摘要:为了探究相变现象对密封性能的影响规律,通过联立N-S方程与质量输运方程,建立了液膜密封相变模型,使用有限体积法对控制方程进行离散,对双列螺旋槽液膜密封相变现象进行了仿真模拟,获得了液膜流线及相态分布并分析了结构参数对相变区域与密封性能的影响。结果表明:液膜发生相变后物性参数发生变化,密封间隙内流场与端面压力分布发生明显改变。内侧螺旋槽可以提供稳定的开启力并保证密封端面处于较好的润滑状态,但同时导致密封泄漏增加。通过减小外侧螺旋槽槽面宽比、槽台宽比、螺旋角、槽深或增大外侧螺旋槽槽数均可降低密封泄漏量,提升密封性能。
关键词:双列螺旋槽;液膜密封;相变现象;性能研究
引 言
螺旋槽液膜密封可依靠螺旋槽产生的动压效应使密封端面分离,降低端面间的磨擦磨损,并且通过对螺旋槽各参数的调整可实现上游泵送与下游泵送的功能,因此化工机械中有着广泛的应用。
密封环端面开设螺旋槽在干气密封与液膜密封中都有着广泛的应用。马春红等[1]对螺旋槽端面微间隙高速气流润滑密封特性进行了研究;陈源等[2]在高速高压条件下分析了螺旋槽结构参数对气膜动态特性系数的影响规律;江锦波等[3]提出一种仿鸟翼微列螺旋槽端面干气密封结构并给出螺旋槽主要结构参数的优选值范围;郝木明等[4]推导了螺旋槽液膜密封压力分布公式并提出基于权重叠加的流场计算方法;周剑锋等[5]研究了微扰动对螺旋槽密封液膜承载力和泄漏率等密封特性参数的影响;陈汇龙等[6]对跨尺度密封端面微间隙流场进行三维数值模拟。当液膜温度高于局部饱和温度时,液膜便会发生相变现象,进入两相运行状态。Lymer[7]首先推导了预测两相密封不稳定性的模型;Hughes等[8]对汽化过程进行简化假设并建立了间断沸腾模型;Lau等[9]提出了简化的似等温低泄漏层流模型;Yasuna等[10]建立了连续沸腾模型针对高泄露的情况有着更高的准确性;Beatty等[11]通过对间隙内流体流动进行简化建立了湍流绝热两相模型;Lebeck[12]提出了流体静力学机械端面密封混合摩擦模型;Etsion等[13-15]对动静环偏斜与液膜汽化之间的相互作用进行了研究;Salant等[16]与 Beeler等[17]对两相密封的轴向稳定性进行了研究并提出应考虑挤压效应对润滑膜刚度和阻尼的影响;Migout等[18]发现平衡比对液膜汽化现象的影响不可忽略;Basu等[19]发现流体的离心惯性在密封高速运转下会减小其承载能力;Saadat等[20]对混合物公式进行了实验验证;顾永泉[21-24]在实验研究和分析的基础上,对似液相与似汽相混相密封的相态稳定性进行探讨和分析;王涛等[25-27]对加工有表面微造型的机械密封汽化现象进行了实验研究;本课题组[28]发现下游泵送螺旋槽密封可有效地抑制相变的进行,但同时造成密封泄漏量增大,导致密封的实用性降低。
为了增强螺旋槽密封在密封易相变介质时的实用性,本文在外径侧增设反向螺旋槽,形成双列反向布置,并对其相变现象进行了数值模拟,分析了螺旋槽结构参数对相变区域与密封性能的影响,为螺旋槽密封在两相运行工况下的结构设计提供理论参考。
1 物理模型
密封环端面结构如图1所示,当密封环如图中方向旋转时,内侧螺旋槽将密封介质泵送至密封间隙内,增强端面的润滑性能,同时产生稳定的开启力。外侧螺旋槽则可有效地将间隙内的介质泵回高压侧,减小泄漏量,提高密封性能。
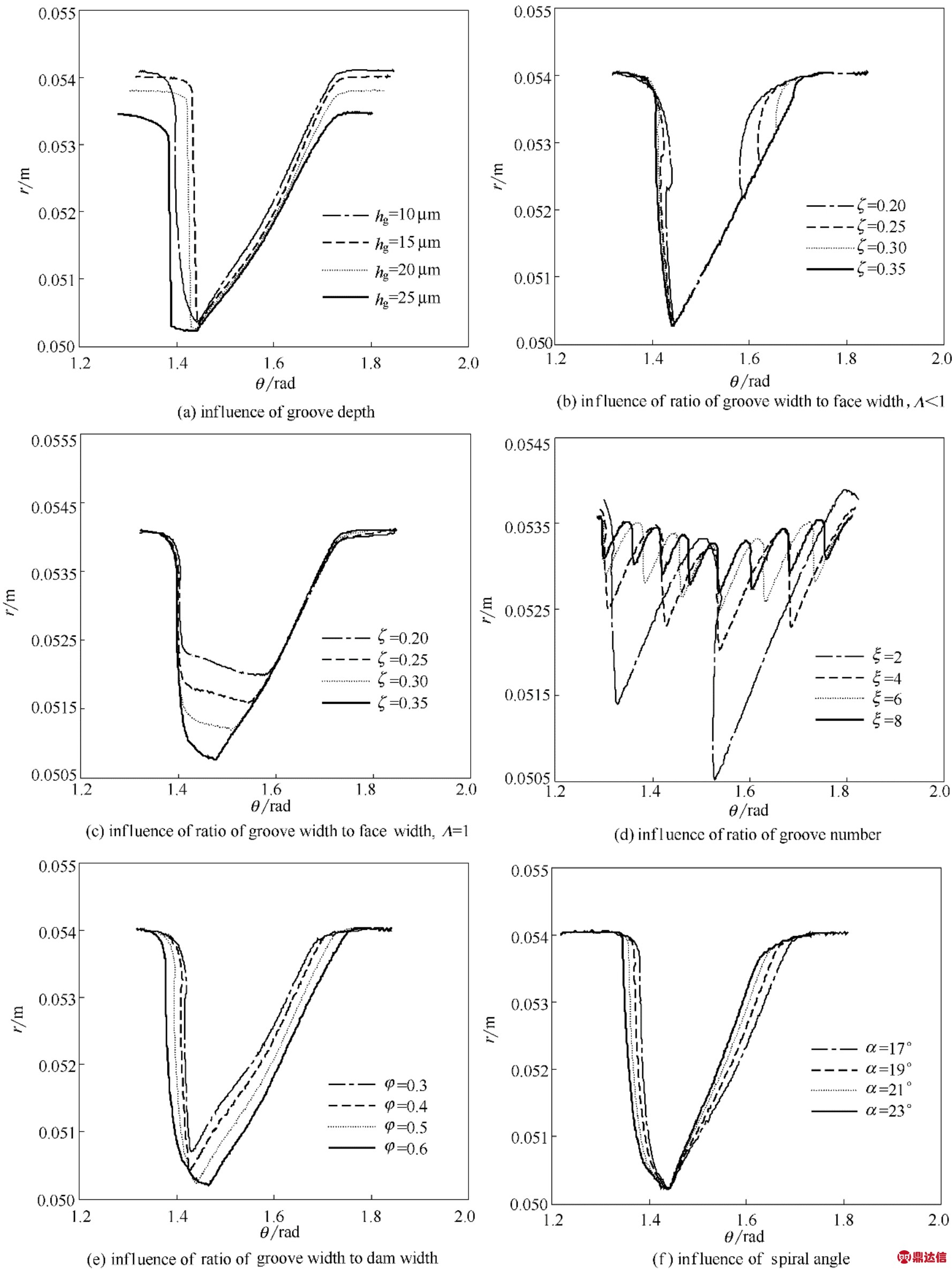
图1 动环模型
Fig.1 Model of moving ring
图1中,Ro、Ri分别为密封环的外径与内径;Rig 与 Rog1、Rog2分别为内侧与外侧螺旋槽槽根半径,θig、θid与 θog、θod分别为内、外侧螺旋槽槽区、坝区对应的角度,αi、αo分别为内、外侧螺旋槽螺旋角。为了便于分析,作如下定义:槽数比ξ= No/Ni;Λ=Rog2/ Ro,Λ=1为外槽型,Λ<1为中槽型,槽面宽比 ζ=(Rog2−Rog1)/(Ro−Ri),槽台宽比 φ=θog/(θog+θod),开漏比η=F/Q,相变率τ=Vv/(Vl+Vv)×100%。
2 数值求解
2.1 控制方程
密封间隙液膜相变过程较为复杂,为了便于对相变现象进行数值模拟,做如下简化。
(1)液相发生相变后物性参数变化区间较大,忽略液膜黏温效应的影响。
(2)密封动静环端面不考虑粗糙度、波度等影响且不发生倾斜。
(3)密封间隙内液膜温度相等且物性参数在轴向保持不变。
(4)液膜相变后以蒸气形态存在并且在两相区不存在滑移现象。
(5)密封间隙内液膜为层流流动。
液膜密封间隙内液膜相变后两相流动仍满足N-S方程,两相之间的质量传递由质量输运方程[29]控制
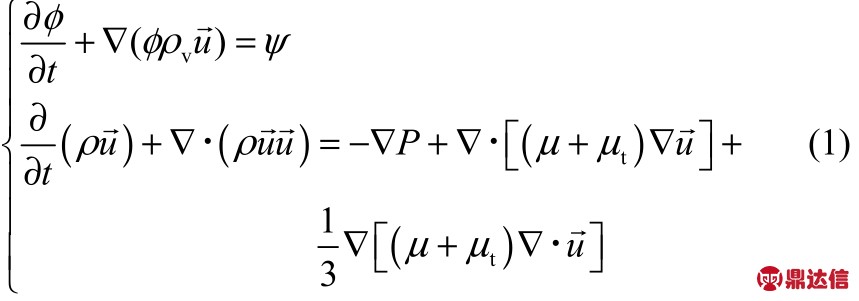
液膜发生相变后,流体膜的密度与黏度的变化可根据Wallis[30]的研究成果用式(2)进行描述
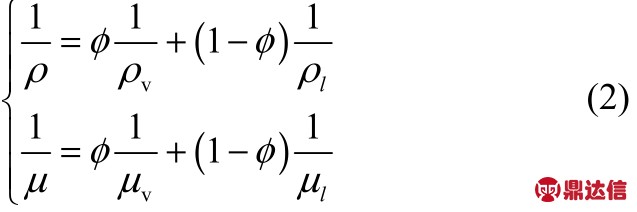
控制汽液两相质量传递的质量源项可由分子动力学理论[28]获得

2.2 求解设置
双列螺旋槽沿周向呈周期性分布,选取单周期进行计算(图2)。通过UDF功能对式(2)、式(3)进行编译,借助Fluent软件求解器对双列螺旋槽密封液膜相变现象进行仿真求解,主要设置如下。
(1)液膜流态采用层流模型。
(2)密封介质液相为液态水,汽相为水蒸气。
(3)边界条件设置:边界Π1和Π2为周期性边界条件,即 P(θ+2π/Ng)=P(θ),边界 Π3、边界 Π4为强制性边界条件,分别为压力入口边界(P=Pi)与压力出口边界(P=Po)。
(4)选择SIMPLE算法与相场耦合求解,扩散项采用中心差分格式离散,对流项采用二阶迎风格式进行离散,收敛精度设为10−9。
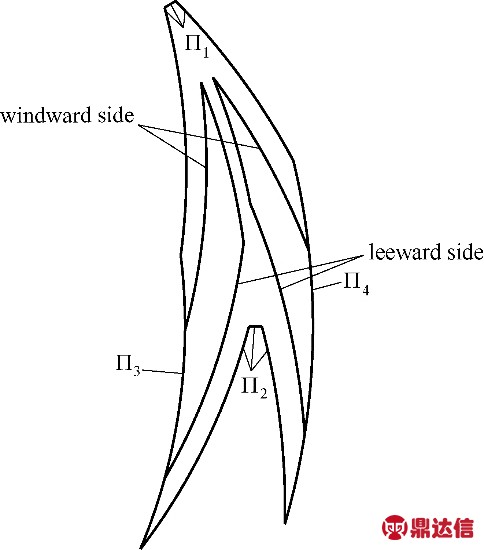
图2 计算域模型
Fig.2 Computational domain model
3 结果分析
3.1 模型验证
对平端面密封相变现象进行模拟并将所得端面压力分布与 Yasuna等[10]所得结果进行对比(图3),由图中可以看出端面压力变化趋向相同且整体偏差较小,可确定本文所使用模型有着较好的精度。
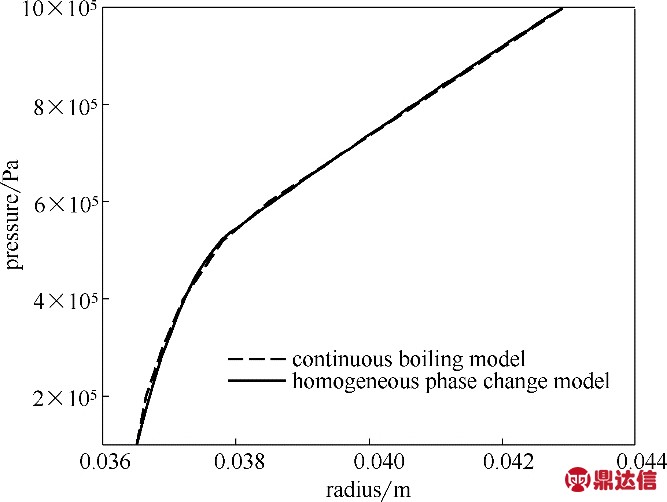
图3 模型对比
Fig.3 Model comparison
3.2 相变影响分析
密封环外径Ro=54.25 mm,内径Ri=44.25 mm,内径入口压力为1 MPa,外径出口压力为0.1 MPa,转速 n=1500 r·min−1,内、外侧螺旋槽螺旋角为 15°,槽台宽比为0.5,内侧螺旋槽槽面宽比为0.5。外侧螺旋槽槽根半径Rog1=50.25 mm,Rog2=54.25 mm,槽面宽比为0.4,膜厚为3 μm。
图4为不同膜温下液膜相态分布图,由于外侧螺旋槽(以下简称“泵回槽”)产生的动压效应改变了端面压力分布,相变区域不再为规则的圆环形状。由图4(a)可以看出在T1时,相变区域主要发生在外侧螺旋槽内,且靠近螺旋槽背风侧,在迎风侧靠近槽根处由于挤压作用仍为液相。随着膜温的升高,外侧螺旋槽之间坝区发生相变,内侧螺旋槽(以下简称“泵出槽”)与泵回槽槽根处共同形成的局部高压区有效的抑制了相变进程,同时泵出槽背风侧扩压作用的影响开始显现,促进了相变的发生,如图4(d)所示。由流线分布可知,当密封介质进入密封间隙后,在泵出槽迎风侧的作用下被泵送至槽根处,形成局部高压使端面分离增强端面润滑性能,但同时也会一定程度地提高密封的泄漏量。当膜温升高至T4时,泵出槽工作区仍为液相,因此泵出槽有着稳定的泵送能力保证密封处于较好的润滑状态。被泵送至泵出槽槽根的介质,经泵回槽槽区流向外径出口处,在泵回槽内流动状态受相变影响较大,液相在迎风侧的作用下泵送至槽根处,而相变后液相转变为汽相导致黏度降低,几乎不受迎风侧影响,直接经过迎风侧由出口流出。在膜温逐渐升高的过程中,相变区域逐步增大,泵回槽内泵送至槽根处的液相减少,以汽相状态产生的泄漏量增大。
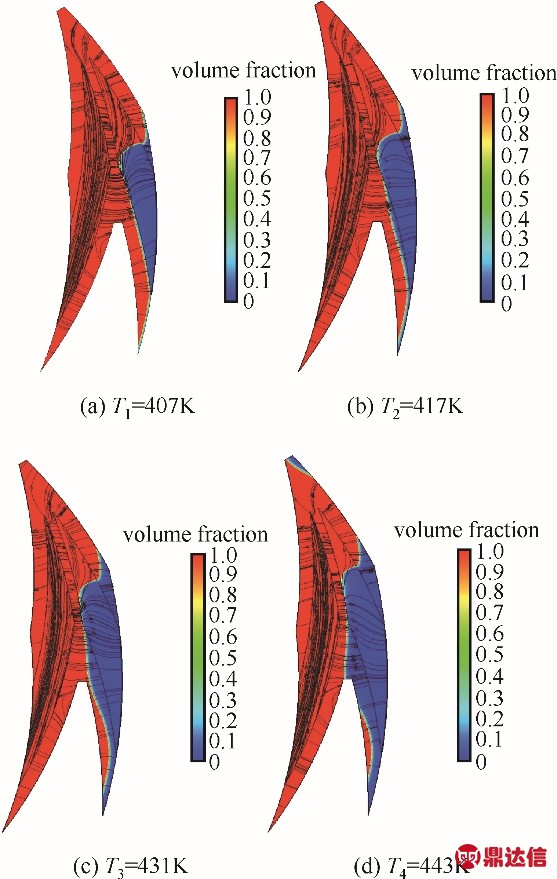
图4 相态分布及流线图
Fig.4 Phase distribution and streamlines
如图5(a)所示,外槽内发生相变后压力分布发生明显改变,参考图4(a)中相态分布,可以发现相变区压力较低且压力梯度较小。随着膜温的升高,泵回槽内液相减少,导致槽根处由挤压作用形成的高压区减小。由于相变可以一定程度上提升端面压力,因此随相变区域的增大,泵回槽内的低压区逐渐减小,如图5(b)~(d)所示。由此看出液膜相变现象不仅改变了端面的润滑状态,同时对间隙内流场与端面压力分布都有着显著的影响。
3.3 结构参数影响分析
由图4可知,液膜发生相变后,其汽液混相区较窄,取汽液混相中汽相占比50%等值线近似表征相变反应区位置,图6、图7分别为膜温T=407 K与T=443 K时的相态分布,图中曲线以上区域为汽相区,曲线以下区域为液相区。
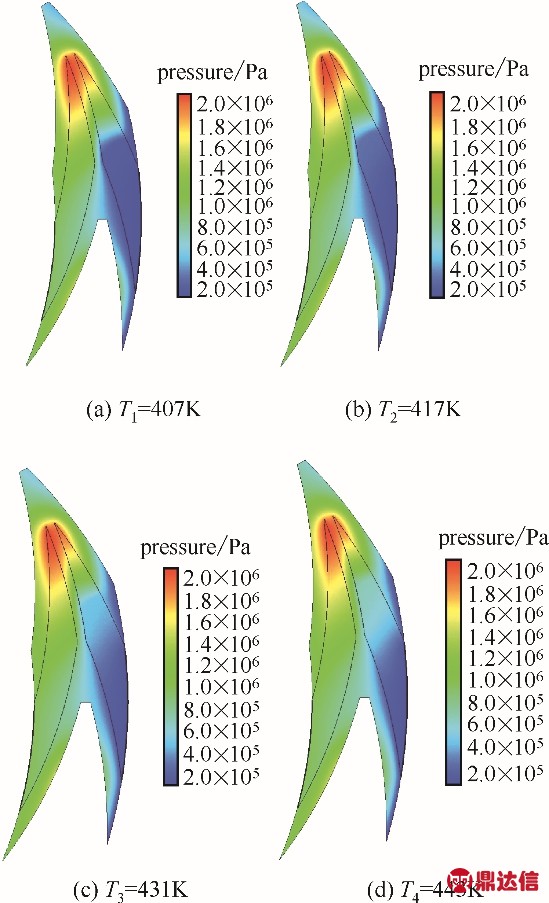
图5 压力分布
Fig.5 Pressure distribution
图6(a)与图7(a)为泵回槽槽深对相变区域的影响。由图6(a)可以看出在膜温T1=407 K时,由于背风侧的扩压作用促使压力降低,导致液相转变为汽相,同时槽根处迎风侧的挤压作用使汽相转变为液相。随着槽深的增大,曲线整体下移(相变区域变大),但曲线最小值仍高于50.25 mm,即相变区域只存在于泵回槽内。当膜温T4=443 K时,相变区域形状出现明显变化且沿径向向内径侧延伸,泵回槽槽区只有槽根迎风侧附近为液相,且随槽深的增加,液相区逐渐减小。由于泵回槽背风侧靠近泵出槽背风侧,因此槽深越大泵回槽背风侧扩压作用越强,相变区域越大,受泵出槽背风侧的影响也就越明显,如图7(a)所示。由于槽深增大促使相变区域面积变大,即液膜相变率增大,使得泵回槽槽区的黏度降低,导致其泵回能力减弱,造成了泄漏量增大,同时由于可泵送至槽根处的液相减小,造成泵回槽动压效应明显减弱,因此端面整体开启力减小,导致密封整体性能降低,如图8所示。
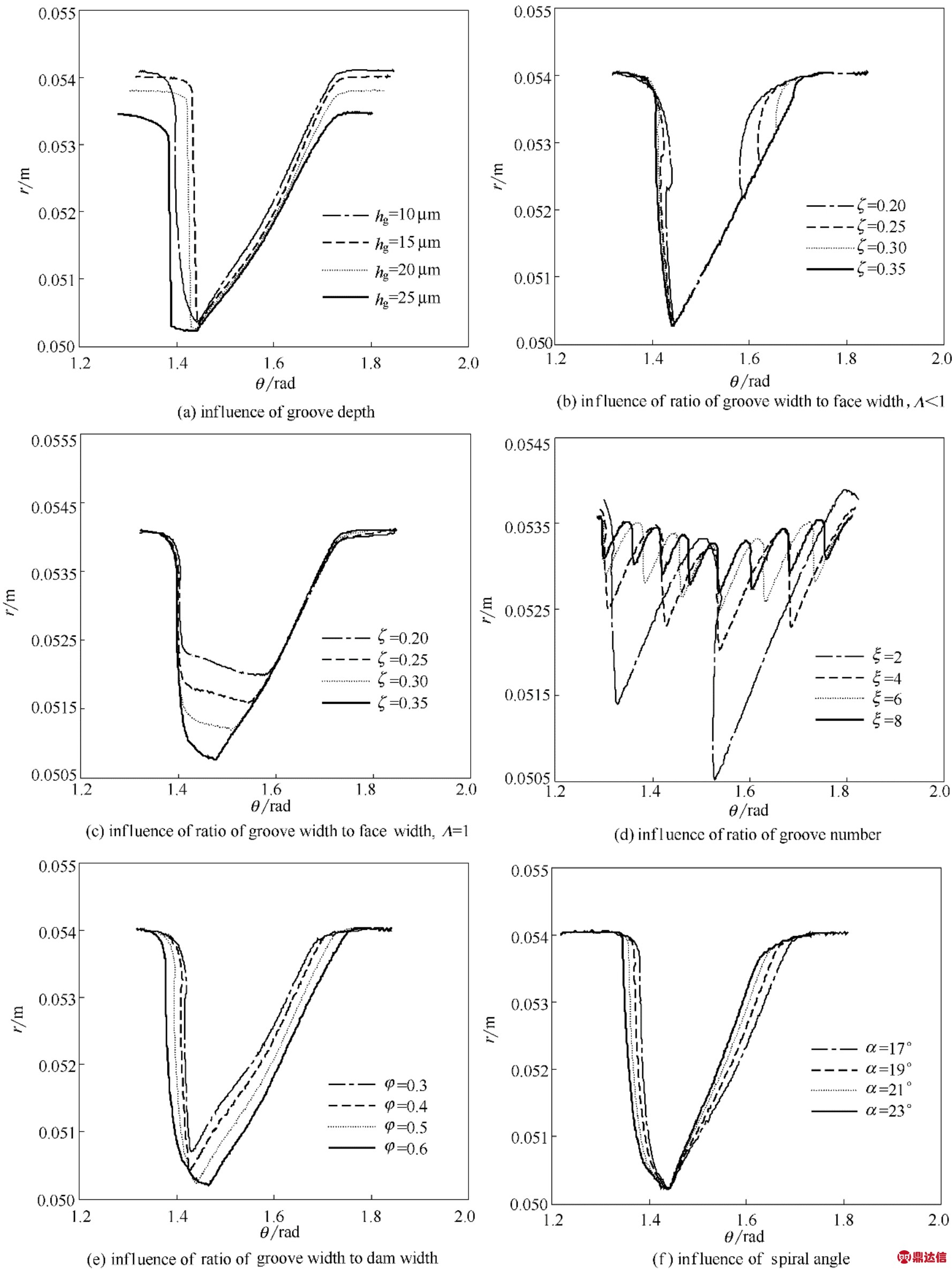
图6 T=407 K时结构参数对相变区域的影响
Fig.6 Influence of structural parameters on phase change region(T=407 K)
图6(b)、图6(c)与图7(b)、图7(c)分别为两种膜温下 Λ<1与 Λ=1时槽面宽比对相变区域的影响。随槽面宽比的增加,当Λ<1时,泵回槽由泵出槽向外径延伸;当Λ=1时,泵回槽由外径向泵出槽延伸。由图可以看出不同膜温下,Λ<1与Λ=1的相变区域面积与形状有着显著的不同,但随着槽面宽比的增加趋于相同。其原因是在槽面宽比较小的情况下,Λ<1时泵回槽受泵出槽产生的高压影响较大,因此相变只发生在背风侧靠近槽根处,随槽面宽比的增加,泵出槽高压区影响逐渐减弱,相变区域面积逐渐增大,即使膜温升高,仍可保证槽根迎风侧附近存在较大的液相区,而Λ=1时泵回槽与外径低压侧联通,且远离泵出槽高压区,导致泵回槽内几乎完全发生相变,膜温升高后更是加大了相变区域的面积。当槽面宽比增大到一定值时,Λ<1时泵回槽将于外径低压侧联通,此时Λ<1与Λ=1的相变区域面积与形状相同。
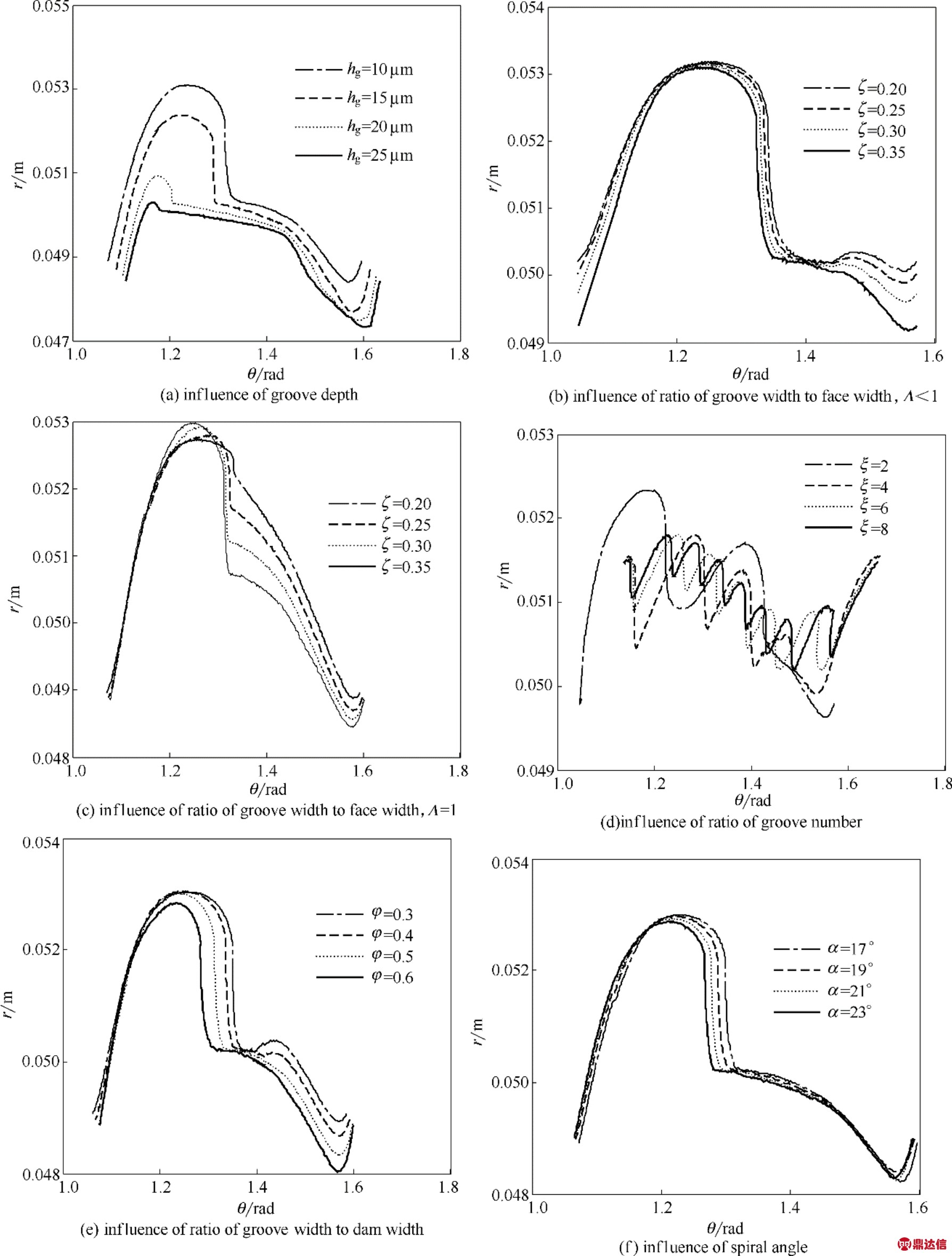
图7 T=443 K时结构参数对相变区域的影响
Fig.7 Influence of structural parameters on phase change region(T=443 K)
对比图9与图10,Λ<1与Λ=1两种情况下,槽面宽比的增加都会促使相变区域变大,导致泵回槽功能减弱,造成密封泄漏量升高与开启力降低,但两种情况下泄漏量的值相差不大,并且相比于Λ=1,Λ<1时液膜相变率更小,开启力更大,因此综合考虑选Λ<1且槽面宽比比值较小时可获得较高的密封性能。
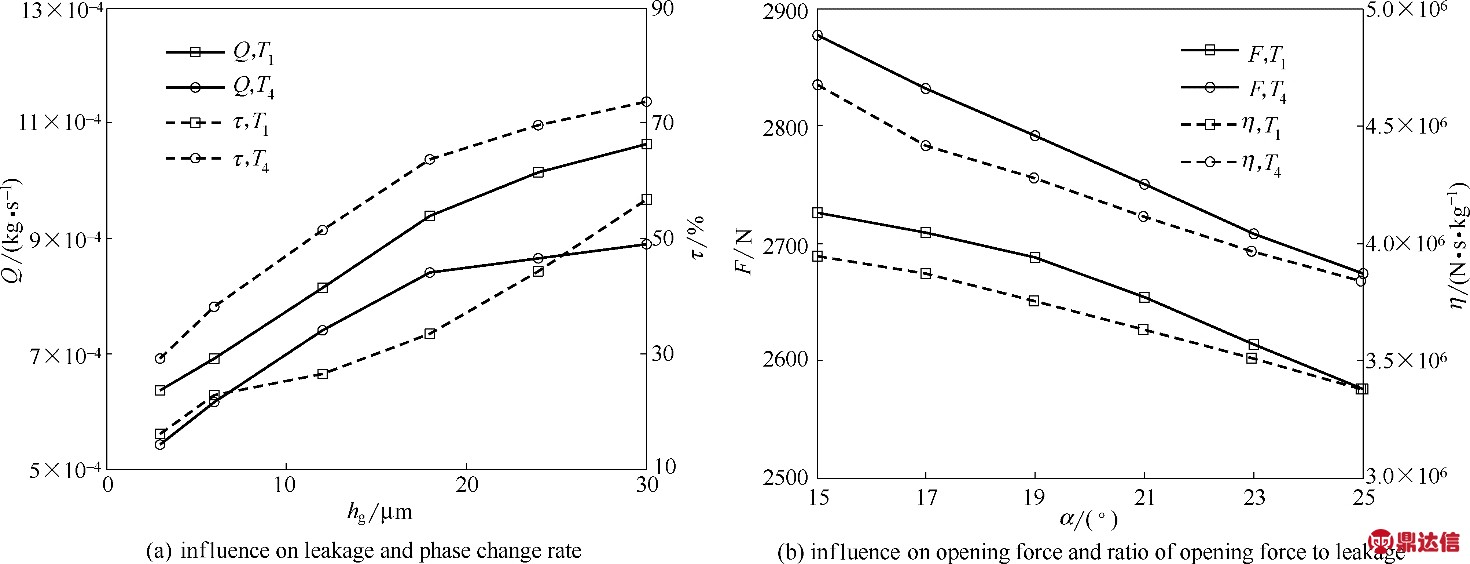
图8 槽深对性能参数的影响
Fig.8 Influence of groove depth on sealing performance
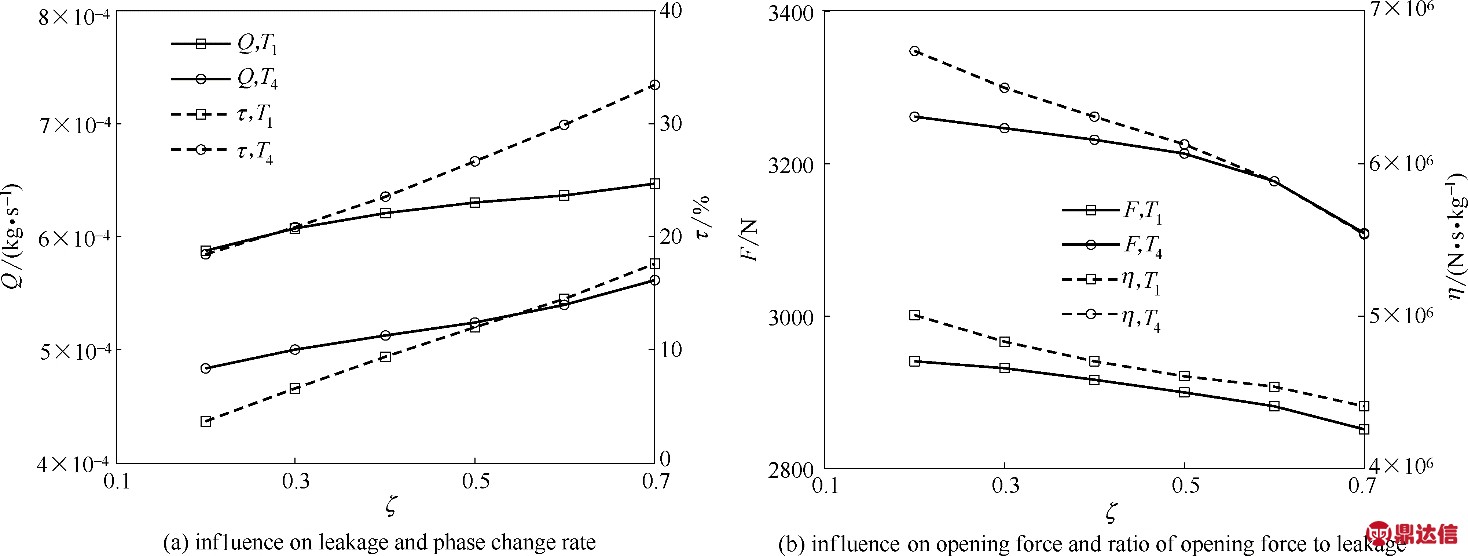
图9 Λ<1时槽面宽比对性能参数的影响
Fig.9 Influence of ratio of groove width to face width on sealing performance(Λ<1)
图6(d)、图7(d)为槽数比对相变区域的影响。由图6(d)可以看出随槽数比的增加原相变区域被分为与槽数相等的几个区域,在单周期内相变区域呈现出先增大后减小的趋势,其原因是受泵出槽所形成压力分布影响所致。但随着槽数的增多,相变区域向外径侧移动,受泵出槽影响逐渐减弱,该趋势也相应的减弱。但随着膜温的升高,相变区域面积扩大,泵回槽槽区为汽相,黏度显著降低,导致泵回槽影响减弱,即使槽数增加,这种趋势依然存在。由于随槽数的增加,相变区域面积减小,泵回槽的泵回能力与其挤压效应增强,因此泄漏量减小,开启力增加,密封整体性能提高。同时由图11(a)中可以看出膜温为 T1时的泄漏量在槽数比大于3时低于膜温为T4时的泄漏量,虽然T4时相变区域更大,其提供的降漏能力更强,但还是弱于泵回槽的泵回能力。
图6(e)、图7(e)为槽台宽比对相变区域的影响。槽内压力分布受迎风侧与背风侧的相互作用影响,槽台宽比较小时,背风侧与迎风侧距离较近,液膜经扩压后立即被挤压,槽内压力变化较小。随槽台宽比的增加,泵回槽槽区周向宽度变大,液膜经背风侧扩压后受挤压影响减弱,压力降低明显,导致汽相区域沿周向向两侧延伸,但径向没有变化,如图6(e)中所示。而膜温为T4时,泵回槽槽根迎风侧抑制相变的能力逐渐减弱,导致相变区域在径向向内径延伸。由此可看出槽台宽比的增大同样会造成泵回槽槽区黏度降低,导致泵回能力减弱,从而造成泄漏量与相变率增加,导致密封性能降低,如图12所示。
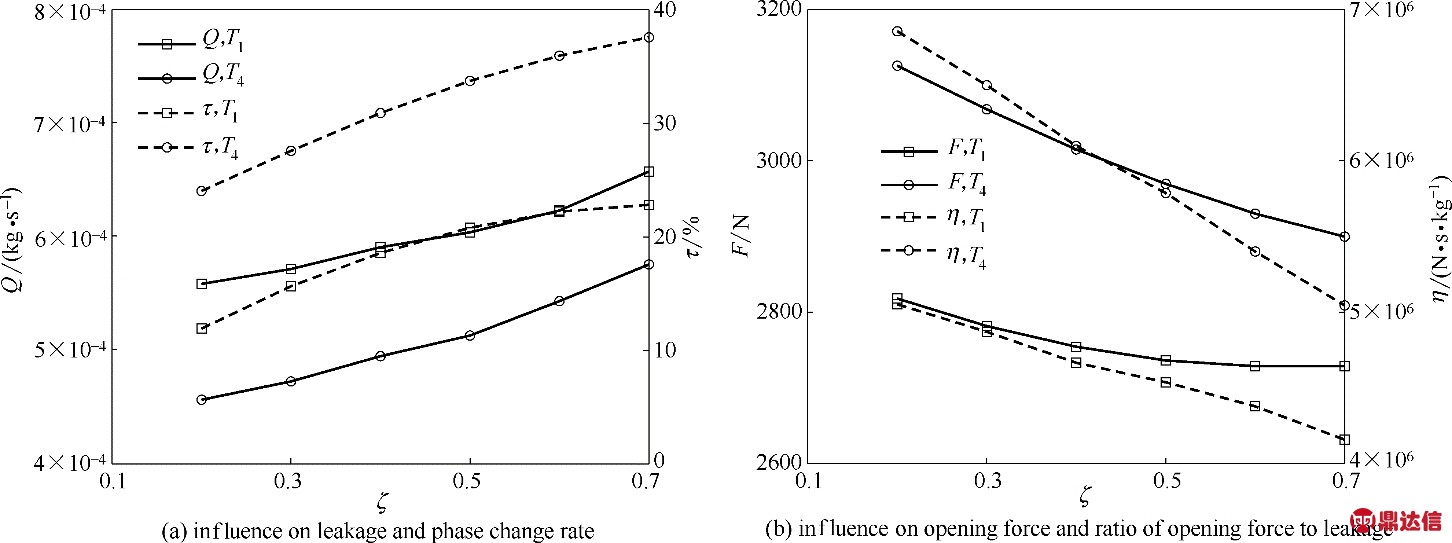
图10 Λ=1时槽面宽比对性能参数的影响
Fig.10 Influence of rate of groove width to face width on sealing performance(Λ=1)
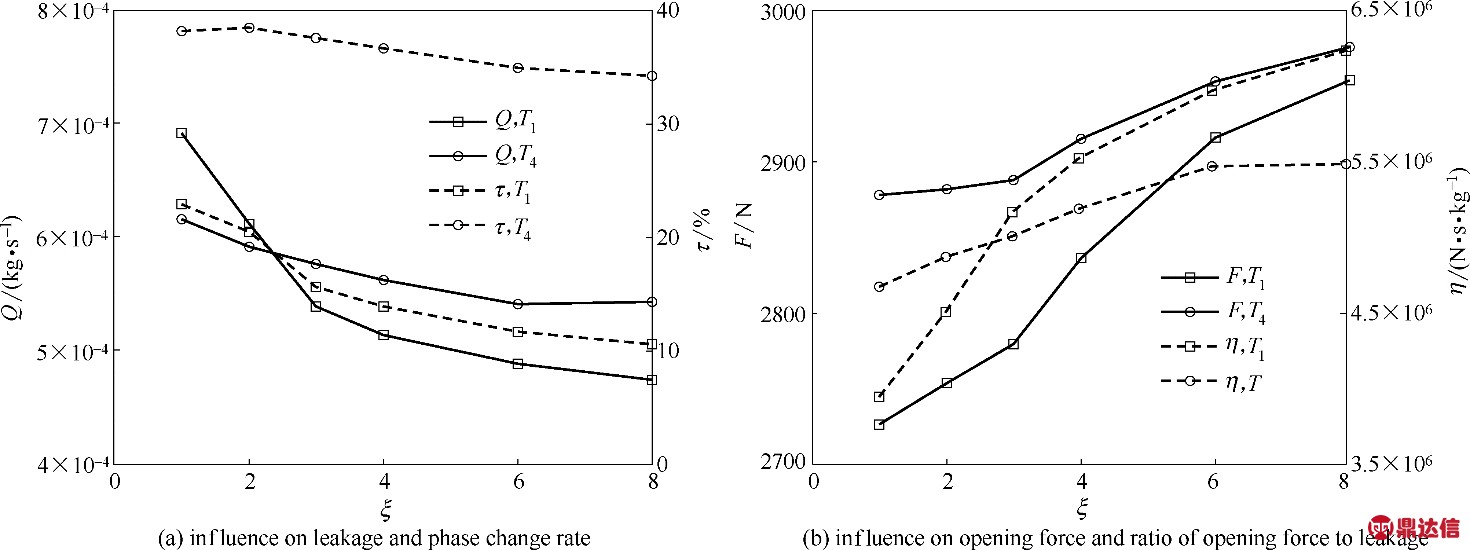
图11 槽数比对性能参数的影响
Fig.11 Influence of ratio of groove number on sealing performance
图6(f)、图7(f)为泵回槽螺旋角αo对相变区域影响。螺旋角αo的变化,改变了泵回槽迎风侧与背风侧的曲率,因此相变区域面积与形状基本没变,只是出现了左移现象。但由图13中看出,虽然相变率不变但泄漏量依然呈现变大的趋势,其原因是由于螺旋角变大,使泵回槽迎风侧工作面面积减小,泵回能力减弱所导致,与其他结构参数影响原因不同。
4 结 论
本文对双列螺旋槽液膜密封相变现象进行了数值模拟,并讨论了结构参数对相变区域与密封性能的影响,得到如下结论。
(1)液膜相变发生后物性参数发生明显变化,从而影响了外侧螺旋槽的泵回能力和动压效应,导致密封间隙内流场与端面压力分布发生明显变化。
(2)不同膜温下,结构参数变化均可导致相变区域以及密封性能发生明显变化。密封泄漏量与相变率随槽深、槽面宽比、槽台宽比与螺旋角的增大而增大,随槽数的增大而减小。而表征密封整体性能的开漏比则随槽深、槽面宽比、槽台宽比与螺旋角的增大而减小,随槽数的增大而增大。相同参数下,外侧螺旋槽中槽型比外槽型相变率更低,开启力更大,密封性能更优。
(3)内侧螺旋槽在增强润滑状态和抑制相变的同时增加了泄漏量,通过对外侧螺旋槽各参数的合理选择,可以有效地降低泄漏量,提高密封整体性能,增强螺旋槽密封在工程应用中的实用性。
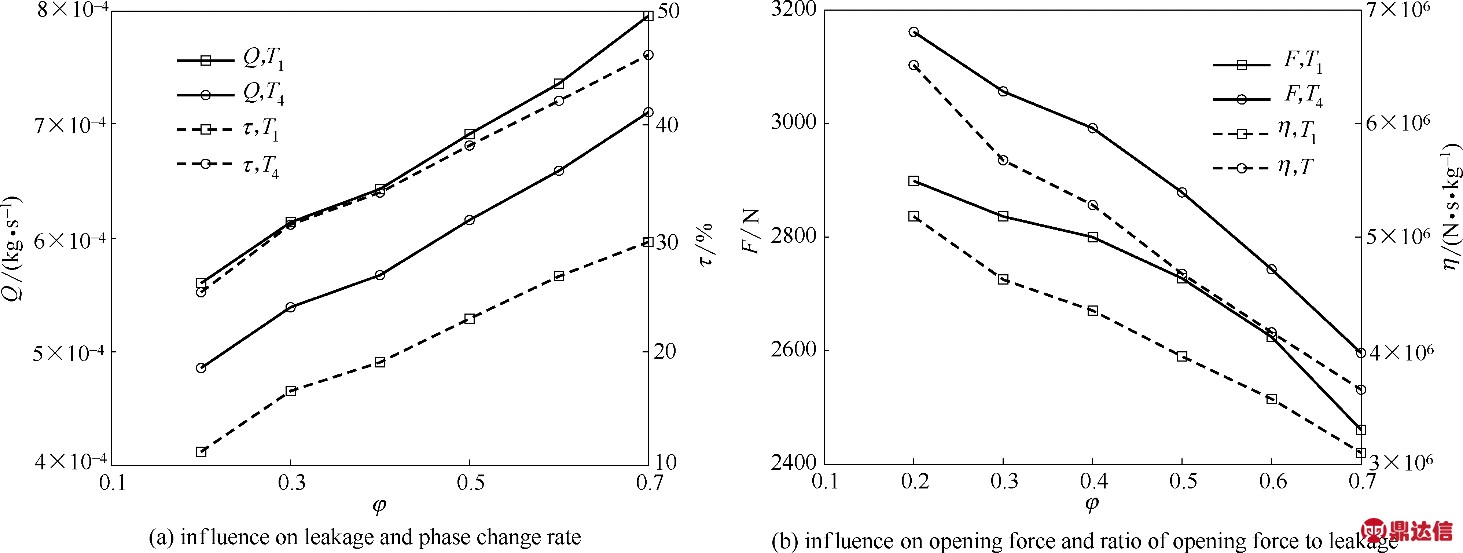
图12 槽台宽比对性能参数的影响
Fig.12 Influence of ratio of groove width to dam width on sealing performance
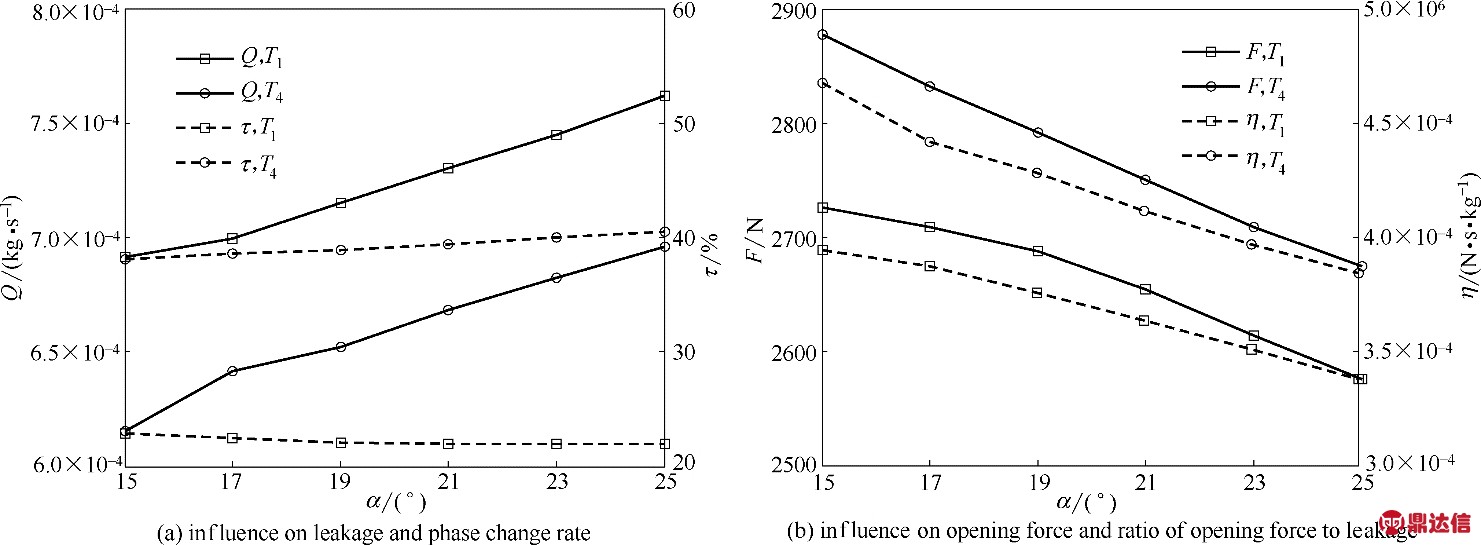
图13 螺旋角对性能参数的影响
Fig.13 Influence of spiral angle on sealing performance
符 号 说 明
d ——相变表面直径,μm
F ——承载力,N
h ——液膜厚度,μm
M ——分子质量,kg·mol−1
Ni ——泵出槽槽数
No ——泵回槽槽数
n ——转速,m·s−1
P ——流体膜压力,Pa
Psat ——饱和压力,Pa
Q ——泄漏量,kg·s−1
R ——气体常数,J·(mol·K)−1
T ——液膜温度,K
u ——流体膜速度,m·s−1
V——体积,m3
α——螺旋角,rad
θ——周向弧度,rad
Λ——槽型系数
μ——动力黏度,Pa·s−1
ρ——密度,kg·m−3
σ——修正系数
φ——混合物汽相质量分数,%
ψ——质量源相,kg·s−1·m−3
下角标
f——相变界面附近液相
i——内径
l——液相
o——外径
r——动环
s ——静环
v ——汽相