摘 要:对核电站反应堆压力容器用金属O形密封环的主要制造工艺和技术关键以及性能试验等进行了介绍。通过从原材料研制到制造工艺开发,金属O形密封环达到了设计技术要求,并已商用于国内300 MW反应堆压力容器,实现了金属O形密封环的完全国产化。
关键词:核电站;反应堆压力容器;O形密封环;制造
0 引言
压水堆核电厂反应堆压力容器是主回路冷却剂压力边界屏障的重要设备,属于核安全1级设备,其使用寿命决定了整个核电站的服役年限。该设备主要用来包容和固定反应堆堆芯,并把核裂变反应控制在其内进行。因此,反应堆压力容器处于高温、高压、放射性环境中,要求其在各种正常运行、试验工况下,均能保持结构完整性,不发生容器的脆性断裂破坏和放射性物质的泄漏。反应堆压力容器由筒体和可拆卸顶盖组成,两者之间采用双道镀银的O形截面金属圆环实现密封,内密封环起主密封作用,外密封环实现二次密封(如图1所示)。反应堆压力容器的密封性能直接关系到整个核电厂的正常启堆和长期安全运行[1-3]。
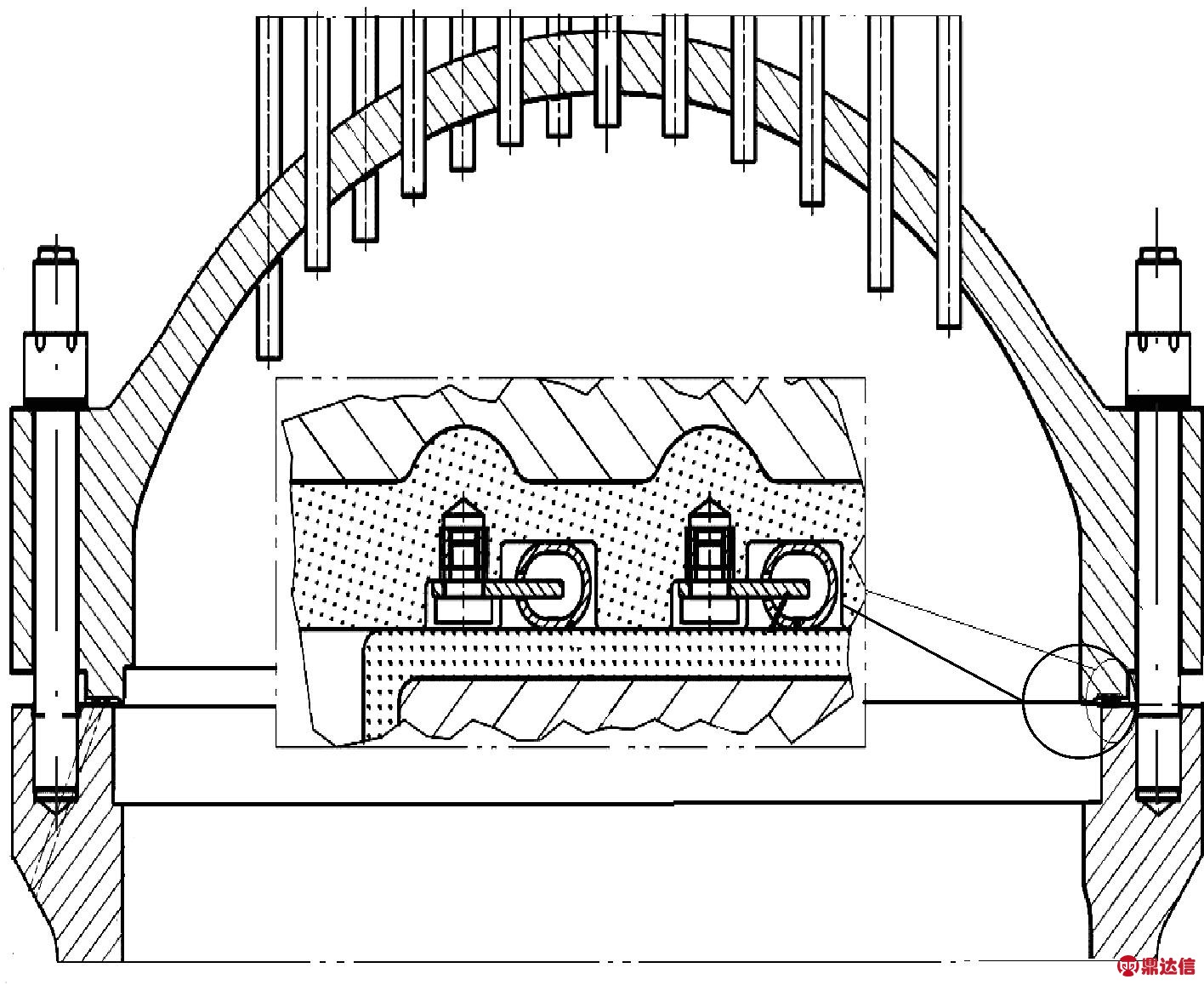
图1 反应堆压力容器用O形密封环
国内自20世纪80年代开始研制核反应堆压力容器O形密封环,材料采用Inconel 718和不锈钢。但是受到国内核电发展和原材料生产等因素影响,尚无厂家正式生产[4-6]。长期以来,国内核电站反应堆压力容器O形密封环全部依赖国外进口,严重制约了我国核电的安全持续发展。为此,自2013年开始,国内多家单位合作,针对300 MW、AP和CAP系列第三代反应堆压力容器O形密封环进行研发,通过逐一攻克关键技术和制造工艺,终于在2014年底成功生产出符合设计技术要求的O形密封环产品,通过了国家能源局的鉴定,并于2015年底应用于国内300 MW商用反应堆压力容器,突破了国外长期垄断的局面,从原材料到产品实现了拥有自主知识产权的O形密封环国产化。
O形密封环的研制主要围绕以下三方面进行:原材料的国产化研制;O形密封环制造工艺和设备的研发;O形密封环的性能试验和研究。
1 O型密封环设计参数
O形密封环的设计参数见表1。
表1 设计参数
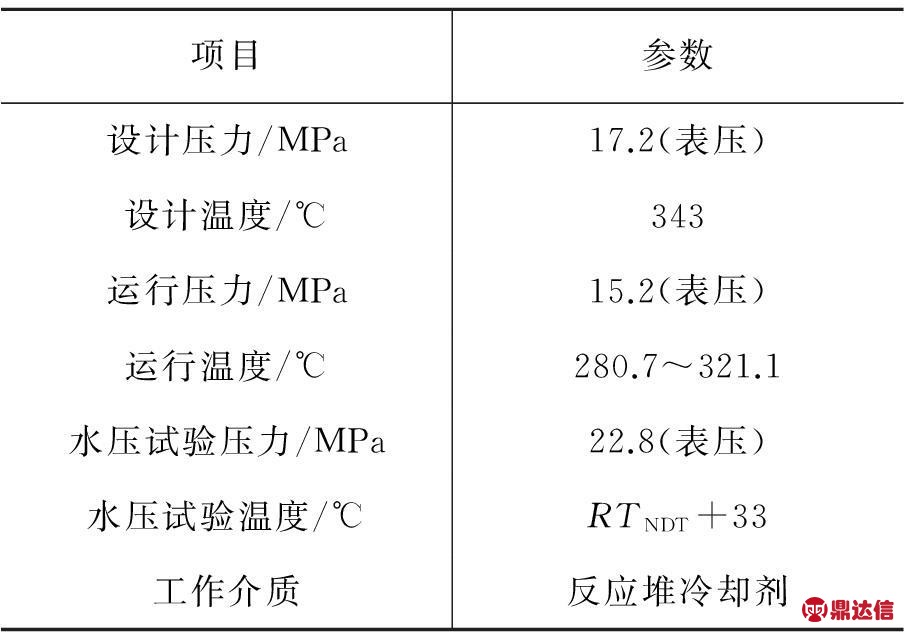
2 O形密封环结构特征
如图2所示,O形密封环是由截面直径为φ mm,壁厚为1.27±0.127 mm的Inconel 718无缝钢管弯曲,焊接成一圆环,环管内侧表面开若干长圆槽,最后在其表面电镀0.15~0.22 mm银层(纯度≥99.9%)。密封是利用Inconel 718管材的弹性变形以及银层的塑性流动而实现。在进入运行时,环管内部与密封系统压力空间相通,环管内的系统压力增加了与密封面的接触压力,从而起到压力自紧作用。这种弹性和塑性的配合以及金属与金属接触的密封设计[7-8],使该密封环具有很好的密封性能,以及补偿因温度和压力波动而引起法兰变形和密封载荷松弛的能力,泄漏率可达到10-9 Pa·m3/s(氦气,ΔP=1 bar)数量级。
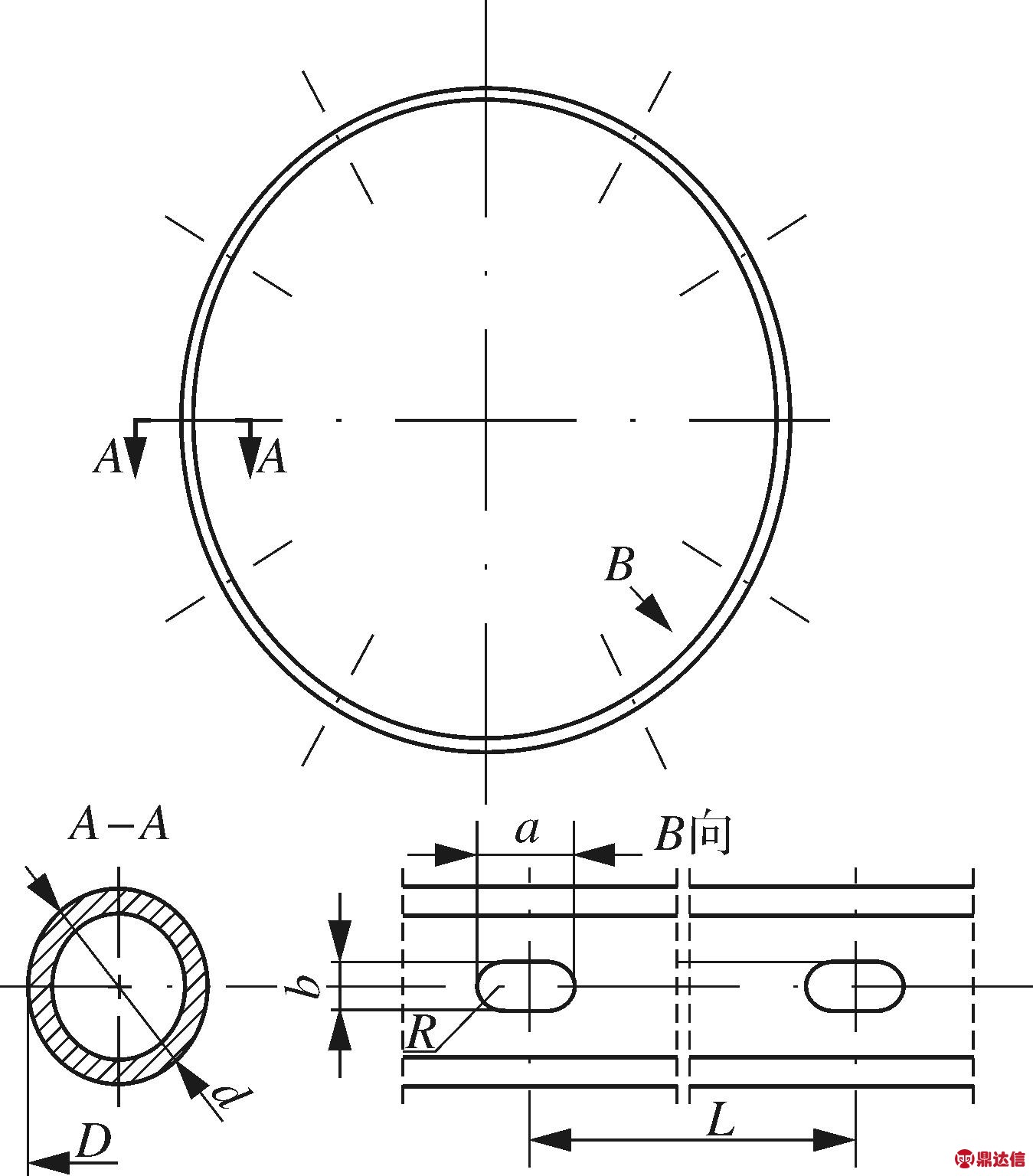
图2 O形密封环结构示意
3 管材制造和性能试验
3.1 制造
表2 Inconel 718合金管材的化学成分
(时效状态) %
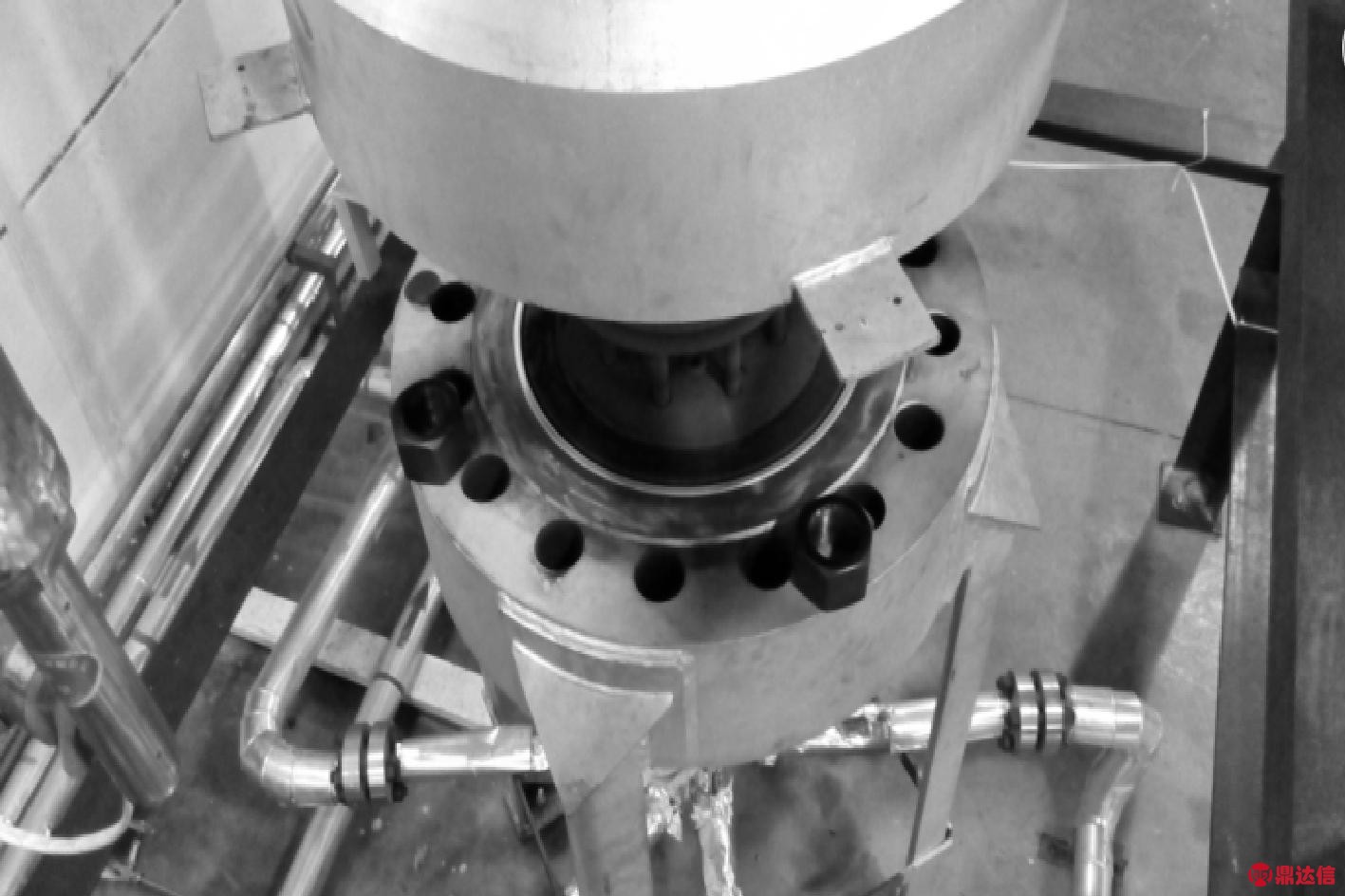
O形密封环的管材为Ni-Cr-Fe系列的Inconel 718材料,是经过固溶处理和时效处理的镍基合金材料。O形密封环的开发前提是实现Inconel 718管材的国产化。对于它们的化学成分、力学性能、尺寸和公差以及热处理要求,除应符合相关材料标准(AMS 5590)的规定外,还要符合核电站设计规范要求。在与国内镍基合金管材制造厂联合,通过近1年时间的工艺探索和产品研制,并经过化学成分、力学性能、压扁试验、挤压试验、扩口试验、水压试验等检测合格,于2014年初成功生产出国产Inconel 718管材。表2,3列出其化学成分、力学性能的测试结果以及与国外管材的比较。表4列出Inconel 718合金管材的检验项目。
表3 Inconel 718合金管材的力学性能
(时效状态)
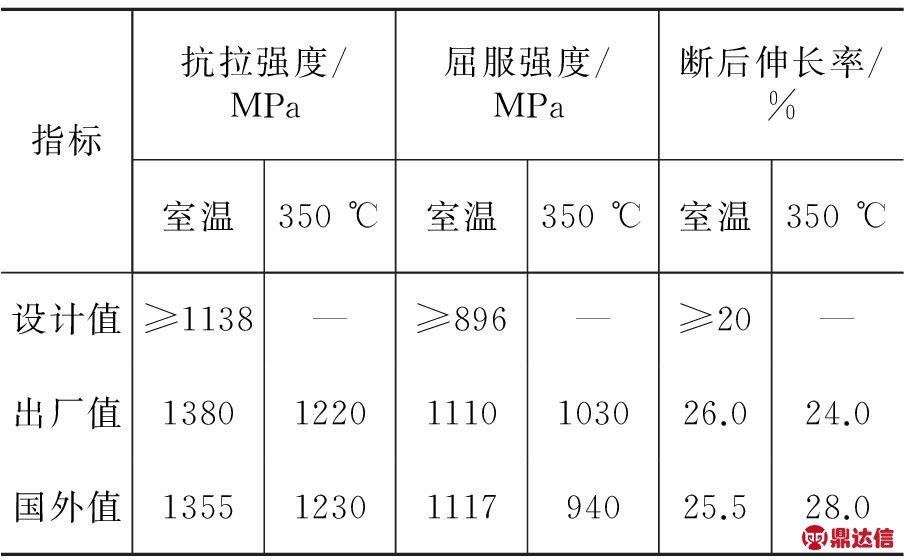
表4 Inconel 718合金管材的检验项目
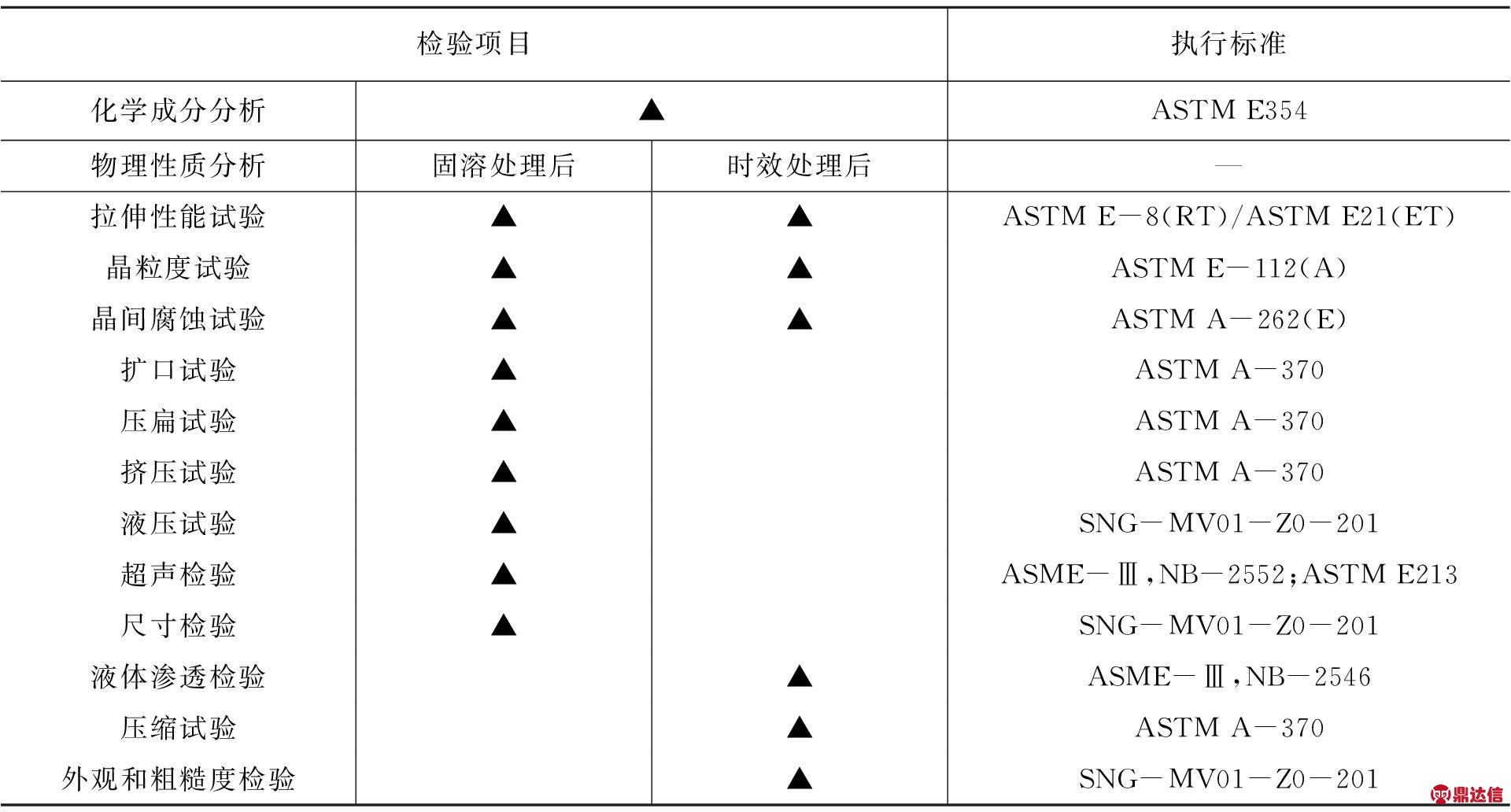
注:▲—需要检验项目。
3.2 性能试验
为了完整评价Inconel 718管材用于O形密封环的使用性能,对Inconel 718管材进行压缩率λ分别为7%,8.8%,12%,16%,20%的压缩回弹试验,并采用ABAQUS软件对不同压缩量下的接触宽度、压扁度、接触压力与回弹量进行有限元分析。以上试样选取长度为102 mm的未镀银Inconel 718的管子(见图3)。测试设备如图4所示。设计要求管材在压缩率16%下总回弹量不小于0.38 mm。
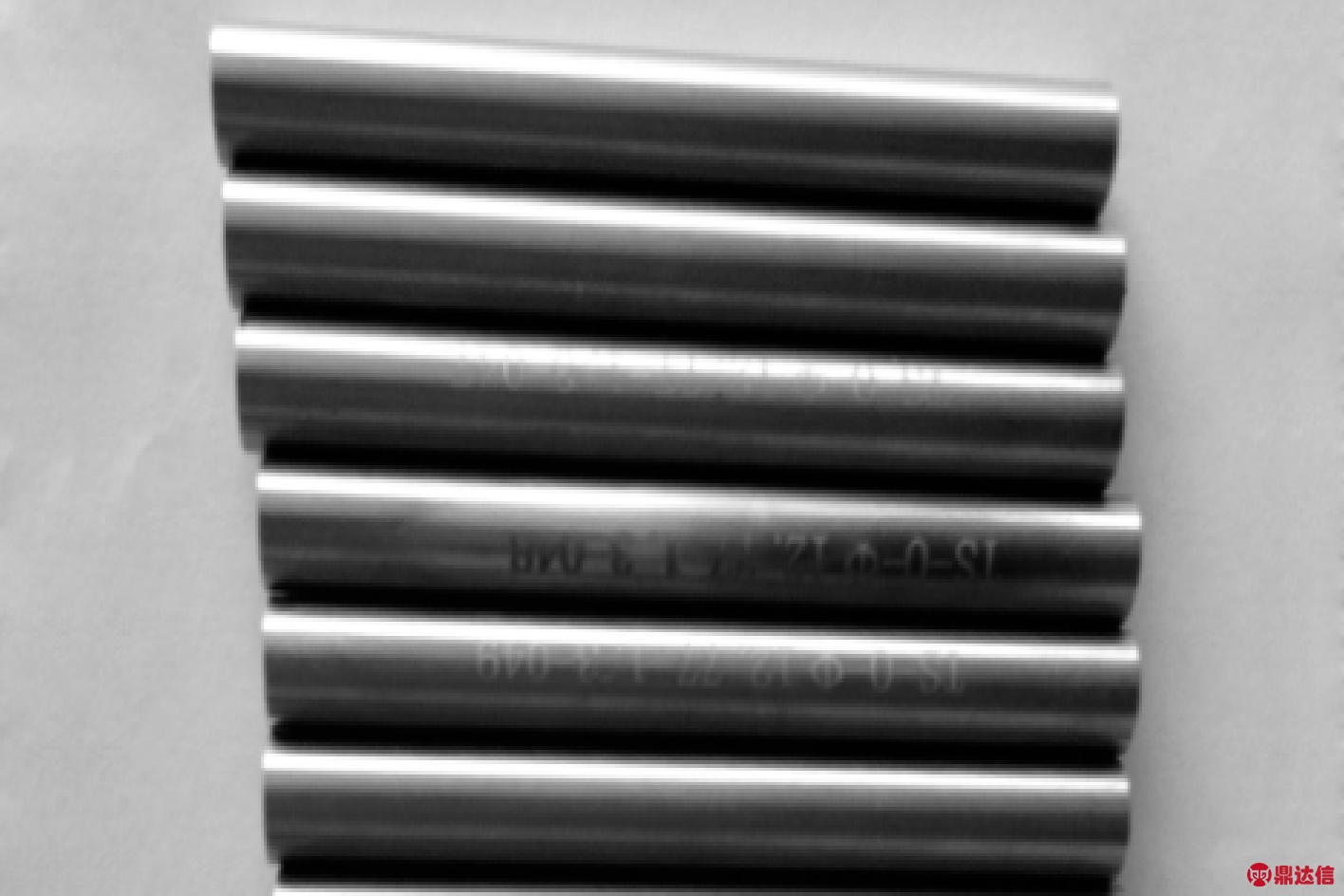
图3 试样实物
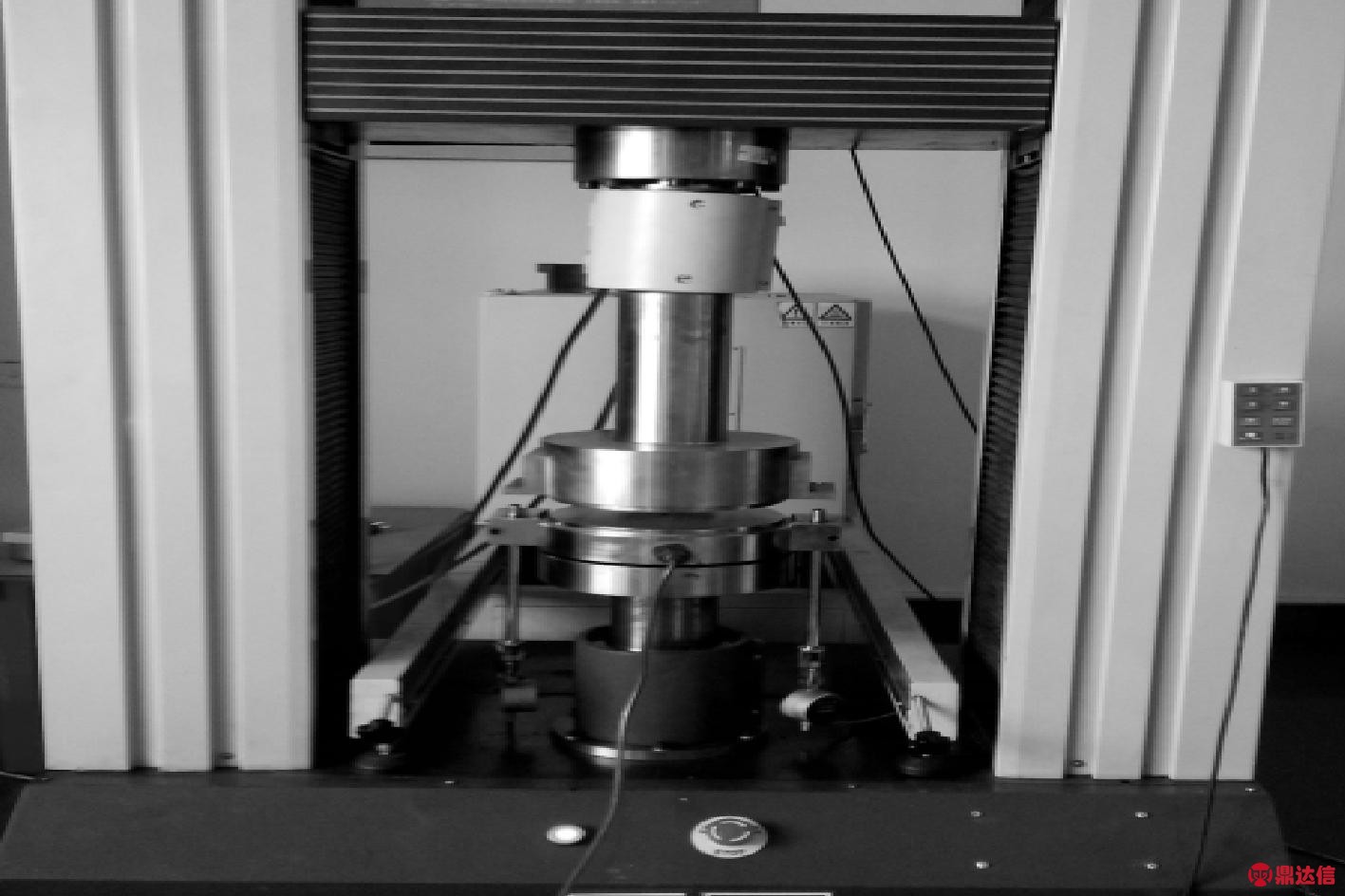
图4 压缩回弹试验装置
压缩回弹试验的位移和压缩载荷关系如图5所示,试验数据如表5所示。
从图5中可以看出,不同压缩量的压缩回弹曲线趋势基本相同。加载曲线可分为两段,第1段为线性阶段,管材的位移与压缩载荷呈线性关系,即管材发生弹性变形,未发生塑性变形;第2段为弹塑性变形阶段,管材发生部分塑性变形,此时压缩载荷的少量增加便会引起较大的位移。不同压缩量的卸载曲线近似为互相平行的直线。压缩率16%的总回弹量为0.40 mm,大于0.38 mm的设计要求。

(a) λ=7%
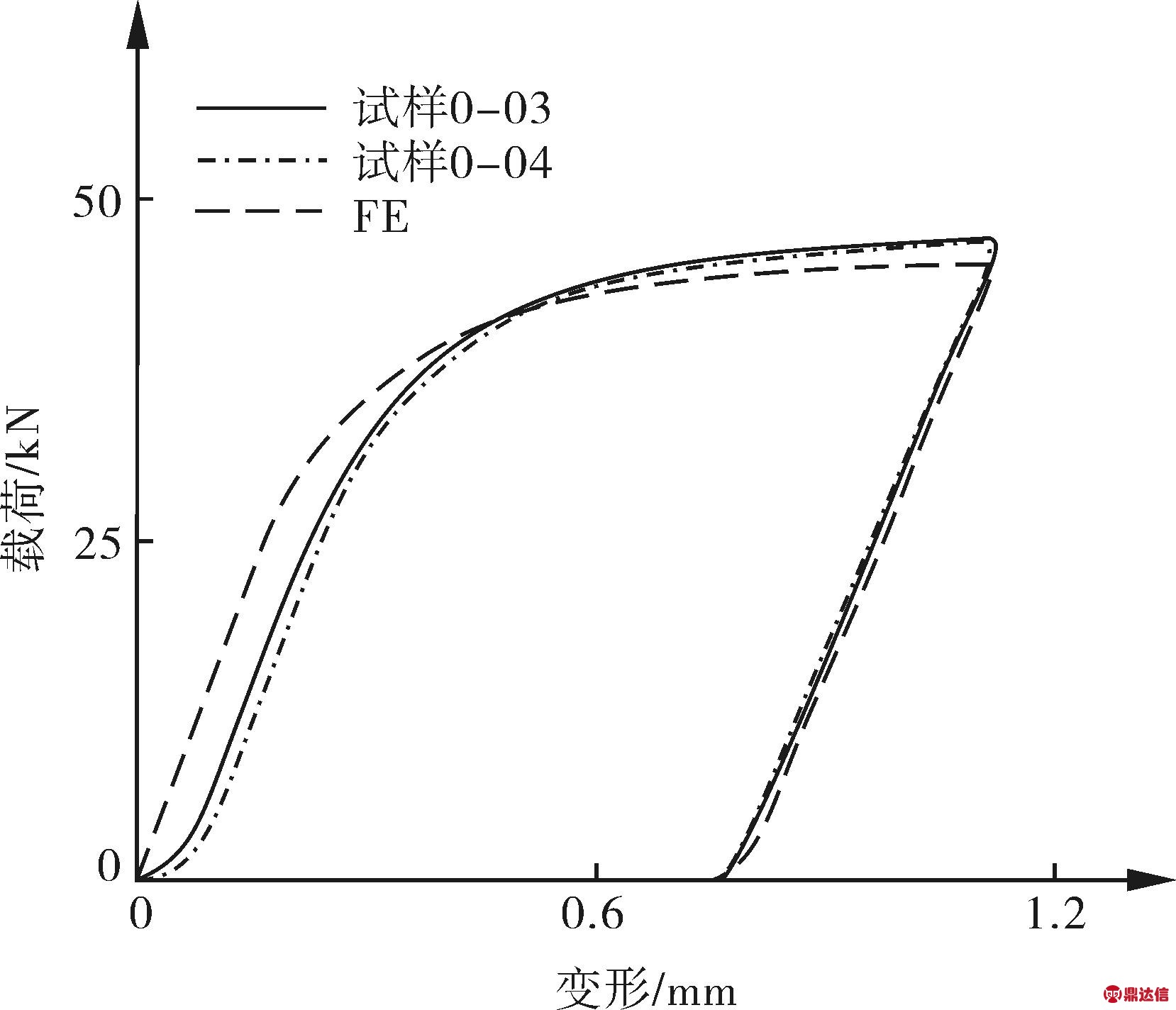
(b) λ=8.8%
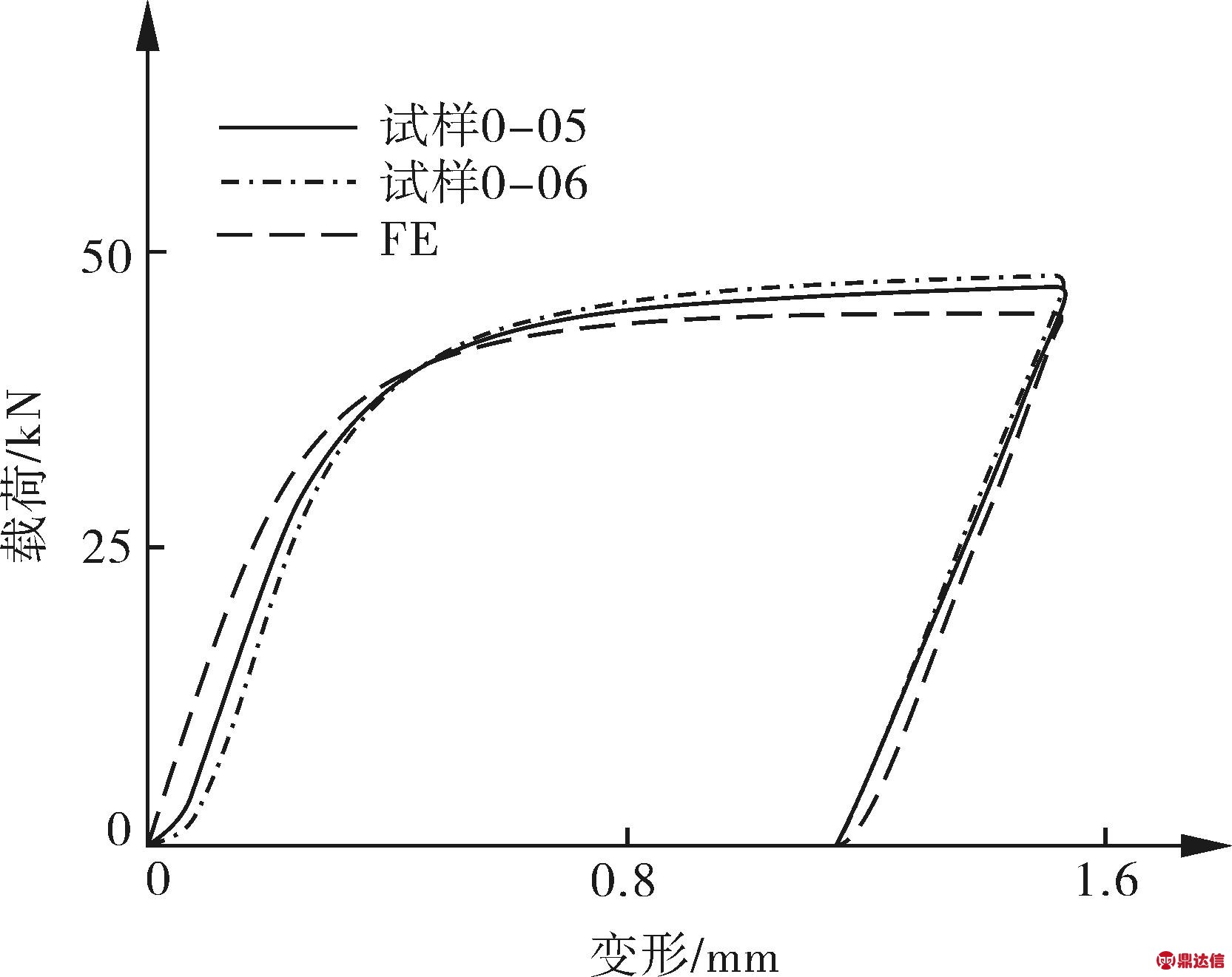
(c) λ=12%
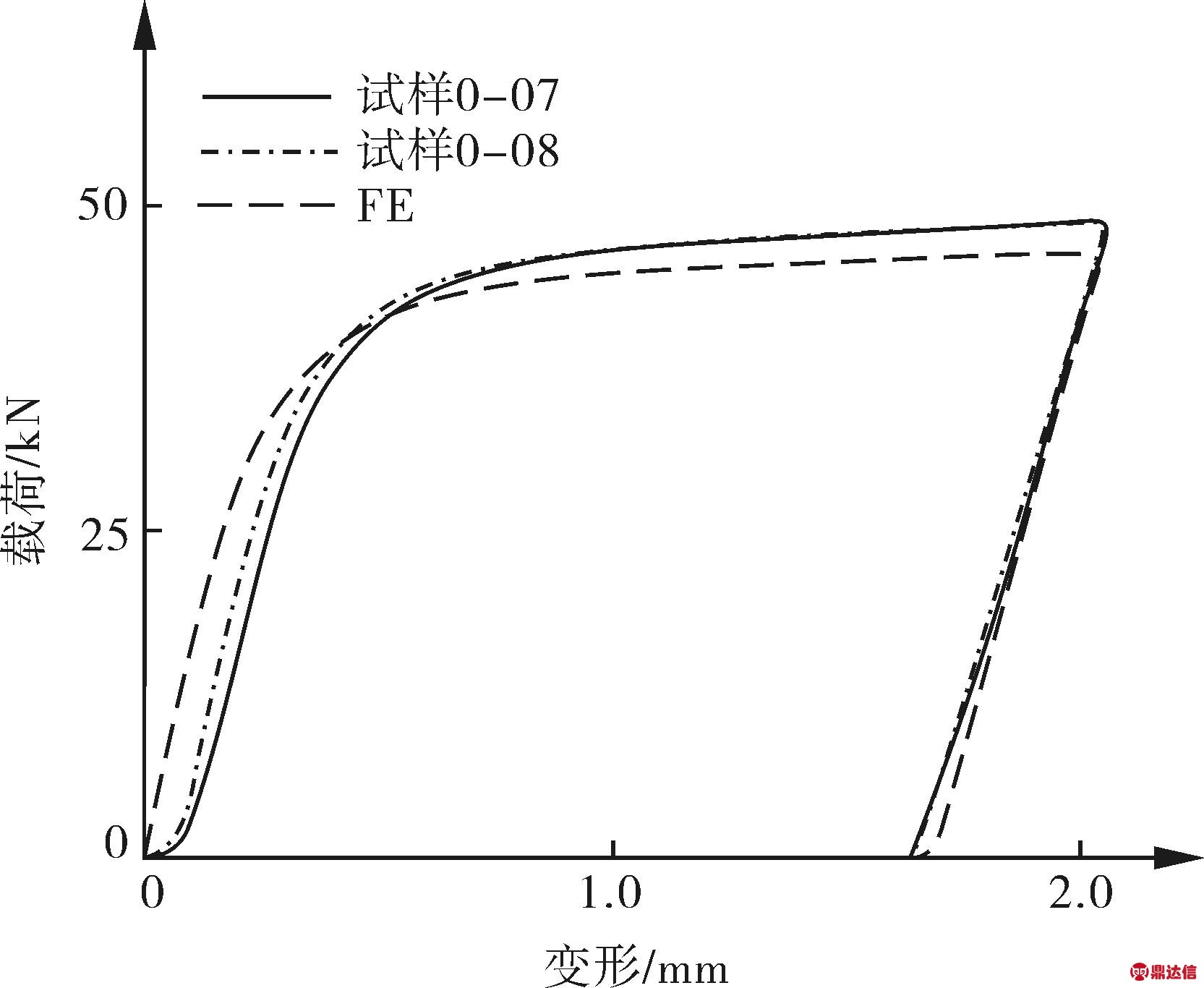
(d) λ=16%
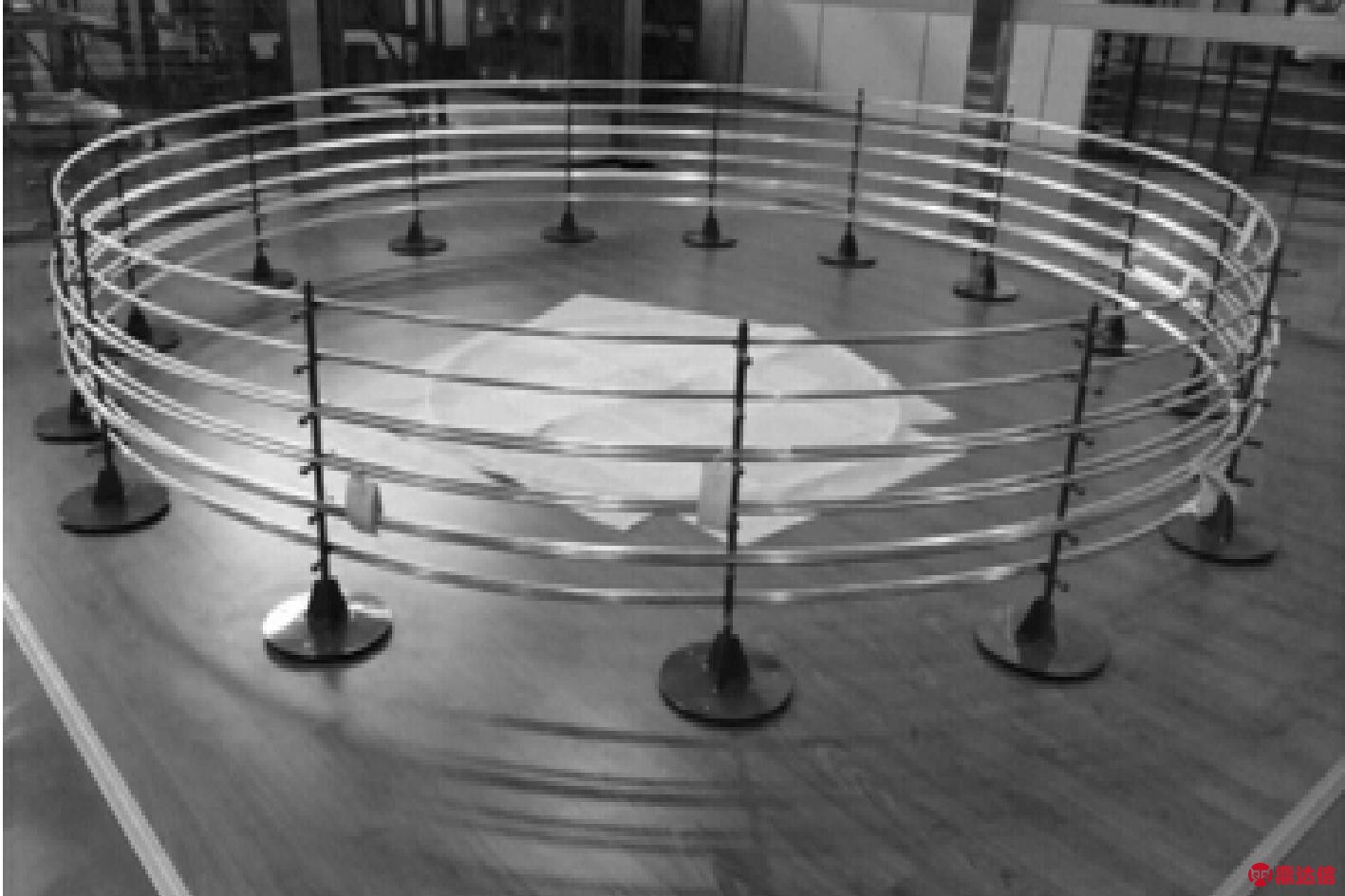
(e) λ=20%
图5 Inconel 718管材压缩和回弹关系
表5 Inconel 718管材的压缩回弹试验数据
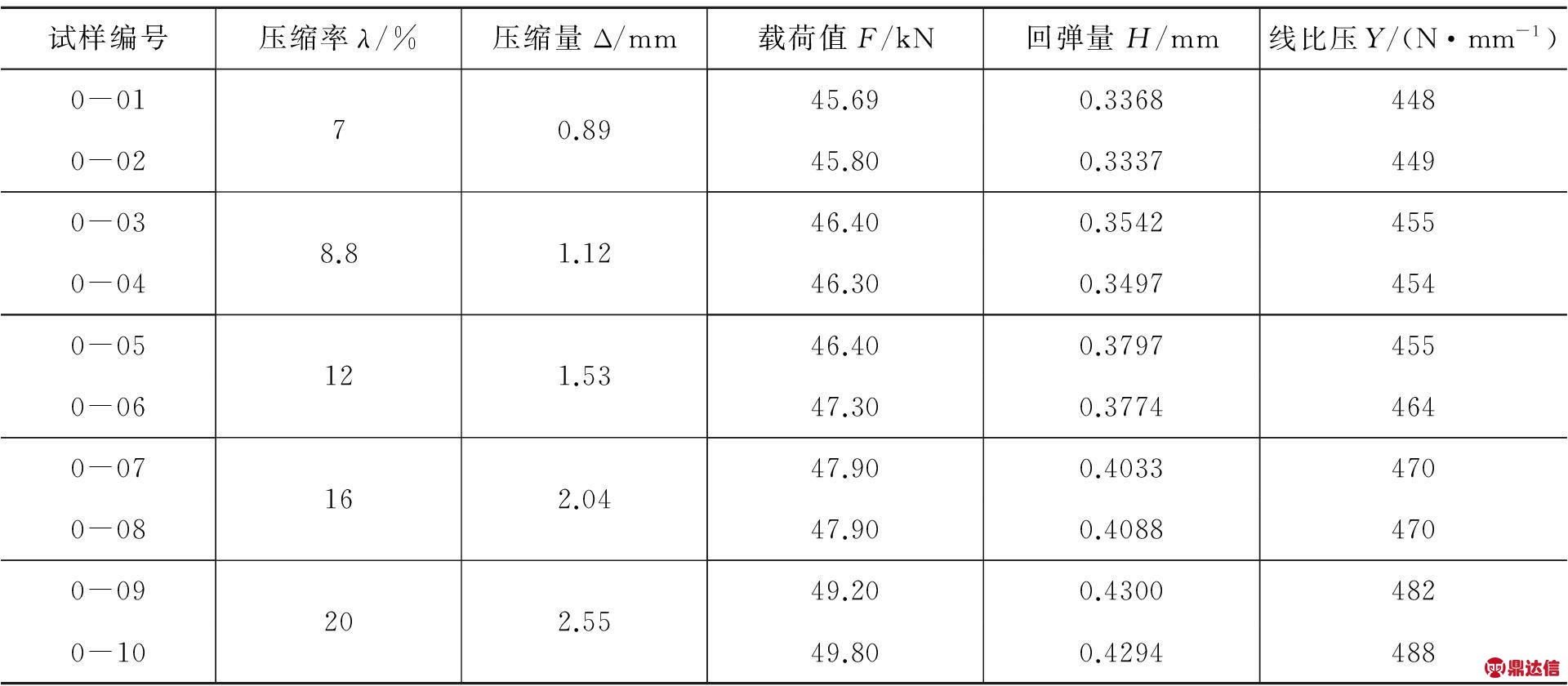
选用ABAQUS有限元分析软件对Inconel 718直管压缩进行结构建模、网格划分和数值计算[9-10] 。
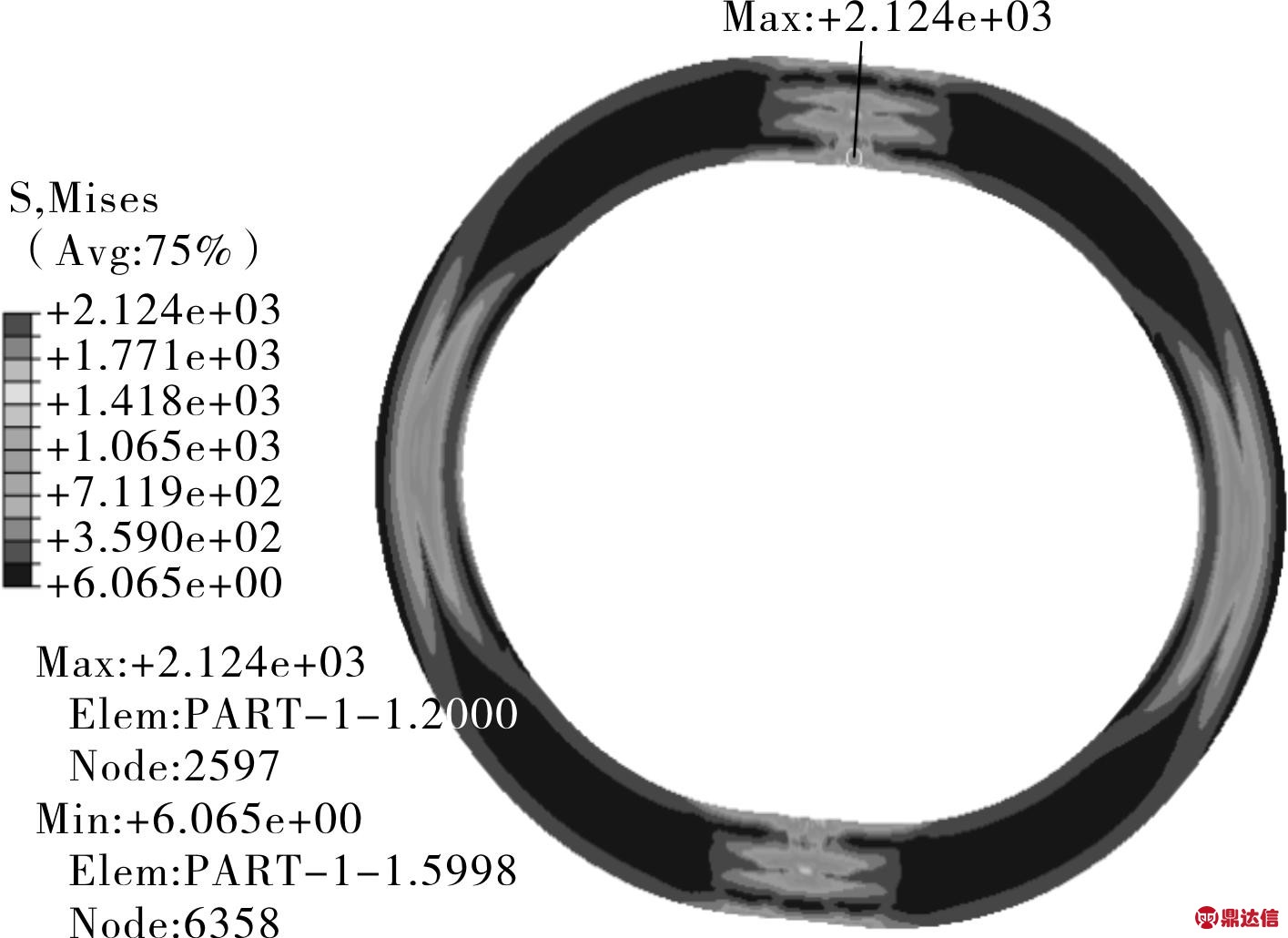
图6 压缩率16%的管材Mises应力云图
图6示出压缩率为16%的Mises应力云图。有限元(FE)计算结果与试验的比较如图5(d)所示。从图中可以看出,有限元模拟与试验曲线最大误差不超过5%。
通过以上对管材化学和物理性能的检测和压缩回弹试验以及数值分析表明:国产Inconel 718管材的综合性能满足设计要求,且管材外径在12.75~12.78 mm之间,直径偏差只有0.03 mm,用于制造反应堆压力容器O形密封环,实现了O形密封环原材料的国产化。
4 O形密封环研制和性能试验
4.1 制造工艺开发
对于O形密封环,国内无可借鉴的制造技术,无成熟的生产工艺,无可参照的专业设备。为此,针对O形密封环的特殊技术要求,从O形密封环下料、开孔、成型、切断、焊接、镀银、检验等整个生产链(见图7),自主开发相应工艺和研制专用装备。图8为生产的O形密封环产品。
图7 O形密封环的生产工艺流程图
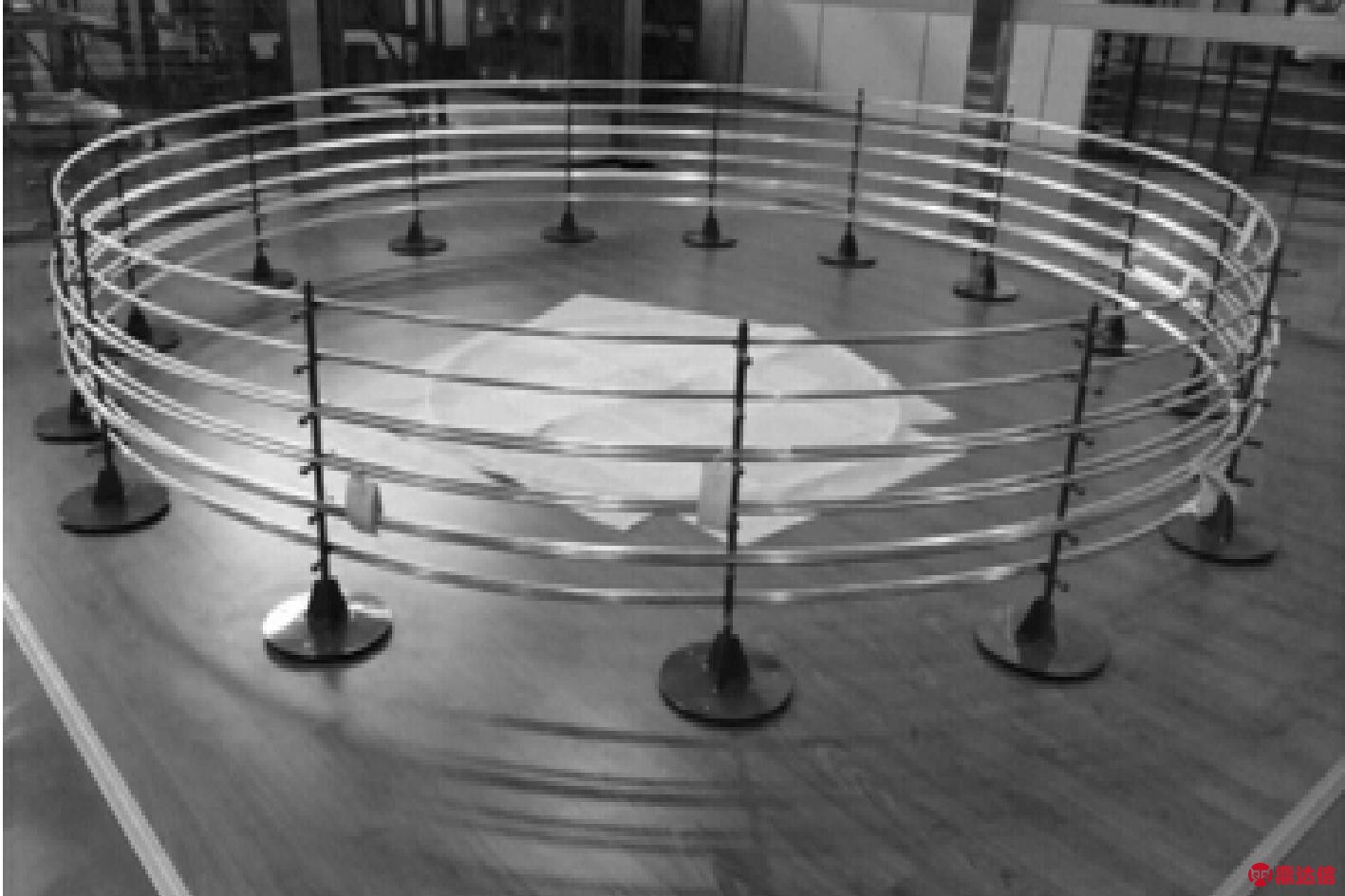
图8 O形密封环产品
4.1.1 成形
O形密封环直径在3000~4000 mm以上,且尺寸精度要求极高,允许直径上偏差为0,而下偏差不大于-0.25 mm,自重状态下的平面度要求小于2 mm。因此,精确控制O形环弯曲成型尺寸,尤其是采用先开槽孔的工艺,虽然解决了减少后续工序清除残留物的困难,但也增加了对槽孔间距和中心精确定位的难度(槽孔中心线沿内径圆周方向在±0.25 mm之内,与管子中心线的对中偏差不大于0.25 mm)。基于生产工艺的创新和C形密封环的制造经验[11],以及自主开发的多滚成型机和圆弧切断机,解决了不同规格O形环精确成型的技术关键。
4.1.2 焊接和热处理
首先,由于管材供货长度一般不大于8000 mm,对于大直径O形密封环需要由两个以上管段拼焊而成(每个O形密封环最多允许有3个焊接接头)。为了满足管段焊接后同轴度及成品环平面度要求,任意两个管段焊接后外表面的错边量必须小于0.050 mm,在焊缝打磨后两管段端口外径的减小量必须小于0.100 mm,且焊缝的内凸起量必须小于0.30 mm,以保证两管段连接处的平滑过渡。其次,由于O形密封环为镍基合金材料,并焊后需要对焊缝进行时效处理,因此,对管段焊接前对口、切断和平口,以及焊后时效处理提出了特殊的要求。但目前国内对该材料和产品的焊接及其设备尚不成熟。在引进圆管专用焊接机的基础上,采用不填丝TIG自熔焊接,并专门设计了圆弧切断、平口工装,经过大量的焊接工艺试验,改进焊接设备和工艺、优选时效处理参数,最终解决了O形密封环高精密焊接的关键技术。O形密封环焊缝经室温和高温拉伸测试、射线照相检测、液体渗透检测和晶间腐蚀检测,焊缝金属、基体金属和热影响区的各项技术指标均达到设计要求。
4.1.3 镀银
改变传统电镀方法,采用多槽整体电镀工艺,镀银过程中不加光亮剂、催化剂等,采用专门的环孔密封技术,开发专用大直径镀银设备,确保对O形密封环表面进行均匀镀银,镀银层沿周向精确控制在0.15~0.22 mm厚度范围内。镀银后的O形密封环表面光滑(Ra0.2 μm),银层致密,无气泡、深坑、银瘤等缺陷。对镀银后的O形密封环取样段进行烘烤检验,即在温度为150~200 ℃,烘烤30 min,用4倍放大镜检查,镀银层未出现起泡、开裂和脱皮现象,与基体结合良好。
4.2 性能试验
4.2.1 技术参数
O形密封环的密封作用基于预先压缩金属环管到一定深度的沟槽中,金属环管发生弹性变形,其反作用力对密封面产生较高的线接触载荷,而镀银层发生塑性变形,填补环管表面的微小凹凸不平,从而建立起初始密封。当施加操作压力时,由于O形密封环具有较高的回弹能力,密封线上仍保持较高的密封载荷。因此,对研制的O形密封环需要专门设计各种试验台架和装置,进行多项性能试验,以考核其能否达到设计的密封性能。
4.2.2 试验内容
(1)压缩回弹试验:测定压缩率分别为7%,8.8%,12%,16%和20%下的室温压缩回弹性能,包括有效回弹量和总回弹量。
(2)泄漏率试验:测定压缩率分别为7%,8.8%,12%,16%和20%下的室温氦气泄漏率(ΔP=1 bar)。
(3)水压试验:水压试验压力为22.9 MPa(绝对),保压时间≥30 min。
(4)冷热态交变试验,包括冷态水压试验和冷热态交变试验,模拟核电站主回路工况,进行升压升温、保温保压和降温降压的循环试验。
以上试验分别采用了规格为φ650(φ535.5) mm×φ13.1 mm的试样环,与O形密封环实物的比例约为1∶6~1∶7。
4.2.3 压缩回弹试验
表6列出试验环(φ650 mm×φ13.1 mm)压缩率分别为7%,8.8%,12%,16%的常温压缩回弹试验结果。
表6 O形密封环压缩回弹试验结果
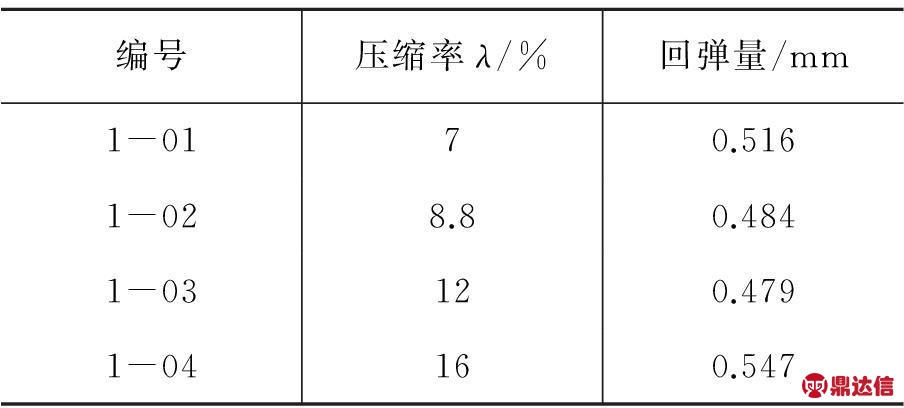
由表6可见,试验环压缩率为8.8%时,回弹量>0.33 mm;压缩率为16%时,回弹量>0.38 mm,达到了设计技术要求。
4.2.4 泄漏率测试
图9示出规格φ650 mm×φ13.1 mm试验环在压缩率16%和室温下的载荷—泄漏率—时间关系曲线,图中显示了加载-保压(初始密封载荷)-加载-保压(达到压缩率的载荷)-卸载试验过程中,用氦质谱检漏仪测得的氦气泄漏率。表7为压缩率8.8%,16%的测试结果。
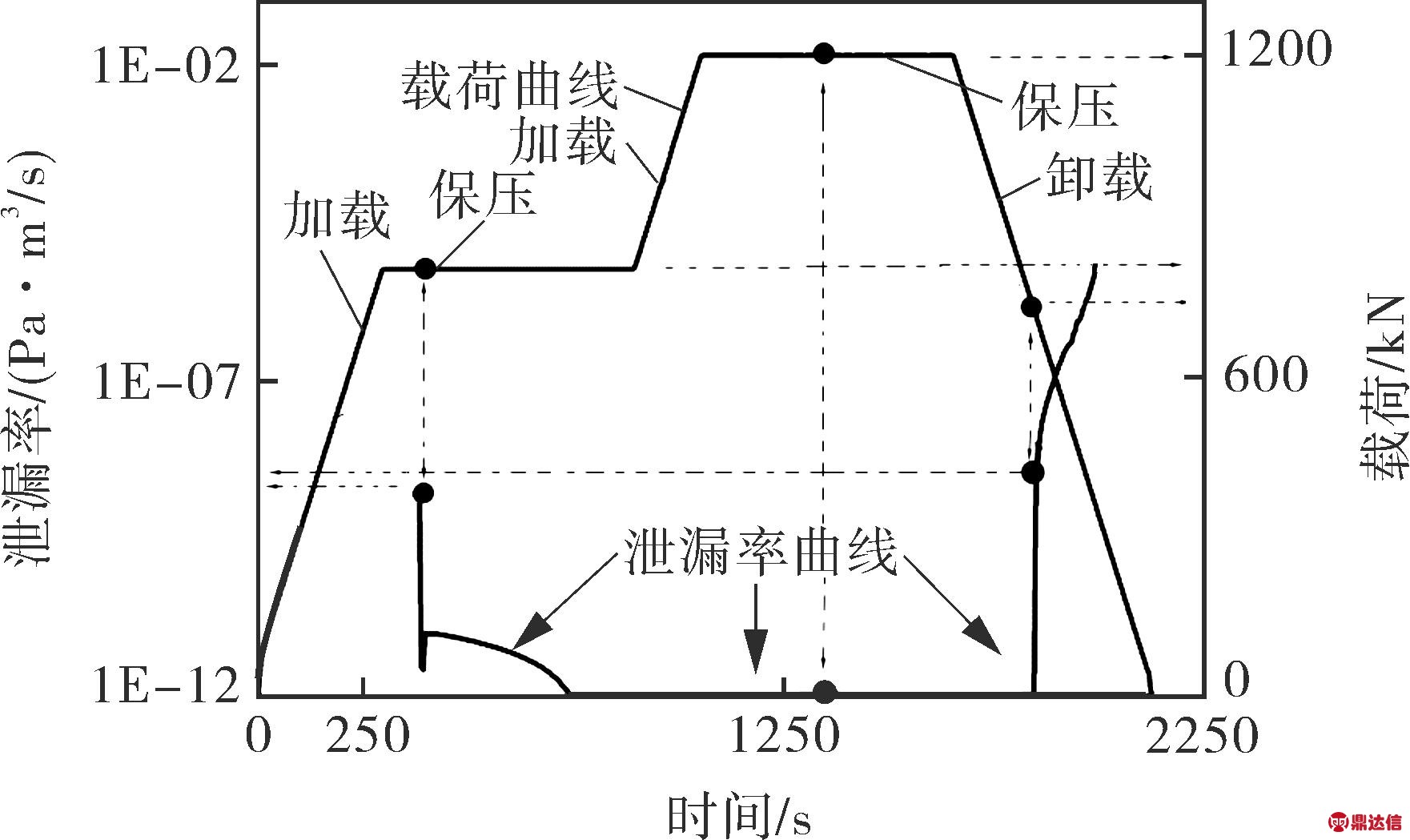
图9 O形密封环泄漏率测试曲线(λ=16%)
表7 O形密封环泄漏率测试结果

由图9和表7可以看出,对于压缩率为16%的试样环,初始密封载荷800 kN时,达到1.3×10-9 Pa·m3/s 以下的泄漏率;16%压缩率的载荷为1200 kN(线密封载荷600 N/mm),此时泄漏率降低到1.1×10-12 Pa·m3/s ;卸载至713 kN时,泄漏率上升到2.3×10-9 Pa·m3/s,则认定密封失效。
4.2.5 水压试验
水压试验压力为22.8 MPa,压缩载荷为7300 kN,保压时间>30 min,试验环的规格为φ535.5 mm×φ13.1 mm。试验结果表明:密封面无泄漏发生;试验完成后,表面镀银层无脱皮、折迭、起皱等缺陷,O形密封环无任何损坏。
4.2.6 冷热态循环试验
冷热循环试验采用规格φ535.5 mm×φ13.1 mm的试验环,进行了升压升温、保温保压和降温降压的循环过程,即升压至15.5 MPa(绝对),升温至350 ℃,保压保温时间30 min,冷却到小于90 ℃。试验平均升温速率>77 ℃/h,试验降温平均速率>85 ℃/h,循环次数20次,试验过程中试验系统装置运行稳定,目视检查密封面未发生任何泄漏或异常情况,试验后O形密封环表面良好,镀银层未出现折皱、起皮等现象。图10示出冷热态循环试验装置。
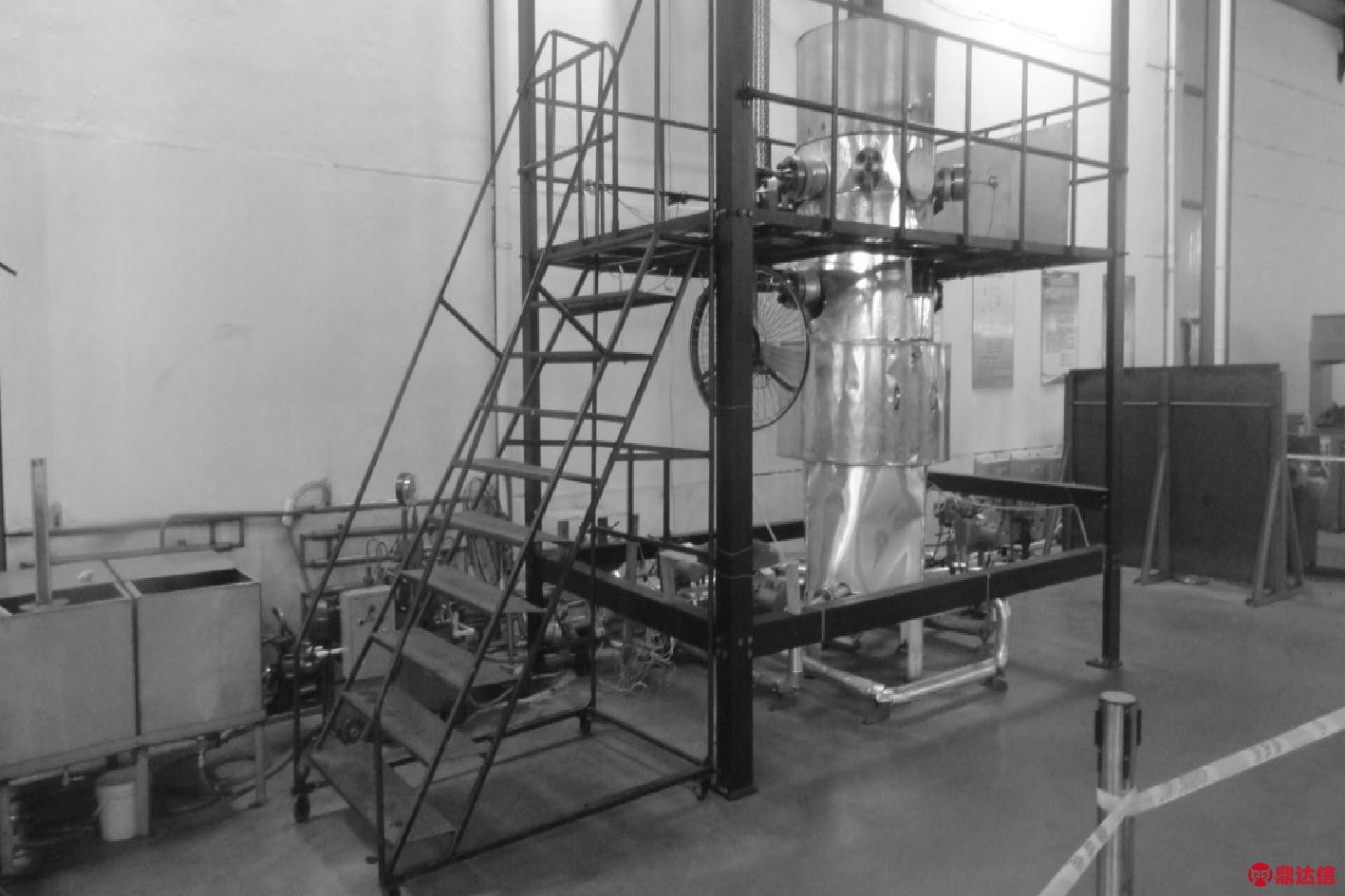
(a)
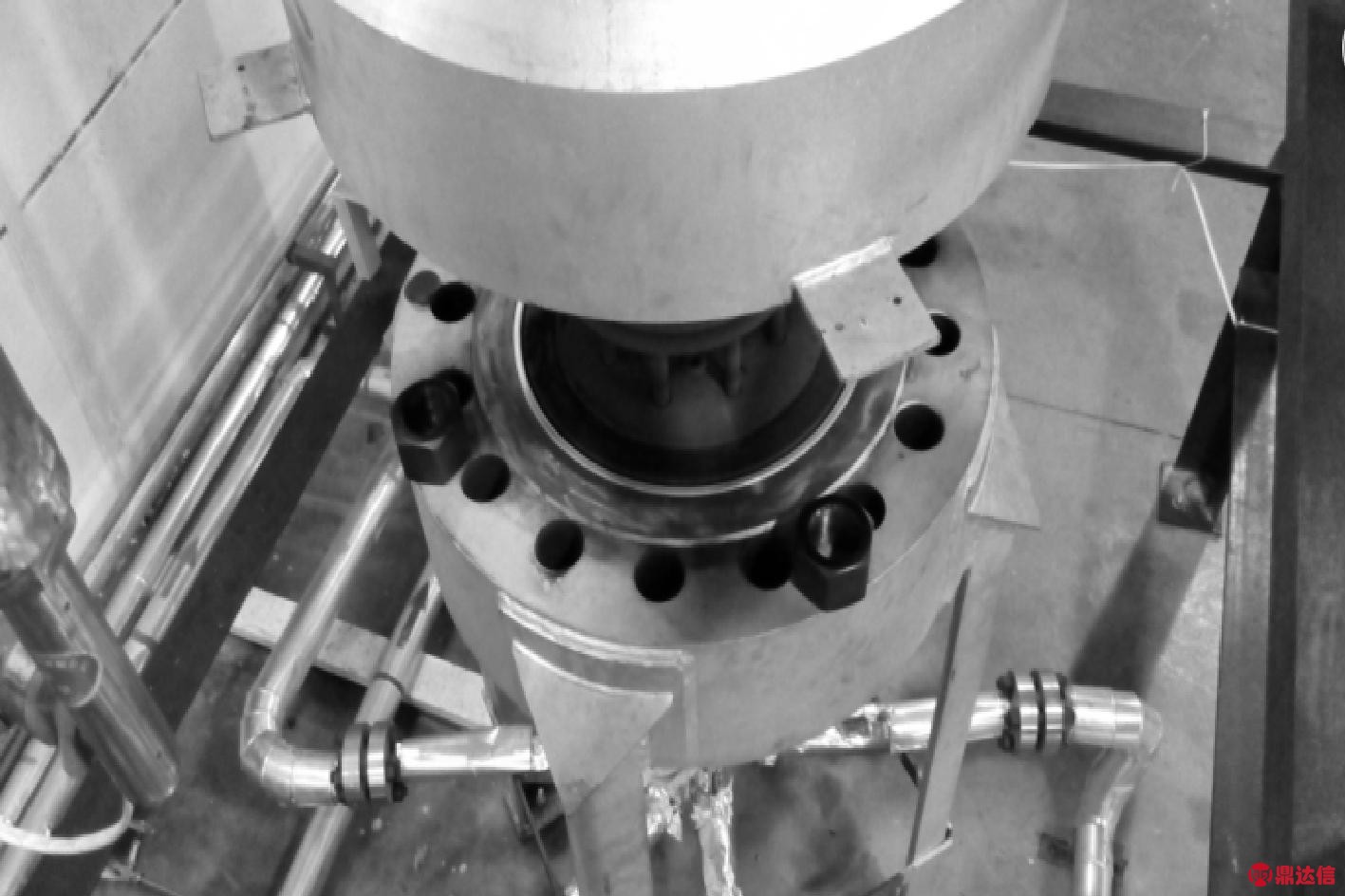
(b)
图10 冷热态循环试验装置
5 结语
(1)对反应堆压力容器用金属O形密封环,从原材料到产品,从工艺到设备,从数值分析到性能试验,进行了成套技术的研究和开发,解决了多项关键制造技术问题,研制的O形密封环的原材料、尺寸、性能均达到了设计规定的技术要求。
(2)生产的O形密封环,拥有完全的自主知识产权,填补了国内空白,突破了国外技术封锁和垄断,并已商用于国内300 MW反应堆压力容器,实现了核电站核心设备关键密封件的国产化,保障了国家的能源安全。