摘要:基于格里森制弧齿锥齿轮,运用局部综合法与轮齿接触分析(TCA)技术,研究等高齿弧齿锥齿轮的几何设计、加工参数设计和刀盘参数。通过UG软件,建立该齿轮的三维精确模型,对大、小轮模型进行运动仿真,模拟齿面的接触区情况。该等高齿设计的弧齿锥齿轮,在加工时只需采用0号刀盘,简化了选刀过程,避免了对角接触。此外,该等高齿设计的弧齿锥齿轮能够进行磨齿加工。在GH35铣齿机上进行铣齿试验,试验结果表明:该等高齿接触区规范,易于调整,提高了加工效率。
关键词:弧齿锥齿轮;等高齿;局部综合;对角接触
0 引言
螺旋锥齿轮具有强度高、传动平稳的特点,广泛应用于高速、重载的空间相交轴传动。按照沿齿长方向大小端齿高是否一致,螺旋锥齿轮分为渐缩齿和等高齿。渐缩齿以格里森制设计为代表,采用圆弧齿形;等高齿以奥利康制设计为代表,采用延伸外摆线齿形。在国内,由于受到现有的铣齿设备只能加工渐缩齿等条件的限制,渐缩齿还是一种主要的加工方法;在国外,等高齿在汽车行业中得到越来越广泛的应用[1-2]。奥利康等高齿在加工时,切削效率高,切削过程中连续分度,分度精度高;在使用时,与渐缩齿相比,其在运转噪声控制、传动平稳性方面有一定的优势。因此,在国内等高齿正逐渐受到重视。考虑到奥利康齿轮热处理后无法磨齿,限制了齿轮副性能的进一步提高;奥利康加工机床、刀盘与其配套设备价格极其昂贵,一般企业难以承受[3]。本文提出在原有格里森渐缩齿设计基础上,进行等高齿设计。
该设计等高齿直接在格里森机床上加工,不增加制造成本。加工时按照节锥安装轮坯,齿根角为0°,理论上不存在对角接触,直接选用0号刀盘。与渐缩齿相比,该设计不仅简化了刀号选取的过程,且在加工的过程中接触区规范,只需简单调整即可获得良好的接触区效果,提高效率的同时,降低了对工人技术水平的要求。此外,与奥利康摆线等高齿相比,该设计等高齿可以进行磨齿,对等高齿表面质量的提高具有重要意义。
1 等高齿弧齿锥齿轮的齿形设计
该等高齿基于原格里森渐缩齿的设计,在轮齿大端对根锥和面锥进行倾斜,使面锥母线、根锥母线与节锥母线平行,即根锥、面锥、节锥大小相等,从而达到等高的效果,大端基本参数与渐缩齿设计基本相同。
由于等高齿的齿高在齿长方向保持一致,采用延伸外摆线齿形,齿槽宽和齿顶宽是收缩的,大端齿槽宽和齿顶宽比小端略宽;采用圆弧齿形,大小端齿槽宽是基本一致的,轮齿小端齿顶会因为过度收缩齿顶变尖,降低了轮齿的强度与美观性。为了避免这个问题,主要采取以下3种方法进行解决:(1)采用小尺寸的铣刀盘,等高齿铣齿时根据刀盘与轮齿的收缩情况确定理论刀盘直径,在保证中点螺旋角的条件下,小刀盘的选用,增大了轮齿齿长方向的曲率,从而缩短了齿长,也就有效地减小了轮齿小端的收缩率;(2)采用短齿制设计,将齿顶高因数由弧齿设计通用的0.85减为0.80或更小;(3)轮齿小端倒角,该方法同样可以降低轮齿小端齿顶收缩。
通过举例说明该等高齿设计,表1为该算例的轮坯几何参数。
表1 弧齿锥齿轮副的轮坯参数
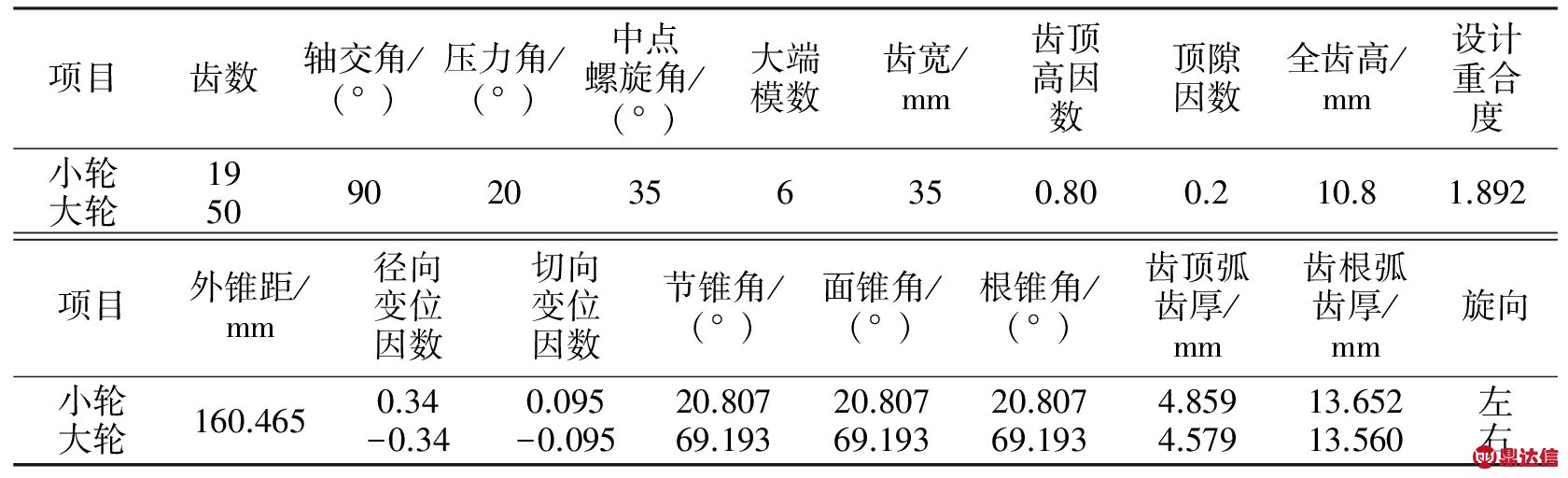
2 等高齿弧齿锥齿轮的轮齿接触分析与加工参数设计
对该等高齿设计运用局部综合法[4-5]进行加工参数计算,理论上使得两齿面在计算参考点附近达到预定的啮合质量,通过轮齿接触分析(TCA)[6],得到更为精确的齿面数据和加工参数。
局部综合是一种二阶分析方法,通过调整参考点处的二阶参数可以有效预控参考点处的啮合性能。在本设计的试验算例中,设置的主要二阶参数有:接触路径与根锥母线的夹角为70°,传动误差的一阶导数值为0.003,接触椭圆的长轴长度为0.26倍齿面宽。采用TCA对该齿轮副进行加工参数验证。TCA分析是一项通过数学计算的方法,模拟齿轮的啮合,可用来验证加工参数是否准确[7-8]。通过对传动误差对称性的调整,大轮凸面的传动误差曲线与接触路径,如图1a所示;大轮凹面的传动误差曲线与接触路径,如图1b所示。理论上该设计齿轮副具有良好的接触性能,相应的加工参数见表2。
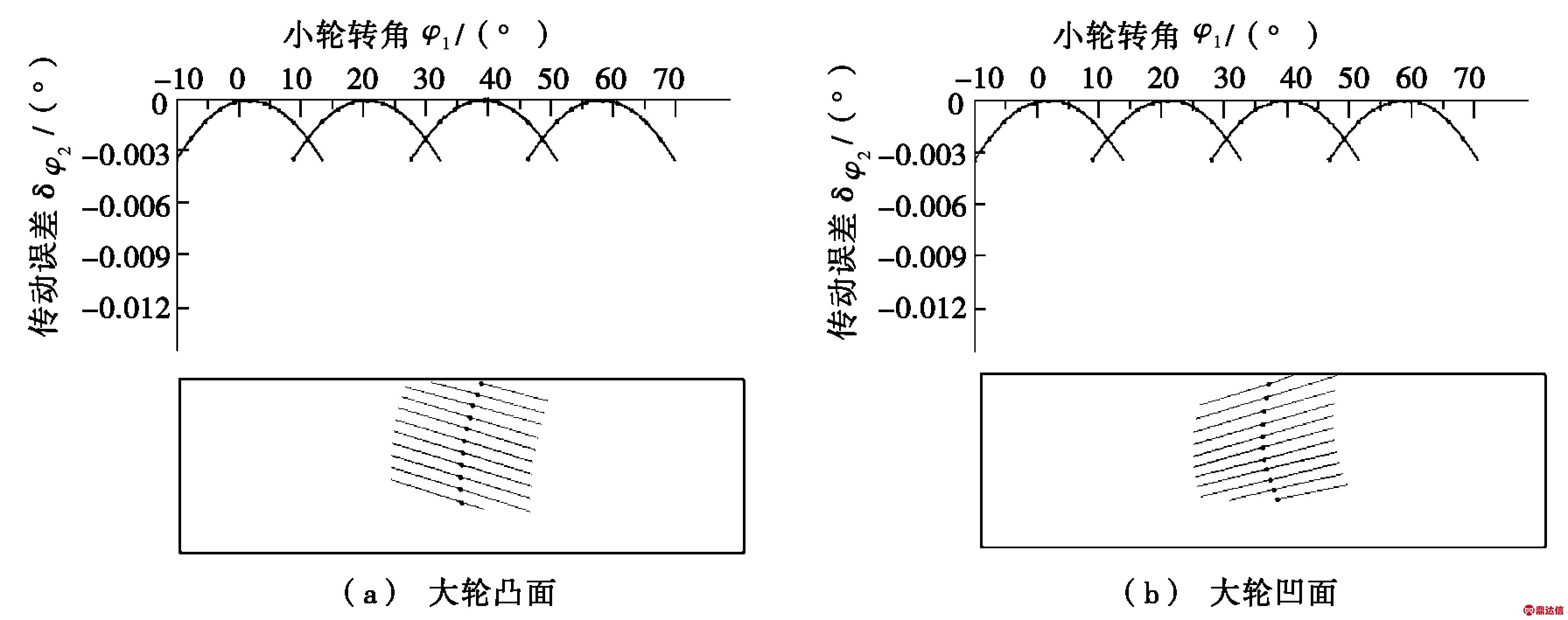
图1 传动误差曲线与接触路径
表2 刀盘参数与机床调整参数
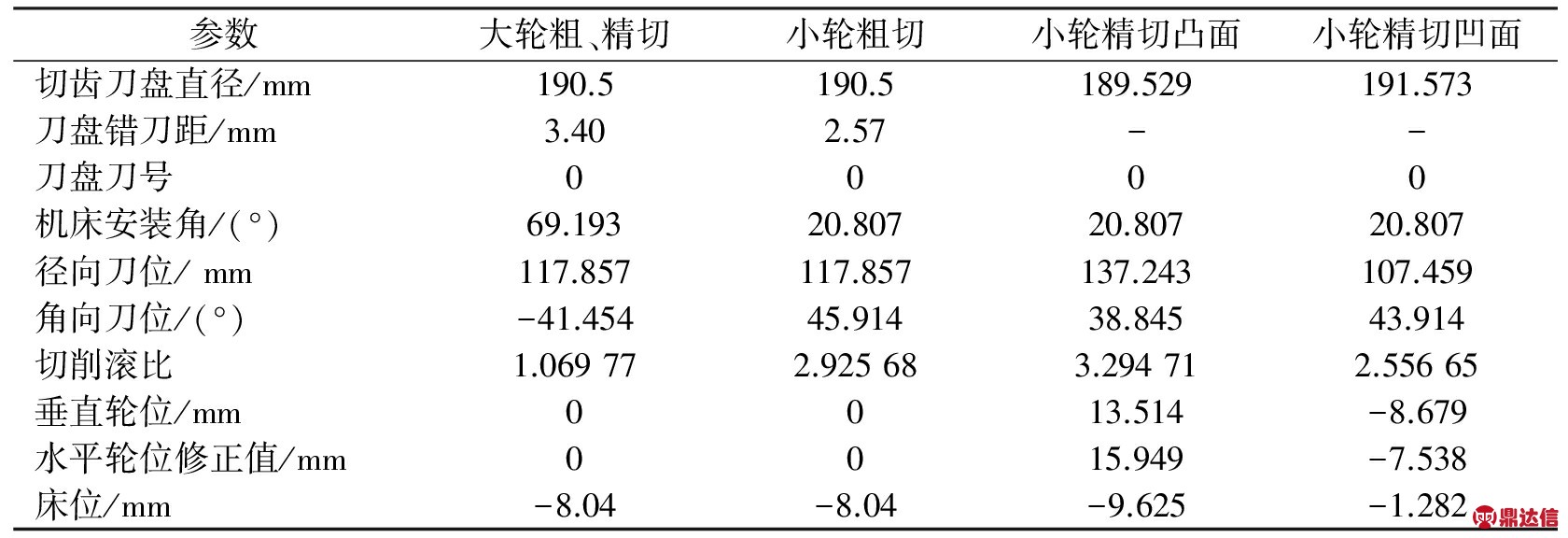
试验在传统格里森弧齿锥齿轮铣齿机上进行,加工过程只需调整刀盘直径、刀齿压力角和机床安装角,其余调整与常规格里森弧齿锥齿轮无异。
0号刀盘的选用,理论上避免了对角接触,接触区规范,易于调整,成为该设计的特点。渐缩齿的加工,采用“平顶产形轮”原理[9],轮坯按照根锥角安装,刀盘轴线垂直于根锥母线,而与节锥母线成一定夹角,若铣齿时铣刀盘的内、外切刀片使用相同压力角,铣出的轮齿在节锥上的压力角并不相等,因此需要对内、外切刀片的压力角进行修正。理论上大、小轮的铣削需要选择不同的刀号进行内、外切刀片压力角的修正,但因为刀号分组以及在实际生产中大、小轮的加工往往采用同一刀号,从而造成了对角接触的产生。对角接触成为影响格里森弧齿锥齿轮接触区状态的重要因素,实际生产中,操作者往往需要多次调整才能获得理想的接触区效果,严重限制了生产效率的提高。一定程度的内对角接触会提高齿轮的接触性能,但应严格避免外对角接触。对角接触带来的负面影响尚无明确定论,但严重的对角接触将影响啮合性能,削弱轮齿强度,降低运转平稳性,增加噪声等。该等高齿设计的根锥、面锥、节锥相等,加工过程中轮坯按照节锥角安装,刀盘轴线垂直于节锥母线,铣出的齿轮在节锥上的压力角相等,根本上避免了对角接触的产生。选择刀号的时候只需选择0号,无需修正内、外切刀片压力角,简化了刀号选取过程的同时,由此加工出的齿轮接触区规范、易于调整,也避免了上述由对角接触带来的诸多问题。
3 基于UG的三维建模与接触区运动仿真
由齿轮副的基本几何参数,得到大轮的加工参数,根据局部综合法,进而得到小轮的加工参数,通过TCA分析,得到更为精确的齿面数据。根据该理论以及齿轮的边界条件,编制程序,计算出一系列按规律排列的齿面接触点,得到与UG曲面建模相匹配的齿面坐标点文件,通过齿面的坐标点拟合曲面可以获得精确的齿面模型。根据该建模过程[10-11],生成齿面坐标点文件,进行弧齿锥齿轮轮齿的精确建模[12-14]。
根据试验算例得到的轮坯几何参数,建立了等高齿曲齿锥齿轮的圆锥体毛坯,通过UG的“通过点”命令,导入小轮齿面坐标点文件,拟合生成小轮齿面。对齿面进行简单修整之后,通过“缝合”、“修剪”命令获得单个齿槽的齿面模型,然后“阵列”得到等高齿弧齿锥齿轮小轮的三维模型。同样,建立大轮的三维模型。
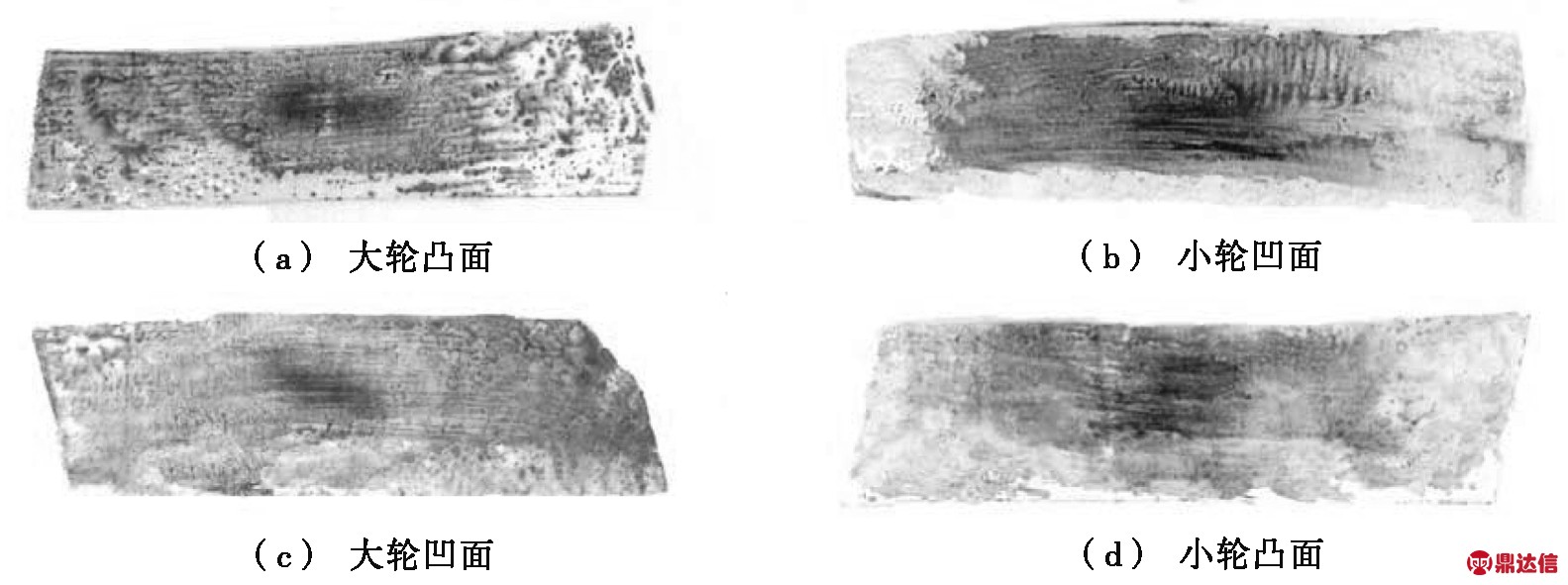
图2 等高齿模型运动仿真瞬时接触状况
为了在试验之前进一步了解齿轮副的接触情况,对该设计齿轮副进行运动仿真。在UG的装配环境下对大小轮进行装配,对必要的参考进行约束。在UG运动仿真模块定义相关运动,进行齿轮副运动仿真。本文采用设置两齿面干涉的方式模拟齿轮副的齿面接触,实际上齿面接触的定义为:当两齿面相接触(接触点或接触线),齿面间距离小于0.006 35 mm时认为齿面是相接触的。为了能够直观地看到齿面接触状况,在设置接触干涉为0.03 mm的情况得到如图2所示的瞬时接触效果。大轮凸面的瞬时接触区与TCA分析结果基本一致,齿面瞬时接触区为位于齿面中间部位的一个椭圆。
4 等高齿弧齿锥齿轮加工试验
本试验采用固定安装法,双面法加工大轮,单面法加工小轮,根据大轮齿面,对小轮齿面进行配切[15]。按照本实例的轮坯几何参数,渐缩齿设计刀盘直径的理论值为264.2 mm,等高齿理论值为165.1 mm,根据设计需要选择名义直径为190.5 mm的标准双面刀盘,刀号采用0号。基于试验条件,本试验在GH35铣齿机上进行。
采用表1中的数据加工齿轮轮坯,严格控制轮坯与夹具的精度。根据表2加工数据进行铣齿试验:首先用双面法加工出大轮,其次按照表2的凸、凹面精切数据调整机床,依次加工出小轮凸面和凹面,小轮凹面如图3所示。将加工好的大轮、小轮按设计安装距安装在滚动检查机上,在大轮的齿面涂上红丹粉,进行滚动检查,滚动的过程中,在齿面的接触区域,小轮齿面会印上红丹粉。
按照初始数据铣齿后,对齿面接触状况进行滚动检查。在齿长方向,小轮凸面接触区基本位于齿面中间略偏大端处,凹面接触区已经位于齿面中部,满足设计要求。在齿高方向,凸、凹面接触都位于齿高中部,均未出现边缘接触。减小偏心角,对小轮凸面接触区进行修正,偏心角初次减小0.4°,铣削之后再次滚检,接触区移向齿宽的中部。最终接触区滚检效果见图4,大轮凸面拓印效果见图5a,大轮凹面拓印效果见图5c,小轮凸面拓印效果见图5d,小轮凹面拓印效果见图5b。观察图4和图5可以清楚看到:红丹粉均匀分布在大、小轮齿面中部,接触区效果良好。
整个铣齿过程中,小轮凹面接触区没有经过任何机床调整修正,一次性出现在齿面理想的位置;只经过一次微调,小轮凸面调整区亦出现在齿面理想的位置。由此可见,本加工方法易于得到理想的齿面接触区,这对于一般的渐缩齿弧齿锥齿轮是难以做到的,可见对角接触对接触区效果的影响之大,而本设计在避免对角接触的同时,简化了齿面接触区调整过程,显著提高了铣齿的加工效率。
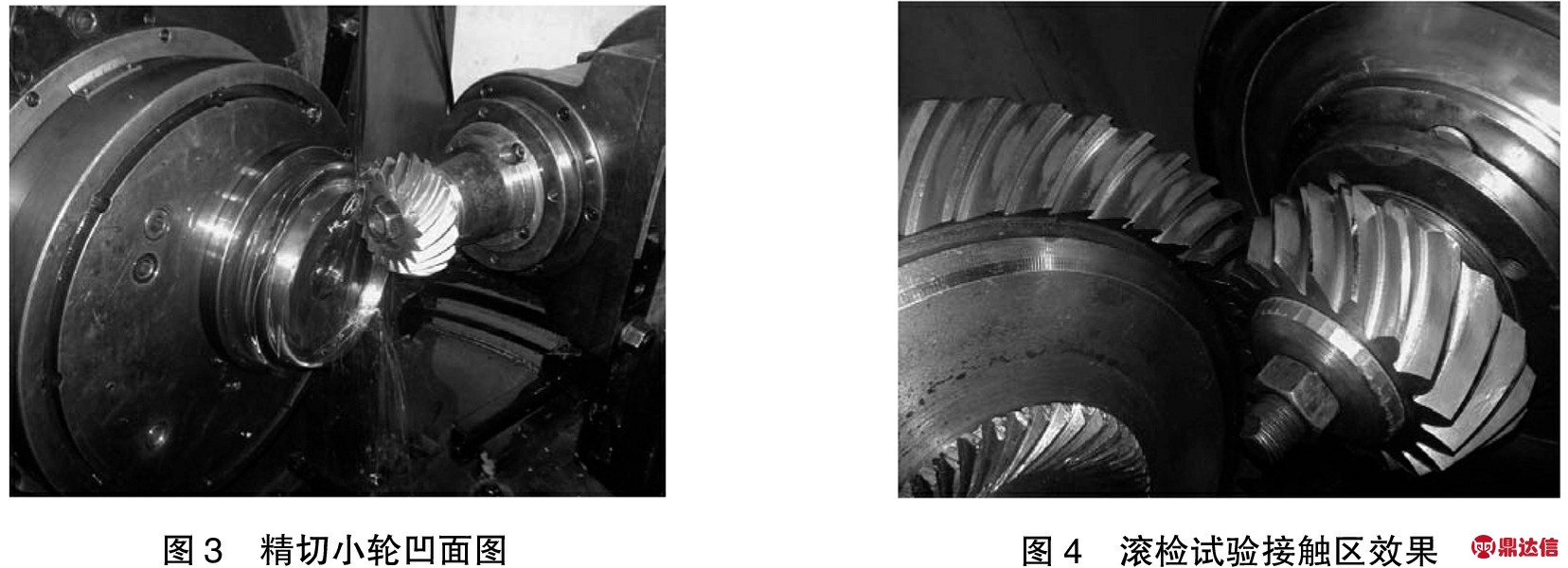
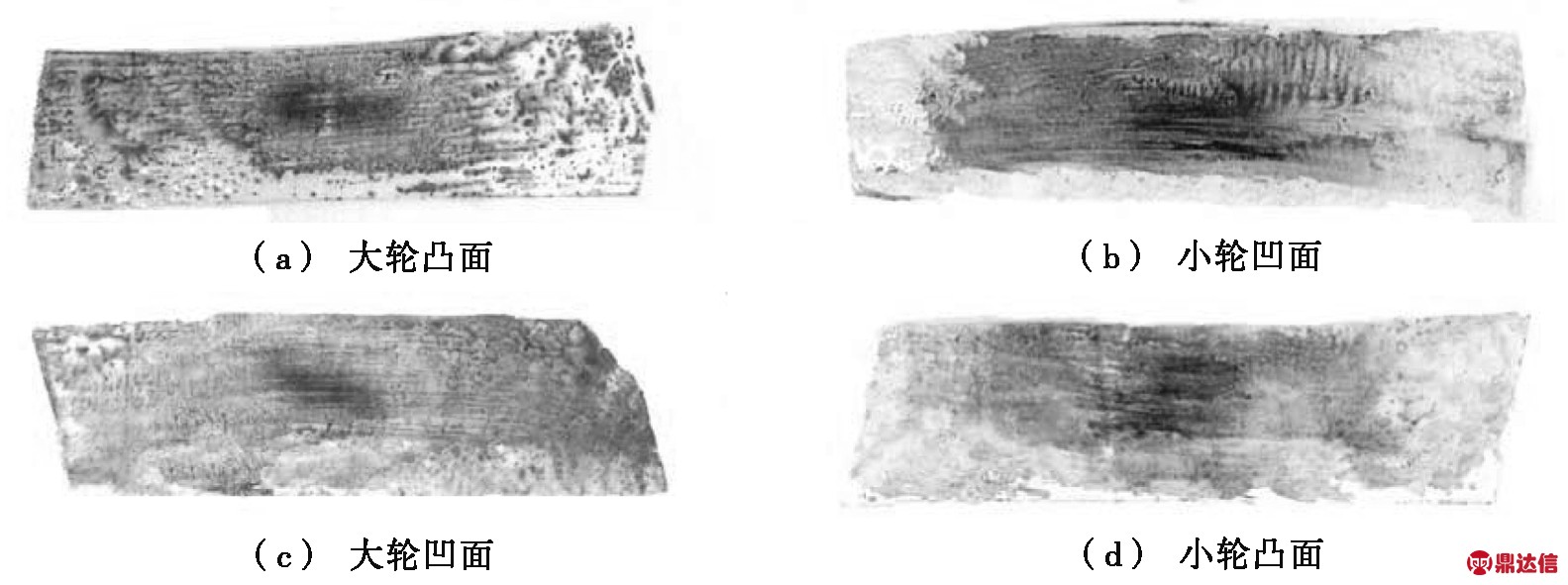
图5 接触区拓印图
对试验样品齿顶收缩量进行测量,大轮大端齿顶宽度为3.1 mm,小端为2.5 mm,收缩量为0.6 mm;小轮大端齿顶宽度为2.8 mm,小端为2.2 mm,收缩量为0.6 mm。三维模型测量结果为:大轮大端齿顶宽度为3.12 mm,小端为2.49 mm,收缩量为0.63 mm;小轮大端齿顶宽度为2.58 mm,小端为1.97 mm,收缩量为0.61 mm。试样样品收缩量与大、小轮设计基本一致,试验样品满足设计要求。
5 结论
本文采用局部综合法和TCA技术,对圆弧齿等高齿齿形进行研究,得到了一套在常规弧齿锥齿轮铣齿机上加工弧齿等高齿的方法,理论上避免了对角接触,并对加工参数进行了计算。通过UG建立了该设计的精确三维模型,模拟了接触区效果。铣齿试验过程中,一次调整即可使接触区位于大、小轮齿面中部,获得理想的接触效果,验证了该设计的实际可行性,消除对角接触之后,该设计接触区规范,易于调整。在滚检过程中,该设计齿轮副运动平稳,噪声低。本文的研究对于提高齿面接触质量和齿轮副的加工效率具有显著的意义。
本文设计与加工出的等高齿针对接触区优化、轮齿强度、运转噪声、振动等性能方面的研究需要进一步展开。