摘 要:为解决重载车辆中由于胀圈密封失效而导致的传动系统故障问题,提出通过胀圈的非圆设计减小辅助密封面和接口处漏率,并减小胀圈失稳破坏的可能性,以提高胀圈密封的可靠性和使用寿命.分别通过基于曲梁解的理论解析和有限元数值模拟方法分析了胀圈装配状态下的受力与变形情况,计算出可以实现辅助密封面理想贴合的非圆胀圈的外轮廓曲线,讨论了解析方法的适用范围和接口形式对非圆线形的影响.通过对胀圈变形和受力状态的有限元分析,发现非圆胀圈的密封间隙和漏率明显减小,密封性能显著提高.
关键词:密封环;非圆设计;接口;数值模拟;旋转密封
胀圈型密封环是一种应用于旋转轴密封的分剖 式弹性圈,具有结构简单紧凑的特点,是目前车辆传动系统中旋转动密封结构的关键零件,在旋转轴和固定衬套间起密封作用.在传动系统中,胀圈具有滑磨性和易损性,决定了传动系统整体的安全性和可靠性.随着液力传动技术的发展,液体压力和转速的不断提高,旋转轴动密封技术已成为传动系统的关键技术之一[1-2].车辆传动装置不断趋于高速化和小型化[3],研究并设计高性能胀圈可以满足未来高速重载车辆的研制需求.
胀圈的设计一般是基于现有规范和经验同简单理论分析相结合的方法.利用这种方法所设计的胀圈在实际高PV值工况下容易出现严重的泄漏和磨损问题,难以满足不断增加的密封介质压力和转速要求.目前,对旋转轴动密封的研究主要还是密封性能的测试,而对机理的研究和分析还不够深入和完善,这导致了高性能动密封环的设计和制造缺乏足够的理论支撑[4].
发表的文献中较多的研究是对于胀圈主密封面泄漏和磨损问题的探讨[5-6],而对胀圈辅助密封面和接口状态的分析相对较少.在液力传动用合金铸铁密封环国家机械行业标准中[7],采用的圆形环设计要求胀圈装配后也近似是圆形并与衬套贴合良好,然而在实际应用中,这种贴合是不容易实现的.胡纪滨等[8]利用了高精度小型电涡流位移传感器对胀圈服役时的周向运动状态做了精确测量.实验表明辅助密封面存在较大间隙.而且随着流体压力的不断增大,间隙不会闭合,成为密封泄漏的通道,引起较大的泄漏率.为此,受到自由形活塞环设计方法的启发[9],设计合理的非圆胀圈可以实现装配后辅助密封面的贴合.
针对胀圈结构设计不合理导致的辅助密封面贴合不佳问题,分别通过基于曲梁解的理论分析方法和有限元数值模拟方法分析了胀圈装配状态下的受力与变形情况,基于反向设计方法计算出了可以实现辅助密封面理想贴合的非圆胀圈的外轮廓曲线,并分析了解析方法的适用范围和接口形式对非圆线形的影响.
1 非圆胀圈的设计方法
1.1 非圆胀圈设计的解析解法
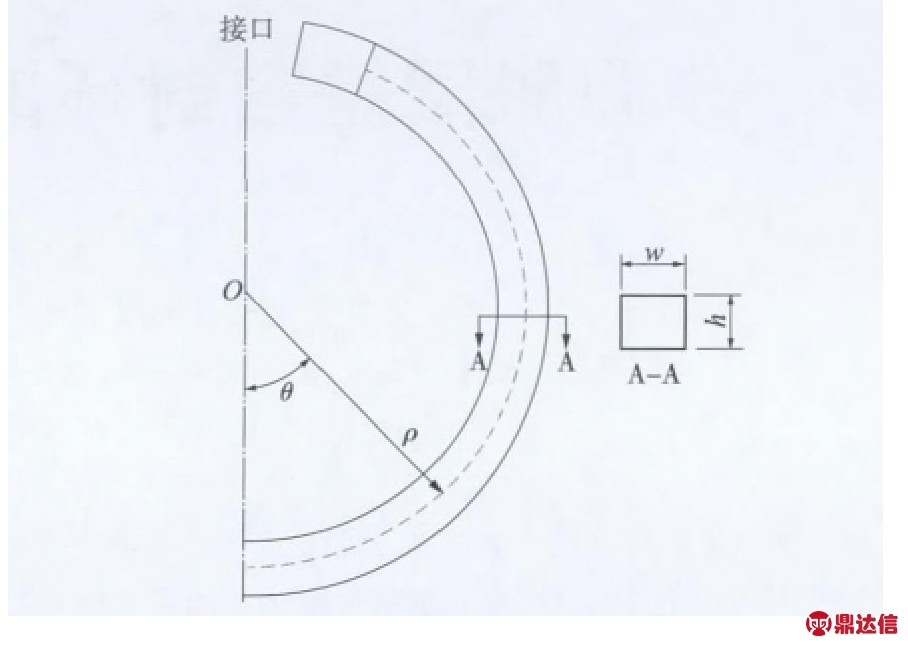
图1 非圆胀圈的几何参数
Fig.1 Geometric parameters of non-circular seal ring
为实现胀圈装配后是圆形,能与衬套理想贴合,受到均匀的接触压力,可采用反求的方法设计高性能的非圆胀圈结构.通过在假定的装配后是圆形的胀圈上施加同接触压力相反的作用力,获得非圆胀圈自由状态下的形状.根据胀圈的对称性,可取1/2模型来研究.由于胀圈的径向宽度同外径相比是小量,可以简化其为一端固支、一端自由的Bernoulli-Euler梁,利用经典曲梁理论,可推导得到不同角度θ值对应的曲率半径的量纲一表达式为
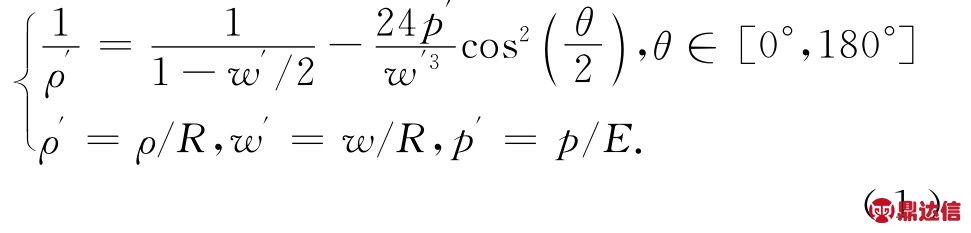
式中:R为固定衬套内壁面半径;w为胀圈径向宽度;p为胀圈所受径向压强;ρ为自由形的基线曲率半径;E为材料的弹性模量;R0为胀圈的外径.将非圆胀圈基线沿径向扩展w/2可得非圆胀圈外轮廓线形.
由于圆形胀圈装配后并非为圆形,若按等周长设计方法,即利用胀圈周长和衬套周长相等的条件,所设计的胀圈会导致接口间隙对碰的情况,容易导致胀圈的失稳破坏,若一味增加接口间隙则会导致漏率增加.采用反求方法获得的非圆胀圈设计,不需要对接口间隙进行单独计算,这就避免了上述问题.同时,考虑到胀圈服役条件下热膨胀问题,需要留有一定的热间隙,量纲一的热间隙可以通过下式简单计算:

其中量纲一的热间隙值定义为

式中:α为胀圈材料的热膨胀系数;ΔT为胀圈服役条件下的温升.
1.2 非圆胀圈的数值解法
解析法具有直观、简单和分析速度快的优点,然而为满足高性能的非圆密封环的设计要求,采用数值法可以获得更精确地非圆胀圈结构.为此,本文用有限元软件Abaqus对非圆胀圈轮廓进行了数值求解.与解析解法一样,采用反求方法求解非圆胀圈的原始结构.建立圆形胀圈三维模型,接口间隙值按式(2)计算,通过在辅助密封面施加与接触力大小相等方向相反的均布压力,获得变形后的胀圈即为所要求解的原始非圆胀圈结构.数值解的优势在于可以考虑接口形状对于非圆胀圈轮廓的影响.两种常用接口结构,如图2所示.
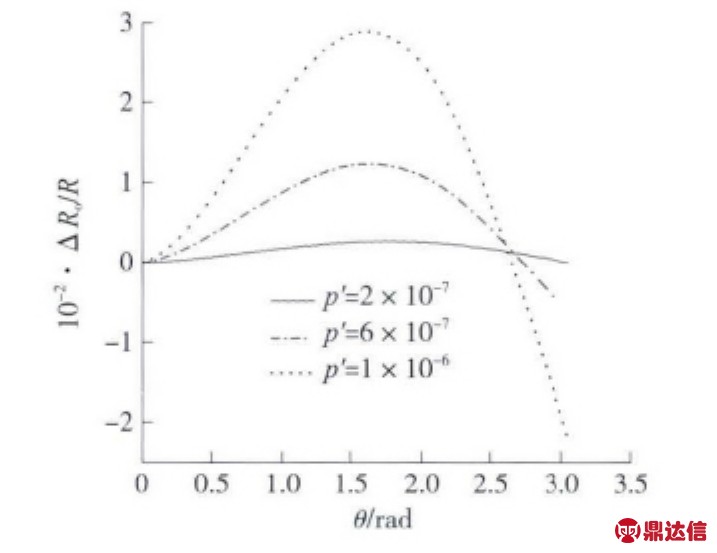
图2 胀圈接口结构几何模型
Fig.2 Geometric model of the incision of seal
2 非圆胀圈的设计结果
如图3~图4是由数值方法得到的非圆胀圈外轮廓曲线.预装配压力p′和径向宽度w′是影响非圆胀圈形状的主要设计参数,通过分别固定w′=0.065和p′=6×10-7,分析p′和w′对设计结果的影响.
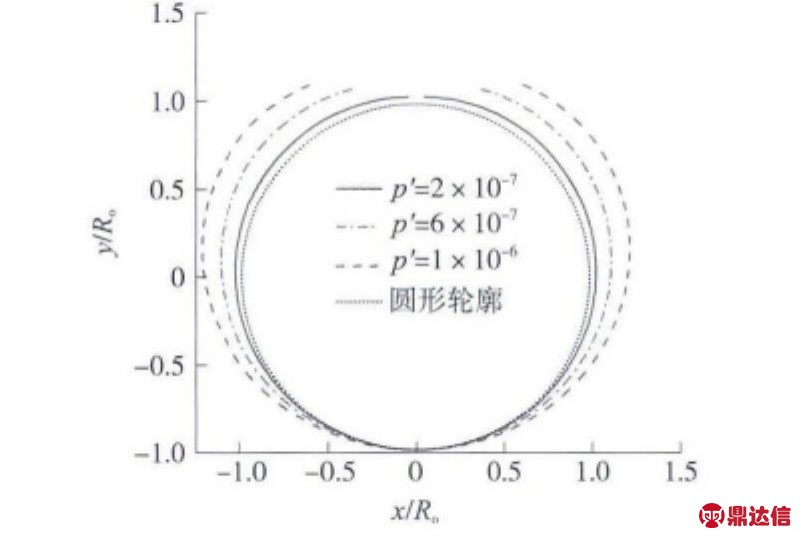
图3 不同预装配压力下的胀圈非圆曲线
Fig.3 Non-circular curves of seal caused by different preassembled pressure
图3所示的是预装配压力对非圆胀圈外轮廓的影响,可以看到p′越大,胀圈变形越大,非圆线形表现为偏离圆形形状越大,呈现出横宽竖扁的形状特征.图4所示的是径向宽度对非圆胀圈外轮廓的影响,w′越大,胀圈刚度越大,变形越小,非圆线形偏离圆形的程度越小.其中Ro为胀圈的外径.
为比较解析解和数值解的偏差,分别对相同预装配压力(p′=6×10-7)下和径向宽度(w′=0.065)下的非圆轮廓结果偏差进行分析比较,如图5~图6所示.
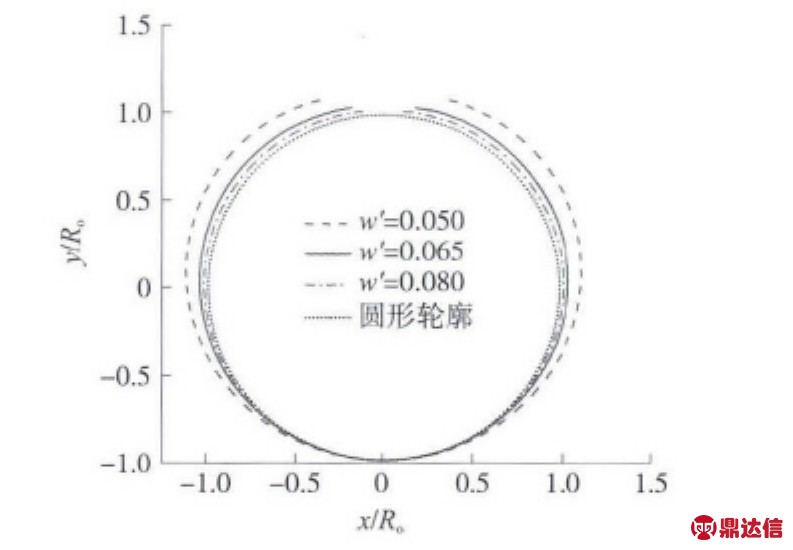
图4 不同径向宽度下的胀圈非圆曲线
Fig.4 Non-circular curves of seal on different radial width
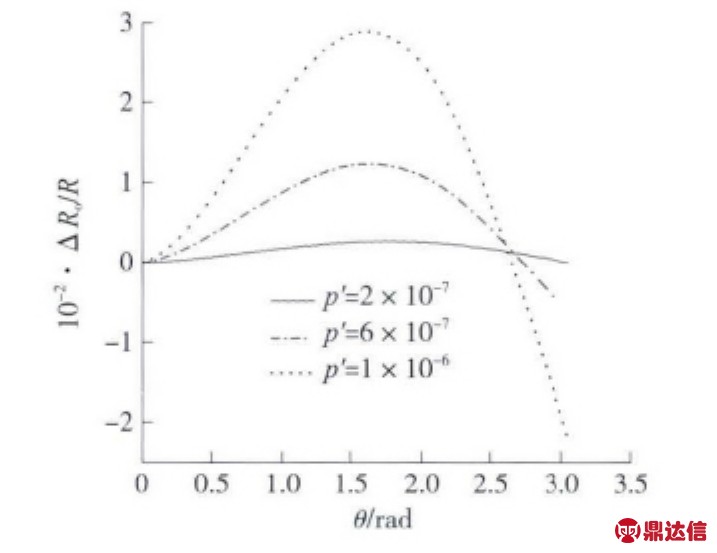
图5 不同p′胀圈的数值法与解析法非圆曲线的偏差
Fig.5 Deviation of non-circular curves between numerical and analytical solutions on different p′
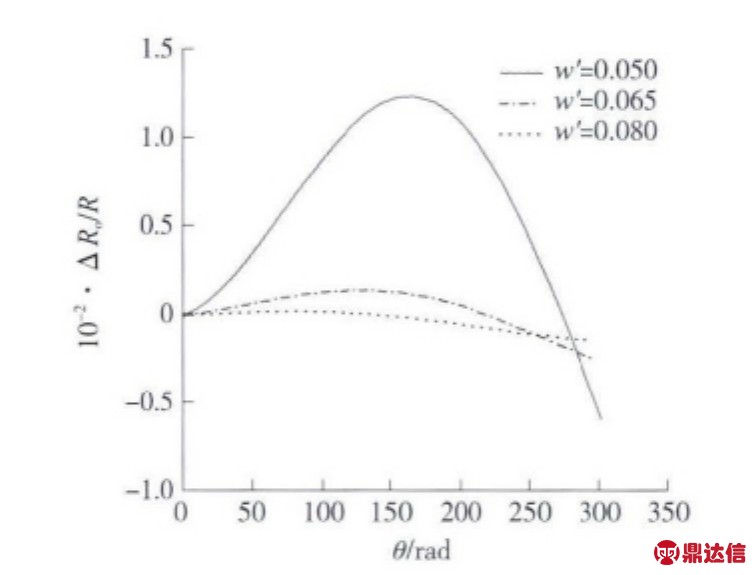
图6 不同w′胀圈的数值法与解析法非圆曲线的偏差
Fig.6 Deviation of non-circular curves between numerical and analytical solutions on different w′
工程实际与计算表明台阶式接口较直截面接口有更好的密封性,但加工难度大,而且在装配使用中台阶根部容易折断.在工程中,非金属胀圈台阶尺寸近似取1/8R.图7~图8分别是相同预装配压力和径向宽度条件下采用直端面接口和台阶式接口时非圆轮廓偏差值的计算结果.由于不同形状的接口处局部刚度的不同,以及作用于胀圈的反推压力分布的不同,非圆线形存在一定的偏差.分析结果表明采用不用的接口形式非圆线形的最大偏差达到2%,这是非常明显的差异,如若不加以注意会导致辅助密封面间隙过大而导致密封失效.因此在高性能非圆胀圈的设计中必须考虑具体接口形状,就要根据不同的接口分别计算非圆线形.
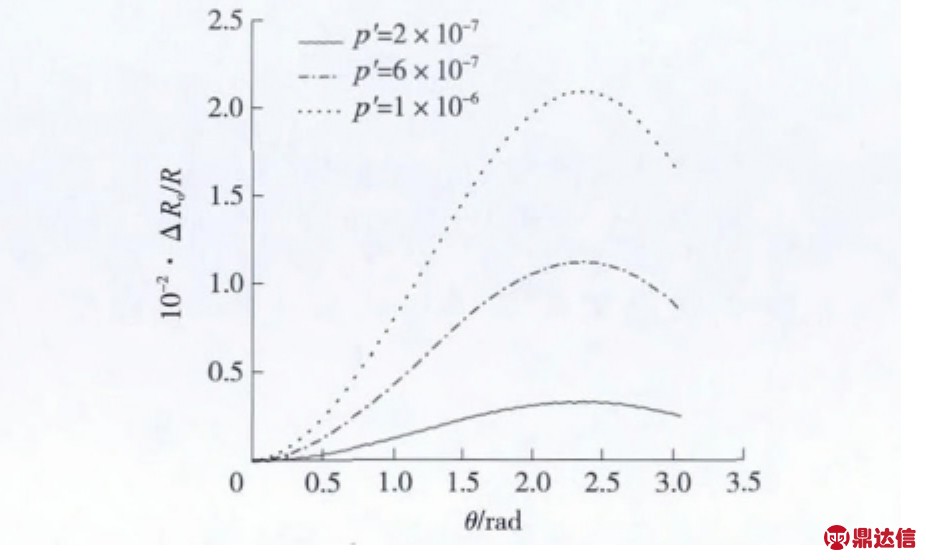
图7 不同p′的直端面接口与台阶式接口非圆曲线的偏差
Fig.7 Deviation of non-circular curves between flat and stepped incision on different p′
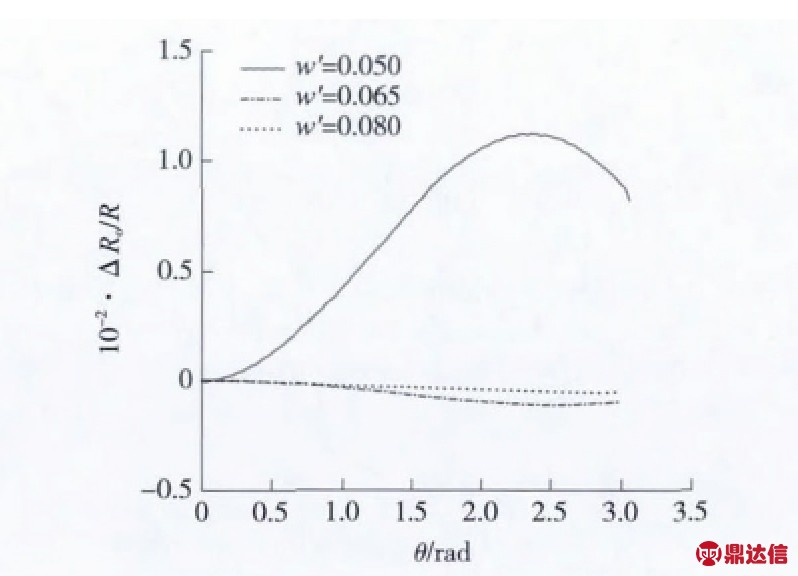
图8 不同w′的直端面接口与台阶式接口非圆曲线的偏差
Fig.8 Deviation of non-circular curves between flat and stepped incision on different w′
3 非圆胀圈的性能分析
为证实非圆胀圈设计对辅助密封面贴合情况改善的意义,对胀圈的装配进行仿真模拟分析.胀圈装配的有限元计算是静态大变形与接触问题,利用胀圈的对称性,取其1/2为研究对象.
数值计算表明:圆形胀圈装卡于衬套后,其形状不再为圆形,导致接触压力分布的不均匀和较大的间隙(如图9所示),这是不利于贴合的.装配后,圆形胀圈与衬套相分离的范围沿周向近似占辅助密封面整体的65%,且分离范围大小不受自由开口尺寸与接口形状的影响.装配后的辅助密封面间隙值随自由开口尺寸的减小而减小,然而由于胀圈弹力的限制要求,自由开口尺寸不能过小,因此圆形胀圈间隙不可避免.由于较大间隙的存在,在流压作用下辅助密封面存在泄漏,而且胀圈会有一定的扭转.在流压变化时,辅助面的、接口的间隙和胀圈扭转程度都会改变,这不利于胀圈在介质压力频繁变换工况下的稳定工作.相比之下,非圆胀圈在装配后的轮廓会近似为圆形,具有更好的贴合效果,接触压力p分布均匀(如图10所示,图中胀圈接口对侧是弧长值零点),可以实现稳定的良好密封.
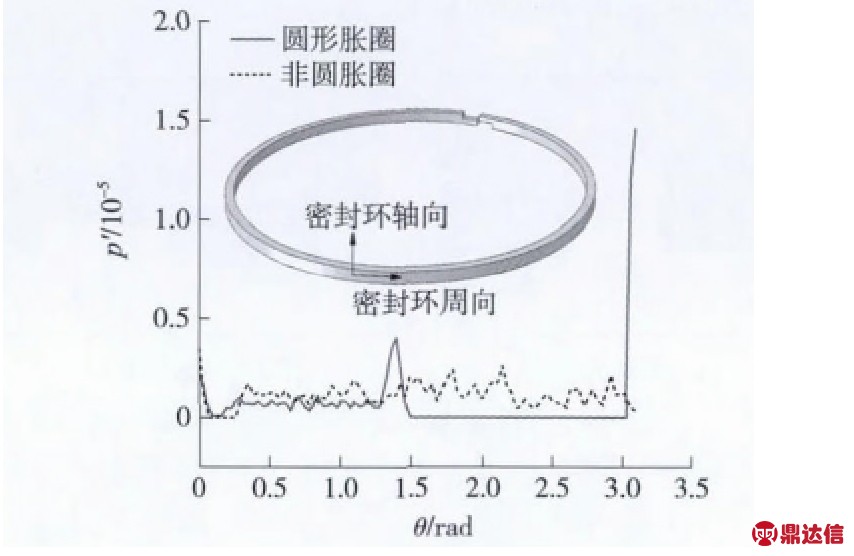
图9 胀圈接触压力
Fig.9 Contact pressure of sealing ring
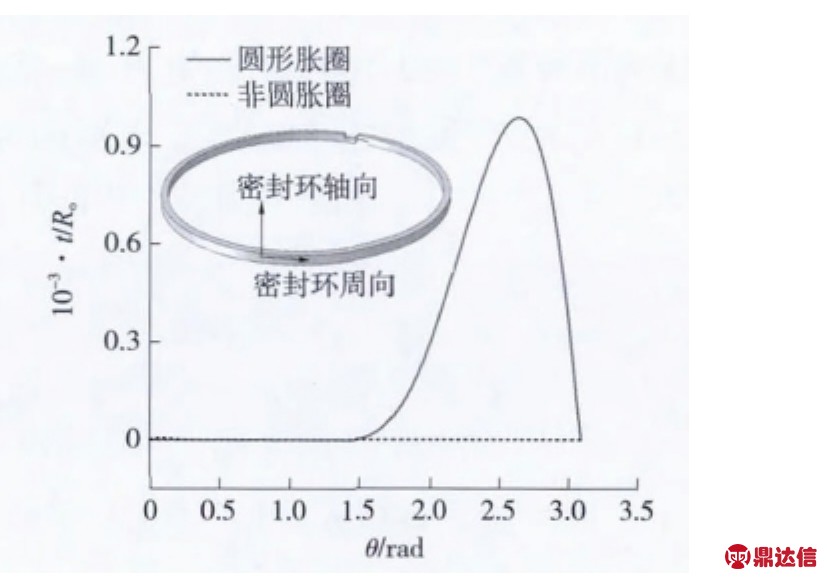
图10 胀圈间隙值
Fig.10 Gap of sealing ring
胀圈的性能指标主要有泄漏率、磨损量、表面温度和使用PV值等,其中漏率对于传动系统的传动效率的影响十分明显.假设辅助密封面是理想平整表面,间隙值t是常数,利用平行间隙黏性压差Poiseuille流动模型,近似计算辅助密封面的液体介质的泄漏.由不可压缩牛顿流体基本方程,推导出漏率的计算式

式中:p0、p2为间隙两侧的压强;μ为流体介质黏性系数.选取实际工况参数,利用式(4)的计算表明:对于外径为150mm的胀圈,在压差为1MPa(接近于实际的运行高压工况)条件下,当间隙值大于30 μm时,漏率达到1L/min以上,而且泄漏率随间隙值的增加呈3次关系增长.这就说明了通过改进设计,可以大幅提高胀圈的密封性能.
4 试验验证
为了验证非圆胀圈对辅助密封面贴合情况改善的作用,加工出了按以上理论分析得到的非圆轮廓设计的胀圈.为了检测贴合情况,利用高精度的环规(圆柱度小于5μm)模拟衬套,将非圆胀圈装入环规观察贴合间隙(如图11所示),发现与传统圆形胀圈相比,非圆胀圈的贴合间隙有显著的改善.在切口正对位置两种胀圈都贴合良好,在切口正对位置的右侧,圆形胀圈存在较大的间隙,这与理论分析结果是一致的,而按本文中分析的非圆轮廓加工的胀圈完全贴合.
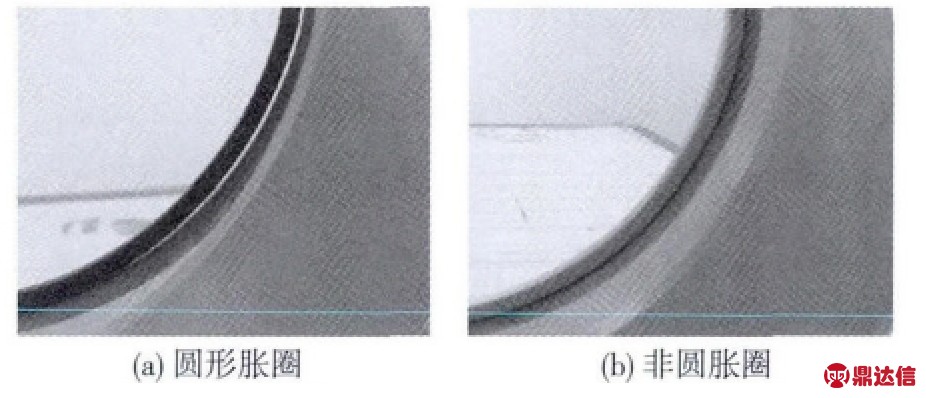
图11 胀圈间隙试验观察
Fig.11 Experimental observation of the gap of seal ring
5 结 论
①提出非圆胀圈的设计方法,利用解析方法和有限元方法对密封环结构参数进行计算.对比发现数值解具有更广泛的适用范围,并且接口形式会影响非圆线形.
②利用有限元方法,比较圆形与非圆胀圈的密封性能,发现非圆胀圈辅助密封面贴合良好,表现为:泄漏间隙很小、接触压力分布均匀和泄漏率较小,可以实现稳定的良好密封.