摘 要:根据现有的齿面接触分析(TCA)基本思想,通过分析以局部共轭原理为基础的螺旋锥齿轮的点啮合齿面设计模型,提出了齿面接触区求解的一种新算法:基于齿轮啮合原理和Enler-Rodrigues公式,计算齿面的三维空间啮合点位置,并将三维齿面啮合点投影到齿轮二维轴截面中,再划定接触点搜索区域,利用Newton-Raphson法求出由所有接触点构成的接触迹;以接触迹为整个接触区域的长轴、瞬时接触椭圆长轴为短轴的基本思路,指定接触迹为搜索梯度方向,确定每一个瞬时接触椭圆长轴大小从而判定接触区的大小、形状和位置。采用一对弧齿锥齿轮为例,并编写TCA程序,验证了此方法的可行性,为齿面的局部修形以及后续的齿面承载接触分析(LTCA)提供了理论基础。
关键词:接触区;点啮合齿面;接触迹;瞬时接触椭圆;梯度;齿面修形
1 点啮合齿面形成机理
在螺旋锥齿轮TCA中,根据不同的工况要求,主要存在线接触和点接触这两种形式。每个啮合瞬间,若共轭两齿面沿一条线接触且满足相对运动规律即为线接触,该共轭方式具有承载能力大、运动平稳和噪声小等优点,但对于零件加工误差和安装误差较为敏感、可调性差等缺点,易造成齿轮边缘接触而损坏;若在每个啮合瞬间,两啮合齿面啮合于一点且满足相对运动规律(接触点处两齿面的相对速度垂直于公法线)即为点接触。一般来说,没有载荷及准静态的工况条件下,齿面接触为点接触;而有载荷特别是重载荷工况下,齿面接触形式为线接触。另外,齿面接触区域的位置大小与实际制造中的齿轮副的安装位置有关;同时实际制造过程的制造误差也会对齿面接触区域产生影响。如果齿轮副正确安装其不考虑制造误差影响时,齿面接触发生在齿轮中部,且不会产生边缘接触的现象。如图1、2所示齿面设计与制造中的合理的齿面接触区域[1]。
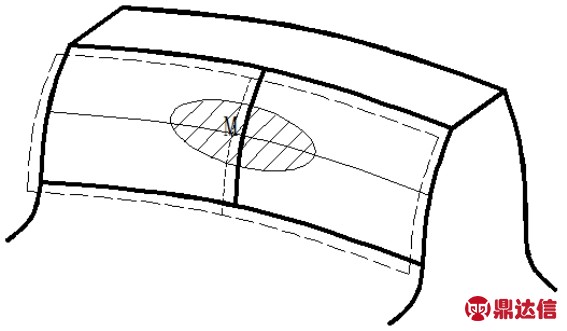
图1 齿面接触区域
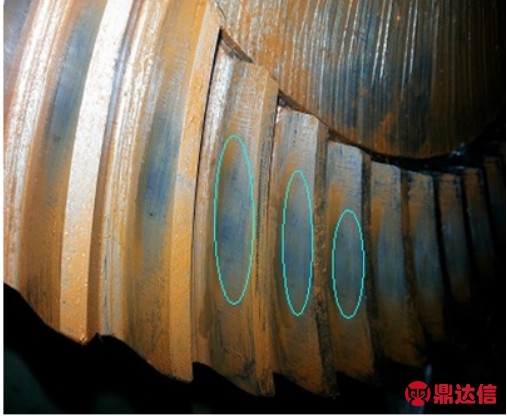
图2 实际接触区形状
2 算法基本思想
从齿轮滚检图片2中可以看到,齿轮的接触轨迹近似为一个较大的椭圆,若齿轮为理想刚体,则整个接触区由一系列点构成,即所谓的“接触印痕”,然而,齿轮在实际齿轮传动过程中,由于载荷的存在会发生齿面弹性变形,而此时的点接触就会变为线接触,而接触印痕会由一个接触点拓展成一个较小的局部接触区,参考文献资料[2]证明该局部接触区的接触边界线数学模型为:

根据赫兹接触理论,接触区域定义为一个椭圆。此时,在瞬时接触椭圆定义中,参数 、 和 具体含义,可参照以下公式:

上式中,δ表示弹性变形量,根据格里森公司的加工手册数据,一般取0.00635mm(切削齿面)或0.00381 mm(研磨齿面);而大轮和小轮在啮合公切面上的法曲率∆k可利用欧拉公式和贝特朗公式求得。根据赫兹接触理论,每一个瞬时接触椭圆的长轴沿齿高方向,短轴沿齿长方向,如图3所示,并判定椭圆长轴(短轴)对应于∆k min (∆k max)方向[3]。因此,整个接触区可以看作由多个小的瞬时接触椭圆构成的一个大椭圆区,而大椭圆的长轴沿接触迹方向,大小可认为由接触点形成的接触迹所确定。
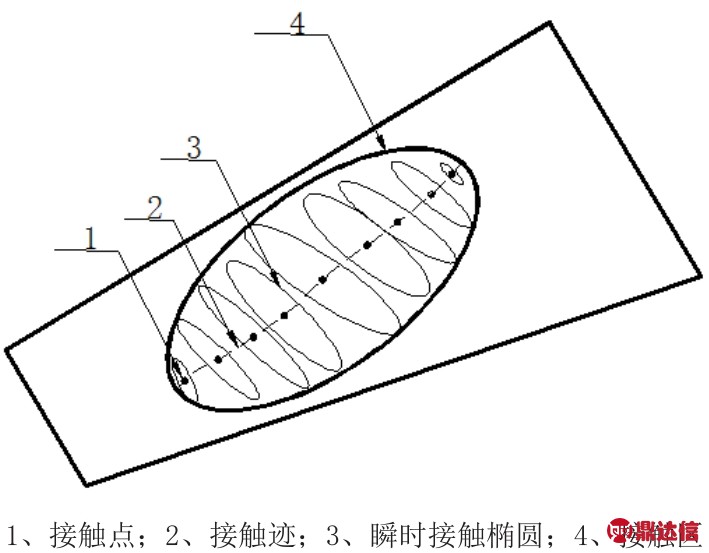
图3 齿面印痕构成要素
3 齿面坐标
如图4所示,在齿轮接触啮合的坐标系下,齿面任意点M到轴线距离表示为ri ,而沿齿轮轴线到设计交叉点Oi 的距离表示为Li ,即

其中,i=1或2分别代表小轮或大轮,齿面坐标(r i , Li )是有关参数(θ i , Φi )的方程。
4 算例分析
文章采用实际工业应用中某型航空发动机螺旋锥齿轮为例,其中大轮凸面和小轮凹面处于齿面共轭接触状态,齿轮副基本参数和加工调整参数[5-6]分别如表1和表2所示。
5 结论
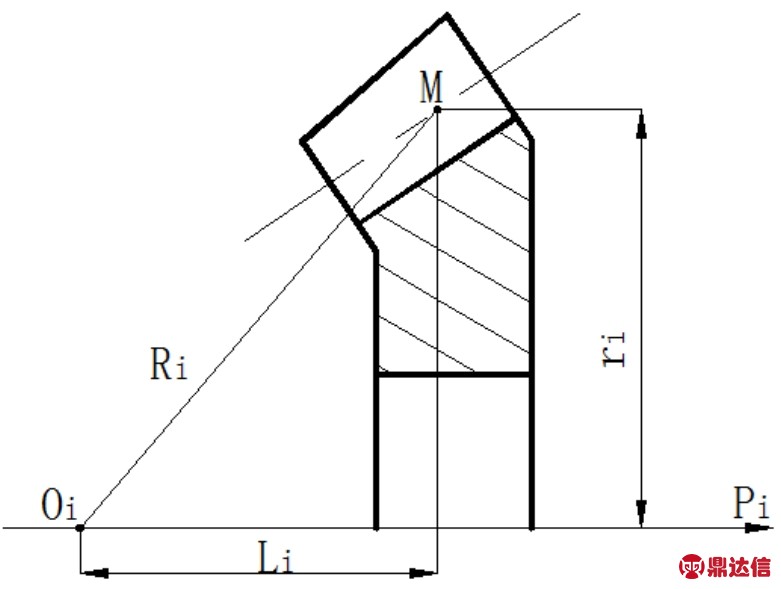
图4 齿面坐标示意图
表1 轮坯基本参数
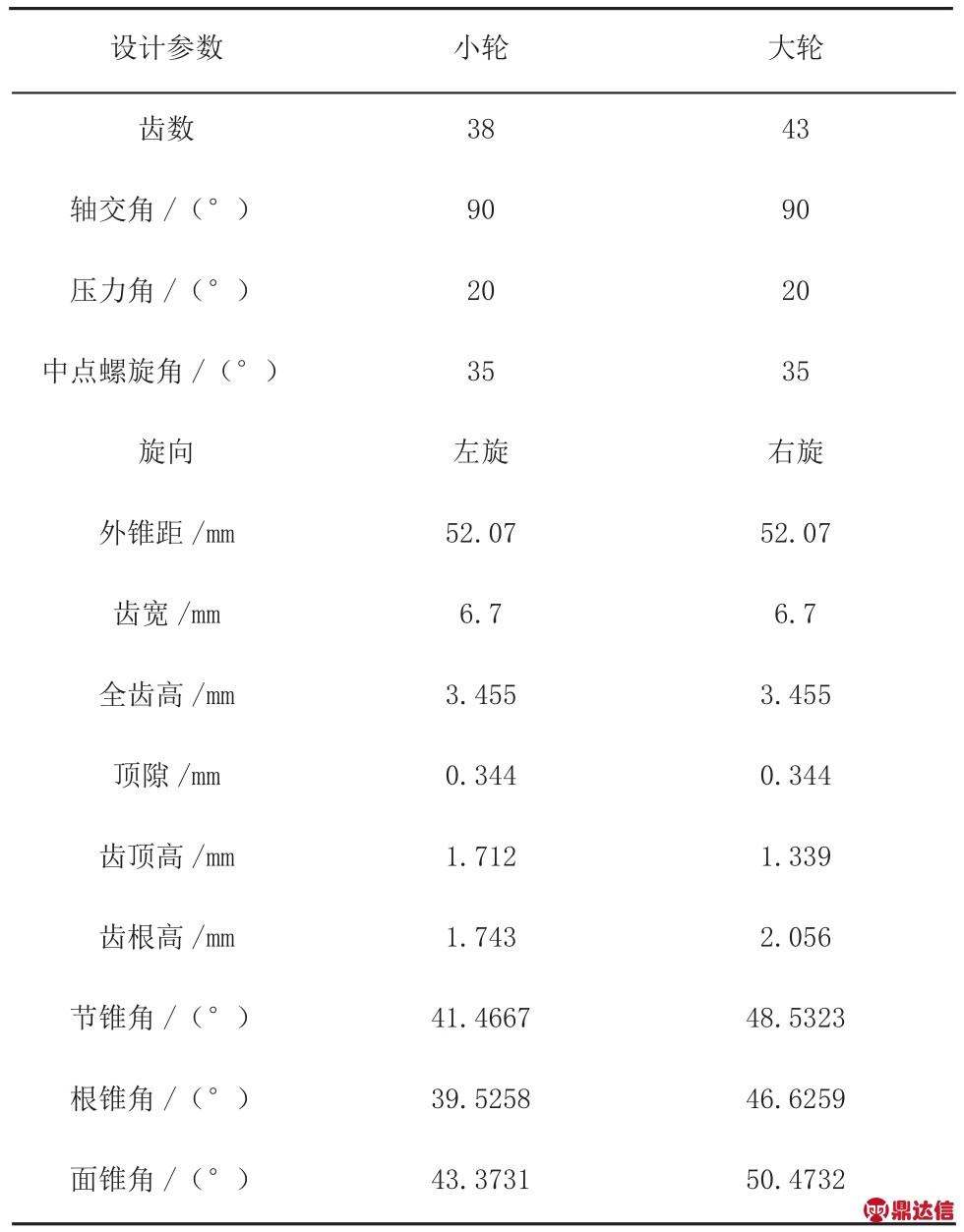
(1)基于齿面局部接触区数学模型和接触区的形状分析,将接触区几何近似处理成椭圆模型,提出了以接触迹为接触区的长轴、局部接触区长轴为短轴的新思路[7]。
(2)文章提出一种新的TCA规划方法,在求解瞬时接触椭圆长轴时,指定接触迹为搜索梯度方向确定瞬时接触椭圆长轴方向和大小;计算结果较传统方法更加真实有效。
表2 轮坯主要加工参数
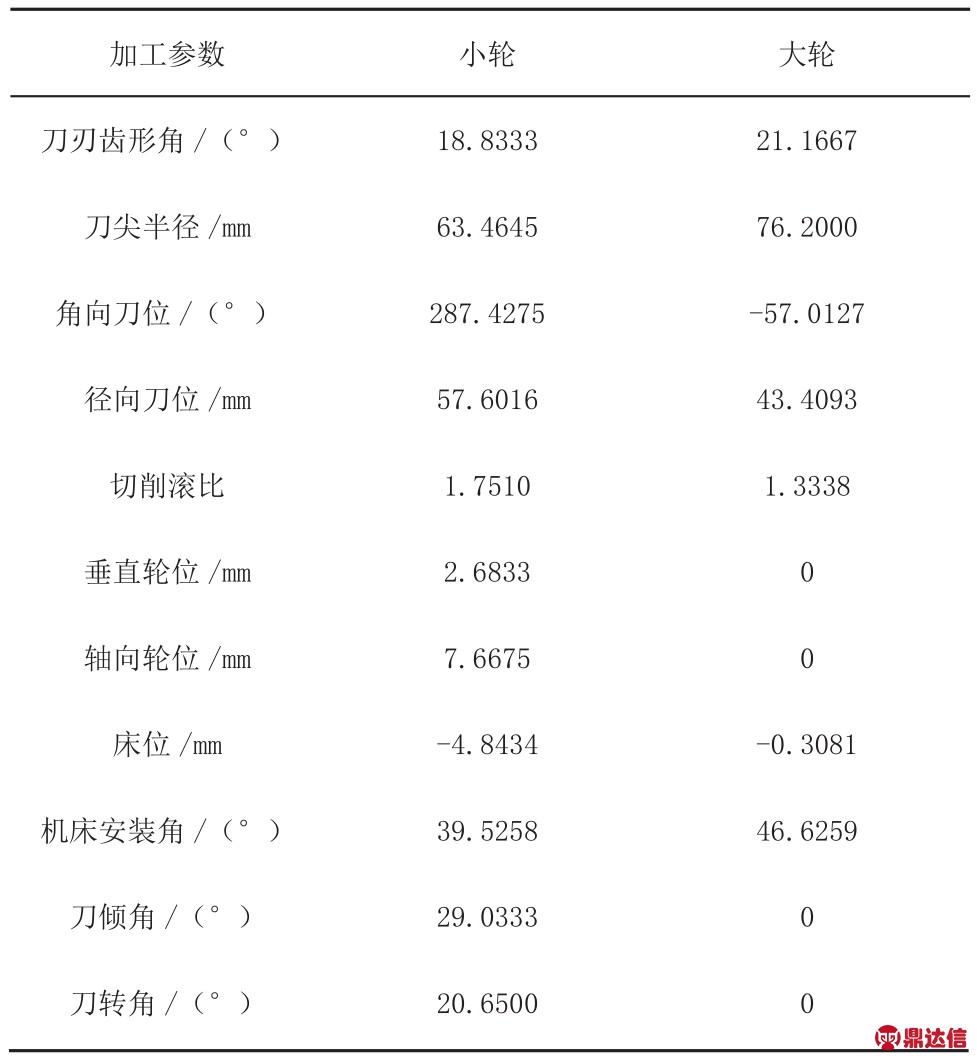
(3)以局部共轭原理为理论基础,该新算法可为实际齿面的局部修形提供一定的理论指导;同时,也可为后续的更加真实有效的齿面载荷接触分析(LTCA)的提供了新的理论途径。