摘要:目的 研究滚压成形过程中环件壁厚的变化规律。方法 基于ABAQUS/Explicit平台建立了GH4169薄壁W截面密封环多道次滚压成形三维弹塑性有限元模型,分析了滚压成形过程中环件壁厚沿周向及轴向的变化情况以及工艺参数对环件壁厚变化的影响规律。在此基础上,进行与模拟条件一致的试验研究,并与模拟结果进行了对比分析。结果 滚压成形过程,环件壁厚沿周向分布均匀而沿轴向分布不均匀;随着变形量增大,减薄带宽度增大;进给辊进给速度增大,环件壁厚不均匀性加剧;随着驱动辊转速、进给辊与环件间摩擦因数的增大,环件壁厚减薄呈减小趋势。结论 环件滚压成形过程中,应合理分配各道次变形量,适宜的工艺参数为:驱动辊转速为2 rad/s,进给速度为0.2 mm/s,摩擦因数为0.1。
关键词:滚压成形;高温合金;W截面密封环;壁厚变化;有限元模拟
航空航天发动机高温、高压油气介质的高可靠密封,是提升飞行器机动性能的重要因素。由于发动机高温高压的特殊条件,橡胶圈等普通密封环已难以满足密封要求,因此,应用金属密封取代传统的橡胶密封已成为提升航空航天发动机性能的重要突破口。高温合金W截面密封环由于具有良好的震动追随性、高的压缩回弹率以及自紧密封功能等优点,已得到国内外航空航天、武器和核工业等领域的广泛认可[1]。
滚压成形技术[2]是一种制造薄壁复杂截面构件的有效方法。高温合金密封环具有壁厚极小(0.1~0.3 mm)、直径大(50~1000 mm)且截面形状复杂(如W型)的结构特性,以及材料强度高(σs≥450 MPa)、伸长率低(σ5<15%)、加工硬化显著的材料特性[3—4];同时其成形过程涉及材料、几何、边界等多因素的非线性耦合[5],难以精确成形,尤其是壁厚变化难以精确控制,严重制约了其使用性能,因此,研究高温合金薄壁W截面密封环滚压成形过程中的壁厚变化规律,对于实现其高性能精确塑性成形具有重要意义。
目前,国内外学者关于复杂截面薄壁件的成形已进行了大量研究。CORONA[6]针对薄壁复杂截面型材辊弯成形中出现的截面畸变问题,建立了理论预测模型,并验证了其可靠性。Awiszus[7]通过控制旋轮的加载轨迹,实现了非圆平面构件的多道次旋压成形。李明等[8]解决了阶梯环形钣金零件滚压成形中的回弹问题。梁鑫光等[9]采用有限元模拟结合试验,研究了进给速度、滚刀的进给方式等不同的成形参数对航天阀门密封件环状结构滚压成形质量的影响规律。但目前对于高温合金复杂截面密封结构成形的研究较少,相关文献报道主要是赵刚要[10—12]、朱宇[13]等学者的研究,至于高温合金薄壁W截面密封环件滚压成形壁厚变化的研究更是鲜有报道,因此文中以有限元数值分析为主,辅以试验验证,系统研究了高温合金薄壁W截面密封环滚压成形过程中,各道次壁厚变化规律以及工艺参数对环件的壁厚变化影响,从而为异型截面密封结构的实际生产及相关工艺参数的选取和优化提供参考。
1 有限元模型
1.1 有限元建模
本研究中目标环件结构如图1所示,坯料几何尺寸为Φ232 mm×16 mm(H)×0.3 mm(t),材料为高温合金GH4169,抗拉强度σb为900 MPa,屈服强度σs为450 MPa,弹性模量E为199.9 GPa,泊松比ν为0.3,其应力-应变曲线见图2。
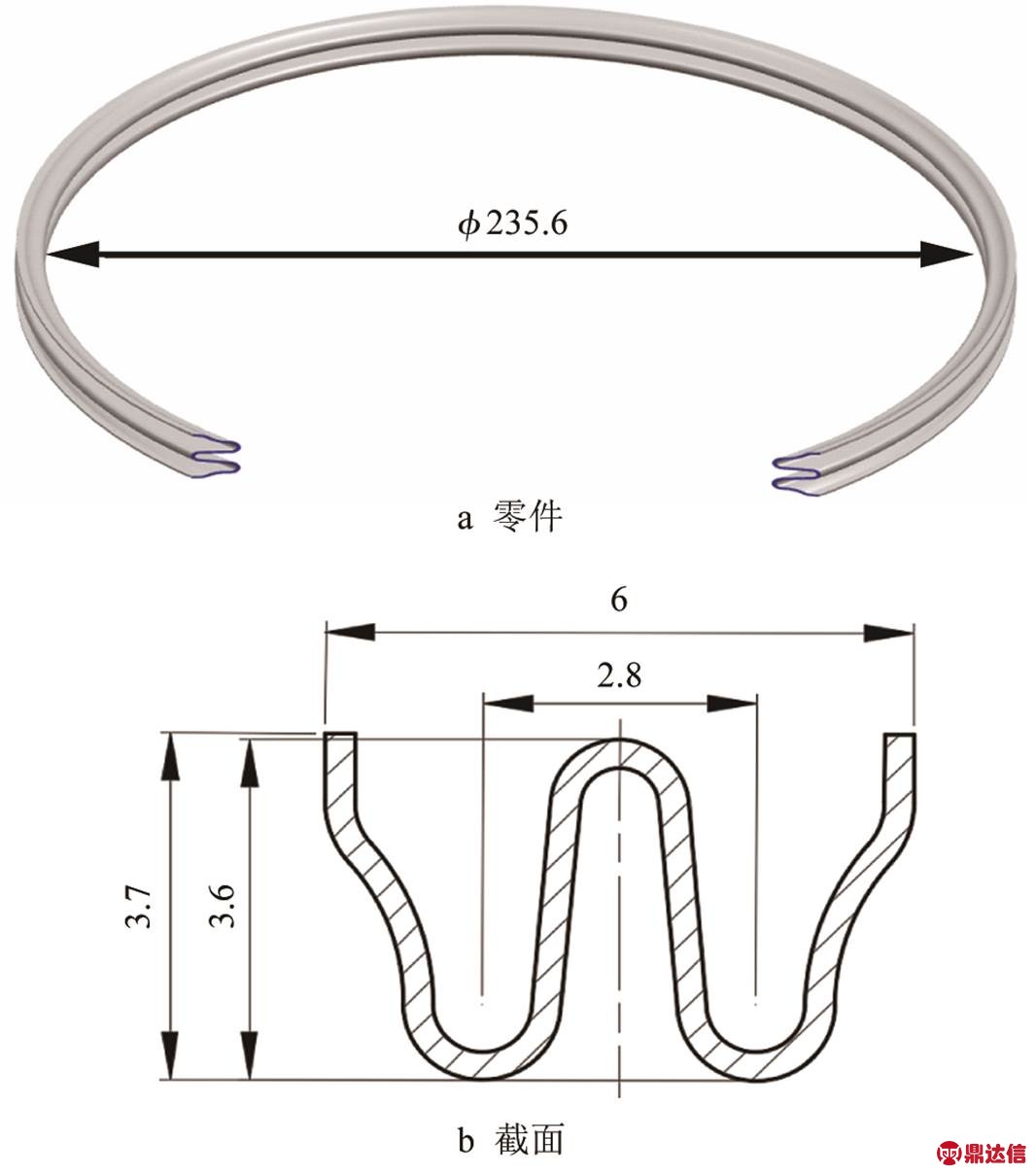
图1 圆形W截面密封结构
Fig.1 Schematic diagram of round W-section seal ring
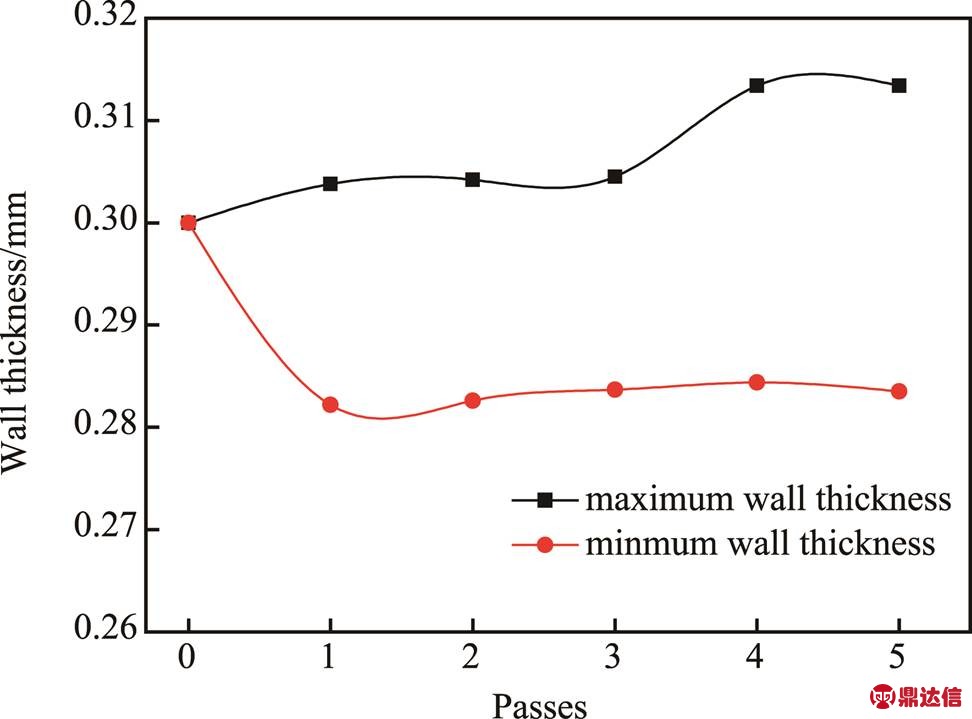
图2 GH4169真实应力-应变曲线
Fig.2 True stress-strain curve of GH4169
基于ABAQUS/Explicit平台建立的有限元模型如图3所示。模型由驱动辊、进给辊、两个导向辊和环坯组成。其中,环坯设置为变形体,并对其赋予材料属性,其余部件均设置为解析刚体,同时采用壳体单元进行简化处理,以提高模拟计算效率,且与坯料接触部分均设置摩擦,摩擦因数均设为0.2。成形过程中,进给辊设置“位移/转角”边界条件,驱动辊设置“速度/角速度”边界条件,环件依靠与进给辊和驱动辊间的摩擦力转动,导向辊设置“位移/转角”边界条件,起稳定支撑环件和矫正圆度的作用。变形体网格采用四节点曲面薄壳减缩积分单元[14](S4R),并对波峰、波谷等主要变形区进行局部网格细化,单元总数为5856个。
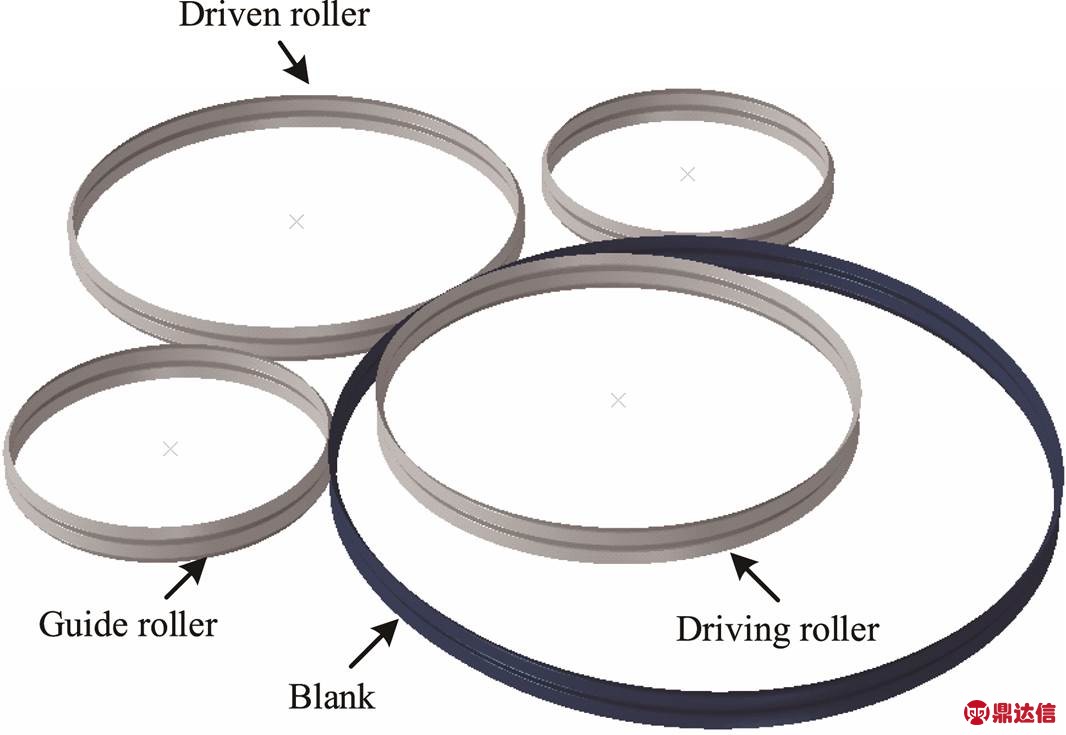
图3 多道次滚压成形有限元装配模型
Fig.3 Finite element assembly model of multi-pass rolling forming
1.2 模拟条件
在研究W截面密封环滚压成形过程壁厚变化时,设计的环件成形轨迹共有5个道次。由于目标件在波峰、波谷处变形量较大,为了更全面揭示其在滚压成形过程中的壁厚变化规律,选取沿环件宽度方向的特征截面,如图4所示,并根据网格划分为其编号。仿真模拟过程中各工艺参数见表1。
1.3 模型可靠性验证
为了验证模型可靠性,进行验证性试验研究,并保持试验与模拟条件一致。多道次滚压试验和模拟结果的轮廓如图5所示。可以看出,滚压成形结束后试验与模拟的圆形密封结构外轮廓与截面形状基本一致,两者结果吻合良好。
图6为试验测定的沿宽度方向横截面各节点壁厚值与模拟结果对比。可以看出,模拟与试验结果最大误差位于波谷圆弧位置(−12号、12号节点),最大误差为11.27%,误差较大,这是因为在实际中,坯料的厚度并不是完全均匀的,此外,由于圆形密封结构的截面形状复杂、深窄槽明显、横截面尺寸很小,使得特征截面各节点壁厚的测量存在一定的误差,尤其是环件波峰段与外密封段之间的波谷位置。但是,模拟与试验结果的壁厚变化趋势相同,且平均误差为3.1%,因此,可以认为,文中建立的有限元模型是可靠的。
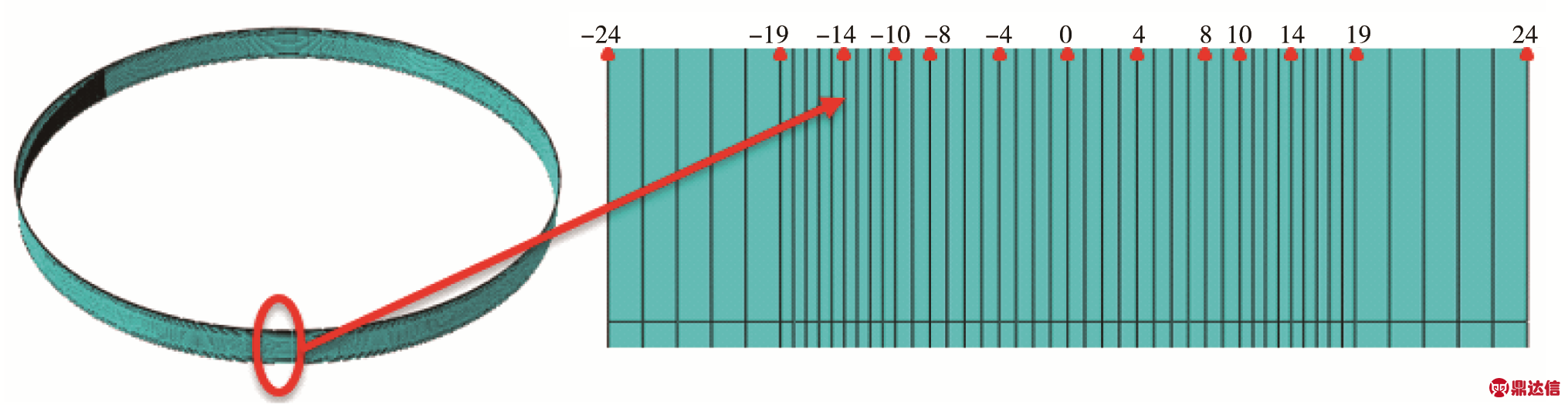
图4 特征截面节点示意图
Fig.4 Cross diagram of section node
表1 多道次滚压成形主要工艺参数取值
Tab.1 Main forming parameters of multi-pass rolling forming

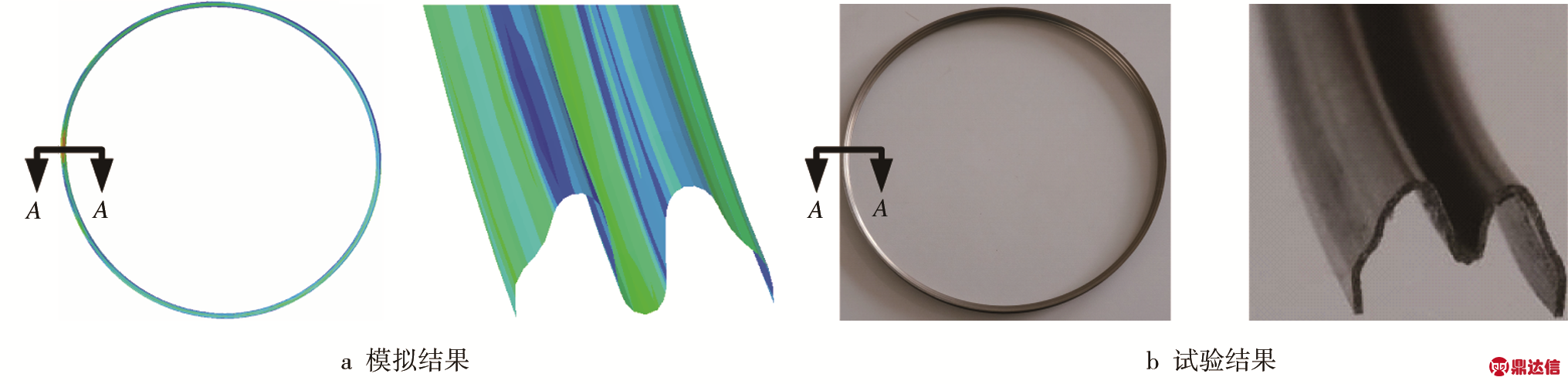
图5 模拟与试验结果对比
Fig.5 Comparison of simulation and test results
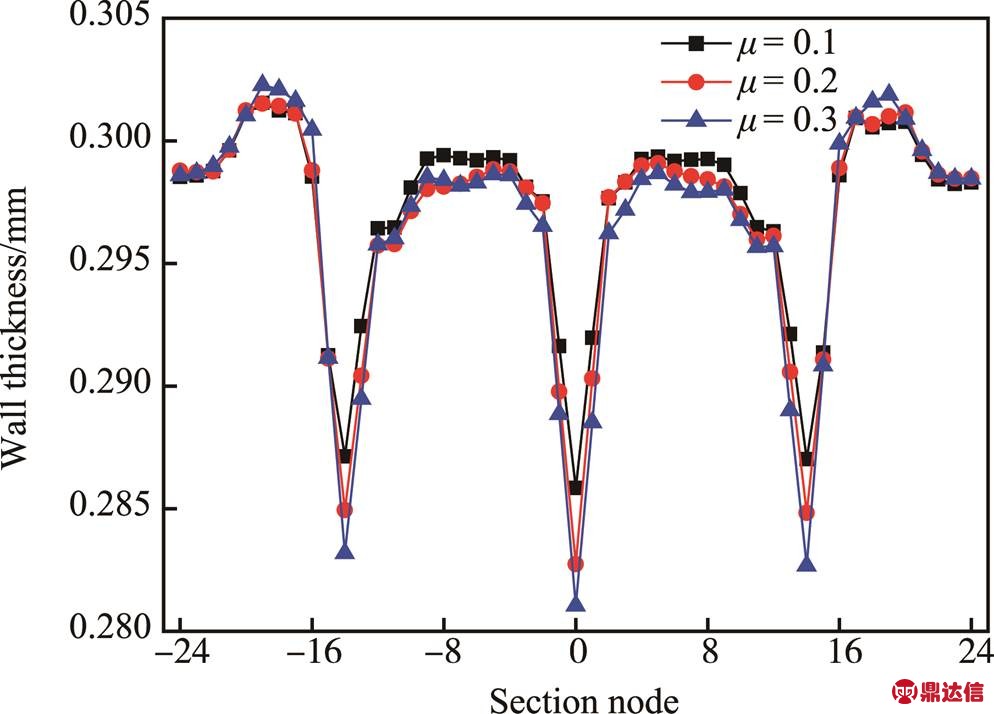
图6 模拟与试验结果壁厚对比
Fig.6 Comparison of wall thickness for simulation and experiment
2 结果与讨论
2.1 滚压过程各道次壁厚变化分析
图7为环件滚压过程各道次壁厚变化分布。由图7可知,环件壁厚沿周向分布比较均匀,而沿宽度方向分布不均匀;随着各道次滚压成形的依次进行,壁厚减薄情况逐渐加重,第一道次波峰、波谷邻近区域出现了壁厚减薄的现象,随变形的继续,壁厚减薄带逐渐向环件波峰与波谷间直线段扩展,壁厚减薄带宽度增大,这是因为随着进给辊的进给加载,环件材料会逐道次贴模,在贴模时环件波峰、波谷处的材料变形受到进给辊与驱动辊的共同作用,承受拉应力,且应力较大使材料减薄比较严重,而非主要变形区的直线段由于发生材料体积转移而出现壁厚增厚的现象。
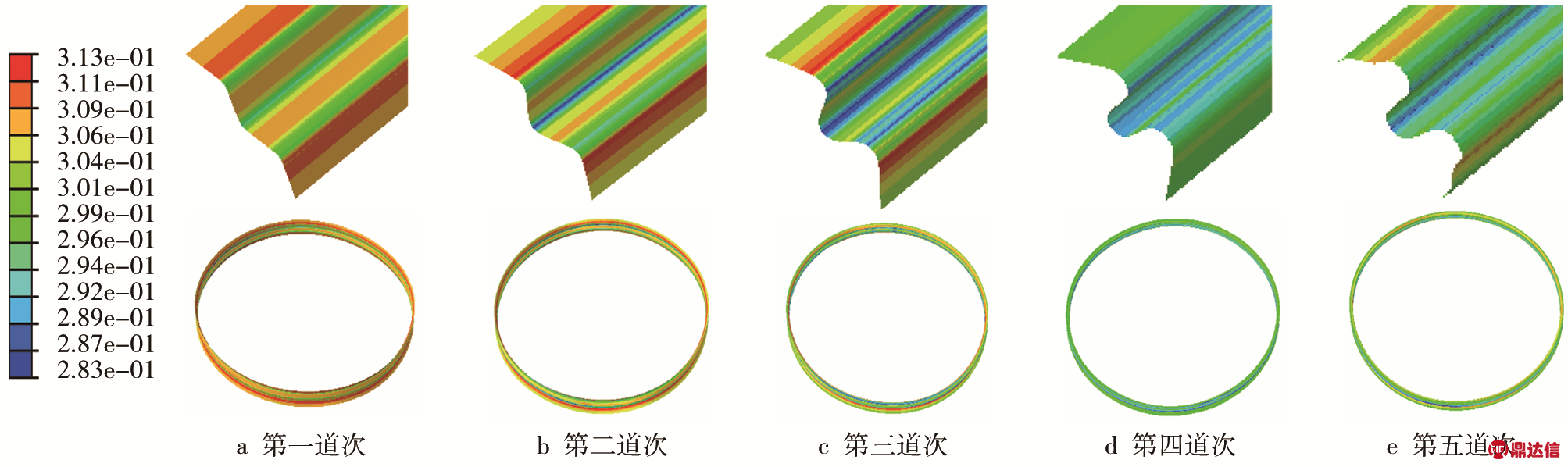
图7 环件滚压过程各道次壁厚变化分布(mm)
Fig.7 Wall thickness distribution at each pass of rolling forming
图8为环件滚压过程各道次壁厚沿宽度方向横截面的变化曲线。可以看出,环件壁厚随着各道次滚压的依次加载成形,沿宽度方向由中心向边缘位置呈先增大,后增小,再增大,又略微呈减小的趋势,呈W形,其中壁厚变薄严重的区域位于节点−2与2之间的环件波峰区及节点10(−10)与14(−14)之间的环件波谷区,这是因为这3个区域为环件的弯曲主变形区,变形量较其他位置大。
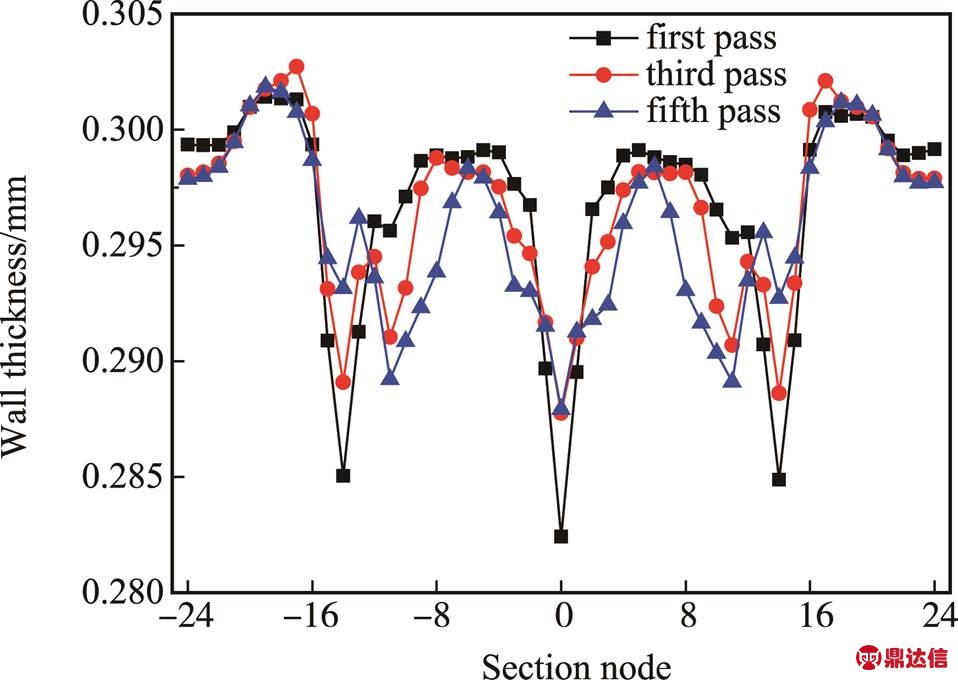
图8 环件滚压过程各道次壁厚沿宽度方向变化曲线
Fig.8 Wall thickness distribution along the width at each pass of rolling forming
图9为滚压过程各道次环件壁厚极值变化曲线。可知,环件壁厚极大值随着各道次滚压成形的依次进行呈逐渐增大趋势,壁厚极小值随着各道次滚压成形的依次进行呈先减小后基本不变的趋势,其中壁厚减薄主要发生在第一道次,减薄量为5.8%,同时伴有壁厚增大现象的发生,这是由第一道次环件的变形分配量最大所导致的。第四道次壁厚极大值增加最为明显,这是因为本道次成形环件波峰、波谷处的深形凹槽,随着滚压成形的进行,环件与模具贴合后,波峰、波谷处材料均向两者之间直线段转移。第五道次成形结束时,壁厚减薄5.9%,远远小于实际要求的20%。
2.2 进给辊进给速度对壁厚变化的影响
取进给辊进给速度为0.05, 0.1, 0.2, 0.3 mm/s[15],研究其对环件壁厚变化的影响,其余模拟计算条件见表1。图10为进给辊进给速度对环件特征截面节点壁厚变化的影响曲线。可知,随进给速度的增大,节点壁厚相应减小,这是因为进给速度增大,进给辊与坯料的作用时间变短,单位时间内的变形量增大,不利于材料的流动,导致其壁厚减薄增大。图11为环件滚压过程壁厚极值随进给速度的变化曲线。可以看出,随着进给速度的增大,环件壁厚极大值呈增大趋势,极小值呈减小趋势,进给速度为0.05, 0.1, 0.2 mm/s时,壁厚极值变化相对不明显,而进给速度增大到0.3 mm/s时,壁厚极值变化剧烈,极大值与极小值差异明显,达到壁厚的29.73%,将严重影响环件成形质量与回弹服役性能,因此,在W截面密封环滚压成形过程中,进给速度的选取不易过大,适宜区间为0.1~0.2 mm/s。
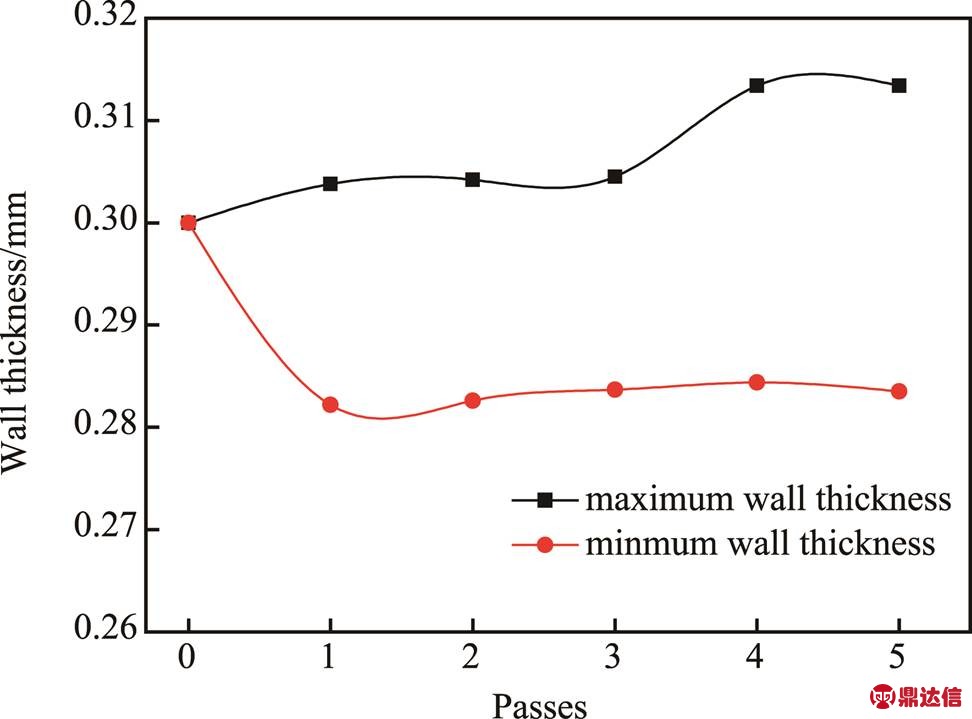
图9 滚压过程各道次环件壁厚极值变化曲线
Fig.9 Wall thickness extreme change at each pass of rolling forming
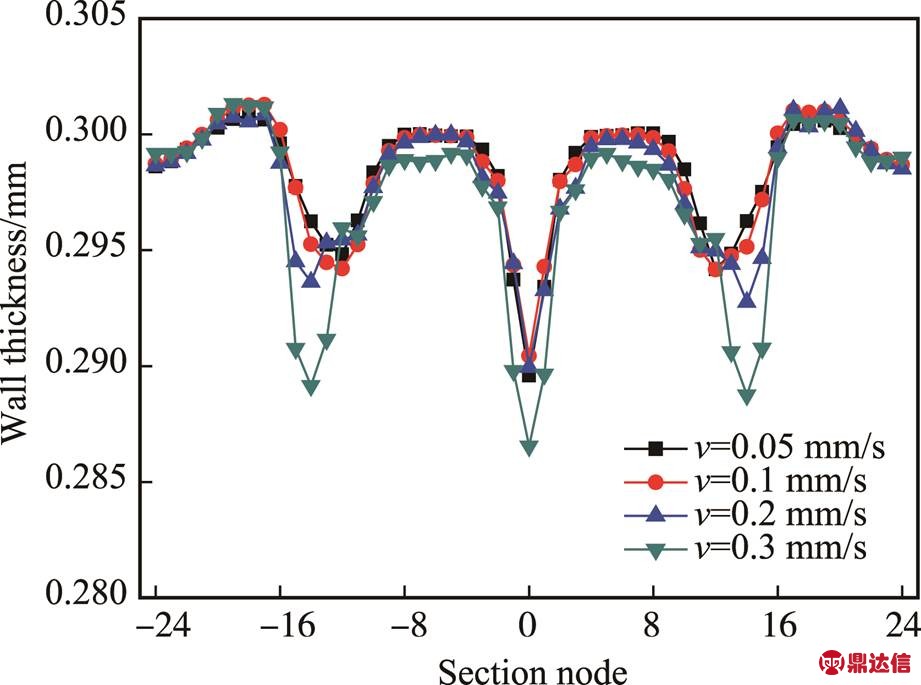
图10 进给速度对环件特征截面节点壁厚变化的影响
Fig.10 Effect of feed rate on the wall thickness variation of ring cross section
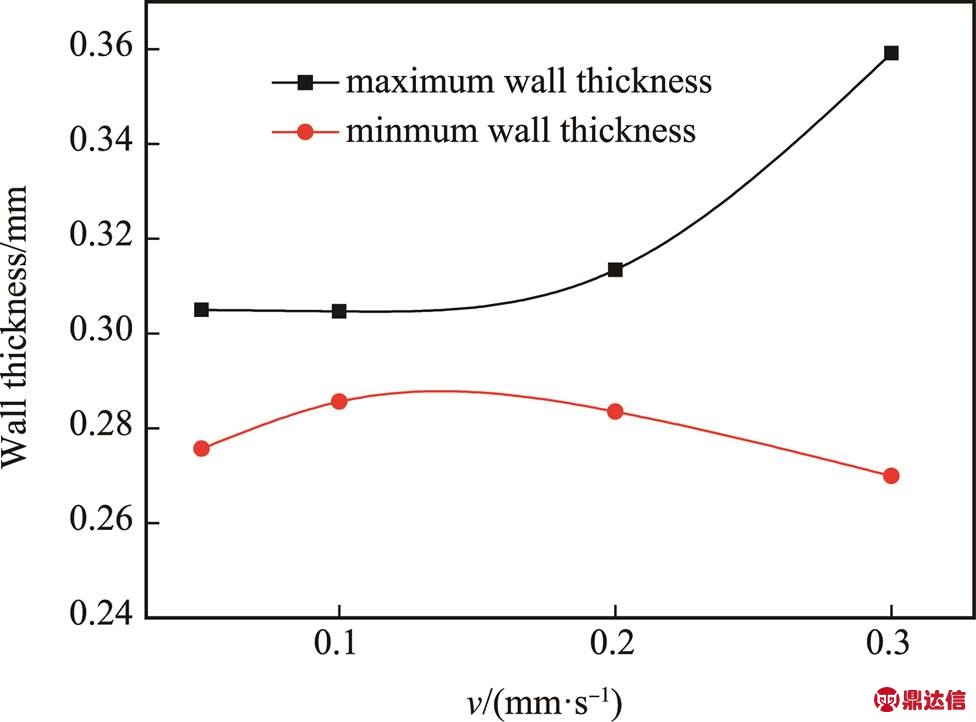
图11 进给速度对环件壁厚的影响规律
Fig.11 Effect of feed rate on the wall thickness of ring
2.3 驱动辊转速对壁厚变化的影响
取驱动辊转速为1, 1.5, 2.0 rad/s[15]研究其对环件壁厚变化的影响,其余模拟计算条件见表1。图12为驱动辊转速对环件特征截面节点壁厚变化的影响曲线。可以看出,环件同一节点处的壁厚值随着驱动辊转速的减小而减小,其中当驱动辊转速由1.5 rad/s减小到1 rad/s时,环件壁厚分布基本相同,表明低转速范围内壁厚变化对转速不敏感。图13为滚压过程各道次环件壁厚减薄率随驱动辊转速的变化曲线。可以看出,环件的壁厚减薄率随着驱动辊转速的增大呈减小趋势,驱动辊转速为2.0 rad/s时,壁厚减薄率为5.2%。这是因为在进给速度与摩擦因数不变的情况下,环件在成形过程中的摆动会随着驱动辊转速的增大而增大,进而降低环坯与模具之间的接触应力,因此,实际生产中可以适当增大驱动辊转速,但转速不宜过大,因为过大的转速易使环件在转动过程中向一边“飞”起,产生动能效应,造成壁厚突变,加剧其分布的不均匀性。
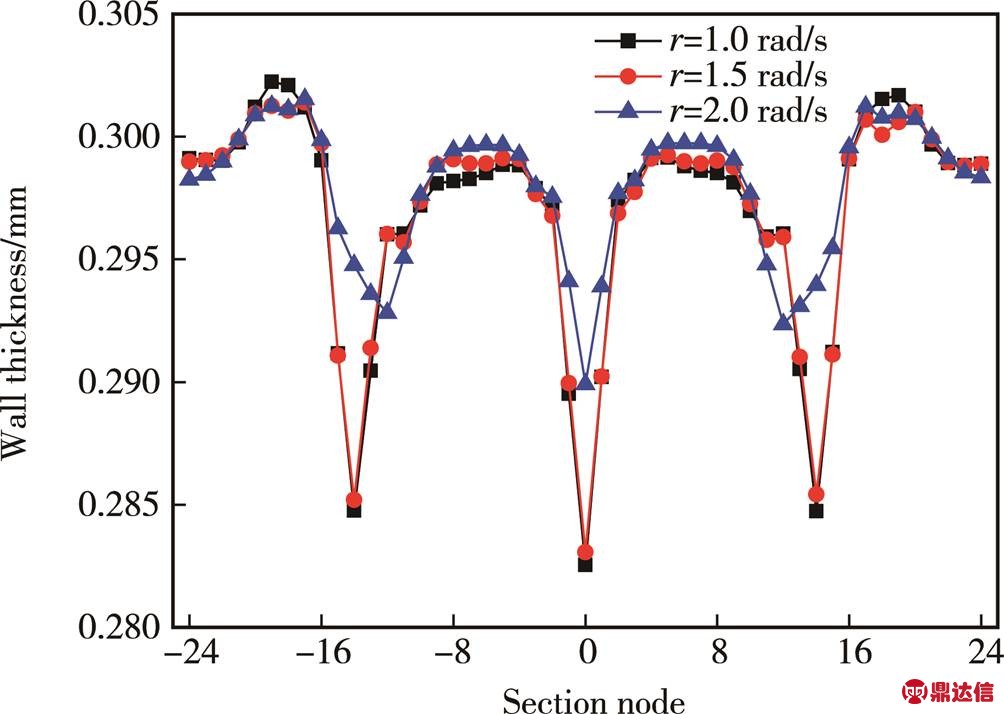
图12 驱动辊转速对环件特征截面节点壁厚变化的影响
Fig.12 Effect of driving roller rotation rate on the wall thickness variation of ring cross section
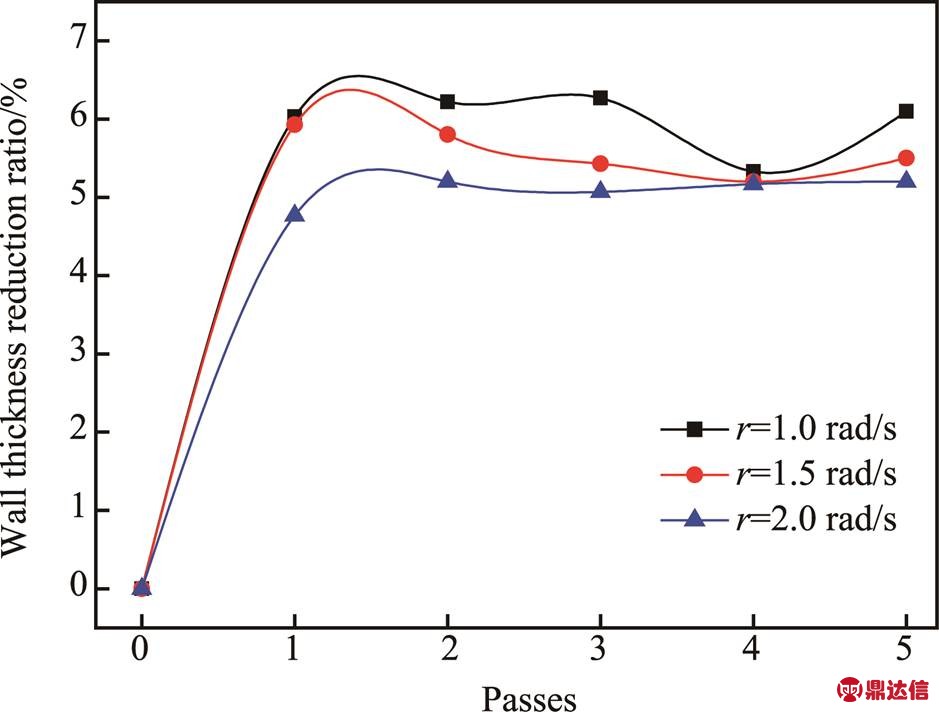
图13 驱动辊转速对环件壁厚的影响规律
Fig.13 Effect of driving roller rotation rate on the wall thickness of ring
2.4 进给辊与环件摩擦对壁厚变化的影响
取进给辊与环件摩擦因数为0.1, 0.2, 0.3[15]研究其对环件壁厚变化的影响,其余模拟计算条件见表2。图14为进给辊与环件间摩擦对其特征截面节点壁厚变化的影响曲线。可以看出,进给辊与环件间摩擦因数越大,特征截面节点壁厚减薄区域的壁厚越小,增厚区域的壁厚越大,环件不均匀变形程度增大。图15为滚压过程各道次环件壁厚极小值随进给辊与环件摩擦的变化曲线。可知,环件的壁厚极小值随着进给辊与环件间摩擦因数的增大而减小。这是因为在进给速度与转速不变的情况下,摩擦因数越大,环件材料向辊轮型槽流动的阻力越大,成形过程中材料的流动也就越困难,因此,成形过程中易适当减小进给辊与环件间摩擦,但不宜过小,因为摩擦力过小无法带动环件转动。
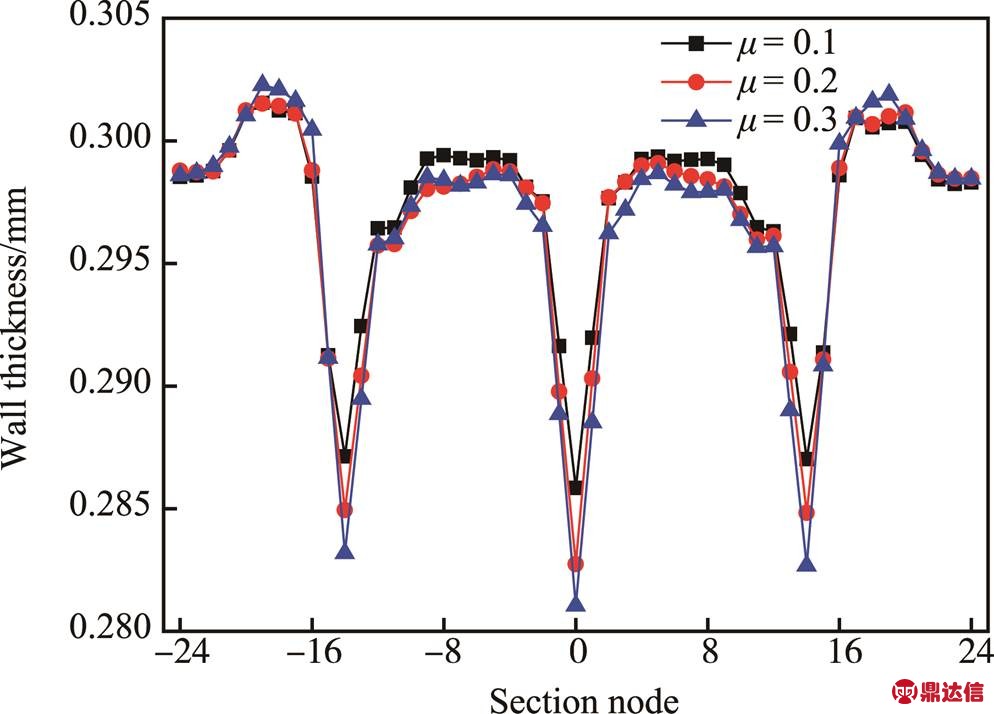
图14 进给辊与环件间摩擦对特征截面节点壁厚变化的影响
Fig.14 Effect of the friction coefficient between driven roller and ring on the wall thickness variation of ring cross section
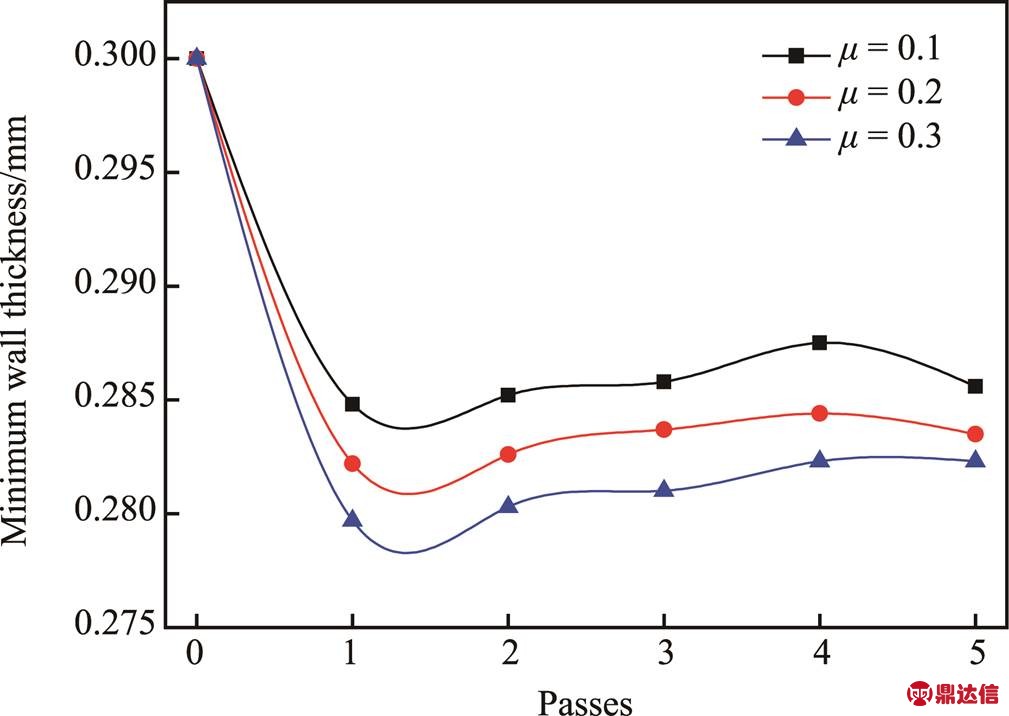
图15 进给辊与环件间摩擦对壁厚的影响规律
Fig.15 Effect of the friction coefficient between driven roller and ring on the wall thickness
3 结论
1)环件滚压成形过程,壁厚减薄主要发生在波峰、波谷位置且主要集中在第一道次,设计成形轨迹时,应合理分配各道次变形量,其中第一道次成形过程环件变形量的分配尤为重要。
2)环件滚压成形过程中,在一定工艺参数范围内,可以适当增大驱动辊转速,减小进给辊与坯料间摩擦与其进给速度,以降低成形件的壁厚减薄。适宜的工艺参数为:驱动辊转速为2 rad/s,进给速度为0.2 mm/s,摩擦因数为0.1。