摘 要:位移传感器技术是一项对现代科学研究和工业生产有着重要影响的传感器技术,基于电磁感应原理,设计了一套钢栅位移传感系统。整个系统由基于ARM的信号处理主板、激励线圈、感应线圈和钢栅尺构成。主板通过感应信号的检测和计算得到位移信息。使用激光干涉仪进行了性能测试,测试结果表明,传感器分辨率达到1 μm,在35 cm的量程内位移误差在10 μm左右。系统运行稳定,结构简单易维护,并且可以支持非直线测量,具有较高的实用性。
关键词:传感器技术;位移传感器;电磁感应;平面线圈;钢栅尺
位移传感器在高精度数控机床、航空航天、石油化工等重要领域有着广泛应用。各行各业尤其是现代化工业对位移传感器的精度、小型化、抗干扰和数字化等等要求越来越高[1]。
常见的位移传感器有光栅尺、球栅尺、磁栅尺等。光栅尺是基于光的透射和反射现象制成,具有高精度与高分辨率,但成本极其昂贵[2]。球栅尺采用全封闭结构,抗污染能力强且寿命长[3]。磁栅尺由于磁栅传感器具有非接触、量程大和精度高等性能,因此市场需求也比较高,其良好的性能和相对低廉的成本,使其具有巨大的应用开发潜力和市场前景[4]。但磁栅尺利用对磁性薄膜充磁来实现磁栅的磁性,会存在消磁和磁滞的现象,运行不稳定且不方便。
本文在磁栅尺原理的基础上,参考AMO感应式测量原理[5],设计了基于全感应原理的位移传感器,采用微多层技术设计的平面线圈替换磁栅尺的磁头和静态磁栅,去除磁性物件,无消磁危险和磁滞反应,使用方便。
1 磁栅尺工作原理
磁栅位移传感器具有非接触、量程大、精度高、可靠性高、寿命长、安装维护方便等特性。因良好的性能以及相对低廉的成本,近年来在测控领域的应用不断增加,年增长率达到了20%~30%左右。传统的磁栅结构如图1所示[6]。
传统磁栅尺以不导磁的材料作为磁基,在上层均匀镀上一层磁膜,并录上磁极性正负交错、间距相等的磁信号格栅做成静态的磁栅[7]。磁头间距为(m±1/4)λ,其中m为正整数,λ为一组磁条的长度。输出电压为:
e1=E0sin(2π/λ)sin(ωt)
(1)
e2=E0cos(2π/λ)sin(ωt)
(2)
E0为磁通量大小相关系数。由上式可见,通过将第1组磁头的激励电流移相45°,并将两组磁头信号求和,通过相位检测法,即可测得位移量的变化[8-9]。
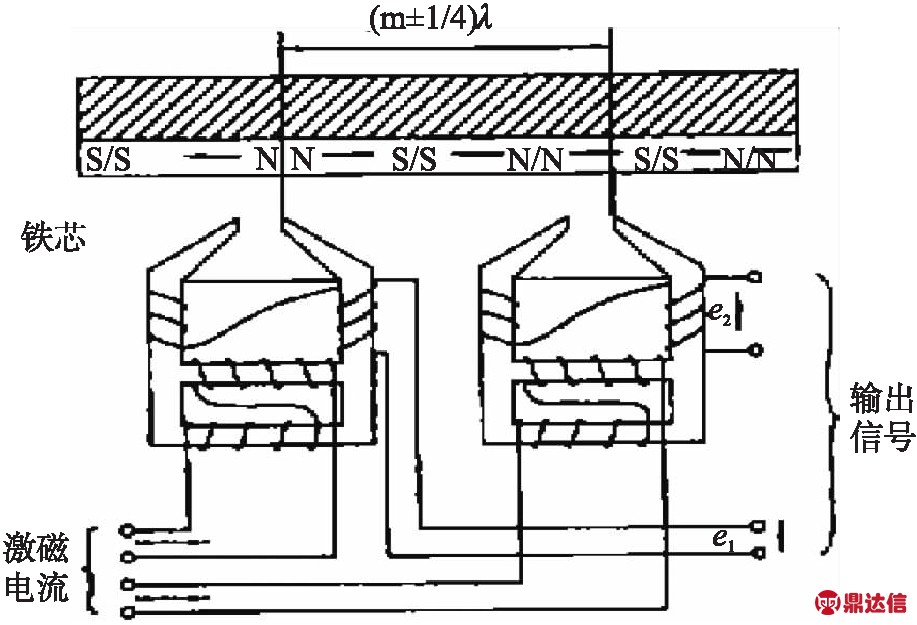
图1 磁栅传感器结构图
2 全感应式位移传感器原理
传统磁栅尺身必须要满足一定要求的磁栅合金制成,且磁性薄膜需要在高精度的专用录磁设备上录磁来实现磁栅尺的磁性,这就使得其制作成本较为昂贵。此外,磁头在滑动过程中可能造成的摩擦还会导致录磁信号有可能被擦掉。为解决上述问题,本论文参考AMO感应式测量原理,利用电磁感应原理,使用平面线圈替换磁栅尺的磁头,且用钢栅尺替换静态磁栅。从而没有磁性元件,所以相对于磁栅尺结构有成本低、寿命长和可靠性高等优点。系统结构如图2所示。
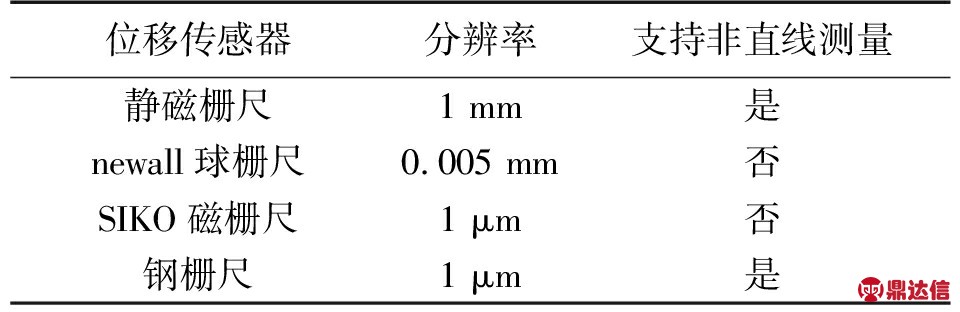
图2 磁栅位移传感器工作示意图
图2中上半部为等间隔镂空的钢栅尺,下半部为由激励线圈和感应线圈构成的平面线圈模块。当正弦交流信号施加到激励线圈上,变化的电压会在钢栅尺附近形成一个变化的磁场,感应线圈在这个变化的磁场中会因电磁感应而得到感应电动势[10]。由式(1)和式(2)可知,相邻两组感应线圈之间会产生相位差为π/2的感应电动势。即选择一组感应线圈的信号为正弦信号时,相邻的一组感应线圈的信号则为余弦信号。当读数头在尺身上进行非接触的自由移动时,感应线圈与栅格的相对位置也会发生变化,因此激励线圈与感应线圈之间的互感系数M也会发生变化,从而会造成感应电动势幅度的变化。由此,可以根据当前位置两组感应线圈的正弦与余弦信号,计算得到当前位置对应的角度值α,该值以栅格长度为周期在0~360°之间变化,从而可以根据连续两次测量得到的角度值计算得到两次测量间的位移值s如式(3)所示:
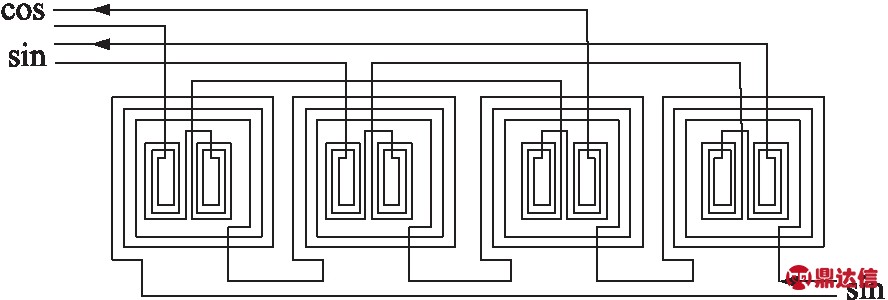
(3)
式中:α为当前测量得到的角度值,α′为上次测量得到的角度值,λ为栅格间距。假设在连续两次测量间隔内位移不会超过半个栅格间距的长度(可以通过控制测量间隔保证)。在连续移动的过程中,还需判断相邻两次测量是否跨越一个栅格,同时需要判断出位移的方向,并依此计算得到当前的绝对位移d,如式(4)所示:
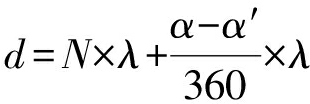
(4)
式中:N为栅格个数。N的计算方法如下:
(1)当前角度大于180°,上次保存的角度小于180°,且两者之差大于180°,则认为滑块往后退了,栅格数需要减1。
(2)当前角度小于180°,上次保存的角度大于180°,且两者之差大于180°,则认为滑块往前进了,栅格数需要加1。
(3)其他情况则认为在同一栅格内发生的位移,则栅格数保持不变,只记录角度值。
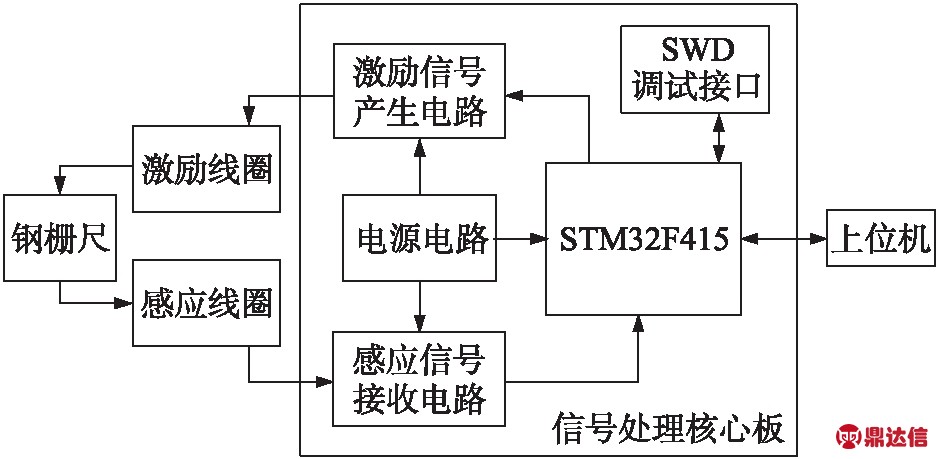
图3 磁栅传感器硬件总体框图
3 全感应式位移传感器设计
3.1 硬件系统设计
本文的钢栅位移传感器是以型号为STM32F415的ARM处理器为核心。系统由信号处理核心板、激励线圈、感应线圈、钢栅尺构成,信号处理核心板包括微处理器STM32F415、激励信号产生电路、感应信号接收电路、电源电路等组成,同时系统设计采用UART接口上传测量得到的位移数据给上位机,系统框图如图3所示。
本论文激励信号的设计如图4所示。首先由ARM处理器通过对时钟分频输出制定频率的PWM波,通过低通滤波器LTC1563获得相应频率的正弦信号VOUT。最后将VOUT通过DRV1100放大2倍得到峰峰值为6.6 V的差分正弦激励信号和
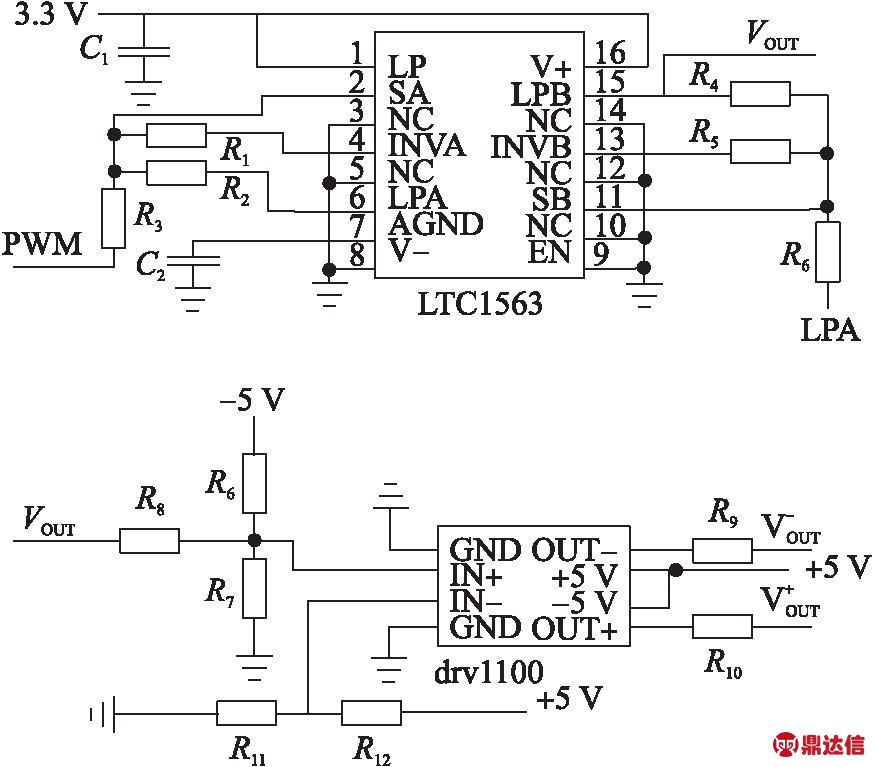
图4 激励信号产生电路
感应信号接收模块将感应线圈信号进行放大,然后通过AD采样传入STM32F415中。由于感应电动势的信号为毫伏级,不仅如此,时常还伴随着较大的共模干扰,所以在设计放大电路时需要较高的放大倍数和共模抑制比。感应信号接收电路如图5所示。对正弦和余弦感应信号同时放大48倍,得到放大后的感应电压XINPUT和YINPUT。
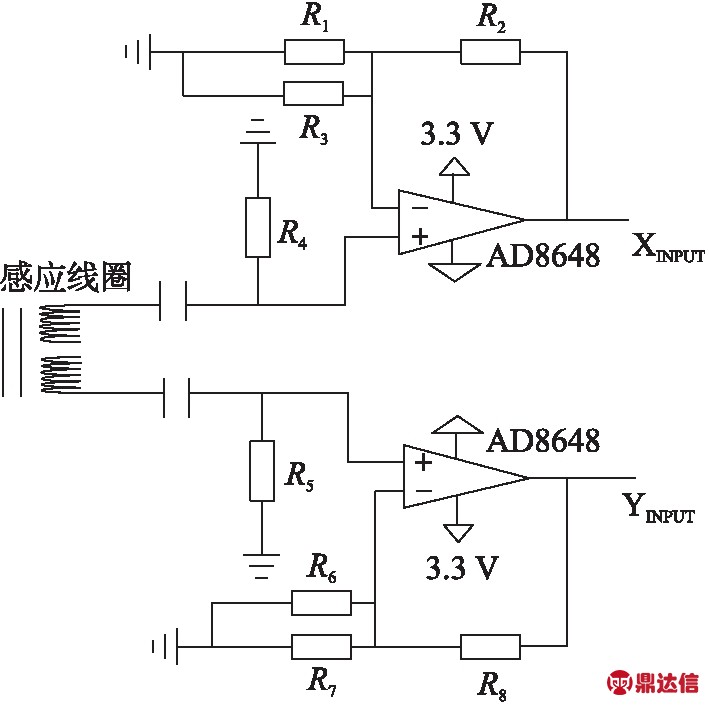
图5 感应信号接收电路图
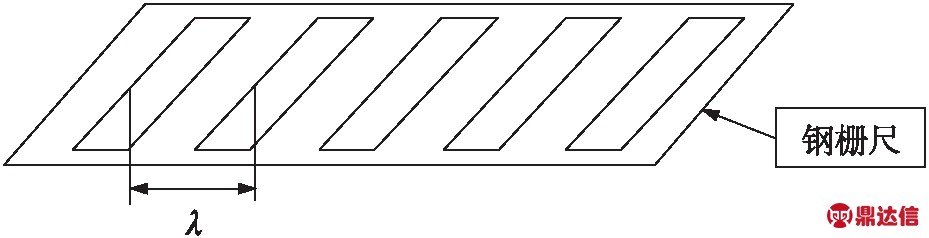
图6 钢栅尺示意图
3.2 钢栅和平面线圈设计
钢栅尺结构示意图如图6所示。钢栅尺由不锈钢制成,每间隔λ有一个镂空的栅格。在激励线圈与感应线圈产生电磁感应的过程中,钢栅尺为其提供感应电动势周期性变化的条件。
本论文方案采用柔性电路板(FPC)平面线圈设计技术。为保证产生相位相差π/2的正弦和余弦感应信号,在平面线圈设计中确保2组感应线圈的间距为(m+1/4)λ,其中λ为磁栅尺的栅格间距,m是正整数,且每组感应线圈采用背靠背(线圈绘制方向相反)的布局方式以提供电磁回路。同时为确保感应信号的产生,采用激励线圈与感应线圈嵌套布局的方式。线圈的设计示意图如图7所示,激励线圈布局于感应线圈外围,2组感应线圈间隔布局。当激励线圈施加正弦激励信号时,在测量方向的相对运动会在读数头和尺身之间改变感应线圈间的周期性交互作用,两组感应线圈之间就会产生相位差为π/2的感应电动势,即形成正弦和余弦函数波形,通过对这两组感应信号的检测和计算即可得到位移信息。
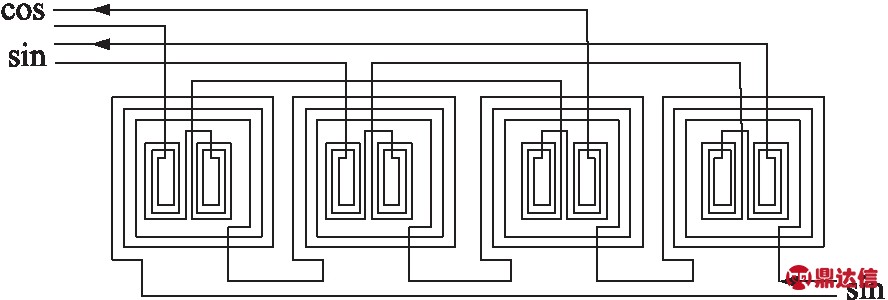
图7 线圈设计示意图
为增大感应信号的强度,本论文的线圈设计采用了多层多级技术。论文使用3层电路板进行激励线圈设计,每层绘制8个激励线圈,共24组线圈;感应线圈使用4层电路板设计,对应正弦和余弦感应线圈每层分别绘制3组,共12组。各组线圈采用水平布局方式,线圈间隔需满足设计需求,除首尾2组外,其他6个激励线圈内均嵌有感应线圈。激励线圈和感应线圈的一个设计实例如图8所示。
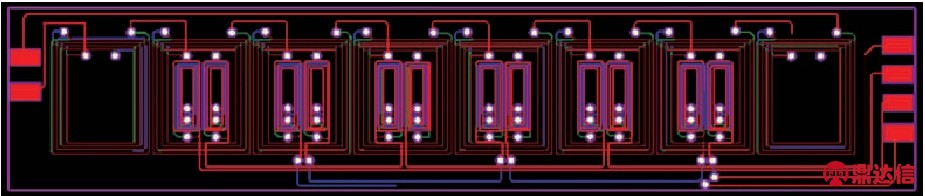
图8 线圈PCB设计实例图
4 软件设计
在系统启动之后,初始化STM32F415。随后对GPIO进行初始化,将I/O口根据系统设计的功能要求进行相应的功能配置。接着对定时器1、2、3分别初始化,设置预分频计数器的值,配置相匹配的引脚输出和相应的捕获中断触发方式。其中定时器1用于激励信号PWM波的生成,定时器2用于处理位移数据并进行相应的位移量计算,定时器3用来进行AD采样。随后对UART模块进行初始化,配置其波特率等相关参数。在程序执行的时,定时器1首先会控制PWM频率并传输到激励信号产生电路中,定时器3控制对感应信号进行AD采样的频率,并把采样数据以DMA的传输方式放入缓存区。定时器2与定时器1进行级联,由定时器1对其进行触发,定时器2以4 kHz的频率触发中断,中断程序对AD采样到的感应信号数据进行处理并计算位移量。在接收到上位机的UART数据请求中断中断后,将测量结果通过UART发送到上位机。软件流程图如图9所示。
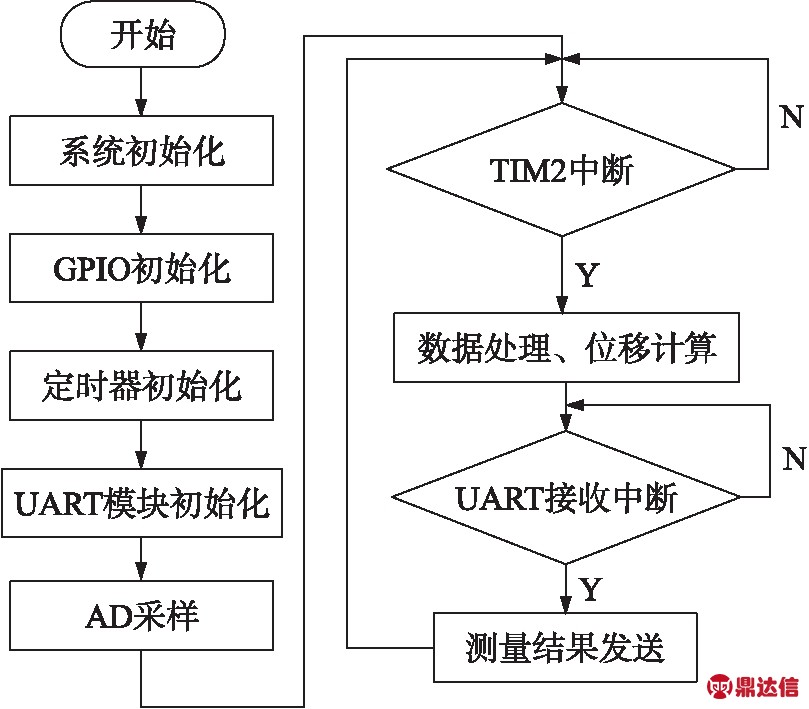
图9 系统软件流程图
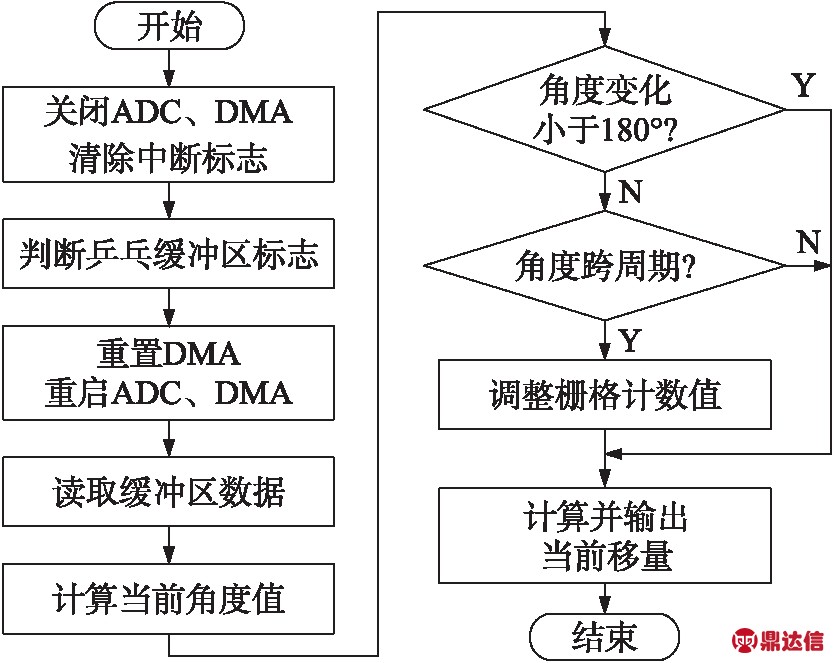
图10 数据处理及位移计算流程图
使用STM32的ADC1与ADC2分别采集正弦和余弦感应信号,并利用DMA实现数据的搬移和乒乓缓冲区技术实现数据接收。在接收到一帧数据接收完成的中断时,中断服务程序首先关闭ADC与DMA,清除中断标志,然后读取乒乓缓冲区标志,并根据乒乓缓冲区标志重置DMA的目的地址,随后重启ADC和DMA进行下一帧数据的接收。处理程序根据乒乓缓冲区标志读取相应缓冲区中的数据计算出当前角度值并记录下来,再依据上次的记录值判断此次角度变化有没有大于180°,依据第2节介绍的方法,判断是前进还是后退并记录N数值变化。最后依据前后角度的变化的值和增减的栅格数量计算出当前位移量。数据处理及位移计算流程如图10所示。
5 系统测试与性能分析
本文所设计的全感应式位移传感器通过与激光干涉仪的测量结果进行比较来完成精度的测试。本论文在测试中,使用RENISHAW公司的ML10 Gold激光干涉仪,其分辨率达到了0.1 μm[11],足以对本钢栅位移传感系统进行精度测试。在测量开始时,先对激光干涉仪与磁栅位移传感器同时进行清零操作,设定激光干涉仪以5 mm为单位进行位移,逐次对上位机中读取到的系统测量值进行记录。以激光干涉仪为基准,对应点标准值与系统测量的结果采用线性拟合算法进行误差补偿[12],并将拟合方式运用于随后的测量中。表1给出了拟合后测量的部分结果。
表1 测量结果

由表1可见,本方案中基于STM32F415的磁栅位移测量系统运行稳定,工作正常,在量程为35 cm的情况下,分辨率为1 μm,测量误差小于12 μm,符合设计要求。
常见的位移传感器产品例如武汉驰栅科技的静磁栅尺[13],英国newall公司的MICROSYN系列的球栅尺以及德国SIKO公司的MSK5000系列磁栅尺[14]。性能如表2所示。
表2 国内外位移传感器与钢栅尺性能对比
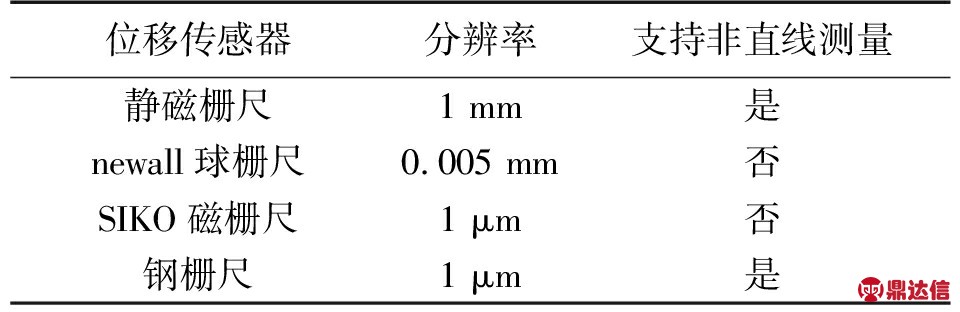
静磁栅尺虽然分辨率只有1 mm,其测量范围为0.01 m~2 000 m,且支持非直线测量。球栅尺的测量精度受球栅中球体直径精度影响,且球体之间相互挤压,也会出现误差。而钢栅尺的尺身由不锈钢以高精密光学蚀刻而成,所以比球栅尺有更高的精度,同时还可以制成弯曲的尺身实现非直线测量。相比于磁栅尺,没有磁性物件,避免消磁和磁滞现象,具有更高的寿命和稳定性。
6 总结
随着工业4.0概念的不断深入,传感器技术的应用也越来越广泛,其中位移传感器作为工业生产中不可或缺的测量和控制部分。而本文完成的磁栅位移传感器,分辨率达到了1 μm,在35 cm的量程内位移误差在10 μm左右。系统运行稳定,结构简单易维护,且支持非直线测量,成本低。完全符合现在工业化的需求。