[摘要] 为探讨车辆传动装置的密封环早期失效的原因,掌握密封摩擦状态转变规律及其对密封性能的影响,利用传动装置密封性能试验台,测得摩擦因数-工况参数曲线(即f-G曲线),研究了不同油温条件下密封摩擦状态的变化规律,分析了密封环摩擦状态转变对密封性能的影响。结果表明,在设定的试验条件下,通过f-G曲线可揭示密封环在高速重载工况下摩擦状态转变规律及其辨识特征;密封环摩擦状态的转变对泄漏量的影响有限,而对密封环温升的影响较为显著。
关键词:重载车辆;传动系统;密封;工况参数;摩擦状态辨识
前言
重载车辆综合传动装置和乘用车机械式自动变速器均使用浮动密封环作为动态密封装置,主要解决旋转件与固定件之间的密封问题[1]。在实际运行过程中,重载车辆综合传动装置湿式离合器中的密封环由于受到各种因素的影响,使其密封性能变差,寿命缩短,最终出现提早失效的现象,直接影响到整个传动装置的使用性能,具体表现为油压无法正常建立,密封环端面严重磨损,泄漏量增多等失效现象。因此,研究密封环接触状态与摩擦行为,就成为重载车辆传动系统设计开发过程中必须解决的关键问题。从传动系统的使用情况看,它频繁变更运行条件,使密封环处于交变的负荷工况中。从设计和试验角度考虑,辨识摩擦状态变化的技术参数,充分掌握重载车辆传动装置密封环的工作状态,对改善密封性能,提高使用寿命具有重要意义。
端面摩擦因数是表征密封端面摩擦状态的主要参数之一,在不同的摩擦状态下,密封摩擦因数各不相同,国内外学者大多通过密封性能试验,根据摩擦因数来判断密封的摩擦状态[2-5]。而密封的摩擦状态可通过工况参数这个摩擦学特性相似准数来表征,一般情况下单一使用工况参数并不能完全表征端面摩擦状况[6],但可通过摩擦因数与工况参数的联合分析来辨别摩擦状况。为全面分析密封环在不同工况下的密封性能,须考虑在不同温度下密封端面摩擦状态和密封性能转变特征。因此,本文中通过几个温度条件下摩擦因数与工况参数的联合分布曲线分析临界工况的辨识特征,掌握不同条件下密封性能与摩擦性能的关系,为设计重载车辆的高可靠性和高寿命密封环提供依据。
1 密封环试验
重载车辆综合传动装置采用的密封环是一种应用在旋转部件的剖分式弹性密封圈,它带有切口形式,依靠自身弹力和油压作用涨开,密封环的主要密封界面是其端面,外圆柱面是辅助密封界面。密封工作示意图如图1所示。在一定的负荷p下,密封环与旋转轴组成一对摩擦副,正常工作时相互紧密贴合并相对转动,实现旋转轴的轴向流体密封。
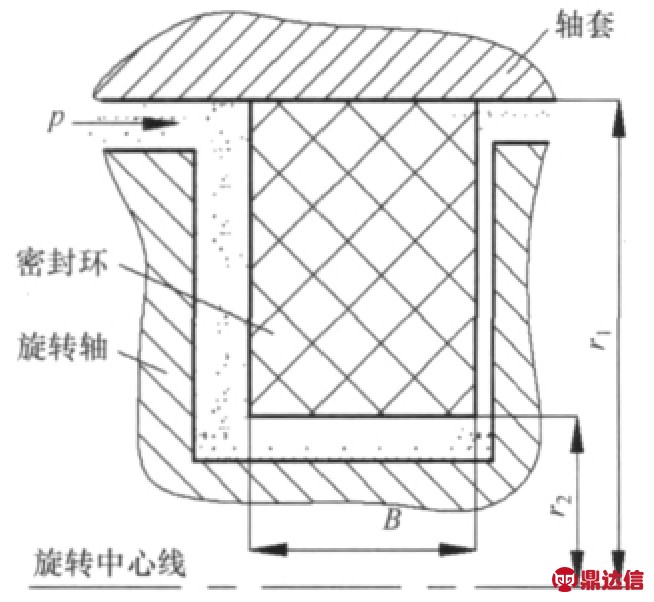
图1 密封工作示意图
试验在自主研制的密封综合性能试验台上进行,如图2所示。密封环安装在主轴上,传动主轴贯穿于试验油腔,另一端与变频电动机相连。转矩和转速传感器与主轴连为一体。油腔加热器、油温传感器和温度控制器组成密封油腔的温度控制与传感系统,选用电阻式温度传感器沿着密封环周向均匀布置,对摩擦副温度进行测试。试验油腔由专门的液压站供压,泄漏量由超声流量计测定。试验系统的转速、压力和油温设定值由上位机进行设置与控制,通过各个传感器反馈转速、转矩、压力、油温变化和密封环温度等测量值。
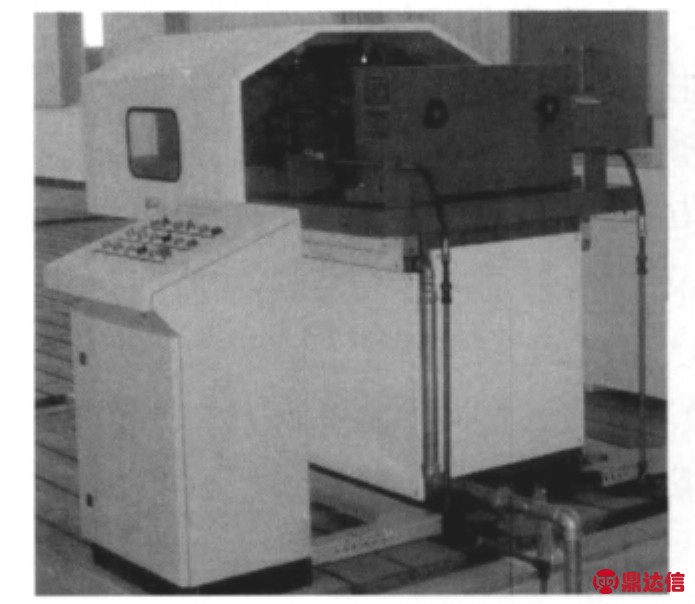
图2 试验装置实物图
密封环采用填充改性的聚四氟乙烯(PTFE)复合材料,其外半径 r1=62.5mm,内半径 r2=59.6mm,轴向厚度B=2.6mm。摩擦对偶件旋转轴的外径与密封环外径相同,材料是38CrSi合金钢。试验条件:主轴的旋转速度为50~5000r/min,试验压力为0.5~2.5MPa,本文中考察pv值(即压力p×速度v)的变化范围为8~79.6MPa·m/s。测试时试验室环境温度为18.5℃。
2 试验结果与分析
2.1 摩擦因数-工况参数试验曲线
在密封系统中,工况参数G根据相似原理推导而来[2],定义为油膜黏性力与油膜负载的比值,即

式中:μ为密封介质的动力黏度,Pa·s;v为密封环端面的相对平均线速度,m/s;WR为密封端面的径向宽度,m;FN为密封端面的总载荷,N。工况参数的大小说明了密封环的运行工况和流体油膜的承载能力,是衡量油膜形成难易程度的无量纲特性值[7-8]。
密封摩擦副的摩擦因数根据转矩传感器检测的摩擦力矩和施加的正压力获得,即

式中:T为摩擦力矩。
研究密封环临界工况的摩擦状态转变特征,进行相关试验研究,不但要获得密封环工作状态变化规律,还须得到在实际工况下密封环的各项性能,主要是泄漏量和密封环温度等指标。在油温80℃的工况下,通过试验获得密封性能与摩擦因数的对应关系和规律。图4为密封环摩擦因数、温升和泄漏量随pv值的变化关系。
利用上述的密封综合性能试验台进行试验,试验前对密封环进行磨合,在试验数据采集时,经过300~350s数据保持平稳后,按照式(1)和式(2)计算并记录工况参数与摩擦因数值。油温分别为40℃、80℃和120℃的条件下获得的试验结果即f-G曲线如图3所示,图中曲线由试验离散值通过四次多项式拟合得到。
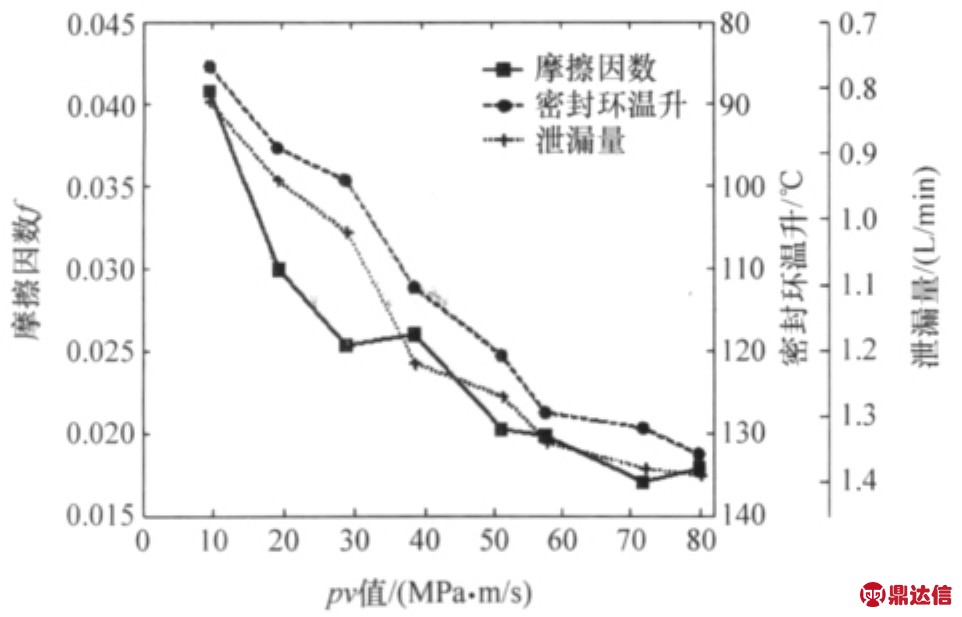
图3 不同油温下的f-G关系曲线
利用f-G关系曲线区分摩擦状态的关键在于获得摩擦状态改变的临界点。密封环的f-G曲线存在着两个状态转折点,分别标志着由流体摩擦转变为混合摩擦和由混合摩擦转变为边界摩擦[10]。图3的曲线形状各不相同,但都有相似的趋势:曲线都先下降,到达一个最低点后又上升。
图3(a)曲线在起始处有一小段f变化平缓的线段,此处摩擦因数处于较低水平,而工况参数G也不大,它表征了这段区域易处于边界摩擦状态。随后曲线开始下降,直到最低点。接着曲线呈现线性上升的趋势,摩擦因数和工况参数都在不断增大,表明这段工况状态中油膜承载能力最大,而油膜间的内阻力矩也随之增大,转速较高。曲线上升的这段区域符合流体摩擦状态的特征;而对应于从变化平缓转为较快下降直到最低点的这段曲线,摩擦状态相应地从边界摩擦转为混合摩擦。
图3(b)和图3(c)曲线趋势状态与图3(a)类似,其基本特征在于:(1)油温在大于等于80℃以后,曲线的下凹程度随着油温的升高而加剧,进一步证实了油温对摩擦状态的影响,油温升高造成了介质运动黏度的减小,油膜最大承载能力降低;(2)曲线的转折点逐渐左移,与此对应的摩擦因数也相对减小,符合密封流体润滑区间值随着油温的升高而逐渐减小的基本规律;(3)在油温较低的工况,边界摩擦区域与混合摩擦区域的转折点不太明显;随着油温的提高区分3种摩擦状态区域的两个转折点逐渐明朗。
由试验数据可以分析得出:在重载、低速和低介质黏度的工况下,密封环易处于边界摩擦状态;在轻载、高速和高黏度工况下,密封环基本处于流体摩擦状态;除此之外的工况基本处于混合摩擦状态,也易处于混合摩擦状态。而且在变工况的密封系统中,摩擦状态随着油温、转速和压力这些工况条件的变化而改变。
2.2 密封性能转变规律
前面的语义仅描述了语句和世界之间的静态关系。但真值仅是自然语言的一方面,甚至不是其关键的部分。近年来,行动逐渐引入到逻辑理论,如从解释到言语行为和会话理论。在数学和计算机科学中有句名言:“从来不研究没有转换的表达”。所以需要在积和进程之间建立一种对偶关系,例如 “论证”是人们追求的活动,也是逻辑学家们所研究的内容。
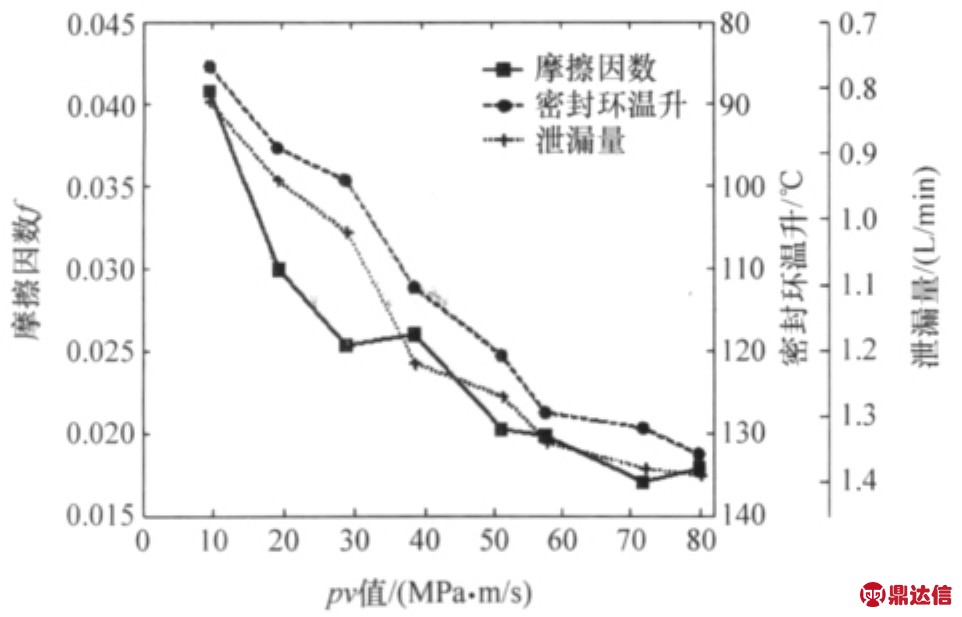
图4 摩擦因数、密封环温升和泄漏量随pv值的变化关系
由图可见:在pv值的变化范围内,反映密封端面摩擦状态的参量摩擦因数与试件温升和泄漏量均呈现出一定的对应关系,但并不成严格的比例;在pv值小于40MPa·m/s时,摩擦因数曲线变化幅度较大,密封环温升与泄漏量均有轻微波动,但下降趋势明显;pv值大于50MPa·m/s时,摩擦因数、密封环温升和泄漏量的变化减缓,其幅值保持在一定的范围内,不再有明显的上升或下降的趋势,尽管密封环温度继续升高,但升高幅度却大大降低,变化维持在较小的范围内。
通过变化曲线可知,摩擦因数与试件温度的对应关系相对比较清晰,随着pv值的增大,即转速越高、压力越大,单位时间内密封摩擦副摩擦次数和剧烈程度相应增加,摩擦热效应增强,密封摩擦副所产生的摩擦热量越多,待pv值到达一定程度时,热量的产生与耗散基本处于一个平衡状态,摩擦引起的温度变化趋于稳定,此时摩擦因数的降幅亦趋平缓,泄漏量也变化不大,表示磨损机制由于摩擦热、工况改变等外部条件的影响发生了转变。由分析可知,在低速低压的运行工况(pv值<40MPa·m/s)时,反映密封性能的各项指标变化比较剧烈,性能不十分稳定;在高速高压(pv值>65MPa·m/s)时,尽管密封温升和泄漏量趋于稳定,但数值较高,不利于密封环长周期的服役,而pv值在45~55MPa·m/s之间时,摩擦因数较小,密封表面温升相对不高,从密封环减小磨损角度和传动系统运行条件方面考虑这是相对适宜的运行工况。
3 结论
通过密封性能试验台进行试验,获得几种典型温度下摩擦因数-工况参数关系曲线,获得液体摩擦转变到混合摩擦和由混合摩擦转变到边界摩擦时摩擦状态改变的临界点,通过试验和比较分析的方法,可以基本掌握密封环在高速重载工况下摩擦状态的转变规律及其辨识特征。
研究重载车辆传动系统密封环摩擦状态转变对密封性能的影响,通过试验获得密封环温升和泄漏量与摩擦因数的对应关系和规律,表明摩擦状态的变化都会带来密封环性能的改变,其中泄漏量主要受到工况条件的影响,密封环温升受摩擦状态的影响更为明显。