摘要:针对薄壁净化斗塑件上端有缩颈、下端有外圆凹槽的特点,设计了特殊的两板模来实现其自动化注塑生产。模具模腔布局为一模一腔,分两次开模打开。为了减小料流对型芯的冲击变形及避免薄壁塑件壁厚的均匀性变差,采用内侧两点扇形浇口进行浇注,同时对型芯中央成型件做锥台配合定位以增强型芯的稳定性。通过设置多个成型件分多次脱模的方式,减小了因脱模力过大造成的薄壁塑件脱模变形。脱模机构中,设置了2 组、四面分布的哈弗滑块来实施缩颈、圆凹槽特征的脱模。利用动模的第一次开模驱动来实施定模抽芯机构的侧抽芯,利用动模的二次开模驱动来实施动模抽芯机构的侧抽芯,有效地简化了模具结构,降低了模具的制造成本。
关键词:薄壁塑件;注塑;模具结构;机构设计;两板模
在注塑壁厚为0.4~1.2 mm 的薄壁塑件时,若塑件结构较为简单,其模具结构设计的难点主要在于结构成型件的设计应能保证较好的加工方便性和加工精度,以保证模腔闭合后注塑时,在注塑机较高的注塑压力冲击下,型芯不产生变形,从而避免成型的失败[1-4]。因而,薄壁塑件的模具结构设计重点在于如何从结构设计及材料选用上保证成型件的强度,使型芯在熔融料流的高压、高速冲击下不产生变形,避免出现模腔内局部区域的壁厚变大或者变小的现象[5-7]。另外,薄壁塑件如有特殊的脱模需要,在选用脱模方式及设置脱模机构时,同样需要考虑壁厚可能会发生改变的这一基本难题[8-9]。为此,在设计脱模机构时应基于简化模具结构、提高机构结构的可靠性、降低模具的加工成本这几个基本要点来实施[10-12]。笔者针对某粉条机薄壁净化斗塑件进行了模具结构设计及脱模机构设计,为此类塑件模具的设计提供参考。
1 塑件分析
粉条机净化斗为圆盘状带有卡紧的斗状回转体塑件,如图1 所示。其上端为外卷翻边卡紧口,下层为叠层过滤筛孔。塑件材料为聚碳酸酯/丙烯腈-丁二烯-苯乙烯塑料,收缩率0.5%。塑件上端的口部往外翻边后其直径为68 mm,口部往下设置有一缩颈,缩颈外形直径为58 mm。塑件下端叠层圆盘在两个台阶层上共设置有72 个Ø3 mm 通孔,圆盘底端有一圆环形圆凹槽,凹槽内径68 mm,外径91 mm。塑件平均壁厚1.2 mm,较之于塑件高度尺寸而言,塑件为薄壁体。
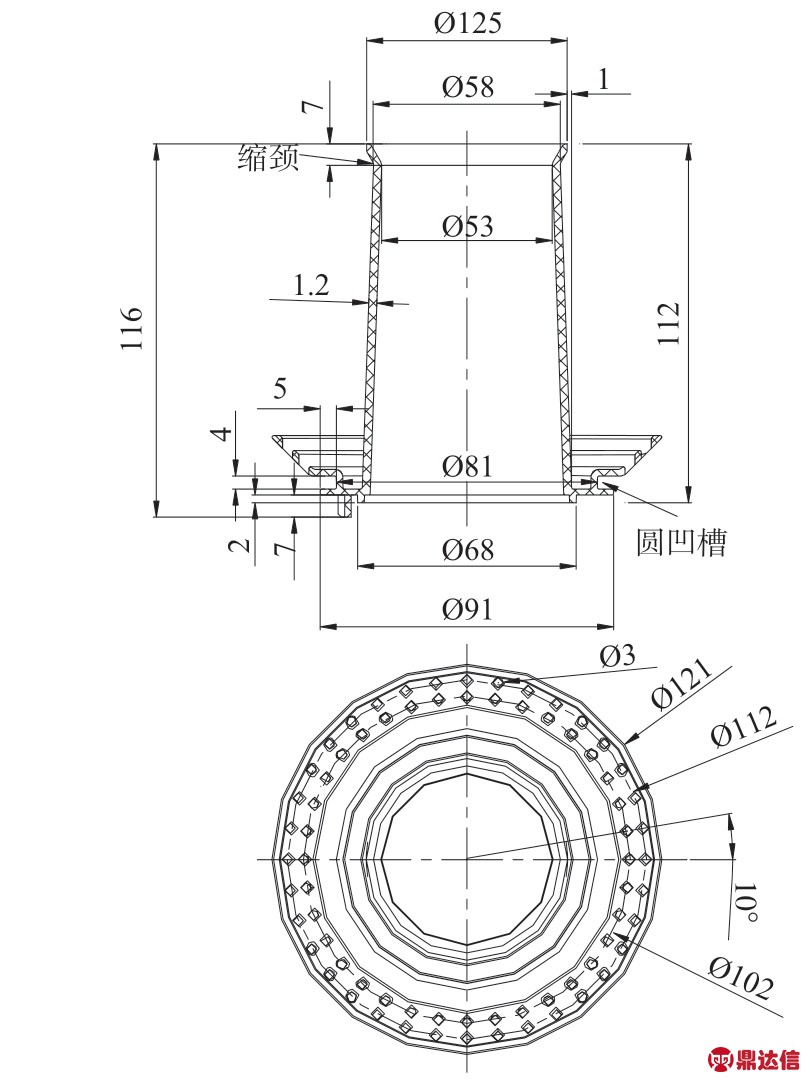
图1 塑件结构
2 模具设计难点
设计该塑件模具时,模具结构设计存在以下几个难点:①塑件为薄壁体,在模腔闭合注塑时,成型件之间不能因高压熔融料流冲击而产生变形,否则会导致圆柱薄壁成型壁厚不均而失败;②缩颈特征处于上端外翻边与下端圆盘中间,该缩颈特征为整圈缩颈,脱模困难;③下端圆盘上设置的72 个孔对型芯的包紧导致整个圆盘脱模困难,脱模时容易产生脱模变形;④圆盘底部的圆环凹槽须整圈侧抽芯脱模;⑤中间圆锥柱与底部圆盘形状差异大,难以获得均匀冷却进而保证两部分的无差异冷却收缩变形。
3 分型设计
针对塑件模具设计的难点问题,分型的合理设计是解决问题的关键。模具分型设计如图2 所示。根据图2,针对上述5 个难点问题,做如下安排:①在塑件内壁的缩颈位置处,设置第一分型面,且内壁的分型仅此一种设计方案;②缩颈特征为侧边内凹,且为整个圆周型,需要进行侧边抽芯脱模,因此设置第二分型面对缩颈所在的外壁圆周进行第二次分割,能保证此分割件取走后,可从上端的成型件中抽出,即塑件能从图2 中所示的避让线构成的圆柱体内向下取出;③在圆盘正上方区域及第二分型面以下外壁区域,设置第三分型面,该分型面为整圆状,以保证外壁成型件的强度,同时,该圆盘外侧区域有72 个孔,包紧力大,因而不宜与其它区域的脱模设置在一起,从而避免产生较大的脱模力,进而避免整个外圆盘脱模时产生较大的变形;④圆凹槽及圆盘下部设置第四分型面,以便于圆凹槽的脱模;⑤第四分型面以下与第一分型面之间区域由第五分型面进行分型。成型件分多步与塑件脱离有利于减小脱模力对塑件脱模产生变形的影响。
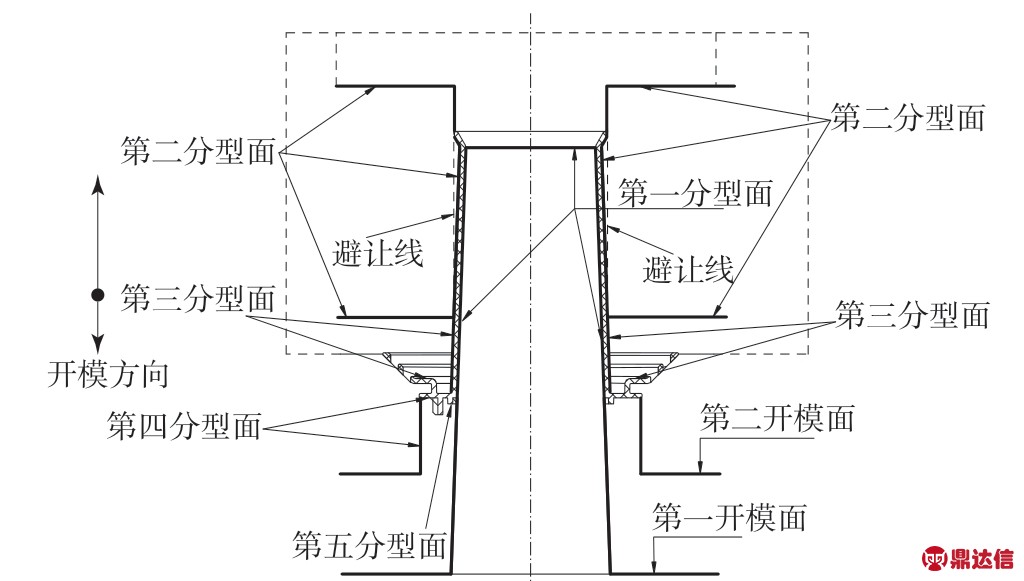
图2 分型设计
按此分型设计,可以设置成如图3 所示的几个塑件成型件:①上端型腔由型腔成型块、第一哈弗成型块、第二哈弗成型块3 个成型件组成;②圆盘外圆由第三哈弗成型块、第四哈弗成型块组成;③下端型芯由型芯成型块、内壁成型块组成。
脱模动作可以设置成以下几步:①注塑完毕后,内壁成型块按F3 方向先从模腔中抽出,内壁先脱模;②上端整圈缩颈特征对应的两个哈弗滑块的成型件——第一哈弗成型块、第二哈弗成型块分别按F1 方向、F2 方向先抽出,从而保证塑件上端的外翻边按F3 方向抽出时能通过型腔成型块的下端口;③外圆凹槽通过第三哈弗成型块、第四哈弗成型块按F4 方向、F5 方向侧抽芯而实现脱模;④塑件最终留于型芯成型块上,其粘模力较小,塑件可以通过顶针顶出脱模而不产生脱模变形。
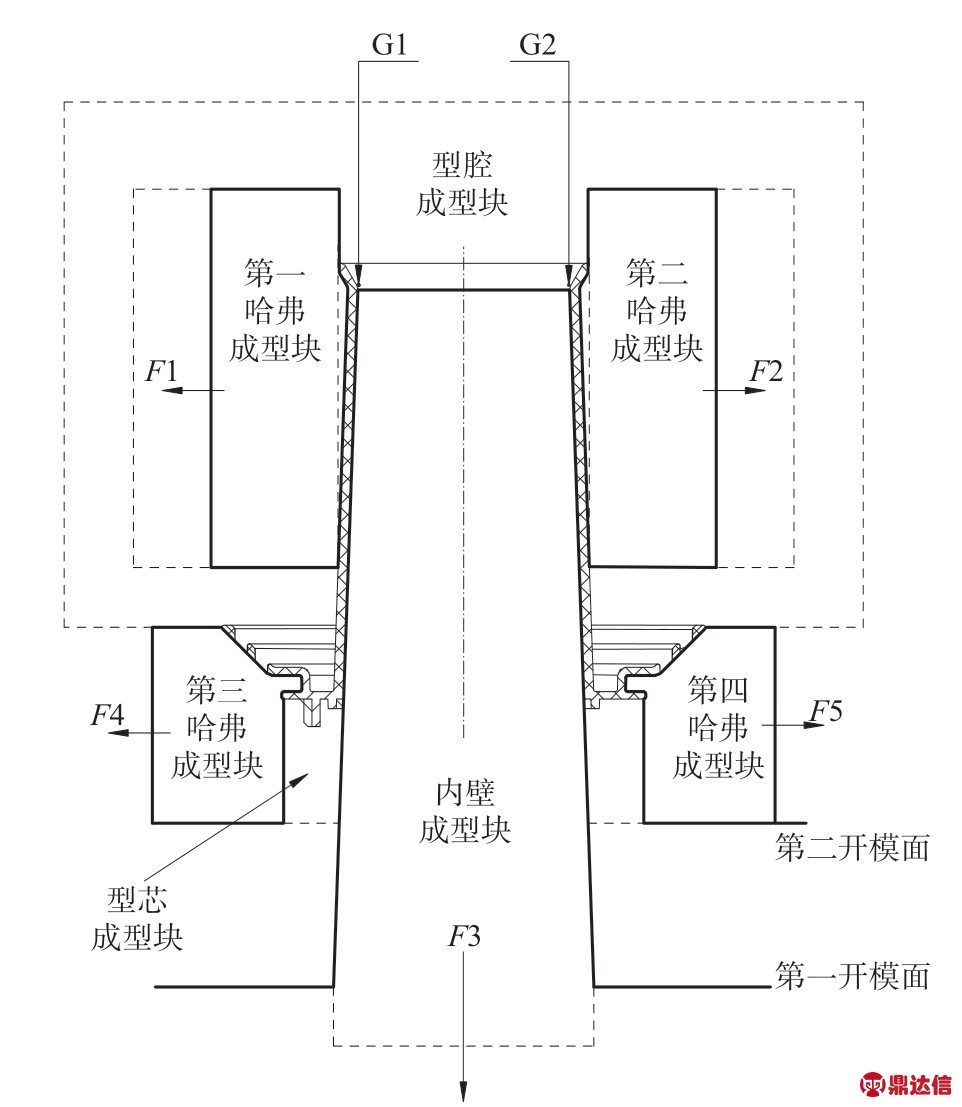
图3 成型件设计
从模具结构的简化而言,可以通过第一开模面的打开,来同步驱动第①、第②步同步动作;可以通过第二开模面的打开来驱动第③步及型腔成型块与塑件分离,这两个动作同步进行。第④步最终顶出可以设置成简单顶杆元件来进行顶出。另外对于塑件的注塑,可方便地在内壁缩颈位置处设置2 个侧浇口(G1 和G2)来对塑件进行浇注,从而避免高温高压熔融料流对内壁成型块的侧向冲击,降低其受冲击产生偏弯变形的可能性,保证塑件的薄壁厚度均匀效果。
因而,按上述分型设计,可解决该塑件模具的设计难题,且明显具有以下优点:①按区域分块成型后,脱模时,各分块成型件的粘模力相对较小,脱模时成型件对塑件的粘连作用力小,将大大减小塑件各区域的脱模变形;②能有效降低成型件的结构复杂性,便于零件加工及内外壁成型件的成型精度,消除因成型件加工误差而导致装配后产生模腔壁厚不均问题;③塑件的缩颈、圆凹槽等特征脱模方便,且脱模力较小;④能有效地避免成型型芯变形;⑤模具结构能实现简化,从而有利于模具制造成本的降低。
4 布局设置
按上述分型及脱模动作设置,塑件在模腔中的布局只能采用一模一腔布局。原因在于第①步、第②步脱模能同时进行,因第一哈弗成型块、第二哈弗成型块为型腔一侧的定模成型块,而内壁成型块为型芯一侧的动模成型块,前者的驱动只能服从于后者的驱动,所以,需要在动模设置一穿过定模的驱动机构件。而第③步的第三哈弗成型块、第四哈弗成型块则需要从定模设置驱动机构件来驱动,因而,对F1,F2 方向构成的直线F1-F2,以及F4,F5 方向构成的直线F4-F5 只能做垂直设置,即塑件的抽芯机构须设置成上、下两层,四面抽芯形式,才能保证4 个抽芯机构的驱动机构在模具空间结构上的无干涉。综上所述,模腔的布局及脱模机构的设置如图4 所示。
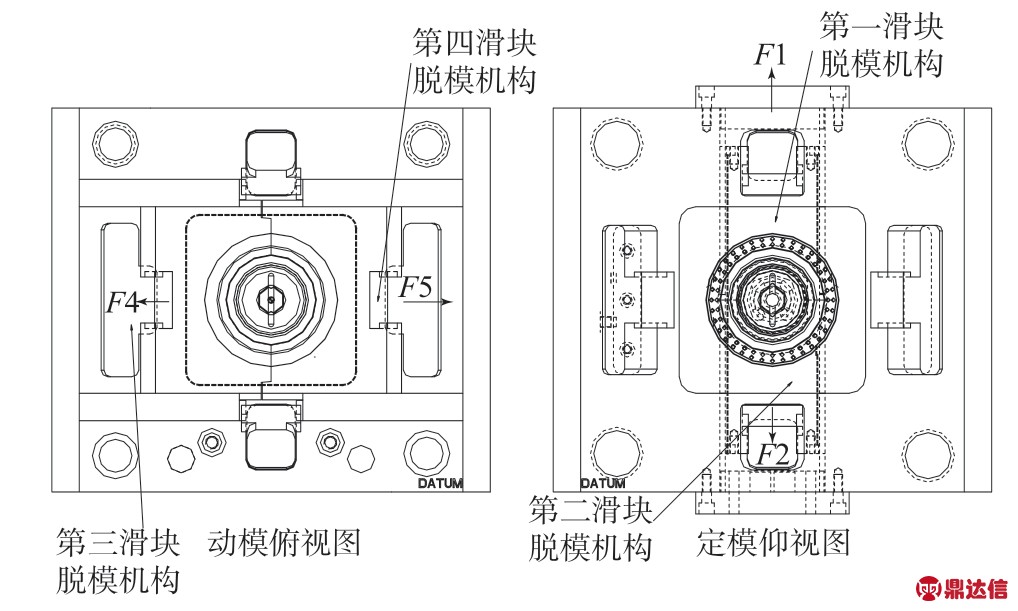
图4 布局设置
5 模具结构
依据前述分型设计及布局设置,模具采用两板模结构,共分为两次开模,如图5 所示。在选用模架时,为保证模具能按P1 →P2 开模面所示分两次开模,模架在动模板9 的下方增设了动模垫板10,动模垫板10 也便于通过定位压块17 来压紧安装内壁型芯镶件16。外型芯镶件18 通过外镶件压环19 压紧安装于动模板9 上。模架规格选用LKM DI3535-A170-B90-C120 型号模架。
5.1 浇口
浇口采用如图3 所示的G1,G2 两点浇口,浇口为扇形冷浇口,浇口截面初始为0.8 mm×2 mm。流道为Ø5 mm 流道,为缩短主流道的长度,将浇口衬套2 直接通过螺钉紧固安装于定模板4 上,并由面板3 上中央位置开设一个孔台肩来将其压紧。定位环1 采用圆环LRA100 型标准件。
5.2 冷却水路

图5 模具结构
1—定位环; 2—浇口衬套; 3—面板; 4—定模板; 5—左楔紧块; 6—左哈弗滑块; 7—左哈弗滑块压条; 8—左滑块限位珠; 9—动模板;10—动模垫板; 11—模脚; 12—底板; 13—顶针盖板; 14—顶针推板; 15—垃圾钉; 16—内壁型芯镶件; 17—定位压块; 18—外型芯镶件;19—外镶件压环; 20—右滑块限位珠; 21—右哈弗滑块压条; 22—右哈弗滑块; 23—右楔紧块; 24—型腔主镶件; 25—密封圈;26—型芯中央圆柱镶件; 27—型腔中央镶件圆环压紧块; 28—顶针; 29—隔水片; 30—拉料杆; 31—前拉块; 32—前哈弗滑块;33—内六角螺丝; 34—后拉块; 35—后哈弗滑块; 36—弹簧拉杆垫套; 37,45—弹簧; 38—弹簧拉杆; 39—定模板导套; 40—动模板导套;41—导柱; 42—复位弹簧; 43—复位杆; 44—动模板拉杆; 46—开锁杆; 47—锁芯弹簧; 48—锁芯; 49—挂钩; 50—锁盒W1~W11—水路编号; P1,P2—开模面
为保证塑件在模腔内能获得均匀的冷却,开设了W1~W11 共11 条随形冷却水路来对成型件进行冷却。动模水路有5 条,分别为:W1 水路用于冷却外镶件压环19;W2,W3 为2 条深井随形水路,用于内壁型芯镶件16 的冷却;W4,W5 分别用于右哈弗滑块22、左哈弗滑块6 的冷却。定模水路有6 条,分别为:W6,W7 用于型腔主镶件24 的冷却;W8,W9 用于型芯中央圆柱镶件26 的随形冷却;W10,W11 分别用于后哈弗滑块35、前哈弗滑块32的冷却。每条水路皆采用Ø8 mm 圆形管道。
5.3 成型件
要保证塑件注塑后壁厚均匀,不但要从浇注系统的影响方面考虑,同时,在成型件的设计中,按分型设计所设置的需要,型腔主镶件24 采用整体式镶件以保证其强度,从而保证塑件的管段外壁的形状不变形,而型芯中央圆柱镶件26 采用简单化圆柱锥形状,以方便加工保证其成型精度。型腔主镶件24中心部位设置一锥台以稳定型芯中央圆柱镶件26。后哈弗滑块35、前哈弗滑块32、右哈弗滑块22、左哈弗滑块6 直接采用T 型槽锁紧块来驱动闭合并锁紧。上述设计与布置有利于这些成型件对应位置处模腔的壁厚得到有效保证。
5.4 哈弗滑块
对应于前述分型设计,塑件上的圆环缩颈采用两个定模哈弗滑块来成型和脱模,其成型滑块分别为前哈弗滑块32、后哈弗滑块35;机构中,前哈弗滑块32、后哈弗滑块35 结构相似,对称布置,以后哈弗滑块35 机构为例,其结构组成主要包括零件34~零件38,工作时,由跟随动模垫板10 同步后退的后拉块34 通过斜T 型槽驱动后哈弗滑块35 来进行侧抽芯。
圆环凹槽采用两个动模哈弗滑块来成型和脱模,其成型滑块分别为左哈弗滑块6、右哈弗滑块22。机构中,左哈弗滑块6 和右哈弗滑块22 的结构相似,以左哈弗滑块6 的机构为例,其主要组成件包括零件5~零件8,工作时,由左楔紧块5 通过斜T 型槽驱动左哈弗滑块6 进行侧抽芯和闭模时的锁紧,该侧抽芯行程为27 mm。右哈弗滑块22 机构的组成件包括零件20~零件23。由右楔紧块23 通过斜T 型槽驱动右哈弗滑块22 进行抽芯和闭模时的锁紧,该侧抽芯行程为15 mm。
5.5 开模机构
模具分两次开模,P1 处开模由弹簧45 驱动,并由拉杆44 定距,开模距离为35 mm。P1 处开模时,动模垫板10 带动前拉块31、后拉块34 完成各自对应的滑块——前哈弗滑块32、后哈弗滑块35的15 mm 的侧抽芯,抽芯完毕,由弹簧37 拉住,靠边定位不动,等待模具闭合时,前拉块31、后拉块34再次插入驱动其复位。
为保证开模时先打开P1,后打开P2,在P2 处设置了一个常用型模板锁闭机构,机构的组成件包括零件46~零件50,P1 打开30 mm 后,开锁杆46 开始驱动锁芯48 的左端压迫锁芯弹簧47 而向左运动,锁芯48 的右端开始脱离挂钩49 而将定模板4 和动模板9 的锁闭打开。由于P1 只能打开35 mm,故P1 打开后,开锁杆46 的上端一直压住锁芯48 而使该锁闭机构保持开锁状态,直到P1 重新闭合,机构再次锁闭定模板4 和动模板9。P2 打开的距离为130 mm。顶针板顶出高度70 mm,P1打开后,顶针28 实际将塑件从外型芯镶件18 上顶出的高度为35 mm (70 mm-35 mm)。取件需要采用机械手自动取件。
6 工作原理
模具装于注塑机台上后,模具动作过程如下:(1)模具闭合。经注塑,保压冷却后,模具等待开模。
(2) P1 处开模。注塑机动模板带动模具动模后退,此时锁闭机构将定模板4 和动模板9 锁闭,在弹簧45 的弹开下,模具首先在P1 处打开,打开时,动模垫板10 带动内壁型芯镶件16 先抽芯,同步地,也带动前拉块31 和后拉块34 驱动位于型腔主镶件24 内的两个哈弗滑块——前哈弗滑块32、后哈弗滑块35 进行抽芯。
(3) P2 处开模。动模继续后退,锁闭机构开锁,模具在P2 处打开,打开时,左哈弗滑块6 和右哈弗滑块22 被相应的左楔紧块5 和右楔紧块23 驱动,完成侧面抽芯动作。
(4)顶出。开模完毕,注塑机顶杆驱动顶针板(顶针盖板13 和顶针推板14)向上顶出,驱动顶针28 及拉料杆30 将塑件及流道废料同步从型芯顶出,完成塑件的完全脱模。
(5)复位闭合。复位时,动模上行,顶出板在复位弹簧42 的驱动下先复位,模具按P2 →P1 顺序完全闭合,等待下一个注塑循环。
7 结语
针对薄壁塑件定模与动模都须实施哈弗滑块侧抽芯脱模的特点,设计了其一模一腔两板两次开模注塑模具。采用内侧两点扇形浇口进行浇注,以降低料流对型芯的冲击,避免造成型芯偏移变形而导致塑件壁厚均匀性变差。针对中央成型件亦做锥台配合定位形式以增强型芯在料流冲击下的稳定性。在成型件设计中,通过设置多个成型件分多次脱模的方式,以减小脱模力过大造成薄壁塑件的脱模变形。脱模机构设置了2 组、四面分布的哈弗滑块来实施缩颈、圆凹槽特征的脱模。在模具结构设计中,巧妙地利用动模的一次开模来驱动定模抽芯机构进行侧抽芯,利用动模的二次开模来驱动动模抽芯机构进行二次侧抽芯,有效地简化了模具结构,简化了机构件的设计,降低了模具的制造成本。