摘 要:为解决目前页岩气井、深井油气勘探开发中广泛存在的环空带压问题,结合理论研究成果及实验室模拟结果,分析得出了目前在“深层、低渗透、非常规”油气资源勘探开发过程中,大压差条件是造成水泥环密封完整性失效主要原因的认识。通过对四川盆地页岩气井、安岳气田和塔里木盆地库车山前等区块高温高压深井在钻井、压裂、生产过程中大压差工况进行梳理和定量计算,运用计算结果解释了上述两个地区气井在大压差条件下水泥环密封完 整性失效的原因:加载阶段水泥环周向出现的拉应力、加载—卸载工况使水泥环产生塑性变形、在卸载过程中界面产生拉应力等,造成水泥环拉伸破坏及界面微环隙,从而破坏密封完整性。归纳总结了井筒全生命周期各环节出现密封完整性失效的风险,初步提出了大压差条件下保障水泥环密封完整性的应对措施:①提升水泥石抗变形能力;②提高第一界面及第二界面胶结力;③提高界面接触力。
关键词:大压差 水泥环 密封完整性 微环隙 页岩气 深层油气 四川盆地 塔里木盆地
0 引言
近年来,随着勘探开发进程不断深入,新的油气资源主要集中在“深层、低渗透、海洋、非常规”等领域。为了提高资源动用率,高能量储层改造成为“深、低、非”的必须技术,同时海上面临高昂的作业成本,也需要进行储层改造。高能量储层改造等新技术的应用,在提高产量的同时,也使水泥环受力环境变得更加复杂。
在低渗透、非常规等油气资源开采过程中,水力压裂是常用的增产手段。压裂时在井口施加高压,压裂后井口压力将大幅降低,而在分段压裂过程中,井筒将反复承受这一压力加载—卸载的循环作用。在深层油气井勘探开发不同阶段(如钻井、压裂、试采、生产等),井筒内流体(钻井液、压裂液、保护液等)密度变化,由于井深较深,将造成井筒内液柱压力大幅变化。这些工况下,保障水泥环密封完整性面临新的挑战。
要分析上述复杂油气资源开发过程中的水泥环完整性问题,首先需要了解这些复杂工况条件下水泥环失效机理。早期研究主要集中于高应力下水泥环应力分布及由此造成的水泥环本体破坏[1-8],从20世纪90年代开始,一系列实验及研究认为[9-16],在固井后的生产过程中(如油气井试压、页岩气井压裂等),套管内压力(下称内压)变化亦可导致在第一界面(水泥环—套管界面)或第二界面(水泥环—围岩界面)产生环空微间隙(下称微环隙),从而造成水泥环密封完整性失效,且内压变化越大,这一效应越明显。上述研究可以归结为两种类型:一种是井筒内压力升高导致水泥环本体破坏,另一种是井筒内压力先升高、后下降,导致微环隙。本文将上述工况统称为大压差工况,即环空内水泥固化之后,井口压力、井筒内流体密度等发生变化,导致井筒内应力大幅变化,其中,既包括井筒内压力升高的过程,也包括压力降低的过程。
随着深层油气井占比逐年增多、水力压裂技术不断推广,大压差工况越来越普遍,且差值相比过去大幅上升。在四川安岳、塔里木深层气井,钻井及生产过程中,由于流体密度变化,套管内液柱压力变化值可达50 MPa以上;在四川页岩气示范区,压裂施工造成的井筒内压差可达90 MPa以上。这些工况下,水泥环能否保持其密封完整性,以及如何保障水泥环的密封完整性,目前仍缺少统一的认识。针对上述问题,本文首先对大压差条件下水泥环密封完整性失效机理进行阐述,然后结合四川盆地页岩气示范区及安岳气田、塔里木盆地克深等地区的现场数据,对这些区块在钻井、生产等过程中大压差工况进行梳理,并分析大压差作用下水泥环密封失效风险,研究成果对深层、低渗透、非常规油气资源勘探开发中水泥环密封完整性设计及未来的研究工作具有指导意义。
1 大压差条件下水泥环密封完整性失效机理研究
Jackson等[9]和Goodwin等[10]在实验室进行了相似的大压差条件下水泥环密封完整性失效的模拟实验,其中,Jackson等将Ø127.0 mm套管置于Ø177.8 mm套管中,在两个套管之间充满G级水泥并养护69 h。之后在Ø127.0 mm套管内进行加压—卸压循环,将内压分别加载至14 MPa、28 MPa、41 MPa、55 MPa、69 MPa,保持一段时间后卸载,在这一过程中,水泥环下端连接0.69 MPa的气源,监测组合体的气窜速度,从而判断系统是否发生密封失效。试验结果表明,在套管内压力升高过程中,未检测到环间气窜,说明内压的加载未导致组合体密封失效;当套管内压升高至55 MPa和69 MPa,然后分别卸载至1.4 MPa和3.3 MPa时,检测到明显气窜,说明此时系统密封失效。Goodwin等实验过程类似,且观测到水泥环径向裂缝及套管—水泥环界面微环隙。上述室内实验,虽然不能完全模拟井下工况,但是揭示了大压差条件下几种可能的水泥环密封完整性失效形式,同时为水泥环应力失效问题的研究,尤其是理论模型的建立,提供了验证的途径。本节分别采用弹性模型(水泥环、套管均为弹性体)及考虑水泥环塑性变形的弹塑性模型对Jackson等的实验进行模拟,阐释大压差条件下水泥环密封完整性失效可能的形式及机理,并通过与实验结果的对比,对两种模型适用性进行了比较。
1.1 弹性模型分析:水泥环有剪切和拉伸破坏风险
一般认为,水泥环密封失效发生于内压峰值处,即水泥环因受力发生拉伸或剪切破坏。此处采用平面应变假设,并认为水泥环、套管均为弹性体,计算内压为69 MPa时组合体应力分布,计算参数如表1所示。图1为计算结果,图1中拉应力为正,压应力为负,下文采用相同约定。
由图1可以看出,水泥环径向受压,周向受拉。对水泥环破坏的判定,常采用Mohr-Coulomb准则结合最大拉应力准则[17]。对水泥环,Mohr-Coulomb准则有如下形式[18]:
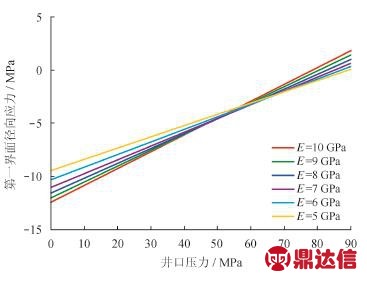
式中σrr表示水泥环径向应力;σθθ表示水泥环周向应力,C表示内聚力;φ表示内摩擦角,参数A用于区分最大、最小主应力,当σθθ>σrr时,A=1,当σθθ≤σrr时,A=-1;F表示水泥环摩尔—库伦判定系数,当F值为正时,水泥环将发生剪切破坏。
取水泥石内摩擦角30°,内聚力11.54 MPa(对应单轴抗压强度40 MPa),则水泥环摩尔—库伦判定系数F值如图1-a所示,水泥环内侧(半径介于63.5~68.9 mm)F值为正,有发生剪切破坏的风险。同时,水泥环在周向上存在拉应力(图1-b),范围为3.77 MPa(水泥环外侧)至-8.93 MPa(水泥环内侧),由于水泥抗拉强度较低(一般为抗压强度的1/20~1/10),水泥环也可能发生拉伸破坏。
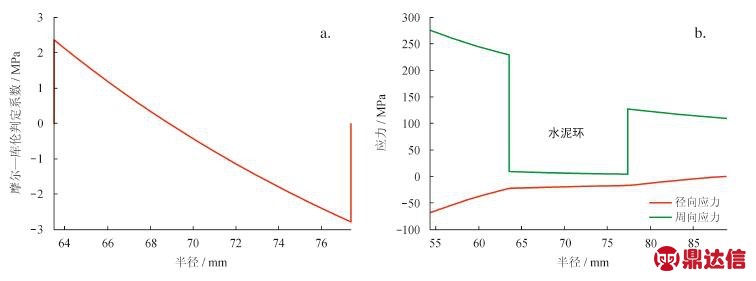
图1 内压为69 MPa时F值及组合体径向与周向应力图
1.2 弹塑性模型分析
采用弹性模型计算时,预测的水泥环破坏形式为剪切和拉伸破坏,且水泥环破坏发生在内压较高时,与实验观测结果不完全一致。首先,实验中,观测到水泥环径向裂缝(拉伸破坏)及套管—水泥环界面处出现裂缝(微环隙),未提及剪切破坏;其次,实验中,水泥环密封失效需要经历内压升高(加载过程)—降低(卸载过程)两个过程,且发生在卸载过程。这些现象难以用弹性力学模型进行解释。同时,水泥石三轴试验表明,随着围压的增加,塑性应变成为水泥石主要的力学特征,在一定的应变范围内(与围压及水泥体系有关,可达5%甚至更高),水泥石表现为剪切塑性屈服而非剪切破坏[19]。
针对以上这些问题,笔者建立了考虑水泥环塑性特征及界面胶结强度的套管—水泥环—地层组合体力学模型[18],模型考虑了加载阶段水泥环的塑性变形积累,以及卸载阶段微环隙的发展。本节介绍采用此模型对Jackson等实验进行模拟,计算内压从0加载至69 MPa(加载过程),再从69 MPa卸载至0(卸载过程)过程中,组合体的受力及变形,解释大压差作用造成微环隙的原因,详细推导及模拟过程可见本文参考文献[18]。下述分析采用如下假设及约定:①组合体为平面应变模型;②套管、地层为弹性体,水泥环为理想弹塑性体,发生剪切屈服时遵循Mohr-Coulomb准则,取水泥石内摩擦角30°,内聚力5.77 MPa(对应屈服强度20 MPa)。
表1 Jackson实验组合体尺寸及力学参数表
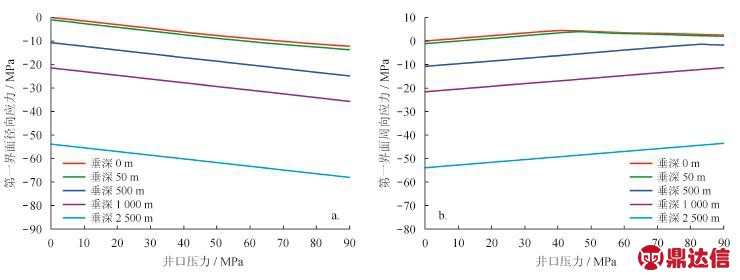
1.2.1 加载过程:水泥环发生塑性变形
内压从0加载至69 MPa的过程中,水泥环和内侧套管界面(第一界面)、水泥环和外侧套管界面(第二界面)的接触力始终为压应力(图2-a),最大值为21.0 MPa。这意味着加载过程中,套管、水泥环以及围岩之间始终受到相互挤压的作用,不会产生微环隙,即使界面由于胶结质量差等因素存在周向裂纹,也不会扩展。
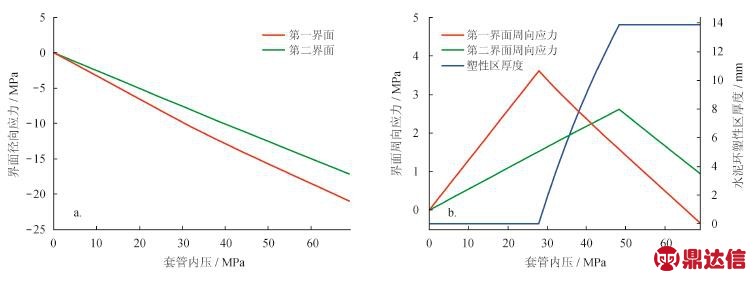
图2 加载阶段界面应力大小及水泥环塑性区厚度图
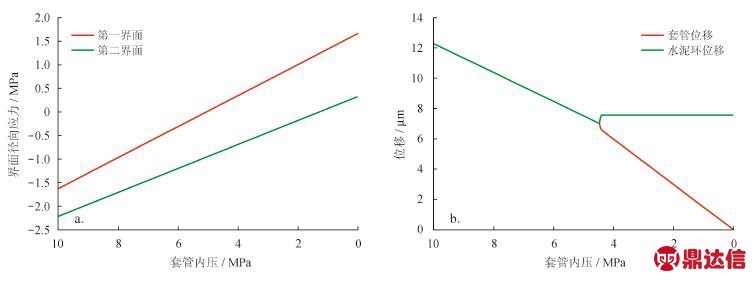
图3 卸载时界面径向应力及第一界面微环隙图
随着内压升高,水泥环将从内边界开始发生塑性屈服,图2-b中蓝线为发生塑性屈服的水泥环厚度。在内压从0加载至27.9 MPa的阶段,水泥环完全处于弹性状态(塑性区厚度为0 mm);当内压超过27.9 MPa时,水泥环从内边界开始开始进入塑性区,随着套管内压的增加,水泥环进入塑性区的范围也逐渐增大;当内压升高至48.3 MPa时,水泥环完全进入屈服状态。图2-b中红线和绿线为第一界面和第二界面周向应力,在水泥环发生塑性屈服以前,界面周向拉力随套管内压力升高不断上升,在水泥环内壁屈服后(内压27.9 MPa),第一界面周向拉力随内压升高而降低,第二界面周向拉力继续上升,在水泥环整体屈服后(内压48.3 MPa),第二界面周向拉力也随内压升高而降低。水泥环周向拉力最高值出现在水泥环屈服之前,第一界面拉力最大为3.60 MPa,第二界面拉力最大为2.61 MPa,如前文所述,由于水泥石抗拉强度较低,在加载过程中,水泥环有出现拉伸破坏的风险。在套管内压力达到峰值69 MPa时,水泥环拉应力低于最高值,其中第二界面拉应力为0.93 MPa,第一界面周向拉应力甚至为负值(-0.34 MPa),即水泥环周向受压。和1.1节弹性模型结果相比,考虑水泥环塑性屈服时,水泥环周向拉应力峰值有所降低,且随着水泥环发生屈服,周向拉应力将减少,甚至转为压应力。
1.2.2 卸载过程:界面受拉,产生微环隙
当水泥环在加载阶段发生塑性变形时,在卸载阶段,水泥环存在不可恢复的残余变形,而套管产生的弹性形变可以完全恢复,因而将在界面处产生拉应力,当拉应力超过界面胶结强度时,将产生微环隙。此处以内压从69 MPa卸载时为例,介绍微环隙产生的过程(图3-a)。卸载过程中,第一界面和第二界面径向应力均随内压的降低而逐渐升高,当套管内压力大于5.1 MPa时,二者均为压应力,不会发生界面脱离;随着内压的进一步降低,两个界面的接触力均由压力转变为拉力,当内压卸载到0 MPa时,第一界面处将产生1.66 MPa的拉应力,若界面胶结强度小于该值,则有产生微环隙的风险。
设第一界面、第二界面胶结力均为0.2 MPa,图3-b为套管外边界径向位移(uso)及水泥环内边界径向位移(uci)随套管内压力变化的曲线,曲线的间距即为微环隙大小。在卸载的初期,uci和uso以相同的速率减小,说明此时水泥环与套管一同收缩,不产生微环隙。压力降到4.5 MPa时,界面拉力超过胶结强度,界面被拉开,套管与水泥环发生分离,此后套管随内压降低继续收缩,而水泥环不再收缩,微环隙不断发展,系统将失去密封能力。在实验中,当内压卸载至3.3 MPa时,检测到系统发生气窜,与模拟结果趋势一致。
由上述模拟可以发现,弹塑性模型由于可以更准确描述水泥石力学特性,相比采用弹性模型,分析结果与实验结果更加接近,主要表现在以下几个方面。
1)在加载阶段(图2),随着套管内压力增加,水泥环周向受拉,因此可能从内边界开始出现径向裂缝(拉伸破坏),但随着水泥环发生塑性屈服,拉应力将减小甚至转为抗压,因此,裂缝不会继续扩展,而是将逐渐处于闭合状态。这从一定程度上可以解释实验中观测到径向裂纹(拉伸破坏),但在加载阶段未检测到环空气窜的现象。
2)弹塑性模型可以计算微环隙的产生及发展过程。微环隙的产生需经历加载和卸载两个过程,加载过程中,水泥环将产生塑性变形,但不会出现微环隙;由于水泥环塑性变形不可恢复,卸载时将出现界面受拉,从而产生微环隙。这一结果与实验中观测到周向裂缝(微环隙),且气窜发生在卸载阶段的现象更加吻合。
本节通过模拟室内实验,阐释了大压差条件下水泥环密封完整性失效形式及机理。在现场实际问题中,由于工况不同,水泥环密封完整性失效的形式及原因也将更加复杂和多样化,下文中将结合页岩气、深层气井现场数据,对大压差条件下水泥环密封完整性失效风险进行分析。
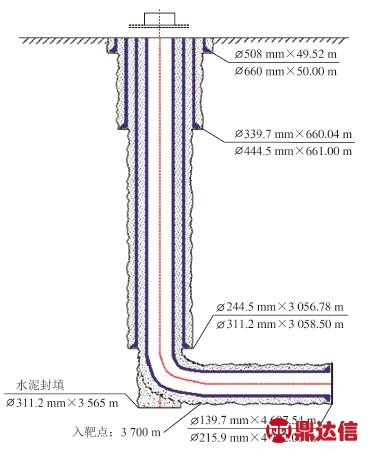
图4 页岩气示范区某井井身结构示意图[20]
2 页岩气井大压差条件下水泥环密封完整性问题分析
在页岩气、致密油气等资源开采过程中,分段压裂是常见的储层改造手段。压裂过程中,水泥环承受反复的压差作用,这一工况下,水泥环能否保证其完整性,是实现长期安全生产的重要环节。鉴于页岩气、致密油气井开发方式类似,本文以四川盆地威远—长宁页岩气示范区某井为例,分析分段压裂过程中大压差作用下可能出现的密封完整性失效风险,并提出对应的解决思路。采用现场数据进行分析,页岩气示范区一种井身结构示意图如图4所示[20],该井采用此类井身结构设计,Ø139.7 mm套管壁厚12.34 mm,水平段垂深2 500 m,压裂施工参数如表2所示。
表2 页岩气示范区某井压裂施工及材料参数表

2.1 不发生失重情况下的水泥环密封完整性分析
采用与1.2节同样的弹塑性模型,假设水泥环居中且完整填充环空空间,并忽略技术套管及表层套管的影响。在注水泥施工完成时,环空内水泥为浆体状态,受自身重力的作用,假设水泥环候凝过程中受力状态不发生变化,则在压裂施工前,水泥环受力状态为σrr=σθθ=-ρcgh,其中,σrr为水泥环径向应力,σθθ为水泥环周向应力,ρc为水泥浆密度,h为垂深。
由1.2节可知,水泥环受力峰值出现在第一界面,此处重点分析第一界面处水泥环的受力状态。在井口压力从0 MPa上升到90 MPa过程中,不同深度处,第一界面处水泥环周向及径向受力如图5所示。从图5可以看出,水泥环在径向受压,且随着垂深的增加,径向压力也增加;周向上,井口处(垂深0 m),水泥环受拉,最高为4.56 MPa,随着垂深的增加,周向应力逐渐转为受压。
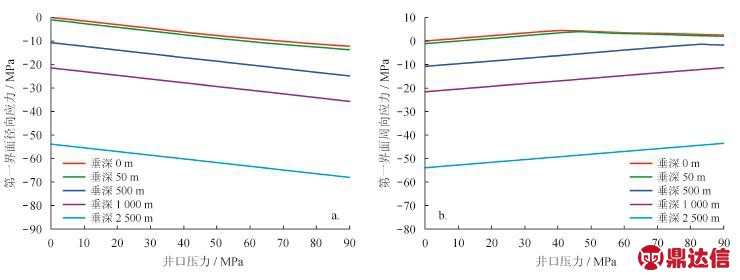
图5 加载过程第一界面处水泥环径向应力与周向应力图
图6 为加载过程水泥环塑性区厚度,在垂深0 m处,水泥环在井口压力达到39.87 MPa时,由内边界(第一界面处)开始发生塑性屈服,在井口压力达到90 MPa时,水泥环半径69.85 mm到98.40 mm范围发生塑性屈服,塑性区厚度达到28.55 mm。随着垂深的增加,加载过程中发生塑性屈服的水泥环范围减少,垂深为500 m处,仅有2.68 mm的水泥环发生塑性屈服,垂深在1 000 m处,水泥环在整个加载过程中不发生屈服。
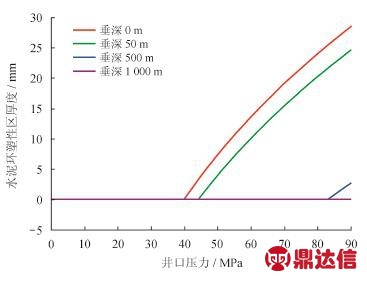
图6 加载过程水泥环塑性区厚度图
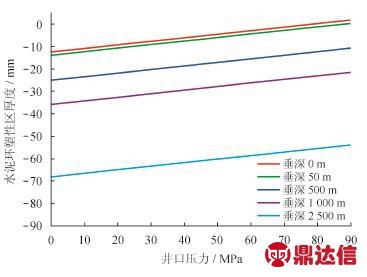
图7 卸载过程第一界面径向应力图
图7 为井口压力从90 MPa卸载至0 MPa时,水泥环在第一界面处的径向应力,在垂深0 m处,随着井口压力的降低,径向应力由受压转变为受拉,在井口压力降至0 MPa时,拉力达到1.82 MPa,垂深50 m处,最高拉力为0.41 MPa,垂深500 m以上,卸载过程径向始终为压应力。可以看出,在井口压力加载—卸载的一个周期中,水泥环密封完整性失效存在两种风险,在加载过程中,水泥环有受拉破坏的风险,在卸载过程中,有出现微环隙的风险。在不考虑水泥环候凝过程失重等因素的作用时,水泥环密封完整性失效主要发生在浅层(垂深0~50 m),随着深度的增加,由于重力的作用,水泥环径向、周向受压均增加,水泥环出现塑性屈服的范围逐渐减少,同时发生拉伸破坏及微环隙的风险也逐渐降低。
2.2 水泥浆发生失重时的水泥环密封完整性分析
在固井过程中,由于水泥浆的桥堵、失水、以及水泥水化、体积收缩等因素的作用,环空候凝水泥浆静液柱压力会随着水泥浆静胶凝强度的发展逐渐降低,即“失重”现象,严重时,水泥浆静液柱压力将降为零[14-15,21]。此处考虑失重的作用,取水泥浆静液柱压力降为零的情况,则在压裂施工前,水泥环受力状态为σrr=σθθ=0。设压裂液密度和候凝时套管内流体密度相同,且不考虑压裂时摩阻损失,则压裂过程中,不同深度处水泥环的受力相同。
在井口压力从0 MPa上升到90 MPa过程中,任意深度第一界面处水泥环周向及径向应力如图8所示,水泥环径向受压,周向受拉。周向拉应力最大为4.56 MPa,水泥环有发生拉伸破坏的风险。图9为加载过程水泥环塑性区厚度,图10为卸载过程第一界面径向应力,可以看出,水泥环在加载过程会发生塑性屈服,且在卸载过程第一界面出现径向拉应力,水泥环有出现微环隙的风险。由于此时不同深度处水泥环的受力相同,全井段水泥环均有发生拉伸破坏及出现微环隙的风险。可见,水泥浆的失重对水泥环密封完整性有不利影响,发生失重时,水泥环出现密封失效的范围由表层扩展至全井段。
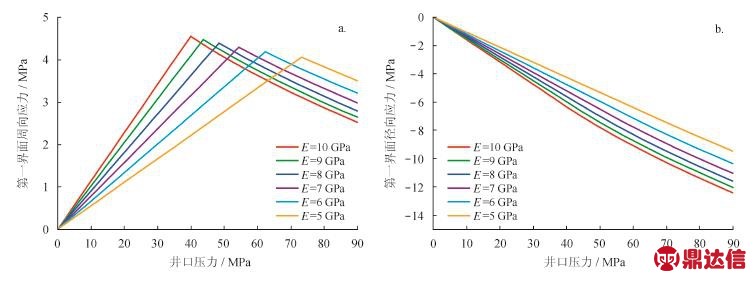
图8 失重条件下加载过程第一界面周向应力与径向应力图
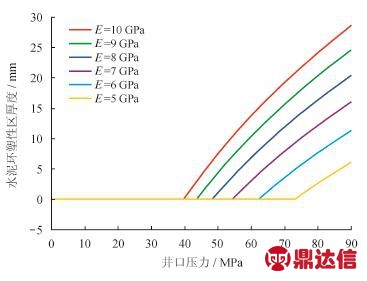
图9 失重条件下加载过程水泥环塑性区厚度图
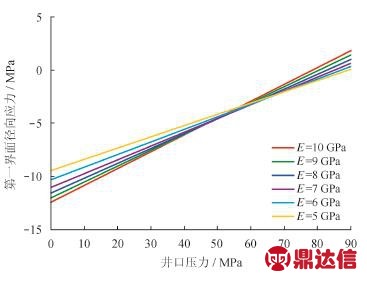
图10 失重条件下卸载过程第一界面径向应力图
水泥石弹性模量与水泥环受力大小有直接联系,是水泥石的重要力学性能参数。常规油井水泥养护7 d后,弹性模量约10 GPa,此后随时间增加还会略有升高,通过添加弹性改造材料等方法对水泥进行韧性改造,可将其弹性模量降至6 GPa甚至更低[22]。由图8~10可以看出,加载过程中,水泥石弹性模量越低,水泥环受力越小;在屈服强度相同的条件下,弹性模量越低,水泥环越不容易发生塑性屈服,水泥石弹性模量为10 GPa时,水泥环在井口压力39.87 MPa开始发生塑性屈服,最终发生塑性屈服的水泥环厚度为28.55 mm,而水泥石弹性模量为5 GPa时,水泥环在井口压力73.17 MPa开始发生塑性屈服,最终发生塑性屈服的水泥环厚度为6.12 mm(图9)。
对应地,水泥弹性模量越低,卸载后径向拉应力越小,水泥石弹性模量为10 GPa时,径向拉力为1.82 MPa,而水泥石弹性模量为5 GPa时,径向拉力为0.11 MPa(图10)。因此,降低水泥环弹性模量对于防止压裂过程中出现微环隙有积极意义。
上述分析可以看出,在压裂过程中,水泥环密封完整性失效可能包括两种形式:①高内压条件下水泥环可能出现周向受拉破坏,这将导致水泥环出现贯穿裂缝;②大压差条件下第一界面及第二界面出现微环隙。针对这些风险,降低水泥环弹性模量可有效减少水泥环受力,避免受拉破坏及微环隙的出现;同时,微环隙的出现与界面承受拉应力和界面胶结强度直接相关,提高界面接触力、提高界面胶结强度是避免微环隙出现的有效手段。
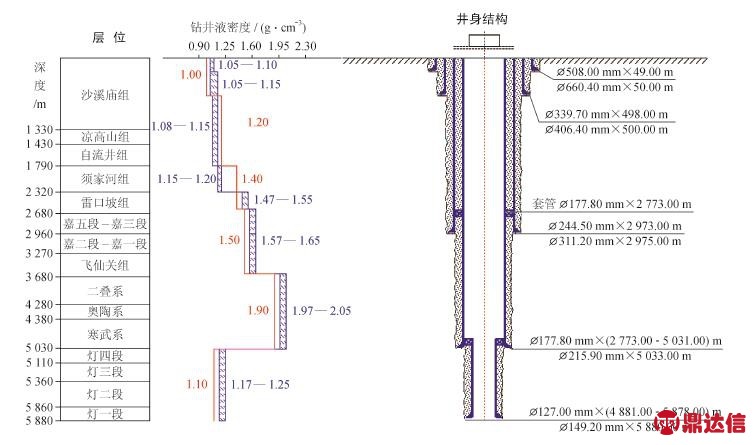
图11 磨溪—高石梯区块一种井身结构示意图[26]
3 深井大压差条件下水泥环密封完整性问题分析
3.1 安岳气田水泥环密封失效风险分析
安岳气田龙王庙组气藏是迄今我国发现的单体规模最大的碳酸盐岩整装气藏,探明天然气地质储量4 403.83×108m3[23],目前已建成110×108m3/a天然气产能[24]。该区块埋藏深、地层复杂,气层分布广、显示活跃[23],开采难度大,安全风险高[25]。经过近年来的技术攻关,区块固井质量已得到一定程度的提高,尤其是表层和技术套管,整体固井质量较好[25],但是钻井及生产期间仍然存在环空带压的风险。结合现场资料初步认为,除了管柱的密封问题外,后期作业的压力变化引起的水泥环完整性失效也可能导致环空带压。本节采用该区块某井施工数据,分析水泥环完整性失效风险。
安岳气田磨溪—高石梯区块一种井身结构如图11所示[26],取采用此类井身结构的某井进行计算。在钻井过程中其钻井液密度反复变化,如Ø244.5 mm套管固井后,下开钻井液密度从1.15 g/cm3提高至2.25 g/cm3,而Ø177.8 mm尾管固井后,下开钻井液密度从2.25 g/cm3降低至1.15 g/cm3,井筒内压力变化明显。这种大压差的现场工况下,水泥环完整性失效风险表现在以下两个方面。
1)对Ø177.8 mm尾管,下次开钻时,钻井液密度从2.25 g/cm3降低至1.15 g/cm3,则套管内液柱压力最高可降低53.9 MPa,由此第一界面压力降低多达12.0 MPa(图12,5 000 m深度处)。由于水泥候凝期间失重的影响,水泥凝固后,第一界面初始接触力可能为零或者处于较低的值[14],降低12.0 MPa后,第一界面将会出现拉应力,此时就存在微环隙的风险。
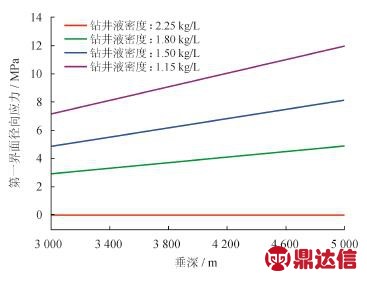
图12 钻井液密度降低造成Ø177.8mm尾管第一界面径向应力变化图

图13 五开钻井时2 900 m处第一界面径向应力图
2)对Ø244.5 mm套管,此次开钻时,钻井液密度1.15 g/cm3,以2 900 m处为例,此过程中套管内液柱压力约31.2 MPa;下次开钻时,钻井液密度升至2.25 g/cm3,此时2 900 m处套管内压力约63.9 MPa;第五次开钻时,钻井液密度又降至1.15 g/cm3,2900 m处套管内压力为31.2 MPa,由此出现了与压裂过程类似的加载—卸载工况,水泥环将产生塑性变形,在卸载过程中界面产生拉应力,从而有产生微环隙的风险(图13)。
3.2 库车山前水泥环密封失效风险分析
库车山前是塔里木油田的三超气井集中分布地,与磨溪—高石梯区块相比,其深度更深(表3),工况更加复杂,同时进行了高能量的压裂改造(井口压力可达100 MPa)。因此,该区块固井水泥环出现密封失效的风险更高,固井水泥环的长期有效封固面临更严峻挑战。
采用库车山前具有代表性的钻井数据,对库车山前钻井、压裂及生产过程中水泥环密封完整性存在的风险进行了梳理。在钻井过程,与磨溪—高石梯区块类似,井筒内液柱压力反复变化,井筒内液柱压力下降、水泥环塑性变形造成微环隙风险;试油试气过程中,井筒内液柱压力降低,第一界面接触力下降,易产生微环隙;压裂过程中,井筒内高压差易造成水泥环结构破坏及微环隙,同时也有套管变形的风险;生产过程中,井筒内温度上升存在水泥环强度衰退、水泥环密封失效及井口抬升的风险。现将各层套管大压差工况及失效风险汇总,如表3所示。这些密封失效过程在上文已有详细分析,此不赘述。
表3 库车山前大压差工况及水泥环密封完整性失效风险汇总
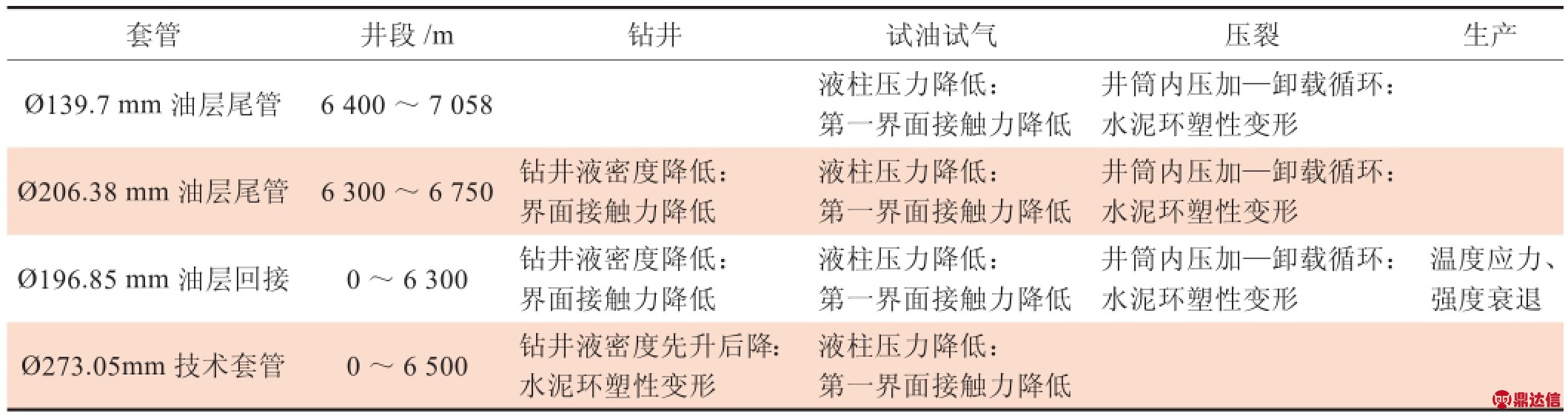
4 大压差工况下保障水泥环密封完整性措施及展望
针对页岩气、深井勘探开发中大压差工况下如何保障水泥环密封完整性的问题,中国石油集团钻井工程技术研究院已开展了一定的研究工作。通过建立完整性模型,结合现场数据进行水泥环完整性分析,梳理出水泥环密封完整性失效的主要原因,并定量计算出保障水泥环完整性所需的强度、弹性模量等水泥环力学性能指标以及界面胶结强度等参数,从而针对性地采取解决措施,包括对水泥石进行韧性改造,提高顶替效率以保证界面胶结强度,采用清水作为顶替液等工艺措施以提高界面接触力。通过这些措施的实施,在页岩气示范区、安岳气田现场试验中初步取得了良好的效果,缓解了多个区块的环空带压问题[22,25]。
随着勘探开发目标向深层、 低渗透、非常规资源发展,大压差的工况未来将更加普遍,为固井水泥环的长期密封完整性带来更为严峻的挑战。结合近年来的研究进展以及现场经验,建议从水泥浆体系、固井工艺及管理等方面着手,制订应对措施。
1)通过模型计算及现场试验的初步经验,提升水泥石抗变形能力(高强度、低弹性模量)、提高第一界面及第二界面胶结力,提高界面接触力是水泥环抵抗完整性失效的有效方式,对应的高性能的水泥浆体系、提高顶替效率及界面接触力的固井工艺措施仍需持续攻关。
2)水泥环密封完整性失效风险贯穿于钻井、试采、压裂及生产全过程,全生命周期的固井水泥环完整性管理是保障井筒密封完整性的发展趋势。在固井前,通过水泥环密封完整性分析计算,确定水泥石性能指标,指导水泥浆体系设计,利用开发的固井质量预测软件,在施工前对固井施工程序进行模拟,预测固井质量;在固井过程中,建立施工全过程监控评价体系,确定是否符合设计要求;固井后,根据地层压力、油气活跃程度,利用声幅结果,确定相应的考核指标;最终建立一套固井前—中—后全过程的质量综合评价方法,统一固井过程管理。
5 结论及建议
笔者结合理论研究及室内实验模拟结果,提出了大压差条件下水泥环密封完整性失效的问题,结合现场数据,初步分析了页岩气井、深井等钻井、压裂、生产过程中大压差条件可能造成的水泥环密封完整性失效风险,依据风险分析采取针对性措施,在现场取得了良好的效果。
由于组合体初始应力的不确定性以及现场工况的复杂性,实际工程中,水泥环密封失效风险包含但不限于本文讨论的范畴,组合体初始应力分布,尤其是水泥浆候凝过程中井筒的应力变化,还需要进一步研究。同时,由于水泥环受到反复的加—卸载作用,水泥环刚度退化、变形积累等行为将对分析结果产生重要影响,这些行为的表征,需要结合水泥石力学试验数据,建立更准确的水泥石本构模型。最后,由于缺少直接的室内实验验证及现场检测手段,数据的缺乏一定程度上影响了理论模型的修正及工艺措施效果的评价,未来需要进一步丰富验证及检测手段。