量符合技术要求。
3.2 金相组织检验分析
在分离叉断裂的球窝处取样,依据GB/T 13298-2015《金属显微组织检验方法》标准进行检验。分离叉表面金相组织为粗大的马氏体组织,呈柱状形态,由表面向心部生长,长度贯穿整个渗碳层,见图7。这种组织的产生是由于加热温度不足的亚温状态,粗大的低碳铁素体没有奥氏体化,但随着表面碳含量的增加而区域性地进入奥氏体转变区;分离叉表面层与心部过渡区局部有异常粗大的铁素体晶粒,见图8。造成这一现象的原因是分离叉在冲压时各部位冷变形不均匀,某些部位变形量正处于临界变形范围内,导致晶粒异常长大[1],在随后的热处理加热保温时导致马氏体异常长大。
表1 分离叉元素含量检验结果 wt%
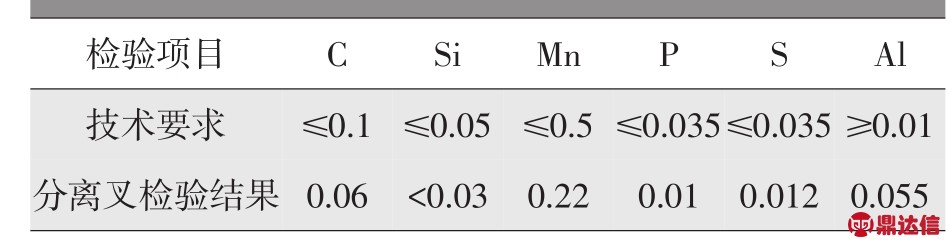
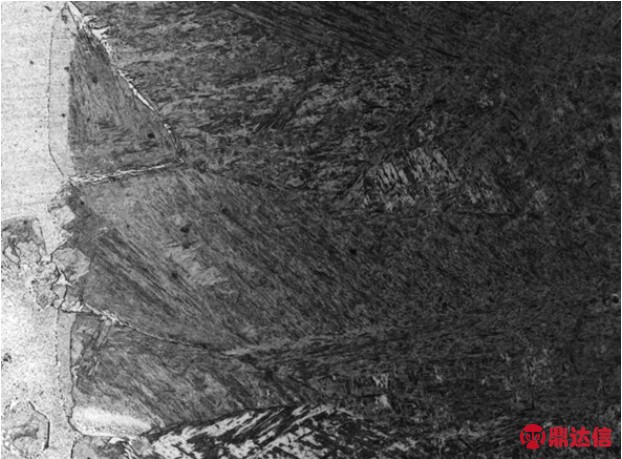
图7 分离叉表面金相组织
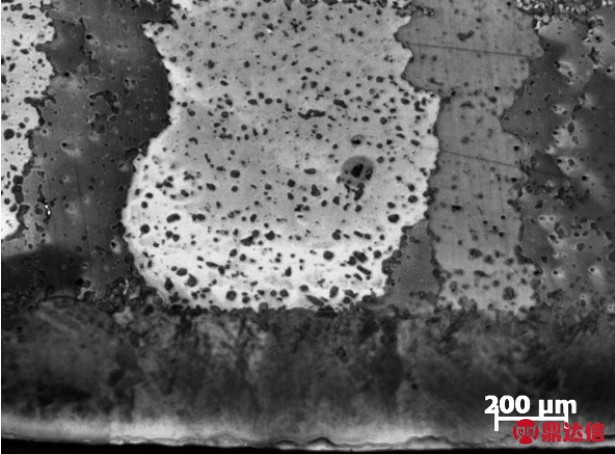
图8 分离叉局部过渡区金相组织
3.3 硬度及硬化层深度检验
在分离叉断裂的球窝处取样,依据GB/T 9450-2005《钢件渗碳淬火有效硬化层深度的测量和校核》标准进行检验。检验结果如表2所示,从表2中可以看出,分离叉材料硬度及硬化层深度符合技术要求。
表2 分离叉表面硬度及硬化层深度检验结果
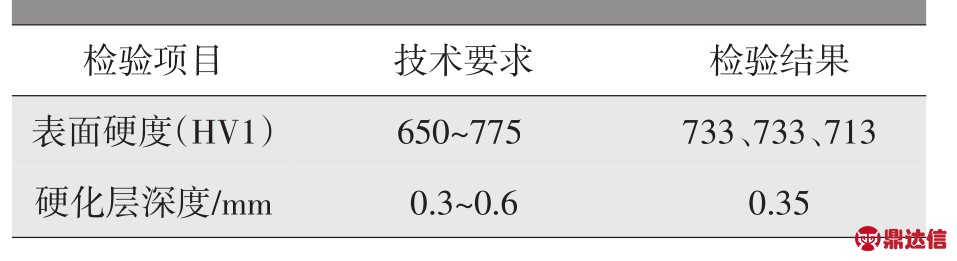
综合以上分析可知,分离叉断裂主要与表面渗层部位脆性大有关,分离叉表面马氏体组织异常粗大是导致分离叉断裂的主要原因。
4 分离叉的工艺改进及试验验证
根据分离叉断裂原因,从分离叉的热处理工艺上进行两种改进方案如下:
a.方案1,采用渗碳后空冷,二次加热淬火的工艺,材料选取SS400;
b.方案2,提高渗碳温度和缩短渗碳时间,材料选取SS400。
4.1 改进后分离叉的试验结果
对两种改进方案的分离叉和原分离叉进行静态疲劳试验,结果如表3所示,由表3可看出,原工艺分离叉的试验次数只有12万次,两种改进方案后的分离叉试验次数均通过200万次未断裂,大大提高了分离叉的静态疲劳试验试验次数,满足了使用要求。
表3 改进方案后的分离叉和原分离叉静态疲劳试验检验结果
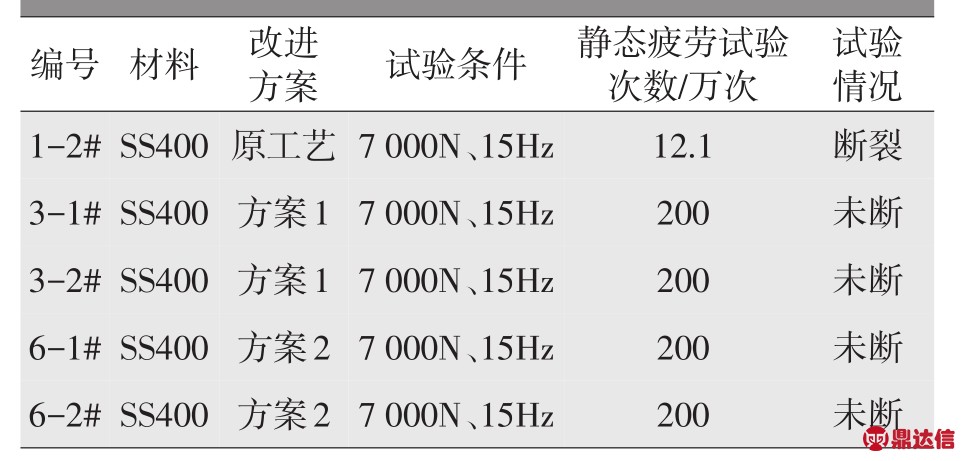
4.2 两种改进后分离叉的理化检验结果
表4是两种改进方分离叉的金相组织、硬度及硬化层深度检验结果,由表4可以看出,两种改进方案结果差别不大,方案1的表面金相组织更细一些,但都较原工艺表面组织有极大改善;两种方案处理出来的分离叉表面硬度均偏高,但这不是分离叉寿命提高的原因,两种方案均大大细化表面表4 改进后分离叉表面硬度及硬化层深度检验结果金相组织,降低表面渗层部位脆性才是分离叉寿命提高的真正原因。
?
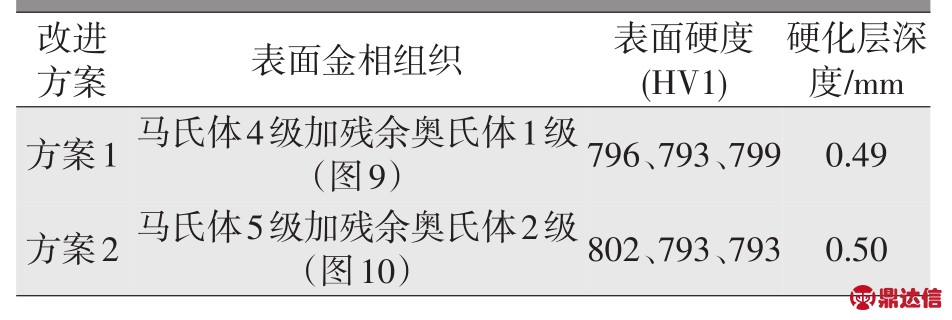
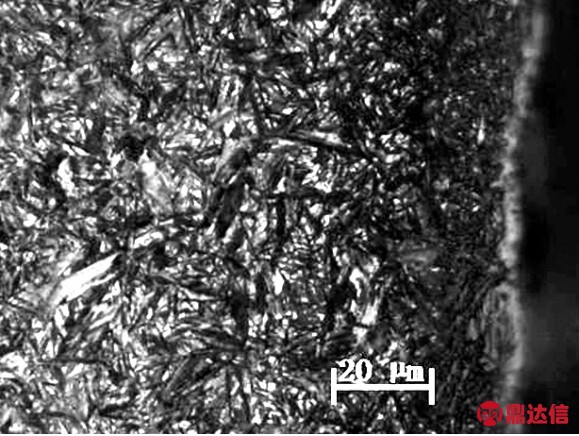
图9 方案1分离叉表面金相组织
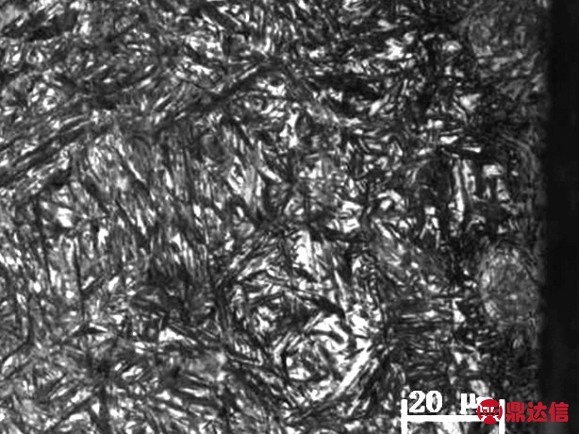
图10 方案2分离叉表面金相组织
对比以上试验结果,虽然方案1和方案2均能通过静态疲劳试验要求,满足使用要求,但考虑到方案1需要增加一次淬火工艺,增加零件成本,因此建议采用改进方案2。
5 结束语
针对轻型分离叉在试验和前期车型使用中均发生多次损坏问题进行失效分析,并进行了相应的改进,通过试验验证得出具体结论如下:
a.分离叉球窝处组织异常粗大导致该部位脆性大是断裂的主要原因。
b.分离叉在球窝处由于变形大,在随后的热处理中导致该部位的组织异常长大,是导致该部位组织异常粗大的重要原因。因为分离叉其它部位相对较好,同时对金相组织又没有明确要求,所以导致检测分析人员没有发现该分离叉组织异常。
c.经过对分离叉的失效分析和改进试验验证后,和相关设计人员一同对分离叉的检测部位和技术要求进行了更改,并要求供货厂家按此要求执行,分离叉再没发生断裂现象。