摘 要:为了改善高压叶片泵的性能,提升配流副的摩擦特性,采用理论分析、数值模拟和试验测试的方法,研究配流副油膜不同部位的温升情况。首先分析了吸油区和排油区的内、外层区域油膜油液运动情况,建立油膜温升的计算模型。然后从理论计算结果、温度场数值模拟云图和试验测试结果进行分析讨论。结果发现,高压子母叶片泵配流副油膜的温升受到工作压力和油膜厚度的影响,油膜厚度一定时,油膜温升值随压力的增大而增大,而工作压力一定时,油膜温升值随油膜厚度增大而减小。配流副吸油区油膜的内外层区域的温升值不一样,外层区域油膜温升值比内层区域高0.5~1 ℃。相同的工作压力下,由于受到剪切流动和较大压差流动的共同作用,吸油区油膜温升值比排油区油膜温升值高1.5~3.5 ℃。排油区外层区域的油膜温升值比内层区域的高,内外层区域油膜温升值沿圆周方向均从两侧向中心方向增大,中心位置温升值最大,差值约为0.25~0.5 ℃。
关键词:泵;温度;试验;油膜厚度;配流副;压力
0 引 言
叶片泵因其具有流量均匀稳定、低噪声及自吸性能较好等优点,在机床、工程机械、船舶等机械设备上得到了广泛的应用[1]。子母叶片泵采用子母叶片结构,性能得到很大提升[2-3]。随着叶片泵工作压力的提高,对其配流副摩擦状况要求更为严格[4]。由于配流盘与转子形成的摩擦副随着叶片泵工作时间的延长,摩擦部位产生温升会导致油液粘度降低从而造成配流副泄漏量增大[5]。温升值过高会导致配流副表面产生热变形而影响配合间隙,还可能引起配流副表面材料失效,使液压油产生裂化变质。特别是配流副不容易形成有效油膜时,局部温升则更加明显,导致摩擦副两壁面间的局部地方出现固体表面接触摩擦,造成局部壁面的温度骤然升高,影响叶片泵的正常工作,对泵造成损坏,叶片泵的使用寿命也会大幅度减小[6-7]。
目前3大类液压泵中,对轴向柱塞泵摩擦副油膜温升的研究相对较多。Wang 等建立了轴向柱塞泵配流副油膜的数学模型和能量方程,模拟了油膜的温度分布。发现配流副的温升随着油粘度的增加而上升,随初始油膜厚度的增加而减小[8]。Li等利用热流固耦合的方法,得出高压高速轴向柱塞泵容腔内流体的压力、温度的变化规律,发现配流副形成楔形间隙,且发生混合摩擦[9]。王章俊等建立了高压轴向柱塞泵配流副的三维仿真模型,得到了配流副油膜的压力场、速度场和温度场特性,观测到实际输出压力与温度的变化规律 [10]。张艳芹等建立了热油携带影响下供油温升方程,采用有限体积法进行油膜温度场模拟,得出热油携带的油膜温度场在不同工况条件下温升曲线[11]。除轴向柱塞泵配流副油膜温升外,学者还对柱塞副和滑靴副的温升展开研究[12-16]。
叶片泵摩擦副温升研究中,有叶片-转子摩擦副和叶片-定子摩擦副的研究[17-19],对于配流副油膜温升的研究目前还未见报道。叶片泵配流副结构和油液流动都较轴向柱塞泵复杂。本文从油膜内油液流动角度,研究双作用子母叶片泵配流副油膜不同部位温升情况。通过理论分析建立温升模型,并进行温度场数值模拟和试验测试,将测试结果与理论研究的结果进行比较。研究结果对探明配流副油膜温升机理,改善配流副摩擦状况,提升泵的性能有一定的指导意义。
1 配流副油膜温升数学模型
1.1 配流副油膜油液运动分析
子母叶片泵工作时,驱动轴带动转子旋转,叶片和转子一起转动的同时,还在叶片槽内做径向伸缩运动,配流盘与转子和叶片发生相对运动,形成的摩擦副内油膜油液在不停流动[20]。根据子母叶片泵的工作原理和配流盘结构,可分析出配流副内油膜油液的运动方向。
叶片泵油膜为配流盘与转子的配合间隙部分,双作用叶片泵的油膜分布关于原点对称,如图1所示。为了分析方便,将油膜分为6个区域,分别是A、B、E和C、D、F区域,其中A、B、E位于配流盘的吸油区,C、D、F位于配流盘的排油区。
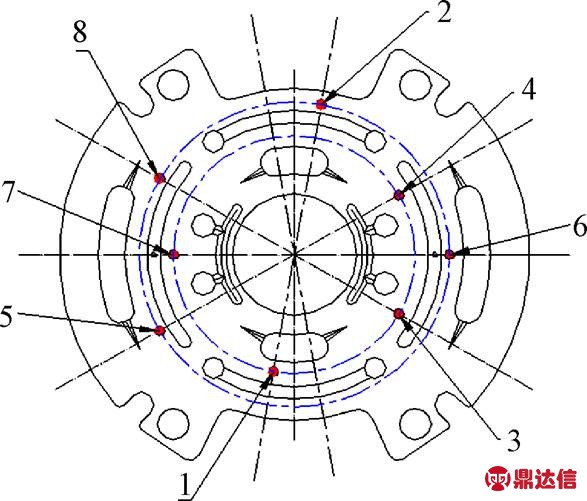
1.吸油口 2.吸油区均压槽 3.吸油区叶片底腔引油槽 4.排油口 5.排油区均压槽 6.排油区叶片底腔阻尼槽
A.吸油口与吸油区均压槽过渡区域 B.吸油区均压槽与叶片底腔引油槽过渡区域 C.排油口与排油区均压槽过渡区域 D.排油区均压槽与叶片底腔阻尼槽过渡区域
1.Oil suction port 2.Pressure-equalizing groove in oil suction area 3.Oil groove for bottom of vane in oil suction area 4.Oil discharge port 5.Pressure-equalizing groove in oil discharge area 6.Oil groove for bottom of vane in oil discharge area
A. Transition area between oil suction port and pressure-equalizing groove in oil suction area B. Transition area between pressure-equalizing groove and oil groove for bottom of vane in suction area C. Transition area between oil discharge port and pressure-equalizing groove in oil discharge area D. Transition area between pressure-equalizing groove and oil groove for bottom of vane in oil discharge area
图1 配流副油膜分布及油液运动方向示意图
Fig.1 Schematic diagram of oil distribution and oil direction of movement for flow distribution pair
在吸油区的A区域,其内外两侧分别作用着高压和低压油,油液在压力差作用下沿着径向向外流动[21],如图1中A区域箭头所示,其方向表示油液流动方向;同理在吸油区B区域、排油区F区域处,油液沿着径向向内流动,如图中箭头所示。而在排油区域C、D和吸油区E区域处,由于这些区域两侧基本上没有压力差,故油膜中油液基本不会在压差的作用下发生径向流动[22-23]。但对于整个油膜来说,由于转子、叶片与配流盘发生相对转动,也会带动配流副内油膜油液做剪切运动,油膜油液总的运动方式为二者的叠加。
1.2 吸油区油膜温升计算模型
对吸油区A、B区域油膜温升计算分析如下,如图2所示,在转子与配流盘相对滑动速度U的作用下,油液发生沿转子旋转方向的剪切流动,同时在压差∆p的作用下,发生沿压力损失方向的压差流动,二者互成正交,此处认为油液黏度μ为常值,不考虑压力和温度对黏度的影响。
对于A区域,平均弧长L和宽度b为
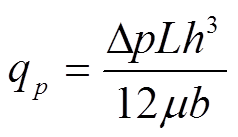
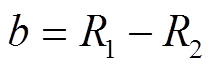
平均相对滑动速度U的计算公式如下
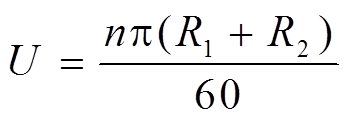
式中U为平均相对滑动速度,m/s;n为叶片泵转子的转速,r/min。
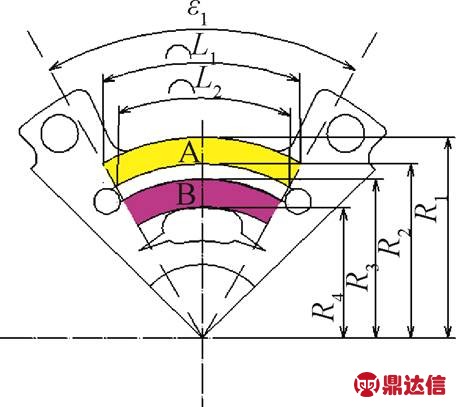
注:R1,R2,R3,R4分别为A和B区域油膜的外部和内部圆弧半径,m;L1,L2分别为A区域油膜的外部和内部圆弧长度,m;ε1为A区油膜所在圆弧夹角,(°)。
Note: R1, R2, R3 and R4 are the radius of outer and inner arc in A and B area, respectively, m; L1, L2 are the length of outer and inner arc in A area, respectively, m; ε1 is the arc angle of A and B area, (°).
图2 吸油区油膜温升计算模型示意图
Fig.2 Diagram of calculation model of temperature rise calculation of oil film in oil suction area
平均压差流量qp计算公式如下
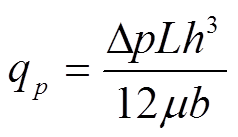
式中qp为平均压差流量,L/min;h为油膜厚度,m;μ为油液动力黏度,Pa·s;Δp为计算的油膜两侧压力差,MPa。
平均剪切流量q0为
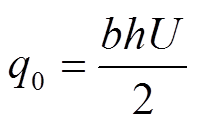
合成流量q可由压差流量和剪切流量的矢量和求得[24]
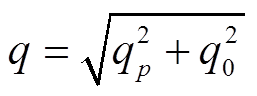
由于二者流动方向互成正交,剪切应力产生的摩擦力阻止转子的运动,而压差流动在壁面产生的切应力并不阻止转子的运动,所以摩擦功率损失Ef只取决于前者,其计算式为
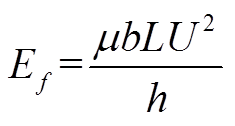
根据能量守恒定律,泄漏功率损失与摩擦功率损失之和等于油液所增加的热功率,即

式中ρ为油液密度,kg/m3;c为油液比热,J/(kg·k);ΔT为油膜温升,℃。
将式(6)、式(7)带入式(8),得到吸油区A区域的温升计算模型
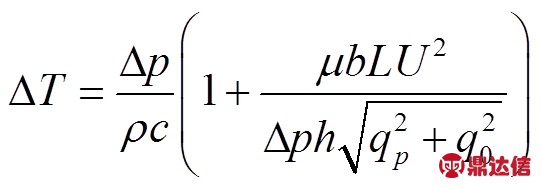
同理可以得到吸油区B区域的温升计算模型。
1.3 排油区油膜温升模型
对排油区C、D区域,其油膜计算模型如图3所示。根据上文对排油区C、D区域的油膜油液运动分析可知,排油区油膜温度升高主要是由剪切流动引起的,液体剪切流动所产生的摩擦热量,使液体发生温升,温升使油液膨胀而产生附加压力场,在该压力场的作用下,构成热楔流动。因此,这是热效应情况下的剪切流动,实际上是剪切流与热楔流的综合,温升计算式如下
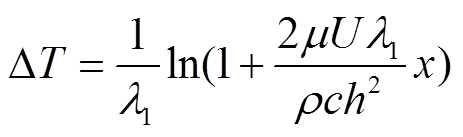
式中λ1为油液黏温系数;x为油液剪切流动距离,m。
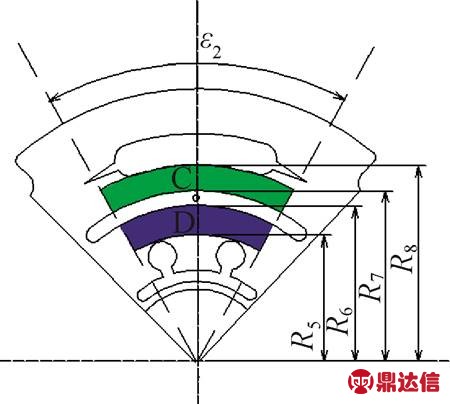
注:R5,R6,R7,R8分别为D和C区域油膜内部和外部圆弧半径,m;ε2为D和C区域油膜所在圆弧夹角,(°)。
Note: R5, R6, R7 and R8 are the radius of inner and outer arc in D and C area, respectively, m; ε2 is the arc angle of D and C area, (°).
图3 排油区油膜温升计算模型示意图
Fig.3 Diagram of calculation model of temperature rise calculation of oil film in oil discharge area
2 配流副油膜温升计算
2.1 吸油区油膜温升计算及结果分析
本文选用型号为VQ2521A的子母叶片泵,额定工作压力为21 MPa,转速为1 480 r/min,液压油选用46号抗磨液压油,其物理参数如表1所示。
表1 液压油的物理参数
Table 1 Physical parameters of hydraulic oil
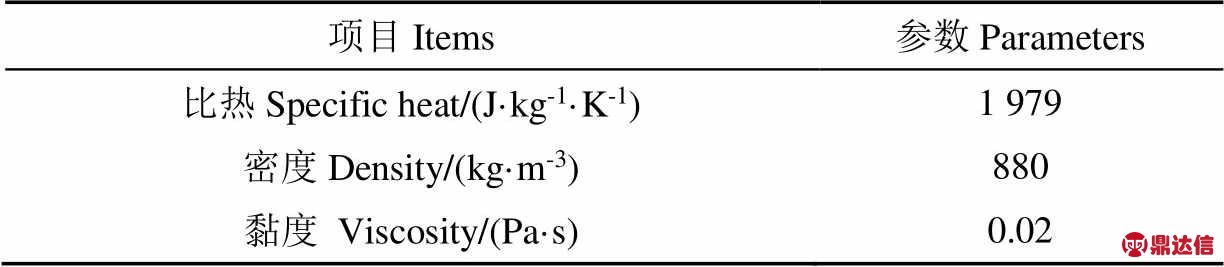
该泵配流盘A、B区域油膜内部和外部圆弧半径R1、R2、R3和R4分别0.035、0.030、0.028、和0.023 m,油膜所在圆弧夹角ε1为60°。
根据叶片泵实际情况,取配流副油膜厚度分别为15、20、25 μm时,将相关参数带入温升计算公式(9),计算得到吸油区A区域温升随工作压力的变化曲线,B区域温升变化计算方法与A的相同,结果如图4所示。
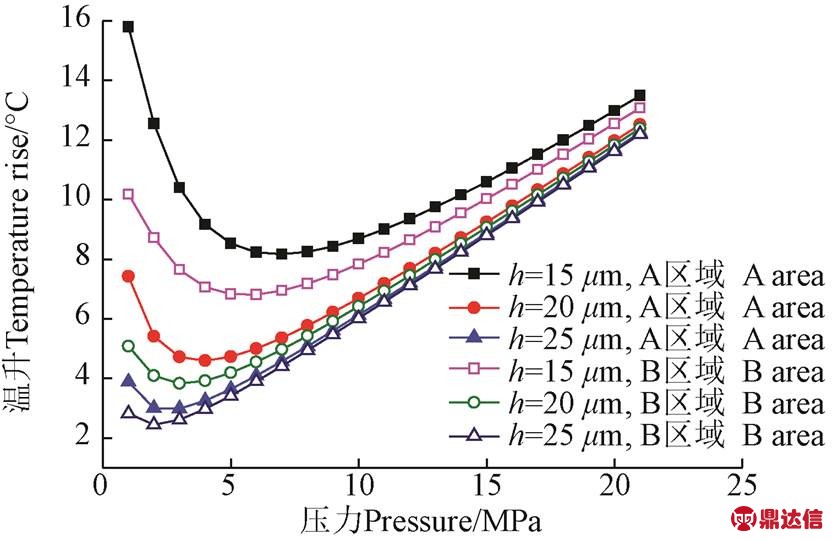
图4 吸油区A和B区域油膜温升随工作压力变化曲线
Fig.4 Temperature rise curve of oil film with working pressure in A and B area
从图4可以看出,在不同油膜厚度下,双作用子母叶片泵随着工作压力的升高,2个区域温升值先减小,至压力约3 MPa附近时达到最小值,随后随着压力的增大,温升值增大且趋势由慢变快,最后接近线性变化。出现这种现象的原因是在压力较低时,温升主要是由油液的剪切流动造成的,而随着工作压力的不断增大,压差流动产生的压差流量不断增加,将热量带走造成曲线前段温升值有所降低;当工作压力继续增大时,压差流动所产生的热量不断增加,成为油膜温度升高的主要因素,即形成了温度随着压力不断升高的趋势。
在配流副吸油区,相同工作压力及油膜厚度下,外层A区域油膜的温升值相对于内层B区域的温升值高。工作压力达到3 MPa以后,同样工作压力下,每一种油膜厚度的A区域温升比B区域温升高约0.5~1 ℃。
油膜厚度对于温升也有一定的影响,工作压力较低时,厚度小时剪切流量和压差流量同样很小,携带的热量少,造成油膜的温度升高明显。而油膜厚度增加时,油膜的温升减小,能够保证配流副稳定工作,不会发生热变形影响间隙配合,但油膜厚度过大,会导致配流副内油液的泄漏量增大,使叶片泵的容积效率降低。当叶片泵工作压力增大到额定压力附近时,油膜厚度对于其温升的影响变小,所以油膜厚度对于叶片泵的性能提升有着重要的影响。
2.2 排油区油膜温升计算及结果分析
配流盘排油区C、D区域的油膜内部和外部圆弧半径R5、R6、R7和R8分别0.023、0.028、0.031和0.035 m,油膜所在圆弧夹角ε2为60°。由式(10)求得C、D区域因剪切流动产生的温升随着滑动速度的变化曲线,D区域位于配流副内层,且D区域平均相对滑动速度范围为0~4 m/s,而C区域位于配流副外层,平均相对滑动速度比D的高,所以D区域滑动速度取值范围比C稍小,如图5所示。
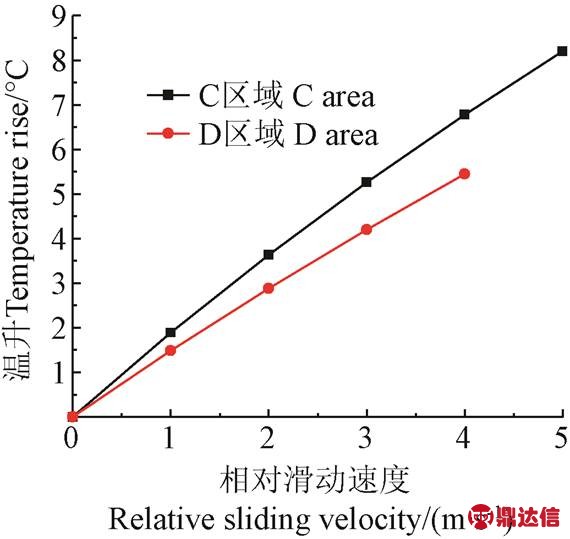
图5 C和D区域油膜温升随相对滑动速度变化曲线
Fig.5 Temperature rise curve of oil film with relative sliding velocity in C and D area
可以看出,C、D区域温升值随着相对滑动速度的增大而增大,在各自最大滑动速度范围内呈现近似线性的变化趋势。同样的滑动速度下,外层C区域产生的温升高于内层D区域产生的温升,相对滑动速度是由泵转速决定的,即剪切流所产生的温升主要是受转速影响。所以,由于剪切流动的影响,从滑动速度角度考虑,外层温升应该比内层的大。
2.3 温度场仿真及结果分析
为了直观地分析上述区域油膜温度分布和温升情况,采用FLUENT软件进行油膜的三维流场仿真。配流副的流道包含配油腰槽和油膜,划分网格时将它们放入相应位置的面中,设定最大网格尺寸为0.2 mm,在配油腰槽底部和油膜表面不存在数据交换面[25]。最终得到流体域的网格数为2 884 199个,节点数为1 194 896个,有限元的网格模型及计算域的进出口标注如图6所示。
设置油膜为厚度20 μm的配流副模型,由于是黏性流动,考虑到热交换,在能量方程中包含粘性产生热,液压油物理特性参数见表1,再定义热传导系数为0.147 W/(m·K)。根据该泵实际情况,对出口压力分别设置为3、7和11 MPa,进出口温度分别为293、320 K的高压叶片泵配流副模型进行稳态模拟[26],得到的油膜温度分布如图7所示。
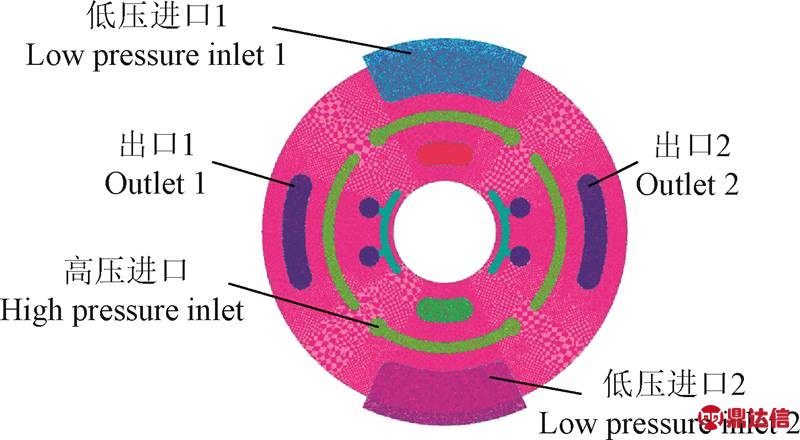
图6 配流副流道网格模型
Fig.6 Mesh model of flow passage of flow distribution pair
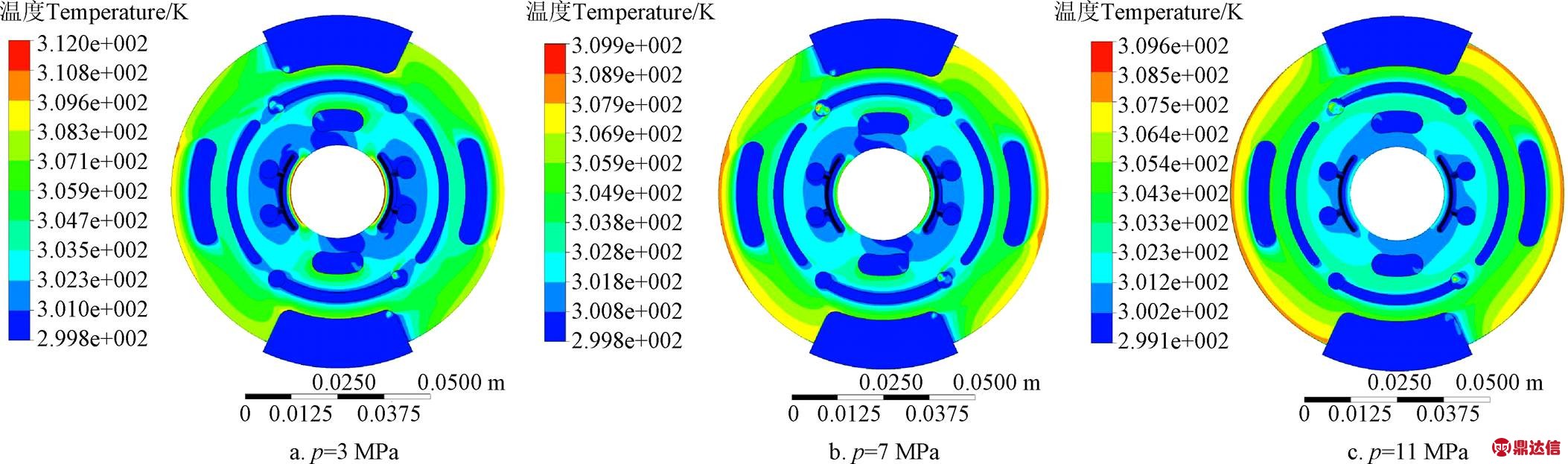
图7 不同出口压力下配流副油膜温度场仿真云图
Fig.7 Nephogram of oil film temperature field of flow distribution pair in different pressure
从图7可以看出,在泵出口压力分别为3、7、11 MPa时,油膜温升大约为4,5和7 K。在吸油区,A区域所在的外层温度高于B区域所在的内层温度,且从中间均压槽沿着半径方向分别向外和向内温度有减小现象。出口压力越大,温度变化梯度越明显。在排油区,随着工作压力的升高,外层C区域和内层B区域温度升高。排油区油膜温升主要是由剪切流动引起,外层C区域温度高于内层B区域的温度。随着压力的增大,C区域由于主要受压差流的影响使得温升逐渐变大,D区域的温升变化不大。
另外,从图上可以看出,吸油区油膜的外层A区域和内层B区域温度比排油区的外层C区域和内层D区域的温度都高,主要是由于吸油区油膜受到剪切流动和较大压差流动的结果所致,仿真结果与上文计算结果相一致。
3 配流副油膜温升测试试验
为了进一步探明配流副油膜不同区域的温升情况,设计了油膜温度测试系统,从试验测试结果进行进一步分析。
3.1 配流副油膜温度测试系统
根据试验的需要,搭建叶片泵配流副油膜测试液压系统,使用节流阀加载,在保证转速一定的情况下,改变叶片泵的输出压力[27-28],采集不同压力下油膜不同位置温度的实际数值,设计的配流副油膜温度测试液压系统原理如图8所示。
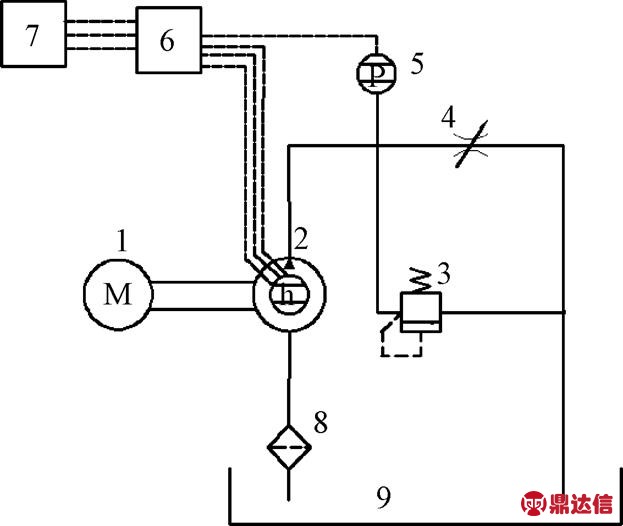
1.电动机 2.试验泵 3.溢流阀 4.节流阀 5.压力传感器 6.数字温度记录仪 7.计算机 8.过滤器 9.油箱
1.Motor 2.Test pump 3.Overflow valve 4.Throttle valve 5.Pressure sensor 6.Digital temperature recorder 7.Computer 8.Filter 9.Fuel tank
图8 油膜温度测试液压系统原理图
Fig.8 Principle diagram of hydraulic system for oil film temperature measurement
3.2 温度测试点的布置
温度测试用传感器探头的安装方法与位置非常重要。配流盘厚度较小,不适合直接安装传感器探头,试验测试可知2个面温度差值非常小,故适合采用间接接触式温度测量方法。采集配流盘背面的各点的温度值,近似认为就是与其对应位置处的配流副油膜温度[29-30]。该方法不会破坏配流副油膜结构及流动特性,对于叶片泵的工作没有负面影响,而且采集到的温度数据较准确。
按照上面分析,在配流盘背面确定了8个测量点,安装锴装热电偶探头,采集配流副油膜不同位置的温度[31-32]。具体是低压区2个,高压区6个,8个测量点沿径向呈现内外2层排列形式,具体安装位置如图9所示,图10为安装传感器探头的试验泵和油膜温度测试现场,图10a中标注了2号传感器探头的安装情况。
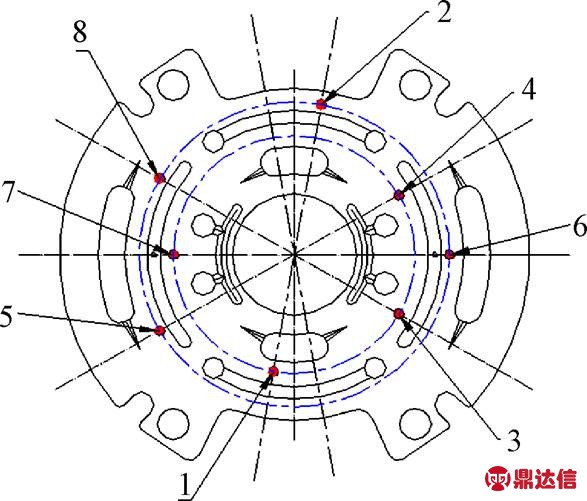
图9 配流盘温度采集点分布图
Fig.9 Distribution diagram of temperature acquisition point in flow distribution plate
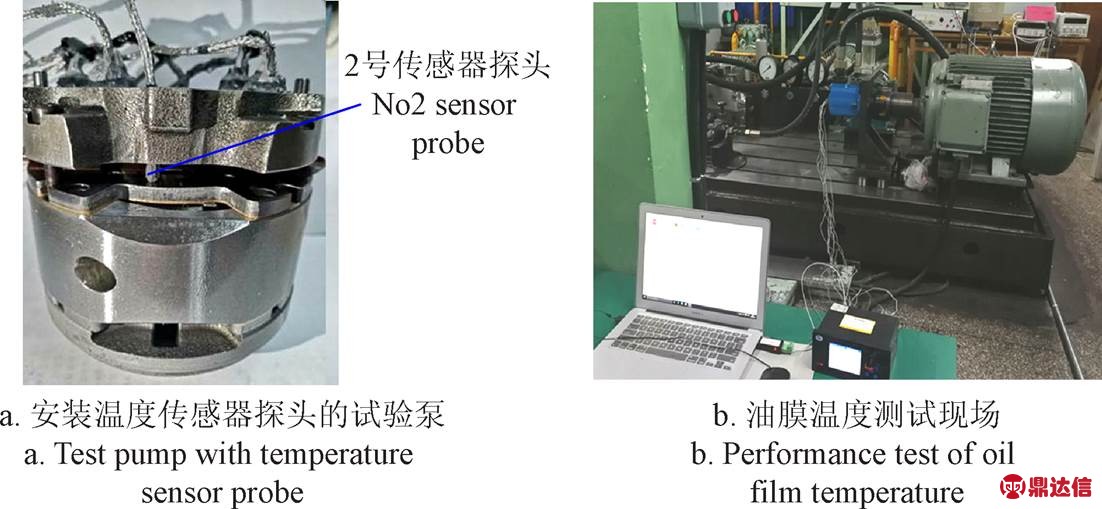
图10 试验泵和油膜温度测试现场
Fig.10 Test pump and performance test of oil film temperature
3.3 试验数据分析
在叶片泵转速一定时,使其分别工作在3、7、11 MPa不同压力下,采集配流副油膜各个测温点的温度值。
1)原始数据处理方法
叶片泵开始稳定运行后,采集到各点的温度值持续升高。产生温度升高的原因主要有2个:一是配流副油膜油液运动产生的油膜温度升高;二是整个系统的油液温升。油液温升主要是由叶片泵总损失功率决定的,当叶片泵的工作压力保持恒定时,其功率损失保持不变,总的能量损失会转化为系统内油液的内能,即压力一定时,油液的温度也随着工作时间呈现线性增长。所以需要对原始数据进行处理,将数据中整个系统功率损失造成的油液温升这一影响因素排除,才能得出配流副油膜油液运动产生的实际温升值。
处理方法是泵启动后,油液温度随泵运转线性增加,将每一测温点实际温度变化值减去油液初始温度19.7 ℃后,得出测温点油液温升数据曲线,将该线性曲线拟合为温升随时间变化函数关系式,从原始温度数据中将这一部分函数关系数据减去,即得到配流副油膜的实际温升值。
2)吸油区温升试验结果分析
在吸油区,对图9所示的1、2号采集点实际温度值进行处理后,得到在3种不同压力下的温升曲线,如图11所示。
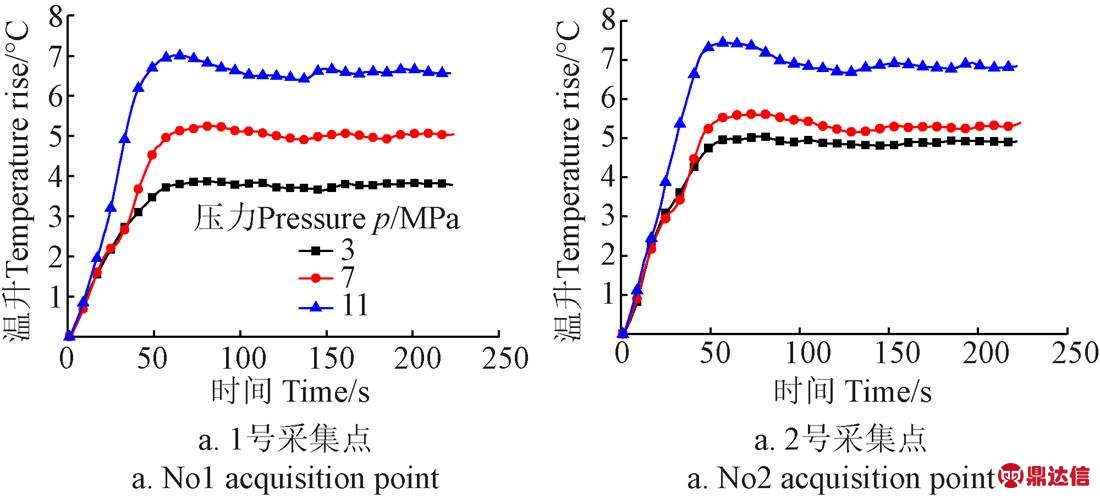
图11 吸油区1、2号采集点温升曲线
Fig.11 Temperature rise curve of No 1 and No2 acquisition point in suction area
从图11可以看出,2个采集点处油膜温升随着工作压力升高而升高,在同等压力下,采集点2产生的温升比采集点1的温升大。不同的工作压力下,二者差值也不同,外层温升比内层的高0.5~1 ℃,即配流副的吸油区油膜,外层温升高于内层温升,这与前面理论分析相吻合。
为了进一步定量分析油膜温升值情况,对3种工作压力下,吸油区温升的理论计算、数值模拟与试验测试结果进行比较。在图7中将A、B区域1号和2号采集点位置的温度仿真结果导出,减去油膜的初始温度,从而得到了在1和2采集点处的温升值数值模拟结果,该泵油膜厚度取为20 μm,比较结果如表2所示。
表2 吸油区温升理论计算、数值模拟与试验测试结果比较
Table 2 Comparison of theoretical calculation, numerical simulation and experimental results of temperature rise in oil suction area
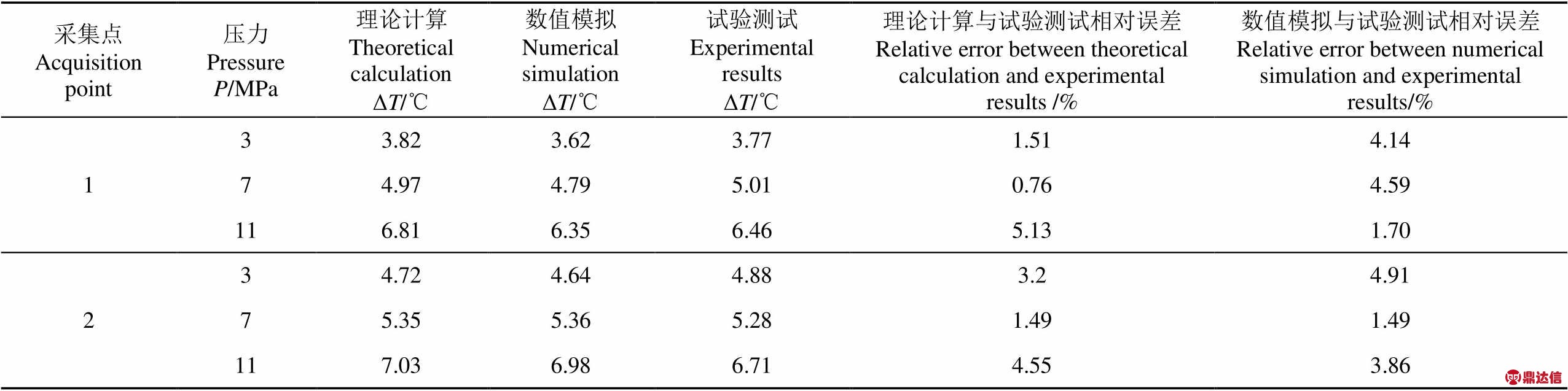
可以看出,3种方法得到的温升值较为接近,工作压力为3、7 MPa时,相对误差较小,当工作压力为11 MPa时,理论计算与测试结果相对误差较大,数值模拟结果与试验测试结果也有一定偏差。产生上述误差原因有:一是理论计算中没有考虑温度和压力对油液粘度的影响;二是数值模拟时仿真模型及初始温度的设定;三是试验时选择间接接触式温度测量方法,近似认为配流盘的两侧没有温差;四是计算时认为油膜厚度为恒定值等。
3)排油区温升实验结果分析
按照同样的数据处理方法,可以得到排油区3至8号采集点的温升变化曲线,如图12所示。
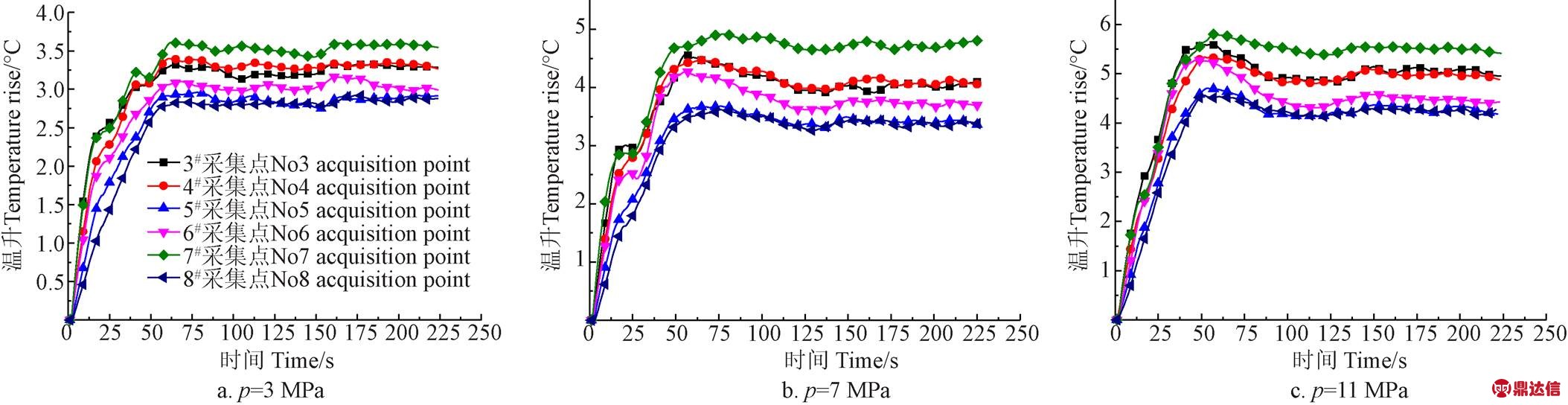
图12 排油区各采集点温升曲线
Fig.12 Temperature rise curve of each acquisition point in discharge area
比较图11和12可以得到,配流副吸油区油膜内层和外层采集点的温升值总体比排油区采集点的温升值大,工作压力越大,该差值越大;相同的工作压力下,吸油区油膜温升值比排油区油膜温升值1.5~3.5 ℃。另外,排油区数值模拟与试验测试结果与吸油区类似,此处不再详述。
从图12可以看出,3号至8号采集点,在同样工作压力下,位于排油区内层D区域的3号、4号、7号采集点处温升值高于其外层C区域的5号、6号、8号,这与上文理论分析与数值模拟得到的结论不一致。试验用泵拆卸后,看到配流盘的D区域存在轻微的刮擦磨损现象,如图13中梯形框位置所示。配流盘和转子之间存在一定的机械表面接触,产生一定的摩擦生热导致试验测试时,D区域温升试验测试值比C区域的温升值大。
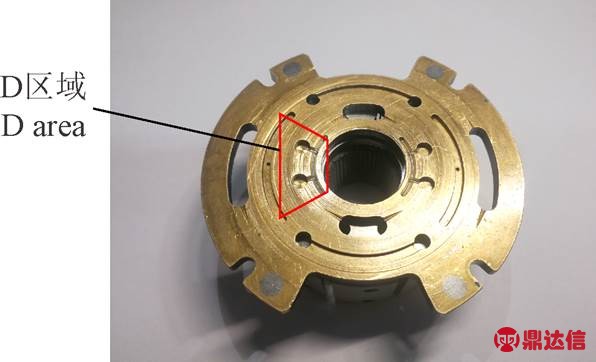
图13 试验泵配流盘磨损情况
Fig.13 Wear diagram of flow distribution plate of test pump
同时可以看出,采集点3号和4号,5号和8号在相同工作压力下温升值基本一致,因为2组的采集点在配流盘同一半径上,关于配流盘中心点对称。
把同一半径上的3号、4号和7号采集点作为一组,把5号、6号和8号采集点作为另一组,分别比较相同工作压力下,排油区同一半径沿周向不同位置的温升变化情况。由数据和试验曲线分析可以看出,相同压力下,在排油区外层C区域7号采集点温升值比3号、4号采集点高0.2~0.5 ℃,内层D区域6号采集点温升值比5号、8号采集点高约0.25 ℃,即排油区域每一层的油膜温度分布大致为中心温升最大,沿圆周方向向两侧逐渐降低。造成这一变化的原因主要是排油区两侧油膜温升受到吸油区的影响,中心处受排油腔油液温升影响所致。
综上分析可知,配流副油膜温升与工作压力和油膜厚度均有关系,油膜厚度对配流副泄漏量有较大影响,在高压叶片泵配流副设计过程中,要综合考虑泄漏量和油膜温升情况。叶片泵工作在额定工作压力时,在保证泄漏量满足容积效率要求情况下,适当放大油膜厚度,对于降低配流副的温升有一定作用。目前配流盘各个区域都设计在同一平面上,根据上文温升研究结果,不同区域对油膜温升贡献大小是不一样的,在满足容积效率前提下,可以尝试根据各区域温升的不同,设计出表面凹凸不平的配流盘。
4 结 论
本文对高压子母叶片泵配流副油膜温升进行理论计算和数值模拟,分析了配流副油膜不同部位的温升情况,并通过试验测试进行了验证,得到如下结论:
1)子母叶片泵配流副油膜温升受到工作压力和油膜厚度的影响。在油膜厚度一定时,泵的工作压力越高,配流副油膜的温升值越大;在工作压力一定时,油膜厚度大则配流副油膜温升小。
2)吸油区配流副油膜温升受到剪切流动和压差流动同时作用,而排油区油膜温升主要受到剪切流动作用。相同的工作压力下,吸油区油膜温升比排油区油膜温升高1.5~3.5 ℃。
3)在吸油区,配流副油膜外层区域油膜温升值比内层区域高0.5~1 ℃,温升值向压力损失的方向增大。
4)在排油区,配流副油膜外层区域的温升值比内层区域的大,内外两层油膜温升值同一半径上,均从两侧至中心方向增大,中心部分油膜温升值最大,差值约为0.25~0.5 ℃。实际工作中,由于配流盘与转子产生机械接触摩擦,导致排油区内层温升增大。