摘 要: 多锥构型湿式摩擦元件是机械式变速装置中的一个新的尝试,其非工作状态下的带排扭矩对变速装置的效率有重要的影响.为了评价多锥构型湿式摩擦元件在全油膜状态下的带排扭矩,建立了两种不同结构的湿式摩擦元件带排扭矩CFD分析模型,获得了润滑油流量、油膜厚度、相对转速等条件对多锥摩擦元件间带排扭矩的影响规律.结果表明:相同工况条件下,多锥构型摩擦元件的带排扭矩要大于平面摩擦副;随着流量和相对转速的增加,带排扭矩线性增加;随着间隙的增加,带排扭矩逐渐减小.通过仿真模型和传统模型的对比,验证了模型的可用性.
关键词: 多锥构型;湿式摩擦元件;润滑油流量;带排扭矩
湿式摩擦元件广泛应用于湿式离合器、液粘离合器和变速装置中.多锥构型湿式摩擦元件是机械式变速装置中一个新的尝试.通过多个锥面代替平面来传递扭矩,在扭矩传递能力方面优势明显,在内外半径相同条件下传递的扭矩可达传统平面摩擦元件的数倍.
图1为典型的多锥摩擦副.摩擦副内径为65 mm,外径为85 mm,表面沿径向分布3个锥角为30°的锥环,有6个锥面共同传递扭矩.在内外半径相同,轴向载荷为500 N,相对转速为500 r/min的工况条件下进行滑摩,多锥摩擦副的平均摩擦扭矩为5 930 N·mm,平面摩擦副的为1 613 N·mm,多锥摩擦副传递的扭矩值是平面摩擦元件的3.6倍.

图1 多锥摩擦副
Fig.1 Conical friction pair
湿式摩擦元件在空转状态下名义间隙一般在0.2~1.0 mm之间.在较小间隙下,由于摩擦元件间流体的剪切力作用,会产生带排功率损失.带排损失不可避免,带排扭矩的存在会降低整个机械变速装置的机械效率,因此有必要对新型多锥摩擦元件间的带排扭矩进行评价,明确带排特性的影响规律.带排扭矩特性主要受结构参数、润滑油特性、工况条件等因素的综合影响.在设计过程中,合理选择和控制主要影响参数对提高变速装置效率具有重要的工程意义.
学者们对带排扭矩的认识是通过试验开始的.Fish[1] 使用SAE#2试验台对湿式离合器的带排损失进行了测试,结果表明带排扭矩随着间隙的增大而减小,随着流量的增加而增大.Kitabayashi等[2]通过试验确定了离合器设计参数对带排扭矩的影响规律,结果表明在低转速条件下,随着转速的增加,带排扭矩线性增加;在高转速条件下流量和沟槽特征的影响更大.
随后对平面摩擦副带排扭矩特性的研究主要是通过计算流体力学和试验相结合的方法.Yuan等[3] 建立了三维稳态二相流计算模型,对摩擦元件的带排扭矩进行计算,得出的结果与文献[2]的基本相同.此外,Yuan等[4] 还建立了考虑表面张力的带排扭矩数值计算模型,对无沟槽摩擦副带排扭矩特性进行试验验证.黄家海等[5- 6] 对片间流体的速度、温度、压力等特性进行了数值计算并通过试验验证了分析结果.张世军[7]、王清[8]、谢言[9]、潘丽[10]对湿式摩擦离合器的计算流体模型开展了研究,对模型的边界和应用范围进行了系统的描述.Aphale 等[11] 通过建立二维和三维流体计算模型对摩擦元件片间流体剪切特性进行计算,并通过试验验证了仿真分析方法的可行性.Yuan等[12]、Hu等[13- 14]建立了考虑离心力作用及表面张力影响的理论模型,并搭建试验台,对湿式离合器中摩擦元件的带排扭矩进行评价.张志刚等[15]根据粘性流体动力学,建立离心力作用下的油膜径向流速方程,讨论了模型中各个分量对带排扭矩的影响.闫清东等[16] 讨论了转速、流量、油温等因素对带排扭矩的影响规律,提出了降低带排扭矩的一些方法.
以往的研究对象主要是平面摩擦副或者表面有微沟槽的摩擦副,而针对新型多锥摩擦副的片间带排扭矩还没有相关研究.文中针对新型多锥摩擦副的结构特点,建立了多锥摩擦副CFD模型,通过计算流体力学分析方法,计算不同润滑油流量、片间油膜厚度、转速条件下的带排扭矩,对多锥构型摩擦元件的带排扭矩特性影响规律进行总结,并与传统的分析模型进行对比,对多锥摩擦元件带排扭矩CFD模型进行评价.
1 理论计算模型
多锥摩擦元件的构型特点如图 2所示.多锥摩擦元件为带有多个锥面的圆环结构.图2中为一对具有两个锥环的多锥摩擦元件.上半部分为具有凸锥构型特征的摩擦元件,下半部分为具有凹锥构型特征的摩擦元件.
分离状态时,摩擦元件片间间隙充满了润滑油.
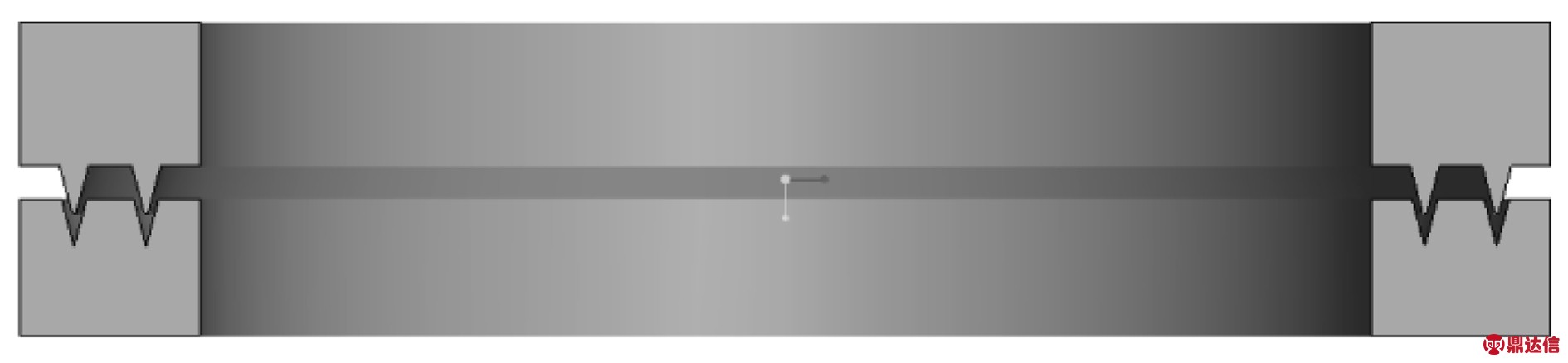
图2 多锥摩擦元件三维示意图
Fig.2 Schematic diagram of conical friction element
多锥摩擦元件带排扭矩的理论计算主要是基于牛顿内摩擦定律,计算油膜粘性剪切力产生的扭矩.
图3是摩擦副计算的几何模型,圆柱坐标系的坐标分别为r、z、θ.将两个锥环分别定义为锥1、锥2.锥角和锥高是主要的特征参数.r1、r2分别为摩擦元件的内外半径.摩擦元件间充满了润滑油,摩擦元件间的油膜厚度为h,摩擦副入口流量为Q,摩擦元件旋转相对角速度为ω,即模型定义上摩擦元件角速度为 ω,下摩擦元件角速度为零.
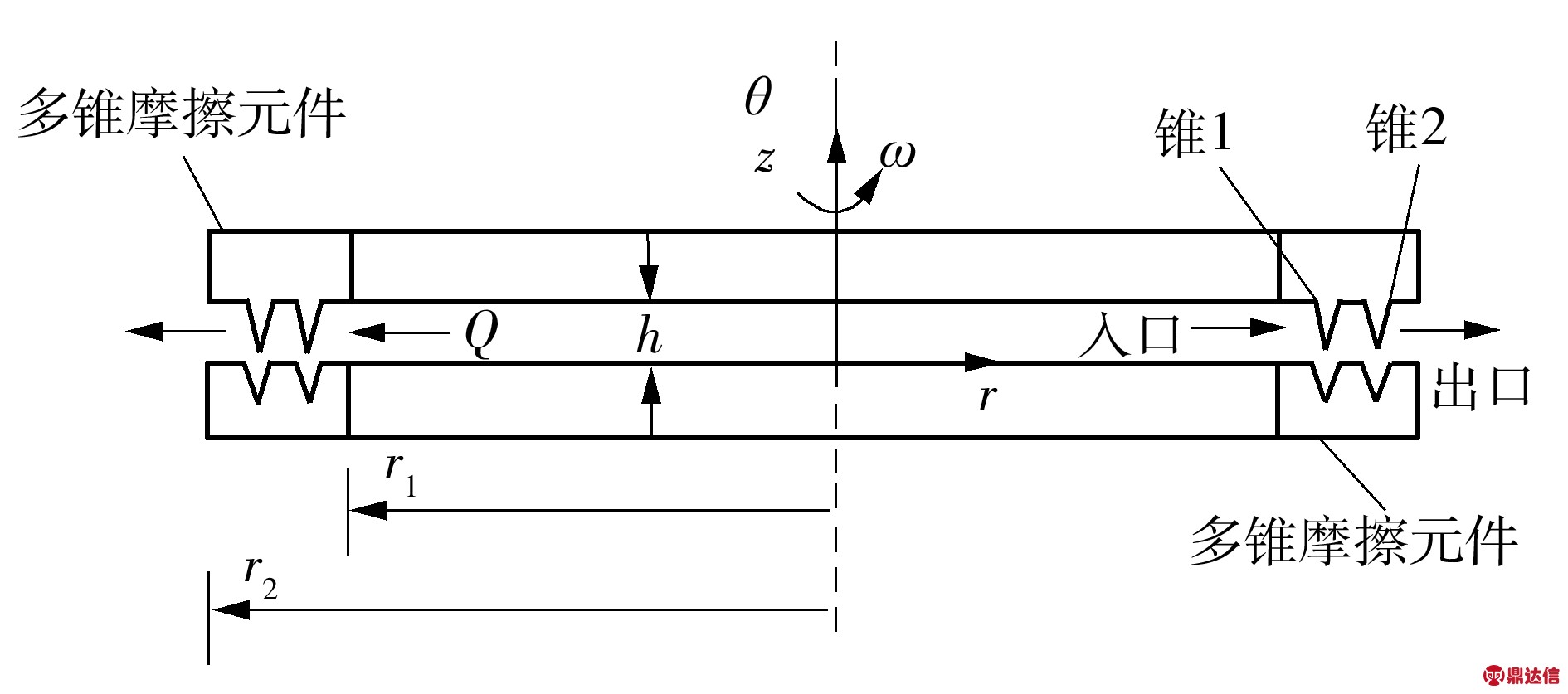
图3 摩擦副的理论计算几何模型
Fig .3 Geometric model for theoretical calculation of friction pairs
油膜剪切力可以由下式表示:
(1)
式中:为油膜的剪切力,Pa;h为间隙内油膜厚度,m;μ为工作油的动力黏度,Pa·s;ω为油膜剪切速度,rad/s.
则油膜传递的扭矩为

(2)
式中,T为油膜传递的扭矩,N·m.
对于多锥摩擦元件,通过定义等效半径re来将多个锥面传递扭矩等效为平面摩擦副.可以根据多锥表面的锥形构型确定re.公式(2)可以表达为
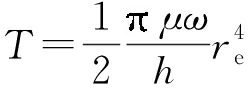
(3)
该模型可以用于评价全油膜状态下的多锥摩擦元件的带排扭矩.从理论模型可以看出,当摩擦元件的结构确定后,湿式摩擦元件的带排扭矩主要与摩擦元件的相对角速度和冷却油的动力黏度系数成正比,与摩擦元件的间隙成反比.
对于双锥摩擦元件来说,确定等效半径较为容易,而如果摩擦元件表面为多个锥的构型,其等效半径的确定会比较繁琐.同时,工况参数,如润滑油流量等对带排扭矩的影响在公式中无法体现.由于摩擦元件间的流体可以定义为牛顿粘性流体,为了更直观有效地评价带排扭矩,同时考虑工况参数对带排扭矩的影响,可以通过CFD数值模拟方法来计算油膜在间隙间的流动和带排扭矩特性.
2 CFD模型的建立
机械变速装置中多锥摩擦元件相对转动,摩擦元件和片间流体之间存在剧烈的相互作用,可以定义摩擦元件内部流体流动是复杂的三维湍流流场.分析时,在高转速状态下采用标准的k-ε方程来模拟,转速较低时,通过近壁区域的壁面函数法来模拟.
针对多锥摩擦元件的特点,为了简化计算过程,提出了以下几条模型假设:①摩擦元件之间流体为全油膜单相流体状态;②流体为定常不可压缩的牛顿流体;③流体密度ρ,流体动力黏度μ为常数;④不考虑热辐射和重力的影响;⑤润滑油在摩擦副的表面上无相对滑动.
考虑到多锥摩擦元件的结构对称特征,为减少计算时间,提高效率,以摩擦副间隙内流体流场的1/24为几何模型,通过定义周期性边界条件,在ANSYS中模拟带排扭矩特性.几何模型如图4所示,上、下两个部分为多锥摩擦元件,片间区域为流体.
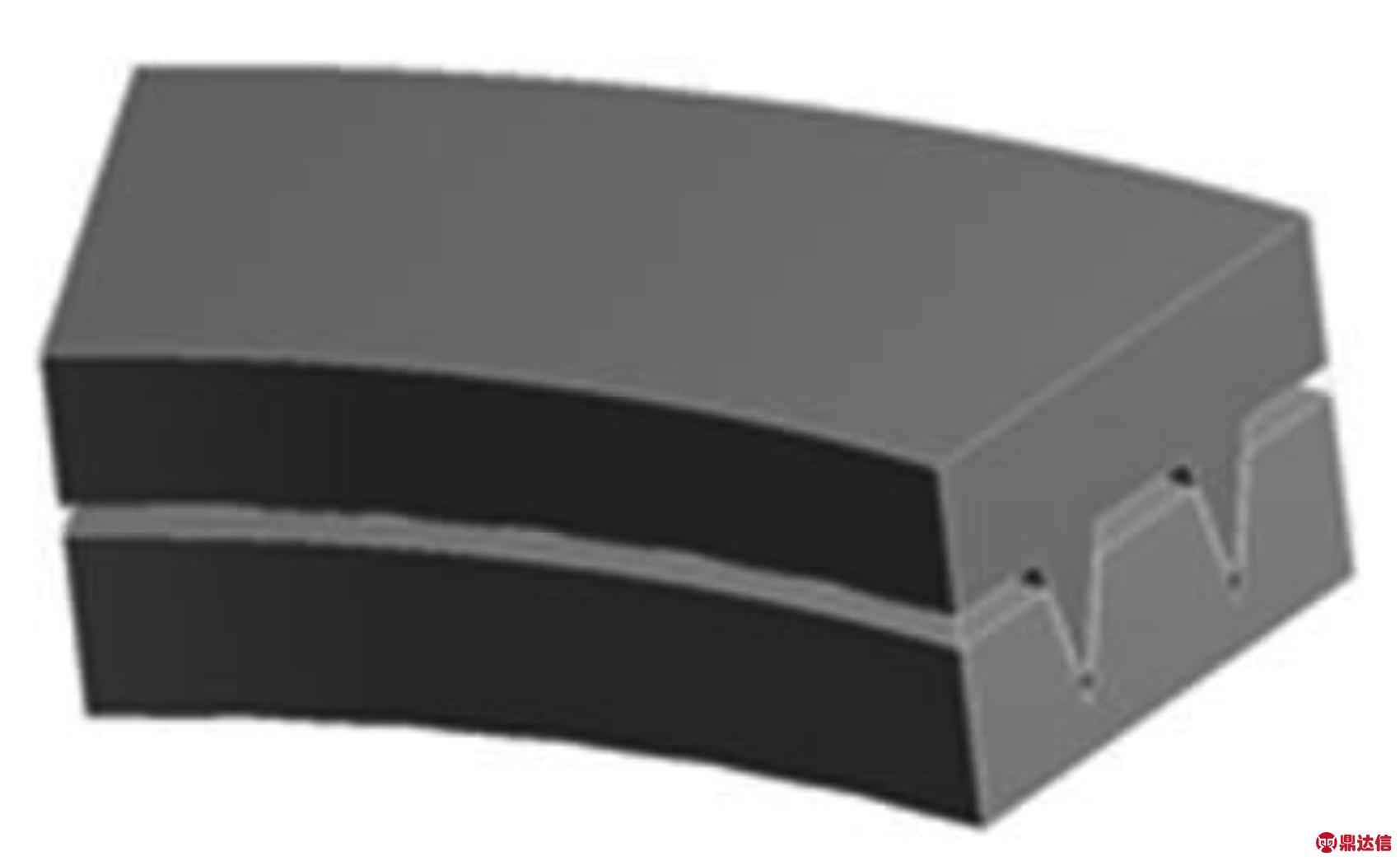
图4 1/24流场几何模型
Fig.4 1/24 geometrical model of flow field
文中对两种不同构型摩擦元件进行分析,如表1所示.1#为平面摩擦副,锥角为0°;2#为多锥摩擦副,锥角为30°.分析过程中固体模型对结果没有影响,故只分析流体计算域.定义流体域的相对压力为105 Pa.流体运动状态为静止.
表1 流体模型几何参数
Table 1 Geometric parameters of flow field

3 模型的边界条件
仿真分析采用CD40润滑油,润滑油的性能参数如下:密度ρ为880 kg/m3,密度不随温度的变化而变化;摩尔质量M为16 kg/mol;比热容c设定为1 900 J/(kg·K);流体动力黏度μ为0.02 Pa·s;流体导热系数k为0.14 W/(m·K).
流体计算域的边界条件主要包括流体入口边界、流体出口边界、旋转摩擦壁面边界、静止壁面边界以及周期性对称边界,如图5所示.
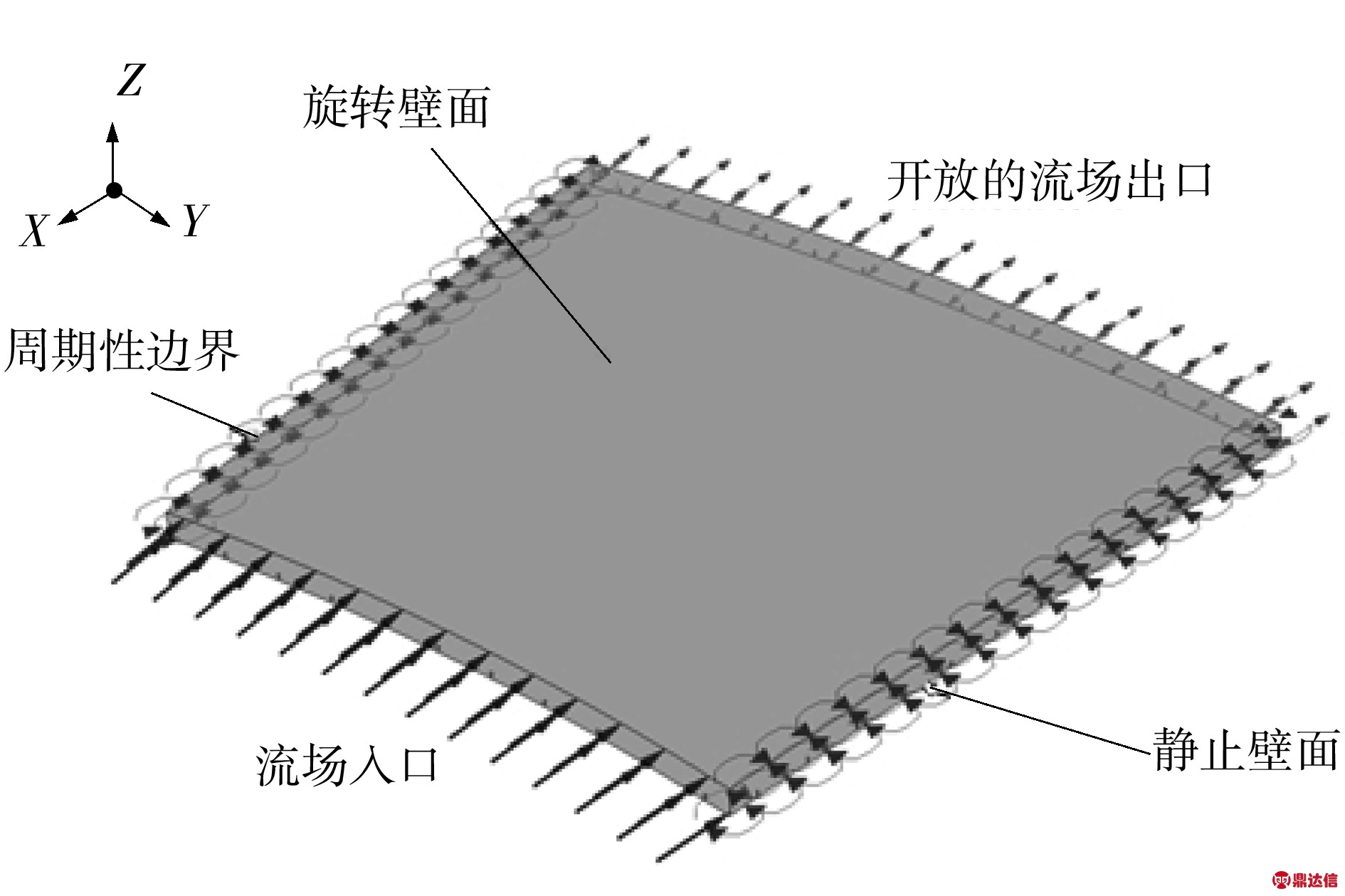
图5 流体模型边界条件
Fig.5 Boundary condition of fluid model
摩擦副的流体入口边界采用质量流量边界条件.模型中设置的质量流量为Q=0.1 kg/s,出口采用开放式边界,与大气相通,设置出口静压p=0 Pa.边界温度设置为静态温度值.多锥摩擦元件与流体在壁面接触,上、下壁面处的速度场采用无滑移边界,与上摩擦副接触的壁面定义为旋转壁面,输入转速为Δω=200~3 000 r/min,模型中设定下多锥摩擦元件为静止壁面边界.将流体侧面定义为周期性边界条件.
两种不同构型的湿式摩擦元件带排扭矩仿真分析模型如图6所示.分别定义了入口、出口、上下壁面和流场侧面周期边界.
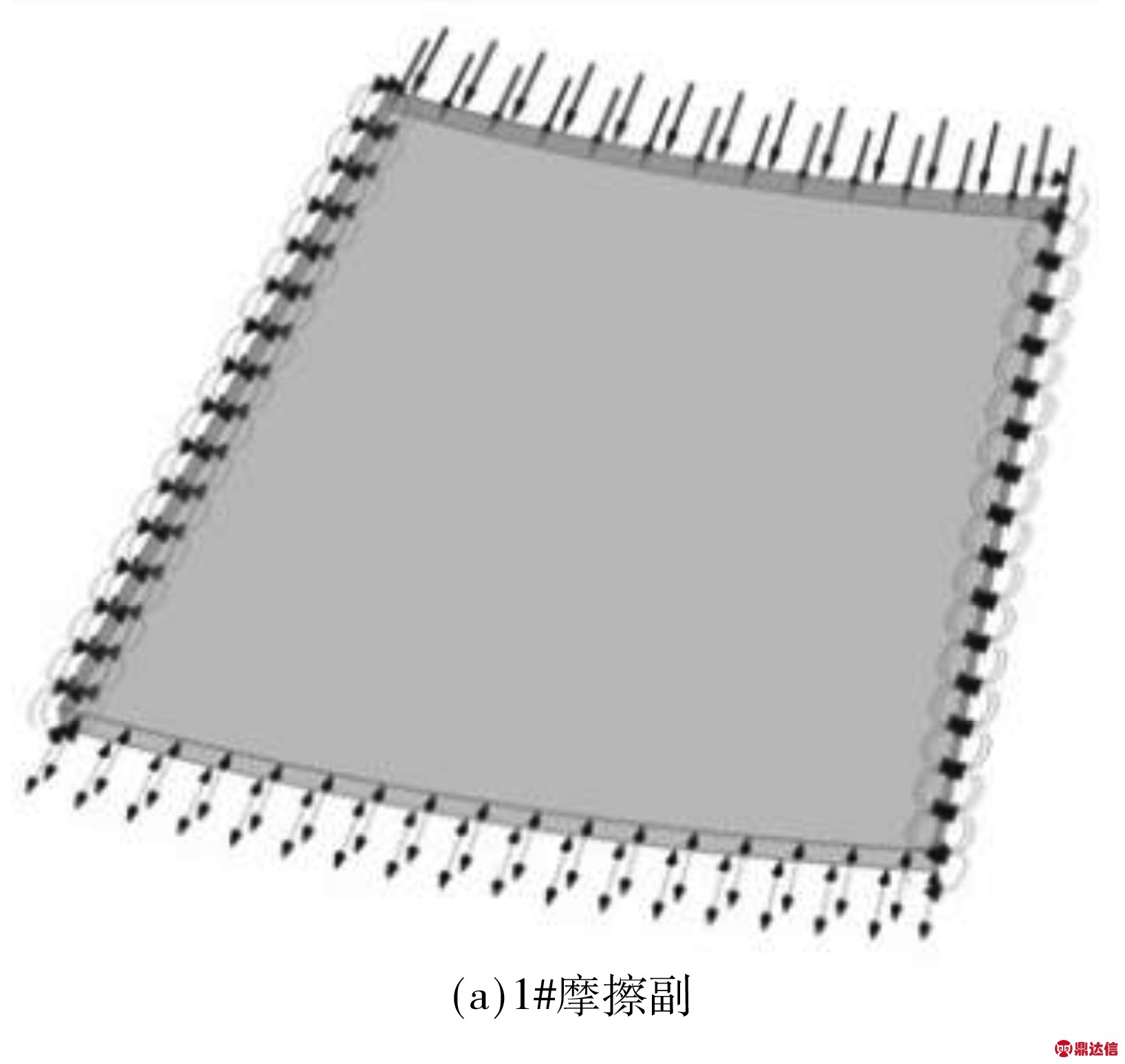
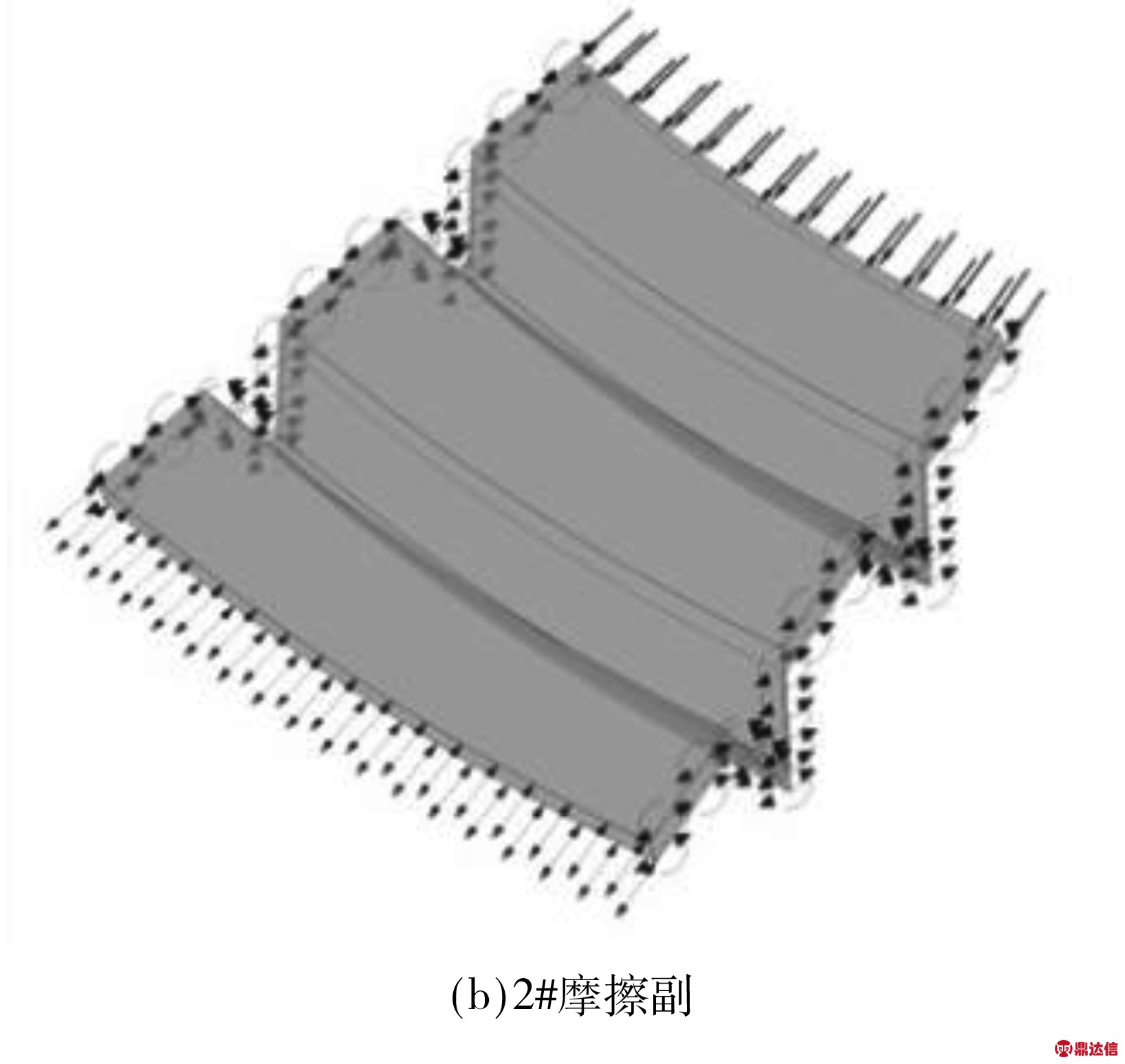
图6 摩擦元件带排扭矩的CFD模型
Fig.6 CFD model for drag torque of friction pairs
求解计算选择高阶求解模式的差分格式,收敛标准是当均方根(RMS)残差值小于1.0×10-4时确定收敛.
在CFD后处理中,提取旋转壁面上的带排转矩为T,文中所计算的是一对摩擦副的1/24油膜,则总的油膜剪切转矩Ttol为
Ttol=T×24
(4)
为了分析结构参数和工况条件对带排扭矩的影响规律,设置了3种仿真工况.
工况1 摩擦元件间隙为4.0×10-4 m,相对转速为1 000 r/min,测定流量参数变化范围为0.1 kg/s(变量1)至1.0 kg/s(变量10),增量为0.1 kg/s.
工况2 相对转速为1 000 r/min,质量流量为0.1 g/s,测定间隙变化范围为0.2×10-3 m(变量1)至1×10-3 m(变量5),增量为0.2×10-3 m.
工况3 测定间隙为4.0×10-4 m,质量流量为0.1 kg/s,相对转速变化范围为200 r/min(变量1)至3 000 r/min(变量15),增量为200 r/min.
4 分析与讨论
带排扭矩对传动过程来说是损耗扭矩,其值越小越好,因此评价结构带排扭矩也依据带排扭矩值的大小来评价.文中通过仿真获得了3种工况条件下,带排扭矩随流量、间隙、相对转速的变化情况.
图7为两种摩擦副在不同流量条件下的带排扭矩.1#摩擦副的带排扭矩随着流量的增大而增大,增速变缓;2#摩擦副的锥2带排扭矩随着流量的增大增速增大,与总带排扭矩变化趋势相同,内侧锥1的带排扭矩随着转速的增大而增大,但增速放缓.
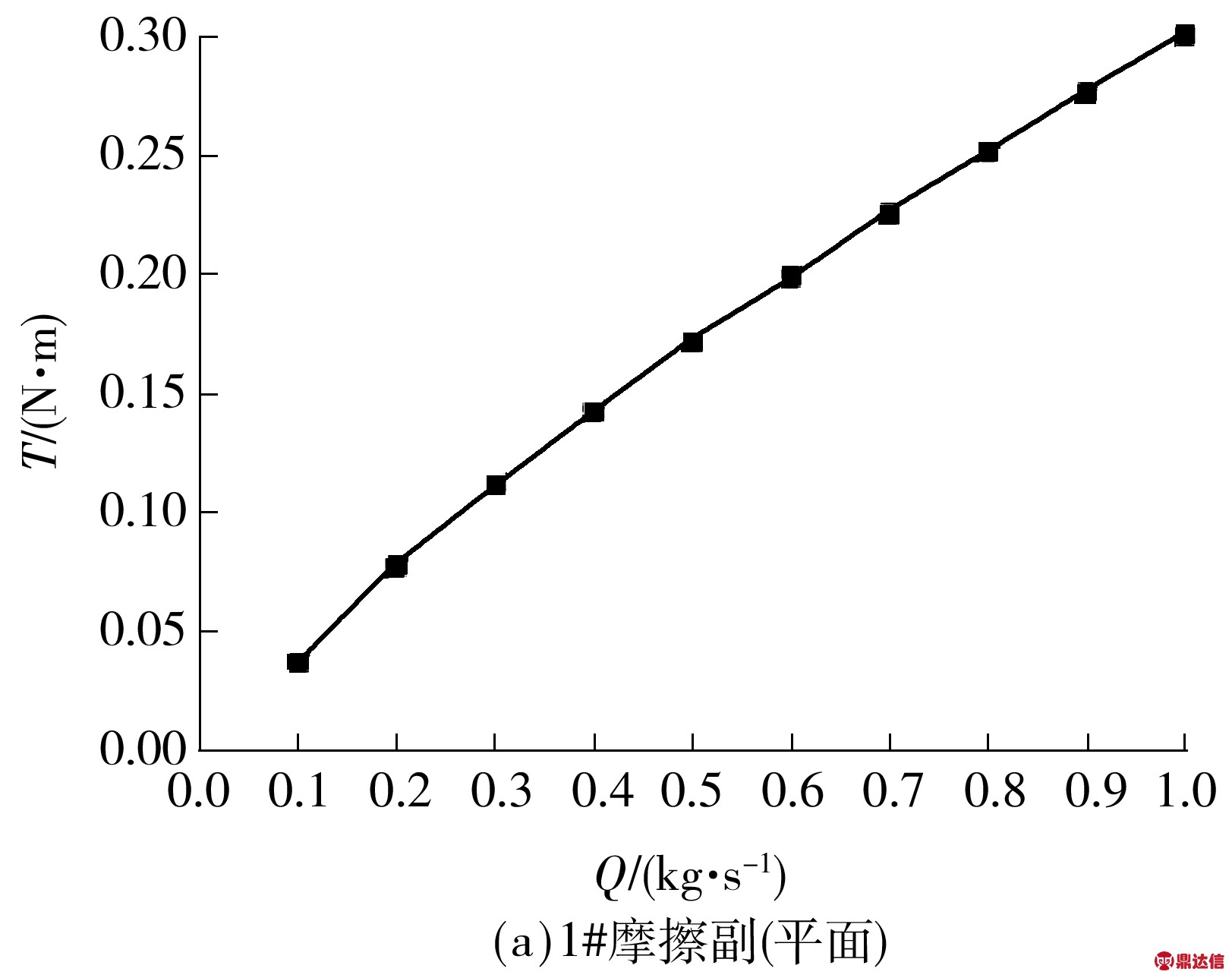
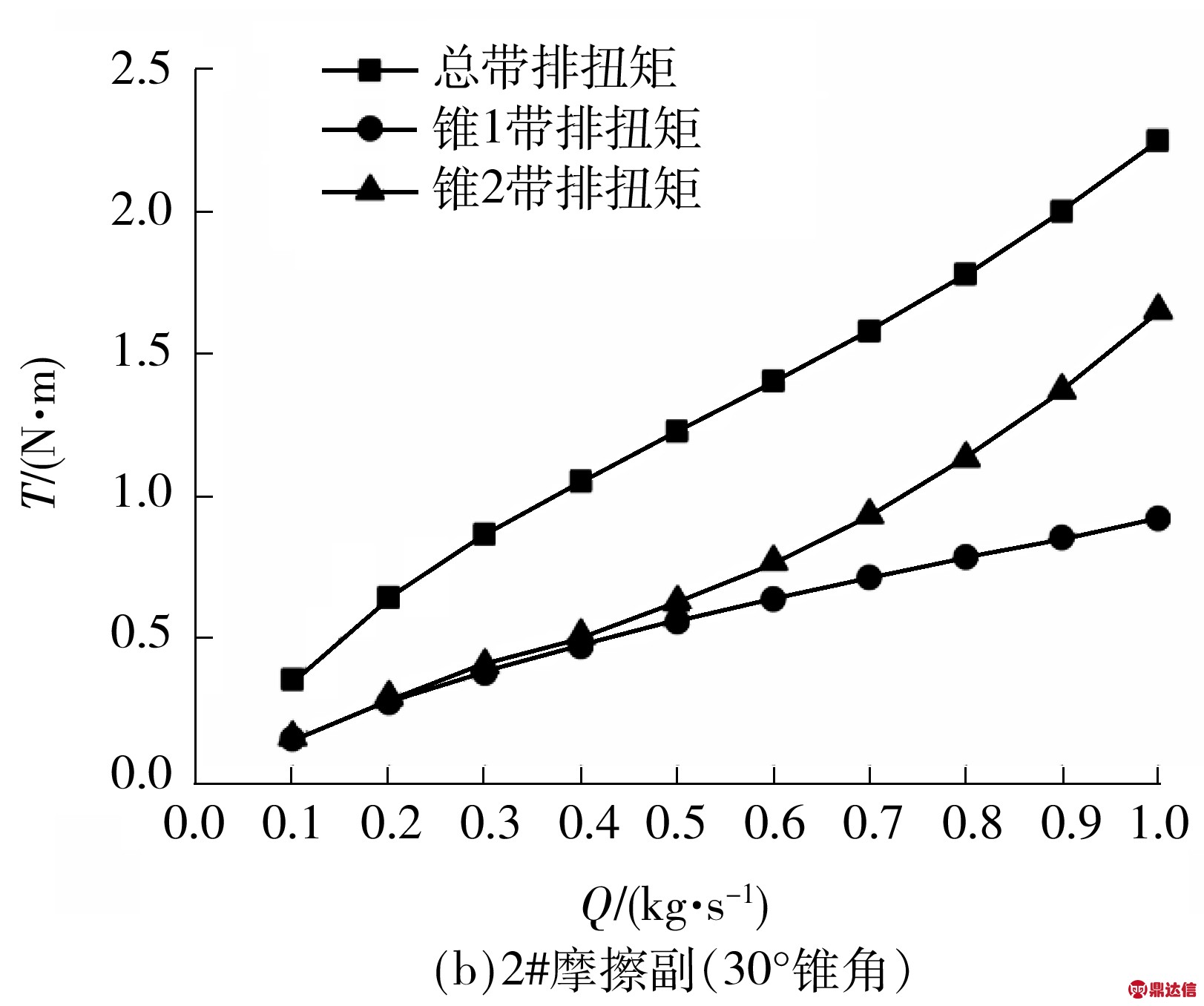
图7 不同流量条件下两种摩擦副的带排扭矩
Fig .7 Drag torque values of friction pair 1# and 2# under di-fferent flow rate
图8为两种摩擦副在不同间隙内油膜厚度(h)条件下的带排扭矩.1#摩擦副的带排扭矩随着间隙内油膜厚度的增大而减小;2#摩擦副的带排扭矩也呈现下降趋势,锥1和锥2的变化趋势相同,外侧锥2的带排扭矩要大于内侧锥1.
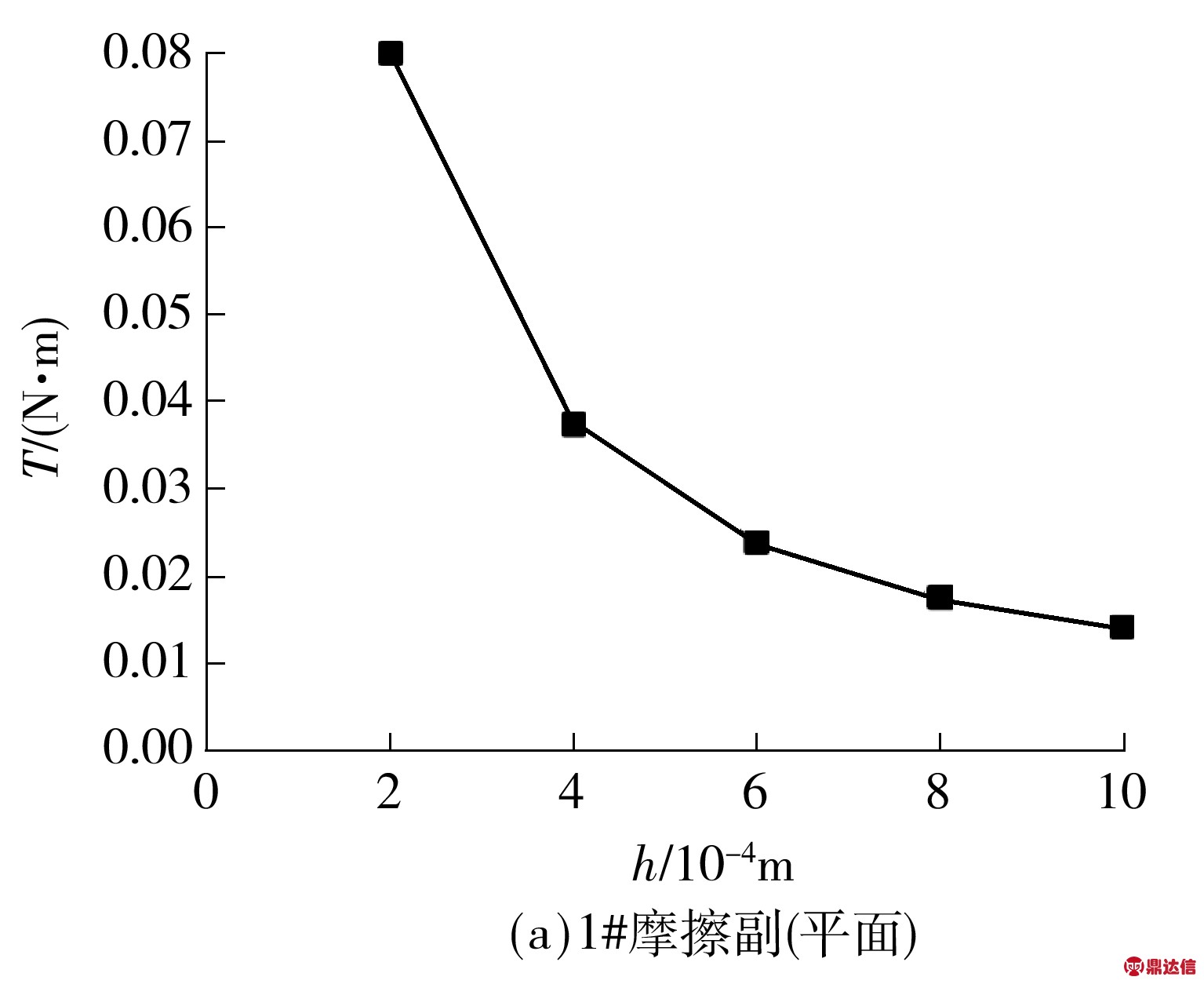
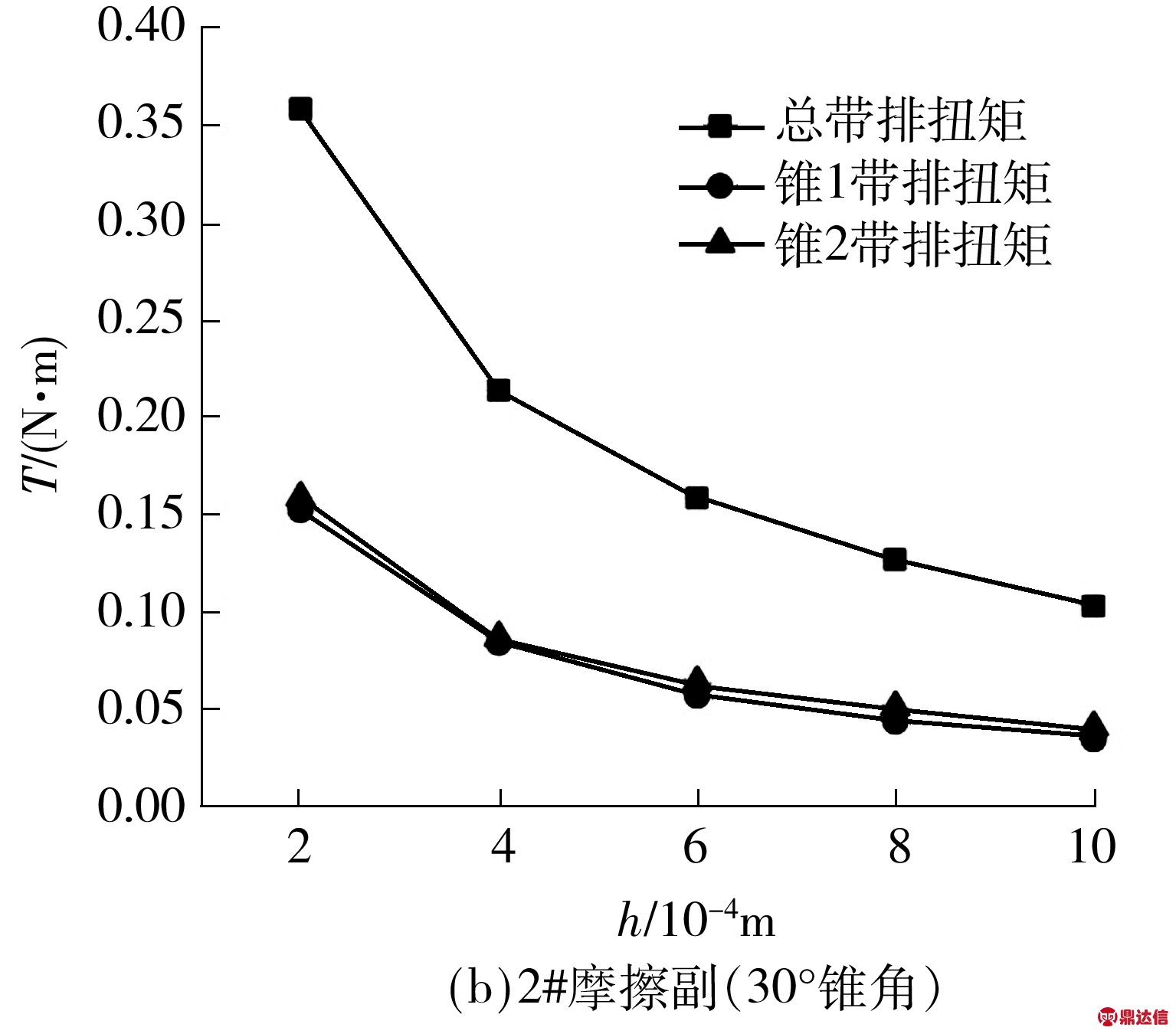
图8 不同间隙条件下两种摩擦副的带排扭矩
Fig.8 Drag torque values of friction pair 1# and 2# under different thickness of oil film
图9为两种摩擦副在不同转速条件下的带排扭矩情况,其中n为相对转速.随着转速的增大,两种摩擦副的带排扭矩不断增加:相同转速条件下,间隙内油膜厚度越大,带排扭矩越小.这也与带排理论公式相同.
图10为多锥结构内外锥的带排扭矩变化情况.随着转速增大,带排扭矩增大;内锥1的带排扭矩值小于外锥2的带排扭矩值.


图9 不同转速条件下两种摩擦副的带排扭矩
Fig.9 Drag torque of friction pair 1# and 2# under different rotating speed
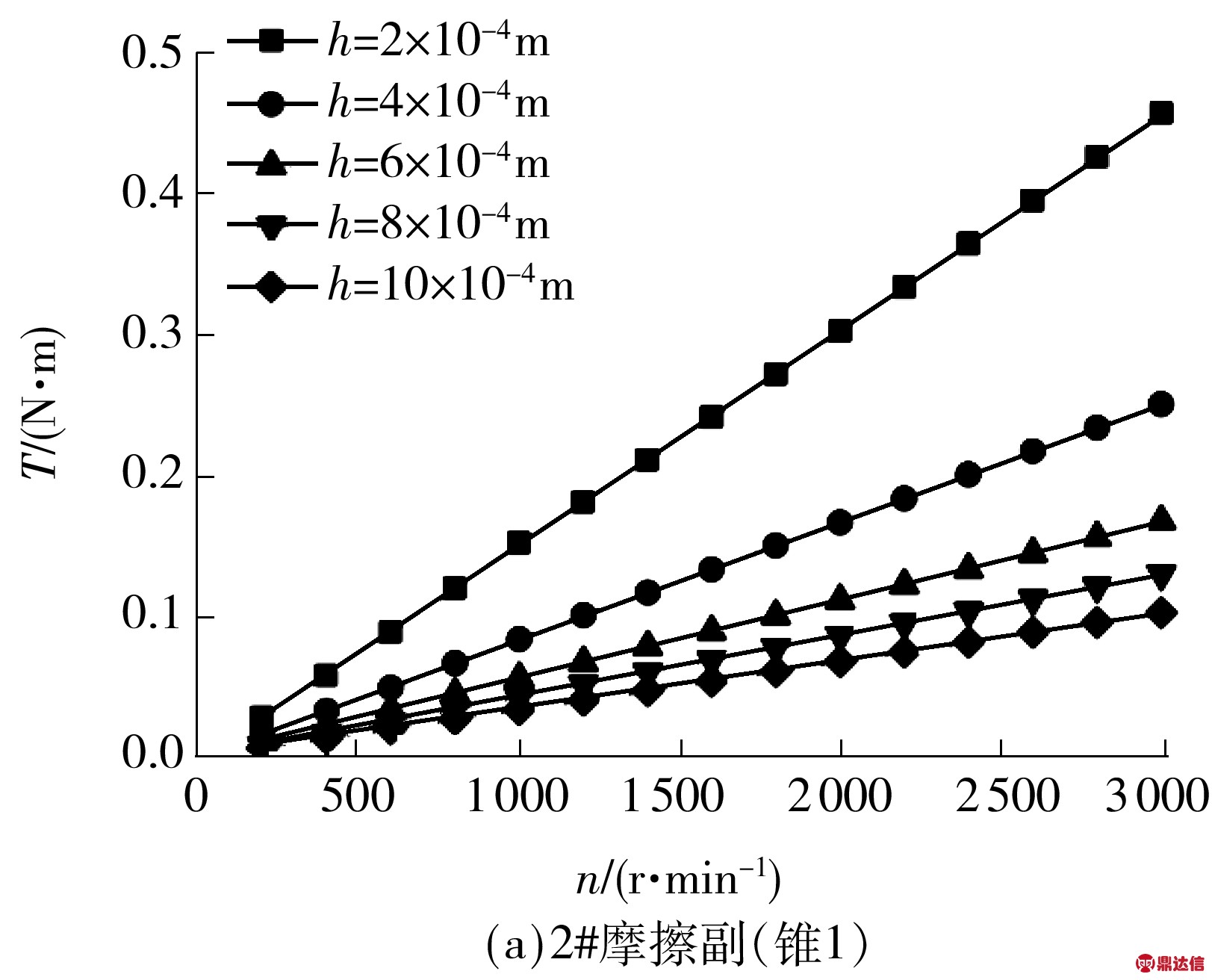

图10 2#摩擦副内侧锥1和外侧锥2的带排扭矩
Fig.10 Drag torque values of cone 1 and cone 2 in friction pair 2#
为了验证模型的有效性,将不同转速条件下的带排扭矩理论计算值与CFD计算值进行了对比.如图11所示,理论计算值要大于CFD计算值;在低转速状态下理论计算值与CFD计算值非常接近;而随着转速增大,误差也开始增大.这是由于数值计算并未考虑流场内的流体状态,而CFD可以较充分的考虑这一点.
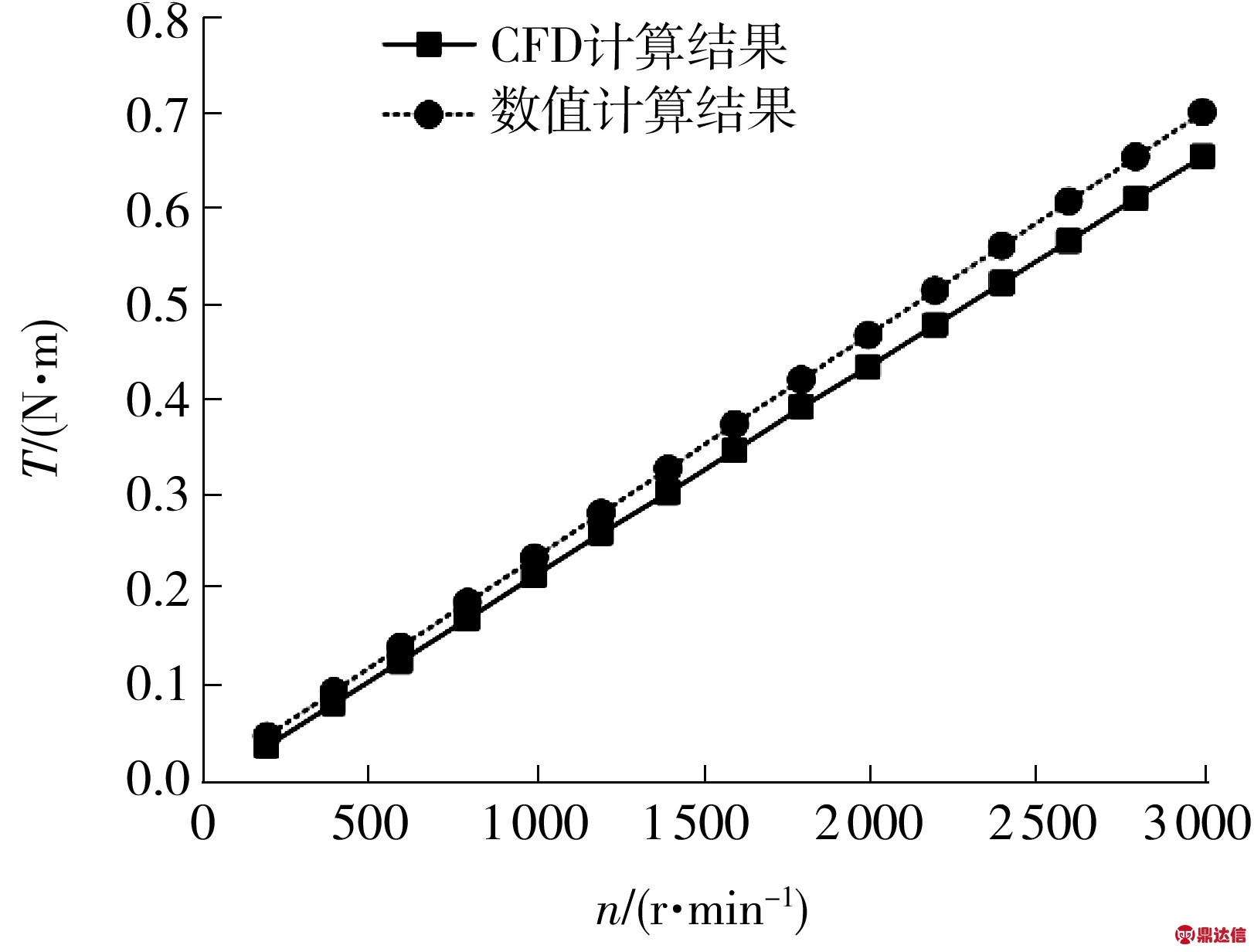
图11 2#摩擦副带排扭矩计算值和CFD模拟值的对比
Fig.11 Comparison between theoretical torque values of friction pair 2# with CFD calculated values
5 结论
对两种摩擦副分别建立了CFD分析模型,讨论了不同流量、转速、间隙条件下的带排扭矩变化规律,并将CFD计算结果与理论计算结果进行了对比,可以得出以下结论:
(1)在相同工况条件下,多锥构型摩擦元件的带排扭矩要大于平面摩擦副.
(2)相同流量和转速条件下,随着间隙的增大,多锥构型摩擦元件带排扭矩值逐渐减小;相同间隙和转速条件下,随着流量的增大,多锥构型摩擦元件的带排扭矩值线性增大.相同流量和间隙条件下,随着转速的增大,多锥构型摩擦元件的带排扭矩线性增大.
(3)与理论计算值相比,多锥摩擦元件带排扭矩CFD计算值要小一些.在转速较低时数值相近,随着转速的增大,误差增加.
(4)模型是考虑全油膜状态下的带排扭矩,会与实际工况略有不同,在低速状态下流体覆盖整个摩擦表面,而在高转速状态下摩擦元件表面是油气混合的状态,需要结合输入流量来确定带排扭矩最大值.