摘 要:针对3½"气密封检测工具胶筒的密封性问题,基于流体渗压原理,利用有限元法建立了胶筒及与之接触部件的几何模型和接触关系,以胶筒实际所受载荷顺序,先后施加了胶筒坐封载荷和流体渗透载荷,以此为分析步,设计正交试验,计算了不同结构参数组合下胶筒的压缩密封情况,优选出了最佳尺寸胶筒,并对优选胶筒和配套使用的3½"气密封检测工具进行实物加工后,进行了胶筒密封承压能力试验,试验结果显示,所设计的胶筒至少满足10 MPa以内的密封性检测要求,研究表明,基于流体渗压原理的有限元法分析方法可初步模拟得到实际坐封载荷下胶筒的极限环空密封压力。研究方法为气密封检测工具胶筒结构设计和胶筒密封性能研究提供了新的思路。
关键词:气密封检测工具;密封;橡胶;仿真分析
0 引言
气密封检测工具被广泛应用于完井工程中管柱入井前的密封性检测,通过气密封检测作业能将气密封性不合格的连接丝扣及时找出以便于替换或调整,保证入井管柱后期运行稳定可靠。SY/T6782-2012套管和油管螺纹连接气密封井口检测系统中对气密封检测技术的相关定义是:利用高压氦氮混合气介质作为检测气体,配合氦质谱检漏仪进行现场检测套管和油管螺纹连接密封性能的方法[1]。胶筒为具有一定厚度的中空圆筒,是气密封检测工具的核心部件,在检测作业中胶筒受轴向压缩后密封中心管与油套管之间的环形空间,保证管柱丝扣在完好的情况下环空压力不发生损失,其密封效果直接影响到工具的检测精度。
气密封工具胶筒工作原理与压缩式封隔器胶筒工作原理相似,关于胶筒密封性的研究,国内外学者开展了大量的研究工作。Guo等[2-3]采用ANSYS优化了胶筒内径和锥体锥角,改善了套管与胶筒之间的接触压力,以提高胶筒密封效果。Ma等[4]采用正交试验法研究了胶筒与支撑环、油管、套管之间摩擦系数对胶筒压差和最大接触应力的影响规律。Hu等[5]研究了3种氢化丁腈橡胶材料的胶筒力学性能,并以密封性能K值、最大Mises应力、肩突值为评判指标研究了材料属性对封隔器胶筒密封性能的影响。Wang等[6]用 BDISTS-WIFI测试系统和 Dasylab 软件测试封隔器胶筒坐封后套管的应变,通过拟合的经验公式确定了给定载荷下不同的摩擦力和法向压力。Dorokhov等[7]通过试验装置测试了密封元件的接触应力,以此为基础研究了封隔器密封元件几何特征、测试压力、径向间隙和材料剪切模量对其密封能力的影响。李奎元等[8]分析了JG型压缩式胶筒在弹性变形、约束变形和稳定变形三阶段力和变形的关系,并介绍了胶筒应力松弛对密封性能的影响。Al-Kharusi等[9]推导了溶胀弹性体密封理论计算公式,并采用ABAQUS进行了数值模拟。研究包括材料和几何参数在不同载荷条件下的密封性能影响。仝少凯[10]采用极坐标法和逆解法推导得到胶筒在自由变形和约束变形2个阶段胶筒与套管接触压力和极限密封压力的计算公式,根据流变学和连续理论,建立了胶筒应力松弛和蠕变的理论方程。杨秀娟等[11-12]研究了胶筒与套管间的摩擦系数对接触应力的影响规律,表明摩擦因素的变化对胶筒密封性能有明显的影响。伍开松等[13]应用ANSYS研究了胶筒的几何特征参数和接触压力之间的关系,优化了特征参数值,得到了胶筒总厚度、筒高和胶筒子厚度对胶筒密封性能的影响规律。于桂杰等[14]利用ANSYS分析软件对比分析了常规胶筒和异型胶筒的密封性能,并研究了圆槽半径对胶筒密封性能的影响规律。王国荣等[15]提出了3种方案,使气密封检测工具的上胶筒回弹速度快于下胶筒,实现了工具的非对称解封,有效解决工具在现场解封过程中被顶出套管的问题。何霞等[16]通过改变胶筒表面圆弧半径R、圆弧顶距胶筒表面距离δ、波纹间隙ΔH等参数研究胶筒与套管间接触应力情况,并得到了最佳参数。张付英等[17]利用有限元分析软件分析了胶筒在轴向载荷和扭转载荷共同作用下的接触密封情况,得到了胶筒端面角、子厚度、筒高和摩擦因数变化情况下胶筒与套管接触应力的变化规律。
本文在前人的研究基础上,以3½''气密封检测工具胶筒为研究对象,建立胶筒压缩密封有限元模型,以胶筒实际所受载荷顺序为分析步,计算不同结构参数下胶筒的压缩密封情况,优选出最佳尺寸胶筒,并对最佳尺寸胶筒进行密封承压能力试验。
1 流体渗压原理
胶筒压缩密封之后,在流体压力的作用下,若接触表面被完全撕开,即表明胶筒无法对该大小的流体压力进行有效密封,被完全撕开瞬间的流体压力即为胶筒在对应的轴向压力下能密封的极限压力,若接触表面未被完全撕开,即表明胶筒在对应的轴向压力下的密封承压能力至少达到该压力值,能对其进行有效密封。Abaqus/Standard允许模拟流体渗入2个接触表面并施加垂直于接触表面的流体压力,如图1所示,接触对中从面由一阶单元1,2的表面组成,节点101,102,103为从面上3个节点;主面由一阶单元3,4的表面组成,节点201,202,203为主面上3个节点。将节点101和节点201作为流体压力加载的起点,分别往节点102和节点202方向传递,这一过程中流体压力既有撕开当前网格单元的作用也有压缩后续网格单元的作用。当流体压力传至节点102和主面上与其相对应的D点时,若节点102的接触应力减小为0,表明在流体压力作用下该点与主面由接触变为分离(或仅仅贴合而未产生挤压),流体压力可以继续往节点103和节点203方向传递;若节点102的接触应力大于0,表明在流体压力作用下该点与主面仍然保持接触状态,流体压力无法继续往后传递。
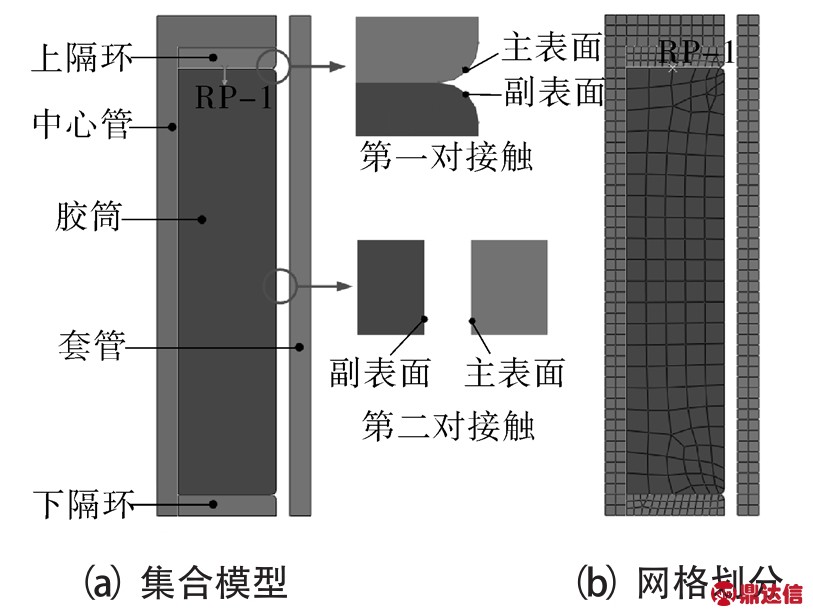
图1 流体渗压载荷施加示意
2 胶筒压缩密封有限元模型建立
根据上述理论和气密封工具结构建立了胶筒压缩密封有限元模型,如图2(a)所示。选取上隔环顶面中部位置建立一参考点RP-1,并建立该点与上隔环顶面的耦合关系,在该参考点上施加垂直向下的力载荷。以胶筒上端面和上隔环圆弧面作为流体渗透压力施加的第一对接触对,其中上隔环圆弧面作为主面,胶筒上端面作为从面;以胶筒外侧与油管或套管内侧接触面作为流体渗透压力施加的第二对接触对,其中油管或套管内表面作为主面,胶筒外侧表面作为从面;针对两对流体渗透压力加载的接触对,分别指定主面和从面上未接触的一点作为流体压力加载起点,流体压力从这四点开始,分别沿2个接触对的主面和从面向仍然保持接触的部位传递。网格划分结果如图2(b)所示。
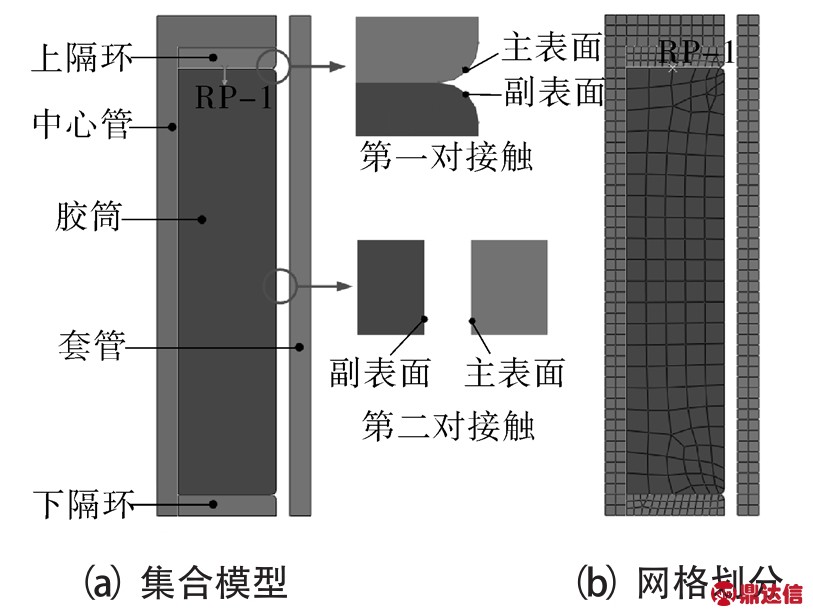
图2 胶筒压缩密封有限元模型
3 胶筒密封承压能力正交试验
设计了不同尺寸参数下的胶筒密封承压能力正交试验。由于大载荷下胶筒容易产生网格畸变,导致求解中断,因此,对10 MPa轴向压力下(对应的轴向力为26 860 N)的胶筒施加环空流体渗透压力。将胶筒外径、内径和高度作为影响因素,每个因素各设置四个水平,得到如表1所示的因素水平。
表1 胶筒压缩密封因素水平
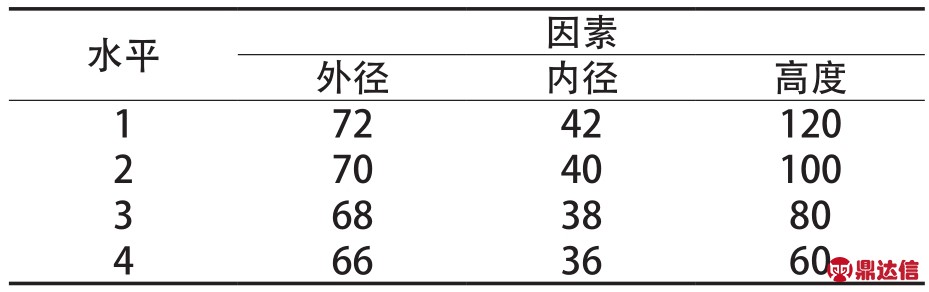
此试验为三因素四水平试验,选用L16(45)正交表最合适,其中3个因素分别占正交表前三列,后两列为空列,如表2所示。
表2 胶筒压缩密封正交试验极差分析结果
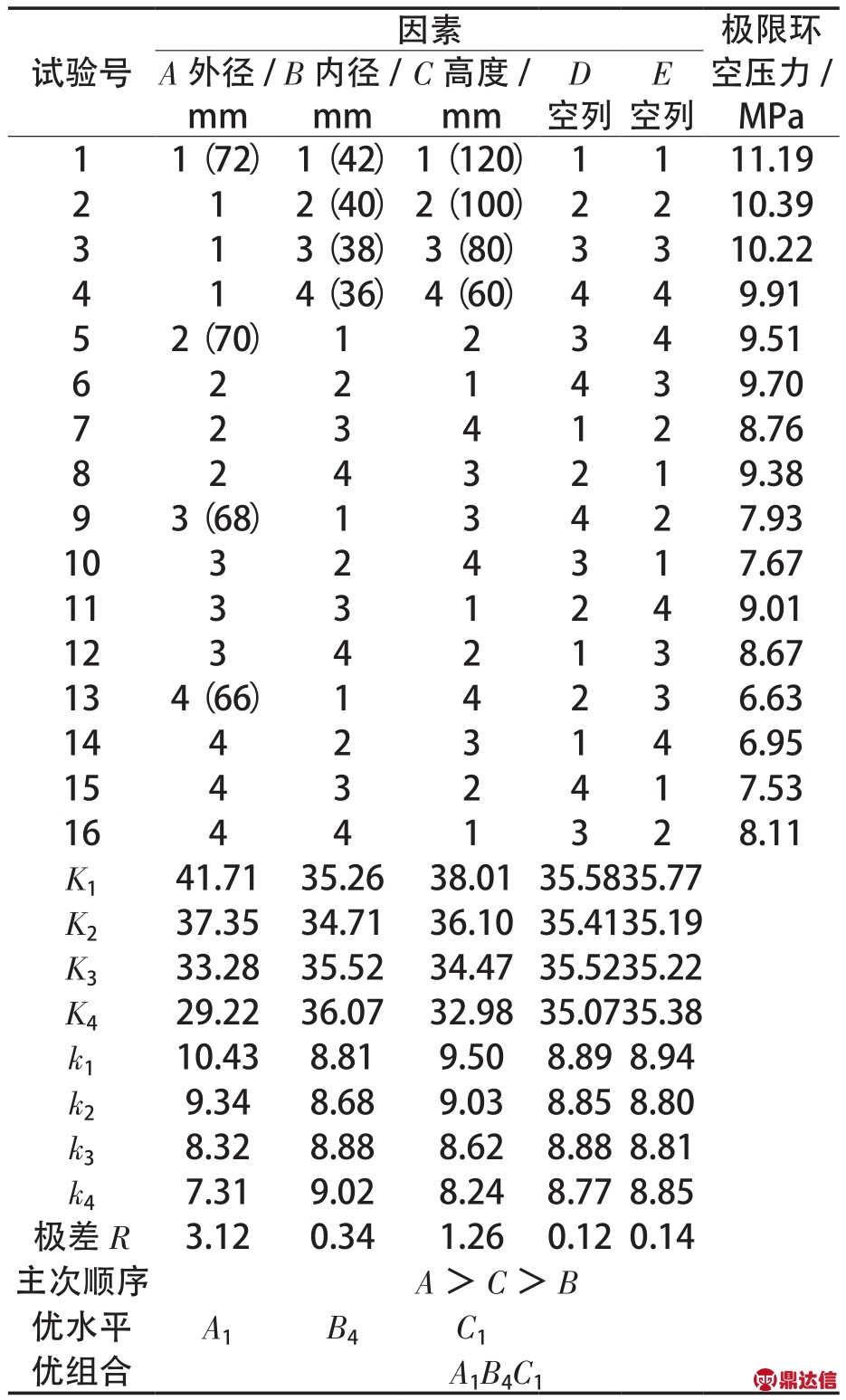
图3所示为正交试验第1组胶筒外侧接触边被环空流体渗透压力完全撕开瞬间,流体渗透压力沿胶筒上端部和外侧分布云图,被撕开的部位完全暴露于流体中,因此各处流体渗透压力大小相等。
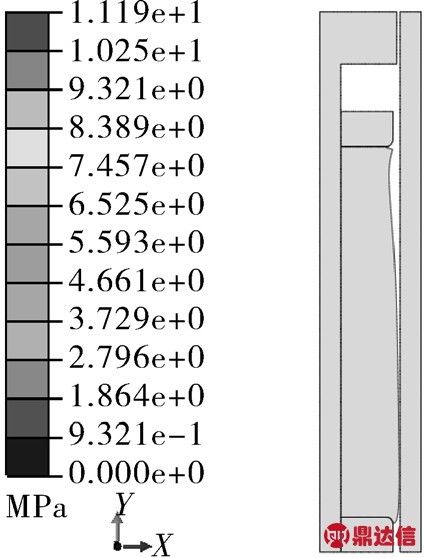
图3 第1组胶筒的环空流体渗透压力云图
随着胶筒上端面和外侧面流体渗透压力的施加,接触面在被流体逐渐撕开的同时,剩余未被撕开部分在轴向压力和流体渗透压力共同作用下被压缩的程度增大,需要施加更大的流体渗透压力才能继续撕开剩余接触部分并将压力往后传递,随着胶筒外侧面被撕开后暴露于流体中的面积逐渐增加以及流体渗透压力的逐渐增大,胶筒受到的径向压力逐渐增大,当超过一定程度后,胶筒在轴向上将会发生回弹,当流体渗透压力继续增加至足够大时,胶筒接触边将被完全撕开,密封也随之失效。
以胶筒所能承受的极限环空压力大小作为胶筒压缩密封承压能力的评判标准,对16组正交试验结果进行极差分析,极差分析结果如表2所示,其中 K1,K2,K3,K4分别表示各因素的 1 水平、2 水平、3 水平和 4 水平的试验结果总和,而 k1,k2,k3,k4分别表示上述各总和的平均值。
由表2可以看出,10 MPa轴向压力下各尺寸参数对胶筒密封能力的影响主次顺序为:外径>高度>内径。当胶筒外径在66~72 mm范围内时,随着胶筒外径增大,胶筒所能承受的极限环空压力增加。最优尺寸组合为胶筒外径72 mm、内径36 mm、高度120mm。
由图4可知,正交试验1,2,3组胶筒的接触应力均高于10 MPa,说明该组合密封效果良好,能满足气密封检测工具的实际检测要求,另外根据计算,选出的最优尺寸组合也满足要求,其接触应力云图如图所示。该尺寸胶筒密封压力最高,将作为实际胶筒尺寸加工后进行密封承压能力试验。
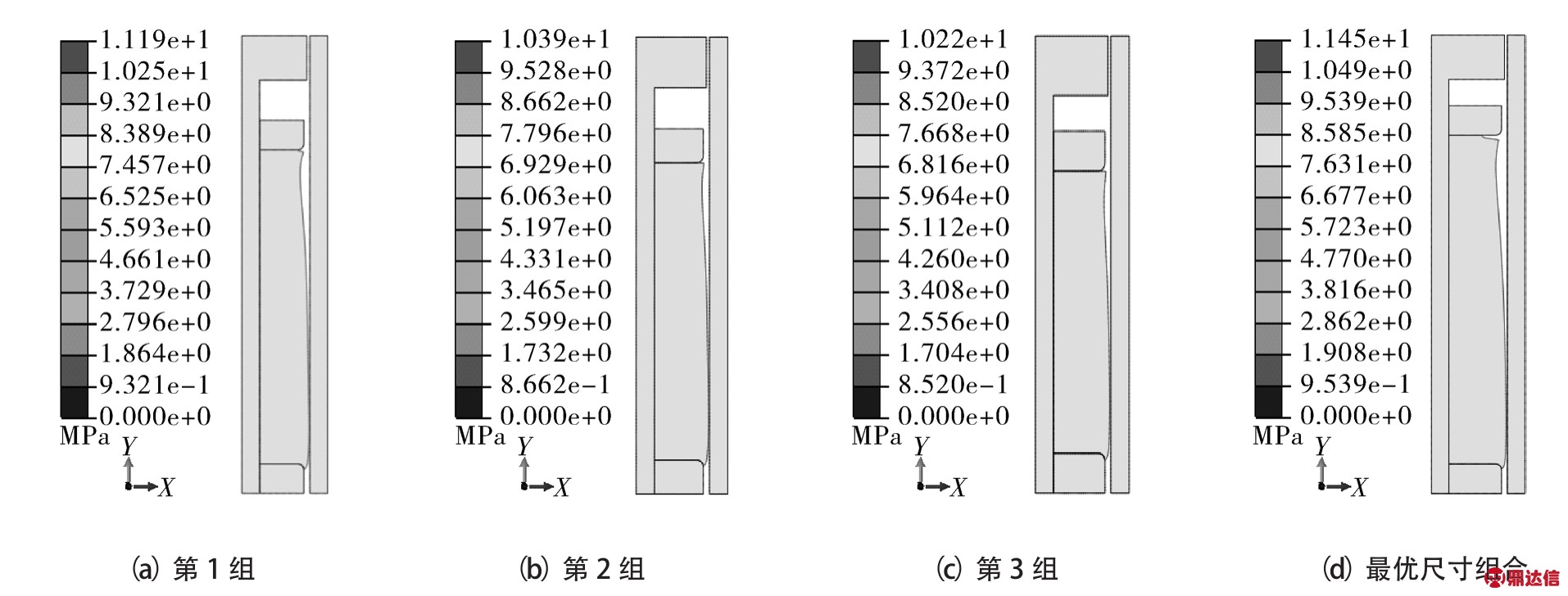
图4 胶筒优选组别流体渗压云图
4 胶筒密封承压能力试验研究
基于以上仿真分析结果,以外径72 mm、内径36 mm和高度120 mm作为胶筒的尺寸参数,对胶筒和3½''气密封检测工具进行实物加工,然后进行胶筒密封承压能力试验。
4.1 试验方案
用堵头替换工具阀座内的进气阀和回气阀,切断工具内部与环空的连接通道,然后将工具放入钢管内,对工具内部和环空分别进行打压,得到在一定轴向压力下胶筒所能密封的极限环空压力,进而验证胶筒压缩密封承压能力仿真分析的准确性。
双线路打压试验方案如图5所示。首先电动试压泵1向工具内加压使胶筒轴向受压接触密封,然后电动试压泵2向钢管与上下胶筒形成的环空密闭腔室加压使胶筒密封承压。溢流阀1,2分别安装在电动试压泵1,2的压力输出管线上,其作用是调节输出压力大小;截止阀1,2分别安装在电动试压泵1,2的输出管线上,其作用是保证输出压力调节好之后再向工具内部通道和环空密闭腔室输出压力。压力传感器1,2分别与数显表1,2相连,从表中可读出轴向压力和环空压力的实时数据。
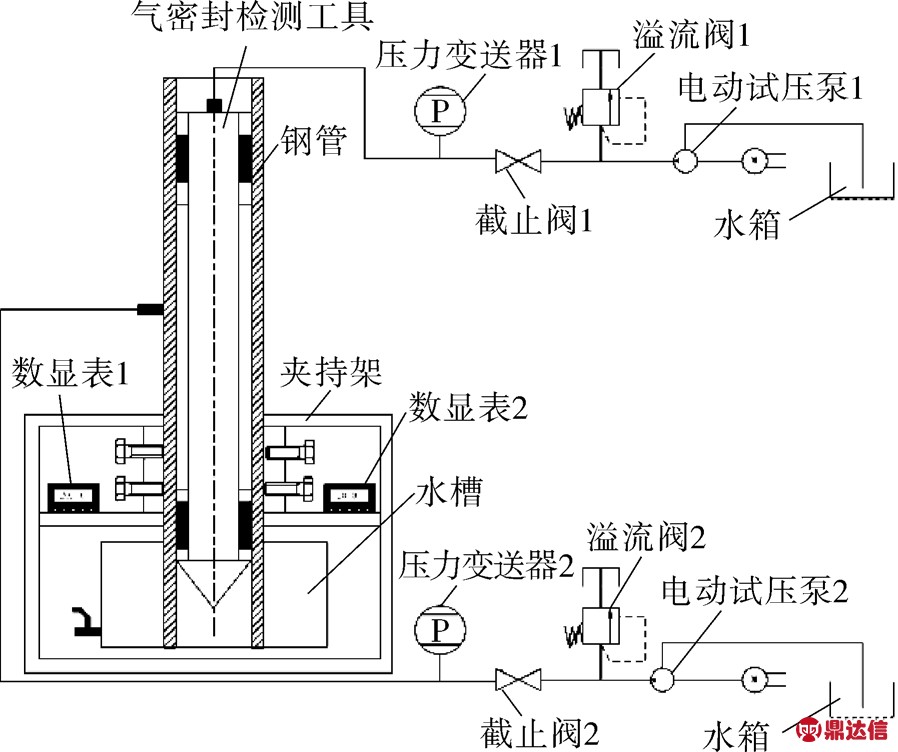
图5 试验方案
4.2 试验设备
试验台架主要由槽钢焊接,台面中部通孔上周向布置若干螺栓用来紧固钢管(模拟套管),防止钢管在试验过程中产生晃动,使其轴线方向始终与水平面保持垂直,可减小由于钢管与气密封检测工具轴线偏移而产生的误差。
主要试验设备如表3所示。
表3 主要试验设备
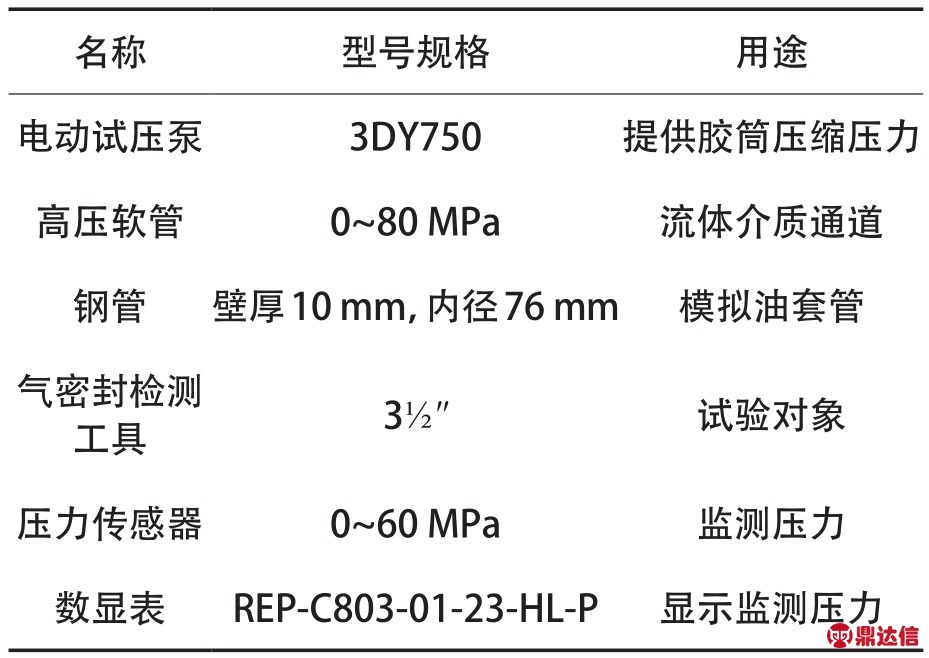
为了尽可能准确地模拟气密封检测工具实际作业时的工况,做了如下设置:(1)流体压力介质选用清水代替氦氮混合气体;(2)用壁厚10 mm、内径76 mm的钢管模拟壁厚为7.34 mm、内径为76 mm的3½''油管,钢管的强度、内壁粗糙度均符合试验要求;(3)气密封检测工具用天车悬吊,确保试验开始前工具处于自由悬空状态。
4.3 试验步骤
双线路打压主要试验步骤如下:
(1)用天车将气密封检测工具下放至钢管内,使钢管中部与电动试压泵连接的小孔处于上下胶筒之间的位置;
(2)开启电动试压泵1,将流体向气密封检测工具内部通道泵送,待数显表1读数在调定值10 MPa附近稳定后,关闭电动试压泵1;
(3)开启电动试压泵2,将高压流体向环空密闭腔室泵送,在数显表2读数上升过程中,观察钢管上下端部是否发生泄漏以及数显表2读数是否发生突然下降,若均未发生,当数显表2读数稳定在10 MPa附近后,增加电动试压泵2的输出压力,每当数显表2读数上升幅度接近1 MPa时停止加压一段时间,待压力逐渐稳定,重复上一过程,持续观察数显表2读数和钢管上下端部情况,直至数显表2读数发生突然下降或钢管上下端部发生明显泄漏,记录泄漏前一瞬间数显表2读数,作为10 MPa压缩轴向压力下胶筒所能承受的极限环空压力;共进行5次试验,记录每次试验数据。
4.4 试验结果及分析
当工具内部压力为10 MPa时,五次试验测得的钢管上部或下部发生明显泄漏瞬间的环空压力值如表4所示,该数值即可认为是10 MPa轴向压力下胶筒所能承受的极限环空压力。
表4 双线路加压试验数据
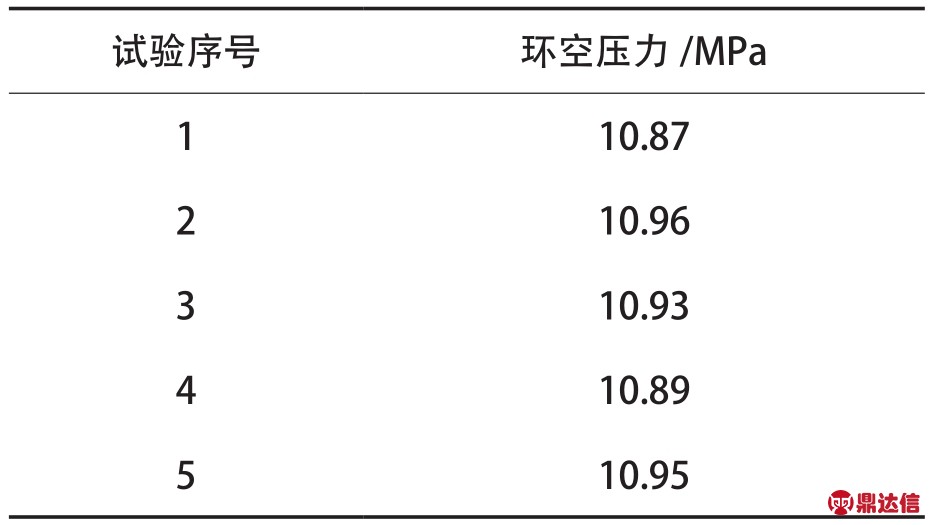
为减小人为因素导致的误差,将5组环空压力试验数据取平均值后得到10.92 MPa,与正交试验得到的结果值11.45 MPa比较,仿真计算结果与试验结果比较接近,相对误差为4.85%,在可接受范围内。这一结果验证了流体渗压原理在胶筒压缩密封仿真分析中的准确性,说明所设计的胶筒至少满足10 MPa压力等级范围内工具的实际检测作业要求。
5 结论
(1)在10 MPa坐封压力下,基于流体渗压原理的有限元分析方法得到的胶筒极限环空密封压力与试验结果基本一致。
(2)通过正交试验得到,胶筒各尺寸参数对胶筒密封性影响的主次顺序为:外径>高度>内径;最优尺寸组合为胶筒外径72 mm、内径36 mm、高度120 mm,此胶筒至少满足10 MPa以内的实际检测作业要求。
(3)基于流体渗压原理的胶筒压缩接触密封有限元分析方法,可初步模拟得到实际坐封载荷下胶筒的极限环空密封压力.