摘要 提出一种齿轮副齿面磕碰点检测方法,用于确定弧齿锥齿轮齿面磕碰点位置。建立准双曲面齿轮副啮合模型,通过改变接触区偏移量,调整啮合参数V、H、J,从而得到规划路径下的TCA接触区位置,V、H、J调整结果用于指导滚检试验。在YX-HTT600齿轮综合误差测量及分析试验机上进行滚检试验,得到了准双曲面齿轮副正常齿面与存在磕碰点的齿面两种情况下的传动误差测量结果。通过对两种传动误差测量结果的对比,验证了提出的齿面点测量方法的可行性。试验结果表明,运用提出的齿面检测方法可实现弧齿锥齿轮全齿面检测,检测结果可反映齿面磕碰点位置,从而为进一步改善弧齿锥齿轮啮合性能奠定基础。
关键词 准双曲面齿轮 路径规划 TCA仿真分析 传动误差
0 引言
弧齿锥齿轮由于其重合度高、传动平稳等优点,作为关键传动部件被广泛应用于航空航天领域。磕碰点属于齿形损伤的一种,产生的原因是弧齿锥齿轮在加工、运输及安装过程中,齿面受到碰撞而产生齿面局部位置凸起,对齿轮副啮合性能产生影响,因此磕碰点的本质是实际齿形与设计齿形在形状上的差异[1]。由于磕碰点在齿面上的位置不确定,并且人眼一般难以分辨齿面上的磕碰点,导致齿轮副啮合性能下降,从而影响齿轮传动链的接触强度和生命周期,严重时可造成设备的重大损伤,因此需要针对齿面磕碰点相对位置的检测方法进行研究。
中航工业航空动力机械研究所的江平等[2]为了降低弧齿锥齿轮副的振动与噪声,提出一种基于传动误差曲线优化的弧齿锥齿轮接触印痕高度的控制方法;亚琛工业大学的Klocke F等[3]通过对齿轮加工过程中出现的制造缺陷与仿真结果比较,得到齿面加工过程中刀具对齿面缺陷的影响;河南科技大学的曹雪梅等[4]根据三坐标测量机测得的实际齿面坐标,精确地反映了齿面误差,为制造高精度的航空弧齿锥齿轮提供了有效的方法;武汉理工大学的黄丰云等[5]通过对主减速器齿轮啮合的振动进行监测,以判断齿轮是否存在的故障及故障类型;东北大学的王奇斌等[6]建立了考虑齿廓偏差的齿轮啮合刚度和传递误差激励模型、齿轮系统振动模型,分析了齿轮系统在啮合刚度激励和传递误差激励下的振动特性。齿面磕碰点属于齿轮制造缺陷的一种,对齿轮副的传动误差及振动等啮合性能都有很大影响,但国内外文献鲜有涉及齿面磕碰点检测方法。
本文中我们提出一种弧齿锥齿轮齿面磕碰点检测方法,该方法用于轻载条件下检测齿面磕碰点。科学规划轻载接触区移动路径,制定V、H、J调整计划,通过MATLAB进行接触区调整计算,检测整个齿面,并根据齿轮副啮合情况判断磕碰点位置。
1 啮合模型的建立
1.1 齿面方程
建立主从动轮加工数学模型,将刀具切削面方程经过一系列坐标变换至待加工齿轮坐标系中,并联立啮合方程求解得到两轮的齿面方程r1(θ1*,φp*)、r2(θ2*,φg*)和单位法矢n1(θ1*,φp*)、n2(θ2*,φg*)。
根据文献[7],将两轮位置矢量和单位法矢分别表示在啮合坐标系中。准双曲面齿轮装配过程中,安装误差主要包括主动轮安装距变动量ΔH、从动轮安装距变动量ΔJ、轴线偏置距变动量ΔV,分别对应主动轮安装距H、从动轮安装距J、轴线偏置距V。图1为存在安装距变动量的齿轮副啮合坐标系,其中,S1为与主动轮固连的坐标系O1x1y1z1,S2为与主动轮固连的坐标系O2x2y2z2,Sh为固定坐标系Ohxhyhzh,Sd为与Sh固连的坐标系Odxdydzd。Mh1、Mhd、Md2为坐标系之间的转换矩阵,分别为

(1)
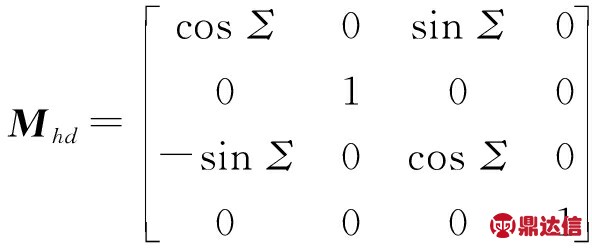
(2)
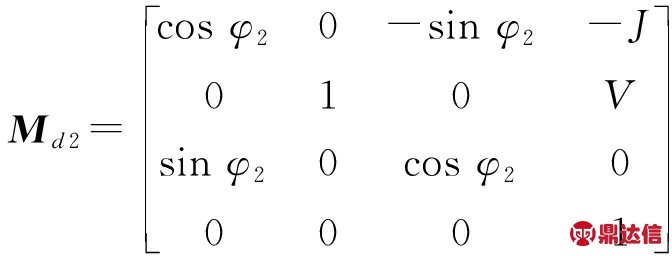
(3)
式中,φ1为啮合时主动轮转过的角度;Σ为轴交角;φ2为啮合时从动轮转过的角度。
将准双曲面齿轮齿面和法线分别转换到固定坐标系Sh中,得到准双曲面齿轮位置矢量和单位法矢,为
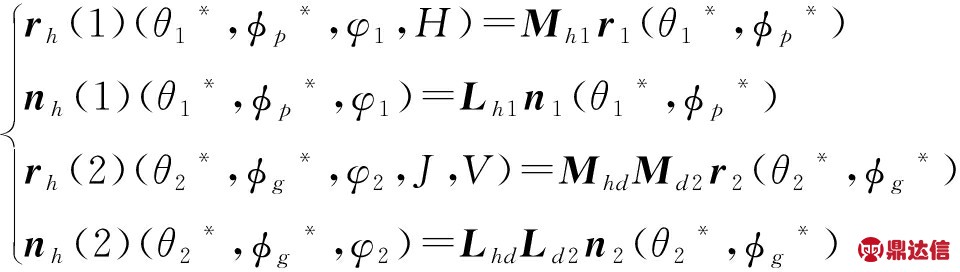
(4)
式中,φ1′为主动轮当前转角;φ2′为主动轮当前转角;φ10为主动轮初始转角;φ20为从动轮初始转角;z1为主动轮齿数;z2为从动轮齿数。
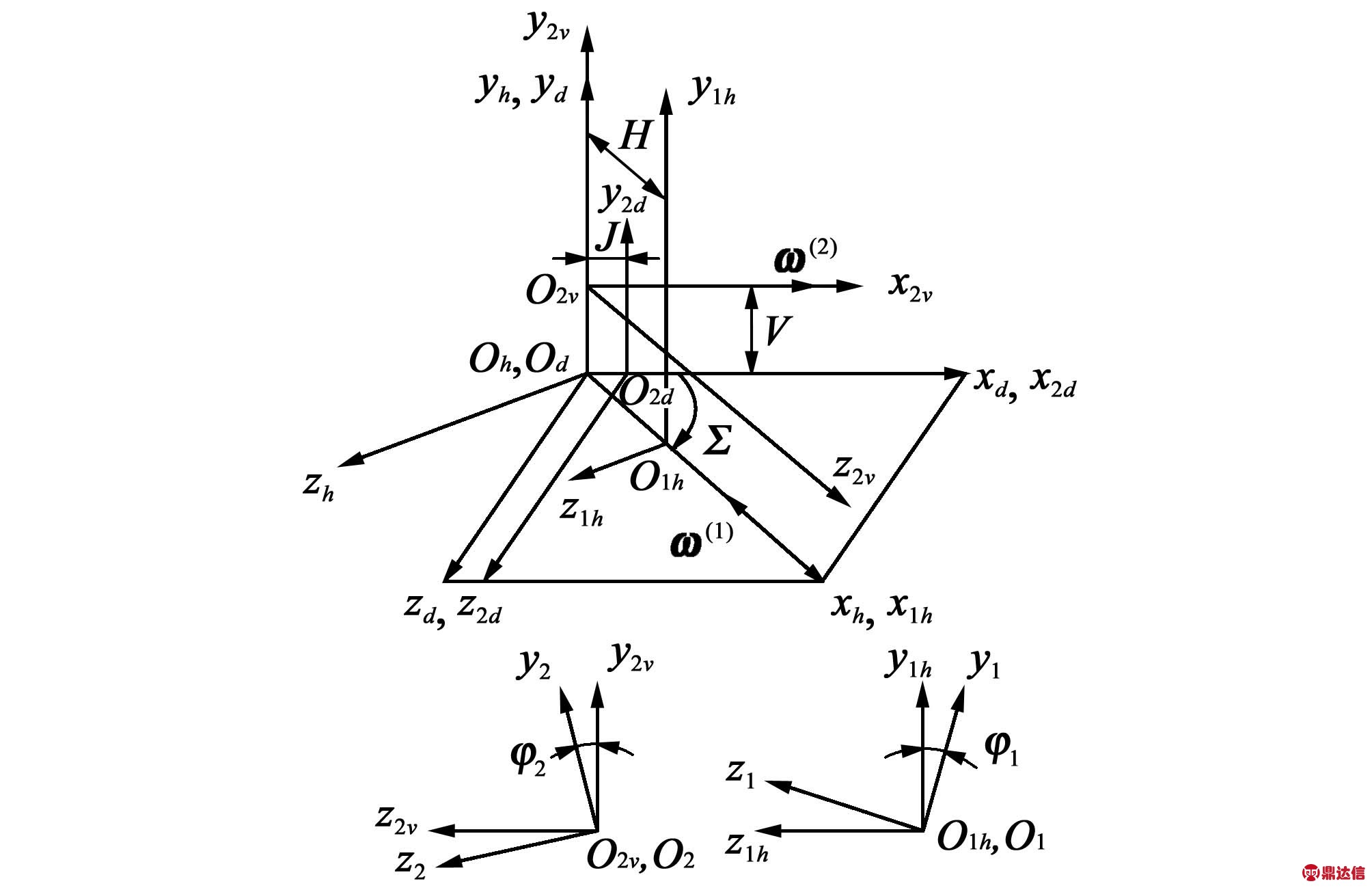
图1 弧齿锥齿轮副啮合坐标系
1.2 V、H、J与接触区位置关系模型
齿面啮合需要满足共轭条件,即齿面啮合点具有相同的位置矢量和单位法矢,齿面方程表达式为

(5)
根据齿轮啮合原理,在名义接触点处的啮合方程为
nh2M·vh(12)=f(θ1*,φp*,φ1,θ2*,φg*,φ2,V,H,J)=0
(6)
式中,θ1*为展成主动轮齿面时刀盘转角;θ2*为展成从动轮齿面时刀盘转角;φp*为展成主动轮齿面时摇台转角;φg*为展成从动轮齿面时摇台转角;Lhd为Mhd的前3×3阶子矩阵;Ld2为Md2的前3×3阶子矩阵。
依据文献[8]14-15的计算方法,齿轮副空间位置控制量V、H和J会对轮齿啮合时的齿侧间隙产生影响,齿轮副的空间位置与齿侧间隙关系为
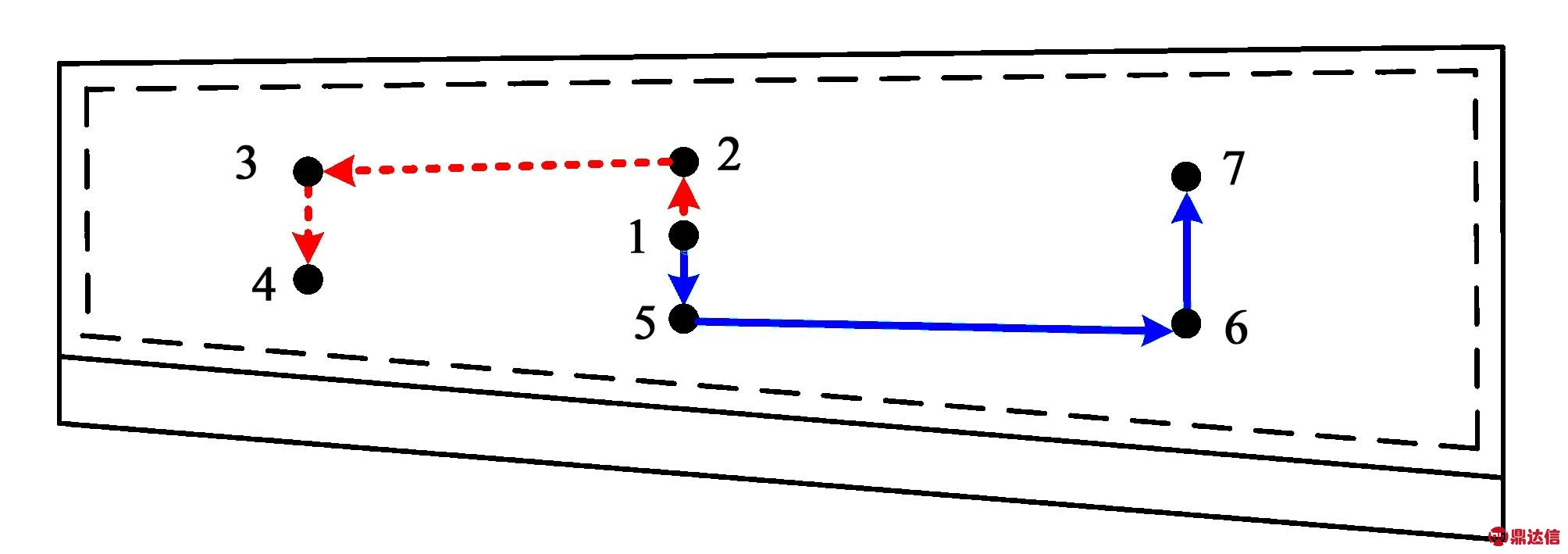
(7)
式中,δ2为从动轮节锥角;r2为从动轮名义半径;E为准双曲面齿轮的偏置距。
给定接触区调整后啮合点在齿面上的位置(x2,y2,z2),调整后接触点的位置相对于名义接触点在齿长、齿高方向上变动量分别为s1与s2[8]15-16。由齿面几何关系可确定调整后接触点位置位于旋转投影坐标系OX2Y2中的坐标为该点与齿面三维坐标系对应点的坐标关系为
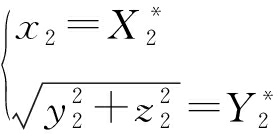
(8)
式中,(x2,y2,z2)为从动轮齿面方程r2(θ2*,φg*)的坐标分量。
由式(8)可求出θ2*和φg*,式(5)~式(7)有7个未知量,7个独立方程,经过MATLAB计算可以求解出运动参数V、H、J的值。
将参数V、H、J调整后的值代入式(5)中进行求解,得到主动轮转角Δφ1与从动轮转角Δφ2之间新的函数对应关系。通过赋予主动轮当前转角φ1′不同的值(一定步长),可以得到与之对应的从动轮转角φ2′,从而得到齿轮副传动误差,为
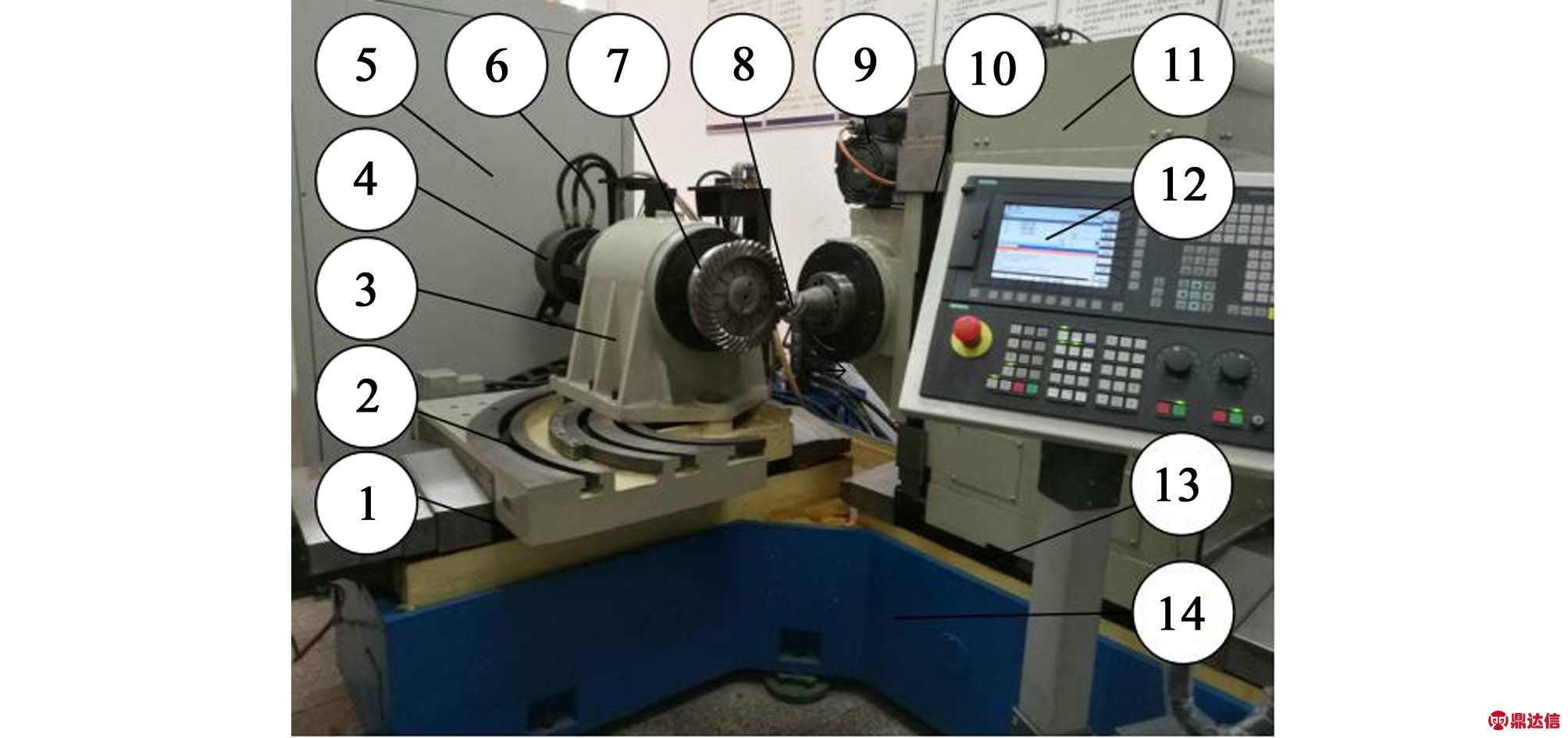
(9)
式中,nh2M为啮合点的公共法矢;vh(12)为啮合点的相对运动速度。
2 接触中心路径规划
齿轮副在实际运转过程中,由于载荷作用,齿面接触区面积相对于准静态条件下会变大,原本位于接触区范围外的磕碰点会进入接触区,从而对齿轮副啮合性能产生影响。本文中将接触中心作为路径规划对象,通过调整接触区位置,从而实现全齿面检测。考虑到大多数齿轮副标准安装条件下的接触区位置,规划路径起始点选择接触中心在齿面中部靠近小端。
考虑到轮齿边缘处倒角、国家标准对接触区齿长和齿高方向的要求以及不出现边缘接触等因素,本文中设定虚线距理论齿顶线、齿根线、小端线、大端线的距离为齿高的5%[9]。齿面啮合接触中心路径规划为如图2所示,图中的虚线框表示接触区可变动区域。
选择点1作为接触中心起始点。由齿面中部向齿顶移动,再移动至小端齿顶,之后向小端齿根移动。图2中 虚线路径表示接触中心依次经过点1、2、3、4移动过程。重新将齿轮副调整至标准安装位置后,调整V、H、J使得接触中心由齿面中部向齿根移动,再移动至大端齿根,之后向大端齿顶移动。图2中实线路径表示接触中心依次经过点1、5、6、7的移动过程。规划路径下7个位置保证磕碰点检测区域覆盖整个齿面。
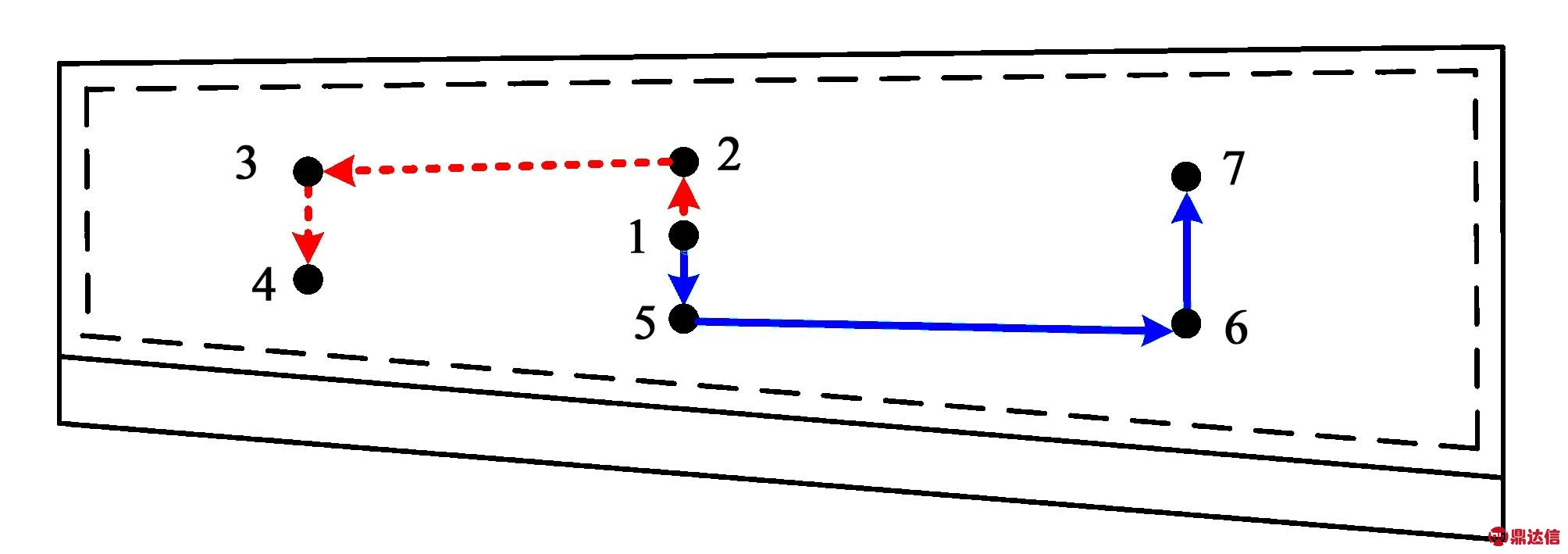
图2 从动轮齿面接触中心移动路径
3 V、H、J调整仿真分析
以一对准双曲面齿轮为研究对象,准双曲面齿轮几何参数见表1,机床加工参数见表2,以主动轮凹面和从动轮凸面啮合情况为例。考虑到从动轮安装距变动量ΔJ只对轮齿啮合侧隙有影响,对接触区的位置影响很小,且滚检过程中的J调整量较小[8]19-22。因此,通过调整主动轮安装距变动量ΔH及轴线偏置距变动量ΔV,实现对弧齿锥齿轮齿轮副接触区位置的调整。
3.1 齿轮副及加工参数
轮坯几何参数见表1,加工参数见表2。
表1 准双曲面齿轮几何参数
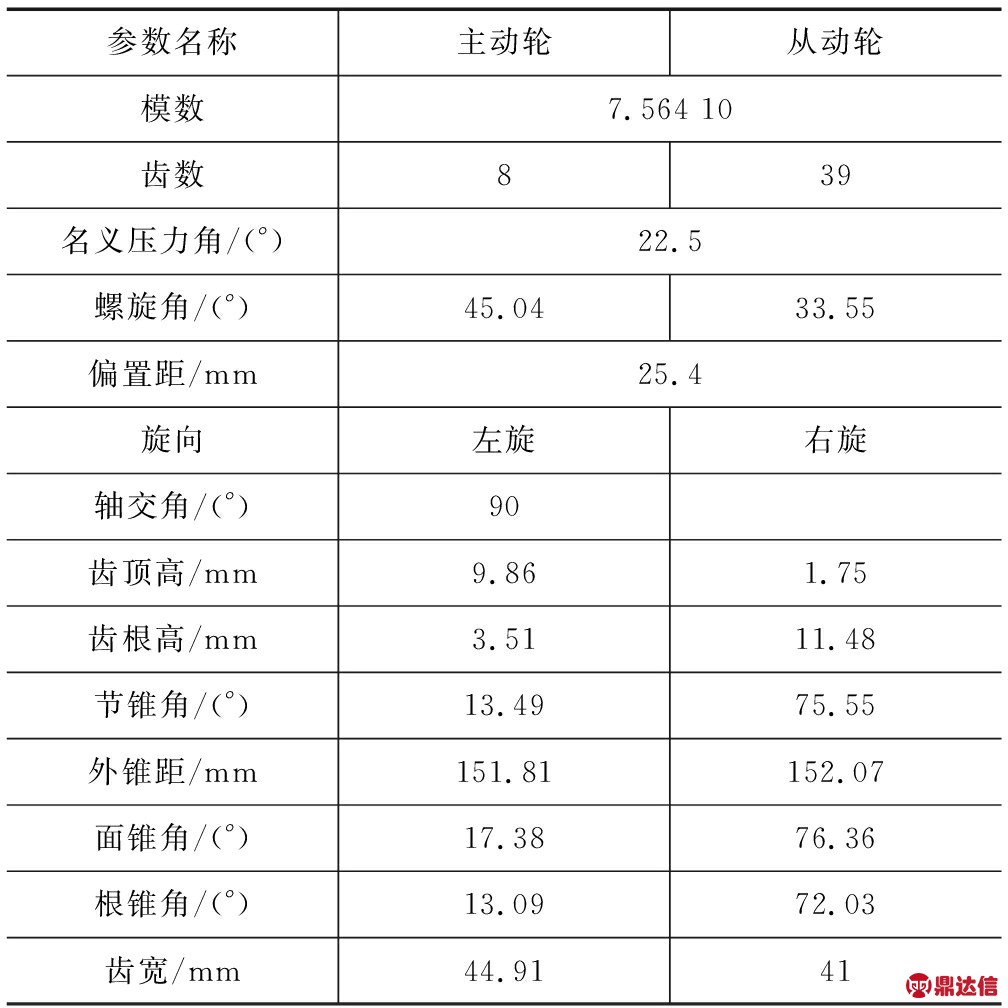
表2 机床加工参数
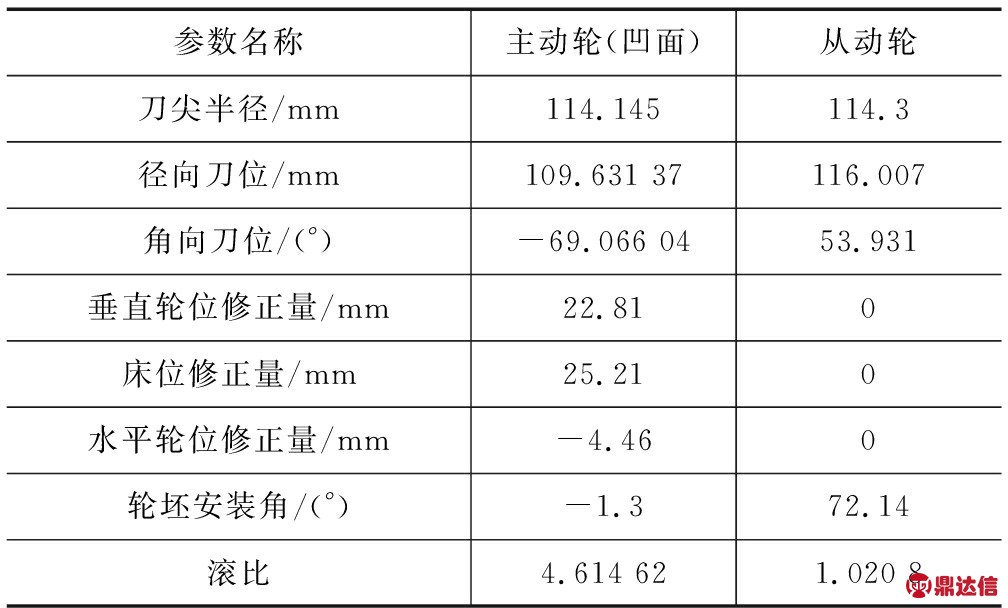
3.2 TCA结果
基于MATLAB的轮齿接触分析程序,通过调整接触区位置,得到对应的准双曲面齿轮副啮合参数V、H、J变化量[10]。本节中选取图2中7个接触中心位置作为检测区域。针对上述7个检测区域进行TCA分析,得到接触区位置仿真图像及对应的V、H、J变动量,如图3所示,用于指导滚检试验。
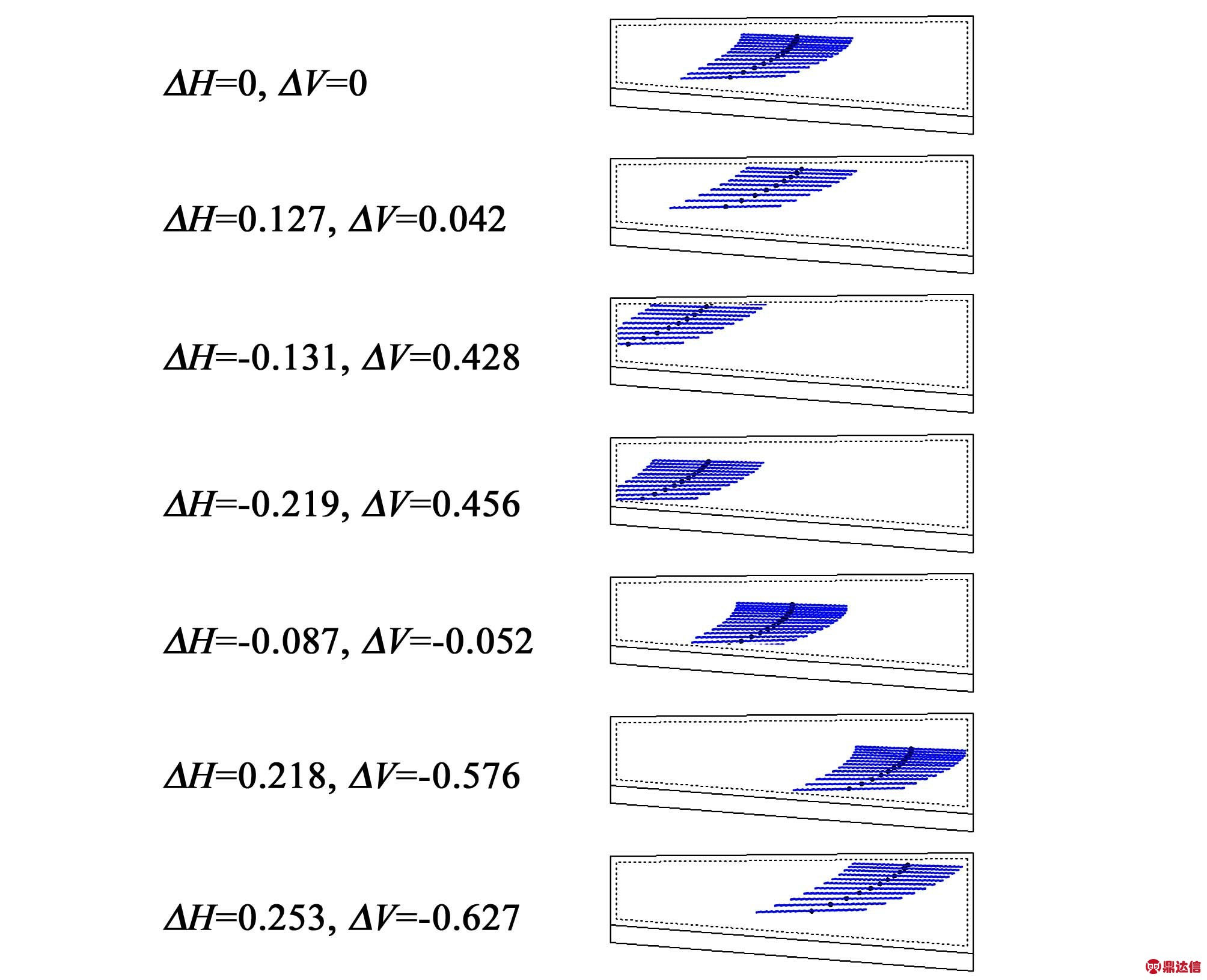
图3 接触区调整对V、H、J变化量的影响
通过编程计算得到7个检测区域相应的理论传动误差曲线,其幅值如表3所示。
表3 理论传动误差曲线幅值
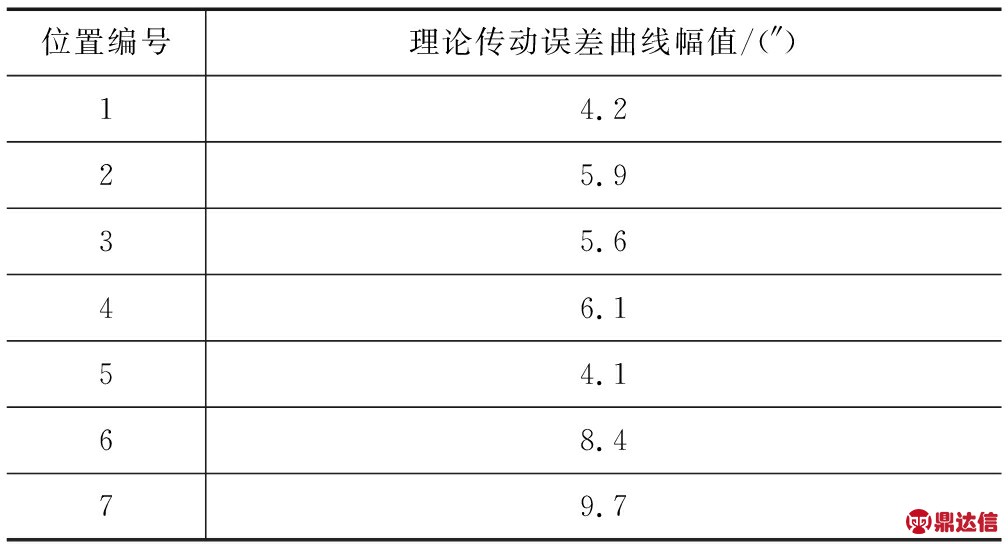
4 滚检试验
试验选取一对8-39的准双曲面齿轮为对象,其轮坯几何参数及加工参数分别对应表1及表2。试验选取主动轮凹面及从动轮凸面为研究对象。
4.1 V、H、J调整与传动误差试验
为检验接触区计算及路径规划的正确性,采用YX-HTT600齿轮综合误差测量及分析试验机进行试验,试验过程如图4所示。滑台1、2、3分别实现X、Y、Z三个方向的进给运动,其中,滑台1可调整齿轮副轴交角。机床由数控面板控制伺服电机1、2、3的运动,啮合参数V、H、J调整分别对应机床Z、X、Y三个方向的移动。齿轮通过液压机构实现装夹。主动轮由伺服电机驱动回转,与从动轮啮合实现齿面检测。
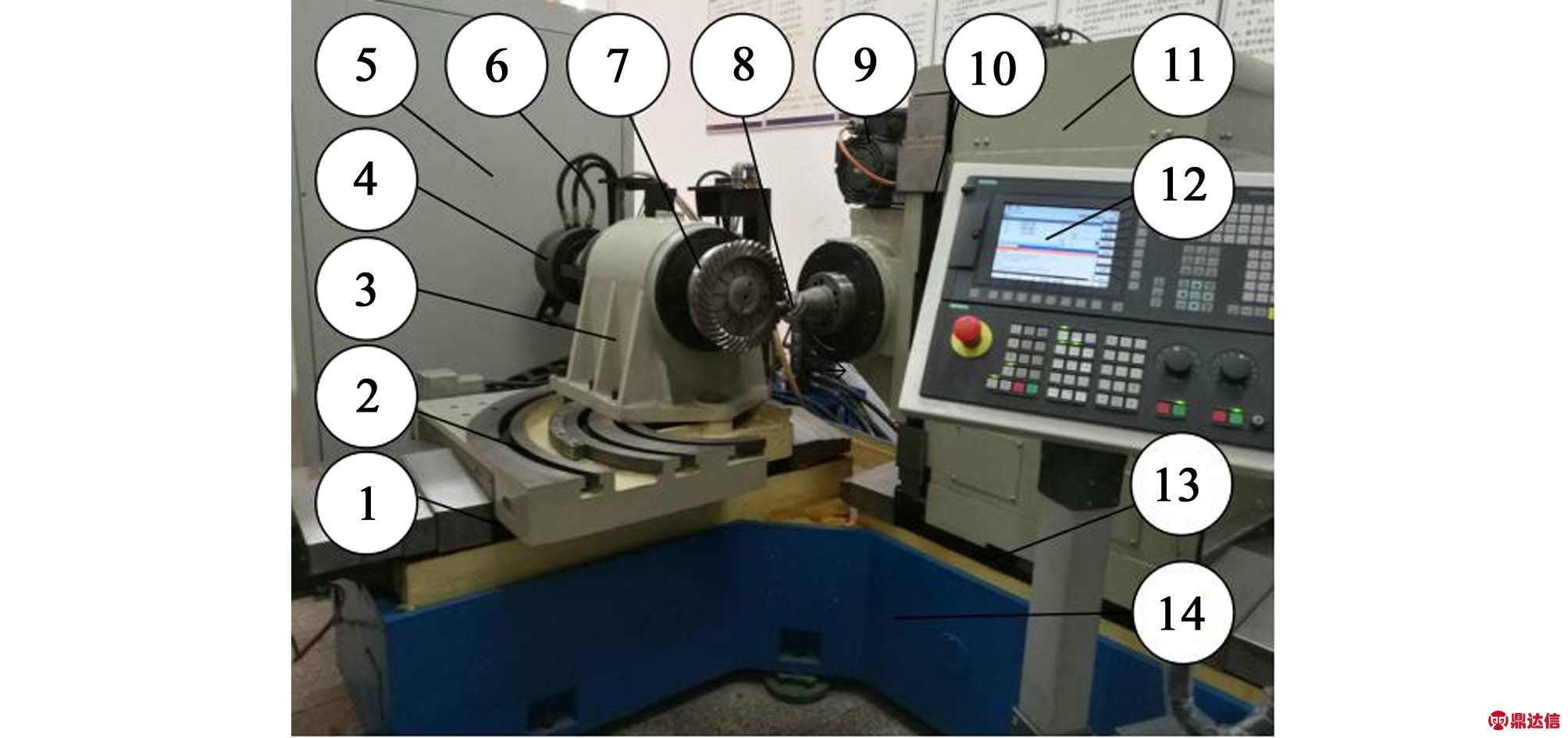
1 X向导轨 2 床鞍 3 被动轮工件箱 4 液压缸 5 配电柜 6 液压管 7 被动轮 8 主动轮 9 伺服电机 10 Z向导轨 11 主动轮工件箱 12 控制面板 13 Y向导轨 14 底座
图4 滚检试验装置
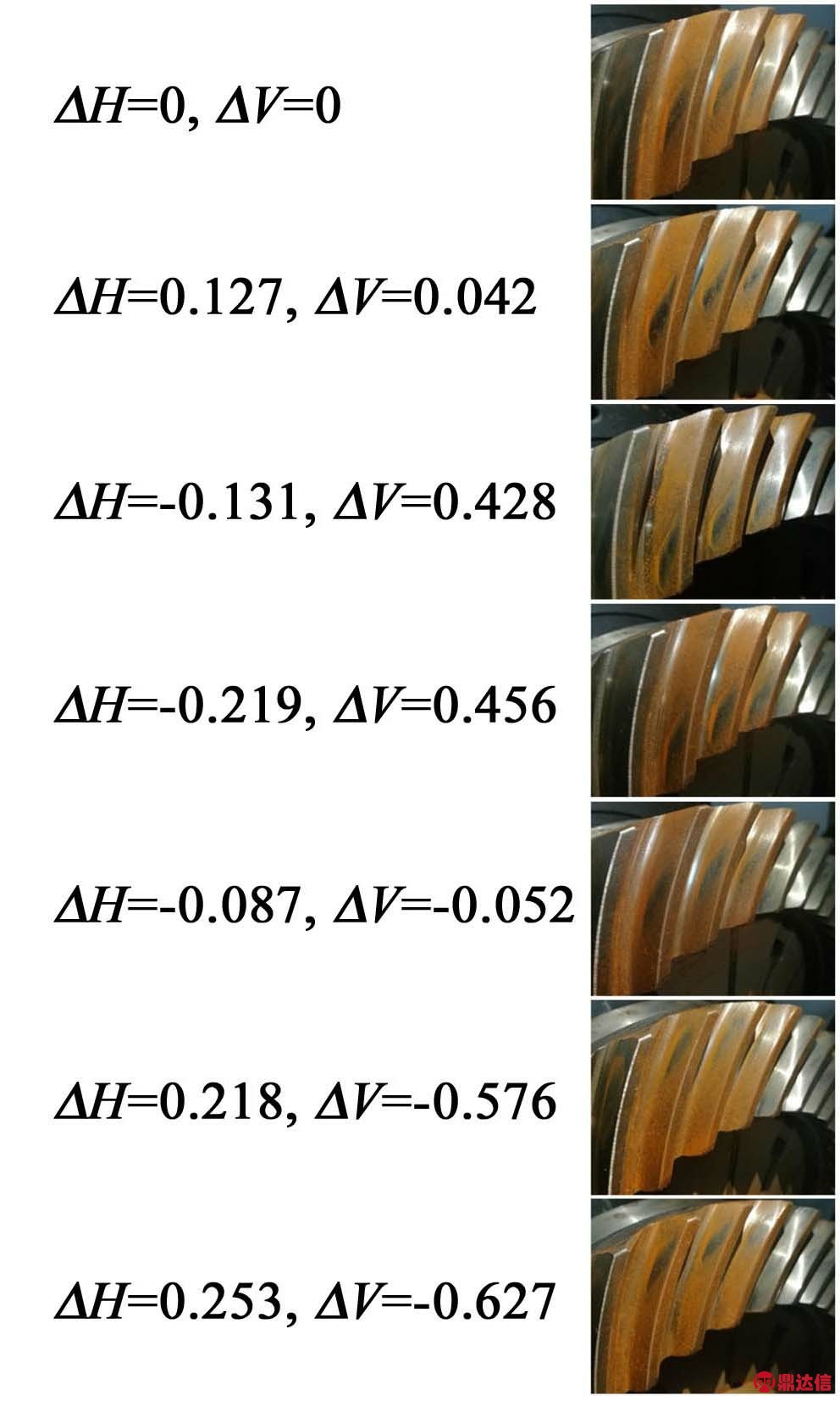
图5 滚检试验V、H、J调整接触区
试验前在从动轮相邻三齿面涂上红丹粉。在低速、轻载条件下,通过对啮合参数V、H、J进行调整,得到与TCA结果对应的接触区位置,如图5所示。接触区调整过程保证了齿面磕碰点检测结果的可靠性。
滚检试验过程中,与主从动轮固连的轴上安装有编码器,用于检测主从动轮转动信号。编码器的输出脉冲通过专用数据采集卡进行动态数据采集。计算机中专用软件对采集信号进行处理,得到单齿传动误差测试曲线。通过调整V、H、J,改变准双曲面齿轮副接触区位置,得到对应上述7个检测区域的传动误差曲线,如图6所示。
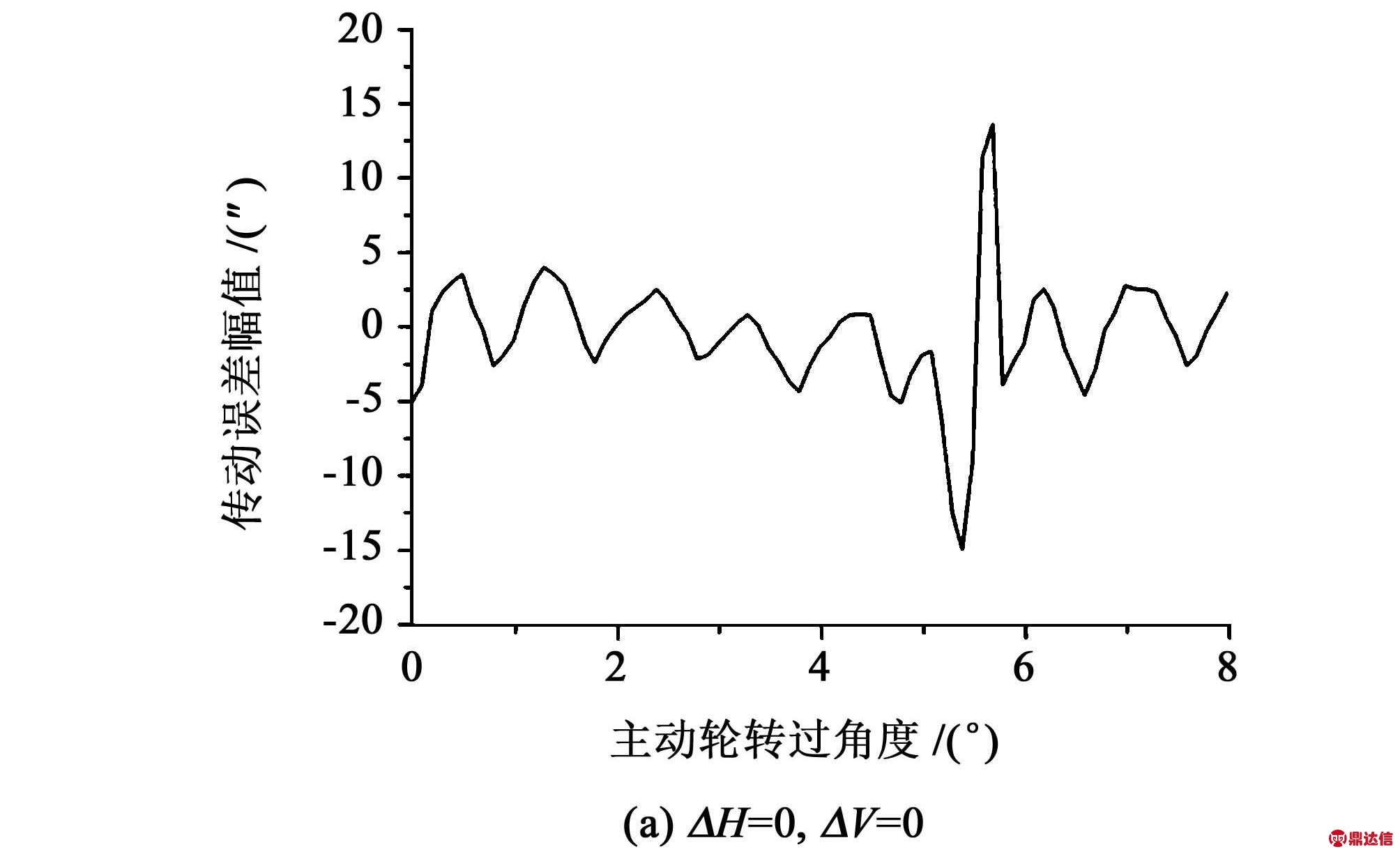
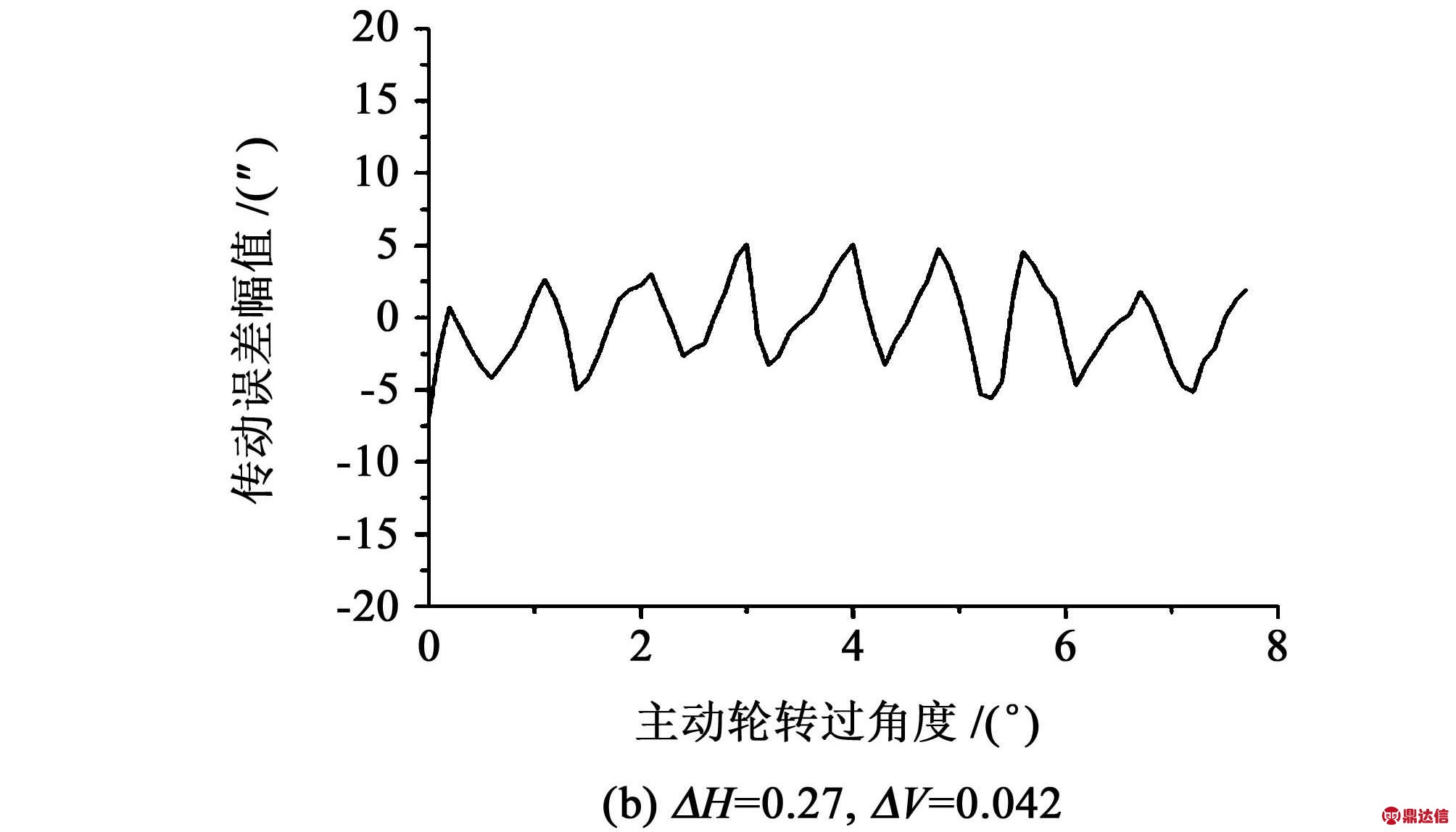
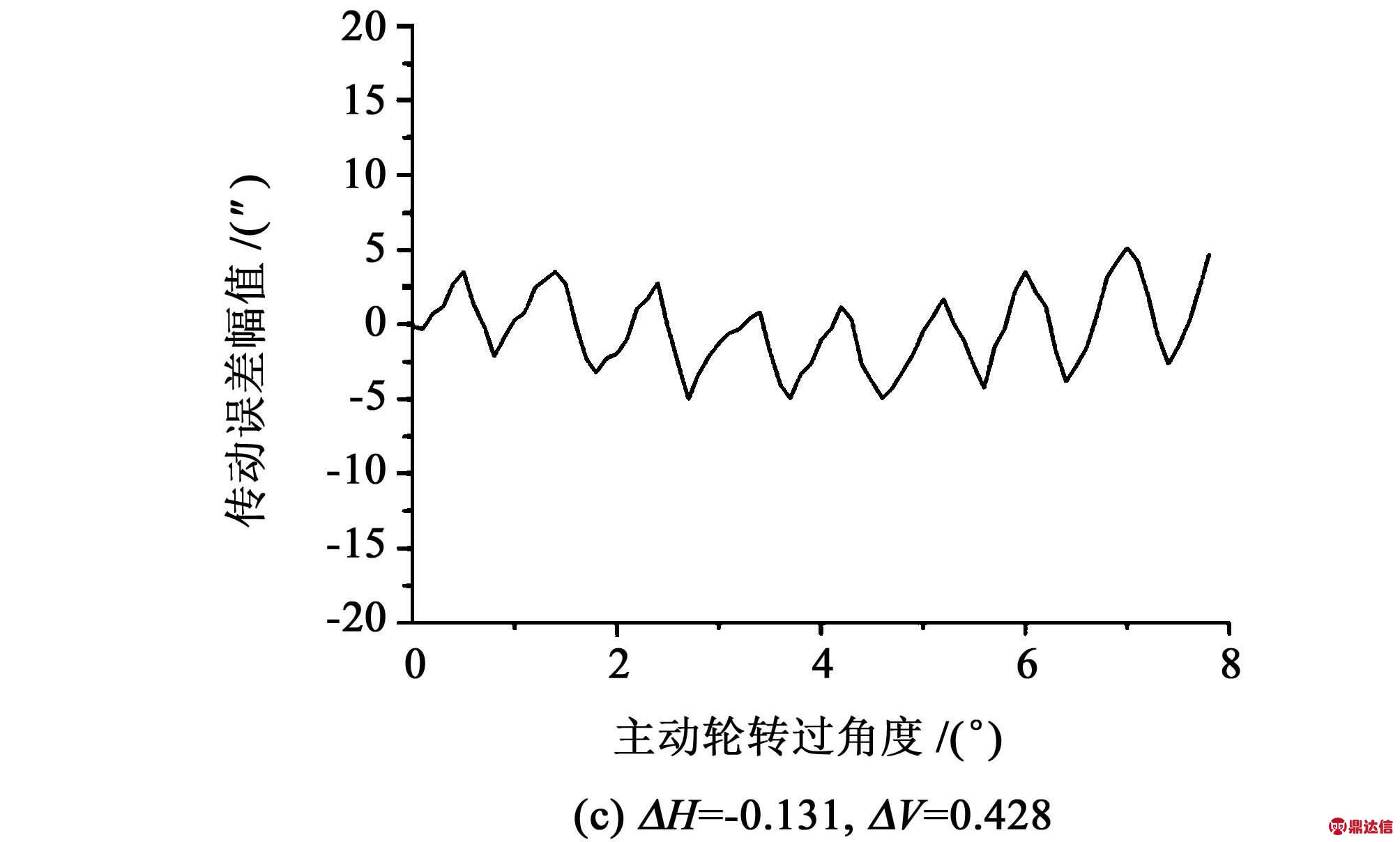
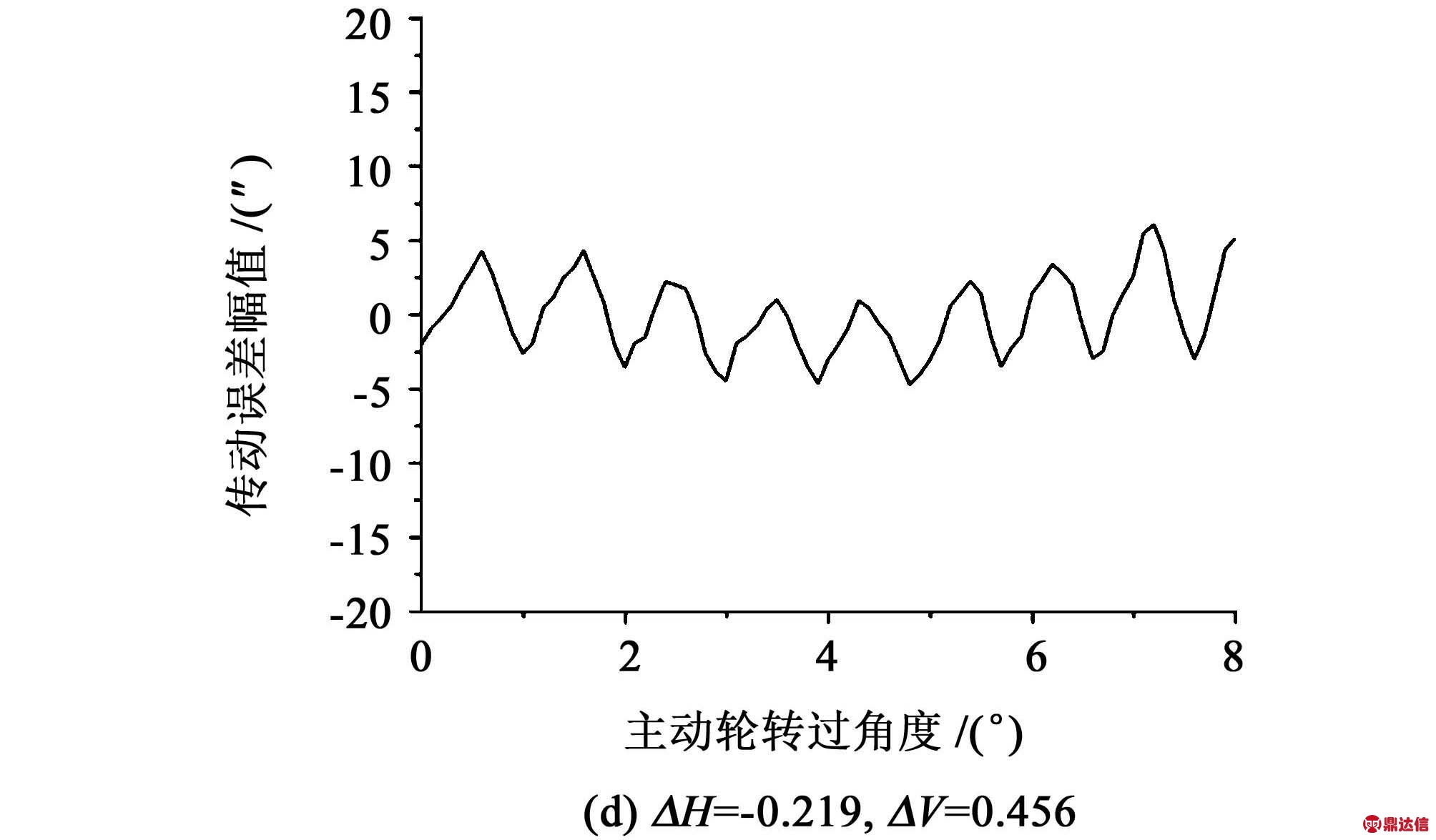
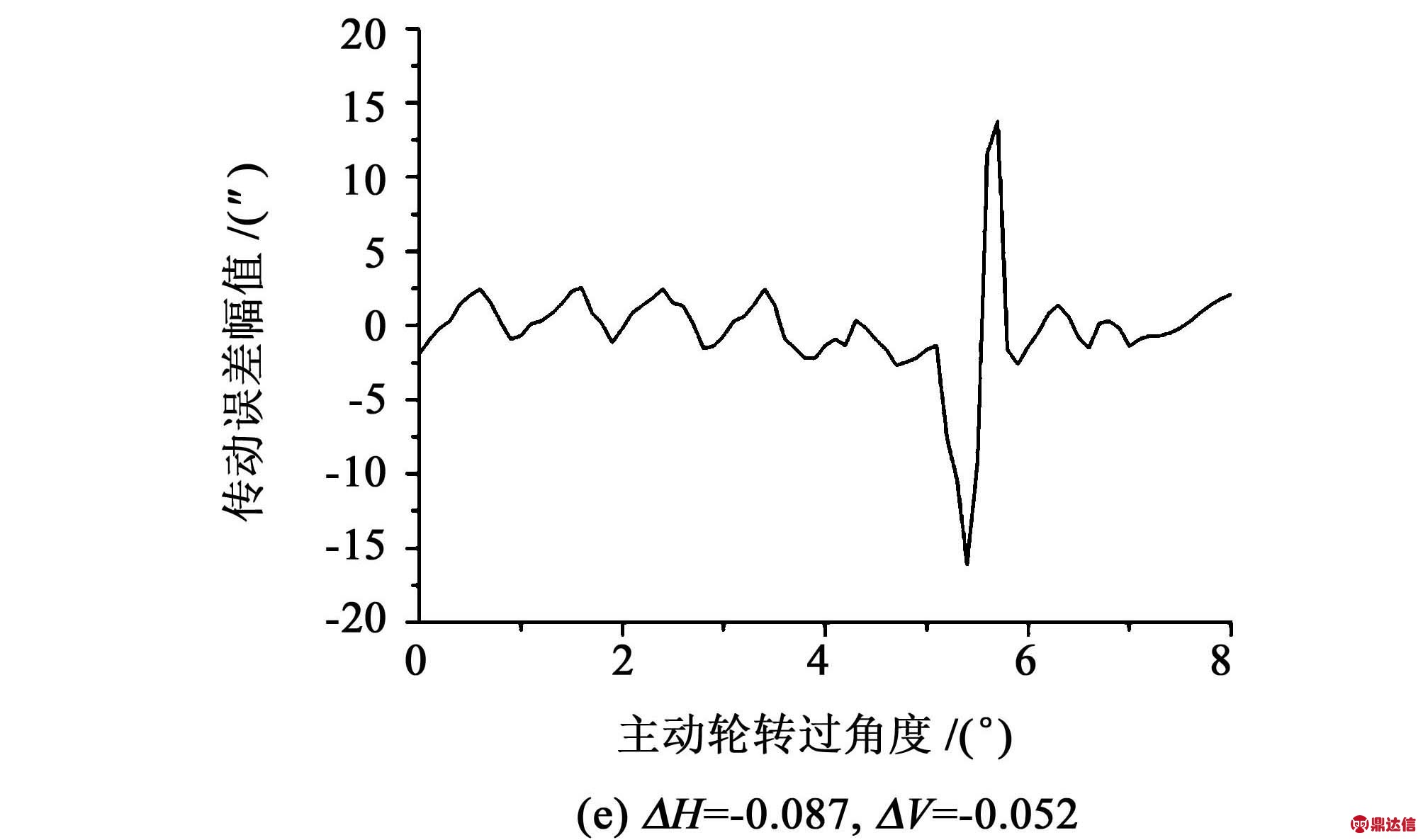
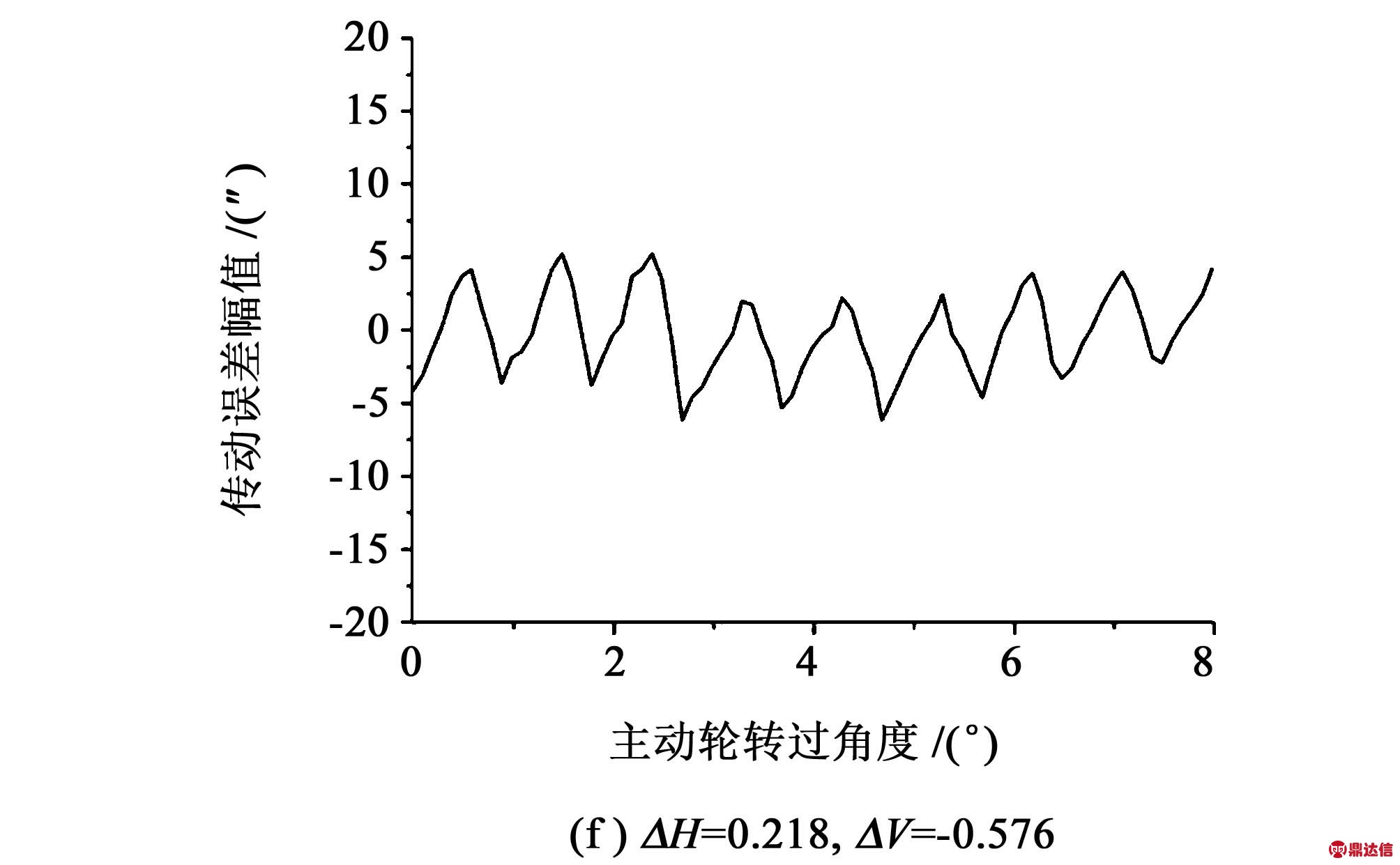
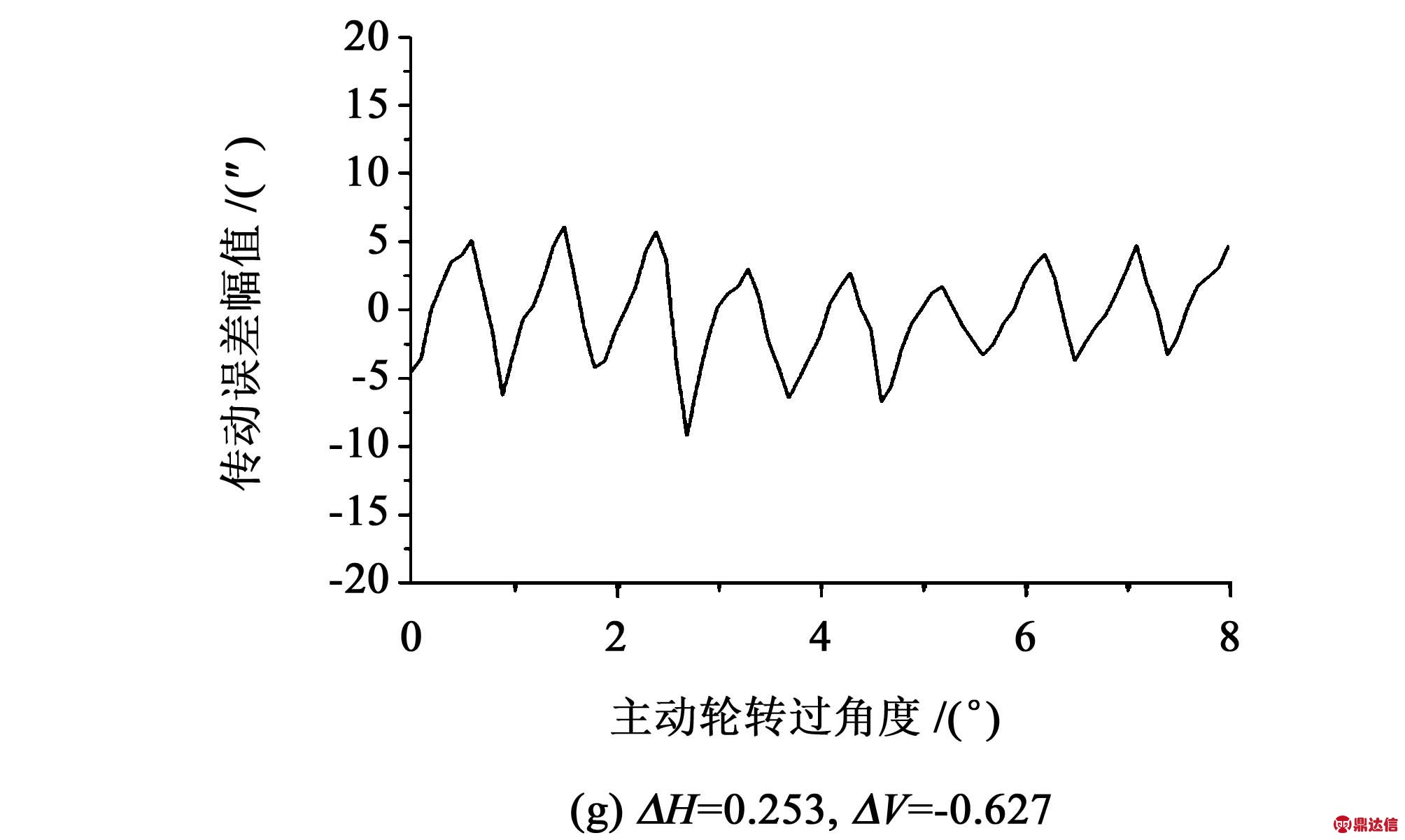
图6 滚检试验传动误差部分曲线
在无磕碰点情况下,通过滚检试验得到7个检测区域相应的传动误差测试曲线,其幅值如表4所示。
表4 传动误差曲线幅值试验结果
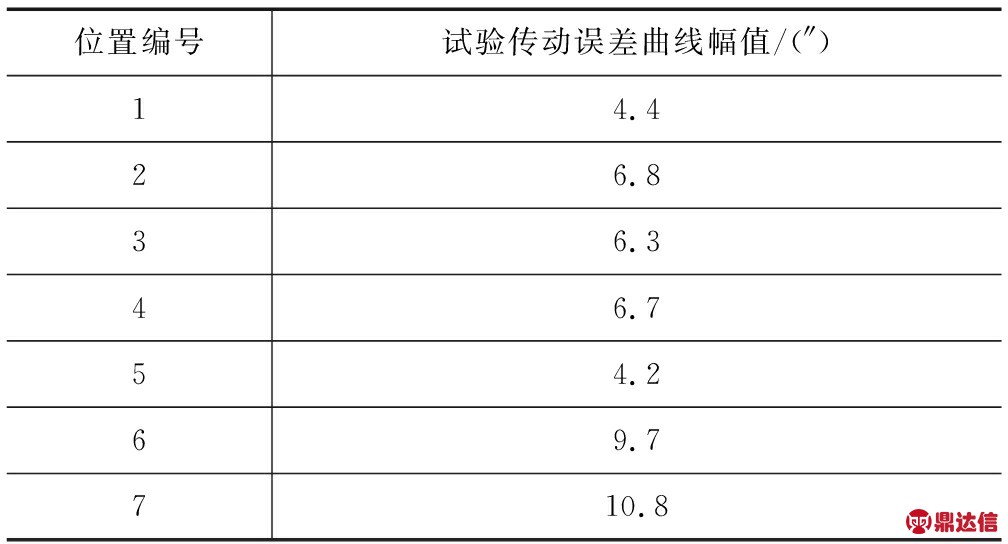
4.2 齿面检测结果及分析
对比表3和表4,理论传动误差曲线与实际传动误差单峰幅值最大误差为16.07%。理论传动误差曲线幅值最大为9.7″。理论传动误差曲线幅值误差设定为20%作为判定磕碰点传动误差幅值的临界值。当实际传动误差幅值超过这一临界值时,则判定该检测区域存在齿面磕碰点。为了更好反映传动误差曲线信息,本文中截取了关键部分啮合齿对相应的传动误差曲线。由图6可得知,传动误差曲线图6(a)、图6(e)两图中第6个波峰幅值急剧增大,传动误差幅值分别达到27.4″、29.9″,明显大于相应的传动误差曲线幅值临界值5.04″和4.92″。由此可知,从动轮凸面第6个齿面中部靠近齿根区域存在磕碰点。
5 结论
(1)根据弧齿锥齿轮副运动关系建立了齿面啮合方程及接触区调整关系模型,得到了接触区位置调整与V、H、J变动量之间的关系。
(2)对磕碰点路径检测进行规划,得到了由7个接触中点组成的接触区移动路径。根据所规划路径,通过改变接触区偏移量,得到对应的啮合参数V、H、J调整量,可用于指导滚检试验。
(3)在YX-HTT600齿轮综合误差测量及分析试验机上进行滚检试验,得到准双曲面齿轮副齿面啮合传动误差曲线。通过与理论传动误差曲线幅值进行对比,选取合适的幅值误差用以判定被检测齿轮副磕碰点,并反映磕碰点位置信息,验证了本文中提出的齿面点测量方法的正确性和有效性。
(4)由于准双曲面齿轮加工、安装及测量过程中存在误差,实际传动误差曲线幅值变化较大,因而本文中提出的检测方法对于轻微磕碰点难以辨别。