摘要:固液两相流算法对双吸离心泵泥沙磨损模拟精度有直接影响。采用改进的固液两相流欧拉算法,考虑了相间阻力和泥沙扩散系数两方面因素,对典型悬移质泥沙粒径条件下的双吸离心泵流场进行了数值计算。研究发现,叶片表面湍流强度在头部和尾部较大,可达6%~10%;叶片头部和尾部的颗粒动态尺度大于中部。由湍流强度和颗粒动态尺度组成的湍动尺度效应,在叶片头部和尾部表现强烈,湍动尺度效应使固液相间阻力增大,更有利于颗粒的扩散,避免了颗粒聚集,对大颗粒的作用强于小颗粒。湍动尺度效应导致叶片表面固相体积分数分布范围减小,大颗粒的变化值大于小颗粒,叶片头部和尾部的改变值大于中部,叶片表面的严重磨损部位为叶片工作面尾部的块状磨损区,这比采用传统算法得到的带状磨损区和偏磨区计算结果,更符合离心泵实际磨损情况,考虑湍动尺度效应后得到的磨损率也有所增大。在此基础上,提出了双吸离心泵叶片水力设计和表面喷涂防护原则,为提高双吸离心泵抵抗泥沙磨损能力奠定了基础。
关键词:双吸离心泵; 泥沙磨损; 固液两相流; 改进欧拉算法
引言
双吸离心泵被广泛应用于黄河沿岸的高扬程灌溉泵站中,其输送介质为含沙水,山西省内多处泵站的过泵平均含沙量为5~10 kg/m3,泥沙体积分数为0.188%~0.377%,泥沙颗粒主要是中值粒径25~50 μm的多棱角、高硬度石英长石悬移质颗粒[1]。双吸离心泵的过流部件普遍存在磨损问题,使叶片外缘被磨损呈锯齿状,叶轮半径减小,叶片表面有密集蚀坑,密封环间隙变大,出现沟槽[2]。导致机组能耗增加、效率下降、出水量减少,严重影响双吸离心泵的安全、稳定运行[3]。
双吸离心泵叶轮内流体处于高速旋转状态,是湍流强度较高的流动。泵内流体湍流强度[4]、悬移质颗粒与含能涡相互作用引起的颗粒周围流体湍流结构变化,以及该变化对颗粒运动的影响均较为强烈[5-6]。颗粒与含能涡的相互作用通常以粒径与含能涡特征尺寸[7]的比值(ds/le)来衡量[5-6],称之为颗粒动态尺度。湍流强度和颗粒动态尺度对颗粒运动的综合影响,称之为固液两相流湍动尺度效应,简称湍动尺度效应。
欧拉数值算法是研究固液两相流的重要方法,其中相间阻力和泥沙扩散系数是欧拉算法中反映固液两相相间作用的主要参数[8-9]。Wen-Yu模型[10]是最常用的相间阻力模型,该模型的阻力系数是在标准阻力系数曲线表达式中添加浓度得到的,是由单个刚性球体在静止流体中作匀速运动试验得到的,但该模型并没有考虑湍流强度对阻力系数的影响[11],在将该模型应用于湍流强度较高的两相流计算时,会出现问题,为此,张自超等[12]提出了一种改进的Wen-Yu模型,通过引入湍流修正函数体现了湍流强度对颗粒运动的影响,解决了Wen-Yu模型因未考虑湍流强度影响而带来的计算不准确问题。
对于泥沙扩散系数的计算,目前多采用类比水流涡粘性系数的泥沙扩散系数半经验模型 [13],代表性模型主要有NON-DC模型[14]和Diffusion-in-VOF模型[15]。这2种模型都是针对特定离散相特性和特定浓度提出的,将它们用于悬移质固液两相流计算时,均忽略了悬移质颗粒与含能涡相互作用对颗粒周围流体湍流流动结构的影响[9,16-17]。张自超等[18]在此基础上提出一种改进的泥沙扩散系数模型DC-PDPC,通过建立流体湍流强度改变率与粒径、浓度的关系,体现了颗粒动态尺度引起的周围流体湍流结构变化对颗粒运动的影响。
本文针对双吸离心泵内的固液两相流流动特点,采用上述2种改进模型对现有固液两相流欧拉算法进行改进,对抽送黄河水的双吸离心泵泥沙磨损特性进行计算,分析典型悬移质颗粒粒径25 μm和50 μm条件下,双吸离心泵叶片表面两相流流场特性和磨损特性。在此基础上,提出提高双吸离心泵抗磨能力的技术措施。
1 欧拉数值算法
1.1 控制方程
欧拉数值算法的控制方程为

(1)


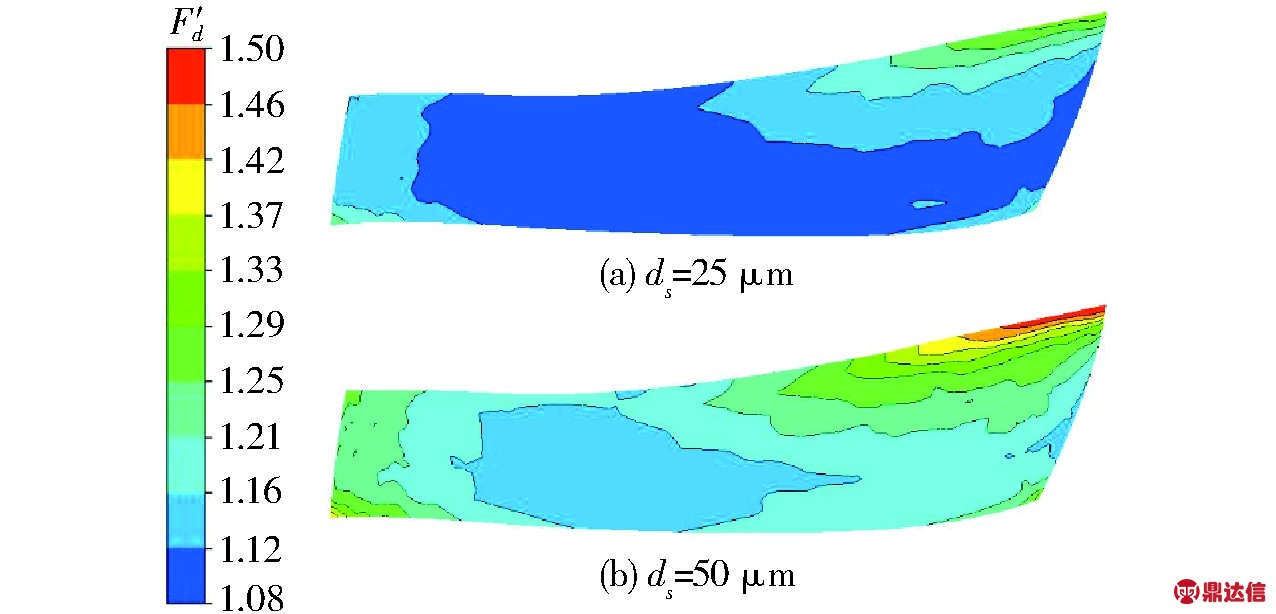
(2)
其中 αl+αs=1
式中 x——坐标方向 t——时间 αq——体积分数 vq——时均速度 p——压强 F——相间作用力 g——体积力 κ——泥沙扩散系数 ρq——密度 μq——动力粘度 μt,q——湍动粘度 λq——体积粘度
其中,下标i、j为张量的表示方法,满足爱因斯坦求和约定;下标q为某一相,l为流相,s为固相;相间阻力的计算体现在式(2)的相间作用力项中,而含泥沙扩散系数项是根据梯度输移假定,通过泥沙扩散系数建立各相浓度、速度脉动关联项与浓度梯度的关系得到的,具体可参照文献[9]。
1.2 相间阻力模型
(1) Wen-Yu模型
用于计算相间阻力的代表性模型是Wen-Yu模型[10],其表达式为
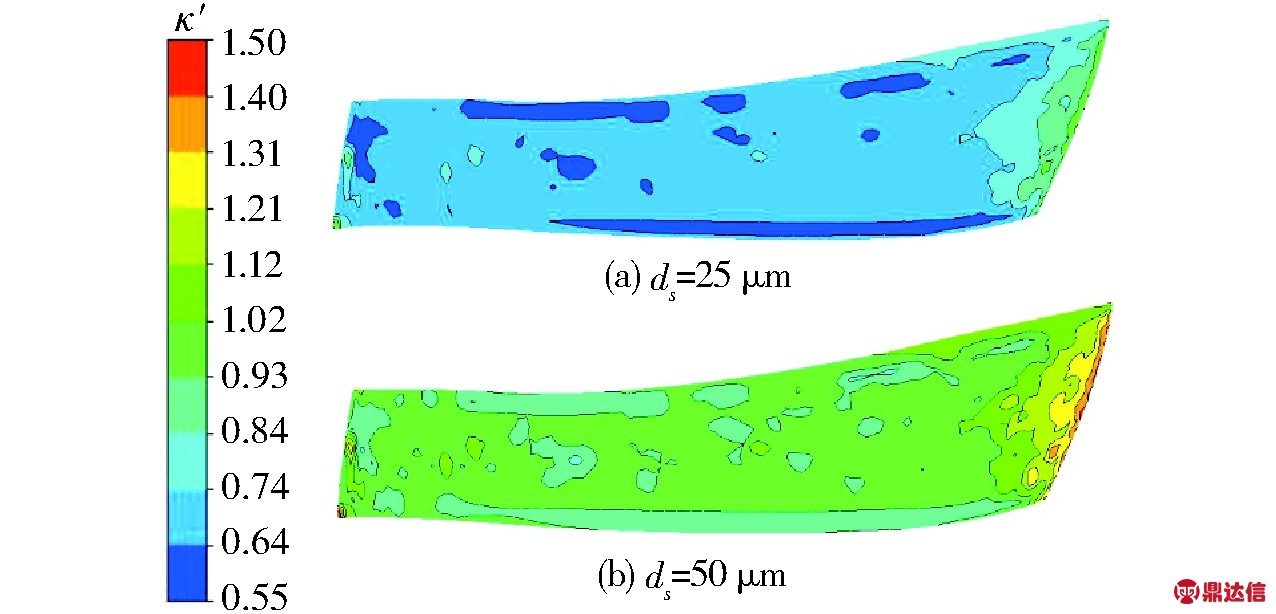
(3)
其中

(4)
式中 CD——阻力系数 Fd——相间阻力 vs——固相速度矢量 vl——液相速度矢量 ds——颗粒粒径 ρl——液相密度 Rep——颗粒雷诺数
(2) TE-Wen-Yu模型
Wen-Yu模型中阻力系数CD未考虑湍流强度对阻力系数的影响[11-12],导致对低浓度含沙水流的浓度计算不准确。为了解决这个问题,笔者引入湍流修正函数对Wen-Yu模型进行修正,得到TE-Wen-Yu模型[12]。该模型的相间阻力计算方法同式(3),阻力系数计算式为

(5)
其中
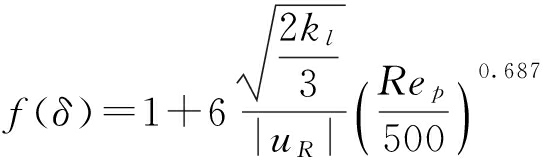
(6)
式中 f(δ)——湍流修正函数 kl——液相湍动能 uR——固液两相的相对速度
1.3 泥沙扩散系数模型
泥沙扩散系数κ的计算,多采用类比水流涡粘性系数的半经验模型[19]
κ=βφμt,l/ρl
(7)
式中 β——颗粒跟随性影响系数,表征颗粒对流体跟随性的影响系数
φ——流体湍流结构变化系数,表征颗粒对流体湍流结构影响的比例系数
(1) Diffusion-in-VOF模型
用于计算泥沙扩散系数κ的代表性模型是Diffusion-in-VOF模型。该模型认为颗粒脉动小于液相脉动[7],并认为流体湍流结构对泥沙扩散系数的影响是恒定的[14-15]。根据Hinze-Tchen公式可得到颗粒跟随性影响系数β,流体湍流结构变化系数φ取常数4/3,β计算式为

(8)
其中
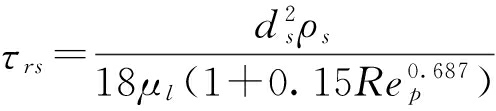
(9)
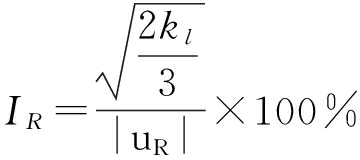
(10)
式中 τrs——颗粒弛豫时间 τT——液相的湍动时间尺度 Cμ——经验常数 εl——液相耗散率 μl——液相动力粘度
(2) DC-PDPC模型
Diffusion-in-VOF中流体湍流结构变化系数φ为常数,忽略了颗粒与含能涡相互作用的影响。为解决这个问题,笔者通过考虑含沙浓度、颗粒动态尺度对颗粒周围流体湍流流动结构的影响,设计了一种新的泥沙扩散系数模型DC-PDPC[18]。该模型的颗粒跟随性影响系数β计算方法同式(8),流体湍流结构变化系数φ为该模型计算的关键,公式为
φ
(11)
所得到的泥沙扩散系数为
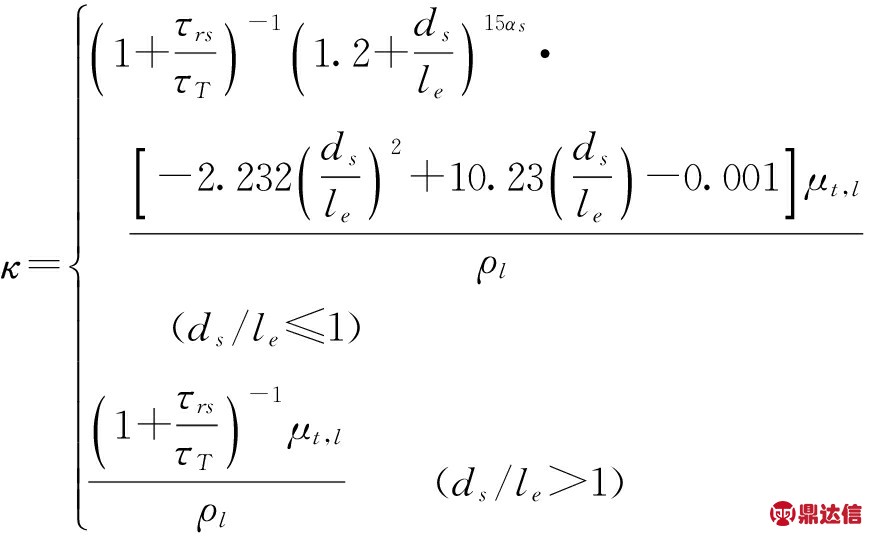
(12)
其中
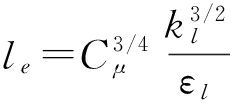
(13)
式中 le——含能涡特征尺寸[7]
1.4 磨损模型
图尔萨大学的磨损模型是目前泥沙两相流磨损计算的经典模型[20],考虑了颗粒冲击速度、冲击角和壁面材料的硬度对磨损的影响,公式为

(14)
F(θ)=5.4θ-10.11θ2+10.93θ3-6.33θ4+1.42θ5
(15)
ER=WRmsand/Acell
(16)
式中 WR——磨损失重率,壁面磨损失去的质量与颗粒质量的比值,kg/kg
BH——壁面材料的布氏硬度
Fs——颗粒形状系数
θ——颗粒入射角,rad
n——经验常数,取2.41
C——经验常数,取2.17×10-7
ER——磨损率,kg/(m2·s)
msand——固相质量流量
Acell——计算单元壁面网格面积
颗粒形状系数对于棱角颗粒Fs=1,半球形颗粒Fs=0.53,球形颗粒Fs=0.2,本文取Fs=0.2。
2 计算对象和边界条件
本文的研究对象为山西省尊村引黄泵站的双吸离心泵,主要参数为:额定流量Qn=3 m3/s,额定转速n=490 r/min,设计扬程H=32 m,比转数ns=162,叶轮直径D=1.12 m,叶片数z=6,泵进口直径D1=1.1 m,泵出口直径D2=0.9 m。图1给出了双吸离心泵的结构图。
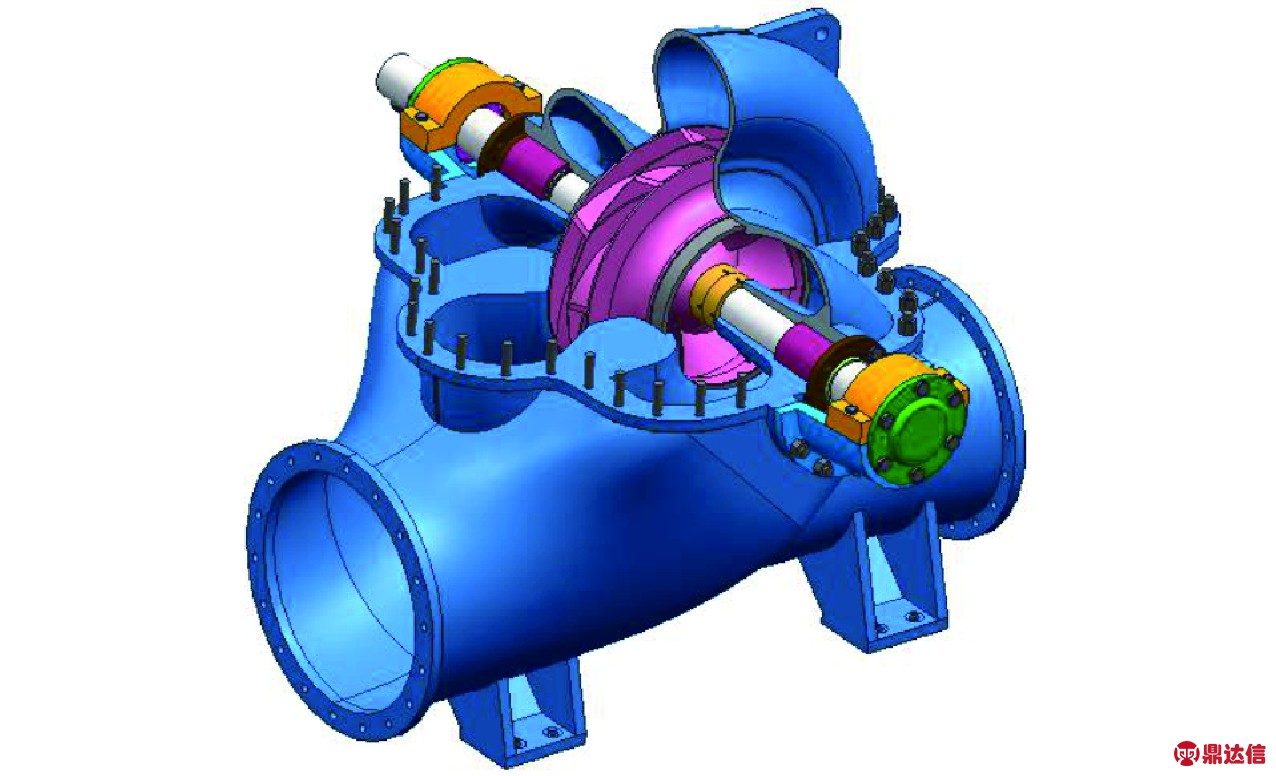
图1 双吸离心泵结构图
Fig.1 Structure image for double suction centrifugal pump
计算含沙条件为:含沙体积分数0.188%,颗粒密度2 650 kg/m3,平均中值粒径ds分别为25 μm、50 μm的2种悬移质典型粒径。
双吸离心泵的计算网格由Gambit生成,在清水状态下,经过网格无关性检查,最终确定各部分网格单元数分别为:叶轮603 620;吸水室564 882;压水室400 447;叶轮与蜗壳之间补充体64 288;进口延长段44 100;出口延长段56 202;总计网格数为1 733 539。网格无关性检查如图2所示,双吸离心泵计算域及网格划分情况如图3所示。

图2 网格无关性检查
Fig.2 Grid-independent verification
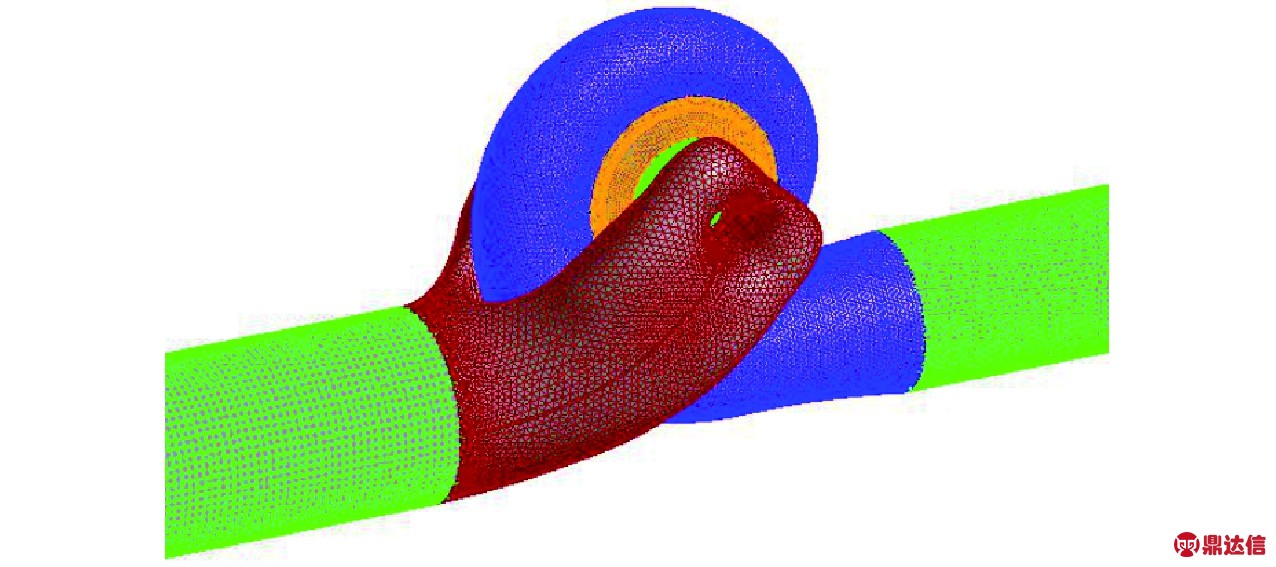
图3 计算域及网格划分
Fig.3 Computational domain and grid
应用Fluent进行数值模拟,运用两相流欧拉传统算法和改进算法对双吸泵进行固液两相流数值计算。由于双吸离心泵内部流动是复杂的固液两相流,作如下假设[21]:不考虑壁面粗糙度,按光滑壁面进行处理;液相为不可压缩流体,固相的物理特性均为常数,不考虑相变;不考虑颗粒形状,颗粒按粒径相同的球形颗粒进行处理;考虑相间阻力作用,忽略升力、马格努斯力、Basset力、附加质量力和压强梯度力[7]。
采用Phase Coupled SIMPLE算法求解二阶迎风格式的离散方程。湍流模型采用RNG k-ε模型,因为该模型可以更好地处理高应变率及流线弯曲程度较大的流动[22];考虑到相间阻力和滑移速度的影响,湍流多相流模型采用Dispersed turbulence 模型,该模型是目前应用较多的一种多相流湍流模型[7,14];相间阻力分别采用传统的Wen-Yu模型和改进的TE-Wen-Yu模型计算;泥沙扩散系数模型分别采用Diffusion-in-VOF模型和DC-PDPC模型进行计算。壁面磨损计算采用图尔萨大学的磨损模型[20]。本文将Wen-Yu模型和Diffusion-in-VOF模型的组合称为传统算法,将TE-Wen-Yu模型和DC-PDPC模型组合称为改进算法,因此,改进算法体现了湍动尺度效应的影响,而传统算法未能体现。
计算域进口采用速度进口,分别给定固液两相的速度,并给定固相体积分数;出口采用自由出流;过流部件内壁面,对液相采用无滑移壁面边界条件,对固相采用自由滑移壁面边界条件,近壁区采用标准壁面函数。
3 计算结果与讨论
3.1 计算得到的外特性分析
为了验证数值计算结果的合理性,采用传统算法和改进算法,对颗粒粒径ds为25 μm、颗粒密度为2 650 kg/m3、体积分数为0.188%的悬移质,在3个工况(0.6Qn、0.8Qn和Qn,Qn表示额定流量)的双吸离心泵的扬程、效率进行数值计算,并与试验值进行对比。试验值是对该双吸离心泵进行现场测试得到的,在水泵进出口安装压力传感器并通过信号采集得到进出口压力脉动,并安装超声波流量计得到水泵流量,采用扭矩仪测量旋转轴扭矩和转速。进出口压力脉动的平均值即为进出口静压。根据进出口静压、流量、扭矩和转速即可得到水泵的扬程和效率。表1、2分别列出了2种算法在各工况下,扬程、效率计算值与试验值的误差分析。
表1 扬程计算值与试验值误差分析
Tab.1 Error analysis between calculated and experiment data for head
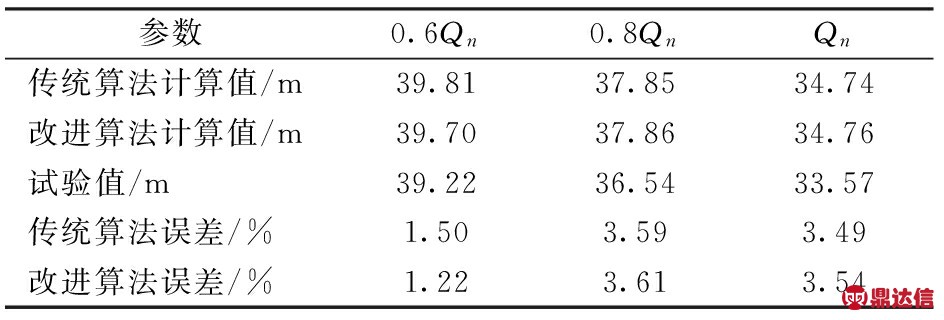
表2 效率计算值与试验值误差分析
Tab.2 Error analysis between calculated and experiment data for efficiency
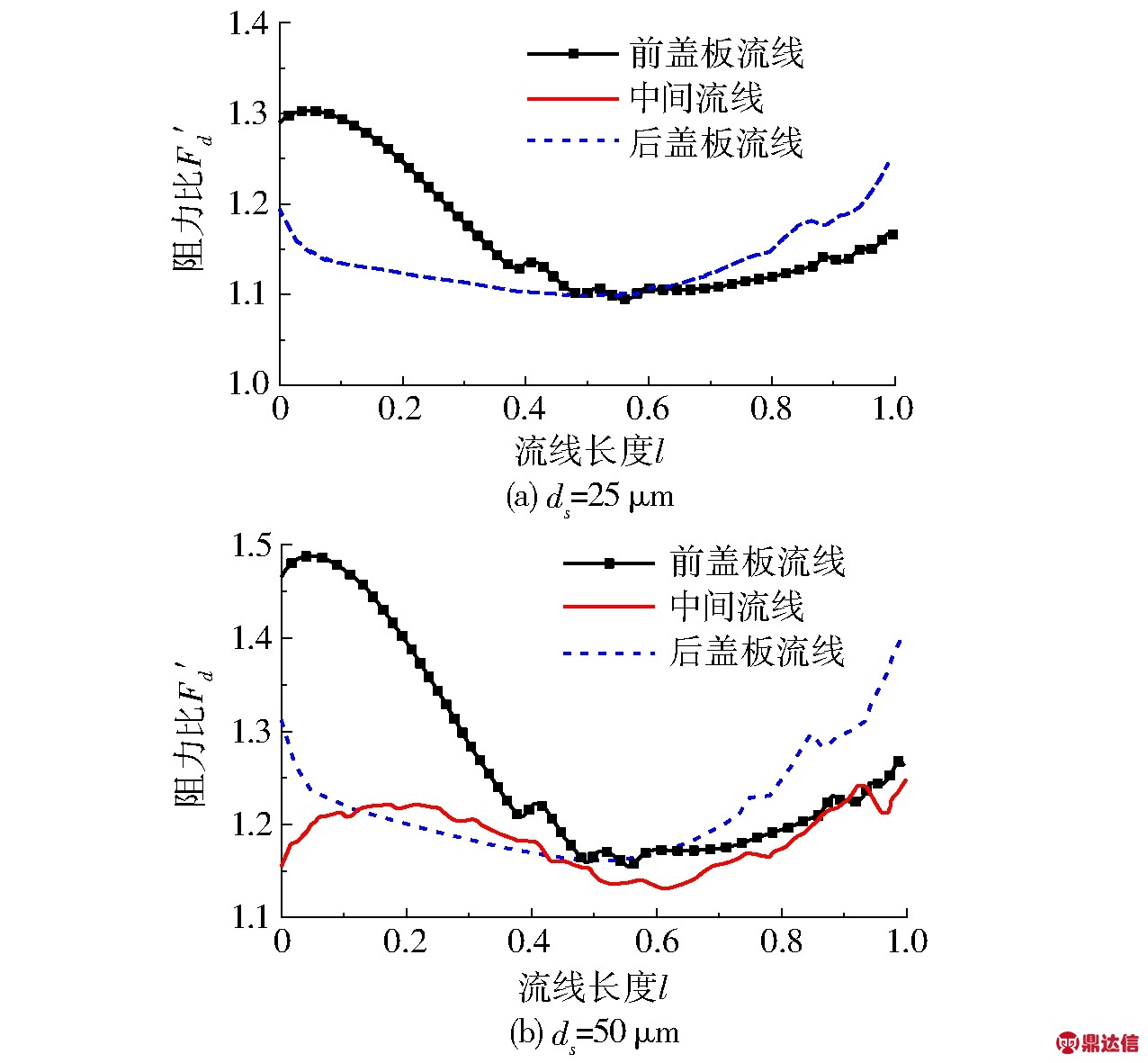
由表1、2可知,传统算法和改进算法计算得到的扬程和效率基本相同,这说明2种算法在外特性计算上没有太大差别。2种算法的计算结果与试验值有一定的误差,计算得到的扬程均高于试验值,最大误差为0.8Qn处的3.61%,而计算得到的效率与试验值较接近,最大误差为2.14%。整体上2种算法的计算值与试验值较为吻合,计算误差在可接受范围内,计算结果合理、可靠,可以用于进一步分析流场特性。
3.2 叶片表面湍流特征
湍流强度和含能涡特征尺寸是湍动尺度效应的重要参数。图4给出了计算得到的双吸离心泵叶片工作面上湍流强度和含能涡特征尺寸的分布。其中,湍流强度计算式为[23]
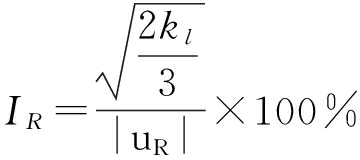
(17)
由图4a可知,叶片工作面的液相湍流强度在1%~10%之间,平均值为4.7%,其中叶片头部湍流强度可达10%。从图4b可知,含能涡特征尺寸为230~840 μm,远大于含沙颗粒的粒径25~50 μm,中部和尾部大于头部,说明中部和尾部的含能涡特征尺寸较大。但是,含能涡特征尺寸并不是影响颗粒扩散的唯一因素,主要是颗粒与含能涡的相互作用,用颗粒粒径与含能涡特征尺寸的比值(颗粒动态尺度)ds/le来衡量。
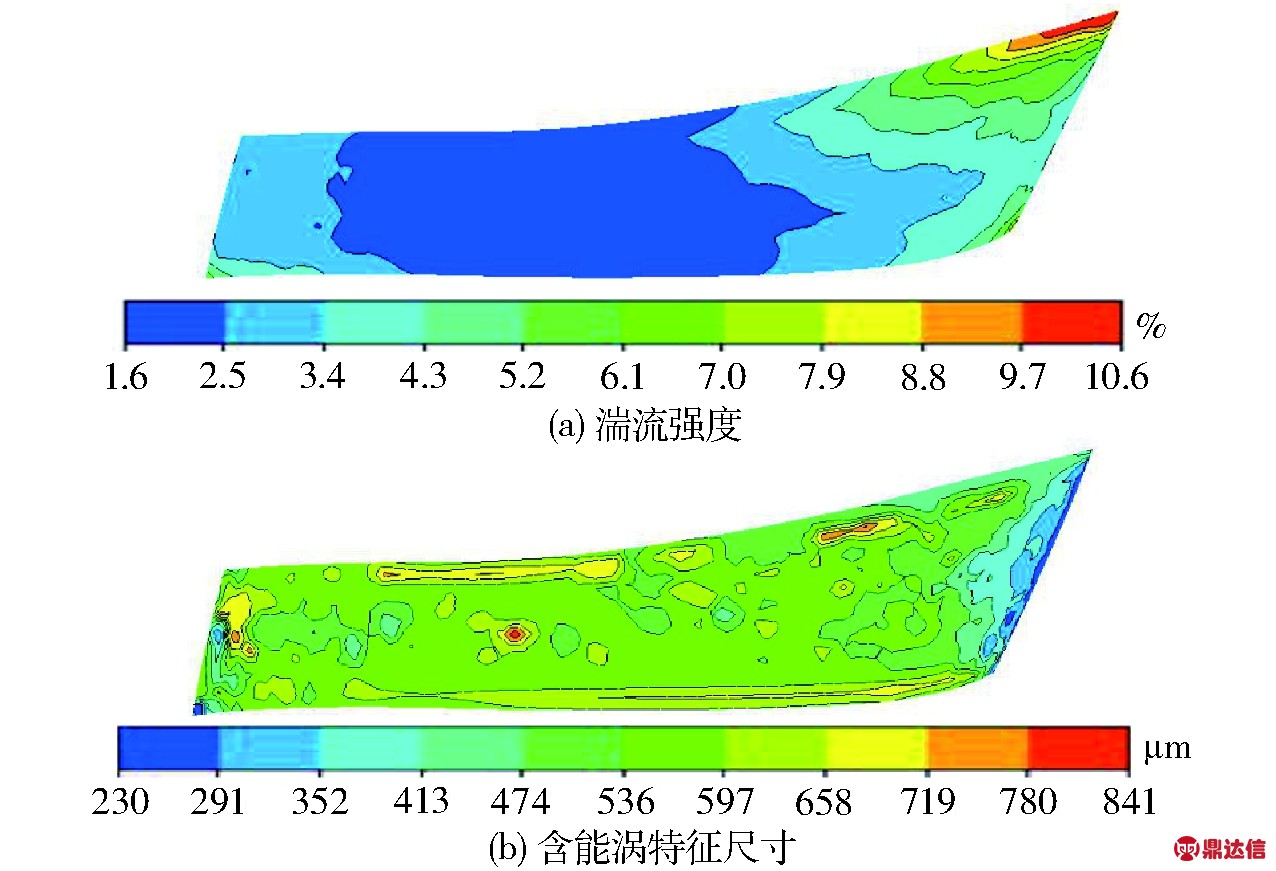
图4 叶片工作面湍流强度和含能涡特征尺寸分布
Fig.4 Turbulence intensity and vortex characteristic scale distributions on blade pressure surface
图5、6分别为粒径25 μm和50 μm条件下叶片工作面3条流线上的湍流强度、颗粒动态尺度分布曲线,图中3条流线分别为叶片工作面与前盖板相交流线、叶片工作面与后盖板相交流线以及叶片工作面的中间流线,分别称为前盖板流线、后盖板流线和中间流线,图中横坐标为从叶片进口到叶片出口的流线长度l(归一化值)。
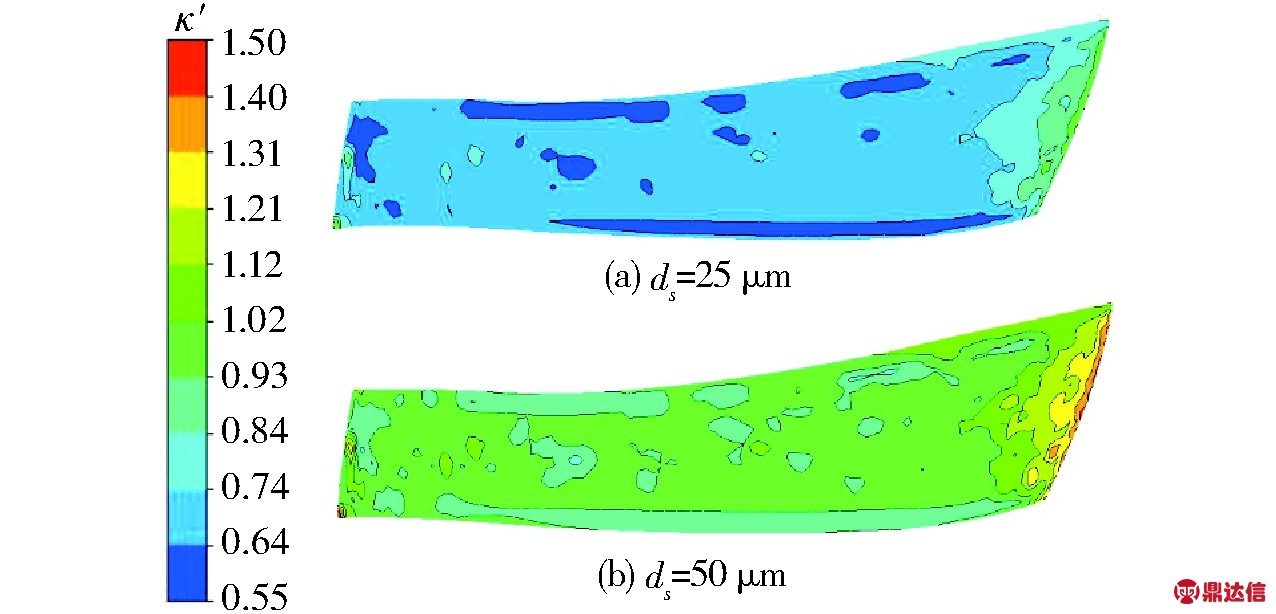
图5 叶片工作面3条流线上湍流强度分布
Fig.5 Turbulence intensity distributions of three streamlines located on blade pressure surface
由图5可知,2种粒径下,液相湍流强度基本相同,说明2种粒径的悬移质颗粒并未对液相的湍流强度造成明显影响。叶片工作面的湍流强度在叶片的头部和尾部较强,可达6%~10%。
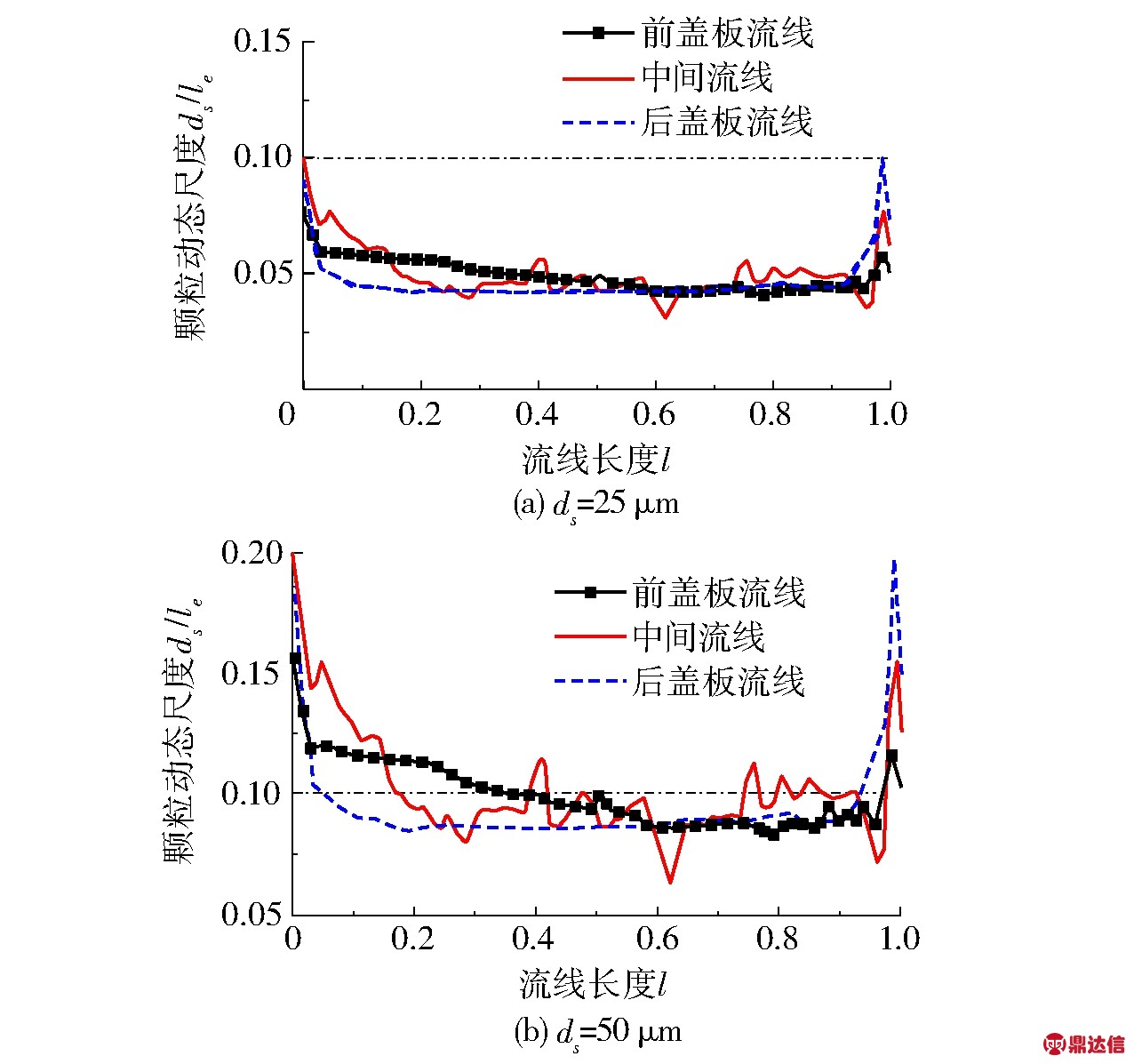
图6 叶片工作面3条流线上颗粒动态尺度分布
Fig.6 Particle dynamic scale distributions of three streamlines located on blade pressure surface
由图6可知,50 μm大颗粒的颗粒动态尺度大于25 μm小颗粒;2种粒径下,均是头部和尾部的颗粒动态尺度大于中部;25 μm小颗粒的颗粒动态尺度均小于0.1,50 μm大颗粒的颗粒动态尺度在头部和尾部大于0.1,在中部小于0.1。颗粒动态尺度小于0.1时表现为对颗粒周围流体湍流强度的削弱作用,大于0.1时为增强作用,进而影响湍流结构的变化。大颗粒在叶片的头部和尾部表现为对颗粒周围流体湍流强度的增强作用。
综上可知,湍流强度和颗粒动态尺度在叶片头部和尾部均较大,表明湍流强度和颗粒动态尺度对固相流场的影响较为强烈。
3.3 固相特性分析
湍流强度和颗粒动态尺度对固相流场的影响统称为湍动尺度效应。在湍流强度低、颗粒粒径远大于含能涡特征尺寸的固液两相流的计算中,如果不考虑湍动尺度效应,则不会对计算结果产生太大影响,但是,对于含低浓度悬移质泥沙颗粒的双吸离心泵,如果不考虑湍动尺度效应,可能导致计算出现偏差。因此,必须分析湍动尺度效应对固相运动的影响。
3.3.1 固液相间作用分析
由图5可知,2种粒径下,叶片工作面上的湍流强度基本相同,但湍流强度对相间阻力的影响,与颗粒的粒径、固液相对速度等有关,湍流强度对不同粒径、不同固液相对速度的颗粒表现出的相间阻力改变是不同的,因此,湍流强度和颗粒雷诺数均是湍流强度对相间阻力的影响因素,见式(6)。图7为2种粒径时,湍流强度引起的相间阻力改变的分布,图中阻力比F′d为考虑湍流强度影响得到的阻力与不考虑湍流强度影响得到阻力的比值。图8为2种粒径时,3条流线上的阻力比分布。
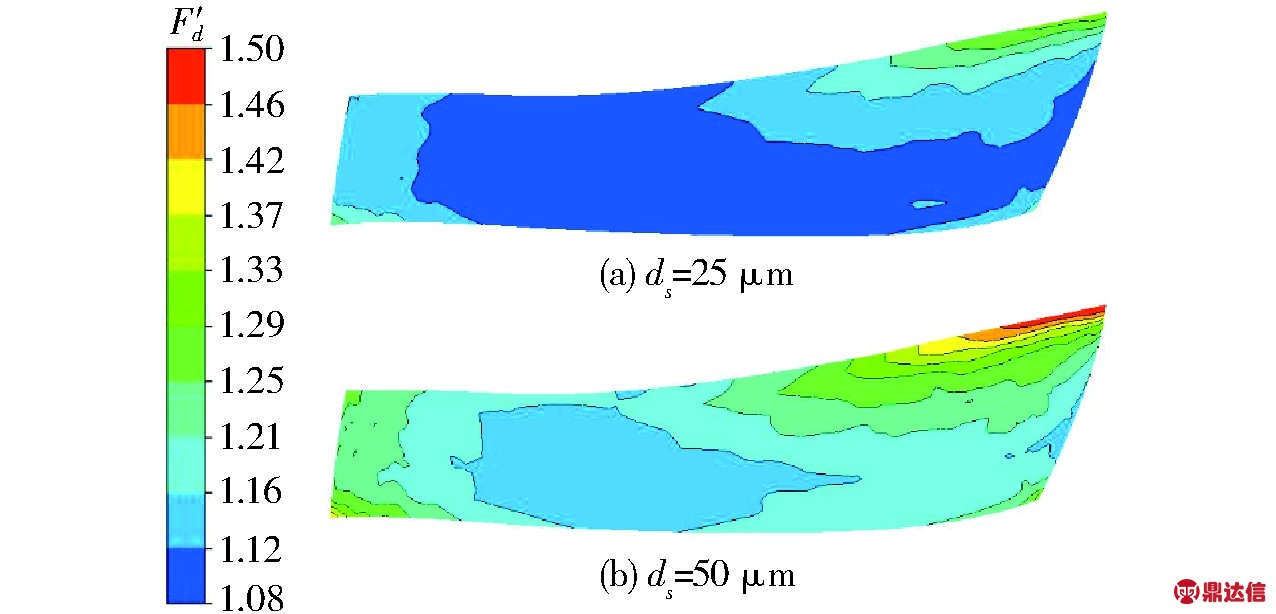
图7 湍流强度引起的叶片工作面阻力比分布
Fig.7 Drag force ratio distributions caused by turbulence intensity on blade pressure surface
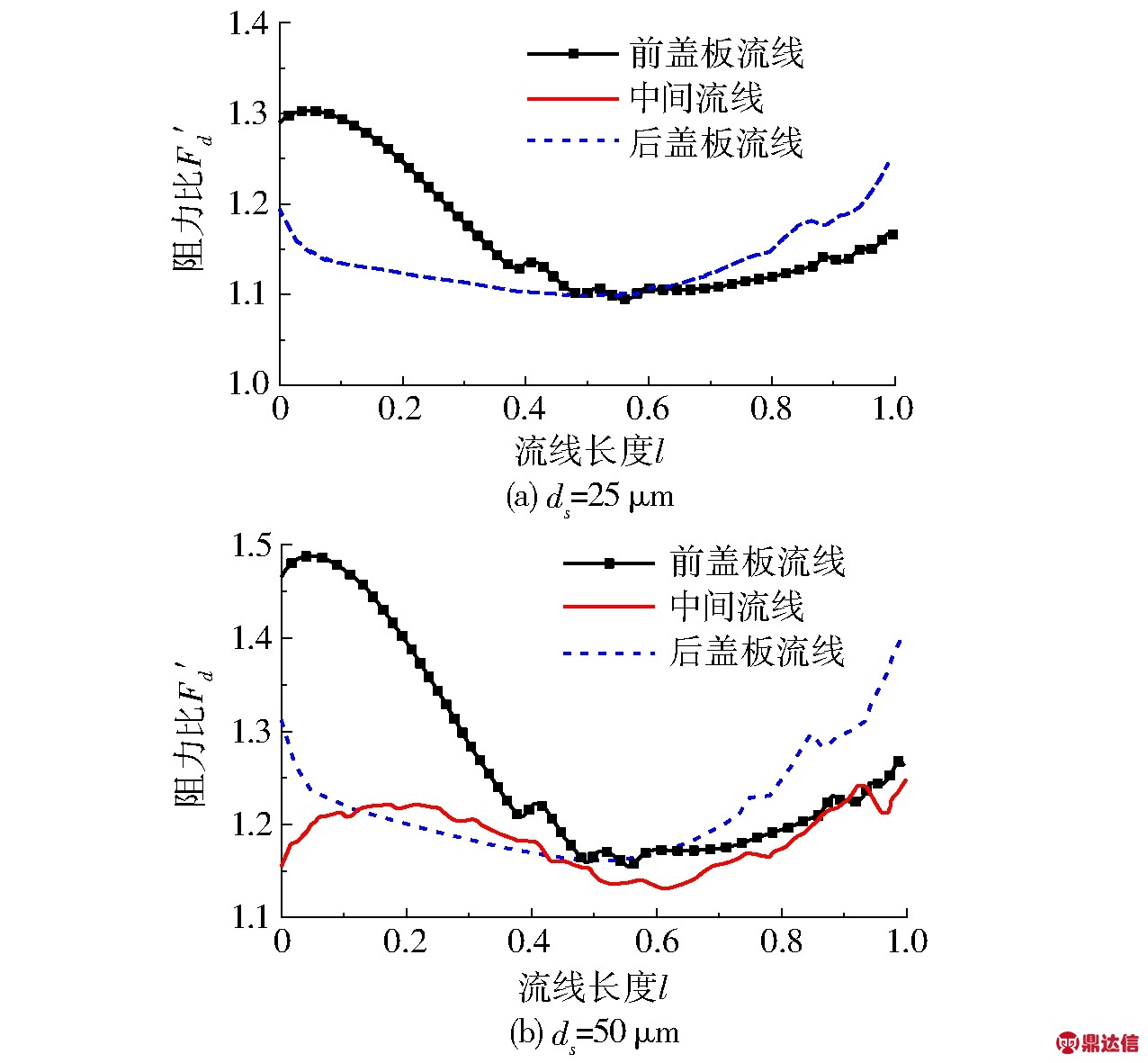
图8 湍流强度引起的3条流线上阻力比分布曲线
Fig.8 Drag force ratio distributions caused by turbulence intensity on three streamlines located on blade pressure surface
由图7、8可知,25 μm小颗粒的阻力比为1.1~1.3,50 μm大颗粒的阻力比为1.1~1.5,大颗粒的阻力比要大于小颗粒。2种粒径下,叶片头部和尾部的阻力比大于中部。说明,不考虑湍流强度时,得到的相间阻力偏小,而考虑湍流强度的影响后,相间阻力有所增大;湍流强度对阻力的影响在头部和尾部强于中部。图8中阻力比的分布趋势与图5中湍流强度的分布趋势相对应。
图9为2种粒径时,颗粒动态尺度对泥沙扩散系数影响的分布,图中泥沙扩散系数比κ′为考虑颗粒动态尺度影响得到的泥沙扩散系数与不考虑颗粒动态尺度影响得到的泥沙扩散系数的比值。为了更清楚地表达泥沙扩散系数比的分布规律,图10给出2种粒径颗粒时,3条流线上的泥沙扩散系数比分布。
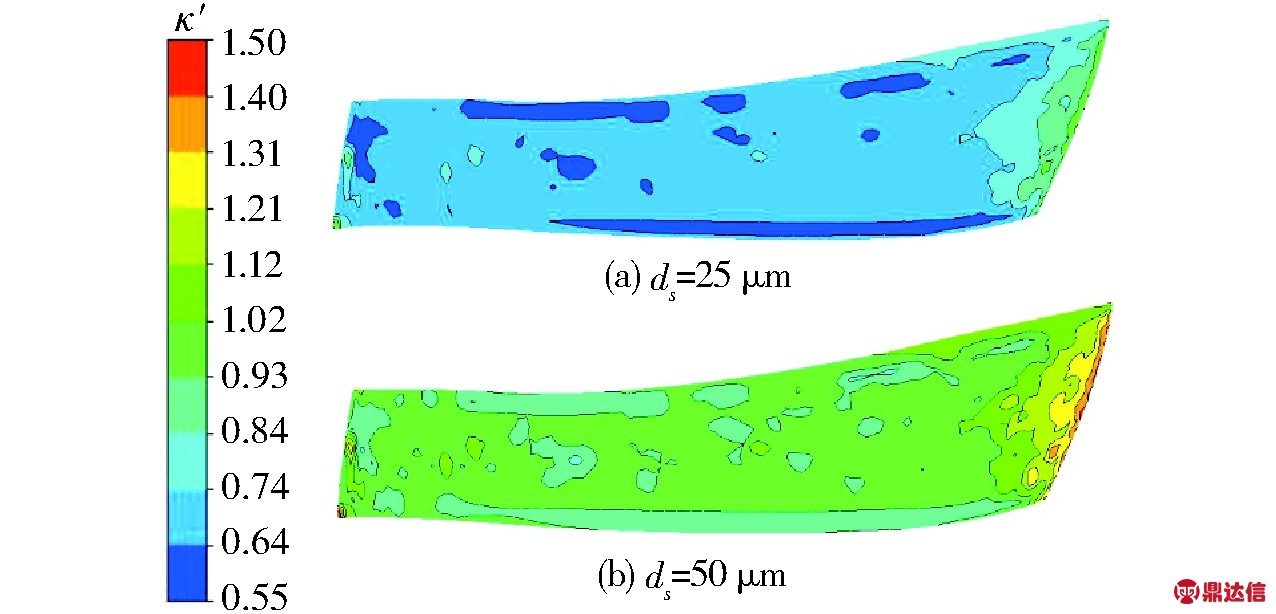
图9 颗粒动态尺度引起的叶片工作面泥沙扩散 系数比分布
Fig.9 Sediment diffusion coefficient ratio distributions caused by particle dynamic scale on blade pressure surface
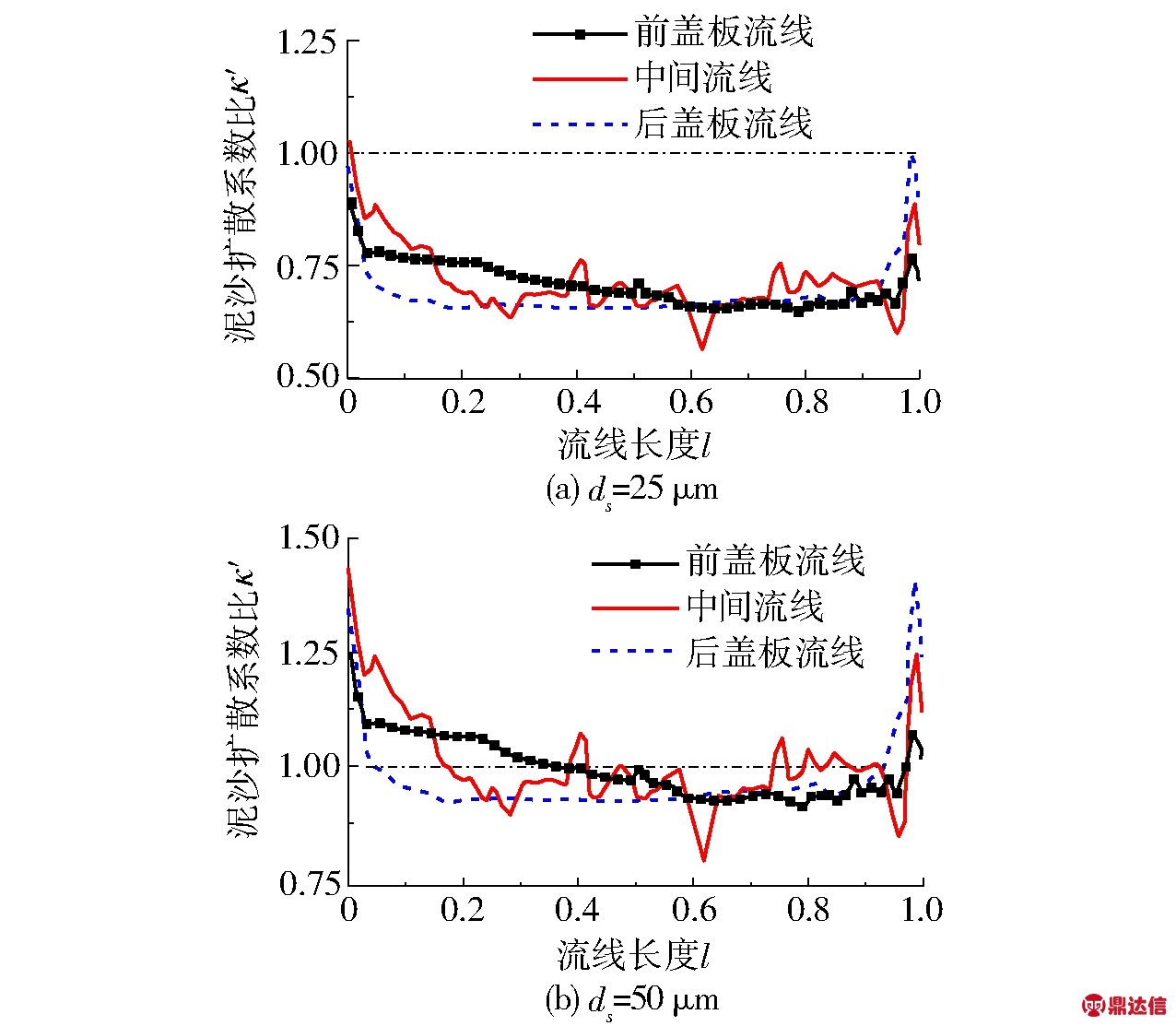
图10 颗粒动态尺度引起的3条流线上泥沙扩散系数 比分布曲线
Fig.10 Sediment diffusion coefficient ratio distributions caused by particle dynamic scale on three streamlines located on blade pressure surface
由图9、10可知,25 μm颗粒条件下泥沙扩散系数比为0.55~1.00,说明颗粒动态尺度导致颗粒的扩散能力变弱;50 μm颗粒条件下泥沙扩散系数比为0.75~1.50,头部和尾部大于1.00,中部小于1.00,说明颗粒动态尺度增强了头部和尾部的颗粒的扩散能力,削弱了中部的颗粒扩散能力;大颗粒的泥沙扩散系数比要大于小颗粒,叶片头部和尾部的泥沙扩散系数比大于中部;说明,颗粒动态尺度使泥沙扩散能力在头部和尾部强于中部。
综上可知,湍动尺度效应使相间阻力和泥沙扩散系数在叶片头部和尾部增长较大,而在中部增长较小,使大颗粒的增大大于小颗粒。相间阻力和泥沙扩散系数的改变导致固相体积分数和固相速度分布的变化。下面对叶片工作面的固相体积分数和固相速度分布进行分析。
3.3.2 固相体积分数和固相速度分析
图11为2种粒径下,湍动尺度效应引起的叶片工作面固相体积分数分布变化的情况。
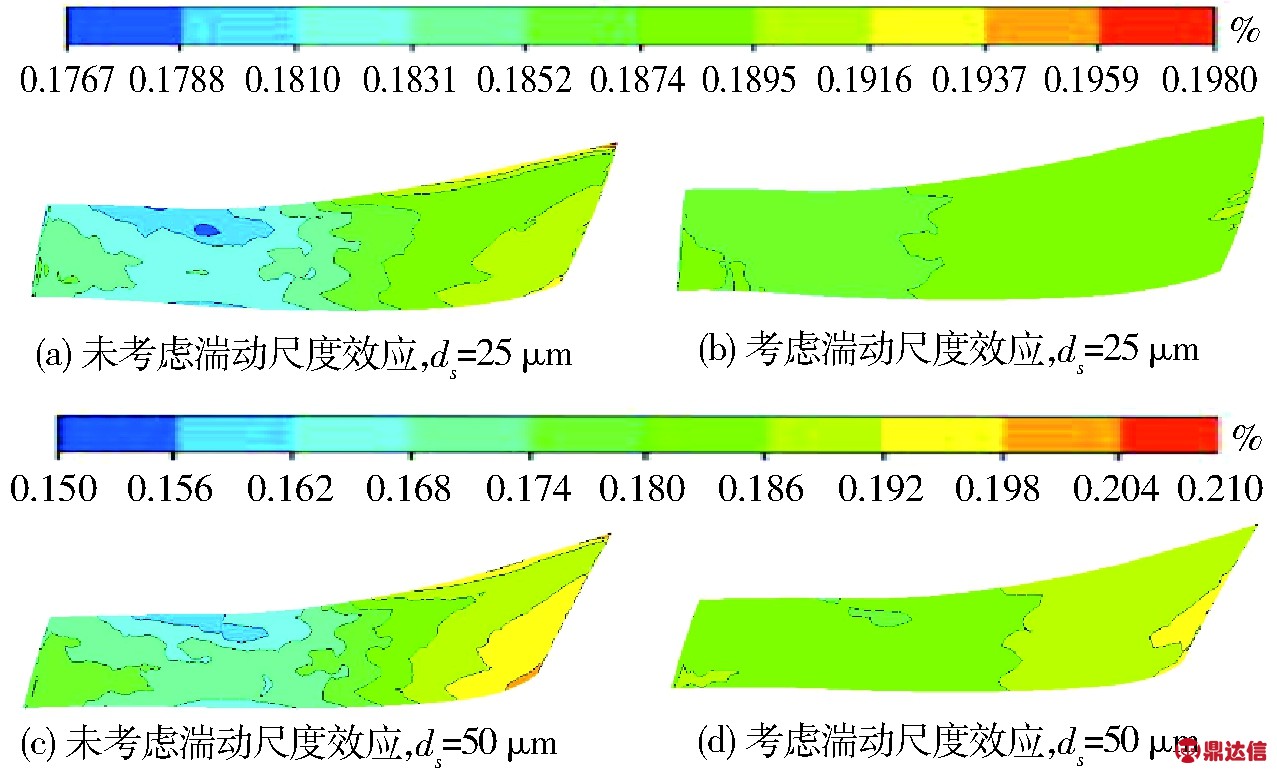
图11 工作面固相体积分数分布
Fig.11 Calculated solid volume fraction distributions for blade pressure surface
图12、13分别给出了叶片工作面的3条流线上固相体积分数、固相速度变化曲线。为了更清楚地显示固相速度的变化趋势,图13仅给出后半部分流线(l为0.5~1.0)上的固相速度分布曲线。表3为2种粒径时,湍动尺度效应引起的叶片工作面的固相体积分数最大值和最小值及其差值的变化。
由图11、表3和图12可看出,湍动尺度效应会引起固相体积分数最大值与最小值的范围明显减小;由图12可以看出,2种粒径下,湍动尺度效应会使固相体积分数在叶片头部和尾部的变化远大于中部,而且50 μm大颗粒的改变值大于25 μm小颗粒,这是因为,湍流强度对阻力的增大作用,颗粒动态尺度对颗粒周围流体湍流强度的增强作用,使相间阻力和泥沙扩散系数在头部和尾部的增大值明显高于中部,而且50 μm大颗粒的相间阻力和泥沙扩散系数改变值大于25 μm小颗粒。
综上可知,湍动尺度效应对双吸离心泵内悬移质颗粒运动具有显著影响,使相间阻力偏大,有利于颗粒的扩散,避免颗粒聚集现象的出现,在叶片头部和尾部的作用强于中部,对大颗粒的作用强于小颗粒。而与图12相对应,图13是相应固相速度的分布,可以看出,湍动尺度效应引起的固相体积分数的改变,导致固相速度相应地变化,只是由于含沙浓度较低,流速较大,固相速度的变化值相对较小。
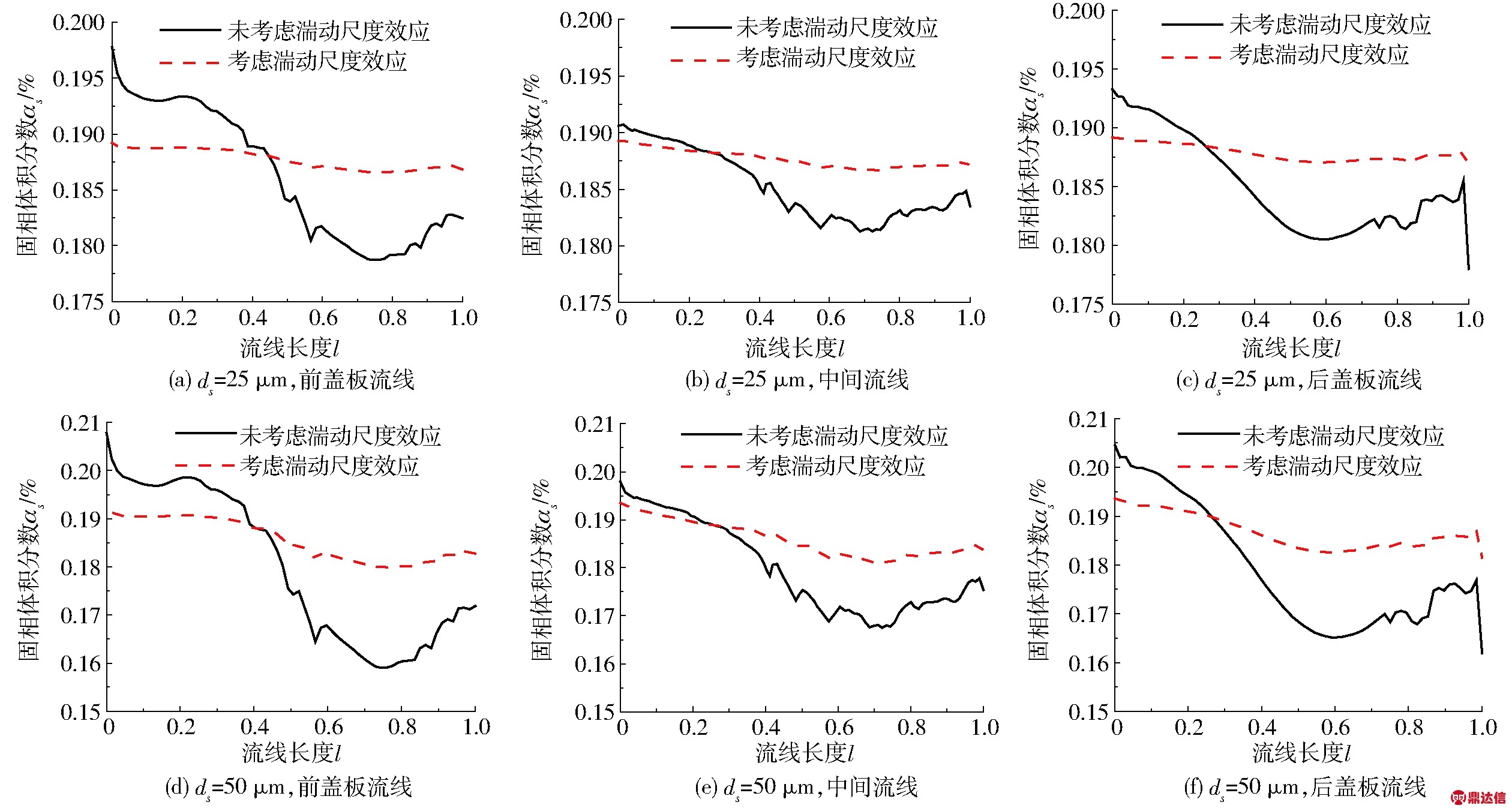
图12 叶片工作面3条流线上固相体积分数分布
Fig.12 Calculated solid volume fraction distributions of three streamlines located on blade pressure surface
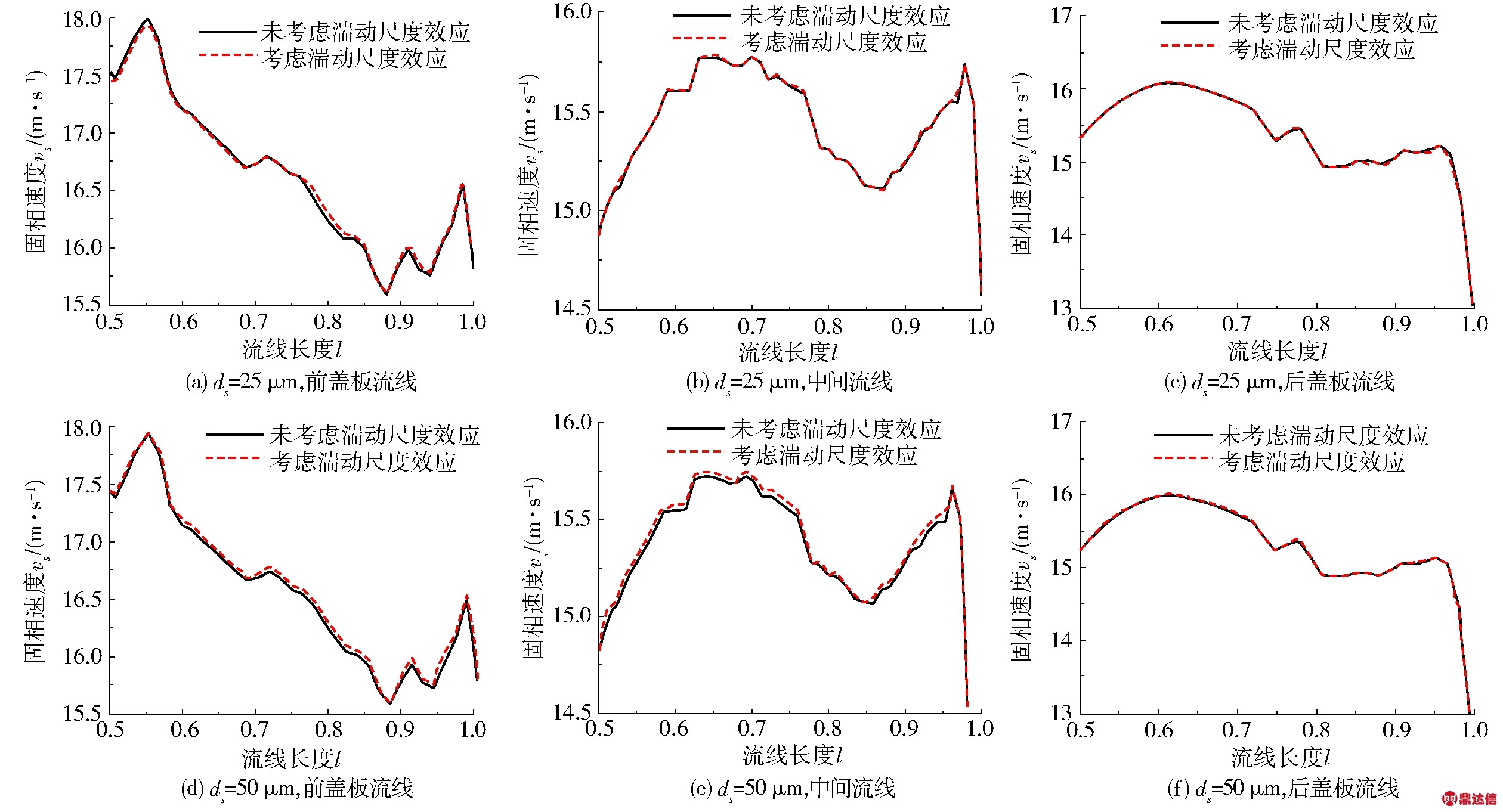
图13 叶片工作面3条流线上固相速度分布
Fig.13 Calculated solid velocity distributions of three streamlines located on blade pressure surface
表3 叶片工作面固相体积分数
Tab.3 Maximum and minimum values of solid volume fraction for blade pressure surface
%
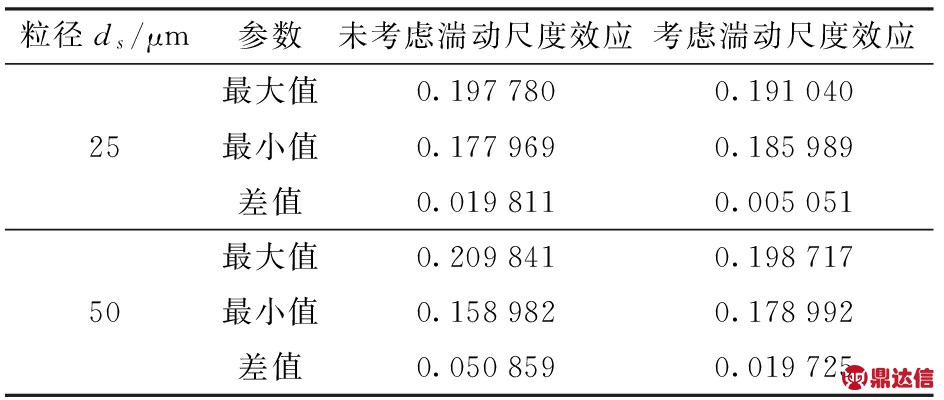
3.4 叶片磨损特性分析
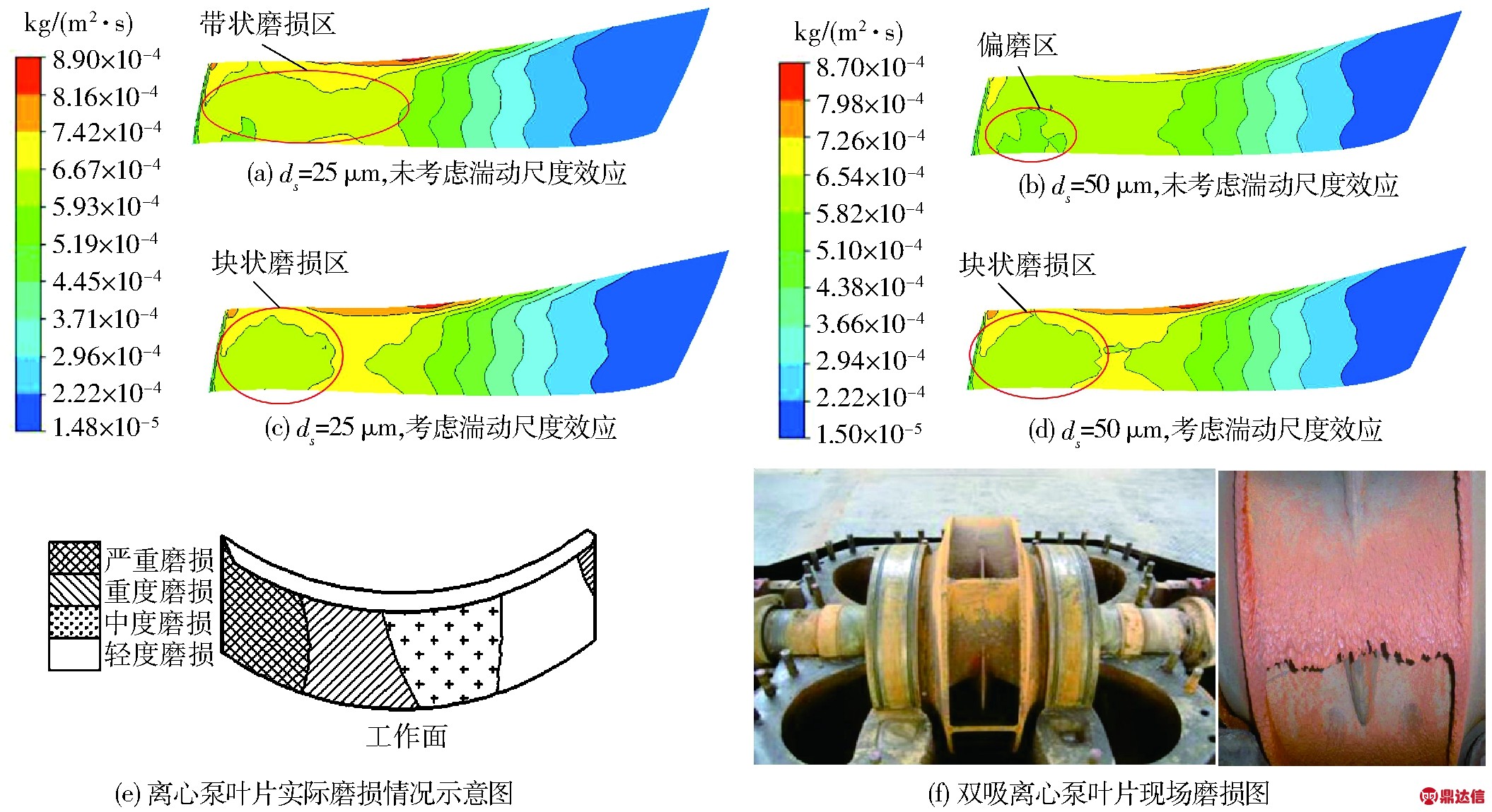
图14 叶片工作面上的磨损率计算结果与实际情况对比
Fig.14 Calculated erosion ratio distributions for blade pressure surface compared with actual erosion conditions of centrifugal pump blade
图14给出了2种粒径下,叶片工作面磨损率分布,图中还给出了离心泵叶片表面的实际磨损部位、磨损程度和现场磨损情况。叶片表面的实际磨损情况是根据总结现有双吸离心泵的实际磨损情况[21,24]得到的。表4给出了湍动尺度效应引起的叶片工作面最大磨损率的变化情况。
由图14可知,2种粒径下,采用改进算法,即考虑湍动尺度效应所得到的叶片尾部磨损区为块状,与实际磨损情况更接近,而采用传统算法,即不考虑湍动尺度效应计算得到的叶片尾部磨损区为带状或局部偏磨状,与实际磨损情况相比有较大偏差。这是因为,在引入湍动尺度效应后,相间阻力增大,提高了颗粒扩散能力,导致磨损计算更加均匀,磨损结果整体上更接近叶片的实际磨损情况,在叶片尾部表现明显。无论在小粒径条件还是大粒径条件下,叶片表面由进口到出口磨损程度逐渐加重,叶片尾部磨损严重;同时,由表4可知,考虑湍动尺度效后,磨损率的最大值有所增加,即磨损程度稍有增大。
表4 叶片工作面磨损率最大值
Tab.4 Maximum value of erosion ratio for blade pressure surface kg/(m2·s)

4 讨论
近年来,双吸离心泵的水力设计方法已由传统的经验设计方法转入以流动理论为基础的交替加载设计方法[25],载荷曲线上主加载点位置与叶片做功方式、水泵汽蚀性能等有直接关系。针对湍动尺度效应在叶片头部和尾部表现强烈,引起固相体积分数在叶片头部和尾部的变化值较大的情况,为了降低双吸离心泵叶片表面最大磨损率、提高磨损均匀度,需要减弱叶片头部和尾部的做功能力。为此,建议在文献[25]给出的交替加载方式基础上,将前加载点后移,后加载点前移。
目前,HVOF工艺喷涂WC-Ni60合金粉末涂层技术、电火花沉积WC-8Co合金涂层技术、液体橡胶改性环氧树脂金刚砂涂敷技术和改性聚氨酯复合树脂涂敷技术,是常用的水泵磨损防护技术[26]。相比于液体橡胶改性环氧树脂金刚砂涂敷技术和改性聚氨酯复合树脂涂敷技术,HVOF工艺喷涂WC-Ni60合金粉末涂层技术和电火花沉积WC-8Co合金涂层技术具有涂层与母材结合好、抗磨性能好、涂层厚度小、耐磨寿命长的优点,但是有工艺相对复杂、成本较高的缺点,因此,一般只用于局部磨损严重区域的抗磨防护。通过本文的研究可以发现,叶片工作面尾部占叶片工作面面积1/4的区域为严重磨损区,而并非带状区和靠近后盖板的偏磨区,因此,应采用HVOF工艺喷涂WC-Ni60合金粉末涂层技术和电火花沉积WC-8Co合金涂层技术对叶片尾部的局部区域进行重点防护。
此外,大颗粒引起的湍动尺度效应作用强于小颗粒,因此,应该尽量减小大颗粒的体积分数,通过修建沉沙池或增加其他的颗粒过滤设施,来降低过泵泥沙含量,从而间接提高双吸离心泵的抗磨能力。
5 结论
(1) 叶片表面湍流强度在头部和尾部湍流强度较大,可达6%~10%;25 μm小颗粒的颗粒动态尺度均小于0.1,对周围流体湍流强度具有削弱作用,50 μm大颗粒条件下的颗粒动态尺度在叶片头部和尾部均大于0.1,对周围流体湍流强度具有增强作用,叶片头部和尾部的颗粒动态尺度大于中部,大颗粒的大于小颗粒。湍动尺度效应在叶片头部和尾部表现强烈,大颗粒的表现强于小颗粒。
(2) 湍动尺度效应使得固液相间阻力有所增大,有利于颗粒的扩散,避免出现颗粒聚集现象,对大颗粒的作用强于小颗粒,在叶片头部和尾部的作用强于中部,计算得到的固相体积分数最大值与最小值的范围明显减小;湍动尺度效应使得大颗粒的固相体积分数改变值大于小颗粒,固相体积分数在叶片头部和尾部的变化远大于中部。
(3) 湍动尺度效应使叶片表面的严重磨损部位为叶片工作面尾部的块状磨损区,而并非未考虑湍动尺度效应得到的带状磨损区和靠近后盖板的偏磨区,考虑湍动尺度效应后得到的磨损结果更符合离心泵叶片的实际磨损情况;湍动尺度效应使磨损率稍有增大。
(4) 为了提高双吸离心泵抗磨能力,在水力设计时,叶轮应该采用混合加载方式,并使前加载点后移,后加载点前移;在叶片表面涂层时,可采用如HVOF工艺重点对叶片工作面尾部局部区域进行重点防护。