摘要:目的 研究工艺参数对高温合金Ω截面密封环旋压成形过程的影响规律,解决该类构件旋压成形难题。方法 基于ABAQUS/Explicit平台建立了高温合金Ω截面密封环普旋三维有限元模型,通过该模型研究了旋压成形过程中的主要工艺参数对其等效应力、等效塑性应变、壁厚变化的影响规律,进而揭示了各参数对环件成形质量的影响。结果 芯模转速增大,不均匀变形程度增大,等效应力峰值先增大后减小,壁厚减薄基本不变;增大旋轮进给率与旋轮圆角半径,均有利于降低不均匀变形程度和等效应力峰值,改善壁厚减薄。结论 当芯模转速为10~15 rad/s,旋轮进给率为0.8~1.0 mm/r,旋轮圆角半径为1.5~2.0 mm时,可以获得成形质量较高的Ω截面密封环。
关键词:旋压;密封环;有限元;工艺参数
高温合金Ω截面密封环具有回弹性好、可压缩范围大、可靠性高等优点,作为发动机关键构件,能起到密封高温高压介质、保护系统的作用[1—3]。高温合金密封环一般采用薄壁带材经冷加工成形,旋压被认为是成形密封环的一种精确高效成形方式[4—5],然而由于Ω截面密封环具有截面形状复杂、壁薄(0.25 mm)的“结构特性”,以及高温合金伸长率低、强度高的“材料特性”,使其成形过程易产生缺陷,从而影响成形精度和成形性能[5—8]。旋压成形过程中,工艺参数是影响成形质量的重要因素,合理的参数匹配是保证材料稳定塑性流动变形的关键条件,进而才能从根本上避免缺陷的产生,获得高质量的目标成形件[9—15],因此,研究并分析工艺参数对Ω截面密封环旋压成形质量的影响规律,对解决该类构件旋压成形难题具有重要意义。
文中针对Ω截面密封环旋压工艺参数展开研究,提出一种Ω截面密封环多步旋压新工艺,先进行Ω形结构上半边的“收口段”外旋和“翻边段”内旋成形,再进行下半边的“收口段”和“翻边段”成形,然后基于Abaqus/Explicit平台建立密封环旋压成形的三维有限元模型,分析Ω截面密封环多道次普旋成形过程中的工艺参数对等效塑性应变、等效应力峰值以及壁厚减薄的影响规律,为优化密封环旋压成形工艺,提高密封环成形质量提供可靠依据。
1 研究方法
1.1 有限元建模
采用的坯料为薄壁环形带材,几何尺寸为56 mm(Φ)×18 mm(H)×0.25 mm(t),材料为高温合金GH4169,其抗拉强度σb=900 MPa,屈服强度σs=450 MPa,弹性模量E=199.9 GPa,泊松比ν=0.3,强度系数K=1124.5,硬化指数n=0.253。在对材料变形抗力数据拟合中,采取的模型为σ=Kεn,拟合函数方程为:
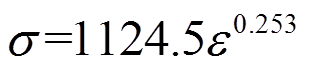
本研究环件单面内表面母线由4段曲线组成,1和3段为圆弧,2和4段为直线,这4段曲线顺次连接形成该薄壁环件内表面母线。Ω形密封环最终截面形状可分为1和2段组成的“收口段”以及3和4段组成的“翻边段”,如图1所示。
基于Abaqus软件,通过动态显式算法对其旋压过程进行有限元建模。其中,环坯选择S4R壳单元,并采用局部网格划分技术对其主要变形区进行网格细分。芯模直径为55.6 mm,采用解析刚体。旋轮采用离散刚体,单元类型为R3D4。接触约束算法采用罚函数法,接触界面采用“有限滑动模式”,旋轮与坯料间摩擦因数取0.1,芯模与坯料间摩擦因数取0.3。建立的装配模型如图2a所示。由于密封环上下对称,两部分成形过程完全一样,所以只对密封环上半部分成形过程进行研究,特征截面节点选取位置如图2b所示。文中研究的几个主要工艺参数有芯模转速、旋轮进给率以及旋轮圆角半径。旋轮圆角半径取0.5, 1, 1.5, 2 mm,进给速率取0.1, 0.4, 0.7, 0.9 mm/r,芯模转速取5, 10, 15, 20 rad/s。
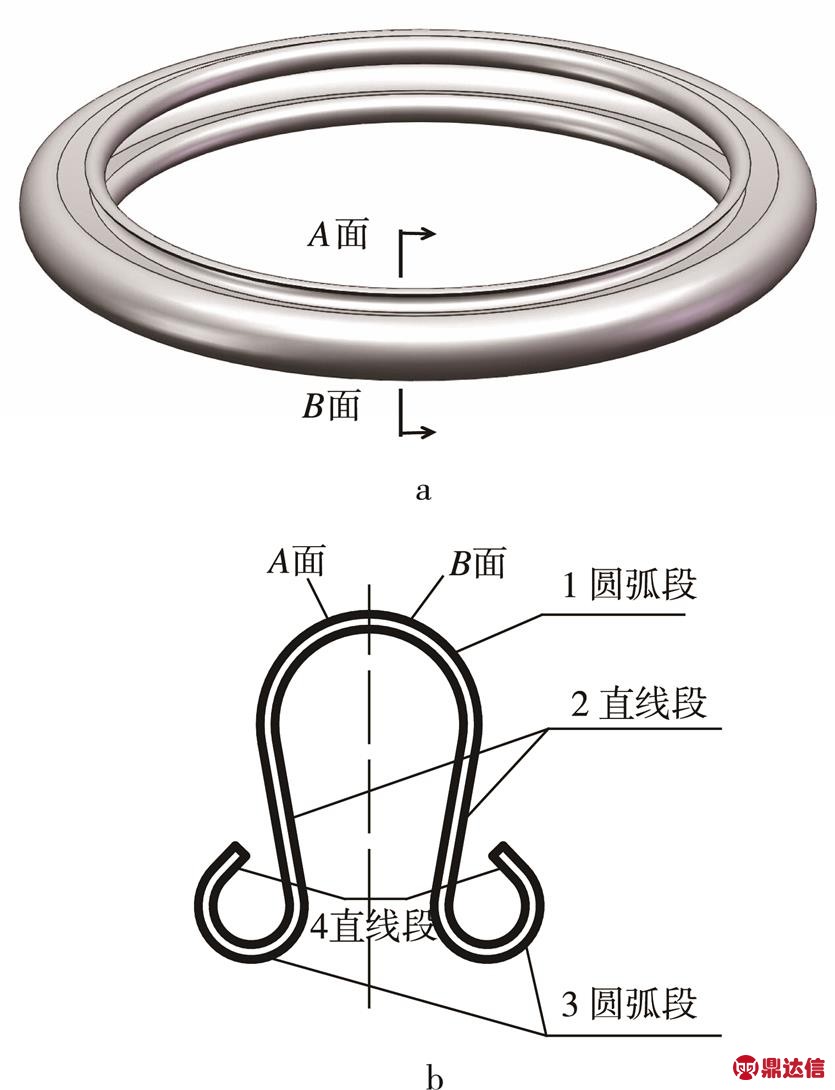
图1 Ω截面密封环结构
Fig.1 Structure of Ω-section sealing ring
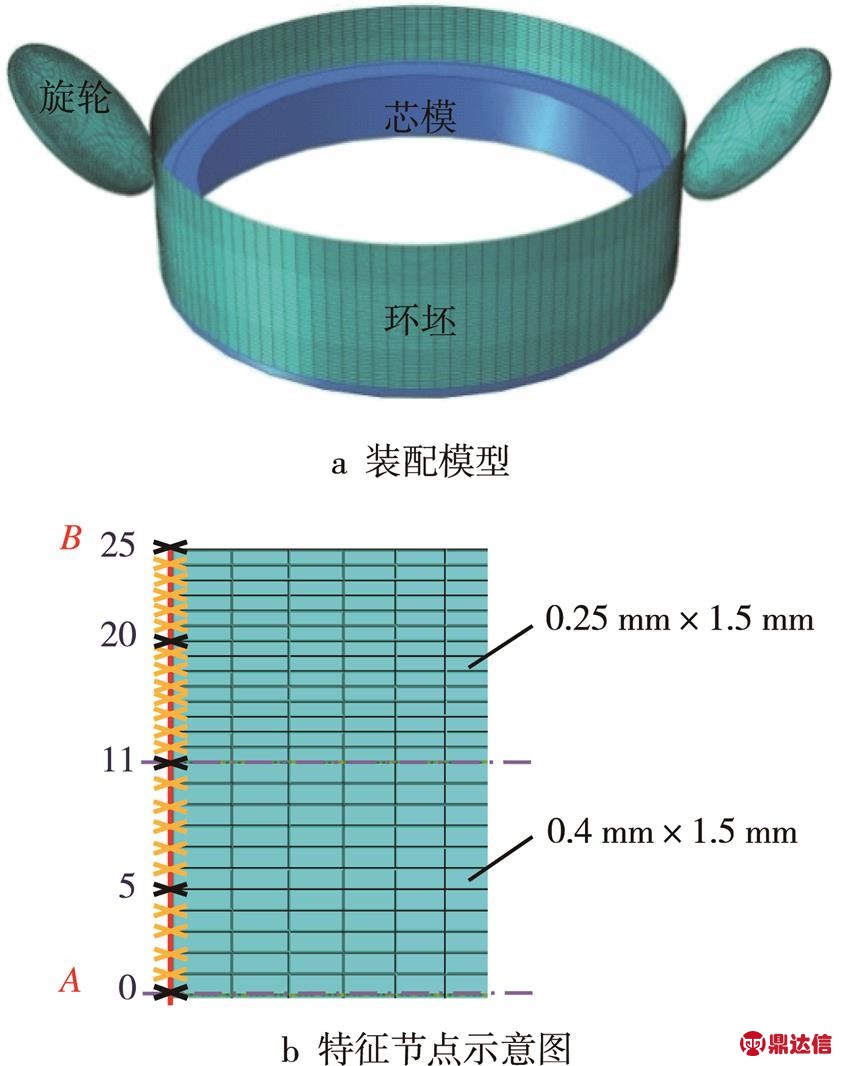
图2 Ω截面密封环旋压成形有限元模型
Fig.2 Finite element model for the spinning processes of Ω-section sealing ring
1.2 模型可靠性验证
在模型中分别设置质量放大因子为1 000, 5 000, 10 000等3种数值,不同质量放大因子下动内能之比时程曲线见图3,可以看出,在不同的质量缩放因子下,每一道次初始时模型的动内能比较大,随后呈快速下降趋势。在质量放大因子为1000和5000时,可以满足在大多数时间下比值是小于15%的,因此可以认为,此时模型计算结果是可靠的。不同质量放大因子下计算时间见图4,从图4观察到,随质量放大因子的减小,模拟求解时间增大,为了在满足计算精度的前提下提高效率,文中选取质量放大因子为5000进行后续的模拟计算。
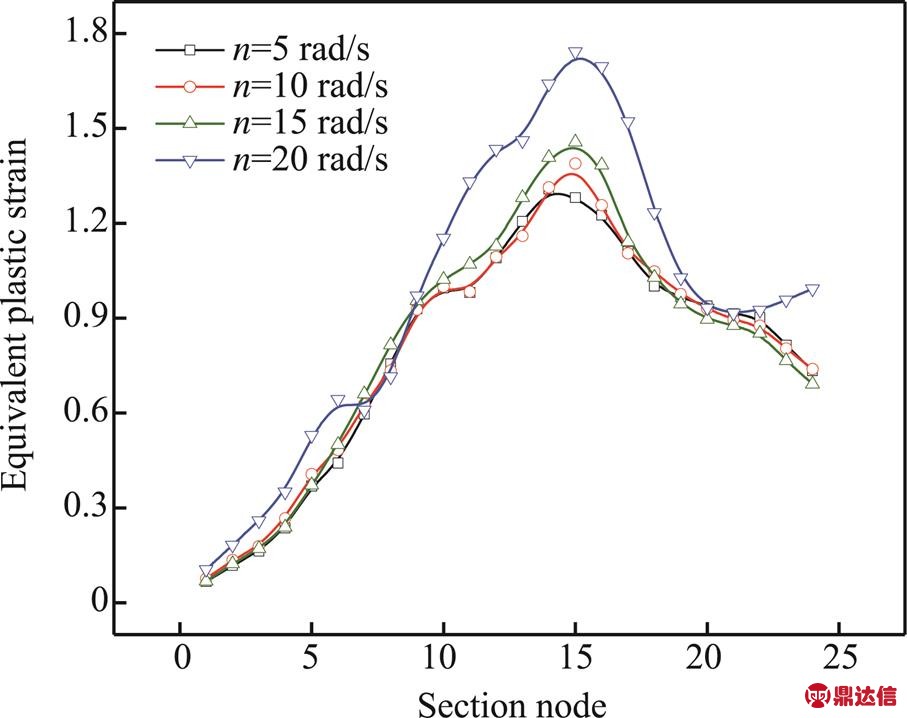
图3 不同质量放大因子下动内能之比时程曲线
Fig.3 Ratio of kinetic energy and internal energy with time for different mass scaling factors
2 结果与讨论
2.1 应变分析
对Ω截面密封环旋压成形过程中的应变分布进行分析,采用芯模转速5 rad/s、旋轮进给率0.4 mm/r、旋轮圆角半径1 mm的工艺参数进行Ω截面密封环旋压成形有限元仿真。各道次等效应变分布情况如图5所示,可以看出,密封环中间“直线段”为大应变区,该区域的宽度随第一阶段外旋过程的进行逐渐变窄,且逐渐向“直线段”的后部移动。这是因为在密封环的旋压成形过程中,环件下方与模具存在约束作用,同时由于结构因素,端部“圆弧段”也会对中间“直线段”材料有约束,因此造成直线段的变形量较大。由于旋轮轨迹采用逐道次贴模,随变形的继续,先成形部分已贴模,旋轮作用位置向端部“圆弧段”移动,因此,应变极大值分布带逐渐变窄且越来越靠近“圆弧段”。内旋翻边阶段环件的变形比较小,因此等效塑性应变值变化不是很明显。此外,可以看出,沿环件周向应变分布比较均匀。
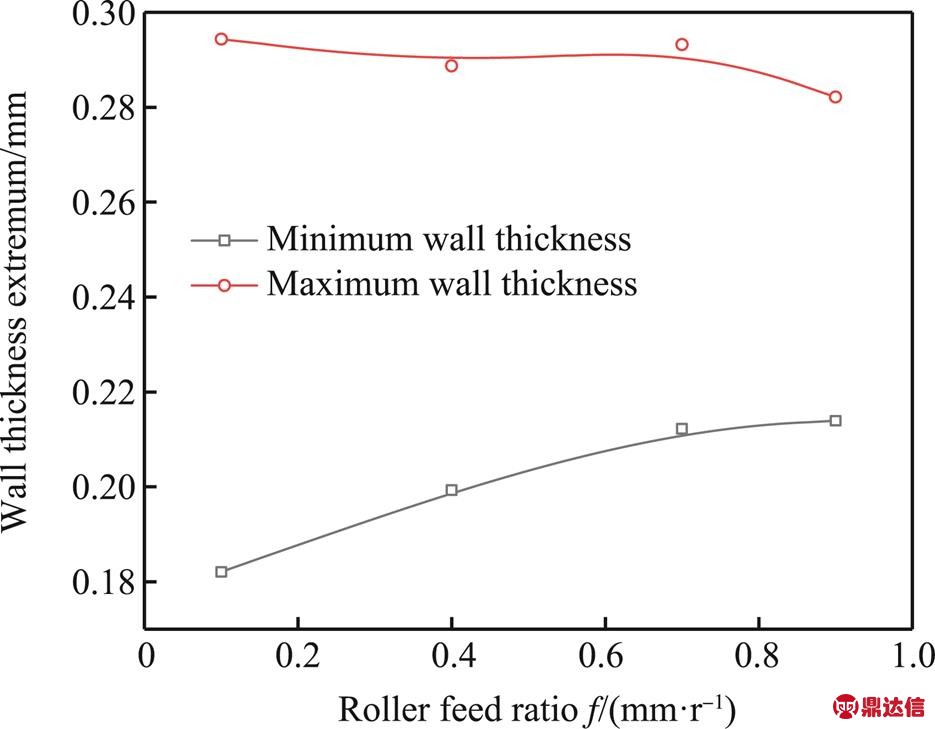
图4 不同质量放大因子下的计算时间
Fig.4 Solution times with different mass scaling factors
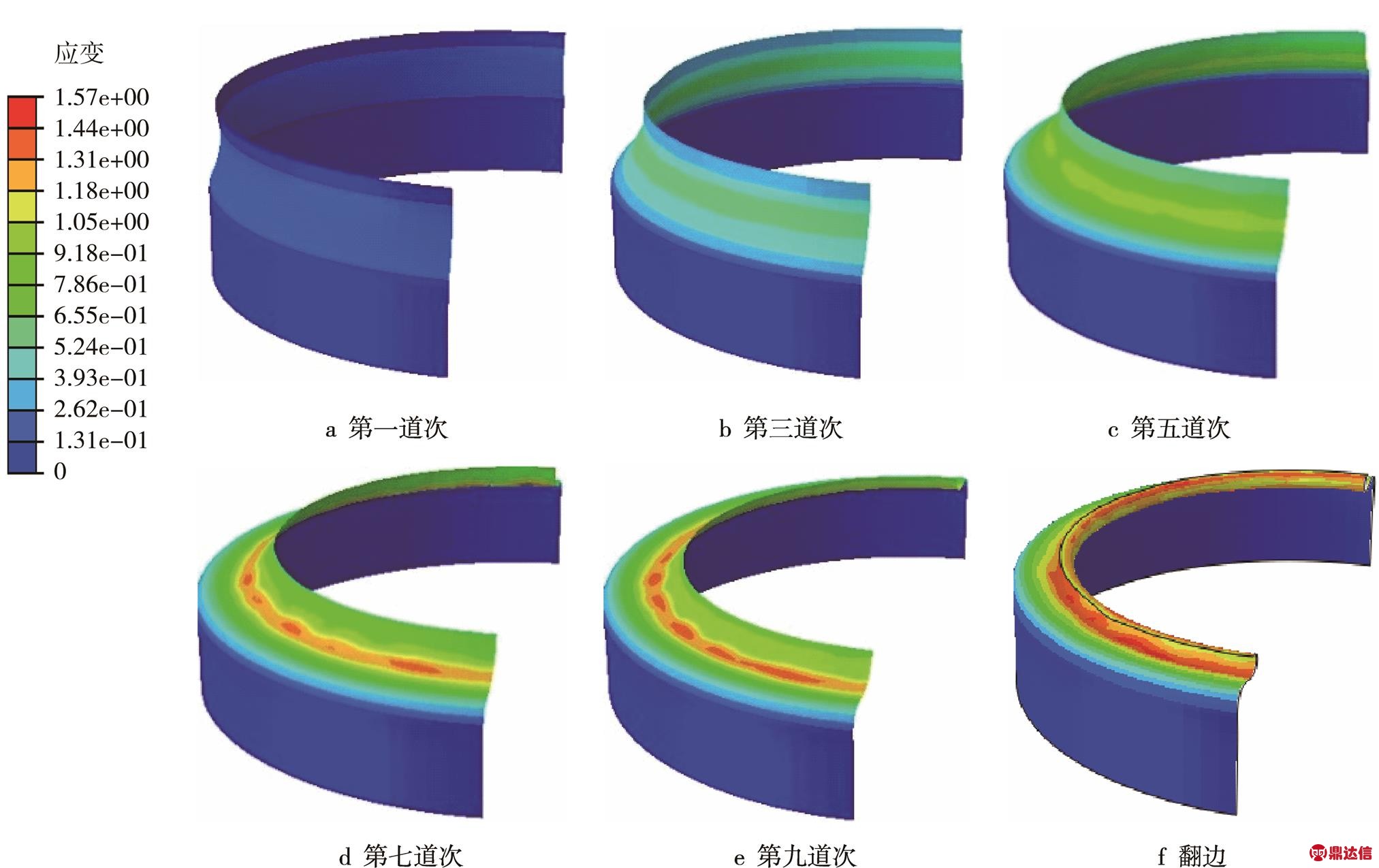
图5 密封环各道次等效应变分布
Fig.5 Equivalent strain distribution at each pass of the sealing ring
2.2 芯模转速对成形结果的影响
图6为不同芯模转速下密封环特征截面节点处的等效应变分布趋势。从图6可以看出,同一芯模转速下,等效应变沿特征截面节点先增大后减小,在中间节点处达到最大值,这是因为中间节点处环件变形量较大,且环件变形区域中部受到两边材料的约束,材料减薄相对较大,导致厚向压应变增大;同时两边材料的约束作用使其两边受拉,导致其轴向拉应变很大,从而造成等效塑性应变增大。随着芯模转速的增大,各节点处等效塑性应变基本呈增大趋势。芯模转速为5 rad/s和10 rad/s时,等效塑性应变差值微小,这说明芯模转速在此范围内对等效塑性应变的影响不大。
图7为芯模转速对环件等效应力最大值的影响。可以看出,随芯模转速增大,等效应力先增大后急剧减小。这是因为随芯模转速增大,坯料变形速度增大,导致应力也增大;但芯模转速增大到20 rad/s时,环件端部微小摆动引起应力释放的程度远远大于变形速度导致的应力增大,所以在该转速下,应力有所降低。
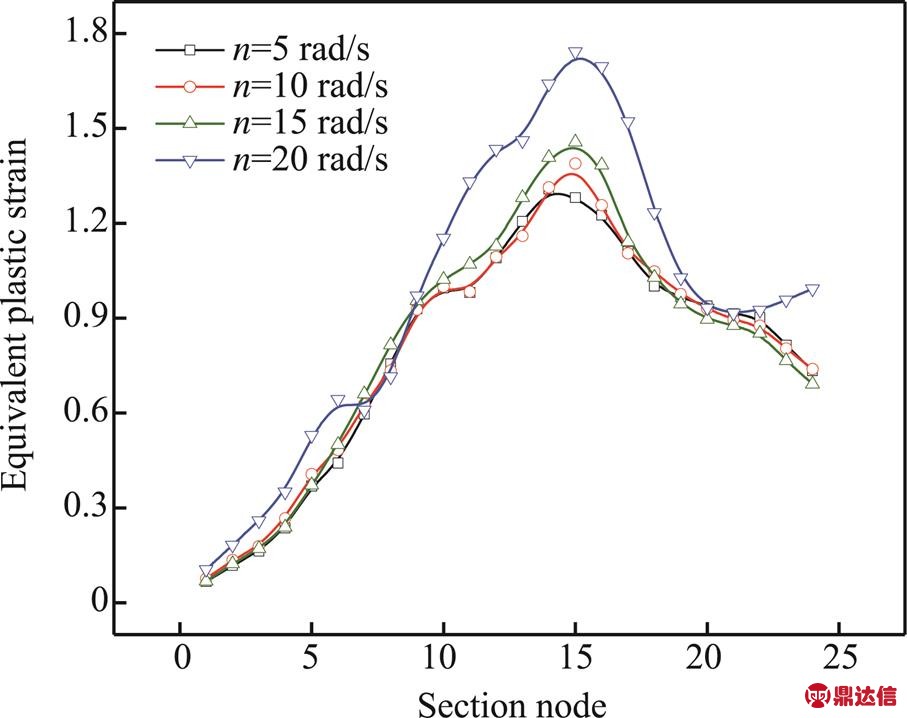
图6 芯模转速对特征截面节点等效应变的影响
Fig.6 Influence of mandrel speed on equivalent strain of section node
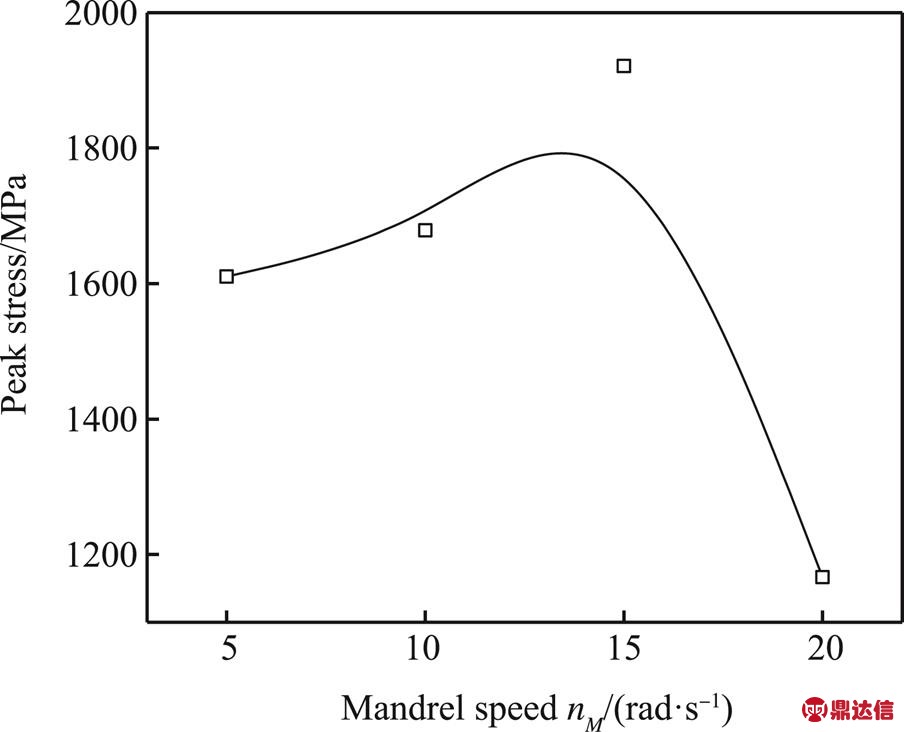
图7 芯模转速对应力最大值的影响
Fig.7 Influence of mandrel speed on maximum stress
图8为芯模转速对密封环壁厚极值的影响,可以看出,随芯模转速的增大,环件壁厚极大值先增大后减小,壁厚极小值缓慢增大。壁厚极值随芯模转速的增大而增大,是由于旋轮辗过相同宽度材料的时间变短,材料在厚度上变形不充分。
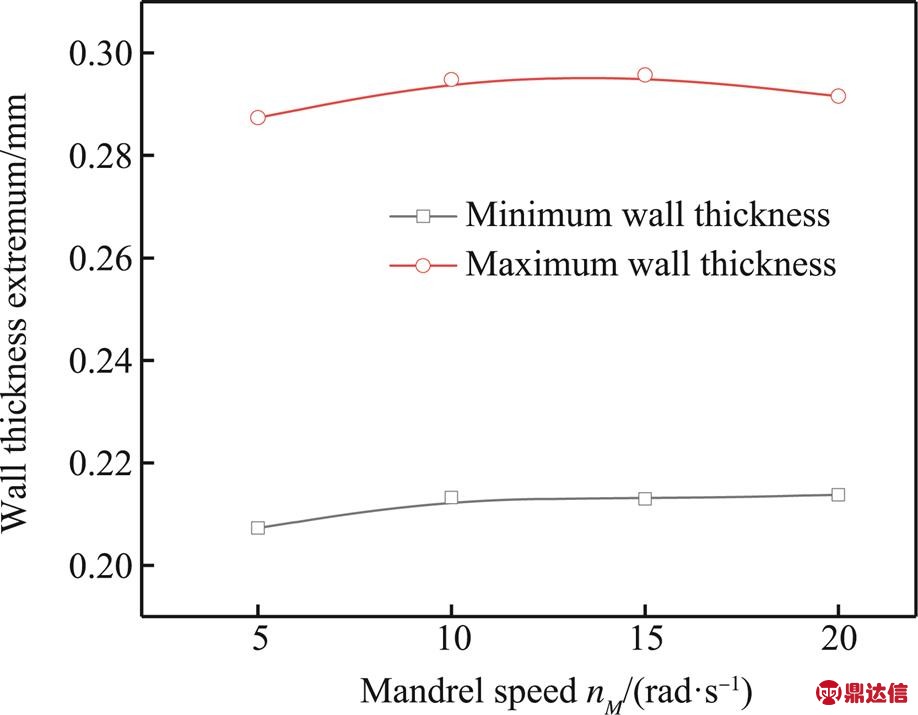
图8 芯模转速对壁厚极值的影响
Fig.8 Influence of mandrel speed on wall thickness extremum
2.3 旋轮进给率对成形结果的影响
图9为不同旋轮进给率下密封环特征截面节点处的等效应变分布趋势。可以看出,同一进给率下,沿环件特征截面节点等效塑性应变先增大后减小,在中间节点处达到最大,也就是进给率增大对0—7号节点的等效应变影响较小,对7—25号节点的等效应变影响显著。这是因为,在前面节点区域,环件刚开始变形,材料变形量较小,而中间区域材料变形量很大,进给率增大造成各节点等效塑性应变改变程度一样时,变形量大的区域等效塑性应变变化绝对值大一些。此外,随旋轮进给率增大,环件不均匀变形程度呈减小趋势。
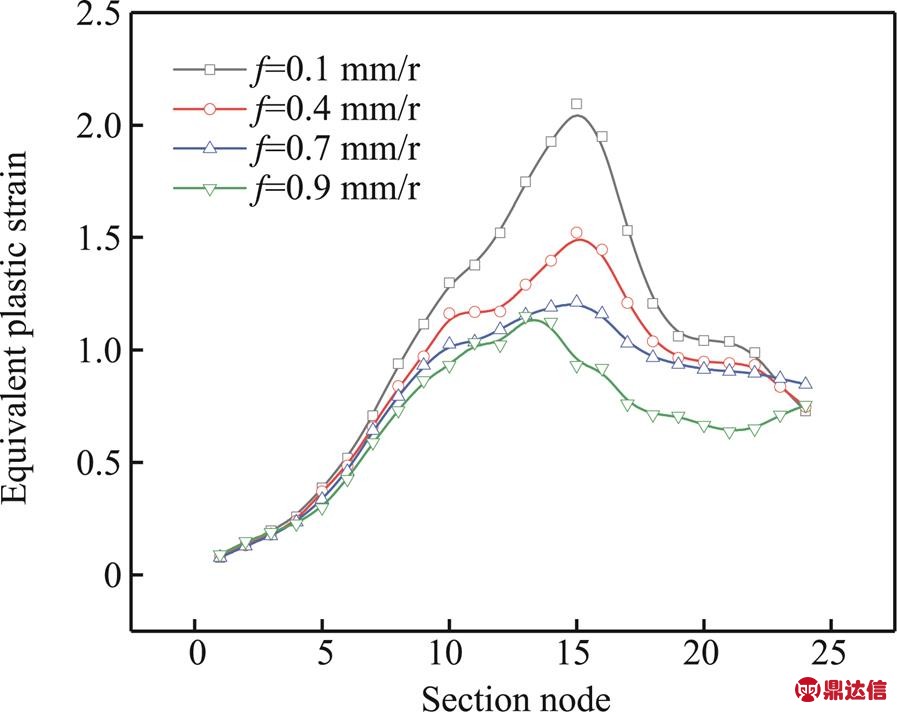
图9 旋轮进给率对特征截面节点等效应变的影响
Fig.9 Influence of roller feed ratio on equivalent strain of section node
图10为进给率对等效应力峰值的影响,可以看出,随旋轮进给率增大,等效应力峰值呈减小趋势。这是因为在无芯模旋压变形时,材料流动比较自由,材料有向旋轮运动方向流动的趋势,且旋轮进给率增大,旋轮作用相对时间缩短,使得材料变形更加容易,进而造成了等效应力峰值和不均匀变形程度同时减小。
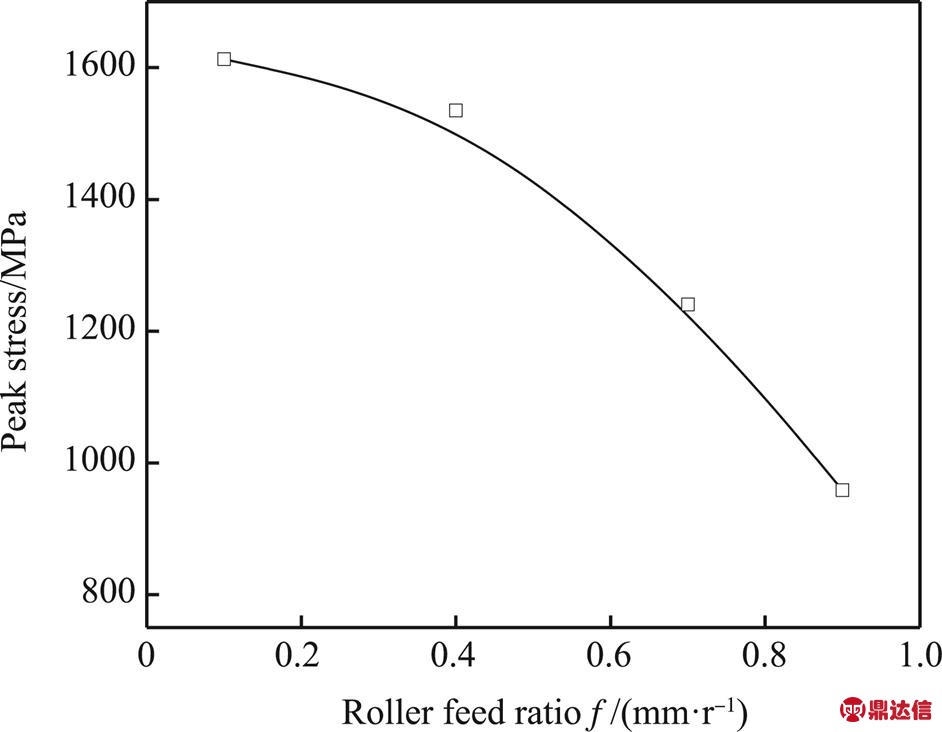
图10 进给率对应力最大值的影响
Fig.10 Influence of roller feed ratio on maximum stress
图11为旋轮进给率对环件壁厚极值的影响。可以发现随旋轮进给率增大,壁厚极大值减小,壁厚极小值增大,这有利于控制壁厚的减薄,也使得环件的壁厚更加均匀。根据体积不变原理,一些区域材料减薄减小,流入端部位置的材料也减小,因此其壁厚增厚程度也减小。在本研究中,壁厚极小值一般分布在中间区域,极大值为环件端部区域,材料流向是从中部流向端部的,这就不难理解随进给率增大,会发生壁厚极小值增大而壁厚极大值减小的现象。
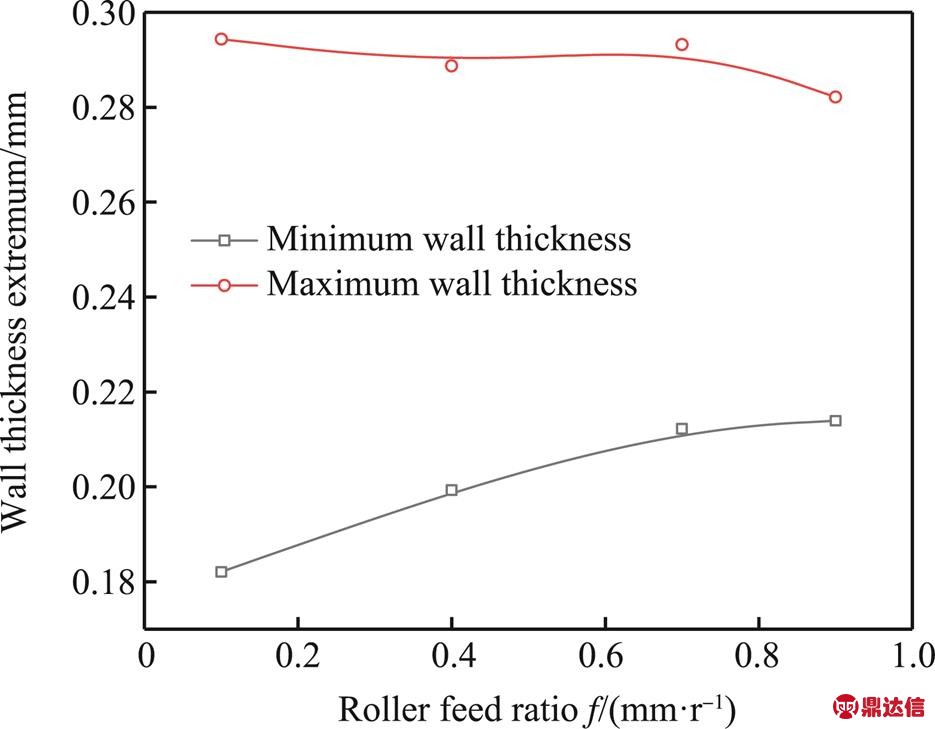
图11 进给率对壁厚极值的影响
Fig.11 Influence of roller feed ratio on wall thickness extremum
2.4 旋轮圆角半径对结果的影响
图12为不同旋轮圆角半径下环件特征截面节点处的等效应变分布趋势,可以看出,等效应变极大值分布在15—20号节点附近,相同节点处,等效塑性应变值随旋轮圆角半径的增大而减小,这说明不均匀变形程度随旋轮圆角半径的增大而减小。这是因为旋轮圆角半径增大,旋轮与坯料接触面积增大,单位接触压力有所减小,使得材料的变形更均匀,从而节点应变减小。也就是说,在本研究取值范围内,大的旋轮圆角半径更有利于变形均匀。图13为旋轮圆角半径对等效应力峰值的影响,可以看出,随旋轮圆角半径增大,峰值应力呈降低趋势,这也验证了上述分析。
从图14可以看出,随旋轮圆角半径增大,壁厚极大值减小,壁厚极小值呈增大趋势。这说明,适当增大旋轮圆角半径有利于控制环件的壁厚减薄。本研究范围内,旋轮圆角半径增大至1.5 mm时,最大壁厚减薄率已经可以控制在13%左右,此时环件壁厚分布也更均匀。
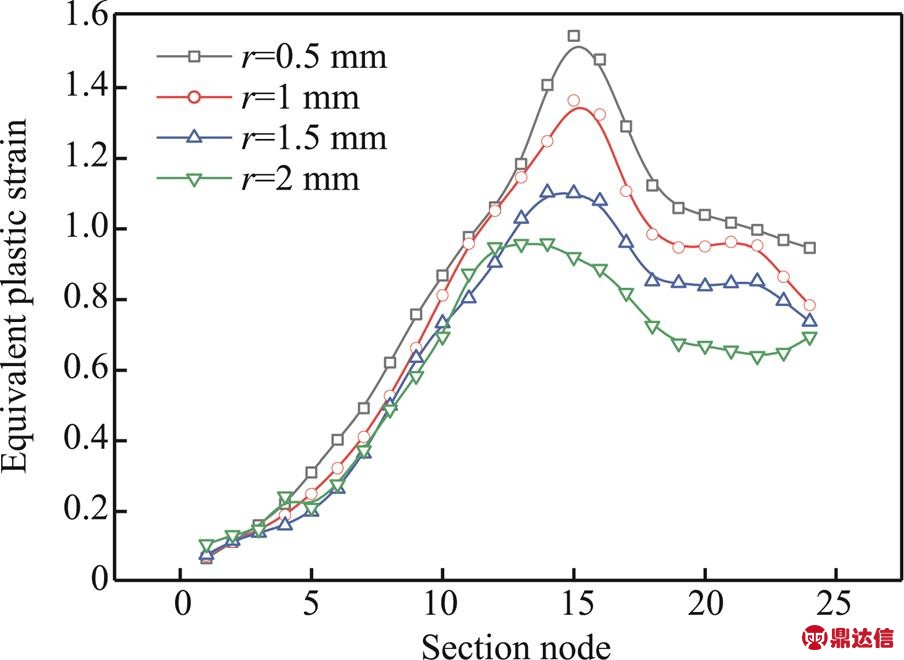
图12 旋轮圆角半径对特征截面节点等效应变的影响
Fig.12 Influence of roller nose radius on equivalent strain of section node
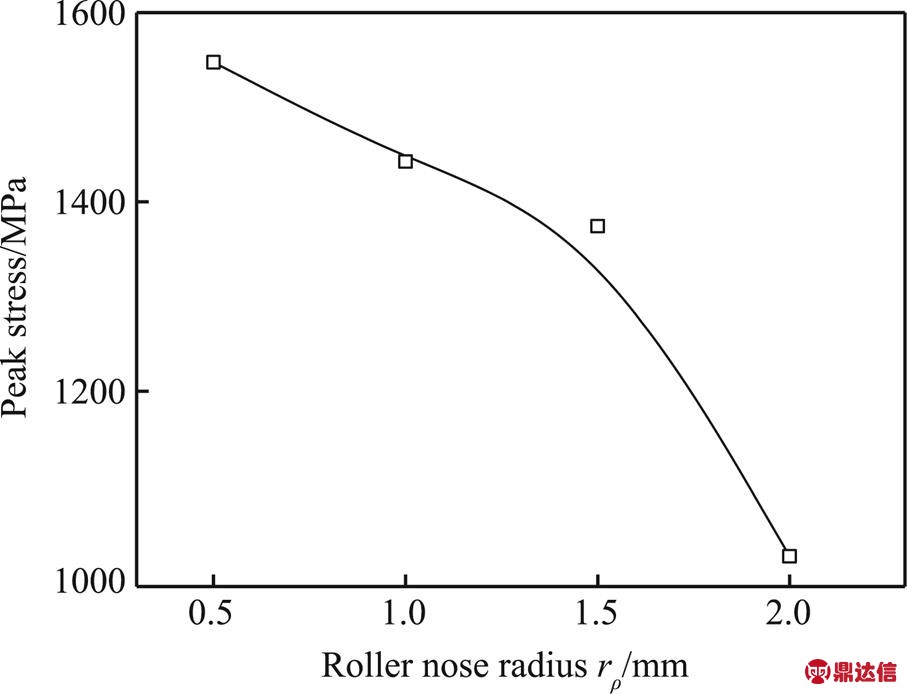
图13 旋轮圆角半径对应力最大值的影响
Fig.13 Influence of roller nose radius on maximum stress
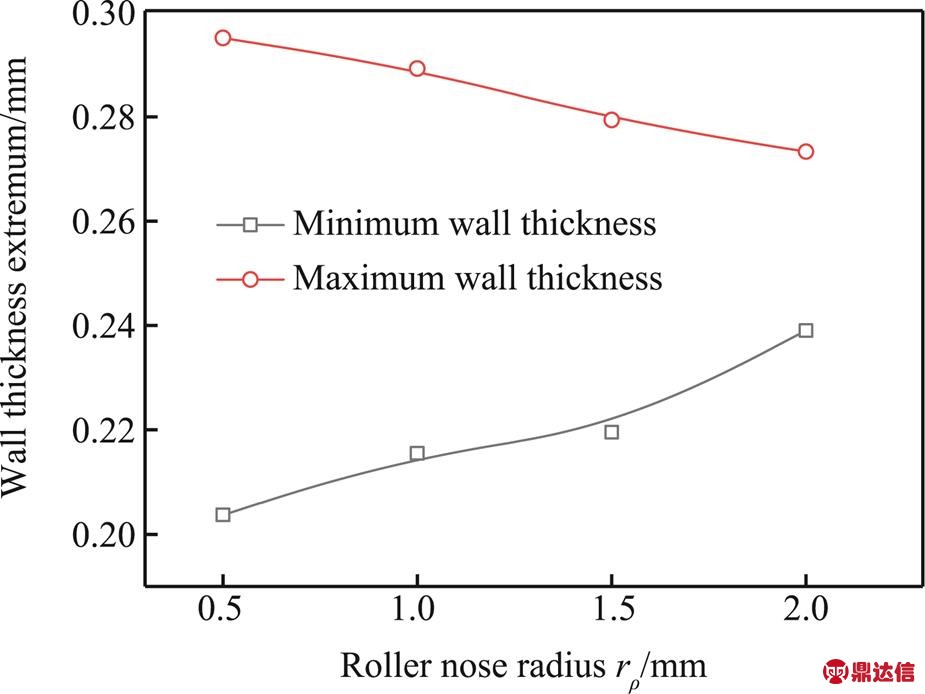
图14 旋轮圆角半径对壁厚极值的影响
Fig.14 Influence of roller nose radius on wall thickness extremum
3 结论
1)芯模转速增大,不均匀变形程度增大,等效应力峰值先增大后减小,壁厚减薄基本不变;增大旋轮进给率与旋轮圆角半径,均有利于降低不均匀变形程度和等效应力峰值,改善壁厚减薄。
2)在本研究所涉及工艺参数范围内,当工艺参数取值区间如下:芯模转速为10~15 rad/s,旋轮进给率为0.8~1.0 mm/r,旋轮圆角半径为1.5~2.0 mm时,可以获得成形质量较高的Ω截面密封环。