摘要: 为了整体提高轴流泵的水力优化设计水平,找出影响轴流泵性能的主要几何参数,运用正交试验方法,以扬程、效率、轴功率和压力脉动作为试验评判指标,将综合频率分析法应用到轴流泵多目标优化设计中。基于L9(34)正交表得到了9组方案,研究叶片数、翼型、轮毂比和叶片与导叶间距离对轴流泵的扬程、效率、轴功率和压力脉动的影响规律,并通过综合频率分析法确定了一组最佳试验方案。结果表明:该最佳试验方案在设计流量下,水流在叶轮及导叶段中的流态较好,水流流线顺畅,分布相对均匀;轴流泵模型在流量和扬程满足改型要求的同时,效率提高了5.7%;轴功率下降了1.21%;压力脉动系数降低了11%,验证了综合频率分析法在多目标正交优化中的可行性。
关键词: 轴流泵; 多目标优化; 正交试验; 综合频率分析法
引言
轴流泵在农田灌溉和调水工程中有着广泛的应用[1]。轴流泵内部的流动状态十分复杂,其复杂的流动状态导致泵内出现压力脉动现象,进而影响机组的稳定运行[2-3]。因此,在轴流泵流量、扬程、效率和轴功率满足设计要求的前提下,提高轴流泵机组运行的稳定性是未来水泵优化设计的一项重要任务。
石丽建等[4]通过改变叶轮的几何设计参数,采用数值模拟对轴流泵进行多工况优化设计,结果表明,轴流泵在非设计工况下的运行效率显著提高,拓宽了轴流泵高效区范围。杨帆等[5]研究了可调后置导叶对轴流泵水力性能的影响,结果发现通过调节后置导叶可改善导叶体内水流流态,达到了减弱甚至消除进口冲角及尾部脱流等不良流态的目的,从而提高泵装置的水力效率。王秀勇等[6]为提高核主泵整机水力性能,以AP1000型核主泵为研究对象,选取导叶进口角冲角等为正交试验因素,优化后的模型较原模型的扬程和效率增加显著。为了优化旋流泵的水力性能,采用正交试验方法,分别选取了不同的试验因素对旋流泵叶轮进行优化设计,找出了影响旋流泵性能的主要结构参数,结果表明,正交优化结合数值模拟可大大减少工作量,优化后的旋流泵模型扬程和效率都有显著提高,验证了正交试验在泵优化设计方面的可行性[7-9]。司乔瑞等[10]将叶频噪声声压级作为判断离心泵设计水平的其中一项指标,在正交试验的基础上借助计算流体力学和计算声学的数值模拟方法,并通过权矩阵分析得出了一组最佳的离心泵几何参数组合。
上述研究主要集中在将泵的流量和扬程作为优化的考察指标[11-13],但到目前为止,将泵的稳定性作为其中一项考察指标的文献还较少。本文以某低扬程轴流泵为研究对象,研究叶片数、翼型、轮毂比和叶片与导叶间距离对轴流泵装置的扬程、轴功率、效率和压力脉动的影响,以期寻找一种高效稳定的轴流泵水力优化设计方法。
1 多指标正交试验理论
1.1 多指标正交试验优化方法
传统的水泵优化方法主要是将多目标优化转换为单指标分析,靠设计者的经验对已有的水泵模型参数进行修改,这种优化设计方法工作量大、效率低。正交试验设计是利用一套规格正交表,安排试验,通过部分试验了解全面试验的情况寻找试验因素对轴流泵各指标的影响规律及主次顺序,确定轴流泵的最优设计参数组合[14]。
通常情况下,在分析所选取试验因素对试验指标的影响时,如果是单指标,且不考虑试验因素间的相互作用,则正交试验所选取的各试验因素最好的水平组合被认为是最佳的几何因素组合。但本次优化选取了多个评判指标,属于多指标正交试验,需要综合考虑因素水平对试验评判指标影响的主次,且最佳的试验方案并不一定在所设计的几组试验中。因此,本文采用综合频率分析法来确定最佳试验方案,其确定最佳试验方案的方法为:如果多指标正交试验的评判指标具有同等权重,则按照因素水平频率出现的高低排序,优先选择出现频率高的因素水平;若因素水平具有相同的频率,则根据生产成本高低及操作的难易程度来确定顺序[15]。
1.2 试验方案的确定
(1)确定考察指标,明确试验目的。试验目的是提高轴流泵水力性能,选取了4个试验评判指标:扬程、效率、轴功率和压力脉动,在水泵优化中,扬程是设计参数,属于判据性指标。
(2)设计因素水平表。根据轴流泵结构设计要求[16],本次试验选择对轴流泵性能具有显著影响的叶片数(因素A)、翼型(因素B)、轮毂比(因素C)和导叶与叶片间的距离(因素D)4个因素进行正交试验,每个因素选取3个水平。
(3)制定正交表,进行正交试验。根据正交试验原理,设计四因素三水平正交试验方案L9(34),如表1所示,探索这4个试验因素对轴流泵性能及稳定性的影响规律。
表1 正交试验方案
Tab.1 Orthogonal experiment scheme
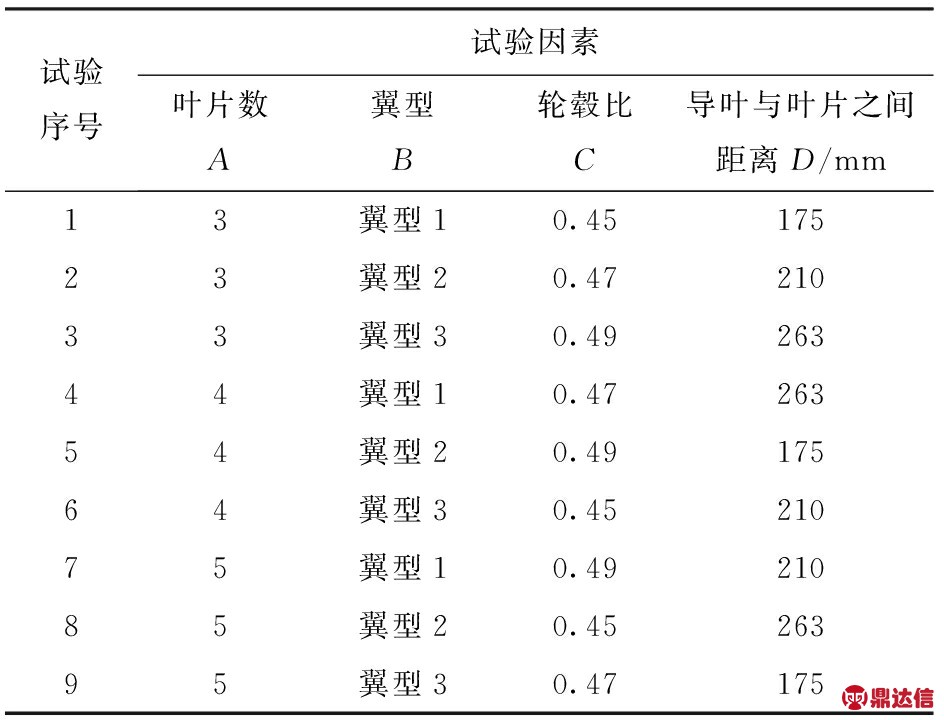
其中各断面翼型安放角的变化如图1所示,其中相对半径为叶片截面上某点的半径与转轮室半径的比值。
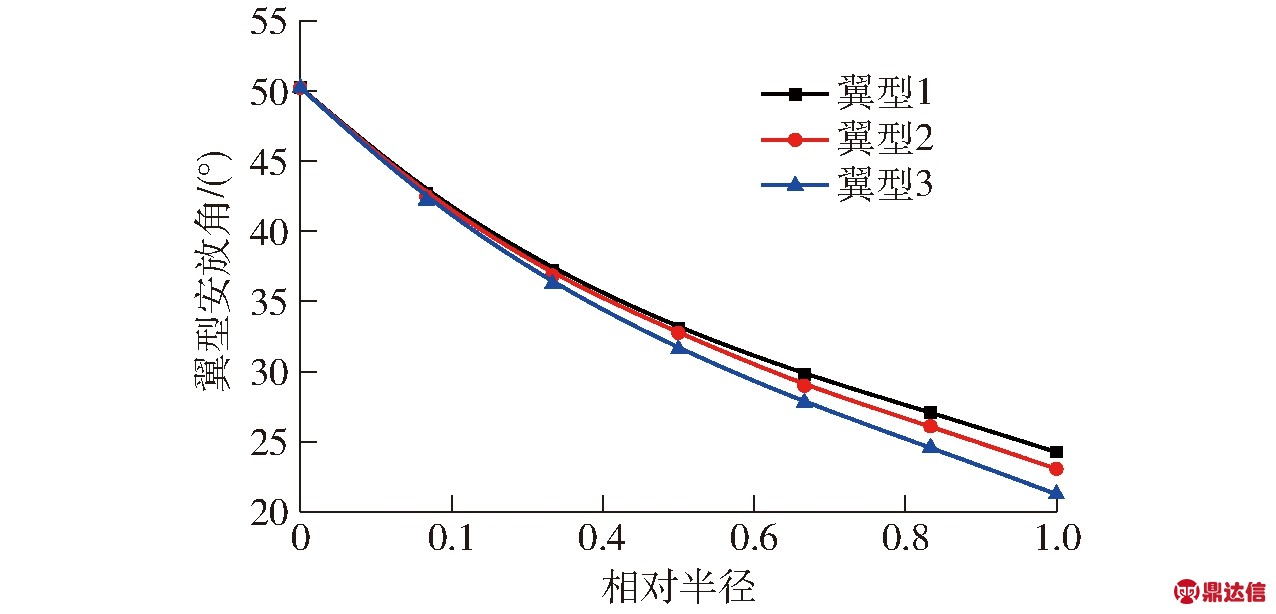
图1 各断面翼型安放角变化
Fig.1 Changes of airfoil seating angle for each section
2 数值计算
2.1 计算域及网格
江都一站、二站经过多年的运行,运行工况已经发生变化,为了解决其长期偏离设计工况运行的问题,研究适合现行运行工况条件的水泵模型,需要对2座泵站的轴流泵模型进行优化。本文中轴流泵原始模型基本参数如下:设计流量Q=298.6 L/s,设计扬程H=6.8 m,转速n=1 461 r/min,叶片数Z=4。改型要求是设计流量在原来基础上提高10%,即新的设计流量Q=328.5 L/s,新的设计扬程增大为7.8 m。计算域包括弯肘型进水流道段、叶轮、导叶、出水弯管和虹吸式出水流道段,如图2所示。
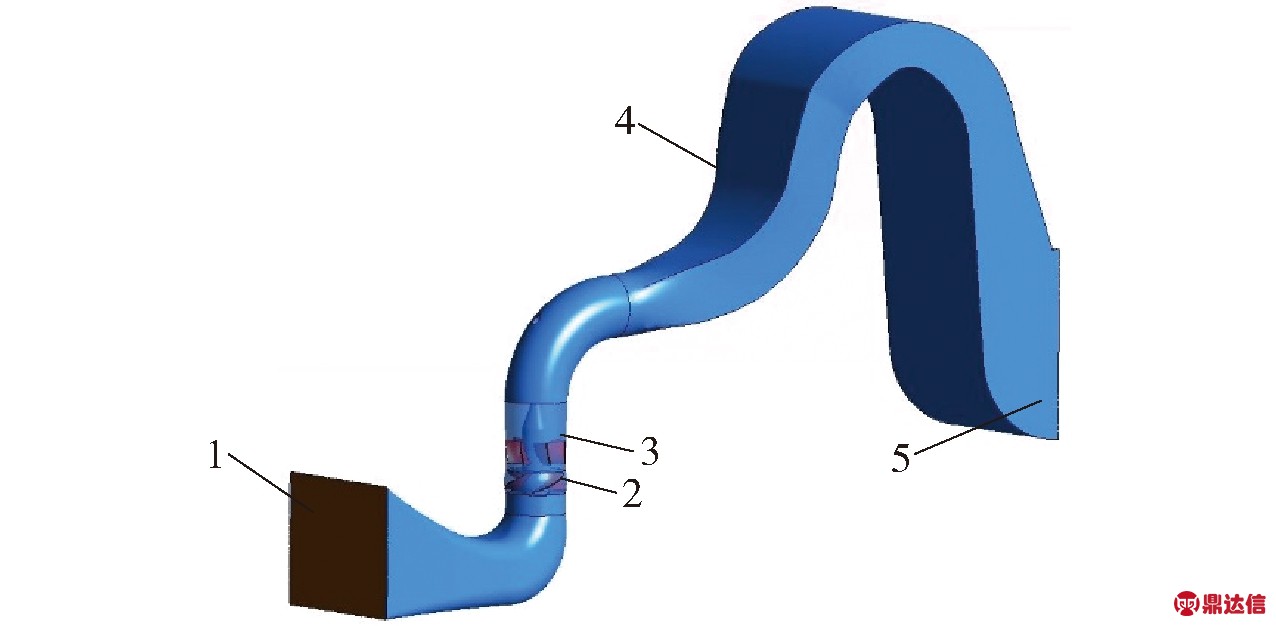
图2 轴流泵的计算域
Fig.2 Calculation domain of axial-flow pump
1.上游进口 2.叶轮 3.导叶 4.虹吸式出水流道 5.下游出口
采用ICEM CFD软件对计算域进行网格划分,考虑到整个模型几何形状复杂且不规则,故采用适应性较强的非结构化网格。为提高数值模拟的准确性,对轴流泵的叶片和导叶部分进行局部加密。并添加边界层网格,将边界层厚度无量纲系数yplus控制在300以内。进行网格无关性验证,考虑到相同的收敛精度(10-5),网格数大于320万时,扬程的相对差值在1%以内,综合考虑计算精度与节省计算机资源,确定最终计算网格数为321万左右。
2.2 计算方法及边界条件
1∶1万土壤化学测量圈定出六处综合异常区编号为AP1~AP6,其中AP1和AP3综合化探异常明显优于其它异常,成矿潜力较大,在本文加以重点介绍。现将两个化探综合异常区的主要特征概述如下:
非定常求解时,时间步长为3.42×10-4 s,即每个时间步长内叶轮旋转3°。为了更好地获取轴流泵内部压力脉动信息,在叶轮进出口和导叶的中部及出口处设置了4组压力脉动监测点,如图3所示。为保证非定常压力脉动计算的准确性及节约计算机资源,本文非定常计算采样时间为8个周期,即叶轮旋转8圈,并取最后2个周期的结果作为压力脉动特性分析的数据。
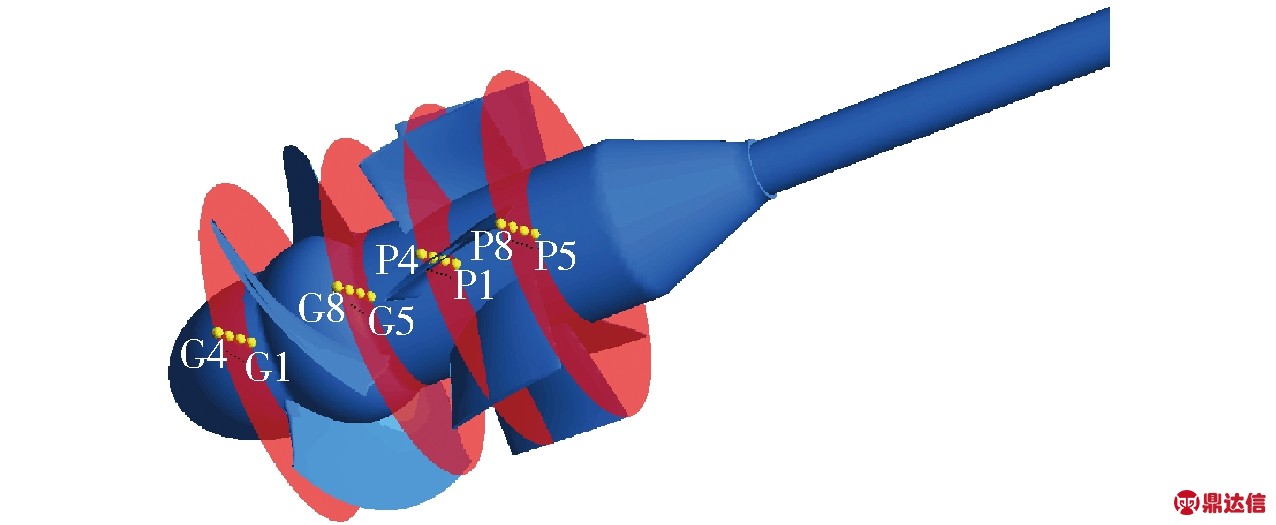
图3 轴流泵内部监测点设置
Fig.3 Set of axial-flow internal monitoring points
2.3 数值计算结果
对9种不同方案在设计流量点处的轴流泵装置进行计算。参照前人研究及本次计算结果可知,轴流泵内的压力脉动主要是由叶片与导叶的动静干涉作用产生的,压力脉动幅值在叶轮出口处最大,因此,选用叶轮出口的计算结果作为本次优化的压力脉动评判数据。通过数值计算得到了轴流泵内部各监测点的压力脉动时域信息,定义一个无量纲的压力脉动系数Cp来描述各监测点的压力脉动特性,其表达式为
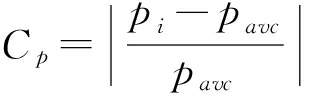
(1)
式中 Cp——无量纲压力脉动系数 pi——监测点在某一时刻静压,Pa pavc——1个转动周期内静压平均值,Pa
9种试验方案下的计算结果如表2所示。
表2 设计流量点处数值模拟结果Tab.2 Summary of design flow numerical simulation results

3 优化设计
根据数值模拟计算结果,对正交试验的4个考察指标进行分析。先对每个考察指标进行单指标的直观分析,然后再利用直观分析结果进行极差分析,最终,根据直观分析与极差分析得到的结果运用综合频率分析法进行分析,确定最佳试验方案。
3.1 直观分析
对9次试验的计算结果进行单指标直观分析,由于方案1~3和方案5~7在设计流量点处,扬程没能达到目标要求,属于不可优化范畴,由此分析得到的较优试验方案分别为:扬程指标的较优试验方案为第4号试验,试验方案为A2B1C2D3;效率指标的较优试验方案为第9号试验,试验方案为A3B3C2D1;轴功率指标的较优试验方案为第8号试验,试验方案为A3B2C1D3;压力脉动系数的较优试验方案为第4号试验,试验方案为A2B1C2D3。
3.2 极差分析
极差分析是转换成单指标正交试验设计,即计算每个指标下对应因素的极差。一般情况下,每个指标下所对应因素的极差是不同的,极差主要是反映了每个因素下所选取的水平对试验指标影响权重的大小。极差越大,说明该因素下所选取的水平对试验指标的影响权重越大。根据表3中计算数据,可以得出各因素水平对4个试验指标的影响。
表3 试验结果的极差分析
Tab.3 Range analysis of test results

通过极差分析可得,各因素对4个评判指标的影响程度不同,为直观显示各因素水平对评判指标的影响,以因素水平为横坐标,各评判指标为纵坐标,得到如图4~7所示的水平指标关系。
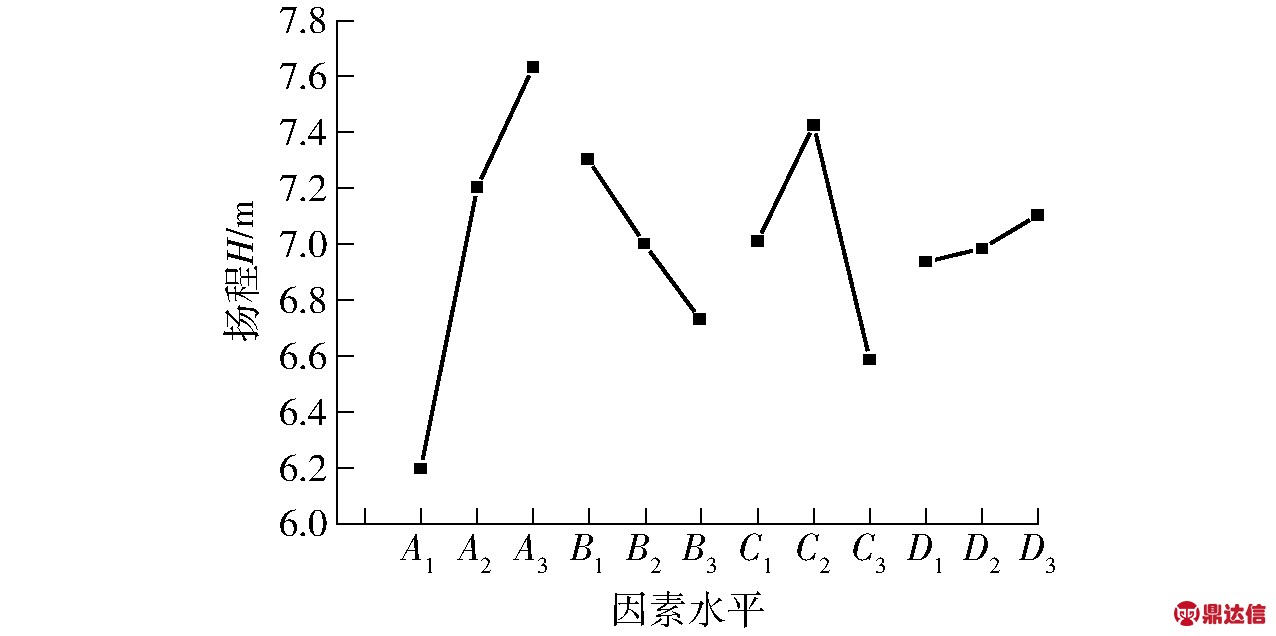
图4 各因素水平与扬程指标关系
Fig.4 Relationship between level of each factor and head
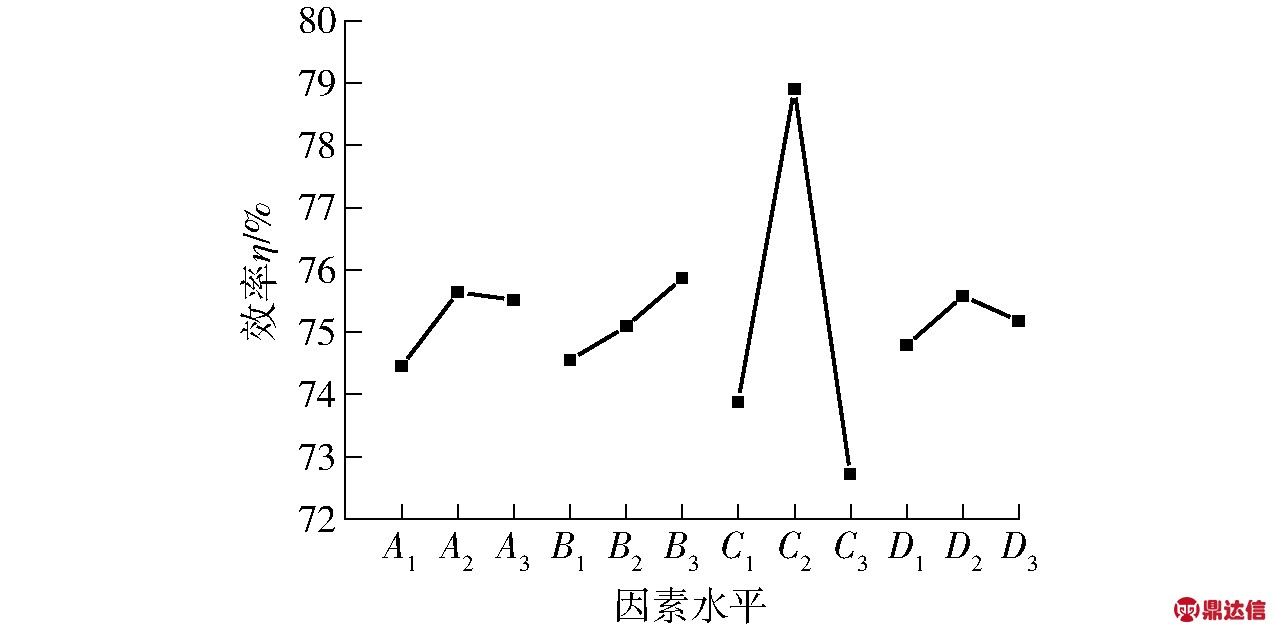
图5 各因素水平与效率指标关系
Fig.5 Relationship between level of each factor and efficiency
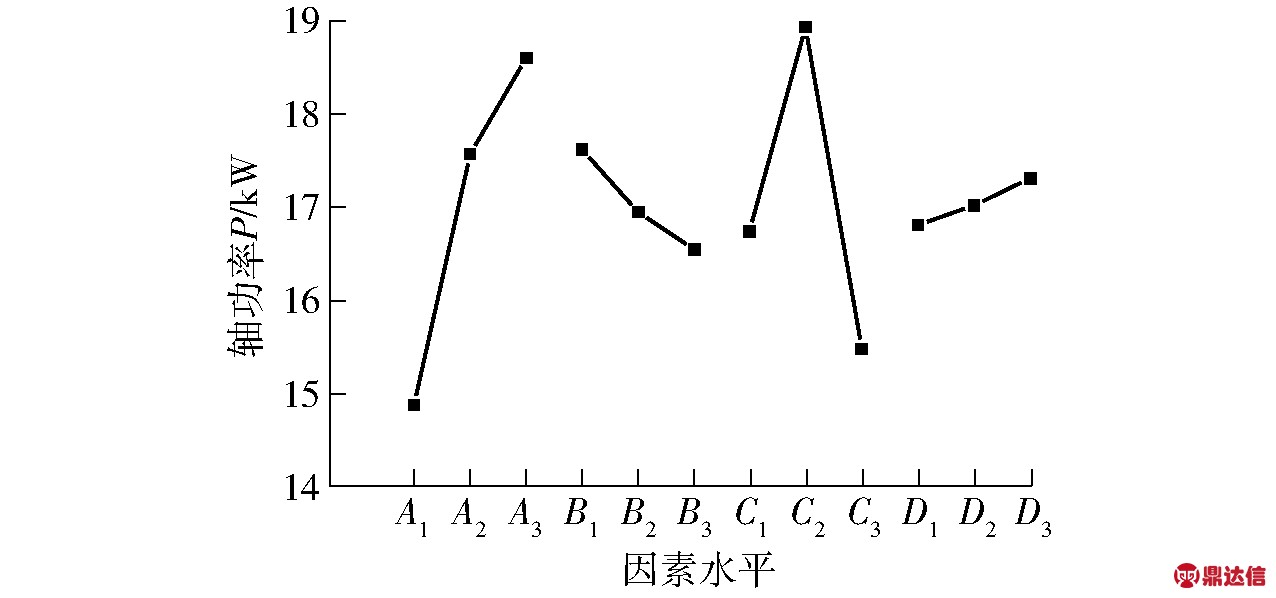
图6 各因素水平与轴功率指标关系
Fig.6 Relationship between level of each factor and axis power
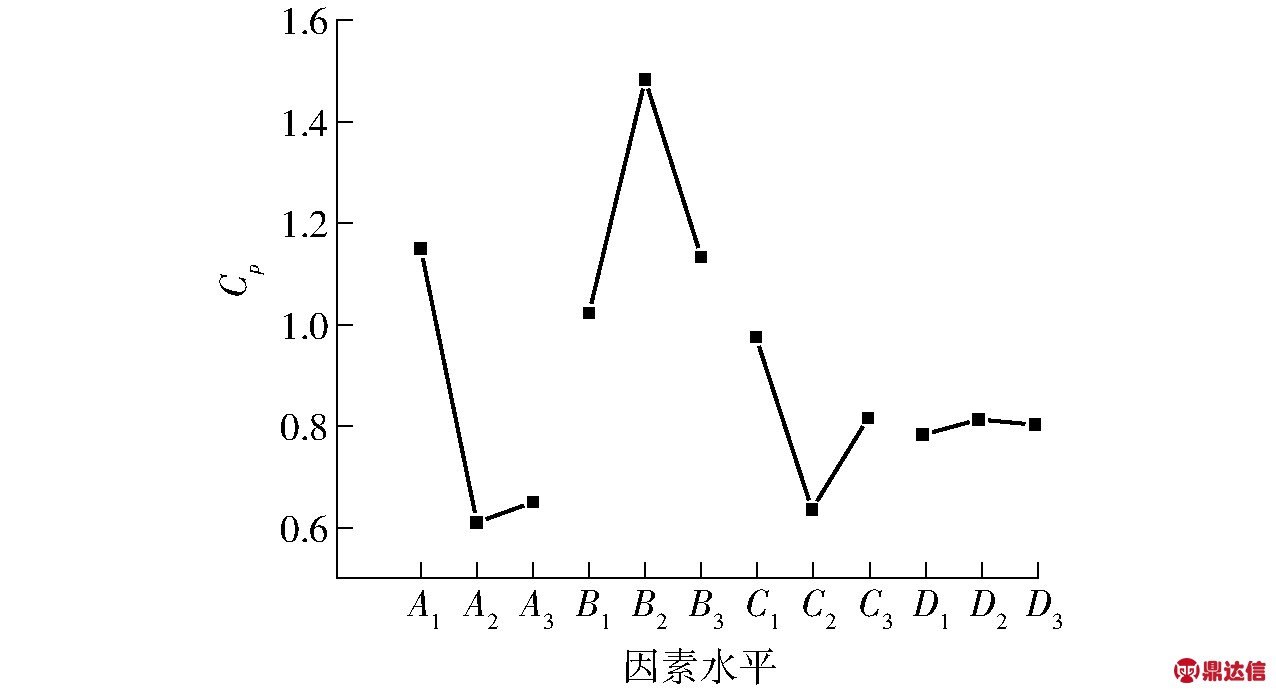
图7 各因素水平与压力脉动系数指标关系
Fig.7 Relationship between level of each factor and pressure pulsation coefficient
通过图4~7可知,在设计流量工况下,叶片数(因素A)的影响为:当增加叶片时,每个叶片的负荷将会减少,从而改善叶轮内水流流态[21]。随着叶片数的增加,轴流泵扬程和轴功率均单调增长,效率增长到一定值后增加缓慢。
翼型(因素B)的影响由速度环量定义
Г=2πRVu
(2)
式中 Γ——速度环量,m2/s R——不同截面的叶轮半径,m Vu——绝对速度的圆周分量,m/s
为使叶片各个截面获得相同的扬程,因此在设计叶片时假设不同叶轮半径R下速度环量相同,所以,叶轮半径R与绝对速度的圆周分量Vu成反比,靠近轮毂处的翼型安放角较大,叶片外缘翼型安放角较小,导致叶片扭曲严重。根据图4~6可得出,当翼型因素水平由翼型3→翼型2→翼型1变化时,随着各断面翼型安放角的减小,轴流泵扬程与轴功率均单调增加,其中扬程由6.73 m增大到7.30 m,但效率由75.86%减小到74.55%,扬程增加显著,效率降低甚微。可发现,减小各断面翼型安放角,可减少叶片的扭曲程度,改善翼型性能,提高叶片的做功能力。
轮毂比(因素C)的影响为:当轮毂比由0.45→0.47→0.49变化时,相应的轴流泵扬程、效率和轴功率均是先增加后减少,且极差较大。由此可知,轮毂除了在固定叶片满足相应的结构强度要求外,轮毂比对叶轮内的水流流态也具有重要的影响,是轴流泵水力设计和优化的一个重要几何参数。
导叶与叶片间距离(因素D)的选取参照S=(0.1~0.15)Dh(Dh为叶轮直径,S为导叶与叶片间最优距离),与因素A、B、C相比,该因素对4个评判指标的影响较小。从图4~6中可以看出,随着导叶与叶片间距离的增大,扬程和轴功率均单调增加,效率先增加后减少,因此存在最优的距离S使水泵效率达到最高。
根据图7可以得出,叶片数(因素A)、翼型安放角(因素B)与轮毂比(因素C)对压力脉动系数影响较大,而导叶与叶片间距离(因素D)对压力脉动系数影响较小。因素B的水平2下,压力脉动系数最大,说明在此因素水平下轴流泵运行稳定性较差。
通过上述极差分析,可得到的较优试验方案分别为:扬程指标的较优试验方案为A3B1C2D3;效率指标的较优试验方案为A2B3C2D2;轴功率指标的较优试验方案为A1B3C3D1;压力脉动指标的较优试验方案为A2B1C2D1。
从计算得到的极差R可知,4个试验因素对试验指标的显著性顺序为:对扬程的影响从大到小依次为A、C、B、D;对效率的影响从大到小依次为C、B、A、D;对轴功率的影响从大到小依次为A、C、B、D;对压力脉动系数的影响从大到小依次为A、B、C、D。
3.3 采用综合频率分析法确定最佳试验方案
本次正交试验的4个评判指标具有同等的重要性,根据前文直观分析得到的试验方案和通过各个指标的极差分析得到的试验方案,对4个因素A、B、C、D所对应不同水平进行综合频率分析。因素A的2水平出现频率是1/2;因素B的1水平出现的频率是1/2;因素C的2水平出现的频率是3/4;因素D的3水平出现的频率是1/2。因此根据综合频率分析法确定的初步最佳试验方案是A2B1C2D3,即叶片数选为4,选用翼型1,轮毂比选为0.47,导叶与叶片距离选为263 mm。
3.4 优化方案分析
优化得出的最佳试验方案A2B1C2D3对应正交表中的方案4,需对该最佳试验方案进行进一步的计算校核。
为对比优化结果,在设计流量Q=328.5 L/s下,提取0.5倍叶高处叶轮及导叶的内部时均流线图,如图8所示。由于轴流泵原始模型在该流量条件下已经偏离设计工况,所以从图8中可以看出在导叶的背面形成了2个较大范围的旋涡,且水流在叶轮及导叶段分布不均匀,水力损失较大;优化后的模型在导叶背面的旋涡基本消失,且水流在叶轮及导叶段水流流线顺畅,分布相对均匀,流态较好。
优化前后的轴流泵叶轮均有4个叶片,采用CFD数值计算时,同一个工况点下的各个叶片表面的压力云图及流速分布图相似。图9为在设计流量Q=328.5 L/s下叶片表面的压力云图及流速分布图。从图9中可以看出,叶片优化前后,水流沿叶片表面的流动顺畅,没有产生旋涡及回流。而优化前叶片压力面在靠近轮毂处出现高压区,优化后的叶片表面高压区基本消失,且压力分布相对更加均匀,优化效果较好。
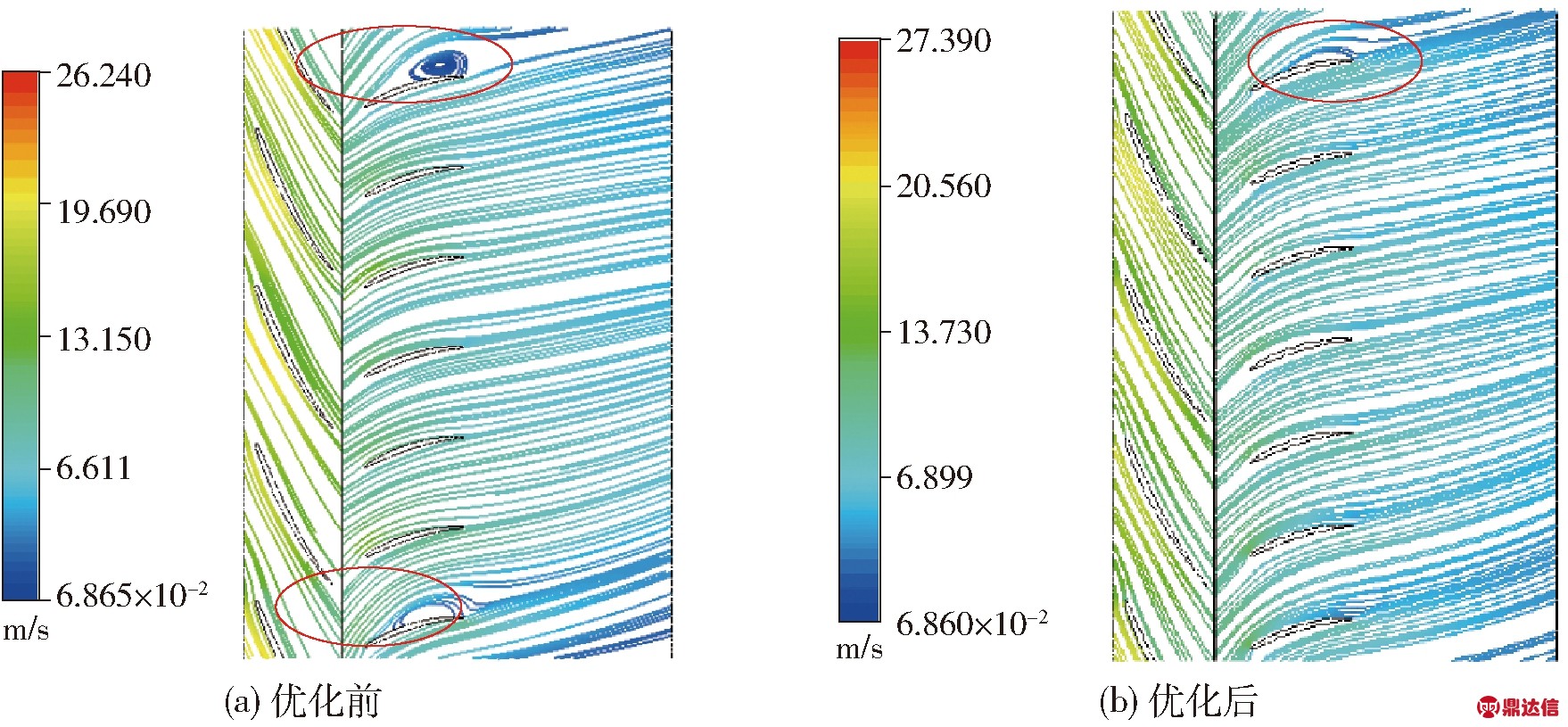
图8 0.5倍叶高处泵内部时均流线图
Fig.8 Distribution of time-average streamline in impeller and guide vane at 0.5 times blade height

图9 叶片表面压力云图及流速分布图
Fig.9 Blade surface pressure contours and velocity distribution
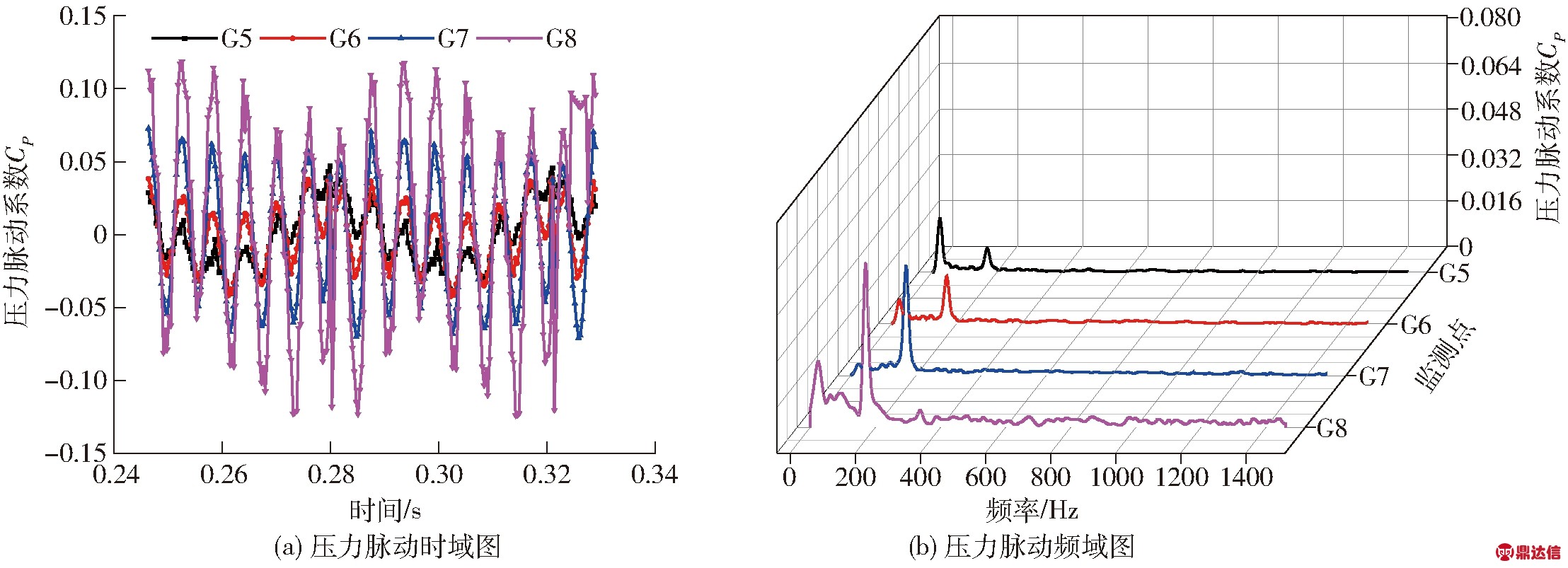
图10 设计流量下轴流泵内压力脉动时域及频域图
Fig.10 Time and frequency domains of pressure pulsation in axial-flow pump under design flow
图10为优化后模型泵在设计流量Q=328.5 L/s下,叶轮出口处监测点的压力脉动时域图及压力脉动频域图。从图10a可知,压力脉动系数Cp从轮毂到轮缘逐渐增大,轮缘处系数最大值是轮毂处的3倍,且压力脉动呈周期性波动。从图10b可知,叶轮出口处的水流受叶片及导叶的动静干涉作用,压力主频为7倍的转频,与轴流泵的导叶个数一致,且在4倍转频处,也有较大的幅值,且经过傅里叶变换得到的压力脉动幅值变化也是从轮毂到轮缘处逐渐增大。
综上所述,相比原始模型,优化后的轴流泵模型在流量和扬程满足改型要求的同时,在新的设计流量下,效率由74.33%增大为78.59%,提高了5.7%;轴功率由20.54 kW减小为20.29 kW,下降了1.21%;压力脉动系数由0.344减小为0.310,降低了11%,发现该优化方案均达到要求,验证了采用综合频率法进行多目标正交优化设计的可行性。
4 模型试验验证
4.1 试验台及测量设备
对优化后的轴流泵装置进行模型试验,图11为轴流泵叶轮及其模型装置。试验在河海大学水力机械多功能试验台上进行,其三维示意图如图12所示。经鉴定,试验台综合精度为±0.37%(A级)精度。试验台为立式封闭循环系统,包括压力水箱、尾水箱、电磁流量计、供水泵(或辅助泵)、电动闸阀、手动蝶阀、Φ500型管道等。电磁流量计型号为:RFM4110-500,精度为±0.2%;差压传感器型号为:EJA110A,精度为0.075%;扭矩仪型号为:JCZ-1000 N·m,精度为±0.1%;与水泵配套的直流电动机功率为120 kW。采用等扬程方法进行模型试验研究,即保持原型与模型的nD(n为转速,D为转轮直径)值相等。通过试验误差分析,本次试验的总误差为±0.27%[22],满足试验规程要求。
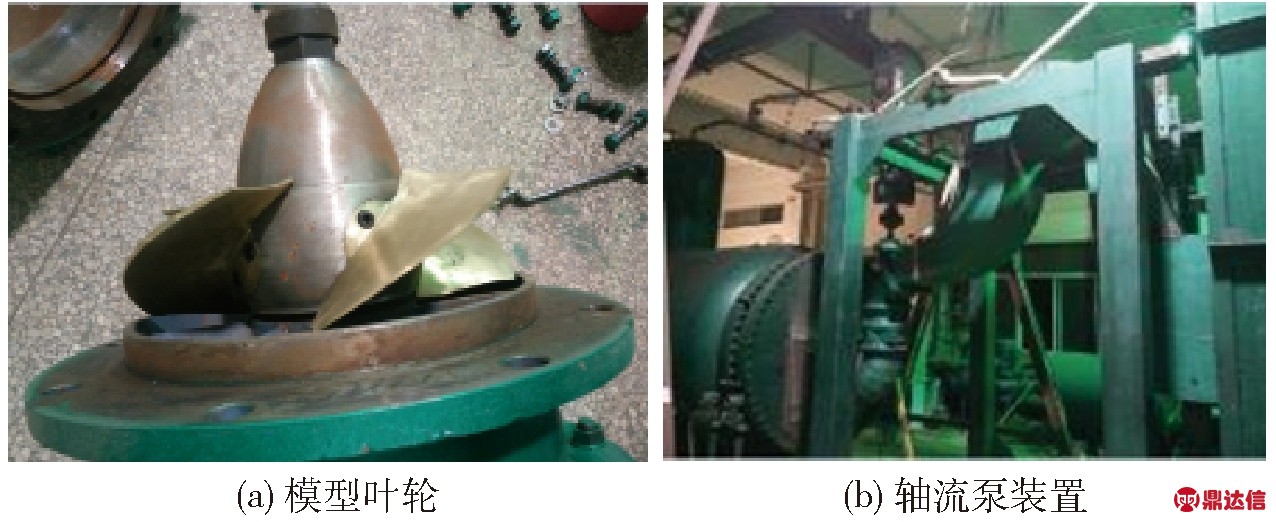
图11 轴流泵装置模型试验
Fig.11 Axial-flow pump device model test
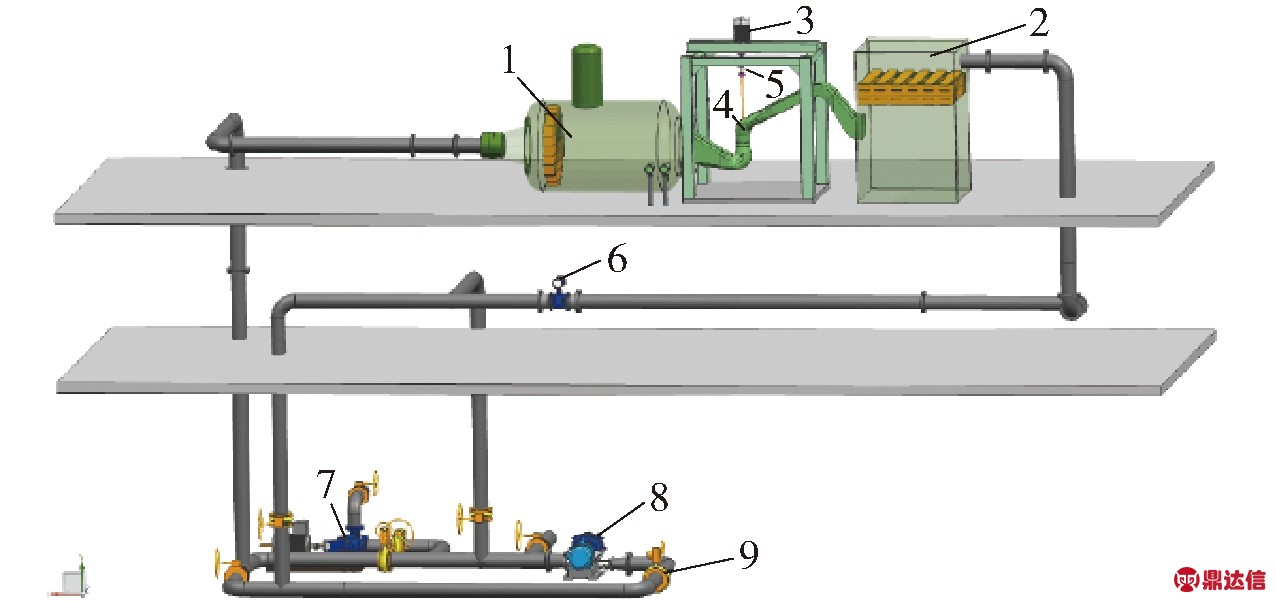
图12 多功能试验台三维模型示意图
Fig.12 3D model diagram of multifunctional test platform
1.尾水箱 2.压力水箱 3.测功电动机 4.模型泵 5.扭矩仪6.电磁流量计 7.充水泵 8.供水泵 9.电磁阀
4.2 试验结果与分析
数值模拟计算结果与试验结果的外特性对比,如图13所示。从图13中可以看出,在小流量及大流量工况下,数值模拟得到的扬程和效率均高于试验值,扬程的最大误差为4.6%,对应的效率最大误差为3.2%。造成这一误差的原因,可能是试验时轴承与密封环摩擦造成了损失;同时在进行模型试验时,手动调节叶片,无法保证4个叶片摆放角度完全一致及在模型试验操作时2个工况点之间没有留有足够的稳定时间,也有可能造成两者的偏差。虽然模拟结果与试验结果存在一点偏差,但从图13中可以看出,数值模拟计算的扬程、效率与试验结果的随流量的变化规律一致,具有较高的吻合度,最大误差均不超过5%。说明本文所采用的数值计算模型与方法可以较准确地预测轴流泵的外特性。
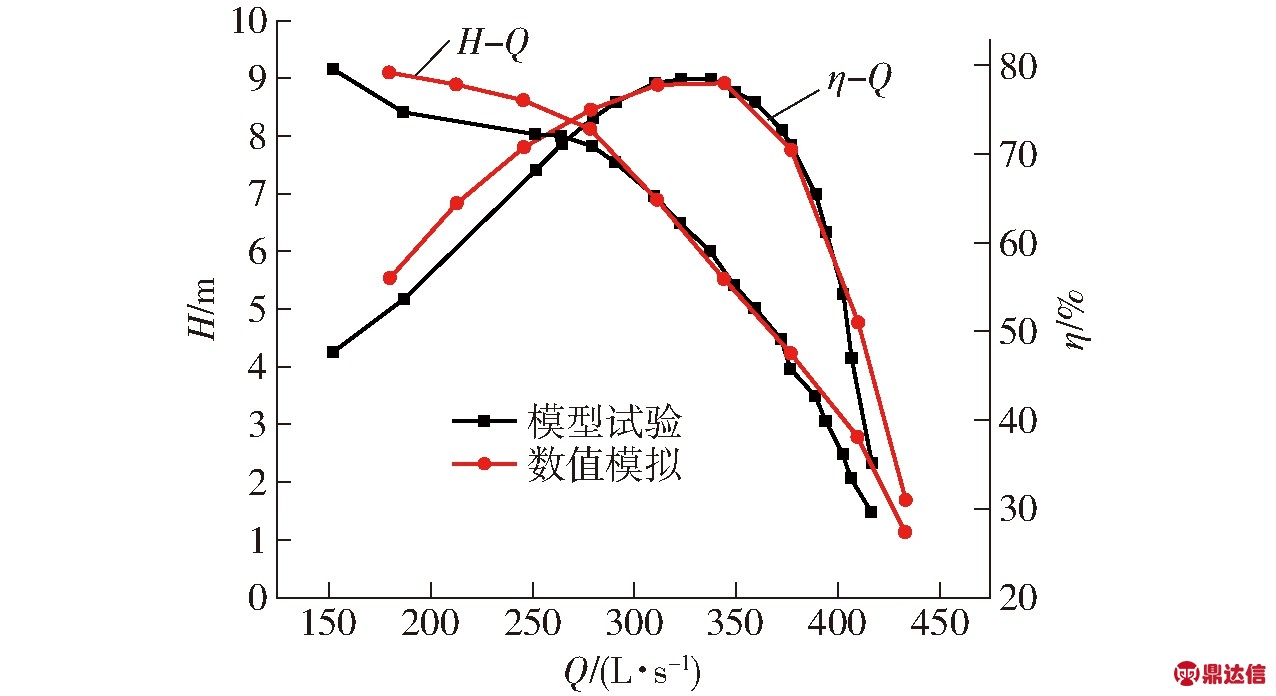
图13 模型泵试验数据与数值模拟数据对比
Fig.13 Comparison of model pump test data with numerical simulation data
根据试验测得数据,绘出轴流泵装置模型综合特性曲线,如图14所示。从图14中可知,优化后的轴流泵模型装置具有较大范围的高效率区,模型装置的最高效率为78.66%,对应的叶片安放角为0°,对应的扬程为7.52 m;根据不同叶片角度下的轴流泵装置性能参数并对照工程的改型要求,叶片安放角为0°时满足设计要求。
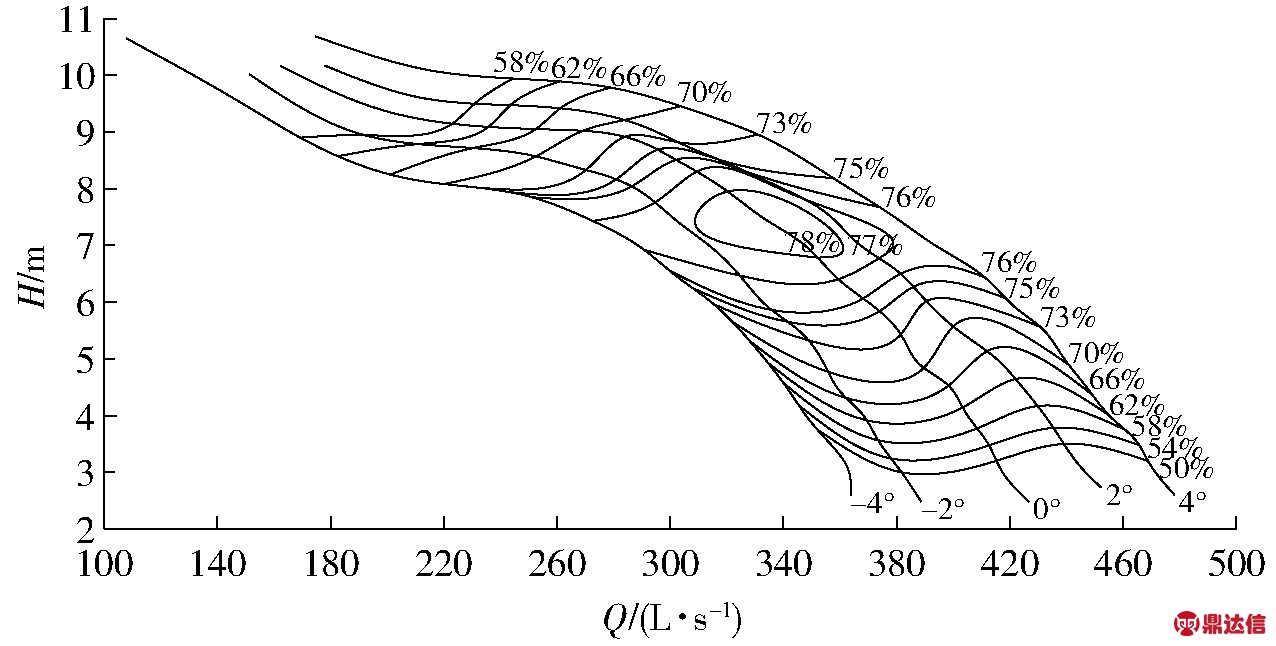
图14 轴流泵装置模型综合特性曲线
Fig.14 Comprehensive characteristic curve of axial-flow pump model
5 结论
(1)极差分析结果表明,与其他试验因素相比,导叶与叶片间距离(因素D)对4个试验评判指标的影响最小,轮毂比(因素C)对4个试验评判指标影响显著,因此轮毂比是轴流泵水力优化设计的一个重要几何参数。
(2)基于正交试验的轴流泵多目标优化设计中,借助直观分析与极差分析结果,采用综合频率分析法确定了最佳试验方案为A2B1C2D3。在该最佳试验方案下,轴流泵模型在流量和扬程满足改型要求的同时,在新的设计流量下,效率提高了5.7%;轴功率下降了1.21%;压力脉动系数绝对值降低了11%,验证了数值模拟技术结合综合频率分析法在轴流泵多目标正交优化试验中的可行性。
(3)根据试验分析,数值模拟得到的轴流泵装置扬程与效率随流量的变化趋势与试验结果一致,数值模拟结果与试验数据的各点误差均在5%以内,进一步说明本文所采用的数值计算模型以及方法可以较准确地预测轴流泵的外特性。