摘要:核主泵的密封性能是钠冷快堆安全评价的重要指标。以某型试验钠冷快堆核主泵为研究对象,提出了一种适用于钠冷快堆核主泵的双端面自泵送机械密封;运用正交试验法设计试验方案,并基于Fluent进行数值仿真模拟,探讨了该机械密封结构参数和工况参数对端面开启力和泄漏率的影响,分析了泵腔氩气零泄漏要求下的密封阻塞流体的压力调节范围。结果表明:在试验参数的范围内,槽面宽比和螺旋角对开启力均有影响,且槽面宽比影响更为显著,开启力随着槽面宽比和螺旋角的增大有上升的趋势;槽面宽比对泄漏率影响显著,泄漏率随槽面宽比的增大迅速增大。得到了最大转速和停机工况下阻塞流体压力与泄漏量、开启力的关系式;当泵腔工作压力为0.05 MPa时,只要阻塞流体压力不超出0.0528~1.6378 MPa区间均能保证密封安全有效。
关键词:核主泵;机械密封;计算流体力学;正交试验;数值模拟;优化
引 言
快中子增殖堆,不用慢化剂,直接用裂变产生的快中子来引发核裂变链式反应,并能增殖核燃料、充分利用铀资源、大大减少核废料中长寿命核素,是一种较为理想的核反应堆型[1-4]。但是,钠作为快堆的冷却剂,易与空气中的氧和水发生化学反应而发生爆炸[5]。1993年俄BN-600型快堆因钠泄漏停运[6],1995年日本“文殊号”快堆钠泄漏[7]等事件都给快堆的发展带来严峻的考验,特别是对钠泵密封提出更高要求。
机械密封因其技术成熟而成为国内外广泛使用的核主泵密封形式。文献[8-10]研究分析了现役核主泵用几种典型的机械密封结构,指出密封结构对机械密封的性能和使用寿命均有显著的影响。双端面机械密封适用于高工况场合,且可靠性强[11-13]。王财生等[14]利用试验装置研究了不同转速、介质压力和弹簧比压等工况下双端面机械密封的摩擦学性能。陈汇龙等[15]利用有限元法分析了双端面密封的温度场,提出合理选择冲洗液的温度和压力能够有效改善密封性能。文献[16-18]研究分析了双端面机械密封在工业应用中的失效原因,指出密封辅助冷却系统是双端面机械密封长时间连续平稳运行的关键所在。然而双端面机械密封运行要求提供的辅助系统不仅增加了其复杂程度,同时也提高了工业生产的成本。孙见君等[19]提出了一种具有良好自冷却、自清洁和自润滑性能的自行“泵出式”流体动压机械密封,并指出在一定槽深下其开启力与泄漏率比能够保持稳定[20]。周敏等[21]运用Fluent分析了这种自泵送机械密封的几何参数和工况参数对密封性能的影响,顾东升等[22]初步优化了自泵送机械密封端面的型槽结构。但以上自泵送机械密封研究均是基于单端面、小直径且被密封介质处于密封环外径侧的情况,未能考虑压力波动时快堆核主泵用机械密封的可靠性。
本文拟针对钠冷快堆核主泵,提出一种阻塞流体压力可调的双端面自泵送机械密封结构,分析其工作原理,并基于正交试验和Fluent数值仿真计算探讨结构参数和工况参数对快堆核主泵用双端面自泵送机械密封的影响关系及其显著性,以泄漏率不超标为目标函数,转速为约束条件,优化自泵送机械密封端面参数,获取阻塞流体的压力调节范围,确保应用于钠冷快堆核主泵的自泵送机械密封安全可靠。
1 结构及原理
1.1 核主泵用双端面自泵送机械密封结构
图1为核主泵用双端面自泵送机械密封轴截面示意图。静环用O形圈、动环、密封外壳围成外密封空间,外密封空间内充入阻塞流体。
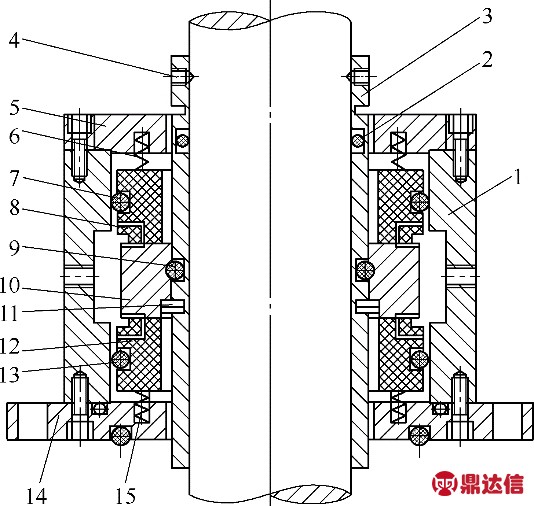
图1 双端面自泵送机械密封轴截面示意图
Fig.1 Schematic diagram of double-end self-pump mechanical seal shaft section
1—housing;2,7,9,13—O-ring;3—shaft sleeve;4—set screw;5,14—spring seat;6,15—spring;8,12—stationary face;10—rotor face;11—drive pin

图2 动静环三维结构
Fig.2 Three-dimensional structure of rotating and stationary seal ring
图2为核主泵用双端面自泵送机械密封的动静环三维结构(图中仅展示动环一侧端面,另一端面结构类似)。动环端面的外侧开设有型线为对数螺旋线的螺旋槽,依槽根半径将动环密封端面划分为槽区和坝区,相邻螺旋槽之间的密封面为密封堰。静环端面开设有与螺旋槽相匹配的储液环槽和轴向径向组合引流孔道,动静环配合时储液环槽覆盖在螺旋槽根部。
对数螺旋线的极坐标表达式[23]为

1.2 工作原理
钠冷快堆核主泵用机械密封的密封对象是液态钠上部有一定压力的保护气体(通常为氩气)。阻塞流体为润滑油。
双端面自泵送机械密封工作原理如下:当动环旋转时,阻塞流体因离心力的作用被加速成高速流体并沿螺旋槽工作面泵送回密封腔。随着螺旋槽内阻塞流体的流出,在螺旋槽的根部形成了压力相对较低的区域,外密封空间的阻塞流体在压差作用下,再次从静环上的轴向径向组合引流孔道流入储液环槽进入螺旋槽,再次被加速成高速流体沿着工作面被泵送回密封腔,形成一次次的自泵送循环。阻塞流体由螺旋槽根部向外径侧流动的过程中,随着螺旋槽截面面积的不断增大,流速降低,其动能转化为分离动静环端面的压力能,保证动静环端面不接触,并在密封端面相对运转时形成剪切流,实现对内径侧氩气的密封。与此同时,阻塞流体的一次次泵送循环,一方面实现了机械密封的自润滑,循环流动的阻塞流体也带走了密封端面间自润滑流体膜的黏性剪切热,产生了自泵送机械密封的自冷却效果,有效地减小了端面的热变形,避免了端面因热变形而导致的摩擦磨损;另一方面,阻塞流体中的颗粒进入密封端面后在离心力作用下,被泵送至密封腔,而不进入密封坝区,避免了密封端面遭受磨粒磨损,表现出了自泵送机械密封的自清洁潜力。当密封坝外侧的阻塞流体的压力大于内侧密封氩气的压力时,阻塞流体会少量泄漏进入氩气中,此时阻塞流体在重力的作用下进入安装在机械密封下侧的甩油环,漏入的阻塞流体经由甩油环流入集液桶,确保不会污染钠液。
自泵送机械密封螺旋槽出口的压力头h与槽内介质流量Q之间的关系及泄漏率qL与密封面两侧压差Δp之间的关系[21]可分别表示为
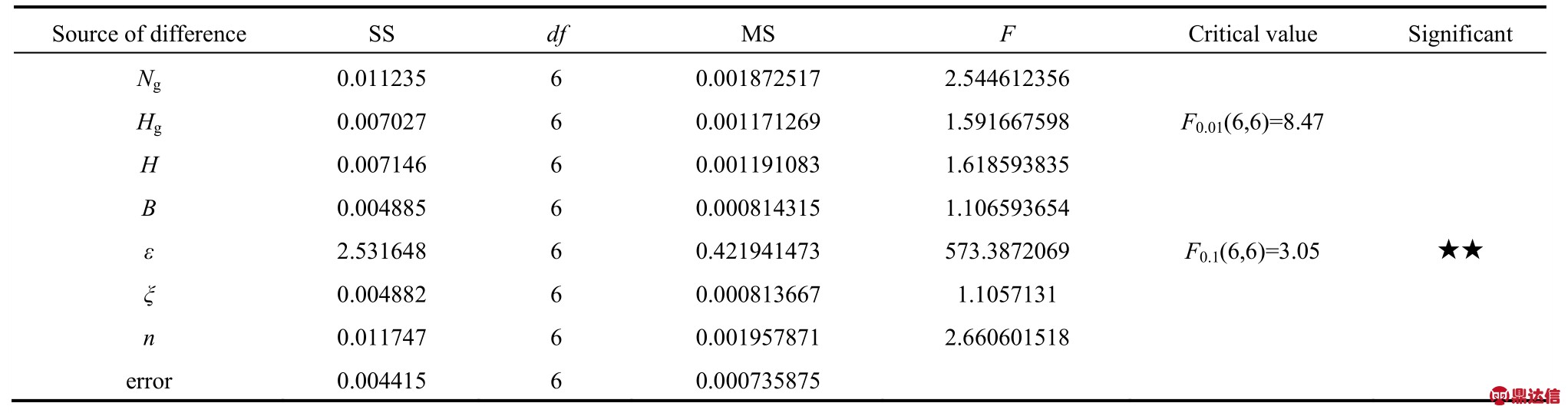
式中,K为与流体槽数相关的环流系数,恒小于 1,当槽数无限多时趋近于 1;η=ηmηhηv为泵送效率,反映能量损失的程度(ηm为机械效率,ηh为水力效率,槽浅,取小值;ηv为容积效率);N为轴功率;ρ为阻塞流体密度;ξ为槽台宽比;μ为阻塞流体动力黏度;h0为端面流体膜厚度;Δpg为密封坝两侧的压差;ro为密封环外半径;b为密封面宽度;l为密封坝宽度。
2 数值模拟正交试验方案
核主泵的泵轴直径 D为 400 mm,调速范围117~660 r·min−1,泵腔中氩气的压力pi为0.05 MPa,密封腔中阻塞流体的压力po为0.4 MPa,阻塞流体的泄漏率要求小于 5 ml·h−1。现设计一正交试验方案,结合数值模拟计算,分析各结构参数和工况参数对该机械密封性能的影响。
自泵送机械密封的结构参数有槽数Ng、螺旋角β、螺旋槽槽深Hg、环槽深H、环槽宽B、槽面宽比ε、槽台宽比ξ以及密封端面的内、外半径ri和ro。此外,核主泵转速n以及密封端面流体膜厚hm对密封性能也有很大影响。取ri=237 mm,ro=253 mm,轴向径向组合引流孔直径d=3 mm,膜厚hm=1.2 μm。选取46号润滑油作为阻塞流体,密度ρ=910 kg·m−3,动力黏度 μ=0.04186 Pa·s。各因素及其水平值见表1。根据因素及水平选用L49(78),以开启力和泄漏率作为表征密封性能的指标,设计的正交试验方案见表2和表4。假设各影响因素均为独立作用条件,无交互作用。
表1 各水平对应的数值
Table 1 Corresponding values of Ng,β,Hg,H,B,ε,ξ,n with different levels
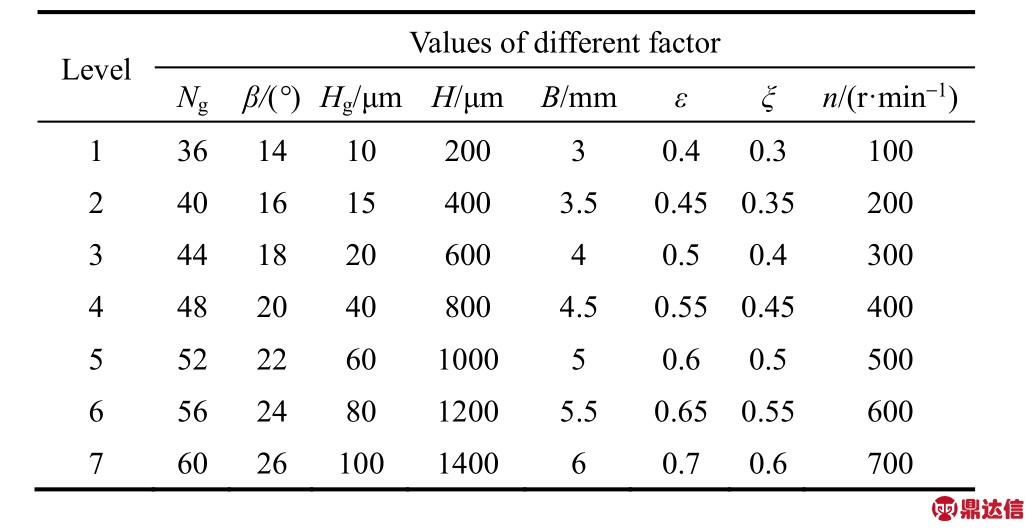
3 数值分析模型
3.1 基本假设
流体膜润滑机械密封的流场计算十分复杂[24]。为了简化计算,并考虑密封环端面结构以及密封特性,作如下假设:
① 流体介质属于牛顿流体,做层流流动;
② 密封端面间的流体流动为连续介质流动,且流体温度和黏度不随时间变化;
③ 密封端面光滑,忽略其粗糙度对流体流动的影响;
④ 液膜很薄,在厚度方向上压力和密度保持不变;
⑤ 密封环的温度及其材料的力学特性不随时间变化;
⑥ 流体介质与密封端面之间无相对滑移;忽略工作过程中系统的扰动和振动影响。
3.2 采样计算区域几何模型
本文所研究的快堆核主泵用双端面自泵送机械密封,动环上的螺旋槽均匀布置在动环端面上。由于端面间流场是轴对称的,理论上各螺旋槽所占区域的流场相同,取其中任意螺旋槽区域进行数值模拟[25],计算区域如图3所示。
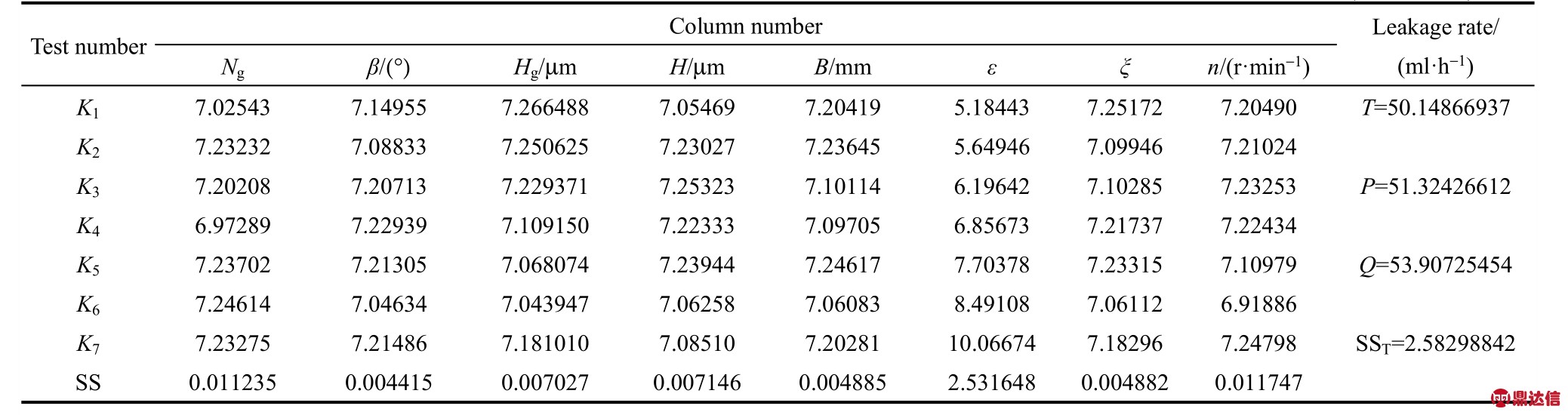
图3 采样计算区域
Fig.3 Sampling calculational region
3.3 控制方程
根据基本假设和计算模型,密封端面间的流体做稳态流动,从而满足Reynolds方程[26-27]
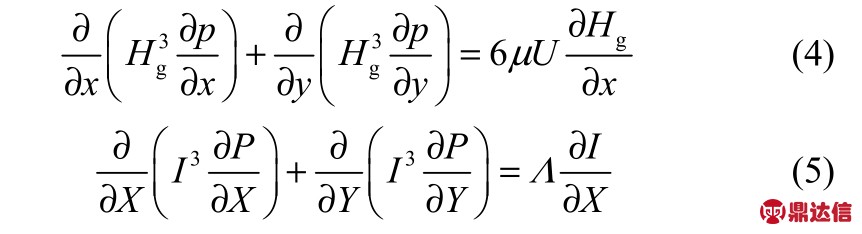
式中,X=x/ri,Y=y/ri,P=p/pi,Λ=6μriU/(pic2),I=Hg/c,ri为密封端面内半径,pi为内径侧压力,Hg为槽深,c为非槽区液膜厚度,U为端面平均线速度,Λ为量纲1压缩数。
3.4 计算区域网格划分
运用ANSYS18.0中的ICEM模块对计算区域进行网格划分,这里选择计算结果精度较高的六面体结构网格。由于膜厚是在微米级别,与整个模型尺寸在数量级上不一致,运用ICEM定义网格全局尺寸之后的自动网格划分方法,在膜厚方向上难以将液膜进行分层。这里采用直接对模型边界进行节点数定义,以保证在膜厚的方向上,液膜能够分层而达到良好的计算精度。将三维模型导入ICEM后,对模型进行拓扑以确保模型是封闭的,再对每一面进行命名以及螺旋槽、环槽、液膜和引流孔进行block的划分,最后对划分好的block的edge进行节点数定义。权衡网格质量、计算机运算能力和网格无关性,将膜厚方向划分为6层,螺旋槽槽深方向划分为10层,环槽深方向划分为30层,引流孔划分为50层,生成网格总数为1873410个,网格如图4所示。
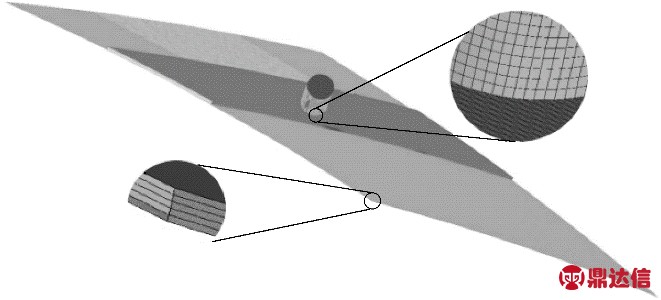
图4 网格划分
Fig.4 Meshing generation
3.5 边界条件及求解器的设置
采用 Reynolds边界条件[28-29]来定义计算区域的两种边界条件。
强制性边界条件:采样计算区域内径出口CD面上有p=pi(氩气的压力),在外径出口AB面以及引流孔进口 L面均有 p=po(密封腔阻塞流体压力)。
周期性边界条件:采样计算区域的边界AD和BC面的压力相等:p|AD=p|BC,即p(θ+2π/Ng)= p(θ);边界 EH和 FG面的压力相等:p|EH=p|FG,即p(θ+2π/Ng)=p(θ)。
根据质量流量守恒,流过面 AD+EH与面BC+FG的质量流量相等:q|AD+q|EH=q|BC+ q|FG,流过面AB+CD的流体质量等于引流孔入口 XT面的流体质量:q|L=q|AB+q|CD。
式(4)和式(5)是非线性偏微分方程,不能用解析法得到方程的解,本文运用 Ansys18.0中Fluent模块进行数值模拟计算。选择三维单精度求解器,求解器模型设置为无黏性(理想)流体,流态为层流,压力速度耦合采用SIMPLEC算法,扩散项的离散格式选择中心差分格式,对流项的离散格式选择二阶迎风格式,模型的收敛绝对精度设定为 10−6。
4 数值模拟正交试验结果与分析
4.1 方差分析的基本步骤与格式
如果用正交表Ln(rm)来设计试验,则因素的水平数为r,正交表的列数为m,总试验次数为n,设试验结果为 yi(i=1,2,…,n),各因素相同水平的试验指标之和为 Ki(i=1,2,…,n),其均值为 ki(i=1,2,…,n),可按如下的步骤进行试验结果的方差分析。
(1)计算离差平方和
① 总离差平方和。设
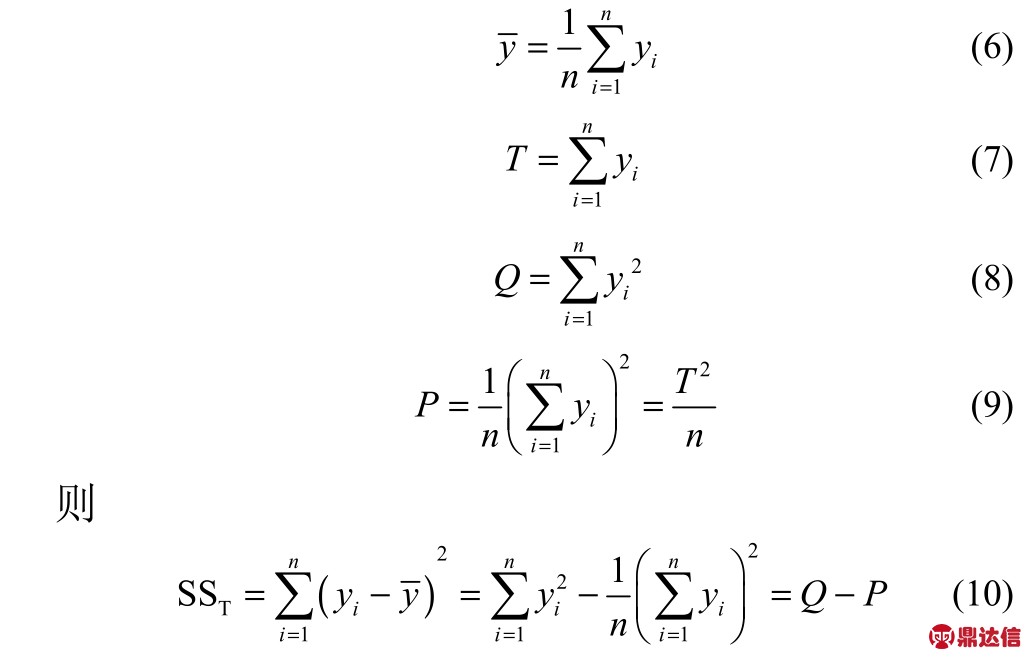
总离差平方和SST反映了试验结果的总差异,其值越大,说明因素水平的变化对试验结果的影响越大。
② 各因素引起的离差平方和。假设正交表中某一列的因素为A,则因素A的离差平方和为

③ 试验误差的离差平方和。正交试验方案设计时,一般要求留有空列以便方差分析,即误差列。如果没有可用的误差列,则需要进行重复试验,或是利用离差平方和中最小的一项做近似估计[30],误差的离差平方和为所有空列对应的离差平方和之和,即

(2)计算自由度
总平方和的总自由度

正交表任一列离差平方和的自由度

显然
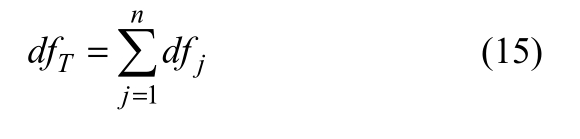
误差自由度

(3)计算平均离差平方和(均方)以因素A为例,因素的均方为
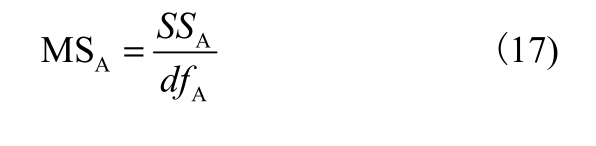
试验误差的均方为
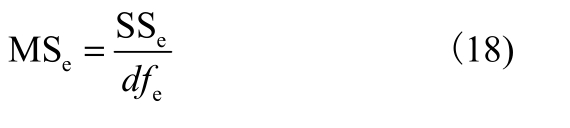
(4)计算F值
将各因素的均方除以误差的均方,得到XT值

(5)显著性检验
对于给定的显著性水平α,先从F分布表中查出临界值Fα(dfA,dfe),然后比较F值与Fα(dfA,dfe)的大小,如果FA>Fα1(dfA,dfe),则说明因素A对试验结果的影响特别显著,标记为“★★”;如果FA介于Fα1(dfA,dfe)和 Fα2(dfA,dfe)之间,则说明 A 对结果有一定的影响,标记为“★”;如果 FA<Fα2(dfA,dfe)则说明因素A对试验结果无显著影响。
4.2 开启力的正交试验及方差分析
以开启力作为考察指标的正交试验安排及结果如表2所示。利用上述的方差分析法对表2的试验数据进行处理,得到结果如表3所示。由于正交试验表没有预留空列,所以表3中的误差是利用离差平方和中最小一项做的近似估计[30],通过开启力方差分析表3,可以发现对开启力影响显著的因素是槽面宽比ε,螺旋角β对开启力也有一定影响,在试验范围内的其他因素对开启力影响均不显著。这是因为槽面宽比ε对应式(3)中的密封坝宽度l,螺旋角β对螺旋槽截面面积影响显著,即与式(2)中的槽内介质流量Q相关,且大直径下,由对数螺旋线的线型可以看出槽面宽比ε和螺旋角β对槽内介质流量Q的影响较大。其中槽面宽比ε和螺旋角β与开启力的关系如图5所示,图中各水平所对应的数值为表2中同一水平试验结果之和Ki,即螺旋角β和槽面宽比ε列K1~K7对应数值。由图5可以看出开启力随螺旋角β和槽面宽比ε的增大亦有增大的趋势。因此,在设计核主泵用双端面自泵送机械密封时,应适当取较大的槽面宽比和较大的螺旋角,以便获得较大的开启力。
4.3 泄漏率的正交试验及方差分析
以泄漏率作为考察指标的正交试验安排及结果如表4所示,表中“+”表示阻塞流体泄漏到氩气侧。方差分析结果如表5所示。可以看出对泄漏率有显著影响的是槽面宽比 ε,试验范围内的其他因素对泄漏率的影响均不显著。与上述开启力结果类似,槽面宽比ε对应式(3)中的密封坝长度l,槽面宽比ε的大小极大地影响着阻塞流体泄漏通道长度。槽面宽比ε与泄漏率的关系如图6所示,图中各水平所对应的数值为表4中同一水平试验结果之和Ki,即槽面宽比ε列K1~K7对应数值。由图6可以看出泄漏率随槽面宽比ε的增大迅速增大。因此,在设计核主泵用双端面自泵送机械密封时,取较小的槽面宽比可获得较小的泄漏率。
表2 以开启力作为考察指标的正交试验结果
Table 2 Orthogonal test results using opening force as target of evaluation
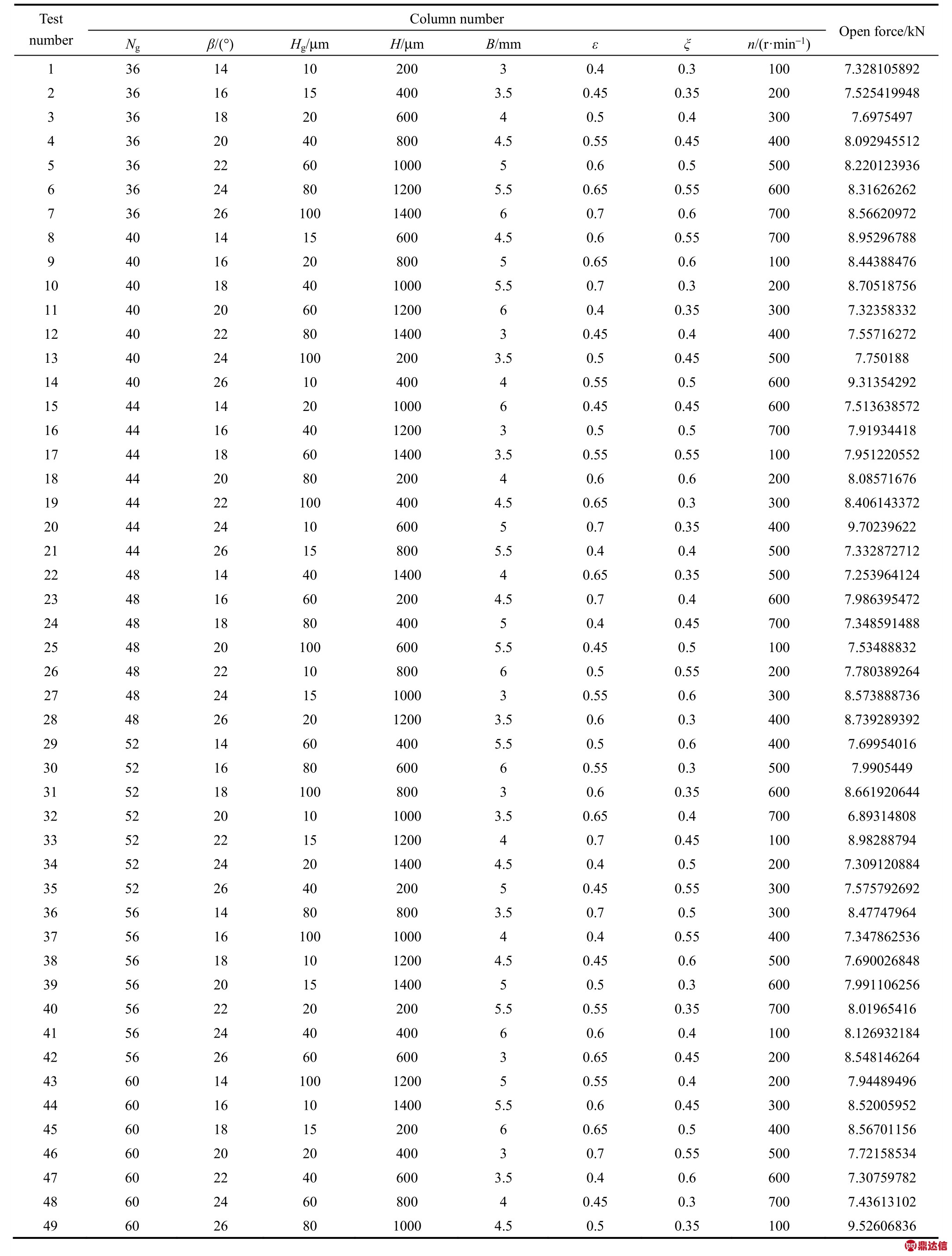
Table 2 (continued)
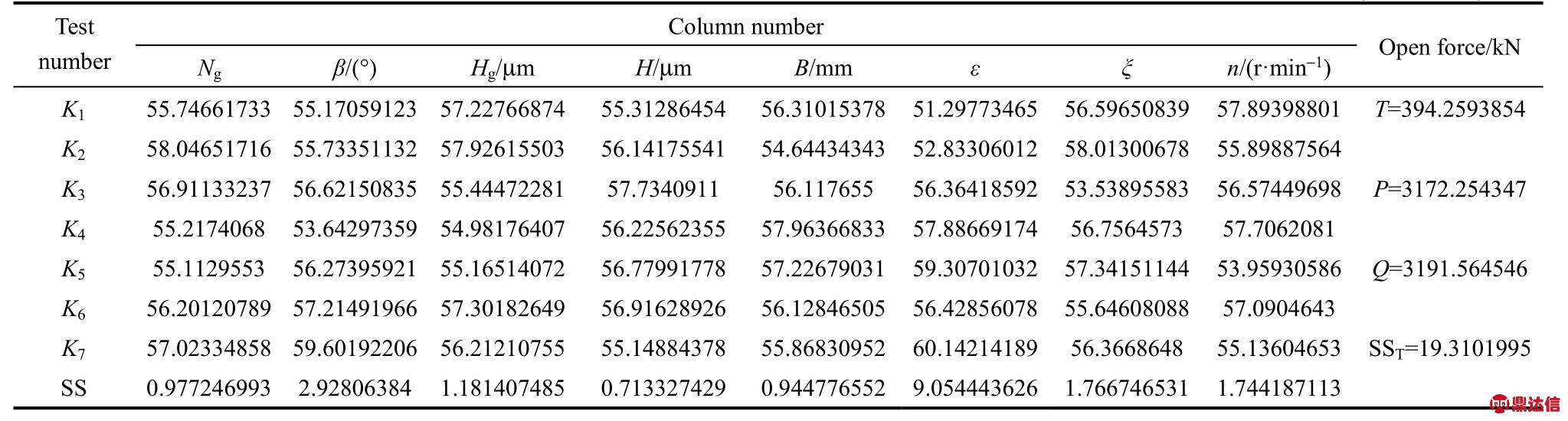
表3 开启力方差分析
Table 3 Variance analysis on opening force
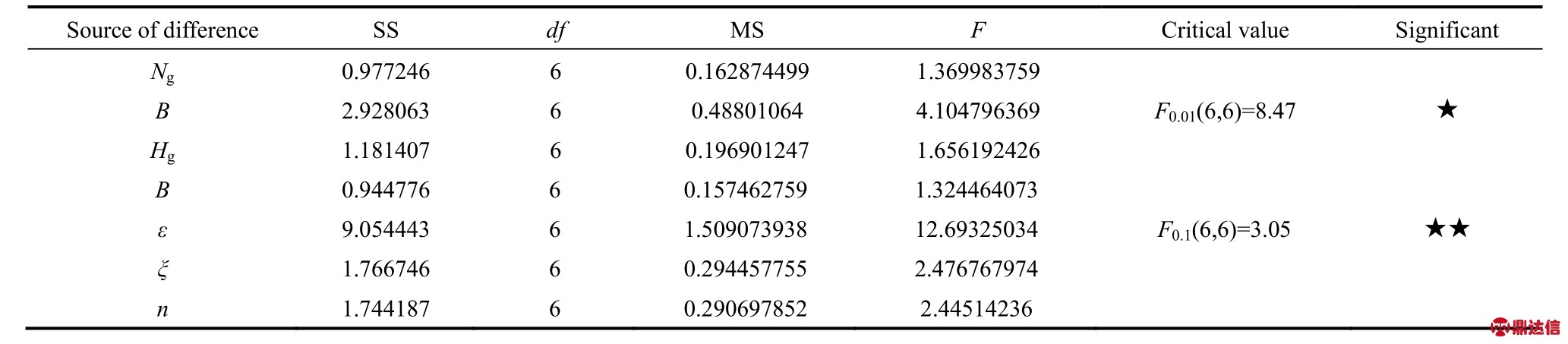
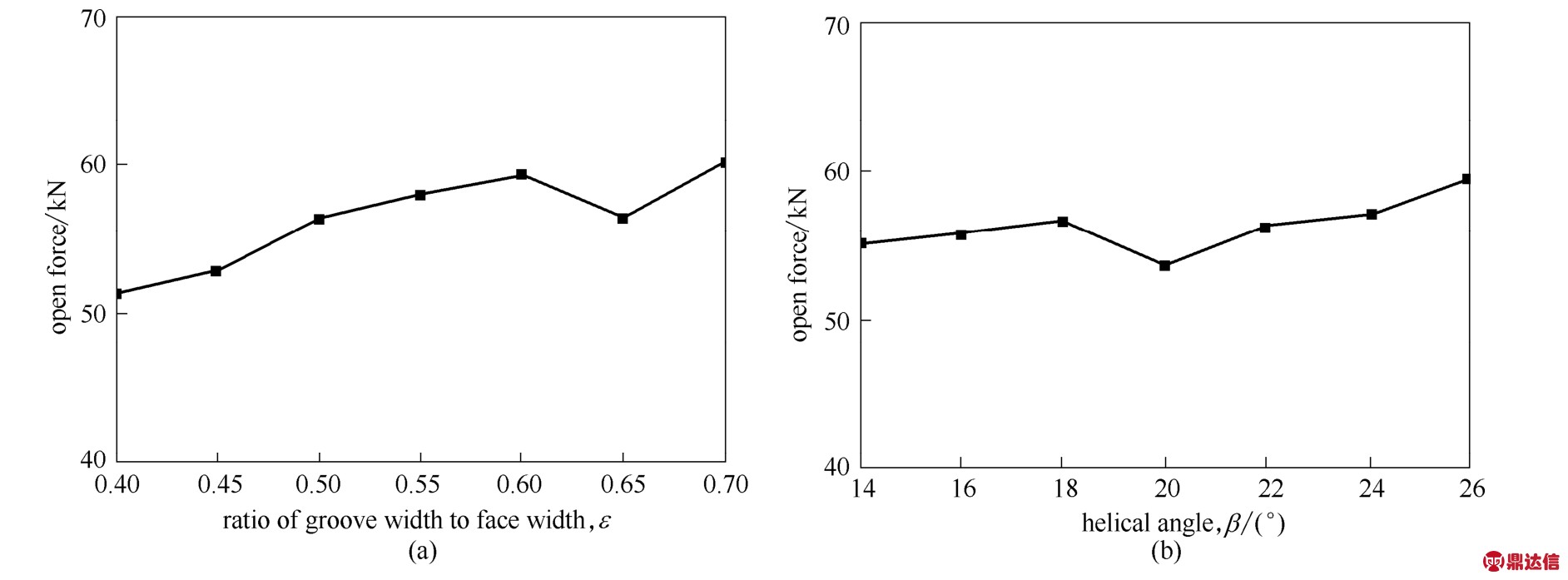
图5 开启力随ε、β的变化
Fig.5 Effect of ε, β on open force respectively
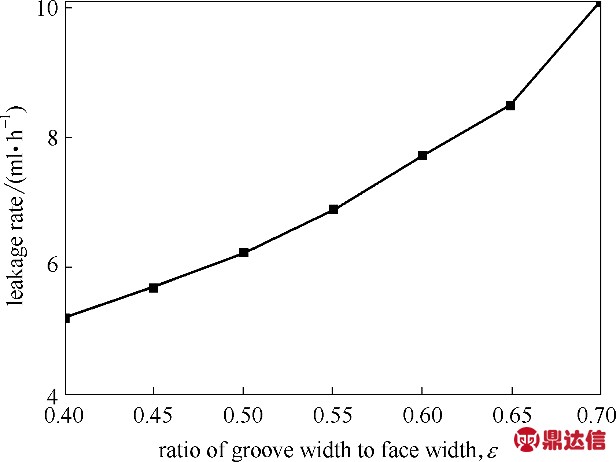
图6 泄漏率随ε的变化
Fig.6 Effect of ε on leakage rate
5 参数优化及验证分析
由上述的试验和分析可知在试验范围内的因素对核主泵用双端面自泵送机械密封性能有影响的是槽面宽比ε和螺旋角β,且开启力随着槽面宽比ε和螺旋角β的增大有增大的趋势,泄漏率随着槽面宽比ε的增大而迅速增加。由此,根据实际运行工况以及多指标正交试验数据处理的综合平衡法[31],在泄漏率较小的情况下,综合优先考虑开启力,设计一组新的因素水平组合,Ng=40、β=26°、Hg=15 μm、H=200 μm、B=3 mm、ε=0.6、ξ=0.35、n=600 r·min−1。在前述相同的条件下,对这一新的参数组合进行仿真模拟计算,得到其开启力为9.66343 kN,泄漏率为 1.09103 ml·h−1。通过与表2和表4的对比,可以发现此参数组合下的密封性能可满足核主泵机械密封性能要求且均优于上述任一组正交试验组合。
表4 以泄漏率作为考察指标的正交试验结果
Table 4 Orthogonal test results using leakage rate as target of evaluation
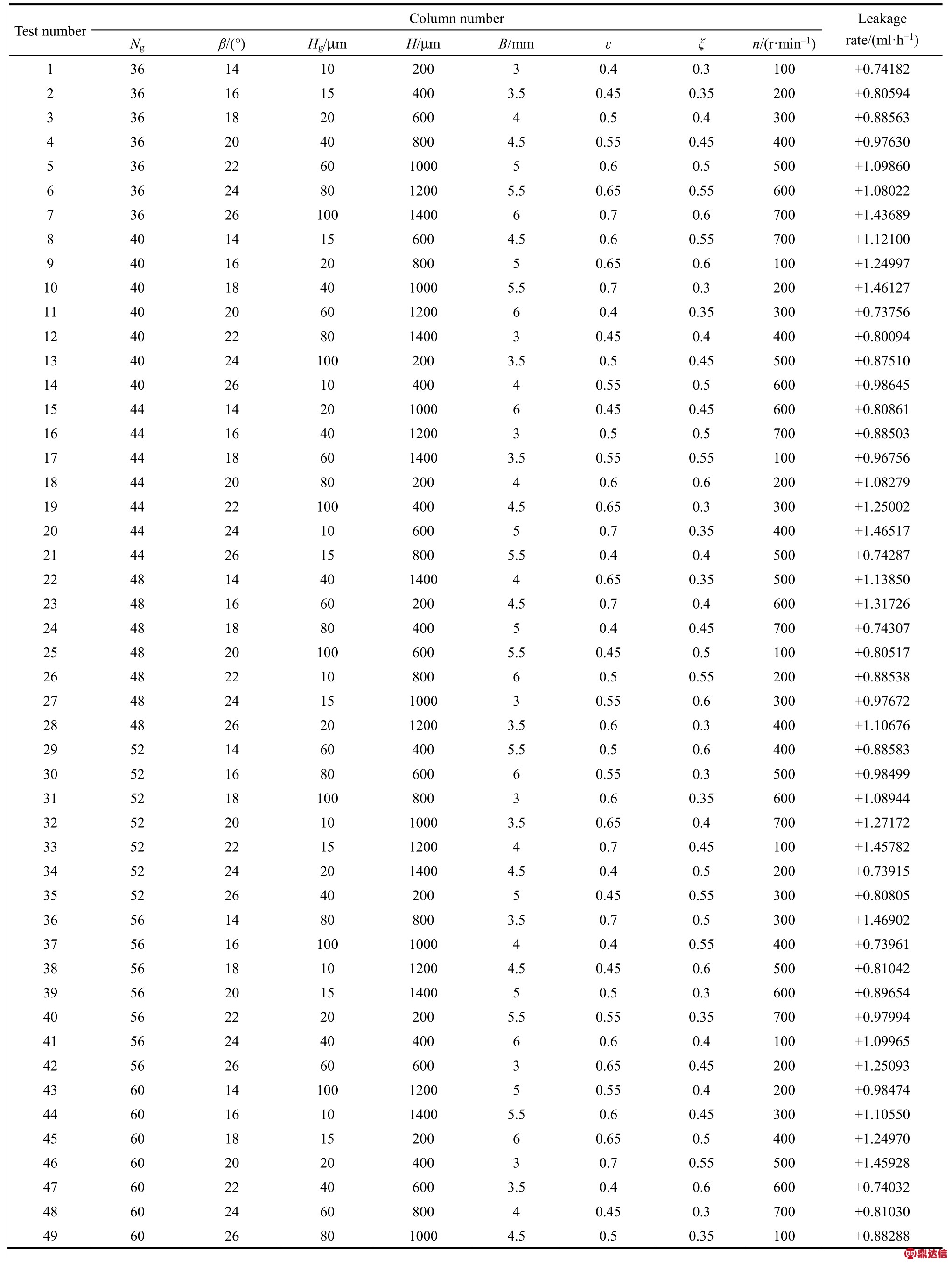
Table 4 (continued)
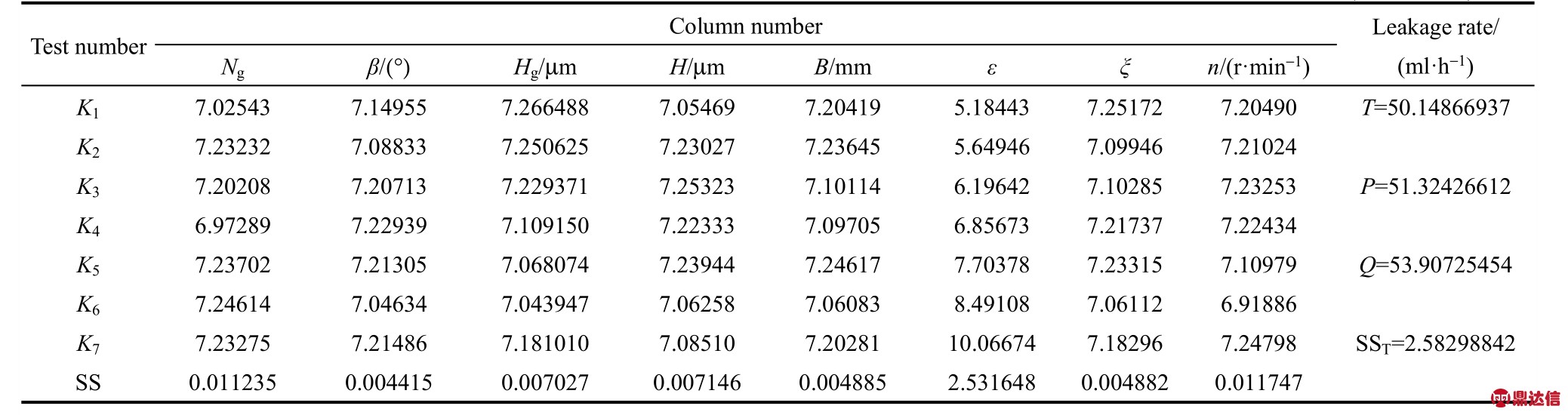
表5 泄漏率方差分析
Table 5 Variance analysis on leakage rate
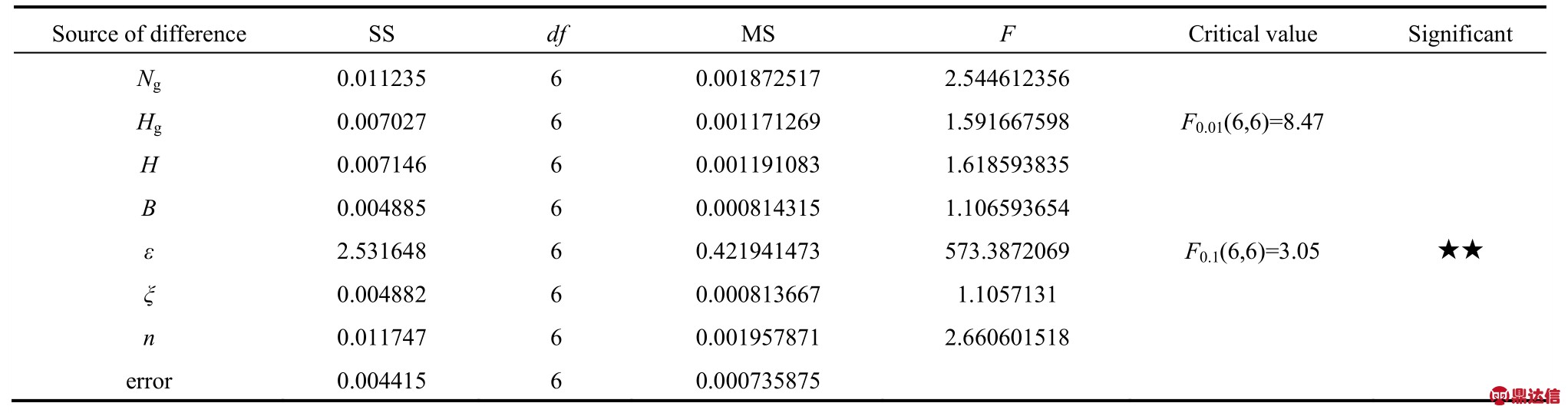
表6 不同转速下的开启力和泄漏率
Table 6 Open force and leakage rate at different speeds
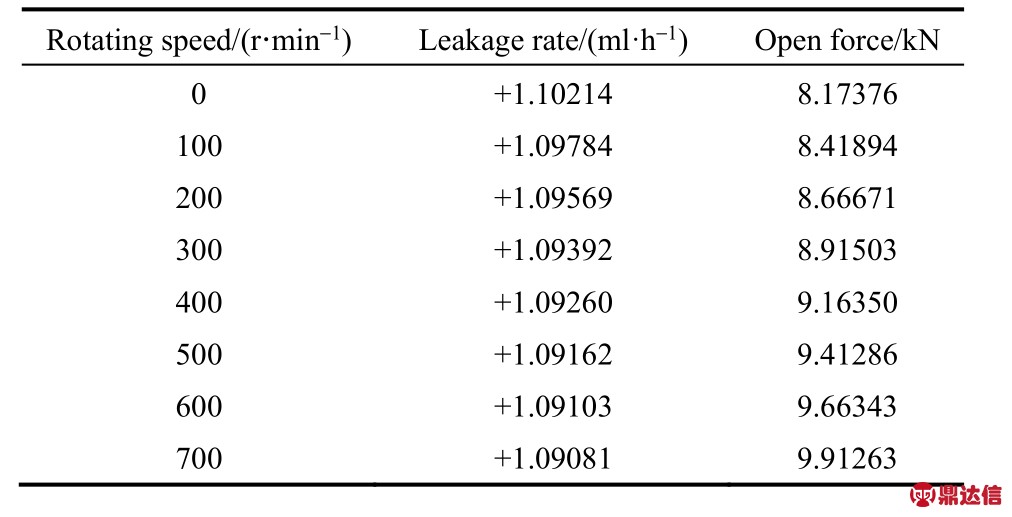
为了确保机械密封在核主泵的调速范围内均能实现泵腔内氩气零泄漏,数值研究了0~700 r·min−1范围内不同转速下双端面自泵送机械密封的开启力和泄漏率,结果如表6所示,表中“+”表示阻塞流体泄漏到氩气侧。由表6可知,在停机以及惰转工况下没有氩气外泄漏,且阻塞流体的内泄漏也在泄漏允许值之内,可满足快堆核主泵密封的性能要求。
6 阻塞流体压力的可调能力
根据以上数值模拟的结果可知,泄漏均为润滑油微内漏,无氩气外泄,保证了冷却剂钠的零泄漏。为了防止核主泵实际运行中因外界干扰导致密封出现不稳定内漏或外漏,下面开展了双端面自泵送机械密封的阻塞流体压力可调性分析。
图7为最大转速时泄漏率和开启力与阻塞流体压力之间的关系曲线。拟合得到的泄漏率、开启力与阻塞流体压力之间的关系式分别为

式(20)、式(21)的R2值均为1,R2是趋势线拟合程度的指标,其值越接近于1或等于1,拟合所得关系式的可靠性越高。
核主泵的理想工作状态是既无阻塞流体的内泄漏,也无氩气的外泄漏。令式(20)中Q1为零,解得阻塞流体的临界压力po值为0.0528 MPa,相应地由式(21)可得开启力F1为2.9302 kN。在保证无外泄漏的同时,内泄漏也不能超过泄漏标准 5 ml·h−1,可得阻塞流体压力值po和开启力F1分别为1.6437 MPa和34.4714 kN。
图8给出了停机工况相应的泄漏率和开启力与阻塞流体压力的关系曲线。停机工况下开启力和泄漏率与阻塞流体压力的关系式如下

式(22)、式(23)的R2值均为1。同理,可得停机时阻塞流体压力po在0.05~1.6378 MPa均可确保无氩气的外泄漏和阻塞流体内泄漏在规定的标准范围之内,相应开启力值F2为1.2315~32.5708 kN。
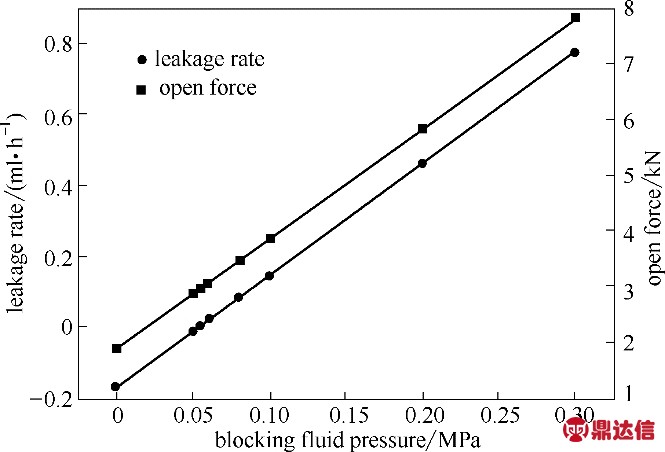
图7 最大转速时阻塞流体压力对泄漏率和开启力的影响
Fig.7 Effect of different blocking fluid pressure on leakage rate and open force at maximum speed
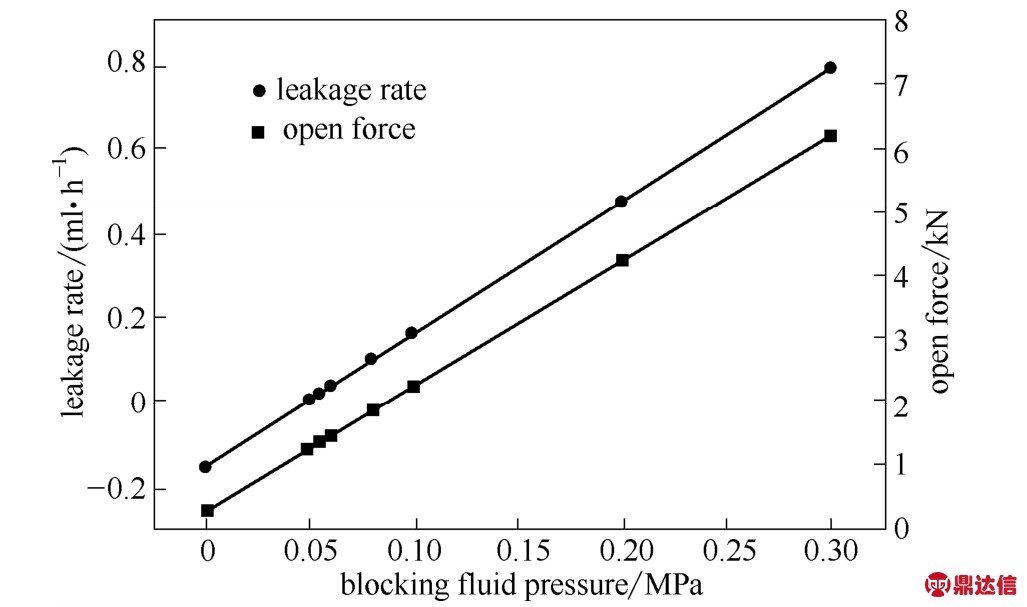
图8 停机时阻塞流体压力对泄漏率和开启力的影响
Fig.8 Effect of different blocking fluid pressure on leakage rate and open force during shutdown
综合以上两种工况阻塞流体的压力调节范围可知,当阻塞流体压力处于0.0528~1.6378 MPa时,均可确保冷却剂钠的零泄漏。
7 结 论
(1)提出了一种阻塞流体压力可调的双端面自泵送机械密封。正交试验和数值模拟分析表明,该机械密封可满足快堆核主泵密封性能要求,适用于钠冷快堆核主泵。
(2)在槽数36~60,螺旋角14°~26°,螺旋槽槽深10~100 μm,环槽深 200~1400 μm,环槽宽3~6 mm,槽面宽比0.4~0.7,槽台宽比0.3~0.6,转速 100~700 r·min−1范围内,槽面宽比和螺旋角对开启力均有影响,且槽面宽比影响更为显著,开启力随着槽面宽比和螺旋角的增大有上升的趋势;槽面宽比对泄漏率影响显著,泄漏率随槽面宽比的增大迅速增大。
(3)以润滑油作为阻塞流体,数值模拟得到了最大转速和停机工况下核主泵用双端面自泵送机械密封的泄漏率、开启力与阻塞流体压力的关系式;据此,分析发现当泵腔工作压力为0.05 MPa时,只要阻塞流体不超出0.0528~1.6378 MPa区间均能保证密封安全有效。
(4)自泵送机械密封的自清洁性将在后续工作中深入研究。
符 号 说 明
B——储液环槽宽度,mm
D——核主泵泵轴直径,mm
d——轴向径向组合引流孔道直径,mm
F1,F2——开启力,kN
H——储液环槽深度,μm
Hg——螺旋槽槽深,μm
hm——密封面非槽区流体膜厚,μm
Ng——螺旋槽槽数
n——转速,r·min−1
pi,po——分别为氩气的压力和阻塞流体压力,MPa
Q1,Q2——泄漏率,ml·h−1
rg——对数螺旋线起始半径,mm
ri,ro——分别为密封环的内径和外径,mm
β——圆周切线与对数螺旋线切线的夹角,(°)
ε——螺旋槽长度与整个密封面宽度之比
ξ——螺旋槽宽度与整个槽台宽度之比
θ——对数螺旋线相对于圆心旋转的角度,rad