摘 要:提出了适合变排量叶片泵叶片结构特点的自动上下料加工模型,并采用“气压缸+杠杆机构”的自动装夹和卸料的方案以及“L形上料槽+双向气压缸”的全自动分料定位方案进行完善,并进行快速装夹,利于实现叶片圆弧面的自动化、高效率加工。
关键词:变排量叶片泵; 叶片圆弧面;快速装夹;自动定位
1 前言
传统定排量机油泵以车辆怠速时的机油需求量为设计基础[1-2],其供油量随发动机转速的提升线性增加,则高速时输出油量过多,浪费机油泵功耗。使用变排量机油泵,可使机油泵的供油量与发动机的需求量相匹配,减少机油泵的功耗 [3],降低车辆的燃油消耗。目前研发应用的变排量泵包括转子泵、齿轮泵和叶片泵(如图1所示),其中叶片泵结构紧凑、排量大、结构设计自由度大,适用范围广。浙江五洲新春集团股份有限公司,现为国外客户供应叶片泵零件叶片环2 000万件/年,根据叶片环与叶片的配比(2个叶片环配置7~11片叶片,如图1所示),容易算出客户需求的叶片在7 000-11 000万片/年,市场前景广阔,亟需叶片的大批量、高效率、高可靠性
的自动化加工工艺。然而,常见的外圆弧面磨削装置对于此种叶片泵叶片圆弧面的磨削加工并不适用[4-8]。前人对于此类零件的加工也进行了一定的研究。毛江峰设计了在外圆磨床加工某真空泵叶片圆弧面的夹具,螺钉夹紧,人工摆动夹具手柄实现圆弧面的磨削[9]。胡剑英为汽车空调压缩机滑片圆弧面在外圆磨床的磨削设计了半自动磨削装置[10],利用曲柄摇杆机构的工作原理实现叶片的自动摆动,但工件的夹紧仍然靠螺纹,必须人工上料和夹紧。显然,这两种设计都未能实现叶片圆弧面的自动化加工,不符合当前“机器换人”的潮流,也难以实现叶片的高效、大批量加工。
2 自动化加工模型
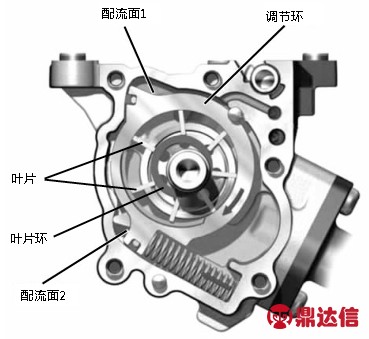
图1 变排量叶片泵
基于叶片泵叶片的结构特点,如尺寸小、重量轻(叶片成品质量不足4g)、精度较高,如图2 所示,初步设计了包括叶片落料,夹具接料、定位、夹紧,夹具体转位摆动磨削,磨削完成后夹具松开的自动上料加工模型,如图 3 所示。叶片夹具的结构和文献[9]中夹具类似。经整理后排列整齐的叶片进入竖直上料槽,靠自身的重力沿上料槽下滑。叶片夹具的转动由磨床数控轴实现,叶片被磨削圆弧面与机床数控轴共轴线。夹具接料时,开口向上,以使滑下的叶片落入,夹紧机构压紧叶片大平面。然后,夹具顺时针转动90°,砂轮靠近叶片,叶片往复摆动,实现圆弧面的磨削。磨削完成后,砂轮退开,夹具再次顺时针转动90°至竖直向下位置,夹具松开,靠叶片的自重从夹具体中掉落。粗看,此模型好像实现了叶片的自动上下料,但仍有非常明显的关键问题:
①欠定位:当叶片从上料槽中落入夹具体时,在叶片自重的作用下,理论上非磨削一侧圆弧面可以定位,大平面靠夹紧力定位,但叶片侧平面没有定位。
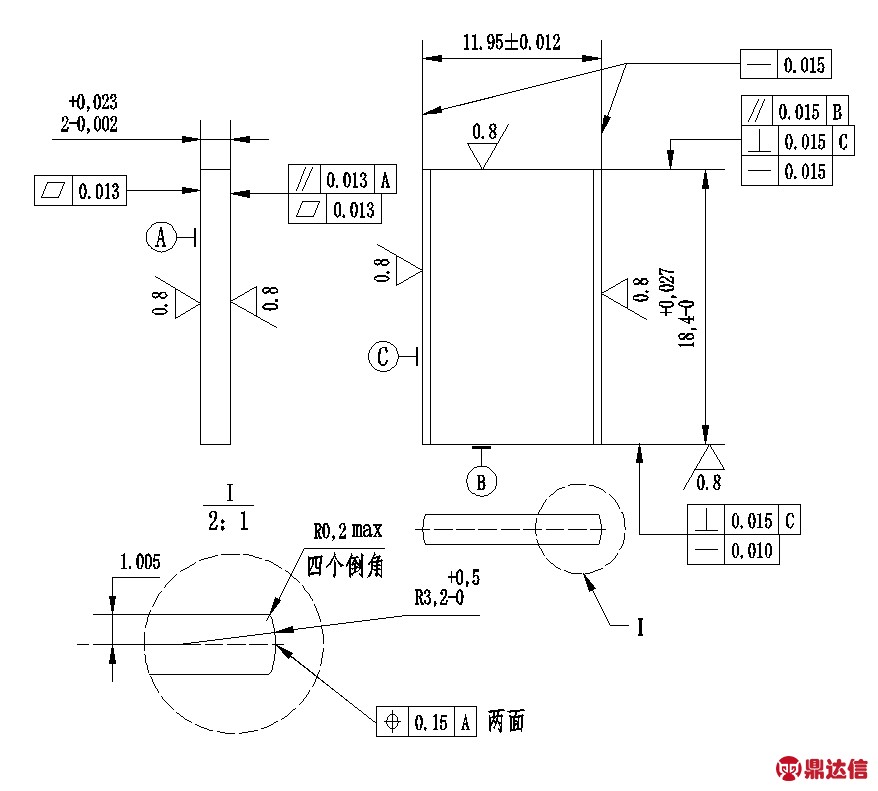
图2 叶片零件图
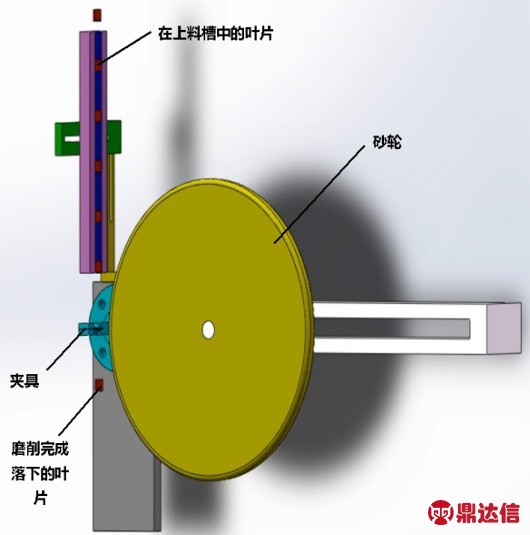
图3 叶片自动上料加工模型
②自动夹紧和卸料:模型中没有说明叶片大平面自动夹紧的方法,而且,由于叶片自重未必能够克服叶片大平面和夹具定位面之间磨削液的张力,叶片不一定能够从松开的夹具体中自动落下。
3 模型完善
3.1 自动上料和完全定位
由于推动叶片进入夹具的是叶片的微小自重,故为了方便叶片的进入,夹具开口的尺寸应略大于叶片相应的尺寸。当叶片进入夹具后,叶片重力克服和夹具之间的摩擦力,推动叶片深入夹具空腔,理想情况下,非磨削圆弧面会接触夹具定位面,然后在夹紧力作用下,叶片一侧大平面紧贴对应定位面,但叶片侧平面没有力的作用,侧平面得不到定位。
如果在夹具两侧定位平面(与叶片侧平面相对应)的其中一侧设置一个推力较小的弹簧定位珠,则叶片在进入夹具开口时,由于弹簧力的推动,叶片另一侧平面会紧贴夹具定位面而得到定位,但由于叶片自重很小,在叶片侧平面和定位珠之间摩擦力的阻挡下,叶片不能进入夹具空腔,其结果是,非磨削圆弧面不能接触夹具对应定位面,仍然是欠定位。当然,可以考虑在叶片上增加一个推动力,以推动叶片完全到达夹具底面,此时叶片非磨削圆弧面、侧平面都能得到定位,再加上大平面上主夹紧力的作用,叶片得到完全定位。
叶片经过振动上料盘的整理之后进入竖直上料槽,在叶片重力作用下于竖直上料槽中应紧密排列,而非图 3 中的稀疏排列,任意两相邻叶片的圆弧面(叶片圆弧面的毛坯面是平面)紧密接触,限制任一叶片绕其大平面法矢的自由转动,最大限度保证叶片侧平面与上料槽对应侧平面完全平行,这会造成难于为即将进入夹具的叶片施加推动力,而且会造成近似矩形叶片的分料困难,难于实现自动上料。
基于以上困难,设计了“L形上料槽+双向气压缸”的全自动定位方案,如图 4 所示。此设计的结构和工作过程如下:经过振动上料盘整理之后,原来杂乱排列的叶片以非磨削圆弧面在下、磨削圆弧面在上的规则排列形式进入竖直布置的L型上料槽,L型上料槽与叶片两侧大平面及两侧平面之间均为间隙配合,叶片在重力的作用下滑落至上料槽底部;当需要上料时,水平气压缸推杆推动叶片水平向左滑动,同时推杆阻止上侧相邻叶片下滑;当叶片被气压缸推动至上料槽最左侧,对应夹具开口位置时,水平气压缸回程,当水平气压缸回程结束,上侧相邻叶片下滑至下挡板,准备下一次上料;然后竖直气压缸开始推程,将叶片推入夹具,叶片在气压缸的推动下,非磨削圆弧面完全贴合夹具定位面,在叶片进入夹具的过程中,叶片右侧平面在左侧弹簧定位珠弹簧力的作用下完全贴合夹具定位面,上料完成。然后,叶片大平面被压紧定位,叶片在夹具中完全定位。
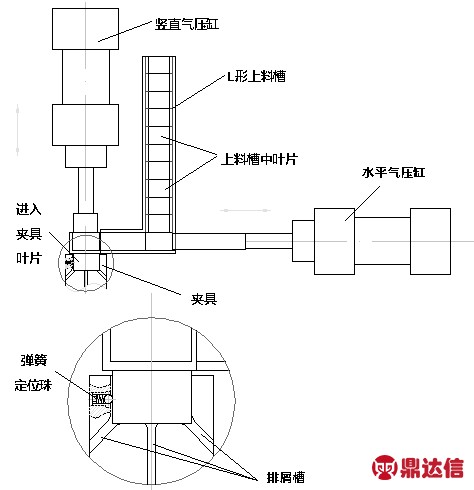
图4 叶片自动上料和定位
3.2 自动夹紧和卸料
仔细分析问题②,其难点在于:为了实现叶片圆弧面的自动化高效加工,叶片的压紧和放松卸料一定不能采用传统的手动方法,而应该采用能够实现自动控制的压紧方法,如电磁、气动、液压,真空等压紧方式。然而,电磁铁或真空夹紧,必然以叶片的大平面作为电磁或真空吸引力的作用面,但即使是叶片的大平面其面积仍然非常小,而且部分要参与磨削,布置吸合力足够的电磁铁或真空吸盘几乎不可能;液压或气动装置的压力足够,但由于叶片圆弧面磨削时,叶片要带着压紧装置一起摆动,难以避免砂轮和气动或液压缸之间的干涉,且气压或液压缸体长度尺寸较大,在夹具90°转位时,需要砂轮退开和复位的距离较大,延长了辅助加工时间,降低总体加工效率。
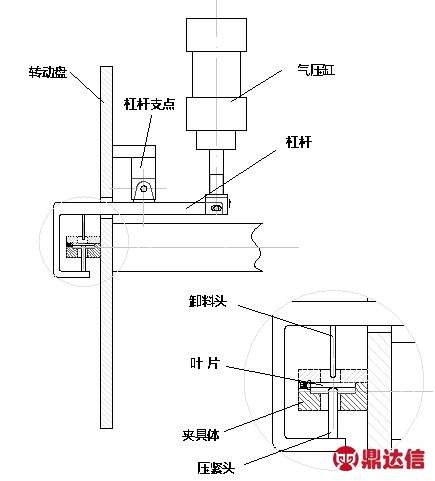
图5 叶片快速压紧、卸料
经过对以上关键问题的认真研究,提出的解决方案是采用“气动缸+杠杆机构"的压紧方案,如图 5 所示。转动盘固定在磨床数控转轴上,其轴线与叶片圆弧面的轴线共线;夹具体(包含叶片)布置在转动盘左侧,而双向推拉气压缸布置在转动盘右侧,由于转动盘的遮挡,气压缸不外露,更显美观;杠杆穿过转动盘,右端和气压缸推杆铰接,左端上下各安装卸料头和压紧头,支点布置在杠杆大约中部位置。此夹紧装置的工作过程如下:当转动盘逆时针转动至叶片夹具开口向上时,叶片在上料装置的推动下到达合适位置,气压缸推杆开始推程,在气压推杆的推动下,压紧端的夹紧头压紧叶片,卸料头松开。然后,转盘顺时针转动90°至水平位置,砂轮进给,叶片摆动,开始磨削。当磨削完成之后,砂轮退回,叶片在转动盘的带动下顺时针转动至竖直向下位置,气压缸开始回程,气压推杆拉动杠杆,压紧端的夹紧头升起,卸料头向下推动叶片,叶片在重力作用下,从夹具体内落下。然后,转盘逆时针转动180°,重新到达夹具开口向上位置,再次上料,进行下一个叶片的磨削。
4 结论
此自动磨削装置的优点包括:
(1)在结构上,有效地避免了夹具和砂轮的干涉;
(2)通过改变支点位置实现杠杆力臂的调节,可以改变夹紧力的大小,柔性好;
(3)巧妙利用了水平、竖直两个气压缸,解决了矩形叶片的分料困难,而且实现了零件的完全、自动定位,可靠保证加工精度要求;
(4)完全摒弃了人力的作用,可以快速实现自动夹紧、放松和充分定位,利于叶片自动化加工的实现,非常适合自动化的大批量生产。